螺纹切削循环G82
螺纹切削循指令G82

教学内容教学备注板书画略图<新课讲授>一、数控切削螺纹的程序指令:直螺纹切削循环G82 X_ Z_ R_ E_ I_ C_ P_ F_在有退刀槽的的工件中指令格式简化为:G82 X_ Z_ I_ F_参数说明:X、Z:螺纹终点坐标F:螺纹导程,即主轴转一圈,刀具相对于工件的进给值,故螺纹切削时转速不宜过高。
I:螺纹起点与终点半径查二、 G82走刀轨迹讲解格式其中着重XZ坐标字F和G01、G02等指令中X ZF的不同用时10分钟讲解和普车加工步骤一致讲解由于刀具刀尖的形状和外圆刀具的不同所引起。
教学内容教学备注做重点说明.板书板书注:在数控车床上车螺纹时,沿螺距方向的,向进给应和车床主轴的旋转保持严格的速比关系,考虑到刀具从停止状态到达指定的进给速度或从指定的进给速度降为零,驱动系统必有一个过渡过程,因此沿轴向进给的加工路线长度,除保证螺纹长度外,还应增加刀具导入距离δ和导出距离δ’,δ和δ’的数值与车床拖动系统的动态特性、螺纹的螺距和精度有关。
一般δ为2-5mm,对大螺距和高精度的螺纹取大值;δ’一般为退刀槽宽度的一半左右,取1-3mm左右。
若螺纹收尾处没有退刀槽时,收尾处的形状与数控系统有关,一般按45°退刀收尾。
三、螺纹的切削方法G82指令加工螺纹,属于直进刀方式。
直进刀方式加工时,车刀的左右两侧刃都参加切削,存在着排屑不畅,散热不好,受力集中等问题。
切削深度越深,切削阻力越大,故一般要求分次进给加工。
四、主轴转速的确定n≤1200/P-K 式中:P:是螺纹的螺距(mm);K:是保险系数,一般取为80用时6分钟吃刀深度递减是因为刀具刀尖形状决定。
用时4分钟教学内容教学备注结合书本讲解。
五、切削次数与背吃刀量六、切削螺纹的尺寸计算:大径 d=D(公称直径)牙高 H=0.65P中经 d2=D2=d-0.65P小径 d1=D1=d-1.3P<例题讲解> 讲解查表方法大概用时10分钟用时8分钟教学内容要求大家按板书<作业>时完成作业用时2分钟余下时间要求学生完成作业及巩固本堂课所学内容。
华中数控车床循环指令

格式: G80 X(U)__Z(W)__F__ ; 说明:
X、Z:绝对值编程时,为切削终点 C在工件坐标系下的坐标; 增量值编程时,为切削终点 C相对于循环起点 A 的有向 距离,图形中用 U、W表示,其符号由轨迹 1 和 2 的方 向确定。
Z:绝对值编程时,为孔底终点在工件坐标系下的坐标; 增 量值编程时 ,为孔底终点 相对于循环 起点的有向距 离,图
形中用 W表示。 e:转孔每进一刀的退刀量,只能为正值; △K:每次进刀的深度,只能为正值;
华中数控车床循环指令
F:进给速度 ;
说明 : G74指令在 HNC-21 7.11 版以后及 HNC-18 4.03 版以后改动为可以实
华中数控车床循环指令
X:绝对值编程时,为槽底终点在工件坐标系下的坐标;
