铝氧率对煅烧和熟料强度影响的探讨
高铝孰料煅烧总结 文档
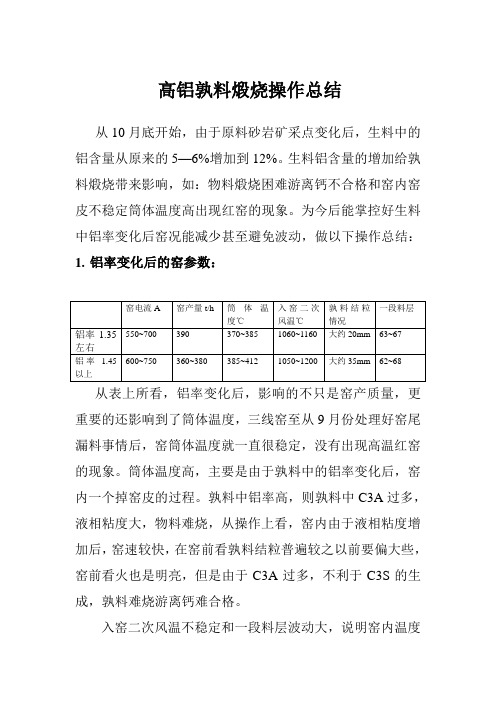
高铝孰料煅烧操作总结从10月底开始,由于原料砂岩矿采点变化后,生料中的铝含量从原来的5—6%增加到12%。
生料铝含量的增加给孰料煅烧带来影响,如:物料煅烧困难游离钙不合格和窑内窑皮不稳定筒体温度高出现红窑的现象。
为今后能掌控好生料中铝率变化后窑况能减少甚至避免波动,做以下操作总结:1.铝率变化后的窑参数:从表上所看,铝率变化后,影响的不只是窑产质量,更重要的还影响到了筒体温度,三线窑至从9月份处理好窑尾漏料事情后,窑筒体温度就一直很稳定,没有出现高温红窑的现象。
筒体温度高,主要是由于孰料中的铝率变化后,窑内一个掉窑皮的过程。
孰料中铝率高,则孰料中C3A过多,液相粘度大,物料难烧,从操作上看,窑内由于液相粘度增加后,窑速较快,在窑前看孰料结粒普遍较之以前要偏大些,窑前看火也是明亮,但是由于C3A过多,不利于C3S的生成,孰料难烧游离钙难合格。
入窑二次风温不稳定和一段料层波动大,说明窑内温度场不稳定,给操作上带来不稳定的因素。
2.铝率高后的操作方法:1.在生料铝率变化前,事先由原料磨出磨率值中得到,与质量调度人员联系,是否为原料或者原煤成分发生变化引起;2.得到铝率变化是由于原燃材料波动引起,第一时间与分厂相关领导联系告知生产情况,第一时间采取预防措施;3.在操作过程中,密切跟踪窑况变化,从各个参数中判断大窑运行情况,从窑头看火和出窑孰料判断窑内窑皮是否稳定、窑内热工制度是否正常,从而第一时间做出调整,如:增加窑头煤、增加窑内通风、减产等;4.通过观察筒体温度判断出窑内温度场的变化和窑皮的掉挂情况,第一时间得出铝率高后对窑内窑皮的影响。
如果筒体温度上升过快,则通过调整燃烧器或者增加外部冷却;5.稳定分解炉温度和入窑二次风温,两者都要兼顾,减少操作上人为的波动,给窑况带来不必要的影响;6.操作上有预见性和责任心,把实际生产情况及时汇报给分厂相关领导,并将自己的操作思想与相关人员进行交流。
3.小结:此次铝率高,事先没有做好应急预案,虽然时间短,但是也给生产带来较大的影响。
熟料铝氧率液相粘度

熟料铝氧率液相粘度
熟料铝氧率,也称为铝率或铁率,用符号表示为IM 或p,计算公式为IM=Al2O3/Fe2O3。
它反映了熟料中Al2O3与Fe2O3的含量之比,并进一步影响了熟料中C3A (铝酸三钙)和C4AF(铁铝酸四钙)的相对含量。
铝氧率还与煅烧过程中液相的性质有关,特别是液相的粘度。
C3A形成的液相粘度大,而C4AF形成的液相粘度小。
当铝氧率IM增加时,液相的粘度也会增加。
这会导致烧成温度增高,物料熔融变得困难,同时C2S和f-CaO 结合生成C3S也变得困难。
当铝氧率IM=1.63时,有利于熟料的结粒。
如果IM值偏离1.63过大,那么对熟料的结粒将产生不利影响。
例如,当IM值增加时,熟料中铝酸三钙的含量增多,导致液相粘度增大,这会使水泥的凝结速度加快。
另一方面,当铝氧率IM值过低时,虽然液相粘度会减小,有利于C3S的形成,但此时熟料中的C4AF量相对较多,窑内的烧结范围会变窄,这可能会导致窑内结成大块,不利于煅烧操作。
因此,在选择铝氧率时,需要综合考虑与KH值的适应性,以确保熟料的煅烧过程顺利进行。
通常,当提高KH值时,应降低铝氧率IM,以降低液相出现的温度和粘
度,从而有助于C3S的形成。
在熟料烧成阶段,液相量L 与铝氧率和温度都有一定的关系。
当液相量在25%~28%时,对熟料结粒最有利。
提高熟料强度的质量控制技术探讨

于设备频繁启动而造成的故障,延长 了设备使用寿命 。
参
考
文
献
[ 1 ] 费维 民. 离心式空气压缩机排 气量减 少的故 障分析 与处理 [ I ] . 台
金 动 力 ,2 0 0 2 ,9 2 ( 4 ) :1 4 — 1 7 .
