全自控氯化氢合成及干燥装置的运行总结及改造
氯化氢干燥系统运行总结
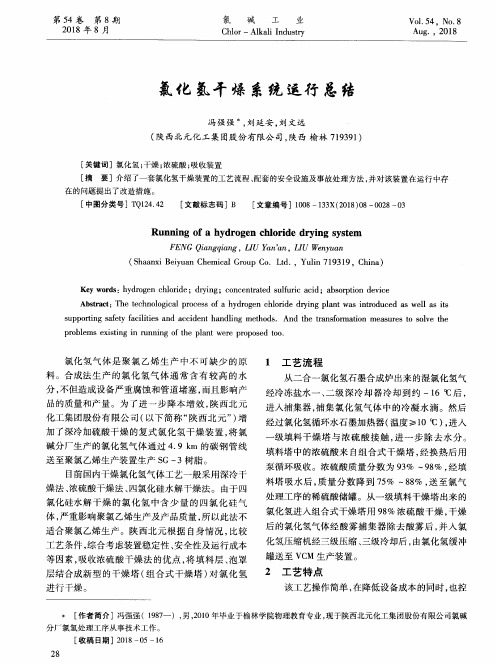
氯 碱 工 业
Chlor——Alkali Industry
Vo1.54 ,No.8 Aug.,2018
氯化 氢干 燥 系统 运 行 总 结
冯 强 强 ,刘 延 安 ,刘 文 远
(陕西 北元化 工集 团股份 有 限公 司 ,陕西 榆 林 719391)
目前 国内干燥氯化氢气体工艺一般采用深冷干 燥法 、浓硫 酸 干燥法 、四氯 化硅 水解 干燥 法 。 由于 四 氯化 硅水 解 干 燥 的氯 化 氢 中含 少 量 的 四氯 化 硅 气 体 ,严 重影 响 聚氯 乙烯生 产及 产 品质 量 ,所 以此法 不 适合 聚氯 乙烯 生 产 。陕 西北 元 根 据 自身情 况 ,比较 工艺 条件 ,综合 考 虑装置稳 定 性 、安 全性 及运 行成本 等因素 ,吸收浓硫酸干燥法 的优点 ,将填料层 、泡罩 层结 合成 新 型 的 干燥 塔 (组 合 式 干 燥 塔 )对 氯 化 氢 进行 干燥 。
1 工艺流程 从 二合一 氯化 氢石 墨合成 炉 出来 的湿氯 化氢气
经冷 冻盐 水一 、二 级深 冷 却 器 冷 却 到 约 一l6℃后 , 进入 捕集 器 ,捕 集 氯 化 氢气 体 中 的冷 凝水 滴 。然后 经过 氯化 氢循 环水 石墨加 热器 (温度 ≥10℃ ),进 入 一 级 填料 干 燥 塔 与浓 硫 酸 接 触 ,进 一 步 除 去 水 分 。 填料 塔 中 的浓 硫 酸来 自组合 式 干燥 塔 ,经 换 热 后 用 泵循 环 吸收 。浓硫 酸质 量 分数 为 93% ~98% ,经 填 料塔 吸水 后 ,质量 分 数 降 到 75% ~88% ,送 至 氯气 处理 工 序 的稀 硫酸 储罐 。从 一级填 料 干燥塔 出来 的 氯化 氢进 入组 合式 干燥 塔 用 98% 浓硫 酸干 燥 ,干燥 后 的氯化 氢气 体 经酸 雾 捕 集 器 除去 酸 雾 后 ,并 入 氯 化 氢压 缩机经 三级 压缩 、三级 冷却 后 ,由氯化 氢缓 冲 罐送 至 VCM 生产 装 置 。 2 工 艺特 点
氯化氢合成中的自动控制技术
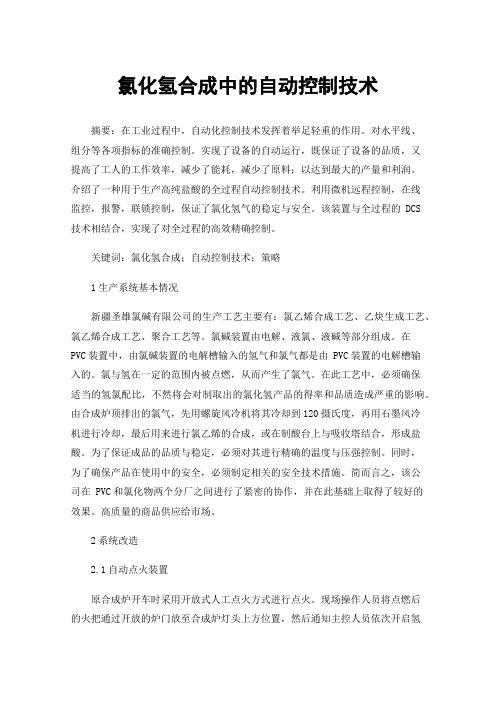
氯化氢合成中的自动控制技术摘要:在工业过程中,自动化控制技术发挥着举足轻重的作用。
对水平线、组分等各项指标的准确控制。
实现了设备的自动运行,既保证了设备的品质,又提高了工人的工作效率,减少了能耗,减少了原料;以达到最大的产量和利润。
