MIM生产流程
MIM脱脂工艺流程

MIM脱脂工艺流程
《MIM脱脂工艺流程》
MIM(Metal Injection Molding)是一种将金属粉末与聚合物混合后,通过注射成型和高温烧结的工艺,制作复杂形状的金属零件的技术。
而脱脂则是MIM工艺中非常关键的一步,它决
定着零件的质量和性能。
下面我们来了解一下MIM脱脂工艺
流程。
首先,金属粉末和聚合物混合后,通过注射成型制作出所需形状的零件。
然后,这些零件需要进行脱脂处理,去除其中的聚合物,使其成为金属粉末的绿体。
脱脂工艺通常分为两个步骤:主要脱脂和终端脱脂。
主要脱脂是将绿体在高温下置于脱脂炉中,大部分聚合物会被热分解或挥发掉,留下的是粉末颗粒之间形成的孔隙结构。
然后进行终端脱脂,这是一个更为精细的处理过程,要求绿体能够在更高温度下进一步去除残留的聚合物,使得零件内部的孔隙结构更加致密。
脱脂工艺的精细程度对MIM零件的质量和性能有着决定性的
影响。
脱脂不彻底会导致零件内部存在气孔和缺陷,降低其强度和密实度;而脱脂过度则会使得零件收缩不均匀,形成裂纹。
因此,对于不同形状和材质的MIM零件,需要设计合理的脱
脂工艺流程,以确保其质量和性能。
总的来说,MIM脱脂工艺是MIM工艺中至关重要的一步,它
的质量和效果直接影响到最终制得的金属零件的质量和性能。
因此,在MIM工艺中,脱脂工艺流程的设计和控制非常重要。
MIM生产流程

MIM生产工艺流程MIM (Metal injection Molding )是金属注射成形的简称。
是将金属粉末与其粘结剂的增塑混合料注射于模型中的成形方法。
它是先将所选粉末与粘结剂进行混合,然后将混合料进行制粒再注射成形所需要的形状。
下图标明了MIM生产流程框图:MIM实物流程图机器实物图产品实物图一混料过程•喂料:将大约60%的金属粉末与40%的粘结剂混合成均质的喂料。
金属粉末喂料粘结剂注射成脱脂烧结成品出货全检后加工二注射成型注射成型:注射成型的设备和技术与注塑成型是相似的。
颗粒状的原料被送入机器加热并在高压下注入模腔。
这个环节形成(green part)冷却后脱模,只有在大约190°c的条件下使粘结剂熔化(与金属粉末充分融合),上述整个过程才能进行,模具可以设计为多腔以提高生产率。
模腔尺寸设计要考虑金属部件烧结过程中产生的收缩。
每种材料的收缩变化是精确的、已知的。
三脱脂过程•脱脂:脱脂是将成型部件中粘结剂与硝酸反应去除的过程。
绝大部分的粘结剂是在烧结前去除的,残留的部分能够支撑部件进入烧结炉四烧结过程烧结:经过脱脂的部件被放进高温、高压控制的熔炉中。
该部件在气体的保护下被缓慢加热,以去除残留的的粘合剂。
粘结剂被完全清除后,该部件就会被加热到很高的温度,颗粒之间的空隙由于颗粒的融合而消失。
该部件定向收缩到其设计尺寸并转变为一个致密的固体。
对于大多数的材料,典型的烧结密度理论上大于97%。
高烧结密度使得产品性能与锻造材料相似。
四整形整形:把变形的产品放到整形模具里用压力压到想要的效果五喷砂喷砂机喷砂后效果图喷砂:利用压缩空气带动磨料(或弹丸)喷射到工件表面,对工件表面进行微观切削或冲击,以实现对工件的除锈、除漆、除表面杂质,表面强化及各种装饰性处理五抛光抛光机抛光前后图抛光:利用抛光轮与抛光膏等精细磨料,对零件表面进行轻微切削和研磨,除去零件表面的细微不平,以达到整平表面、提高光洁度的目的.形成镜面.六拉丝拉丝机拉丝后图拉丝是用(磨粒较粗糙的)砂带或砂轮在不锈钢表面打磨,使不锈钢表面粗糙度增加,破坏其“镜面反射”特性。
