推荐-优秀防护罩的冲压模具设计 精品
防护罩注塑模设计

该 零 件 精 度 要 求较 高 , 需 3个 方 向 ( 在 同一 且 不
平 面 上 ) 芯成 型 , 模 具加 工 要 求严 格 。 抽 对
零 件 在模 具 中需 采 用 3个 方 向 ( 在 问 一 不 平 面上 ) 芯 成 型 , 采 用普 通 抽 结 构 外 。 由 抽 除
除 后会 留下 疤 痕 , 此 处 将 来 有 标 牌 覆 盖 , 影 但 不 响 零件 外 观 , 且 大 大 简化 了模 具 结 构 , 免 了 而 避
采 用点 浇 口三 板 式 的模 具 结 构 , 证 了零 件 成 保
于零 件 两 侧各 有 倾 斜 4 。 5 的异 形 孔 , 且 孑 内 有 并 L
防护罩的冲压模具设计

2)为防磨损,应选用合金元素高的材料
3)对于大型冲模应选用淬透性好的材料
4)为保持钢材硬度能力,要选用耐回火性高的含铬、钼合金钢
综上所述,该工件的精度及结构尺寸都能满足冲压工艺要求,工件的拉深工艺性较好。该工件在满足冲压工艺性要求的前提下,采用的冲压基本工序是落料、拉深、翻边。
1.2 材料
冲压工艺对材料的基本要求主要是:
(1)对冲压成形性能的要求为了有利于冲压变形和制件质量的提高,材料应具有良好的冲压成形性能。 而冲压成形性能与材料的机械性能密切相关,通常要求材料应具有:良好的塑性,屈强比小, 弹性模量高,板厚方向性系大,板平面方向性系数小。
(2)对材料厚度公差的要求材料的厚度公差应符合国家规定标准。因为一定的模具间隙适用于一定厚度的材料, 材料厚度公差太大,不仅直接影响制件的质量,还可能导致模具和冲床的损坏。.对表面质量的要求材料的表面应光洁平整,无分层和机械性质的损伤,无锈斑、氧化皮及其它附着物。 表面质量好的材料,冲压时不易破裂,不易擦伤模具,工件表面质量好。
以电动机防护罩零件为例,结合其模具特有工艺性,进行了工艺性分析,并分析了成形过程的三种不同的冲压工艺方案, 然后选复合模作为该副模具的工艺生产方案。并对模具的各部分主要尺寸进行理论运算,以确定各冲模的尺寸,经过计算分析完成该模具的主要设计计算,凸、凹模工作部分的设计计算,还有主要零部件的结构设计,。完成一系列的计算后,画出总装图、凸凹模配合图等设计模具必备的图纸。
综上所述,冲压材料我选择钢08F作为冲压件的材料。
钢08F为优质碳素钢,碳的质量分数很低,塑性好,有较好的冲压、弯曲性能,取抗剪强度 ,抗拉强度 ,屈服点 , 断面收缩率 。
1.3结构形状
冲压磨具生产中的创新设计案例

冲压磨具生产中的创新设计案例近年来,随着工业科技的飞速发展,冲压磨具的设计和生产已经取得了长足的进步。
在这个不断变化的市场环境中,创新设计成为了冲压磨具企业赖以生存和发展的重要因素。
本文将介绍几个冲压磨具生产中的创新设计案例,以此展示创新设计对企业发展的重要性。
案例一:智能化冲压磨具随着人工智能技术的快速发展,智能化冲压磨具成为了磨具生产行业的新趋势。
一家磨具企业通过引入人工智能技术,研发出了一种能够自动调节磨具温度和磨削力度的智能化冲压磨具。
这种磨具能够根据不同工件的材质和要求,自动调节磨削参数,从而提高磨削精度和生产效率。
智能化冲压磨具的创新设计帮助企业实现了全自动化生产,大幅度提升了生产效率,带来了更高的经济效益。
案例二:环保型冲压磨具在当前日益严峻的环境问题下,环保成为了企业发展的一项重要指标。
一家冲压磨具企业顺应环保潮流,通过创新设计开发了一种环保型冲压磨具。
该磨具采用了可再生资源制造,以减少对环境的影响。
同时,该磨具在使用过程中也采用了节能减排的技术,大大减少了能源消耗和废气排放。
环保型冲压磨具的创新设计不仅满足了市场对环保产品的需求,也提升了企业形象,更好地适应了未来的发展趋势。
案例三:多功能冲压磨具随着市场对产品多样化需求的增加,一家冲压磨具企业开发了一种多功能冲压磨具,以满足不同产品的加工需求。
该磨具具有可调节的磨削模式和工作台,可以适应不同形状和尺寸的工件加工。
