机械毕业设计英文外文翻译71车床夹具设计分析
机械类毕业设计外文翻译
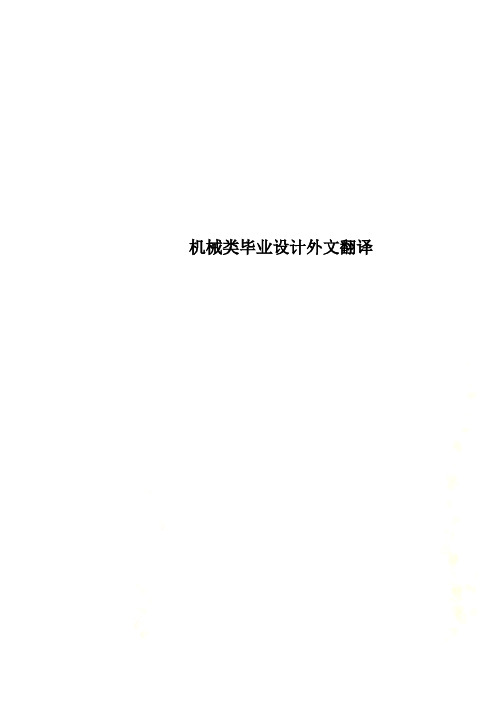
机械类毕业设计外文翻译外文原文Options for micro-holemakingAs in the macroscale-machining world, holemaking is one of the most— if not the most—frequently performed operations for micromachining. Many options exist for how those holes are created. Each has its advantages and limitations, depending on the required hole diameter and depth, workpiece material and equipment requirements. This article covers holemaking with through-coolant drills and those without coolant holes, plunge milling, microdrilling using sinker EDMs and laser drilling.Helpful HolesGetting coolant to the drill tip while the tool is cutting helps reduce the amount of heat at the tool/workpiece interface and evacuate chips regardless of hole diameter. But through-coolant capability is especially helpful when deep-hole microdrilling because the tools are delicate and prone to failure when experiencing recutting of chips, chip packing and too much exposure to carbide’s worst enemy—heat.When applying flood coolant, the drill itself blocks access to the cutting action. “Somewhere about 3 to 5 diam eters deep, the coolant has trouble getting down to the tip,” said Jeff Davis, vice president of engineering for Harvey Tool Co., Rowley, Mass. “It becomes wise to use a coolant-fed drill at that point.”In addition, flood coolant can cause more harm than good when microholemaking. “The pressure from the flood coolant can sometimes snap fragile drills as they enter the part,” Davis said.The toolmaker offers a line of through-coolant drills with diameters from 0.039" to 0.125" that are able to produce holes up to 12 diameters deep, as well as microdrills without coolant holes from 0.002" to 0.020".Having through-coolant capacity isn’t enough, though. Coolant needs to flow at a rate that enables it to clear the chips out of the hole. Davis recommends, at a minimum, 600 to 800 psi of coolant pressure. “It works much better if you have higher pressure than that,” he added.To prevent those tiny coolant holes from becoming clogged with debris, Davis also recommends a 5μm or finer coolant filter.Another recommendation is to machine a pilot, or guide, hole to prevent the tool from wandering on top of the workpiece and aid in producing a straight hole. When applying a pilot drill, it’s important to select one with an included angle on its point that’s equal t o or larger than the included angle on the through-coolant drill that follows.The pilot drill’s diameter should also be slightly larger. For example, if the pilot drill has a 120° included angle and a smaller diameter than a through-coolant drill with a 140°included angle, “then you’re catching the coolant-fed drill’s corners and knocking those corners off,” Davis said, which damages the drill.Although not mandatory, pecking is a good practice when microdrilling deep holes. Davis suggests a pecking cycle that is 30 to 50 percent of the diameter per peck depth, depending on the workpiece material. This clears the chips, preventing them from packing in the flute valleys.Lubricious ChillTo further aid chip evacuation, Davis recommends applying an oil-based metalworking fluid instead of a waterbased coolant because oil provides greater lubricity. But if a shop prefers using coolant, the fluid should include EP (extreme pressure) additives to increase lubricity and minimize foaming. “If you’ve got a lot of foam,” Davis noted, “the chips aren’t being pulled out the way they are supposed to be.”He added that another way to enhance a tool’s slipperiness while extending its life is with a coating, such as titanium aluminum nitride. TiAlN has a high hardness and is an effective coating for reducing heat’s impact when drilling difficult-to-machine materials, like stainless steel.David Burton, general manager of Performance Micro Tool, Janesville, Wis., disagrees with the idea of coating microtools on the smaller end of the spectrum. “Coatings on tools below 0.020" typically have a negative effect on every machining aspect, from the quality of the initial cut to tool life,” he said. That’s because coatings are not thin enough and negatively alter the rake and relief angles when applied to tiny tools.However, work continues on the development of thinner coatings, and Burton indicated that Performance Micro Tool, which produces microendmills and microrouters and resells microdrills, is working on a project with others to create a submicron-thickness coating. “We’re probably 6 months to 1 year from testing it in the market,” Burton said.The microdrills Performance offers are basically circuit-board drills, which are also effective for cutting metal. All the tools are without through-coolant capability. “I had a customer drill a 0.004"-dia. hole in stainless steel, and he was amazed he could do it with a circuit-board drill,” Burton noted, adding that pecking and running at a high spindle speed increase the d rill’s effectiveness.The requirements for how fast microtools should rotate depend on the type of CNCmachines a shop uses and the tool diameter, with higher speeds needed as the diameter decreases. (Note: The equation for cutting speed is sfm = tool diameter × 0.26 × spindle speed.)Although relatively low, 5,000 rpm has been used successfully by Burton’s customers. “We recommend that our customers find the highest rpm at the lowest possible vibration—the sweet spot,” he said.In addition to minimizing vibration, a constant and adequate chip load is required to penetrate the workpiece while exerting low cutting forces and to allow the rake to remove the appropriate amount of material. If the drill takes too light of a chip load, the rake face wears quickly, becoming negative, and tool life suffers. This approach is often tempting when drilling with delicate tools.“If the customer decides he wants to baby the tool, he takes a lighter chip load,” Burton said, “and, typically, the cutting edge wears much quicker and creates a radius where the land of that radius is wider than the chip being cut. He ends up using it as a grinding tool, trying to bump material away.” For tools larger than 0.001", Burton considers a chip load under 0.0001" to be “babying.” If the drill doesn’t snap, premature wear can result in abysmal tool life.Too much runout can also be destructive, but how much is debatable. Burton pointed out that Performance purposely designed a machine to have 0.0003" TIR to conduct in-house, worst-case milling scenarios, adding that the company is still able to mill a 0.004"-wide slot “day in and day out.”He added: “You would think with 0.0003" runout and a chip load a third that, say, 0.0001" to 0.00015", the tool would break immediately because one flute would be taking the entire load and then the back end of the flute would be rubbing.When drilling, he indicated that up to 0.0003" TIR should be acceptable because once the drill is inside the hole, the cutting edges on the end of the drill continue cutting while the noncutting lands on the OD guide the tool in the same direction. Minimizing run out becomes more critical as the depth-to-diameter ratio increases. This is because the flutes are not able to absorb as much deflection as they become more engaged in the workpiece. Ultimately, too much runout causes the tool shank to orbit around the tool’s center while the tool tip is held steady, creating a stress point where the tool will eventually break.Taking a PlungeAlthough standard micro drills aren’t generally available below 0.002", microendmills that can be used to “plunge” a hole are. “When people want to drillsmaller than that, they use our endmills and are pretty successful,” Burton said. However, the holes can’t be very deep because the tools don’t have long aspect, or depth-to-diameter, ratios. Therefore, a 0.001"-dia. endmill might be able to only make a hole up to 0.020" deep whereas a drill of the same size can go deeper because it’s designed to place the load on its tip when drilling. This transfers the pressure into the shank, which absorbs it.Performance offers endmills as small as 5 microns (0.0002") but isn’t keen on increasing that line’s sales. “When people try to buy them, I very seriously try to talk them out of it bec ause we don’t like making them,” Burton said. Part of the problem with tools that small is the carbide grains not only need to be submicron in size but the size also needs to be consistent, in part because such a tool is comprised of fewer grains. “The 5-m icron endmill probably has 10 grains holding the core together,” Burton noted.He added that he has seen carbide powder containing 0.2-micron grains, which is about half the size of what’s commercially available, but it also contained grains measuring 0.5 and 0.6 microns. “It just doesn’t help to have small grains if they’re not uniform.”MicrovaporizationElectrical discharge machining using a sinker EDM is another micro-holemaking option. Unlike , which create small holes for threading wire through the workpiece when wire EDMing, EDMs for producing microholes are considerably more sophisticated, accurate and, of course, expensive.For producing deep microholes, a tube is applied as the electrode. For EDMing smaller but shallower holes, a solid electrode wire, or rod, is needed. “We try to use tubes as much as possible,” said Jeff Kiszonas, EDM product manager for Makino Inc., Auburn Hills, Mich. “But at some point, nobody can make a tube below a certain diameter.” He added that some suppliers offer tubes down to 0.003" in diameter for making holes as small as 0.0038". The tube’s flushing hole enables creating a hole with a high depth-to-diameter ratio and helps to evacuate debris from the bottom of the hole during machining.One such sinker EDM for produc ing holes as small as 0.00044" (11μm) is Makino’s Edge2 sinker EDM with fine-hole option. In Japan, the machine tool builder recently produced eight such holes in 2 minutes and 40 seconds through 0.0010"-thick tungsten carbide at the hole locations. The electrode was a silver-tungsten rod 0.00020" smaller than the hole being produced, to account for spark activity in the gap.When producing holes of that size, the rod, while rotating, is dressed with acharged EDM wire. The fine-hole option includes a W-axis attachment, which holds a die that guides the electrode, as well as a middle guide that prevents the electrode from bending or wobbling as it spins. With the option, the machine is appropriate for drilling hole diameters less than 0.005".Another sinker EDM for micro-holemaking is the Mitsubishi VA10 with afine-hole jig attachment to chuck and guide the fine wire applied to erode the material. “It’s a standard EDM, but with that attachment fixed to the machine, we can do microhole drilling,” said Dennis Powderly, sinker EDM product manager for MC Machinery Systems Inc., Wood Dale, Ill. He added that the EDM is also able to create holes down to 0.0004" using a wire that rotates at up to 2,000 rpm.Turn to TungstenEDMing is typically a slow process, and that holds true when it is used for microdrilling. “It’s very slow, and the finer the details, the slower it is,” said , president and owner of Optimation Inc. The Midvale, Utah, company builds Profile 24 Piezo EDMs for micromachining and also performs microEDMing on a contract-machining basis.Optimation produces tungsten electrodes using a reverse-polarity process and machines and ring-laps them to as small as 10μm in diameter with 0.000020" roundness. Applying a 10μm-dia. electrode produces a hole about 10.5μm to 11μm in diameter, and blind-holes are possible with the company’s EDM. The workpiece thickness for the smallest holes is up to 0.002", and the thickness can be up to 0.04" for 50μm holes.After working with lasers and then with a former EDM builder to find a better way to produce precise microholes, Jorgensen decided the best approach was DIY. “We literally started with a clean sheet of paper and did all the electronics, all the software and the whole machine from scratch,” he said. Including the software, the machine costs in the neighborhood of $180,000 to $200,000.Much of the company’s contract work, which is provided at a shop rate of $100 per hour, involves microEDMing exotic metals, such as gold and platinum for X-ray apertures, stainless steel for optical applications and tantalum and tungsten for the electron-beam industry. Jorgensen said the process is also appropriate for EDMing partially electrically conductive materials, such as PCD.