HCPL-3120中文资料
莫萨公司OnCell 3120-LTE-1系列产品说明书

OnCell3120-LTE-1SeriesIndustrial LTE Cat.1cellular gatewaysFeatures and Benefits•Low power consumption(40mW in standby)•GuaranLink for reliable cellular connectivity•Dual cellular operator backup with dual-SIM•Cellular WAN and Ethernet WAN backup mechanism for a complete pathredundancy•Rugged hardware design well suited for hazardous locations(ATEX Zone2/IECEx)•VPN secure connection capability with IPsec,GRE,and OpenVPN protocolsCertificationsIntroductionThe OnCell3120-LTE-1Series is a set of reliable,secure,low power consumption LTE gateways with state-of-the-art global LTE Cat1coverage. These LTE cellular gateways provide reliable connections from remote serial and Ethernet devices to a cellular network so that your applications can be easily implemented for IIoT remote-access scenarios.With its efficient power saving features,the OnCell3120-LTE-1Series lowers power consumption to less than40mW when in standby mode which can be managed using schedules.To enhance industrial reliability,the OnCell3120-LTE-1features GuaranLink to ensure robust cellular connectivity.Remote Access Gateway with VPN and Network Security•Managed by centralized IP management software,OnCell Central Manager•Secure and reliable VPN support with NAT/OpenVPN/GRE/IPsec functionality•Cybersecurity features based on IEC62443-4-2Industrial-grade Reliability•Rugged hardware design well suited for hazardous locations(ATEX,C1D2,IECEx)•GuaranLink for reliable cellular connectivity•WAN backup between cellular and Ethernet•-30to70°C wide operating temperature•Low power consumption:Less than40mW in standby modeSpecificationsCellular InterfaceCellular Standards LTE CAT-1,HSPA,UMTS,EDGE,GPRS,GSMLTE Data Rate10MHz bandwidth:10.2Mbps DL,5.2Mbps ULHSPA Data Rates7.2Mbps DL,5.76Mbps ULBand Options(EU)LTE Band1(2100MHz)/LTE Band3(1800MHz)/LTE Band7(2600MHz)/LTE Band8(900MHz)/LTE Band20(800MHz)/LTE Band28A(700MHz)UMTS/HSPA900MHz/1800MHz/2100MHzGSM900MHz/1800MHzBand Options(AU)LTE Band3(1800MHz)/LTE Band5(850MHz)/LTE Band8(900MHz)/LTE Band28(700MHz)UMTS/HSPA2100MHz/850MHz/900MHzBand Options(US)LTE Band2(1900MHz)/LTE Band4(1700MHz(AWS))/LTE Band5(850MHz)/LTEBand12(700MHz)/LTE Band13(700MHz)/LTE Band14(700MHz)/LTE Band66(1700MHz)/LTE Band71(600MHz)UMTS/HSPA1900MHz/1700MHz/850MHzNo.of SIMs2SIM Format Nano SIMCellular Antenna Connectors2SMA femaleEthernet Interface10/100BaseT(X)Ports(RJ45connector)2USB InterfaceNo.of USB Ports1USB Connector USB Type AUSB Standards USB2.0Serial InterfaceNo.of Ports1Connector DB9maleSerial Standards RS-232/422/485Data Bits5,6,7,8Stop Bits1,1.5,2Parity None,Even,Odd,Space,MarkBaudrate75bps to921.6kbpsConsole Port RS-232(TxD,RxD,GND),4-pin header output(115200,n,8,1)Serial SignalsRS-232TxD,RxD,RTS,CTS,DTR,DSR,DCD,GNDRS-422Tx+,Tx-,Rx+,Rx-,GNDRS-485-2w Data+,Data-,GNDRS-485-4w Tx+,Tx-,Rx+,Rx-,GNDEthernet Software FeaturesManagement GuaranLink,DHCP server,DDNS,ARP,Telnet,TCP/IP,UDP,SMTP,Remote SMSControl,Power Saving,Syslog,SNMPv1/v2c/v3,Serial Console,Telnet Console,WebConsole,OnCell Central Manager,Wireless Search UtilityFirewall Filter:MAC,IP protocol,port-based,Access IP listSecurity HTTPSTime Management SNTP ClientIPsec VPNAuthentication PSK/X.509/RSAEncryption DES,3DES,AES,MD5,SHA-1,DH2,DH5Concurrent VPN Tunnels5NATFeatures NAT loopback,1-to-1,N-to-1,Port forwardingOpenVPNOpenVPN OpenVPN(client and server),Tunnel mode(routing)and TAP mode(bridge) Encryption Blowfish CBC,DES CBC,DES-EDE3CBC,AES-128/192/256CBC Concurrent VPN Tunnels5Power ParametersInput Current0.8A(max.)Input Voltage9to36VDCPower Consumption5W(typ.)Power Connector Terminal blockReverse Polarity Protection SupportedPower Button Reset buttonPhysical CharacteristicsHousing MetalIP Rating IP30Dimensions128.5x26x89.1mm(5.06x1.02x3.51in)Weight550g(1.22lb)Installation DIN-rail mounting,Wall mounting(with optional kit)Environmental LimitsOperating Temperature Standard Models:0to55°C(32to131°F)Wide Temp.Models:-30to70°C(-22to158°F)Storage Temperature(package included)-40to85°C(-40to185°F)Ambient Relative Humidity5to95%(non-condensing)Standards and CertificationsEMC EN55032/35,EN61000-6-2/-6-4EMI CISPR22,FCC Part15B Class AEMS IEC61000-4-2ESD:Contact:4kV;Air:8kVIEC61000-4-3RS:80MHz to1GHz:10V/mIEC61000-4-4EFT:Power:1kV;Signal:1kVIEC61000-4-5Surge:Power:1kV;Signal:1kVIEC61000-4-6CS:10V;150kHz to80MHzIEC61000-4-8:30A/mFreefall IEC60068-2-32Hazardous Locations ATEX,IECEx,Class I Division2Radio Frequency PTCRB,FCC ID SLE-LE910CXNFRadio RCM,KCCarrier Approvals VerizonAT&TCellular Standards EN301511EN301908-1EN62311(MPE SAR)AS/CA S042EN301489-1/-52Safety IEC60950-1,IEC62368-1,UL60950-1,UL62368-1 Shock IEC60068-2-27Vibration IEC60068-2-6Green Product RoHS,CRoHS,WEEEMTBFTime585,775hrsStandards Telcordia SR332WarrantyWarranty Period5yearsDetails See /warrantyPackage ContentsDevice1x OnCell3120-LTE-1Series LTE cellular gateway1 Installation Kit1x DIN-rail kitDocumentation1x quick installation guide1x warranty cardDimensions1.An activated nano SIM card(not included)must be provided by a third party Cellular Service Provider.Ordering InformationOnCell3120-LTE-1-EU LTE Cat1B1(2100MHz)/B3(1800MHz)/B7(2600MHz)/B8(900MHz)/B20(800MHz)/B28A(700MHz)-0to55°C Wall,DIN railOnCell3120-LTE-1-EU-T LTE Cat1B1(2100MHz)/B3(1800MHz)/B7(2600MHz)/B8(900MHz)/B20(800MHz)/B28A(700MHz)-30to70°C Wall,DIN railOnCell3120-LTE-1-AU LTE Cat1B3(1800MHz)/B5(850MHz)/B8(900MHz)/B28(700MHz)-0to55°C Wall,DIN railOnCell3120-LTE-1-AU-T LTE Cat1B3(1800MHz)/B5(850MHz)/B8(900MHz)/B28(700MHz)-30to70°C Wall,DIN railOnCell3120-LTE-1-US LTE Cat1B2(1900MHz)/B4(1700MHz)/B5(850MHz)/B12(700MHz)/B13(700MHz)/B14(700MHz)/B66(1700MHz)/B71(600MHz)-0to55°C Wall,DIN railOnCell3120-LTE-1-US-T LTE Cat1B2(1900MHz)/B4(1700MHz)/B5(850MHz)/B12(700MHz)/B13(700MHz)/B14(700MHz)/B66(1700MHz)/B71(600MHz)-30to70°C Wall,DIN railAccessories(sold separately)AntennasANT-LTEUS-ASM-01GSM/GPRS/EDGE/UMTS/HSPA/LTE,omni-directional rubber duck antenna,1dBiANT-LTE-ASM-02GPRS/EDGE/UMTS/HSPA/LTE,omni-directional rubber duck antenna,2dBiANT-LTE-ANF-04GSM/GPRS/EDGE/UMTS/HSPA/LTE,omni-directional outdoor antenna,4dBi,IP66Wireless Antenna CablesCRF-SMA(M)/N(M)-300N-type(male)to SMA(male)CFD200cable,3mA-CRF-SMSF-R3-100Cellular magnetic base,SMA connector,1mMounting KitsWK-35-042plates(35x44x2.5mm)with6screws(FTSx6M3x4mm)©Moxa Inc.All rights reserved.Updated May04,2022.This document and any portion thereof may not be reproduced or used in any manner whatsoever without the express written permission of Moxa Inc.Product specifications subject to change without notice.Visit our website for the most up-to-date product information.。
HCPL-0720资料

Functional Diagram*Pin 3 is the anode of the internal LED and must be left unconnected for guaranteed data sheet performance. Pin 7 is not connected internally.**A 0.1 µF bypass capacitor must be connected between pins 1 and 4, and 5 and 8.DescriptionAvailable in either an 8-pin DIP or SO-8 package style respectively, the HCPL-772X or HCPL-072X optocouplers utilize the latest CMOS IC technology to achieve outstanding performance with very low power consumption. TheHCPL-772X/072X require only two bypass capacitors for complete CMOS compatability.AgilentHCPL-0720/7720 and HCPL-0721/772140 ns Propagation Delay,CMOS OptocouplerData SheetFeatures•+5 V CMOS compatibility•20 ns maximum prop. delay skew •High speed: 25 MBd •40 ns max. prop. delay•10 kV/µs minimum common mode rejection•–40 to 85°C temperature range •Safety and regulatory approvals UL recognized3750 V rms for 1 min. per UL 1577CSA component acceptance notice #5IEC/EN/DIN EN 60747-5-2–V IORM = 630 Vpeak for HCPL-772X option 060–V IORM = 560 Vpeak for HCPL-072X option 060Applications•Digital fieldbus isolation: CC-Link,DeviceNet, Profibus, SDS •AC plasma display panel level shifting•Multiplexed data transmission •Computer peripheral interface •Microprocessor system interfaceBasic building blocks of the HCPL-772X/072X are a CMOS LED driver IC, a high speed LED and a CMOS detector IC. A CMOS logic input signal controls the LED driver IC which supplies current to the LED. The detector IC incorporates an integrated photodiode, a high-speedtransimpedance amplifier, and a voltage comparator with an output driver.**V DD1V I*GND 1V DD2**V OGND 2V I , INPUTLED1H LOFF ONTRUTH TABLE (POSITIVE LOGIC)NC*V O , OUTPUTH LCAUTION: It is advised that normal static precautions be taken in handling and assembly of this component to prevent damage and/or degradation which may be induced by ESD.Package Outline DrawingHCPL-772X 8-Pin DIP PackageSelection Guide 8-Pin DIP Small Outline (300 Mil)SO-8Data Rate PWD HCPL-7721HCPL-072125 MB 6 ns HCPL-7720HCPL-072025 MB 8 nsDIMENSIONS IN MILLIMETERS AND (INCHES).0.254+ 0.076- 0.051(0.010+ 0.003)- 0.002)*OPTION 300 AND 500 NOT MARKED.NOTE: FLOATING LEAD PROTRUSION IS 0.25 mm (10 mils) MAX.Ordering InformationSpecify Part Number followed by Option Number (if desired)ExampleHCPL-7720#XXXX060 = IEC/EN/DIN EN 60747-5-2 Option.300 = Gull Wing Surface Mount Option (HCPL-7720 only).500 = Tape and Reel Packaging Option.XXXE = Lead Free Option.No Option and Option 300 contain 50 units (HCPL-772X), 100 units (HCPL-072X) per tube.Option 500 contain 1000 units (HCPL-772X), 1500 units (HCPL-072X) per reel.Option data sheets available. Contact Agilent sales representative or authorized distributor.Remarks: The notation “#” is used for existing products, while (new) products launched since 15th July 2001 and lead free option will use “–”Package Outline DrawingHCPL-772X Package with Gull Wing Surface Mount Option 300Package Outline DrawingHCPL-072X Outline Drawing (Small Outline SO-8 Package)(0.025 ± 0.005)(0.100)BSCDIMENSIONS IN MILLIMETERS (INCHES).LEAD COPLANARITY = 0.10 mm (0.004 INCHES).NOTE: FLOATING LEAD PROTRUSION IS 0.25 mm (10 mils) MAX.