深部金属矿山岩爆监测、预警和控制
“深部重大工程灾害的孕育演化机制与动态调控理论”立项报告
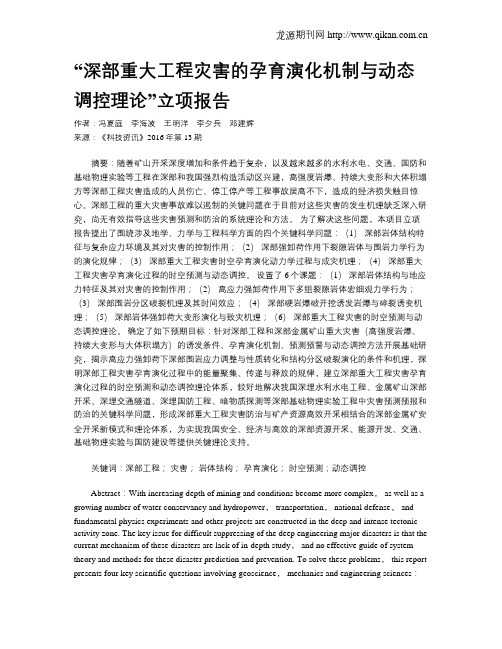
“深部重大工程灾害的孕育演化机制与动态调控理论”立项报告作者:冯夏庭李海波王明洋李夕兵邓建辉来源:《科技资讯》2016年第13期摘要:随着矿山开采深度增加和条件趋于复杂,以及越来越多的水利水电、交通、国防和基础物理实验等工程在深部和我国强烈构造活动区兴建,高强度岩爆、持续大变形和大体积塌方等深部工程灾害造成的人员伤亡、停工停产等工程事故居高不下,造成的经济损失触目惊心。
深部工程的重大灾害事故难以遏制的关键问题在于目前对这些灾害的发生机理缺乏深入研究,尚无有效指导这些灾害预测和防治的系统理论和方法。
为了解决这些问题,本项目立项报告提出了围绕涉及地学、力学与工程科学方面的四个关键科学问题:(1)深部岩体结构特征与复杂应力环境及其对灾害的控制作用;(2)深部强卸荷作用下裂隙岩体与围岩力学行为的演化规律;(3)深部重大工程灾害时空孕育演化动力学过程与成灾机理;(4)深部重大工程灾害孕育演化过程的时空预测与动态调控。
设置了6个课题:(1)深部岩体结构与地应力特征及其对灾害的控制作用;(2)高应力强卸荷作用下多组裂隙岩体宏细观力学行为;(3)深部围岩分区破裂机理及其时间效应;(4)深部硬岩爆破开挖诱发岩爆与碎裂诱变机理;(5)深部岩体强卸荷大变形演化与致灾机理;(6)深部重大工程灾害的时空预测与动态调控理论。
确定了如下预期目标:针对深部工程和深部金属矿山重大灾害(高强度岩爆、持续大变形与大体积塌方)的诱发条件、孕育演化机制、预测预警与动态调控方法开展基础研究,揭示高应力强卸荷下深部围岩应力调整与性质转化和结构分区破裂演化的条件和机理,探明深部工程灾害孕育演化过程中的能量聚集、传递与释放的规律,建立深部重大工程灾害孕育演化过程的时空预测和动态调控理论体系,较好地解决我国深埋水利水电工程、金属矿山深部开采、深埋交通隧道、深埋国防工程、暗物质探测等深部基础物理实验工程中灾害预测预报和防治的关键科学问题,形成深部重大工程灾害防治与矿产资源高效开采相结合的深部金属矿安全开采新模式和理论体系,为实现我国安全、经济与高效的深部资源开采、能源开发、交通、基础物理实验与国防建设等提供关键理论支持。
金属矿山矿体围岩工程地质勘察在生产中的作用

( )采场充填体压坏开裂; 8 ( )采场侧壁脱层开裂 。 9
( C
32 影 响 因素 .
顶板管理 ,地质构造、岩体工程 地质条件 、岩体结构及
其 稳 定 性 , 空 区及 空 区群 , 断 层 ,原 岩 应 力 场 ,岩 爆 和
地震活动等七类 。
图 1 各 种 断 面 的胴 体 应 力 状 态比 较
【 摘 要 】广 西高峰矿业有 限责任公 司是一 家有 色金属采选为主 的矿 业企业 ,位 于广西南丹县 大厂镇 ,随着矿 山采矿的深
入 ,高峰 公 司随着开采深度 的增加 ,深部 矿岩体 内部的应力越来越大 ,岩体弹性势 能释放和开裂破坏 比较普遍 ,地压活动破 坏、 地震扰动破坏和 生产破坏越 来越严 重 ,给生产安全带 来不利 的影响 。通过在 高峰 深部 矿岩体进行 广泛的工程地质调查 ,对 井下
1 工程地质概况
高峰矿 田主要位 于广 西西北部 ,含矿地层 主要 由泥盆系
中部、一 3 19南部、- 5 、- 6 、一 7 、一 0 1 1 16 17 2 0北部 ) ,特 别是 在一 5 1 1及其下部 区域 ,矿岩整体性差且节理裂隙发育,多数 区域较破碎 ,部分区域极破碎 。
( )O组成 的,矿井深度 9 0多米 ,矿井采 用竖井 、斜井 、 系 0 盲斜井 、斜 坡道联合 开拓 ,随着 开采深度 的增 加,井下矿岩
【 稿 日期 】2 1 — 0 2 收 0 1 1— 4
围岩应力是初始应力在巷道周 围的重新分布 ,所 以初始 应 力状态对洞体应力重新分布起主导作用。地应 力主要 由岩 石 自重应力场构成 ,这时铅直应力为最大应力,而水平应力 很小。采场巷道 由于这种铅直受力条件 ( 1 图 )理论上在拱 顶及洞底可能 出现拉应力区 ( L’号表示 ) ,在拱脚及洞脚部
矿山地质灾害的主要类型分析
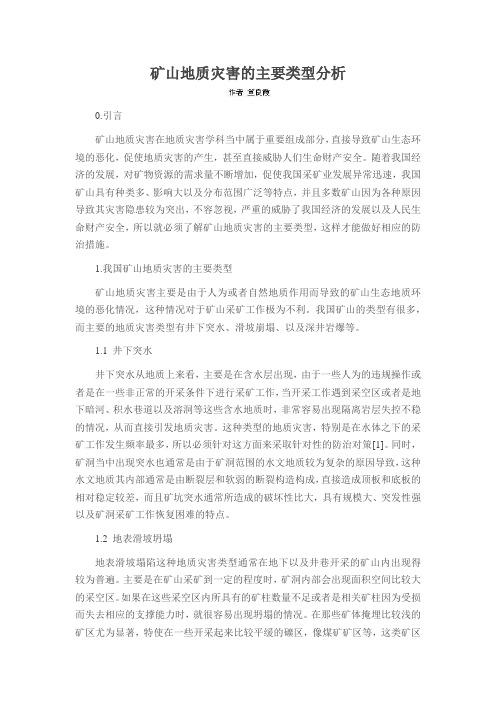
矿山地质灾害的主要类型分析0.引言矿山地质灾害在地质灾害学科当中属于重要组成部分,直接导致矿山生态环境的恶化,促使地质灾害的产生,甚至直接威胁人们生命财产安全。
随着我国经济的发展,对矿物资源的需求量不断增加,促使我国采矿业发展异常迅速,我国矿山具有种类多、影响大以及分布范围广泛等特点,并且多数矿山因为各种原因导致其灾害隐患较为突出,不容忽视,严重的威胁了我国经济的发展以及人民生命财产安全,所以就必须了解矿山地质灾害的主要类型,这样才能做好相应的防治措施。
1.我国矿山地质灾害的主要类型矿山地质灾害主要是由于人为或者自然地质作用而导致的矿山生态地质环境的恶化情况,这种情况对于矿山采矿工作极为不利。
我国矿山的类型有很多,而主要的地质灾害类型有井下突水、滑坡崩塌、以及深井岩爆等。
1.1 井下突水井下突水从地质上来看,主要是在含水层出现,由于一些人为的违规操作或者是在一些非正常的开采条件下进行采矿工作,当开采工作遇到采空区或者是地下暗河、积水巷道以及溶洞等这些含水地质时,非常容易出现隔离岩层失控不稳的情况,从而直接引发地质灾害。
这种类型的地质灾害,特别是在水体之下的采矿工作发生频率最多,所以必须针对这方面来采取针对性的防治对策[1]。
同时,矿洞当中出现突水也通常是由于矿洞范围的水文地质较为复杂的原因导致,这种水文地质其内部通常是由断裂层和软弱的断裂构造构成,直接造成顶板和底板的相对稳定较差,而且矿坑突水通常所造成的破坏性比大,具有规模大、突发性强以及矿洞采矿工作恢复困难的特点。
1.2 地表滑坡坍塌地表滑坡塌陷这种地质灾害类型通常在地下以及井巷开采的矿山内出现得较为普遍。
主要是在矿山采矿到一定的程度时,矿洞内部会出现面积空间比较大的采空区。
如果在这些采空区内所具有的矿柱数量不足或者是相关矿柱因为受损而失去相应的支撑能力时,就很容易出现坍塌的情况。
在那些矿体掩埋比较浅的矿区尤为显著,特使在一些开采起来比较平缓的礦区,像煤矿矿区等,这类矿区出现地面塌陷的情况更为普遍。
深部开采矿山岩爆倾向性研究
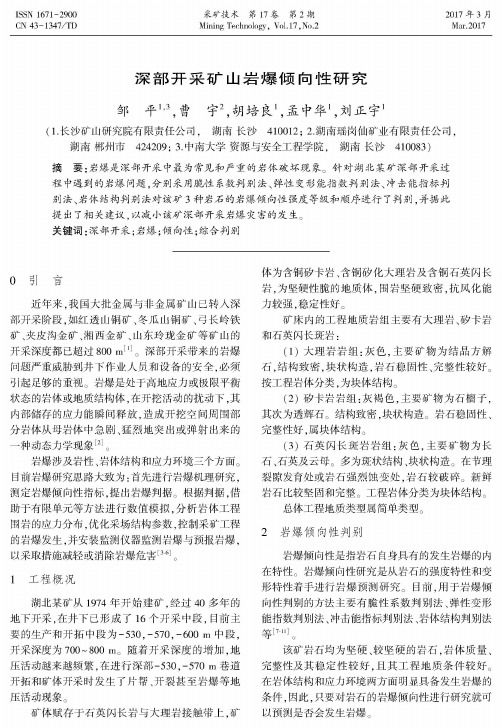
ISSN 1671-2900CN 43-1347/TD采矿技术第17卷第2期Mining Technology, Vol. 17,No.22017年3月Mar.2017深部开采矿山岩爆倾向性研究邹平1,3,曹宇2,胡培良!,孟中华刘正宇1(1.长沙矿山研究院有限责任公司,湖南长沙410012; 2.湖南瑶岗仙矿业有限责任公司,湖南郴州市424209; 3.中南大学资源与安全工程学院,湖南长沙410083)摘要:岩爆是深部开采中最为常见和严重的岩体破坏现象。
针对湖北某矿深部开采过 程中遇到的岩爆问题,分别采用脆性系数判别法、弹性变形能指数判别法、冲击能指标判 别法、岩体结构判别法对该矿3种岩石的岩爆倾向性强度等级和顺序进行了判别,并据此 提出了相关建议,以减小该矿深部开采岩爆灾害的发生。
关键词:深部开采;岩爆;倾向性;综合判别0引百近年来,我国大批金属与非金属矿山已转人深 部开采阶段,如红透山铜矿、冬瓜山铜矿、弓长岭铁 矿、夹皮沟金矿、湘西金矿、山东玲珑金矿等矿山的 开采深度都已超过800 m[l]。
深部开采带来的岩爆 问题严重威胁到井下作业人员和设备的安全,必须 引起足够的重视。
岩爆是处于高地应力或极限平衡 状态的岩体或地质结构体,在开挖活动的扰动下,其 内部储存的应力能瞬间释放,造成开挖空间周围部 分岩体从母岩体中急剧、猛烈地突出或弹射出来的 一种动态力学现象[2]。
岩爆涉及岩性、岩体结构和应力环境三个方面。
目前岩爆研究思路大致为:首先进行岩爆机理研究, 测定岩爆倾向性指标,提出岩爆判据。
根据判据,借 助于有限单元等方法进行数值模拟,分析岩体工程 围岩的应力分布,优化采场结构参数,控制采矿工程 的岩爆发生,并安装监测仪器监测岩爆与预报岩爆, 以采取措施减轻或消除岩爆危害[36]。
1工程概况湖北某矿从1974年开始建矿,经过40多年的 地下开采,在井下已形成了 16个开采中段,目前主 要的生产和开拓中段为-530,-570,-600 m中段,开采深度为700〜800 m。
深部重大工程灾害的孕育演化机制与动态调控理论
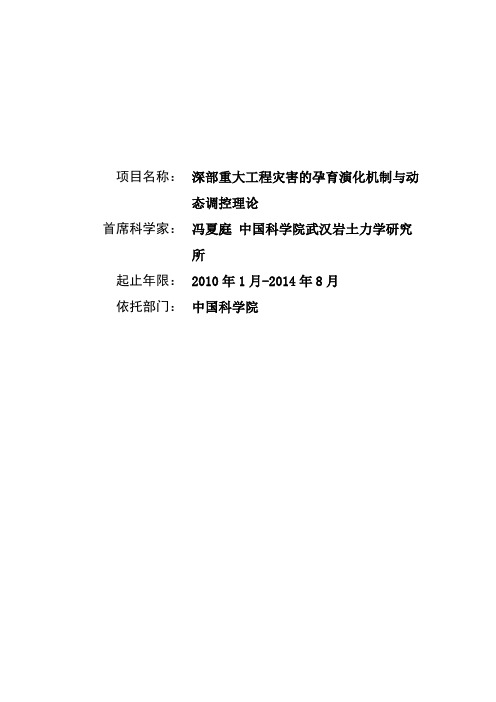
项目名称:深部重大工程灾害的孕育演化机制与动态调控理论首席科学家:冯夏庭中国科学院武汉岩土力学研究所起止年限:2010年1月-2014年8月依托部门:中国科学院一、研究内容1、拟解决的关键科学问题根据国家重大需求、国际科学前沿和国内外研究现状,本项目紧密围绕深部重大工程灾害的孕育演化机制与动态调控理论的基础研究,从多学科交叉的视角,凝练出拟解决的四个关键科学问题。
科学问题一:深部岩体结构与地应力特征及其对灾害的控制作用深部岩体的物质性、结构性及赋存性是有别于其它材料的本质特征。
深部岩体的“三性”及其相互关系是控制深部工程灾害的关键因素。
就“物质性”而言,本项目的研究对象是深部硬岩;就“结构性”而言,深部工程岩体结构和地质缺陷具有高度的隐蔽性、不确定性和时空变异性。
因此,如何识别深部岩体的地质特征成为需要研究的首要关键问题,比如,如何采用弹性波正反演理论、瞬变电磁波反演理论以及这两种方法的综合方法,解译并识别岩体结构及相关构造,等等。
为合理表征岩体结构特征,需要综合深部岩体探测结果与基于围岩表面岩体结构精确测量结果,建立考虑体积密度、空间RQD和几何分布特征的三维岩体结构参数化模型。
同时,需要研究高应力强卸荷作用下岩体结构时空演化规律、岩体力学行为的结构控制、结构与应力协调控制和结构控制转化为应力控制的机制、条件和模型。
针对深部岩体的“赋存性”,需要研究岩体复杂的应力环境特征及高精度的测试方法;重点需要揭示具有强烈构造活动特征的工程区地应力场形成机制,建立考虑强烈构造活动和复杂地形地貌形成过程以及非线性边界条件的深部长大工程区三维地应力场反演理论;需要研究高应力强卸荷作用下深部工程围岩应力场演化过程的分析方法,建立典型深埋长大工程区的三维地应力场形成与开挖扰动引起的演化模型。
本科学问题的研究为深部重大工程灾害的孕育演化机制、时空预测与调控理论研究提供必要的地质模型、应力模型及其相关数据。
科学问题二:深部强卸荷作用下裂隙岩体与围岩力学行为的演化规律考察岩体有三个基本视角:地质属性、力学行为和工程性质。
岩爆形成条件,预测预报与防治
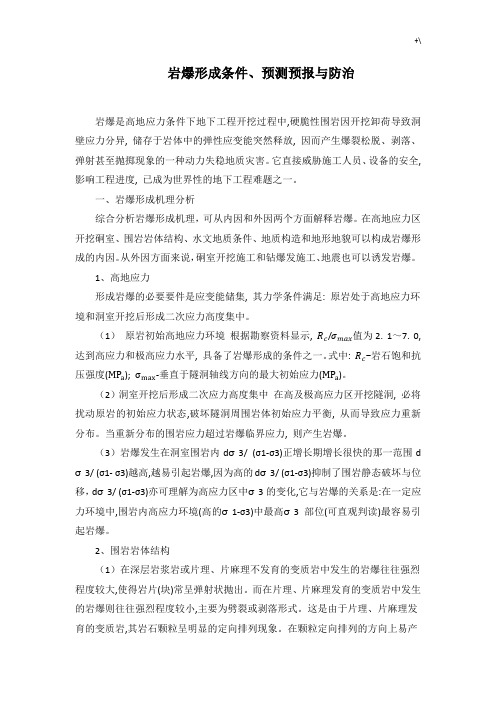
