影响熟料质量的有害成份
影响水泥熟料质量的因素

一、氧化镁原料中所含MgO经高温煅烧,其中部分与熟料矿物结合成固溶体,部分熔于液相中,因此,当熟料中含有少量MgO时,能降低熟料的烧成温度,增加液相数量,降低粘度,改善水泥的色泽。
在硅酸盐水泥中,MgO与主要熟料矿物化合的最大含量为2%,超过部分呈游离状态,以方镁石的形式出现。
方镁石与水反应生成Mg(OH)2,其体积较游离MgO增大,而且反应速度极慢,导致已经硬化的水泥凝固体内部发生体积膨胀而开裂,造成所谓MgO 膨胀性破裂。
二、游离二氧化硅燧石是原料中的有害杂质,以隐晶质的α-石英为主,结构致密,质地坚硬,耐压强度高,化学活性低,对窑磨操作均有不良影响。
三、氯氯在烧成系统中主要生成CaCl2或氯化碱,其挥发性特别高,在窑内几乎全部再次挥发,形成氯、碱循环富集,致预热器生料中氯化物的含量提高近百倍,为此,国际上生料中氯含量的通用阀值≤0.015%,国内目前的控制值为0.020%。
四、碱(K2O+Na2O)碱对水泥生产的影响主要有两方面,一是影响新型干法熟料烧成系统的正常生产,二是影响熟料的质量。
煅烧含碱过高的生料,由于碱性挥发物在窑尾和预热器中的循环富集,易引起结皮堵塞,回转窑内则是料子发粘,烧结温度范围缩小,飞砂严重,窑皮疏松,致使熟料质量下降,严重时将无法正常生产。
生料中的碱除一部分挥发循环外,其余的大部分均以硫酸盐的形式存在于熟料中。
如果含碱量过高,则其凝结时间将缩短,以致急凝,安定性不良,抗折强度降低,并出现1d、3d的抗压强度略有升高,而7d、28d的抗压强度明显下降。
五、硫生料和燃料中的硫在燃烧过程中生成SO2,又在窑烧成带汽化,在窑气中与R2O结合,形成气态的硫酸碱,然后凝聚在温度较低处的生料颗粒表面。
这些R2SO4除一小部分被窑灰带走外,因其挥发分较低,故大部分被固定在熟料中而带出窑外。
这是SO2与R2O含量比例正好平衡时的情况。
如果SO2含量有富裕,则在预热器中它与生料中的CaCO3反应生成CaSO4进入窑内。
如何石灰石有害成分?切记提高熟料强度

一、前言某公司两条5000t/d新型干法水泥熟料生产线于2010年10月建成投产。
自备的扁担山石灰岩矿山石灰岩矿富含煌斑岩、麻石等低品位岩石,成分波动较大。
生产采用高、低硅砂岩、铁粉等组份配料。
砂岩、铁粉等原材料均需外供,使用的烟煤低位热值在5400×4.18kJ/kg左右。
2015年10月,公司熟料强度持续偏低,28d抗压强度均值在54MPa,个别样品甚至只有48MPa,与公司熟料强度控制目标56MPa相比,强度下降很大。
强度下降,意味着竞争力下降,水泥中熟料配比上升,成本增加。
二、原因分析从原燃材料成分,生产配料,煅烧过程数据来看,均未发生明显变化。
检查化验室压块设备,磨具,养护等设备及环节,没有发现异常情况。
而公司砂岩均为外购,矿点较多,成分波动,碱含量偏高。
2015年12月,公司生产部门把提高熟料强度重点放在加强进厂砂岩的品质控制上,加强辅料堆场均化。
生料中控制w(K₂O+Na₂O)<1.0%,w(Cl)<0.015%~0.020%,熟料强度并没有得到明显改善。