MIM粉末注射制造工艺
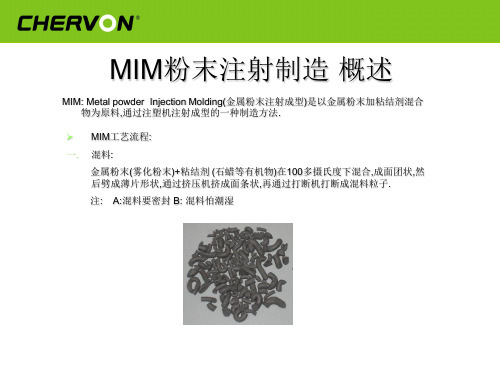
二.成形: 成形: 混料在150℃形成液体,通过注射成形机成形,成形好后将胶口及飞边去掉(该状态和面团一样, 混料在150℃形成液体,通过注射成形机成形,成形好后将胶口及飞边去掉(该状态和面团一样,刀 片可以刮) 片可以刮)
三.脱脂: 脱脂: 将成形好的工件埋在氧化铝粉里,然后放在脱脂炉里,以氢气为燃料,氨气为保护气, 将成形好的工件埋在氧化铝粉里,然后放在脱脂炉里,以氢气为燃料,氨气为保护气, 较高温脱脂. 较高温脱脂. 注:A:氧化铝粉的目的是使工件收热均匀. B:氨气的目的是防止工件氧化. :A:氧化铝粉的目的是使工件收热均匀. B:氨气的目的是防止工件氧化. 四.烧结: 烧结: 将脱脂好的工件整齐放在陶瓷托架上,脱架放在钼舟(M 将脱脂好的工件整齐放在陶瓷托架上,脱架放在钼舟(MO)上,然后放在烧结炉里,以氢气为燃料,氨 然后放在烧结炉里,以氢气为燃料, 气为保护气,1200℃ 1300℃高温烧结. 气为保护气,1200℃-1300℃高温烧结.
二.公差: 公差: MIM烧结时尺寸变化是各向同性的,即在各个方向上尺寸变化是一致的. MIM烧结时尺寸变化是各向同性的,即在各个方向上尺寸变化是一致的. 精度一般在IT11级 个别精度可达IT10级 标准公差如小表: 精度一般在IT11级,个别精度可达IT10级,标准公差如小表:
三.材料: 材料: 材料的选择主要由设计所要求的性能所决定,如强度,硬度,耐磨性等. 材料的选择主要由设计所要求的性能所决定,如强度,硬度,耐磨性等. 常用材料见下表: 常用材料见下表:
MIM粉末注射制造 MIM粉末注射制造 概述
MIM: Metal powder Injection Molding(金属粉末注射成型)是以金属粉末加粘结剂混合 Metal Molding(金属粉末注射成型) 物为原料,通过注塑机注射成型的一种制造方法. 物为原料,通过注塑机注射成型的一种制造方法. MIM工艺流程: MIM工艺流程: 一. 混料: 混料: 金属粉末(雾化粉末)+粘结剂 石蜡等有机物) 100多摄氏度下混合,成面团状, 金属粉末(雾化粉末)+粘结剂 (石蜡等有机物)在100多摄氏度下混合,成面团状,然 后劈成薄片形状,通过挤压机挤成面条状,再通过打断机打断成混料粒子. 后劈成薄片形状,通过挤压机挤成面条状,再通过打断机打断成混料粒子. 注: A:混料要密封 A:混料要密封 B: 混料怕潮湿
mim工艺流程

mim工艺流程MIM工艺流程。
MIM(Metal Injection Molding)是一种将金属粉末与聚合物混合,然后通过模具成型和烧结工艺制作金属零件的先进制造技术。
MIM工艺流程包括原料混合、注射成型、脱模、烧结和后处理等环节,下面将详细介绍MIM工艺的具体流程。
首先,原料混合是MIM工艺的第一步。
在这一阶段,金属粉末和聚合物粉末按照一定的配方比例进行混合。
金属粉末通常是由不同种类的金属粉末混合而成,以获得所需的材料性能。
而聚合物粉末则用于提供成型时所需的流动性和可成型性。
混合后的原料需要经过干燥处理,以去除其中的水分和挥发性有机物,确保成型过程中不会产生气泡和缺陷。
接下来是注射成型阶段。
