镗削加工和镗床机床工艺夹具外文文献翻译、中英文翻译、外文翻译
机械加工工艺夹具类高速铣削外文翻译、中英文翻译、外文文献翻译

英文资料High-speed millingHigh-speed machining is an advanced manufacturing technology, different from the traditional processing methods. The spindle speed, cutting feed rate, cutting a small amount of units within the time of removal of material has increased three to six times. With high efficiency, high precision and high quality surface as the basic characteristics of the automobile industry, aerospace, mold manufacturing and instrumentation industry, such as access to a wide range of applications, has made significant economic benefits, is the contemporary importance of advanced manufacturing technology. For a long time, people die on the processing has been using a grinding or milling EDM (EDM) processing, grinding, polishing methods. Although the high hardness of the EDM machine parts, but the lower the productivity of its application is limited. With the development of high-speed processing technology, used to replace high-speed cutting, grinding and polishing process to die processing has become possible. To shorten the processing cycle, processing and reliable quality assurance, lower processing costs.1 One of the advantages of high-speed machiningHigh-speed machining as a die-efficient manufacturing, high-quality, low power consumption in an advanced manufacturing technology. In conventional machining in a series of problems has plagued by high-speed machining of the application have been resolved.1.1 Increase productivityHigh-speed cutting of the spindle speed, feed rate compared withtraditional machining, in the nature of the leap, the metal removal rate increased 30 percent to 40 percent, cutting force reduced by 30 percent, the cutting tool life increased by 70% . Hardened parts can be processed, a fixture in many parts to be completed rough, semi-finishing and fine, and all other processes, the complex can reach parts of the surface quality requirements, thus increasing the processing productivity and competitiveness of products in the market.1.2 Improve processing accuracy and surface qualityHigh-speed machines generally have high rigidity and precision, and other characteristics, processing, cutting the depth of small, fast and feed, cutting force low, the workpiece to reduce heat distortion, and high precision machining, surface roughness small. Milling will be no high-speed processing and milling marks the surface so that the parts greatly enhance the quality of the surface. Processing Aluminum when up Ra0.40.6um, pieces of steel processing at up to Ra0.2 ~ 0.4um.1.3 Cutting reduce the heatBecause the main axis milling machine high-speed rotation, cutting a shallow cutting, and feed very quickly, and the blade length of the workpiece contacts and contact time is very short, a decrease of blades and parts of the heat conduction. High-speed cutting by dry milling or oil cooked up absolute (mist) lubrication system, to avoid the traditional processing tool in contact with the workpiece and a lot of shortcomings to ensure that the tool is not high temperature under the conditions of work, extended tool life.1.4 This is conducive to processing thin-walled partsHigh-speed cutting of small cutting force, a higher degree of stability, Machinable with high-quality employees compared to the company may be very good, but other than the company's employees may Suanbu Le outstanding work performance. For our China practice, we use the models to determine the method of staff training needs are simple and effective. This study models can be an external object, it can also be a combination of internal and external. We must first clear strategy for the development of enterprises. Through the internal and external business environment and organizational resources, such as analysis, the future development of a clear business goals and operational priorities. According to the business development strategy can be compared to find the business models, through a comparative analysis of the finalization of business models. In determining business models, a, is the understanding of its development strategy, or its market share and market growth rate, or the staff of the situation, and so on, according to the companies to determine the actual situation. As enterprises in different period of development, its focus is different, which means that enterprises need to invest the manpower and financial resources the focus is different. So in a certain period of time, enterprises should accurately selected their business models compared with the departments and posts, so more practical significance, because the business models are not always good, but to compare some aspects did not have much practical significance, Furthermore This can more fully concentrate on the business use of limited resources. Identify business models, and then take the enterprise of the corresponding departments and staff with the business models for comparison, the two can be found in the performance gap, a comparative analysis to find reasons, in accordance with this business reality, the final identification of training needs. The cost of training is needed, if not through an effective way to determine whether companies need to train and the training of the way, but blind to training, such training is difficult to achieve the desired results. A comparison only difference between this model is simple and practical training.1.5 Can be part of some alternative technology, such as EDM, grinding high intensity and high hardness processingHigh-speed cutting a major feature of high-speed cutting machine has the hardness of HRC60 parts. With the use of coated carbide cutter mold processing, directly to the installation of ahardened tool steel processing forming, effectively avoid the installation of several parts of the fixture error and improve the parts of the geometric location accuracy. In the mold of traditional processing, heat treatment hardening of the workpiece required EDM, high-speed machining replace the traditional method of cutting the processing, manufacturing process possible to omit die in EDM, simplifying the processing technology and investment costs .High-speed milling in the precincts of CNC machine tools, or for processing centre, also in the installation of high-speed spindle on the general machine tools. The latter not only has the processing capacity of general machine tools, but also for high-speed milling, a decrease of investment in equipment, machine tools increased flexibility. Cutting high-speed processing can improve the efficiency, quality improvement, streamline processes, investment and machine tool investment and maintenance costs rise, but comprehensive, can significantly increase economic efficiency.2 High-speed millingHigh-speed milling the main technical high-speed cutting technology is cutting the development direction of one of it with CNC technology, microelectronic technology, new materials and new technology, such as technology development to a higher level. High-speed machine tools and high-speed tool to achieve high-speed cutting is the prerequisite and basic conditions, in high-speed machining in the performance of high-speed machine tool material of choice and there are strict requirements.2.1 High-speed milling machine in order to achieve high-speed machiningGeneral use of highly flexible high-speed CNC machine tools, machining centers, and some use a dedicated high-speed milling, drilling. At the same time a high-speed machine tool spindle system and high-speed feeding system, high stiffness of the main characteristics of high-precision targeting and high-precision interpolation functions, especially high-precision arc interpolation function. High-speed machining systems of the machine a higher demand, mainly in the following areas:General use of highly flexible high-speed CNC machine tools, machining centers, and some use a dedicated high-speed milling, drilling. At the same time a high-speed machine tool spindle system and high-speed feeding system, high stiffness of the main characteristics of high-precision targeting and high-precision interpolation functions, especially high-precision arc interpolation function. High-speed machining systems of the machine a higher demand, mainly in the following areas:High-speed milling machine must have a high-speed spindle, the spindle speed is generally 10000 ~ 100000 m / min, power greater than 15 kW. But also with rapid speed or in designated spots fast-stopping performance. The main axial space not more than 0 .0 0 0 2 m m. Often using high-speed spindle-hydrostatic bearings, air pressure-bearing, mixed ceramic bearings, magneticbearing structure of the form. Spindle cooling general use within the water or air cooled.High-speed processing machine-driven system should be able to provide 40 ~ 60 m / min of the feed rate, with good acceleration characteristics, can provide 0.4 m/s2 to 10 m/s2 acceleration and deceleration. In order to obtain good processing quality, high-speed cutting machines must have a high enough stiffness. Machine bed material used gray iron, can also add a high-damping base of concrete, to prevent cutting tool chatter affect the quality of processing. A high-speed data transfer rate, can automatically increase slowdown. Processing technology to improve the processing and cutting tool life. At present high-speed machine tool manufacturers, usually in the general machine tools on low speed, the feed of the rough and then proceed to heat treatment, the last in the high-speed machine on the half-finished and finished, in improving the accuracy and efficiency at the same time, as far as possible to reduce processing Cost.2.2 High-speed machining toolHigh-speed machining tool is the most active one of the important factors, it has a direct impact on the efficiency of processing, manufacturing costs and product processing and accuracy. Tool in high-speed processing to bear high temperature, high pressure, friction, shock and vibration, such as loading, its hardness and wear-resistance, strength and toughness, heat resistance, technology and economic performance of the basic high-speed processing performance is the key One of the factors. High-speed cutting tool technology development speed, the more applications such as diamond (PCD), cubic boron nitride (CBN), ceramic knives, carbide coating, (C) titanium nitride Carbide TIC (N) And so on. CBN has high hardness, abrasion resistance and the extremely good thermal conductivity, and iron group elements between the great inertia, in 1300 ℃ would not have happened significant role in the chemical, also has a good stability. The experiments show that with CBN cutting toolHRC35 ~ 67 hardness of hardened steel can achieve very high speed. Ceramics have good wear resistance and thermal chemical stability, its hardness, toughness below the CBN, can be used for processing hardness of HRC <5 0 parts. Carbide Tool good wear resistance, but the hardness than the low-CBN and ceramics. Coating technology used knives, cutting tools can improve hardness and cutting the rate, for cutting HRC40 ~ 50 in hardness between the workpiece. Can be used to heat-resistant alloys, titanium alloys, hightemperature alloy, cast iron, Chungang, aluminum and composite materials of high-speed cutting Cut, the most widely used. Precision machining non-ferrous metals or non-metallic materials, or the choice of polycrystalline diamond Gang-coated tool.2.3 High-speed processing technologyHigh-speed cutting technology for high-speed machining is the key. Cutting Methods misconduct, will increase wear tool to less than high-speed processing purposes. Only high-speed machine tool and not a good guide technology, high-speed machining equipment can not fullyplay its role. In high-speed machining, should be chosen with milling, when the milling cutter involvement with the workpiece chip thickness as the greatest, and then gradually decreased. High-speed machining suitable for shallow depth of cut, cutting depth of not more than 0.2 mm, to avoid the location of deviation tool to ensure that the geometric precision machining parts. Ensure that the workpiece on the cutting constant load, to get good processing quality. Cutting a single high-speed milling path-cutting mode, try not to interrupt the process and cutting tool path, reducing the involvement tool to cut the number to be relatively stable cutting process. Tool to reduce the rapid change to, in other words when the NC machine tools must cease immediately, or Jiangsu, and then implement the next step. As the machine tool acceleration restrictions, easy to cause a waste of time, and exigency stop or radical move would damage the surface accuracy. In the mold of high-speed finishing, in each Cut, cut to the workpiece, the feed should try to change the direction of a curve or arc adapter, avoid a straight line adapter to maintain the smooth process of cutting.3 Die in high-speed milling processing ofMilling as a highly efficient high-speed cutting of the new method,inMould Manufacturing has been widely used. Forging links in the regular production model, with EDM cavity to be 12 ~ 15 h, electrodes produced 2 h. Milling after the switch to high-speed, high-speed milling cutter on the hardness of HRC 6 0 hardened tool steel processing. The forging die processing only 3 h20min, improve work efficiency four to five times the processing surface roughness of Ra0.5 ~ 0.6m, fully in line with quality requirements.High-speed cutting technology is cutting technology one of the major developments, mainly used in automobile industry and die industry, particularly in the processing complex surface, the workpiece itself or knives rigid requirements of the higher processing areas, is a range of advanced processing technology The integration, high efficiency and high quality for the people respected. It not only involves high-speed processing technology, but also including high-speed processing machine tools, numerical control system, high-speed cutting tools and CAD / CAM technology. Die-processing technology has been developed in the mold of the manufacturing sector in general, and in my application and the application of the standards have yet to be improved, because of its traditional processing with unparalleled advantages, the future will continue to be an inevitable development of processing technology Direction.4 Numerical control technology and equipping development trend and countermeasureEquip the engineering level, level of determining the whole national economy of the modernized degree and modernized degree of industry, numerical control technology is it develop new developing new high-tech industry and most advanced industry to equip (such as information technology and his industry, biotechnology and his industry, aviation, spaceflight, etc. national defense industry) last technology and getting more basic most equipment. Marx has ever said "the differences of different economic times, do not lie in what is produced, and lie in how to produce,produce with some means of labor ". Manufacturing technology and equipping the most basic means of production that are that the mankind produced the activity, and numerical control technology is nowadays advanced manufacturing technology and equips the most central technology. Nowadays the manufacturing industry all around the world adopts numerical control technology extensively, in order to improve manufacturing capacity and level, improve the adaptive capacity and competitive power to the changeable market of the trends. In addition every industrially developed country in the world also classifies the technology and numerical control equipment of numerical control as the strategic materials of the country, not merely take the great measure to develop one's own numerical control technology and industry, and implement blockading and restrictive policy to our country in view of " high-grade, precision and advanced key technology of numerical control " and equipping. In a word, develop the advanced manufacturing technology taking numerical control technology as the core and already become every world developed country and accelerate economic development in a more cost-effective manner, important way to improve the overall national strength and national position. Numerical control technology is the technology controlled to mechanical movement and working course with digital information, integrated products of electromechanics that the numerical control equipment is the new technology represented by numerical control technology forms to the manufacture industry of the tradition and infiltration of the new developing manufacturing industry, namely the so-called digitization is equipped, its technological range covers a lot of fields: (1)Mechanical manufacturing technology; (2)Information processing, processing, transmission technology; (3)Automatic