介绍了一种用于生产高纯盐酸的全过程自动控制技术。
利用微机远程控制,在线监控,报警,联锁控制,保证了氯化氢气的稳定与安全。
该装置与全过程的 DCS技术相结合,实现了对全过程的高效精确控制。
关键词:氯化氢合成;自动控制技术;策略1生产系统基本情况新疆圣雄氯碱有限公司的生产工艺主要有:氯乙烯合成工艺、乙炔生成工艺、氯乙烯合成工艺、聚合工艺等。
氯碱装置由电解、液氯、液碱等部分组成。
在PVC装置中,由氯碱装置的电解槽输入的氢气和氯气都是由 PVC装置的电解槽输入的。
氯与氢在一定的范围内被点燃,从而产生了氯气。
在此工艺中,必须确保适当的氢氯配比,不然将会对制取出的氯化氢产品的得率和品质造成严重的影响。
由合成炉顶排出的氯气,先用螺旋风冷机将其冷却到120摄氏度,再用石墨风冷机进行冷却,最后用来进行氯乙烯的合成,或在制酸台上与吸收塔结合,形成盐酸。
为了保证成品的品质与稳定,必须对其进行精确的温度与压强控制。
同时,为了确保产品在使用中的安全,必须制定相关的安全技术措施。
简而言之,该公司在 PVC和氯化物两个分厂之间进行了紧密的协作,并在此基础上取得了较好的效果。
高质量的商品供应给市场。
2系统改造2.1自动点火装置原合成炉开车时采用开放式人工点火方式进行点火。
现场操作人员将点燃后的火把通过开放的炉门放至合成炉灯头上方位置,然后通知主控人员依次开启氢气旁路切断阀、氢气切断阀,待进入合成炉的氢气燃烧稳定后,现场操作人员将火把抽出后熄灭;通知主控人员开启氯气旁路切断阀、氯气切断阀,使氯气进入合成炉与氢气混合燃烧,火焰稳定后,关闭炉门。
点炉操作过程中需要4名操作人员,点火步骤繁琐,且从合成炉抽取火把时,存在炉内火焰冲出炉门、爆鸣、灯头炸裂等风险,容易发生安全生产事故。
氯气干燥系统运行总结
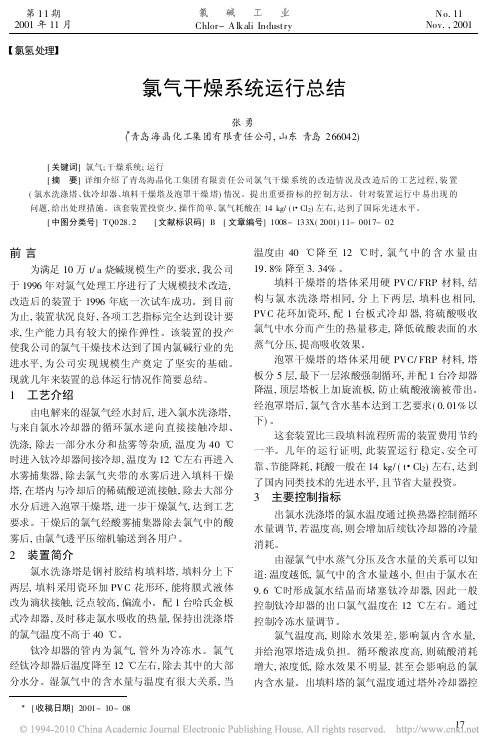
氯氢处理氯气干燥系统运行总结张勇(青岛海晶化工集团有限责任公司,山东青岛266042)[关键词]氯气;干燥系统;运行[摘要]详细介绍了青岛海晶化工集团有限责任公司氯气干燥系统的改造情况及改造后的工艺过程,装置(氯水洗涤塔、钛冷却器、填料干燥塔及泡罩干燥塔)情况。
提出重要指标的控制方法。
针对装置运行中易出现的问题,给出处理措施。
该套装置投资少,操作简单,氯气耗酸在14kg/(t!Cl2)左右,达到了国际先进水平。