+ 0.076- 0.051+ 0.003)- 0.002)(0.012)MIN.5.207 ± 0.254 (0.205 ± 0.010)DIMENSIONS IN MILLIMETERS (INCHES).LEAD COPLANARITY = 0.10 mm (0.004 INCHES) MAX.OPTION NUMBER 500 NOT MARKED.NOTE: FLOATING LEAD PROTRUSION IS 0.15 mm (6 mils) MAX.*Regulatory InformationThe HCPL-772X/072X have been approved by the following organizations:ULRecognized under UL 1577,component recognition program,File E55361.CSAApproved under CSA Component Acceptance Notice #5, File CA88324.IEC/EN/DIN EN 60747-5-2Approved under:IEC 60747-5-2:1997 + A1:2002EN 60747-5-2:2001 + A1:2002DIN EN 60747-5-2 (VDE 0884 Teil 2):2003-01.(Option 060 only)Solder Reflow Thermal ProfilePb-Free IR ProfileTIME (SECONDS)T E M P E R A T U R E (°C )ROOM°C of ACTUAL NOTES:THE TIME FROM 25 °C to PEAK TEMPERATURE = 8 MINUTES MAX.T smax = 200 °C, T smin = 150 °CAll Agilent data sheets report the creepage and clearance inherent to the optocoupler component itself. These dimensions are needed as a starting point for the equipment designer when determining the circuit insulation requirements. However, once mounted on a printed circuit board, minimum creepage andclearance requirements must bemet as specified for individualequipment standards. Forcreepage, the shortest distancepath along the surface of aprinted circuit board between thesolder fillets of the input andoutput leads must be considered.There are recommendedtechniques such as grooves andribs which may be used on aprinted circuit board to achievedesired creepage and clearances.Creepage and clearance distanceswill also change depending onfactors such as pollution degreeand insulation level.Insulation and Safety Related SpecificationsValueParameter Symbol772X072X Units ConditionsMinimum External Air L(I01)7.1 4.9mm Measured from input terminals to output Gap (Clearance)terminals, shortest distance through air. Minimum External L(I02)7.4 4.8mm Measured from input terminals to output Tracking (Creepage)terminals, shortest distance path along body. Minimum Internal Plastic0.080.08mm Insulation thickness between emitter and Gap (Internal Clearance)detector; also known as distance throughinsulation.Tracking Resistance CTI≥175≥175Volts DIN IEC 112/VDE 0303 Part 1 (Comparative TrackingIndex)Isolation Group IIIa IIIa Material Group (DIN VDE 0110, 1/89,Table 1)IEC/EN/DIN EN 60747-5-2 Insulation Related Characteristics (Option 060)HCPL-772X HCPL-072X Description Symbol Option 060Option 060Units Installation classification per DIN VDE 0110/1.89, Table 1for rated mains voltage ≤150 V rms I-IV I-IVfor rated mains voltage ≤300 V rms I-IV I-IIIfor rated mains voltage ≤450 V rms I-IIIClimatic Classification55/85/2155/85/21Pollution Degree (DIN VDE 0110/1.89)22Maximum Working Insulation Voltage V IORM630560V peak Input to Output Test Voltage, Method b†V PR11811050V peak V IORM x 1.875 = V PR, 100% ProductionTest with t m = 1 sec, Partial Discharge < 5 pCInput to Output Test Voltage, Method a†V PR945840V peak V IORM x 1.5 = V PR, Type and Sample Test,t m = 60 sec, Partial Discharge < 5 pCHighest Allowable Overvoltage†V IOTM60004000V peak (Transient Overvoltage, t ini = 10 sec)Safety Limiting Values(Maximum values allowed in the event of a failure,also see Thermal Derating curve, Figure 11.)Case Temperature T S175150°C Input Current I S,INPUT230150mA Output Power P S,OUTPUT600600mW Insulation Resistance at T S, V10 = 500 V R IO≥109≥109Ω†Refer to the front of the optocoupler section of the Isolation and Control Component Designer’s Catalog, under Product Safety Regulations section IEC/EN/DIN EN 60747-5-2, for a detailed description.Note:These optocouplers are suitable for “safe electrical isolation” only within the safety limit data. Maintenance of the safety data shall be ensured by means of protective circuits.Note:The surface mount classification is Class A in accordance with CECC 00802.Absolute Maximum RatingsParameter Symbol Min.Max.Units Figure Storage Temperature T S–55125°CAmbient Operating Temperature[1]T A–40+85°CSupply Voltages V DD1, V DD20 6.0VoltsInput Voltage V I–0.5V DD1 +0.5VoltsOutput Voltage V O–0.5V DD2 +0.5VoltsAverage Output Current I O10mALead Solder Temperature 260°C for 10 sec., 1.6 mm below seating planeSolder Reflow Temperature Profile See Solder Reflow Temperature Profile SectionRecommended Operating ConditionsParameter Symbol Min.Max.Units Figure Ambient Operating Temperature T A–40+85°CSupply Voltages V DD1, V DD2 4.5 5.5VLogic High Input Voltage V IH 2.0V DD1V1, 2 Logic Low Input Voltage V IL0.00.8VInput Signal Rise and Fall Times t r, t f 1.0msElectrical SpecificationsTest conditions that are not specified can be anywhere within the recommended operating range.All typical specifications are at T A = +25°C, V DD1 = V DD2 = +5 V.Parameter Symbol Min.Typ.Max.Units Test Conditions Fig.Note DC SpecificationsLogic Low Input I DD1L 6.010.0mA V I = 0 V2 Supply CurrentLogic High Input I DD1H 1.5 3.0mA V I = V DD1Supply CurrentOutput Supply Current I DD2L 5.59.0mAI DD2H7.09.0Input Current I I–1010µALogic High Output V OH 4.4 5.0V I O = -20 µA, V I = V IH1, 2 Voltage 4.0 4.8I= -4 mA, V I = V IHOV OL00.1V I O = 20 µA, V I = V ILLogic Low OutputVoltage0.1V I O = 400 µA, V I = V IL0.5 1.0I O = 4 mA, V I = V ILSwitching SpecificationsPropagation Delay Time t PHL2040ns C L = 15 pF3, 63to Logic Low Output CMOS Signal LevelsPropagation Delay Time t PLH2340to Logic High OutputPulse Width PW40Data Rate25MBdPulse Width Distortion PWD7721/072136ns74|t PHL - t PLH|7720/072038nsPropagation Delay Skew t PSK205 Output Rise Time t R9ns(10 - 90%)Output Fall Time t F8ns(90 - 10%)Common Mode|CM H|1020kV/µs V I = V DD1, V O>6 Transient Immunity at0.8 V DD1,Logic High Output V CM = 1000 VCommon Mode|CM L|1020V I = 0 V, V O > 0.8 V,Transient Immunity at V CM = 1000 VLogic Low OutputInput Dynamic Power C PD160pF7 DissipationCapacitanceOutput Dynamic Power C PD210DissipationCapacitanceNotes:1.Absolute Maximum ambient operating temperature means the device will not be damaged if operated under these conditions.It does not guarantee functionality.2.The LED is ON when V I is low and OFF when V I is high.3.t PHL propagation delay is measured from the 50% level on the falling edge of the V I signal to the 50% level of the falling edge of the V O signal. t PLH propagation delay is measured from the 50% level on the rising edge of the V I signal to the 50% level of the rising edge of the V O signal.4.PWD is defined as |t PHL - t PLH |.%PWD (percent pulse width distortion) is equal to the PWD divided by pulse width.5.t PSK is equal to the magnitude of the worst case difference in t PHL and/or t PLH that will be seen between units at any given temperature within the recommended operating conditions.6.CM H is the maximum common mode voltage slew rate that can be sustained while maintaining V O > 0.8 V DD2. CM L is themaximum common mode voltage slew rate that can be sustained while maintaining V O < 0.8V. The common mode voltage slew rates apply to both rising and falling common mode voltage edges.7.Unloaded dynamic power dissipation is calculated as follows: C PD * V DD2 * f + I DD *V DD , where f is switching frequency in MHz.8.Device considered a two-terminal device:pins 1, 2, 3, and 4 shorted together and pins 5, 6, 7, and 8 shorted together.9.In accordance with UL1577, each HCPL-072Xis proof tested by applying an insulation test voltage ≥4500 V RMS for 1 second (leakage detection current limit, I I-O ≤5 µA). Each HCPL-772X is proof tested by applying an insulation test voltage ≥4500 Vrms for 1second (leakage detection current limit.I I-O ≤ 5 µA.)10.The Input-Output Momentary WithstandVoltage is a dielectric voltage rating that should not be interpreted as an input-output continuous voltage rating. For the continuous voltage rating refer to your equipment level safety specification or Agilent Application Note 1074 entitled “Optocoupler Input-Output Endurance Voltage.”11.C I is the capacitance measured at pin 2 (V I ).Figure 1. Typical output voltage vs. input voltage.Figure 2. Typical input voltage switching threshold vs. input supply voltage.Figure 3. Typical propagation delays vs.temperature.V O (V )V I (V)41532V I T H (V )1.6V DD1 (V)2.11.72.22.01.81.9T P L H , T P H L(n s )15T A (C)27172925192123Package Characteristics ParameterSymbol Min.Typ.Max.Units Test Conditions Fig.Note Input-Output Momentary 072X V ISO3750VrmsRH ≤50%,8, 9,Withstand Voltage 772X3750t = 1 min.,10T A = 25°C Resistance R I-O 1012ΩV I-O = 500 Vdc 8(Input-Output)Capacitance C I-O 0.6pFf = 1 MHz(Input-Output)Input CapacitanceC I 3.011Input IC Junction-to-Case -772X θjci 145°C/WThermocouple Thermal Resistance-072X 160located at center Output IC Junction-to-Case -772X θjco 140underside of packageThermal Resistance-072X135Package Power DissipationP PD150mWFigure 4. Typical pulse width distortion vs.temperature.Figure 5. Typical rise time vs. temperature.Figure 6. Typical fall time vs. temperature.Figure 7. Typical propagation delays vs.output load capacitance.Figure 8. Typical pulse width distortion vs. output load capacitance.Figure 9. Thermal derating curve, dependence of safety limiting value with case temperature per IEC/EN/DIN