工厂常见八大浪费完整版
八大浪费

八大浪费1.不良、修理的浪费所谓不良、修理的浪费,指的是由于工厂内出现不良品,需要进行处置的时间、人力、物力上的浪费,以及由此造成的相关损失。
这类浪费具体包括:材料的损失、不良品变成废品;设备、人员和工时的损失;额外的修复、鉴别、追加检查的损失;有时需要降价处理产品,或者由于耽误出货而导致工厂信誉的下降。
2.加工的浪费加工的浪费也叫过分加工的浪费,主要包含两层含义:第一是多余的加工和过分精确的加工,例如实际加工精度过高造成资源浪费;第二是需要多余的作业时间和辅助设备,还要增加生产用电、气压、油等能源的浪费,另外还增加了管理的工时。
3.动作的浪费动作的浪费现象在很多企业的生产线中都存在,常见的动作浪费主要有以下12种:两手空闲、单手空闲、作业动作突然停止、作业动作过大、左右手交换、步行过多、转身的角度太大,移动中变换“状态”、不明技巧、伸背动作、弯腰动作以及重复动作和不必要的动作等,这些动作的浪费造成了时间和体力上的不必要消耗。
4.搬运的浪费从JIT的角度来看,搬运是一种不产生附加价值的动作,而不产生价值的工作都属于浪费。
搬运的浪费具体表现为放置、堆积、移动、整列等动作浪费,由此而带来物品移动所需空间的浪费、时间的浪费和人力工具的占用等不良后果。
国内目前有不少企业管理者认为搬运是必要的,不是浪费。
因此,很多人对搬运浪费视而不见,更谈不上去消灭它。
也有一些企业利用传送带或机器搬运的方式来减少人工搬运,这种做法是花大钱来减少工人体力的消耗,实际上并没有排除搬运本身的浪费。
5.库存的浪费按照过去的管理理念,人们认为库存虽然是不好的东西,但却是必要的。
JIT的观点认为,库存是没有必要的,甚至认为库存是万恶之源。
如图1-1,由于库存很多,将故障、不良品、缺勤、点点停、计划有误、调整时间过长、品质不一致、能力不平衡等问题全部掩盖住了。
例如,有些企业生产线出现故障,造成停机、停线,但由于有库存而不至于断货,这样就将故障造成停机、停线的问题掩盖住了,耽误了故障的排除。
八大浪费及相关知识(全)
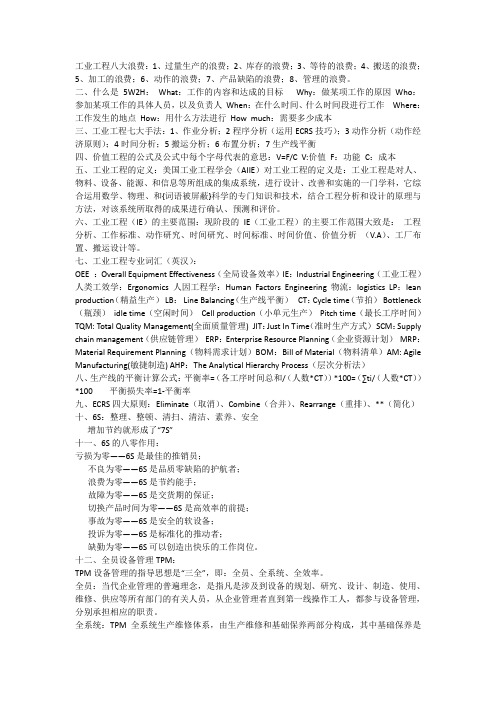
工业工程八大浪费:1、过量生产的浪费;2、库存的浪费;3、等待的浪费;4、搬送的浪费;5、加工的浪费;6、动作的浪费;7、产品缺陷的浪费;8、管理的浪费。
二、什么是5W2H:What:工作的内容和达成的目标Why:做某项工作的原因 Who:参加某项工作的具体人员,以及负责人 When:在什么时间、什么时间段进行工作 Where:工作发生的地点 How:用什么方法进行 How much:需要多少成本三、工业工程七大手法:1、作业分析;2程序分析(运用ECRS技巧);3动作分析(动作经济原则);4时间分析;5搬运分析;6布置分析;7生产线平衡四、价值工程的公式及公式中每个字母代表的意思:V=F/C V:价值F:功能C:成本五、工业工程的定义:美国工业工程学会(AIIE)对工业工程的定义是:工业工程是对人、物料、设备、能源、和信息等所组成的集成系统,进行设计、改善和实施的一门学科,它综合运用数学、物理、和{词语被屏蔽}科学的专门知识和技术,结合工程分析和设计的原理与方法,对该系统所取得的成果进行确认、预测和评价。
六、工业工程(IE)的主要范围:现阶段的IE(工业工程)的主要工作范围大致是:工程分析、工作标准、动作研究、时间研究、时间标准、时间价值、价值分析(V.A)、工厂布置、搬运设计等。
