氯化氢合成与吸收工艺设计及运行总结
氯化氢副产蒸汽合成炉装置运行总结
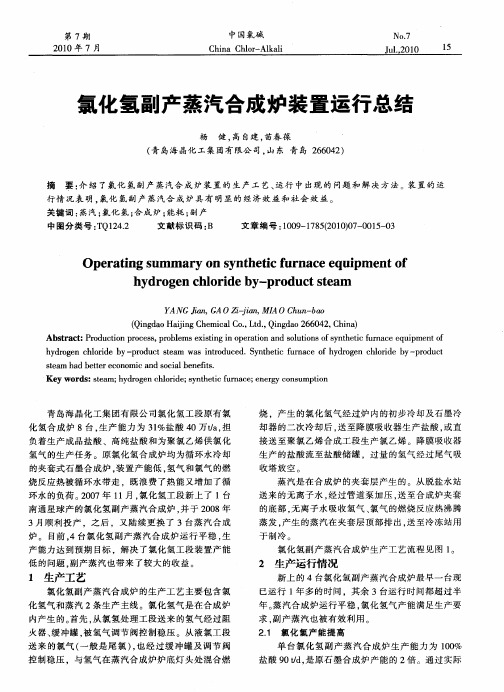
却 器 的二次 冷 却后 , 至 降膜 吸收 器生 产盐 酸 , 直 送 或
接 送 至聚氯 乙烯合 成工 段 生产 氯 乙烯 。降膜 吸 收器 生 产 的盐 酸流 至盐 酸储 罐 ,过 量 的氢气 经过 尾气 吸 收塔放 空 。 蒸 汽是 在合 成 炉 的夹套 层产 生 的 。从 脱 盐水 站 送来 的无离 子 水 , 过管 道 泵加 压 , 经 送至合 成 炉夹套 的底部 , 离子 水 吸收氢 气 、 元 氯气 的燃烧 反应 热沸 腾
烧 ,产 生 的氯 化氢 气经 过 炉 内的初 步冷 却及 石 墨冷
化氢 合 成 炉 8台 , 产 能力 为 3%盐 酸 4 生 1 0万 t , , 担 a
负着 生产 成 品盐 酸 、高纯 盐酸 和为 聚氯 乙烯 供氯 化 氢气 的生 产任 务 。原 氯化 氢合 成炉 均 为循环 水冷 却
单 台氯化 氢 副 产 蒸 汽合 成 炉 生 产 能 力 为 1 0 0 %
中 图分类 号 :Q142 T 2.
文献 标识 码 : B
文章 编号 :0 9 18 (0 00 — 0 5 0 10 — 7 52 1 )7 0 1— 3
Op r t gs m m a y o y t e i r a ee u p e f e a i u n r n s n h t f n c q i m nt c u o h d o e h o i eb - r d c t a y r g n c l rd y p o u t e m s
1 生产工 艺
氯化氢 副 产蒸 汽合 成炉 的生 产工 艺 主要 包含 氯 化氢气 和蒸 汽 2条 生产 主线 。氯 化 氢气是 在 合成 炉
内产 生 的。 首先 , 氯氢 处理 工段 送来 的氢气 经过 阻 从
氯化氢合成工艺流程图合成法(3篇)

摘要:氯化氢(HCl)是一种重要的无机化工原料,广泛应用于合成盐酸、氯气、合成纤维、塑料、染料、农药等领域。
氯化氢的合成方法主要有合成氨法、盐酸合成法、氢气氯化法等。
本文主要介绍氢气氯化法合成氯化氢的工艺流程图及其合成方法。
一、引言氯化氢是一种无色、有刺激性气味的气体,具有强烈的腐蚀性。
在工业生产中,氯化氢的合成方法多种多样,其中氢气氯化法因其原料易得、工艺简单、生产成本低等优点而被广泛应用。
本文将详细介绍氢气氯化法合成氯化氢的工艺流程图及其合成方法。
二、氢气氯化法合成氯化氢的原理氢气氯化法合成氯化氢的原理是:在高温、高压、催化剂的作用下,氢气与氯气反应生成氯化氢。
反应方程式如下:H2 + Cl2 → 2HCl三、氢气氯化法合成氯化氢的工艺流程图1. 原料准备(1)氢气:选用高纯度的氢气,一般要求氢气纯度大于99.99%。
(2)氯气:选用高纯度的氯气,一般要求氯气纯度大于99.5%。
2. 氢气与氯气混合将氢气与氯气按一定比例混合,混合比一般为1:1。
3. 催化剂准备选用合适的催化剂,如钼催化剂、钴催化剂等。
催化剂的活性对氯化氢的合成反应速率和产率有很大影响。
4. 反应将混合好的氢气与氯气送入反应器,在高温、高压、催化剂的作用下进行反应。
反应温度一般在400-500℃,压力一般在1-5MPa。
反应生成的氯化氢气体在冷凝器中冷凝成液体,同时分离出未反应的氢气和氯气。
6. 分离将冷凝后的氯化氢液体进行分离,得到氯化氢产品。
7. 废气处理未反应的氢气和氯气在废气处理系统中进行处理,如吸收、吸附等,以达到环保要求。