“The customer normally doesn’t care too much about the cost,” he said. “We’ve done parts where there’s $20,000 [in time and material] involved, and you can put the whole job underneath a fingernail. We do everything under a microscope.”Light CuttingBesides carbide and tungsten, light is an a ppropriate “tool material” formicro-holemaking. Although most laser drilling is performed in the infrared spectrum, the SuperPulse technology from The Ex One Co., Irwin, Pa., uses a green laser beam, said Randy Gilmore, the company’s director of laser tec hnologies. Unlike the femtosecond variety, Super- Pulse is a nanosecond laser, and its green light operates at the 532-nanometer wavelength. The technology provides laser pulses of 4 to 5 nanoseconds in duration, and those pulses are sent in pairs with a delay of 50 to 100 nanoseconds between individual pulses. The benefits of this approach are twofold. “It greatly enhances material removal compared to other nanosecond lasers,” Gilmore said, “and greatly reduces the amount of thermal damage done to the workpiece material” because of the pulses’ short duration.The minimum diameter produced with the SuperPulse laser is 45 microns, but one of the most common applications is for producing 90μm to 110μm holes in diesel injector nozzles made of 1mm-thick H series steel. Gilmore noted that those holes will need to be in the 50μm to 70μm range as emission standards tighten because smaller holes in injector nozzles atomize diesel fuel better for more efficient burning.In addition, the technology can produce negatively tapered holes, with a smaller entrance than exit diameter, to promote better fuel flow.Another common application is drilling holes in aircraft turbine blades for cooling. Although the turbine material might only be 1.5mm to 2mm thick, Gilmore explained that the holes are drilled at a 25° entry angle so the air, as it comes out of the holes, hugs the airfoil surface and drags the heat away. That means the hole traverses up to 5mm of material. “Temperature is everything in a turbine” he said, “because in an aircraft engine, the hotter you can run the turbine, the better the fuel economy and the more thrust you get.”To further enhance the technology’s competitiveness, Ex One developed apatent-pending material that is injected into a hollow-body component to block the laser beam and prevent back-wall strikes after it creates the needed hole. After laser machining, the end user removes the material without leaving remnants.“One of the bugaboos in getting lasers accepted in the diesel injector community is that light has a nasty habit of continuing to travel until it meets another object,” Gilmore said. “In a diesel injector nozzle, that damages the interior surface of the opposite wall.”Although the $650,000 to $800,000 price for a Super- Pulse laser is higher than a micro-holemaking EDM, Gilmore noted that laser drilling doesn’t require electrodes. “A laser system is using light to make holes,” he said, “so it doesn’t have a consumable.”Depending on the application, mechanical drilling and plunge milling, EDMing and laser machining all have their place in the expanding micromachining universe. “People want more packed into smaller spaces,” said Makino’s Kiszonas.中文翻译微孔的加工方法正如宏观加工一样,在微观加工中孔的加工也许也是最常用的加工之一。
机械加工工艺夹具类外文文献翻译、中英文翻译、外文翻译

TOOL WEAR MECHANISMS ON THE FLANK SURFACE OF CUTTINGINSERTSFOR HIGH SPEED WET MACHINING5.1 IntroductionAlmost every type of machining such as turning, milling, drilling, grinding..., uses a cutting fluid to assist in the cost effective production of pa rts as set up standard required by the producer [1]. Using coolant with some cutting tools material causes severe failure due to the lack of their resistance to thermal shock (like AL2O3 ceramics), used to turn steel. Other cutting tools materials like cubic boron nitride (CBN) can be used without coolant, due to the type of their function. The aim of using CBN is to raise the temperature of the workpice to high so it locally softens and can be easily machined.The reasons behind using cutting fluids can be summarized as follows.® Extending the cutting tool life achieved by reducing heat generated and as a result less wear rate is achieved. It will also eliminate the heat from theshear zone and the formed chips.® Cooling the work piece of high quality materia l under operation plays an important role since thermal distortion of the surface and subsurfacedamage is a result of excessive heat that must be eliminated or largelyreduced to produce a high quality product.Reducing cutting forces by its lubricating e ffect at the contact interface region and washing and cleaning the cutting region during machining from small chips. The two main reasons for using cutting fluids are cooling and lubrication.Cutting Fluid as a Coolant:The fluid characteristics and condition of use determine the coolant action of the cutting fluid, which improves the heat transfer at the shear zone between the cutting edge, work piece, and cutting fluid. The properties of the coolant in this case must include a high heat capacity to carry away heat and good thermal conductivity to absorb the heat from the cutting region. The water-based coolant emulsion with its excellent high heat capacity is able to reduce tool wear [44]. Cutting Fluid as a Lubricant:The purpose is to reduce friction bet ween the cutting edge, rake face and the work piece material or reducing the cutting forces (tangential component). As the friction drops the heat generated isdropped. As a result, the cutting tool wear rate is reduced and the surface finish is improved.Cutting Fluid PropertiesFree of perceivable odorPreserve clarity throughout lifeKind and unirritated to skin and eyes.Corrosion protection to the machine parts and work piece.Cost effective in terms off tool life, safety, dilution ratio, and fluid lif e.[1]5.1.1 Cutting Fluid TypesThere are two major categories of cutting fluidsNeat Cutting OilsNeat cutting oils are poor in their coolant characteristics but have an excellent lubricity. They are applied by flooding the work area by a pump and re-circulated through a filter, tank and nozzles. This type is not diluted by water, and may contain lubricity and extreme-pressure additives to enhance their cutting performance properties. The usage of this type has been declining for their poor cooling ability, causing fire risk, proven to cause health and safety risk to the operator [1].® Water Based or Water Soluble Cutting FluidsThis group is subdivided into three categories:1.Emulsion ` mineral soluble' white-milky color as a result of emulsion of oil inwater. Contain from 40%-80% mineral oil and an emulsifying agent beside corrosion inhibitors, beside biocide to inhibit the bacteria growth.2.Micro emulsion `semi-synthetic' invented in 1980's, has less oil concentrationand/or higher emulsifier ratio 10%-40% oil. Due to the high levels ofemulsifier the oil droplet size in the fluid are smaller which make the fluid more translucent and easy to see the work piece during operation. Otherimportant benefit is in its ability to emulsify any leakage of oil from themachine parts in the cutting fluid, a corrosion inhibitors, and bacteria control.3.Mineral oil free `synthetic' is a mix of chemicals, water, bacteria control,corrosion inhibitors, and dyes. Does not contain any mineral oils, andprovides good visibility.23 to the work piece. bare in mind that the lack of mineral oil in this type of cuttingfluid needs to take more attention to machine parts lubrication since it should not leave an oily film on the machine parts, and might cause seals degradation due the lack of protection.5.1.2 Cutting Fluid SelectionMany factors influence the selection of cutting fluid; mainly work piece material, type of machining operation, machine tool parts, paints, and seals. Table 5-1 prepared at the machine tool industry res earch association [2] provides suggestions on the type of fluid to be used.5.1.3 Coolant ManagementTo achieve a high level of cutting fluids performance and cost effectiveness, a coolant recycling system should be installed in the factory. This system will reduce the amount of new purchased coolant concentrate and coolant disposable, which will reduce manufacturing cost. It either done by the company itself or be rented out, depends on the budget and management policy of the company [1].Table 5-1 Guide to the selection of cutting fluids for general workshop applications.Machining operation Workpiece materialFree machining and low - carbon Medium- Carbon steels High Carbon and alloy steels Stainlessand heattreated GrindingClear type soluble oil, semi synthetic or chemical Turning General purpose, soluble oil, semi synthetic or synthetic fluid Extreme-pressuresoluble oil,semi-synthetic orsyntheticfluid Milling General purpose, soluble oil, semi synthetic or synthetic Extreme- pressure soluble oil, semi- synthetic or synthetic Extreme-pressuresoluble oil,semi-synthetic orsyntheticfluid(neat cutting oilsmay beDrillingExtreme- pressure soluble oil, semi- synthetic or GearShapping Extreme-pressure soluble oil, Neat-cutting oils preferable HobbingExtreme-pressure soluble oil, semi-synthetic or synthetic fluid (neat cutting oils may be Neat-cutti ng oils BratchingExtreme-pressure soluble oil, semi-synthetic or synthetic fluid (neat Tapping Extreme-pressure soluble oil, semi-synthetic or Neat-cuttingpreferableNote: some entreis deliberately extend over two or more columns, indicating awide range of possible applications. Other entries are confined to a specific class of work material.Adopt ed f rom Edw ard and Wri ght [2]5.2 Wear Mechanisms Under Wet High Speed M achiningIt is a common belief that coolant usage in metal cutting reduces cuttingtemperature and extends tools life. However, this researchshowed that this is not necessarily true to be generalized overcutting inserts materials. Similar research was ca rried out ondifferent cutting inserts materials and cutting conditionssupporting our results. Gu et al [36] have recorded adifference in tool wear mechanisms between dry and wetcutting of C5 milling inserts. Tonshoff et al [44] alsoexhibited different wear mechanisms on AL 2O 3/TiC inserts inmachining ASTM 5115, when using coolants emulsionscompared to dry cutting. In addition, Avila and Abrao [20]experienced difference in wear mechanisms activated at theflank side, when using different coolants in t estingAL 2O 3lTiC tools in machining AISI4340 steel. The wearmechanisms and the behavior of the cutting inserts studied inthis research under wet high speed-machining (WHSM)condition is not fully understood. Therefore, it was theattempt of this research to focus on the contributions incoating development and coating techniques of newlydeveloped materials in order to upgrade their performance attough machining conditions. This valuable research providesinsight into production timesavings and increase inprofitability. Cost reductions are essential in the competitiveglobal economy; thus protecting local markets and consistingin the search of new ones.5.3 Experimental Observations on Wear Mechanisms of Un-CoatedCemented Carbide Cutting Inserts in High Speed WetMachiningIn this section, the observed wear mechanisms are presented of uncoated cemented carbide tool (KC313) in machining ASTM 4140 steel under wet condition. The overall performance of cemented carbide under using emulsion coolant has been improved in terms of extending tool life and reducing machining cost. Different types of wear mechanisms were activated at flank side of cutting inserts as a result of using coolant emulsion during machining processes. This was due to the effect of coolant in reducing the average temperature of the cutting tool edge and shear zone during machining. As a result abrasive wear was reduced leading longer tool life. The materials of cutting tools behave differently to coolant because of their varied resistance to thermal shock. The following observations recorded the behavior of cemented carbide during high speed machining under wet cutting.Figure5-1 shows the flank side of cutting inserts used at a cutting speed of 180m/min. The SEM images were recorded after 7 minutes of machining. It shows micro-abrasion wear, which identified by the narrow grooves along the flank side in the direction of metal flow, supported with similar observations documented by Barnes and Pashby [41] in testing through-coolant-drilling inserts of aluminum/SiC metal matrix composite. Since the cutting edge is the weakest part of the cutting insert geometry, edge fracture started first due to the early non-smooth engagement between the tool and the work piece material. Also, this is due to stress concentrations that might lead to a cohesive failure on the transient filleted flank cutting wedge region [51, 52]. The same image of micro-adhesion wear can be seen at the side and tool indicated by the half cone27 shape on the side of cutting tool. To investigate further, a zoom in view was taken atthe flank side with a magnification of 1000 times and presented in Figure 5-2A. It shows clear micro-abrasion wear aligned in the direction of metal flow, where the cobalt binder was worn first in a higher wear rate than WC grains which protruded as big spherical droplets. Figure 5-2B provides a zoom-in view that was taken at another location for the same flank side. Thermal pitting revealed by black spots in different depths and micro-cracks, propagated in multi directions as a result of using coolant. Therefore, theii~ial pitting, micro-adhesion and low levels of micro-abrasion activated under wet cutting; while high levels of micro-abrasion wear is activated under dry cutting (as presented in the prev ious Chapter).Figure 5-3A was taken for a cutting insert machined at 150mlmin. It shows a typical micro-adhesion wear, where quantities of chip metal were adhered at the flank side temporarily. Kopac [53] exhibited similar finding when testing HSS-TiN drill inserts in drilling SAE1045 steel. This adhered metal would later be plucked away taking grains of WC and binder from cutting inserts material and the process continues. In order to explore other types of wear that might exist, a zoom-in view with magnification of 750 times was taken as shown in Figure5-3B. Figure 5-3B show two forms of wears; firstly, micro-thermal cracks indicated by perpendicular cracks located at the right side of the picture, and supported with similar findings of Deamley and Trent [27]. Secondly, micro-abrasion wear at the left side of the image where the WC grains are to be plucked away after the cobalt binder was severely destroyed by micro-abrasion. Cobalt binders are small grains and WC is the big size grains. The severe distort ion of the binder along with the WC grains might be due to the activation of micro-adhesion and micro-abrasionFigure 5-1 SEM image of (KC313) showing micro abrasion and micro-adhesion (wet).SEM micrographs of (KC313) at 180m/min showing micro-abrasion where cobalt binder was worn first leaving protruded WC spherical droplets (wet).