control technology; (4)Servo drive technology;(5)Technology of the sensor; (6)Software engineering ,etc..Development trend of a numerical control technologyThe application of numerical control technology has not only brought the revolutionary change to manufacturing industry of the tradition, make the manufacturing industry become the industrialized symbol , and with the constant development of numerical control technology and enlargement of the application, the development of some important trades (IT , automobile , light industry , medical treatment ,etc. ) to the national economy and the people's livelihood of his plays a more and more important role, because the digitization that these trades needed to equip has already been the main trend of modern development. Numerical control technology in the world at present and equipping the development trend to see, there is the following several respect [1- ] in its main research focus.5 A high-speed, high finish machining technology and new trend equippedThe efficiency, quality are subjavanufacturing technology. High-speed, high finish machining technology can raise the efficiency greatly , improve the quality and grade of the products, shorten production cycle and improve the market competitive power. Japan carries the technological research association first to classify it as one of the 5 great modern manufacturing technologies forthis, learn (CIRP) to confirm it as the centre in the 21st century and study one of the directions in international production engineering.In the field of car industry, produce one second when beat such as production of 300,000 / vehicle per year, and many variety process it is car that equip key problem that must be solved one of; In the fields of aviation and aerospace industry, spare parts of its processing are mostly the thin wall and thin muscle, rigidity is very bad, the material is aluminium or aluminium alloy, only in a situation that cut the speed and cut strength very small high, could process these muscles, walls. Adopt large-scale whole aluminium alloy method that blank " pay empty " make the wing recently, such large-scale parts as the fuselage ,etc. come to substitute a lot of parts to assemble through numerous rivet , screw and other connection way, make the intensity , rigidity and dependability of the component improved. All these, to processing and equipping the demand which has proposed high-speed, high precise and high flexibility.According to EMO2001 exhibition situation, high-speed machining center is it give speed can reach 80m/min is even high , air transport competent speed can up to 100m/min to be about to enter. A lot of automobile factories in the world at present, including Shanghai General Motors Corporation of our country, have already adopted and substituted and made the lathe up with the production line part that the high-speed machining center makes up. HyperMach lathe of U.S.A. CINCINNATI Company enters to nearly biggest 60m/min of speed, it is 100m/min to be fast, the acceleration reaches 2g, the rotational speed of the main shaft has already reached 60 000r/min. Processing a thin wall of plane parts, spend 30min only, and same part general at a high speed milling machine process and take 3h, the ordinary milling machine is being processed to need 8h; The speed and acceleration of main shaft of dual main shaft lathes of Germany DMG Company are up to 120000r/mm and 1g.In machining accuracy, the past 10 years, ordinary progression accuse of machining accuracy of lathe bring 5μm up to from 10μm already, accurate grades of machining center from 3~5μm, rise to 1~1.5μm, and ultraprecision machining accuracy is i t enter nanometer grade to begin already (0.01μm).In dependability, MTBF value of the foreign numerical control device has already reached above 6 000h, MTBF value of the servo system reaches above 30000h, demonstrate very high dependability .In order to realize high-speed, high finish machining, if the part of function related to it is electric main shaft, straight line electrical machinery get fast development, the application is expanded further .5.2 Link and process and compound to process the fast development of the lathe in 5 axesAdopt 5 axles to link the processing of the three-dimensional curved surface part, can cut with the best geometry form of the cutter , not only highly polished, but also efficiency improves by a large margin . It is generally acknowledged, the efficiency of an 5 axle gear beds can equal 2 3 axle gearbeds, is it wait for to use the cubic nitrogen boron the milling cutter of ultra hard material is milled and pared at a high speed while quenching the hard steel part, 5 axles link and process 3 constant axles to link and process and give play to higher benefit. Because such reasons as complicated that 5 axles link the numerical control system , host computer structure that but go over, it is several times higher that its price links the numerical control lathe than 3 axles , in addition the technological degree of difficulty of programming is relatively great, have restricted the development of 5 axle gear beds.At present because of electric appearance of main shaft, is it realize 5 axle complex main shaft hair structure processed to link greatly simplify to make, it makes degree of difficulty and reducing by a large margin of the cost, the price disparity of the numerical control system shrinks. So promoted 5 axle gear beds of head of complex main shaft and compound to process the development of the lathe (process the lathe including 5).At EMO2001 exhibition, new Japanese 5 of worker machine process lathe adopt complex main shaft hair, can realize the processing of 4 vertical planes and processing of the wanton angle, make 5 times process and 5 axles are processed and can be realized on the same lathe, can also realize the inclined plane and pour the processing of the hole of awls. Germany DMG Company exhibits the DMUVoution series machining center, but put and insert and put processing and 5 axles 5 times to link and process in once, can be controlled by CNC system or CAD/CAM is controlled directly or indirectly.5.3 Become the main trend of systematic development of contemporary numerical control intelligently, openly, networkedly.The numerical control equipment in the 21st century will be sure the intelligent system, the intelligent content includes all respects in the numerical control system: It is intelligent in order to pursue the efficiency of processing and process quality, control such as the self-adaptation of the processing course, the craft parameter is produced automatically; Join the convenient one in order to improve the performance of urging and use intelligently, if feedforward control , adaptive operation , electrical machinery of parameter , discern load select models , since exactly makes etc. automatically; The ones that simplified programming , simplified operating aspect are intelligent, for instance intelligent automatic programming , intelligent man-machine interface ,etc.; There are content of intelligence diagnose , intelligent monitoring , diagnosis convenient to be systematic and maintaining ,etc..Produce the existing problem for the industrialization of solving the traditional numerical control system sealing and numerical control application software. A lot of countries carry on research to the open numerical control system at present, such as NGC of U.S.A. (The Next Generation Work-Station/Machine Control), OSACA of European Community (Open System Architecture for Control within Automation Systems), OSEC (Open System Environment for Controller) of Japan, ONC (Open Numerical Control System) of China, etc.. The numerical control system melts tobecome the future way of the numerical control system open. The so-called open numerical control system is the development of the numerical control system can be on unified operation platform, face the lathe producer and end user, through changing, increasing or cutting out the structure target(numerical control function), form the serration, and can use users specially conveniently and the technical know-how is integrated in the control system, realize the open numerical control system of different variety , different grade fast, form leading brand products with distinct distinction. System structure norm of the open numerical control system at present, communication norm , disposing norm , operation platform , numerical control systematic function storehouse and numerical control systematic function software development ,etc. are the core of present research.The networked numerical control equipment is a new light spot of the fair of the internationally famous lathe in the past two years. Meeting production line , manufacture system , demand for the information integration of manufacturing company networkedly greatly of numerical control equipment, realize new manufacture mode such as quick make , fictitious enterprise , basic Entrance that the whole world make too. Some domestic and international famous numerical control lathes and systematic manufacturing companies of numerical control have all introduced relevant new concepts and protons of a machine in the past two years, if in EMO2001 exhibition, " Cyber Production Center " that the company exhibits of mountain rugged campstool gram in Japan (Mazak) (intellectual central production control unit, abbreviated as CPC); The lathe company of Japanese big Wei (Okuma ) exhibits " IT plaza " (the information technology square , is abbreviated as IT square ); Open Manufacturing Environment that the company exhibits of German Siemens (Siemens ) (open the manufacturing environment, abbreviated as OME),etc., have reflected numerical control machine tooling to the development trend of networked direction.5.4 Pay attention to the new technical standard, normal setting-up5.4.1 Design the norm of developing about the numerical control systemAs noted previously, there are better common ability, flexibility, adaptability, expanding in the open numerical control system, such countries as U.S.A. ,European Community and Japan ,etc. implement the strategic development plan one after another , carry on the research and formulation of the systematic norm (OMAC , OSACA , OSEC ) of numerical control of the open system structure, 3 biggest economies in the world have carried on the formulation that nearly the same science planned and standardized in a short time, have indicated a new arrival of period of change of numerical control technology. Our country started the research and formulation of standardizing the frame of ONC numerical control system of China too in 2000.5.4.2 About the numerical control standardThe numerical control standard is a kind of trend of information-based development of manufacturing industry. Information exchange among 50 years after numerical control technology was born was all because of ISO6983 standard, namely adopt G, M code describes how processes,。
车床和铣床机械加工工艺夹具装备外文文献翻译、中英文翻译、外文翻译

机械设计制造及自动化专业毕业设计(论文)外文翻译附录二LATHES & MILLINGA shop that is equipped with a milling machine and an engine lathe can machine almost any type of product of suitable size.The basic machines that are designed primarily to do turning,facing and boring are called lathes. Very little turning is done on other types of machine tools,and none can do it with equal facility. Because lathe can do boring,facing,drilling,and reaming in addition to turning,their versatility permits several operations to be performed with a single setup of the workpiece. This accounts for the fact that lathes of various types are more widely used in manufacturing than any other machine tool.Lathes in various forms have existed for more than two thousand years. Modern lathes date from about 1797,when Henry Maudsley developed one with a leads crew. It provided controlled,mechanical feed of the tool. This ingenious Englishman also developed a change gear system that could connect the motions of the spindle and leadscrew and thus enable threads to be cut.Lathe Construction.The essential components of a lathe are depicted in the block diagram of picture. These are the bed,headstock assembly,tailstock assembly,carriage assembly,quick-change gearbox,and the leadscrew and feed rod.The bed is the back bone of a lathe. It usually is made of well-normalized or aged gray or nodular cast iron and provides a heavy,rigid frame on which all the other basic components are mounted. Two sets of parallel,longitudinal ways,inner and outer,are contained on the bed,usually on the upper side. Some makers use an inverted V-shape for all four ways,whereas others utilize one inverted V and one flat way in one or both sets. Because several other components are mounted and/or move on the ways they must be made with precision to assure accuracy of alignment. Similarly,proper precaution should betaken in operating a lathe to assure that the ways are not damaged. Any inaccuracy in them usually means that the accuracy of the entire lathe is destroyed. The ways on most modern lathes are surface hardened to offer greater resistance to wear and abrasion.The headstock is mounted in a fixed position on the inner ways at one end of the lathe bed. It provides a powered means of rotating the work at various speeds. It consists,essentially,of a hollow spindle,mounted in accurate bearings,and a set of transmission gears——similar to a truck transmission——through which the spindle can be rotated at a number of speeds. Most lathes provide from eight to eighteen speeds,usually in a geometric ratio,and on modern lathes all the speeds can be obtained merely by moving from two to four levers. An increasing trend is to provide a continuously variable speed range through electrical or mechanical drives.Because the accuracy of a lathe is greatly dependent on the spindle,it is of heavy construction and mounted in heavy bearings,usually preloaded tapered roller or ball types. Along- itudinal hole extends through the spindle so that long bar stock can be fed through it. The size of this hole is an important size dimension of a lathe because it determines the maximum size of bar stock that can be machined when the material must be fed through the spindle.The inner end of the spindle protrudes from the gear box and contains a means for mounting various types of chucks,face plates,and dog plates on it. Whereas small lathes often employ a threaded section to which the chucks are screwed,most large lathes utilize either cam-lock or key-drive taper noses. These provide a large-diameter taper that assures the accurate alignment of the chuck,and a mechanism that permits the chuck or face plate to be locked or unlocked in position without the necessity of having to rotate these heavy attachments.Power is supplied to the spindle by means of an electric motor through a V-belt or silent-chain drive. Most modern lathes have motors of from 5 to15 horsepower to provide adequate power for carbide and ceramic tools at their high cutting speeds.The tailstock assembly consists,essentially,of three parts. A lower casting fits on the inner ways of the bed and can slide longitudinally thereon,with a means for clamping the entire assembly in any desired location. An upper casting fits on the lower one and can be moved transversely upon it on some type of keyed ways. This transverse motion permits aligning the tailstock and headstock spindles and provides amethod of turning tapers. The third major component of the assembly is the tailstock quill. This is a hollow steel cylinder,usually about2 to3 inches in diameter,that can be moved several inches longitudinally in and out of the upper casting by means of a hand wheel and screw. The open end of the quill hole terminates in a Morse taper in which a lathe center,or various tools such as drills,can be held. A graduated scale,several inches in length,usually is engraved on the outside of the quill to aid in controlling its motion in and out of the upper casting. A locking device permits clamping the quill in any desired position.The carriage assembly provides the means for mounting and moving cutting tools. The carriage is a relatively flat H-shaped casting that rests and moves on the outer set of ways on the bed. The transverse bar of the carriage contains ways on which the cross slide is mounted and can be moved by means of a feed screw that is controlled by a small hand wheel and a graduated dial. Through the cross slide a means is provided for moving the lathe tool in the direction normal to the axis of rotation of the work.On most lathes the tool post actually is mounted on a compound rest. This consists of abase,which is mounted on the cross slide so that it can be pivoted about a vertical axis,and an upper casting. The upper casting is mounted on ways on this base so that it can be moved back and forth and controlled by means of a short lead screw operated