systemiii
2X M5 HiPer SYBR Premix EsTaq plus (with Tli RNase

2X M5 HiPer SYBR Premix EsTaq plus (with Tli RNaseH)使用说明书产品名称单位货号2X M5 HiPer SYBR Premix EsTaq plus (with Tli RNaseH) 50 μl反应× 40 次MF788-T2X M5 HiPer SYBR Premix EsTaq plus (with Tli RNaseH) 50 μl反应× 200 次MF788-012X M5 HiPer SYBR Premix EsTaq plus (with Tli RNaseH) 50 μl反应× 400 次MF788-02【储存条件】长期保存,请置于-20˚C,有效期24个月。
经常使用,可置于4˚C保存至少六个月。
【产品简介】本产品采用Sybrgreen嵌合荧光法进行荧光定量的专用试剂。
制品中含有荧光定量反应的最适浓度Sybrgreen,是一种2×浓度的预混试剂,进行实验时,PCR反应液的配制十分方便简单。
制品中使用了antiTaq抗体的Hot Start法用DNA聚合酶,与荧光定量反应适合Buffer组合,可以有效抑制非特异性的PCR扩增,大大提高PCR的扩增效率,可以进行高灵敏度的荧光定量扩增反应。
本产品Buffer 经过改良,使反应特异性比SybrGreenPremix Ex Taq (withTli RNaseH)(货号MF787)更高。
另外,本产品中添加了Tli RNaseH (耐热性RNaseH),以cDNA作为模板进行PCR反应时,可以很好地抑制由于cDNA中残存mRNA 对PCR反应造成的阻害作用。
适合于快速荧光定量扩增反应,可以在宽广的定量区域内得到良好的标准曲线,对靶基因进行准确定量、检测,重复性好,可信度高。
【产品组份】MF788-T MF788-012x M5 HiPer SYBR Premix EsTaq plus (withTli RNaseH) * 1.0 ml 5x1mlROX Reference Dye(50×)** 40μl 200μlROX Reference Dye II(50×)** 40μl200μl*由以下组分预混而成:EsTaq plus,dNTP Mixture,Mg2+,Tli RNaseH,Sybrgreen。
X20系统用户手册说明书
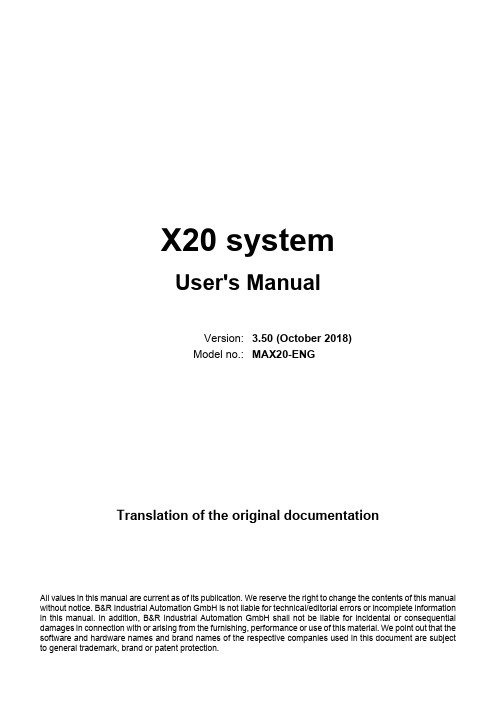
system32文件删除方法
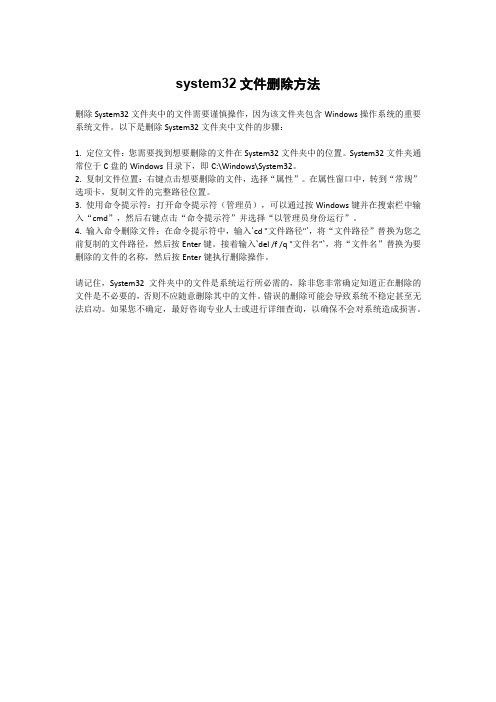
system32文件删除方法
删除System32文件夹中的文件需要谨慎操作,因为该文件夹包含Windows操作系统的重要系统文件。
以下是删除System32文件夹中文件的步骤:
1. 定位文件:您需要找到想要删除的文件在System32文件夹中的位置。
System32文件夹通常位于C盘的Windows目录下,即C:\Windows\System32。
2. 复制文件位置:右键点击想要删除的文件,选择“属性”。
在属性窗口中,转到“常规”选项卡,复制文件的完整路径位置。
3. 使用命令提示符:打开命令提示符(管理员),可以通过按Windows键并在搜索栏中输入“cmd”,然后右键点击“命令提示符”并选择“以管理员身份运行”。
4. 输入命令删除文件:在命令提示符中,输入`cd "文件路径"`,将“文件路径”替换为您之前复制的文件路径,然后按Enter键。
接着输入`del /f /q "文件名"`,将“文件名”替换为要删除的文件的名称,然后按Enter键执行删除操作。
请记住,System32文件夹中的文件是系统运行所必需的,除非您非常确定知道正在删除的文件是不必要的,否则不应随意删除其中的文件。
错误的删除可能会导致系统不稳定甚至无法启动。
如果您不确定,最好咨询专业人士或进行详细查询,以确保不会对系统造成损害。
Promega—PolyATract mRNA Isolation System III

采用Promega公司的PolyATract mRNA Isolation System III。
从总RNA中分离mRNA1.探针的退火1)在一个无菌的、无RNase的离心管中,加入未稀释的总RNA溶液,使终体积达到1.5ml。
可使用更大量的总RNA,其浓度可至过饱和,即有絮状RNA沉淀析出,但当有絮状RNA沉淀存在时,后续的退火反应操作会受到一定程度影响;也可使用更少量的总RNA(50ug),但mRNA产量可能无法保证。
2)将离心管置于65℃水浴中10分钟或略长时间。
3)加入15ul 的Biotinylated-Oligo(dT)探针和39ul的20×SSC到RNA中。
颠倒数次以混匀,静置于室温下至充分冷却。
这将需要10分钟或略少的时间。
在该溶液冷却期间,制备0.5×和0.1×SSC贮存液2.贮存液制备1)通过在三个无菌的、无RNase的离心管中各自混合30ul的20×SSC和1.170ml 的无RNase的水来制备三份1.2ml的无菌的0.5×SSC。
2)通过在三个无菌的、无RNase的离心管中各自混合7ul的20×SSC和1.393ml 的无RNase的水来制备三份1.4ml的无菌的0.1×SSC。
3.链霉抗生物素蛋白-磁珠(Streptavidin-Paramagnetic Particles)的漂洗1)取三管链霉抗生物素蛋白-磁珠,轻弹离心管的底部使SA-PMPs重悬直至其充分分散,吸取悬液合并于一管。
2)使汇总的SA-PMPs重悬直至其充分分散,然后将离心管置于磁柱中直至SA-PMPs已经聚集在离心管壁上(大约30秒)。
小心地移出上清。
不要离心沉淀颗粒。
3)用0.5×SSC漂洗SA-PMPs三次(每次0.9ml),每次都使用磁柱来捕获它们,然后小心地移去上清。
4)重悬漂洗过的SA-PMPs于0.3ml的0.5×SSC中。
FM ACOUSTICS Inspiration System XS III落地式音箱

FM ACOUSTICS Inspiration System XS III落地式音箱
一言
【期刊名称】《现代音响技术》
【年(卷),期】2011(000)012
【摘要】对很多音响爱好者来说.FM ACOUSTICS留给他们的第一外在印象也许是售价上的贵价和产品的独一无二的工业设计。
当然.这种感觉在发烧友听过产品、摩受到声音.并了解了技术后。
却又会觉得它的贵是非常合理的。
【总页数】2页(P88-89)
【作者】一言
【作者单位】不详
【正文语种】中文
【中图分类】TN912.26
【相关文献】
1.FM Acoustics FM 268前级是一部完全以最严谨的技术手段架构起来的真正全
平衡结构的前级放大器 [J], 一言
2.FM Acoustics FM268前级 [J], 一言
3.FM Acoustics FM118四十周年限量版单声道后级 [J], 一言
4.音响中的劳斯莱斯FM Acoustics 268+1811+XS1 [J], 无
5.FM ACOUSTICS 追求极致完美境界——FM ACOUSTICS的传奇 [J], 庄宏道因版权原因,仅展示原文概要,查看原文内容请购买。
LOCS III 白内障分级 权威
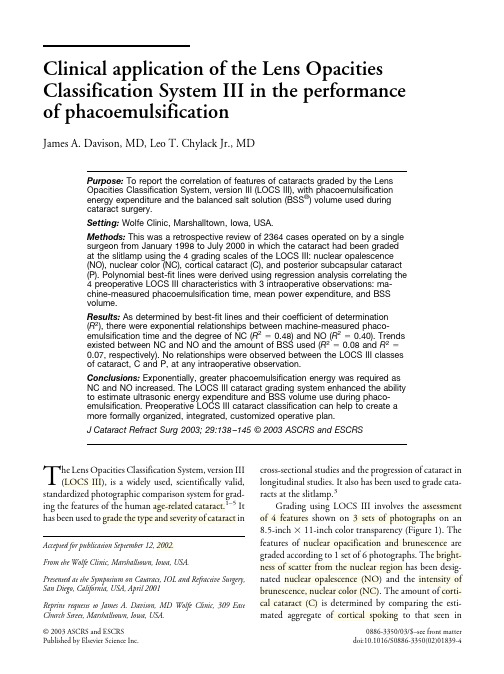
Clinical application of the Lens Opacities Classification System III in the performance of phacoemulsificationJames A.Davison,MD,Leo T.Chylack Jr.,MDPurpose:To report the correlation of features of cataracts graded by the Lens Opacities Classification System,version III (LOCS III),with phacoemulsification energy expenditure and the balanced salt solution (BSS ®)volume used during cataract surgery.Setting:Wolfe Clinic,Marshalltown,Iowa,USA.Methods:This was a retrospective review of 2364cases operated on by a single surgeon from January 1998to July 2000in which the cataract had been graded at the slitlamp using the 4grading scales of the LOCS III:nuclear opalescence (NO),nuclear color (NC),cortical cataract (C),and posterior subcapsular cataract (P).Polynomial best-fit lines were derived using regression analysis correlating the 4preoperative LOCS III characteristics with 3intraoperative observations:ma-chine-measured phacoemulsification time,mean power expenditure,and BSS volume.Results:As determined by best-fit lines and their coefficient of determination (R 2),there were exponential relationships between machine-measured phaco-emulsification time and the degree of NC (R 2ϭ0.48)and NO (R 2ϭ0.40).Trends existed between NC and NO and the amount of BSS used (R 2ϭ0.08and R 2ϭ0.07,respectively).No relationships were observed between the LOCS III classes of cataract,C and P,at any intraoperative observation.Conclusions:Exponentially,greater phacoemulsification energy was required as NC and NO increased.The LOCS III cataract grading system enhanced the ability to estimate ultrasonic energy expenditure and BSS volume use during phaco-emulsification.Preoperative LOCS III cataract classification can help to create a more formally organized,integrated,customized operative plan.J Cataract Refract Surg 2003;29:138–145©2003ASCRS and ESCRSThe LensOpacitiesClassification System,versionIII (LOCSIII),isa widelyused,scientificallyvalid,standardizedphotographic comparisonsystemfor grad-ingthe featuresof thehuman age-relatedcataract.1–5It hasbeen used to grade the type and severity of cataract incross-sectional studies and the progression of cataract in longitudinal studies.It also has been used to grade cata-racts at the slitlamp.3Grading using LOCS III involves the assessment of 4features shown on 3sets of photographs on an 8.5-inch ϫ11-inch color transparency (Figure 1).The features of nuclear opacification and brunescence are graded according to 1set of 6photographs.The bright-ness of scatter from the nuclear region has been desig-nated nuclear opalescence (NO)and the intensity of brunescence,nuclear color (NC).The amount of corti-cal cataract (C)is determined by comparing the esti-mated aggregate of cortical spoking to that seen inAccepted for publication September 12,2002.From the Wolfe Clinic,Marshalltown,Iowa,USA.Presented at the Symposium on Cataract,IOL and Refractive Surgery,San Diego,California,USA,April 2001Reprint requests to James A.Davison,MD Wolfe Clinic,309East Church Street,Marshalltown,Iowa,USA.