七、工业工程专业词汇(英汉):OEE :Overall Equipment Effectiveness(全局设备效率)IE:Industrial Engineering(工业工程)人类工效学:Ergonomics 人因工程学:Human Factors Engineering 物流:logistics LP:lean production(精益生产)LB:Line Balancing(生产线平衡) CT:Cycle time(节拍)Bottleneck (瓶颈)idle time(空闲时间)Cell production(小单元生产) Pitch time(最长工序时间)TQM: Total Quality Management(全面质量管理) JIT:Just In Time(准时生产方式)SCM:Supply chain management(供应链管理)ERP:Enterprise Resource Planning(企业资源计划)MRP:Material Requirement Planning(物料需求计划)BOM:Bill of Material(物料清单)AM: Agile Manufacturing(敏捷制造) AHP:The Analytical Hierarchy Process(层次分析法)八、生产线的平衡计算公式:平衡率=(各工序时间总和/(人数*CT))*100=(∑ti/(人数*CT))*100 平衡损失率=1-平衡率九、ECRS四大原则:Eliminate(取消)、Combine(合并)、Rearrange(重排)、**(简化)十、6S:整理、整顿、清扫、清洁、素养、安全增加节约就形成了“7S”十一、6S的八零作用:亏损为零――6S是最佳的推销员;不良为零――6S是品质零缺陷的护航者;浪费为零――6S是节约能手;故障为零――6S是交货期的保证;切换产品时间为零――6S是高效率的前提;事故为零――6S是安全的软设备;投诉为零――6S是标准化的推动者;缺勤为零――6S可以创造出快乐的工作岗位。
生产中的八大浪费
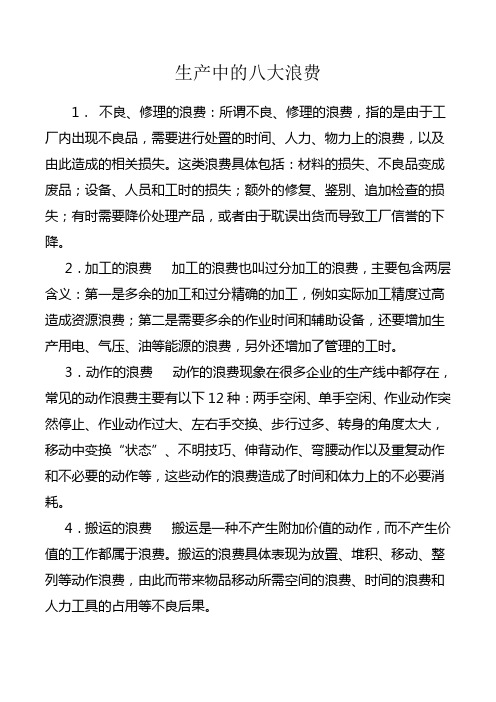
生产中的八大浪费1.不良、修理的浪费:所谓不良、修理的浪费,指的是由于工厂内出现不良品,需要进行处置的时间、人力、物力上的浪费,以及由此造成的相关损失。
这类浪费具体包括:材料的损失、不良品变成废品;设备、人员和工时的损失;额外的修复、鉴别、追加检查的损失;有时需要降价处理产品,或者由于耽误出货而导致工厂信誉的下降。
2.加工的浪费加工的浪费也叫过分加工的浪费,主要包含两层含义:第一是多余的加工和过分精确的加工,例如实际加工精度过高造成资源浪费;第二是需要多余的作业时间和辅助设备,还要增加生产用电、气压、油等能源的浪费,另外还增加了管理的工时。
3.动作的浪费动作的浪费现象在很多企业的生产线中都存在,常见的动作浪费主要有以下12种:两手空闲、单手空闲、作业动作突然停止、作业动作过大、左右手交换、步行过多、转身的角度太大,移动中变换“状态”、不明技巧、伸背动作、弯腰动作以及重复动作和不必要的动作等,这些动作的浪费造成了时间和体力上的不必要消耗。
4.搬运的浪费搬运是一种不产生附加价值的动作,而不产生价值的工作都属于浪费。
搬运的浪费具体表现为放置、堆积、移动、整列等动作浪费,由此而带来物品移动所需空间的浪费、时间的浪费和人力工具的占用等不良后果。
5.库存的浪费由于库存很多,将故障、不良品、缺勤、计划外停机、计划有误、调整时间过长、品质不一致、能力不平衡等问题全部掩盖住了。
6.制造过多或过早的浪费制造过多或过早,提前用掉了生产费用,不但没有好处,还隐藏了由于等待所带来的浪费,失去了持续改善的机会。
有些企业由于生产能力比较强大,为了不浪费生产能力而不中断生产,增加了在制品,使得制品周期变短、空间变大,还增加了搬运、堆积的浪费。
此外,制造过多或过早,会带来庞大的库存量,利息负担增加,不可避免地增加了贬值的风险。
7.等待的浪费由于生产原料供应中断、作业不平衡和生产计划安排不当等原因造成的无事可做的等待,被称为等待的浪费。
工业工程八大浪费

工业工程八大浪费:1、过量生产的浪费;2、库存的浪费;3、等待的浪费;4、搬送的浪费;5、加工的浪费;6、动作的浪费;7、产品缺陷的浪费;8、管理的浪费。