岩爆形成条件、预测预报与防治岩爆是高地应力条件下地下工程开挖过程中,硬脆性围岩因开挖卸荷导致洞壁应力分异, 储存于岩体中的弹性应变能突然释放, 因而产生爆裂松脱、剥落、弹射甚至抛掷现象的一种动力失稳地质灾害。
它直接威胁施工人员、设备的安全, 影响工程进度, 已成为世界性的地下工程难题之一。
一、岩爆形成机理分析综合分析岩爆形成机理,可从内因和外因两个方面解释岩爆。
在高地应力区开挖硐室、围岩岩体结构、水文地质条件、地质构造和地形地貌可以构成岩爆形成的内因。
从外因方面来说,硐室开挖施工和钻爆发施工、地震也可以诱发岩爆。
1、高地应力形成岩爆的必要要件是应变能储集, 其力学条件满足: 原岩处于高地应力环境和洞室开挖后形成二次应力高度集中。
(1)原岩初始高地应力环境根据勘察资料显示, /值为2. 1~7. 0, 达到高应力和极高应力水平, 具备了岩爆形成的条件之一。
式中: -岩石饱和抗压强度(); -垂直于隧洞轴线方向的最大初始应力()。
(2)洞室开挖后形成二次应力高度集中在高及极高应力区开挖隧洞, 必将扰动原岩的初始应力状态,破坏隧洞周围岩体初始应力平衡, 从而导致应力重新分布。
当重新分布的围岩应力超过岩爆临界应力, 则产生岩爆。
(3)岩爆发生在洞室围岩内dσ3/ (σ1-σ3)正增长期增长很快的那一范围d σ3/ (σ1- σ3)越高,越易引起岩爆,因为高的dσ3/ (σ1-σ3)抑制了围岩静态破坏与位移,dσ3/ (σ1-σ3)亦可理解为高应力区中σ3的变化,它与岩爆的关系是:在一定应力环境中,围岩内高应力环境(高的σ1-σ3)中最高σ3部位(可直观判读)最容易引起岩爆。
2、围岩岩体结构(1)在深层岩浆岩或片理、片麻理不发育的变质岩中发生的岩爆往往强烈程度较大,使得岩片(块)常呈弹射状抛出。
而在片理、片麻理发育的变质岩中发生的岩爆则往往强烈程度较小,主要为劈裂或剥落形式。
这是由于片理、片麻理发育的变质岩,其岩石颗粒呈明显的定向排列现象。
深部矿岩岩爆倾向性评估方法及支护建议
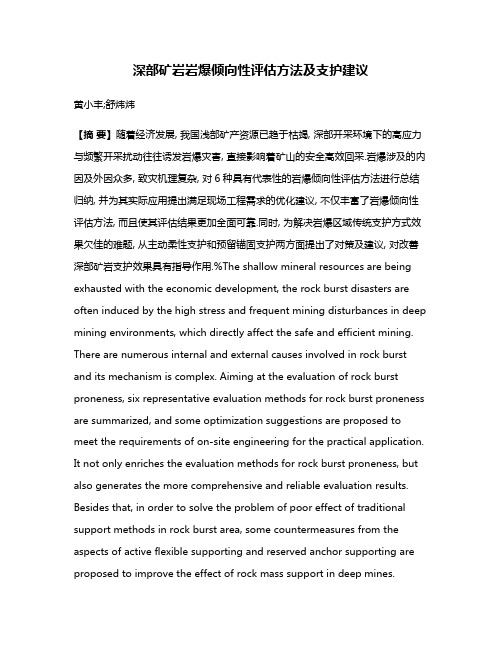
深部矿岩岩爆倾向性评估方法及支护建议黄小丰;舒炜炜【摘要】随着经济发展, 我国浅部矿产资源已趋于枯竭, 深部开采环境下的高应力与频繁开采扰动往往诱发岩爆灾害, 直接影响着矿山的安全高效回采.岩爆涉及的内因及外因众多, 致灾机理复杂, 对6种具有代表性的岩爆倾向性评估方法进行总结归纳, 并为其实际应用提出满足现场工程需求的优化建议, 不仅丰富了岩爆倾向性评估方法, 而且使其评估结果更加全面可靠.同时, 为解决岩爆区域传统支护方式效果欠佳的难题, 从主动柔性支护和预留锚固支护两方面提出了对策及建议, 对改善深部矿岩支护效果具有指导作用.%The shallow mineral resources are being exhausted with the economic development, the rock burst disasters are often induced by the high stress and frequent mining disturbances in deep mining environments, which directly affect the safe and efficient mining. There are numerous internal and external causes involved in rock burst and its mechanism is complex. Aiming at the evaluation of rock burst proneness, six representative evaluation methods for rock burst proneness are summarized, and some optimization suggestions are proposed to meet the requirements of on-site engineering for the practical application. It not only enriches the evaluation methods for rock burst proneness, but also generates the more comprehensive and reliable evaluation results. Besides that, in order to solve the problem of poor effect of traditional support methods in rock burst area, some countermeasures from the aspects of active flexible supporting and reserved anchor supporting are proposed to improve the effect of rock mass support in deep mines.【期刊名称】《现代矿业》【年(卷),期】2018(000)012【总页数】4页(P32-34,40)【关键词】深部开采;岩爆;倾向性评估;岩体支护【作者】黄小丰;舒炜炜【作者单位】湖南辰州矿业有限责任公司;中南大学资源与安全工程学院【正文语种】中文矿产资源作为国家经济发展的基本保障,其浅部资源已经趋于枯竭,大量矿井逐渐向深部延伸。
矿山安全监测与预警技术

故发生,保障工作人员的生命安全。
02
提高矿山生产效率
通过监测设备对矿山环境和工作状态的实时监控,可以及时发现设备故
障或生产异常,及时采取措施进行修复和调整,提高生产效率。
03
促进矿山可持续发展
矿山安全监测技术的推广和应用,有助于提高矿山安全管理水平,促进
矿山的可持续发展。
矿山安全监测技术的发展历程
矿压监测是矿山安全监测的重要环节 ,主要监测矿山压力的变化情况,预 防因矿压异常导致的安全事故。
矿压监测系统由传感器、数据采集器 、传输设备和监控中心组成,能够实 现数据的实时传输和处理,为矿山安 全生产提供有力保障。
矿压监测方法
包括应力监测、位移监测和声发射监 测等,通过安装传感器和数据采集系 统,实时监测矿山岩体的应力状态和 变形情况。
04
矿山安全预警技术应用
基于数据挖掘的预警模型
数据挖掘技术
通过分析历史数据,发现数据中 的模式和规律,用于预测未来的 矿山安全状况。
预警模型应用
基于数据挖掘的预警模型能够实 时监测矿山环境、设备运行状况 等数据,及时发现异常情况并发 出预警。
优势与局限
数据挖掘技术能够处理大量数据 ,发现潜在的安全风险,但需要 足够的历史数据支持,且对数据 质量要求较高。
矿山安全监测的常用方法
传感器监测法
视频监控法
通过在矿山关键部位安装传感器,实时监 测矿山的温度、湿度、压力、气体浓度等 参数,实现数据的实时采集和传输。
通过在矿山上安装摄像头,对矿山工作区 域进行实时监控,可以直观地观察到工作 人员的工作状态和矿山的整体情况。
雷达监测法
无线传感器网络法
利用雷达技术对矿山周边环境和设备进行 监测,可以实现对人员和车辆的定位和跟 踪。
- 1、下载文档前请自行甄别文档内容的完整性,平台不提供额外的编辑、内容补充、找答案等附加服务。
- 2、"仅部分预览"的文档,不可在线预览部分如存在完整性等问题,可反馈申请退款(可完整预览的文档不适用该条件!)。
- 3、如文档侵犯您的权益,请联系客服反馈,我们会尽快为您处理(人工客服工作时间:9:00-18:30)。
Engineering 3 (2017) 538–545ResearchEfficient Exploitation of Deep Mineral Resources—ReviewMonitoring, Warning, and Control of Rockburst in Deep Metal MinesXia-Ting Feng a ,b ,*, Jianpo Liu a , Bingrui Chen b , Yaxun Xiao b , Guangliang Feng b , Fengpeng Zhang aa Key Laboratory of Ministry of Education on Safe Mining of Deep Metal Mines, Northeastern University, Shenyang 110819, ChinabState Key Laboratory of Geomechanics and Geotechnical Engineering, Institute of Rock and Soil Mechanics, Chinese Academy of Sciences, Wuhan 430071, Chinaa r t i c l e i n f oa b s t r a c tArticle history:Received 6 July 2017Revised 13 July 2017Accepted 14 July 2017Available online 16 August 2017This paper reviews the recent achievements made by our team in the mitigation of rockburst risk. It includes the development of neural network modeling on rockburst risk assessment for deep gold mines in South Af-rica, an intelligent microseismicity monitoring system and sensors, an understanding of the rockburst evo-lution process using laboratory and in situ tests and monitoring, the establishment of a quantitative warning method for the location and intensities of different types of rockburst, and the development of measures for the dynamic control of rockburst. The mitigation of rockburst at the Hongtoushan copper mine is presented as an illustrative example.