2 材料在单向静拉伸载荷下的力学性能-静载拉伸试验,拉伸性能指标解析
《材料性能学》课后答案

《材料性能学》课后答案《⼯程材料⼒学性能》(第⼆版)课后答案第⼀章材料单向静拉伸载荷下的⼒学性能⼀、解释下列名词滞弹性:在外加载荷作⽤下,应变落后于应⼒现象。
静⼒韧度:材料在静拉伸时单位体积材科从变形到断裂所消耗的功。
弹性极限:试样加载后再卸裁,以不出现残留的永久变形为标准,材料能够完全弹性恢复的最⾼应⼒。
⽐例极限:应⼒—应变曲线上符合线性关系的最⾼应⼒。
包申格效应:指原先经过少量塑性变形,卸载后同向加载,弹性极限(ζP)或屈服强度(ζS)增加;反向加载时弹性极限(ζP)或屈服强度(ζS)降低的现象。
解理断裂:沿⼀定的晶体学平⾯产⽣的快速穿晶断裂。
晶体学平⾯--解理⾯,⼀般是低指数,表⾯能低的晶⾯。
解理⾯:在解理断裂中具有低指数,表⾯能低的晶体学平⾯。
韧脆转变:材料⼒学性能从韧性状态转变到脆性状态的现象(冲击吸收功明显下降,断裂机理由微孔聚集型转变微穿晶断裂,断⼝特征由纤维状转变为结晶状)。
静⼒韧度:材料在静拉伸时单位体积材料从变形到断裂所消耗的功叫做静⼒韧度。
是⼀个强度与塑性的综合指标,是表⽰静载下材料强度与塑性的最佳配合。
⼆、⾦属的弹性模量主要取决于什么?为什么说它是⼀个对结构不敏感的⼒学姓能?答案:⾦属的弹性模量主要取决于⾦属键的本性和原⼦间的结合⼒,⽽材料的成分和组织对它的影响不⼤,所以说它是⼀个对组织不敏感的性能指标,这是弹性模量在性能上的主要特点。
改变材料的成分和组织会对材料的强度(如屈服强度、抗拉强度)有显著影响,但对材料的刚度影响不⼤。
三、什么是包⾟格效应,如何解释,它有什么实际意义?答案:包⾟格效应就是指原先经过变形,然后在反向加载时弹性极限或屈服强度降低的现象。
特别是弹性极限在反向加载时⼏乎下降到零,这说明在反向加载时塑性变形⽴即开始了。
包⾟格效应可以⽤位错理论解释。
第⼀,在原先加载变形时,位错源在滑移⾯上产⽣的位错遇到障碍,塞积后便产⽣了背应⼒,这背应⼒反作⽤于位错源,当背应⼒(取决于塞积时产⽣的应⼒集中)⾜够⼤时,可使位错源停⽌开动。
第2章_金属在单向静拉伸载荷下的力学性能

常见的:
低碳钢
铝合金
苏打石灰玻璃
2.3 塑性变形
塑性变形:外载荷卸去后,不能恢复的变形 塑性:材料受力,应力超过屈服点后,仍能 继续变形而不发生断裂的性质
2.3.1 塑性变形方式及特点
一、塑性变形方式
金属材料常见的塑性变形方式为滑移和孪生
• 1--- 淬火、高温回火后的高碳钢:只 有弹性形变、少量的均匀塑性形变;
• 2--- 低合金结构钢:与低碳钢的曲线 类似;
• 3--- 黄铜:弹性形变、均匀塑性形变 和不均匀塑性形变;
• 4--- 陶瓷、玻璃类材料:只有弹性变 形而没有明显的塑性形变;
• 5--- 橡胶类材料:弹性形变量很大, 高达 100% ;
滑移 最主要的变形机制;
孪生
重要的变形机制,一般发生在低温形 变或快速形变时
2.3.1 塑性变形方式及特点
1、滑移
是金属材料在切应力作用下沿滑移面和滑 移方向进行的切变过程。
滑移面:原子最密排面; 滑移方向:原子最密排方向; 滑移系:滑移面和滑移方向的组合。 滑移面×滑移方向=滑移系。 滑移系越多,材料的塑性越好。 晶体结构的影响较大,fcc>bcc>hcp
应力值为其屈服极限。)
c d
③均匀变形阶段:屈服后,欲继 续变形使试样应变增大,必须
不断增加载荷使应力超过σs,
此阶段的变形明显而均匀的,
直到曲线达到最高点σb,均匀
b
变形结束,如图中的bc段。此
a
最大应力σb称为材料的强度极 限或抗拉强度,它表示材料对
最大均匀塑性变形的抗力。
形变硬化:随塑性变形增大, 塑性变形抗力不断增加的现象。
第一章 材料在静拉伸载荷下力学性能1(弹性变形)

0.2
= P0.2 / A0
工程上根据要求高低, P、 e、 s都可以作屈服强 度使用(规定残余伸长应 力)。