二、什么是5W2H:What:工作的内容和达成的目标Why:做某项工作的原因 Who:参加某项工作的具体人员,以及负责人 When:在什么时间、什么时间段进行工作 Where:工作发生的地点 How:用什么方法进行 How much:需要多少成本三、工业工程七大手法:1、作业分析;2程序分析(运用ECRS技巧);3动作分析(动作经济原则);4时间分析;5搬运分析;6布置分析;7生产线平衡四、价值工程的公式及公式中每个字母代表的意思:V=F/C V:价值F:功能C:成本五、工业工程的定义:美国工业工程学会(AIIE)对工业工程的定义是:工业工程是对人、物料、设备、能源、和信息等所组成的集成系统,进行设计、改善和实施的一门学科,它综合运用数学、物理、和{词语被屏蔽}科学的专门知识和技术,结合工程分析和设计的原理与方法,对该系统所取得的成果进行确认、预测和评价。
六、工业工程(IE)的主要范围:现阶段的IE(工业工程)的主要工作范围大致是:工程分析、工作标准、动作研究、时间研究、时间标准、时间价值、价值分析(V.A)、工厂布置、搬运设计等。
七、工业工程专业词汇(英汉):OEE :Overal l Equipm ent Effect ivene ss(全局设备效率)IE:Indust rialEngine ering(工业工程)人类工效学:Ergono mics人因工程学:HumanFactor s Engine ering物流:logist ics LP:lean produc tion(精益生产)LB: Line Balanc ing(生产线平衡) CT:Cycletime(节拍) Bottle neck(瓶颈)idle time(空闲时间) Cell produc tion(小单元生产) Pitchtime(最长工序时间)TQM: TotalQualit y Manage ment(全面质量管理) JIT:Just In Time(准时生产方式)SCM:Supply chainmanage ment(供应链管理)ERP:Enterp riseResour ce Planni ng(企业资源计划)MRP:Materi al Requir ement Planni ng(物料需求计划)BOM:Bill of Materi al(物料清单)AM: AgileManufa cturi ng(敏捷制造) AHP:The Analyt icalHierar chy Proces s(层次分析法)八、生产线的平衡计算公式:平衡率=(各工序时间总和/(人数*CT))*100=(∑ti/(人数*CT))*100 平衡损失率=1-平衡率九、ECRS四大原则:Elimin ate(取消)、Combin e(合并)、Rearra nge(重排)、**(简化)十、6S:整理、整顿、清扫、清洁、素养、安全增加节约就形成了“7S”十一、6S的八零作用:亏损为零――6S是最佳的推销员;不良为零――6S是品质零缺陷的护航者;浪费为零――6S是节约能手;故障为零――6S是交货期的保证;切换产品时间为零――6S是高效率的前提;事故为零――6S是安全的软设备;投诉为零――6S是标准化的推动者;缺勤为零――6S可以创造出快乐的工作岗位。
常见的八大浪费

常见的八大浪费在工厂中最为常见的浪费主要有八大类,分别是:不良、修理的浪费,加工的浪费,动作的浪费,搬运的浪费,库存的浪费,制造过多?过早的浪费,等待的浪费和管理的浪费。
下面具体分析各类浪费现象。
1.不良、修理的浪费:所谓不良、修理的浪费,指的是由于工厂内出现不良品,需要进行处置的时间、人力、物力上的浪费,以及由此造成的相关损失。
这类浪费具体包括:材料的损失、不良品变成废品;设备、人员和工时的损失;额外的修复、鉴别、追加检查的损失;有时需要降价处理产品,或者由于耽误出货而导致工厂信誉的下降。