©2003ASCRS and ESCRS0886-3350/03/$–see front matter Published by Elsevier Science Inc.doi:10.1016/S0886-3350(02)01839-45separate photographs.Similarly,the estimated amountof posterior subcapsular cataract(P)is determined by comparing it to another5photographs depicting in-creasing amounts of posterior subcapsular cataract.The grade for each feature is derived by locating the image of the patient’s lens on the scale of severity for each feature represented in the color transparency.The NC and NO are graded on a decimal scale of0.1to6.9. The severity of C and P are graded on a decimal scale of 0.1to5.9.The final LOCS III grade comprises4deci-mal values,1each for NO,NC,C,and P.In the original publication describing the LOCS III system,1an assessment of within-grader and between-grader reproducibility was done and expressed as a“95% confidence interval”for each scale.On average,these 95%confidence intervals were approximately0.7units. The intervals were used to define a significant change in the severity of the cataract.For example,if the NO grade was2.3at baseline and1year later it was3.5,the increase in severity(3.5–2.3ϭ1.2)was greater than the95% confidence interval(0.7)and it was therefore reasonable to conclude that one was95%confident that the change was statistically significant.If the increase had been only 0.5units,the increase could more likely be the result of the intrinsic methodologic noise of the LOCS III system and not a true increase in the severity of the cataract.Since1998,LOCS III has been used systematically in the clinical practice of one author(J.A.D.).Preoper-ative LOCS III grading of all surgical patients was done at the slitlamp to improve clinical documentation in the clinical record.Parenthetical descriptions were rarely added but usually included the critical nature of the centrality within the visual axis of subtle localized inter-faced zones of NO and NC,cortical spokes,or subcap-sular opacities.There was consistency in grading over time,and patients could be told with greater confidence whether their cataracts were stable or progressing.It was also helpful to have accurate measures of cataract severity when discussing cases with third-party payer representa-tives;surgical interventional decisions to offer surgery to some patients could be better defended.Over time,LOCS III slitlamp grading was empiri-cally incorporated into the decision-making process and planning of upcoming surgeries.Ultimately,this re-sulted in a more organized,integrated,customized op-erative plan for each patient.Patients and MethodsIn this retrospective study,2364consecutive cases of phacoemulsification were analyzed with respect to the 4LOCS III characteristics and machine-measured phaco-emulsification time,average machine measured power(%), and the balanced salt solution(BSS)volume used.All data points had been recorded in2186cases.Surgery was per-formed from January1998to July2000by a single surgeon (J.A.D),who also performed LOCS III grading of all cataracts at the slitlamp.A standardized nuclear-fracture quadrant-aspiration phacoemulsification technique was used with a straight 45-degree0.9mm ABS MicroTip with the Alcon Legacy 20,000machine.6After topical anesthesia was administered,a temporal clear corneal incision was made.Grooving was ac-complished with the machine in memory I(phacoemulsifica-Figure1.(Davison)The LOCS III standard images in an8.5-inchϫ11-inch color transparency as used in the office at the slitlamp.The top row contains the standards for NO and NC.The second row contains the standards for grading C and the bottom row,for grading P.J CATARACT REFRACT SURG—VOL29,JANUARY2003139tion power maximum,90%;vacuum maximum,50mm Hg;aspiration flow rate,14cc/minute)(Figure 2).Wider,deeper grooves were made as nuclear hardness increased.The pos-terior nuclear plate was torn from the periphery toward the center by cross action with the phacoemulsification tip and a custom,modified,0.37mm cyclodialysis spatula (Figure 3).Quadrant aspiration was accomplished in memory III (phaco-emulsification power maximum,70%;vacuum maximum,500ϩmm Hg;aspiration flow rate,35cc/minute).The aspiration process was kept posterior to the iris plane within the capsular bag as much as possible to protect thecorneal endothelium from damage from fragment impact and abrasion (Figures 4to 6).Sodium hyaluronate 3.0%–chon-droitin sulfate 4.0%(Viscoat )was usually injected into the anterior chamber before quadrant aspiration when the NC was greater than 4.5.In some cases,Viscoat was reinjected before aspiration of the fourth quadrant because of the ten-dency of the capsular bag to flatten after the third quadrant had been removed,which forces the remaining process ante-rior to the iris plane.In some eyes,soft quadrants or the last fragment of the fourth firm quadrant were removed using reduced vacuum (maximum 300mm Hg),maximumpowerFigure 2.(Davison)After initial grooving is completed,a secondrotation of the nucleus allows for improved visualization while deeper grooving progresses in hardnuclei.Figure 3.(Davison)Nuclear cracking is created from the peripherytoward the center with a cross action of the phacoemulsi fication tip and the cyclodialysisspatula.Figure 4.(Davison)The 45-degree phacoemulsi fication tip isturned sideways with its aperture facing the interior wall of the first nuclear quadrant.Low levels of emulsi fication energy are used to engage and impale the central portion of thequadrant.Figure 5.(Davison)A low level of ultrasonic energy and a higherlevel of vacuum allow the tip to adhere to the softer edge of the quadrant and drag it centrally.J CATARACT REFRACT SURG —VOL 29,JANUARY 2003140(50%),and a reduced aspiration flow rate (25cc/minute)(Figures 7and 8).Polynomial best-fit lines were derived by regression anal-ysis among the 4LOCS III characteristics and the 3phaco-emulsification observations.ResultsThe mean machine-measured phacoemulsification time increased as the NO and NC grades increased (Table 1).As determined by the best-fit lines and their coefficients of determination (R 2),there was an expo-nential relationship between NO and machine-mea-sured phacoemulsification time (R 2ϭ0.40).A trend existed between NO and the mean power (R 2ϭ0.15)and the amount of BSS used (R 2ϭ0.07)(Figure 9).A slightly stronger exponential relationship existed between NC and machine-measured phacoemulsifica-tion time (R 2ϭ0.48).A trend also existed between NC and mean power (R 2ϭ0.18)and the amount of BSS used (R 2ϭ0.08)(Figure 10).No relationships were observed between the LOCS III classes of cataract,C and P,and any intraoperative observation (Figures 11and 12).DiscussionIn the original LOCS III publication,the NO and NC scales were highly correlated with each other and the relationships between objective measures of NO,NC,and the LOCS III grade of the standard imageswereFigure 6.