煅烧温度和时间对熟料质量的影响
石灰回转窑煅烧参数
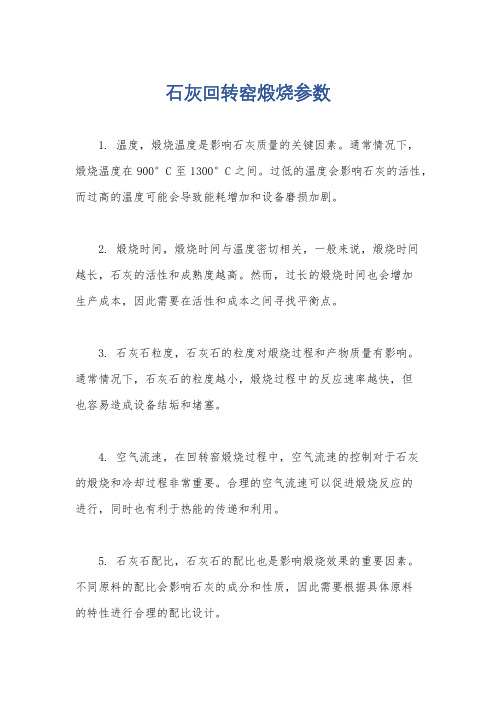
石灰回转窑煅烧参数
1. 温度,煅烧温度是影响石灰质量的关键因素。
通常情况下,
煅烧温度在900°C至1300°C之间。
过低的温度会影响石灰的活性,而过高的温度可能会导致能耗增加和设备磨损加剧。
2. 煅烧时间,煅烧时间与温度密切相关,一般来说,煅烧时间
越长,石灰的活性和成熟度越高。
然而,过长的煅烧时间也会增加
生产成本,因此需要在活性和成本之间寻找平衡点。
3. 石灰石粒度,石灰石的粒度对煅烧过程和产物质量有影响。
通常情况下,石灰石的粒度越小,煅烧过程中的反应速率越快,但
也容易造成设备结垢和堵塞。
4. 空气流速,在回转窑煅烧过程中,空气流速的控制对于石灰
的煅烧和冷却过程非常重要。
合理的空气流速可以促进煅烧反应的
进行,同时也有利于热能的传递和利用。
5. 石灰石配比,石灰石的配比也是影响煅烧效果的重要因素。
不同原料的配比会影响石灰的成分和性质,因此需要根据具体原料
的特性进行合理的配比设计。
除了上述参数外,还有其他一些影响石灰回转窑煅烧的因素,如燃料选择、窑速控制、窑体结构等。
综合考虑这些参数,可以优化石灰回转窑煅烧的生产工艺,提高石灰的质量和产量,降低能耗和生产成本。
熟料矿物组成
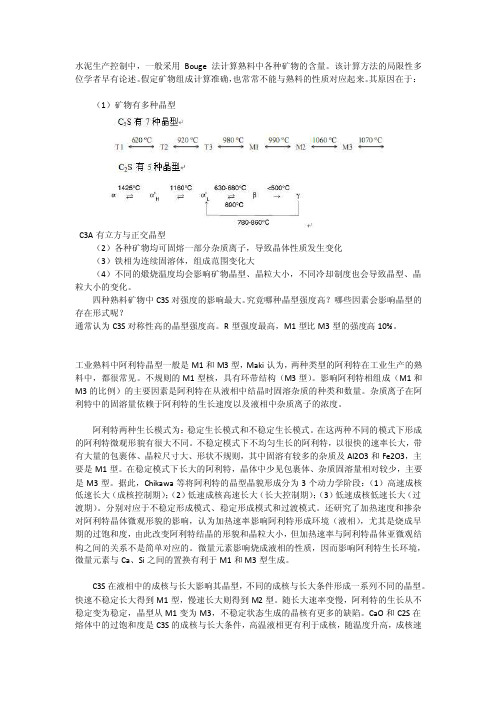
水泥生产控制中,一般采用Bouge法计算熟料中各种矿物的含量。
该计算方法的局限性多位学者早有论述。
假定矿物组成计算准确,也常常不能与熟料的性质对应起来。
其原因在于:(1)矿物有多种晶型C3A有立方与正交晶型(2)各种矿物均可固熔一部分杂质离子,导致晶体性质发生变化(3)铁相为连续固溶体,组成范围变化大(4)不同的煅烧温度均会影响矿物晶型、晶粒大小,不同冷却制度也会导致晶型、晶粒大小的变化。
四种熟料矿物中C3S对强度的影响最大。
究竟哪种晶型强度高?哪些因素会影响晶型的存在形式呢?通常认为C3S对称性高的晶型强度高。
R型强度最高,M1型比M3型的强度高10%。
工业熟料中阿利特晶型一般是M1和M3型,Maki认为,两种类型的阿利特在工业生产的熟料中,都很常见。
不规则的M1型核,具有环带结构(M3型)。
影响阿利特相组成(M1和M3的比例)的主要因素是阿利特在从液相中结晶时固溶杂质的种类和数量。
杂质离子在阿利特中的固溶量依赖于阿利特的生长速度以及液相中杂质离子的浓度。
阿利特两种生长模式为:稳定生长模式和不稳定生长模式。
在这两种不同的模式下形成的阿利特微观形貌有很大不同。
不稳定模式下不均匀生长的阿利特,以很快的速率长大,带有大量的包裹体、晶粒尺寸大、形状不规则,其中固溶有较多的杂质及Al2O3和Fe2O3,主要是M1型。
在稳定模式下长大的阿利特,晶体中少见包裹体、杂质固溶量相对较少,主要是M3型。
据此,Chikawa等将阿利特的晶型晶貌形成分为3个动力学阶段:(1)高速成核低速长大(成核控制期);(2)低速成核高速长大(长大控制期);(3)低速成核低速长大(过渡期)。
