多工位级进模设计
多工位级进模的设计

多工位级进模的设计多工位级进模是一种高效的集成电路设计方法,能够有效提高集成电路设计的速度和效率。
本文将介绍多工位级进模的概念、设计原则以及其在集成电路设计中的应用。
一、概念与原理多工位级进模是一种将传统的级进模拟法和多工作位技术相结合的设计方法。
它通过将一个电路分成多个工作位,并行处理每个工作位的数据,从而大大提高了设计的效率。
在传统的级进模拟法中,设计者需要按照顺序逐个设计每个电路模块,然后将它们按照级进的方式连接起来。
这种方法存在着设计时间长、设计过程复杂等问题。
而多工位级进模则采用并行处理的方式,将一个电路分成多个工作位,每个工作位独立设计,最后再将它们合并在一起。
这种方法不仅可以提高设计效率,还可以减少设计过程中的冗余。
二、多工位级进模的设计原则1. 分工明确:在设计多工位级进模时,需要明确每个工作位的任务和功能。
每个工作位应该独立处理一部分任务,并将结果传递给下一个工作位。
2. 数据共享:在多工位级进模的设计中,各个工作位之间需要进行数据共享。
设计者需要合理规划数据的传递和交换方式,确保数据在各个工作位之间流动顺畅。
3. 数据同步:在多工位级进模的设计中,各个工作位之间需要进行数据同步。
设计者需要合理安排同步信号,以确保各个工作位能够按照正确的顺序进行处理。
4. 效率优化:在设计多工位级进模时,需要考虑如何优化设计效率。
可以通过设计合理的并行处理流程、合理分配资源、合理利用并行计算等方式来提高设计效率。
三、多工位级进模在集成电路设计中的应用多工位级进模广泛应用于集成电路设计的各个领域,如数字电路设计、模拟电路设计、系数字混合电路设计等。
在数字电路设计中,多工位级进模可以帮助设计者快速设计复杂的逻辑电路。
设计者可以将逻辑电路分成多个工作位,每个工作位独立设计,最后再将它们合并在一起,大大提高了设计效率。
在模拟电路设计中,多工位级进模可以帮助设计者快速设计复杂的模拟电路。
设计者可以将模拟电路分成多个工作位,每个工作位独立设计,最后再将它们合并在一起,减少了设计过程中的冗余。
多工位级进模的排样设计

2.2.4双边载体排样
双边载体排样是在产品条料的两侧分别留出一定宽度的材 料,并在适当位置与产品两边相连接,实现对产品条料的送 进,它比单边载体排样送进更顺利,料带定位精度更高,适 合产品两端都有接口可连,特别适合送进强度较弱的薄板料。 但是,相对材料利用率较低,且通常需要采用双边导正。
图2-7所示为双边载体排样,共有16个工位,其中 (1)~(4) 工位为冲裁; (5)~(14) 工位为弯曲;(15) 工位将制件从条 料上分离;(16) 工位为将废料切断,这一步根据实际情况而 定,如果有自动收料装置时,可不设计。
边料载体虽然增大了条料两侧搭边的宽度,材料的利用率有所 降低,但是提供了冲导正工艺孔需要的载体,特别是所冲带料较 薄时,可保证送料的刚度和精度。这种载体主要多用于薄料(t小 于0.2mm),制件精度要求较高的场合。
2.2.3单边载体排样
单边载体排样是在产品条料的一侧留出一定宽度的材料,并 在适当位置与产品相连接,实现对产品条料的送进,一般适合切 边型排样。
