立式组合机床的动力滑台液压课程设计
液压传动课程设计组合机床动力滑台液压系统设计
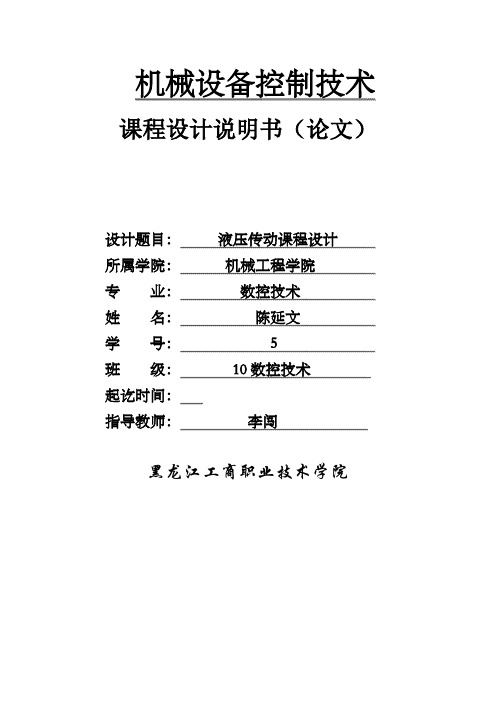
机械设备控制技术课程设计说明书(论文)设计题目:液压传动课程设计所属学院:机械工程学院专业:数控技术姓名:陈延文学号: 5班级:10数控技术起讫时间:指导教师:李闯黑龙江工商职业技术学院目录1.课程设计任务书……………………………………………………第3页2.第一章设计任务书………………………………………………第4页3.第二章液压系统设计计算………………………………………第5页课程设计任务书第一章:设计任务书第一节:设计题目设计一台组合机床动力滑台液压系统。
第二节:设计参数工作台要求完成快进——铣削进给——快退——停止等自动循环,工作台采用平导轨第三节:设计要求1.机床自动化要求:要求系统采用电液结合,实现自动循环,速度换接无冲击,且速度要稳定,能经受必然量的反向负荷。
2.完成如下工作:①按机床要求设计液压系统,绘出液压系统图。
②肯定滑台液压缸的结构参数。
③计算系统各参数,列出电磁铁动作顺序表。
第二章:液压系统设计计算第一节:负载及运动分析1工作负载 负载分析中,暂不考虑回油腔的背压力,液压缸的密封装置产生的摩擦阻力在机械效率中加以考虑。
因工作部件是卧式放置,重力的水平分力为零,这样需要考虑的力有:切削力、导轨的摩擦力和惯性力。
导轨的正压力大小等于动力部件的重力.启动时只受静摩擦力,加速时受动摩擦力和惯性力,快进时只受动摩擦力,工进时受切削力和动摩擦力,其中切削力为F fw =10500N,快退时也只受动摩擦力.2摩擦负载因为卧式放置,所以正压力即为重力.由静止开始运动的时候受静摩擦力,运动的时候受动摩擦力.设导轨的静摩擦力为fs F 、动摩擦力为fd F 则: 摩擦负载即为导轨的摩擦阻力:静摩擦阻力 N F f F N s fs 110055002.0=⨯=⨯= 动摩擦阻力 N F f F N d fd 55055001.0=⨯=⨯= 3惯性负载在系统加速的时候受惯性负载N N t m F m 46.2102.080.9605.45500=⨯⨯=∆∆=υ4各工况负载若是忽略切削力引发的颠覆力矩对导轨摩擦力的影响,而且设液压缸的机械效率η=,则液压缸在各工作阶段的总机械负载可以算出,见表1表1 液压缸各运动阶段负载表5快进、工进和快退时间和速度快进时的行程为l=100mm,整个快进进程可看做速度为v1=4.5m/min的匀速运动,所以快进时间为t=l/v1=100/1000⨯60=1S工进时的行程为l=100mm,此进程的速度为v2=60~1000mm/min,所以此进程的工进时间t=l/ v2=100/(60~1000) ⨯60=(6~100)s快退时的行程为l=200mm, 整个快退进程可看做速度为v3=4.5m/min的匀速运动,所以快退时间为t=l/v3=400/1000⨯60=第二节:肯定液压缸参数1.初选液压缸的工作压力参考同类组合机床见表2,初定液压缸的工作压力表 2 各类机械常常利用的系统工作压力2.肯定液压缸的主要结构尺寸本题要求动力滑台的快进快退速度相等,现采用活塞杆固定的单杆式液压缸。
组合机床动力滑台液压系统设计
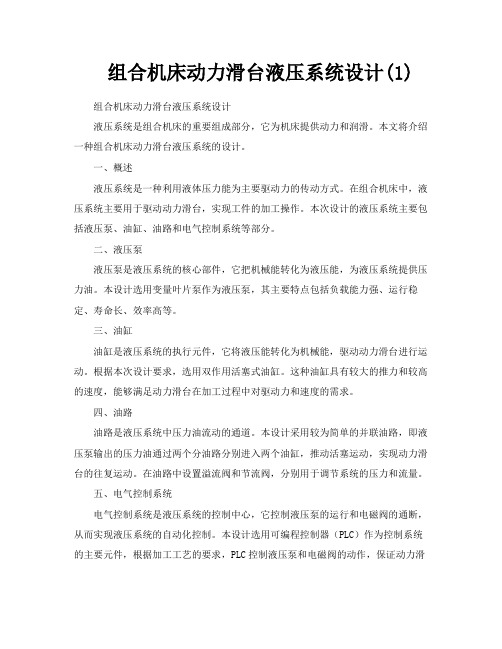