同时,该磨具还配备了智能控制系统,可以根据产品要求自动调整磨削参数,提高加工精度。
多功能冲压磨具的创新设计不仅提高了企业的生产效率和产品质量,也为客户提供了更多的灵活选择,增强了企业的市场竞争力。
综上所述,创新设计在冲压磨具生产中起到了至关重要的作用。
智能化冲压磨具、环保型冲压磨具和多功能冲压磨具的创新设计案例证明了创新对企业发展的推动作用。
面对日新月异的市场竞争,冲压磨具企业应积极引入创新设计理念,不断提高产品质量和生产效率,以适应市场需求的变化,实现可持续发展。
防护罩冲压工艺及模具设计

Punching Process and Die Design of Shield LIU Yanli,GAO Jinliang,ZHANG W eihua,W ANG Liang,CHEN Yong (Institute of Technology,Beijing North Vehicle Group Corporation,Beijing 100072,China) Abstract:The structure and punching process of shield were analyzed. The process program of punching was deter— m ined. A com pound incision and extend punch die was designed according to the determ inistic process program . T he struc— ture feature,working principle and design points of the com pound incision and extend punch die were introduced.The prac— tical production showed that the structure of the die is rationa1. T he die can be operated stably, the products produced by the die had good quality. Key words:Shield,Process analysis,Com pound incision and extend punch
冲压模具机械在操作过程的安全防范措施

冲压模具机械在操作过程的安全防范措施一、操作前准备阶段:1.安全培训:操作人员应接受必要的安全培训,了解冲压模具机械的原理、结构和操作规程,并熟悉设备上的安全警示标志和操作说明。
2.个人防护:操作人员应佩戴必要的个人防护装备,如安全帽、防护眼镜、防护服、耐酸碱手套等。
3.检查设备:操作人员在操作前应仔细检查冲压模具机械的各个部件是否完好,是否有松动、裂纹或漏电等问题,并确保机械设备的电源和传动装置处于正常状态。
二、操作过程中的安全措施:1.安全装置:冲压模具机械应配备必要的安全装置,如防护罩、急停按钮、安全光幕等。
操作人员在操作过程中要确保这些安全装置的正常工作和有效性,不得擅自停用或移动安全装置。
2.适当工作姿势:操作人员在操作冲压模具机械时,应保持正确的工作姿势,避免长时间弯腰、低头、过度伸展或扭曲身体,以免引发劳动损伤。
3.安全固定模具:在更换模具时,应确保模具的安全固定,避免因模具松动或脱落导致意外事故。
4.避免手部接触:操作人员在运行中的冲压模具机械附近应保持手部的安全距离,避免手部接触活动部件或处于模具闭合区域,以防夹伤或其它伤害发生。
5.防滑措施:地面应保持干燥、清洁,避免有杂物阻碍操作人员的行动;操作区域的台面或地面应加设防滑垫或胶垫,以防止操作人员在操作时出现滑倒事故。
6.工作环境安全:操作人员应保持周围工作环境整洁、无杂物,避免杂物或其他人员碰撞机械,以免引发意外事故。
同时,也需要确保操作区域具备良好的通风和照明条件。
