熟料煅烧技术资料
水泥生产工艺熟料煅烧

➢ 3.1 新型干法煅烧工艺技术
➢ 3.1.1 悬浮预热技术
➢ 悬浮预热技术是在水泥中空窑的尾部(生料喂入端) 装设悬浮预热器(也称旋风预热器),使出窑废热气体 在预热器内通过,同时使入窑的低温生料粉分散于废热 气流之中,在悬浮状态下进行热交换,使物料得到迅速 加热升温后再入窑煅烧的一项技术。
➢ 传统的回转窑煅烧水泥熟料过程完全是在窑内进行 的,即生料喂入到窑内后的干燥→预热→碳酸盐分解→ 放热反应→熟料矿物的形成→冷却这六个过程完全是在 回转窑内完成的(见下图),使得窑体长度相对较长, 热量损失较大,窑的产量不高。
新型干法(现代水泥)回转窑
悬浮或立筒预热器
干法回转窑
加热机
立波尔回转窑(已被淘汰)
普通干法回转窑(逐渐被淘汰)
湿法回转窑(逐渐在改造成为新型干法窑)
二次风入窑 出窑熟料
不同类型回转窑各带划分
➢ 3.1.1.1 悬浮预热器单元组成
➢ 悬浮风预热器单元由换热管道、预热器、衬料、出风 管(废热气体将热量传给生料后排出)、下料管和锁风阀 (重锤)组成,见下图(C1代表第一级旋风预热器,以下 类推)。悬浮预热器系统由上述多个(四级串联的称为四 级旋风预热器,五级串联的称为五级旋风预热器)单元组 合构成:
热电偶 重锤
分解后的 生料入窑
窑体(窑尾)
分解炉、第四级预热器、 回转窑窑尾之间的关系
分解炉
重锤
喷煤嘴(3个) 三次风来自冷却机
窑体(窑尾)
物气料体放温温热度度反::应~~带11370000CC
回转窑
物气料体温温度度::13烧0~01成70带104C5~0~130冷0 C却物带料温度: ~1000 C
煤粉三次风
火焰
熟料煅烧与组成(谷风研究)
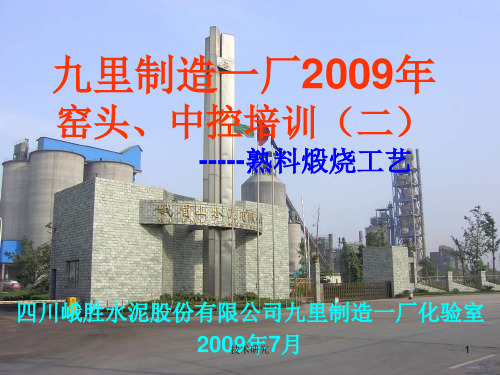
结构疏松多 不大,存在于黄粉或欠烧
孔
料中,结构疏松多孔, 遇水反应快,强度下降
因配料不当、生料过粗或 呈“死烧状 大,强度降低,3天后强
煅烧不良,尚未与S、A、F 态”,结构
CaO
62%~67%
SiO2 Al2O3 Fe2O3
15%~20% 4%~7% 2.5%~6%
技术研究
6
2. 熟料的矿物组成
硅酸盐水泥熟料是0~60μm。
(1)主要矿物
硅酸三钙(3CaO·SiO2,简写成C3S)
硅酸二钙(2CaO·SiO2,简写成C2S)
技术研究
13
◇多晶转变 纯C2S在1450℃以下有同质多晶现象。 其中:γ-C2S的密度为2.97g/cm3,β-C2S的密 度 为 3.28g/cm3 , 故 发 生 β→γ 转 变 时 , 伴 随 着体积膨胀10%,结果是熟料崩溃,生产中称 之为粉化。而γ-C2S几乎无水硬性。
技术研究
14
◇水化特性 水化反应比C3S慢得多,28d只水化20%左
技术研究
4
1.熟料的化学组成
◆主要化学成分与含量 (1)主要氧化物:CaO SiO2 Al2O3 Fe2O3 其总和通常占熟料总量的95%以上。 (2)其它氧化物:如MgO SO3 Na2O K2O TiO2 P2O5等,其总量通常占熟料的5%以下。
技术研究
5
◆主要化学成分要求
实际生产中,硅酸盐水泥中个主要 氧化物含量的波动范围一般为:
技术研究
11
◇矿物水化特性 凝结时间正常,水化较快,水化反应主要在
28d以内进行,约经一年后水化过程基本结束。 早期强度高,强度的绝对值和增进率较大。其