四、氢气氯化法合成氯化氢的合成方法1. 反应器设计选用合适的反应器,如固定床反应器、流化床反应器等。
反应器的设计应满足高温、高压、催化剂的要求。
2. 催化剂选择与制备根据反应条件,选择合适的催化剂。
催化剂的制备方法有浸渍法、溶胶-凝胶法等。
3. 反应条件优化通过实验研究,优化反应温度、压力、催化剂用量等条件,以提高氯化氢的产率和反应速率。
二合一副产蒸汽氯化氢合成炉运行总结

设备 ; 中压 蒸 汽用 于其 他加 热设 备 , 途 更 加 广 泛 。 用 二 合一 副 产蒸 汽合 成 炉利 用氯 气 和氢气 燃 烧 时放 出 的反应 热 , 并将 反 应热 转 变成 中压 蒸汽 。 由运行 结果 可 以看 出 。 合一 副产 蒸 汽炉 具有 明显 的优 越 性 。 二 ( ) 合一 副产 蒸 汽 炉 蒸 汽段 为钢 制 水 冷 壁 炉 I二
第 9期
2 1年 9月 01
中 国氯碱
C i a C l r Al a i hn ho— k l .
No9 . S o. e . 201 1
二合一 副产 蒸汽氯化氢合成炉运行总结
张 同荣 。 柯 曾
( 庆三 阳化 工有 限公 司 , 重 重庆 4 4 0 ) 0 0 0
西 北地 区重 要 的有 色金 属冶 炼精 深 加工产 业 基地 。
甘 肃 民勤 6 0万t / a电石 和
2 o万t 0 / 泥 生产 线 项 目开 工 a水
日前 , 疆 阜 康 市新 引进 的 2 新 6家 企 业 。 大 批 一 工业 项 目集 中开 工 。 近 年来 , 阜康 积极 扶 持发 展 煤 电煤化 工产 业 , 加 速 煤 电煤 化 工产业 间的耦 合 , 动产业 升 级换 代 , 推 涌
Ab t a t T e p o e sf w a d c a a t r t so - n o e h d o h o c a i y t e i u n c i y s r c : h r c s o n h r c e i i ft l sc wo i - n y r c lr cd s n h ss r a e w t b - i f h p o u t se m e e i to u e ,a d i e e i n u r d c ta w r n r d c d n t b n f s a d s mme e e a s n lz d s t y r w r lo a a y e .An h d a c d d te a v n e , e o o c l n r c i a f h c n lg r r v d c n mi a d p a t l et h o o ywe ep o e . a c ot e Ke r s h d o h o ca i ; t a b - r d c; y t e if r a e ywo d : y r c l r c d se m; y p o u t s n h ssu n c i
组合式二合一石墨氯化氢合成炉运行总结

的一次盐 水预 热使 用 。在盐水 预热过 程 中形成 的冷
凝 水返 回纯水 罐 .烧碱蒸 发 工序产 生 的蒸 汽冷 凝 水 也 收集 至 纯水 罐 . 过 纯水 泵供 入 蒸 汽炉 , 而 , 通 从 节
与来 自液化 的尾 氯 ( 度 ≥9 %) 缓 冲罐将 压力 控 纯 O 经 制 为 01— . a 经 流量 计 、 .2 01 MP . 6 调节 阀进入 合成 炉 。 氯 氢 气 体 的配 比严 格 控 制 为 1 0 10 ~ . :.0 . :. 1 0 11 , 0 5 0