分别对应于不稳定形成模式、稳定形成模式和过渡模式。
还研究了加热速度和掺杂对阿利特晶体微观形貌的影响,认为加热速率影响阿利特形成环境(液相),尤其是烧成早期的过饱和度,由此改变阿利特结晶的形貌和晶粒大小,但加热速率与阿利特晶体亚微观结构之间的关系不是简单对应的。
煅烧温度和时间对熟料质量的影响
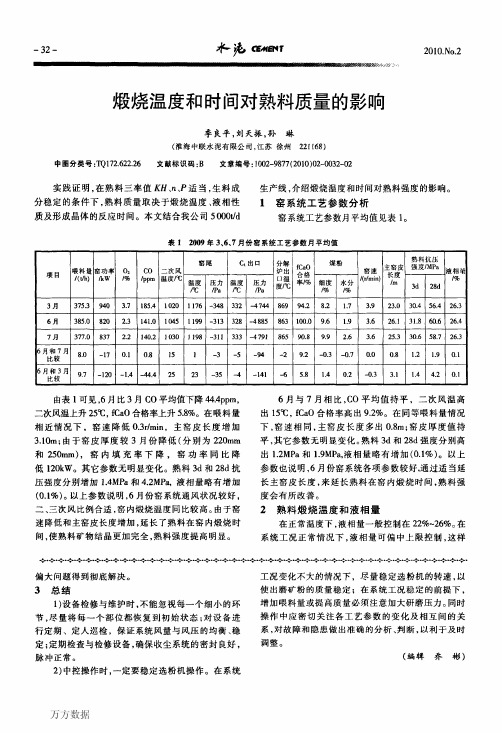
375.3 385.0 377.0
940 820 837
3.7 2.3
2.2
185.4 141.o 140.2
1020
l
176
l
—348 —313 —3II
94.2
8.2
3.9
23.O
30.4
56.4 60.6
58.7
26.3 26.4
26.3
1045 】030
199 198
328 333—4885来自—4791 —946月与7月相比,CO平均值持平,二次风温高 出15℃,fCaO合格率高出9.2%。在同等喂料量情况 下,窑速相同,主窑皮长度多出0.8m;窑皮厚度值持 平,其它参数无明显变化。熟料3d和28d强度分别高 出1.2MPa和1.9MPa,液相量略有增加(0.1%)。以上 参数也说明,6月份窑系统各项参数较好,通过适当延 长主窑皮长度,来延长熟料在窑内煅烧时间,熟料强 度会有所改善。
≤60
卜窑转速,r/min;
D广一窑衬内径,m;
|s——窑斜度,(o)。
表1中3种情况下物料在烧成带停留时间与窑 速、窑皮长度之间关系见表5。
表5物料在烧成带停留时间、窑速及窑皮长度和厚度
时间
3月 6月 7月
投料量
/(t/h) 375.3 385.0 377.0
窑速 /(dminl
3.9
窑皮长度
/m
节,尽量将每一个部位都恢复到初始状态;对设备进 行定期、定人巡检,保证系统风量与风压的均衡、稳 定;定期检查与检修设备,确保收尘系统的密封良好, 脉冲正常。 2)中控操作时,一定要稳定选粉机操作。在系统
万方数据
2010.No.2
季良平,等:煅烧温度和时间对熟料质量的影响
153、煅烧温度对硫铝酸盐水泥熟料矿物组成及性能有何影响

煅烧温度对硫铝酸盐水泥熟料矿物组成及性能有何影响(1)烧成温度对熟料矿物组成的影响实验室煅烧试验结果表明,在1200~1400℃温度范围内都可以烧成以SAC34和C2S为主的硫铝酸盐水泥熟料。
但随着烧成温度的不同,熟料的矿物组成会有如下变化: 当烧成温度在1200℃时,除SAC34和C2S外,还有C2AS、2C2S·CaSO4及CaSO4存在,后三种矿物在1250℃还存在,说明在此温度下熟料的有用矿物还没有完全形成。
当烧成温度上升至1300℃时,2C2S·CaSO4和C2AS基本消失,温度在1300~1350℃范围内,熟料中主要矿物为SAC34和C2S,烧成温度若再升高,即当温度达1400℃时,SAC34部分分解,熟料中SAC34反而减少,出现C2AS和C12A7矿物,还有微量f-CaO存在。