(Davison)The bulk of the quadrant is central while mod-erate ultrasonic energy,vacuum,and aspiration flow are used to remove the firm portions of thequadrant.Figure 7.(Davison)Aspiration can begin after an edge of the lastquadrant is lifted free of the posteriorcapsule.Figure 8.(Davison)The cyclodialysis spatula protects the poste-rior capsule as phacoemulsi fication power is applied during removal of the last quadrant.Lower levels of vacuum and aspiration flow rate help protect the posterior capsule from inadvertent aspiration.Table 1.Mean machine-measured ultrasound time(minutes).J CATARACT REFRACT SURG —VOL 29,JANUARY 2003141Figure9.(Davison)A significant relationship is seen betweenLOCS III NO and ultrasound time but not mean ultrasound power andBSS volume used.Figure10.(Davison)A significant relationship is seen betweenLOCS III NC and ultrasound time but not mean ultrasound power andBSS volume used.142J CATARACT REFRACT SURG—VOL29,JANUARY2003Figure11.(Davison)No relationship is seen between LOCS III Cand ultrasound time,mean ultrasound power,and BSS volume used.Figure12.(Davison)No relationship is seen between LOCS III Pand ultrasound time,mean ultrasound power,and BSS volume used. J CATARACT REFRACT SURG—VOL29,JANUARY2003143nearly linear.The NO was assessed independently with image analysis of optical density,and NC was assessed independently with fast spectral scanning colorimetry of each LOCS III standardized image.Highly different grades of NO and NC in the same cataract were un-likely.Similarly,the relationship between the expendi-ture of phacoemulsification energy and the LOCS III grades of NO and NC appears to be linear for LOCS III grades below approximately3.7.Above that,the rela-tionship between LOCS III grade and phacoemulsifica-tion energy expenditure seems to become exponential. Although in LOCS III NO and NC are graded sepa-rately,most clinicians are accustomed to describing nu-clear change by a single term,nuclear sclerosis.Both color change and increased light scattering are part of the pro-cess of nuclear sclerosis,and it is therefore not surprising to have found that both NO and NC are similarly pos-itively correlated with ultrasonic energy exposure.When viewing a cataractous lens with LOCS III NO and NC grades of4.0to5.0,most surgeons intu-itively anticipate increased phacoemulsification times. The nucleus is simply harder,so it will take more energy to emulsify.The LOCS III NC grade has been corre-lated with hardness of the central nucleus as measured by the resistance to a fine conical probe measured by a dynamometer.7Phacoemulsification energy recorded by cumulative delivered energy as well as by postopera-tive anterior chamber flare has been shown to be corre-lated with LOCS III NC and NO.8The surgeon in this study finds it useful to be able to accurately grade opalescence and brunescence(and the severity of C and P)to better estimate when prolonged ultrasonic time or increased ultrasonic energy is likely.It has proved advantageous to integrate LOCS III grading into routine operative planning.By doing so,the sur-geon will be better prepared to manage the more scle-rotic nucleus and his or her preoperative planning can be more patient specific.The surgeon in this study empirically formulated several recommendations for customizing a surgical plan using preoperative LOCS III grading as a part of a com-plete preoperative ophthalmic examination.These are listed below.1.A retentive viscoelastic material is recommended in cases in which the LOCS III NO or NC grade is4.0 or greater.2.If the LOCS III NO or NC grade is5.0,the capsulorhexis will be more easily visualized if indocya-nine green dye is used to stain the anterior capsule.3.If the pupil is smaller than4.5mm and the LOCS III NO or NC grade is greater than4.5,use of a pupil expansion/maintenance device should be considered.4.If zonular integrity is compromised and the LOCS III NO or NC grade is4.5or greater,a backup ciliary-sulcus-supported intraocular lens(IOL)or ante-rior chamber IOL should be available.5.Surgeons in training should learn and use LOCS III grading to enable them to select“normal”cases with nuclei of enough substance to easily manipulate yet readily emulsify.Very soft or very hard nuclei may present unnecessary challenges.6.The LOCS III is helpful and should be used in the trials of new technologies for cataract removal.For ex-ample,in one author’s experience(J.A.D.)with early AquaLase technology(Alcon Surgical),efficient removal of a nucleus with an NC grade greater than3.7was not possible.Of course,the relationships between LOCS III characteristics and phacoemulsification energy expendi-ture vary with the individual technique and equipment used.Despite this individual-specific variation,it is likely that the trends observed will be seen with other surgeons as long as a mechanical removal technique is used.Incorporating LOCS III grading into a preopera-tive regimen should not only improve surgical planning, it should also improve clinical documentation,commu-nication among providers and with third-party payers, and the accuracy of longitudinal follow-up.Most im-portant,preoperative LOCS III classification should contribute to more predictable and effective cataract surgery.References1.Chylack LT Jr,Wolfe JK,Singer DM,et al.The LensOpacities Classification System III;the Longitudinal Study of Cataract Study Group.Arch Ophthalmol1993;111:831–8362.Maraini G,Pasquini P,Tomba MC,et al.An independentevaluation of the Lens Opacities Classification System II (LOCS II);the Italian-American Cataract Study Group Ophthalmology1989;96:611–6153.Karbassi M,Khu PM,Singer DM,Chylack LT Jr.Evalu-J CATARACT REFRACT SURG—VOL29,JANUARY2003 144ation of Lens Opacities Classification System III applied at the slitlamp.Optom Vis Sci1993;70:923–928ton RD,Chylack LT Jr,Ko¨pcke W.Letters to theeditor.Ophthalmic Epidemiol1996;3:59–605.van den Berg TJTP,Coppens JC.Conversion of lens slitlamp photographs into physical light-scattering units.In-vest Ophthalmol Vis Sci1999;40:2151–21576.Davison JA.Performance comparison of the Alcon Legacy200001.1mm TurboSonics and0.9mm Aspiration By-pass System tips.J Cataract Refract Surg1999;25:1386–13917.Hu C,Zhang X,Hui Y,Chung H.[The nuclear hardnessand associated factors of age-related cataract].[Chinese] Yen Ko Tsa Chih2000;36:337–3408.Ursell PG,Spalton DJ,Tilling K.Relation between post-operative blood-aqueous barrier damage and LOCS III cataract gradings following routine phacoemulsification surgery.Br J Ophthalmol1997;81:544–547J CATARACT REFRACT SURG—VOL29,JANUARY2003145。