(a)SEM micrographs of (KC313) at 180m/min showing thermal pitting (wet).Figure 5-2 Magnified views of (KC313) under wet cutting: (a) SEM micrographs of (KC313) at 180mlmin showing micro-abrasion where cobalt binderwas worn first leaving protruded WC spherical droplets (wet ), (b) SEMmicrographs of (KC313) at 180.m/min showing thermal pitting (wet ).SEM image showing micro-adhesion wear mechanism under 150m/min (wet).(a)SEM image showing micro-thermal cracks, and micro-abrasion.Figure 5-3 Magnified views of (KC313) at 150m/min (wet): (a) SEM image showing micro-adhesion wear mechanism under 150m/min (wet), (b) SEM image showing micro-fatigue cracks, and micro-abrasion (wet).Wear at the time of cutting conditions of speed and coolant introduction. Therefore, micro-fatigue, micro-abrasion, and micro-adhesion wear mechanisms are activated under wet condition, while high levels of micro-abrasion were observed under dry one.Next, Figure 5-4A was taken at the next lower speed (120m/min). It shows build up edge (BUE) that has sustained its existence throughout the life of the cutting tool, similar to Huang [13], Gu et al [36] and Venkatsh et al [55]. This BUE has protected the tool edge and extended its life. Under dry cutting BUE has appeared at lower speeds (90 and 60 m/min), but when introducing coolant BUE started to develop at higher speeds, This is due to the drop in shear zone temperature that affected the chip metal fl ow over the cutting tool edge, by reducing the ductility to a level higher than the one existing at dry condition cutting. As a result, chip metal starts accumulating easier at the interface between metal chip flow, cutting tool edge and crater surface to form a BUE. In addition to BUE formation, micro-abrasion wear was activated at this speed indicated by narrow grooves.To explore the possibility of other wear mechanisms a zoom-in view with a magnification of 3500 times was taken and shown in Figure 5-4B. Micro- fatigue is evident by propagated cracks in the image similar to Deamley and Trent [27] finding. Furthermore, Figure 5-4B shows indications of micro-abrasion wear, revealed by the abrasion of cobalt binder and the remains of big protruded WC grains. However, the micro-abrasion appeared at this speed of 120m/min is less severe than the same type of micro-wear observed at 150m/min speed, supported with Barnes [41] similar findings. Therefore, micro-abrasion, BUE and micro-fatigue were activated under wet condition while, adhesion, high levels micro-abrasion, and no BUE were under dry cutting.SEM i m a g e o f(KC313) showing build up e d g e under 120m/min (wet).(a)SEM i m a g e o f(KC3 13) showing micro-fatigue, and micro-abrasion (wet). Figure 5-4 SEM images of (KC313) at 120m/min (wet), (a) SEM image of (KC313). showing build up edge, (b) SEM image of(K C313) showing micro-fatigue and micro-abrasion33 Figure 5-5 is for a cutting tool machined at 90m/min, that presents a goodcapture of one stage of tool life after the BUE has been plucked away. The bottom part of the flank side shows massive metal adhesion from the work piece material. The upper part of the figure at the edge shows edge fracture. To stand over the reason of edge fracture, the zoom-in view with magnification of 2000 times is presented in Figure 5-6A. The micro-fatigue crack image can be seen as well as micro-attrition revealed by numerous holes, and supported with Lim et al [31] observations on HSS-TiN inserts. As a result of BUE fracture from the cutting tool edge, small quantities from the cutting tool material is plucked away leaving behind numerous holes. Figure 5-6B is another zoom-in view of the upper part of flank side with a magnification of 1000 times and shows micro-abrasion wear indicated by the narrow grooves. Furthermore, the exact type of micro-wear mechanism appeared at the flank side under 60 m/min. Therefore, in comparison with dry cutting at the cutting speed of 90 m/min and 60 m/min, less micro-abrasion, bigger BUE formation, and higher micro-attrition rate were activated.Figure 5-5 SEM image showing tool edge after buildup edge was plucked away.SEM image showing micro-fatigue crack, and micro-attrition.(a)SEM image showing micro-abrasion.Figure 5-6 SEM images of (KC313) at 90m/min:(a) SEM image showing micro-fatigue crack, and micro-attrition, (b) SEM image showingmicro-abrasion.5.4 Experimental Observations on Wear Mechanisms of Coated CementedCarbide with TiN-TiCN-TiN Coating in High Speed WetMachiningInvestigating the wear mechanisms of sandwich coating under wet cutting is presented in this section starting from early stages of wear. Figure 5-7 shows early tool wear starting at the cutting edge when cutting at 410m/min. Edge fracture can be seen, it has started at cutting edge due to non-smooth contact between tool, work piece, micro-abrasion and stress concentrations. To investigate further the other possible reasons behind edge fracture that leads to coating spalling, a zoom-in view with magnification of 2000 times was taken and presented at Figure 5-8A. Coating fracture can be seen where fragments of TiN (upper coating) had been plucked away by metal chips. This took place as result of micro-abrasion that led to coating spalling. On the other hand, the edge is t he weakest part of the cutting insert geometry and works as a stress concentrator might lead to a cohesive failure on the transient filleted flank cutting wedge region [51, 52].Both abrasion wear and stress concentration factor leave a non-uniform edge configuration at the micro scale after machining starts. Later small metal fragments started to adhere at the developed gaps to be later plucked away by the continuous chip movement as shown in Figure 5-8A. Another view of edge fracture was taken of the same cutting tool with a magnification of 2000 times as shown in Figure 5-8B. It presents fracture and crack at the honed tool edge. A schematic figure indicated by Figure 5-9, presented the progressive coated cutting inserts failure starting at the insert edge. It was also noticed during the inserts test that failure takes place first at the inserts edge then progressed toward the flank side. Consequently, a study on optimizing the cutting edgeFigure 5-7 SEM image of (KC732) at 410m/min showing edge fractur e and micro-abrasion (wet).SEM image showing edge fracture.(a)SEM image showing fracture and crack at the honed insert edge.Figure 5-8 SEM of (KC732) at 410m/min and early wear stage (wet): (a) SEM image showing edge fracture, (b) SEM image showing fr acture and crack atthe honed insert edge.radius to improve coating adhesion, and its wear resistance, might be also a topic for future work.Figure 5-1.0A was taken after tool failure at a speed of 410m/min. It shows completely exposed substrate and severe sliding wear at the flank side. The coating exists at the crater surface and faces less wear than the flank side. Therefore it works as an upper protector for the cutting edge and most of the wear will take place at the flank side as sliding wear. Figu re 5-10B is a zoom-in view with magnification of 3500 times, and shows coating remaining at the flank side. Nonetheless, micro-abrasion and a slight tensile fracture in the direction of metalchip flow. Ezugwa et al [28] and Kato [32] have exhibited simila r finding. However, the tensile fracture in this case is less in severity than what had been observed at dry cutting. This is due to the contribution of coolant in dropping the cutting temperature, which has reduced the plastic deformation at high temperature as a result. Hence, in comparison with the dry cutting at the same speed, tensile fracture was available with less severity and micro-abrasion/sliding. However, in dry cutting high levels of micro-abrasion, high levels of tensile fracture and sliding wear occurred.Figure 5-11 was taken at early stages of wear at a speed of 360m/min. It shows sliding wear, coating spalling and a crack starting to develop between TiN and TiCN coating at honed tool edge. Figure5-12A shows nice presentation of what had been described earlier regarding the development of small fragments on the tool edge. The adhered metal fragments work along with micro-abrasion wear to cause coating spalling.SEM image showing sliding wear.(a)SEM image showing micro-abrasion and tensile fracture.Figure 5-10 SEM images of (KC732) at 410m/min after failure (wet): (a) SEM image showing sliding wear, (b) SEM image showing micro-abrasionand tensile fracture.Figure 5-11 SEM image at early stage of wear of 360m/min (wet) showing coating and spalling developing crack between TiN and TiCN layers.The size of the metal chip adhered at the edge is almost 15g. Since it is unstable it will be later plucked away taking some fragments of coatings with it and the process continues. Another zoom in view with a magnification of 5000 times for the same insert is shown in Figure 5-12B indicating a newly developed crack between the coating layers.Figure 5-13A is taken of the same insert after failure when machining at 360m/min and wet condition. Coating spalling, and sliding wear can be seen and indicated by narrow grooves. In addition, initial development of notch wear can be seen at the maximum depth of cut.Further investigation is carried out by taking a zoom in view with a magnification of 2000 times as shown in Figure 5-13B. A clear micro-abrasion wear and micro-fatigue cracks were developed as shown, which extended deeply through out the entire three coating layers deep until the substrate. Therefore, in comparison with dry cutting, micro-fatigue crack, less tensile fracture, less micro-abrasion wear were activated at wet cutting. While micro- fatigue crack, high levels of micro-abrasion, and high levels of tensile fracture are distinguish the type of wear under dry condition at the same cutting spee d.Next, Figure 5-14A is taken for cutting tools machined at 310m/min. The results are similar to the previous inserts machined at 360m/min, where adhesion of metal fragments occurred at the tool edge, sliding wear and coating spalling. In addition, the black spot appeared at the top of the figure on the crater surface is a void resulting from imperfections in the coating process. At this condition, the crater surface will be worn faster than the flank surface.SEM image showing adhered metal fragments at tool edge.(a)SEM image showing developed crack between coating layers.Figure 5-12 SEM image of (KC732) at early wear 360m/min (wet): (a) SEM image showing adhered metal fragments at tool edge, (b) SEM image showingdeveloped crack between coating layers.(a)SEM image showing coating spalling and sliding wear after tool failure(b)SEM image showing micro-abrasion, and micro-fatigue cracks developedbetween coating layersFigure 5-13 SEM image of KC732 after failure machined at 360m/min(b)(wet): (a) SEM image showing coating spalling and sliding wear after toolfailure, (b) SEM image showing micro-abrasion, and micro-fatiguecracks developed between coating layers.翻译:在高速潮湿机械加工条件下后刀面表层磨损机理5.1 介绍几乎每类型用机器制造譬如转动, 碾碎, 钻井, 研..., 使用切口流体协助零件的有效的生产当设定标准由生产商[ 1 ] 需要。
机械毕业设计英文外文翻译基于事例推理的夹具设计研究与应用

附录1 英文原文Application and development Of case based reasoning in fixture designAbstract: Based on the case based designing (CBD) methodology, the fixture similarity is in two respects: the function and the structure information. Then, the computer aided fixture design system is created on case based reasoning (CBR),in which the attributes of the main features of workpiece and structure of fixture as case index code are designed for the retrieve of the similar cases, and the structure and hierarchical relation of case library are set up for store. Meanwhile, the algorithm based on the knowledge guided in the retrieve of the similar cases, the strategy of case adapt at ion and case storage in which the case ident if cat ion number is used to distinguish from similar cases are presented. The application of the system in some projects improves the design efficiency and gets a good result .Keywords: case based reasoning ;fixture design; computer aided design(CAD)Fixtures are devices that serve as the purpose of holding the workpiece securely and accurately, and maintaining a consistent relationship with respect to the tools while machining. Because the fixture structure depends on the feature of the product and the status of the process planning in the enterprise, its design is the bottleneck during manufacturing, which restrains to improve the efficiency and lead time. And fixture design is a complicated process, based on experience that needs comprehensive qualitative knowledge about a number of design issues including workpiece configuration, manufacturing processes involved, and machining environment. This is also a very time consuming work when using traditional CAD tools (such as Unigraphics, CATIA or Pro/E), which are good at performing detailed design tasks, but provide few benefits for taking advantage of the previous design experience and resources, which are precisely the key factors in improving the efficiency. The methodology of case based reasoning (CBR) adapts the solution of a previously solved case to build a solution for a new problem with the following four steps: retrieve, reuse, revise, and retain [1]. This is a more useful method than the use of an expert system to simulate human thought because proposing a similar case and applying a few modifications seems to be self explanatory and more intuitive to humans .So various case based design support tools have been developed fornumerous areas[2-4], such as in injection molding and design, architectural design, die casting die design, process planning, and also in fixture design. Sun used six digitals to compose the index code that included workpiece shape, machine portion, bushing, the 1st locating device, the 2nd locating device and clamping device[5]. But the system cannot be used for other fixture types except for drill fixtures, and cannot solve the problem of storage of the same index code that needs to be retained, which is very important in CBR[6].1 Construction of a Case Index and Case Library1.1 Case indexThe case index should be composed of all features of the workpiece, which are distinguished from different fixtures. Using all of them would make the operation in convenient. Because the forms of the parts are diverse, and the technology requirements of manufacture in the enterprise also develop continuously, lots of features used as the case index will make the search rate slow, and the main feature unimportant, for the reason that the relative weight which is allotted to every feature must diminish. And on the other hand, it is hard to include all the features in the case index.Therefore, considering the practicality and the demand of rapid design, the case index includes both the major feature of the workpiece and the structure of fixture. The case index code is made up of 16 digits: 13 digits for case features and 3 digits for case identification number.The first 13 digits represent 13 features. Each digit is corresponding to an attribute of the feature, which may be one of“*”, “?”, “1”, “2”,…,“A”,“B”,…, “Z”,…, etc. In which, “*”means anyone, “?”uncertain, “0”nothing.The system rules: fixture type, workpiece shape, locating model cannot be “*”or“?”