7.紧急救援准备:操作人员应了解紧急救援措施和设备,掌握消防器材的位置和使用方法,以备在发生事故时能够迅速应对,保护自己和他人的安全。
三、操作后阶段:1.设备停机:在操作结束后,操作人员应将冲压模具机械停机,并确保其断电,并及时清理设备周围的工具和杂物。
2.设备维护:定期进行设备维护保养,包括清洁设备、润滑零部件、检查电气连接等,确保设备的正常运行和安全性能。
3.事故记录:任何一起事故或异常情况都应进行详细记录,以便于事后的分析和改进。
冲压模具设计图纸

固定挡料销A7X4X3
1
45#
7
凹模固定板
1
45#
6
GB2863.5-81
落料凹模
1
9Mn2V
5
GB2855.6-81
下模座200X100X40
1
T10
4
GB2869.2-81
限位柱81
1
45#
1
3
GB2868.5-81
导料板180X25X8
2
A3
工件图 材料:T2 厚度:2.0
技术要求 未注明圆角为R5 未注明倒角5X45°
4
Q235-A
14
GB2863.1-81
落料凸模
1
9Mn2V
13
GB/T70.1-2000
内六角螺钉M8X50
4
Q235-A
12
GB/T2855.5-81
上模座200X100X35
1
T10
2
11
GB/T70.1-2000
卸料螺钉M5X50
4
Q235-A
10
橡胶
2
9
卸料板
1
45#
8
GB2866.11-81
12 19 20
H7 m6
13
14
15
16
17 18
21 22
H7 m6 H7 m6
11 10 9 8 7 6 5
H7 m6 H7 m6
23
说明 本模具采用始用挡料销和固定挡料销挡料。条 料从右方送进,开始两次行程由第一第二两始用挡 料销26挡料,第三次行程以后即由固定挡料销8挡 料。 模具的冲孔与落料凹模采用整体固定板7固定, 冲孔凸模与落料凸模由固定板20固定。采用弹性卸 料板9,在卸料的同时,起到压边的作用。采用限 位柱4,保护模具,防止模板在高速长时间的过负 荷冲击中发生潜变。
音响防尘罩塑料模具设计

音响防尘罩塑料模具设计一、前言随着科技的不断发展和进步以及人们生活水平的提高,音响在生活中的应用越来越广泛,成为现代人娱乐生活中必不可少的一部分。
而音响防尘罩作为音响附件中的一个重要组成部分,起到防尘、保护音箱内部元件的作用,成为音响的重要保护工具。
如何对音响防尘罩进行设计,提高其实用性和美观度,对于提升音响使用体验具有非常重要的意义。
本文将从音响防尘罩塑料模具设计的角度展开探讨,主要介绍音响防尘罩塑料模具设计的优化方向和注意事项。
二、音响防尘罩的塑料模具设计优化方向1、结构的简单化音响防尘罩作为一种塑料产品,其模具设计过程需要考虑到产品的结构和制造过程。
要充分考虑到产品的拆卸、组装、注塑的方便性和实用性,结构应尽可能简单,避免增加生产过程中的成本和复杂度,提高整个生产过程的效率。
2、材料的选择在音响防尘罩的塑料模具设计中对材料的选择十分重要。
应该优先考虑到材料的性能,如重量、耐热性、耐腐蚀性、强度等,根据产品的特性进行适当的材料选择。
同时,还要考虑到材料的成本,寻找高性价比的材料,降低成本。
3、模具的制造模具对于产品的注塑和外观起着至关重要的作用。
在设计时要充分考虑到模具的制造工艺和使用寿命。
模具应选用高品质材料,尽可能的减少且避免制造中的误差,提高产品质量。
在模具的制作过程中,要确保模具的精度和耐用性,提高产量和减少成本。
三、音响防尘罩的塑料模具设计注意事项1、外观设计与注塑成型技术的结合音响防尘罩的外观设计和注塑成型技术的结合是模具设计的重要考虑因素。
在保持产品设计美观的同时,还要考虑到注塑成型过程中的塑料流动、收缩等问题,避免出现产品变形等问题。
2、模具的稳定性音响防尘罩的塑料模具设计需要考虑到模具的稳定性,在注塑和生产过程中确保模具的精度和稳定性,避免产生模具摆动、振动、暴露的问题。
同时,还要做好模具的保养和维护,延长模具的使用寿命。
3、产品质量控制无论产品是有规模的或小规模的生产,产品的质量问题都必须时刻予以关注。
冲压模具设计装配图.