© 2017 THE AUTHORS. Published by Elsevier LTD on behalf of the Chinese Academy of Engineering andHigher Education Press Limited Company. This is an open access article under the CC BY-NC-NDlicense (/licenses/by-nc-nd/4.0/).Keywords:Deep metal mining Rockburst Monitoring Warning Mitigation1. IntroductionDue to an increasing demand for mineral resources in China, numerous metal mines, such as the Hongtoushan copper mine, the Dongguashan copper mine, the Jiapigou gold mine, the Sanshandao gold mine, the Fankou lead-zinc mine, the Linglong gold mine, and so forth, have operated at depths exceeding 1000 m [1]. Deep min-ing inevitably creates an increase in and concentration of ground stress, and the maximum principal stress in the deep stope of some metal mines can exceed 50 MPa [2]. Under these conditions, the incidences of dynamic failures such as rockburst have rapidly in-creased in recent years in metal mines in China.Factors that induce rockburst include strong blasting distur-bance and high stress concentration caused by overlying mining and tectonic structural planes. For example, the Baiyinnuoer lead-zinc mine, a large lead-zinc polymetallic deposit in North China, has a goaf volume greater than millions of cubic meters. Because of the existence of such huge-volume goafs in this mine, in situ stress is highly concentrated in the rock mass of some mining zones. Under this condition, dynamic disasters such as rock ejection and roof cav-ing appear during tunnel excavation when the underground mining reaches only a depth of 300 m. These seriously affect the normal production safety of the mine, as shown in Fig. 1. The failure pattern in the tunnels clearly indicates that the direction of the maximum principal stress is influenced by goafs. In the Dongguashan copper mine, more than a tenth of the rockbursts that led to casualties oc-curred from 1996 to 1999. In April 2006, a rockburst in the Erdaogou gold mine resulted in injury to many workers and a considerable ore loss, and made mining work much more difficult at the lower levels. In January 2013 in the Linglong gold mine of Shandong Province, two workers were injured by a shock wave induced by a rockburst, and a great deal of electrical equipment was destroyed. According to incomplete statistics, in the period from 2001 to 2007, more than 13 000 accidents occurred in Chinese metal mines that became se-rious threats to the safe production of the mine and that resulted in more than 16 000 workers injured. Moreover, a large amount of valuable resources could not be extracted.Several strategies have been proposed to reduce the risk of rock-burst; these include the development of a new-generation micro-seismicity monitoring system, increasing current understanding of the rockburst evolution process using laboratory and in situ tests and monitoring, the establishment of a quantitative warning and* Corresponding author.E-mail address: xtfeng@, xia.ting.feng@/10.1016/J.ENG.2017.04.0132095-8099/© 2017 THE AUTHORS. Published by Elsevier LTD on behalf of the Chinese Academy of Engineering and Higher Education Press Limited Company.This is an open access article under the CC BY-NC-ND license (/licenses/by-nc-nd/4.0/).Contents lists available at ScienceDirectjo ur n al h om e pag e: w w /locate/engEngineering539X.-T. Feng et al. / Engineering 3 (2017) 538–545risk assessment for the location and intensities of different types of rockburst, and the development of measures to dynamically control rockburst. An expert system with neural network modeling has been developed to assess the risk of rockburst in coal mines [3] and in deep gold mines in South Africa [4]. This paper reviews the progress that has been made in reducing rockburst risk, and provides an ex-ample to illustrate the applicability of these new strategies.2. Development of an intelligent microseismicity monitoring system and method2.1. An intelligent microseismicity monitoring systemWith the development of computer and communication tech-nologies, modern microseismicity monitoring technology is widely used in the field of rock and mining engineering. However, there are some key technical obstacles that affect the application of micro-seismic technology. For example, in the absence of global position-ing system (GPS) signals, the timing service precision of the collec-tor will greatly affect the location accuracy of microseismic sources. Outside of the sensor array, microseismic source locations are unavailable. In order to solve these problems, further