[中图分类号]T Q028.2[文献标识码]B[文章编号]1008-133X(2001)11-0017-02前言为满足10万t/a烧碱规模生产的要求,我公司于1996年对氯气处理工序进行了大规模技术改造,改造后的装置于1996年底一次试车成功。
到目前为止,装置状况良好,各项工艺指标完全达到设计要求,生产能力具有较大的操作弹性。
该装置的投产使我公司的氯气干燥技术达到了国内氯碱行业的先进水平,为公司实现规模生产奠定了坚实的基础。
现就几年来装置的总体运行情况作简要总结。
1工艺介绍由电解来的湿氯气经水封后,进入氯水洗涤塔,与来自氯水冷却器的循环氯水逆向直接接触冷却、洗涤,除去一部分水分和盐雾等杂质,温度为40∀时进入钛冷却器间接冷却,温度为12∀左右再进入水雾捕集器,除去氯气夹带的水雾后进入填料干燥塔,在塔内与冷却后的稀硫酸逆流接触,除去大部分水分后进入泡罩干燥塔,进一步干燥氯气,达到工艺要求。
干燥后的氯气经酸雾捕集器除去氯气中的酸雾后,由氯气透平压缩机输送到各用户。
2装置简介氯水洗涤塔是钢衬胶结构填料塔,填料分上下两层,填料采用瓷环加PVC花形环,能将膜式液体改为滴状接触,泛点较高,偏流小。
配1台哈氏金板式冷却器,及时移走氯水吸收的热量,保持出洗涤塔的氯气温度不高于40∀。
钛冷却器的管内为氯气,管外为冷冻水。
氯气经钛冷却器后温度降至12∀左右,除去其中的大部分水分。
湿氯气中的含水量与温度有很大关系,当温度由40∀降至12∀时,氯气中的含水量由19.8%降至3.34%。
氯化氢副产蒸汽合成炉装置运行总结
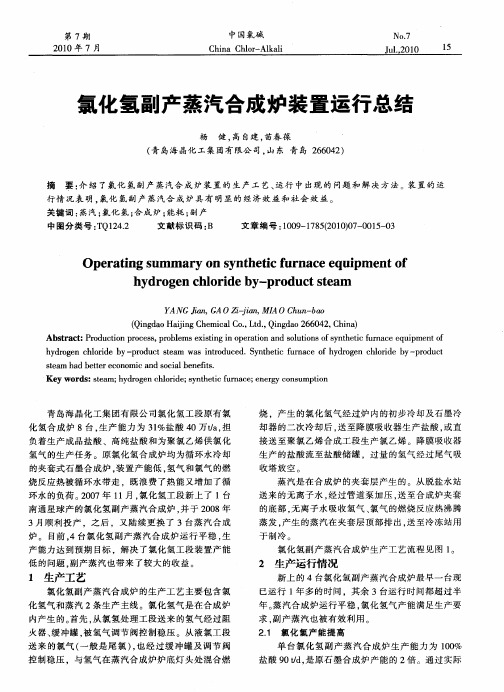
却 器 的二次 冷 却后 , 至 降膜 吸收 器生 产盐 酸 , 直 送 或
接 送 至聚氯 乙烯合 成工 段 生产 氯 乙烯 。降膜 吸 收器 生 产 的盐 酸流 至盐 酸储 罐 ,过 量 的氢气 经过 尾气 吸 收塔放 空 。 蒸 汽是 在合 成 炉 的夹套 层产 生 的 。从 脱 盐水 站 送来 的无离 子 水 , 过管 道 泵加 压 , 经 送至合 成 炉夹套 的底部 , 离子 水 吸收氢 气 、 元 氯气 的燃烧 反应 热沸 腾
烧 ,产 生 的氯 化氢 气经 过 炉 内的初 步冷 却及 石 墨冷
化氢 合 成 炉 8台 , 产 能力 为 3%盐 酸 4 生 1 0万 t , , 担 a
负着 生产 成 品盐 酸 、高纯 盐酸 和为 聚氯 乙烯 供氯 化 氢气 的生 产任 务 。原 氯化 氢合 成炉 均 为循环 水冷 却
单 台氯化 氢 副 产 蒸 汽合 成 炉 生 产 能 力 为 1 0 0 %
中 图分类 号 :Q142 T 2.