2018/11/12 中原工学院 14
抗拉强度 :
b
试件断裂前所能承受的最大工程应 力,以前称为强度极限。取拉伸图上 的最大载荷,即对应于b点的载荷除以 试件的原始截面积,即得抗拉强度, 记为σ b
第一章
材料在单向静拉伸载荷 下的 力学性能
2018/11/12 中原工学院 1
单向静拉伸载荷
静载:加载速度很小(1- 10MPa/s) 大气环境中 常压 常温
2018/11/12
中原工学院
2
1.1 材料在静拉伸时的力学行为概述
1、拉伸性能:
静拉伸是材料力学性能试验中最基 本的试验方法。 通过拉伸试验可测材料的弹性模量 E、 屈服强度σs 、抗拉强度σb 、、 断裂强 度σk 、延伸率、断面收缩率等重要的 力学性能指标,统称拉伸性能,是材 料的基本力学性能。
σ
2018/11/12
b
= Pmax/A0
中原工学院 15
延伸率:
材料的塑性常用延伸率表示。测 定方法如下:拉伸试验前测定试件 的标距L0,拉伸断裂后测得标距为 Lk,然后按下式算出延伸率
LK L0 100% L0
2018/11/12 中原工学院 16
拉断后测量LK注意事项
2018/11/12
L
此处Ψ是截面收缩率
2018/11/12
中原工学院
19
断裂强度:
拉伸断裂时的真应力称为断裂强度,记为σ K 。 试验时测出断裂点的截荷PK,试件的最小截面 积AK,则 σ K = PK / AK 通常在拉伸试验中,不测定断裂强度 ,可以根 据下列经验公式估算断裂强度 σ K =σ b(1+Ψ K)
2 材料在单向静拉伸载荷下的力学性能-静载拉伸试验,拉伸性能指标
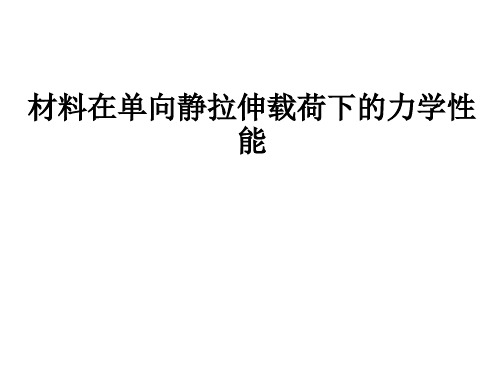
§1 拉伸力—伸长曲线和应力—应变曲线
1.1 单向拉伸试验 最常用的金属力学性能试验方法。
GB/T 228-2002 金属材料室温拉伸试验方法
§1 拉伸力-伸长曲线和应力-应变曲线
拉伸试验方法
试样长度要求:
l0 5d 0 或 l0 10d 0
试样加载速率: 10 1 / s
• 工程应力:载荷除以试件的 原始截面积。σ =F/A0 • 工程应变:伸长量除以原始 标距长度。
=Δ L/L0
• 变形过程:弹性变形→屈服 →均匀塑性变形→塑性失稳 →断裂
退火低碳钢的(条件)应力-应变曲线
§1.2 应力—应变曲线
低碳钢典型的应力-应变曲线
弹性变形阶段:曲线的起始 部分,图中的 oa 段。多数情况 下呈直线形式,符合虎克定律。 屈服阶段:超出弹性变形范 围之后,有的材料在塑性变形 初期产生明显的塑性流动。此 时,在外力不增加或增加很小 或略有降低的情况下,变形继 续产生,拉伸图上出现平台或 呈锯齿状,如图中的ab段。
与工程应力-应变曲线相比较,在弹性变 形阶段,由于试棒的伸长和截面收缩都很 小,两曲线基本重合,真实屈服应力和工 程屈服应力在数值上非常接近,但在塑性 变形阶段,两者之间出现了显著的差异。
在工程应用中,多数构件的变形量限 制在弹性变形范围内,二者的差别可 以忽略,同时工程应力、工程应变便 于测量和计算,因此,工程设计和材 料选用中一般以工程应力、工程应变 为依据,但在材料科学研究中,真应 力和真应变将具有重要的意义。
材料在单向静拉伸载荷下的力学性 能
材料在单向静拉伸载荷下的力学性能
单向静拉伸:工业上应用最广泛的金属力学性能试 验 方法之一。 特点:温度、应力状态和加载速率确定。 目的: 1) 揭示金属材料在静载荷作用下常见的 力学行为,即弹性变形、塑性变形和断裂; 2) 标定基本力学性能指标。 内容:1.1 拉伸力—伸长曲线和应力—应变曲线 1.2 弹性变形 1.3 塑性变形 1.4 金属的断裂
第一章 单向静拉伸载荷下的力学性能

2、弹性极限 、
由弹性变形过渡到弹-塑性变形时的应力。超过弹性极限,开 始发生塑性变形 σe=Fe / A0
实际意义? σp、σe的实际意义?