EN 60747-5-2.P W D (n s )00T A (C)803602041402T R (n s )08T A (C)8010602011940T F (n s )02T A (C)8066020734054O U T P U T P O W E R – P S , I N P U T C U R R E N T – I S0T A – CASE TEMPERATURE – °C400600800200100300500700(150)T P L H , T P H L (n s)C I (pF)P WD (n s )150C I (pF)50540613032520354524O U T P U T P O W E R – P S , I N P U T C U R R E N T – I ST A – CASE TEMPERATURE – °CApplication InformationBypassing and PC Board Layout The HCPL-772X/072Xoptocouplers are extremely easy to use. No external interface circuitry is required because the HCPL-772X/072X use high-speed CMOS IC technology allowingCMOS logic to be connecteddirectly to the inputs and outputs.As shown in Figure 10, the only external components required for proper operation are two bypass capacitors. Capacitor values should be between 0.01 µF and 0.1 µF. For each capacitor, the total lead length between both ends of the capacitor and the power-supply pins should not exceed 20 mm. Figure 11illustrates the recommended printed circuit board layout for the HPCL-772X/072X.Figure 10. Recommended printed circuit board layout.Figure 11. Recommended printed circuit board layout.Propagation Delay, Pulse-WidthDistortion and Propagation Delay Skew Propagation Delay is a figure of merit which describes how quickly a logic signal propagates through a system. The propagation delayfrom low to high (t PLH ) is the amount of time required for an input signal to propagate to the output, causing the output to change from low to high.Similarly, the propagation delay from high to low (t PHL ) is the amount of time required for the input signal to propagate to the output, causing the output to change from high to low. See Figure 12.Figure 12.INPUTOUTPUTV IV OV OHV OL0 V5 V CMOS2.5 V CMOSV DD2V OV DD1V IC1, C2 = 0.01 µF TO 0.1 µFV DD2V OGND 2V DD1V IGND 1C1, C2 = 0.01 µF TO 0.1 µFFigure 13. Propagation delay skew waveform.Figure 14. Parallel data transmission example.Propagation delay skew repre-sents the uncertainty of where an edge might be after being sent through an optocoupler. Figure14 shows that there will be uncertainty in both the data and clock lines. It is important that these two areas of uncertainty not overlap, otherwise the clock signal might arrive before all of the data outputs have settled, or some of the data outputs maystart to change before the clocksignal has arrived. From theseconsiderations, the absoluteminimum pulse width that can besent through optocouplers in aparallel application is twice t PSK.A cautious design should use aslightly longer pulse width toensure that any additionaluncertainty in the rest of thecircuit does not cause a problem.The HCPL-772X/072Xoptocouplers offer the advantageof guaranteed specifications forpropagation delays, pulse-widthdistortion, and propagation delayskew over the recommendedtemperature and power supplyranges.Pulse-width distortion (PWD) is the difference between t PHL andt PLH and often determines the maximum data rate capability of a transmission system. PWD can be expressed in percent by dividing the PWD (in ns) by the minimum pulse width (in ns) being trans-mitted. Typically, PWD on the order of 20 - 30% of the minimum pulse width is tolerable. Propagation delay skew, t PSK, is an important parameter to con-sider in parallel data applications where synchronization of signals on parallel data lines is a concern. If the parallel data is being sent through a group of optocouplers, differences in propagation delays will cause the data to arrive at theoutputs of the optocouplers atdifferent times. If this differencein propagation delay is largeenough it will determine themaximum rate at which paralleldata can be sent through theoptocouplers.Propagation delay skew is definedas the difference between theminimum and maximum propa-gation delays, either t PLH or t PHL,for any given group of optocoup-lers which are operating underthe same conditions (i.e., the samedrive current, supply voltage,output load, and operatingtemperature). As illustrated inFigure 13, if the inputs of a groupof optocouplers are switchedeither ON or OFF at the sametime, t PSK is the differencebetween the shortest propagationdelay, either t PLH or t PHL, and thelongest propagation delay, eithert PLH or t PHL.As mentioned earlier, t PSK candetermine the maximum paralleldata transmission rate. Figure 14is the timing diagram of a typicalparallel data application withboth the clock and data linesbeing sent through theoptocouplers. The figure showsdata and clock signals at theinputs and outputs of theoptocouplers. In this case the datais assumed to be clocked off of therising edge of the clock.V V V VDATA INPUTSCLOCKDATA OUTPUTSCLOCKOptical Isolation for Field Bus NetworksTo recognize the full benefits of these networks, each recommends Agilent optocouplers. Since network communication is bi-directional (involving receivingFigure 15. Typical field bus communication physical model.data from and transmitting data onto the network), two Agilent optocouplers are needed. Byproviding galvanic isolation, data integrity is retained via noise reduction and the elimination of false signals. In addition, the network receives maximumprotection from power system faults and ground loops.Within an isolated node , such as the DeviceNet Node shown in Figure 16, some of the node’s components are referenced to a ground other than V- of thenetwork. These components could include such things as devices with serial ports, parallel ports, RS232and RS485 type ports. As shown in Figure 16, power from the network is used only for the transceiver and input (network) side of the optocouplers.Isolation of nodes connected to any of the three types of digital field bus networks is best achieved by using the HCPL-772X/072Xoptocouplers. For each network,the HCPL-772X/072X satisify the critical propagation delay and pulse width distortion require-ments over the temperature range of 0°C to +85°C, and power supply voltage range of 4.5V to 5.5V.Digital Field Bus Communication systems. In today’s manufacturing environment, however, automated systems are expected to help manage the process, not merely monitor it. With the advent of digital field bus communication networks such as CC-Link,DeviceNet, PROFIBUS, and Smart Distributed Systems (SDS), gone are the days of constrainedinformation. Controllers can now receive multiple readings from field devices (sensors, actuators,etc.) in addition to diagnostic information.The physical model for each of these digital field bus communica-tion networks is very similar as shown in Figure 15. Each includes one or more buses, an interface unit, optical isolation, transceiver,and sensing and/or actuating devices.CONTROLLERMOTOR STARTERGALVANIC ISOLATION BOUNDARYFigure 16. Typical DeviceNet Node.Implementing CC-Link with the HCPL-772X/072XCC-Link (Control and Communication Link) isdeveloped to merge control and information in the low-level network (field network) by PCs,thereby making the multivendor environment a reality. It has data control and message-exchange function, as well as bit control function, and operates at the speed up to 10 Mbps.Figure 17. Recommended CC-Link application circuit.Power Supplies and BypassingThe recommended CC-Link circuit is shown in Figure 17. Since the HCPL-772X/072X are fullycompatible with CMOS logic level signals, the optocoupler is connected directly to the transceiver. Two bypasscapacitors (with values between 0.01 µF and 0.1 µF) are required and should be located as close aspossible to the input and output power supply pins of the HCPL-772X/072X. For each capacitor,the total lead length between both ends of capacitor and the power supply pins should not exceed 20mm. The bypass capacitors are required because of the highspeed digital nature of the signals inside the optocoupler.RD1Implementing DeviceNet and SDS with the HCPL-772X/072XWith transmission rates up to 1Mbit/s, both DeviceNet and SDS are based upon the samebroadcast-oriented, communica-tions protocol — the Controller Area Network (CAN). Three types of isolated nodes arerecommended for use on these networks: Isolated Node Powered by the Network (Figure 18),Figure 18. Isolated node powered by the network.Isolated Node with Transceiver Powered by the Network (Figure 19), and Isolated Node Providing Power to the Network (Figure 20).Isolated Node Powered by the NetworkThis type of node is very flexible and as can be seen in Figure 18, is regarded as “isolated” because not all of its components have the same ground reference. Yet, all components are still powered by the network. This node contains two regulators: one is isolated and powers the CAN controller, node-specific application and isolated (node) side of the two optocoup-lers while the other is non-isolated. The non-isolatedregulator supplies the transceiver and the non-isolated (network)half of the two optocouplers.– (SIGNAL)– (POWER)GALVANIC ISOLATION BOUNDARYSIGNAL POWERIsolated Node with Transceiver Powered by the NetworkFigure 19 shows a node powered by both the network and another source. In this case, the trans-ceiver and isolated (network) side of the two optocouplers arepowered by the network. The rest of the node is powered by the AC line which is very beneficial when an application requires asignificant amount of power. This method is also desirable as it does not heavily load the network.More importantly, the unique “dual-inverting” design of the HCPL-772X/072X ensure the network will not “lock-up” if either AC line power to the node is lost or the node powered-off.Specifically, when input power(V DD1) to the HCPL-772X/072X located in the transmit path is eliminated, a RECESSIVE bus state is ensured as theHCPL-772X/072X output voltage (V O ) go HIGH.