[ 2 ]莫才颂,林荣雄. 离心式压缩机 组振动原 因分析及处理[ 1 ] .轴承 ,
的影 响最大 的参数 为 I M,该参 数影响熟料 2 8 d抗压强度 比较
明显 。在 调 整 过 程 中 ,要 确 保 生料 细度 稳 定 控 制 在 1 2±0 . 2范
游离钙
∞
升重
(
围内。从 2 0 1 3 年 5月开始进行调整 ,经过调整后 ,2 0 1 3 年4 #
L S F S M 咖P a ) R
g / D
窑平均强度 为 5 8 . 1 M P a ,较 2 0 1 2年 9 一l 2月的 5 5 . 9MP a 提 高
9 5 8 2 . 6 2 9 . 4 5 6 . 5
≤1 .2
1 . 1 6
0 6 8
1 2 7 4
了2 . 2 MP a ;2 0 1 3年调整 后 ( 即6 —1 2月) ,4 #窑平 均强度 为
整为 L S F: 9 6±1 . 5 、S M: 2 . 5 ±0 . 1 、I M: 1 . 6 5± 0 . 1 。本 次 调 整
铝氧率 I M与熟料 2 8 d 抗 压强度 的关系图如图 6所示。
表 5 熟料铝氧率 l M与熟料 2 8d抗压强度的关系
I M
统 计 范 围 平均
2 0 1 3 ( 4 ) :3 8 — 4 0 .
原料化学成分对熟料烧成影响

原料化学成分影响原料中除主要氧化物CaO、SiO2、Al2O3、Fe2O3外,同时夹杂的其他一些微量氧化物,它们会直接影响预分解窑内的反应及煅烧操作。
1、R2O与SO3碱和的存在增加了熟料液相粘度, 导致烧结范围缩小,易引起烟道、分解炉、预热器中结皮堵塞, 同时,过剩的硫在窑中循环也易引起预热器结皮堵塞和窑内结圈,导致熟料质量下降及系统热工制度紊乱。
微量的碱和SO3能降低最低共融温度,降低熟料烧成温度,增加液相量起助融作用,但碱含量高时会出现煅烧困难,增加f- CaO 的含量, 降低熟料质量。
如建德三狮水泥有限公司的碱主要由砂岩带入,改厂控制进厂砂岩和页岩中碱含量w (K2O+0.5Na2O)<3.0%, 控制生料中硫碱比: w(SO3)/ w (K2O+0.5Na2O)≤0.1%。
2、MgOMgO超过一定范围后会使液相提前出现并增加总的液相含量,使煅烧温度降低, 导致熟料质量下降。
如建德三狮水泥有限公司石灰石品位较高, 熟料中MgO主要来自砂岩和页岩,该厂控制进厂砂岩和页岩中w(MgO)<2.0%。
3、氯(Cl- )氯(Cl- ) 在煅烧过程中挥发, 在烧成系统内形成循环富集, 并易引起预热器结皮堵塞,导致熟料质量下降。
如建德三狮水泥有限公司在配料过程中控制生料中w (Cl- )≤0.015%。
4、TiO2粘土原料中含有少量的氧化钛,一般的熟料中氧化钛含量不超过0.3%,当熟料中含有少量的氧化钛,由于它能与各种水泥熟料矿物形成固溶体,特别是对β-C2S起稳定作用,课提高熟料的质量。
但含量过多,则因与氧化钙反应生成没有水硬性的钙钛矿等,消耗了氧化钙,减少了熟料中的阿里特含量,从而影响水泥强度。
因此,氧化钛在熟料中的含量应小于1%。
某立窑厂家,生产PO425R型PO425水泥,产品质量一直很稳定。
1993年3月份立窑煅烧突然出现结窑现象严重,熟料早强明显下降。
当时一方面进行领导跟班作业,另一方面从工艺配方、原燃材料方面查找原因。
快烧急冷是提高熟料质量的重要措施

快烧急冷是提高熟料质量的重要措施欲提高水泥的ISO强度,首先要提高熟料的强度,提高熟料的反应活性和水化速度,这除了要使熟料具有合理的化学成分和矿物组成外,还必须使熟料得到充分合理的煅烧。