by a hand wheel and a calibrated dial.Manual and powered motion for the carriage,and powered motion for the cross slide,is provided by mechanisms within the apron,attached to the front of the carriage. Manual movement of the carriage along the bed is effected by turning a hand wheel on the front of the apron,which is geared to a pinion on the back side. This pinion engages a rack that is attached beneath the upper front edge of the bed in an inverted position.To impart powered movement to the carriage and cross slide,a rotating feed rod is provided. The feed rod,which contains a keyway through out most of its length,passes through the two reversing bevel pinions and is keyed to them . Either pinion cam be brought into mesh with amating bevel gear by means of the reversing lever on the front of the apron and thus provide “forward” or “reverse” power to the carriage. Suitable clutches connect either the rack pinion orthe cross-slide screw to provide longitudinal motion of the carriage or transverse motion of cross slide.For cutting threads,a second means of longitudinal drive is provided by a lead screw. Whereas motion of the carriage when driven by the feed-rod mechanism takes place through a friction clutch in which slippage is possible,motion through the lead screw is by a direct,mechanical connection between the apron and the lead screw. This is achieved by a split nut. By means of a clamping lever on the front of the apron,the split nut can be closed around the lead screw. With the split nut closed,the carriage is moved along the lead screw by direct drive without possibility of slippage.Modern lathes have a quick-change gear box. The input end of this gearbox is driven from the lathe spindle by means of suitable gearing. The out put end of the gear box is connected to the feed rod and lead screw. Thus,through this gear train,leading from the spindle to the quick-change gearbox,thence to the lead screw and feed rod,and then to the carriage,the cutting tool can be made to move a specific distance,either longitudinally or transversely,for each revolution of the spindle. A typical lathe provides,through the feed rod,forty-eight feeds ranging from 0.002 inch to0.118 inch per revolution of the spindle,and,through the lead screw,leads for cutting forty-eight different threads from 1.5 to 92perinch.On some older and some cheaper lathes,one or two gears in the gear train between the spindle and the change gear box must be changed in order to obtain a full range of threads and feeds.Milling is a basic machining process in which the surface is generated by the progressive formation and removal of chips of material from the workpiece as it is fed to a rotating cutter in a direction perpendicular to the axis of the cutter. .In some cases the workpiece is stationary and the cutter is fed to the work. In most instances a multiple-tooth cutter is used so that the metal removal rate is high,and frequently the desired surface is obtained in a single pass of the work.The tool used in milling is known as a milling cutter. It usually consists of acylindrical body which rotates on its axis and contains equally spaced peripheral teeth that intermittently engage and cut the workpiece. In some cases the teeth extend part way across one or both ends of the cylinder.Because the milling principle provides rapid metal removal and can produce good surface finish,it is particularly well-suited for mass-production work,and excellent milling machines have been developed for this purpose. However,very accurate and versatile milling machines of a general-purpose nature also have been developed that are widely used in job-shop and tool and die work. A shop that is equipped with a milling machine and an engine lathe can machine almost any type of product of suitable size.Types of Milling Operations. Milling operations can be classified into two broad categories,each of which has several variations:1.In peripheral milling a surface is generated by teeth located in the periphery of the cutter body;the surface is parallel with the axis of rotation of the cutter. Both flat and formed surfaces can be produced by this method. The cross section of the resulting surface corresponds to the axial contour of the cutter. This procedure often is called slab milling.1.In face milling the generated flat surface is at right angles to the cutteraxis and is thecombined result of the actions of the portions of the teeth located on both the periphery and thewith the face portions providing a finishing action.The basic concepts of peripheral and face milling are illustrated in Fig. Peripheral milling operations usually are performed on machines having horizontal spindles,whereas face milling is done on both horizontal-and vertical-spindle machines.Surface Generation in Milling. Surfaces can be generated in milling by two distinctly different methods depicted in Fig. Note that in up milling the cutter rotates against the direction of feed the workpiece,whereas in down milling the rotation is in the same direction as the feed .As shown in Fig., the method of chip formation is quitedifferent in the two cases. In up milling the c hip is very thin at the beginning, where the tooth first contacts the work,and increases in thickness, be-coming a maximum where the tooth leaves the work. The cutter tends to push the work along and lift it upward from the table. This action tends to eliminate any effect of looseness in the feed screw and nut of the milling machine table and results in a smooth cut. However, the action also tends to loosen the work from the clamping device so that greater clamping forcers must be employed. In addition, the smoothness of the generated surface depends greatly on the sharpness of the cutting edges.In down milling,maximum chip thickness occurs close to the point at which the tooth contacts the work. Because the relative motion tends to pull the workpiece into the cutter,all possibility of looseness in the table feed screw must be eliminated if down milling is to be used. It should never be attempted on machines that are not designed for this type of milling. In as mush as the material yields in approximately a tangential direction at the end of the tooth engagement,there is much less tendency for the machined surface to show tooth marks than when up milling is used. Another consider able advantage of down milling is that the cutting force tends to hold the work against the machine table,permitting lower clamping force to be employed. This is particularly advantageous when milling thin workpiece or when taking heavy cuts.Sometimes a disadvantage of down milling is that the cutter teeth strike against the surface of the work at the beginning of each chip. When the workpiece has a hard surface,such as castings do,this may cause the teeth to dull rapidly.Milling Cutters. Milling cutters can be classified several ways. One method is to group them into two broad classes,based on tooth relief,as follows:1. Profile-cutters have relief provided on each tooth by grinding a small land back of the cutting edge. The cutting edge may be straight or curved.2.In form or cam-relieved cutters the cross section of each tooth is an eccentric curve behind the cutting edge,thus providing relief. All sections of the eccentric relief,parallel with the cutting edge,must have the same contour as the cutting edge. Cutters of this type are sharpened by grinding only the face of the teeth,with the contour of the cutting edge thus remaining unchanged.Another useful method of classification is according to the method of mounting the cutter. Arbor cutters are those that have a center hole so they can be mounted on an arbor. Shank cutters have either tapered or straight integral shank. Those with tapered shanks can be mounted directly in the milling machine spindle,whereas straight-shank cutters are held in a chuck. Facing cuttersusually are bolted to the end of a stub arbor.Types of Milling Cutters. Plain milling cutters are cylindrical or disk-shaped,having straight or helical teeth on the periphery. They are used for milling flat surfaces. This type of operation is called plain or slab milling. Each tooth in a helical cutter engages the work gradually,and usually more than one tooth cuts at a given time. This reduces shock and chattering tendencies and promotes a smoother surface. Consequently,this type of cutter usually is preferred over one with straight teeth. Side milling cutters are similar to plain milling cutters except that the teeth extend radially part way across one or both ends of the cylinder toward the center. The teeth may be either straight or helical. Frequently these cutters are relatively narrow,being disklike in shape. Two or more side milling cutters often are spaced on an arbor to make simultaneous,parallel cuts,in an operation called straddle milling.Interlocking slotting cutters consist of two cutters similar to side mills,but made to operate as a unit for milling slots. The two cutters are adjusted to the desired width by inserting shims between them.Staggered-tooth milling cutters are narrow cylindrical cutters having staggered teeth,and with alternate teeth having opposite helix angles. They are ground to cut only on the periphery,but each tooth also has chip clearance ground on the protruding side. These cutters have a free cutting action that makes them particularly effective in milling deep slots. Metal-slitting saws are thin,plain milling cutters,usually from 1/32 to 3/16 inch thick,which have their sides slightly“dished”to provide clearance and prevent binding. They usually have more teeth per inch of diameter than ordinary plain milling cutters and are used for milling deep,narrow slots and for cutting-off operations.附录2车床和铣床车间里拥有一台车床和一台普通铣床就能加工出具有适合尺寸的各种产品。
钻和镗机床夹具外文文献翻译、中英文翻译、外文翻译

Northcott,W.H.A treatise on lathes and turning: simple, mechanical, and ornament-al[M].London:Longmans,Green,2010:104-112.Drilling and boring(Excerpts)Flat articles are most conveniently driven by the face-plate,and long articles by the screwed chuck.The manner of attaching work to the former depends altogether upon the shape of the article,and no description will give an idea of all the methods employed.The operator will very frequently have to devise means for attaching his work,but this is not at all difficult.Any means may be employed that will not twist or strain the article,or in revolvingcome in the way of the lathe-bed or tools.A set of bolts of various lengths and with T-heads will be veryuseful,and a set of four of the clamps at Fig.129 are exceedinglyconvenient.In using these,the work is held against the face-plate andthe bolts of the clamps are put into its most convenient slots.Thesmall screw is adjusted so as to raise the end of each clamp,rathermore than the thickness of the work off the face-plate,the large bolt being then tightened in all the four clamps,the work is pinched at four places between the face-plate and the ends of the clamps.It is generally necessary to bore holes as nearly as possible concentric with the rest of the work;for instance,when the article is a spur wheel or a pulley,it is necessary that the hole should be made concentric or true with the teeth of the wheel,or the face of the pulley;so that when the hole is made on driving the article,on a mandril the rim will run true,and will not require much to be turned off it,or more from one side than from another.When certain parts of articles have to remain unturned,it is a good plan to chuck the work true with those portions,without regarding those parts which have to be turned;so that ,when these points are rendered true by turning the whole article is nearly concentric.As the surface of the plate is quite true,it is evident that the surface of the article,or those points of the surface which are against the face-plate,will run true when the hole is bored and the work put on to the mandril.But there is no such guarantee that any part of the edge of the article will be true;it is therefore necessary,before tightening the bolts finally,to set the edge or rim true,in the same manner as when centering a piece of iron.That is,a piece of chalk is held against the work in motion,and,as those parts showing the chalk are the farthest from the centre,a tap with a hammer or mallet is given the article at those points,to drive them nearerthe centre of the lathe.This is repeated until the chalk touches either all round,or at opposite points,when the clamp bolts may be tightened and the boring commenced.When articles have to be true with their inside edges,it is evident that this operation must be reversed.Wherever the chalk shows,those points must be hammered away from the centre.It is a difficult matter for one pair of hands to hold work against the face-plate whilst putting in the bolts for fastening it on in place.Workmen are in the habit of keeping it temporarily in place by forcing it against the face-plate by the boring bit or drill and the centre of the moving headstock.This practice cannot altogether be recommended,as,besides a direct tendency to damage the points of the drill and of the centre,it is a very frequent occurrence for the whole—the work and drill to—come down with a run on to the lathe-bed or to the ground;and this leads to serious damage to all things concerned,as the workman will readily admit if his toes happen to be between the work and the ground.Other more careful workmen—if the work have a rough hole through it already—fasten the work temporarily to the face-plate by means of a bolt,screwing into the centre hole of the lathe-spindle,and a piece of straight iron with a hole through it,for a cross piece to span the hole.This practice is certainly all that can be desired,so far as both safety and convenience go;but it has one objection—the screwing and unscrewing of this bolt are apt to damage or wear the centre hole,and cause the centre to fit slackly.Probably the best plan,when chucking heavy work,is,either to put a block of woo-d of the right height under the work,or to remove the face-plate from the lathe,and lay it horizontal,with its face upwards,when the work may be fastened to it with ease and convenience.When the work is properly chucked,it is set in motion,and the place where the hole is to be commenced should be trued up.The boring-rest is then put in place,just in front of the work;care being taken not to put it near enough for the bolts in revolving to strike against it.There are two holes in this boring-rest;one—the large one—is for the boring bits,the small one is for the drills.One of these holes is placed just opposite the centre of the work,and the proper drill or bit is put through it;the other end of the bits is furnished with a centre mark,into which the centre of the moving headstock must be placed,and the cutting edge of the drill forced into the revolving work,by moving the hand-wheel and forcing out the screw.The rectangular hole in the boring-rest only prevents the bit from revolving;besides this,it has to be kept steady,especially at the commencement of the hole.If the hole be a small one,the boring-wrench is put on over the drill,and the other end of the lever forced down bythe workman's left hand.When the hole is a large one,the pressure thus obtained is not enough;but a larger lever of the same sort is then used,and a good heavy weight hung on to its end,and kept there whilst the bit is cutting its way through the hole.If the article be of wrought iron or steel,the cutting edge of the bit must be kept moist with soapsuds or soda-water;but with brass and cast-iron this is not required.In cutting large holes out of the solid,all the material cannot be removed by one instrument.A small drill must first be sent through,to be followed by a series of others,each taking an increasing cut,until the required size of the hole is nearly obtained,when the last bit should be carefully sent through;but it must not be made to take so heavy a cut as the bits preceding it.In taking a series of heavy cuts at the hole,the metal composing the—article especially if cast-iron or brass—will be rendered rather hot by the friction;it is,therefore,a good plan to allow the article to cool before passing through the finishing or last bit.If this be not done,and the hole is finished whilst the surrounding metal is hot,it will be found that when the metal has cooled,the finishing bit is unable to enter again owing to the contraction of the metal.It may,however,happen that the spindle to work into the hole has been made rather under the standard size.In this case it will be advisable to take advantage of this expansion and contraction of the metal,and make it subservient to our purpose,by boring the last cut but one with a dull bit,and taking a heavy cut.The metal will then be made very hot and the hole will expand;so that if the finishing bit be then quickly passed through the result will be that when the