文献 标识 码 : B
文章 编号 :0 9 18 (0 00 — 0 5 0 10 — 7 52 1 )7 0 1— 3
Op r t gs m m a y o y t e i r a ee u p e f e a i u n r n s n h t f n c q i m nt c u o h d o e h o i eb - r d c t a y r g n c l rd y p o u t e m s
1 生产工 艺
氯化氢 副 产蒸 汽合 成炉 的生 产工 艺 主要 包含 氯 化氢气 和蒸 汽 2条 生产 主线 。氯 化 氢气是 在 合成 炉
内产 生 的。 首先 , 氯氢 处理 工段 送来 的氢气 经过 阻 从
氯化氢生产装置运行总结
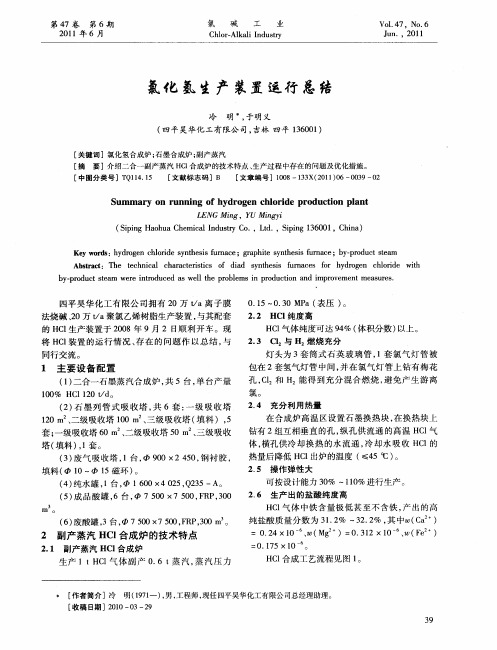
H 1 成 工艺 流程 见 图 1 C合 。
[ 作者简 介]冷
明 (9 1 ) 男 , 17 一 , 工程 师 , 现任 四平吴华化工有 限公 司总经理助理 。
3 9
[ 收稿 日期 ]2 1 0 00— 3—2 9
;
¥ 料与 设备 材
2 5 操 作弹性 大 .
可按 设计 能 力 3 % ~10 进行 生产 。 0 % 1 2 6 生 产 出的盐 酸纯 度高 .
H1 C 气体中铁含量极低甚至不含铁 , 产出的高
( ) 酸罐 , , 750X 0 ,R ,0 6废 3台 0 750 F P30m 。 纯盐 酸 质 量分 数 为 3 . % ~3 . % , 中W( a ) 12 22 其 C
氯。
2 4 充分 利 用热 量 .