28d强度可达到一年强度的70%~80%。水化热较高; 抗水性较差。
第5章 硅酸盐水泥熟料的煅烧
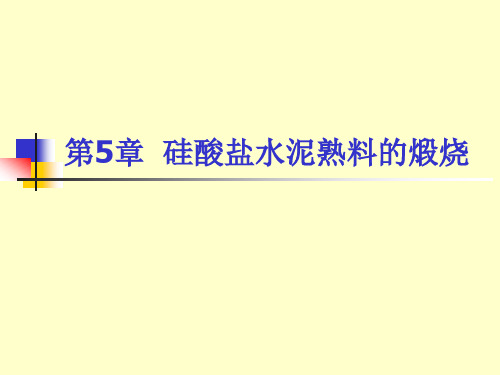
1.最低共熔温度(组分多,温度低)
存在次要氧化物,最低共熔温度一般1250 ℃ 矿化剂、氧化钒、氧化锌也有影响。
影响熟料烧结过程的因素
2.液相量(一般为20~30% )
1400℃
L 2 . 95 A 2 . 2 F M R
(液相量与煅烧温度、组分含量有关)
1450℃
L 3 . 0 A 2 . 25 F M R
五、熟 料 的 冷 却
熟料的冷却 烧成温度→常温;液相→凝固 熟料颗粒结构形成(凝固和相变) C2S的多晶转变 C3S分解 冷却目的 改善熟料质量与易磨性;降低熟料的温度,便于 运输(安全)、储存(砼开裂) 和粉磨(假凝) 回收热量,预热二次空气,降低热耗、提高热利 用率。
冷却方式
平衡冷却 淬冷 独立结晶
成
形成C2S〃CaSO4, 4CaO〃3Al2O3〃SO3 无水硫铝酸钙早强,适量有利
1050℃形成,1400 ℃分解
C 4A 3S
三、 复合矿化剂
石膏和萤石复合矿化剂(氟硅酸钙,硫硅酸钙,氟硫硅 酸钙;低温烧成,高温烧成)
重晶石和萤石(BaO可提高水泥早期和后期强度) 氧化锌及其复合矿化剂(阻止C2S转化、促进C3S形成, 提高水泥早期强度、降低水泥需水量。过多会影响水泥 凝结核强度。)
(1)温度
(2)铝率
(3)加入MgO、SO3、硫酸钾、硫酸钠,粘度降低
降低
(4)加入氧化钾、氧化钠,粘度增加。
影响熟料烧结过程的因素
4.液相的表面张力(小,润湿,利于固液反应)
(1)温度 (2)镁、碱、硫增加,表面张力下降
影响熟料烧结过程的因素
《水泥熟料煅烧》课件
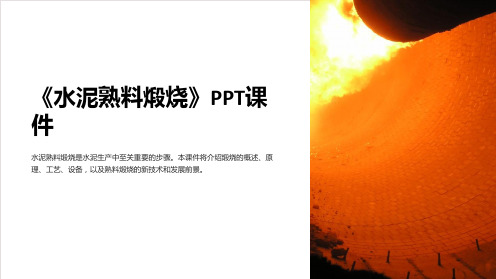
熟料煅烧的设备
熟料预热器用于预热和预分解熟料,以提高煅烧效率。 窑头、窑尾、回转窑是常用的熟料煅烧设备,它们通过高温处理熟料并使其 进行各种反应。 熟料冷却器用于冷却高温下煅烧后的熟料,以保证产品质量。
熟料煅烧的新技术
高温回收利用技术可以有效回收和利用熟料煅烧过程中产生的热能,提高能 源利用效率。
余热利用技术将熟料煅烧过程中产生的余热转化为其他形式的能源,进一步 提高能源利用效率。
窑壳隔热技术可以减少热量散失,降低能源消耗,提高熟料煅烧的效果。
熟料煅烧的发展前景
以节能减排为主导的技术创新将推动熟料煅烧工艺的发展和改进。 工艺改进和理论研究的深化将进一步提高熟料煅烧的效率和产品质量。 熟料煅烧的生态环保与可料煅烧》PPT课 件
水泥熟料煅烧是水泥生产中至关重要的步骤。本课件将介绍煅烧的概述、原 理、工艺、设备,以及熟料煅烧的新技术和发展前景。
概述
煅烧是指将水泥原料经高温处理,使之有一定的煅烧反应,形成矿物质组成 和结构上有所改变的水泥熟料。 影响熟料煅烧质量的因素包括原料成分、煅烧温度、气氛、时间及配比等。
熟料煅烧的原理
熟料煅烧的化学反应是指原料在高温下发生的各种物质转化和化学反应,如水化硅酸钙生成三钙硅酸盐等。 熟料煅烧的物理过程包括水分蒸发、碳酸盐分解、氧化反应和石灰石分解等。
熟料煅烧的工艺
熟料煅烧工艺流程包括原料预处理、煅烧、冷却和熟料磨制等。 熟料煅烧工艺参数控制包括窑温、煅烧时间、配比等的控制,以确保熟料煅 烧质量的稳定性和优良性。