*Bus V+ SensingIt is suggested that the Bus V+sense block shown in Figure 19 be implemented. A locally poweredFigure 20. Isolated node providing power to the network.Isolated Node Providing Power to the NetworkFigure 20 shows a node providing power to the network. The AC line powers a regulator whichprovides five (5) volts locally. The AC line also powers a 24 voltisolated supply, which powers the network, and another five-volt regulator, which, in turn, powersthe transceiver and isolated (network) side of the two optocouplers. This method is recommended when there are a limited number of devices on the network that don’t require much power, thus eliminating the need for separate power supplies.More importantly, the unique “dual-inverting” design of the HCPL-772X/072X ensure the network will not “lock-up” if either AC line power to the node is lost or the node powered-off.Specifically, when input power (V DD1) to the HCPL-772X/072X located in the transmit path is eliminated, a RECESSIVE bus state is ensured as theHCPL-772X/072X output voltage (V O ) go HIGH.– (SIGNAL)– (POWER)GALVANIC ISOLATION BOUNDARYSIGNAL POWERFigure 19. Isolated node with transceiver powered by the network.(SIGNAL) (POWER)GALVANIC ISOLATION BOUNDARYSIGNAL POWERnode with an un-powered isolated Physical Layer will accumulate errors and become bus-off if it attempts to transmit. The Bus V+sense signal would be used to change the BOI attribute of the DeviceNet Object to the “auto-reset” (01) value. Refer to Volume 1, Section 5.5.3. This would cause the node to continually reset until bus power was detected. Once power was detected, the BOIattribute would be returned to the “hold in bus-off” (00) value. The BOI attribute should not be left in the “auto-reset” (01) value since this defeats the jabber protection capability of the CAN error confinement. Any inexpensive low frequency optical isolator can be used to implement this feature.Power Supplies and Bypassing The recommended DeviceNet application circuit is shown in Figure 21. Since the HCPL-772X/072X are fully compatible with CMOS logic level signals, theoptocoupler is connected directlyFigure 21. Recommended DeviceNet application circuit.Implementing PROFIBUS with the HCPL-772X/072XAn acronym for Process Fieldbus,PROFIBUS is essentially a twisted-pair serial link very similar to RS-485 capable of achieving high-speed communication up to 12MBd. As shown in Figure 22, a PROFIBUS Controller (PBC) establishes the connection of a field automation unit (control or central processing station) or a field device to the transmission medium. The PBC consists of the line transceiver,optical isolation, frame character transmitter/receiver (UART), and the FDL/APP processor with the interface to the PROFIBUS user.to the CAN transceiver. Two bypass capacitors (with values between 0.01 and 0.1 µF) arerequired and should be located as close as possible to the input and output power-supply pins of the HCPL-772X/072X. For eachPROFIBUS USER:CONTROL STATION (CENTRAL PROCESSING)OR FIELD DEVICEUSER INTERFACEFDL/APP PROCESSORTRANSCEIVEROPTICAL ISOLATIONUARTPBCMEDIUMcapacitor, the total lead length between both ends of thecapacitor and the power supply pins should not exceed 20 mm.The bypass capacitors are required because of the high-speed digital nature of the signals inside the optocoupler.R11 M–GALVANIC ISOLATION BOUNDARYFigure 22. PROFIBUS Controller (PBC).Power Supplies and Bypassing The recommended PROFIBUS application circuit is shown in Figure 23. Since the HCPL-772X/072X are fully compatible with CMOS logic level signals, theoptocoupler is connected directly to the transceiver. Two bypass capacitors (with values between 0.01 and 0.1 µF) are required and should be located as close as possible to the input and output power-supply pins of the HCPL-772X/072X. For eachcapacitor, the total lead length between both ends of thecapacitor and the power supply pins should not exceed 20 mm.The bypass capacitors are required because of the high-speed digital nature of the signals inside the optocoupler.Being very similar to multi-station RS485 systems, the HCPL-061N optocoupler provides a transmit disable function which isnecessary to make the bus freeafter each master/slavetransmission cycle. Specifically,the HCPL-061N disables the transmitter of the line driver by putting it into a high state mode.In addition, the HCPL-061Nswitches the RX/TX driver IC into the listen mode. The HCPL-061N offers HCMOS compatibility and the high CMR performance (1 kV/µs at V CM = 1000 V)essential in industrialcommunication interfaces.Figure 23. Recommended PROFIBUS application circuit.GALVANIC ISOLATION HCPL-061N。
ADNS-3120-001中文资料

DescriptionThe ADNS-3120-001 Solid-State Optical Mouse Lens is designed for use with Avago Technologies Optical Mouse Sensors ADNS-3040 and the illumination subsystem provided by the ADNS-2220 LED Assembly Clip and the HLMP-ED80-PS000 LED. Together with the LED, ADNS-3120-001 provides the directed illumination and optical imaging necessary for proper operation of the Optical Mouse Sensor. The lens is a precision molded optical component and should be handled with care to avoid scratching of the optical surfaces.Ordering InformationSpecify Part Number as follows:Flange Part Number Material Trim ADNS-3120-001PolycarbonateADNS-3120-001Solid-State Optical Mouse Lens Data SheetFigure 1. ADNS-3120-001 Outline DrawingFigure 3. Logo Locations.Figure 2. Optical System Assembly DiagramMechanical Assemble RequirementsAll specifications reference Figure 2, Optical System Assembly Diagram.ParameterSymbolMin.TypicalMax.UnitsConditionsDistance from Object Surface to Lens Reference PlaneA 2.452.55 2.65mm Distance from Mouse Sensor Lid contact with lens Surface to Object SurfaceB9.43mmSensor lid must be in contactwith lens housing surfaceNOTES:1. TOPSIDE LOGO EXTENDS 0.2 mm ABOVE THE FLANGE SURFACE.2. BOTTOMSIDE LOGO EXTENDS 0.1 mm BELOW THE SURFACE.3. BOTTOMSIDE LOGO IS EITHER LEFT SIDE, AS SHOWN AS ABOVE, OR PRISM SIDE OF THE LENSLens Design Optical Performance SpecificationsAll specifications are based on the Mechanical Assembly Requirements.ParameterSymbolMin.TypicalMax.Units ConditionsNumerical Aperture NA0.10.130.16Magnification 0.851.00 1.15Image at nominal locationDesign Wavelength l639nm Object to Image Distance 11.00mmLens Material*Index of Refraction N 1.5801.5818 1.5840l = 639nmDepth of Field DOF±0.5mm Field Coverage Radius1.8mm*Lens material is polycarbonate. Cyanoacrylate based adhesives should not be used as they will cause lens material deformation.Mounting Instructions for the ADNS-3120-001 Lens to theBase Plate.An IGES format drawing file with design specifications formouse base plate features is available.These features are useful in maintaining proper position-ing and alignment of the ADNS-3120-001 when usedwith the Avago Technologies Optical Mouse Sensor. Thisfile can be obtained by contacting your local Avago Tech-nologies sales representative.ADNS-3120-001 LENS RECESSADNSDIMENSIONS: 31.5 x 17.0 mmKEY PYRAMID FEATURE:2.50mm HEIGHT MAX.Figure 4. Illustration of base plate mounting features.For product information and a complete list of distributors, please go to our web site: Avago, Avago Technologies, and the A logo are trademarks of Avago Technologies Limited in the United States and other countries. Data subject to change. Copyright © 2008 Avago Technologies Limited. All rights reserved. Obsoletes 5989-3581ENAV02-0945EN - March 17, 2008。
单相交流串励电机调速系统设计
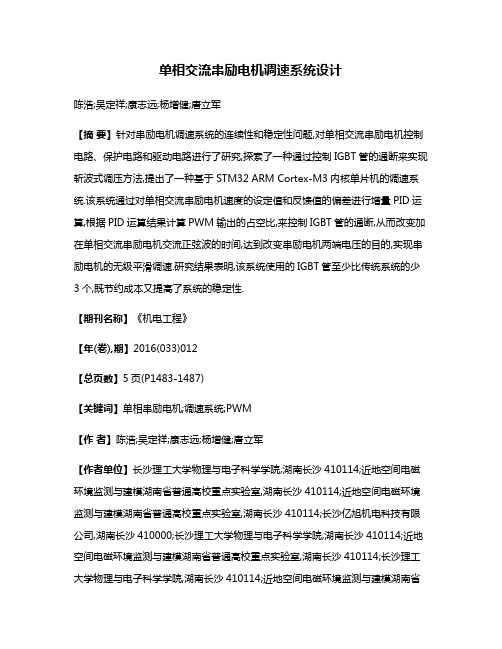
单相交流串励电机调速系统设计陈浩;吴定祥;康志远;杨增健;唐立军【摘要】针对串励电机调速系统的连续性和稳定性问题,对单相交流串励电机控制电路、保护电路和驱动电路进行了研究,探索了一种通过控制IGBT管的通断来实现斩波式调压方法,提出了一种基于STM32 ARM Cortex-M3内核单片机的调速系统.该系统通过对单相交流串励电机速度的设定值和反馈值的偏差进行增量PID运算,根据PID运算结果计算PWM输出的占空比,来控制IGBT管的通断,从而改变加在单相交流串励电机交流正弦波的时间,达到改变串励电机两端电压的目的,实现串励电机的无级平滑调速.研究结果表明,该系统使用的IGBT管至少比传统系统的少3个,既节约成本又提高了系统的稳定性.【期刊名称】《机电工程》【年(卷),期】2016(033)012【总页数】5页(P1483-1487)【关键词】单相串励电机;调速系统;PWM【作者】陈浩;吴定祥;康志远;杨增健;唐立军【作者单位】长沙理工大学物理与电子科学学院,湖南长沙410114;近地空间电磁环境监测与建模湖南省普通高校重点实验室,湖南长沙410114;近地空间电磁环境监测与建模湖南省普通高校重点实验室,湖南长沙410114;长沙亿旭机电科技有限公司,湖南长沙410000;长沙理工大学物理与电子科学学院,湖南长沙410114;近地空间电磁环境监测与建模湖南省普通高校重点实验室,湖南长沙410114;长沙理工大学物理与电子科学学院,湖南长沙410114;近地空间电磁环境监测与建模湖南省普通高校重点实验室,湖南长沙410114;长沙理工大学物理与电子科学学院,湖南长沙410114;近地空间电磁环境监测与建模湖南省普通高校重点实验室,湖南长沙410114【正文语种】中文【中图分类】TH39;TM546+.4单相串励电动机输出转矩大,转速一般可以达到几千转甚至几万转每分钟,电路控制简单,交直流可以两用,广泛应用于家用电器、电动工具、搅拌机等场合[1]。
HLMP-C323-O0000中文资料