locsiii标准

locsiii标准LOCSIII标准是一种针对开放式控制系统(Open Control System)的国际标准,旨在促进不同厂商之间的互操作性和兼容性。
在全球范围内得到广泛应用。
一、LOCSIII标准的产生和发展随着工业自动化技术的不断发展,越来越多的企业和设备制造商开始意识到开放式控制系统的重要性。
为了满足这一需求,LOCSIII标准应运而生。
该标准最初由IEC和AISA联合发起,旨在建立一个统一的、开放的控制系统标准。
随着标准的推广和应用,越来越多的国家和企业开始采用LOCSIII标准,使其成为全球范围内广泛应用的工业自动化标准之一。
二、LOCSIII标准的内容LOCSIII标准主要包括以下内容:1.开放式控制系统的体系结构:该标准定义了开放式控制系统的基本架构,包括硬件和软件的组成、通信协议和接口等。
2.通信协议:LOCSIII标准规定了不同设备之间的通信协议,包括通信协议的层次结构、数据传输格式、通信速率等。
3.设备描述语言:该标准定义了一种通用的设备描述语言(DDL),用于描述控制系统的硬件和软件组成、功能和性能等。
DDL可以方便地被不同厂商的设备所理解和支持。
4.安全要求:LOCSIII标准还规定了控制系统安全方面的要求,包括网络安全、数据安全、设备安全等方面的要求。
三、LOCSIII标准的实践和应用LOCSIII标准在工业自动化领域得到了广泛应用,为企业和设备制造商提供了统一的、开放的控制系统标准。
通过采用LOCSIII标准,企业可以轻松实现不同设备之间的互操作和数据交换,提高了生产效率和管理水平。
同时,由于该标准得到了全球范围内的认可和支持,企业还可以方便地与国际合作伙伴进行合作和交流。
在中国,越来越多的企业和研究机构开始关注和应用LOCSIII标准。
一些国内知名企业和研究机构已经成功研发出符合LOCSIII标准的控制系统产品,并在国内得到了广泛应用。
此外,一些国内的标准组织也开始参照LOCSIII标准制定相关的行业标准和规范,进一步推动了该标准在国内的应用和发展。
iii型板式无砟轨道工效指标

iii型板式无砟轨道工效指标The III-type slab track is a modern track system widely used in high-speed railways and urban transit systems. It is known for its excellent performance in terms of efficiency and effectiveness. In this response, I will discuss the efficiency indicators of the III-type slab track from various perspectives.Firstly, the III-type slab track offers high construction efficiency. Compared to traditional ballasted track systems, the slab track requires less time and effort to install. The precast concrete slabs used in the system can be manufactured off-site, leading to faster construction on-site. This not only reduces the construction period but also minimizes disruptions to train services during construction. The efficiency in construction contributes to the overall efficiency of the track system.Secondly, the III-type slab track demonstratesexcellent maintenance efficiency. The design of the track system allows for easy access to the track components, making inspection and maintenance activities more convenient. The use of precast concrete slabs alsosimplifies the replacement of damaged or worn-out components, reducing maintenance downtime. Additionally,the slab track's resistance to deformations and settlements ensures longer maintenance intervals, further enhancing the overall maintenance efficiency.Thirdly, the III-type slab track offers highoperational efficiency. The track system's stability and durability result in reduced track irregularities, such as track geometry deviations and vertical alignments. This improves ride comfort for passengers and reduces wear and tear on rolling stock. The reduced track irregularitiesalso contribute to higher train speeds, allowing for faster and more efficient transportation. The operationalefficiency of the III-type slab track ultimately translates into improved service reliability and customer satisfaction.Furthermore, the III-type slab track demonstratesenvironmental efficiency. The use of precast concrete slabs reduces the amount of construction waste generated during installation. These slabs can also be recycled at the endof their lifespan, minimizing environmental impact. Additionally, the track system's high durability and resistance to deterioration reduce the need for frequent maintenance, resulting in lower energy consumption and carbon emissions associated with maintenance activities.The environmental efficiency of the III-type slab track aligns with sustainable development goals and promotes eco-friendly transportation infrastructure.Moreover, the III-type slab track offers economic efficiency. The reduced construction and maintenance requirements of the slab track system result in lower life-cycle costs compared to traditional ballasted track systems. The longer maintenance intervals and increased service life of the track components further contribute to cost savings. Additionally, the operational efficiency of the slab track allows for higher train speeds and increased capacity, leading to improved revenue generation. The economic efficiency of the III-type slab track makes it anattractive option for railway and transit operators seeking cost-effective solutions.Lastly, the III-type slab track demonstrates safety efficiency. The track system's stability and resistance to deformations minimize the risk of derailments and accidents. The reduced track irregularities also enhance the safety of train operations by reducing the likelihood of wheeldefects and excessive vibrations. The safety efficiency of the III-type slab track ensures the well-being of passengers and personnel, making it a reliable and secure track system.In conclusion, the III-type slab track exhibits various efficiency indicators. Its high construction efficiency, maintenance efficiency, operational efficiency, environmental efficiency, economic efficiency, and safety efficiency make it a preferred choice for modern railwayand transit systems. The III-type slab track not only improves transportation efficiency but also contributes to sustainable development and enhances the overall quality of the rail infrastructure.。
- 1、下载文档前请自行甄别文档内容的完整性,平台不提供额外的编辑、内容补充、找答案等附加服务。
- 2、"仅部分预览"的文档,不可在线预览部分如存在完整性等问题,可反馈申请退款(可完整预览的文档不适用该条件!)。
- 3、如文档侵犯您的权益,请联系客服反馈,我们会尽快为您处理(人工客服工作时间:9:00-18:30)。
