精益生产与新产品研发经典培训教材
合集下载
精益生产培训教材((000002)

16
业绩对比
项目
地区
生产率(辆/人/年)
质量(缺陷/100辆车)
场地(平方英尺/车/年
库存(8个样件,天)
团队(占劳动力%)
工种轮换(0-无 4-高 )
建议数/年/雇员
缺勤率
自动化(组装)
日本
55 60 5.7 0.2 69 3.0
61.6 5.0 1.7
北美
6 82 7.8 2.9 17 0.9
• Ongoing efforts to improve Quality, Productivity, and Responsiveness
• Recognition of employee abilities
• 消除浪费 • 不断改进 • 员工参与
• Builds on synchronous manufacturing
Starting with Toyota in the late 50’s and
catching on in the mid – 80’s in the reminder of the industrial world, Lean Manufacturing has become a key strategy for manufacturers
交货期的保障
2020/1/11
21
生产管理的任务
Quality 质量
Cost 成本
ivery 交货
2020/1/11
22
生产管理者的职责
• 组长:质量及不合格品的注意;生产线 停线的责任
• 领班:生产力改进;成本降低 • 主管:生产控制,作业标准,质量控制,
福特首创的装配线是大规模低品种生产方式的代表, 工人被当成工作的机器
精益生产预览培训教材

某企业精益生产推广案例
企业背景:某大型制造企业,生产多种产品 推广原因:提高生产效率,降低成本 推广过程:成立精益生产小组,进行培训和实施 推广效果:生产效率提高20%,成本降低15%,产品质量提升
精益生产未来发展
智能化精益生产
智能化技术:利用人工智能、大 数据等技术提高生产效率
智能化管理:通过信息化手段实 现生产过程的实时监控和管理
持续改进
建立持续改进的文化和氛围 制定持续改进的计划和目标 定期评估和改进生产流程 鼓励员工提出改进建议和参与改进活动 持续改进的成果分享和激励机制
精益生产案例分析
某企业精益生产实施案例
企业背景:某汽车制造企业 实施时间:2015年 实施目标:提高生产效率,降低成本
实施过程:引入精益生产理念,优化 生产流程,提高员工素质
构成:价值流图通常包括原材料、生产过程、成品、客户等环节,以及信息流、物料流、 时间流等信息。
作用:价值流图可以帮助企业发现生产过程中的瓶颈、浪费和不合理之处,从而进行优 化和改进。
绘制方法:绘制价值流图时,需要按照生产过程的实际流程,将各个环节和信息进行梳 理和绘制,并标注出关键数据,如生产时间、库存量等。
目视化管理
目视化管理的定义:通过视觉信号来传递信息,使员工能够快速、准确地了解生产状况和问题 目视化管理的作用:提高生产效率、降低成本、提高产品质量、减少浪费 目视化管理的工具:看板、信号灯、颜色标记、图表等 目视化管理的应用:生产现场、仓库、办公室等
精益生产实施步骤
制定实施计划
制定计划:根据目标和现状 制定实施计划,包括时间、 人员、资源等
培训目标:提高员工对精益 生产的理解和应用能力
培训方式:理论讲解、案例 分析、实践操作
精益生产基础知识培训教材(PPT 122页)

让咱们进入第一篇的学 习吧,很有意思的, 可要打起神哦!!!