metal cools the hole will again contract,and form a closer fit with the spindle previously turned too small.These little facts are small in themselves;;but,by bearing them in mind,they may frequently be turned to useful account.It is scarcely necessary to observe that,in all cases,care must be taken not to exceed a certain heat,or to allow the work to get hot enough to lower the temper of the tool.Long cylindrical or other shaped articles,through which a holeis required,cannot be conveniently attached to the face-plate;andtherefore,for these articles,the screwed or bell-chuck, Fig.121,isused.The chuck being put on the lathe-spindle,the article isinserted between the screws,which are then screwed down to encompass and tightly hold it.The beginner will,probably,have some little difficulty in adjusting these screws so as to hold the work true;but the matter is much simplified by trueing the inside set of screws first,and afterwards adjusting the outside ones.These screws should be set down tight enough to prevent the article slipping or moving about;but if when the hole is made the material will be thin,care should be taken not to set the screws down tighter than necessary,as otherwise the metal will be compressed,and the hole rendered out of shape in their neighbourhood.When the articles to be drilled are too long for this chuck alone,the ends are turned up true for an inch or two;and one end is then chucked true,and held between the outside set only of the screws of the chuck,whilst the other end is supported by being run in the die-stay.This is fastened to the lathe-bed,at the proper place,and a wooden or metal bearing,having a hole the same size as the end of the work,is put into the V's,and adjusted so as to bring the centre of the work in the line of lathe-centres.The lathe isthen set in motion,and the hole drilled in the usual manner.For these long articles the best tool I know of is the D-bit,shown at Fig.124.Thistool is not half so much used as it ought to be,and,when used it is in conjunction with several other drills,and in such a roundabout manner that very few have patience touse it at all.These other drills are,however quite unnecessary after the D-bit is once started.The best manner of proceeding is as follows:First,place the boring-rest in position,and with an ordinary drill,of the same size as the D-bit,drill out a recess about1/8 or 1/4 of an inch in depth;remove the boring-rest,place the centre mark at the endof the D-bit,against the centre of the headstock,and screw up carefully until the drill isin-to cut;the hole may then be bored through with ease and the certainty of its being true.The drill must be kept well lubricated with soda-water and oil,and occasionally removed,and the hole cleared of shavings.If the hole be more than a foot long,it will be better to drill it half from each end;and,if great truth be required,two of these drills should be used as in the other cases,As in long holes it is rather difficult to keep drills well moistened,the workman will find it a good plan to have a small syringe,and inject or squirt the lubricant into the hole with force;by so doing,not only will the drill be kept wet,but the shavings will,in a great measure,be washed out and the hole cleared.On comparing the D form of drill with others,it will be found that the cutting edge is only equal to half the diameter of the hole;at the same time the drill stem is strong and well able to stand torsional strain,to which drills are mostly subject.In the ordinary drill,the cutting edge is equal to about one and a half diameters of the hole,whilst the stem is not nearly so well calculated to bear the strain.It therefore appears reasonable to conclude that the D-bit is better adapted than the others to cut a long hole out of the solid,or indeed to cut a long hole out at all;and this is found to be the case.I have had considerable practice with this drill,and have so much confidence in its powers that I would undertake,with it alone,to drill a one-inch hole through a shaft thirty orforty feet long.Holes required to be very smooth and straight,or require to be very slightly enlarged,are ground on a lead or copper lap,Fig.128.Also in the of articles which have been hardened or case hardened,the action of the fire is sure to have had a effect uponthe hole.In some cases the hole is bent;in others,the surface is rather blistered;in all cases it is rendered somewhat rough.All imperfections are removed by grinding the holeon a lap.The method of using these laps is very simple:they are put between the lathe-centres,and driven by a lathe-carrier in the ordinary way.The laps'surface is covered with a coat of fine emery powder and oil;the former may be caused to stick tothe lead by being slightly forced into it by a few taps with a hammer.The hole is then put on the lap,which is set in rapid rotation,and the article moved up and down;and,being prevented from moving around with the lap,the inside of the hole is ground by the adhering emery.The emery and oil must be continually replenished,and the surface of the lap kept moist with it,as,if allowed to get dry,the two surfaces will bind or cling to each other,and abrasion will result.If the article be heavy,precaution should be taken of turning it over,so as to grind every portion of the hole alike;otherwise the weight of the article,pressing all on one side of the hole,will cause it to be ground more on that side than the others,and the hole will be rendered non-circular.Care must also be taken to keep the middle of the lap well supplied with emery,and not to grind one end or the two ends of the hole larger than the middle.This,however,is a very common occurrence,and requires some little address to get over.Where practicable,it is also advisable to reverse the direction the lathe occasionally,as sometimes,in lapping out a hole,the hole will draw itself onwards,and the workman's whole force will be insufficient to prevent its tightening itself on and binding.In this case,the best way is to either let the work go around with the lap,and to immediately stop the lathe and drive the work back with a mallet before it gets cool and contracts firmly on to the lap;or to reverse the direction of the lathe,when the hole will generally run back of its own accord,unless it is gone on too far and become tight.It is sometimes a very difficult matter to get work off a lap when the grinding surfaces have allowed to get dry and to abrade themselves.威廉·亨利·诺斯考特.论车床和车削:简单,机械,装饰[M].伦敦:朗文公司,2010:104-112.钻和镗(摘录)平的制品最方便的驱动是通过面板,长的制品用螺纹卡盘。
车床机床夹具类外文文献翻译、中英文翻译、外文翻译

中北大学信息商务学院本科毕业设计英文参考资料题目 Lathes系名专业姓名学号指导教师2016年6 月2 日译文标题车床简介原文标题Lathes作者(Serope kalpakjian)译名卡尔帕基安国籍美国原文出处/原文:LathesLathes are machine tools designed primarily to do turning, facing and boring, Very little turning is done on other types of machine tools, and none can do it with equal facility. Because lathes also can do drilling and reaming, their versatility permits several operations to be done with a single setup of the work piece. Consequently, more lathes of various types are used in manufacturing than any other machine tool.The essential components of a lathe are the bed, headstock assembly, tailstock assembly, and the leads crew and feed rod.The bed is the backbone of a lathe. It usually is made of well normalized or aged gray or nodular cast iron and provides s heavy, rigid frame on which all the other basic components are mounted. Two sets of parallel, longitudinal ways, inner and outer, are contained on the bed, usually on the upper side. Some makers use an inverted V-shape for all four ways, whereas others utilize one inverted V and one flat way in one or both sets, They are precision-machined to assure accuracy of alignment. On most modern lathes the way are surface-hardened to resist wear and abrasion, but precaution should be taken in operating a lathe to assure that the ways are not damaged. Any inaccuracy in them usually means that the accuracy of the entire lathe is destroyed.The headstock is mounted in a foxed position on the inner ways, usually at the left end of the bed. It provides a powered means of rotating the word at various speeds . Essentially, it consists of a hollow spindle, mounted in accurate bearings, and a set of transmission gears-similar to a truck transmission—through which the spindle can be rotated at a number of speeds. Most lathes provide from 8 to 18 speeds, usually in a geometric ratio, and on modern lathes all the speeds can be obtained merely by moving from two to four levers. An increasing trend is to provide a continuously variable speed range through electrical or mechanical drives.Because the accuracy of a lathe is greatly dependent on the spindle, it is of heavyconstruction and mounted in heavy bearings, usually preloaded tapered roller or ball types. The spindle has a hole extending through its length, through which long bar stock can be fed. The size of maximum size of bar stock that can be machined when the material must be fed through spindle.The tailsticd assembly consists, essentially, of three parts. A lower casting fits on the inner ways of the bed and can slide longitudinally thereon, with a means for clamping the entire assembly in any desired location, An upper casting fits on the lower one and can be moved transversely upon it, on some type of keyed ways, to permit aligning the assembly is the tailstock quill. This is a hollow steel cylinder, usually about 51 to 76mm(2to 3 inches) in diameter, that can be moved several inches longitudinally in and out of the upper casting by means of a hand wheel and screw.The size of a lathe is designated by two dimensions. The first is known as the swing. This is the maximum diameter of work that can be rotated on a lathe. It is approximately twice the distance between the line connecting the lathe centers and the nearest point on the ways, The second size dimension is the maximum distance between centers. The swing thus indicates the maximum work piece diameter that can be turned in the lathe, while the distance between centers indicates the maximum length of work piece that can be mounted between centers.Engine lathes are the type most frequently used in manufacturing. They areheavy-duty machine tools with all the components described previously and have power drive for all tool movements except on the compound rest. They commonly range in size from 305 to 610 mm(12 to 24 inches)swing and from 610 to 1219 mm(24 to 48 inches) center distances, but swings up to 1270 mm(50 inches) and center distances up to3658mm(12 feet) are not uncommon. Most have chip pans and a built-in coolant circulating system. Smaller engine lathes-with swings usually not over 330 mm (13 inches ) –also are available in bench type, designed for the bed to be mounted on a bench on a bench or cabinet.Although engine lathes are versatile and very useful, because of the time required for changing and setting tools and for making measurements on the work piece, thy are not suitable for quantity production. Often the actual chip-production tine is less than 30% of the total cycle time. In addition, a skilled machinist is required for all the operations, and such persons are costly and often in short supply. However, much of the operator’s time is consumed by simple, repetitious adjustments and in watching chips being made. Consequently, to reduce or eliminate the amount of skilled labor that is required, turret lathes, screw machines, and other types of semiautomatic and automatic lathes have been highly developed and are widely used in manufacturing.2 Numerical ControlOne of the most fundamental concepts in the area of advanced manufacturing technologies is numerical control (NC). Prior to the advent of NC, all machine tools ere manually operated and controlled. Among the many limitations associated with manual control machine tools, perhaps none is more prominent than the limitation of operator skills. With manual control, the quality of the product is directly related to and limited to the skills of the operator. Numerical control represents the first major step away from human control of machine tools.Numerical control means the control of machine tools and other manufacturing systems through the use of prerecorded, written symbolic instructions. Rather than operating a machine tool, an NC technician writes a program that issues operational instructions to the machine tool. For a machine tool to be numerically controlled, it must be interfaced with a device for accepting and decoding the programmed instructions, known as a reader.Numerical control was developed to overcome the limitation of human operators, and it has done so. Numerical control machines are more accurate than manually operated machines, they can produce parts more uniformly, they are faster, and the long-run tooling costs are lower. The development of NC led to the development of several other innovations in manufacturing technology:Electrical discharge machining,Laser cutting,Electron beam welding.Numerical control has also made machine tools more versatile than their manually operated predecessors. An NC machine tool can automatically produce a wide of parts, each involving an assortment of widely varied and complex machining processes. Numerical control has allowed manufacturers to undertake the production of products that would not have been feasible from an economic perspective using manually controlled machine tolls and processes.Like so many advanced technologies, NC was born in the laboratories of the Massachusetts Institute of Technology. The concept of NC was developed in the early 1950s with funding provided by the U.S. Air Force. In its earliest stages, NC machines were able to made straight cuts efficiently and effectively.However, curved paths were a problem because the machine tool had to be programmed to undertake a series of horizontal and vertical steps to produce a curve. The shorter the straight lines making up the steps, the smoother is the curve, Each line segment in the steps had to be calculated.This problem led to the development in 1959 of the Automatically Programmed Tools (APT) language. This is a special programming language for NC that uses statementssimilar to English language to define the part geometry, describe the cutting tool configuration, and specify the necessary motions. The development of the APT language was a major step forward in the fur ther development from those used today. The machines had hardwired logic circuits. The instructional programs were written on punched paper, which was later to be replaced by magnetic plastic tape. A tape reader was used to interpret the instructions written on the tape for the machine. Together, all of this represented a giant step forward in the control of machine tools. However, there were a number of problems with NC at this point in its development.A major problem was the fragility of the punched paper tape medium. It was common for the paper tape containing the programmed instructions to break or tear during a machining process. This problem was exacerbated by the fact that each successive time a part was produced on a machine tool, the paper tape carrying the programmed instructions had to be rerun through the reader. If it was necessary to produce 100 copies of a given part, it was also necessary to run the paper tape through the reader 100 separate tines. Fragile paper tapes simply could not withstand the rigors of a shop floor environment and this kind of repeated use.This led to the development of a special magnetic plastic tape. Whereas the paper carried the programmed instructions as a series of holes punched in the tape, the plastic tape carried the instructions as a series of magnetic dots. The plastic tape was much stronger than the paper tape, which solved the problem of frequent tearing and breakage. However, it still left two other problems.The most important of these was that it was difficult or impossible to change the instructions entered on the tape. To made even the most minor adjustments in a program of instructions, it was necessary to interrupt machining operations and make a new tape. It was also still necessary to run the tape through the reader as many times as there were parts to be produced. Fortunately, computer technology became a reality and soon solved the problems of NC associated with punched paper and plastic tape.The development of a concept known as direct numerical control (DNC) solved the paper and plastic tape problems associated with numerical control by simply eliminating tape as the medium for carrying the programmed instructions. In direct numerical control, machine tools are tied, via a data transmission link, to a host computer. Programs for operating the machine tools are stored in the host computer and fed to the machine tool an needed via the data transmission linkage. Direct numerical control represented a major step forward