轮胎行业橡胶工艺基本知识及问答
轮胎工艺知识点总结
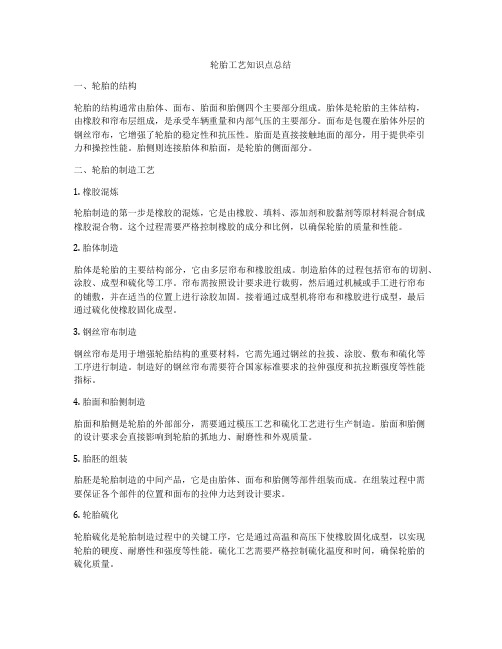
轮胎工艺知识点总结一、轮胎的结构轮胎的结构通常由胎体、面布、胎面和胎侧四个主要部分组成。
胎体是轮胎的主体结构,由橡胶和帘布层组成,是承受车辆重量和内部气压的主要部分。
面布是包覆在胎体外层的钢丝帘布,它增强了轮胎的稳定性和抗压性。
胎面是直接接触地面的部分,用于提供牵引力和操控性能。
胎侧则连接胎体和胎面,是轮胎的侧面部分。
二、轮胎的制造工艺1. 橡胶混炼轮胎制造的第一步是橡胶的混炼,它是由橡胶、填料、添加剂和胶黏剂等原材料混合制成橡胶混合物。
这个过程需要严格控制橡胶的成分和比例,以确保轮胎的质量和性能。
2. 胎体制造胎体是轮胎的主要结构部分,它由多层帘布和橡胶组成。
制造胎体的过程包括帘布的切割、涂胶、成型和硫化等工序。
帘布需按照设计要求进行裁剪,然后通过机械或手工进行帘布的铺敷,并在适当的位置上进行涂胶加固。
接着通过成型机将帘布和橡胶进行成型,最后通过硫化使橡胶固化成型。
3. 钢丝帘布制造钢丝帘布是用于增强轮胎结构的重要材料,它需先通过钢丝的拉拔、涂胶、敷布和硫化等工序进行制造。
制造好的钢丝帘布需要符合国家标准要求的拉伸强度和抗拉断强度等性能指标。
4. 胎面和胎侧制造胎面和胎侧是轮胎的外部部分,需要通过模压工艺和硫化工艺进行生产制造。
胎面和胎侧的设计要求会直接影响到轮胎的抓地力、耐磨性和外观质量。
5. 胎胚的组装胎胚是轮胎制造的中间产品,它是由胎体、面布和胎侧等部件组装而成。
在组装过程中需要保证各个部件的位置和面布的拉伸力达到设计要求。
6. 轮胎硫化轮胎硫化是轮胎制造过程中的关键工序,它是通过高温和高压下使橡胶固化成型,以实现轮胎的硬度、耐磨性和强度等性能。
硫化工艺需要严格控制硫化温度和时间,确保轮胎的硫化质量。
7. 轮胎检验和包装轮胎制造完成后需要进行严格的质量检验,包括外观质量、尺寸测量、硫化性能和性能测试等。
合格的轮胎在包装之前还需要进行气密性试验和动平衡试验等。
三、轮胎的检验和测试轮胎制造过程中的检验和测试是确保轮胎质量的重要环节。
轮胎-轮胎制造工艺基础知识
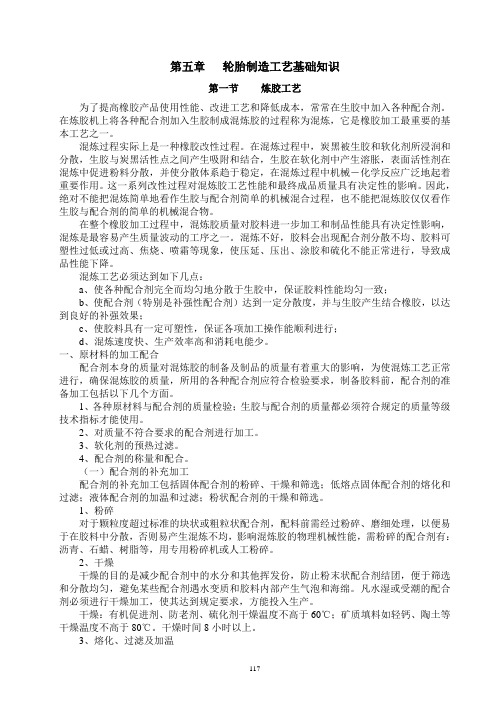
第一节 炼胶工艺
为了提高橡胶产品使用性能、改进工艺和降低成本,常常在生胶中加入各种配合剂。 在炼胶机上将各种配合剂加入生胶制成混炼胶的过程称为混炼,它是橡胶加工最重要的基 本工艺之一。
混炼过程实际上是一种橡胶改性过程。在混炼过程中,炭黑被生胶和软化剂所浸润和 分散,生胶与炭黑活性点之间产生吸附和结合,生胶在软化剂中产生溶胀,表面活性剂在 混炼中促进粉料分散,并使分散体系趋于稳定,在混炼过程中机械-化学反应广泛地起着 重要作用。这一系列改性过程对混炼胶工艺性能和最终成品质量具有决定性的影响。因此, 绝对不能把混炼简单地看作生胶与配合剂简单的机械混合过程,也不能把混炼胶仅仅看作 生胶与配合剂的简单的机械混合物。
常用配合剂磅称规格见下表:
配合剂种类
ห้องสมุดไป่ตู้
磅称规格
公差(g)
超促进剂
天平
±0.5
小药料、硫磺
案秤
±5
氧化锌
台秤
±50
小药总重
台秤
±100
生胶、炭黑
磅称
±200
填充剂
台秤
±50
芳烃油(自动称量)
电子秤
±150
炭黑(自动称量)
电子秤
±300
自动称量能远距离操作,远距离指示,称量误差小,可称多种配合剂。但自动称量,
118
就是利用低分子物质对橡胶的物理溶胀作用来减小大分子间的相互作用力,从而降低了胶 料的粘度,提高其可塑性和流动性。这种方法只能作为生胶塑炼过程中的一种辅助增塑方 法,用于提高塑化效果。
(2)化学增塑法 利用某些化学物质对生胶大分子链的化学破坏作用来减小生胶的弹性和粘度,提高其 可塑性和流动性,这种方法叫化学增塑法。从生胶塑化机理看,化学增塑是比较有效的增 塑方法,但只能作为其它机械塑化方法中的一种辅助增塑法使用。 (3)机械增塑法 利用机械的高剪切力作用使橡胶大分子链破坏降解而获得可塑性的方法叫机械增塑法 或机械塑炼法。这是目前生胶塑炼加工中使用最广泛而又行之有效的增塑方法,可以单独 用于生胶塑炼加工,也可以与物理增塑法及化学增塑法配合使用,能进一步提高机械塑炼 效果和生产效率。 2、生胶塑炼的增塑机理 生胶塑炼的实质是使橡胶的大分子链断裂破坏,能够促使大分子链发生破坏降解的因 素主要有:机械力的作用、氧的氧化裂解作用、热的热活化作用、静电与臭氧的作用、化 学塑解剂的破坏作用。 (三) 塑炼工艺 生胶塑炼加工前需经过一些准备加工,然后才能进行塑炼,塑炼后的胶料还要经过压 片、冷却、停放和质量检查、质量合格后方能供下一步加工使用。 1、生胶的准备 生胶塑炼前的准备加工包括烘胶、切胶、选胶和破胶等处理过程。 (1)烘胶 天然胶经过长时间的运输和储存之后,常温下的粘度很高,易硬化和产生结晶,特别 是在气温较低的条件下,常会因结晶而硬化,使生胶难于切割和加工。因此,应先进行加 热软化,以便于进行切割和塑炼加工,从而保护炼胶设备,提高塑炼效果,同时还能使水 分挥发掉。 烘胶一般在专用的烘胶房中进行,烘胶房的下面和周边设有蒸汽加热器,生胶在烘胶 房内按一定规则和顺序堆放在存放架上,但不得与加热器接触。天然胶烘胶温度、时间按 季节气温、地区 的温度、天然胶块重的差异而不同。低于 40 公斤的烘胶温度:55±10℃ 大 于 40 公斤的烘胶温度:65±10℃;烘胶时间:夏季(5-10 月)24-36 小时;冬季(11-4 月) 36-72 小时。烘完后的胶料要求内外均匀、无夹心、无氧化发粘现象。 (2)切胶和选胶 为便于使用,天然胶在塑炼前要进行切胶,GK-400 密炼机要求胶块不大于 40 公斤, XM-270 要求不大于 10 公斤。 生胶经加温后自烘胶房取出,在切胶前必须将外包装皮剥掉,并保证表面无沙砾和其 他杂质,然后才能进行切割。切胶用单刃式切胶机或多刃式切胶机,具体以生产规模和条 件而定。 生胶切完后,须经外观检查,并注明胶种。若胶包中有不符等级品种质量规定的生胶 或杂质、霉烂等现象,应加以挑选和分级处理,以便按质量等级适当选用。 2、塑炼工艺 塑炼按设备分可分为开炼机塑炼、密炼机塑炼和螺杆机塑炼 (1)开炼机塑炼 开炼机塑炼是应用最早的机械塑炼方法,与其他机械塑炼方法相比,开炼机塑炼法自 动化程度低,生产效率低,劳动强度大,操作危险性大,所以不适用于现代化大规模生产, 在此不做过多介绍。 (2)密炼机塑炼工艺