组合机床动力滑台液压系统设计(1) 组合机床动力滑台液压系统设计液压系统是组合机床的重要组成部分,它为机床提供动力和润滑。
本文将介绍一种组合机床动力滑台液压系统的设计。
一、概述液压系统是一种利用液体压力能为主要驱动力的传动方式。
在组合机床中,液压系统主要用于驱动动力滑台,实现工件的加工操作。
本次设计的液压系统主要包括液压泵、油缸、油路和电气控制系统等部分。
二、液压泵液压泵是液压系统的核心部件,它把机械能转化为液压能,为液压系统提供压力油。
本设计选用变量叶片泵作为液压泵,其主要特点包括负载能力强、运行稳定、寿命长、效率高等。
三、油缸油缸是液压系统的执行元件,它将液压能转化为机械能,驱动动力滑台进行运动。
根据本次设计要求,选用双作用活塞式油缸。
这种油缸具有较大的推力和较高的速度,能够满足动力滑台在加工过程中对驱动力和速度的需求。
四、油路油路是液压系统中压力油流动的通道。
本设计采用较为简单的并联油路,即液压泵输出的压力油通过两个分油路分别进入两个油缸,推动活塞运动,实现动力滑台的往复运动。
在油路中设置溢流阀和节流阀,分别用于调节系统的压力和流量。
五、电气控制系统电气控制系统是液压系统的控制中心,它控制液压泵的运行和电磁阀的通断,从而实现液压系统的自动化控制。
本设计选用可编程控制器(PLC)作为控制系统的主要元件,根据加工工艺的要求,PLC控制液压泵和电磁阀的动作,保证动力滑台按要求的程序进行加工操作。
同时,PLC还可以实时检测系统的运行状态,保证系统的稳定性和安全性。
六、系统调试与优化完成液压系统的设计后,需要对系统进行调试和优化,以保证其性能和可靠性。
首先进行空载调试,检查系统是否存在泄漏或异常噪声等问题;然后进行负载调试,在一定的负载条件下测试系统的性能;最后进行加工试验,以检验液压系统在真实加工条件下的性能。
根据试验结果对系统进行优化调整,以使液压系统的性能达到最佳状态。
七、结论本文对组合机床动力滑台液压系统进行了设计。
动力滑台液压系统课程设计
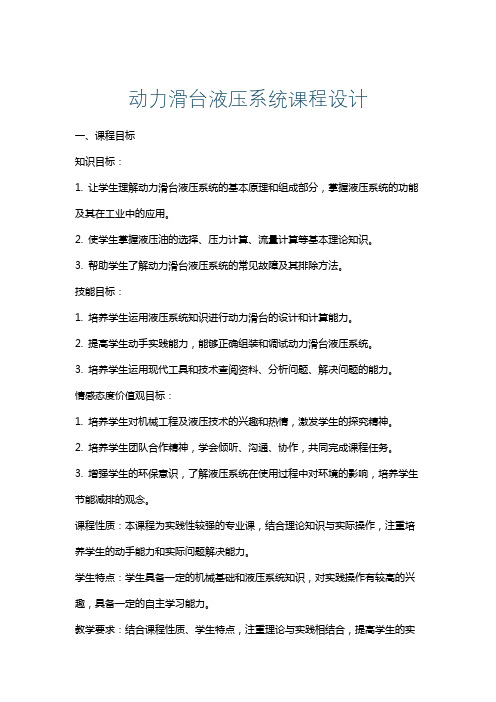
动力滑台液压系统课程设计一、课程目标知识目标:1. 让学生理解动力滑台液压系统的基本原理和组成部分,掌握液压系统的功能及其在工业中的应用。
2. 使学生掌握液压油的选择、压力计算、流量计算等基本理论知识。
3. 帮助学生了解动力滑台液压系统的常见故障及其排除方法。
技能目标:1. 培养学生运用液压系统知识进行动力滑台的设计和计算能力。
2. 提高学生动手实践能力,能够正确组装和调试动力滑台液压系统。
3. 培养学生运用现代工具和技术查阅资料、分析问题、解决问题的能力。
情感态度价值观目标:1. 培养学生对机械工程及液压技术的兴趣和热情,激发学生的探究精神。
2. 培养学生团队合作精神,学会倾听、沟通、协作,共同完成课程任务。
3. 增强学生的环保意识,了解液压系统在使用过程中对环境的影响,培养学生节能减排的观念。
课程性质:本课程为实践性较强的专业课,结合理论知识与实际操作,注重培养学生的动手能力和实际问题解决能力。
学生特点:学生具备一定的机械基础和液压系统知识,对实践操作有较高的兴趣,具备一定的自主学习能力。
教学要求:结合课程性质、学生特点,注重理论与实践相结合,提高学生的实际操作能力和创新能力。
在教学过程中,关注学生的个体差异,充分调动学生的积极性,确保课程目标的实现。
通过课程学习,使学生能够将所学知识应用于实际工作中,为我国液压技术的发展做出贡献。