如图2-6所示的是产品生产批量较大或为提高材料利用率, 而采用的双向交叉排样。实际上是一模出两根料带,并在两 个产品( 可以是同一产品,也可以是不同产品 )相邻的地方找 出合适的部位用一连接带连起来,俗称“手拉手”,这样大 大增加整个条料的强度,在所有冲裁和成形的工序完成后再 把牵手部位冲掉即可,这一步称为“分手”。但是,实践证 明一根条料分出的料带越多、工位越多,生产过程越不稳定, 冲压得到的产品精度也越低。该排样共有18个有效工位( 其 余为空位 ),其中 (1) 为预压;(2) (3) (4) (5) (8) (16) 工 位为冲裁;(6) (7) (9) (10) (11) (12) (13) (14) (15) (17)工位为弯曲(第16工位在这里被称为分手 );(18) 为调整 工位。
多工位级进模的设计基础知识02

多工位级进模的设计〔根底知识〕024.2 凹模多工位级进模凹模的设计与制造较凸模更为复杂和困难。
凹模的结构常用的类型有整体式、拼块式和嵌块式。
整体式凹模由于受到模具制造精度和制造方法的限制已不适用于多工位级进模。
1.嵌块式凹模图6.4.6 所示是嵌块式凹模。
嵌块式凹模的特点是:嵌块套外形做成圆形,且可选用标准的嵌块,加工出型孔。
嵌块损坏后可迅速更换备件。
嵌块固定板安装孔的加工常使用坐标镗床和坐标磨床。
当嵌块工作型孔为非圆孔,由于固定局部为圆形必须考虑防转。
图6.4.7为常用的凹模嵌块结构。
a图为整体式嵌块,b图为异形孔时,因不能磨削型孔和漏料孔而将它分成两块〔其分割方向取决于孔的形状〕,要考虑到其拼接缝要对冲裁有利和便于磨削加工,镶入固定板后用键使其定位。
这种方法也适用于异形孔的导套。
此主题相关图片如下:此主题相关图片如下:在设计排样时,不仅要考虑嵌块布置的位置还应考虑嵌块的大小,以及与凹模嵌块相对应的凸模、卸料嵌套等。
如图6.4.8所示。
2.拼块式凹模拼块式凹模的组合形式因采用的加工方法不同而分为两种结构。
当采用放电加工的拼块拼装的凹模,结构多采用并列组合式;假设将凹模型孔轮廓分割后进行成形磨削加工,然后将磨削后的拼块装在所需的垫板上,再镶入凹模框并以螺栓固定,那么此结构为成形磨削拼装组合凹模。
图6.4.9为图6.2.2所示弯曲零件采用并列组合凹模的结构示意图,图中省略了其他零部件。
拼块的型孔制造用电加工完成,加工好的拼块安装在垫板上并与下模座固定。
图6.4.10为该零件采用磨削拼装的凹模结构,拼块用螺钉,销钉固定在垫板上,镶入模框并装在凹模座上。
圆形或简单形状型孔可采用圆凹模嵌套。
当某拼块因磨损需要修正时,只需要更换该拼块就能继续使用。
磨削拼装组合的凹模,由于拼块全部经过磨削和研磨,拼块有较高的精度。
在组装时为确保相互有关联的尺寸,可对需配合面增加研磨工序,对易损件可制作备件。
关于分块原那么和拼块的设计见2.9。
多工位级进模设计实例

多工位级进模设计实例
1.6 计算冲裁各工艺力
6.总的冲裁力 7.卸料力 8.推件力 9.冲裁总工艺力
多工位级进模设计实例
1.7 压力中心的确定
由于冲裁力较小,并且采用对角导柱模架, 受力平稳,同时根据零件的排样图可以看出, 模具压力中心不会超出冲模模柄的投影面积。 故压力中心确定为本模具的凹模对称中心。
冲压工艺与模具设计
多工位级进模设计实例
1.1 零件的工艺性分析
1. 零件尺寸精度
2. 零件结构
形状
3. 确定冲压 工艺方案
多工位级进模设计实例
1.1 零件的工艺性分析
簧片
1.2 排样设计
多工位级进模设计实例
排样图
1.3 模具工作工程
多工位级进模设计实例
模具工作过程
1.4 材料利用率
多工位级进模设计实例
落料凸模
多工位级进模设计实例
1.10 模具主要部件零件图
卸料板
多工位级进模设计实例
1.10 模具主要实例
1.5 凹模轮廓尺寸
1
2
凹模计算尺寸
根据凹模轮廓 尺寸选取标准
凹模
选取模具结构 的典型组合
3
根据典型组合 选取标准模架
4