对于要求在服役时其应力应变关系严格维持 直线关系的构件,如测力计弹簧,是依靠 变形的应力正比于应变的关系显示载荷大 小的,则选择这类构件的材料应以材料的 比例极限为依据; 若服役条件要求构件不允许产生微量塑性变 形,则应以弹性极限选材
------------------------------(1)
位错运动时,切应变速率与可动位错密度ρm及其运 动速率之间关系
------------------------------(2)
换算成拉伸应变速率
------------------------------(3)
位错总密度ρ随拉伸应变εp增加( ρ0为塑性变形刚开 始时的总位错密度)
影响金属材料的力学性能的内在因素: 影响金属材料的力学性能的内在因素:材 料的化学成分、组织结构、冶金质量、 料的化学成分、组织结构、冶金质量、残 余应力及表面和内部缺陷等; 余应力及表面和内部缺陷等; 外因:载荷性质(静载荷、冲击载荷、 外因:载荷性质(静载荷、冲击载荷、交 变载荷)、载荷谱、应力状态( )、载荷谱 变载荷)、载荷谱、应力状态(拉、压、 弯曲、扭转、剪切、 弯曲、扭转、剪切、接触应力及各种复合 应力)、温度、环境介质等; )、温度 应力)、温度、环境介质等; 金属力学性能的物理本质及宏观变化规律 与金属在变形和断裂过程中位错的运动、 与金属在变形和断裂过程中位错的运动、 增殖和交互作用(位错之间的交互作用、 增殖和交互作用(位错之间的交互作用、 位错与点缺陷的交互作用) 位错与点缺陷的交互作用)等微观过程有 关。
断面收缩率(ψ):是拉伸试样断裂处截面的相对 收缩值,等于断裂处截面绝对收缩值(∆Ak=A0-Ak) 除以试样原始截面积(A0),也用百分数表示: ψ=( A0-Ak)/ A0 ×100% A0 Ak 试样原始截面积 试样断裂后断裂处的最小截面积
金属材料在静拉伸载荷下的力学性能
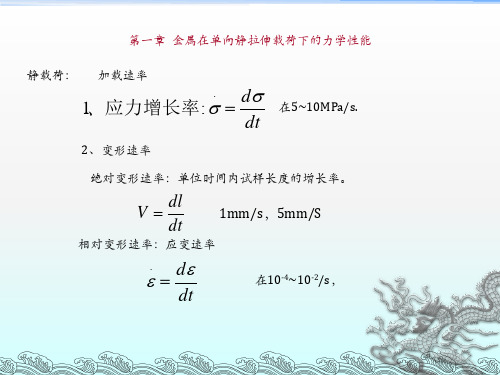
五缩颈现象
缩颈:拉伸试验时,变形集中于局部区域 的特殊现象.