二、教学内容1. 理论知识:- 动力滑台液压系统的基本原理及其组成部分(对应教材第3章)- 液压油的性质与选择(对应教材第4章)- 液压系统的压力计算与流量计算(对应教材第5章)- 动力滑台液压系统的设计方法及步骤(对应教材第6章)- 常见故障分析与排除方法(对应教材第7章)2. 实践操作:- 动力滑台液压系统的组装与调试(结合教材第3章、第6章)- 液压系统的运行与维护(结合教材第7章)- 故障诊断与排除实践(结合教材第7章)3. 教学大纲:- 第一周:动力滑台液压系统基本原理及组成部分学习- 第二周:液压油的性质与选择,压力计算与流量计算- 第三周:动力滑台液压系统设计方法及步骤- 第四周:实践操作(组装、调试、运行与维护)- 第五周:常见故障分析与排除方法,故障诊断与排除实践教学内容安排和进度依据学生的实际学习情况和掌握程度进行调整,确保学生能够充分理解和掌握课程内容,为实际应用打下坚实基础。
组合机床动力滑台液压系统设计设计任务书

任务书
设计(论文)
组合机床动力滑台液压系统设计
课题名称
学生姓名院(系)专业
指导教师职称学历
毕业设计(论文)要求:
1.要求在完成论文期间,态度端正,积极主动,大量查阅文献资料。
2.按时完成毕业设计内容,技术路线准确,可行。
3.绘制零件图和装配图,图纸量不少于1.5张A0图纸。
4.完成毕业设计说明书,格式正确,要求字数不少于6000字。
5.完成电子文档及PPT文档。
毕业设计(论文)内容与技术参数:
1.动力滑台工作台循环为:快进→工进→二工进→快退→停止。
2.轴向切削力为30468N,移动部件总重力为9800N。
3.快进行程为100mm,快进速度为0.1m/s。
4.工进行程为50mm,工进速度为0.88×10-3m/s,加减速时间为0.2s。
5.平导轨静摩擦系数为0.2,动摩擦系数为0.1。
毕业设计(论文)工作计划:
1.2012年11月~12月:接受毕业设计任务,查阅整理文献资料。
2.2013年1月:确定课题设计方案。
3.2013年2月~4月:绘制设计图纸及编写设计说明书。
4.2013年5月10日之前:定稿打印,准备毕业设计答辩。
接受任务日期年月日要求完成日期年月日学生签名年月日指导教师签名年月日院长(主任)签名年月日。
组合机床液压动力滑台的液压及电气设计设计说明书

设计说明书目录第一章绪论1、课题意义、背景及应用现状2、液压控制特点3、机械式与液压式滑台特点第二章液压滑台的液压系统动力设计1、运动负载分析计算2、确定执行元件类型及基本参数3、确定液压控制方案4、确定液压控制元件5、校核第三章液压滑台的电气控制设计1、确定控制对象2、确定电气控制方案第四章液压缸结构设计1、确定类型主要参数2、确定部件连接方式3、排气缓冲设计4、检验第五章总结第一章绪论1课题意义、背景及应用现状1.1课题意义通过对专用铣床动力滑台的负载分析及工艺分析,熟悉机床液压及电气设计的基本思路、方法,掌握机电设备电气与液压系统设计机液压执行机构的机构设计方法。
通过本课题的训练加强对机床液压与电气控制知识的综合应用,具备初步的工程实践能力。
1.2液压动力滑台背景及应用现状动力滑台是组合机床用以实现进给运动的通用部件,其运动由液压缸驱动。
在滑台上可根据加工工艺要求安装各类动力箱和切削头,以完成车、铣、镗、钻、扩、铰、攻螺纹等加工工序,并能按多种进给方式实现自动工作循环。