公司两条熟料生产线,当生料磨停机检修或避峰时,烟囱废气中二氧化硫含量明显上升,甚至有超标的情况出现。
硫的化学分析检测耗时长,检验量大,对生产的控制指标不便捷,效果差。
一般水泥企业日常很少对原材料中SO₃的含量进行监测。
为了确保二氧化硫排放达标,2016年3月,公司品质部对原燃材料的硫含量进行全面检验和统计分析。
硅酸盐水泥熟料生产的原料中,一般硫的来源有二,一是黏土或页岩中常含有少量硫,或者硫铁矿、硫酸盐或其他有机硫化合物。
硫的第二个来源是燃料。
通过对公司矿山开采石灰石岩普查得知,石灰石原料中硫含量整体较高。
当生料进入回转窑后,在通常的氧化气氛中,含硫化合物最终都被氧化成为三氧化硫。
由于水泥生料为碱性,当其进入回转窑时就会吸收煤燃烧所产生的气态硫化物,造成生料中含硫化合物逐渐增多,当生料进入高温区时,所有存在的硫酸钙都会部分分解,因而生料中的含硫量是先增至最大值,然后再降低。
熟料中六价铬高的原因及控制

熟料中六价铬高的原因及控制熟料是水泥的主要原料之一,其中六价铬是一个重要的污染物。
本文将探讨熟料中六价铬高的原因,并提出相应的控制措施,以减少对环境的影响。
六价铬是一种有毒物质,对人体和环境都具有一定的危害。
熟料中六价铬含量高的原因主要有以下几个方面。
熟料中六价铬高的原因之一是原料中六价铬的含量高。
熟料生产过程中使用的原料通常包括石灰石、粘土等,这些原料中往往含有六价铬。
如果原料中六价铬的含量较高,那么在熟料生产过程中就会导致六价铬的含量升高。
熟料中六价铬高的原因之二是熟料生产过程中的化学反应。
在熟料生产过程中,原料经过破碎、混合、煅烧等工艺过程,会发生一系列的化学反应。
其中,一些反应会导致六价铬的含量升高。
比如,在高温下,铬的氧化态容易发生变化,从而生成六价铬。
熟料中六价铬高的原因还与熟料生产过程中的操作和设备有关。
熟料生产过程中需要使用煤粉、燃油等燃料进行煅烧,这些燃料中可能含有六价铬。
如果燃烧过程不完全,就会导致六价铬的含量升高。
另外,熟料生产过程中也使用了一些添加剂,这些添加剂中也可能含有六价铬。
如果添加剂的质量不合格或使用不当,就会导致六价铬的含量增加。
针对熟料中六价铬高的问题,我们可以采取一系列的控制措施来减少六价铬的排放。
我们可以加强原料的筛选和管理。
选择质量合格的原料,并进行充分的混合和破碎,以减少六价铬的含量。
我们可以优化熟料生产过程中的工艺参数。
通过控制煅烧温度、煅烧时间等参数,减少六价铬的生成。
我们还可以改进燃料的选择和燃烧设备的设计。
选择低铬或无铬的燃料,并加强燃烧过程的控制,确保燃烧充分,减少六价铬的排放。
我们还可以加强对添加剂的管理和控制。
选择合格的添加剂,并确保其使用正确,避免添加剂中六价铬的释放。
我们还应建立完善的监测和管理体系,定期检测熟料中六价铬的含量,并进行数据分析和监测报告,及时发现问题并采取相应的措施进行调整。
熟料中六价铬高的原因主要包括原料中六价铬含量高、化学反应、操作和设备等方面。
水泥、熟料质量控制管理