轮胎橡胶工艺

轮胎橡胶工艺1. 引言轮胎是汽车的重要组成部分,它直接影响到汽车的行驶性能和安全性。
而轮胎的核心材料之一就是橡胶。
橡胶工艺是指将橡胶原料经过一系列的加工工艺,制成轮胎的过程。
本文将详细介绍轮胎橡胶工艺的流程和关键技术。
2. 轮胎橡胶工艺流程轮胎橡胶工艺的流程通常包括以下几个步骤:2.1 橡胶混炼橡胶混炼是将橡胶原料与各种添加剂进行混合的过程。
这一步骤的目的是使橡胶具有良好的可加工性和性能。
常用的橡胶混炼设备包括开炼机和密炼机。
开炼机主要用于初步混合橡胶原料,密炼机则用于更细致的混炼。
2.2 轮胎胎体制备轮胎胎体是轮胎的主体部分,由多层橡胶和帘布组成。
制备轮胎胎体的工艺包括帘布切割、帘布涂胶、帘布铺层等步骤。
帘布切割是将帘布按照预定的尺寸进行切割,帘布涂胶是将切割好的帘布进行胶液涂布,帘布铺层则是将胶液涂布的帘布层层叠加,形成轮胎胎体的骨架。
2.3 胎面胎侧制备胎面和胎侧是轮胎的外层,主要由橡胶和纤维材料组成。
胎面胎侧的制备工艺包括胶料制备、胶料加工、胶料涂布等步骤。
胶料制备是将橡胶原料和其他添加剂进行混炼,胶料加工是将混炼好的胶料进行塑炼和挤出,胶料涂布则是将挤出的胶料涂布在帘布上。
2.4 胎体缓冲制备胎体缓冲是位于胎面和胎侧之间的一层橡胶,用于缓冲和支撑轮胎。
胎体缓冲的制备工艺包括胶料制备、胶料加工、胶料涂布等步骤,类似于胎面胎侧的制备过程。
2.5 胎圈装配胎圈是固定轮胎在车轮上的金属环,胎圈装配是将轮胎胎体和胎圈进行组装的过程。
这一步骤主要包括帘布固定、帘布切除、帘布胶合等工艺。
2.6 硫化硫化是将轮胎放入硫化机中,通过加热和加压使橡胶材料发生化学反应,形成硫化交联结构的过程。
硫化是轮胎制造中最重要的工艺步骤,它决定了轮胎的最终性能和质量。
3. 轮胎橡胶工艺的关键技术轮胎橡胶工艺涉及到多种关键技术,以下是其中几个重要的技术:3.1 橡胶混炼技术橡胶混炼技术是轮胎橡胶工艺的基础,它直接影响到橡胶的加工性能和性能。
橡胶工艺基本常识(1)

2.硫与硫载体并用,促进剂用量与SEV中一致。
橡胶工艺基本常识(1)
NR的三种硫化体系配合如表2-1所示:
配方成分 CV
EV
高促低硫 无硫配合
S
2.5 0.5
—
NOBS 0.6 3.0
1.1
TMTD — 0.6 1.1
橡胶工艺基本常识(1)
4. 工艺正硫化时间(t90 ) (Optimum curing time):胶料 从加热开始,至转矩上升到最大转矩的90%时所需要 的时间。
M90=ML+(MH-ML)×90%
5.理论正硫化时间(Theoretical curing time):交联密度 达到最大程度时所需要的时间。