多工位级进模设计实例
1.6 计算冲裁各工艺力
1.工件外轮廓周边长度 2.孔(φ6 mm)周边长度 3.侧刃冲切长度 4.冲切一个工件的周边长度 5.一个工步内冲切工件的总长度
9、21—
10—防转销;
11—模柄; 13—卸料螺钉;
14—垫板; 15—
16—弹簧; 17—导套;
18—导柱; 20—承料板;
22—下模座
簧片落料冲孔级进模
多工位级进模设计实例

多工位级进模设计实例在计算机科学领域中,多工位级进模设计是一种用于提高处理器性能的技术。
它通过将处理器划分为多个工位,并在每个工位上同时执行不同的指令,以实现指令级并行处理。
本文将介绍几个多工位级进模设计的实例,以帮助读者更好地理解这一概念。
实例一:乘法器设计乘法运算是计算机中常见的运算之一。
在传统的乘法器设计中,需要进行多次乘法和加法操作,整个运算过程比较耗时。
而采用多工位级进模设计,可以将乘法运算拆分为多个阶段,每个阶段在一个工位上并行执行。
例如,可以将乘法器划分为部分积生成、部分积累加和最终结果生成等多个工位,在每个工位上同时执行不同的操作。
这样可以大大提高乘法器的运算速度。
实例二:浮点数加法器设计浮点数加法是计算机中常见的浮点运算之一。
在传统的浮点数加法器设计中,需要进行多次位运算和规格化等操作,整个运算过程较为复杂。
而采用多工位级进模设计,可以将浮点数加法器划分为多个阶段,每个阶段在一个工位上并行执行。
例如,可以将浮点数加法器划分为对阶段、对尾数相加和规格化等多个工位,在每个工位上同时执行不同的操作。
这样可以显著提高浮点数加法器的运算速度。
实例三:流水线设计流水线是多工位级进模设计中常用的一种技术。
它将处理器的指令执行过程划分为多个阶段,并在每个阶段上同时执行不同的指令。
例如,可以将流水线划分为取指、译码、执行、访存和写回等多个阶段,在每个阶段上并行执行不同的指令。
这样可以大大提高处理器的指令执行效率。
实例四:并行排序算法设计排序算法是计算机中常用的一种算法。
传统的排序算法通常是串行执行的,即每次只处理一个元素。
而采用多工位级进模设计,可以将排序算法划分为多个阶段,每个阶段在一个工位上并行执行。
例如,可以将排序算法划分为分组、局部排序和合并等多个工位,在每个工位上同时处理不同的元素。
这样可以显著提高排序算法的执行速度。
多工位级进模设计是一种提高处理器性能的重要技术。
通过将处理器划分为多个工位,并在每个工位上同时执行不同的指令,可以实现指令级并行处理,从而大大提高处理器的运算速度和指令执行效率。
本科毕业设计论文(多工位级进模设计)

第一章概论1.1 级进模概述一个冲压零件,如用简易模具冲制,一般来说,每项冲压工序,如冲裁〔冲孔、冲切或落料〕、弯曲、拉深、成型等,就需要一副模具。
这对于一个比较复杂的冲压零件来说,则需要几副模具才能完成。
因此这种简易模具的生产效率,相对来说仍是较低的。
对于大批料生产的定型产品,用简易模具进行生产是极不适应的。
多工位级进模是冷冲模的一种。
级进模又称跳步模,它是在一副模具内,按所加工的零件分为假设干个等距离工位,在每个工位上设置一定的冲压工序,完成冲压零件的某部分加工。
被加工材料〔一般为条料或带料〕在控制送进距离机构的控制下,经逐个工位冲制后,便得到一个完整的冲压零件〔或半成品〕。
这样,一个比较复杂的冲压零件,用一副多工位级进模即可冲制完成。
在一副多工位级进模中,可以连续完成冲裁、弯曲、拉深、成型等工序。
一般地说,无论冲压零件的形状怎样复杂,冲压工序怎样多,均可用一副多工位级进模冲制完成。