文献[1]指出:“化学成分和计算矿物成分相同的水泥,其水化速度可能明显不同”;“熟料生产方法和烧成过程,如窑型、烧成温度、煅烧制度和冷却速度不同,会影响熟料的物相组成和分布、晶粒大小、晶体缺陷浓度等”;“真实的晶体总不完善,并有缺陷存在。
它们的固溶体更是这样”;“正是晶体结构的差异和位错的密度影响着它们的水化速率。
”文献[2]也指出:“煅烧热力强度和煅烧气氛、煅烧温度、升温速率、保温时间和冷却速度对熟料的晶相组成、结构和形状有很大影响。
试验结果表明:煅烧充分、煅烧温度高、升温速率快、急冷的硅酸盐水泥熟料28 d抗压强度最高。
”因此熟料的煅烧要采用快烧、急冷的方法。
1 快烧急冷的意义:(1)快烧就是在有足够高的烧成温度、能保证熟料煅烧充分的前提下,使熟料快速烧成并快速通过高温带,得到晶体细小、发育不完全、晶体缺陷浓度大,但fCaO不高的熟料。
这种熟料反应活性大,水化速度快,对水泥各龄期强度尤其是对3d抗压强度有利。
(2)已烧成的高温熟料得到急冷,可使阿利特晶体停止发育,保持晶体细小、晶格缺陷、位错密度大。
同时熟料中液相也较多地凝固成玻璃相,从而提高熟料的水化速度和强度。
(3)粗大的晶体在粉磨时要消耗更多的能量,而采用快烧急冷方法烧成的熟料,矿物晶体细小,发育不良,有较好的易磨性。
急冷使熟料中液相形成晶体的数量减少,玻璃相增加,也改善了易磨性。
(4)高温熟料在急冷过程中,形成的方镁石晶体细小,甚至部分MgO还是玻璃态,这会加快MgO的水化速度,可改善含镁较高水泥的安定性。
因此在化学成分和矿物组成相仿的情况下,煅烧充分、快烧急冷的熟料具有更高的水化活性,熟料强度甚至可提高一个标号,易磨性也大大改善。
2 熟料快烧急冷的技术条件及应采取的必要措施2.1 预烧是前提。
铝含量及其存在形式对熟料质量的影响研究

黄英姿,等:铝含量及其存在形式对熟料质量的影响研究中图分类号:TQ172.6文献标志码:B文章编号:"07-0389(2021)02-08-04[DOIJ10.13697/ki.32-1449/tu.2021.02.002铝含量及其存在形式对熟料质量的影响研究黄英姿,陈俊,向丛阳(中国葛洲坝集团水泥有限公司,湖北武汉430070)摘要:准确测定熟料中各含铝矿物相含量,并研究对应的熟料性能变化,有益于企业更好地进行水泥生产和质量监控。
本文提出化学萃取法分离与提取熟料物相,对比了该方法与Bogue法和Rietveld法的不同;研究了相同和不同工艺条件下铝含量对矿物相、力学性能、工作性的影响;并以具体的实践案例指导高铝原材料用于水泥生产,实现现有设备条件下煅烧熟料品质的提升。
关键词:铝含量;化学萃取;熟料性能Influence of aluminum contenU and its existing form on clinker qualityHuang Yingzi,Chen Jun,Xiang Congyang(Chiea Gezhogba Group Cement CO.,LtV.,Wuhan,430070,China)Abstraci:Accurately de t ermite tVe content of each aluminum-coutainina miaeral phase ie tVe clinker,ant study tVe correspoudina changes in cUnker performancc,which is beaeficiai te eaterprises in bettee ccmeaV proUectiou ank quality mouitorina.Iu this paper,tVe chemical extractiou methou is proposea te separate ant extect tVe cdnaer phase,ant