DescriptionThese non-diffused lamps are designed to produce a bright light source and smooth radiationpattern. A slight tint is added to the lens for easy color identification.This lamp has been designed with aHLMP-C115, HLMP-C117, HLMP-C123, HLMP-C215, HLMP-C223,HLMP-C315, HLMP-C323, HLMP-C415, HLMP-C423, HLMP-C515,HLMP-C523, HLMP-C615, HLMP-C623Features•Very high intensity •Exceptional uniformity •Microtint lens for color identification•Consistent viewability All colors: AlGaAs RedHigh Efficiency Red Yellow Orange GreenEmerald Green •15° and 25° family•Tape and reel options available •Binned for color and intensity Applications•Ideal for backlighting front panels*•Used for lighting switches •Adapted for indoor and outdoor signsAgilentT-13/4 Super Ultra-Bright LED LampsData Sheet20mil lead frame, enhanced flange, and tight meniscus controls, making it compatible with radial lead automated insertion equipment.Selection GuidePart Number Luminous Intensity Iv (mcd) Color2θ1/2[1]Standoff Leads HLMP-Min.Max.DH AS AlGaAs15No C115290.0–C115-O00xx290.0–C115-OP0xx290.01000.0Yes C117-OP0xx290.01000.025No C12390.2–C123-L00xx90.2–Red15No C215138.0–C215-M00xx138.0–C215-MN0xx138.0400.025No C22390.2–C223-L00xx90.2–C223-MN0xx138.0400.0 Yellow15No C315147.0–C315-L00xx147.0–C315-LM0xx147.0424.025No C32396.2–C323-K00xx96.2–C323-KL0xx96.2294.0 Orange15No C415138.0–C415-M00xx138.0–C415-M0D0xx138.0–C415-MN0xx138.0400.025No C42390.2–C423-L00xx90.2–C423-LM0xx90.2276.0 Green15No C515170.0–C515-L00xx170.0C515-LM0xx170.0490.025No C52369.8–C523-J00xx69.8–C523-KL0xx111.7340.0 Emerald Green15No C61517.0–C615-G00xx17.0–25No C623 6.7–C623-E00xx 6.7–Part Numbering SystemHLMP - C x xx - x x x xxMechanical Options00: Bulk01: Tape & Reel, Crimped Leads02: Tape & Reel, Straight LeadsB2: Right Angle Housing, Even LeadsUQ: Ammo Pack, Horizontal LeadsColor Bin Options0: Full Color Bin DistributionD: Color Bins 4 & 5 onlyMaximum Iv Bin Options0: Open (No Maximum Limit)Others: Please refer to the Iv Bin TableMinimum Iv Bin OptionsPlease refer to the Iv Bin TableViewing Angle & Standoffs Options15: 15 Degree, without Standoffs17: 15 Degree, with Standoffs23: 25 Degree, without StandoffsColor Options1. AS AlGaAs Red2. High Efficiency Red3. Yellow4. Orange5. Green6. Emerald GreenPackage OptionsC: T-1 3/4 (5 mm)Absolute Maximum Ratings at T A = 25°CHighHighDH AS Efficiency Performance AlGaAs Red and Green and ParameterRed Orange Yellow Emerald Green Units DC Forward Current [1]30302030mA Transient Forward Current [2]500500500500mA (10 µsec Pulse)Reverse Voltage (Ir = 100 µA)5555V LED Junction Temperature 110110110110°C Operating Temperature Range –20 to +100–55 to +100–20 to +100°C Storage Temperature Range –55 to +100°CWave Soldering Temperature 250°C for 3 seconds [1.59 mm (0.063 in.) from body]Lead Solder Dipping Temperature 260°C for 5 seconds[1.59 mm (0.063 in.) from body]Notes:1. See Figure 5 for maximum current derating vs. ambient temperature.2. The transient current is the maximum nonrecurring peak current the device can withstand without damaging the LED die and wire bond.Package DimensionsHLMP-Cx15 and HLMP-Cx23HLMP-Cx17(0.039)NOTES:1. ALL DIMENSIONS ARE IN MILLIMETERS (INCHES).2. LEADS ARE MILD STEEL, SOLDER DIPPED.3. AN EPOXY MENISCUS MAY EXTEND ABOUT 0.5 mm (0.020 in.) DOWN THE LEADS.± 0.20± 0.008)Electrical Characteristics at T A = 25°CForward Reverse Capacitance Speed of ResponseVoltage Breakdown C (pF)Thermalτs (ns)Vf (Volts)Vr (Volts)Vf = 0Resistance Time Constant@ If = 20 mA@ Ir = 100 µA f = 1 MHz RθJ-PIN e-t/τsPart Number Typ.Max.Min.Typ.(°C/W)Typ.HLMP-C115 1.8 2.253021030HLMP-C117HLMP-C123HLMP-C215 1.9 2.651121090HLMP-C223HLMP-C315 2.1 2.651521090HLMP-C323HLMP-C415 1.9 2.654210280HLMP-C423HLMP-C515 2.2 3.0518210260HLMP-C523HLMP-C615 2.2 3.0518210260HLMP-C623Optical Characteristics at T A = 25°CLuminous Color,ViewingIntensity Peak Dominant Angle LuminousIv (mcd)Wavelength Wavelength2θ1/2Efficacy@ 20 mA[1]λpeak (nm)λd[2] (nm)(Degrees)[3]ηvPart Number Min.Typ.Typ.Typ.Typ.(lm/w) HLMP-C1152906006456371180HLMP-C117HLMP-C1239020026HLMP-C215138300635626171459017023HLMP-C315146300583585175009617025HLMP-C415138300600602173809017023HLMP-C515170300568570205956917028HLMP-C61517455585602065662728Notes:1. The luminous intensity, Iv, is measured at the mechanical axis of the lamp package. The actual peak of the spatial radiation pattern may not bealigned with this axis.2. The dominant wavelength, λd, is derived from the CIE Chromaticity Diagram and represents the color of the device.3. 2θ1/2 is the off-axis angle where the luminous intensity is 1/2 the on-axis intensity.Figure 1. Relative intensity vs. wavelength.Figure 2. Forward current vs. forward voltage (non-resistor lamp).Figure 3. Relative luminous intensity vs. forward current.WAVELENGTH – nmR E L A T I V E I N T E N S I T Y1.00.50I F – F O R W A R DC U R R E N T – m AV F – FORWARD VOLTAGE – VI F – F O R W A R D C U R R E N T – m AV F – FORWARD VOLTAGE – VHIGH EFFICIENCY RED, ORANGE,YELLOW, AND HIGH PERFORMANCEGREEN, EMERALD GREENR E L A T I V E L U M I N O U S I N TE N S I T Y (N O R M A L I Z E D A T 20 m A )I F – DC FORWARD CURRENT – mA R E L A T I V E L U M I N O U S I N T E N S I T Y (N O R M A L I Z E D A T 20 m A )0I DC – DC CURRENT PER LED – mA10201.60.80.4515301.2250.20.61.01.4HER, ORANGE, YELLOW, AND HIGH PERFORMANCE GREEN, EMERALD GREENFigure 5. Maximum forward dc current vs. ambient temperature. Derating based on T j MAX = 110°C.Figure 4. Relative efficiency (luminous intensity per unit current) vs. peak current.Figure 6. Relative luminous intensity vs. angular displacement. 15 degree family.R E L A T I V E E F F I C I E N C Y (N O R M A L I Z E D A T 20 m A )0I PEAK – PEAK FORWARD CURRENT – mA0.60.8300201001.21.00.20.45020010DH As AlGaAs REDηP E A K – R E L A T I V E E F F I C I E N C Y (N O R M A L I Z E D A T 20 m A )I PEAK – PEAK FORWARD CURRENT – mAHER, ORANGE, YELLOW, HIGHPERFORMANCE GREEN, EMERALD GREENI F – F O R W A R D C U R R E NT – m AT A – AMBIENT TEMPERATURE – °C DH As AlGaAs REDI F – F O R W A R D C U R R E N T – m AT A – AMBIENT TEMPERATURE – °CHER, ORANGE, YELLOW, AND HIGH PERFORMANCE GREEN, EMERALD GREEN N O R M A L I Z E D L U M I N O U S I N T E N S I T Y10ANGULAR DISPLACEMENT – DEGREES0.80.60.50.70.2450.10.30.4403530252010515-5-10-15-20-25-30-35-40-450.9Figure 7. Relative luminous intensity vs. angular displacement. 25 degree family.Intensity Bin Limits Intensity Range (mcd)ColorBin Min.Max.L 101.5162.4M 162.4234.6N 234.6340.0O 340.0540.0P 540.0850.0Q 850.01200.0R 1200.01700.0Red/OrangeS 1700.02400.0T 2400.03400.0U 3400.04900.0V 4900.07100.0W 7100.010200.0X 10200.014800.0Y 14800.021400.0Z 21400.030900.0L 173.2250.0M 250.0360.0N 360.0510.0O 510.0800.0P 800.01250.0YellowQ 1250.01800.0R 1800.02900.0S 2900.04700.0T 4700.07200.0U 7200.011700.0V 11700.018000.0W18000.027000.0N O R M A L I Z E D L U M I N O U S I N T E N S I T Y10ANGULAR DISPLACEMENT – DEGREES0.80.60.50.70.2450.10.30.4403530252010515-5-10-15-20-25-30-35-40-450.9Intensity Bin Limits, continuedIntensity Range (mcd) Color Bin Min.Max.E7.612.0F12.019.1G19.130.7H30.749.1I49.178.5J78.5125.7K125.7201.1L201.1289.0 Green/M289.0417.0 Emerald Green N417.0680.0O680.01100.0P1100.01800.0Q1800.02700.0R2700.04300.0S4300.06800.0T6800.010800.0U10800.016000.0V16000.025000.0W25000.040000.0 Maximum tolerance for each bin limit is ± 18%.Color CategoriesLambda (nm)Color Category #Min.Max.6561.5564.55564.5567.5 Green4567.5570.53570.5573.52573.5576.51582.0584.53584.5587.0 Yellow2587.0589.54589.5592.05592.0593.01597.0599.52599.5602.03602.0604.5 Orange4604.5607.55607.5610.56610.5613.57613.5616.58616.5619.5 Tolerance for each bin limit is ± 0.5 nm.Mechanical Option MatrixMechanical Option Code Definition00Bulk Packaging, minimum increment 500 pcs/bag01Tape & Reel, crimped leads, minimum increment 1300 pcs/bag02Tape & Reel, straight leads, minimum increment 1300 pcs/bagB2Right Angle Housing, even leads, minimum increment 500 pcs/bagUQ Ammo Pack, horizontal leads, in 1K minimum incrementNote:All categories are established for classification of products. Products may not be available in all categories. Please contact your local Agilent representative for further clarification/information./semiconductorsFor product information and a complete list ofdistributors, please go to our web site.For technical assistance call:Americas/Canada: +1 (800) 235-0312 or(916) 788-6763Europe: +49 (0) 6441 92460China: 10800 650 0017Hong Kong: (+65) 6756 2394India, Australia, New Zealand: (+65) 6755 1939Japan: (+81 3) 3335-8152 (Domestic/Interna-tional), or 0120-61-1280 (Domestic Only)Korea: (+65) 6755 1989Singapore, Malaysia, Vietnam, Thailand,Philippines, Indonesia: (+65) 6755 2044Taiwan: (+65) 6755 1843Data subject to change.Copyright © 2004 Agilent Technologies, Inc.Obsoletes 5965-6165ENovember 11, 20045988-2149EN。
HCPL-2631SD中文资料

Single-channel: 6N137, HCPL-2601, HCPL-2611 Dual-Channel: HCPL-2630, HCPL-2631 High Speed-10 MBit/s Logic Gate Optocouplers
July 2005
Test Conditions Symbol
(Note 4) (TA = 25°C) (RL = 350Ω, CL = 15 pF) (Fig. 12) (Note 5) (TA = 25°C) (RL = 350Ω, CL = 15 pF) (Fig. 12) (RL = 350Ω, CL = 15 pF) (Fig. 12) (RL = 350Ω, CL = 15 pF) (Note 6) (Fig. 12) (RL = 350Ω, CL = 15 pF) (Note 7) (Fig. 12) (IF = 7.5 mA, VEH = 3.5 V) (RL = 350Ω, CL = 15 pF) (Note 8) (Fig. 13) (IF = 7.5 mA, VEH = 3.5 V) (RL = 350Ω, CL = 15 pF) (Note 9) (Fig. 13) (TA = 25°C) |VCM| = 50V, (Peak) (IF = 0 mA, VOH (Min.) = 2.0V) 6N137, HCPL-2630 HCPL-2601, HCPL-2631 HCPL-2611 (RL = 350Ω) (Note 10) (Fig. 14) |VCM| = 400V |CML| |VCM| = 50V (Peak) |TPHLTPLH| tr tf tELH tEHL |CMH| TPHL TPLH
Electrical Characteristics (TA = 0 to 70°C Unless otherwise specified) Individual Component Characteristics
XP-3110,3140,3160,3120气体检测仪说明书
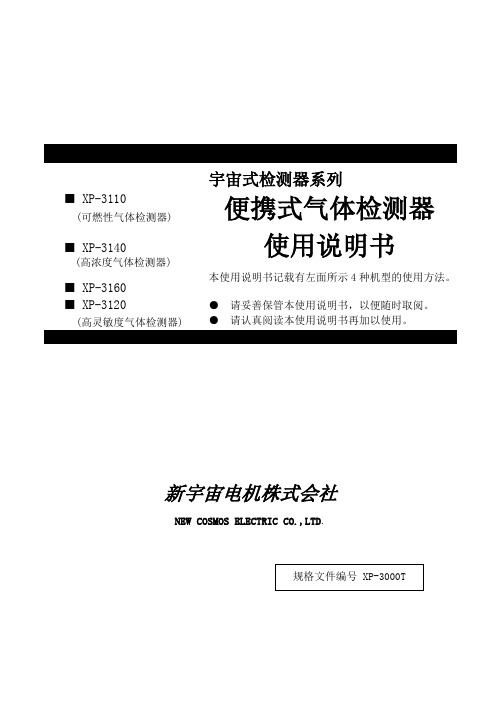
■ 图形符号的说明
正文中使用了危险、警告、注意等用语。上述词语具体定义如下:
! 危险 如不避免,将发生造成死亡或重伤的危险情况。 ! 警告 如不避免,将发生可能造成死亡或重伤的危险情况。
! 注意 附注
如不避免,将发生造成轻伤或物质损失的危险情况。 使用方面的建议事项
1. 前言(续)
■ 安全使用说明
报警灯闪烁
附注
气体浓度画面中长按[],报警点显示约 3 秒,可确认设 定的报警点。
检测高浓度气体,超出显示范围时,显示为 OL。 高浓度气体可能对传感器造成不好影响,所以要迅速吸入洁净空气。气体浓度下 降,确认气体抽出后,请切断电源。
3. 使用方法(续)
各种功能与设定方法
气体浓度画面中,按[MENU]约 3 秒,发出“哔、哔、哔”报警音,可进行下述设
编号时显示。
a. 源开/关时使用。 在气体浓度画面显示过程中,用于范 围切换。
b. 于自动零位调整。
c. 于点亮背景灯。
d. 于停止报警蜂鸣器鸣叫。
·对象气体为 2 种以上时,用于确认气 体编号(无报警时)。
·长按按钮,用于确认报警点。 e.