裂,且有变色污染性。
(3)一般不单独使用,常与M,DM,CZ等并用,
既可以活化硫化体 系又克服了自身的缺点,只在硬
ห้องสมุดไป่ตู้
质橡胶制品中单独使用。
橡胶工艺基本常识(1)
6.硫脲类
结构通式为:
作用特点 促进剂的促进效能低,抗焦烧性能差,除了CR、CO、CPE
用于促进和交联外,其它二烯类橡胶很少使用。其中Na-22是 CR常用的促进剂。
双(三乙氧基甲硅烷基丙基)四硫化物
Si69的作用: 硫载体(抗返原剂) 偶联剂
橡胶工业中常用的其他抗返原剂: 环己烷-1,6-二硫代硫酸钠二水合化合物(Duralink HTS) 1,3-双(柠檬酰亚胺甲基)苯(Perkalink-900) N,N/-间亚苯基双基双马来酰亚胺(HVA-2) 双马来酰亚胺类(DL-268)
DMDT — —
1.1
橡胶方面知识培训

橡胶方面知识培训橡胶方面知识培训橡胶是一种常见的塑料材料,广泛用于汽车、轮胎、电缆、管道、防水材料等行业。
了解橡胶的性质、加工工艺、检测方法等方面的知识,对于从事相关行业的工程师和技术员来说非常重要。
本文将介绍橡胶方面的知识培训内容。
一、橡胶的基本知识1. 橡胶的种类和特点橡胶主要分为天然橡胶和合成橡胶两大类。
天然橡胶具有良好的耐磨性、弹性和可加工性,但价格较高;合成橡胶可以根据需求进行定制,价格较低,但在某些方面性能不如天然橡胶。
2. 橡胶的结构和性质橡胶由聚合物链构成,不同的聚合物链之间通过交联作用相连。
橡胶具有良好的弹性、抗张强度和耐磨性,在高温、低温和化学物质的作用下仍能保持较好的性能。
3. 橡胶的加工方法橡胶加工主要分为静态成型和动态成型两种。
静态成型包括压缩成型和注塑成型,动态成型包括挤出成型、胶粘成型等。
不同的成型方法适用于不同的产品,需要根据实际需求进行选择。
二、橡胶的检测方法1. 物理性能测试橡胶的物理性能包括拉伸性能、硬度、耐磨性等。
通过拉伸试验机、硬度计等仪器进行测试,可以评估橡胶的性能。
2. 化学物质检测橡胶的化学性质很重要,包括抗氧化性、抗老化性等。
通过对橡胶样品进行荧光光谱、紫外-可见光谱、红外光谱等测试,可以评估橡胶的化学性质。
3. 微结构分析橡胶的微结构对其性能有重要影响,通过电子显微镜,扫描电镜等技术进行精细的结构分析,可以更好地理解橡胶的性能和应用。
三、橡胶的设计与应用1. 橡胶材料的选择在设计使用橡胶制品时,需要考虑到产品的环境条件、使用寿命、性能要求等因素,选取合适的橡胶材料。
2. 橡胶制品的设计橡胶制品的设计需要考虑到产品的结构、加工方法、性能要求等因素,通过CAD、PROE等软件进行设计和模拟分析,确保产品具有优良的性能和稳定的品质。
3. 橡胶制品的应用维护在橡胶制品的维护和保养过程中,需要考虑到产品的加工材料、使用环境、耐磨性等因素,采用正确的维护方法,延长产品的使用寿命。
轮胎加工分享小知识点总结
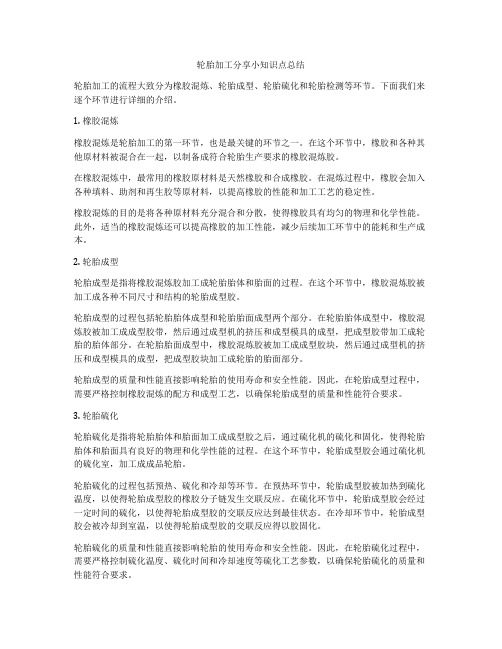