hy o e hl r d p r to um m a y dr g n c o i eo e a i n s r
SUN e g i Z n -l
( n nY nynC e cln u t o Ld, y n 6 4 0,hn ) He a o gi h mi d s y . t. aI rC , Wu a g 2 0 C ia 4
体 . 格 的 氯化 氢 气体 一部 分 通 过缓 冲罐 供 给 P C 合 V 转 化 工序 使 用 , 部分 经 一 、 级石 墨 吸 收器 、 一 二 尾气 吸收塔 , 用纯 水 吸 收制备 高纯 盐酸 。 在 开停 机 过程 或生 产不稳 定 阶段 中产生 的不合
后, 若氢气 与 空气混 合 比例不 当 , 生 的爆 炸性 气体 产 致 使石英 灯 头爆裂 , 成设备 损失 , 给系统 生产 带 造 也
s nt ssf r c ; n t p r to ft o e so i z to ; heo r to o d to n l ss y he i u na e i o e a in o pr c s ptmiai n t pe ai n c n ii n a a y i . he he Ke r s y wo d :By r d c ta f r c ; y r g nc l rd y t ss p o e si r v me t o r to umma p o u tse m u na e h d o e h o i e s n he i; r c s mp o e n ; pe ai n s y r
氯化氢合成装置工艺
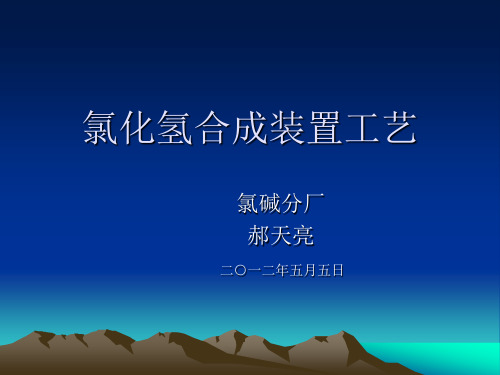
冷却换热块
上气室
下气室
上换热块
石英灯头
冷却换热块
汽包
(二)、降膜吸收器
1、降膜吸收器原理 管内走吸收剂及吸收气体,管间走冷却剂;上
封头内为吸收器头部,内有分布装置,保证吸收剂 均匀地分布到每根吸收管内,并在管内壁形成薄膜 往下流。本设备属湿壁式表面吸收装置,适用于伴 随放热的易溶腐蚀性气体(如HC1,SO2等)的吸 收。操作时吸收剂通过布膜器沿垂直列管内壁以薄 膜状下降,气体自上而下(并流)通过内管空间, 气液两相在流动的液膜上进行传质。列管外通冷却 剂以除去吸收过程中放出的热量 。
(5)点着氢气软管插入灯头氢气管,用铁丝 扎紧。
(6)打开氯气切断阀HV-5458,用手动小阀 缓慢加氯气。观察火焰颜色,待火焰变为青 白色时封炉门。
(7)打开尾气排空,加吸收水。给合成炉提 量至氢气500m³/h,氯气380m³/h左右后等 合成炉升温。
(8)当蒸汽压力并入蒸汽总管后逐步给合成 炉提量。自控阀限位后将手阀开大,改用自 控阀调节。
顶部防爆膜 冷却换热块5个
循环水进口 平衡管
炉门 纯水进口
循环水出口 上气室 蒸汽出口
汽包
下气室 氯化氢出口
上换热块 下换热块
两侧防爆口 上节石墨筒体 中节石墨筒体 下节石墨筒体
视镜
石墨底盘
循环水 冷却水
纯水
冷却水
防爆口
循环水
氯化氢
蒸汽出口 闪蒸罐
纯水
视镜 氯气 氢气
石墨底盘
石墨筒体
下换热块
氯化氢合成装置工艺
氯碱分厂 郝天亮
二○一二年五月五日
讲述内容
1、本装置生产任务及产品简介 2、氯化氢合成的原理 3、工艺流程 4、点炉及停炉步骤 5、主要设备结构及其原理 6、主要控制指标 7、常见事故及处理方法 8、联锁说明 9、应急处理操作