improve the capacity of a microseismicity monitoring system to capture weak signals, and provide more reliable technical support for disaster warnings, a new generation of microseismicity monitoring system was developed (Fig. 2), as described below.The system hardware consists of sensors, signal fidelity boxes,data-acquisition devices, timing servers, data servers, and related data communications equipment. The software system consists of a microseism acquisition instrument configure (MAC) system based on a web browser for the collectors, microseismic system monitor- diagnosis-configure code (MMC) software of configuration and monitoring for the microseismic system, and a real-time waveform dynamic monitoring system for the waveform. Furthermore, real- time geo-disaster microseism signals identification and analysis system (GMS) software and visual geo-disaster microseism signals three-dimensional dynamic display (GMD) software are employed for microseismic information during the development of geological hazards. The MAC system regulates and manages the collectors, while the MMC software monitors and manages the microseismic system. The GMS monitors provide analysis and warning of micro-seismic activities, and the GMD software displays three-dimensional microseismic information and disaster risks.The characteristics and advantages of this system are summa-rized as follows:(1) This system realizes 32-bit analog-to-digital (AD) conversion and improves the ability of the microseismic system to capture weak microfracture signals in weak rocks.(2) The system employs a precision time protocol to update time-synchronization strategies. Moreover, in the absence of GPS signals, the time-synchronization precision of the stations reaches the sub-microsecond level, making it possible to reach high-preci-sion orientation of the fracture sources.(3) The system can collect all signals within 24 h in order to avoid signal loss due to improper thresholds.(4) Based on an artificial neural network (ANN) and particle swarm optimization (PSO) algorithms, signals of microseismic sources outside of the sensor array can be effectively and accurately identified, allowing operators to locate fracture sources rapidly and accurately.(5) Using Internet technology, system faults are diagnosed in real time in order to issue early warnings and send information to desig-nated mobile phones, e-mail addresses, or service centers.(6) Using public platforms, triggering and continuous data are original and open to access; therefore, users can carry out first-hand scientific research and secondary development according to their specific needs.The technical parameters of the main hardware of the system are described below.2.1.1. Technical parameters of the sensorsVelocity sensors. GU(T)10 sensors (Institute of Rock and Soil Mechanics, Chinese Academy of Sciences) are used. Their sen-sitivity, coil resistance, frequency range, and measurable range are 100 (±5%) V·(m·s −1)−1, 4000 (±5%) Ω, 10–1000 (±10%) Hz, and10–2000Hz, respectively. The specification sizes of unidirectionalFig. 1. Rock ejection from the roof of a tunnel in the Baiyinnuoer lead-zinc mine.Fig. 2. The new-generation microseismicity monitoring system. (a) Sensors; (b) data collector; (c) timing server.540X.-T. Feng et al. / Engineering 3 (2017) 538–545(DSL) transmission, the time-synchronization precision of the moni-toring nodes reaches the sub-microsecond level.(3) Utilizing the timing server for timing and network transmis-sion, the time-synchronization precision of the monitoring nodes reaches the sub-microsecond level.(4) Utilizing the timing server for timing and long-distance DSL transmission, the time-synchronization precision of the monitoring nodes reaches the microsecond level.2.2. An intelligent in situ microseismicity monitoring method In mining projects, consideration must be made in microseis-micity monitoring to elaborate the evolution of rock mass fractures, both in the entire mining area and at a particular working face. Fig. 3 [5] shows a typical sensor network in a metal mine. A sensor arrangement can be applied through the excavated caverns at the sublevel in order to monitor the stability of the entire mining region (Fig. 3(a)). The radius of this kind of monitoring may extend for several hundred meters or even more. Goafs are a continual issue in the development of ore extraction, and severe monitoring per-formance loss of the microseismic system will occur around these goafs. Unfortunately, there is a large chance of rockburst in these regions. In