不得不说:不良的本身就是错误的产物,为什么产生不良,我们是不是要做5Why,现实工作中我们会找各种各样的借口,事实上少量的不良时我们缺少发现的决心,大量问题出现时,我们找到的大部分是别人的过失,独独少了我们发现少量不良时的自己2.加工的浪费加工的浪费也叫过分加工的浪费,主要包含两层含义:第一是多余的加工和过分精确的加工,例如实际加工精度过高造成资源浪费;第二是需要多余的作业时间和辅助设备,还要增加生产用电、气压、油等能源的浪费,另外还增加了管理的工时。
不得不说:加工这个阶段的浪费我们已习以为常,有时我们甚至认为加工如果是浪费的话,何时不是浪费,其实这个环节的问题日久就会成疾,多余的作业时间本身就是浪费生产成本,我们盯的是人工,但不敢发现这一块。
3.动作的浪费动作的浪费现象在很多企业的生产线中都存在,常见的动作浪费主要有以下12种:两手空闲、单手空闲、作业动作突然停止、作业动作过大、左右手交换、步行过多、转身的角度太大,移动中变换“状态”、不明技巧、伸背动作、弯腰动作以及重复动作和不必要的动作等,这些动作的浪费造成了时间和体力上的不必要消耗。
不得不说:这可能就是IE工程发展的牺牲品,把人员当成机器。
当我们考虑动作浪费的时候,有没有考虑到人员的承受力和疲劳度,欲速则不达。
当然减少大规模动作也是对工作人的一种尊重。
生产车间常见的八大浪费
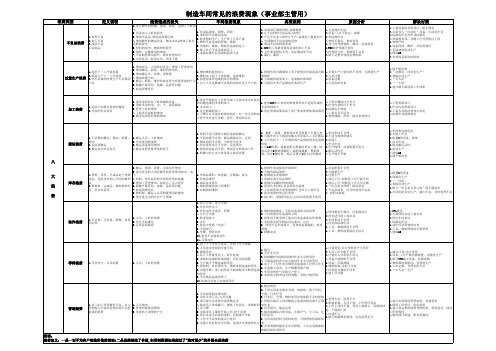
1.聊天 2.无作业发呆 3.射频螺杆切割机切割时作业人员的等待 4.天线端盖机在自动点胶时作业人员的等待 5.由于下工位作业员堆积而造成前工位停止作业 6.中途插入急单,生产频繁切换产线 7.车间突然停气导致生产停工 8.未按签字档布局及时调整,导致产线停线
1.计划变更/设计变时时产生等待 2.人员工作分配不合理 3.计划对人员需求不均匀 4.设备产能搭配不合理 5.设备、仪器故障 6.物料短缺,送料不及时 7.信息流与物流不同步 8.前工序问题
8.出货延误、取消定单,信誉下降
典型案例
原因分析
1.未请领正确的材料,用错材料 2.让不良材料当良品流入制程 3.产生不良未立即停止生产,造成返工数量加大 4.交调测试不良造成的返修 5.调试不良的拆装重调 C加工参数设错而造成的加工不良 7.文件要求指标不看,实际测试却不良 8.漏打、漏焊
1. 橱柜、油筒、材料供应处等放置于不便之处 1.车间布局不合理
2.天线车间大天线因电梯太窄而靠人工手扛搬运 2.不适当的摆放储存
3.工序间因下一工序堆积将产品堆放到旁边的物 3.单能工
料架
4.坐式作业
4.以L52为例,盖板装配完要做时效去三楼,时 5.生产线体、设备配置不恰当
效完在去5楼紧固螺钉,装配线路板,整机联 6.搬运活性差
1.工程重新设计 2.作业内容重新设计 3.工装夹具的改善和自动化 4.标准作业的彻底化
搬运浪费
1.不必要的搬运、移动、放置、 1.搬运人员、工时增加
转动
2.空间使用的浪费
2.长距离搬运
3.搬运设备费用增加
3.搬运流动灵活性差
4.搬运过程质量事故的发生
1.材料不适当摆放与储存造成的搬运 2.平面布置不合理,搬运路线过长、迂回 3.物流组织不合理,中转环节过多 4.作业流程设计不合理,反复移动 5.检验状态标识不清,增加区分和移动工作 6.机械与其它永久性设备之错误安置
生产中的八大浪费
生产中的八大浪费1.不良、修理的浪费:所谓不良、修理的浪费,指的是由于工厂内出现不良品,需要进行处置的时间、人力、物力上的浪费,以及由此造成的相关损失。
这类浪费具体包括:材料的损失、不良品变成废品;设备、人员和工时的损失;额外的修复、鉴别、追加检查的损失;有时需要降价处理产品,或者由于耽误出货而导致工厂信誉的下降。
2.加工的浪费加工的浪费也叫过分加工的浪费,主要包含两层含义:第一是多余的加工和过分精确的加工,例如实际加工精度过高造成资源浪费;第二是需要多余的作业时间和辅助设备,还要增加生产用电、气压、油等能源的浪费,另外还增加了管理的工时。