水泥熟料煅烧工技能与知识(一)

水泥熟料煅烧工技能与知识(一)编码:25—005工种名称:水泥熟料煅烧工工种定义:利用窑炉将生料煅烧成水泥熟料适用范围:回转窑、机立窑等级线:初、中、高培训期:二年初级水泥熟料煅烧工知识要求:1.水泥生产工艺流程。
2.本岗位操作(工作)标准及各项规程制度。
3.本岗位各项经济技术指标及计算方法。
4.本岗位各种设备、仪表、配件、工具的名称、规格、材质、性能、结构、使用维护方法及更换周期。
5.本岗位所用润滑剂的种类、名称、性能和使用方法。
6.生料、燃烧成份、细度(粒度)变化对窑产质量和操作影响的一般知识。
7.立窑生料球的水份、粒度、孔隙率、强度和配煤量对煅烧的影响。
8.立窑煅烧方法的基本知识。
9.熟料率值、燃料质量、风煤(油)配合、喷煤管(油枪)对火焰形状、燃烧速度、温度、窑皮结构和熟料产质量影响的一般知识。
10.窑内各带的划分及物料在各带内发生的物理—化学变化的一般知识。
11.预分解窑的分解炉、预热器的作用、各测点工艺参数的一般知识。
12.稳定立窑底火的一般知识。
13.各指示仪表参数发生变化时,反映的窑内热工制度变化的一般知识。
14.钳工、电气的一般知识。
15.全面质量管理的基本知识。
16.全面质量管理的基本知识。
技能要求:1.独立操作本岗位设备,在指导下点火开窑的熄火停窑。
2.维护本岗位设备,正确处理常见一般故障。
3.担负本岗位设备小修工作。
4.根据熟料在烧成带的结粒、色泽、粒度翻动情况、外观组织、黑影远近等因素控制熟料升重、质量。
5.根据立窑出窑熟料的色泽、外观状况,判断熟料质量和窑面煅烧情况,判断烧成温度和底火位置。
6.一般机械零件图的识图。
7.正确填写岗位记录。
中级水泥熟料煅烧工知识要求:1.本工种各项经济技术指标及计算方法。
2.本工种各种设备、仪表、配件、工具的名称、规格、材质、性能、结构、使用维护方法及更换周期。
3.本工种设备各种轴承、齿轮公差与配合。
4.燃料燃烧与传热的一般知识。
5.物料在窑内各带发生物理—化学反应的理论知识,加速各带物理—化学反应的途径。
《水泥工艺学》第6章熟料煅烧技术
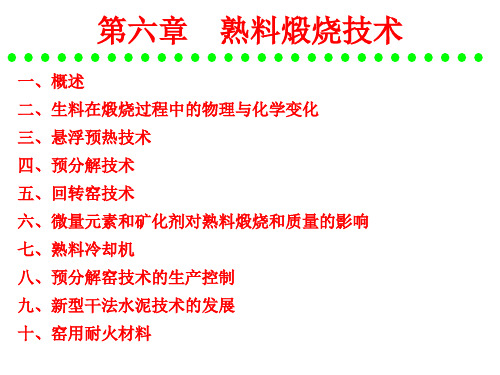
6.2.3 碳酸盐分解
1、分解反应特点 ①.可逆反应:受T、PCO2影响。 影响。 可逆反应: ②.强吸热反应:是熟料形成过程中消耗热量最多的一个 强吸热反应: 工艺过程。约占预分解窑的1/2 湿法1/3 1/2, 工艺过程。约占预分解窑的1/2,湿法1/3 44%,一般在40%左右, 40%左右 ③.烧失量大:纯CaCO3为44%,一般在40%左右,与石灰质 烧失量大: 原料的品质有关。 原料的品质有关。
6.2.2 脱水
脱水是指粘土矿物分解放出化合水 。 层间水在100℃ 左右即可排除, 而配位水则必须高达400 400~ 层间水在 100℃左右即可排除 , 而配位水则必须高达 400 ~ 100 600℃以上才能脱去。 600℃以上才能脱去。
6.2.2 脱水
粘土中的主要矿物高岭土发生脱水分解反应如下式所示: 粘土中的主要矿物高岭土发生脱水分解反应如下式所示: Al2O3·2SiO2·2H20 高岭土 Al203 + 2SiO2 无定形 无定形 + 2H2O↑ 水蒸气
6.2.1 干燥