. When the system is designed, the attribute information of the three items does not have these options, which means the certain attribute must be selected.The last three digits are the case identification number, which means the 13 digits of the case feature are the same, and the number of these three digits is used for distinguishing them.The system also rules: “000”is a prototype case, which is used for retrieval, and other cases are “001”,“002”,…, which are used for reference cases to be searched by designers. If occasionally one of them needs to be changed as theprototype case, first it must be required to apply to change the one to “000”, and the former is changed to referential case automatically.The construction of the case index code is shown in Fig.1.1.2 Case libraryThe case library consists of lots of predefined cases. Case representation is one of the most important issues in case based reasoning. So compounding with the index code,.1.3 Hierarchical form of CaseThe structure similarity of the fixture is represented as the whole fixture similarity, components similarity and component similarity. So the whole fixture case library, components case library, component case library of fixture are formed correspondingly. Usually design information of the whole fixture is composed of workpiece information and workpiece procedure information, which represent the fixture satisfying the specifically designing function demand. The whole fixture case is made up of function components, which are described by the function components’ names and numbers. The components case represents the members. (function component and other structure components,main driven parameter, the number, and their constrain relations.) The component case (the lowest layer of the fixture) is the structure of function component and other components. In the modern fixture design there are lots of parametric standard parts and common non standard parts. So the component case library should record the specification parameter and the way in which it keeps them.2 Strategy of Case RetrievalIn the case based design of fixtures ,the most important thing is the retrieval ofthe similarity, which can help to obtain the most similar case, and to cut down the time of adaptation. According to the requirement of fixture design, the strategy of case retrieval combines the way of the nearest neighbor and knowledge guided. That is, first search on depth, then on breadth; the knowledge guided strategy means to search on the knowledge rule from root to the object, which is firstly searched by the fixture type, then by the shape of the workpiece, thirdly by the locating method. For example, if the case index code includes the milling fixture of fixture type, the search is just for all milling fixtures, then for box of workpiece shape, the third for 1plane+ 2pine of locating method. If there is no match of it, then the search stops on depth, and returns to the upper layer, and retrieves all the relative cases on breadth.Retrieval algorithms:1)According to the case index information of fixture case library, search the relevant case library;2)Match the case index code with the code of each case of the case library, and calculate the value of the similarity measure;3)Sort the order of similarity measure, the biggest value, which is the most analogical case.Similarity between two cases is based on the similarity between the two cases. features. The calculation of similarity measure depends on the type of the feature. The value of similarity can be calculated for numerical values, for example, compare Workpiece with the weight of 50kg and 20kg. The value can also be calculated between non numerical values, for example, now the first 13 digits index code is all non numerical values. The similarity measure of a fixture is calculated as follows:where S is the similarity measure of current fixture, n is the number of the index feature, is the weight of each feature, is the similarity measure of the attribute of the i2th feature with the attribute of relative feature of the j-th case in the case library. At the same time, , the valuecounts as follows:.Where is the value of the index attribute of the i-th feature, and is the value of attribute of the relative i-th feature of the j-th case in case library. So there are two methods to select the analogical fixture. One is to set the value. If the values of similarity measure of current cases were less than a given value, those cases would not be selected as analogical cases. When the case library is initially set up, and there are only a few cases, the value can be set smaller. If there are lots of analogical cases, the value should get larger. The other is just to set the number of the analogical cases (such as10), which is the largest value of similarity measure from the sorted order.3 Case adaptation and Case Storage3.1 Case adaptationThe modification of the analogical case in the fixture design includes the following three cases:1) The substitution of components and the component;2) Adjusting the dimension of components and the component while the form remains;3) The redesign of the model.If the components and component of the fixture are common objects, they can be edited, substituted and deleted with tools, which have been designed.3.2 Case storageBefore saving a new fixture case in the case library, the designer must consider whether the saving is valuable. If the case does not increase the knowledge of the system, it is not necessary to store it in the case library. If it is valuable, then the designer must analyze it before saving it to see whether the case is stored as a prototype case or as reference case. A prototype case is a representation that can describe the main features of a case family. A case family consists of those cases whose index codes have the same first 13 digits and different last three digits in the case library. The last three digits of a prototype case are always “000”. A reference case belongs to the same family as the prototype case and is distinguished by the different last three digits.From the concept that has been explained, the following strategies are adopted:1) If a new case matches any existing case family, it has the same first 13 digits as an existing prototype case, so the case is not saved because it is represented well by the prototype case. Or is just saved as a reference case (the last 3 digits are not “000”, and not the same with others) in the case library.2) If a new case matches any existing case family and is thought to be better at representing this case family than the previous prototype case, then the prototype case is substituted by this new case, and the previous prototype case is saved as a reference case.3) If a new case does not match any existing case family, a new case family will be generated automatically and the case is stored as the prototype case in the case library.4 Process of CBR in Fixture DesignAccording to the characteristics of fixture design, the basic information of the fixture design such as the name of fixture, part, product and the designer, etc. must be input first. Then the fixture file is set up automatically, in which all components of the fixture are put together. Then the model of the workpiece is input or designed. The detailed information about the workpiece is input, the case index code is set up, and then the CBR begins to search the analogical cases, relying on the similarity measure, and the most analogical case is selected out. If needed, the case is adapted to satisfy the current design, and restored into the case library. The flowchart of the process is shown in Fig.3.5 Illustrating for Fixture Design by CBRThis is a workpiece (see Fig.4). Its material is 45# steel. Its name is seat. Its shape is block, and the product batch size is middle, etc. A fixture is turning fixture that serves to turn the hole, which needs to be designed.The value of feature, attribute, case index code and weight of the workpiece is show n in Tab.2.Through searching, and calculating the similarity, the case index code of the most similar case is 19325513321402000, and the detailed information is show n in Tab. 3.The similarity is calculated as follows:So the value of similarity measure of the fixture which needs to be designed with the most analogical case in case library is 0.806, and the structure of the most analogical case is shown in Fig.5.After having been substituted the component, modified the locating model and clamp model, and adjusted the relative dimension, the new fixture is designed, and the figure is show n in Fig.6.As there is not the analogical fixture in the case library, the new fixture is restored in to the case library. The case index code is 19325513311402000.6 ConclusionCBR, as a problem solving methodology, is a more efficient method than an expert system to simulate human thought, and has been developed in many domains where knowledge is difficult to acquire. The advantages of the CBR are as follows: it resembles human thought more closely; the building of a case library which has self learning ability by saving new cases is easier and faster than the building of a rule library; and it supports a better transfer and explanation of new knowledge that ismore different than the rule library. A proposed fixture design framework on the CBR has been implemented by using Visual C ++, UG/Open API in U n graphics with Oracle as database support, which also has been integrated with the 32D parametric common component library, common components library and typical fixture library. The prototype system, developed here, is used for the aviation project, and aids the fixture designers to improve the design efficiency and reuse previous design resources.外文翻译基于事例推理的夹具设计研究与应用摘要: 根据基于事例的设计方法,提出采用工序件的特征信息和夹具的结构特征信息来描述夹具的相似性,并建立了包括这2方面主要特征信息为基础的事例索引码,设计了事例库的结构形式,创建了层次化的事例组织方式;同时,提出了基于知识引导的夹具事例检索算法,以及事例的修改和采用同族事例码进行相似事例的存贮,形成了基于事例推理的夹具设计.所开发的原型系统在型号工程夹具设计等项目的设计过程中得到了应用,并取得了令人满意的使用效果.关键词: 基于事例的推理夹具设计 CAD夹具是以确定工件安全定位准确为目的的装置,并在加工过程中保持工件与刀具或机床的位置一致不变。
夹具设计中英文对照

Optimization of fixture design with consideration of thermal deformation inface milling考虑端铣中热变形的最佳化夹具设计Huang, YingAbstract摘要Effective methods of fixture design are proposed to reduce machining error caused by cutting heat in face milling. Experiments show that thermal effect is critical to final error in the finish cut and that it dominates cutting accuracy. Therefore, a mathematical model is structured of the cutting heat source on behalf of the cutting tool, and the flatness error generation process in face finishing is demonstrated by computational simulation based on the moving cutting heat source model with FEW Concerning surface flatness due to the moving cutting heat source for relatively thin plate-shaped workpieces, different methodologies have been proposed to reduce flatness error, namely, the application of additional supports and optimization of the fixturing support layout. Cutting experiments and computational analyses show the effectiveness of the additional supports and the optimization methodology applied on the fixture design in view of flatness error due to cutting heat. The proposed methodologies are applicable and beneficial to improve cutting accuracy not only of plate-shaped workpieces but also of other geometry workpieces.用于减小端铣中因切削热而引起的加工误差的有效的夹具设计方法已经被提出。
车床机床夹具类外文文献翻译、中英文翻译、外文翻译