轮胎加工分享小知识点总结轮胎加工的流程大致分为橡胶混炼、轮胎成型、轮胎硫化和轮胎检测等环节。
下面我们来逐个环节进行详细的介绍。
1. 橡胶混炼橡胶混炼是轮胎加工的第一环节,也是最关键的环节之一。
在这个环节中,橡胶和各种其他原材料被混合在一起,以制备成符合轮胎生产要求的橡胶混炼胶。
在橡胶混炼中,最常用的橡胶原材料是天然橡胶和合成橡胶。
在混炼过程中,橡胶会加入各种填料、助剂和再生胶等原材料,以提高橡胶的性能和加工工艺的稳定性。
橡胶混炼的目的是将各种原材料充分混合和分散,使得橡胶具有均匀的物理和化学性能。
此外,适当的橡胶混炼还可以提高橡胶的加工性能,减少后续加工环节中的能耗和生产成本。
2. 轮胎成型轮胎成型是指将橡胶混炼胶加工成轮胎胎体和胎面的过程。
在这个环节中,橡胶混炼胶被加工成各种不同尺寸和结构的轮胎成型胶。
轮胎成型的过程包括轮胎胎体成型和轮胎胎面成型两个部分。
在轮胎胎体成型中,橡胶混炼胶被加工成成型胶带,然后通过成型机的挤压和成型模具的成型,把成型胶带加工成轮胎的胎体部分。
在轮胎胎面成型中,橡胶混炼胶被加工成成型胶块,然后通过成型机的挤压和成型模具的成型,把成型胶块加工成轮胎的胎面部分。
轮胎成型的质量和性能直接影响轮胎的使用寿命和安全性能。
因此,在轮胎成型过程中,需要严格控制橡胶混炼的配方和成型工艺,以确保轮胎成型的质量和性能符合要求。
3. 轮胎硫化轮胎硫化是指将轮胎胎体和胎面加工成成型胶之后,通过硫化机的硫化和固化,使得轮胎胎体和胎面具有良好的物理和化学性能的过程。
在这个环节中,轮胎成型胶会通过硫化机的硫化室,加工成成品轮胎。
轮胎硫化的过程包括预热、硫化和冷却等环节。
在预热环节中,轮胎成型胶被加热到硫化温度,以使得轮胎成型胶的橡胶分子链发生交联反应。
在硫化环节中,轮胎成型胶会经过一定时间的硫化,以使得轮胎成型胶的交联反应达到最佳状态。
在冷却环节中,轮胎成型胶会被冷却到室温,以使得轮胎成型胶的交联反应得以胶固化。
橡胶基本知识问答

橡胶基本知识问答(一)一、根据橡胶的来源,橡胶可分为哪几类?答:按来源来分,橡胶可分为天然橡胶、再生橡胶、合成橡胶。
合成橡胶又可分通用合成橡胶和特种合成橡胶,通用合成橡胶有:丁苯橡胶、顺丁橡胶、氯丁橡胶、丁腈橡胶、乙丙橡胶、丁基橡胶、异戊橡胶等。
特种橡胶有:氯磺化聚乙烯、氯化聚乙烯、氯醇橡胶、丙烯酸酯橡胶、氟橡胶、硅橡胶、聚胺酯橡胶等等。
二、常用橡胶的特性怎样?它们有哪些用途?三、什么叫橡胶配方?它一般由哪几部分组成?它们的作用是什么?答:橡胶配方是指橡胶与配合剂的配比方案,它一般由生胶、硫化剂、促进剂、活性剂、防老剂、补强剂、增塑剂等几部分组成。
它们的作用是:生胶;它是胶料中的最重要的组分,它是决定胶料的使用性能、工艺性能和产品成本上升的主要因素。
硫化剂:即交联剂,它为橡胶分子与分子之间提供交联的物质。
促进剂:提高硫化剂的活性,加快硫化速度,缩短硫化时间,影响交联结构,改善硫化胶的物理机械性能,减少硫化剂的用量。
活性剂:一般不加速橡胶的硫化反应,但会显著影响交联键的生成速度和数量。