原料混合后,将其装入注射成型机中进行加热熔融,并注入模具中进行成型。
注射成型是MIM工艺中最关键的一步,模具的设计和注射参数的控制直接影响着成型零件的质量和成型周期。
在注射成型过程中,需要控制好温度、压力和流速等参数,以确保成型零件的尺寸精度和表面质量。
成型完成后,进行脱模处理。
脱模是指将成型后的零件从模具中取出的过程。
由于MIM工艺成型的零件通常具有复杂的结构和薄壁结构,因此脱模过程需要特别小心,以避免零件变形或损坏。
同时,还需要对脱模后的零件进行修整和去除支撑结构,以准备后续的烧结工艺。
随后是烧结阶段。
烧结是MIM工艺中最重要的一步,通过高温处理将成型后的零件中的聚合物烧尽,使金属粉末颗粒之间结合成型,最终得到密度高、性能优良的金属零件。
烧结温度和时间是影响零件密度和性能的关键因素,需要根据不同材料和零件的要求进行精确控制。
最后是后处理阶段。
烧结后的零件需要进行表面处理、机加工、热处理等工艺,以满足不同零件的要求。
例如,一些零件需要进行抛光或镀层处理,以提高表面光洁度和耐腐蚀性能;而一些零件还需要进行热处理,以改善材料的力学性能和耐磨性能。
总的来说,MIM工艺流程包括原料混合、注射成型、脱模、烧结和后处理等多个环节,每个环节都需要精心设计和严格控制,以确保最终生产出高质量的金属零件。
【流程管理】MIM简介及基本流程

金属粉末注射成型技术(Metal Powder Injection Molding,简 称MIM)是将现代塑料注射成形技术引入粉末冶金领域而 形成的一门新型粉末冶金近净形成形技术。其基本工艺过 程是:首先将固体粉末与有机粘结剂均匀混炼,经制粒后 在加热塑化状态下(~150℃)用注射成形机注入模腔内固 化成形,然后用化学或热分解的方法将成形坯中的粘结剂 脱除,最后经烧结致密化得到最终产品。与传统工艺相比, 具有精度高、组织均匀、性能优异,生产成本低等特点, 其产品广泛应用于电子信息工程、生物医疗器械、办公设 备、汽车、机械、五金、体育器械、钟表业、兵器及航空 航天等工业领域。因此,国际上普遍认为该技术的发展将 会导致零部件成形与加工技术的一场革命,被誉为“当今 最热门的零部件成形技术”和“21世纪的成形技术”。
金属粉末注射成形MIM制品
笔记本电脑铰链转角
MIM工艺手机类产品
锁配件(锁头.锁舌.按键.复杂异形部件
MIM金属注射成型产品
工艺特点
金属粉末注射成型技术是集塑料成型工艺学、高分子化学、粉末 冶金工艺学和金属材料学等多学科透与交叉的产物,利用模具可 注射成型坯件并通过烧结快速制造高密度、高精度、三维复杂形 状的结构零件,能够快速准确地将设计思想物化为具有一定结构、 功能特性的制品,并可直接批量生产出零件,是制造技术行业一 次新的变革。该工艺技术不仅具有常规粉末冶金工艺工序少、无 切削或少切削、经济效益高等优点,而且克服了传统粉末冶金工 艺制品、材质不均匀、机械性能低、不易成型薄壁、复杂结构件 的缺点,特别适合于大批量生产小型、复杂以及具有特殊要求的 金属零件。工艺流程金属粉末+粘结剂→混炼→注射成形→脱脂 →烧结→后处理 MIM工艺所用金属粉末颗粒尺寸一般在0.5~20μm;从理论 上讲,颗粒越细,比表面积也越大,易于成型和烧结。而传统的 粉末冶金工艺则采用大于40μm的较粗的粉末。 有机胶粘剂作用是粘接金属粉末颗粒,使混合料在注射机料 筒中加热具有流变性和润滑性,也就是说带动粉末流动的载体。 因此,粘接剂的选择是整个粉末注射成型的关键。对有机粘接剂 要求: 1.用量少,用较少的粘接剂能使混合料产生较好的流变性; 2.不反应,在去除粘结剂的过程中与金属粉末不起任何化学 反应; 3.易去除,在制品内不残留。