氯化氢合成与吸收工艺设计及运行总结
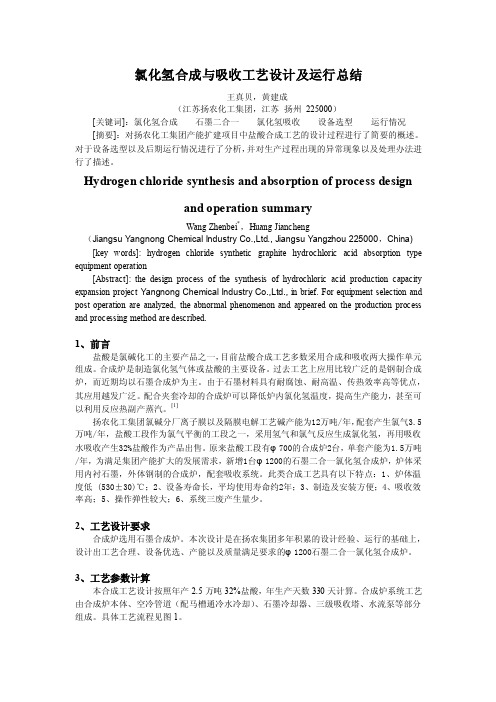
氯化氢合成与吸收工艺设计及运行总结王真贝,黄建成(江苏扬农化工集团,江苏扬州225000)[关键词]:氯化氢合成石墨二合一氯化氢吸收设备选型运行情况[摘要]:对扬农化工集团产能扩建项目中盐酸合成工艺的设计过程进行了简要的概述。
对于设备选型以及后期运行情况进行了分析,并对生产过程出现的异常现象以及处理办法进行了描述。
Hydrogen chloride synthesis and absorption of process designand operation summaryWang Zhenbei*,Huang Jiancheng(Jiangsu Yangnong Chemical Industry Co.,Ltd., Jiangsu Yangzhou 225000,China) [key words]: hydrogen chloride synthetic graphite hydrochloric acid absorption type equipment operation[Abstract]: the design process of the synthesis of hydrochloric acid production capacity expansion project Yangnong Chemical Industry Co.,Ltd., in brief. For equipment selection and post operation are analyzed, the abnormal phenomenon and appeared on the production process and processing method are described.1、前言盐酸是氯碱化工的主要产品之一,目前盐酸合成工艺多数采用合成和吸收两大操作单元组成。
合成炉是制造氯化氢气体或盐酸的主要设备。
氯化氢合成系统技术改造总结
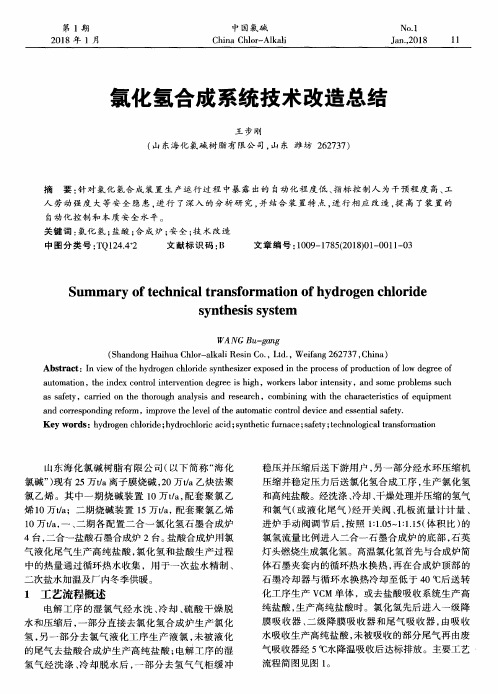
中国氯碱
China Chlor—Alkalj
No.1 Jan.,2018
1 1
氯化 氢 合 成 系统 技 术 改 造总 结
王 步 刚 (山 东海化氯碱 树 脂有 限公 司,山 东 潍坊 262737)
摘 要 :针 对 氯 化 氢 合 成 装 置 生 产 运 行 过 程 中 暴 露 出的 自动 化 程 度 低 、指 标 控 制 人 为 干 预 程 度 高 、工 人 劳动 强度 大 等安 全 隐患 ,进 行 了深入 的分 析研 究 ,并 结合 装 置 特 点 ,进 行 相应 改 造 ,提 高 了装 置 的 自动 化 控 制 和 本 质 安 全 水 平 。 关 键 词 :氯 化 氢 ;盐 酸 ;合 成 炉 ;安 全 ;技 术 改 造 中图分 类 号 :TQ124.4 2 文献标 识 码 :B 文 章编 号 :1009—1785(2Ol8)01—00l1-03