液压动力滑台应满足进给速度稳定、速度换接平稳、系统效率高、发热小等要求。
液压传动和气压传动称为流体传动,是根据17世纪帕斯卡提出的液体静压力传动原理而发展起来的一门新兴技术,是工农业生产中广为应用的一门技术。
如今,流体传动技术水平的高低已成为一个国家工业发展水平的重要标志。
第一个使用液压原理的是1795年英国约瑟夫·布拉曼(JosephBraman,1749-1814),在伦敦用水作为工作介质,以水压机的形式将其应用于工业上,诞生了世界上第一台水压机。
1905年他又将工作介质水改为油,进一步得到改善。
第一次世界大战(1914-1918)后液压传动广泛应用,特别是1920年以后,发展更为迅速。
液压元件大约在 19 世纪末 20 世纪初的20年间,才开始进入正规的工业生产阶段。
1925 年维克斯(F.Vikers)发明了压力平衡式叶片泵,为近代液压元件工业或液压传动的逐步建立奠定了基础。
组合机床动力滑台液压系统液压课程设计

湖南科技大学课程设计说明书课程名称:专业模块课程设计题目名称:组合机床动力滑台液压系统专业: 机械设计制造及其自动化姓名:泮一平学号: 1153010531指导教师:刘长鸣2015年 1月 8日目录一、液压传动的工作原理与组成、、、、、、、、、、、、、、、、、、、、、、、、、、、、二、设计要求、、、、、、、、、、、、、、、、、、、、、、、、、、、、、、、、、、、、、、、、、、、三、液压系统的工况分析、、、、、、、、、、、、、、、、、、、、、、、、、、、、、、、、、、四、确定液压系统主要参数、、、、、、、、、、、、、、、、、、、、、、、、、、、、、、、、五、液压元件的选择、、、、、、、、、、、、、、、、、、、、、、、、、、、、、、、、、、、、、、六、验算液压系统性能、、、、、、、、、、、、、、、、、、、、、、、、、、、、、、、、、、、、七、设计小结、、、、、、、、、、、、、、、、、、、、、、、、、、、、、、、、、、、、、、、、、、、一、液压传动的工作原理与组成液压传动就是用液体作为工作介质来传递能量与进行控制的传动方式。
液压系统利用液压泵将原动机的机械能转换为液体的压力能,通过液体压力能的变化来传递能量,经过各种控制阀与管路的传递,借助于液压执行元件(缸或马达)把液体压力能转换为机械能,从而驱动工作机构,实现直线往复运动与回转运动。
驱动机床工作台的液压系统就是由邮箱、过滤器、液压泵、溢流阀、开停阀、节流阀、换向阀、液压缸以及连接这些元件的油管、接头等组成。
1、工作原理(1)电动机驱动液压泵经滤油器从邮箱中吸油,油液被加压后,从泵的输出口输入管路。
油液经开停阀、节流阀、换向阀进入液压缸,推动活塞而使工作台左右移动。
液压缸里的油液经换向阀与回油管排回邮箱。
(2)工作台的移动速度就是通过节流阀来调节的。
当节流阀开大时,进入液压缸的油量增多,工作台的移动速度增大;当节流阀关小时,进入液压缸的油量减少,工作台的移动速度减少。
「液压传动大作业_组合机床动力滑台液压系统设计」

「液压传动大作业_组合机床动力滑台液压系统设计」液压传动技术在组合机床动力滑台中的应用越来越广泛,因为液压传动系统具有结构简单、体积小、重量轻、功率密度大、可靠性高等优点。
本文将详细讨论组合机床动力滑台液压系统的设计,包括系统的工作原理、液压元件的选型和系统控制部分的设计。
首先,我们需要了解组合机床动力滑台的工作原理。