MIM简介及基本流程

数据清洗和整理
对实验数据进行清洗和整理,去除异常值和缺失值, 确保数据质量。
03
解读主要指标
关注实验结果中的关键指标,如均值、中位数、标准 差等,了解数据分布情况。
04
对比分析
将实验结果与对照组或基线数据进行对比,判断实验 效果。
05
深入分析
针对实验结果进行深入分析,探究可能的原因和影响 因素。
结果解读示例
MIM技术通过精密注射成型和 后处理,可实现高精度制造, 提高零件的互换性和装配精度 。
MIM技术制备的金属零件具有 优异的力学性能,如高硬度、 高强度、良好的耐磨性和耐腐 蚀性等。
mim的应用领域
医疗器械
MIM技术可用于制备医疗器械中的精密零件, 如牙科种植体、手术器械等。
航空航天
MIM技术可用于制备航空航天领域中的高性能 金属零件,如发动机部件、飞机结构件等。
电子产品
MIM技术可用于制备电子产品中的小型精密结 构件,如手机零部件、连接器等。
汽车制造
MIM技术可用于制备汽车制造中的精密结构件 和功能件,如发动机零件、刹车系统部件等。
02
mim的基本流程
前期准备
确定研究问题
明确研究目的,确定研究问题,这是整个实 验过程的基础。
实验设计
根据研究问题设计实验,包括实验对象、实 验方法、实验步骤等。
总结词
mim技术为材料科学研究提供了新的 视角和手段,有助于深入理解材料的 结构和性能关系。
详细描述
mim技术可以模拟材料的微观结构和 演化过程,预测材料的性能和行为。 通过mim实验,研究人员可以观察到 材料在不同条件下的变化,从而优化 材料的制备工艺和性能。
案例二:mim在生物学研究中的应用
一种mim电容及其制造方法与流程

一种mim电容及其制造方法与流程(中英文版)Title: A MIM Capacitor and Its Manufacturing Method and Process In recent years, the demand for high-frequency and high-power devices has been increasing, which has led to a growing need for capacitors with high dielectric constant and low parasitic resistance.The metal-insulator-metal (MIM) capacitor is a type of capacitor that has shown great potential in meeting these requirements.This article introduces a MIM capacitor and its manufacturing method and process.金属-绝缘体-金属(MIM)电容器是一种具有高介电常数和低寄生电阻的电容器,近年来,随着高频和高功率器件的需求不断增加,MIM电容器展现出了巨大的潜力。
本文介绍了一种MIM电容器及其制造方法和流程。