稳压 并 压缩 后 送 下游 用 户 ,另 一部 分 经 水 环压 缩 机 压缩 并 稳 定压 力 后送 氯 化氢 合 成 工 序 ,生 产氯 化 氢 和高 纯盐 酸 。经洗 涤 、冷 却 、干燥 处理并 压缩 的氢 气 和 氯气 (或 液 化 尾 气 )经 开 关 阀 、孔 板 流量 计 计 量 、 进 炉手 动 阀调节 后 ,按 照 1:1.05—1:1.15(体积 比 )的 氯氢 流 量 比例 进 入二 合 一石 墨 合成 炉 的底 部 ,石 英 灯 头燃 烧 生成 氯化氢 。高温氯 化氢 首先 与合 成炉 简 体 石 墨 夹套 内的循 环 热水 换 热 ,再 在 合 成 炉顶 部 的 石墨冷却器与循环水换热冷却至低 于 4O℃后送转 化 工 序 生产 VCM 单 体 ,或 去盐 酸 吸 收 系统 生产 高 纯 盐 酸 ,生产 高 纯 盐 酸时 。氯化 氢 先后 进 入 一 级 降 膜 吸 收器 、二 级 降 膜 吸 收 器 和 尾 气 吸 收 器 ,由 吸 收 水 吸 收 生产 高纯 盐 酸 ,未被 吸收 的部分 尾 气 再 由废 气吸收器经 5℃水降温吸收后达标排放 。主要工艺 流程 简 图见 图 1。
高纯氯化氢气体的制备方法综述
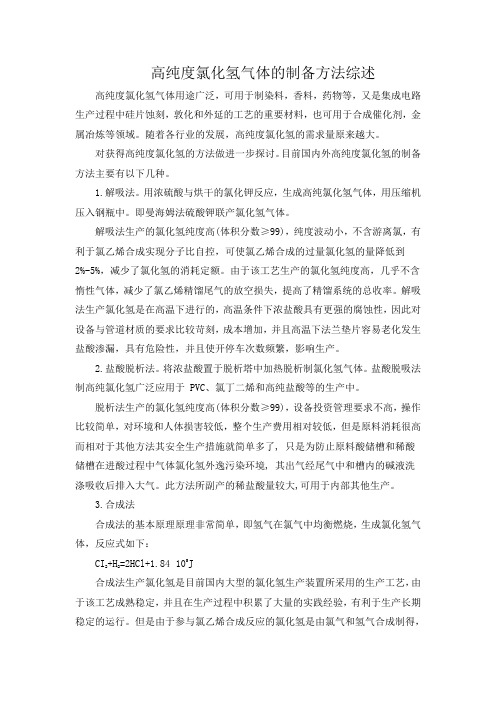
高纯度氯化氢气体的制备方法综述高纯度氯化氢气体用途广泛,可用于制染料,香料,药物等,又是集成电路生产过程中硅片蚀刻,敦化和外延的工艺的重要材料,也可用于合成催化剂,金属冶炼等领域。
随着各行业的发展,高纯度氯化氢的需求量原来越大。
对获得高纯度氯化氢的方法做进一步探讨。
目前国内外高纯度氯化氢的制备方法主要有以下几种。
1.解吸法。
用浓硫酸与烘干的氯化钾反应,生成高纯氯化氢气体,用压缩机压入钢瓶中。
即曼海姆法硫酸钾联产氯化氢气体。
解吸法生产的氯化氢纯度高(体积分数≥99),纯度波动小,不含游离氯,有利于氯乙烯合成实现分子比自控,可使氯乙烯合成的过量氯化氢的量降低到2%-5%,减少了氯化氢的消耗定额。
由于该工艺生产的氯化氢纯度高,几乎不含惰性气体,减少了氯乙烯精馏尾气的放空损失,提高了精馏系统的总收率。
解吸法生产氯化氢是在高温下进行的,高温条件下浓盐酸具有更强的腐蚀性,因此对设备与管道材质的要求比较苛刻,成本增加,并且高温下法兰垫片容易老化发生盐酸渗漏,具有危险性,并且使开停车次数频繁,影响生产。
2.盐酸脱析法。
将浓盐酸置于脱析塔中加热脱析制氯化氢气体。
盐酸脱吸法制高纯氯化氢广泛应用于 PVC、氯丁二烯和高纯盐酸等的生产中。
脱析法生产的氯化氢纯度高(体积分数≥99),设备投资管理要求不高,操作比较简单,对环境和人体损害较低,整个生产费用相对较低,但是原料消耗很高而相对于其他方法其安全生产措施就简单多了, 只是为防止原料酸储槽和稀酸储槽在进酸过程中气体氯化氢外逸污染环境, 其出气经尾气中和槽内的碱液洗涤吸收后排入大气。
此方法所副产的稀盐酸量较大,可用于内部其他生产。
3.合成法合成法的基本原理原理非常简单,即氢气在氯气中均衡燃烧,生成氯化氢气体,反应式如下:CI2+H2=2HCl+1.84×105J合成法生产氯化氢是目前国内大型的氯化氢生产装置所采用的生产工艺,由于该工艺成熟稳定,并且在生产过程中积累了大量的实践经验,有利于生产长期稳定的运行。
- 1、下载文档前请自行甄别文档内容的完整性,平台不提供额外的编辑、内容补充、找答案等附加服务。
- 2、"仅部分预览"的文档,不可在线预览部分如存在完整性等问题,可反馈申请退款(可完整预览的文档不适用该条件!)。
- 3、如文档侵犯您的权益,请联系客服反馈,我们会尽快为您处理(人工客服工作时间:9:00-18:30)。
氯化氢合成与吸收工艺设计及运行总结王真贝,黄建成(江苏扬农化工集团,江苏扬州225000)[关键词]:氯化氢合成石墨二合一氯化氢吸收设备选型运行情况[摘要]:对扬农化工集团产能扩建项目中盐酸合成工艺的设计过程进行了简要的概述。