对不同烧成温度下形成熟料中SO3和SAC34的测定结果表明,随着烧成温度的提高,熟料中SO3不断减少,在1200℃时,熟料中SO3为11.27%,此时CaSO4除生成有用矿物SAC34外,还与C2S反应生成复盐2C2S·CaSO4,即2C2S+CaSO4→2C2S·CaSO4。
当烧成温度在1400℃时,原已形成的SAC34部分分解,SO3则挥发逸出,熟料中SO3仅剩6.59%,熟料的SA/>3.82,SO3已不足与CaO和Al2O3完全形成C4A3S,故有其他矿物生成。
熟料中SAC34含量的变化开始时随烧成温度的升高而增多,在1300~1350℃时,SAC34的生成量最大,但烧成温度到1400℃后,熟料中SAC34明显减少。
对工厂熟料物相检定结果显示,煅烧温度较低的低烧熟料中同样含有2C2S·CaSO4和C2AS等矿物,这种熟料在窑内约在1200℃左右煅烧而成。
在1300~1350℃范围内烧成的正常熟料中主要含有C4A3S和C2S矿物。
而熔块料则在过烧情况下形成,估计烧成温度≥1400℃,发现有C2AS和C12A7及微量f-CaO存在。
浅谈影响熟料质量的因素

■生产技术Technology浅谈影响熟料质量的因素王丽媛(汪清北方水泥有限公司,吉林延边朝鲜族自治州133203 )摘要:在新型干法水泥熟料生产中,影响水泥熟料质量的因素很多,文中介绍了影响水泥熟料质量的主 要几大因素,在生产中要严格控制,实践表明,除要控制原材料和燃料外,配料要合理,中控操作中要加强 风、煤、料的合理匹配及优化,才能保证生产出优质、高产、低耗、环保型熟料。
关键词:水泥;熟料;质量;影响中图分类号:T0172.62 文献标识码:B文章编号:1671—8321 (2019) 09—0098—020引言新型水泥熟料生产中,质量就是生命,随着水泥市 场的竞争日益激烈和残酷,企业要发展和壮大,必须占领 市场,这样才能生存下去,这就要求我们要树立“质量第 一”的思想和观念,抓好生产的各个环节控制和各部门 的沟通及协调工作,努力降低生产成本,提高熟料质量。
水泥的质量主要决定于熟料的质量,要获得优质的 熟料,根据预分解窑生产的工艺特点,生产实践表明,除 要控制原材料和燃料外,配料要合理,中控操作中要加强 风、煤、料的合理匹配及优化,只有这样才能生产出优质 的熟料。
1熟料质量的控制指标1.1游离氧化钙游离氧化钙(f-CaO)的含量和熟料立升重、强度是预分解窑熟料煅烧过程中检验熟料质量的重要指标。
游 离氧化钙含量过高影响到水泥的安定性和强度,严重时 引起安定性不良,使水泥制品变形和开裂。
1.2熟料立升重熟料立升重的测量是检验熟料烧结过程中结粒的致 密程度,确保熟料的强度,反映熟料的矿物组成,指导窑 系统操作和配料。
因此,熟料煅烧过程中质量控制的目的 是结合工艺生产条件及各项生产经济指标,通过对窑系 统的正常操作控制游离氧化钙和熟料立升重在适当的范 国内,一般预分解窑f-C a O可以控制在丨.5%以下,熟料立 升重&丨250k g/L,但根据不同窑型的生产状况,不同水泥 企业对f-C a O含量、熟料立升重控制范围不尽相同。
浅谈如何提高预分解窑熟料的质量

M O主要来 自砂岩和页岩 , g 我们控制进厂砂 岩和页