over punched tape and plastic tape. However, it is subject to the same limitations as all technologies that depend on a host computer. When the host computer goes down, the machine tools also experience downtime. This problem led to the development of computernumerical control.3 TurningThe engine lathe, one of the oldest metal removal machines, has a number of useful and highly desirable attributes. Today these lathes are used primarily in small shops where smaller quantities rather than large production runs are encountered.Th e engine lathe has been replaced in today’s production shops by a wide variety of automatic lathes such as automatic of single-point tooling for maximum metal removal, and the use of form tools for finish on a par with the fastest processing equipment on the scene today.Tolerances for the engine lathe depend primarily on the skill of the operator. The design engineer must be careful in using tolerances of an experimental part that has been produced on the engine lathe by a skilled operator. In redesigning an experimental part for production, economical tolerances should be used.Turret Lathes Production machining equipment must be evaluated now, more than ever before, this criterion for establishing the production qualification of a specific method, the turret lathe merits a high rating.In designing for low quantities such as 100 or 200 parts, it is most economical to use the turret lathe. In achieving the optimum tolerances possible on the turrets lathe, the designer should strive for a minimum of operations.Automatic Screw Machines Generally, automatic screw machines fall into several categories; single-spindle automatics, multiple-spindle automatics and automatic chucking machines. Originally designed for rapid, automatic production of screws and similar threaded parts, the automatic screw machine has long since exceeded the confines of this narrow field, and today plays a vital role in the mass production of a variety of precision parts. Quantities play an important part in the economy of the parts machined on the automatic screw machine. Quantities less than on the automatic screw machine. The cost of the parts machined can be reduced if the minimum economical lot size is calculated and the proper machine is selected for these quantities.Automatic Tracer Lathes Since surface roughness depends greatly on material turned, tooling , and feeds and speeds employed, minimum tolerances that can be held on automatic tracer lathes are not necessarily the most economical tolerances.In some cases, tolerances of 0.05mm are held in continuous production using but one cut . groove width can be held to 0.125mm on some parts. Bores and single-point finishes can be held to 0.0125mm. On high-production runs where maximum output is desirable, a minimum tolerance of 0.125mm is economical on both diameter and length of turn。
机床刀具设计机械加工工艺夹具外文文献翻译、中英文翻译、外文翻译

英语原文:Design Of Tool Machine PropResearch significanceThe original knife machine control procedures are designed individually, not used tool management system, features a single comparison, the knife only has to find the tool knife, knife positioning the shortest path, axis tool change, but does not support large-scale tool.Automatic knife in the knife election, in the computer memory knife-election on the basis of using the Siemens 840 D features, and the election procedures knife more concise, and complete the space Daotao View. ATC use the knife rapid completion of STEP-7 programming, and have been tested in practice. In the positioning of the knife, PLC controlled modular design method, which future production of similar machines will be very beneficial, it is easy to use its other machine. Automatic tool change systems will be faster growth, reduced tool change time, increase the positioning accuracy tool is an important means to help NC technology development.Tool and inventory components of modern production is an important link in the management, especially for large workshop management. The traditional way of account management, and low efficiency, high error rate, and not sharing information and data, tools and the use of state can not track the life cycle, are unable to meet the current information management needs. With actual production, we have to establish a workshop tool for the three-dimensional tool storage system to meet the knife workshop with auxiliary storage and management needs.The system uses optimization technology, a large number of computer storage inventory information, timely, accurate, and comprehensive tool to reflect the inventory situation. The entire system uses a graphical interface, man-machine dialogue tips from the Chinese menu, select various functions can be realized and the importation of all kinds of information. Management system using online help function. Through the workshop management, network management and sharing of information. Have automated inventory management, warehousing management tool, a tool for the management and statistical functions.1.System components and control structureThe entire system, including the structure and electrical machinery control systems.1.1.1Mechanical structure and working principleTool from the stent, drive, drive system, Turret, shielding, control system, and electrical components. Support from the column, beam, the upper and lower guide Central track, and track support component.1) Drive for the system chosen VVVF method. Cone used brake motors, with VVVF by Cycloid reducer through sprocket drive.2) Drag a variable frequency drive system and control technology. VVVF adopted, will speed drive shaft in the normal range adjustment to control the speed rotary turret to 5 ~ 30mm in, the drive shaft into two, two under through sprocket, the two profiled rollers Chain driven rotating shelves. Expansion chain adopted by the thread tight regulation swelling, swelling the regular way. - Conditioned, under the same chain-of-conditioning, so that the chain of uniform.3) Turret and shields the entire total of 14 independent Turret. 13 of them as a socket-Turret, as adrawer-Turret, each Turret back through the pin and, under the conveyor chain link chain plate, installed at the bottom roller, chain driven rotating turret rotation along the track. Outlet-Turret and BT50-BT40 Turret Turret two kinds of forms. To strengthen management, security, landscaping modeling, shelf peripherals and shields. Turret-drawer drawer placed at six other Des V oeux a knife, can be categorized with some of knife auxiliary equipment, such as bits, such as turning tools.1.1.2.Electrical Control SystemThis tool storage systems is the main electrical control their shelves for operational control and position control. Operational control equipment, including operation of the start of braking control. Position Control is the main location and address of the shelves for testing. Control system as shown in Figure 1.图 1 Tool Control System for the1) Electric Transmission horizontal rotary tool storage systems are the mechanical movements are repeated short-term work system. And the run-time system needs some speed, speed transmission needs, the system will use VVVF method can be used simple structure, reliable operation of the motor and frequency inverter.2) Control of the system is divided into two kinds of manual control and automatic control, manual control as a general reserve and debugging methods of work; ways to the system control computer (IPC) and the control unit (inverter contactor , etc.) consisting of a control system.3) location and positioning accuracy of the system automatically identify the site and location using a detection device as proximity switches, relays through the plate-point isolation and the number plate recorded close to the switching signal acquisition and operation of Hutchison with a Optimal Path addressable identify the current location and shelves of the purpose of the shelf location. In order to enable a more accurate positioning system, adopted two photoelectric switches, to detect the two shelves of the two films.1.2.The functions of the knifeknife The is the role of reserves a certain number of tools, machine tool spindle in hand to achieve the fungibility a disc cutter knife is the type of library, the chain knives, and other means, in the form of the knife and capacity according to the Machine Tool to determine the scope of the process.mon typesThe knife is a tool storage devices, the common knife mainly in the following forms:(1) the turret knifeIncluding the first level turret vertical turret and the first two, see Figure 2.6 a) and b):(2) the disc cutterDisc knife in the library with discoid knife, cutting tool along See how vertical arrangement (including radial and axial from knife from knife), along See how radial array into acute or arranged in the form of the knife. Simple, compact, more applications, but are ring-cutter, low utilization of space. Figure 2.7 a) to c). If the knife storage capacity must be increased to increase the diameter of the knife, then the moment of inertia also increased correspondingly, the election campaign long knife. Tool number not more than 32 general. Cutter was multi-loop order of the space utilization knife, but inevitably given the knife from complex institutions, applicable to the restricted space Machine Tool storage capacity and more occasions. Two-disc structure is two smaller capacity knife on both sides of the sub-spindle place, more compact layout, the number of certificates corresponding increase knife, apply to small and medium-sized processing center.(3) the chain knifeIncluding single-and multi-ring chain ring chain, chain link can take ma ny forms change, see Figure 2.8 a) to c), the basic structureFeatures: knife apply to thelarger capacity of theoccasion, the space of thesmall number of generallyapplicable to the tool in the30-120. Only increase thelength of the chain tool willincrease the number shouldnot be increasedcircumferential speed of itsmoment of inertia of theknife does not increase thedisc as large.(4) linear combination knife and the knife libraryThe linear knife simple structure in Figure 2.9, tool single order, the capacity of small knife, used for CNC lathe and drill press on. Because the location of fixed knife, ATC completed action by the spindle without manipulator. The cutter knife is generally the turret combination turret with a combination of the disc cutter knife and the chain combination. Every single knife the knife certificates of smaller, faster tool change. There are also some intensive drum wheel, and the lattice-type magazine for the knife, the knife-intensive though. Small footprint, but because of structural constraints, basically not used for single processing center, the concentration used for FMS for the knife system.1.4 Tool storage capacityTool storage capacity of the first to consider the needs of processing, from the use of point of view, generally 10 to 40 knives, knife will be the utilization of the high, and the structure is compact.1.5 Tool options(1) choose to order processing tool according to the order, followed Add to the knife every knife in the Block. Each tool change, the order of rotation of a cutter knife on location, and remove the need knives, has been used by the cutter knife can be returned to the original Block, can also order Add Block, a knife. However, as the knife in the tool in different processes can not be repeated use of the knife must increase the capacity and lower utilization rate.(2) most of the arbitrary choice of the current system of using arbitrary NC election knives, divided into Daotao coding, coding and memory-cutter, three. Daotao coding tool code or knives or Daotao need to install the code used to identify, in accordance with the general principle of binary coding coding. Tool knife election coding method uses a special knife handle structure, and each of the coding tool. Each of the tool has its own code, thereby cutting tool can be in different processes repeatedly used, not to replace the tool back at the original knife, the knife capacity can be reduced accordingly. Memory-election this paper knife, in this way can knives and knife in the position corresponding to the Daotao memory of the PLC in the NC system, no matter which tool on the Inner knife, tool information is always there in mind, PLC . On the knife with position detection devices, will be the location of each Daotao. This tool can be removed and sent back to arbitrary. On the knife is also a mechanical origin, every election, the nearest knife selection.1.6.Control of the knife(1) the knife as a system to control the positioning axis. In the ladder diagram in accordance with the instructions for computing T code comparison of the output angle and speed of instructions to the knife the knife servo drive servo motor. Tool storage capacity, rotation speed, and / deceleration time, and other system parameters can be set in such a manner free from any outside influence positioning accurate and reliable but the cost is higher.(2) knife from the hydraulic motor drives, fast / slow the points, with proximity switches count and positioning. In comparison ladder diagram of the current storage system knife (knife spindle) and goals knife (pre-knife) and computing, then output rotation instructions, judging by the shortest path rotation in place. This approach requires sufficient hydraulic power and electromagnetic valve knife the rotational speed can be adjusted through the throttle. But over time may be oily hydraulic, oil temperature and environmental factors impact the change in velocity and accuracy. Not generally used in large and medium-sized machine tool change frequently.(3) the knife from AC asynchronous motor driven cam mechanism (Markov institutions), with proximity switches count, which means stable operation, and generally accurate and reliable positioning cam used in conjunction with a mechanical hand, ATC fast-positioning.2. ATC, the main types, characteristics, and the scope of application2.1 Auto Rotary ToolRotary Tool automatically on the useof CNC machine tool is a simpleinstallation of automatic tool change, theQuartet and 47.60 Turret Tool variousforms, such as rotary turret were installedon four, six or more of the Tool , NCinstructions by ATC. Rotary Tool has twovertical and horizontal, relatively simplestructure, applicable to economic CNClathe.Rotary Tool in the structure must havegood strength and stiffness, resistance tobear rough Cutting Tool in the cuttingforce and reduce the role of deformationand improve processing accuracy.Rotating Tool to choose reliablepositioning programme structure andreasonable position, in order to ensure thateach rotary turret to a higher position afterrepeated positioning accuracy (typically0.001 to 0.005mm). Figure 2.1 shows thespiral movements of the Quartet Turret.Auto Rotary Tool in the simplest ofATC, is 180 º rotary ATC devices, asshown in Figure 2.2 ATC instructionsreceived, the machine control system put ATC spindle control to the designated location at the same time, the tool movement to the appropriate location, ATC, with the rotary axis and at the same time, the knives matching tool; drawbars from Spindle Cutting Tools rip, ATC, will be the tool from their position removed; ATC, 180 º rotary tool spindle and the tool and tool away; ATC, the Rotary At the same time, the tool refocusing its position to accept Spindle removed from the cutting tool; Next, ATC, will be replaced with the cutter knives were unloaded into the spindle and tool: Finally, back to the original ATC, "standby" position. At this point, ATC completed procedures to continue to run. This ATC, the main advantage of simple structure, the less movement, fast tool change. The main disadvantage is that knives must be kept in parallel with the axis of the plane, and after the home side compared to the tool, chip and liquid-cutting knife into the folder, it is necessary to the tool plus protection. Cone knife folder on the chip will cause ATC error, or even damage knife folders, and the possibility of spindle. Some processing centre at the transfer, and the tool side. When the ATC command is called, the transfer-cutter knives will be removed, the machine go forward, and positioning with the ATC, in line with the position. 180 º "Rotary ATC devices can be used horizontal machine, can also be used for vertical machining centers.2. 