对于设备选型以及后期运行情况进行了分析,并对生产过程出现的异常现象以及处理办法进行了描述。
Hydrogen chloride synthesis and absorption of process designand operation summaryWang Zhenbei*,Huang Jiancheng(Jiangsu Yangnong Chemical Industry Co.,Ltd., Jiangsu Yangzhou 225000,China) [key words]: hydrogen chloride synthetic graphite hydrochloric acid absorption type equipment operation[Abstract]: the design process of the synthesis of hydrochloric acid production capacity expansion project Yangnong Chemical Industry Co.,Ltd., in brief. For equipment selection and post operation are analyzed, the abnormal phenomenon and appeared on the production process and processing method are described.1、前言盐酸是氯碱化工的主要产品之一,目前盐酸合成工艺多数采用合成和吸收两大操作单元组成。
合成炉是制造氯化氢气体或盐酸的主要设备。
过去工艺上应用比较广泛的是钢制合成炉,而近期均以石墨合成炉为主。
由于石墨材料具有耐腐蚀、耐高温、传热效率高等优点,其应用越发广泛。
配合夹套冷却的合成炉可以降低炉内氯化氢温度,提高生产能力,甚至可以利用反应热副产蒸汽。
[1]扬农化工集团氯碱分厂离子膜以及隔膜电解工艺碱产能为12万吨/年,配套产生氯气3.5万吨/年,盐酸工段作为氯气平衡的工段之一,采用氢气和氯气反应生成氯化氢,再用吸收水吸收产生32%盐酸作为产品出售。
原来盐酸工段有φ700的合成炉2台,单套产能为1.5万吨/年,为满足集团产能扩大的发展需求,新增1台φ1200的石墨二合一氯化氢合成炉,炉体采用内衬石墨,外体钢制的合成炉,配套吸收系统。
此类合成工艺具有以下特点:1、炉体温度低 (530±30)℃;2、设备寿命长,平均使用寿命约2年;3、制造及安装方便;4、吸收效率高;5、操作弹性较大;6、系统三废产生量少。
2、工艺设计要求合成炉选用石墨合成炉。
本次设计是在扬农集团多年积累的设计经验、运行的基础上,设计出工艺合理、设备优选、产能以及质量满足要求的φ1200石墨二合一氯化氢合成炉。
3、工艺参数计算本合成工艺设计按照年产2.5万吨32%盐酸,年生产天数330天计算。
合成炉系统工艺由合成炉本体、空冷管道(配马槽通冷水冷却)、石墨冷却器、三级吸收塔、水流泵等部分组成。
具体工艺流程见图1。
图1 盐酸合成工艺流程图3.1合成系统计算3.1.1合成炉燃烧体积计算合成工艺采用合成炉作为氯气和氢气反应的场所,本次设计合成炉是石墨二合一合成炉,采用三层灯头,氯气从中间进入,氢气从二层进入,氢气包裹着氯气安静燃烧,最外围一层淌冷凝酸,那么选取合适的燃烧容积V是保证炉内氯气和氢气混合、燃烧状态良好、火焰垂直向上无散射、无偏烧的先决条件。
根据扬农化工集团φ700合成炉设计的成功经验。