于各种功能设定。
2. 各部名称与功能(续)
1m 气体导管
附注 显示报错信息时,请参照“报错信息 P18”。
3. 使用方法(续)
3. 检测
气体浓度画面 如显示<气体浓度画面>,便可进行检测。 LCD 副画面,显示时钟。 →关于气体报警,参照 P10。
<气体浓度画面>
附注
在夜间等进行测量时,有时无法看清 LCD 显示,可按“LIGHT”, 点亮 LCD 背景灯。约 30 秒后自动熄灭。
便携式气体检测器主体带便携包背带1m气体导管带排放过滤器及吸管更换用过滤片fe22号碱性干电池使用说明书登记卡和保证书检查成绩书操作说明卡充电电池组bp1充电时需要使用记录数据收集装置软件cdrusb线ac电源ad2ac电源ad2mswinddowsxpos其它版本下将无法运行硬盘空间
HCPL-0631

HCPL-0631HCPL-0631 光电耦合器为结合GaAsP发光二极管和高增益光检测器的光学耦合逻辑门器件,使能输入允许检测器可以被选通。
外文名:HCPL-0631 高速:典型10MBd 兼容:LSTTL/TTL 电流:5mAHCPL-0631HCPL-0631 光电耦合器为结合GaAsP发光二极管和高增益光检测器的光学耦合逻辑门器件,使能输入允许检测器可以被选通。
紧凑SO8封装。
10M高速。
单通道: HCPL0600, HCPL0601, HCPL0611双通道: HCPL0630, HCPL0631, HCPL0661应用:接地回路消除;LSTTL to TTL, LSTTL or 5VCMOS;数据发送,线接收;数据复接型号介绍检测器芯片输出为集电极开路肖特基箝位晶体管,内置屏蔽可以保证5,000V/µs 的高共模抑制(CMR) 能力。
这个独特设计带来最佳交流和直流电路隔离并兼容TTL,光电耦合器的交流和直流参数可以在-40°C 到85°C 的温度范围得到保证,带来无障碍的系统性能。
HCPL-0631 适合高速逻辑接口、输入和输出缓冲以及传统长线驱动器无法承受环境的长线驱动器,建议使用在极高接地或感应噪声环境。
HCPL-0631特点∙VCM = 50V 时5kV/µs 共模抑制(CMR) 能力∙高速:典型10MBd∙兼容LSTTL/TTL∙5mA 低输入电流∙-40°C 到85°C 工作温度范围交流和直流性能保证∙提供8-pin DIP、SOIC-8 和宽体封装选择∙选通输出(仅单通道产品)∙安全规范认证:- UL1577 3,750Vrms/1min- CSA∙选择包括:- 300 = 鸥翼型表面贴装- 500 = 卷带式封装- xxxE = 无铅HCPL-0631应用∙隔离长线接收器∙电脑外设接口∙微处理系统接口∙模数和数模转换数字隔离∙开关电源∙仪器输入/输出隔离∙消除接地环路∙取代脉冲变压器HCPL-0631品牌介绍安华高是高性能的混和信号和数字信号处理的IC,它的产品分为放大器和比较器、数模/模数转换器、嵌入式处理与DSP、模拟微控制器、RF和IF器件、电源和散热管理、音频和视频产品、宽带产品、接口器件、基准源、开关和多路复用器、无线产品。
- 1、下载文档前请自行甄别文档内容的完整性,平台不提供额外的编辑、内容补充、找答案等附加服务。
- 2、"仅部分预览"的文档,不可在线预览部分如存在完整性等问题,可反馈申请退款(可完整预览的文档不适用该条件!)。
- 3、如文档侵犯您的权益,请联系客服反馈,我们会尽快为您处理(人工客服工作时间:9:00-18:30)。
2.0 Amp Output Current IGBT Gate Drive Optocoupler Technical DataHCPL-3120HCPL-J312HCNW3120Features• 2.0 A Minimum Peak Output Current• 15 kV/µs Minimum Common Mode Rejection (CMR) at V CM = 1500 V• 0.5 V Maximum Low Level Output Voltage (V OL )Eliminates Need for Negative Gate Drive• I CC = 5 mA Maximum Supply Current• Under Voltage Lock-Out Protection (UVLO) with Hysteresis• Wide Operating V CC Range:15 to 30 Volts• 500 ns Maximum Switching Speeds• Industrial Temperature Range: -40°C to 100°C • Safety Approval UL Recognized2500 Vrms for 1 min. for HCPL-31203750 Vrms for 1 min. for HCPL-J3125000 Vrms for 1 min. for HCNW3120CSA ApprovalVDE 0884 Approved V IORM = 630 Vpeak for HCPL-3120 (Option 060)V IORM = 891 Vpeak for HCPL-J312V IORM = 1414 Vpeak for HCNW3120BSI Certified (HCNW3120only) (Pending)Applications• IGBT/MOSFET Gate Drive • AC/Brushless DC Motor Drives• Industrial Inverters • Switch Mode Power SuppliesA 0.1 µF bypass capacitor must be connected between pins 5 and 8.CAUTION: It is advised that normal static precautions be taken in handling and assembly of this componentto prevent damage and/or degradation which may be induced by ESD.Functional DiagramTRUTH TABLEV CC - V EE V CC - V EE“POSITIVE GOING”“NEGATIVE GOING”LED (i.e., TURN-ON)(i.e., TURN-OFF)V O OFF 0 - 30 V 0 - 30 V LOW ON 0 - 11 V 0 - 9.5 V LOW ON 11 - 13.5 V 9.5 - 12 V TRANSITIONON13.5 - 30 V12 - 30 VHIGH13SHIELD 248675N /CCATHODE ANODE N/C V CC V O V O V EE13SHIELD248675N /CCATHODE ANODE N/C V CC N/C V O V EEHCNW3120HCPL-3120/J312DescriptionThe HCPL-3120 contains a GaAsP LED while the HCPL-J312 and the HCNW3120 contain an AlGaAs LED. The LED is optically coupled to an integrated circuit with a power output stage. These optocouplers are ideally suited for driving power IGBTs and MOSFETs used in motor control inverter applications. The high operating voltage range of theoutput stage provides the drivevoltages required by gatecontrolled devices. The voltageand current supplied by theseoptocouplers make them ideallysuited for directly driving IGBTswith ratings up to 1200 V/100 A.For IGBTs with higher ratings,the HCPL-3120 series can beused to drive a discrete powerstage which drives the IGBT gate.The HCNW3120 has the highestinsulation voltage ofV IORM=1414Vpeak in theVDE0884. The HCPL-J312 has aninsulation voltage ofV IORM=891Vpeak and theV IORM=630Vpeak is alsoavailable with the HCPL-3120(Option060).Selection GuidePart Number HCPL-3120HCPL-J312HCNW3120HCPL-3150* Output Peak Current ( I O) 2.0 A 2.0 A 2.0 A0.5 AVDE0884 Approval V IORM=630 Vpeak V IORM=891 Vpeak V IORM=1414 Vpeak V IORM=630 Vpeak(Option 060)(Option 060)*The HCPL-3150 Data sheet available. Contact Agilent sales representative or authorized distributor.Ordering InformationSpecify Part Number followed by Option Number (if desired)Example:HCPL-3120#XXX060 = VDE0884, V IORM = 630 Vpeak (HCPL-3120 only)300 = Gull Wing Surface Mount Option500 = Tape and Reel Packaging OptionOption 500 contains 1000 units (HCPL-3120/J312), 750 units (HCNW3120) per reel.Other options contain 50 units (HCPL-3120/J312), 42 units (HCNW312) per tube.Option data sheets available. Contact Agilent sales representative or authorized distributor.(0.025 ± 0.005)MAX.(0.100)BSCDIMENSIONS IN MILLIMETERS (INCHES).LEAD COPLANARITY = 0.10 mm (0.004 INCHES).+ 0.076 - 0.051+ 0.003) - 0.002)Package Outline DrawingsHCPL-3120 and HCPL-J312 Outline Drawing (Standard DIP Package)HCPL-3120 and HCPL-J312 Gull Wing Surface Mount Option 300 Outline DrawingDIMENSIONS IN MILLIMETERS AND (INCHES).+ 0.076 - 0.051(0.010+ 0.003)- 0.002)* MARKING CODE LETTER FOR OPTION NUMBERS. "V" = OPTION 060OPTION NUMBERS 300 AND 500 NOT MARKED.1.78 ± 0.15 MAX.BSCDIMENSIONS IN MILLIMETERS (INCHES).LEAD COPLANARITY = 0.10 mm (0.004 INCHES).HCNW3120 Outline Drawing (8-Pin Wide Body Package)HCNW3120 Gull Wing Surface Mount Option 300 Outline Drawing1.78 ± 0.15 0.254+ 0.076 - 0.0051+ 0.003) - 0.002)Reflow Temperature ProfileRegulatory InformationAgency/StandardHCPL-3120HCPL-J312HCNW3120Underwriters Laboratory (UL)Recognized under UL 1577, Component RecognitionProgram, Category, File E55361Canadian Standards Association (CSA)File CA88324, per Component Acceptance Notice #5Verband Deutscher Electrotechniker (VDE)DIN VDE 0884 (June 1992)Option 060British Standards Institute (BSI)PendingCertification According to BS EN60065: 1994(BS415:1994), BS EN60950: 1992 (BS7002:1992)240TIME – MINUTEST E M P E R A T U R E – °C220200180160140120100806040200260MAXIMUM SOLDER REFLOW THERMAL PROFILE(NOTE: USE OF NON-CHLORINE ACTIVATED FLUXES IS RECOMMENDED.)Insulation and Safety Related SpecificationsValueHCPL-HCPL-HCNWParameter Symbol 3120J3123120Units ConditionsMinimum External L(101)7.17.49.6mmMeasured from input terminals to Air Gap (Clearance)output terminals, shortest distance through air.Minimum External L(102)7.48.010.0mmMeasured from input terminals to Tracking (Creepage)output terminals, shortest distance path along body.Minimum Internal 0.080.5 1.0mmInsulation thickness between emitter Plastic Gapand detector; also known as distance (Internal Clearance)through insulation.Tracking Resistance CTI >175>175>200VoltsDIN IEC 112/VDE 0303 Part 1(Comparative Tracking Index)Isolation GroupIIIa IIIa IIIaMaterial Group (DIN VDE 0110, 1/89,Table 1)VDE0884 Insulation Related CharacteristicsHCPL-3120DescriptionSymbolOption 060HCPL-J312HCNW3120UnitInstallation classification per DIN VDE 0110/1.89, Table 1for rated mains voltage ≤150 V rms I-IV I-IV I-IV for rated mains voltage ≤300 V rms I-IV I-IV I-IV for rated mains voltage ≤450 V rms I-IIII-III I-IV for rated mains voltage ≤600 V rms I-III I-IV for rated mains voltage ≤1000 V rms I-III Climatic Classification55/100/2155/100/2155/100/21Pollution Degree (DIN VDE 0110/1.89)222Maximum Working Insulation Voltage V IORM 6308911414V peak Input to Output Test Voltage, Method b*V PR118116702652V peakV IORM x 1.875 = V PR , 100% Production Test, t m = 1 sec, Partial Discharge < 5pC Input to Output Test Voltage, Method a*V PR 94513362121V peak V IORM x 1.5 = V PR , Type and SampleTest, t m = 60 sec, Partial Discharge < 5pC Highest Allowable Overvoltage*V IOTM600060008000V peak(Transient Overvoltage, t ini = 10 sec)Safety Limiting Values – maximum values allowed in the event of a failure,also see Figure 37. Case Temperature T S175175150°C Input Current I S INPUT 230400400mA Output PowerP S OUTPUT600600700mW Insulation Resistance at T S , V IO = 500 VR S≥109≥109≥109Ω*Refer to the VDE0884 section (page 1-6/8) of the Isolation Control Component Designer's Catalog for a detailed description of Method a/b partial discharge test profiles.Note: These optocouplers are suitable for “safe electrical isolation” only within the safety limit data. Maintenance of the safety data shall be ensured by means of protective circuits. Surface mount classification is Class A in accordance with CECC 00802.All Agilent data sheets report the creepage and clearance inherent to the optocoupler component itself. These dimensions areneeded as a starting point for the equipment designer whendetermining the circuit insulation requirements. However, once mounted on a printed circuit board, minimum creepage and clearance requirements must be met as specified for individual equipment standards. For creep-age, the shortest distance path along the surface of a printed circuit board between the solder fillets of the input and output leads must be considered. There are recommended techniques such as grooves and ribs which may be used on a printed circuit board to achieve desired creepage and clearances. Creepage and clearance distances will alsochange depending on factors such as pollution degree and insulation level.Absolute Maximum RatingsRecommended Operating ConditionsElectrical Specifications (DC)Over recommended operating conditions (T A = -40 to 100°C, I F(ON) = 7 to 16 mA, V F(OFF) = -3.0 to 0.8 V, V CC = 15 to 30 V, V EE = Ground) unless otherwise specified.