中北大学信息商务学院本科毕业设计英文参考资料题目 Lathes系名专业姓名学号指导教师2016年6 月2 日译文标题车床简介原文标题Lathes作者(Serope kalpakjian)译名卡尔帕基安国籍美国原文出处/原文:LathesLathes are machine tools designed primarily to do turning, facing and boring, Very little turning is done on other types of machine tools, and none can do it with equal facility. Because lathes also can do drilling and reaming, their versatility permits several operations to be done with a single setup of the work piece. Consequently, more lathes of various types are used in manufacturing than any other machine tool.The essential components of a lathe are the bed, headstock assembly, tailstock assembly, and the leads crew and feed rod.The bed is the backbone of a lathe. It usually is made of well normalized or aged gray or nodular cast iron and provides s heavy, rigid frame on which all the other basic components are mounted. Two sets of parallel, longitudinal ways, inner and outer, are contained on the bed, usually on the upper side. Some makers use an inverted V-shape for all four ways, whereas others utilize one inverted V and one flat way in one or both sets, They are precision-machined to assure accuracy of alignment. On most modern lathes the way are surface-hardened to resist wear and abrasion, but precaution should be taken in operating a lathe to assure that the ways are not damaged. Any inaccuracy in them usually means that the accuracy of the entire lathe is destroyed.The headstock is mounted in a foxed position on the inner ways, usually at the left end of the bed. It provides a powered means of rotating the word at various speeds . Essentially, it consists of a hollow spindle, mounted in accurate bearings, and a set of transmission gears-similar to a truck transmission—through which the spindle can be rotated at a number of speeds. Most lathes provide from 8 to 18 speeds, usually in a geometric ratio, and on modern lathes all the speeds can be obtained merely by moving from two to four levers. An increasing trend is to provide a continuously variable speed range through electrical or mechanical drives.Because the accuracy of a lathe is greatly dependent on the spindle, it is of heavyconstruction and mounted in heavy bearings, usually preloaded tapered roller or ball types. The spindle has a hole extending through its length, through which long bar stock can be fed. The size of maximum size of bar stock that can be machined when the material must be fed through spindle.The tailsticd assembly consists, essentially, of three parts. A lower casting fits on the inner ways of the bed and can slide longitudinally thereon, with a means for clamping the entire assembly in any desired location, An upper casting fits on the lower one and can be moved transversely upon it, on some type of keyed ways, to permit aligning the assembly is the tailstock quill. This is a hollow steel cylinder, usually about 51 to 76mm(2to 3 inches) in diameter, that can be moved several inches longitudinally in and out of the upper casting by means of a hand wheel and screw.The size of a lathe is designated by two dimensions. The first is known as the swing. This is the maximum diameter of work that can be rotated on a lathe. It is approximately twice the distance between the line connecting the lathe centers and the nearest point on the ways, The second size dimension is the maximum distance between centers. The swing thus indicates the maximum work piece diameter that can be turned in the lathe, while the distance between centers indicates the maximum length of work piece that can be mounted between centers.Engine lathes are the type most frequently used in manufacturing. They areheavy-duty machine tools with all the components described previously and have power drive for all tool movements except on the compound rest. They commonly range in size from 305 to 610 mm(12 to 24 inches)swing and from 610 to 1219 mm(24 to 48 inches) center distances, but swings up to 1270 mm(50 inches) and center distances up to3658mm(12 feet) are not uncommon. Most have chip pans and a built-in coolant circulating system. Smaller engine lathes-with swings usually not over 330 mm (13 inches ) –also are available in bench type, designed for the bed to be mounted on a bench on a bench or cabinet.Although engine lathes are versatile and very useful, because of the time required for changing and setting tools and for making measurements on the work piece, thy are not suitable for quantity production. Often the actual chip-production tine is less than 30% of the total cycle time. In addition, a skilled machinist is required for all the operations, and such persons are costly and often in short supply. However, much of the operator’s time is consumed by simple, repetitious adjustments and in watching chips being made. Consequently, to reduce or eliminate the amount of skilled labor that is required, turret lathes, screw machines, and other types of semiautomatic and automatic lathes have been highly developed and are widely used in manufacturing.2 Numerical ControlOne of the most fundamental concepts in the area of advanced manufacturing technologies is numerical control (NC). Prior to the advent of NC, all machine tools ere manually operated and controlled. Among the many limitations associated with manual control machine tools, perhaps none is more prominent than the limitation of operator skills. With manual control, the quality of the product is directly related to and limited to the skills of the operator. Numerical control represents the first major step away from human control of machine tools.Numerical control means the control of machine tools and other manufacturing systems through the use of prerecorded, written symbolic instructions. Rather than operating a machine tool, an NC technician writes a program that issues operational instructions to the machine tool. For a machine tool to be numerically controlled, it must be interfaced with a device for accepting and decoding the programmed instructions, known as a reader.Numerical control was developed to overcome the limitation of human operators, and it has done so. Numerical control machines are more accurate than manually operated machines, they can produce parts more uniformly, they are faster, and the long-run tooling costs are lower. The development of NC led to the development of several other innovations in manufacturing technology:Electrical discharge machining,Laser cutting,Electron beam welding.Numerical control has also made machine tools more versatile than their manually operated predecessors. An NC machine tool can automatically produce a wide of parts, each involving an assortment of widely varied and complex machining processes. Numerical control has allowed manufacturers to undertake the production of products that would not have been feasible from an economic perspective using manually controlled machine tolls and processes.Like so many advanced technologies, NC was born in the laboratories of the Massachusetts Institute of Technology. The concept of NC was developed in the early 1950s with funding provided by the U.S. Air Force. In its earliest stages, NC machines were able to made straight cuts efficiently and effectively.However, curved paths were a problem because the machine tool had to be programmed to undertake a series of horizontal and vertical steps to produce a curve. The shorter the straight lines making up the steps, the smoother is the curve, Each line segment in the steps had to be calculated.This problem led to the development in 1959 of the Automatically Programmed Tools (APT) language. This is a special programming language for NC that uses statementssimilar to English language to define the part geometry, describe the cutting tool configuration, and specify the necessary motions. The development of the APT language was a major step forward in the fur ther development from those used today. The machines had hardwired logic circuits. The instructional programs were written on punched paper, which was later to be replaced by magnetic plastic tape. A tape reader was used to interpret the instructions written on the tape for the machine. Together, all of this represented a giant step forward in the control of machine tools. However, there were a number of problems with NC at this point in its development.A major problem was the fragility of the punched paper tape medium. It was common for the paper tape containing the programmed instructions to break or tear during a machining process. This problem was exacerbated by the fact that each successive time a part was produced on a machine tool, the paper tape carrying the programmed instructions had to be rerun through the reader. If it was necessary to produce 100 copies of a given part, it was also necessary to run the paper tape through the reader 100 separate tines. Fragile paper tapes simply could not withstand the rigors of a shop floor environment and this kind of repeated use.This led to the development of a special magnetic plastic tape. Whereas the paper carried the programmed instructions as a series of holes punched in the tape, the plastic tape carried the instructions as a series of magnetic dots. The plastic tape was much stronger than the paper tape, which solved the problem of frequent tearing and breakage. However, it still left two other problems.The most important of these was that it was difficult or impossible to change the instructions entered on the tape. To made even the most minor adjustments in a program of instructions, it was necessary to interrupt machining operations and make a new tape. It was also still necessary to run the tape through the reader as many times as there were parts to be produced. Fortunately, computer technology became a reality and soon solved the problems of NC associated with punched paper and plastic tape.The development of a concept known as direct numerical control (DNC) solved the paper and plastic tape problems associated with numerical control by simply eliminating tape as the medium for carrying the programmed instructions. In direct numerical control, machine tools are tied, via a data transmission link, to a host computer. Programs for operating the machine tools are stored in the host computer and fed to the machine tool an needed via the data transmission linkage. Direct numerical control represented a major step forward over punched tape and plastic tape. However, it is subject to the same limitations as all technologies that depend on a host computer. When the host computer goes down, the machine tools also experience downtime. This problem led to the development of computernumerical control.3 TurningThe engine lathe, one of the oldest metal removal machines, has a number of useful and highly desirable attributes. Today these lathes are used primarily in small shops where smaller quantities rather than large production runs are encountered.Th e engine lathe has been replaced in today’s production shops by a wide variety of automatic lathes such as automatic of single-point tooling for maximum metal removal, and the use of form tools for finish on a par with the fastest processing equipment on the scene today.Tolerances for the engine lathe depend primarily on the skill of the operator. The design engineer must be careful in using tolerances of an experimental part that has been produced on the engine lathe by a skilled operator. In redesigning an experimental part for production, economical tolerances should be used.Turret Lathes Production machining equipment must be evaluated now, more than ever before, this criterion for establishing the production qualification of a specific method, the turret lathe merits a high rating.In designing for low quantities such as 100 or 200 parts, it is most economical to use the turret lathe. In achieving the optimum tolerances possible on the turrets lathe, the designer should strive for a minimum of operations.Automatic Screw Machines Generally, automatic screw machines fall into several categories; single-spindle automatics, multiple-spindle automatics and automatic chucking machines. Originally designed for rapid, automatic production of screws and similar threaded parts, the automatic screw machine has long since exceeded the confines of this narrow field, and today plays a vital role in the mass production of a variety of precision parts. Quantities play an important part in the economy of the parts machined on the automatic screw machine. Quantities less than on the automatic screw machine. The cost of the parts machined can be reduced if the minimum economical lot size is calculated and the proper machine is selected for these quantities.Automatic Tracer Lathes Since surface roughness depends greatly on material turned, tooling , and feeds and speeds employed, minimum tolerances that can be held on automatic tracer lathes are not necessarily the most economical tolerances.In some cases, tolerances of 0.05mm are held in continuous production using but one cut . groove width can be held to 0.125mm on some parts. Bores and single-point finishes can be held to 0.0125mm. On high-production runs where maximum output is desirable, a minimum tolerance of 0.125mm is economical on both diameter and length of turn。
机床刀具设计机械加工工艺夹具外文文献翻译、中英文翻译、外文翻译