tVe din'ereacc between tVis methou and tVe Bouue methou ant Rietveld methou is ccmparee;the inOpexcc of aluminum ccutexi ou the mite r at phase,mechamcui ppperties and worPaPilith unteo the same ant differ6x0process ccutitious is studieX;Specifin practicci cases euine the use of higU-alumiaa raw mate-rialt in cemeei ppUuctiou,ant reelize the improvemeai of the quadty of culcinea clintee untee the existint equipmeat coutitious.Key wordt:OuidityAluminum couteet;chemicui extractiou;clinter performancc0引言硅酸盐水泥熟料以石灰石为主要原料,同时按适当比例配以硅质、铁质、铝质校正原料,经研磨成细粉烧至部分熔融所得,是一种以硅酸钙为主要矿物成分的水硬性胶凝物质。
煅烧温度和时间对熟料质量的影响
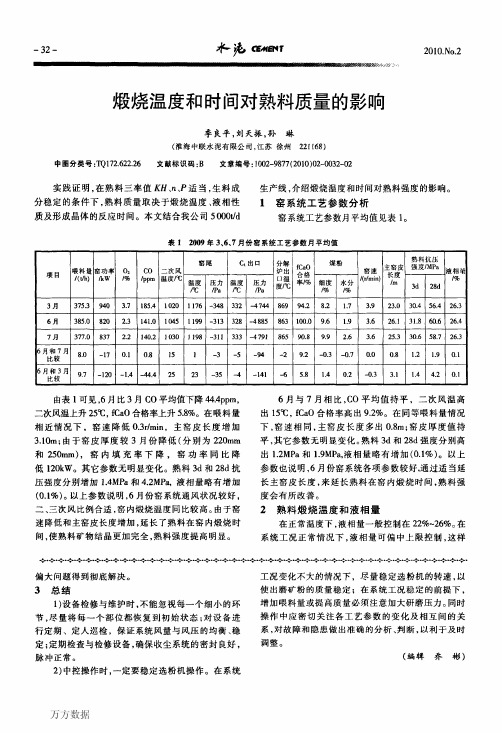
375.3 385.0 377.0
940 820 837
3.7 2.3
2.2
185.4 141.o 140.2
1020
l
176
l
—348 —313 —3II
94.2
8.2
3.9
23.O
30.4
56.4 60.6
58.7
26.3 26.4
26.3
1045 】030
199 198
328 333—4885来自—4791 —946月与7月相比,CO平均值持平,二次风温高 出15℃,fCaO合格率高出9.2%。在同等喂料量情况 下,窑速相同,主窑皮长度多出0.8m;窑皮厚度值持 平,其它参数无明显变化。熟料3d和28d强度分别高 出1.2MPa和1.9MPa,液相量略有增加(0.1%)。以上 参数也说明,6月份窑系统各项参数较好,通过适当延 长主窑皮长度,来延长熟料在窑内煅烧时间,熟料强 度会有所改善。
≤60
卜窑转速,r/min;
D广一窑衬内径,m;
|s——窑斜度,(o)。
表1中3种情况下物料在烧成带停留时间与窑 速、窑皮长度之间关系见表5。
表5物料在烧成带停留时间、窑速及窑皮长度和厚度
时间
3月 6月 7月
投料量
/(t/h) 375.3 385.0 377.0
窑速 /(dminl
3.9
窑皮长度
/m
节,尽量将每一个部位都恢复到初始状态;对设备进 行定期、定人巡检,保证系统风量与风压的均衡、稳 定;定期检查与检修设备,确保收尘系统的密封良好, 脉冲正常。 2)中控操作时,一定要稳定选粉机操作。在系统
万方数据
2010.No.2
季良平,等:煅烧温度和时间对熟料质量的影响
煅烧温度和时间对熟料质量的影响

.煅烧温度和时间对熟料质量的影响作者:刘天振纯阅读单位:淮海中联水泥有限公司发布日期:2013-08-15来源:影响熟料质量方面因素很多,但熟料在窑内煅烧是最重要环节之一。
熟料矿物形成实际上是在液相量出现以后进行的。
影响熟料质量方面因素很多,但熟料在窑内煅烧是最重要环节之一。
熟料矿物形成实际上是在液相量出现以后进行的。
液相主要有氧化铁、氧化铝、氧化钙所组成(包括其他次要组分氧化镁、氧化钾、氧化钠等),在高温液相作用下,CS逐渐溶解于液相中与f-cao化合成CS,32随着温度升高和时间延长,CS晶核不断形成,小晶体逐3渐长大,最终形成阿里特晶体。