——精益生产概况
精益生产概况
123
定义:
精益生产又称精良生产,其中“精”表示精良、精确、精美;“益” 表示利益、效益等等。一种以追求最大限度地减少企业生产所占用 的资源和降低企业管理和运营成本为主要目标的生产方式。
它是美国麻省理工学院在一项名为“国际汽车计划”的研究项目中 提出来的。它们在做了大量的调查和对比后,认为日本丰田汽车公 司的生产方式是最适用于现代制造企业的一种生产组织管理方式, 称之为精益生产。
精益生产体系
Act
Plan
Kaizen
Check
Do
精益生产基础知识培训
2010.09.24
精益生产体系
➢ 精益生产概况
1. 定义 2. 目标 3. 发展史
➢ 精益生产体系
1. 理念 2. 工具 3. 原则 4. 方法
➢ 精益生产的基础之-5S ➢ 总结
精益生产基础
精益生产体系
➢ 课程安排
•
第一天
•
16:50-17:00
欢迎 学员介绍 精益生产概况(定义、目标、发展史) 课间休息 精益生产体系(理念、工具、原则) 上午课程总结回顾,问题解答 午饭 团队游戏 分组收集信息,价值流图实践练习 课间休息 每组介绍价值流图,点评 设计未来的价值流图 每组介绍未来价值流图,点评 第一天培训总结回顾,问题解答
丰田生产方式又称精细生产方式,或精益生产方式。
精益生产基础
精益生产概况
123
精益生产是一门流程管理哲学,主要来自于丰田制造系统 (TPS)。其焦点在如何减少“7大浪费”以增加客户价值。
丰田的成功使Lean成为21世纪前10年管理科学的热点。
——精益生产概况
精益生产概况
123
定义:
精益生产又称精良生产,其中“精”表示精良、精确、精美;“益” 表示利益、效益等等。一种以追求最大限度地减少企业生产所占用 的资源和降低企业管理和运营成本为主要目标的生产方式。
它是美国麻省理工学院在一项名为“国际汽车计划”的研究项目中 提出来的。它们在做了大量的调查和对比后,认为日本丰田汽车公 司的生产方式是最适用于现代制造企业的一种生产组织管理方式, 称之为精益生产。
精益生产体系
Act
Plan
Kaizen
Check
Do
精益生产基础知识培训
2010.09.24
精益生产体系
➢ 精益生产概况
1. 定义 2. 目标 3. 发展史
➢ 精益生产体系
1. 理念 2. 工具 3. 原则 4. 方法
➢ 精益生产的基础之-5S ➢ 总结
精益生产基础
精益生产体系
➢ 课程安排
•
第一天
•
16:50-17:00
欢迎 学员介绍 精益生产概况(定义、目标、发展史) 课间休息 精益生产体系(理念、工具、原则) 上午课程总结回顾,问题解答 午饭 团队游戏 分组收集信息,价值流图实践练习 课间休息 每组介绍价值流图,点评 设计未来的价值流图 每组介绍未来价值流图,点评 第一天培训总结回顾,问题解答
丰田生产方式又称精细生产方式,或精益生产方式。
精益生产基础
精益生产概况
123
精益生产是一门流程管理哲学,主要来自于丰田制造系统 (TPS)。其焦点在如何减少“7大浪费”以增加客户价值。
丰田的成功使Lean成为21世纪前10年管理科学的热点。
5W方法培训教材(精益生产)

「5W分析」的目的?
投诉回答的内容有追究出真正的原因?并
对其实施对策了吗?
同样的问题再发,那就要去怀疑追究的原
因是否充分!!
9
精益生产
问题解决方法的基本步骤
活用PDCA
1的答案无法被认为是在第一步中写下的问题的根本原因 的话,继续问“为什么”,并找出答案。
连续提问并回答,直到认为问题的根本原因已被识别。
N次因(根因)
6
精益生产
WHY WHY WHY WHY WHY WHY
WHY
问题表象 直接原因
(中间原因)
根本原因
7
精益生产
何谓「5W分析」?
是让发生问题现象的要因有规则地,按顺序地, 毫无遗漏地找出来,并追究出其真因的分析方法.
为何①
为何②
为何③
问题
原因①
原因②
原因③
???
根本原因
対策
8
精益生产
水進入眼中
抓水桶中的魚
被父親罵了
把父親珍貴的金魚 弄死了
板手従上面掉 落下來
從此圖無法推測34
為何④
正在看別處
水桶中的金魚亂跳 將金魚移到其他場
所 金魚放入水桶在搬 運途中、弄翻了水桶
精益生产
案例2:“今天上班迟到案了例101分钟-”迟到
35
精益生产
案例1-迟到 今天上班迟到了10分钟
为什么会迟到?