排除生料中自由水分的工艺过程称为干燥。 排除生料中自由水分的工艺过程称为干燥。 生料中还有不超过1.O%的水。 生料中还有不超过1.O%的水。 1.O 自由水分的蒸发温度一般为27~150℃左右。 自由水分的蒸发温度一般为27~150℃左右。 27 左右 当温度升高到100~150℃时,生料自由水分全部被排除。 当温度升高到100~150℃时 生料自由水分全部被排除。 100 自由水分蒸发热耗大。每千克水蒸发潜热高达2257 kJ(在 自由水分蒸发热耗大。每千克水蒸发潜热高达2257 kJ(在 100℃下 100℃下)。
6.1 概述
悬浮预热、窑外分解技术, 悬浮预热、窑外分解技术,从根本上改变 了物料的预热、分解过程的传热状态, 了物料的预热、分解过程的传热状态,将窑内 物料堆积状态的预热和分解过程, 物料堆积状态的预热和分解过程,分别移到悬 浮预热器和分解炉内进行。 浮预热器和分解炉内进行。
第五章 熟料的煅烧
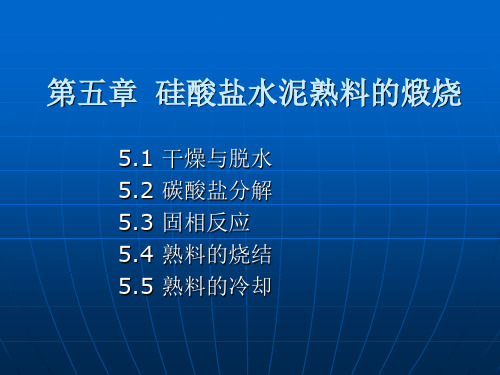
熟料煅烧
二、影响固相反应的主要因素 1. 生料的细度和均匀性
生料愈细,则其颗粒尺寸愈小,比表面积愈 大,各组分之间的接触面积愈大,同时表面的质 点自由能亦大,使反应和扩散能力增强,因此反 应速度愈快。但是,当生料磨细到一定程度后, 如继续再细磨,则对固相反应的速度增加不明显, 而磨机产量却会大大降低,粉磨电耗剧增。因此, 必须综合平衡,优化控制生料细度。生料的均匀 性好,即生料内各组分混合均匀,可以增加各组 分之间的接触,所以能加速固相反应。
由于熟料中还含有氧化镁、氧化钾、氧化钠等其 他成分,可以认为这些成分全部变成液相,因而 计算时还需要加氧化镁含量M与碱含量R,如:
1400℃ P=2.95A+2.2F+M+R 一般熟料在烧成阶段的液相量约为20%~30%, 而白水泥熟料由于Fe2O3含量低,烧成时液相量可 能只有15%左右。
三、液相粘度
其反应式如下:
C2S+CaO C3S
随着温度升高和时间的延长,液相量增加, 液相粘度减小,氧化钙、硅酸二钙不断溶解和扩 散,硅酸三钙不断形成,并使小晶体逐渐发育长 大,最终形成几十微米大小的发育良好的阿利特 晶体,完成熟料的烧结过程。
液相
硅酸盐水泥熟料
一、最低共熔温度
物料在加热过程中,两种或两种以上组分开 始出现液相的温度称为最低共熔温度。表4.1列出 一些系统的最低共熔温度(minimum eutectic temperature)。可知:组分性质与数目都影响系统的 最低共溶温度。硅酸盐水泥熟料由于含有氧化镁、 氧化钾、氧化钠、硫矸、氧化钛、氧化磷等次要 氧化物,因此其最低共熔温度约为1250~1280℃。 矿化剂和其他微量元素对降低共熔温度有一定作 用。
第五章 硅酸盐水泥熟料的煅烧
熟料烧成工艺技术

熟料烧成工艺技术熟料烧成工艺技术是指将生料在高温条件下煅烧成熟料的一项工艺过程。
熟料是制造水泥的主要原料,熟料烧成工艺技术的优劣直接影响着水泥的质量和生产成本。
熟料烧成工艺技术主要包括熟料原料的准备、煅烧过程以及冷却等环节。
首先是熟料原料的选择和准备。
熟料原料主要包括石灰石、粘土、铁矿石等,这些原料的配比和质量直接影响着熟料的成分和性能。
在熟料原料准备过程中,需要进行粉碎、混合和均化等处理,以确保原料的均匀性和可操作性。
其次是熟料的煅烧过程。
煅烧是将原料在高温条件下加热,使之发生化学反应,生成熟料的过程。