完成熟料的烧结过程。
实践证明,CS的生成,如果熟料配料时三率值KH、3N、P 适当,生料成分稳定的条件下,主要取决于熟料煅烧温度、液相量、液相性质以及形成晶体反应时间。
本文重点介绍熟料煅烧温度和晶体反应时间对熟料强度的影响。
淮海中联水泥(287.08元/吨,0%)有限公司2#窑是由南京凯盛水泥设计院设计,2005年3月投产的5000t/d资料Word.熟料生产线,2007年8月公司利用现有1条日产5000t/d熟料生产线的窑尾、窑头废气余热,配套建设了1*9MW的纯低温余热发电系统。
该厂3、6、7月份窑系统工艺参数平均台帐(一)6月与3月份工艺参数对比。
CO平均值下降-44.12ppm。
二次风温上升+25.2℃. f-cao合格率上升+5.81%,在同等喂料量情况下窑速降低-0.3rpm,主窑皮长度增加+3.10m;由于窑皮厚度较3月份降低(见表五)。
窑内填充率下降窑功率同比降低-120A。
其它参数无明显变化。
熟料3天、7天、28天强度分别增加+1.38 Mpa、+5.59 Mpa、+4.19Mpa,液相量略有增加+0.1%。
通过参数对比分析:CO平均值下降和二次风温以及f-cao合格率上升,都能说明窑系统通风状况较好,二、三次风比例合适,窑内煅烧温度同比较高;在同等喂料量情况下由于窑速降低和主窑皮长度增加,延长了熟料在窑内煅烧时间,使熟料矿物结晶更加完全,熟料强度提高明显。
- 1、下载文档前请自行甄别文档内容的完整性,平台不提供额外的编辑、内容补充、找答案等附加服务。
- 2、"仅部分预览"的文档,不可在线预览部分如存在完整性等问题,可反馈申请退款(可完整预览的文档不适用该条件!)。
- 3、如文档侵犯您的权益,请联系客服反馈,我们会尽快为您处理(人工客服工作时间:9:00-18:30)。
从公式 ( ) () 1 、2 可知 , 氧率 / 的大 小只 受到 铝 M
Al 和 F : 两 种 氧化 物含 量 的控 制 , 不 受 C O : O, e O, 并 a
和 SO 含 量 的影 响 ;硅率 S 的高低 只 受 到 SO 、 i M i:
1 F )× e , O
一
1 6一 SI H A C M N C UN E E T
【E 矗 !【] I!
物 总量 >7 %时 , / 0 熟料 2 8天 抗压 强度 可达 到 一年 强 度 的 8 %, 以要 提 高 熟 料 强 度 , 必 须 适 当 同时 0 所 就
也就最 困难 。 际上 , 灰饱 和系数 KH 除受上述 四 实 石 种 氧化 物控 制外 , 在配 比上 还要 同时 考虑原 料 品位 、 燃 料 品质 、 生产 窑 型和 生产 方 法 、 料 细度 与 水分 、 生 均 化程 度 、 易烧性 和 f a 等 因素 的影响 。 CO
率值 ,M 为最 易 、 M 次之 、 H 因素变 数 最 多 , I S K 当然
熟 料 三 率 值 控 制 在 仁08 9 . 5 S 28 ~ .8 ~09 , . 2 0 29 ,M= . ~ 1 8 熟 料 3 . / I6 . 。 0 5 6 d强 度 也 随 之 上 升 至 2 ~ 8 a 间 ,但 上 述不 正 常 的窑 况依 然 很难 消 5 2 MP 之
将 () 2 代入 K 表达 式 , : H 得
・
KH =. aO 16 A I 3 0 35 e203 . C 5 2 0 F
- -
.
.
.
.
.
.
.
.
.
.
.
.
.
,
.
.
.
.
.
.
.
.
.
.
.
.
.
.
.
.
.
.
.
.
.
.
.
.
.
.
.
.
.
.
.
.
.
.
.
.
.