*All typical values at T A = 25°C and V CC - V EE = 30 V, unless otherwise noted.Switching Specifications (AC)Over recommended operating conditions (T A = -40 to 100°C, I F(ON) = 7 to 16 mA, V F(OFF) = -3.0 to 0.8 V, V CC = 15 to 30 V, V EE = Ground) unless otherwise specified.*All typical values at T A = 25°C and V CC - V EE = 30 V, unless otherwise noted.Package CharacteristicsOver recommended temperature (T A = -40 to 100°C) unless otherwise specified.Parameter Symbol Device Min.Typ.Max.Units Test Conditions Fig.NoteInput-Output V ISO HCPL-31202500V RMS RH < 50%,8, 11Momentary HCPL-J3123750t = 1 min.,9, 11Withstand Voltage**HCNW31205000T A = 25°C 10, 11Resistance R I-O HCPL-31201012ΩV I-O = 500 V DC 11(Input-Output)HCPL-J312HCNW312010121013T A = 25°C1011T A = 100°CCapacitance C I-O HCPL-31200.6pF f = 1 MHz (Input-Output)HCPL-J3120.8HCNW31200.50.6LED-to-Case θLC 467°C/W Thermocouple 28Thermal Resistance LED-to-Detector θLD 442°C/W Thermal ResistanceDetector-to-Case θDC 126°C/W Thermal Resistance*All typicals at T A = 25°C.**The Input-Output Momentary Withstand Voltage is a dielectric voltage rating that should not be interpreted as an input-output continuous voltage rating. For the continuous voltage rating refer to your equipment level safety specification or Agilent Application Note 1074 entitled “Optocoupler Input-Output Endurance Voltage.”located at center underside ofpackage Notes:1. Derate linearly above 70°C free-air temperature at a rate of 0.3 mA/°C.2. Maximum pulse width = 10 µs,maximum duty cycle = 0.2%. This value is intended to allow forcomponent tolerances for designs with I O peak minimum = 2.0 A. See Applications section for additional details on limiting I OH peak.3. Derate linearly above 70°C free-air temperature at a rate of4.8 mW/°C.4. Derate linearly above 70°C free-air temperature at a rate of5.4 mW/°C.The maximum LED junction tempera-ture should not exceed 125°C.5. Maximum pulse width = 50 µs,maximum duty cycle = 0.5%.6. In this test V OH is measured with a dc load current. When driving capacitive loads V OH will approach V CC as I OH approaches zero amps.7. Maximum pulse width = 1 ms,maximum duty cycle = 20%.8. In accordance with UL1577, each optocoupler is proof tested by applying an insulation test voltage ≥3000 Vrms for 1 second (leakage detection current limit, I I-O ≤ 5 µA).9. In accordance with UL1577, each optocoupler is proof tested by applying an insulation test voltage ≥4500 Vrms for 1 second (leakage detection current limit, I I-O ≤ 5 µA).10. In accordance with UL1577, eachoptocoupler is proof tested by applying an insulation test voltage ≥6000 Vrms for 1 second (leakage detection current limit, I I-O ≤ 5 µA).11. Device considered a two-terminaldevice: pins 1, 2, 3, and 4 shorted together and pins 5, 6, 7, and 8shorted together.12. The difference between t PHL and t PLHbetween any two HCPL-3120 parts under the same test condition.13. Pins 1 and 4 need to be connected toLED common.14. Common mode transient immunity inthe high state is the maximum tolerable dV CM /dt of the common mode pulse, V CM , to assure that the output will remain in the high state (i.e., V O >15.0V).15. Common mode transient immunity ina low state is the maximum tolerable dV CM /dt of the common mode pulse,V CM , to assure that the output will remain in a low state (i.e., V O <1.0V).16. This load condition approximates thegate load of a 1200 V/75A IGBT.17. Pulse Width Distortion (PWD) isdefined as |t PHL -t PLH | for any given device.Figure 7. I CC vs. Temperature.Figure 8. I CC vs. V CC .Figure 4. V OL vs. Temperature.Figure 5. I OL vs. Temperature.Figure 6. V OL vs. I OL .Figure 1. V OH vs. Temperature.Figure 2. I OH vs. Temperature.Figure 3. V OH vs. I OH .(V O H – V C C ) – H I G H O U T P U T V O L T A G E D R O P – V-4T A – TEMPERATURE – °C -1-2-3I O H – O U T P U T HI G H C U R R E N T – AT A – TEMPERATURE – °C (V O H – V C C ) – O U T P U T H I G H V O L T A G E D R O P – VI OH – OUTPUT HIGH CURRENT – AV O L – O U T P U T L O W V O L T A G E – V0T A – TEMPERATURE – °C 0.250.050.150.200.10I O L – O U T P U T L O W C U R R E NT – AT A – TEMPERATURE – °CV O L – O U T P U T L O W V O L T A G E– VI OL – OUTPUT LOW CURRENT – A3412I C C – S U P P L Y C U R R E N T – m A1.5T A – TEMPERATURE – °C 3.02.53.52.0I C C – S U P P L Y C U R R E N T –m A1.5V CC – SUPPLY VOLTAGE – V3.02.53.52.0Figure 9. I FLH vs. Temperature.Figure 10. Propagation Delay vs. V CC .Figure 11. Propagation Delay vs. I F .Figure 12. Propagation Delay vs.Temperature.Figure 14. Propagation Delay vs. Cg.Figure 13. Propagation Delay vs. Rg.I F L H – L O W T O H I G H C U R R E N T T H R E S H O L D – m AT A – TEMPERATURE – °C 32415I F L H – L O W T O H I G H C U R R E N T T H R E S H O L D – m AT A – TEMPERATURE – °C HCPL-J312I F L H – L O W T O H I G H C U R R E N T T H R E S H O L D – m AT A – TEMPERATURE – °CHCNW3120T p – P R O P A G A T I O N D E L A Y – n s100V CC – SUPPLY VOLTAGE – V 400300500200T p – P R O P A G A T I O N D E L A Y – n s100I F – FORWARD LED CURRENT – mA 400300500200T p – P R O P A G A T I O N DE L A Y – n s100T A – TEMPERATURE – °C400300500200T p – P R O P A G A T I O N D E L A Y – n s100Rg – SERIES LOAD RESISTANCE – Ω400300500200T p – P R O P A G AT I O N D E L A Y – n s100Cg – LOAD CAPACITANCE – nF400300500200Figure 15. Transfer Characteristics.Figure 16. Input Current vs. Forward Voltage.Figure 17. I OH Test Circuit.V O – O U T P U T V O L T A G E – VI F – FORWARD LED CURRENT – mA5251513025342010HCPL-3120 / HCNW3120V O – O U T P U T V O L T A G E – V0I F – FORWARD LED CURRENT – mA1352551525341020HCPL-J31230I F – F O R W A R D C U R R E N T – m AV F – FORWARD VOLTAGE – VOLTSV F – FORWARD VOLTAGE – VOLTSI F – F O R W A R D C U R R E N T – m ACC = 15 to 30 VI F = 7 to 16 mAFigure 20. V OL Test Circuit.Figure 21. I FLH Test Circuit.Figure 19. V OH Test Circuit.Figure 18. I OL Test Circuit.Figure 22. UVLO Test Circuit.CC = 15 to 30 VCC = 15 to 30 VI F 16 mACC = 15 to 30 VCC = 15 to 30 VI FFigure 24. CMR Test Circuit and Waveforms.Figure 23. t PLH , t PHL , t r , and t f Test Circuit and Waveforms.CC = 15 to 30 V I= 30 VCM V OSWITCH AT B: I F = 0 mAV OSWITCH AT A: I F = 10 mA V OLV OHApplications InformationEliminating Negative IGBT Gate Drive (Discussion appliesto HCPL-3120, HCPL-J312, and HCNW3120)To keep the IGBT firmly off, the HCPL-3120 has a very low maximum V OL specification of 0.5V. The HCPL-3120 realizes this very low V OL by using a DMOS transistor with 1Ω(typical) on resistance in its pull down circuit. When the HCPL-3120 is in the low state, the IGBT gate is shorted to the emitter by Rg + 1Ω. Minimizing Rg and the lead inductance from the HCPL-3120 to the IGBT gate andemitter (possibly by mounting the HCPL-3120 on a small PC board directly above the IGBT) can eliminate the need for negative IGBT gate drive in many applica-tions as shown in Figure 25. Care should be taken with such a PC board design to avoid routing theIGBT collector or emitter traces close to the HCPL-3120 input as this can result in unwantedcoupling of transient signals into the HCPL-3120 and degrade performance. (If the IGBT drain must be routed near the HCPL-3120 input, then the LED should be reverse-biased when in the off state, to prevent the transient signals coupled from the IGBT drain from turning on the HCPL-3120.)Figure 25. Recommended LED Drive and Application Circuit.ACCONTROLINPUTSelecting the Gate Resistor (Rg) to Minimize IGBTSwitching Losses. (Discussion applies to HCPL-3120, HCPL-J312 and HCNW3120)Step 1: Calculate Rg Minimum from the I OL Peak Specifica-tion. The IGBT and Rg in Figure 26 can be analyzed as a simple RC circuit with a voltage supplied by the HCPL-3120.(V CC – V EE - V OL )Rg ≥–––––––––––––––I OLPEAK(V CC – V EE - 2 V )=–––––––––––––––I OLPEAK (15 V + 5 V - 2 V)=––––––––––––––––––2.5 A =7.2 Ω ≅ 8 ΩThe V OL value of 2V in the pre-vious equation is a conservative value of V OL at the peak current of 2.5A (see Figure 6). At lower Rg values the voltage supplied by the HCPL-3120 is not an ideal voltage step. This results in lower peak currents (more margin)than predicted by this analysis.When negative gate drive is not used V EE in the previous equation is equal to zero volts.Figure 26. HCPL-3120 Typical Application Circuit with Negative IGBT Gate Drive.AC- HVDCCONTROLINPUTStep 2: Check the HCPL-3120Power Dissipation and Increase Rg if Necessary. The HCPL-3120 total power dissipation (P T ) is equal to the sum of the emitter power (P E ) and the output power (P O ):P T = P E + P OP E = I F •V F •Duty CycleP O = P O(BIAS) + P O (SWITCHING)= I CC •(V CC - V EE )+ E SW (R G , Q G )•f For the circuit in Figure 26 with I F(worst case) = 16mA, Rg = 8Ω, Max Duty Cycle = 80%, Qg = 500 nC,f =20 kHz and T A max = 85C:P E = 16 mA •1.8 V •0.8 = 23 mW P O = 4.25 mA •20 V+ 5.2 µJ •20 kHz = 85 mW + 104 mW = 189 mW> 178 mW (P O(MAX) @ 85C = 250 mW −15C*4.8 mW/C)The value of 4.25 mA for I CC in the previous equation was obtained by derating the I CC max of 5 mA(which occurs at -40°C) to I CC max at 85C (see Figure 7).Since P O for this case is greater than