Instruction and Operation ManualSystem IIILiquid to LiquidHeat ExchangerNESLAB Manual P/N 013736Rev. 06/05/97System III Liquid to Liquid Heat ExchangerInstruction and Operation ManualTable of ContentsPREFACECompliance (3)Unpacking (3)Warranty (3)After-sale Support (3)SECTION ISafetyWarnings (4)SECTION IIGeneral InformationDescription (5)Specifications (5)SECTION IIIInstallationSite (7)Facility Water Requirements (7)Electrical Requirements (8)Voltage Selection (8)Plumbing Requirements (8)Fluids (9)Water Quality Standards and Recommendations (9)Filling Requirements (11)Automatic Refill Device (Optional) (11)SECTION IVOperationStart Up (12)Temperature Adjustment (12)Flow Control (13)Monitors (13)Fault Interlock Contact (13)Fault Response Modes (14)Pump Motor Overload Protector (Optional) (14)SECTION VMaintenance& ServiceService Contracts (15)Pump Strainer (15)Facility Water Strainer (15)Algae (16)Configuration (16)Voltage Selection (16)Fault Selection (16)Pressure Relief Valve (17)Fuses (17)Phase Rotation (17)SECTION VITroubleshootingChecklist (18)Service Assistance (19)Parts List (19)SECTION VIIDiagramsFlow Diagram (20)Wiring Diagram 3Ø Units (21)Wiring Diagram 1Ø Units (21)Front View (22)Rear View (22)SECTION VIIIWarranty (23)PrefaceComplianceProducts tested and found to be in compliance with the requirements definedin the EMC standards defined by 89/336/EEC as well as Low Voltage Direc-tive (LVD) 73/23/EEC can be identified by the CE label on the rear of the unit.The testing has demonstrated compliance with the following directives:LVD, 73/23/EEC Complies with UL 3101-1:93EMC, 89/336/EEC EN 55011, Class A VerificationEN 50082-1:1992IEC 1000-4-2:1995IEC 1000-4-3:1994IEC 1000-4-4:1995For any additional information refer to the Letter of Compliance that shippedwith the unit (Declaration of Conformity).UnpackingRetain all cartons and packing material until the unit is operated and found tobe in good condition. If the unit shows external or internal damage, or doesnot operate properly, contact the transportation company and file a damageclaim. Under ICC regulations, this is your responsibility.WarrantyUnits have a warranty against defective parts and workmanship for one fullyear from date of shipment. See back page for more details.After-sale SupportNESLAB is committed to customer service both during and after the sale. Ifyou have questions concerning the operation of your unit, contact our SalesDepartment. If your unit fails to operate properly, or if you have questionsconcerning spare parts or Service Contracts, contact our ServiceDepartment. Before calling, please obtain the following information from theunit's serial number label:- BOM number________________________- Serial number_______________________Section I SafetyWarningsMake sure you read and understand all instructions and safety precautionslisted in this manual before installing or operating your unit. If you have anyquestions concerning the operation of your unit or the information in thismanual, contact our Sales Department.Performance of installation, operation, or maintenance proceduresother than those described in this manual may result in a hazardoussituation and may void the manufacturer's warranty.Observe all warning labels.Never remove warning labels.Never operate damaged or leaking equipment.Always turn off the unit and disconnect the line cord from the powersource before performing any service or maintenance procedures, orbefore moving the unit.Always empty the reservoir before moving the unit.Never operate equipment with damaged line cords.Never operate without fluid.Refer service and repairs to a qualified technician.In addition to the safety warnings listed above, warnings are postedthroughout the manual. These warnings are designated by an exclamationmark inside an equilateral triangle with text highlighted in bold print. Readand follow these important instructions. Failure to observe these instructionscan result in permanent damage to the unit, significant property damage, orpersonal injury or death.Section II General InformationDescriptionThe System III Liquid to Liquid Heat Exchanger is designed to remove heatfrom water-cooled instruments.The unit consists of a heat exchanger, recirculation pump, PVC reservoir,and an analog controller.SpecificationsTemperature RangeTemperature StabilityCooling Capacity1A B CA= 6gpm pump flowB= 10 gpm pump flowC= 12gpm pump flow510152025Facility Water Flow GPM1.Cooling capacity is based in a 10°C difference between the temperature of the coolingwater supply and the cooling fluid flowing from the System III to the instrument beingcooled (see Section III, Facility Water Requirements). Pressure drop obtained with theSystem III modulating valve fully open.Pump CapacityFlow (gallons/minute) Reservoir Volume2GallonsLitersDimensions3(H x W x D)InchesCentimetersShipping Weight4PoundsKilograms1.254.720¾ x 173/8 x 2752.7 x 44.1 x 68.620693.45101520A2. Larger volume reservoirs are available.3. Large volume units measure 32½ x 23 x 27 (82.5 x 58.4 x 68.6).4. Large volume units weigh approximately 355 pounds (161 kilograms).DECBFA=TU-3, 50HzB=TU-3, 60HzC=TU-7, 50HzD=TU-7, 60HzE=CP-55, 60HzF=CP-55, 50HZSection III InstallationSiteThe unit should be located in a laboratory or clean industrial environmentwith easy access to a facility cooling water supply and a drain. Never placethe unit in a location where excessive heat, moisture, or corrosive materialsare present.Refer to the pump label on the rear of the unit to identify the specific type ofpump in your unit. Units with a TU-7, TU-8 or TU-9 pump are equipped witha pump motor fan. The fan is used to cool the pump motor and prevent themotor from overheating. Air is drawn through the front of the unit and isdischarged through the rear of the unit. A minimum clearance of 6 inches(0.15 meters) at the front and rear of the unit is necessary for ventilation. Facility WaterRequirementsRefer to the Cooling Capacity chart in Section II, Specifications. The flowrate of the cooling water supply must meet or exceed these requirements forthe unit to operate at its full rated capacity. If the cooling water does notmeet these standards, the cooling capacity will be derated. The chart isbased on a difference between the temperature of the cooling water supply(House Water) and the cooling fluid flowing from the System III to theinstrument being cooled.As the heat load increases, the required flow rate of the cooling water supplyincreases. For example, on a System III with a 6 gpm pump flow, if the heatload is 12 kilowatts, approximately 3 gpm of cooling water flow is required toremove the heat. However, if the heat load is increased to 36 kilowatts, about8 gpm of cooling water flow is required.The flow meter on the front of the unit does not measure the flow rate of thecooling water supply. The