3.动作的浪费动作的浪费现象在很多企业的生产线中都存在,常见的动作浪费主要有以下12种:两手空闲、单手空闲、作业动作突然停止、作业动作过大、左右手交换、步行过多、转身的角度太大,移动中变换“状态”、不明技巧、伸背动作、弯腰动作以及重复动作和不必要的动作等,这些动作的浪费造成了时间和体力上的不必要消耗。
4.搬运的浪费搬运是一种不产生附加价值的动作,而不产生价值的工作都属于浪费。
搬运的浪费具体表现为放置、堆积、移动、整列等动作浪费,由此而带来物品移动所需空间的浪费、时间的浪费和人力工具的占用等不良后果。
5.库存的浪费由于库存很多,将故障、不良品、缺勤、计划外停机、计划有误、调整时间过长、品质不一致、能力不平衡等问题全部掩盖住了。
6.制造过多或过早的浪费制造过多或过早,提前用掉了生产费用,不但没有好处,还隐藏了由于等待所带来的浪费,失去了持续改善的机会。
有些企业由于生产能力比较强大,为了不浪费生产能力而不中断生产,增加了在制品,使得制品周期变短、空间变大,还增加了搬运、堆积的浪费。
此外,制造过多或过早,会带来庞大的库存量,利息负担增加,不可避免地增加了贬值的风险。
7.等待的浪费由于生产原料供应中断、作业不平衡和生产计划安排不当等原因造成的无事可做的等待,被称为等待的浪费。
八大浪费
八大浪费TIMWOOD1、生产过剩。
过早或过多地生产出产品,这通常会造成其他的浪费,例如人员过多、因存货过多而导致储存与输送成本。
存货可能指的是实物存货,或是排队等候的大批信息。
2、在现场等候的时间。
员工只是在一旁监视自动化机器,还是必须站在一旁等候下一个处理步骤、工具、供应、零部件等,或是因为存货用完、整批处理延迟、机器设备停工、生产力停滞不前等因素造成员工暂时没有工作可做。
3、不必要的运输。
在流程中把在制品从一地搬运到另一地(即便只是短距离);或是必须进出仓库或在流程之间搬运原材料、零部件或最终成品。
4、过度处理或不正确的处理。
采取不必要的步骤以处理零部件;因为工具与产品设计不良,导致不必要的动作及产生瑕疵而造成缺乏效率的处理;当产品超出必要的质量时,也会造成浪费。
有时,必须做一些额外的“工作”,以填补多出的时间,避免无所事事地等候。
5、存货过剩。
过多的原材料、在制品或者最终的成品,导致较长的提前期,堆积过时品、毁损品、较高的运输与储存成本及延迟。
此外,过多的存货还造成其他的隐性问题,例如生产不均衡、供应者延迟递送、瑕疵品、机器设备停工、拉长准备期等。
6、不必要的移动搬运。
员工在执行工作的过程中,必须做一些不必要、不能创造价值的动作,例如寻找、前往取得或堆放零部件和工具等等。
此外,走动也是浪费。
7、瑕疵。
生产出瑕疵品或必须修改的东西。
修理或重做、报废、更换、检验等都代表浪费的处理、时间和精力。
8、未被使用的员工创造力。
由于未使员工参与未能倾听员工意见而造成未能善用员工的时间、构想、技能,从而使员工失去改进和学习的机会。
常见的八大浪费在工厂中最为常见的浪费主要有八大类,分别是:不良、修理的浪费,过分加工的浪费,动作的浪费,搬运的浪费,库存的浪费,制造过多?过早的浪费,等待的浪费和管理的浪费。
下面具体分析各类浪费现象。
1.不良、修理的浪费所谓不良、修理的浪费,指的是由于工厂内出现不良品,需要进行处置的时间、人力、物力上的浪费,以及由此造成的相关损失。
八大浪费(最新)
按照过去的管理理念,人们认为库存虽然是不好的东西, 但却是必要的。精益生产的观点认为,库存是没有必要 的,甚至认为库存是万恶之源。
库存掩盖问题
水平线
故障
不良品
运输问题
点点停 能力不平衡
调整时间长
协作问题Biblioteka 缺勤品质不一致计划有误
6、制造过多(早)的浪费
内容:不必要的时间生产不必要的东西。造成流程阻碍,不良 的发生、库存,半成品的增加,材料、零件的滥用,资金周 转率下降,计划柔软性的阻碍。
4、搬运的浪费
内容:具体表现为放置、堆积、移动、整列,灵活性差等动作浪费, 由此而带来物品移动所需空间的浪费、时间的浪费 和人力工具的 占用等不良后果。 自我问答:为何搬运?方法是计程车或公车?