生产量多
接了很多定单
作业方法没有明确
很少进行该作业
没有及时进行仪器矫正
要做的事情太多了
铅笔芯断了
用的是2B的铅笔
公司要赚钱
注意事项1:推论要理性、客观、避免借口
21
精益生产培训教材(PPT 70页)
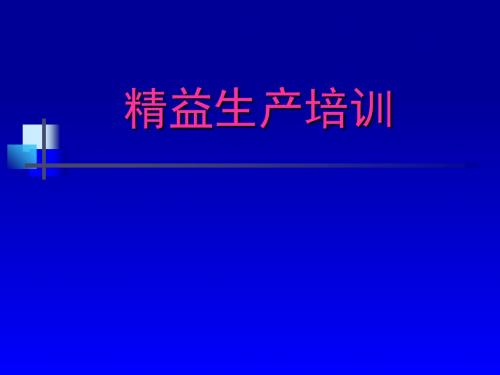
第三部分:精益生产之方式要求 3.2 单件流
第三部分:精益生产之方式要求 3.3 拉动式
何谓“拉动式生产”? 生产活动是由“客户”需求决定的,在进行生产
时,每一个生产过程都是由下一个生产过程的需求决 定,从而不生产额外的产品,这样就可以消除因生产 过剩产生的多余库存了。 为何需要“拉动式生产”? —没有需求的生产是没有意义的; —拉动使生产有了方向性; —通过一级一级的拉动可以使流程有序平稳地进行, 避免了浪费。
以顾客为导向的效率:
提高产量的做法:
改善
400pcs/4人·8hr
600pcs/5人·8hr
做客户需求的产量:
改善
400pcs/4人·8hr
360pcs/3人·8hr
以最少的人员,做出市场实际需求量的产品才是以顾 客为导向的真正的效率提升。
一、精益管理的诞生
课程内容
精益与其说是一种生产方式,更确切
Time ”,简称“JIT”。
“JIT”的概念
JIT是英文“Just In Time”的缩写,翻译成中 文为准时(及时)生产,即通常所讲的使生产做到 “在需要的时候,按需要数量生产所需要的产品”。
其主要目的是使生产过程不要处于盲目状态,而 是建立一种均匀、稳定的、有节奏的生产线。
丰田公司通过多年不断改善,建立了JIT的生产模 式:
一项很细小专一的工作 大批量:每分钟一辆,每天7000辆 价格低:像自来水一样便宜
1.3 精益生产方式
追求零浪费!!
只在适当的时
间里生产市场需 精 要的必要数量的 益
产品
所有的经营活动 都要有效益和 最大的经济性
精益生产的特点:
消除一切浪费,追求精益求精和不断改善。精 简并消除一切不增值的岗位。精简产品开发设 计,生产,管理中一切不产生附加值的工作, 以最优品质,最低成本和最高效率对市场需求 作出最迅速的响应。
精益生产与新产品研发经典培训教材
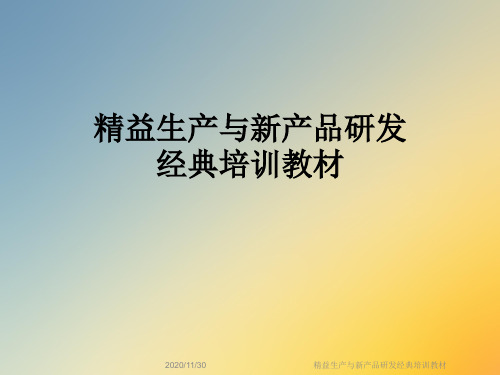
实施“价值流动”原则,组织必须要能够控制信息流 动。主要目的是减少延误,在所有可能的地方以并行 的方式处理信息,从一项活动进展到下一项活动要持 续地增加信息价值,并消除非增值信息。
精益生产与新产品研发经典培训教材
精益原则在研发中的应用
v 原则四:依靠客户需求拉动价值流 在精益研发中,价值流是产品研发全过程的集合,
v 精益供应(2003) 本书以汽车业的供应关系为研究对象,探
讨的是总装厂商和零部件供应商之间旧有关系 的突破和向精益关系的转变。这是继《精益思 想》一书提出精益生产之后,将精益概念由生 产领域推向供应领域的一个新发展。作者提出 精益供应关系是对大批量生产方式下旧有的自 制或外购常规思维的挑战
精益生产与新产品研发经典培训教材
精益生产与新产品研发经典培训教材
精益供应
以欺负供货商的方式实现公司本身的绩效,这种 心态完全违反了丰田生产方式的精神。
——大野耐一
精益生产与新产品研发经典培训教材
v 丰田对新供货商采取谨慎观察评估的态度,一开始只 会下非常少量的订单,新供货商若能在初期订单展现 高标准绩效,就能获得更高数量的订单。丰田也会教 导它们丰田模式,并把它们纳入丰田公司家族。供货 商一旦加入丰田公司家族,除非出现最糟糕的行为, 丰田公司不会把它们踢出“家门”。
质量控制点管理
17