英语原文:Design Of Tool Machine PropResearch significanceThe original knife machine control procedures are designed individually, not used tool management system, features a single comparison, the knife only has to find the tool knife, knife positioning the shortest path, axis tool change, but does not support large-scale tool.Automatic knife in the knife election, in the computer memory knife-election on the basis of using the Siemens 840 D features, and the election procedures knife more concise, and complete the space Daotao View. ATC use the knife rapid completion of STEP-7 programming, and have been tested in practice. In the positioning of the knife, PLC controlled modular design method, which future production of similar machines will be very beneficial, it is easy to use its other machine. Automatic tool change systems will be faster growth, reduced tool change time, increase the positioning accuracy tool is an important means to help NC technology development.Tool and inventory components of modern production is an important link in the management, especially for large workshop management. The traditional way of account management, and low efficiency, high error rate, and not sharing information and data, tools and the use of state can not track the life cycle, are unable to meet the current information management needs. With actual production, we have to establish a workshop tool for the three-dimensional tool storage system to meet the knife workshop with auxiliary storage and management needs.The system uses optimization technology, a large number of computer storage inventory information, timely, accurate, and comprehensive tool to reflect the inventory situation. The entire system uses a graphical interface, man-machine dialogue tips from the Chinese menu, select various functions can be realized and the importation of all kinds of information. Management system using online help function. Through the workshop management, network management and sharing of information. Have automated inventory management, warehousing management tool, a tool for the management and statistical functions.1.System components and control structureThe entire system, including the structure and electrical machinery control systems.1.1.1Mechanical structure and working principleTool from the stent, drive, drive system, Turret, shielding, control system, and electrical components. Support from the column, beam, the upper and lower guide Central track, and track support component.1) Drive for the system chosen VVVF method. Cone used brake motors, with VVVF by Cycloid reducer through sprocket drive.2) Drag a variable frequency drive system and control technology. VVVF adopted, will speed drive shaft in the normal range adjustment to control the speed rotary turret to 5 ~ 30mm in, the drive shaft into two, two under through sprocket, the two profiled rollers Chain driven rotating shelves. Expansion chain adopted by the thread tight regulation swelling, swelling the regular way. - Conditioned, under the same chain-of-conditioning, so that the chain of uniform.3) Turret and shields the entire total of 14 independent Turret. 13 of them as a socket-Turret, as adrawer-Turret, each Turret back through the pin and, under the conveyor chain link chain plate, installed at the bottom roller, chain driven rotating turret rotation along the track. Outlet-Turret and BT50-BT40 Turret Turret two kinds of forms. To strengthen management, security, landscaping modeling, shelf peripherals and shields. Turret-drawer drawer placed at six other Des V oeux a knife, can be categorized with some of knife auxiliary equipment, such as bits, such as turning tools.1.1.2.Electrical Control SystemThis tool storage systems is the main electrical control their shelves for operational control and position control. Operational control equipment, including operation of the start of braking control. Position Control is the main location and address of the shelves for testing. Control system as shown in Figure 1.图 1 Tool Control System for the1) Electric Transmission horizontal rotary tool storage systems are the mechanical movements are repeated short-term work system. And the run-time system needs some speed, speed transmission needs, the system will use VVVF method can be used simple structure, reliable operation of the motor and frequency inverter.2) Control of the system is divided into two kinds of manual control and automatic control, manual control as a general reserve and debugging methods of work; ways to the system control computer (IPC) and the control unit (inverter contactor , etc.) consisting of a control system.3) location and positioning accuracy of the system automatically identify the site and location using a detection device as proximity switches, relays through the plate-point isolation and the number plate recorded close to the switching signal acquisition and operation of Hutchison with a Optimal Path addressable identify the current location and shelves of the purpose of the shelf location. In order to enable a more accurate positioning system, adopted two photoelectric switches, to detect the two shelves of the two films.1.2.The functions of the knifeknife The is the role of reserves a certain number of tools, machine tool spindle in hand to achieve the fungibility a disc cutter knife is the type of library, the chain knives, and other means, in the form of the knife and capacity according to the Machine Tool to determine the scope of the process.mon typesThe knife is a tool storage devices, the common knife mainly in the following forms:(1) the turret knifeIncluding the first level turret vertical turret and the first two, see Figure 2.6 a) and b):(2) the disc cutterDisc knife in the library with discoid knife, cutting tool along See how vertical arrangement (including radial and axial from knife from knife), along See how radial array into acute or arranged in the form of the knife. Simple, compact, more applications, but are ring-cutter, low utilization of space. Figure 2.7 a) to c). If the knife storage capacity must be increased to increase the diameter of the knife, then the moment of inertia also increased correspondingly, the election campaign long knife. Tool number not more than 32 general. Cutter was multi-loop order of the space utilization knife, but inevitably given the knife from complex institutions, applicable to the restricted space Machine Tool storage capacity and more occasions. Two-disc structure is two smaller capacity knife on both sides of the sub-spindle place, more compact layout, the number of certificates corresponding increase knife, apply to small and medium-sized processing center.(3) the chain knifeIncluding single-and multi-ring chain ring chain, chain link can take ma ny forms change, see Figure 2.8 a) to c), the basic structureFeatures: knife apply to thelarger capacity of theoccasion, the space of thesmall number of generallyapplicable to the tool in the30-120. Only increase thelength of the chain tool willincrease the number shouldnot be increasedcircumferential speed of itsmoment of inertia of theknife does not increase thedisc as large.(4) linear combination knife and the knife libraryThe linear knife simple structure in Figure 2.9, tool single order, the capacity of small knife, used for CNC lathe and drill press on. Because the location of fixed knife, ATC completed action by the spindle without manipulator. The cutter knife is generally the turret combination turret with a combination of the disc cutter knife and the chain combination. Every single knife the knife certificates of smaller, faster tool change. There are also some intensive drum wheel, and the lattice-type magazine for the knife, the knife-intensive though. Small footprint, but because of structural constraints, basically not used for single processing center, the concentration used for FMS for the knife system.1.4 Tool storage capacityTool storage capacity of the first to consider the needs of processing, from the use of point of view, generally 10 to 40 knives, knife will be the utilization of the high, and the structure is compact.1.5 Tool options(1) choose to order processing tool according to the order, followed Add to the knife every knife in the Block. Each tool change, the order of rotation of a cutter knife on location, and remove the need knives, has been used by the cutter knife can be returned to the original Block, can also order Add Block, a knife. However, as the knife in the tool in different processes can not be repeated use of the knife must increase the capacity and lower utilization rate.(2) most of the arbitrary choice of the current system of using arbitrary NC election knives, divided into Daotao coding, coding and memory-cutter, three. Daotao coding tool code or knives or Daotao need to install the code used to identify, in accordance with the general principle of binary coding coding. Tool knife election coding method uses a special knife handle structure, and each of the coding tool. Each of the tool has its own code, thereby cutting tool can be in different processes repeatedly used, not to replace the tool back at the original knife, the knife capacity can be reduced accordingly. Memory-election this paper knife, in this way can knives and knife in the position corresponding to the Daotao memory of the PLC in the NC system, no matter which tool on the Inner knife, tool information is always there in mind, PLC . On the knife with position detection devices, will be the location of each Daotao. This tool can be removed and sent back to arbitrary. On the knife is also a mechanical origin, every election, the nearest knife selection.1.6.Control of the knife(1) the knife as a system to control the positioning axis. In the ladder diagram in accordance with the instructions for computing T code comparison of the output angle and speed of instructions to the knife the knife servo drive servo motor. Tool storage capacity, rotation speed, and / deceleration time, and other system parameters can be set in such a manner free from any outside influence positioning accurate and reliable but the cost is higher.(2) knife from the hydraulic motor drives, fast / slow the points, with proximity switches count and positioning. In comparison ladder diagram of the current storage system knife (knife spindle) and goals knife (pre-knife) and computing, then output rotation instructions, judging by the shortest path rotation in place. This approach requires sufficient hydraulic power and electromagnetic valve knife the rotational speed can be adjusted through the throttle. But over time may be oily hydraulic, oil temperature and environmental factors impact the change in velocity and accuracy. Not generally used in large and medium-sized machine tool change frequently.(3) the knife from AC asynchronous motor driven cam mechanism (Markov institutions), with proximity switches count, which means stable operation, and generally accurate and reliable positioning cam used in conjunction with a mechanical hand, ATC fast-positioning.2. ATC, the main types, characteristics, and the scope of application2.1 Auto Rotary ToolRotary Tool automatically on the useof CNC machine tool is a simpleinstallation of automatic tool change, theQuartet and 47.60 Turret Tool variousforms, such as rotary turret were installedon four, six or more of the Tool , NCinstructions by ATC. Rotary Tool has twovertical and horizontal, relatively simplestructure, applicable to economic CNClathe.Rotary Tool in the structure must havegood strength and stiffness, resistance tobear rough Cutting Tool in the cuttingforce and reduce the role of deformationand improve processing accuracy.Rotating Tool to choose reliablepositioning programme structure andreasonable position, in order to ensure thateach rotary turret to a higher position afterrepeated positioning accuracy (typically0.001 to 0.005mm). Figure 2.1 shows thespiral movements of the Quartet Turret.Auto Rotary Tool in the simplest ofATC, is 180 º rotary ATC devices, asshown in Figure 2.2 ATC instructionsreceived, the machine control system put ATC spindle control to the designated location at the same time, the tool movement to the appropriate location, ATC, with the rotary axis and at the same time, the knives matching tool; drawbars from Spindle Cutting Tools rip, ATC, will be the tool from their position removed; ATC, 180 º rotary tool spindle and the tool and tool away; ATC, the Rotary At the same time, the tool refocusing its position to accept Spindle removed from the cutting tool; Next, ATC, will be replaced with the cutter knives were unloaded into the spindle and tool: Finally, back to the original ATC, "standby" position. At this point, ATC completed procedures to continue to run. This ATC, the main advantage of simple structure, the less movement, fast tool change. The main disadvantage is that knives must be kept in parallel with the axis of the plane, and after the home side compared to the tool, chip and liquid-cutting knife into the folder, it is necessary to the tool plus protection. Cone knife folder on the chip will cause ATC error, or even damage knife folders, and the possibility of spindle. Some processing centre at the transfer, and the tool side. When the ATC command is called, the transfer-cutter knives will be removed, the machine go forward, and positioning with the ATC, in line with the position. 180 º "Rotary ATC devices can be used horizontal machine, can also be used for vertical machining centers.2. 2 ATC head-turret installedWith rotating CNC machine tool often used such ATC devices, with a few turret head spindle, each with a spindle on both knives, the first tower interim process can be automatic tool change-realization. The advantage is simple structure, tool change time is short, only about 2 s. However, due to spatial constraints, the number of spindle can not be too much, usually only apply to processes less, not to high precision machine tools, such as the NC drill, such as CNC milling machine. In recent years there has been a mechanical hand and the turret head with a knife for the automatic tool change ATC devices, as shown in Figure 2.3. It is in fact a turret head ATC, and the knife-ATC device combination. The principle is as follows:5 turret on the first two tool spindle 3 and 4, when using the tool spindle 4 processing tool, the manipulator 2 will be the next step to the need for the tool does not work on the tool spindle 3 until after the completion of this process , the first rotary turret 180 º, ATC completed. ATC most of their time and processing time coincidence, the only real tool change time turret transposition of the first time, this approach mainly used for ATC and NC NC drilling file bed.2. 