组合机床动力滑台主要包括工作台、液压缸、导轨等部分。
液压缸通过液压油的压力对工作台施加力,使其能够进行运动。
液压缸可以根据实际需要进行伸缩,从而实现对工件的加工。
在设计液压系统时,需要注意选择合适的液压元件。
首先,液压泵的选型非常重要,它的功率和流量必须能够满足系统的需求。
其次,液压缸的选择也需要根据工作台的负载和速度来确定。
此外,还需要选择合适的阀门、油缸和油管等液压元件,以确保系统的正常运行。
设计液压控制部分时,需要考虑液压系统的控制方式。
常见的控制方式有手动控制和自动控制。
手动控制方式适用于简单的操作,但在复杂的工作中往往需要自动控制方式。
自动控制方式可以通过PLC或CNC控制系统实现,这样可以实现更精确的控制和更高的生产效率。
在实际使用中,还需要考虑液压系统的安全性和维护性。
安全性是指系统在工作过程中能够保持稳定和可靠的工作状态,防止发生意外事故。
维护性是指系统在工作后能够方便地进行检修和维护。
因此,在设计中需要考虑安全阀、过滤器、压力表等安全元件的配置,并留出维修通道和维修空间。
总结起来,组合机床动力滑台液压系统的设计需要考虑工作原理、液压元件的选型和系统控制部分的设计。
在实际应用中,还需要考虑系统的安全性和维护性。
通过合理的设计和选型,可以实现液压系统的高效、稳定和可靠运行。
立式组合机床动力滑台液压系统设计

立式组合机床动力滑台液压系统设计立式组合机床是一种多功能的机床,结合了数控铣床、数控镗床、数控钻床等多种功能于一体,具有高效、精度高等优点。
而动力滑台是机床的核心部件之一,其液压系统的设计对机床的性能、质量和使用寿命有着重要的影响。
下面将对立式组合机床的动力滑台液压系统设计进行详细阐述。
1.液压油箱及其过滤系统的设计液压油箱是液压系统的重要组成部分,其设计需要保证足够的容积和理想的工作温度,同时需要考虑降低噪音和振动,以保证机床的稳定性和工作效率。
在设计过程中,应选择合适的液压油箱尺寸,并合理布置液压元件,以便维修和检修。
2.主动力元件(液压泵)的选择和设计立式组合机床的液压系统需要液压泵提供动力,因此在设计过程中需要选择合适的液压泵。
一般来说,应选择能够满足工作需求并具有较高效率和可靠性的液压泵。
同时,还需要设计合适的动力连接装置,确保液压泵与机床动力滑台之间的耦合。
3.液压执行元件(液压缸)的选择和设计液压缸是动力滑台的主要执行元件,其选择和设计需要考虑滑台的移动速度、工作负荷和精度要求等因素。
一般来说,应选择能够提供足够力量和行程,并具有较高精度和可靠性的液压缸。
另外,还需要设计合适的缓冲装置和密封装置,以提升液压缸的性能和使用寿命。
4.控制元件(阀门)的选择和设计液压系统的控制元件主要包括方向控制阀、流量控制阀和压力控制阀等。
在设计过程中,需要选择合适的控制阀,以实现对液压系统的精确控制和调节。
同时,还需要合理布置阀门和管路,以便维修和检修。
5.液压系统的安全保护措施液压系统的安全保护措施是设计中必不可少的一部分。
在设计过程中,需要考虑液压系统的各种安全保护装置,包括过压保护、漏油保护、过载保护等。
同时,还需要设计合适的安全操作装置和报警装置,以保证操作人员的安全和机床的正常运行。
总之,立式组合机床的动力滑台液压系统设计需要全面考虑机床的工作需求和性能要求,合理选择和布置液压元件,确保液压系统的可靠性和稳定性。
- 1、下载文档前请自行甄别文档内容的完整性,平台不提供额外的编辑、内容补充、找答案等附加服务。