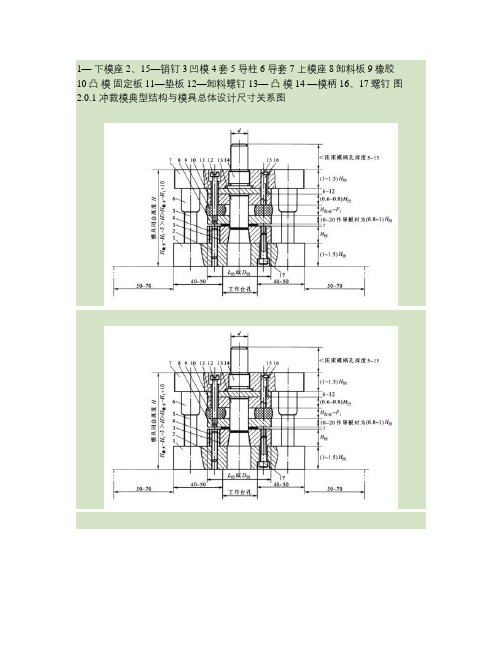
1—下模座2、15—销钉3凹模4套5 导柱 6 导套 7 上模座 8卸料板9橡胶10凸模固定板 11—垫板12—卸料螺钉13—凸模14 —模柄 16、17螺钉图2.0.1 冲裁模典型结构与模具总体设计尺寸关系图复合模的基本结构1—凸模;2—凹模;3—上模固定板;4、16—垫板;5—上模座;6—模柄;7—推杆; 8—推块; 9—推销;10—推件块;11、18—活动档料销;12—固定挡料销;13—卸料板14—凸凹模;15—下模固定板;17—下模座;19—弹簧1-下模座;2、5-销钉;3-凹模;4-凸模 1-凹模;2-凸模;3-定位钉;4-压料板;5-靠板 6-上模座;7-顶杆;8-弹簧;图3.4.2 L形件弯曲模 9、11-螺钉;10-可调定位板1.冲裁间隙过大时,断面将出现二次光亮带。
( ×)2.冲裁件的塑性差,则断面上毛面和塌角的比例大。
( ×)3.形状复杂的冲裁件,适于用凸、凹模分开加工。
( ×)4.对配作加工的凸、凹模,其零件图无需标注尺寸和公差,只说明配作间隙值。
( ×)5.整修时材料的变形过程与冲裁完全相同。
( ×)6.利用结构废料冲制冲件,也是合理排样的一种方法。
(∨)7.采用斜刃冲裁或阶梯冲裁,不仅可以降低冲裁力,而且也能减少冲裁功。
( ×)8.冲裁厚板或表面质量及精度要求不高的零件时,为了降低冲裁力,一般采用加热冲裁的方法进行。
(∨)9.冲裁力是由冲压力、卸料力、推料力及顶料力四部分组成。
( ×)10.模具的压力中心就是冲压件的重心。
( ×)11.冲裁规则形状的冲件时,模具的压力中心就是冲裁件的几何中心。
( ×)12.在压力机的一次行程中完成两道或两道以上冲孔(或落料)的冲模称为复合模。
×13.凡是有凸凹模的模具就是复合模。
( ×)14.在冲模中,直接对毛坯和板料进行冲压加工的零件称为工作零件。
- 1、下载文档前请自行甄别文档内容的完整性,平台不提供额外的编辑、内容补充、找答案等附加服务。
- 2、"仅部分预览"的文档,不可在线预览部分如存在完整性等问题,可反馈申请退款(可完整预览的文档不适用该条件!)。
- 3、如文档侵犯您的权益,请联系客服反馈,我们会尽快为您处理(人工客服工作时间:9:00-18:30)。
设计任务书设计题目:防护罩的冲压模具设计设计要求:1.防护罩工艺性分析及冲裁方案的确定;2.有关计算及模具设计;3.模具制造工艺编制与装配。
摘要我本次设计的零件为防护罩。
此工件采用的材料钢08F及厚度1.5mm保证了足够的强度和刚度,该零件外形复杂,工序烦琐,故设计成复合模进行冲裁。
合理排样、减小废料。
材料为优质碳素钢,采用冲压加工经济性良好。
以电动机防护罩零件为例,结合其模具特有工艺性,进行了工艺性分析,并分析了成形过程的三种不同的冲压工艺方案,然后选复合模作为该副模具的工艺生产方案。
并对模具的各部分主要尺寸进行理论运算,以确定各冲模的尺寸,经过计算分析完成该模具的主要设计计算,凸、凹模工作部分的设计计算,还有主要零部件的结构设计,。
完成一系列的计算后,画出总装图、凸凹模配合图等设计模具必备的图纸。