合成炉生产强度取55~95kg(m3·h)为宜,本次设计取90kg/(m3·h)。
经计算单台合成炉燃烧容积y取11.1m3。
[2]3.1.2合成炉炉体换热面积计算合成炉内,氯气和氢气反应生成氯化氢气体,该反应为放热反应,为促进反应向正方向进行,必须及时移出反应热,同时保证生产的安全稳定。
散热面积采用下式计算:S=Q/K△£R,式中:S为散热面积,m2;K为传热系数,kJ/(m2·h·℃);Q为反应总热量,kJ/h;R 为修正系数;△£为平均温差,℃。
根据计算,总移出热量Q=229.56kj/s,总传热系数K=14.58w/m2·℃,平均温差△£=475℃,修正系数R=1.35,经计算的S为44.8m2。
3.1.3合成炉其它参数选取炉体结构为圆柱体。
炉体内直径为1.2m,外直径为1.6m,高为20m。
灯头:气体3层分布,内为φ100管(氯),外中φ125管(氢),炉内上升速度:0 120m/s,工作炉温:(570±20)℃,炉压:101.3kPa,校核后,取炉体体积V=11.3m3,炉体换热面积S=68.3m2。
3.1.3冷却器选型氯化氢气体经冷却后(≤108℃),在含有水的情况下,生成盐酸具有强腐蚀性。
因此冷却器选择材质为石墨,顾及系统压降及安全选择石墨径向式园块孔冷却器同时它能经受更大压力的冲击,更能耐高温而不易损坏。
按照冷却器气相进口温度为150℃,出口温度为40℃,冷却水进水温度30℃,出水温度33℃计算,冷凝器总传热系数为2400Kj/hr·m2·℃,冷却负荷为4899814.205Kj/d,冷凝器面积要求为32.59m2,圆整后为33m2,选型JXZ-03。
3.2吸收系统计算3.2.1 吸收塔塔径选取经计算,吸收系统混合气体体积流量为17489.6618m3/d,液相体积流量为50.94412m3/d,填料选取25mm*25mm*2.5mm的瓷质拉西环以乱堆方式填充。
经计算及查乱堆填料泛点线得出泛点气速umax=1.6m/s,空塔气速的适宜值取泛点气速的60%~80%,本设计取u=1.05m/s 作为设计气速,计算圆整后,塔径取0.7m。
3.2.2 吸收塔填料高度选取工作温度选取30℃,对气相传质系数kyα=0.0116kmol/(m3·s),液相传质系数k Lα=0.6732kmol/(m3·s),总传质系数K Yα=0.01069kmol/(m3·s),惰性气体流量V=2085.8925kg/d,溶剂流量L=5044.119kg/d,塔截面积Ω=0.1923m2。
通过计算得出传质单元高度为0.4027m,传质单元数为7.37,修正系数取1.5,实装填料高度取4.45m,分三级吸收塔安装。
[3]3.2.3合成一级吸收塔选型盐酸具有强腐蚀性,径向园块孔降膜吸收塔具有耐冲击,压降小,换热效果好等优点,故选择石墨径向式园块孔降膜吸收塔。
按照吸收塔气相进口温度为40℃,出口温度为40℃,冷却水进水温度30℃,出水温度35℃,淌酸温度45℃,进酸质量分数12.8%,淌酸质量分数32%计算,吸收塔总传热系数为2637.81Kj/hr·m2·℃,冷却负荷为26457407.5Kj/d,冷凝器面积要求为33.89m2,圆整后为35m2,选型MS-07,吸收效率折合拉西环填料高度2.78m。
3.2.4合成二级吸收塔选型塔类型选择同合成一级吸收塔,按照吸收塔气相进口温度为40℃,出口温度为30℃,冷却水进水温度35℃,出水温度40℃,淌酸温度45℃,进酸质量分数2.2%,淌酸质量分数12.8%计算,吸收塔总传热系数为2637.81Kj/hr·m2·℃,冷却负荷为13205209.99Kj/d,冷凝器面积要求为28.9m2,圆整后为30m2,选型MS-06,吸收效率折合拉西环填料高度1.47m。