2 ATC head-turret installedWith rotating CNC machine tool often used such ATC devices, with a few turret head spindle, each with a spindle on both knives, the first tower interim process can be automatic tool change-realization. The advantage is simple structure, tool change time is short, only about 2 s. However, due to spatial constraints, the number of spindle can not be too much, usually only apply to processes less, not to high precision machine tools, such as the NC drill, such as CNC milling machine. In recent years there has been a mechanical hand and the turret head with a knife for the automatic tool change ATC devices, as shown in Figure 2.3. It is in fact a turret head ATC, and the knife-ATC device combination. The principle is as follows:5 turret on the first two tool spindle 3 and 4, when using the tool spindle 4 processing tool, the manipulator 2 will be the next step to the need for the tool does not work on the tool spindle 3 until after the completion of this process , the first rotary turret 180 º, ATC completed. ATC most of their time and processing time coincidence, the only real tool change time turret transposition of the first time, this approach mainly used for ATC and NC NC drilling file bed.2. 3.Daidao system for the automatic tool changeFigure 2.4 shows the knife and the whole machine tool CNC machine tools for the appearance of Fig. Figure 2.5 shows the knife and split-type machine to the appearance of CNC machine tool plans.At this point, knife storage capacity, a heavier tool can, and often additional transport unit to complete the knife between the spindle and cutting tool transport.Daidao the knife from the ATC, the election knives, automatic loading and unloading machine tool and tool exchange institutions (manipulator), composed of four parts, used widely.Tool Automatic Tool Change the manipulator system, the whole process more complicated ATC. We must first used in the processing of all installed in the standard tool on the knife handle in the machine outside the pre-size, according to a certain way Add to the knife. ATC, selected first in the knife knife, and then from ATC, from the knife from the knife or spindle, exchange, the new knife into the spindle, the old knife back into the knife.ATC, as the former two knives to accommodate a limited number can not be too many, can not meet the needs of complex parts machining, CNC machine tool Automatic Tool Change Daidao the use of the automatic tool change devices. The knife has more capacity, both installed in the spindle box side or above. As for the automatic tool change Daidao device CNC machine tool spindle box only a spindle, spindle components to high stiffness to meet the machining requirements. The number of establishments in larger knife, which can meet the more complex parts of the machining processes, significantly improving productivity. Daidao system for the automatic tool change applied to drilling centres and CNC machining centers. The comparison drawn Daidao automatic tool change system is the most promising.3.PLC control of the knife random mode of election 3. 1Common methods of automatic election knifeAutomatic control of the knife CNC refers to the system after the implementation of user instructions on the knife library automation process, including the process to find knives and automatic tool change [(63,71]. CNC Machining Center device (CNC) directive issued by the election knife , a knife, the tool required to take the knife position, said the election automatic knife. automatically elected knife There are two ways: random sequence election knives and knife election method.3.1.1 order election knifeTool Selection order is the process tool according to the sequence of the insert knife, the use of knives in order to take place, used knives back at the original knife, can also order Add Block, a knife. In this way, no need Tool identification devices, and drive control is a relatively simple, reliable and can be used directly from the points of the knife machinery to achieve. But the knives in each of the tool in different processes can not be reused, if the tool is installed in accordance with the order of the knife, there will be serious consequences. The need to increase the number of knives and knife the capacity of the tool and reduce the utilization of the knife.3.1.2Random election knifeRandom election under the knife is arbitrary instructions to select the required tools, then there must be tool identification devices. Tool knife in the library do not have the processing in accordance with the order of the workpiece can be arbitrary storage. Each of the tool (or knife blocks) are for a code, automatic tool change, the rotary cutter, every tool have been the "tool identification device" acceptable identification. When CNC tool code and the code in line with directives of the tool selected, the rotary cutter knives will be sent to the ATC position, waiting to grab manipulator. Random knife election is the advantage of the cutter knife in the order has nothing to do with the processing sequence, the same tool can be used repeatedly. Therefore, the relatively small number of knives, knife the corresponding smaller. Random elections knife on the tool must be coded to identify. There are three main coding.1. Tool coding. Adopt special knife handle structure coding, the drawbars on the knife handle back-end packages such as spacing of the coding part of the lock-nut fixed. Coding diameter ring diameter of a size two, respectively, said that binary "1" and "0" to the two rings are different, can be a series of code. For example, there are six small diameter of the ring can be made to distinguish between 63 (26-1 = 63) of the coding tool. All of 0 normally not allowed to use the code, to avoid the cutter knife Block did not confuse the situation.2. Knife Block coding. On the knife Block coding, coding tool, and tool into line with the number of knives in the Block. ATC knife when the rotation, so that each knife seats followed through knowledge knife, knife found blocks, knives stopped the rotation. At this time there is no knife handle encoding part of the knife handle simplified.3. Annex coding methods. This style of coding keys, coded cards, coding and coding-disc, which is the most widely used coding keys. First toknives are attached to a tool of the show wrapped coding keys, and when the cutter knife to the store at knife in, so put the number of keys to remember knife Block Road, will be inserted into key to the coding Block next to the key hole in the seat for the knife to the numbers. ConclusionFocused on in today's manufacturing environment tool storage and management of new models and methods, practical application of good results in systems integration and optimization, and other aspects of operations will be further explored, so that it has a higher theoretical and practical level.译文:机床刀具设计课题研究意义机床原来的刀库控制程序是单独设计的,没有采用刀具管理系统,功能也比较单一,只实现了刀库刀具的找刀、刀库最短路径定位、主轴换刀,而且不支持大型刀具。
机床行业中英文对照
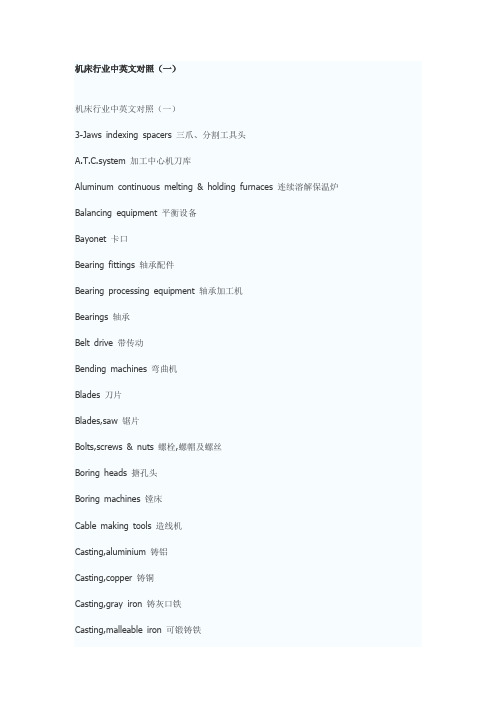
机床行业中英文对照(一)机床行业中英文对照(一)3-Jaws indexing spacers 三爪、分割工具头A.T.C.system 加工中心机刀库Aluminum continuous melting & holding furnaces 连续溶解保温炉Balancing equipment 平衡设备Bayonet 卡口Bearing fittings 轴承配件Bearing processing equipment 轴承加工机Bearings 轴承Belt drive 带传动Bending machines 弯曲机Blades 刀片Blades,saw 锯片Bolts,screws & nuts 螺栓,螺帽及螺丝Boring heads 搪孔头Boring machines 镗床Cable making tools 造线机Casting,aluminium 铸铝Casting,copper 铸铜Casting,gray iron 铸灰口铁Casting,malleable iron 可锻铸铁Casting,other 其他铸造Casting,steel 铸钢Chain drive 链传动Chain making tools 造链机Chamfer machines 倒角机Chucks 夹盘Clamping/holding systems 夹具/支持系统CNC bending presses 电脑数控弯折机CNC boring machines 电脑数控镗床CNC drilling machines 电脑数控钻床CNC EDM wire-cutting machines 电脑数控电火花线切削机CNC electric discharge machines 电脑数控电火花机CNC engraving machines 电脑数控雕刻机CNC grinding machines 电脑数控磨床CNC lathes 电脑数控车床CNC machine tool fittings 电脑数控机床配件CNC milling machines 电脑数控铣床CNC shearing machines 电脑数控剪切机CNC toolings CNC刀杆CNC wire-cutting machines 电脑数控线切削机Conveying chains 输送链Coolers 冷却机Coupling 联轴器Crimping tools 卷边工具Cutters 刀具Cutting-off machines 切断机Diamond cutters 钻石刀具Dicing saws 晶圆切割机Die casting dies 压铸冲模Die casting machines 压铸机Dies-progressive 连续冲模Disposable toolholder bits 舍弃式刀头Drawing machines 拔丝机Drilling machines 钻床Drilling machines bench 钻床工作台Drilling machines,high-speed 高速钻床Drilling machines,multi-spindle 多轴钻床Drilling machines,radial 摇臂钻床Drilling machines,vertical 立式钻床drills 钻头Electric discharge machines(EDM) 电火花机Electric power tools 电动刀具Engraving machines 雕刻机Engraving machines,laser 激光雕刻机Etching machines 蚀刻机Finishing machines 修整机Fixture 夹具Forging dies 锻模Forging,aluminium 锻铝Forging,cold 冷锻Forging,copper 铜锻Forging,other 其他锻造Forging,steel 钢锻Foundry equipment 铸造设备Gear cutting machines 齿轮切削机Gears 齿轮Gravity casting machines 重力铸造机Grinder bench 磨床工作台Grinders,thread 螺纹磨床Grinders,tools & cutters 工具磨床Grinders,ultrasonic 超声波打磨机Grinding machines 磨床Grinding machines,centerless 无心磨床Grinding machines,cylindrical 外圆磨床Grinding machines,universal 万能磨床Grinding tools 磨削工具Grinding wheels 磨轮Hand tools 手工具Hard/soft and free expansion sheet making plant 硬(软)板(片)材及自由发泡板机组Heat preserving furnaces 保温炉Heating treatment funaces 熔热处理炉Honing machines 搪磨机Hydraulic components 液压元件Hydraulic power tools 液压工具机床行业中英文对照(一)Hydraulic power units 液压动力元件Hydraulic rotary cylinders 液压回转缸Jigs 钻模Lapping machines 精研机Lapping machines,centerless 无心精研机Laser cutting 激光切割Laser cutting for SMT stensil 激光钢板切割机Lathe bench 车床工作台Lathes,automatic 自动车床Lathes,heavy-duty 重型车床Lathes,high-speed 高速车床Lathes,turret 六角车床Lathes,vertical 立式车床Lubricants 润滑液Lubrication Systems 润滑系统Lubricators 注油机Machining centers,general 通用加工中心Machining centers,horizontal 卧式加工中心Machining centers,horizontal & vertical 卧式及立式加工中心Machining centers,vertical 立式加工中心Machining centers,vertical double-column type 立式双柱加工中心Magnetic tools 磁性工具Manifolds 集合管Milling heads 铣头Milling machines 铣床Milling machines,bed type 床身式铣床Milling machines,duplicating 仿形铣床Milling machines,horizontal 卧式铣床Milling machines,turret vertical 六角立式铣床Milling machines,universal 万能铣床Milling machines,vertical 立式铣床Milling machines,vertical & horizontal 立式及卧式铣床Mold & die components 模具单元Mold changing systems 换模系统Mold core 模芯Mold heaters/chillers 模具加热器/冷却器Mold polishing/texturing 模具打磨/磨纹Mold repair 模具维修Molds 模具Nail making machines 造钉机Oil coolers 油冷却器Overflow cutting machines for aluminium wheels 铝轮冒口切断机P type PVC waterproof rolled sheet making plant P型PVC高分子防水PCB fine piecing systems 印刷电器板油压冲孔脱料系统Pipe & tube making machines 管筒制造机Planing machines 刨床Planing machines vertical 立式刨床Pneumatic hydraulic clamps 气油压虎钳Pneumatic power tools 气动工具Powder metallurgic forming machines 粉末冶金成型机Presses,cold forging 冷锻冲压机presses,crank 曲柄压力机Presses,eccentric 离心压力机Presses,forging 锻压机Presses,hydraulic 液压冲床Presses,knuckle joint 肘杆式压力机Presses,pneumatic 气动冲床Presses,servo 伺服冲床Presses,transfer 自动压力机Pressing dies 压模Punch formers 冲子研磨器Quick die change systems 速换模系统Quick mold change systems 快速换模系统Reverberatory furnaces 反射炉Rollers 滚筒Rolling machines 辗压机Rotary tables 转台Sawing machines 锯床Sawing machines,band 带锯床Saws,band 带锯Saws,hack 弓锯Saws,horizontal band 卧式带锯Saws,vertical band 立式带锯shafts 轴Shapers 牛头刨床Shearing machines 剪切机Sheet metal forming machines 金属板成型机Sheet metal working machines 金属板加工机Slotting machines 插床spindles 主轴Stamping parts 冲压机Straightening machines 矫直机Switches & buttons 开关及按钮Tapping machines 攻螺丝机Transmitted chains 传动链Tube bending machines 弯管机Vertical hydraulic broaching machine 立式油压拉床Vises 虎钳Vises,tool-maker 精密平口钳Wheel dressers 砂轮修整器机床行业中英文对照(一)Woven-Cutting machines 织麦激光切割机Wrenches 扳手。
机械加工工艺装备夹具外文文献翻译、中英文翻译、外文翻译
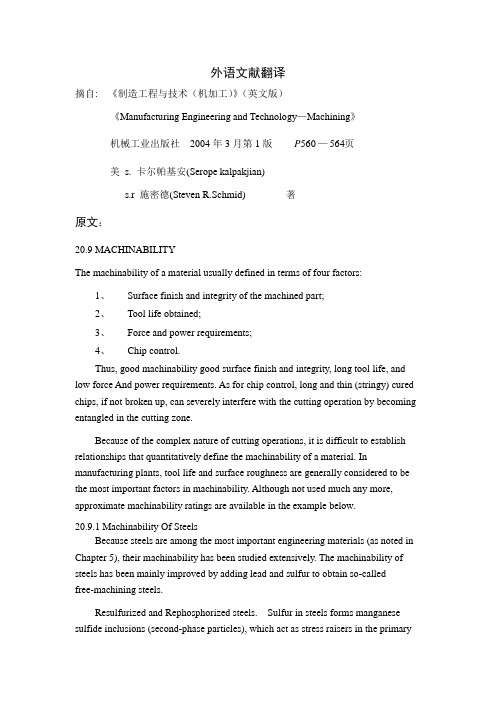
外语文献翻译摘自: 《制造工程与技术(机加工)》(英文版)《Manufacturing Engineering and Technology —Machining 》机械工业出版社 2004年3月第1版 页—564560P美 s. 卡尔帕基安(Serope kalpakjian)s.r 施密德(Steven R.Schmid) 著原文:20.9 MACHINABILITYThe machinability of a material usually defined in terms of four factors:1、Surface finish and integrity of the machined part; 2、Tool life obtained; 3、Force and power requirements; 4、 Chip control.Thus, good machinability good surface finish and integrity, long tool life, and low force And power requirements. As for chip control, long and thin (stringy) cured chips, if not broken up, can severely interfere with the cutting operation by becoming entangled in the cutting zone.Because of the complex nature of cutting operations, it is difficult to establish relationships that quantitatively define the machinability of a material. Inmanufacturing plants, tool life and surface roughness are generally considered to be the most important factors in machinability. Although not used much any more, approximate machinability ratings are available in the example below.20.9.1 Machinability Of SteelsBecause steels are among the most important engineering materials (as noted in Chapter 5), their machinability has been studied extensively. The machinability of steels has been mainly improved by adding lead and sulfur to obtain so-called free-machining steels.Resulfurized and Rephosphorized steels. Sulfur in steels forms manganese sulfide inclusions (second-phase particles), which act as stress raisers in the primaryshear zone. As a result, the chips produced break up easily and are small; this improves machinability. The size, shape, distribution, and concentration of these inclusions significantly influence machinability. Elements such as tellurium and selenium, which are both chemically similar to sulfur, act as inclusion modifiers in resulfurized steels.Phosphorus in steels has two major effects. It strengthens the ferrite, causing increased hardness. Harder steels result in better chip formation and surface finish. Note that soft steels can be difficult to machine, with built-up edge formation and poor surface finish. The second effect is that increased hardness causes the formation of short chips instead of continuous stringy ones, thereby improving machinability.Leaded Steels. A high percentage of lead in steels solidifies at the tip of manganese sulfide inclusions. In non-resulfurized grades of steel, lead takes the form of dispersed fine particles. Lead is insoluble in iron, copper, and aluminum and their alloys. Because of its low shear strength, therefore, lead acts as a solid lubricant (Section 32.11) and is smeared over the tool-chip interface during cutting. This behavior has been verified by the presence of high concentrations of lead on thetool-side face of chips when machining leaded steels.When the temperature is sufficiently high-for instance, at high cutting speeds and feeds (Section 20.6)—the lead melts directly in front of the tool, acting as a liquid lubricant. In addition to this effect, lead lowers the shear stress in the primary shear zone, reducing cutting forces and power consumption. Lead can be used in every grade of steel, such as 10xx, 11xx, 12xx, 41xx, etc. Leaded steels are identified by the letter L between the second and third numerals (for example, 10L45). (Note that in stainless steels, similar use of the letter L means “low carbon,” a condition that improves their corrosion resistance.)However, because lead is a well-known toxin and a pollutant, there are serious environmental concerns about its use in steels (estimated at 4500 tons of lead consumption every year in the production of steels). Consequently, there is a continuing trend toward eliminating the use of lead in steels (lead-free steels). Bismuth and tin are now being investigated as possible substitutes for lead in steels.Calcium-Deoxidized Steels. An important development is calcium-deoxidized steels, in which oxide flakes of calcium silicates (CaSo) are formed. These flakes, in turn, reduce the strength of the secondary shear zone, decreasing tool-chip interfaceand wear. Temperature is correspondingly reduced. Consequently, these steels produce less crater wear, especially at high cutting speeds.Stainless Steels. Austenitic (300 series) steels are generally difficult to machine. Chatter can be s problem, necessitating machine tools with high stiffness. However, ferritic stainless steels (also 300 series) have good machinability. Martensitic (400 series) steels are abrasive, tend to form a built-up edge, and require tool materials with high hot hardness and crater-wear resistance. Precipitation-hardening stainless steels are strong and abrasive, requiring hard and abrasion-resistant tool materials.The Effects of Other Elements in Steels on Machinability. The presence of aluminum and silicon in steels is always harmful because these elements combine with oxygen to form aluminum oxide and silicates, which are hard and abrasive. These compounds increase tool wear and reduce machinability. It is essential to produce and use clean steels.Carbon and manganese have various effects on the machinability of steels, depending on their composition. Plain low-carbon steels (less than 0.15% C) can produce poor surface finish by forming a built-up edge. Cast steels are more abrasive, although their machinability is similar to that of wrought steels. Tool and die steels are very difficult to machine and usually require annealing prior to machining. Machinability of most steels is improved by cold working, which hardens the material and reduces the tendency for built-up edge formation.Other alloying elements, such as nickel, chromium, molybdenum, and vanadium, which improve the properties of steels, generally reduce machinability. The effect of boron