岩中 wM O< . ( g )2 %。 0 () O。 O 会使窑内熟料液相量增加 , 3 S S 煅烧温 度降低 ;另过剩的硫在窑中循环容易引起预热器结 皮堵塞和窑内结圈 .导致熟料质量下降及系统热工
质石英含量 ( 主要通过现场 目测 )并对原材料进行 , 合理有效的均化。 () g 。少量 的 M O存在能使生料易烧性和 2 MO g 熟料的色泽得到改善 ,超过一定范围后会使液相提 前出现并增加总的液相含量 , 使煅烧温度降低 , 导致 熟料质量下降。我公 司石灰石 品位较高 ,熟料 中
煅烧温 wf C O) (- a
度- / ℃
l350 140 0 150 0
3 抗 压强度 d
2 5 7. 2 6 9. 3 2 4. O 7. 6 2 4 4.
2 d抗压强度 8
54. 8 57. 2 64. 7 0 4. 4 1 0 8此 , 须对原 燃材 料加 强均 化措 施 。 必
质量下降。我们在 配料过程 中控制生料 中 (l c- )
≤ 0. 5 。 01 %
1 . 1原燃材料中微量组分对质量的影响及控制 原燃材料 中微量组分[ 主要包括 : 晶质 一 石英 、 M O S , ( N 2)氯 等] g 、O 、 K0,a 、 碱 0 对预分解 窑的熟料
注 意 这 些 组
分的影响。 ( ) 晶 1
质 一 石英 。
我 公 司 由 石
工薮磊根 据 X 荧光分析仪 岗位记录统计 , 中生料 的硫碱 比为 09 。 一 其 . 0
灰石和砂岩原料带人的晶质 O 石英结构致密 , 以 t 一 难 磨细 ,在煅烧 中不易与氧化钙化合 ,易导致熟料 fC O增加和熟料后期强度下降 。我们所采取的主 -a
中热水泥熟料率值控制-概述说明以及解释
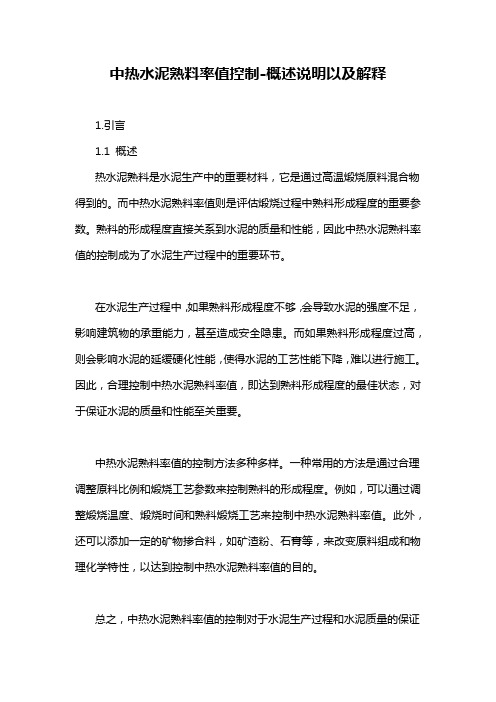
中热水泥熟料率值控制-概述说明以及解释1.引言1.1 概述热水泥熟料是水泥生产中的重要材料,它是通过高温煅烧原料混合物得到的。
而中热水泥熟料率值则是评估煅烧过程中熟料形成程度的重要参数。
熟料的形成程度直接关系到水泥的质量和性能,因此中热水泥熟料率值的控制成为了水泥生产过程中的重要环节。
在水泥生产过程中,如果熟料形成程度不够,会导致水泥的强度不足,影响建筑物的承重能力,甚至造成安全隐患。
而如果熟料形成程度过高,则会影响水泥的延缓硬化性能,使得水泥的工艺性能下降,难以进行施工。
因此,合理控制中热水泥熟料率值,即达到熟料形成程度的最佳状态,对于保证水泥的质量和性能至关重要。
中热水泥熟料率值的控制方法多种多样。
一种常用的方法是通过合理调整原料比例和煅烧工艺参数来控制熟料的形成程度。
例如,可以通过调整煅烧温度、煅烧时间和熟料煅烧工艺来控制中热水泥熟料率值。
此外,还可以添加一定的矿物掺合料,如矿渣粉、石膏等,来改变原料组成和物理化学特性,以达到控制中热水泥熟料率值的目的。
总之,中热水泥熟料率值的控制对于水泥生产过程和水泥质量的保证至关重要。
通过合理调整原料比例和煅烧工艺参数,以及添加适量的矿物掺合料,我们能够有效控制中热水泥熟料率值,提高水泥的质量和性能。