order to solve this problem, sensor density should be increased around goafs to improve sensitivity and reduce position error. At the same time, the anisotropic wave velocity of the rock mass (i.e., the different speeds of P- and S-waves propagating from the fracture source to each microseismic sensor) should be adopt-ed for location rock mass fracture events near these goafs. On the whole, the sensor arrangement in the partial working face approx-imates that of cavern projects, as shown in Fig. 3(b) and Fig. 3(c). Partial sensors are installed through the excavated tunnels near the monitored working face. Other extra sensors are supplied as needed to focus on the regions with rockburst risk. In addition, a dynamic sensor network based on monitored microseismicity and on the risk of rockburst assessment is suggested, using the recycled installationand three-directional sensors are, respectively, ϕ33 mm × 120 mm and ϕ58.5 mm × 180 mm.Constant current acceleration sensors. AU(T)2000 sensors (Institute of Rock and Soil Mechanics, Chinese Academy of Sciences) are used. Their sensitivity, resolution, frequency range, and measur-able range are 2 V·g −1 (g = 9.8 m·s −2), 0.04 milli-g , 0.2–3000 (±10%) Hz, and ±2.5g , respectively. Their supply voltage, constant current source, bias voltage, and proper temperature are 18–30 V, 2–10 mA, 9–14 V DC , and –40–120 °C, respectively. The specification sizes of unidirectional and three-directional sensors are ϕ33 mm ×120 mm and ϕ58.5 mm × 180 mm, respectively.Constant voltage acceleration sensors. AU(T)30000 sensors (Institute of Rock and Soil Mechanics, Chinese Academy of Sciences) are used. Their sensitivity, resolution, frequency range, and fre-quency response are 30 (±5%) V·g −1, 0.00005g , ±0.16g , and 50–5000 Hz ± 3 dB, respectively. Their supply voltage, bias voltage, and proper temperature are 24–28 V DC , 19 V DC ± 1.5 V DC , and –20–55 °C, respectively. The specification sizes of the unidirectional sensors are ϕ24.8 mm × 122 mm, and they weigh 156 g.2.1.2. Parameters of collectorsAs they are able to realize 32-bit AD conversion, the signal collec-tors can sample at frequencies of 4 kHz, 2 kHz, 1 kHz, 500 Hz, and 250 Hz. The dynamic range is not less than 120 dB, and the timing is realized using GPS or the timing server. In addition, the collector has eight channels and a power consumption of less than 5 W. Col-lectors with geometrical dimensions of 245 mm × 192 mm × 92 mm and a weight of 3 kg are able to work at temperatures ranging from −20 °C to 80 °C.2.1.3. Synchronization parameters of the timing server(1) Through GPS timing and network transmission, the time- synchronization precision of the monitoring nodes reaches the sub-microsecond level.(2) Through GPS timing and long-distance digital subscriber lineFig. 3. A typical sensor network in a metal mine [5]. (a) The entire monitoring area; (b, c) local sensors for the working face.541X.-T. Feng et al. / Engineering 3 (2017) 538–545of sensors method.Rather than an accelerometer, a geophone is suggested for moni-toring rockburst in deep mines. The monitored distance of an accel-erometer is insufficient for the whole mining area. For the specific stope, the complete radiated wave from a rockburst source some-times cannot be recorded by an accelerometer. Information on the communication of the microseismic system and the positioning of monitoring parameters can be found in Ref. [5].Adequate noise-filtering and microseismic source locating are the bases of microseismic data analysis. Conventional data analysis methods based on the far-field microseismic source are suitable for regional monitoring. For the local stope, the signal-to-noise ratio of the rock mass fracture signals is low due to the strong noise; mean-while, the types of noise vary and some of their related characteris-tics are similar to rock mass fracture signals. As a result, convention-al human-made and signal-index noise-filtering methods become unreliable. A multi-index noise-filtering method such as neural networks is thus essential [6]. Due to the limits of the sensor layout, rock mass fracture sources are sometimes outside of the sensor ar-ray. The reliability of conventional linear event-locating methods, such as the Geiger, conjugate gradient, and steepest descent meth-ods, is questionable. For this situation, a perfect non-linear method is a better choice, such as the Monte Carlo, ANN, or downhill sim-plex and PSO methods [6]. Calibration shots should be executed fre-quently to ensure location accuracy, and the constant velocity