改善:U 字型设备的配置
流程作业 站著工作 多能工活性指数提升 少人化
目前普遍认为搬运是必要的,不是浪费。因此,很多人对搬运浪费 视而不见,更谈不上去消灭它。也有人利用传送带或机器搬运的方 式来减少人工搬运,这种做法是花大钱来减少工人体力的消耗,实 际上并没有排除搬运本身的浪费。
1、不良、修理的浪费
内容:材料的损失、不良品变成废品;设备、人员和工时的损失; 额外的修复、鉴别、追加检查的损失;有时需要降价处理 产品,或者由于耽误出货而导致工厂信誉的下降。
自我问答:为何曾发生?是否有再发防止的措施?
改善:自动化
愚巧化(防呆化) 作业标准 全数检查 在工程中造就品质 无取放的流程作业 确立品质保证体系
自我问答:为何要多做?停止机制;换线改善呢。 改善: Full Work System 一个流程 看板 少人化 一次性计划 平均化生产
总结:制造过多或过早,提前用掉了生产费用,不但没有好处, 还隐藏了由于等待所带来的浪费,失去了持续改善的机会。
精益生产八大浪费记忆口诀
精益生产八大浪费记忆口诀精益生产是一种管理方法,旨在提高生产效率和质量,减少浪费。
其核心理念是避免八大浪费。
下面是记忆口诀,用以帮助记忆:1.待料浪费:材料等待加工,长时间占用资源,是一种浪费。
2.过程浪费:流程不顺畅,存在重复、无效操作,是一种浪费。
3.运输浪费:材料或产品频繁运输,增加成本和时间,是一种浪费。
4.库存浪费:过多的库存占用空间和资金,增加了风险和成本,是一种浪费。
5.缺陷浪费:出现产品缺陷,需要修复或重做,增加了成本和工作量,是一种浪费。
6.人力浪费:人员不合理分配,或者没有进行充分培训,浪费了人力资源,是一种浪费。
7.等待浪费:因为某些环节的停顿而产生等待,增加了生产周期,是一种浪费。
8.过产量浪费:生产超出需求,过多的产品无法及时销售,增加了风险和成本,是一种浪费。
这是八大浪费的记忆口诀。
通过记住这八个关键词,我们可以更好地理解和应用精益生产的原则。
下面我们将详细介绍每种浪费并提供例子。
第一种浪费,即待料浪费,指的是材料等待加工的时间过长,占用了资源。
比如,在一个工厂中,原材料被放在一边等待加工,而加工设备被其他任务占用,这样就产生了待料浪费。
第二种浪费,即过程浪费,指的是流程不顺畅,存在重复、无效操作。
比如,在一个生产线上,同一个工序被重复进行,或者某些操作并不对最终产品产生贡献,这样就产生了过程浪费。
第三种浪费,即运输浪费,指的是材料或产品频繁运输,增加了成本和时间。
比如,在一个仓库中,产品需要多次搬运和运输,而这些运输过程并没有增加价值,这就是一种浪费。
第四种浪费,即库存浪费,指的是过多的库存占用空间和资金,增加了风险和成本。
比如,一个超市因为销售不畅,积压了大量商品,这些库存无法及时销售,就产生了库存浪费。
第五种浪费,即缺陷浪费,指的是出现产品缺陷,需要修复或重做,增加了成本和工作量。
比如,一个生产线上的产品因为质量问题,需要进行多次修复或者全部报废,这就是一种缺陷浪费。
- 1、下载文档前请自行甄别文档内容的完整性,平台不提供额外的编辑、内容补充、找答案等附加服务。
- 2、"仅部分预览"的文档,不可在线预览部分如存在完整性等问题,可反馈申请退款(可完整预览的文档不适用该条件!)。
- 3、如文档侵犯您的权益,请联系客服反馈,我们会尽快为您处理(人工客服工作时间:9:00-18:30)。
工厂常见八大浪费完整版一、品质缺陷(不良品、修理的浪费)
◆任何的不良品产生,皆造成材料、机器、人工等的浪费。
◆及早发现不良品,容易确定不良来源,进而减少不良品的产生。
◆关键是第一次要把事情做对,做到“零缺陷”
由于工厂内出现不良品,需要进行处置的时间、人力、物力上的浪费,以及由此造成的相关损失。
这类浪费具体包括:材料的损失、不良品变成废品;设备、人员和工时的损失;额外的修复、鉴别、追加检查的损失;有时需要降价处理产品,或者由于耽误出货而导致工厂信誉的下降。
二、处理(加工浪费)
◆定义:指的是与工程进度及加工精度无关的不必要的加工,也叫过分加工的浪费,主要包含两层含义:第一是多余的加工和过分精确的加工,例如实际加工精度过高造成资源浪费;第二是需要多余的作业时间和辅助设备,还要增加生产用电、气压、油等能源的浪费,另外还增加了管理的工时。
◆有一些加工程序是可以省略、替代、重组或合并。
◆很多时候会习惯并认为现在的做法较好
三、动作的浪费
12种动作浪费:
◆两手空闲◆单手空闲◆不连贯停顿◆幅度太大◆左右手交换◆步行多