简要分析了模具关键零部件的设计及加工工艺.对拉深模从设计到零部件的加工工艺以及装配工艺等进行了详细阐述,绘制了模具装配图及主要工作零件图,详细分析了模具工作过程。
进行冲压设计就是根据已有的生产条件,综合考虑影响生产过程顺利进行的各方面因素,合理安排零件的生产工序,最优地选用,确定各工艺参数的大小和变化范围,设计模具,选用设备等,以使零件的整个生产过程达到优质,高产,低耗,安全的目的。
关键词:落料,拉深,翻边,复合模目录311 冲压工艺分析1.1工件分析零件简图:如图1所示生产批量:大批量材料:08F材料厚度:1.5mm要求: 要求确定该零件冲压成形工艺,设计冲压成形模具。
即做出该零件的拉深及翻边工艺图1-1 防护罩工件简图该工件属于典型的有凸缘圆筒形拉深,要求内形尺寸,形状简单对称,该工件作为另一零件的罩,对表面粗糙度没有特殊要求。
所有尺寸均为自由公差,按IT14级确定工件的公差,可用落料获得的圆形板料进行拉深,拉深成为外径为 223.4mm,内圆角R为6mm的有凸缘圆筒,工件总高度尺寸75mm可在拉深中达到要求。
一般冲压均能满足其尺寸精度要求,对零件的厚度变化也没有要求。
圆筒形件的毛坯为圆形板料,可以通过落料获得。
08F钢是碳素结构钢,具有良好的冲压性能。
综上所述,该工件的精度及结构尺寸都能满足冲压工艺要求,工件的拉深工艺性较好。
该工件在满足冲压工艺性要求的前提下,采用的冲压基本工序是落料、拉深、翻边。
1.2 材料冲压工艺对材料的基本要求主要是:(1) 对冲压成形性能的要求为了有利于冲压变形和制件质量的提高,材料应具有良好的冲压成形性能。
•而冲压成形性能与材料的机械性能密切相关,通常要求材料应具有:良好的塑性,屈强比小,•弹性模量高,板厚方向性系大,板平面方向性系数小。
(2) 对材料厚度公差的要求材料的厚度公差应符合国家规定标准。
因为一定的模具间隙适用于一定厚度的材料,•材料厚度公差太大,不仅直接影响制件的质量,还可能导致模具和冲床的损坏。
.对表面质量的要求材料的表面应光洁平整,无分层和机械性质的损伤,无锈斑、氧化皮及其它附着物。
•表面质量好的材料,冲压时不易破裂,不易擦伤模具,工件表面质量好。
(3) 常用冲压材料冲压用材料的形状有各种规格的板料、带料和块料。
板料的尺寸较大,•一般用于大型零件的冲压,对于中小型零件,多数是将板料剪裁成条料后使用。
•带料(又称卷料)有各种规格的宽度,展开长度可达几千米,适用于大批量生产的自动送料,•材料厚度很小时也是做成带料供应。
块料只用于少数钢号和价钱昂贵的有色金属的冲压。
综上所述,冲压材料我选择钢08F 作为冲压件的材料。
钢08F 为优质碳素钢,碳的质量分数很低,塑性好,有较好的冲压、弯曲性能,取抗剪强度400a MP τ=,抗拉强度240b a MP σ=,屈服点240s a MP σ=, 断面收缩率00=60ϕ。
1.3结构形状该工件结构复杂,所要冲裁的板料厚度为1.5mm 。
1.4尺寸精度该工件未表注公差的尺寸,根据工件的使用性能,可按IT6级制造。
2 模具的技术要求及材料选用2.1模具的技术要求利用模具生产制品零件,其模具质量的好坏,寿命的长短,直接关系到产品制造精度、性能和成本。
是提高劳动生产率、降低消耗、创造效益,尽快使产品占领市场的重要性条件。