is negligible. Gaseous elements such as hydrogen and nitrogen can have particularly detrimental effects on the properties of steel. Oxygen has been shown to have a strong effect on the aspect ratio of the manganese sulfide inclusions; the higher the oxygen content, the lower the aspect ratio and the higher the machinability.In selecting various elements to improve machinability, we should consider the possible detrimental effects of these elements on the properties and strength of the machined part in service. At elevated temperatures, for example, lead causes embrittlement of steels (liquid-metal embrittlement, hot shortness; see Section 1.4.3), although at room temperature it has no effect on mechanical properties.Sulfur can severely reduce the hot workability of steels, because of the formation of iron sulfide, unless sufficient manganese is present to prevent such formation. Atroom temperature, the mechanical properties of resulfurized steels depend on the orientation of the deformed manganese sulfide inclusions (anisotropy). Rephosphorized steels are significantly less ductile, and are produced solely to improve machinability.20.9.2 Machinability of Various Other MetalsAluminum is generally very easy to machine, although the softer grades tend to form a built-up edge, resulting in poor surface finish. High cutting speeds, high rake angles, and high relief angles are recommended. Wrought aluminum alloys with high silicon content and cast aluminum alloys may be abrasive; they require harder tool materials. Dimensional tolerance control may be a problem in machining aluminum, since it has a high thermal coefficient of expansion and a relatively low elastic modulus.Beryllium is similar to cast irons. Because it is more abrasive and toxic, though, it requires machining in a controlled environment.Cast gray irons are generally machinable but are. Free carbides in castings reduce their machinability and cause tool chipping or fracture, necessitating tools with high toughness. Nodular and malleable irons are machinable with hard tool materials.Cobalt-based alloys are abrasive and highly work-hardening. They require sharp, abrasion-resistant tool materials and low feeds and speeds.Wrought copper can be difficult to machine because of built-up edge formation, although cast copper alloys are easy to machine. Brasses are easy to machine, especially with the addition pf lead (leaded free-machining brass). Bronzes are more difficult to machine than brass.Magnesium is very easy to machine, with good surface finish and prolonged tool life. However care should be exercised because of its high rate of oxidation and the danger of fire (the element is pyrophoric).Molybdenum is ductile and work-hardening, so it can produce poor surface finish. Sharp tools are necessary.Nickel-based alloys are work-hardening, abrasive, and strong at high temperatures. Their machinability is similar to that of stainless steels.Tantalum is very work-hardening, ductile, and soft. It produces a poor surfacefinish; tool wear is high.Titanium and its alloys have poor thermal conductivity (indeed, the lowest of all metals), causing significant temperature rise and built-up edge; they can be difficult to machine.Tungsten is brittle, strong, and very abrasive, so its machinability is low,although it greatly improves at elevated temperatures.Zirconium has good machinability. It requires a coolant-type cutting fluid,however, because of the explosion and fire.20.9.3 Machinability of Various MaterialsGraphite is abrasive; it requires hard, abrasion-resistant, sharp tools.Thermoplastics generally have low thermal conductivity, low elastic modulus, and low softening temperature. Consequently, machining them requires tools with positive rake angles (to reduce cutting forces), large relief angles, small depths of cut and feed, relatively high speeds, andproper support of the workpiece. Tools should be sharp.External cooling of the cutting zone may be necessary to keep the chips from becoming “gummy” and sticking to the tools. Cooling can usually be achieved with a jet of air, vapor mist, or water-soluble oils. Residual stresses may develop during machining. To relieve these stresses, machined parts can be annealed for a period of time at temperatures ranging from C ︒80 to C ︒160 (F ︒175to F ︒315), and then cooled slowly and uniformly to room temperature.Thermosetting plastics are brittle and sensitive to thermal gradients duringcutting. Their machinability is generally similar to that of thermoplastics.Because of the fibers present, reinforced plastics are very abrasive and aredifficult to machine. Fiber tearing, pulling, and edge delamination are significant problems; they can lead to severe reduction in the load-carrying capacity of the component. Furthermore, machining of these materials requires careful removal of machining debris to avoid contact with and inhaling of the fibers.The machinability of ceramics has improved steadily with the development of nanoceramics (Section 8.2.5) and with the selection of appropriate processing parameters, such as ductile-regime cutting (Section 22.4.2).Metal-matrix and ceramic-matrix composites can be difficult to machine, depending on the properties of the individual components, i.e., reinforcing or whiskers, as well as the matrix material.20.9.4 Thermally Assisted MachiningMetals and alloys that are difficult to machine at room temperature can be machined more easily at elevated temperatures. In thermally assisted machining (hot machining), the source of heat—a torch, induction coil, high-energy beam (such as laser or electron beam), or plasma arc—is forces, (b) increased tool life, (c) use of inexpensive cutting-tool materials, (d) higher material-removal rates, and (e) reduced tendency for vibration and chatter.It may be difficult to heat and maintain a uniform temperature distribution within the workpiece. Also, the original microstructure of the workpiece may be adversely affected by elevated temperatures. Most applications of hot machining are in the turning of high-strength metals and alloys, although experiments are in progress to machine ceramics such as silicon nitride.SUMMARYMachinability is usually defined in terms of surface finish, tool life, force and power requirements, and chip control. Machinability of materials depends not only on their intrinsic properties and microstructure, but also on proper selection and control of process variables.译文:20.9 可机加工性一种材料的可机加工性通常以四种因素的方式定义:1、分的表面光洁性和表面完整性。
机械工程及自动化组合镗床中英文对照外文翻译文献
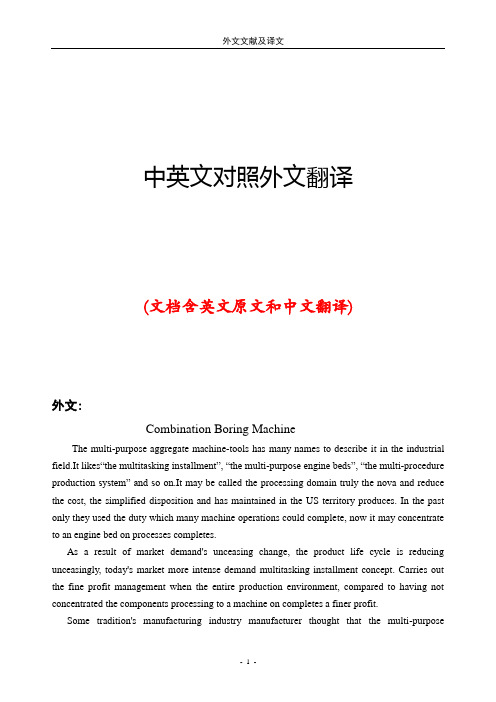
中英文对照外文翻译(文档含英文原文和中文翻译)外文:Combination Boring MachineThe multi-purpose aggregate machine-tools has many names to describe it in the industrial field.It likes“the multitasking installment”, “the multi-purpose engine beds”, “the multi-procedure pr oduction system” and so on.It may be called the processing domain truly the nova and reduce the cost, the simplified disposition and has maintained in the US territory produces. In the past only they used the duty which many machine operations could complete, now it may concentrate to an engine bed on processes completes.As a result of market demand's unceasing change, the product life cycle is reducing unceasingly, today's market more intense demand multitasking installment concept. Carries out the fine profit management when the entire production environment, compared to having not concentrated the components processing to a machine on completes a finer profit.Some tradition's manufacturing industry manufacturer thought that the multi-purposeaggregate machine-tools are too complex, very difficult to find the appropriate operators also the difficult problem innovates on the spot on the insufficiency for the metal working basic principle and in the Production workshop related new engine bed use solution aspect training.Intuition type technical controlThe equipment use “carries off the quantity of heat” the type design, has different material which the lathe bed, the steeliness straight line rolling guide, on the steeliness revolving tool box saddle, the equipment uses, all these combine make an engine bed together. These with the thermal conductivity, the volume expansion are related. All different size's thing can by the different speed growth.As a result of this reason, needs to make the hot friendly engine bed, with the aim of knowing gives off heat the weak point in where, can compensate through the reasonable engine bed design. The part is the entire journey movement. The engine bed glide produces rubs and transform hotly. The machining produces the hot filings fall to the different place, the refrigerant can mix in the entire process in which. Will present the different temperature province continually on the cutting tool, will therefore also have many things to have the influence to the thermostability. The cutting tool technology turned the multi-purpose aggregate machine-tools has had the milling and cutting power “the versatile machine”.According to the material introduced that the most remarkable characteristic is in these engine bed whole has the intuition. The anti-collision preservation technology was already mature, in certain circumstances, even if uses the manual operation pattern, can also avoid the occurrence which collides. Because the control software has the very good intuition, the user operation friendly degree unceasingly is also enhancing. Believe the multi-purpose aggregate machine-tools by its survivability world-wide in the more different processing scenes.The off-line programming optimization and the NC automatic control system's formation already made this technology to be easier to accept, when therefore uses the procedure when the engine bed, does not need to spend many time tune-up procedure and confirmed that some part does not have the question. If components need to provide the high and low two revolving tool box saddle simultaneously to carry on the rough machining, in this kind of situation the programming is quite difficult, because it needs two revolving tool box saddles also to feed. The AdMac system may realize tool rest's automatic programming which simultaneously feeds to these, and can cause the correct main axle speed, the correct feed rate and so on all parameters to realize the synchronization.Okuma Corporation's collision avoidance system design based on actual processing operating mode anti-collision simulation, therefore, if the operator has installed the wrong cutting tool orhas established the wrong parameter, the control system will examine and prevents the engine bed to enter the processing condition. Through cooperates with the Siemens, INDEX Corporation may provide the 3D pattern now “the hypothesized engine bed”, has custom-made according to some specific model's engine bed. The result indicated that the simulation processes not only the fabricated parts and the actual end product is similar, is the one-to-one copy simply.The intuition type control interface, the simulation as well as other software technique are progressive, the more Production workshops have opened wide the front door to the multi-purpose aggregate machine-tools, but if does not have the corresponding knowledge to train and to solve the question creativity, the manufacturer is also very difficult to realize and the full use advanced engine bed flexibility aspect superiority. The work which does to the machine are more, the machine will be more complex, also needs to have the stronger skill person correspondingly to be able to operate it.If machinist past one day operated 3 engine beds, then he has this kind of multi-purpose engine bed now, might produce more components. More importantly, he may draw support from software's help to cause the production efficiency to be higher, regarding transformation processing components preparation, may also establish the processing craft plan. Because the replacement components need to lower 3 main axles, therefore before replacing the components, the workshop should process as far as possible many components. Regarding the multi-purpose engine beds, the transformation components speed is quick, the production batch of time interval is shorter, the stock is lower, the production efficiency is higher. Can use multi-purpose engine bed's some workshops fully, very quick will discover the post function the unification. Now, a workshop may only use an operator, an adjuster and a programming teacher, in the future these 3 work definitely may do by a person.In the traditional post description the machinist will transit becomes one to adjust engineer, if this engineer the familiar components processing programming, that were also more ideal. Regarding such transformation, training has been simple, so long as trains 1 individual line, but is not 3 individuals. Looking from the long views, this will provide to the people the higher post degree of satisfaction. When adjusts engineer to be responsible to process the programming, and pays attention to the components processing personally time the entire process, he completely has become this components control. In addition, but should also makes more effort in the cutting tool choice and the programming aspect, must make any model the multi-purpose aggregate machine-tool to succeed, the workshop needs to provide the skilled machinist, has ability and completes many kinds of operations nimbly. Therefore, crosswise training was at any time in the past more important. Regarded as the milling and the lathe work the different discipline theviewpoint never to return. Regarding the programmers, this belongs to their time. Regarding personnel who will program, will understand the engine bed and controls it, this will be their ability manifestation.The cutting tool will choose most people not to install the passenger vehicle tire to the race car on, but processed the cutting tool to have such situation. The cutting tool should match with the new engine bed, is conceivably redundant on the new engine bed uses the old cutting tool to the production efficiency influence. In order to match the multi-purpose aggregate machine-tools, the new cutting tool and the cutting tool adapter technology was already developed. At present the industrial field is developing the development the processing cutting tool, may complete the turning on the identical tool rest, boring and drills truncates the processing, is only processes the phase to differ from regarding the work piece angle. The processing operates the difference even confuses is unclear. The new processing cutting tool may complete the milling and the turning.Since has moved the technology (engine bed) is this century develops is extremely rapid and one of influence enormous science and technology. The modern automation technology is one kind of completely new productive forces, is one of direct creation public wealth principal means that is playing the enormous promotion effect to humanity's production activity and the material civilization. Therefore, the automated technology receives various countries widely to take seriously with more and more applications. The machinery automation (engine bed), mainly refers to the machine-building industry applies the automated technology, realizes the processing object continuously the automatic production, realizes the optimized effective automatic production process, the increase production investment processing transformation and the flow rate. The machinery automation technology's application and the development, are the machine-building industry technological transformations, the technology advancement principal means and the technological development main direction. Machinery automation technical standards, not only affects the entire machine-building industry the development, and has the very tremendous immediate influence to the national economy various departments' technology advancement. Therefore, develops our country's machine-building industry automation technology, conforms to our country socialism basic principle, conforms to our country modern production law of development. How to develop our country's machinery automation technology (engine bed), here has the technical policy question, should be realistic, all embark from our country's concrete national condition, do each foundation work, takes the China's road of machinery automation technological development. The domestic and foreign industry history tells us, realizes the machinery automation is from to high-level, from simply to complex, from is preliminarily imperfect the consummation the developing process. After machine's operation usesthe automatic regulator, the production method only then gradually transits from the mechanization to the mechanism control (tradition) automated, the numerical control automation, the computer control automation. Only then after having established the Automated factory, the