6σ质量管理
18
自働化体系设计
改善模块 生产现场改善模块
设备管理模块 布局及生产方式模块 现场人力资源模块 生产作业改善模块 生产物流及信息流模块
质量管理模块
精益生产与新产品研发经典培训教材
精益研发
在整个产品生命周期中,产品研发虽然只占产品整体成 本的5%,但它却对产品产生70%的影响,这种影响包括成本 、利润、质量、性能等。
精益生产与新产品研发经典培训教材
精益原则在研发中的应用
v 原则四:依靠客户需求拉动价值流 在精益研发中,价值流是产品研发全过程的集合,
v 精益供应(2003) 本书以汽车业的供应关系为研究对象,探
讨的是总装厂商和零部件供应商之间旧有关系 的突破和向精益关系的转变。这是继《精益思 想》一书提出精益生产之后,将精益概念由生 产领域推向供应领域的一个新发展。作者提出 精益供应关系是对大批量生产方式下旧有的自 制或外购常规思维的挑战
精益生产与新产品研发经典培训教材
精益生产与新产品研发经典培训教材
精益供应
以欺负供货商的方式实现公司本身的绩效,这种 心态完全违反了丰田生产方式的精神。
——大野耐一
精益生产与新产品研发经典培训教材
v 丰田对新供货商采取谨慎观察评估的态度,一开始只 会下非常少量的订单,新供货商若能在初期订单展现 高标准绩效,就能获得更高数量的订单。丰田也会教 导它们丰田模式,并把它们纳入丰田公司家族。供货 商一旦加入丰田公司家族,除非出现最糟糕的行为, 丰田公司不会把它们踢出“家门”。
质量控制点管理
17
6σ质量管理
18
自働化体系设计
改善模块 生产现场改善模块
设备管理模块 布局及生产方式模块 现场人力资源模块 生产作业改善模块 生产物流及信息流模块
质量管理模块
精益生产与新产品研发经典培训教材
精益研发
在整个产品生命周期中,产品研发虽然只占产品整体成 本的5%,但它却对产品产生70%的影响,这种影响包括成本 、利润、质量、性能等。
精益生产培训教材(PPT 144页)

学习提纲
生产方式的变革 精益思想的基本原则 精益生产的工具运用与选择 导入精益生产的程序与步骤 精益生产与流程再造
第一章 生产方式的变革
手工生产
低产量 个性化
大规模生产
同步生产
精益生产组织
大批量少品种 工序式生产 设备大难组合
消除浪费 不断改进 员工参与
在同步生产的基础 上,强调缩短生产 周期提高资源利用 率需求驱动
细致、简单、重复 不需专门技能
较粗、多技能、丰富 多技能
高 低 高 物资匮乏、供不应求
低 更低 更高 买方市场
科学管理阶段
20世纪20年代后期开始,科学管理逐渐发展对整个生产领域进行全 面、系统的设计和组织的工业工程学。工业工程学是生产系统管理 工作的一个分支专业领域,指的是对生产所提供的直接支持性服务 ,包括生产进度安排、绩效标准(工时定额)的制订、工作方法的 改进、质量控制、生产设施布局和物料搬运方法的设计等。泰罗、 甘特、吉尔布雷斯是奠基人。
( 1950年初危机,解雇员工2146名,其它员工罢工2月……总裁离任,但与工会协议要将大 野耐一的工作方法列为准则。1950年6月,朝鲜战争爆发,丰田生产卡车,管理层害怕招聘 人再解雇,考虑少人化。可是,怀疑大野耐一的思想,直到1953年,大野耐一做发动机、变 速箱、总装厂总经理,思想才得以实施,1960年,应用到供应方) 2、1969年------生产研究办公室 部分工作主要管理供应商 到现场指导(要求逐年降价); 1973年 供应商参照执行丰田要求管理其合作方。 -到目前为止,第三层以外的供应商未控制到,尤其是原材料方。
案例:1908年福特运用流水线。14分钟装配一辆车!