进厂石灰石主要质量控制项目:日常以控制 CaO含量为主,即进厂石灰石品位。对于其中的有 害成份,一般随石灰石品位变化:石灰石品位越 高,有害成份越低;石灰石品位越低,有害成份 越高。
进厂石灰石品位控制原则:控制合理的进厂 石灰石品位,是为了保证生料率值满足预计的要 求。石灰石品位既非越高越好、也非越低越好, 应根据所使用的硅铝质原料的硅酸率来限定。如 所用硅铝质原料的硅酸率偏高,进厂石灰石的品 位应偏低控制;硅铝质原料的硅酸率偏低,则进 厂石灰石品位应偏高控制。
类别
CaO(%)
MgO (%)
石灰石
一级品二 级品
>48 45~48
<2.5 <3.0
泥灰岩
35~45 <3.0
R2O(%) SO3(%) 燧石或石英
<1.0 <1.0
<1.0 <1.0
<4.0 <4.0
<1.2 <1.0
<4.0
2、硅铝质原料
天然硅铝质原料的种类很多,有粘土、黄土、页岩、 砂岩、粉砂岩等。
烟煤
≥22
≤28.0
≤1.0
≥5000
贫瘦煤
10≤V≥20
≤28.0
≤1.0
≥5000
原燃材料质量控制
生、熟料质量控制应以配料为纲,从原燃材料质量抓 起,强化过程均化.原材料质量是制备成分合适,均匀稳 定的生料基础条件,生料质量是熟料质量的基础。
1、石灰石质原料控制
石灰石质原料是构成生料的主要原料,一般在生料中 占85%左右。石灰石的质量指标控制主要包括CaO、MgO、 R2O、SO3、Cl-等。其中CaO是构成生料的主要成份,MgO、 R2O、SO3、Cl-的含量为有害成份。CaO、MgO、R2O、SO3、 Cl-的含量是石灰石矿山前期勘探需查明的主要内容。较 高的CaO、较低的MgO、R2O、SO3、Cl-含量是优质石灰石矿 山和生产优质熟料的基本要求,矿山选址的依据。
浅谈新型干法水泥生产中熟料的质量分析与控制
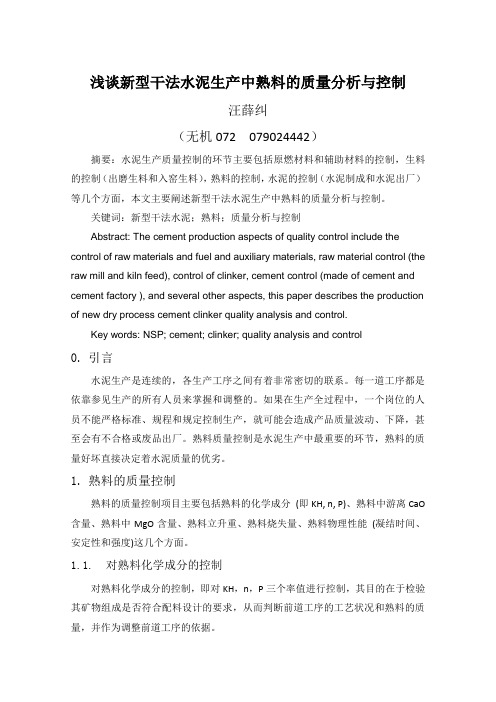
浅谈新型干法水泥生产中熟料的质量分析与控制汪薛纠(无机072 079024442)摘要:水泥生产质量控制的环节主要包括原燃材料和辅助材料的控制,生料的控制(出磨生料和入窑生料),熟料的控制,水泥的控制(水泥制成和水泥出厂)等几个方面,本文主要阐述新型干法水泥生产中熟料的质量分析与控制。
关键词:新型干法水泥;熟料;质量分析与控制Abstract: The cement production aspects of quality control include the control of raw materials and fuel and auxiliary materials, raw material control (the raw mill and kiln feed), control of clinker, cement control (made of cement and cement factory ), and several other aspects, this paper describes the production of new dry process cement clinker quality analysis and control.Key words: NSP; cement; clinker; quality analysis and control0.引言水泥生产是连续的,各生产工序之间有着非常密切的联系。