1 主 要 设 备 配 置
() 1 二合 一石 墨蒸 汽 合 成 炉 , 5台 , 台产 量 共 单
1 0% HC11 0 t d。 0 2 /
( ) 墨 列 管 式 吸 收 塔 , 6套 : 级 吸 收 塔 2石 共 一 10m 、 2 二级 吸 收塔 10m 、 0 三级 吸 收塔 ( 料 ), 填 5 套; 一级 吸 收塔 6 二级 吸 收塔 5 3、 级 吸收 0m 、 01 三 1 塔( 填料 ) 1 。 ,套 ( ) 气 吸收 塔 , , 90X240 钢 衬 胶 , 3废 1台 0 5 , 填料 ( l l 环 ) O~ 5磁 。 (× 2 ,25一A。 6 ( ) 品酸 罐 , 5成 6台 , 750×750,R ,0 0 0 F P 30
[ 关键 词]氯化氢合成炉 ; 石墨合成炉 ; 副产蒸汽
[ 摘
要]介绍二合一副产蒸 汽 H 1 C 合成 炉的技术特点 、 生产过 程中存在的问题及优化措施 。 [ 文献标志码 ]B [ 文章编号 ]10 0 8—13 2 1 )6— 0 9— 2 3 X(0 1 0 0 3 0
副产0.20MPa蒸汽氯化氢合成炉运行总结—金泰氯碱
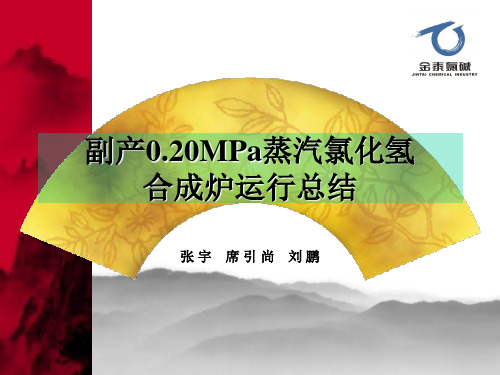
氯化氢(t) 蒸汽(t)
实际累计数据:
氯化氢 40,831 t
蒸汽
30,309 t
实际合成每吨氯化氢的产汽量为: 30309/40831=0.74 t/t
理论合成每吨氯化氢的产汽量为: 44700/50000=0.89 t/t
产率为: 0.74/0.89=83%
四
利用合成炉副产的蒸汽
反
卤水和盐水的加热
每摩尔HCl的合成反应热
92.048 kJ
每小时产生的反应热 12,609,315 kJ/h
氯化氢带出的热量
902,250 kJ/h
蒸汽带走的热量(不考虑热损失)
11,707,065 kJ/h
理论产汽量
4.47t/h
三
表:2006年合成炉运行数据
8000
运
6000
行
数
4000
据
2000
分
0
析
5月 6月 7月 8月 9月 10月 11月 12月
应
热
冬季的取暖
的
二期时计划采用低压蒸汽制冷机组
利
进行液氯冷冻及聚合的软水升温
用
低压蒸汽年产值
216万元
五
循环水费用年节约 纯水补充年花费
22.38万元 24万元
经
经济效益计算
济
216+22.38-24=214.38万元/年
效
益
工艺安装总造价约320万元
约1.49年就可收回合成炉全部投资
一 设计
二 装置介绍
三 运行数据分析
目
四 反应热的利用
录
五 经济效益
六 运行效果
七 改进建议
八 技术进展
氯化氢合成控制系统浅析
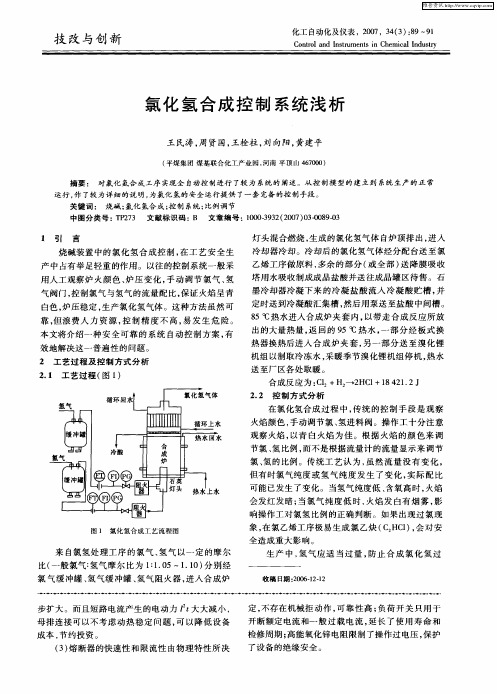
生产 中 , 氢气 应适 当 过量 , 止合 成氯 化 氢过 防
收稿 日期 :0 61 .2 20 —21
步扩大 。而且短路 电流产生 的电动力 , 大大减小 , £
定, 不存在机械拒 动作 , 靠性 高 ; 荷开关 只用 于 可 负
开断额定电流和一般 过载 电流 , 长 了使用 寿命 和 延
11 )。当氯气 流 量 F 一 2 .0 T 3 A变化 时 , 0 由氯气 在 线