科学管理的工作内容
1、实行定量工作任务管理,完成任务者有奖; 2、强调并突出计划工作的管理职能,把计划与执行分开; 3、在标准工作条件和方法下进行时间研究,据以制订各类工作的时
精益生产培训教材(共 38张PPT)
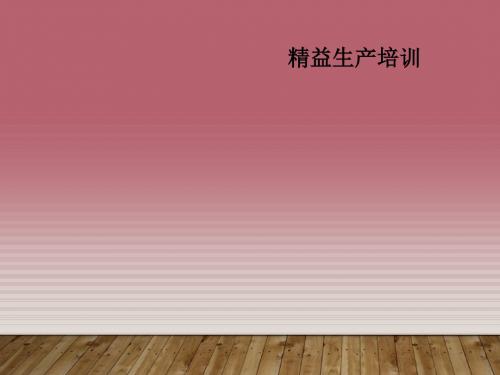
柏拉图
柏拉图
28
• 改善效果之确认
(元)
25000
改善前
(%)
100 75
(元)
25000
改善後 效果
支 出 金 額
20000 15000 10000 5000 0
累 計 比 率
支 出 金 額
20000 15000 10000 5000 0
50 25 0
伙 零 水 教 交 其 食 用 電 育 際 他 費 錢 瓦 費 費 斯 費
经过取消、合并、重排后的必要工序,应 采用最简单的方法或设备替代,以节省人
作业改善压缩
分割转移
作 业 时 间
作 業 改 善
作 业 时 间
工序
1
2
3
4
5
工序
2
3
并行作业,增加人员
拆解去除
1人 作业 作 业 时 间 作 业 时 间
2人 作业
工序
1
2
3
4
5
工序
1
2
3
作业改善后合并
重排
作 业 时 间
作 业 时 间
伙 零 水 教 交 食 用 電 育 際 費 錢 瓦 費 費 斯 費
29 柏拉图
• 效果确认的柏拉图制作要决
1. 2. 3. 4. 必须两个柏拉图并排,分为改善前与改善后。 收集数据的期间和对象必须一致。 季节性的变化应列入考虑。 对於改善项目以外的要因也要加以注意。
3.多能工培养
多能工是指掌握多个岗位作业技
21
QC手法——鱼骨图
开车人数增加
交通事故多
道路施工
收入提高 生活品质提高 虛榮心作祟休闲增加 休息日多 活动地点多 货车任意卸貨 购物商圈 停车位少 等候停车对伍长 收費速度慢
- 1、下载文档前请自行甄别文档内容的完整性,平台不提供额外的编辑、内容补充、找答案等附加服务。
- 2、"仅部分预览"的文档,不可在线预览部分如存在完整性等问题,可反馈申请退款(可完整预览的文档不适用该条件!)。
- 3、如文档侵犯您的权益,请联系客服反馈,我们会尽快为您处理(人工客服工作时间:9:00-18:30)。
设备管理模块 布局及生产方式模块
现场人力资源模块 生产作业改善模块 生产物流及信息流模块
质量管理模块
精益研发
在整个产品生命周期中,产品研发虽然只占产品整体成 本的5%,但它却对产品产生70%的影响,这种影响包括成本、 利润、质量、性能等。
精益研发
1
精益研发的内涵
2
精益研发的特点
3
精益原则在研发中的应用
一问:“为什么机器停了?” 答:“因为超过了负荷,保险丝就断了。” 二问:“为什么超负荷呢?” 答:“因为轴承的润滑不够。” 三问:“为什么润滑不够?” 答:“因为润滑泵吸不上油来。” 四问:“为什么吸不上油来?” 答:“因为油泵轴磨损、松动了。” 五问:“为什么磨损了呢?”