model for event location should be used carefully. For a local stope with complex geological conditions, the anisotropy or layered velocity model is essential.3. Mechanisms of different types of rockburstIn situ microseismicity monitoring has revealed that most moni-tored rockbursts have a microseismic precursor [5,6]. This microseis-micity can be seen as a rock mass fracturing process underpinning the rockburst. The mechanism of the rockburst can be interpreted if the types of related rock mass fractures (tensile, mixed, and shear) can be identified. Energy ratio, moment tensor analysis, and P-wave development methods (Table 1) [6‒9] based on real microseismic information are extensively used to identify the types of rock mass fracturing. It should be noted that the reliability of these methods must first be checked against changes in the monitoring situation. A comprehensive method that combines these methods can effec t ively improve the judgement accuracy [9]. The macro failure character-istics of a rockburst, as observed by means of a field survey, along with the fracture modes (tensile or shear) of the fracture surfaces at explosive rock blocks, as examined by scanning electron microscope, serve as auxiliary information to determine the mechanism of rock-burst evolution.Fig. 4 shows the evolutionary characteristics in the development process of a typical rockburst. It can be seen that:(1) For a strain burst, the events are mostly documented througha tension mechanism. Only a few events of mixed and shear types can be distinguished during the development process of this kind of rockburst.(2) In the beginning of a strain-structure slip rockburst, no mat-ter whether there is a single, a set, or two sets of stiff structures, several events with low radiated seismic energy occur in the tensile mechanism. Next, the three types of mechanism event appear alter-nately.(3) Aside from strain burst and strain-structure slip rockbursts, most fracturing events are tensile. However, the final occurrence of a rockburst displays the failure mechanism of shear.(4) The appearance of a major event (lg E > 4.8) depends on the type of rockburst. For most strain-structure slip rockbursts, major events occur at each stage. However, major events can only be seen in the middle and late periods of a strain burst’s evolution.The strain burst mechanism analysis of a typical deep tunnel indicated that more than 92.5% of fracturing events appear through tension mechanisms and the mixed and shear events are only about 5% on average. As the number of stiff structures increases, the ratio of tensile events decreases quickly. If there is a single stiff structure or one set of stiff structures, the ratio of tensile events is usually less than 86%. This ratio drops to 68% when there are two stiff structures or two sets of stiff structures. In short, stiff structures are a major control factor in the rockburst evolution mechanism. However, more than 70% of events display a tensile mechanism in the rockburst de-velopment process.4. Rockburst warning4.1. Definition of rockburst warningIn this study, the phrase “rockburst warning” is used to indicate a warning of the location, intensity, and probability of a rockburst, rather than a warning of the time of a rockburst occurrence. The warning result is used for rockburst mitigation.4.2. Basis of rockburst warningStudies show that most rockbursts show the following key fea-tures during their development processes.(1) Microseismic events in the spatial distribution approach nucleation as an evolution of the rockburst. Studies show that the spatial distribution of microseismic events during the development process of a rockburst creates spatial fractal behavior [10]. The spa-tial distribution of microseismic events reveals fractal self-similarity. The nucleation and self-similarity of the spatial distribution of the microseismic events indicate that monitored microseismicity can be utilized to warn of the location of a potential rockburst in the area.(2) The energy of microseismic events during the development process of the most immediate rockburst creates temporal fractal behavior [10]. The temporal distributions of energy and the numberTable 1Microseismic methods to identify types of rock mass fracturing.Method Judgement indexJudgement criteria ExampleEnergy ratioRatio of the S- and P-wave energies (E S /E P )S P S P S P 10 Tensile failure 1020 M ixed failure 20 Shear failureE E E E E E <≤≤>Ref. [7]Moment tensor analysisPercentage shear component of moment tensor (DC %)%40% Tensile failure 40%%60% Mixed failure %60% Shear failure DC DC DC ≤<<≥Refs. [8,9]P-wave development Development degree of P-waves (P D )D D 0.047 Tensile failure 0.047Shear failureP P ≥<Refs. [6,9]542X.