◆转身角度大◆移动中变换状态◆不明技巧◆伸背动作◆弯腰动作◆重复不必要动作
这些动作的浪费造成了时间和体力上的不必要消耗。
四、运输(搬运的浪费)
◆国内目前有不少企业管理者认为搬运是必要的,不是浪费。
因此,很多人对搬运浪费视而不见,更谈不上去消灭它。
从JIT的角度来看,搬运是一种不产生附加价值的动作,而不产生价值的工作都属于浪费。
◆用“输送带”的方式来克服,行吗这种做法是花大钱来减少工人体力的消耗,实际上并没有排除搬运本身的浪费。
1、取放浪费;
2、等待浪费;
3、在制品过多浪费;
4、空间浪费。
◆搬运的浪费具体表现为放置、堆积、移动、整列等动作浪费,由此而带来物品移动所需空间的浪费、时间的浪费和人力工具的占用等不良后果。
五、库存的浪费
库存过多掩盖问题,降低库存暴露问题
◆精益生产认为:“库存是万恶之源” ,所有改善行动皆会直接或间接地和消除库存有关。
①产生不必要的搬运、堆积、放置、防护处理、找寻等浪费②使先进先出的作业困难
③损失利息及管理费用④物品的价值会减低,变成呆滞品
⑤占用厂房空间、造成多余工场、仓库建设等⑥设备能力及人员需求的误判
◆因库存造成无形损失,绝不亚上述有形损失,精益生产者认为库存会隐藏问题,而“问题”在精益生产者被认为是宝藏,问题如果能不断地被发现解决,则利益便会不断地产生
1、没有管理的紧张感,阻碍改进:
2、库存量一多,因机械故障、不良产品所带来的不利后果不能马上显现出来,因而也不会产生对策。
3、由于有了充足的库存,出现问题时可以用库存先顶上,问题就可以慢慢解决甚至不用解决,最起码是被掩盖住了,不急迫了,不会被上级追究了,于是乎本部门的工作成绩就出来了。
按照过去的管理理念,人们认为库存虽然是不好的东西,但却是必要的。
JIT的观点认为,库存是没有必要的,甚至认为库存是万恶之源。
由于库存很多,将故障、不良品、缺勤、点点停、计划有误、调整时间过长、品质不一致、能力不平衡等问题全部掩盖住了。
例如,有些企业生产线出现故障,造成停机、停线,但由于有库存而不至于断货,这样就将故障造成停机、停线的问题掩盖住了,耽误了故障的排除。
如果降低库存,就能将上述问题彻底暴露于水平面,进而能够逐步地解决这些库存浪费。
六、过渡生产(制造过多或过早浪费)
◆TPS强调的是“适时生产”。
◆多做能提高效率,提早做好能减少产能损失(不做白不做,机器还不是一样停着)
1、提早用掉了材料费、人工费而已,并不能得到什么好处。
2、把“等待浪费”隐藏,使管理人员漠视等待的发生和存在。
3、积压在制品,使生产周期L/T变长无形的),而且会使现场工作空间变大,不知不觉中吞蚀我们的利润。
4、产生搬运、堆积浪费,先进先出变得困
难。
制造过多或过早,提前用掉了生产费用,不但没有好处,还隐藏了由于等待所带来的浪费,失去了持续改善的机会。
有些企业由于生产能力比较强大,为了不浪费生产能力而不中断生产,增加了在制品,使得制品周期变短、空间变大,还增加了搬运、堆积的浪费。
此外,制造过多或过早,会带来庞大的库存量,利息负担增加,不可避免地增加了贬值的风险。
七、等待的浪费
◆生产线的品种切换◆工作量少时,便无所事事◆时常缺料,设备闲置
◆上工序延误,下游无事可做◆设备发生故障◆生产线工序不平衡
◆有劳逸不均的现象◆制造通知或设计图未送达
由于生产原料供应中断、作业不平衡和生产计划安排不当等原因造成的无事可做的等待,被称为等待的浪费。
生产线上不同品种之间的切换,如果准备工作不够充分,势必造成等待的浪费;每天的工作量变动幅度过大,有时很忙,有时造成人员、设备闲置不用;上游的工序出现问题,导致下游工序无事可做。
此外,生产线劳逸不均等现象的存在,也是造成等待浪费的重要原因。
八、管理的浪费
管理浪费指的是问题发生以后,管理人员才采取相应的对策来进行补救而产生的额外浪费。
管理浪费是由于事先管理不到位而造成的问题,科学的管理应该是具有相当的预见性,有合理的规划,并在事情的推进过程中加强管理、控制和反馈,这样就可以在很大程度上减少管理浪费现象的发生
如何消除时间,人员,管理之浪费
■明确那些是高价值与低价值的工作
■应用20/80原理
■工作计划管理与目标管理有利于时间管理
企业存在哪些时间上浪费的
1) 生产周期时间长
2) 采购时间偏长
3) 出现异常情况时处理不及时
4) 生产线转换MODEL时切换时间过长
5) 换机,换模时间过长
6) 工作计划不合理,导致时间上的浪费
7) 工作量变动太大,出现人员,设备闲置.