• 缩颈前是均匀变形,缩 颈后是不均匀变形,即 局部变形
e p
用规定的微量塑性变形(残余伸长)所需的应力来表征。
四、弹性比功
表征金属材料吸收弹性功的能力。
弹性比能
应变比能
应力-应变曲线下弹性范围所吸收的变形功
弹性比功ae=σeεe/2
=σe2/2E
σe↑E↓
→a e ↑
理想的弹簧材料要求有高的弹性比功
Байду номын сангаас
成分与热处理对弹性极限影响大, 对弹性模量影响不大。
. ε = bρ V
开始塑性变形时,可动ρ小,要求V大
V=(τ /τ 0)m'
要求 τ大
塑性变形后
ρ ↑ 要求V小
m'小,则τ变化大,屈服明显。
BCC: m′<20, 屈服明显 FCC: m′ >100~200,屈服不明显
要↓ τ
3、屈服强度σs 表征材料对微量塑性变形的抗力。
σs:上屈服点σsu和下屈服点σsl
E
拉伸杨氏模量: E = σ /ε
切变模量G =τ/γ
G E 2(1 v)
泊松比:υ= —εX/εZ
对金属υ值约为0.33(或1/3)
广义胡克定律
1
1 E
[1
v( 2
3 )]
2
1 E
[ 2
v( 3
1)]
3
1 E
[ 3
v(1
2 )]
物理意义: 产生单位应变所需的应力
技术意义: E,G称为材料的刚度
2、多晶体塑性变形的特点 1)各晶粒变形的不同时性和不均匀性 2)各晶粒变形的相互协调性
材料在单向静拉伸载荷下的力学性能

材料在单向静拉伸载荷下的力学性能1.1拉伸试验 1.1.1 概述拉伸试验是标准拉伸试样在静态轴向拉伸力不断作用下以规定的拉伸 速度拉至断裂,并在拉伸过程中连续记录力与伸长量,从而求出其强度判 据和塑性判据的力学性能试验。
强度指标:弹性极限、屈服强度、抗拉强度 ;塑性指标:断后伸长率、断面收缩率。
1.1.2 概念应力:应力是在它所作用面积上的力, 用N/mm 2表示,在米制单位中,用千帕(kPa )或兆帕(MPa )表示。
应变:是被测试材料尺寸的变化率,它是加载后应力引起的尺寸变化。
由于应变是一个变化率,所以它没有单位拉悻前 ------ w -----原始标距(L o ):施力前的试样标距。
断后标距(L u ):试样断裂后的标距。
平行长度(L c ):试样两头部或两夹持部分 (不带头试样)之间平行部分的 长度。
断后伸长率(A ):是断后标距的残余伸长 (L U -L o )与原始标距(L o )之比的 百分(7 =(M Pa5率。
断面收缩率(Z):断裂后试样横截面积的最大缩减量(S o-S U)与原始横截面积(So)之比的百分率。
最大力(F m):试样在屈服阶段之后所能抵抗的最大力。
屈服强度:当金属材料呈现屈服现象时,在试验期间达到塑性变形发生而力不增加的应力点。
上屈服强度:试样发生屈服而力首次下降前的最高应力。
下屈服强度:在屈服期间,不计初始瞬时效应时的最低应力。
1.1.3 拉伸应力-应变曲线以低碳钢的拉伸应力一应变曲线为例。
OB —弹性阶段,BC —屈服阶段CD —强化阶段,DE —颈缩阶段试样在各阶段变化的示意图金属材料在弹性变形阶段,其应力和应变成正比例关系,符合胡克定律,即( T=E •&,其比例系数E称为弹性模量。
弹性极限d P与比例极限d e非常接近,工程实际中近似地用比例极限代替弹性极限。
屈服强度:当金属材料呈现屈服现象时,在试验期间达到塑性变形发生而力不增加的应力点,应区分上屈服强度和下屈服强度。
材料性能学期末考试

中原工学院材料与化工学院材料性能学《材控专业课后习题》第一章材料在单向拉伸时的力学性能1-1名词解释1.弹性比功:材料在弹性变形过程中吸收变形功的能力.2.包申格效应:金属材料经预先加载产生少量塑性变形,而后再同向加载,规定残余伸长应力增加,反向加载,规定残余伸长应力降低的现象.其来源于金属材料中的位错运动所受阻力的变化。
可通过热处理(再结晶退火)消除。
3.塑性:材料断裂前产生塑性变形的能力4.韧性:材料变形时吸收变形力的能力5.脆性断裂(弹性断裂):材料断裂前不发生塑性变形,而裂纹的扩展速度往往很快。