每一道工序都是依靠参见生产的所有人员来掌握和调整的。
如果在生产全过程中,一个岗位的人员不能严格标准、规程和规定控制生产,就可能会造成产品质量波动、下降,甚至会有不合格或废品出厂。
熟料质量控制是水泥生产中最重要的环节,熟料的质量好坏直接决定着水泥质量的优劣。
1.熟料的质量控制熟料的质量控制项目主要包括熟料的化学成分(即KH, n, P)、熟料中游离CaO 含量、熟料中MgO含量、熟料立升重、熟料烧失量、熟料物理性能(凝结时间、安定性和强度)这几个方面。
水泥生产中熟料的控制方法和常见问题解决办法
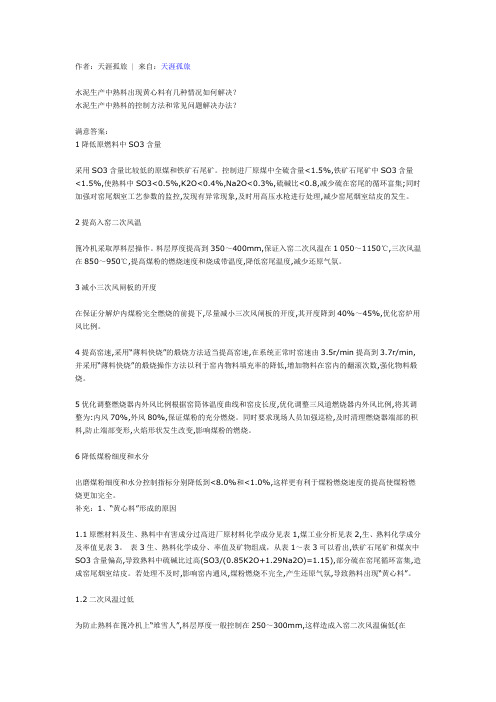
作者:天涯孤旅|来自:天涯孤旅水泥生产中熟料出现黄心料有几种情况如何解决?水泥生产中熟料的控制方法和常见问题解决办法?满意答案:1降低原燃料中SO3含量采用SO3含量比较低的原煤和铁矿石尾矿。
控制进厂原煤中全硫含量<1.5%,铁矿石尾矿中SO3含量<1.5%,使熟料中SO3<0.5%,K2O<0.4%,Na2O<0.3%,硫碱比<0.8,减少硫在窑尾的循环富集;同时加强对窑尾烟室工艺参数的监控,发现有异常现象,及时用高压水枪进行处理,减少窑尾烟室结皮的发生。
2提高入窑二次风温篦冷机采取厚料层操作。
料层厚度提高到350~400mm,保证入窑二次风温在1 050~1150℃,三次风温在850~950℃,提高煤粉的燃烧速度和烧成带温度,降低窑尾温度,减少还原气氛。
3减小三次风闸板的开度在保证分解炉内煤粉完全燃烧的前提下,尽量减小三次风闸板的开度,其开度降到40%~45%,优化窑炉用风比例。
4提高窑速,采用“薄料快烧”的煅烧方法适当提高窑速,在系统正常时窑速由3.5r/min提高到3.7r/min,并采用“薄料快烧”的煅烧操作方法以利于窑内物料填充率的降低,增加物料在窑内的翻滚次数,强化物料煅烧。
5优化调整燃烧器内外风比例根据窑筒体温度曲线和窑皮长度,优化调整三风道燃烧器内外风比例,将其调整为:内风70%,外风80%,保证煤粉的充分燃烧。
同时要求现场人员加强巡检,及时清理燃烧器端部的积料,防止端部变形,火焰形状发生改变,影响煤粉的燃烧。
6降低煤粉细度和水分出磨煤粉细度和水分控制指标分别降低到<8.0%和<1.0%,这样更有利于煤粉燃烧速度的提高使煤粉燃烧更加完全。
补充:1、“黄心料”形成的原因1.1原燃材料及生、熟料中有害成分过高进厂原材料化学成分见表1,煤工业分析见表2,生、熟料化学成分及率值见表3。
表3生、熟料化学成分、率值及矿物组成,从表1~表3可以看出,铁矿石尾矿和煤灰中SO3含量偏高,导致熟料中硫碱比过高(SO3/(0.85K2O+1.29Na2O)=1.15),部分硫在窑尾循环富集,造成窑尾烟室结皮。
关于熟料的组成
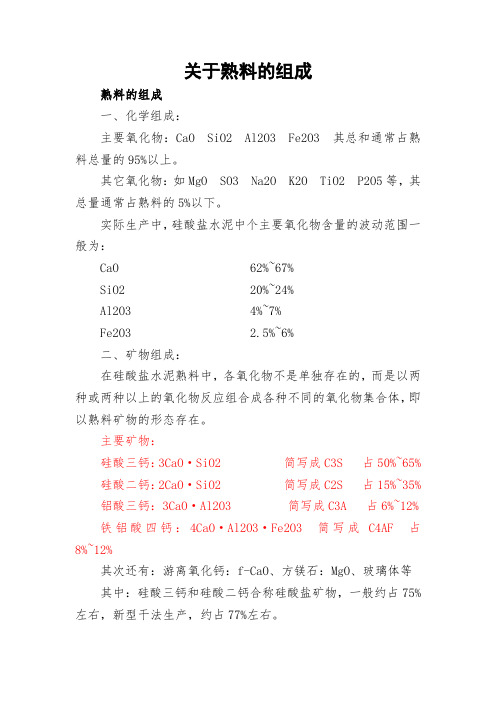