多工位级进模的结构比较复杂,模具制造精度高,这对模具设计者来说需要考虑的内容很多,尤其是级进模条料排样图的设计,模具各部分结构的考虑等都是十分重要的。
级进模,尤其是多工位级进模,配合高速冲床,实现高速自动化作业,能使冲压生产料率大幅度提高。
它在提高生产效率、降低成本、提高质量和实现冲压自动化等方面有着非常现实的意义。
多工位级进模可以对于一些形状十分复杂的冲压件进行冲裁、弯曲、拉深、成形加工。
对大批量生产的冲压零件尤其应当采用多工位级进模进行冲制。
级进模特点及其现状级进模是在压力机一次行程中完成多个工序的模具,它具有操作安全的显著特点,模具强度较高,寿命较长。
使用级进模便于冲压生产自动化,可以采用高速压力机生产。
级进模较难保证内、外形相对位置的一致性。
多工位级进模冲压工艺具有生产效率高,材料利用率高,冲压设备比较简单,对操作工人技术等级要求不高等优点,所以在工业生产中,应用广泛,并已成为不可缺少的重要加工手段之一。
多工位级进模设计

多工位级进模设计多工位级进模的特点是生产效率高,生产周期短,占用的操作人员少,非常适合大批量生产。
主要介绍了多工位级进模有别于普通冲模的工作特点和设计特点。
标签:模具;多工位级进模;冲压模具1 多工位级进模定义及特点1.1 多工位级进模定义多工位级进模是在普通级进模的基础上发展起来的一种高精度、高效率、高寿命的模具,是技术密集型模具的重要代表,是冲模发展方向之一。
这种模具除进行冲孔落料工作外,还可根据零件结构的特点和成形性质,完成压筋、冲窝、弯曲、拉深等成形工序,甚至还可以在模具中完成装配工序。
1.2 多工位级进模特点冲压时,将带料或条料由模具入口端送进后,在严格控制步距精度的条件下,按照成形工艺安排的顺序,通过各工位的连续冲压,在最后工位经冲裁或切断后,便可冲制出符合产品要求的冲压件。
为保证多工位级进模的正常工作,模具必须具有高精度的导向和准确的定距系统,配备有自动送料、自动出件、安全检测等装置。
所以多工位级进模与普通冲模相比要复杂,具有如下特点:其特点概括起来有以下几条:(1)可以完成多道冲压工序,局部分离与连续成形结合。
(2)具有高精度的导向和准确的定距系统。
(3)配备有自动送料、自动出件、安全检测等装置。
(4)模具结构复杂,镶块较多,模具制造精度要求很高,制造和装调难度大。
(5)多工位级进模主要用于冲制厚度较薄(一般不超过2mm)、产量大,形状复杂、精度要求较高的中、小型零件。
用这种模具冲制的零件,精度可达IT10级。
2 多工位级进模的排样设计2.1 排样设计应遵循的原则排样设计是在零件冲压工艺分析和必要的工艺试验的基础之上进行的。
多工位级进模的排样,除了遵守普通冲模的排样原则外,还应考虑如下几点:(1)利于成形,后工序不能影响前已成形工序。
(2)载体形式选择:多工位冲压时条料上连接工序件,并使工序件在模具上稳定送进的部分材料。
其中,载体的基本形式分为双边载体、单边载体、中间载体等几种载体。
第四节多工位级进模的排样设计一
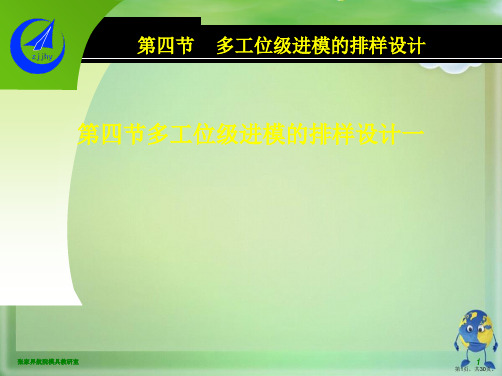
张家界航院模具教研室
13
第13页,共30页。
第四节 多工位级进模的排样设计
二、条料排样图设计时应考虑的因素 多工位级进模切废后,各段的连接方式有三种:
(1)搭接
张家界航院模具教研室
14
第14页,共30页。
第四节 多工位级进模的排样设计
二、条料排样图设计时应考虑的因素
为单排。
应用范围:薄料、制件精度要求高。 料厚t<0.2 mm, 工位数多(可
大于15个)
张家界航院模具教研室
19
第19页,共30页。