增量值编程时,为槽底终点相对于循环起点的有向距离,用 Z:绝对值编程时,为槽宽的终点在工件坐标系下的坐标;
U 表示。
增量值编程时,为槽的宽度(没有考虑刀具宽度),图形中用 W表示。
e:为 0 或不填; △K:每次进刀的深度,只能为正值;
该指令执行如图所示 A→B→C→D→A的轨迹动作。
圆锥端面 切削循环 格式: G81 X(U)__Z(W)__ K__F__ ; 说明: X、Z:绝对值编程时,为切削终点 C在工件坐标系下的坐标; 增量值编程时,为切削终点 C相对于循环起点 A 的有向 距离,图形中用 U、W表示。 K:为切削起点 B相对于切削终点 C的 Z 向有向距离。 该指令执行如图所示 A→B→C→D→A的轨迹动作。
格式: G82X(U)__Z(W)__R__E__C__P__F/J__Q__
说明:
一般钻孔循环G81与锪孔循环G82
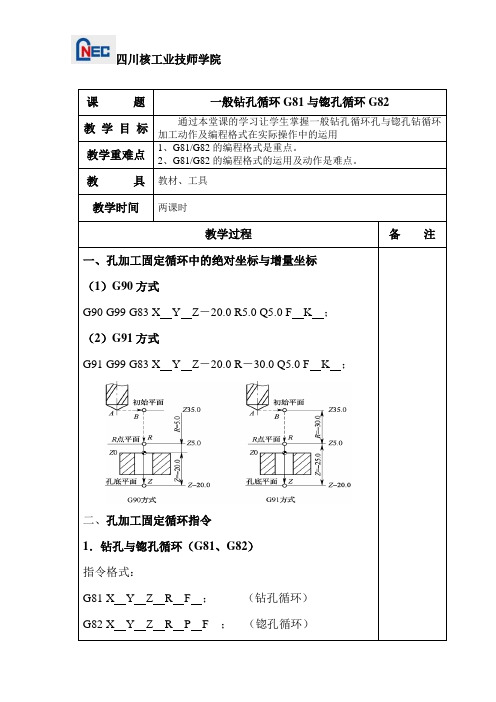
G80 G49 M09;(取消固定循环,取消长度补偿)
G91 G28 Z0;
M30;
课后反思
作业布置
1、绘制G81/G82指令的动作简图?
2、利用G81/G82编写教材P92图3---7的加工程序。
3、程序范例
例加工如图所示孔,试用G81或G82指令及G90方式进行编程。
O0002;
G17G49G40 G80 G21;(程序初始化)
G91 G28 Z0;
T01
M06;(换1号刀,φ9mm钻头)
G90 G00 G54X0 Y0M03 S1200;(G17平面快速定位)
G43 Z20.0 H01 M08;(Z向快速定位到初始平面)
二、孔加工固定循环指令
1.钻孔与锪孔循环(G81、G82)
指令格式:
G81 XYZRF;(钻孔循环)
G82 XYZRPF;(锪孔循环)
2、动作示意图
动作说明:
G81指令用于正常的钻孔,切削进给执行到孔底,然后刀具从孔底快速移动退回。
G82动作类似于G81,只是在孔底增加了进给后的暂停动作。在盲孔加工中可减小孔底表面粗糙度。常用于锪孔或台阶孔的加工。
反循环回转钻孔原理正循环回转钻孔原理正反循环钻孔反循环钻孔灌注桩正反循环钻孔灌注桩正循环钻孔反循环回转钻孔钻孔灌注桩正循环正循环回转钻孔钻孔灌注桩
课题
一般钻孔循环G81与锪孔循环G82
教学目标
通过本堂课的学习让学生掌握一般钻孔循环孔与锪孔钻循环加工动作及编程格式在实际操作中的运用
教学重难点
1、G81/G82的编程格式是重点。
G99 G81 X25.0 Y0Z-25.0 R5.0 F80;(加工两个孔)
校本华中系统g71g72g73g32g82的编程介绍
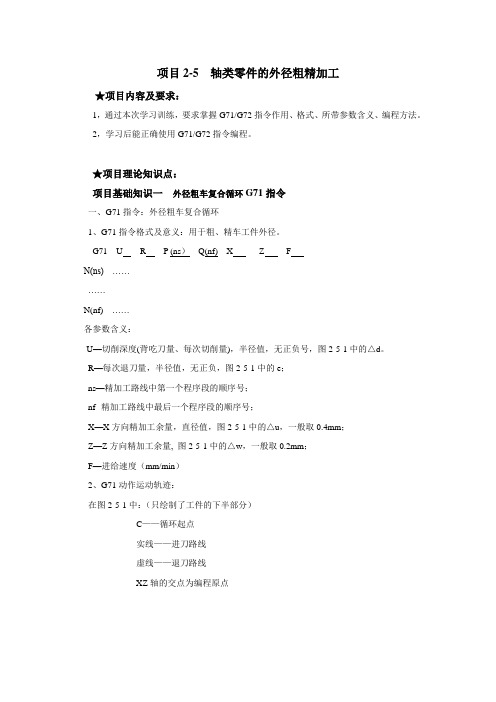
项目2-5 轴类零件的外径粗精加工★项目内容及要求:1,通过本次学习训练,要求掌握G71/G72指令作用、格式、所带参数含义、编程方法。