成份分析仪 A 一0 T3 2将 氯气纯 度值 送 主调节 器 FC I一 32 0 A进行折百运算补偿 , 同时 , 根据压力变送器 一 32 温度 变送 器 T一 2的检 测值 , 0、 I0 3 对氯 气流 量 F 一 r 32 0 A进 行压力 、 温度补 偿 , 氯气 流量 F 一0 A成 使 T3 2 为真 值 流量 FC3 2 I-0 A(Q ) 同 时 , 气 流 量 f 一 , 氢 T r 31 0 A经 同样 处理 后 , 到氢 气 真值 流 量 FC3 1 得 I一 A 0
・
9 0・
化 工 自 动 化 及 仪 表
第3 4卷
氯: 一方面可 以防止 在做酸 时尾 气含 氯高形 成氢 氯
3 1 真值 流量的获取 .
爆炸性混和气体 的 条件 , 别是采 用 液氯生 产 的废 特 氯来合成盐酸时 , 更要提 高氢氯 配 比, 避免尾气 系统 发生爆炸 ; 另一方 面防止 在 氯乙烯 工序 氯化 氢气体
靠 , 浪费人 力 资 源 , 制精 度 不 高 , 但 控 易发 生 危 险 。
本文将介绍一 种安 全可靠 的系 统 自动控 制 方案 , 有 效地解决这一普遍性 的问题 。
2 工 艺 过 程 及 控 制 方 式 分 析 2 1 工 艺过 程 ( I . 图 )
氯化氢合成炉远程控制和自动点火系统改造总结 张东元

氯化氢合成炉远程控制和自动点火系统改造总结张东元摘要:通过对老旧的氯化氢石墨合成炉远程控制系统改造和设计自动点火系统过程的分析、运行参数和运行经验的总结,得出老旧的低压蒸汽石墨合成炉可以进行现场本体开孔改造,并可通过对自控系统进行全新设计,实现老旧式合成炉的远程控制和自动点火功能。
关键词:合成炉;远程控制;自动点火1 远程自动控制1.1 氯、氢主管线安装切断系统(1)联锁X#-Y#炉氢气、氯气切断阀关闭;(2)联锁关闭氢气缓冲罐进口系统切断阀;(3)联锁关闭氯气缓冲罐进口系统切断阀;(4)乙炔系统水环泵送出压力达到70kPa时,大回路旁路切断阀开。
1.2 分比例调节系统考虑到氢气过量太多会使氯化氢纯度降低,氢气过量太少虽会使氯化氢纯度上升,但氯化氢中游离氯含量会超量,为此设计上考虑氯化氢纯度为93%~96%,并优先考虑游离氯含量在20×10-6以下为条件进行程序设计。
氯气通过主切断阀后并联进入各合成炉,单台合成炉均设计有流量计和手动阀、自动切断阀、主自动调节阀,主自动调节阀旁并联有一个辅助自动调节阀及前后手阀组,主自动调节阀可控制流量在0~2500m3/h,辅助调节阀可控制流量在0~250m3/h,即主流量的10%,氢气系统也采用相同流程。
氯气和氢气的微量调节均采用单回路闭环控制,每次只调节一个变量,保证系统稳定生产。
同时设置在线游离氯含量超标(超250×10-6,可设置)一键紧停程序。
2 自动点火系统2.1 自控系统引火完成后,程序自动进入点燃炉膛灯头火焰的程序,通过自控阀门、限流孔板、火焰检测等组合完成。
火焰监测采用冗余式火焰检测方法,利用光波原理,通过信号转换,获得开关量输出与模拟量输出的双组信号。
2.2 合成炉准备合成炉抽真空,分析合格后,合成炉准备完成。
10 min内完成点炉程序。
2.3 点火程序设置(1)枪内空气吹扫合成炉装置准备就绪,DCS启动程序。