第四节 多工位级进模的排样设计
三、载体设计
5.中间载体
特点:具有单侧载体和双侧载体的优点,可节省大量的材料。中间
载体适合对称性零件的冲制,最适合对称且两外侧有弯曲的制件,这
8)冲制不同形状及尺寸的多孔工序时,尽量把大孔和小孔分开安排在不同工 位,以便修磨时能确保孔距精度。
9)为提高凹模强度及便于模具加工与制造,在冲裁形状复杂的制件时,可用
分断切除方法,即将其分解为单形孔分步进行冲裁。
张家界航院模具教研室
5
第5页,共30页。
第四节 多工位级进模的排样设计
一、条料排样图设计原则
张家界航院模具教研室
8
第8页,共30页。
第四节 多工位级进模的排样设计
二、条料排样图设计时应考虑的因素
5.模具结构
6.被加工材料
(1)材料供料状态
(2)加工材料的物理力学性能 (3)纤维方向
(4)材料利用率
张家界航院模具教研室
9
第9页,共30页。
第四节 多工位级进模的排样设计
二、条料排样图设计时应考虑的因素
- 1、下载文档前请自行甄别文档内容的完整性,平台不提供额外的编辑、内容补充、找答案等附加服务。
- 2、"仅部分预览"的文档,不可在线预览部分如存在完整性等问题,可反馈申请退款(可完整预览的文档不适用该条件!)。
- 3、如文档侵犯您的权益,请联系客服反馈,我们会尽快为您处理(人工客服工作时间:9:00-18:30)。
基本概念
双侧载体 单侧载体是在条料的一侧设计的载体,实现对工序件的运载 。
中间载体
中间载体是指载体设计在条料的中间,该方法一般适用于对称零 件,尤其是两侧有弯曲的对称零件。
空位工位
当条料送进这个工位时,不进行任何加工,随着条料的送进,再 进入下一个工位,这样的工位称为空位工位。
级进模步距
级进模步距是指条料在模具中每送进一次,所需要向前移动的 送料距离。
平接
平接是在零件的直边上先冲切去一段,然后在另一工位再冲切去余 下部分,两侧冲切刃口平行、共线但不重叠 。
切接
切接是指在零件的圆弧部位上或圆弧与圆弧相切处进行分段切除的 连接方式,即在前工位先冲切一部分圆弧段,以后工位再冲切出其 余的圆弧部分,要求先后冲切出的圆弧光滑连接 。
单侧载体 单侧载体是在条料的一侧设计的载体,实现对工序件的运载 。
1 8孔; ③—空工位; ④—冲切两端局部余料;
⑤—冲两工件之间的分断槽余料;⑥—弯曲; ⑦—冲中部长方孔;ຫໍສະໝຸດ ⑧—载体切断,零件与条料分离
冲压工艺与模具设计
冲压工艺与模具设计
基本概念
多工位级进模
多工位级进模它是在一副模具内按照所需加工零件的冲压工 艺分成若干个等距离工位,在每个工位上设置一定的冲压工 序,完成零件某一部分的冲压工作。
搭接
形孔分两次冲裁,第1工位冲切出 A、C 区,第2工位冲出B区,B 区 长度方向比被冲裁部位的实际长度略长些,长处部分即为搭接区。
调试及维修困难。
(5)材料利用率较其他模具低,对于复杂零件产生的废料较多。
2.多工位级进模的分类
1)按冲压工序性质分类
(1) 冲裁多 工位级 进模
(2) 多工序成形 多工位级
进模
2) 按冲压件的成形
方法分类
(1)封闭形孔级进模
(2)切除余料级进模
封闭形孔连续式多工位冲压
①—冲导正销孔; ②—
1.多工位级进模的主要特点
(1)在一副模具内可以连续完成冲裁、弯曲、拉深、成形等多道冲压工序, 具有较高的生产效率。
(2)备有自动送料、自动出件、安全检测等装置,因而操作安全、自动化 程度高。
(3)具有高精度的导向和定距系统,因此产品的加工精度高 。 (4)模具结构复杂,镶块较多,模具制造精度要求很高,所以模具制造、