P O(MAX), Rg must be increased to reduce the HCPL-3120 power dissipation.P O(SWITCHING MAX)= P O(MAX) - P O(BIAS)= 178 mW - 85 mW = 93 mWP O(SWITCHINGMAX)E SW(MAX)=–––––––––––––––f93 mW= ––––––– = 4.65 µW 20 kHzFor Qg = 500 nC, from Figure 27,a value of E SW = 4.65 µW gives a Rg = 10.3 Ω.P EParameterDescription I F LED Current V FLED On Voltage Duty CycleMaximum LED Duty CycleP O ParameterDescription I CC Supply Current V CC Positive Supply Voltage V EENegative Supply VoltageE SW (Rg,Qg)Energy Dissipated in the HCPL-3120 for eachIGBT Switching Cycle (See Figure 27)f Switching FrequencyFigure 27. Energy Dissipated in the HCPL-3120 for Each IGBT Switching Cycle.E s w – E N E R G Y P E R S W I T C H I N G C Y C L E – µJ0Rg – GATE RESISTANCE – Ω6144121082Thermal Model(Discussion applies to HCPL-3120, HCPL-J312and HCNW3120)The steady state thermal model for the HCPL-3120 is shown in Figure 28. The thermal resistance values given in this model can be used to calculate the tempera-tures at each node for a given operating condition. As shown by the model, all heat generated flows through θCA which raises the case temperature T Caccordingly. The value of θCAdepends on the conditions of the board design and is, therefore,determined by the designer. The value of θCA = 83°C/W wasobtained from thermal measure-ments using a 2.5 x 2.5 inch PCboard, with small traces (no ground plane), a single HCPL-3120 soldered into the center of the board and still air. The absolute maximum powerdissipation derating specifications assume a θCA value of 83°C/W.From the thermal mode in Figure 28 the LED and detector IC junction temperatures can be expressed as:T JE = P E • (θLC ||(θLD + θDC ) + θCA )θLC * θDC+ P D •(–––––––––––––––– + θCA )+ T AθLC + θDC + θLDθLC •θDCT JD = P E (––––––––––––––– + θCA)θLC + θDC + θLD+ P D •(θDC ||(θLD + θLC ) + θCA ) + T AInserting the values for θLC and θDC shown in Figure 28 gives:T JE = P E •(256°C/W + θCA ) + P D •(57°C/W + θCA ) + T A T JD = P E •(57°C/W + θCA )+ P D •(111°C/W + θCA ) + T A For example, given P E = 45 mW,P O = 250 mW, T A = 70°C and θCA = 83°C/W:T JE = P E •339°C/W + P D •140°C/W +T A= 45 mW •339°C/W + 250 m W•140°C/W + 70°C = 120°C T JD = P E •140°C/W + P D •194°C/W +T A= 45 mW •140C/W + 250 m W•194°C/W + 70°C = 125°CT JE and T JD should be limited to 125°C based on the board layout and part placement (θCA ) specific to the application.T JE =LED junction temperatureT JD =detector IC junction temperatureT C =case temperature measured at the center of the package bottom θLC =LED-to-case thermal resistance θLD =LED-to-detector thermal resistance θDC =detector-to-case thermal resistance θCA =case-to-ambient thermal resistance∗θCA will depend on the board design and the placement of the part.Figure 28. Thermal Model.θLD = 442 °C/W T JET JDθLC = 467 °C/WθDC = 126 °C/WθCA = 83 °C/W*T CT ALED Drive CircuitConsiderations for Ultra High CMR Performance.(Discussion applies to HCPL-3120, HCPL-J312, and HCNW3120)Without a detector shield, the dominant cause of optocoupler CMR failure is capacitivecoupling from the input side of the optocoupler, through the package, to the detector IC as shown in Figure 29. The HCPL-3120 improves CMR performanceby using a detector IC with an optically transparent Faraday shield, which diverts the capaci-tively coupled current away from the sensitive IC circuitry. How-ever, this shield does noteliminate the capacitive coupling between the LED and optocoup-ler pins 5-8 as shown in Figure 30. This capacitivecoupling causes perturbations in the LED current during common mode transients and becomes the major source of CMR failures forFigure 29. Optocoupler Input to OutputCapacitance Model for Unshielded Optocouplers.Figure 30. Optocoupler Input to OutputCapacitance Model for Shielded Optocouplers.a shielded optocoupler. The main design objective of a high CMR LED drive circuit becomes keeping the LED in the proper state (on or off) during common mode transients. For example,the recommended application circuit (Figure 25), can achieve 15kV/µs CMR while minimizing component complexity.Techniques to keep the LED in the proper state are discussed in the next two sections.CMR with the LED On (CMR H).A high CMR LED drive circuit must keep the LED on during common mode transients. This is achieved by overdriving the LED current beyond the input threshold so that it is not pulled below the threshold during a transient. A minimum LED cur-rent of 10 mA provides adequate margin over the maximum I FLH of 5mA to achieve 15kV/µs CMR.CMR with the LED Off(CMR L).A high CMR LED drive circuitmust keep the LED off (V F≤V F(OFF)) during common modetransients. For example, during a-dV cm/dt transient in Figure 31,the current flowing through C LEDPalso flows through the R SAT andV SAT of the logic gate. As long asthe low state voltage developedacross the logic gate is less thanV F(OFF), the LED will remain offand no common mode failure willoccur.The open collector drive circuit,shown in Figure 32, cannot keepthe LED off during a +dVcm/dttransient, since all the currentflowing through C LEDN must besupplied by the LED, and it is notrecommended for applicationsrequiring ultra high CMR Lperformance. Figure 33 is analternative drive circuit which,like the recommended applicationcircuit (Figure 25), does achieveultra high CMR performance byshunting the LED in the off state.CM • • •• • •Figure 33. Recommended LED Drive Circuit for Ultra-High CMR.Figure 31. Equivalent Circuit for Figure 25 During Common Mode Transient.Figure 32. Not Recommended Open Collector Drive Circuit.Under Voltage Lockout Feature. (Discussion applies toHCPL-3120, HCPL-J312, and HCNW3120)The HCPL-3120 contains an under voltage lockout (UVLO)feature that is designed to protect the IGBT under fault conditions which cause the HCPL-3120supply voltage (equivalent to thefully-charged IGBT gate voltage)to drop below a level necessary to keep the IGBT in a low resistance state. When the HCPL-3120output is in the high state and the supply voltage drops below the HCPL-3120 V UVLO– threshold (9.5<V UVLO– < 12.0) the opto-coupler output will go into the low state with a typical delay,UVLO Turn Off Delay, of 0.6µs.When the HCPL-3120 output is in the low state and the supply voltage rises above the HCPL-3120 V UVLO+ threshold (11.0 <V UVLO+ < 13.5) the optocoupler output will go into the high state (assumes LED is “ON”) with a typical delay, UVLO Turn On Delay of 0.8 µs.Figure 34. Under Voltage Lock Out.V O – O U T P U T V O L T A G E – V(V CC - V EE ) – SUPPLY VOLTAGE – V1014268412Figure 37. Thermal Derating Curve, Dependence of Safety Limiting Value with Case Temperature per VDE 0884.(DUE TO OPTOCOUPLER)= (t PHL MAX - t PHL MIN ) + (t PLH MAX - t PLH MIN ) = (t PHL MAX - t PLH MIN ) – (t PHL MIN - t PLH MAX ) = PDD* MAX – PDD* MIN*PDD = PROPAGATION DELAY DIFFERENCENOTE: FOR DEAD TIME AND PDD CALCULATIONS ALL PROPAGATIONDELAYS ARE TAKEN AT THE SAME TEMPERATURE AND TEST CONDITIONS.V OUT1I LED2V OUT2I LED1Figure 35. Minimum LED Skew for Zero Dead Time.Figure 36. Waveforms for Dead Time.*PDD = PROPAGATION DELAY DIFFERENCENOTE: FOR PDD CALCULATIONS THE PROPAGATION DELAYSARE TAKEN AT THE SAME TEMPERATURE AND TEST CONDITIONS.V OUT1I LED2V OUT2I LED1IPM Dead Time and Propagation DelaySpecifications. (Discussionapplies to HCPL-3120, HCPL-J312, and HCNW3120)The HCPL-3120 includes a Propagation Delay Difference (PDD) specification intended to help designers minimize “dead time” in their power inverterdesigns. Dead time is the time period during which both the high and low side powertransistors (Q1 and Q2 in Figure 25) are off. Any overlap in Q1and Q2 conduction will result in large currents flowing through the power devices between thehigh and low voltage motor rails.O U T P U T P O W E R – P S , I N P U T C U R R E N T – I S0T S – CASE TEMPERATURE – °C1000400600800200100300500700900O U T P U T P O W E R – P S , I N P U T C U R R E N T – I S0T S – CASE TEMPERATURE – °C 600400800200100300500700To minimize dead time in a given design, the turn on of LED2 should be delayed (relative to the turn off of LED1) so that under worst-case conditions, transistor Q1 has just turned off when transistor Q2 turns on, as shown in Figure 35. The amount of delay necessary to achieve this condi-tions is equal to the maximum value of the propagation delay difference specification, PDD MAX, which is specified to be 350ns over the operating temperature range of -40°C to 100°C.Delaying the LED signal by themaximum propagation delaydifference ensures that theminimum dead time is zero, but itdoes not tell a designer what themaximum dead time will be. Themaximum dead time is equivalentto the difference between themaximum and minimum propaga-tion delay difference specifica-tions as shown in Figure 36. Themaximum dead time for theHCPL-3120 is 700ns (= 350ns -(-350ns)) over an operatingtemperature range of -40°C to100°C.Note that the propagation delaysused to calculate PDD and deadtime are taken at equal tempera-tures and test conditions sincethe optocouplers under consider-ation are typically mounted inclose proximity to each other andare switching identical IGBTs.Data subject to change.Copyright © 1999 Agilent TechnologiesObsoletes 5965-4779E5965-7875E (11/99)。