2,学习后能正确使用G71/G72指令编程。
★项目理论知识点:项目基础知识一外径粗车复合循环G71指令一、G71指令:外径粗车复合循环1、G71指令格式及意义:用于粗、精车工件外径。
G71 U R P (ns)Q(nf) X Z FN(ns) …………N(nf) ……各参数含义:U—切削深度(背吃刀量、每次切削量),半径值,无正负号,图2-5-1中的△d。
R—每次退刀量,半径值,无正负,图2-5-1中的e;ns—精加工路线中第一个程序段的顺序号;nf--精加工路线中最后一个程序段的顺序号;X—X方向精加工余量,直径值,图2-5-1中的△u,一般取0.4mm;Z—Z方向精加工余量, 图2-5-1中的△w,一般取0.2mm;F—进给速度(mm/min)2、G71动作运动轨迹:在图2-5-1中:(只绘制了工件的下半部分)C——循环起点实线——进刀路线虚线——退刀路线XZ轴的交点为编程原点图2-5-13、使用G71编程时的说明:(1)应用G71前必须设一循环起点,图图2-5-1中的C点。
(2)G71程序段本身不进行精加工,粗加工是按后续程序段ns~nf给定的精加工编程轨迹A→A′→B→B′,沿平行于Z轴方向进行。
(3)G71程序段不能省略除F、S、T以外的地址符。
G71程序段中的F、S、T只在循环时有效,精加工时处于ns到nf程序段之间的F、S、T有效。
(4)循环中的第一个程序段(即ns段)必须包含G00或G01指令,即A→A′的动作必须是直线或点定位运动,但不能有Z轴方向上的移动。
(5) ns到nf程序段中,不能包含有子程序。
(6)G71循环时可以进行刀具位置补偿,但不能进行刀尖半径补偿。
因此在G71指令前必须用G40取消原有的刀尖半径补偿。
在ns到nf程序段中可以含有G41或G42指令,对精车轨迹进行刀尖半径补偿。
G82螺纹切削循指令

3、G82指令格式
直螺纹切削循环
G82 X_ Z_ R_ E_ I_ C_ P_ F_
在有退刀槽的的工件中指令格式简化为:
G82 X_ Z_ I_ F_
参数说明: X、Z:螺纹终点坐标 F:螺纹导程,即主轴转一圈,刀具相对于工件的进 给值,故螺纹切削时转速不宜过高。 I:螺纹起点与终点半径差
G82参数含义
加工程序
O0001; T0101; N10 M03S600; N20 G00 X40.0Z2.0M08; N30 G82 X29.2Z- 52.0F1.5; N40 X28.6; N50 X28.2; N60 X28.04; N70 G00 X100.0Z50.0M09; N80 M05; N90 M30;
注:转速的确定也跟机床的刚性、刀具和工件的 材料有关。
5.3 切削次数与背吃刀量
5.4 例题讲解
毛坯尺寸φ35×65,材料45
切削次数与背吃刀量解析表
第一刀 第二刀 第三刀 第四刀
背吃刀量 0.8 0.6 0.4 0.16