而模具的质量、使用寿命、制造精度及合格率很大程度上取决于设计时对模具材料的选用、热处理工艺要求、模具零件配合精度及公差等级的选择和表面质量要求。
2.2 模具材料的选用及要求2.2.1冷冲模材料应具有的性能冷冲模包括冲裁模、弯曲模、拉深模、成形模和冷挤压模等。
冷冲模在工作中承受冲击、拉深、压缩弯曲、疲劳磨擦等机械的作用。
模具常常发生脆断、堆塌、磨损、啃伤和软化等形成的失效。
因此,作为冷冲模主要材料的钢材,应具有的性能。
(1)应具有较高的变形抗力:主要抗力指标包括淬火、回火抗压强度、弯强度等。
其中硬度是模具注意重要的抗力指标,高的硬度是保持模具耐磨性的必要条件。
工作零件热处理后的硬度在60HRC强度和抗弯强度才能保证模具具有较高的变形能力。
(2)应具有较高的断裂抗主要抗力指标有材料的抗冲击性能抗压强度、抗弯强度断裂抗力和冲击载荷下抵抗模具裂纹产生一个特性,也是作为防止断裂的一个重要依据。
其基体中碳含量越高冲击韧性越高。
故对韧性的要求应依据载荷较大的冷冲镦及剪切模易受偏心弯曲载荷细长凸模或有应力集中的模具,都需要有较高的韧性。
(3)应具有较高的耐磨性和抗疲劳性能:对于在一定条件下工作的模具钢,为了提高耐磨性,需要在硬度高的基体上均匀分布有大量细小硬的碳化物相同硬度下,提高钢的性能是模具在交变应力条件下产生的疲劳破坏,如模具长期使用有刮痕凹槽等。
(4)应具有较好的冷、热加工工艺性:钢材的加工性能包括可锻性、可加工性、淬透性、淬硬性较小的脱碳敏感性和较小变形倾向等,以方便模具的加工,易于成形及防止热处理后变形等。
2.2.2材料的选择原则(1)要选择满足模具零件工作要求的最佳综合性能的材料:要选择满足模具零件工作要求的最佳综合性能的材料。
(2)要针对模具失效形式选用钢材:钢材的失效是影响模具寿命的主要因素包括:1)为防模具开裂,要选用韧性好的材料2)为防磨损,应选用合金元素高的材料3)对于大型冲模应选用淬透性好的材料4)为保持钢材硬度能力,要选用耐回火性高的含铬、钼合金钢5)为防热处理变形,对于形杂的零件应选用含碳量高、淬透性好的高合金材料。
(3)要根据制品批量大小,以最低的成本的选材原则选用:对于需冲压数量较多模具,一般采用优质合金钢,而数量少的则采用碳素钢,以降低成本。
(4)要根据冲模零件的作用选择:凸、凹模具应选用优质的钢材制作,对于数量不多或厚度不大的可采用有色金属或黑色金属。
而对于支撑板、卸料零件、导向件应选用一般钢材。
(5)要根据冲模精密程度选用:在制造小型精密模具而又复杂时可选用优质合金钢制作,而对于比较简单,形状、精度有要求不高的模具应选用比较便宜的碳钢或低合金钢。
C M V为模具材料。
该合金钢具有较好综上所述,此模具采用合金工具钢12r O的耐磨性,较好的淬火不变形性,较好的红硬性,较小的脱碳敏感性,较深的淬硬深度,但它的切削加工性较差,耐冲击性也较差。
基本能满足此模具的冲裁。
此模具的弯曲部分也采用这种材料。
凸模的热处理硬度为58~62HRC,凹模的热处理硬度为62~64HRC。
3冲压工艺方案的确定该工件包括落料、拉深、翻边,切边、冲孔两个基本工序,现只做落料、拉深、翻边基本工序.经分析可以有以下三种工艺方案:方案一:先落料,后拉深翻边.采用单工序模生产。