- 2、"仅部分预览"的文档,不可在线预览部分如存在完整性等问题,可反馈申请退款(可完整预览的文档不适用该条件!)。
- 3、如文档侵犯您的权益,请联系客服反馈,我们会尽快为您处理(人工客服工作时间:9:00-18:30)。
立式组合机床的动力滑台液压课程设计Company number:【0089WT-8898YT-W8CCB-BUUT-202108】课程设计说明书专业:机械设计制造及其自动化班级学号:学生姓名:岳维指导教师:唐炜2012年1月 5日江苏科技大学南徐学院目录1.工况分析 (1)2.拟定液压系统原理图 (2)3.液压系统的计算和选择液压元件 (8)液压缸主要尺寸的确定 (4)确定液压泵的流量、压力和选择泵的规格 (5)液压阀的选择 (5)确定管道尺寸 (6)液压油箱容积的确定 (7)4.液压系统的验算 (6)压力损失的验算 (6)系统温升的验算 (8)某立式组合机床的动力滑台采用液压传动。
已知切削负载为31000N,滑台工进速度为50mm/min,快进、快退速度为6m/min,滑台(包括滑台上的动力头)的质量为1500kg,滑台对导轨的法向作用力为1500N,往复运动的加、减速时间为,滑台采用平面导轨,静、动摩擦系数分别为和,快速行程为180mm ,工进行程为50mm 。
试设计该机床的液压系统和液压缸。
1.工况分析首先根据已知条件,绘制运动部件的速度循环图,如图所示,然后计算各阶段的外负载并绘制负载图。
液压缸所受外负载F 包括三种类型,即Fw 为工作负载,对于金属切削机床来说,即为沿活塞运动方向的切削力,在本例中为31000N ;Fa —运动部件速度变化时的惯性负载;Ff —导轨摩擦阻力负载,启动时为静摩擦阻力,启动后为动摩擦阻力,对于平导轨可由下式求得G —运动部件重力;F Rn —垂直于导轨的工作负载,事例中为零;f —导轨摩擦系数,本例中取静摩擦系数,动摩擦系数为。
求得: F fs =*14700N=2940N F fa =*14700N=1470N上式中F fs 为静摩擦阻力,F fa 为动摩擦阻力。
g —重力加速度;△t —加速度或减速度,一般△t=~ △v —△t 时间内的速度变化量。
在本例中根据上述计算结果,列出各工作阶段所受的外负载(见表,并画出如图所示的 负载循环图。
图速度和负载循环图2.拟定液压系统原理图NF a 300605.068.914700=⨯⨯=(1)确定供油方式考虑到该机床在工作进给时负载较大,速度较低。
而在快进、快退时负载较小,速度较高。
从节省能量、减少发热考虑,泵源系统宜选用双泵供油或变量泵供油。
现采用限压式变量叶片泵。
(2)调速方式的选择在中小型专用机床的液压系统中,进给速度的控制一般采用节流阀或调速阀。
根据铣削类专用机床工作时对低速性能和速度负载特性都有一定要求的特点,决定采用限压式变量泵和调速阀组成的容积节流调速。
这种调速回路具有效率高、发热小和速度刚性好的特点,并且调速阀装在回油路上,具有承受负切削力的能力。
(3)速度换接方式的选择本系统采用电磁阀的快慢速换接回路,它的特点是结构简单、调节行程比较方便,阀的安装也较容易,但速度换接的平稳性较差。
若要提高系统的换接平稳性,则可改用行程阀切换的速度换接回路。
(4)夹紧回路的选择用二位四通电磁阀来控制夹紧、松开换向动作时,为了避免工作时突然失电而松开,应采用失电夹紧方式。