坐标 X29.2 Z-52 X28.6 Z-52 X28.2 Z-52 X28.04 Z-52
( 单头螺纹p为0,可以省略,双头P为180)
F :螺纹的导程(单头螺纹为螺距)
I: 车圆柱螺纹时,可省略,车锥螺纹时为螺纹切削起点与终 点的半径之差(注意是半径差)
新课:螺纹切削循环G82
G82走刀轨迹:
加工圆柱螺纹时的走刀轨迹如右 图:(有退刀槽)
在右图中,各点的名称及取值:
5、G82指令加工螺纹
了解螺纹相关图片
内外螺纹加工原理
内外螺纹刀杆及刀片
外螺纹产品
内螺纹产品
外径螺纹车刀
数控铣床G81G82G83指令用途与区别
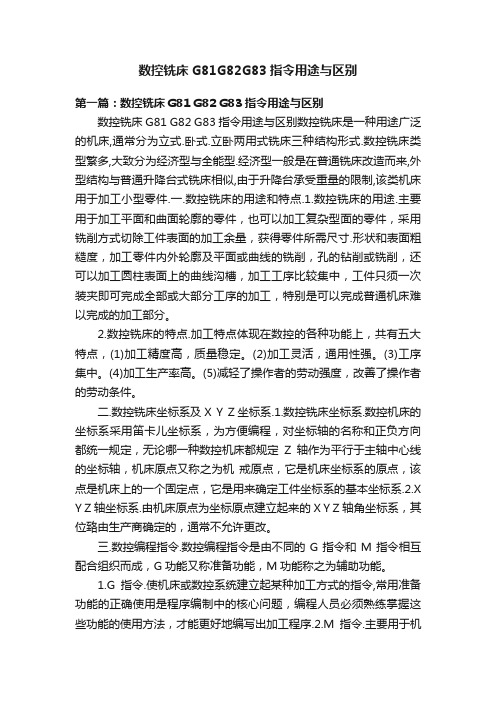
数控铣床G81G82G83指令用途与区别第一篇:数控铣床G81 G82 G83指令用途与区别数控铣床G81 G82 G83指令用途与区别数控铣床是一种用途广泛的机床,通常分为立式.卧式.立卧两用式铣床三种结构形式.数控铣床类型繁多,大致分为经济型与全能型.经济型一般是在普通铣床改造而来,外型结构与普通升降台式铣床相似,由于升降台承受重量的限制,该类机床用于加工小型零件.一.数控铣床的用途和特点.1.数控铣床的用途.主要用于加工平面和曲面轮廓的零件,也可以加工复杂型面的零件,采用铣削方式切除工件表面的加工余量,获得零件所需尺寸.形状和表面粗糙度,加工零件内外轮廓及平面或曲线的铣削,孔的钻削或铣削,还可以加工圆柱表面上的曲线沟槽,加工工序比较集中,工件只须一次装夹即可完成全部或大部分工序的加工,特别是可以完成普通机床难以完成的加工部分。
2.数控铣床的特点.加工特点体现在数控的各种功能上,共有五大特点,(1)加工精度高,质量稳定。
(2)加工灵活,通用性强。
(3)工序集中。
(4)加工生产率高。
(5)减轻了操作者的劳动强度,改善了操作者的劳动条件。
二.数控铣床坐标系及X Y Z坐标系.1.数控铣床坐标系.数控机床的坐标系采用笛卡儿坐标系,为方便编程,对坐标轴的名称和正负方向都统一规定,无论哪一种数控机床都规定Z轴作为平行于主轴中心线的坐标轴,机床原点又称之为机戒原点,它是机床坐标系的原点,该点是机床上的一个固定点,它是用来确定工件坐标系的基本坐标系.2.X Y Z轴坐标系.由机床原点为坐标原点建立起来的X Y Z轴角坐标系,其位臵由生产商确定的,通常不允许更改。
三.数控编程指令.数控编程指令是由不同的G指令和M指令相互配合组织而成,G功能又称准备功能,M功能称之为辅助功能。
1.G指令.使机床或数控系统建立起某种加工方式的指令,常用准备功能的正确使用是程序编制中的核心问题,编程人员必须熟练掌握这些功能的使用方法,才能更好地编写出加工程序.2.M指令.主要用于机床加工操作时的工艺性指令,辅助功能主要指控制机床开——关功能的一类指令,执行该类指令可以完成机床在加工操作时的辅助动作或控制状态。