因此,在水泥生产过程中,我们应该重视中热水泥熟料率值的控制,并不断探索更加精细化的控制方法,以满足不同建筑物工程对水泥的需求。
1.2文章结构【1.2 文章结构】本文主要围绕中热水泥熟料率值的控制展开,以下为文章的基本结构:第一部分为引言,首先概述了中热水泥熟料以及其在水泥生产中的重要性。
接着介绍了文中的结构和内容安排,并明确了文章的目的和意义。
通过引言部分,读者可以对文章的主题和结构有所了解。
第二部分为正文,首先对热水泥熟料进行了定义和特点的介绍,包括其在水泥生产中的作用和特性,为后续中热水泥熟料率值的控制打下基础。
然后详细探讨了中热水泥熟料率值的意义,包括对水泥产品品质、生产成本和环境影响等方面的影响。
熟料质量控制及煅烧方面的影响因素

培训材料熟之三料质量控制及煅烧方面的影响因素一、熟料质量控制的重要性1、熟料质量是确保水泥质量的核心,熟料质量达不到要求,难以磨制优质的水泥产品。
其中配料和煅烧是决定熟料质量的关键。
2、从生料到熟料,是一个化学反应过程。
化学反应,最基本的核心就是要求参预化学反应的物质间的比例要满足理论要求。
参预化学反应的某一物质的量,不得过剩或者不足,否则,化学反应形成的结果,不是当初设计的结果。
因此,熟料生产过程实际上要求是很精细的,不是表面上的那种粗糙现象。
3、设计合理的熟料率值,通过良好的煅烧,才干生产出优质的水泥熟料。
1、原料磨工艺变化现代水泥企业,以节能高效为主要导向,装备和工艺流程日益简化和高效。
2、原料磨由过去的球磨机改为现代立磨,原料磨工艺装备的改变,对产品质量的影响。
3、球磨机的工艺特点,决定了生料细度更加均匀,900 孔细度小,只在 3.0%以内, 1800 孔细度在 12%以内。
立磨的生料细度粗, 900 孔细度在 6.0-8.0%, 1800 孔细度在 22%摆布。
由上看出,现代水泥工业改成立磨后,生料的颗粒级配产生了较大的变化,立磨的生料粗大颗粒占比例明显上升,中等颗粒的比例,也较球磨机增加了一倍。
4、现代水泥工业、细度标准的变化。
80 年代,国家旋窑管理规程对细度有控制要求,最开始的标准规定生料细度小于等于 10%,作为一次水泥工艺管理的标准来执行,其后更改为 12%。
后来随着先进水泥工艺发展,生料细度作为一次过程控制指标,再也不强制执行,由企业根据自身生产需要自行控制。
质量体系认证,也将细度标准作为企业自行制定来审核,细度标准被企业自身不断放松标准。
按照现行立磨的生产工艺,生料细度按 10%、12%、16% 等等标准,已经无法满足当前立磨工艺的要求,根据立磨的特点及与窑的产能关系,细度只能控制在 20-22%之间,即使控制较好的工厂细度也在 8 摆布。
但是 , 目前的细度控制指标,不表示细度粗对煅烧没有影响。
- 1、下载文档前请自行甄别文档内容的完整性,平台不提供额外的编辑、内容补充、找答案等附加服务。
- 2、"仅部分预览"的文档,不可在线预览部分如存在完整性等问题,可反馈申请退款(可完整预览的文档不适用该条件!)。
- 3、如文档侵犯您的权益,请联系客服反馈,我们会尽快为您处理(人工客服工作时间:9:00-18:30)。
.