对点火枪关闭氮气控制阀,打开空气控制阀将空气调节阀开至最大设定值,进行空气吹扫;吹扫时间约10s;(2)枪内点火空气调节阀至较小值。
- 1、下载文档前请自行甄别文档内容的完整性,平台不提供额外的编辑、内容补充、找答案等附加服务。
- 2、"仅部分预览"的文档,不可在线预览部分如存在完整性等问题,可反馈申请退款(可完整预览的文档不适用该条件!)。
- 3、如文档侵犯您的权益,请联系客服反馈,我们会尽快为您处理(人工客服工作时间:9:00-18:30)。
全自控氯化氢合成及干燥装置的运行总结及改造
摘要:介绍了氯化氢合成及干燥装置的工艺,分析了该装置的特优点及运行中的存在的问题,并进行了相应改进。
关键词:氯化氢合成装置工艺优点缺陷改进
一、装置简介
山西潞安高纯硅业科技有限责任公司(以下简称“潞安多晶硅”)氯化氢合成工序采用的进口us400/g二合一石墨合成炉及配套的干燥系统、吸收系统于2012年8月投料试车成功,其核心设备采用法国独特的向下点火式二合一石墨合成炉及美国分子筛吸附装置,整个装置实现了dcs+plc相结合控制,具有很高的自动化程度。
二、氯化氢合成及干燥装置工艺流程
该装置由两套相同的合成单元、一套分子筛干燥单元组成。
由自电解制氢工序的干燥氢气与由液氯汽化工序来的干燥氯气经过调
压阀减压和流量调节进入二合一合成炉内的燃烧室,氢气和氯气在火焰向下的燃烧器里混合燃烧生成氯化氢气体,气体向下流经燃烧室和冷却段,出合成炉的氯化氢气体含水量约700ppmv。
再进入石墨冷凝冷却器、除雾器经 -21℃冷冻盐水冷凝除水后含水量降至100ppmv左右,再经过干燥单元的分子筛吸附塔进行变温吸附脱水后,氯化氢气体含水量小于5ppmv。
然后经隔膜压缩机压缩后送入三氯氢硅合成工序。
为保证安全和环保,本装置每条生产线还配备有一套主要由氯化氢降膜吸收器、盐酸中间罐、尾气塔组成的氯化氢吸收系统,可用
来吸收装置因负荷调整或紧急泄放而排出的氯化氢气体。
工艺的核心是合成单元(或整合的燃烧室和冷却器),这个单元由浸渍石墨材料构成,并由水冷却的钢外壳包住。
氢气和氯气由合成装置的顶部进入专业设计的特殊燃烧器燃烧,从而确保完全燃烧。
分子筛干燥单元主要由2个轮流使用于吸附氯化氢水份和再生的吸附塔组成。
2个塔在操作过程中进行切换,至少一个吸附塔是在吸附模式,另一个在再生模式。
一个循环合计有96小时,48个小时用于吸附,48个小时用于再生、备用。
再生结束,吸附塔又重新具备处理原料气并生产净化气的能力。
两个吸附塔轮流进行上述的步骤,保证连续处理原料气,同时连续生产净化气。
三、装置的特点及运行中的优点
通过运行情况可以看出,此套氯化氢合成及干燥装置具有一些优越性。
1.此装置的氯化氢合成炉燃烧室、冷却部分均为等均压石墨材质,较传统钢制合成炉,防腐性能更为优越,但热利用率较低。
2.合成炉燃烧器即灯头,设置在合成炉顶端,在燃烧室和冷却段的上端,火焰是朝下的。
其他炉子的灯头一般都安装在合成炉底部,火焰是朝上的,在氢气和空气燃烧时生成的水,经炉体上不的冷却段冷凝后,由于重力作用自上而下滴在高温的石英灯头上,突然局部冷却,会使石英灯头炸裂损坏;而安装在顶端的都疼,即便有冷年水生成由于重力和气流的作用,可避免滴落在灯头上,减少了灯
头的损坏率,从而增加了灯头的寿命。