考虑到夹紧时间可调节和当进油路压力瞬时下降时仍能保持夹紧力,所以接入节流阀调速和单向阀保压。
在该回路中还装有减压阀,用来调节夹紧力的大小和保持夹紧力的稳定。
最后把所选择的液压回路组合起来,即可组合成图所示的液压系统原理图。
图 液压系统原理图3.液压系统的计算和选择液压元件液压缸主要尺寸的确定1)工作压力p 的确定。
工作压力p 可根据负载大小及机器的类型来初步确定,表取液压缸工作压力为3MPa 。
2)计算液压缸内径D 和活塞杆直径d 。
由负载图知最大负载F 为32470N ,按表可取P 2为,ηcm 为,考虑到快进、快退速度相等,取d /D 为。
将上述数据代入式可得根据指导书表,将液压缸内径圆整为标准系列直径D=125mm ;活塞杆直径d ,按d /D= 及表活塞杆直径系列取d=90mm 。
()[]mmD 1267.01305195.0103014.332470425=⎭⎬⎫⎩⎨⎧--⨯⨯⨯⨯⨯=按工作要求夹紧力由两个夹紧缸提供,考虑到夹紧力的稳定,夹紧缸的工作压力应低于进给液压缸的工作压力,现取夹紧缸的工作压力为, 回油背压力为零,ηcm 为,可得按表及表液压缸和活塞杆的尺系列,取夹紧液压缸的D 和d 分别为125mm 及90mm 。
按最低工进速度验算液压缸的最小稳定速度,由式可得式中q min 是由产品样本查得调速阀AQF3-E10B 的最小稳定流量为0.05L /min 。
本例中调速阀是安装在回油路上,故液压缸节流腔有效工作面积应选取液压缸有杆腔的实际面积,即可见上述不等式能满足,液压缸能达到所需低速。
3)计算在各工作阶段液压缸所需的流量确定液压泵的流量、压力和选择泵的规格1)泵的工作压力的确定 考虑到正常工作中进油管路有一定的压力损失,所以泵的工作压力为p p —液压泵最大工作压力; p 1—执行元件最大工作压力;∑△p —进油管路中的压力损失,初算时简单系统可取~,复杂系统取 ~,本例取。
上述计算所得的p p 是系统的静态压力,考虑到系统在各种工况的过渡阶段出现的动态压力往往超过静态压力。
另外考虑到一定的压力贮备量,并确保泵的寿命,因此选泵的额定压力p n 应满足p n ≥~ p p 。
中低压系统取小值,高压系统取大值。
在本例中p n = p p =。
2)泵的流量确定 液压泵的最大流量应为 q p —液压泵的最大流量;mm D 6.8995.0102514.31500045=⨯⨯⨯⨯=223min min 5101005.0cm cm v q A =⨯=〉min/42.9min /1042.96010201.04433322L m v D q =⨯=⨯⨯⨯⨯==--ππ()()min/35min /1035609.0125.044332222L m v d D q =⨯=⨯-⨯=-=-ππ快退快退(∑q)min同时动作的各执行元件所需流量之和的最大值。
如果这时溢流阀正进行工作,尚须加溢流阀的最小溢流量2~3L/min;K L—系统泄漏系数,一般取KL=~,现取KL=。
3)选择液压泵的规格根据以上算得的p p和q p,再查阅有关手册,液压阀的选择根据所拟定的液压系统图,按通过各元件的最大流量来选择液压元件的规格。
选定的液压元件如表所示。
油管内径尺寸一般可参照选用的液压元件接口尺寸而定,也可按管路允许流速进行计算。