通过学习持续改善
改善的工具体系
2.团队合作
精益领导者 精益员工 供应商
精益员工
A. 能把大量的工作任务和责任转移到在真正为组织增 值工作的生产线工人身上:投资员工,培训多能工;
B. 有一个处在适当位置的缺陷监测系统,一旦发现问 题,生产线工人就能对自己负责区域就能快速追查 并找到其最终原因。
精益供应网络
寻找坚实伙伴,以长期互惠方式共同成长,共 存共荣。
NO.
改善工具名称
1
现场5S管理
2
QCC活动
3
现场管理看板
4
设备管理TPM
5
设备管理流程优化
6
一个流生产布局
7
生产均衡化
8
现场组织结构设计
9
基层员工薪酬体系设计
10
作业研究
11
程序分析
12
现场主义
13
看板及信息化系统
14
物料配送标准化
16
质量控制点管理
17
6σ质量管理
18
自働化体系设计
改善模块 生产现场改善模块
选择:谨慎观察、评估 态度:不断激励改进
以欺负供货商的方式实现公司本身的绩效, 这种心态完全违反了丰田生产方式的精神。 ——大野耐一
3.持续改善
现场现物,自习观察,深入思考。 决策要慢,执行要快 通过学习持续改善
现场现物,自习观察,深入思考
并不是亲自到现场查看而已,而是要问:“发生了什么? 你看到什么? 情况如何?问题何在?”
实行差异化,简化产品开发流程
Cloke Product Lifecycle Management(2006)
Greives
• 注意从新客户和最主要客户处获得新思想
大量生产
自身的内部管理 库存是必要的恶物 强调达到个人工作高效 次品看成生产中的必然结果 数量很大的标准化产品
刚性自动化 组织机构庞大 可随时解雇,工作无保障 互不信任,无长期打算 附属于岗位的“设备”
二、全局图
三、精益思想
精益观念 团队合作 持续改善
1.精益观念
使命 顾客至上 杜绝浪费
LeaKnaPrlrsosodnu,ctAshSlsttarrotmwith Lean Design (2000)
• 将JIT制造体系应用于新产品开发流程 • 没有对精益开发做系统研究
• 提出精益产品开发的概念,包含:供应商关系、跨 职能团队、并行工程、活动集成、战略管理等。
• 没有考虑价值识别和价值流图的应用 • 通过模块化设计建立共同平台,尽可能晚地对产品
• 首次提出精益生产方式的概念
Womack, Jones, Roos • 首次提出精益研发的概念
Developing Products in Half the Time (1991)
TheSDmifitfihc,ulRt ePiantehrttsoeLnean Product
Development(1996)
4
精益研发的实现方式
精益研发的内涵
精益研发 精:精良,提高品质 益:效益,高附加值
创造技术领先优势 提高产品技术附加值
精益生产 精:精炼,消除浪费 益:效益,降低成本
提高效率,降低成本 形成成本领先优势
核心思想:顾客价值最大化,资源浪费最小化, 用更少的资源创造更多的价值。
文献综述
改变世界的机器(1991)
Ad新d发Y展ou阶r 段Text 精益A生dd产Y体ou系r 的Te系xt统化 丰田T生P产S方形式的成形和成与完完善善阶段
TPS形成和完善 1.丰田佐吉
2.丰田喜一郎
6.新乡重夫
TPS
3
精益生产体系系统化(1980s-1990s)
Jame R. Womack, Daniel T. Jones Horst Wildemann:精益管理 Richard Lamming:精益供应 Karlsson,C.,Ahlstrom,P. 精益开发 Jeffrey K.Liker:如何推广精益生产