-T. Feng et al. / Engineering 3 (2017) 538–545of microseismic events reveal fractal self-similarity. Furthermore, there is a correlation between rockburst intensity and microseis-micity. In general, the more active the microseismicity (i.e., higher energy and a larger number of events), the greater the intensity of the rockburst [11]. This indicates that the monitored energy and the number of microseismic events in a temporal distribution can be used to warn of the intensity of a potential rockburst in the area.4.3. Method of rockburst warningBased on the in situ microseismicity and rockburst case study, a rockburst warning formula can be established and can be used to provide some warning of rockbursts [11]. In order to improve the accuracy of this rockburst warning, the following characteristics should be considered.(1) As mentioned above, in terms of the development mechanism and the effect of geological structure, rockbursts can be divided into different types, with a different microseismicity for each type [9,12]. Therefore, different formulas should be developed for each rock-burst type.(2) The microseismicity changes with construction methods, such as drilling and blasting, and tunnel boring machine (TBM) methods [6]. Therefore, different formulas should be developed for different construction methods.(3) The microseismicity and risk of rockburst change with varia-tions in geological condition, in situ stresses, rock mass properties, excavation, and support. Therefore, there should be a dynamic rock-burst warning based on the variation of the microseismicity.Considering these factors, a warning formula was developed based on the in situ microseismicity and case study that can be ex-pressed as follows [11]:61mr mr mri j jij P w P ==∑ (1)where m is the construction method, r is the rockburst type, i is therockburst intensity (extremely intense, intense, moderate, slight, or none), j is the microseismic parameter and six parameters in total, w is the weighting coefficient, and P ji is the functional relationship between microseismicity and rockburst (one example is shown in Fig. 5). The probability of every rockburst event ranges from 0 to 100%. The bigger the probability, the greater the rockburst risk [11].5. Measures to mitigate rockburst riskSeveral methods have been developed to reduce the risk of rockburst, such as: optimization of the excavation (or mining) sec-tion size and sequences in order to reduce the stress concentration induced by excavation or mining; high stress aided blasting; dis-tressing to release part of the energy; and the support absorbing energy. Here, a method of using high in situstresses to improveFig. 4. Evolution mechanisms of different typical rockburst types. (a) A moderate strain burst; (b) an intense strain-structure slip rockburst with a set of stiff structures; (c) a mod-erate strain-structure slip rockburst with two stiff structures.Fig. 5. Functional relationship between microseismicity and rockburst [11].543 X.-T. Feng et al. / Engineering 3 (2017) 538–545blasting effectiveness in order to reduce the risk of rockburst is in-troduced.5.1. Principle of the methodThe deep rock mass is in a high-stress (high-energy) environ-ment. During deep mining by the drilling-and-blasting method, rock fragmentation is completed under the combined effect of high static stress and dynamic stress induced by explosion. The blasting vibra-tion is one of the main causes of dynamic disasters such as rockburst in surrounding rocks. In the blasting process of deep high-energy rocks, the dynamic stress from blasting can induce the disordered release of high energy in the rock mass. As a result, over-breakage and lack-breakage occur to a slight degree, and affect the formation of excavation peripheries. In severe cases, rockburst occurs. Since it is known that the dynamic stress from blasting can induce high energy release in the rock mass, the orderly release of high energy can be achieved by optimizing the engineering layout and the blasting pro-gram. Thus, the energy is used in the rock fracture process to improve the blasting efficiency and effect, and the risk of rockburst may be reduced. A new method involves high-stress-induced rock cracking to promote rock blasting and to control rockburst risk. The core idea of the method is as follows: The energy in the rock blasting zone is used to