flow meter measures the flow rate of the coolingfluid returning to the instrument being cooled.ElectricalRequirementsRefer to the serial number label on the rear of the unit for the specificelectrical requirements of your unit.Ensure the voltage of the power source meets the specified voltage, ±10%.The unit construction provides extra protection against the risk ofelectric shock by grounding appropriate metal parts. The extra protec-tion may not function unless the power cord is connected to a properlygrounded outlet. It is the user's responsibility to assure a proper groundconnection is provided.Voltage SelectionIf the unit is to be operated from a 220 to 240V source, a voltage rangeselector switch inside the unit must be reset. See Service section forinstructions on changing the voltage selector.PlumbingRequirementsBefore installing the unit to an instrument that previously used tap water as acooling fluid, flush the instrument several times to remove any rust or scalethat has built up. The manufacturer of the instrument should be able torecommend a cleaning fluid for their equipment.The plumbing connections are located on the rear of the unit and are labelledFACILITY WATER and RECIRCULATING CLEAN FLUID. The top fittingsare outlets and the bottom fittings are inlets.These connections are 1 inch FPT.A basket strainer is supplied with the unit to protect the heat exchanger frombecoming clogged by dirty cooling water. Install this strainer on theFACILITY WATER inlet. A clogged strainer can adversely affect coolingcapacity. See Section V, Facility Water Strainer for cleaning instructions.Connect the FACILITY WATER connections to the cooling water supply andthe drain.Connect the RECIRCULATING CLEAN FLUID connections to the instrumentbeing cooled.Flexible tubing, if used, should be of heavy wall or reinforced construction.All tubing should be rated to withstand 80 psi at +40°C. Make sure all tubingconnections are securely clamped. Avoid running tubing near radiators, hotwater pipes, etc. If substantial lengths of tubing are necessary, insulationmay be required to prevent the loss of cooling capacity.Tubing and insulation are available from NESLAB. Contact our SalesDepartment for more information (see Preface, After-sale Support).It is important to keep the distance between the unit and the instrumentbeing cooled as short as possible, and to use the largest diameter tubingpractical. Tubing should be straight and without bends. If reductions mustbe made, they should be made at the inlet and outlet of the instrument beingcooled, not at the unit.If substantial lengths of cooling lines are required, they should be pre-filledwith cooling fluid before connecting them to the unit.FluidsRefer to the Water Quality and Recommendations section.Tap water is the recommended cooling fluid.Water Quality Standardsand RecommendationsPermissible(PPM)Desirable(PPM)Microbiologicals(algae,bacteria,fungi)00Inorganic ChemicalsCalcium<400.6Chloride250<25Copper 1.3 1.0Iron0.3<0.1Lead0.0150Magnesium<12 0.1Manganese 0.05<0.03Nitrates\Nitrites10 as N 0Potassium<20 0.3Silicate25<1.0Sodium<20 0.3Sulfate250 <50Hardness17<0.05Total Dissolved Solids 5010Other ParameterspH 6.5-8.57-8Resistivity0.01*0.05-0.1** Megohm-Cm (Compensated at 25C)Unfavorably high total ionized solids (TIS) can accelerate the rate of galvanic corrosion. These contaminants can function as electrolytes which increase the potential for galvanic cell corrosion and lead to localized corrosion such as pitting which can be observed at the studs and on the outside surface of cooling coils. Eventually, the pitting will become so extensive that the coil will leak refrigerant into the water reservoir.As an example, raw water in the United States averages 171 ppm (as NaCl).The recommended level for use in a water system is between 0.5 to 5.0 ppm (as NaCl).Recommendation: Initially fill the tank with distilled/deionized water. Do not use untreated tap water as the total ionized solids level may be too high.Maintain this water quality at a resistivity of between 1 to 10 megohm-cm (compensated at 25°C) by using a purification system. Although the initial fill may be as high as 10 megohm-cm (compensated at 25°C), the desired level for long time usage is 1 to 3 megohm-cm (compensated at 25°C).The above two recommendations will reduce the electrolytic potential of the water and prevent or reduce the galvanic corrosion observed.R e s i s t i v i t y (m e g o h m -c m @ 25°C )Not Recommended, Increasingly Corrosive Operations with Stainless Steel Systems Operations with Mixed MetalsCopper/Brass/Stainless Steel CONSULT MATERIALS ENGINEER102030405060708018.3015.0010.003.001.000.100.05Water Quality ConsiderationsTemperature °CFillingRequirementsRemove the reservoir cover. Fill the reservoir with clean cooling fluid towithin 1 inch of the top of the reservoir. Have extra cooling fluid on hand andfollow the steps described in Section IV, Start Up.Automatic RefillDevice (Optional)The automatic refill device maintains the correct level of cooling fluid in thereservoir. The device consists of a float switch in the reservoir and asolenoid valve at the rear of the unit. If the cooling fluid level falls, the floatswitch will drop, opening the solenoid valve and allowing make-up fluid to fillthe reservoir. Once the cooling fluid reaches the proper level, the floatswitch will rise and the solenoid valve will close.Connect the 3/8 inch OD stainless steel barbed fitting on the solenoid valveto the make-up fluid source using 5/16 or 3/8 inch ID flexible tubing.Tubing is available from NESLAB. Contact our Sales Department for moreinformation (see Preface, After-sale Support).Section IV OperationStart UpBefore starting the unit, double check all electrical and plumbing connectionsand make sure the circulating system (the System III, the instrument beingcooled, and the tubing that connects them) has been properly filled withcooling fluid.Turn the RECIRCULATING FLOW CONTROL to “0”. Press the STARTbutton. The pump will start.The low fluid level monitor in the reservoir prevents the unit from operating ifthe fluid level in the reservoir is below the safe operating level. By slightly,and/or intermittently opening the RECIRCULATING FLOW CONTROL(toward “+”) and using extra cooling fluid to keep the reservoir topped off, thesystem can be