煅烧温度和时间对熟料质量的影响作者:刘天振纯阅读
单位:淮海中联水泥有限公司发布日期:2013-08-15来源:
影响熟料质量方面因素很多,但熟料在窑内煅烧是最重要环节之一。
熟料矿物形成实际上是在液相量出现以后进行的。
影响熟料质量方面因素很多,但熟料在窑内煅烧是最重要环节之一。
熟料矿物形成实际上是在液相量出现以后进行的。
液相主要有氧化铁、氧化铝、氧化钙所组成(包括其他次要组分氧化镁、氧化钾、氧化钠等),在高温液相作用下,CS逐渐溶解于液相中与f-cao化合成CS,32随着温度升高和时间延长,CS晶核不断形成,小晶体逐3渐长大,最终形成阿里特晶体。
完成熟料的烧结过程。
实践证明,CS的生成,如果熟料配料时三率值KH、3N、P 适当,生料成分稳定的条件下,主要取决于熟料煅烧温度、液相量、液相性质以及形成晶体反应时间。
本文重点介绍熟料煅烧温
度和晶体反应时间对熟料强度的影响。
淮海中联水泥(287.08元/吨,0%)有限公司2#窑是由南京凯盛水泥设计院设计,2005年3月投产的5000t/d资料Word
.
熟料生产线,2007年8月公司利用现有1条日产5000t/d熟料生产线的窑尾、窑头废气余热,配套建设了1*9MW的纯低温余热发电系统。
该厂3、6、7月份窑系统工艺参数平均台帐(一)
6月与3月份工艺参数对比。
CO平均值下降-44.12ppm。
二次风温上升+25.2℃. f-cao合格率上升+5.81%,在同等喂料量情况下窑速降低-0.3rpm,主窑皮长度增加+3.10m;由于窑皮厚度较3月份降低(见表五)。
窑内填充率下降窑功率同比降低-120A。
其它参数无明显变化。
熟料3天、7天、28天强度分别增加+1.38 Mpa、+5.59 Mpa、+4.19Mpa,液相量略有增加+0.1%。
通过参数对比分析:CO平均值下降和二次风温以及f-cao合格率上升,都能说明窑系统通风状况较好,二、三次风比例合适,窑内煅烧
温度同比较高;在同等喂料量情况下由于窑速降低和主窑皮长度增加,延长了熟料在窑内煅烧时间,使熟料矿物结晶更加完全,熟料强度提高明显。
6月与7月份工艺参数对比。
CO平均值持平。
二次风温分别上升+15.0℃. f-cao合格率上升+9.23%,在同等资料Word
.
喂料量情况下窑速相同,主窑皮长度增加+0.8m;窑皮厚度值持平(见表五),其它参数无明显变化。
熟料3天、7天、28天强度分别增加+1.18 Mpa、+2.29 Mpa、+1.89Mpa,液相量略有增
加+0.04%。
通过参数对比分析:
CO平均值持平和二次风温以及f-cao合格率上升,都能说明窑
系统用风状况合适,窑内煅烧温度保持较高;主窑皮长度略有增加,说明通过适当延长主窑皮长度,来延长熟料在窑内煅烧时间,熟料强度会有所改善。
一、熟料煅烧温度、液相量
液相出现温度,即系统最低共融温度与组分的成分和性质有关。
在CaO-SiO-FeO四元系统中,最低共融温3322度1338℃,由于生料中含有氧化镁、氧化钾、氧化钠等次要组分,因此最低共融温度1250℃,1260℃液相开始出现,1300--1450℃CS开始形成,1450℃以上CS形33成非常迅速。
此温度称之熟料煅烧温度。
随着温度上升,液相量逐渐增加,粘度降低。
有利益熟料CS形
成,熟料3质量较好。
但过高的液相量会给煅烧操作带来困难,如结大块、结圈或烧流损坏设备等。
一般熟料在煅烧阶段液相量为20--30%。
因各企业系统工况和设备差异,液相量的确定要根据本企业实际情况进行控制。
在正常温度下液相量一般控制在22-26%。
在系统工况正常情况下,液相量可偏中上限控制,这样有利于CS形成,我厂液相量控制3资料Word
.