精益生产方式的新发展阶段 (20世纪末-至今)
在此阶段,精益思想跨出了它的诞生地— —制造业,作为一种普遍的管理哲理在各个行 业传播和应用,先后出成功地在建筑设计和施 工中应用,在服务行业、民航和运输业、医疗 保健领域、通信和邮政管理以及软件开发和编 程等方面应用,使精益生产系统更加完善。
3.精益生产的定义
精益生产与研发
1
精益起源和思想
2
精益研发
3
精益供应与生产
4
精益案例
PART1 精益生产起源和思想
起源和定义 全局图 精益思想
一、起源和定义
1.认识精益生产:起源和发展
产生原因分析 必然性:市场需求 偶然性:战后丰田 契 机:石油危机
2.精益生产的发展阶段
20世纪末-至今 1980s-1990s 1930s-1970s
麻省理工学院(MIT) 丰田公司总结的精益指导思想 精益更是一种企业运作的理念
4.精益生产与大量生产
精益生产
优化范围 库存理念 业务控制 质量控制 产品特征 自动化性质 组织结构 雇员关系 供应商关系 “人”的观念
整个大生产系统 库存是万恶之源 相互协作及业务流程的精简 消除一切次品所带来的浪费 面向用户、生产周期短 柔性自动化,但尽量精简 删除多余环节,扁平化 终身雇佣,以企业为家 同舟共济、生死与共 尽力发挥人的能动性
1.精益观念
使命 运营所在地国家 员工 公司的整体成长 社会责任
1.精益观念
顾客至上 “带着顾客第一的意识奋力
拼搏!”
2)“顾客希望从这个流程中 获得什么?”
3)丰田式客户关系
1.精益观念
杜绝浪费 库存浪费 过渡生产(制造过多或过早浪费) 品质缺陷(不良品浪费) 运输(搬运浪费) 处理(加工浪费) 动作浪费
现场人力资源模块 生产作业改善模块 生产物流及信息流模块
质量管理模块
精益研发
在整个产品生命周期中,产品研发虽然只占产品整体成 本的5%,但它却对产品产生70%的影响,这种影响包括成本、 利润、质量、性能等。
精益研发
1
精益研发的内涵
2
精益研发的特点
3
精益原则在研发中的应用
一问:“为什么机器停了?” 答:“因为超过了负荷,保险丝就断了。” 二问:“为什么超负荷呢?” 答:“因为轴承的润滑不够。” 三问:“为什么润滑不够?” 答:“因为润滑泵吸不上油来。” 四问:“为什么吸不上油来?” 答:“因为油泵轴磨损、松动了。” 五问:“为什么磨损了呢?”
通过学习持续改善
改善的工具体系
2.团队合作
精益领导者 精益员工 供应商
精益员工
A. 能把大量的工作任务和责任转移到在真正为组织增 值工作的生产线工人身上:投资员工,培训多能工;
B. 有一个处在适当位置的缺陷监测系统,一旦发现问 题,生产线工人就能对自己负责区域就能快速追查 并找到其最终原因。
精益供应网络
寻找坚实伙伴,以长期互惠方式共同成长,共 存共荣。
NO.
改善工具名称
1
现场5S管理
2
QCC活动
3
现场管理看板
4
设备管理TPM
5
设备管理流程优化
6
一个流生产布局
7
生产均衡化
8
现场组织结构设计
9
基层员工薪酬体系设计
10
作业研究
11
程序分析
12
现场主义
13
看板及信息化系统
14
物料配送标准化
16
质量控制点管理
17
6σ质量管理
18
自働化体系设计
改善模块 生产现场改善模块
选择:谨慎观察、评估 态度:不断激励改进
以欺负供货商的方式实现公司本身的绩效, 这种心态完全违反了丰田生产方式的精神。 ——大野耐一
3.持续改善
现场现物,自习观察,深入思考。 决策要慢,执行要快 通过学习持续改善
现场现物,自习观察,深入思考
并不是亲自到现场查看而已,而是要问:“发生了什么? 你看到什么? 情况如何?问题何在?”