production process can overall automate, can make the productivity to enhance comprehensively, achieves automated the high-level ideal stage.The machinery automation technology first starts from the 1920s in the machine manufacture cold finishing production in enormous quantities process to develop the application, after in the 60s, to adapt the market demand and the change, for the enhancement machine-building industry to the market nimble rapid reaction's ability, starts to establish the variable automation production system, namely revolves the computer technology the flexible automation. It is in the manufacture system invariable or in the change small situation, the machinery equipment either production management process through the automatic detection, the information processing, the analysis judgment realizes the anticipated operation or some kind of process automatically, and can from make one kind of components to transform automatically to makes another kind of different components. The social practice proved that under this kind of definition's manufacture system automation and the contemporary majority enterprises are not actually accommodating. The contemporary society also not in the science and technology, the material and the personnel aspect prepares to realize this automated condition, insists such to do only meets the wasted effort. This kind of situation is not exceptional regarding the separate production method's machine-building industry, the difficulty can bigger.In the 80s internationally appeared started to use computer integration manufacture system CIMS (Computer Integrated Manufacturing), the flexible automation production pattern also had this kind of situation. The initial period take the information integration as a key point, take the high automaticity as the characteristic, but in realized in the process to encounter the difficulty. In view of the fact that realizes the large amount investment which the computer integration manufacture system's automation overall needs (an overall Automated factory to spend several hundred hundred million US dollars, flexible manufacture system regular price is 600 ~ 25,000,000 US dollars), undertakes the huge risk, in addition questions and so on technical difficulty and reliability, the world industrially advanced country started “to run into a wal l produces a different product”, transfers pays great attention the information integration the effect, pursues low cost automation LCA (Low Cost Automation) enterprise organizational structure and movement way.The aggregate machine-tool future development more use transmissions and so on variable speed motor and ball bearing guide screw, will simplify structure, the reduction production metre;Uses the numerical control system and the headstock, the jig automatic replacement system, enhances the craft controllability; As well as integrates the flexible manufacture system and so on.The aggregate machine-tool is take the general part as a foundation, matches by presses the work piece specific shape and the processing technological design special-purpose part and the jig, the composition semiautomatic or the automatic special purpose machine. The aggregate machine-tool selects the method which generally multiple spindle, the multi-knives, the multi-working procedures, many or the multi-locations simultaneously process, production efficiency ratio general engine bed high several times to several dozens times. Because the general part already the standardization and the seriation, might according to need to dispose nimbly, could reduce the design and the manufacturing cycle. The multi-axle-boxes are aggregate machine-tool's core parts. It selects the common parts, carries on the design according to the special-purpose request, in the aggregate machine-tool design's process, is one of work load big parts. It is acts according to the work piece processing hole quantity which and the position the working procedure chart and the processing schematic drawing determined, the cutting specifications and the main axle type design transmission various main axles movement power unit. Its power from the general power box, installs together with the power box in to feed sliding table, may complete drills, twists and so on working processes. This topic designed has used in the HT200 top head hole processing the drill hole aggregate machine-tool. According to the top head hole components size which must process carries on the aggregate machine-tool general multi-axle-boxes the design, draws up the multi-axle-box primitive basis chart, the definite main axle and the gear modulus, determined the transmission system, calculates the main axle and drive shaft's coordinate. Through the above design, realized a top head one-sided six processing to complete, has achieved the design requirements well。
- 1、下载文档前请自行甄别文档内容的完整性,平台不提供额外的编辑、内容补充、找答案等附加服务。
- 2、"仅部分预览"的文档,不可在线预览部分如存在完整性等问题,可反馈申请退款(可完整预览的文档不适用该条件!)。
- 3、如文档侵犯您的权益,请联系客服反馈,我们会尽快为您处理(人工客服工作时间:9:00-18:30)。
中国地质大学长城学院本科毕业设计外文资料翻译系别:工程技术系专业:机械制造设计及其自动化姓名:李旭学号: 052115012015年 4 月 2 日英文翻译原文:(一)镗削加工和镗床像车床加工零件一样,镗床能在中空的工件或由钻削加工或其它工艺所加工的孔上进行内轮廓圆的加工。
镗削是由那些类似车削的刀具完成的。
因为镗头必须达到镗杆的全长,刀具将发生弯曲,因此,尺寸精度的保持性成为了一个重大问题。
镗杆必须有足够的刚度——刀杆是由较高弹性模量的材料制造的,比如碳化钨(硬质合金)——去减小弯曲和避免摇动和振动。
镗杆被设计有减振的能力。
镗床既能加工在车床上加工的较小工件,镗铣床又能加工巨大的工件。
这类机械既有立式的又有卧式的并且能够完成如:车削、车端面、切槽、和倒角。
一台立式的镗床类似一台车床,但它有一根垂直的工件旋转轴。
刀具(通常用于切削的单独切削点是由M-2和M-3高速钢和C-8硬质合金制造的)被安装于能垂直运动(用于镗削和车削)和径向运动(用于车端面)并由十字导轨导向的刀头上。
刀头能够旋转去加工圆锥形表面。
在卧式镗床上工件被装夹在能在水平面内两个轴向和径向上移动的工作台上,刀具被安装于能做垂直和纵向两方向上运动的主轴箱上。
钻头、铰刀、螺纹刀和铣刀都能安装于机床主轴上。
镗床具有许多优良的性能,它所加工工件的直径是1m-4m(3ft-12ft),工件尺寸达到20m(60ft)的可在专用的立式镗床上加工。
机床功率范围可达到150kw(200hp)。
这些可用于所有运动都能编程的数字控制加工。
利用这些控制,只需要很少的相关操作,并且稳定性和生产率大大提高了。
镗床的切削速度和进给速度和车床比较相似。
坐标镗床是属于具有较高精度支撑的立式镗床。
尽管它们可用于各类尺寸的工件加工和拥有夹紧合安装的刀具空间。
它们正被多功能的数控机床取代。
镗床的设计要求:导轨的效率,类似于车削的经济型操作,另外,应该考虑以下因素:a.无论何时,应尽可能注意是加工通孔而并盲孔。
(盲孔系列是指那些没有穿国工件厚度的孔)b.应该控制径向进给速率,很难去支撑径向,因为切削力引起镗杆的弯曲变形。
c.应该避免交叉的内表面加工。
(2)机床基础为了满足规定的设计规格,大多数情况下初步加工的产品都必须再经过进一步的尺寸和表面的精加工。
要达到这样的精确规定公差的要求,少量材料需要被切除掉,而机床通常就是用于此种操作。
在美国,材料切除是一项大业务——每年这方面的支出超过36×109美元,包括材料、劳力和机床运输。
60%的机械工程和工业工程毕业生都通过贸易、设计、机械修理工厂,或通过在相关行业工作而与机械工业密不可分,因而如果他们花费一定的时间精力来学习这个领域中的材料切除和机床技术的话会是很明智的选择。
机床提供切割工具的方式,以使工件成型,达到规定的尺寸;此种机器依靠其基础部件的运作来掌握工具和工件之间的联系。
其基础部件的运作如下:①.床身、构造和框架。
这三种主要的部件为锭子和滑移的基础,并将它们联系起来;操作中的变形和震动必须尽量避免。
②.滑移与滑轨。
机械部件(如滑移)的转换通常是通过在精密的指导表面(滑轨)的控制下做直线运动而完成的。
③.锭子与轴承。
角位移是围绕一个旋转轴线发生的;这个转轴的位置必须一直处于严格精确的限制之中,并由精密锭子和轴承提供保障。
④.动力仪器。
电动机是被广泛应用于机床的动力仪器。
通过将各电动机放置于合适的位置,传输带和齿轮运输会被降低到最低限度。
⑤.传输联接。
联接是一个通常用来指机械驱动的、水压驱动的、气压驱动的和电力驱动的机械装置,将有角移置和直线移置联系起来,使其符合规定。
加工操作大体上分为两类:①. 粗加工。
其金属切除率高且由此导致的切除力较大,但规定的尺寸精度相对较低。
②. 精加工。
其金属切除率低且由此导致的切除力较小,但规定的尺寸精度相对较高。
静载荷及动载荷,如处于非平衡状态的砂轮所导致的结果,自然在精加工方面比在粗加工操作方面更为重要。
任何加工过程所达到的精确度通常会受到偏差大小的影响,这种影响是是操作动力的结果。
机床框架通常由铸铁制造,虽然有些机床可能为钢铸件或低碳钢结构。
选择铸铁是因为其价格、硬度、耐压强度及减少加工操作中的震动的能力。
为了避免铸件出现轻重不均的部分,精心设计的肋材构架系统被采用,最大可能地抵抗造成弯曲和变形的压力。
两种肋材构架分别为箱形和对角线形。
箱形结构便于生产,因为壁上的孔径允许核心的定位和抽取。
对角线楞条配置则提供更大的抗纽刚度并允许金属屑从部件当中的孔隙落出,因此经常被用于机床。
车床的滑移和滑轨指引并且为相互影响运动的部件定位,通常根据工件更改车床的位置。
运动一般采取直线运动的形式,但有时是旋转,例如,对应于工件的螺纹螺旋角方向而转动万能螺纹磨床上的砂轮头的一个角度。
基本的对称滑移部件为扁平、V形、燕尾槽形及汽缸形。
这些部件既可单独使用又可根据用途以不同方式组合使用。
滑轨的特征如下:⒈如果滑移要在一条直线上移动位置,这条直线必须位于两个相互垂直的平面之间且必须没有滑动旋转。
⒉机床滑轨的直线性规定公差一般介于0~0.02mm/100mm之间;在水平表面此公差可以被处理以得到凸形表面这样就可以抵消滑轨下沉的作用。
⒊润滑油。
滑轨可能被以下两种系统中的任何一种润滑:⑴.间歇通过油脂或油嘴润滑。
这种方法适合运作不频繁和速度不高的情况。
⑵.持续润滑,如通过计量阀和管道根据需要抽取;通过这些方法操作的表面之间的润滑油薄膜必须非常薄,以避免滑移漂浮。
如果滑移表面是镜平面,油就会被挤出,使表面粘接。
因此实际操作中滑移表面不是被杯状轮边缘压平,就是被刮去。
两种操作过程都会产生微小的表面凹痕,这种凹痕会导致少量润油存留,而且零件的完全分离可能不会总是发生;因此,滑移的正确定位得到保留。
⒋保护。
为了维护滑轨,使其正常工作,必须满足如下条件:⑴.必须避免外来物质如铁屑的进入。
如果这种条件不可能满足,则应该采用不会滞留铁屑的,如倒V形的滑移。
⑵.润滑油必须保留。
润滑油在垂直的或倾斜滑移表面上的粘性特质非常重要;特制的润滑油市场有售。
润滑油的粘性同时能防止其被切削液冲走。
⑶.必须防止由保护装置导致的意外损坏。
译文:(一)BORING AND BORING MACHINESAs carried out on a lathe, boring produces circular internal profiles in hollow work-pieces or on a hole made by drilling or another process, Boring is done with cutting tools that are similar to those used in turning. Because the boring bar has to reach the full length of the bore, tool deflection and, therefore, maintainance of dimensional accuracy can be a significant problem.The boring bar must be sufficiently stiff—that is, made of a material with high elastic modulus, such as tungsten carbide –to minimize deflection and avoid vibration and chatter. Boring bars have been designed with capabilities for damping vibration.Although boring operations on relatively small work-pieces. Can be carried out on a lathe, boring mills are used for large work-pieces. These machines are either vertical or horizontal, and are capable of performing operations such as turning, facing, grooving, and chamfering. A vertical boring machine is similar to a lathe but has a vertical axis of work-piece rotation.The cutting tool (usually a single point made of M-2 and M-3 high-speed steel and C-7 and C-8 carbide) is mounted on the tool head, which is capable of vertical movement (for boring and turning) and radial movement (for facing), guided by the cross-rail. The head can be swiveled to produce conical (tapered) surfaces.In horizontal boring machine, the work-piece is mounted on a table that can move horizontally in both the axial and radial directions. The cutting tool is mounted on a spindle that rotates in the headstock, which is capable of both vertical and longitudinal movements. Drills, reamer, taps, and milling cutters can also be mounted on the machine spindle.Boring machine are available with a variety of features. Although work-piece diameters are generally 1 m-4 m(3ft-12ft),work-piece as large as 20 m(60ft) can be machined in some vertical boring machines. Machine capacities range up to 150 kw (200hp).these machines are also available with computer numerical controls, which allow all movements to be programmed. With such controls, little operaror involvement is required and consistency and productivity are improved. Cutting speeds and feeds for boring are similar to those forturning.(For capabilities of boring operations)Jig borers are vertical boring machines with high –precision bearings. Although they are available in various sizes and used in tool rooms for making jigs and fixtures, they are now being replaced by more versatile numerical control machines.Design considerations for boring. Guidelines for efficient and economical boring operations are similar to those for turning. Additionally, the following factors should be considered:a.Whenever possible, through holes rather than blind holes should bespecified.(The term blind hole refers to a hole that does not gothough the thickness of the work-piece )b.The greater the length –to –bore-diameter ratio, the more difficult itis to hold dimensions because of the deflections of the boring bardue to cutting forces.c.Interrupted internal surfaces should be avoided.(2)Fundamentals of Machine ToolsIn many cases products form the primary forming processes must undergo further refinements in size and surface finish to meet their design specifications. To meet such precise tolerances the removal of small amounts of material is needed. Usually machine tools are used for such operation.In the United States material removal is a big business-in excess of $ per year, including material, labor, overhead, and machine-tool shipments, is spent. Since 60 percent of the mechanical and industrial engineering and technology graduates have something connection with the machining industry either through sale, design, or operation of machine shops, or working in related industry, it is wise for an engineering student to devote some time in his curriculum to studying material removal and machine tools.A machine tool provides the means for cutting tools to shape a workpieceto required dimensions; the machine supports the tool and the workpiece in a controlled relationship through the functioning of its basic members, which are as follow:(a) Bed, Structure or Frame. This is the main member which provides a basis for, and a connection between, the spindles and slides; the distortion and vibration under load must be kept to a minimum.(b) Slides and Sideways. The translation of a machine element (e.g. the slide) is normally achieved by straight-line motion under the constraint of accurate guiding surfaces (the slideway).(c) Spindles and Bearings. Angular displacements take place about an axis of rotation; the position of this axis must be constant within extremely fine limits in machine tools, and is ensured by the provision of precision spindles and bearings.(d) Power Unit. The electric motor is the universally adopted power unit for machine tools. By suitably positioning individual motors, belt and gear transmissions are reduced to a minimum.(e) Transmission Linkage. Linkage is the general term used to denote the mechanical, hydraulic, pneumatic or electric mechanisms which connect angular and linear displacements in defined relationship.There are two broad divisions of machining operations:(a) Roughing, for which the metal removal rate, and consequently the cutting force, is high ,but the required dimensional accuracy relatively low .(b) Finishing, for which the metal removal rate, and consequently the cutting force, is low, but the required dimensional accuracy and surface finish relatively high .It follows that static loads and dynamic loads, such as result form an unbalanced grindingwheel, are more significant in finishing operations than in roughing operations, The degree of precision achieved in any machining process will usually be influenced by the magnitude of the deflections, which occur as a result of the force acting.Machine tool frames are generally made in cast iron, although some may be steel casting or mild-steel fabrications. Cast iron is chosen because of its cheapness, rigidity, compressive strength and capacity for damping the vibrations set-up in machine operations, To avoid massive sections in castings, carefully designed systems of ribbing are used to offer the maximum resistance to bending and torsional stresses. Two basic types of ribbing are box and diagonal. The box formation is convenient to produce, apertures in walls permitting the positioning and extraction of cores. Diagonal ribbing provides greater torsional stiffness and yet permits swarf to fall between the sections; it is frequently used for lathe beds.The slides and slideways of a machine tool locate and guide members which move relative to each other, usually changing the position of the tool relative to workpiece .The movement generally takes the form of translation in a straight line, but is sometimes angular rotation, e.g. tilting the wheel-head of auniversal thread-grinding machine to an angle corresponding which the helix angle of the workpiece thread. The basic geometric elements of slides are flat, vee, dovetail and cylinder. These elements may be used separately or combined in various ways according to the applications . Features of slideways are as follows :(a) Accuracy of Movement. Where a slide is to be displaced in a straight line, this line must lie in two mutually perpendicular planes and there must be no slide rotation. The general tolerance for straightness of machine tool slideways is 0~0.02mm per 1000mm; on horizontal surfaces this tolerance may be disposed so that a convex surface results, thus countering the effect of "sag" of the slideway.(b) Means of Adjustment. To facilitate assembly, maintain accuracy and eliminate "play" between sliding members after wear has taken place, a strip is sometimes inserted in slides. This is called a gibstrip. Usually, the gib is retained by socket-head screws passing through elongated slots;and is adjusted by grub-screws secured by lock nuts.(c) Lubrication. Slideways may be lubricated by either of the followingsystems:1)Intermittently through grease or oil nipples, a method suitable where movements are infrequent and speed low.2) Continuously e.g. by pumping through a metering valve and pipe-work to the point of application; the film of oil introduced between surfaces by these means must be extremely thin to avoid the slide ―floating‖.If sliding surfaceswere optically flat oil would be squeezed out,resulting in the surfaces sticking. Hence in practice slide Sill"faces are either grourld using the edge of a cup wheel,or scraped. Both processes produee minulte surface depressions,which retain‗‗pocket‖ of oil, and complete separation of the parts may not occur at all points.(d) Protection.To maintain slideways in good order, the following conditions must be met:1) Ingress of foreign matter,e.g.swarf,must be prevented. Where this is no possible,it is desirable to have a form of slideway,which does not retain swarf,e.g. the inverted vee.2) Lubricating oil must be retained.The adhesive property of oil for use on vertical or inclined slide surface is important; oils are available which have been specially developed for this purpose. The adhesiveness of oil also preverts it being washed away by cutting fluids.3) Accidental damage must be prevented by protective guards.。