The MIM capacitor consists of a top metal layer, a dielectric layer, and a bottom metal layer.The top and bottom metal layers serve as the electrodes, while the dielectric layer acts as the insulating material.The dielectric layer is made of a material with a high dielectric constant, such as barium titanate or strontium titanate, to increase the capacitance.MIM电容器由顶部金属层、介电层和底部金属层组成。
mim工艺流程
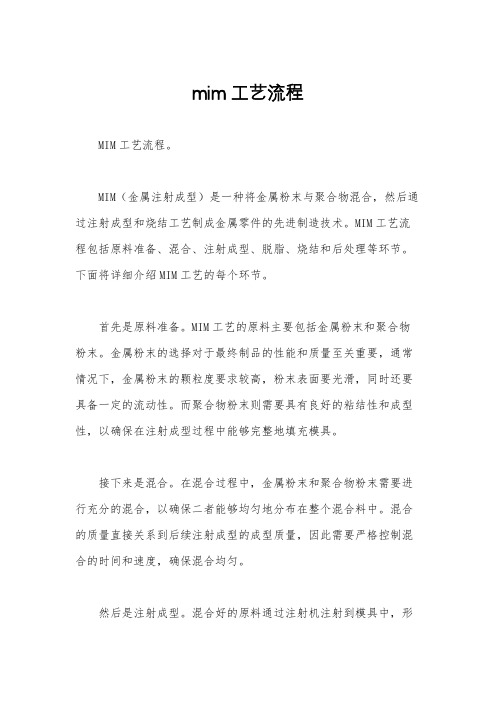
mim工艺流程MIM工艺流程。
MIM(金属注射成型)是一种将金属粉末与聚合物混合,然后通过注射成型和烧结工艺制成金属零件的先进制造技术。
MIM工艺流程包括原料准备、混合、注射成型、脱脂、烧结和后处理等环节。
下面将详细介绍MIM工艺的每个环节。
首先是原料准备。
MIM工艺的原料主要包括金属粉末和聚合物粉末。
金属粉末的选择对于最终制品的性能和质量至关重要,通常情况下,金属粉末的颗粒度要求较高,粉末表面要光滑,同时还要具备一定的流动性。
而聚合物粉末则需要具有良好的粘结性和成型性,以确保在注射成型过程中能够完整地填充模具。
接下来是混合。
在混合过程中,金属粉末和聚合物粉末需要进行充分的混合,以确保二者能够均匀地分布在整个混合料中。
混合的质量直接关系到后续注射成型的成型质量,因此需要严格控制混合的时间和速度,确保混合均匀。
然后是注射成型。
混合好的原料通过注射机注射到模具中,形成所需形状的绿体。
注射成型是整个MIM工艺中最关键的一步,它直接影响到成型品的精度和表面质量。
因此,需要严格控制注射的压力、速度和温度,以确保绿体的质量。
接着是脱脂。
脱脂是指将绿体中的聚合物去除的过程,通常采用热处理的方式进行脱脂。
脱脂的目的是将聚合物热分解,使金属粉末之间形成致密的结合,并为后续的烧结做准备。
然后是烧结。
烧结是将脱脂后的绿体在高温下进行烧结,使金属粉末之间形成致密的结合,最终得到密度高、强度高的金属零件。
烧结温度和时间的控制对于成品的性能和质量至关重要。
最后是后处理。
在烧结后,金属零件需要进行表面处理、精密加工等工艺,以满足不同客户的需求。
后处理的工艺种类繁多,可以根据具体情况进行选择。
总的来说,MIM工艺流程包括原料准备、混合、注射成型、脱脂、烧结和后处理等环节。
每个环节都需要严格控制,以确保最终产品的质量和性能。
MIM工艺具有成型精度高、制造周期短、材料利用率高等优点,适用于制造复杂形状、精密尺寸的金属零件,因此在航空航天、医疗器械、汽车等领域有着广泛的应用前景。
- 1、下载文档前请自行甄别文档内容的完整性,平台不提供额外的编辑、内容补充、找答案等附加服务。
- 2、"仅部分预览"的文档,不可在线预览部分如存在完整性等问题,可反馈申请退款(可完整预览的文档不适用该条件!)。
- 3、如文档侵犯您的权益,请联系客服反馈,我们会尽快为您处理(人工客服工作时间:9:00-18:30)。
MIM生产流程