关于熟料的组成熟料的组成一、化学组成:主要氧化物:CaO SiO2Al2O3Fe2O3其总和通常占熟料总量的95%以上。
其它氧化物:如MgO SO3Na2O K2O TiO2P2O5等,其总量通常占熟料的5%以下。
实际生产中,硅酸盐水泥中个主要氧化物含量的波动范围一般为:CaO62%~67%SiO220%~24%Al2O34%~7%Fe2O3 2.5%~6%二、矿物组成:在硅酸盐水泥熟料中,各氧化物不是单独存在的,而是以两种或两种以上的氧化物反应组合成各种不同的氧化物集合体,即以熟料矿物的形态存在。
主要矿物:硅酸三钙:3CaO·SiO2简写成C3S占50%~65%硅酸二钙:2CaO·SiO2 简写成C2S占15%~35%铝酸三钙:3CaO·Al2O3简写成C3A占6%~12%铁铝酸四钙:4CaO·Al2O3·Fe2O3简写成C4AF占8%~12%其次还有:游离氧化钙:f-CaO、方镁石:MgO、玻璃体等其中:硅酸三钙和硅酸二钙合称硅酸盐矿物,一般约占75%左右,新型干法生产,约占77%左右。
铝酸三钙和铁铝酸四钙合称熔剂矿物,一般约占22%左右,新型干法生产,约占20%左右。
硅酸盐矿物和熔剂矿物总和约占95%左右。
熟料矿物特性一、硅酸三钙(A矿、又称阿里特、约占55%左右)(一)、存在形式:1、纯C3S只在2065℃~1250℃温度范围内稳定,在2065℃以上不一致熔融为CaO 与液相;在1250℃以下分解为C2S和CaO。
2、纯C3S具有同质多晶现象。
3、化学组成:熟料中C3S不纯,总是与少量的其他氧化物如Al2O3、Fe2O3、MgO、R 2O等形成固溶体。
4、显微结构:在反光显微镜下为黑色多角形颗粒(如下图),又称阿利特(Alite),简称A矿。
4、显微结构:在反光显微镜下为黑色多角形颗粒(二)、矿物水化特性:1、水化较快,水化反应主要在28d以内进行,约经一年后水化过程基本结束。
水泥熟料质量过程控制

IM:提升0.05-0.30。因此稳定原煤灰分是 熟料率值稳定的基础。进厂原煤必须要 求采取均化措施。
h
34
5、粉煤灰炉渣的选择和利用
我厂粉煤灰炉渣资源主要来自热电分 厂,也有部分粉煤灰来自周边电厂,二 者都是煤的燃尽物,成份大体相同,是 铝质 校正原料。
h
35
5.1粉煤灰和炉渣的质量要求
h
4
物检组
检测项目: 水泥的物理性能:细度、比表面积、安定 性、密度、凝结时间(初凝和终凝)、 熟料的龄期、强度(抗折和抗压)。 出磨水泥的龄期、强度(抗折和抗压)。 出厂水泥的龄期、强度(抗折和抗压)。
h
5
配料组
检测项目: 出磨和入窑的三率值:KH、SM、IM。 熟料的三率值: KH、SM、IM。
h
26
4、原煤资源的特点和选择
4.1、燃料质量控制 ①燃料种类: 烟煤、无烟煤等。 ②进厂原煤质量控制工业分析、水份。 ③入窑煤粉质量控制细度、水份、工业分析
。抓好原煤均化。
h
27
我厂原煤资源主要来自淮化集团, 国投新集和贸易煤,品质中低,发热量 20000KJ/Kg左右,属有烟煤,灰份波 动大一般在22% - 32%之间。煤的燃 烧首先是挥发份的燃烧,挥发份是由烃 类的CO、O2、N2等组成的混合气体 ,固定碳发热量大约是挥发份的1.5倍 。二者共同构成火焰形态,灰份大则燃 烧慢火焰长,适当的水份可提高煤粉燃 烧的辐射热。