实行差异化,简化产品开发流程
Cloke Product Lifecycle Management(2006)
Greives
• 注意从新客户和最主要客户处获得新思想
大量生产
自身的内部管理 库存是必要的恶物 强调达到个人工作高效 次品看成生产中的必然结果 数量很大的标准化产品
刚性自动化 组织机构庞大 可随时解雇,工作无保障 互不信任,无长期打算 附属于岗位的“设备”
二、全局图
三、精益思想
精益观念 团队合作 持续改善
1.精益观念
使命 顾客至上 杜绝浪费
LeaKnaPrlrsosodnu,ctAshSlsttarrotmwith Lean Design (2000)
• 将JIT制造体系应用于新产品开发流程 • 没有对精益开发做系统研究
• 提出精益产品开发的概念,包含:供应商关系、跨 职能团队、并行工程、活动集成、战略管理等。
• 没有考虑价值识别和价值流图的应用 • 通过模块化设计建立共同平台,尽可能晚地对产品
• 首次提出精益生产方式的概念
Womack, Jones, Roos • 首次提出精益研发的概念
Developing Products in Half the Time (1991)
TheSDmifitfihc,ulRt ePiantehrttsoeLnean Product
Development(1996)
4
精益研发的实现方式
精益研发的内涵
精益研发 精:精良,提高品质 益:效益,高附加值
创造技术领先优势 提高产品技术附加值
精益生产 精:精炼,消除浪费 益:效益,降低成本
提高效率,降低成本 形成成本领先优势
核心思想:顾客价值最大化,资源浪费最小化, 用更少的资源创造更多的价值。
文献综述
改变世界的机器(1991)
Ad新d发Y展ou阶r 段Text 精益A生dd产Y体ou系r 的Te系xt统化 丰田T生P产S方形式的成形和成与完完善善阶段
TPS形成和完善 1.丰田佐吉
2.丰田喜一郎
6.新乡重夫
TPS
3
精益生产体系系统化(1980s-1990s)
Jame R. Womack, Daniel T. Jones Horst Wildemann:精益管理 Richard Lamming:精益供应 Karlsson,C.,Ahlstrom,P. 精益开发 Jeffrey K.Liker:如何推广精益生产
精益生产方式的新发展阶段 (20世纪末-至今)
在此阶段,精益思想跨出了它的诞生地— —制造业,作为一种普遍的管理哲理在各个行 业传播和应用,先后出成功地在建筑设计和施 工中应用,在服务行业、民航和运输业、医疗 保健领域、通信和邮政管理以及软件开发和编 程等方面应用,使精益生产系统更加完善。
3.精益生产的定义
精益生产与研发
1
精益起源和思想
2
精益研发
3
精益供应与生产
4
精益案例
PART1 精益生产起源和思想
起源和定义 全局图 精益思想
一、起源和定义
1.认识精益生产:起源和发展
产生原因分析 必然性:市场需求 偶然性:战后丰田 契 机:石油危机
2.精益生产的发展阶段
20世纪末-至今 1980s-1990s 1930s-1970s
麻省理工学院(MIT) 丰田公司总结的精益指导思想 精益更是一种企业运作的理念
4.精益生产与大量生产
精益生产
优化范围 库存理念 业务控制 质量控制 产品特征 自动化性质 组织结构 雇员关系 供应商关系 “人”的观念
整个大生产系统 库存是万恶之源 相互协作及业务流程的精简 消除一切次品所带来的浪费 面向用户、生产周期短 柔性自动化,但尽量精简 删除多余环节,扁平化 终身雇佣,以企业为家 同舟共济、生死与共 尽力发挥人的能动性
1.精益观念
使命 运营所在地国家 员工 公司的整体成长 社会责任
1.精益观念
顾客至上 “带着顾客第一的意识奋力
拼搏!”
2)“顾客希望从这个流程中 获得什么?”
3)丰田式客户关系
1.精益观念
杜绝浪费 库存浪费 过渡生产(制造过多或过早浪费) 品质缺陷(不良品浪费) 运输(搬运浪费) 处理(加工浪费) 动作浪费