filled without repeated tripping of the low fluid level monitor.If the unit shuts down, top off the reservoir and restart it. When the systemis full, the reservoir level will no longer drop when the RECIRCULATINGFLOW CONTROL valve is opened (toward “+”).TemperatureAdjustmentA control valve, located in the FACILITY WATER inlet line, regulates the flowrate of the cooling water supply as it enters the unit. The valve regulates theflow rate based on the heat load. Flow through the unit stops automaticallywhen the unit is shut off.Turn the TEMPERATURE CONTROL knob on the control panel to desiredoperating temperature. The temperature control system actuates a controlvalve in the FACILITY WATER line. The control valve adjusts the flow of thecooling water supply to produce the desired operating temperature.When selecting an operating temperature, remember that the lowest achiev-able temperature is a function of the available flow rate, the temperature ofthe cooling water supply and the heat load.The amber IDLE and green COOL lights indicate the control valve’s status.When the temperature control valve is wide open (for maximum cooling), theCOOL light is on steady. When the control valve is closed, the IDLE light ison. As the control valve moves between these extremes, the two lights flashwith varying on-time to indicate the approximate position of the control valve.Flow ControlThe RECIRCULATING FLOW CONTROL handle is connected to a three-way valve that controls the flow of the cooling fluid to the instrument beingcooled. The handle is located on the front of the unit.When the handle is in the “+” position, the valve is open and all availablecooling fluid is supplied to the instrument being cooled. When the handle isin the “0” position, the valve is closed and no cooling fluid is supplied to theinstrument being cooled. When the handle is between these two positions,the flow rate of the cooling fluid is between full flow and no flow. Use theflow meter to adjust the desired flow rate.The gauge next to the flow control handle indicates the operating pressure.MonitorsThe unit is equipped with the following monitors:Low Fluid LevelHigh TemperatureA fault condition will cause the unit to be shut down immediately. The faultmust be identified and corrected before the unit can be restarted.Low Fluid Level MonitorThe low fluid level monitor is connected to a float switch in the reservoir. Alow fluid level fault occurs when the cooling fluid in the reservoir drops belowthe operating level.High Temperature MonitorThe high temperature monitor is connected to a sensor that monitors thecooling fluid temperature as it exits the heat exchanger. The monitorsprotect the heat exchanger from exposure to excessively hot cooling fluid. Atemperature fault occurs when the cooling fluid temperature exceeds the settemperature limit.Set the temperature limit using the HIGH TEMPERATURE LIMIT knob onthe control panel.Fault InterlockContactA set of contacts is connected to a receptacle on the control panel. Thecontacts are rated 15A/240V. This is not a power inlet or outlet. Thereceptacle is isolated from the circuitry. Its ground pin is connected to thechassis. The contacts are closed during normal operation and open whenthe unit is turned off or when a fault is detected.Fault ResponseModesIn the event of a low fluid level or high temperature fault, two modes ofresponse to a fault are possible: SHUTOFF and SIGNAL ONLY.In the SHUTOFF mode, if either fault occurs, the fault interlock contacts willopen, the FAULT light will light and the unit will shut down.In the SIGNAL ONLY mode, the fault interlock contacts will open, the FAULTlight will light, but the unit will continue to operate. This mode is available forcustomers who prefer to accept the risk of damage to the System III in orderto continue to provide all available cooling fluid to the instrument beingcooled in the event of a failure.The unit is shipped from the factory with the SHUTOFF mode selected. Themode selector switch is inside the unit to prevent tampering or inadvertentoperation. Refer to Section V, Fault Selection for instructions on changingthe fault response mode.Pump MotorOverload Protector(optional)Three phase units with three phase pump motors have a pump motoroverload protector. These units can be identified as having a MOL light nextto the FAULT light on the control panel.The overload protector prevents the pump motor from exposure toexcessively high current. If an overload fault occurs, due, for example, to aheavy work load, the MOL light will light and the unit will shut down. Theoverload protector will automatically reset after about two minutes. The unitmust be manually restarted.Section V Maintenance & ServiceFor personal safety and equipment reliability, the following procedureshould only be performed by a competent technician. Contact ourService Department for assistance (see Preface, After-sale Support). Service ContractsNESLAB offers on-site Service Contracts that are designed to provideextended life and minimal down-time for your unit. For more information,contact our Service Department (see Preface, After-sale Support).Pump StrainerA wire mesh pump strainer is located at the bottom of the reservoir. If debrisis drawn into the reservoir, the strainer will prevent the material from beingsucked into the pump and damaging the pump vanes.After initial installation, the strainer may become clogged with debris andscale within the first week. Therefore, the strainer must be cleaned after thefirst week of installation. After this first cleaning, the frequency of cleaningdepends on the purity of the cooling water. We recommend a visual inspec-tion of the reservoir be made monthly after the initial cleaning. After severalmonths, the frequency of cleaning will be established.If the strainer is visibly clogged, cleaning is required.Disconnect the power cord from the power source and drain the reservoirbefore cleaning the strainer.Remove the strainer by unscrewing it.Clean the strainer by rinsing it with water.Refer to Section III, Filling Requirements for instructions on replacing thecooling fluid.Facility WaterStrainerThe facility water strainer is the user-installed basket strainer on theFACILITY WATER inlet. NOTE: The strainer is designed to be used only withwater. Clean the strainer when it becomes