在25-26.5%。
从表一对比分析可以得出,6月份窑系统二风温提高和熟料
f-cao合格率上升,表明窑内煅烧温度的提高。
保证和适当提高窑内煅烧温度对熟料质量有利。
熟料在窑内煅烧温度与生料易烧性、喷煤管设计、煤粉质量等都有关系;系统用风是否合理(总风量大小、二、三次风比例)对窑内温度也有不同程度影响。
所以窑内温度合理掌握,在生产运行中需要多方面考虑,根据某一因素变化作适当调整,在动态中寻找平衡,且不可死板硬套。
我厂在保证窑内煅烧温度方面有以下措施:
1、在控制煤粉质量方面
我公司使用的是国产喷煤管,煤工业分析(表二)根据生产需要我们制定了煤粉与细度对应关系(表三),缓解因煤粉水分上升带来的不利影响。
当煤粉Aad上升时,煤粉细度也适当降低。
在原煤水分超出磨机设计要求时,为降低煤粉水分,在保证磨机安全运行基础上,可根据原煤挥发份适当提高磨机出口温度进行规范:见(表四)
资料Word
.
、保障总风量与料量合理配合,在窑系统达到或超2
含量:旋风筒出口OC1过设计产能后控制依据:2 330℃。
CO 含量:≤350ppm; C1出口温度在≤1.9-2.5%;、二、三次风比例配合问题,我们正常情况下三次 3
C5;在线控制分解炉出口温度和风闸板开度在50-60%下料管温C5下料管温度之间,一般控制解炉出口温度比℃,严禁出现温
度倒挂现象,如果出现倒挂现10-20度高内燃烧不好,这时可适当增加三次象,说明煤粉在分解炉风量或改善煤粉质量进行必要控制。
温度窑尾温度控制在1030℃,4、控制窑头二次风温≥
℃,当发现窑尾温度偏高或二次风温偏低时,适501150±当减少窑内通风量。
窑头二次风温、窑尾温度高低除与窑内通风大小有关外,与窑头用煤量、煤粉质量以及燃烧器本身设计性能等都有关。
二、烧成时间
形成不仅需要煅烧温度,还要有一定时间(一般S C3),熟料煅烧时间与合适的温度梯度场、烧10-20min在资料Word
.
成带长度、窑转速、窑衬内径、窑斜度等有关,煅烧时间与烧成带窑长度成正比,与窑转速、窑衬内径、窑斜度成反比。
合适的温度梯度场,即达到烧成温度1300--1450℃后的火焰要有一定长度,没有明显的峰值出现。
使物料在正常烧成温度的时间延长,避免包壳熟料出现,这种熟料结粒正常,一般在¢20-30mm,但熟料破开后会发现,外部裹有一环致密坚硬的外壳,内部熟料颜色与外部一致,但密实度较外部差。
这类熟料多数因为窑内温度较高,但温度场分布不均,是明显的短焰急烧熟料。
这类熟料在正常烧成温度场内停留时间较短。
质量方面表现为f-cao往往较低,但熟料28天强度不高,长时间存放容易出
现粉化现象。
在这种煅烧环境下烧成带局部温度上升,会造成耐火砖使用周期下降。
合理的窑皮长度、平整度是表明窑内温度梯度是否合适的标志。
物料在正常情况下通过窑内所用时间:
t = 11.4L/(n.Di.S)
式中t---运动时间min
L---烧成带窑长度m
n----窑转速r/min
Di---窑衬内径m
资料Word
.
S---窑斜度°
熟料在(表一)三种情况下烧成带停留时间与窑速、窑皮长度之间关系(表五)
从表五中可以看出,第一种情况熟料在烧成带停留时间最短仅9.09min,3月与6月情况相比平均缩短-1.86min;7月与6月情况相比平均缩短-0.33min。
综合表一、表五分析,主窑皮长度增
加0.80m、3.1m和在同等喂料量情况下窑速降低约0.3rpm,都会延长熟料在窑内的煅烧时间。
而适当延长熟料在烧成带停留时间,使熟料矿物晶体发育更加完全,可在一定程度上提高熟料强度和稳定熟料质量。
三、结论
正常结粒熟料的形成需要足够的熟料烧成温度和时间,而熟料烧成温度和烧成时间又与生料易烧性、煤粉质量、烧成带长度、厚度以及窑速等有关。
在正常生产运行中,企业应根据实际生产工艺状况,及时调整系统有关工艺参数,以保障熟料能在合适的温度梯度范围内停留足够的煅烧时间,形成结晶良好的熟料矿物成分,已达到稳定或提高熟料质量的目的。
资料Word
.
资料Word。