螺纹车削固定循环指令G82
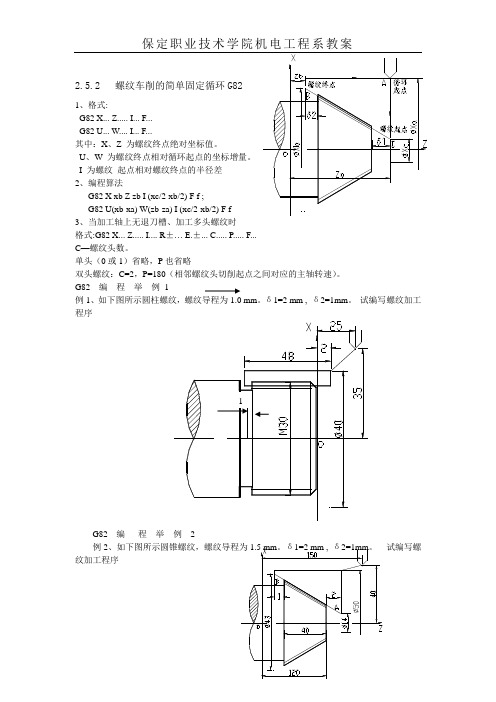
3、当加工轴上无退刀槽、加工多头螺纹时格式:G82 X... Z..... I.... R ±… E.±... C..... P..... F...C —螺纹头数。
单头(0或1)省略,P 也省略双头螺纹:C=2,P=180(相邻螺纹头切削起点之间对应的主轴转速)。
G82 编 程 举 例 1例1、如下图所示圆柱螺纹,螺纹导程为1.0 mm 。
δ1=2 mm , δ2=1mm 。
试编写螺纹加工程序G82 编 程 举 例 2例2试编写螺纹加工程序G91 g82 x-7.8 z-43.0 I-14.5 F1.5;G82 X-8.4 Z-43.0 I-14.5;G82 X-8.8 Z-43.0 I-14.5;G82 X-8.96 Z-43.0 I-14.5;2.5.3 螺纹车削复合循环指令G76G76 C(c) R(r) E(e) A(a) X(U) Z(W) I(i) K(k) U(d) V(dmin) Q(ap1) F(f) ;其中:c –精整次数(取值01~99)r –螺纹Z向退尾长度(00~99)e –螺纹X向退尾长度(00~99)a -- 牙型角(取80º,60º,55º,30º,29º,0º)通常为60ºU、W –绝对编程时为螺纹终点的坐标值;相对编程时,为螺纹终点相对于循环起点A的有向距离。
i -- 锥螺纹的起点与终点的半径差k -- 螺纹牙型高度(半径值)d -- 精加工余量f -- 螺纹导程(螺距)dmin -- 最小进给深度d -- 第一次切削深度(半径值)螺纹加工方法螺纹加工常用切削循环方式。
两种方式:直进法(G32、G82)斜进法(G76)一般应用:直进法:导程小于3mm的螺纹加工斜进法:导程大于3mm的螺纹加工(斜进法使刀具单侧刃加工减轻负载)。
UG钻孔G82的如何使用跟G81有什么区别
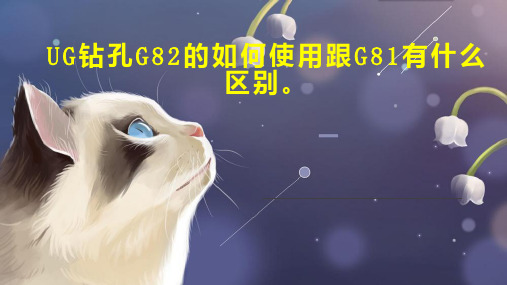
内容介绍
前几天有友在问,G82钻孔如何使用,跟G81有什么区别。 首先我们来讲一下两者的区别,G81钻孔循环,俗称一钻到底。G81比较适合打点与钻一些不太深 的孔。 G82钻孔循环,一样的一钻到底,但是它可以在孔底停留一段时间。G82主要应用在绞孔与粗镗。
方法/步骤
我们现在还面临一个问题就是如何在 后处理输出成G82,UG钻孔循环没有 单独的针对G82的循环类型。
方法/步骤
2.循环类型使用标准钻,如下图:
方法/步骤
3.指定孔,如下图:
方法/步骤
4.选择模型深度,生成刀轨,如下图:
方法/步骤
5.通过后处理,输出的是参数,如 下图:
方法/步骤
.选择秒,自己设定时间,如下图:
方法/步骤
8.再次后处理,得到G82钻孔循环, 后面多了P值,就是暂停的时间。如 下图:
谢谢观看