visibly clogged or dirty.Disconnect the power cord from the power source and turn off the facilitycooling water.Place a container under the strainer to collect any water that spills out of thebasket when it is removed.Unscrew the clear plastic basket. Remove the screen and rinse it with water.Replace the screen and the basket.AlgaeTo restrict the growth of algae in the reservoir, it is recommended that thereservoir cover be kept in place and that all circulation lines be opaque. Thiswill eliminate the entrance of light which is required for the growth of mostcommon algae.NESLAB recommends the use of Chloramine-T, one gram per gallon.ConfigurationThe unit top is secured to the cabinet by four ball stud retainers; one at eachcorner. Remove cabinet top by prying upward gently (cover pops off) inorder to perform the following adjustments.In some cases, the side access panels may need to be removed. Theaccess panels are secured using screws installed through the bottom of thecabinet. NOTE: Some models have a one piece cover rather than separatetop and side panels. This type of cover is secured by five screws on each sideof the case.Voltage SelectionRemove the top cover from the cabinet.The VOLTAGE SELECT toggle switch is located on the right side of thecontrol box. Two ranges are available: 200-208V and 220-240V. Set theswitch for the appropriate range.Replace the top cover.Fault SelectionRemove the top cover from the cabinet.See Section IV, Fault Response Modes for a discussion of these options.Locate the SHUTOFF/SIGNAL ONLY toggle switch on the right side of thecontrol box. Set the switch for the desired mode.Replace the top cover.Pressure ReliefValveA pressure relief valve is located on the pump discharge line. The reliefvalve establishes the maximum operating pressure of the unit. If thepressure of the fluid leaving the pump exceeds the valve setting, the reliefvalve will bypass the fluid within the unit to relieve to the pressure. The reliefvalve does not determine the actual operating pressure; the actual operatingpressure is determined by the flow control valve setting and pressure dropthrough the instrument being cooled.If adjustment is necessary, consult our Service Department for assistance(see Preface, After-sale Support).FusesRefer to the serial number label on the rear of the unit for the specificelectrical requirements of your unit. Replacement fuses are 3/4 amp, timedelay fuses. Do not replace with an alternate amperage.Single Phase UnitsRemove the top cover from the cabinet.The fuses are located on the right side of the control box.Three Phase UnitsRemove the top cover, the right access panel and the control box cover.The fuses are located inside the control box.Phase RotationThree phase units with three phase pump motors are equipped with a phaserotation interlock. These units can be identified as having a PHASE lightnext to the FAULT light on the control panel.This interlock prevents the unit from starting if the phase rotation is wrong.If the phasing is wrong, the PHASE light will light and the unit will not start.Unplug the unit. Reverse any two power cord wires in the power cord plug.Never remove the green ground wire.Plug in the unit. The PHASE light should be off and the unit should start.Section VI TroubleshootingChecklistUnit does not start, FAULT light does not come on when STARTbutton is pushed.- Check the voltage of the power source. Refer to the serial number on therear of the unit for the specific electrical requirements of your unit. Makesure the voltage of the power source meets the specified voltage, ±10%.- Check the fuses (see Section V, Fuses).When START switch is pushed, unit does not run, FAULT light comeson (SHUTOFF mode)- Check fluid level in the reservoir. The low fluid level monitor prevents theunit from starting if the fluid level is below the safe operating level.- Make sure the TEMPERATURE CONTROL setting is less than the HIGHTEMPERATURE LIMIT setting.Unit runs, but FAULT light is on (SIGNAL ONLY mode)- Check fluid level in the reservoir. The low fluid level monitor indicates afault if the fluid level is below the safe operating level.- Make sure the TEMPERATURE CONTROL setting is less than the HIGHTEMPERATURE LIMIT setting.Unit continues to run for a short periods and then stops- Check fluid level in the reservoir. If low, check the system for leaks.- Make sure the heat load is not greater than the cooling capacity (see.Section II, Cooling Capacity).- Make sure the cooling water supply meets the requirements outlined inSection III, Facility Water Requirements.- Possible power interruption has occurred causing “latch” relay to unlatch.Attempt to restart.- Ensure proper voltage (see Section III, Voltage Selection).Green light always on, temperature is not dropping- Make sure the heat load is not greater than the cooling capacity (see.Section II, Specifications).- Make sure the cooling water supply meets the requirements outlined inSection III, Facility Water Requirements.- Clean the pump and facility water strainersAmber light always on, temperature is not rising- Little, to no, heat load exists in instrument being cooled.Poor Temperature StabilityThe System III is designed to maximize heat removal with minimal facilitycooling water requirements. Under conditions of excessive cooling capacity,instability may result. The condition may be aggravated by :High temperature setpointLow facility water temperatureSmall heat loadHigh facility water pressureThe situation can be remedied by limiting the available facility cooling water.Facility water pressure can be reduced with a pressure regulator before theSystem III. However, excessive restriction of facility water will reduce theSystem III's capacity.Service AssistanceIf, after following these troubleshooting steps, your units fails to operateproperly, contact our Service Department for assistance (see Preface, After-sale Support). Before calling please obtain the following information:BOM numberSerial numberVoltage of unitVoltage of power sourceTemperature at which the problem occursTemperature, pressure and flow rate of cooling water supplyParts ListOur Service Department can provide you with a complete list of spare partsfor your unit (see Preface, After-sale Support). Before calling, pleaseobtain the following information:BOM numberSerial number。