煅烧过程需要控制熟料中CaO、SiO2、Al2O3、Fe2O3等成分的含量和比例,以确保熟料的硅酸盐和铝酸盐矿物分解得充分和合理。
同时,还需要控制煅烧过程中的温度、时间和气氛等因素,以确保煅烧过程的顺利进行和熟料的品质。
最后是熟料的冷却过程。
煅烧后的熟料需要进行冷却处理,以降低温度并稳定其组织结构。
冷却过程需要适应熟料的产量和质量要求,采取不同的冷却方式,如风冷、排热气、水冷等。
冷却过程中还需要注意熟料的收缩和裂纹等问题,以避免熟料的质量问题。
熟料烧成工艺技术在水泥生产中具有重要的意义。
一方面,熟料烧成工艺技术直接影响着水泥的质量。
熟料的成分和比例决定着水泥的性能,如强度、硬化时间、抗渗透性等。
合理控制熟料烧成工艺技术可以提高水泥的质量,并满足不同材料要求的工程建设需求。
另一方面,熟料烧成工艺技术还影响着水泥的生产成本。
高效、低能耗的熟料烧成工艺技术可以降低生产成本,提高企业的经济效益。
总之,熟料烧成工艺技术是水泥工业中不可或缺的一环,它直接影响着水泥的质量和生产成本。
合理选择熟料原料、控制煅烧过程和冷却过程,将有助于提高水泥的质量和降低生产成本,进一步推动水泥产业的可持续发展。
- 1、下载文档前请自行甄别文档内容的完整性,平台不提供额外的编辑、内容补充、找答案等附加服务。
- 2、"仅部分预览"的文档,不可在线预览部分如存在完整性等问题,可反馈申请退款(可完整预览的文档不适用该条件!)。
- 3、如文档侵犯您的权益,请联系客服反馈,我们会尽快为您处理(人工客服工作时间:9:00-18:30)。
§5.2 . 熟料形成的热化学
热化学方程式 表示化学反应与热效应关 系的方程式 生料在煅烧过程中的物理化学变化 吸热反应 放热反应 表5.5
一、熟料的形成热(理论热耗)
1、定义:在一定生产条件下,用某一基准温度(一 般是0℃或20℃)的干燥物料,在没有任何物料损 失和热量损失的条件下,制成1kg同温度的熟料所需 要的热量称为熟料的形成热(熟料理论热耗)。 2、计算原理:理论热耗=吸收的总热量-放出的总 热量,一般为1630~1800kJ/kg-ck。(表5.6) 3、影响因素:熟料的形成热是熟料形成在理论上消 耗的热,它仅与原、燃料的品种、性质及熟料的化 学成分与矿物组成、生产条件有关。
1100~1200大量形成C3A
C4AF
C2S含量达最大值
三
固 相 反 应
反应特点:
多级反应 放热反应
三
固 相 反 应
(二)影响固相反应的主要因素 1、生料细度及其均匀程度;(比表面积、充分接触) 2、原料物理性质(结晶,慢,磨细); 3、温度对固相反应的影响; 4、矿化剂。
四、熟 料 烧 结
反应温度:
MgCO3 始于402~408℃最高700 ℃ CaCO3 600 ℃开始,812~928 ℃快速分解
(一)碳酸钙分解反应的特点 (一)碳酸钙分解反应的特点
反应特点:
可逆反应(温度, CO2分压 ) 强吸热反应(分解所需热量:湿法1/3,干法1/2) 烧失量大(CO2) 分解温度与 CO2分压 和矿物结晶程度有关 (图5.1) ( CO2分压 大,分解温度高;伴生矿物和杂质降低分解 温度;结晶,分解温度高)
(温度、组成、结构)图5.7
愈快 ) (粒径,粘度)表5.4,图5.8
5.C2S、CaO溶于液相的速率(速率愈大,C3S的成核与发育
五、熟 料 的 冷 却
熟料的冷却:
烧成温度 常温 熔体晶化 凝固 熟料颗粒结构形成(凝固和相变) C2S的多晶转变 C3S分解