.
.
.
.
.
.
.
.
.
.
.
.
.
.
.
.
.
.
.
.
.
.
.
.
.
.
.
.
.
.
.
.
.
.
.
.
.
.
.
.
,
.
—
—
28 i .S O2
众 所周 知 , 熟料强度 主 要来源 于硅 酸盐 矿物 , 而 CS又是硅 酸 盐矿 物 强度 的主 要 提供 者 。有 数据 表
明, 当硅酸 盐矿 物含量 一 定时 , , 量 占硅酸 盐矿 C S含
2 S ( . × 胁 8M
和 熟料 强度 所起 到 的作用 具 有矛 盾 的两 重性 。 我 们知 道 , 料 中 Al , F 2 , 熟 : 和 eo 的主 要 作用 是 O
提 高熟 料 KH值和 S 值 , 以此 来 提 高 中硅 酸盐 矿 M
物 总量 及 CS的含量 。而 硅酸 盐 矿物 及 C S的形 成 , , 并 不是 毫无 条件 的, 需要碳 酸钙 在 分解 的同 时 , 它 其 分 解 产物 C O 要 与 物料 中 的 C S F A1 通 a :、e 、 : 等 O O
我们 知道 , 计算 熟料 的三率 值数 学表达 式 为:
=
() 1
上e 1 3 .2, )
煅 烧 的 实践 和物 化 分析 证 明并 非如 此 , 由于 CA 早
期强度 的绝对 值 不高 ,它 的强度 3天 之 内就大 部分
发挥 出来 , 以后 却几乎 不 再增长 甚 至倒 退 。而 CAF 4
除 ,C O 合格率 也较 低 ,强度 也很 难 再有进 一 步 的 fa
突破 。 0 7年 初 , 过几 年 的生产实 践 , 对 自身 的 20 经 针 实 际情况 , 我们 对熟 料率值 的控 制进 行 了一 定调 整 ,
依据 如下 。
2 从 工 艺 理 论 与 实 践 进 行 分 析
中 图分 类 号 : Q1 2 6 1 1 T 7 .2 .
文献标识码 : B
文 章 编 号 :0 7 6 4 2 1 ) 5 0 1 — 4 1 0 — 3 4( 0 0 0 — 0 6 0
我 公 司 20 ̄ 5 0 d熟料 生产 线 2 0 0 4年 投 入 生 产 。 由于 生产 初期 受矿 山石 灰石 采 剥 比和 煤质 的影 响 , 加 之对 生料 易烧性 及 配 料方 案 还 处于 摸 索阶 段 , 所 以熟料 3天抗 压强度 并不 高 ,很长 一段 时间徘 徊在 2  ̄2 MP 4 7 a之 间 ,且 窑 内结 圈严 重 , C 下 料 支管 结 皮较 厚 , 篦冷 机热 端经 常堆积 ‘ 雪人 ” 出球 出蛋频 , 繁 。 0 6年 下半年 , 灰石 、 质和 生料配 比的稳定 20 石 煤 性 大 为提 高 , 灰 石 C O 含量 可达 4 %以上 , 的 石 a 9 煤
() 2 SO i2
将 () 1 式代 入 S 表达 式 , : M 得
SM = Si 2 O
=
的早期 强度 只类似 于 C S 、后 期强 度只 类似 于 CS 。
所 以 , C C )对 熟 料 强 度 的 贡 献 率 比 不 上 ( A+
( S CS 。 C3 + 2 )
有 人 认 为 铝 氧 率 / 中 的 Al 和 F : 分 M 2 O3 e 成 O 较高时, 能够较 多 地吸 收 C O变 成 C 和 C A , a A 4 F 从
而避 免 过 多地析 出 f a C O造 成 熟料 强度 的 降低 。但
1 由率值 定 义进 行 逻 辑 推 理 分 析
Al 和 F 2, 种 氧化 物成 份 的控 制 , 不 受 C O : 0, e 三 o 并 a 的影 响 ; 有公 式 () 的石灰饱 和 系数 KH 同时受 只 3中 到 C O、 i A1 F 2 3 a SO 、 : 和 e 四种 氧化 物 的控 制 。换 O O 句话 说 ,铝 氧率 I 可 以决定或 影 响硅 率 S 的大 M M 小 ;而硅 率 S 和 铝氧 率 I 又可 以决定 或 影 响石 M M 灰饱和 系数 K 的大 小 。 H 反之 则不 成立 。 以控 制三 所