断口呈现与正应力垂直,宏观上比较齐平光亮,为放射状或结晶状。
6.韧性断裂(延性断裂或者塑性断裂):材料断裂前及断裂过程中产生明显塑性变形的断裂过程。
断口呈现暗灰色、纤维状。
7.剪切断裂:材料在切应力作用下沿滑移面分离而造成断裂.断口呈现锋利的楔形或微孔聚集型,即出现大量韧窝。
8.河流花样:解理裂缝相交处会形成台阶,呈现出形似地球上的河流状形貌9.解理台阶:解理裂纹的扩展往往是沿晶面指数相同的一族相互平行,但位于“不同高度”的晶面进行的。
不同高度的解理面存在台阶。
10.韧窝:通过孔洞形核、长大和连接而导致韧性断裂的断口1—3材料的弹性模数主要取决于什么因素?答:影响弹性模数的因素:键合方式和原子结构、晶体结构、化学成分、微观组织、温度、加载条件和负荷持续时间1—4决定金属材料屈服强度的主要因素有哪些?答:1、晶体结构:屈服是位错运动,因此单晶体理论屈服强度=临界切应力2、晶界和亚结构:晶界是位错运动的重要障碍,晶界越多,常温时材料的屈服强度增加。
晶粒越细小,亚结构越多,位错运动受阻越多,屈服强度越大。
3、溶质元素:由于溶质原子与溶剂原子直径不同,在溶质原子周围形成晶格畸变应力场,其与位错应力场相互作用,使位错运动受阻,增大屈服强度.固溶强化、柯氏气团强化、沉淀强化、时效强化、弥散强化4、第二相:弥散分布的均匀细小的第二相有利于提高屈服强度5、环境因素对屈服强度的影响1)温度的影响:温度升高,屈服强度降低,但变化趋势因不同晶格类型而异。
- 1、下载文档前请自行甄别文档内容的完整性,平台不提供额外的编辑、内容补充、找答案等附加服务。
- 2、"仅部分预览"的文档,不可在线预览部分如存在完整性等问题,可反馈申请退款(可完整预览的文档不适用该条件!)。
- 3、如文档侵犯您的权益,请联系客服反馈,我们会尽快为您处理(人工客服工作时间:9:00-18:30)。
一般采用圆形或板形二种试样。可分为三个部分,即 工作部分、过渡部分和夹持部分。 其中工作部分必须表面光滑,以保证材料表面也是单 向拉伸状态;过渡部分必须有适当的台阶和圆角,以降低 应力集中,避免该处变形和断裂;夹持部分是与试验机夹 头连接的部分,以定位试样。
§1.1 拉伸力—(绝对)伸长曲线
• 工程应力—应变曲线的作用:根据该曲线可获得 材料静拉伸条件下的力学性能指标:比例极限 σp 、 弹性极限σe 、屈服点σs 、抗拉强度σb 。可提供 给工程设计或选材应用时参考。
• 工程应力—应变曲线的局限:在拉伸过程中,试 棒的截面积和长度随着拉伸力的增大是不断变化 的,工程应力 — 应变曲线并不能反映实验过程 中的真实情况。
退火低碳钢的(条件)应力-应变曲线
b. 弹性极限
试样加载后再卸载,以不出现残留的 永久变形为标准,材料能够完全弹性 恢复的最高应力值为弹性极限,用σe 表示,超过σe时,即认为材料开始屈 服。 上述二定义并非完全相等,有的材料, 如高强度晶须,可以超出应力应变的 线性范围,发生较大的弹性变形。橡 胶材料可以超过比例极限发生较大的 变形后仍能完全恢复,而没有任何永 久变形。 工程上之所以区分它们,是因为有些 设计,如火炮筒材料,要求有高的比 退火低碳钢的(条件)应力-应变曲线 例极限,而弹簧材料则要求有高的弹 性极限。
与工程应力-应变曲线相比较,在弹性变 形阶段,由于试棒的伸长和截面收缩都很 小,两曲线基本重合,真实屈服应力和工 程屈服应力在数值上非常接近,但在塑性 变形阶段,两者之间出现了显著的差异。
在工程应用中,多数构件的变形量限 制在弹性变形范围内,二者的差别可 以忽略,同时工程应力、工程应变便 于测量和计算,因此,工程设计和材 料选用中一般以工程应力、工程应变 为依据,但在材料科学研究中,真应 力和真应变将具有重要的意义。
§1 拉伸力—伸长曲线和应力—应变曲线
1.1 单向拉伸试验 最常用的金属力学性能试验方法。
GB/T 228-2002 金属材料室温拉伸试验方法