防老剂:防止橡胶在光、热、臭氧及化学药品等作用下发生老化,抑制和减缓橡胶老化。
补强剂:改善和提高橡胶的机械强度,改善橡胶的耐磨,耐寒性能。
增塑剂:改善橡胶加工过程中的加工性能。
四、什么是塑炼?塑炼的方法有哪些?答:塑炼是把具有高弹性的生胶通过机械或化学方法,使其弹性消失,塑性增加的操作,其目的是便于半成品的制作,并使配合剂能够分散均匀。
塑炼方法有机械塑炼和密炼机塑炼。
机械塑炼是通过具有不同转速的开炼机,使生胶受到剪切力破坏,从而提高可塑性。
密炼机塑炼是采用高温塑炼,通过高温氧化作用破坏橡胶分子,从而获得可塑性。
五、什么是混炼?开炼机的混炼工艺是怎样的?答:混炼是使具有一定塑性的生胶与各种配合剂均匀混合的操作过程。
其目的是使各种配合剂均匀分散到橡胶中去,使胶料具有一致的,均匀的物理性能,从而制出优质的成品。
开炼机的混炼工艺:生胶的热炼加入防老剂、活性剂、防焦剂薄通一至二次加入1/2炭黑加入增塑剂、另1/2炭黑待增塑剂和炭黑吃完后,加入促进剂、硫化剂,硫化剂,左右割三至四次薄通四至六次出片冷却。
橡胶工艺基础知识

二 、橡胶配合
二 、橡胶配合
• 橡胶的配合:
橡胶具有宝贵的高弹性和其它一系列优良的性能,但其本 身在性能上仍有许多缺点。例如天然橡胶保持高弹性的温度范 围只在5-35左右,生胶的机械强度也比较低,可见,用纯生胶 是不能制造出适合使用要求的橡胶制品的。
根据制品的性能要求,考虑加工工艺性能和成本等因素,把 生胶和配合剂组合在一起的过程。一般的配合体系包括生胶、 硫化体系、补强体系、防护体系、增塑体系等。有时还包括其 它一些特殊的体系如阻燃、着色、发泡、抗静电、导电等体系 。
• A2残余焦烧时间——进入模具后加热开始到开始 硫化这段时间
若:操作焦烧时间 > 焦烧时间,就发生焦烧
• 防止焦烧:
A、 具有较长的焦烧时间:配方
M
A
B 、混炼、停放要低温, 成型时要迅速,即减少操作焦烧 时间
优点: 具良好抗候性及抗臭氧性, 具极佳的抗水性 及抗老化性 ,电绝缘性能优良,耐化学腐蚀,冲击弹性 较好。
缺点:硫化速度慢;与其它不饱和橡并用难;不建议 用于食品用途或是暴露于芳香氢之中。
主要用于要求耐老化、耐水、耐腐蚀、电气绝缘等几 个领域。如:轮胎的浅色胎侧、电缆、耐热运输带、门 窗密封条、密封垫圈等。
橡胶工艺
---橡胶制品---
一 、橡胶分类及特点
一 、橡胶分类及特点
• 橡胶按原料分为天然橡胶和合成橡胶。 • 按形态分为块状生胶、乳胶、液体橡胶和粉末
橡胶。
▪ 乳胶为橡胶的胶体状水分散体;液体橡胶为橡胶的低
聚物,未硫化前一般为粘稠的液体;粉末橡胶是将乳 胶加工成粉末状,以利配料和加工制作。
• 20世纪60年代发明的热塑性橡胶,无需化学硫
优点:弹性良好及具良好的压缩变形,配方内不含 硫磺,因此非常容易来制作.具抗动物及植物油的特性, 不会因中性化学物,脂肪、油脂、多种油品,溶剂而影 响物性,具防燃特性。
- 1、下载文档前请自行甄别文档内容的完整性,平台不提供额外的编辑、内容补充、找答案等附加服务。