方案二:落料一拉深翻边复合冲压.采用复合模生产。
方案三:拉深级进冲压,采用级进模生产。
方案一模具结构简单,但需要两道工序两副模具,生产效率低,难以满足该工件大批量生产和客户的要求.所以此方案不可取.方案二只需要一副模具,生产效率明显要比方案一好,尽管模具结构模具结构较方案一复杂,但由于零件的几何形状简单对称,模具制造并不困难.方案三也只需要一副模具,生产效率高,但模具结构比较复杂,送进操作不方便,加之工件尺寸偏大.通过对上述三种方案的分析比较,该零件若能一次拉深,则其冲压生产采用方案二为佳。
4必要的工艺尺寸计算4.1 毛坯尺寸计算图4-1 工件简图工件简图如上图所示,计算尺寸:d1=208.4;d2=221.9;d3=226;d4=236;r=6;R=1.5;h=64.5根据表面积相等原则,用解析法求该零件的毛坯直径D 。
(常用旋转体拉深件坯料直径的计算公式)。
当r 不等于R时,毛坯直径D: D=2324222212156.428.64828.6d d R Rd h d r rd d -++++++ =340510765569616.16496.8364572761.19816.43430=-+++++4.2 排样设计与计算冲裁件面积A A=mm D 0.90792434034014.34/2=⨯⨯=⨯π D ——毛坏件直径条料宽度BB=D+2a+C=351mma ——侧搭边值,a=1.5;a1=1.2c ——导料板与最宽条料之间的间隙,其最小值见表4—1。
取c=8。
表4—1导料板与条料之间的最小间隙Cmin材料厚度t无测压装置 有侧压装置 条料宽度B条料宽度100以下100~200200~300100以下100以上~0.50.5~1 1~2 0.5 0.5 0.50.5 0.5 11 1 15 5 58 8 8步距SS=D+1a =341.2mm一个步进距的材料材料率η η=nA/BS ⨯100%=%8.752.341351907921=⨯⨯其结构示意图如下:图4-2 排样示意图4.3 拉深次数的确定4.3.1能否一次拉深成形图4-3有凸缘圆筒形件的拉深系数为 Dd m t =式中:t m ——有凸缘圆筒形件的拉深系数; d ——零件筒形部分的直径; D ——坯料直径 拉深系数D d m t ==3404.223=0.66 坯料相对厚度(t/D)⨯100=0.44由上式可以看出,有凸缘圆筒形件的拉深系数取决于有关尺寸的三个相对比值即d d t /(凸缘的相对直径)、h/d(零件的相对高度)、R/d(相对圆角半径).其中以d d t /影响最大,h/d 次之,R/d 影响最小. d d t /和h/d 越大,表示拉深时毛坯变形区的宽度大,拉深成形的难度也大.当d d t /和h/d 超过一定值时,便不能一次拉深,因为叫拉深系数t m 大于表4—2的极限拉深系数值,则凸缘圆筒形件可以一次拉深成形.查表表4—2发现min /d h 小于表中数值,能一次拉深成形.所以采用落料-拉深翻边复合冲压.表4—2 有凸缘的圆筒形件第一次拉深的极限拉深系数该零件属于浅拉深。
4.4 冲压工序力计算该模具拟采用正装复合模,固定卸料与顶件。