冷却目的:
改善熟料质量与易磨性; 降低熟料的温度,便于运输(安全)、储存(砼开裂) 和粉磨(假凝) 回收热量,预热二次空气,降低热耗、提高热利用率。
熟 料 烧 结
四、熟 料 烧 结
条件:
温度:
1300~1450~1300℃
液相量:
20%~30%
时间:
10~20min
(二)影响熟料烧结过程的因素
1.最低共熔温度(组分多,温度低,表5.2) 2.液相量(一般为20~30%; )
(液相量与煅烧温度、组分含量有关)
3.液相粘度(小,扩散快) (AL,Fe有关 图5.5,温度图5.4,组分,图5.6) 4.液相的表面张力(小,润湿,利于固液反应)
理论热耗 热效率= 100% 实际热耗
(二)、影响熟料热耗的因素
1、生产方法与窑型;(干、湿,表5.7) 2、废气余热的利用; 3、生料组成(矿渣代替部分石灰石、石灰)、细 度及生料易烧性; 4、燃料的燃烧情况;(不完全燃烧) 5、窑体的散热损失(保温); 6、矿体剂及微量元素的作用。
反应生成SiF4和CaF2的在高温,蒸汽作用下分解生成活性 的SiO2,CaO。
二、氟化钙的矿化作用
2 降低液相出现的温度和粘度,促进C3S形成
高温,加入氟化钙,1%~3%,烧成温度下降50~100℃
~ 950 4CaO 2SiO2 CaF2 850 2C2 S CaF2 1040 2C2 S CaF2 C2 S CaF2 1130 3( C2 S ) 3CaO CaF2 3C3 S CaF2 1175 3C3 S CaF2 C3 S F (含氟固溶体 )+液相
磷石膏-萤石
作用:加速分解反应;加速固相反应;降低液相出现的温度;
加速C3S的形成 使用矿化剂易引起的问题:凝结时间不正常,快凝或慢凝。
二、氟化钙的矿化作用
(一)作用机理 1.加速CaCO3分解,促进固相反应(高温,蒸汽)
CaF2 H 2O CaO 2 HF 4 HF SiO2 SiF4 2 H 2O 2 HF CaCO3 CaF2 H 2O CO2
(二)碳酸钙分解过程
图5.2 1、气流向颗粒表面传热(物理过程) 2、热量由表面以传导方式向分解面传递; (物理过程) 3、碳酸钙在一定温度下,继续分解、吸收热量并放出 CO2; (化学过程) 4、放出的CO2从分解面通过CaO层,向四周进行内部扩 散; (物理过程) 5、扩散到颗粒边缘的CO2,通过边界层向介质扩散。 (物理过程)
二、熟料热耗(实际热耗)
定义:每煅烧1kg熟料窑内实际消耗的热量称为熟料 实际热耗,简称熟料热耗,也叫熟料单位热耗。
理论热耗:1630--1800 KJ/kg ; 实际热耗:3400--7500KJ/kg
热损失 热耗>熟料形成热, 降低热耗,降低各种热损失(废气、散热等)。 碳酸钙分解吸热量最大 熟料冷却放热量最大
熟料烧结过程:
当物料温度升高到最低共熔温度后,C3A、 C4AF、MgO、R2O等熔融成液相。C2S、CaO逐 步溶解于液相中, C2S吸收CaO形成C3S。 反应式: C2S+ CaO→ C3S 随着温度的升高和时间延长,液相量增加, 液相粘度降低, C2S、CaO不断溶解、扩散, C3S 晶核不断形成,并逐渐发育、长大,形成几十微 米大小、发育良好的阿利特晶体。晶体不断重排、 收缩、密实化,物料逐渐由疏松状态转变为色泽 灰黑、结构致密的熟料。 C3S 的 形 成
(二)使用矿化剂时注意事项