3.2.5合成三级吸收塔选型按照吸收塔气相进口温度为30℃,出口温度为27℃,淌酸温度32℃,进酸质量分数0%,淌酸质量分数 2.2%,以乱推拉西环填料计算,溶剂流量L=5044.119kg/d,塔截面积Ω=0.1923m2。
通过计算得出传质单元高度为0.4027m,传质单元数为0.5,修正系数取1.5,实装填料高度取0.31m。
4、结论与讨论4.1 运行总结2012年7月14日,合成炉点火成功,经过一系列调试,各项运行指标达到了设计要求:氯化氢体积分数为86.5%~92%,无游离氯;炉压为0.02~0.03MPa;氯化氢出口温度为45~55℃;吸收水转子流量控制范围在0.5m3/h~1.4m3/h;高纯酸比重在1.158~1.160kg/m3,对应的酸浓度为31~32%。
对比之前使用的铁质合成炉,石墨二合一合成炉具有以下优点:1、石墨材料耐腐性强,使用过程炉体腐蚀小,使用至今没有发现炉体有腐蚀现象,使用周期较铁质合成炉长;2、生产负荷高,产能大,炉体采用夹套水冷却,冷却效果好,可调控空间大,降低后续吸收系统冷却负荷,查看过去生产记录,目前该合成炉的日产量相当于过去使用的同规格铁制合成炉1.5倍以上;3、成品酸质量提高,产出氯化氢中含铁量低,产酸质量达标率高,目前生产的高纯酸质量分数为31.2%~32.2%,含Ca2++Mg2+≤200PPm,Fe3+≤500PPm。
4、炉体带有夹套水冷却,内衬石墨,外用钢材,导热效果好,且防腐蚀不易漏,无高温辐射,安全稳定,工作环境得到明显改善。
4.2 存在问题1、开车初期,由于合成炉进气量大,炉头火焰观察困难,控制进气H2:Cl2=1.15:1较难,容易过氯,造成氯化氢的游离氯在瞬间超标,影响了正常以及操作;2、开车点火后,塔内炉压容易偏高,导致易熄火的现象,经过逐一排查的办法,发现水流泵抽力较低,如果系统压力有波动,易导致炉内压力高;3、停车,抽真空,正常检修过程中,出现防爆膜爆裂现象,经过检查发现观察炉火的视镜出漏真空的现象,同时检查炉顶的防爆膜,由于采用利旧的防爆膜,出现了老化的现象;4、三级吸收塔淌酸管道存在淌酸不畅现象,同时易发生爆鸣,经过检查发现三级吸收塔淌酸管道液封前走向有一定的上扬,导致管内气体难以排出,产生酸封气以及爆鸣的现象。
4.3 整改措施1、清理观察视镜,方便观察。
对氯气进气管道孔板流量计重新核查,由于孔板流量计孔径大小选择偏大,导致流量系数C0变大,同时孔截面积A0增加,导致按照压差调节时精度降低,控制过程容易产生偏差,导致过氯现象。
针对现有工况对孔板流量计的孔径重新计算选型,通过计算,将孔板内径由原来的Φ50mm调整到Φ45mm,再根据压力、温度等条件计算孔板流量计出对应刻度的摩尔数,并对三班员工进行培训,严格控制进气比在技控点要求范围内;2、对水流泵的抽力进行重新计算确定,更换水流泵由原来的配套金属水流泵更换为四氟水流泵,对于看开车点火前水流泵的运行操作进行规范,针对此合成炉的特点,调整炉压技控点指标,保证炉内压力在合理的技控点指标内;3、对炉头观察炉火的视镜进行紧固,对炉内防爆压力进行核算,选定适宜规格的防爆膜并更换,制定定期工作,增加防爆膜处的巡回点;4、对液封前的管路进行调整,将原来的上扬趋势改为有一定的向下倾斜趋势,利于将淌酸夹带的气体排回吸收塔,消除淌酸不畅以及爆鸣等安全隐患。