promote rock fragmentation, reduce the explosive consump-tion, and improve the blasting effect; the energy in the non-explosive rock mass is absorbed and controlled, while the energy level of the rock and the risk of rockburst are reduced; and finally, the blasting vibration is reduced and the regulation of rockburst is realized.5.2. Method implementationThe first step of this method involves an investigation of the mechanism of rock fragmentation under coupled deep high stress and dynamic stress by blasting, and of the mechanism of dynamic catastrophe induced by blasting vibration. Here, numerical simula-tions and experiments are used to study the blasting failure laws of the energetic rock mass under high stress; the activation, transfer, and release characteristics of the static energy in the rock mass during the blasting process; and the disaster mechanism and the in-fluence factors of the high-stress rock mass induced by the blasting vibration. The experimental results show that static stress has a sig-nificant effect on the shape and volume of the blasting zone in the presence of a free surface, as shown in Fig. 6[13]. The design of the drilling-blasting scheme in deep rock engineering must consider the influence of static stress.The second step involves real-time monitoring of the stress field in the working area and in the surrounding rock mass during drilling- blasting excavation. Through a combination of microseismicity monitoring, stress measurement, and numerical simulation, the stress and energy distribution characteristics of the working area and surrounding rock mass are obtained and used as the basis for the design of the drilling-blasting scheme.The final step uses the drilling-and-blasting design theory and method, which consider the difference of the stress field. According to the stress transfer law, the stress field and the energy field are regulated by the cutting position, the caving sequence, and the zone of each caving. Thus, the stress field is more favorable to rock frag-mentation by blasting and rockburst control.According to the stress distribution characteristics, the blasting parameters, charge structure, and delay time are optimized and regulated. The shape of the blasting area and the rock fragmentation effect are controlled, and the blasting vibration is reduced.6. Case studyThe Hongtoushan copper mine, one of the deepest nonferrous metal mines in China, has a mining depth of over 1300 m. Ground hazard events such as collapse and rockburst have rapidly increased in frequency, threatening life and causing financial losses. For exam-ple, a strong rockburst occurred in the ramp near the stope at the −647 m level on 18 May 1999, resulting in 10 m of long rock mass being damaged and about 60 m3 of rocks being thrown to the oppo-site side. On 8 January 2005, a rockburst caused dozens of rocks to be thrown from the wall and roof of the stope, as shown in Fig. 7. In addition, due to the extremely complicated geological conditions, impact caving was easily induced when tectonic structural planes were encountered in the mining process. For example, at the No.10 stope at the −767 m level, an upward slice cutting-and-filling stoping method was applied, with an exposed area of more than 2400 m2. While mining the topmost layer, a structural plane was revealed between the wall and roof of the stope, resulting in a large area of orebody caving from the roof. The caving area was about 400 m2 with a height of more than 3 m and an ore quantity of about 3500 t. To address this situation, microseismicity monitoring tech-nology was employed in 2007 below the −647 m level, and a few rockburst preventative measures were adopted to strengthen the risk management.6.1. Rockburst predictionMany factors influence the accuracy of microseismic data, includ-ing the number of sensors, microseismic event location precision, and precise processing of data. Therefore, rockbursts are predicted using microseismic multi-parameters including the apparent vol-ume, spatial correlation length, energy index, fractal dimension, and b value [14]. Before a large-scale fracture or rockburst occurs, these microseismic multi-parameters display distinct precursory char-acteristics. This method can significantly improve the accuracy of rockburst prediction.6.2. Mining sequence and blasting parameters optimization by utilizing high stressIn deep mining practice, high in situ stress is conducive to breakingFig. 6. The shape of the explosion failure zone under uniaxial lateral stress [13]. (a) 0MPa; (b) 5MPa; (c) 10MPa.。