3.Daidao system for the automatic tool changeFigure 2.4 shows the knife and the whole machine tool CNC machine tools for the appearance of Fig. Figure 2.5 shows the knife and split-type machine to the appearance of CNC machine tool plans.At this point, knife storage capacity, a heavier tool can, and often additional transport unit to complete the knife between the spindle and cutting tool transport.Daidao the knife from the ATC, the election knives, automatic loading and unloading machine tool and tool exchange institutions (manipulator), composed of four parts, used widely.Tool Automatic Tool Change the manipulator system, the whole process more complicated ATC. We must first used in the processing of all installed in the standard tool on the knife handle in the machine outside the pre-size, according to a certain way Add to the knife. ATC, selected first in the knife knife, and then from ATC, from the knife from the knife or spindle, exchange, the new knife into the spindle, the old knife back into the knife.ATC, as the former two knives to accommodate a limited number can not be too many, can not meet the needs of complex parts machining, CNC machine tool Automatic Tool Change Daidao the use of the automatic tool change devices. The knife has more capacity, both installed in the spindle box side or above. As for the automatic tool change Daidao device CNC machine tool spindle box only a spindle, spindle components to high stiffness to meet the machining requirements. The number of establishments in larger knife, which can meet the more complex parts of the machining processes, significantly improving productivity. Daidao system for the automatic tool change applied to drilling centres and CNC machining centers. The comparison drawn Daidao automatic tool change system is the most promising.3.PLC control of the knife random mode of election 3. 1Common methods of automatic election knifeAutomatic control of the knife CNC refers to the system after the implementation of user instructions on the knife library automation process, including the process to find knives and automatic tool change [(63,71]. CNC Machining Center device (CNC) directive issued by the election knife , a knife, the tool required to take the knife position, said the election automatic knife. automatically elected knife There are two ways: random sequence election knives and knife election method.3.1.1 order election knifeTool Selection order is the process tool according to the sequence of the insert knife, the use of knives in order to take place, used knives back at the original knife, can also order Add Block, a knife. In this way, no need Tool identification devices, and drive control is a relatively simple, reliable and can be used directly from the points of the knife machinery to achieve. But the knives in each of the tool in different processes can not be reused, if the tool is installed in accordance with the order of the knife, there will be serious consequences. The need to increase the number of knives and knife the capacity of the tool and reduce the utilization of the knife.3.1.2Random election knifeRandom election under the knife is arbitrary instructions to select the required tools, then there must be tool identification devices. Tool knife in the library do not have the processing in accordance with the order of the workpiece can be arbitrary storage. Each of the tool (or knife blocks) are for a code, automatic tool change, the rotary cutter, every tool have been the "tool identification device" acceptable identification. When CNC tool code and the code in line with directives of the tool selected, the rotary cutter knives will be sent to the ATC position, waiting to grab manipulator. Random knife election is the advantage of the cutter knife in the order has nothing to do with the processing sequence, the same tool can be used repeatedly. Therefore, the relatively small number of knives, knife the corresponding smaller. Random elections knife on the tool must be coded to identify. There are three main coding.1. Tool coding. Adopt special knife handle structure coding, the drawbars on the knife handle back-end packages such as spacing of the coding part of the lock-nut fixed. Coding diameter ring diameter of a size two, respectively, said that binary "1" and "0" to the two rings are different, can be a series of code. For example, there are six small diameter of the ring can be made to distinguish between 63 (26-1 = 63) of the coding tool. All of 0 normally not allowed to use the code, to avoid the cutter knife Block did not confuse the situation.2. Knife Block coding. On the knife Block coding, coding tool, and tool into line with the number of knives in the Block. ATC knife when the rotation, so that each knife seats followed through knowledge knife, knife found blocks, knives stopped the rotation. At this time there is no knife handle encoding part of the knife handle simplified.3. Annex coding methods. This style of coding keys, coded cards, coding and coding-disc, which is the most widely used coding keys. First toknives are attached to a tool of the show wrapped coding keys, and when the cutter knife to the store at knife in, so put the number of keys to remember knife Block Road, will be inserted into key to the coding Block next to the key hole in the seat for the knife to the numbers. ConclusionFocused on in today's manufacturing environment tool storage and management of new models and methods, practical application of good results in systems integration and optimization, and other aspects of operations will be further explored, so that it has a higher theoretical and practical level.译文:机床刀具设计课题研究意义机床原来的刀库控制程序是单独设计的,没有采用刀具管理系统,功能也比较单一,只实现了刀库刀具的找刀、刀库最短路径定位、主轴换刀,而且不支持大型刀具。
机械工程专业毕业设计外文翻译
英文原文名Lthes中文译名车床10/ 1中文译文:车床车床主要是为了进行车外圆、车端面和镗孔等项工作而设计的机床。
车削很少在其他种类的机床上进行,而且任何一种其他机床都不能像车床那样方便地进行车削加工。
由于车床还可以用来钻孔和铰孔,车床的多功能性可以使工件在一次安装中完成几种加工。
因此,在生产中使用的各种车床比任何其他种类的机床都多。
车床的基本部件有:床身、主轴箱组件、尾座组件、溜板组件、丝杠和光杠。
床身是车床的基础件。
它能常是由经过充分正火或时效处理的灰铸铁或者球墨铁制成。
它是一个坚固的刚性框架,所有其他基本部件都安装在床身上。
通常在床身上有内外两组平行的导轨。
有些制造厂对全部四条导轨都采用导轨尖朝上的三角形导轨(即山形导轨),而有的制造厂则在一组中或者两组中都采用一个三角形导轨和一个矩形导轨。
导轨要经过精密加工以保证其直线度精度。
为了抵抗磨损和擦伤,大多数现代机床的导轨是经过表面淬硬的,但是在操作时还应该小心,以避免损伤导轨。
导轨上的任何误差,常常意味着整个机床的精度遭到破坏。
主轴箱安装在内侧导轨的固定位置上,一般在床身的左端。
它提供动力,并可使工件在各种速度下回转。
它基本上由一个安装在精密轴承中的空心主轴和一系列变速齿轮(类似于卡车变速箱)所组成。
通过变速齿轮,主轴可以在许多种转速下旋转。
大多数车床有8~12种转速,一般按等比级数排列。
而且在现代机床上只需扳动2~4个手柄,就能得到全部转速。
一种正在不断增长的趋势是通过电气的或者机械的装置进行无级变速。
由于机床的精度在很大程度上取决于主轴,因此,主轴的结构尺寸较大,通常安装在预紧后的重型圆锥滚子轴承或球轴承中。
主轴中有一个贯穿全长的通孔,长棒料可以通过该孔送料。
主轴孔的大小是车床的一个重要尺寸,因此当工件必须通过主轴孔供料时,它确定了能够加工的棒料毛坯的最大尺寸。
数字控制的机器比人工操纵的机器精度更高、生产出零件的一致性更好、生产速度更快、而且长期的工艺装备成本更低。
机械类车床外文翻译
毕业设计(论文)——外文翻译(原文)Lathe来源:/wiki/LatheA lathe is a machine tool which spins a block of material to perform various operations such as cutting, sanding, knurling, drilling, or deformation with tools that are applied to the workpiece to create an object which has symmetry about an axis of rotation.Lathes are used in woodturning, metalworking, and glassworking. Lathes can be used to shape pottery, the best-known design being the potter's wheel. Most suitably equipped metalworking lathes can also be used to produce most solids of revolution, plane surfaces and screw threads or helices. Ornamental lathes can produce three-dimensional solids of incredible complexity. The material is held in place by either one or two centers, at least one of which can be moved horizontally to accommodate varying material lengths. Examples of objects that can be produced on a lathe include cue sticks, table legs, bowls, baseball bats, crankshafts and camshafts.HistoryThe lathe is an ancient tool, dating at least to the Egyptians ,and known and used in Greece, the Roman and Byzantine Empires.The origin of turning dates to around 1300BC when the Egyptians first developed a two-person lathe. One person would turn the wood workpiece with a rope while the other used a sharp tool to cut shapes in the wood. The Romans improved the Egyptian design with the addition of a turning bow. Early bow lathes were also developed and used in Germany, France and Britain. In the Middle Ages a pedal replaced hand-operated turning, freeing both the craftsman's hands to hold the woodturning tools. The pedal was usually connected to a pole, often a straight-grained sapling. The system today is called the "spring pole" lathe. Spring pole lathes were in common use into the early 20th Century. A two-person lathe, called a "great lathe", allowed a piece to turn continuously (like today's power lathes). A master would cut the wood while an apprentice turned the crank。
机械毕业设计中英翻译
英语原文:CAD/CAM is the technical expression, indicates the computer-aided design and the computer aided manufacturing.This is one item in the design and the production, carries out certain function technology about the use computer data.This technology is completing the design and the production direction to the place develops.In these two traditions was considered is in the production process out of the ordinary, independent function.In brief, CAD/CAM will be able to provide the technology base for the future complete computer production.Looked from the computer science angle that, the design and the manufacture process is one has, processing, the exchange and the management process about the product information.The people use the computer to take the main technical method, from forms in one's mind to the product to put in the market in the entire process information to carry on the analysis and processing, produces and utilizes each kind of numerical information and the graph information, carries on the product the design and the manufacture.The CAD/CAM technology is not the traditional design, the manufacture flow method simple reflection, also is not limits in the partial use computer takes the tool in the individual step or the link, but is unifies the computer science and the project domain specialized technology as well as human's wisdom and the experience take the modern scientific method as the instruction, in the design, in the manufacture entire process each completely manager, as far as possible use computer system completes the work which these duplication high, the labor big, the computation complex as well as depends on purely artificially completes with difficulty, but assists must replaces the engineers and technicians to complete the entire process, obtains the desired effec The CAD/CAM system as well as plans the hardware, the software for supports the environment, (subsystem) realizes through each function module to the product description, the computation, the analysis, optimized, the cartography, the technological process design, the simulation as well as the NC processing.But the generalized CAD/CAM integrative system also should include aspects and so on production plan, management, quality control.Since 1946 first electronic accounting machine has been born in US, people on unceasing computer technology Introduces the machine design? Manufacture domain.As early as in the 50's, for the first time develops successfully the numerical control engine bed, may realize through the different numerical control procedure to the different components processing Afterwards, Massachusetts Institute of Technology's servo laboratory succeeds with the computer manufacture numerical control paper tape, has realized the NC programming automation.In this foundation, the people proposed the following tentative plan: The APT software is feeds the path method realization computer assistance programming through the description, that, can not describe feeds the path, but is direct description components itself? From this has had the CAD initial concept.The entire 50's, the electronic accounting machine also is in the electron tube time, uses the machine language programming, the computer mainly uses in thescience computation, also only has the output function for it disposition graph equipment.CADCAM system basic compositionCAD/CAM system hardware dispositionCAD/CAM system software compositionCAD/CAM system software dispositionComputer aided manufacturing (CAM) may define for uses the computer system to design, to manage and controls a productive plan the movement, through direct or indirect planned production resources computer contact surface.If defines states, the computer aided manufacturing application has 2 big aspects:1) computer supervisory control.This is the direct application, the computer with the production process connection, uses in supervising directly and the control production process2) produces the support application.This is the indirect application, middle the productive plan, the computer uses in supporting the production operation, but is not the computer and the production process links directly.Charting productive forces increaseThe CAD/CAM system may undertake the one whole set new charting theory to be able to strengthen the productivity.Again completes next step, keeps firmly in mind the entire design to be possible to store up the system.When the planner receives one with has saved the blueprint specification similar work piece, he only must recollect, and adjusts it the work storage place, revises in the original blueprint not to conform to a new work piece request part, productivity enhances.The original work piece efficiency enhances, but this can enhance the next step working efficiency.This is a complete at times renewal database support, can facilitate the user to use Improve mapping analysisThe charting analysis is another important work, it can by certain synthesize the CAD/CAM system automatic operation.This in pipeline design, in particular an important application.The