金属注射成形(简称MIM)是将粉末冶金和塑料成形工艺相结合而发展起来的
金属零件制造新技术,在大批量制造小型复杂精密金属零件方面迅猛发展。
下图标明了MIM生产流程框图:
MIM实物流程图
机器实物图产品实物图
一混料过程
•喂料:将大约60%的金属粉末与40%的粘结剂混合成均质的喂料。
二注射成形
•注射成形:将喂料置入注射成形机进行注射成形,此过程类似注塑加
工。
零件的形状和结构在模具中成形。
三脱粘过程
•脱粘:运用物理或者化学方法脱除零件中的粘结剂,零件由金属粉末
与粘结剂的混合物变为单纯的金属零件,体积发生收缩,形状和结构
不变。
四烧结过程
•烧结:此流程是将零件致密化处理,体积进一步收缩,形状和结构不
变,此时相对密度≥95%。
2.注塑成型原理及注塑过程介绍
注(射模)塑(或称注射成型)是塑料先在注塑机的加热料筒中受热熔融,而后由柱塞或往复式螺杆将熔体推挤到闭合模具的模腔中成型的一种方法。
它不
仅可在高生产率下制得高精度,高质量的制品,而且可加工的塑料品种多和用途
广,因此注塑是塑料加工中重要成型方法之一。
A注塑机的基本功能:
注塑是通过注塑机来实现的。
注塑机的基本功能是:1。
加热塑料,使其达到熔融状态;2。
对熔体施加高压,使其射出而充满模腔。
B注塑过程/设备
热塑性塑料的注塑操作一般是由塑炼。
充模。
压实和冷却等所组成的。
所用设备是由注塑机。
注塑模具及辅助设备(如物料干燥等)组成的。
C注射装置:
注射装置在注塑机过程中主要实现塑炼。
计量。
注射和保压补缩等功能。
螺杆式注射装置用得最多,它是将螺杆塑炼和注射用柱塞统一成为一根螺杆而成的。
实质上,应称为同轴往复复杆式注射装置。
它在工作时,料斗内的塑料靠自身的重量落入加热料筒内,通过螺杆的转动,塑料沿螺槽向前移动,这时物料受到加热料筒外部加热器加热,同时内部还有剪切产生的热,温度上升在成为熔融状态。
随着加热料筒前端材料的贮存,这些材料产生的反作用力(背压)将螺杆向后推,利用限位开关限制其后退量,当后退到一定位置时,使螺杆停止转动,由此决定(计量)一次的注射量。
模内的材料冷却后,制品一经取出,就再次合上模具,进入注射工序,这时注射装置的液压缸(注射油缸)向螺杆施力,在高压下螺杆成为射料杆,将其前端的熔体从喷嘴注入模具内。
螺杆式注射装置是由螺杆,料筒,喷嘴和驱动装置等部分构成的。
注射用螺杆一般分加料,压缩,和计量三段,压缩比为2~3,长径比为16~18。
当熔体从喷嘴射出去时,由于加压熔体上的注射力怕反作用力,一部分熔体会通过螺杆的螺槽逆流到后部。
为防止这种现象,在螺杆的端部装上止逆阀。
对于硬聚氯乙烯,则采用锥形螺杆头。
料筒是装纳螺杆的部分,它是由耐热。
耐高压的钢材制的。
在料筒的外围安装数组电热圈以加热筒内的物料,用热电偶控制温度,使塑料具有适宜的温度。
喷嘴是联接料筒和模具的过渡部分,其上装有独立的加热圈,因为它是直接影响塑料熔融状的重要部分。
一般注塑多采用敞开喷嘴对于低粘度聚酉先胺。
则采用针阀式喷嘴。
驱动螺杆的转动可用电动机或液压马达,螺杆的往复运动是借助液压力实现的。
通过注射装置表征注塑机的参数有:注射量是指注塑机每次注入模内的最大量,可用注射聚苯乙烯熔体的质量表示,或用注射熔体的容积表示;注射压力是指在注射时施加于料筒截面上的压力;注射速度则指注射时螺杆的移动速度。
粉末注射成形热脱脂过程机理研究
以气雾化316L不锈钢及羰基元素混合Fe<,2>Ni粉为研究对象,采用