本系统主油路流量为差动时流量q=76L/min,压油管的允许流速取u=4m/s,则内径d为若系统主油路流量按快退时取q=35L/min,则可算得油管内径d=13mm。
综合诸因素,现取油管的内径d为16mm。
吸油管同样可按上式计算(q=/min、v=1.5m/s),现参照YBX-40变量泵吸油口连接尺寸,取吸油管内径d为35mm。
液压油箱容积的确定本例为中压液压系统,液压油箱有效容量按泵的流量的5~7倍来确定,现选用容量为160L的油箱。
4.液压系统的验算已知该液压系统中进、回油管的内径均为16mm,各段管道的长度分别为:AB=0.3m,AC=1.7m,AD=1.7m,DE=2m。
选用L-HL32液压油,考虑到油的最低温度为15℃,查得15℃时该液压油的运动粘度ν=150cst=1.5cm 2/s ,油的密度ρ=920kg /m 3。
压力损失的验算1)工作进给时进油路压力损失。
运动部件工作进给时的最大速度为/min ,进给时的最大流量为/min ,则液压油在管内流速v 1为管道流动雷诺数Re l 为Re l <2300,可见油液在管道内流态为层流,其沿程阻力系数15.143.5757511===e R λ。
进油管道BC 的沿程压力损失△p l-1为查得换向阀4WE6E50/AG24的压力损失△p l-2=×106pa忽略油液通过管接头、油路板等处的局部压力损失,则进油路总压力损失△p 1为 2)工作进给时回油路的压力损失。
由于选用单活塞杆液压缸,且液压缸有杆腔的工作面积为无杆腔工作面积的二分之一,则回油管道的流量为进油管道的二分之一,则 回油管道的沿程压力损失△p 2-1为查产品样本知换向阀3WE6A50/AG24的压力损失△p 2-2= X 106pa ,换向阀4WE6E50/AG24的压力损失△p 2-3=×106pa ,调速阀2FRM5—20/6的压力损失△p 2-4= ×106pa 。
回油路总压力损失△p 2为pa p p p p p 664232221221055.010)5.0025.0025.0001.0(⨯=⨯+++=∆+∆+∆+∆=∆----3)变量泵出口处的压力p p4)快进时的压力损失。
快进时液压缸为差动连接,自汇流点A 至液压缸进油口C 之间的管路AC 中,流量为液压泵出口流量的两倍即/min ,AC 段管路的沿程压力损失△p 1-l 为同样可求管道AB 段及AD 段的沿程压力损失△p l-2和△p l-3为查产品样本知,流经各阀的局部压力损失为4EW6E50/AG24的压力损失△p 2-1=×106pa ;3EW6E50/AG24的压力损失△p 2-2=×106pa 。
据分析在差动连接中,泵的出口压力p p 为快退时压力损失验算从略。
上述验算表明无需修改原设计。
系统温升的验算在整个工作循环中,工进阶段所占的时间最长,为了简化计算,主要考虑工进时的发热量。
一般情况下,工进速度大时发热量较大,由于限压式变量泵在流量不同时,效率相差极大,所以分别计算最大、最小时的发热量,然后加以比较,取数值大者进行分析。
当v=5cm /min 时此时泵的效率为,泵的出口压力为,则有 此时的功率损失为当v=120cm /min 时,q=/min ,总效率η= 则kW P 718.07.06042.92.3=⨯⨯=输入可见在工进速度低时,功率损失为,发热量最大。
假定系统的散热状况一般取K=10×10-3kW/(cm 2.℃),油箱的散热面积A 为 系统的温升为验算表明系统的温升在许可范围内。