pipeline design paper very is usually complex moreover must conform to the precise industry specification.The other giftedCAD/CAM also can affect a company in other aspects the project system.It can enhance the entire physical process the efficiency, the permission present project plan and the report procedure appraisal.CAD/CAM can improve improves the quality of the product the guarantee technology.It can automatic accurate and the integrity document material, the maintenance partial data accurate and bill of materials accurate.DeficiencyCAD/CAM insufficient spot not that obvious, but they can destroy even the most perfect design, the biggest shortcoming is only can directly skips from the manual charting and the recordpreservation to CAD/CAM, the elephant installs a set of jet engine in the populace automobile.The automobile possibly can run quick somewhat, but if the foundation enhancement has not coordinated the heavy pressure, the entire automobile can disperse the frame.CAD/CAM applicationSKETCHPAD, the CAD/CAM technology has passed through very long chi.It is already applied in the middle of each widespread industry.It uses in each aspect, controls from the airplane to the weapon research, manufactures from the map to the movement medical service, from circuit analysis to building steel analysis.CAD/CAM is being applied in each kind of charting and the production, installs the schematic diagram from the movie to the large-scale long-distance monitoring direct set battleship, its application to is developing variously.Now CAD/CAM market.Now in the market has four kind of different CAD/CAM sellers.First is some subordinate companies sells comes from a big enterprise part or the branch CAD/CAM technology.The IBM CAD/CAM branch is an example.If belongs to Mc-Donnell-Douglas McAuto; Belongs to General Electric Lalma, with belongs to Schlumberger Applican, if the multi-large number CAD/CAM subordinate company the main corporation has the massive service intercourse, not only sale supervisory system moreover when one's position is lowly one's words carry no weight service office.When they control the massive accounts also with provides the service, these companies on in optimum condition, because they may extract the massive profits.But they must undertake the complex administrative chain of command, this obstructs in them makes the fast response to the market tendency, or their itself studies and outside the development department, the merge improves on again their new production line the new technical developmentCAD/CAM technology and the product development road of futureAfter many year promotions, the CAD technology already widely applied in professions and so on machinery, electron, astronautics, chemical industry, building.Played using the CAD technology enhanced the enterprise the rated capacity, the optimization design proposal, reduces technical personnel's labor intensity, reduction design cycle, beefed-up design roles and so on standardization.In recent years, our country CAD technology development and the application have obtained the considerable development, besides has carried on sinicizing and the re-development to many overseas softwares, but also was born many had the independent copyright CAD system, If high Chinese CAD, opens item CAD and so on, because these software price is cheap, conforms to our country national condition and the standard, therefore has received widespread welcome, has won the more and more big market share. But, our country CAD/CAM software no matter is from the product development level from the commercialization, the marketability degree all has not the small disparity with the developed country.Because the overseas CAD/CAM software appears early, the development and the application time is also long,therefore they develop quite maturely, now basically already has seized the international market.These overseas software company uses its technical and the fund superiority, starts vigorously to our country market march At present, the overseas some outstanding softwares, like UG, SolidWorks, Pro/Engineer, CATIA and so on, already have seized part of domestic markets.Therefore, our country CAD/CAM software prospect is unoptimistic.But, we also should see clearly own superiority, for instance understood our country market, provides the technical support to be convenient, price small advantage and so on.Not only under these premises, we importantly with the trend of the times, the track international newest tendency, observe each international standard, in international domestic forms the oneself unique superiority, must base the home, the union national condition, face the domestic economic development need,develops has oneself characteristic, conforms to CAD/CAM software which the Chinese is familiar with.。
机床——机械类外文文献翻译、中英文翻译
毕业设计(论文)外文资料翻译系部:专业:姓名:学号:外文出处:English For Electromechanical(用外文写)Engineering附件:1.外文资料翻译译文;2.外文原文。
附件1:外文资料翻译译文机床机床是用于切削金属的机器。
工业上使用的机床要数车床、钻床和铣床最为重要。
其它类型的金属切削机床在金属切削加工方面不及这三种机床应用广泛。
车床通常被称为所有类型机床的始祖。
为了进行车削,当工件旋转经过刀具时,车床用一把单刃刀具切除金属。
用车削可以加工各种圆柱型的工件,如:轴、齿轮坯、皮带轮和丝杠轴。
镗削加工可以用来扩大和精加工定位精度很高的孔。
钻削是由旋转的钻头完成的。
大多数金属的钻削由麻花钻来完成。
用来进行钻削加工的机床称为钻床。
铰孔和攻螺纹也归类为钻削过程。
铰孔是从已经钻好的孔上再切除少量的金属。
攻螺纹是在内孔上加工出螺纹,以使螺钉或螺栓旋进孔内。
铣削由旋转的、多切削刃的铣刀来完成。
铣刀有多种类型和尺寸。
有些铣刀只有两个切削刃,而有些则有多达三十或更多的切削刃。
铣刀根据使用的刀具不同能加工平面、斜面、沟槽、齿轮轮齿和其它外形轮廓。
牛头刨床和龙门刨床用单刃刀具来加工平面。
用牛头刨床进行加工时,刀具在机床上往复运动,而工件朝向刀具自动进给。
在用龙门刨床进行加工时,工件安装在工作台上,工作台往复经过刀具而切除金属。
工作台每完成一个行程刀具自动向工件进给一个小的进给量。
磨削利用磨粒来完成切削工作。
根据加工要求,磨削可分为精密磨削和非精密磨削。
精密磨削用于公差小和非常光洁的表面,非精密磨削用于在精度要求不高的地方切除多余的金属。
车床车床是用来从圆形工件表面切除金属的机床,工件安装在车床的两个顶尖之间,并绕顶尖轴线旋转。
车削工件时,车刀沿着工件的旋转轴线平行移动或与工件的旋转轴线成一斜角移动,将工件表面的金属切除。
车刀的这种位移称为进给。
车刀装夹在刀架上,刀架则固定在溜板上。
溜板是使刀具沿所需方向进行进给的机构。
- 1、下载文档前请自行甄别文档内容的完整性,平台不提供额外的编辑、内容补充、找答案等附加服务。
- 2、"仅部分预览"的文档,不可在线预览部分如存在完整性等问题,可反馈申请退款(可完整预览的文档不适用该条件!)。
- 3、如文档侵犯您的权益,请联系客服反馈,我们会尽快为您处理(人工客服工作时间:9:00-18:30)。
附录ALathe fixture design and analysisMa Feiyue(School of Mechanical Engineering, Hefei, Anhui Hefei 230022,China)Abstract: From the start the main types of lathe fixture, fixture on the flower disc and angle iron clamp lathe was introduced, and on the basis of analysis of a lathe fixture design points.Keywords: lathe fixture; design; pointsLathe for machining parts on the rotating surface, such as the outer cylinder, inner cylinder and so on. Parts in the processing, the fixture can be installed in the lathe with rotary machine with main primary uranium movement. However, in order to expand the use of lathe, the work piece can also be installed in the lathe of the pallet, tool mounted on the spindle.THE MAIN TYPES OF LATHE FIXTUREInstalled on the lathe spindle on the lathe fixtureInstalled in the fixture on the lathe spindle in addition to three-jaw chuck, four jaw chuck, faceplate, front and rear dial with heart-shaped thimble and a combination of general-purpose lathe fixture folder outside (as these fixtures have been standardized and machine tool accessories, can be purchased when needed do not have to re-design), usually need to design special lathe fixture. Common special lathe folder with the following types.Fixture took disc latheThis process is to find the generic is installed on the faceplate is difficult to ensure the accuracy of the workpiece, so the need to design special lathe fixture. The lathe fixture design process, first select the cylindrical workpieceand the end cylinder B, the semi-circular surface finishing (finishing second circularsurface when the car has been good with circular surface) ispositioned datum, limit of six degrees of freedom, in line with the principle of base overlap.The work piece fixture to ensure the accuracy of measures:The workpiece fixture to ensure the accuracy of measures:(1) tool by the workpiece machining position relative to the guarantee. (2) symmetry of size 0.02. Rely on sets of holes5.56h Φ22.5Φ0.023023+Φ0.023023+Φ180.02±and positioning theworkpiece with the precision of andlocate the position of dimensional accuracy and process specification requirements to ensure that the same parts of the four circular surface must be processed on the same pins.(3) all fixtures and clip bushing hole axis vertical concrete face A tolerance of .because the A side is the fixture with the lathe when the transition assembly base plate installed.(4) specific folder on the-hole plate with the transition to the benchmarks pin design requires processing each batch of parts to be sold in the transitional disk with a coat made of a tight match, and the local processing of the face plate to reduce the transition fixture on the set of small errors.The angle iron fixtureIf the processing technology for the and, drilling, boring, reaming process scheme. Boring is required in the face A face of finishing B ( range) and the A, B sides and the holeaxis face runout does not exceed . In addition, the processing of -hole, you should also ensure that its axis with the axis of thedegree of tolerance for the uranium ; size 5.56h Φ0.0100.00220.5++Φ0.005mm 207H Φ20Φ0.0102.5+Φ0.0110.00510++Φ12Φ10Φ0.02mm 2.5Φ0.0110.00510++Φ0.01mm Φ10Φand the location of ; and and of the axis of the axis of displacement tolerance not more than .Based on the above analysis on the part of process size, choose the -hole on the workpiece surface and M, N two planes to locate the benchmark.Installed on the lathe pallet fixtureLimited equipment in the factory, similar to the shape of the parts box, its small size, designed for easy installation without turning the main pumping in the fixture, you can drag the panel removal tool holder, fixture and workpiece mounted on the pallet. Processing, mounted on the lathe tool on the main primary uranium movement, feed the work piece for movement, so you can expand the scope of application of lathe.LATHE FIXTURE DESIGN POINTSThe design features of the positioning deviceLathe fixture positioning device in the design, in addition to considering the limited degrees of freedom, the most important thing is to make the surface of the workpiece axis coincides with the 15.50.1±80.1mm ± 2.5Φ10Φ17.5Φ0.02mm 17.5Φaxis of spindle rotation. This is described in the previous two sets of lathe fixture when special emphasis. In addition, the positioning device components in the specific folder location on the workpiece surface accuracy and dimensional accuracy of the location has a direct relationship, so the total figure on the fixture, be sure to mark the location positioning device dimensions and tolerances, and acceptance as a fixture conditions.Jig weight design requirementsProcessing in the lathe, the workpiece rotation together with the fixture will be a great centrifugal force and the centrifugal force increases sharply with increasing speed. This precision machining, processing, and the vibration would affect the surface quality of parts. Therefore, the lathe fixture between devices should pay attention to the layout of equipment necessary to balance the design weights.Dlamping device design requirementsLathe fixture in the course of their work should be the role of centrifugal force and cutting force, the size of its force and direction of the workpiece position relative to the base is changing. Therefore, a sufficient clamping device clamping force and a good self-locking.To ensure safe and reliable clamping. However, the clamping force can not be too large, and require a reasonable layout of the force, and will not undermine the accuracy of the location positioning device.Llathe fixture connection with the machine tool spindle design Lathe fixture connected with the spindle directly affects the accuracy of the rotary fixture accuracy, resulting in errors in the workpiece. Therefore, the required fixture rotation axis lathe spindle axis with high concentricity.Lathe fixture connected with the spindle structure, depending on the spindle when turning the front of the structure model is confirmed, by machine instructions or the manual check on. Lathe spindle nose are generally outside the car with cone and cone, or a journal and other structures with the flange end connections to the fixture base. Note, however, check the manual should be used with caution, because many manufacturers of machine tools, machine tools of similar size may differ. The most reliable method for determining, or to field measurements in order to avoid errors or losses. Determine the fixture and the spindle connecting structure, generally based on fixture size of the size of the radial: radialdimension less than , or small lathe fixture. Pairs of fixture requirements of the overall structureLathe fixture generally work in the state of the cantilever in order to ensure process stability, compact fixture structure should be simple, lightweight and safe, overhang length to as small as possible, the center of gravity close to the front spindle bearing. Fixture overhang length L and the ratio of outer diameter D profile can refer to the following values used:Less than the diameter D in fixture, ;Diameter D between the fixture in ,; Fixture diameter D is greater than , .To ensure security, installed in the specific folder on the components of the folder is not allowed out beyond the specific diameter, should also consider cutting the wound and coolant splash and other issues affecting safe operation.References140mm (23)D d <-150mm 1.25L D ≤150300mm :0.9L D ≤300mm 0.6L D ≤[1] Chen Guofu. Lathe fixture [J]. Mechanical workers. Cold, 2000 (12)[2] Dong Yuming. Yang Hongyu. Fixture design in the common problems [J]. Mechanical workers. Cold, 2005 (1)[3] Liu Juncheng The machine clamps the clamping force in the design process calculations [J]. tool technology, 2007 (6)附录B车床夹具设计分析(合肥学院机械工程系,安徽合肥230022)摘要:从车床夹具的主要类型着手,对花盘式车床夹具和角铁式夹具进行了介绍,并在此基础上分析了车床夹具设计要点。