h
15
1、石灰石的质量控制
①依据资源状况及配料要求,确定石灰 石控制指标,日常检测品位、水份、粒 度。
②全面掌握矿山石灰石质量状况及变化 规律。
③做好不同质量石灰石的台段搭配,确 保进厂石灰石品位。
- 1、下载文档前请自行甄别文档内容的完整性,平台不提供额外的编辑、内容补充、找答案等附加服务。
- 2、"仅部分预览"的文档,不可在线预览部分如存在完整性等问题,可反馈申请退款(可完整预览的文档不适用该条件!)。
- 3、如文档侵犯您的权益,请联系客服反馈,我们会尽快为您处理(人工客服工作时间:9:00-18:30)。
影响熟料质量的有害成份
一、氧化镁
原料中所含MgO经高温煅烧,其中部分与熟料矿物结合成固溶体,部分熔于液相中,因此,当熟料中含有少量MgO时,能降低熟料的烧成温度,增加液相数量,降低粘度,改善水泥的色泽。
在硅酸盐水泥中,MgO与主要熟料矿物化合的最大含量为2%,超过部分呈游离状态,以方镁石的形式出现。
方镁石与水反应生成Mg(OH)2,其体积较游离MgO增大,而且反应速度极慢,导致已经硬化的水泥凝固体内部发生体积膨胀而开裂,造成所谓MgO膨胀性破裂。
二、游离二氧化硅
燧石是原料中的有害杂质,以隐晶质的α-石英为主,结构致密,质地坚硬,耐压强度高,化学活性低,对窑磨操作均有不良影响。
三、氯
氯在烧成系统中主要生成CaCl2或氯化碱,其挥发性特别高,在窑内几乎全部再次挥发,形成氯、碱循环富集,致预热器生料中氯化物的含量提高近百倍,为此,国际上生料中氯含量的通用阀值≤0.015%,国内目前的控制值为0.020%。
四、碱(K2O+Na2O)
碱对水泥生产的影响主要有两方面,一是影响新型干法熟料烧成系统的正常生产,二是影响熟料的质量。
煅烧含碱过高的生料,由于碱性挥发物在窑尾和预热器中的循环富集,易引起结皮堵塞,回转窑内则是料子发粘,烧结温度范围缩小,飞砂严重,窑皮疏松,致使熟料
质量下降,严重时将无法正常生产。
生料中的碱除一部分挥发循环外,其余的大部分均以硫酸盐的形式存在于熟料中。
如果含碱量过高,则其凝结时间将缩短,以致急凝,安定性不良,抗折强度降低,并出现1d、3d的抗压强度略有升高,而7d、28d的抗压强度明显下降。
五、硫
生料和燃料中的硫在燃烧过程中生成SO2,又在窑烧成带汽化,在窑气中与R2O结合,形成气态的硫酸碱,然后凝聚在温度较低处的生料颗粒表面。
这些R2SO4除一小部分被窑灰带走外,因其挥发分较低,故大部分被固定在熟料中而带出窑外。
这是SO2与R2O含量比例正好平衡时的情况。
如果SO2含量有富裕,则在预热器中它与生料中的CaCO3反应生成CaSO4进入窑内。
在烧成带,其大部分再分解成CaO和气态SO2,小部分残存于熟料中。
这样,气态SO2在窑气中循环富集,易堵塞。
反之,如碱有富裕,则剩余的碱就会生成高挥发性的氯化碱和中等挥发性的碳酸碱,形成氯和碱的循环,影响预热器的正常操作。