8) 经常因物料缺料或上工序发生延误而使机器闲置或生产线停拉;
10) 机器设备经常发生故障;
11) 生产线未能取得平衡.
12) 部门之间配合不协调,导致时间决策上浪费;
13) 会议过多,造成的浪费.
如何消除时间上的浪费
■根据浪费时间的原因,制定具体的应对解决措施
■建立,完善各种制度和运作流程.
■建立时间标准并适时改善调整
■切实执行(跟进,监督)
■定期检讨,评估,和持续改善.
消除人员浪费的意义:
1) 提高工作效率
2) 降低劳务费用
3) 减少员工消极怠工,推托之情型发生,并减少由此引发的其它浪费发掘潜在的过剩人员
1) 如何发掘生产线上的人员过剩
2) 如何发掘管理人员过剩
3) 如何发掘职能部门人员过程
如何消除人员上的浪费
1) 分析存在那些潜在的过剩人员
A,定岗定员
B,岗位设置的合理性
C,工作量的饱和程度
2) 无益工作的剔除
A,明确那些是无益的工作
B,工作流程的精简,合并
3) 改进操作和设备,提高生产效率,实现少人化如何消除人员上的浪费
1) 重新调整组织结构,精减人员
2) 扩大职责范围,管理幅度
3) 充分授权
如何减少管理工作中的八大浪费
1,管理要素不能得有效利用的闲置浪费
2,无目标,无计划造成的管理成本浪费
3,缺乏凝集力的协调浪费
4,低效造成的效率浪费
5,按个人意愿造成的无序浪费
6,缺乏责任心和主动精神的等待浪费
7,敷衍了事的应付浪费
8,因监督管理所增设管理人员之浪费
日常管理容易陷入的八大误区
1,我没法管喜欢做技术工作—不善于管人
2,是我的功劳.习惯依靠个人努力去完成任务—单干,不善于建立有效的工作网络,工作团队
3,主要由我做,我真不放心.事无巨细,不善于授权一把抓
4,管它有没有完成虽有工作目标,但缺乏目标控制
5,我喜欢随意,走一步看一步.不善于,不习惯做计划
6,怕什么有问题再说.救火现象普遍
7,谁能帮帮我未经过系统的管理技能培训,知识不够
8,啊弥陀佛,幸好没什么变化,没出差错.
主管人员常犯的八种错误
(1)缺乏主人与责任意识,拒绝承担个人责任
(2)"本位主义"思想严重,只注重个人与部门利益
(3)管理方式单一,缺乏针对性领导
(4)未能很好地培训与引导下属
(5)角色错位
(6)欠缺自律,作风随意,忽略负面影响
(7)工作缺乏跟踪与监控
(8)用人失误,包庇能力不足的人
成功主管的八项准则
(1)明确的目标
(2)做正确的事
(3)合作致胜
(4)积极的心态
(5)沟通无极限
(6)以主人自居
(7)在客户身边
(8)追求卓越
主管人员的类型分析
强迫压制型:固执守旧,过分压制员工,害怕员工威胁他的地位
哥们义气型:对待员工常常称兄道弟,讲哥们义气,在工作中感情用事,缺乏原则性,不能发挥主管应有作用
教练型:即有技术又懂管理,注重培训员工和班组团队的建设,有明确的目标意识,主动发现并解决问题
劳动模范型:工作能踏踏实实,勤勤恳恳,只知道自己做事,不会管理员工,不适合担任领导工作
大撒把型:不乐意做管理人员,做一天和尚撞一天钟,工作得过且过,没有责任心,采取无为而治的做法,徒有虚名
唯命是从型:强调绝对服从,对上级是忠心耿耿,而且毫不怀疑与抗拒,但也绝不会主动做事,一切听从上级的指示,不求有功但求无过.往往缺乏创新和管理能力
生产技术型:技术业务能手,但缺乏人际关系协调能力,工作方法简单,常常用对待机器的方法对待员工。