1.根据生料的易烧性决定是否采用(结晶SiO2 多,熔
剂矿物多)
2.用量适当,一般小于1% 3.掺加量要均匀 4.掺有萤石的熟料应急冷(1250℃时萤石促进C3S分解,
C2S 晶型转变)
三 硫酸盐类矿化剂(石膏)
氧化气氛 CaO SO3 还原气氛 CaS 2C2S·CaO (硫硅石) 4CaO·Al2O3·SO3 (无水硫铝酸钙)早强,适量有利
§5.3 矿化剂、晶种对熟料煅烧 和质量的影响
定义:在煅烧过程中,能加速熟料矿物的形成,本身不参加
反应或只参加中间反应的物质。
一、 矿化剂
类型:
矿化剂(1种)
含氟化合物:如:CaF2(萤石) 硫化物:如:石膏 氯化物:CaCl2 其他:如:铜矿渣、磷矿渣
复合矿化剂(2种)石膏—萤石 重晶石—萤石
晶种掺加量及生产工艺的调整
1.晶种及其掺加量(C3S,2~3.5%) 2.晶种加入工艺(单独计量配料) 3.率值及熟料热耗的调整中(高KH,高P, 减煤)
六、使用矿化剂、晶种时的注意事项
使用矿化剂、晶种有积极的一面,也有消极的一面, 如增加成本,有副作用等,使用时应注意: 1、根据实际情况考虑是否采用; 2、选择合适的品种; 3、掺量要合适,计量要精确; 4、掺入要均匀; 5、相应调整配料方案及操作措施; 6、矿化剂、晶种可以同时使用。
§5.1 生料在煅烧过程中 的物理化学变化
干燥(自由水蒸发) 粘土质原料脱水 碳酸盐分解 固相反应 熟料烧结 熟料冷却
吸热
吸热
强吸热
放热
微吸热 放热
一、干燥与脱水 一、干燥与脱水
(一)干燥 自由水的蒸发。 含水量与生产方法和窑型有关(含水量增加热耗增加) (二)脱水 粘土质原料脱去化合水(结构水和层间吸附水) 高岭土(Al2O3· 2SiO2· 2H2O)
第五章 熟料煅烧技术
§5-1 生料在煅烧过程中的物理化学变化
§5-2 熟料形成的热化学
§5-3 矿化剂、晶种对熟料煅烧和质量影响
§5-4 挥发性组分及其他微量元素的作用
§5-5 水泥熟料的煅烧方法及设备
§5-6 水泥熟料煅烧技术的发展 §5-7 熟料煅烧工艺技术的改造
煅
烧
生料在水泥窑内经过连续加热,高温煅烧至部分熔 融,经过一系列的物理化学反应,得以硅酸钙为主 要成分的硅酸盐水泥熟料的工艺过程叫硅酸盐水泥 熟料的煅烧,简称煅烧。
三
固 相 反 应
(一)反应过程 CaO与SiO2、Al2O3、Fe2O3进行固相反应生成 (C3S)、(C2S)、(C3A)、(C4AF)。
800℃
CaO+ Al2O3
CaO+ Fe2O3 2 CaO+ SiO2
→
→ →
CaO· Al2O3 (CA)
CaO· Fe2O3 (CF) 2 CaO·SiO2 (C2S) 2CaO· Fe2O3(C2F) 12 CaO· 7Al2O3(C12A7) 2 CaO·Al2O3 ·SiO2
冷却方式:
冷却速度慢 (平衡冷却)(4~5 ℃/min) 冷却速度快 急冷(淬冷)(18~20 ℃/min)
快冷对改善熟料质量的作用:
防止或减少C3S的分解; 避免β-C2S转变成γ -C2S ; 改善了水泥安定性;(MgO玻璃体易水化) 使熟料C3A晶体减少,提高水泥抗硫酸盐性能; 改善熟料易磨性; 可克服水泥瞬凝或快凝。
800~900℃
CaO· Fe2O3+ CaO 7 CaO· Al2O3+5 CaO 900~1100℃ 2 CaO+ SiO2 + Al2O3