3.系统安全性高,系统设置有17项停车连锁条件,当其中任意条件不满足时,都将会影响系统安全,plc都将会执行紧急停车程序,各相关阀门按程序执行动作:氯气氢气切断阀自动关闭,氮气阀自动打开进行充氮吹扫,自动切换为吸收模式,用水将系统内残存的hcl气体吸收掉,使得整个生产过程中,不会出现超温、超压、超限等事故发生,安全系数大大提升。
4.系统配置的分子筛干燥吸附塔,通过不同配比装入的氧化铝、硅胶、分子筛矿石等填料对含水氯化氢气体进行吸附脱水,效果明显,产品含水量很低,达到20ppm以下,最低可达3~5ppm;通过变温变压使两个吸附塔实现连续地吸附、解吸循环,完成连续生产。
四、装置的运行缺陷及改造
1.氢气氯气压力控制不稳定。
系统在氢气氯气管线上设置有调压阀,调压阀后的管线上设置有流量调节阀,在运行过程中,当上游提供氢气氯气工段压力波动较大时,由于调压阀有一定的滞后性,不能马上调整到设计压力,致使调压阀后的流量调节阀在压力有大波动的情况下不能及时调节流量,达到连锁限制时导致系统停车,为生产的连续性带来诸多的不便。
相应改造:在氢气氯气管线上各增加一个3m3的缓冲罐,使得压力波动有更大的缓冲余量,值得系统更加稳定,改造后在使用过程中效果良好。
2.氯化氢合成炉火焰温度最高可达2000℃,燃烧室内温度达
400℃左右,高温的氯化氢气体通过石墨燃烧室与钢外壳之间通入的冷却水进行换热冷却,用的冷却水为普通循环冷却水,其中钙镁离子较多,在高温下极容易在石墨块及壁上结垢,堵塞流道,减少换热面积影响换热效率,从而影响氯化氢气体的冷却效果,且需要拆炉进行清洗。
相应改造:使用脱盐水作为冷却水,即可避免结垢问题;另外增加一个循环槽、一台板式换热器和两台循环水泵即可实现成本相对较高的脱盐水的循环使用,节约了成本,见图1。
3.装置的合成炉、冷凝器、降膜吸收器等设备内使用的石墨块内件,虽然防腐性能优越,但石墨件具有硬度大、韧性差、易破损、难维护的特点,在运输和冬季保养上带来了很多困难。
我厂在设备到场半年多后准备调试时,结果发现合成炉保不住压,将合成炉拆卸后取出石墨块进行打压试验,发现好多石墨块已经破损,两台合成炉的石墨块都出现了不同程度的破损,由于石墨件的特性很多问题不能修补只能更换,设备厂家判定可能为冬季石墨块内的未排尽的积水上冻膨胀使石墨块开裂。
改进措施:在设备的服务侧管道上增加一空气管道,当设备停运后首先降服务侧的水通过排尽阀排出,然后用干燥空气对服务侧及石墨块的各流道进行吹扫,将排不尽的水用空气吹出。
同时在石墨设备的钢壳外壁缠绕低温电伴热带,在冬季设备停运时电伴热常开,保持设备内温度在0℃以上即可,防止死角的积水上冻。
4.在运行过程中,有时会出现过氯,或者氯化氢吸收不完全的情
况,通过尾气塔顶部排如大气中,造成现场出现酸雾和刺激性气味,污染环境。
相应改造:增加一套碱洗涤装置,将尾气塔的尾气接入该装置中,通过10%的碱液将未吸收掉的氯化氢及氯气中和掉,避免了超标尾气排入大气中,见图2。
五、结语
全自控氯化氢合成及干燥装置在试生产当中经过了改造之后,运行效果良好,系统稳定,产品合格,清洁环保,保证了文明和安全生产。
作者简介:赵璐(1986-),男,山西长治人,职称:助理工程师,学历:本科,主要研究方向:化工生产与管理。