§1 拉伸力-伸长曲线和应力-应变曲线
拉伸试验方法
试样长度要求:
l0 5d 0 或 l0 10d 0
试样加载速率: 10 1 / s
• 工程应力:载荷除以试件的 原始截面积。σ =F/A0 • 工程应变:伸长量除以原始 标距长度。
=Δ L/L0
• 变形过程:弹性变形→屈服 →均匀塑性变形→塑性失稳 →断裂
退火低碳钢的(条件)应力-应变曲线
§1.2 应力—应变曲线
低碳钢典型的应力-应变曲线
弹性变形阶段:曲线的起始 部分,图中的 oa 段。多数情况 下呈直线形式,符合虎克定律。 屈服阶段:超出弹性变形范 围之后,有的材料在塑性变形 初期产生明显的塑性流动。此 时,在外力不增加或增加很小 或略有降低的情况下,变形继 续产生,拉伸图上出现平台或 呈锯齿状,如图中的ab段。
F
A
0
F
定义:由拉伸试验机自 动记录或绘图装置,将 作用在试样上的力和所 引起的伸长自动记录绘 出的力 - 伸长曲线。记录 拉伸实验中力与伸长量 的关系曲线。
L0
6
§1.2 应力—应变曲线
应力―载荷除以试件的原始截面积即得工程应力,σ
度即得工程应变,ε
§1.4 拉伸性能指标
材料拉伸性能指标又称为力学性能指标,用
应力 -应变曲线上反映变形过程性质发生变化的
临界值表示。
力学性能指标可分为两类:反映材料对塑
性变形和断裂抗力的指标,称为材料的强度指 标;反应材料塑性变形能力的指标,称为材料的 塑性指标。
1.
a.
屈服强度指标 材料的屈服强度理解为开始塑 性变形时的应力值。但实际上 对于连续屈服的材料,屈服强 度很难作为判断材料屈服的准 则。工程上采用规定一定的残 留变形量的方法,确定屈服强 度,主要有以下三种。 比例极限 应力-应变曲线上符合线性关 系的最高应力值为比例极限, 用σp表示,超过σp时,即认为 材料开始屈服。
c. 屈服强度
以规定发生一定的残留变形为标准,如通常以0.2%的 残留变形应力作为屈服强度,用σ0.2或σys表示。 对于不连续屈服即具有明显屈服点的材料,其应力-应 变曲线上的屈服平台就是材料屈服变形的标志。
退火低碳钢的(条件)应力-应变曲线
2. 抗拉强度
材料的极限承载能力用抗拉强度表示。拉伸试验时,与最高载荷 Pb对应的应力值σb即为抗拉强度。 对于脆性材料和不形成颈缩的塑性材料,其拉伸最高载荷就是断 裂载荷,因此,其抗拉强度也代表断裂抗力。 对于形成颈缩的塑性材料,其抗拉强度代表产生最大均匀变形的 抗力,也表示材料在静拉伸条件下的极限承载能力。
材料在单向静拉伸载荷下的力学性 能
材料在单向静拉伸载荷下的力学性能
单向静拉伸:工业上应用最广泛的金属力学性能试 验 方法之一。 特点:温度、应力状态和加载速率确定。 目的: 1) 揭示金属材料在静载荷作用下常见的 力学行为,即弹性变形、塑性变形和断裂; 2) 标定基本力学性能指标。 内容:1.1 拉伸力—伸长曲线和应力—应变曲线 1.2 弹性变形 1.3 塑性变形 1.4 金属的断裂
§1.2 应力—应变曲线
低碳钢典型的应力-应变曲线
均匀塑性变形阶段:屈服后, 欲继续变形,必须不断增加载 荷,此阶段的变形是均匀的, 直到曲线达到最高点,均匀变 形结束,如图中的bc段。 形变硬化:随塑性变形增大, 变形抗力不断增加的现象。 不均匀塑性变形阶段:从试 样承受的最大应力点开始直到 断裂点为止,如图中的 cd 段。 在此阶段,随变形增大,载荷 不断下降,产生大量不均匀变 形,且集中在颈缩处,最后载 荷达到断裂载荷时,试样断裂。
退火低碳钢的(条件)应力-应变曲线
3. 实际断裂强度 拉伸断裂时的载荷除以断口处的真实截面面积所得的 应力值称为实际断裂强度Sk。 在这里采用的是试样断裂时的真实界面面积,Sk也是 真实应力,其意义是表征材料对断裂的抗力,因此有时
也称为断裂真应力。
塑性指标
塑性: 是指材料断裂前产生塑性变形的能力。 意义: 防止偶然过载造成危害; 保证机件正常运行; 有利于塑性加工和修复。