PW-HDPE-SA粘结剂,研究了热脱脂阶段的脱脂行为.本文将热脱脂分为三个阶段:初始阶段、中间阶段和最终阶段.其中对初始阶段及中间阶段连通孔隙的形成和打开进行了详细研究.初始阶段研究中根据对脱脂生坯内不同位置蒸汽压的分析,以及毛细力大小的理论计算,并对比生坯与脱脂样的SEM照片发现:随着脱脂的进行,试样中的小颗粒金属球随着粘结剂的流动向试样外表面流动,造成脱脂样表面小球聚集;只要脱除4%左右的粘结剂,试样中就会形成初始孔隙.粘结剂在不同的曲率半径处蒸汽压不一样,生坯表面小球之间粘结剂能较快脱出,而大球之间的粘结剂脱除较慢.中间阶段研究通过对两元粘结剂体系热脱脂过程的详细分析得出控制脱脂速率的两个动力学关键过程:扩散控制和渗透控制.并且在理论计算的基础上提出了脱脂临界厚度的概念.脱脂时,临界厚度大的生坯升温速率可以较快以提高生产率,临界厚度小的生坯升温速率必须缓慢以防止出现起泡、开裂和变形等缺陷.粉末颗粒尺寸、脱脂温度和粉末装载量对临界厚度都有影响.临界厚度与粉末颗粒尺寸成正比和脱脂温度及粉末装载量成反比.
作者: 李益民姜峰黄伯云
金属粉末注射成形(MIM)粘结剂中高分子物质的分解和排除是一个较缓慢的过程,对这一过程进行理论研究,有助于指导粘结剂的设计和脱脂过程优化。
为此,当Fe-2Ni粉末的注射成形坯经充分溶剂脱脂后,用热重法对坯块中的PMMA的热分解行为进行了理论研究和实验验证。
假设进行一级反应,根据各种升温速率的热重计算结果,得到了喂料中PMMA热分解反应速率的理论计算表达式:ln(1-α)=1.33×10^9t·exp(-1479/T);对厚度为6.37mm的注射坯充分溶剂脱酯后,验证了坯块中PMMA分解速率,发现在350℃和400℃时等温脱脂的速率与理论值较接近,但低于理论值;经过优化,对6.37mm厚的注射坯,采取5~10℃/min的升温速度升温,可以2h内完成热脱脂过程。
(共4页)
金属粉末注射成形(MIM)零件的先进热加工工艺与设备.由于MIM-Master系列设备具有连续脱粘-高温烧结及快速冷却功能,可在大规模生产时加强工艺参数的控制,改善产品质量.最后把高温烧结与快速冷却组合成一个连续过程,能实现MIM 零件烧成品的硬化.快速冷却的独特优点是在分解氨气氛中烧结316L不锈钢可提高期密度,并可以采用可靠而价廉的气氛以降低成本.
采用金属注射成形方法制备了Ti-6Al-4V合金坯体,研究了不同热脱脂气氛(真空和氮气)、脱脂速率、脱脂温度以及此温度时保温时间对钛合金脱脂坯及合金碳、氧含量的影响.实验结果表明:真空脱脂坯中碳含量稍高于氮气气氛,但氧含量较低;真空热脱脂速率增加,脱脂坯中碳含量变化很小,但氧含量明显降低;真空脱脂温度超过550℃,碳含量维持在0.1wt%,但氧含量增加;600℃下真空脱脂,保温时间超过1h,坯体中碳含量几乎无变化,但氧含量增加.脱脂坯的最大尺寸偏差为0.1mm,最小尺寸偏差为0.04mm,从而脱脂坯的尺寸精度较高。
如果系统的毛细管阻力较大(管径小或长度长),使蒸发压力降低,压缩机吸气压力降低,压缩机的排压和冷凝压力都会相应降低的。
冷凝器进风和压缩机吸气压力(蒸发压力)对冷凝压力都有直接的影响。
系统的蒸发压力同时受到毛细管的影响,如果毛细管偏长,系统的蒸发压力一定会降低,这也是对的。
如果系统的注氟量偏多,蒸发压力和冷凝压力均偏高,这也是对的。
系统的过冷度和过热度和毛细管也有着直接的关系。