- 2、"仅部分预览"的文档,不可在线预览部分如存在完整性等问题,可反馈申请退款(可完整预览的文档不适用该条件!)。
- 3、如文档侵犯您的权益,请联系客服反馈,我们会尽快为您处理(人工客服工作时间:9:00-18:30)。
轮胎行业橡胶工艺基本知识及问答
轮胎是车辆行驶的关键部件之一,不仅能够提供车辆的支撑,还能够影响车辆的操控性、稳定性、燃油经济性等方面。
而轮胎的制造离不开橡胶工艺,下面就对轮胎行业的橡胶工艺基本知识进行了整理及问答。
一、橡胶工艺的基本流程
橡胶工艺的基本流程分为三个步骤,分别是制胶、加工和硫化。
制胶:将天然橡胶和合成橡胶以及其他添加剂混合在一起,加入硫化剂和促进剂,形成白色或浅灰色的混合料。
加工:将混合料切碎后进行加工,包括压延、自动化机械或手工裁切成形,塑化成为胎坯。
硫化:将胎坯放在硫化室中,在压力和温度下进行硫化,使橡胶分子交联,成为整体。
二、橡胶混合料的添加剂及其作用
1.天然橡胶和合成橡胶:为轮胎的主要原材料,能够提供
轮胎的支撑。
2.活性填充剂:能够加强橡胶材料的刚度和韧性,提高轮
胎的耐磨性和耐龟裂性。
3.油类:能够提高橡胶混合料的加工流动性,并使橡胶材料在低温时仍然柔软。
4.橡胶软化剂:能够增加橡胶的弹性和柔软性,提高轮胎的载荷能力和操控性。
5.硫化剂:是制造轮胎必不可少的添加剂,能够使橡胶材料在加热条件下发生交联反应,增加橡胶的强度和耐久性。
6.促进剂:能够调节硫化剂的活性,促进橡胶材料的硫化速度和硫化程度。
三、轮胎硫化的原理
轮胎在硫化过程中,经过加热和加压的作用,硫化剂和促进剂在一定温度和压力下发生反应,形成交联结构,使橡胶分子交联成为一个整体。
交联结构的形成能够给轮胎提供足够的抗拉强度和韧性,使轮胎更加耐用,且能够适应各种路况和驾驶方式。
四、橡胶工艺中存在的问题及解决方法
1.均匀性:轮胎制造过程中的混料、加工、硫化等环节都需要保证均匀性,否则会影响轮胎品质,解决方法是优化生产流程和加强设备管理。
2.能耗问题:轮胎制造涉及到加热、加压等大量的能源消耗,在保证质量和效益的前提下需要降低能耗,可以采用新型能源和节能技术,提高加工和硫化的效率。
3.供应链问题:轮胎材料多种多样,涉及到供应链的多元化和质量控制,需要保证供应商的质量和供货稳定性。
五、橡胶工艺常见问题及答疑
1.为什么轮胎需要硫化?
答:硫化是将橡胶材料交联成为一个整体,增加轮胎强度和耐用性的必要过程。
2.轮胎的弹性来源是什么?
答:轮胎的弹性来源于橡胶材料的弹性和气体内压形成的弹力。
3.橡胶混合料的添加剂对轮胎品质有何影响?
答:添加剂的不同都能对轮胎的使用性能和寿命产生影响,如活性填充剂能够提高轮胎的耐磨性和耐龟裂性,而橡胶软化剂则能够增加轮胎的韧性和弹性。
4.橡胶工艺存在哪些难点?
答:橡胶混合料加工的均匀性、轮胎硫化的能耗和供应链的质量控制都是当前橡胶工艺存在的难点。
总之,橡胶工艺是制造轮胎的基础,也是轮胎品质的重要保障,透过橡胶工艺的基本流程及问题可见,制造优质的轮胎需要设备先进、工艺精湛和质量严控,这是制造业的一贯标准和要求。