高炉热风炉炉壳制作工艺
大型高炉热风炉热处理工法

图2预热装置示意图
表2热处理通知
炉号
施焊时间
施焊班组
需加热温度(℃)
通知人姓名
通知日期
(3)准备预热前应先接好电源,电源输入方式采用三相四线。热处理机不是同一时间加热,而是分六个炉区循环加热。在热处理时,导线的额定限度一定不能小于输出功率。
1、电缆线是连接电源与热处理设备之间的导线,其安全载流量由表6确定:
表6低压聚氯乙稀(PVC)绝缘四芯电缆安全载流量
主线芯截面(mm2)
中芯截面(mm2)
安全载流量(A)
空气中敷设
直接埋地
铜
铝
铜
铝
4
16
25
35
50
70
95
120
150
185
240
2.5
6(10)
10(16)
10(16)
16(25)
25(35)
2、焊后脱氢处理
(1)有些试板在焊接结束后要进行必要的消氢处理,例如宁钢2#高炉热风炉中材质为Q235B与Q345B板对接安装焊缝接结束后就进行了消氢处理。在进行消氢处理之前做一些质量检查是必要的,所以在焊接结束后首先应对接接头焊缝、热影响区、母材分别进行应力和硬度测试、金相组织抽查及几何尺寸的测量,并记录。
采取局部预备热处理时,应防止局部应力过大。预热的范围为焊缝两侧各不小于焊件厚度的3倍区域,且不小于100mm。当使用低氢型焊接材料时,可根据试验适当降低预热温度。因对环境恶劣和难施焊的部位选择了较低的预热温度,所以在焊后相应采取低温后热处理,以补偿焊前预热温度的不足。
热风炉炉壳及框架制作安装施工方案

目录目录 (1)一、简介 (3)二、施工准备 (4)2.1编制依据 (4)2.2施工平面布置 (5)2.3生产要素需用计划 (5)2.4 基础验收 (7)2.5 基础划线 (8)2.6 组装临时平台的铺设 (8)2.7 热风炉本体外壳制作、安装方案和程序 (9)2.8 热风炉本体外壳制作、安装总技术要求 (9)2.9 热风炉本体施工通用制作工艺 (11)2.9.1 板材下料 (11)2.9.2 坡口制作 (11)2.9.3 焊接 (11)2.10 热风炉钢结构通用制作工艺 (12)2.10.1排版下料 (12)2.10.2 坡口制作 (13)2.10.3 梁、柱的焊接 (14)2.11 热处理 (17)三、制作和安装 (17)3.2.1、炉壳板下料: (18)3.3、炉壳板安装 (20)3.3.1、下部筒体组对、安装 (20)3.3.2、炉箅子组对、安装 (22)3.3.3、热风炉上部筒体的安装 (22)3.3.4、安装注意事项: (23)3.4、热风炉气密性试验 (23)3.5、热风炉钢结构平台制作安装 (23)4.1 热风炉炉壳及钢结构平台制作安装进度及保证施工进度的措施 (24)4.2 热风炉炉壳及钢结构平台制作安装工程质量的保证措施 (24)4.2.1 质量方针: (25)4.2.2 质量目标: (25)4.2.3 质量保证体系 (25)4.2.4 质量职责 (25)4.2.5 质量控制程序 (26)4.2.6 建设阶段的质量管理制度 (26)4.2.7 竣工验收阶段 (27)4.3保证安全生产、文明施工及环境保护的措施 (27)4. 3.1安全保证措施 (27)4. 3.2 确定安全防范措施 (27)4.3.3 加强安全生产教育 (28)4.3.6 认真执行安全检查制度 (29)4.3.7 施工机械的安全措施 (29)4.3.8 施工现场的安全措施和要求 (30)4.3.9 焊接与切割的安全措施 (31)4.3.10 高空作业的安全技术措施、要求和行为规范 (31)4.3.11 起重机械的安全技术措施、要求和施工规范 (32)热风炉炉壳及平台钢结构制作安装施工方案福建三金钢铁公司1#高炉工程中,热风炉及热风炉平台钢结构,热风炉包括热风炉底部梁结构、外壳、球形顶等;热风炉平台钢结构包括2.500平台、5.800平台、11.000平台、14.000平台、18.500平台、20.800平台、25.000平台等平台、以及平台钢柱、栏杆、钢扶梯等几部分组成。
热风炉炉壳焊接工艺探讨

热风炉炉壳焊接工艺探讨发布时间:2021-04-20T15:43:04.893Z 来源:《城市建设》2021年3月作者:蓝瑟琴[导读] 热风炉是钢厂高炉主要配套设备之一,一般一座高炉相应的配套3至4台热风炉,其作用是为高炉提供上千摄氏度的高温热风,炉壳工作环境比较恶劣,炉壳焊接质量决定了炉壳寿命,本文主要以某大型高炉配套热风炉焊接施工为例,阐述热风炉的焊接工艺及质量控制。
广西柳州十一冶建设有限责任公司安装工程分公司蓝瑟琴 545007摘要:热风炉是钢厂高炉主要配套设备之一,一般一座高炉相应的配套3至4台热风炉,其作用是为高炉提供上千摄氏度的高温热风,炉壳工作环境比较恶劣,炉壳焊接质量决定了炉壳寿命,本文主要以某大型高炉配套热风炉焊接施工为例,阐述热风炉的焊接工艺及质量控制。
关键词:热风炉焊接工艺收缩量焊接参数焊接要求0前言某大型高炉工程为单座高炉配套4台热风炉,单个单个热风炉炉壳共分23带,由δ=25mm、δ=30mm、δ=36mm、δ=50mm、δ=60mm 和δ=70mm厚的六种规格钢板卷制焊接而成;炉顶标高达46.875m,炉壳最大直径(内径)12080mm。
热风炉炉壳设计温度为130℃,设计压力为0.55MPa,风压为0.65KN/m2。
热风炉焊接质量要求高。
炉壳施工中最重要的就是要保证炉壳立缝、横缝的焊接质量,以下为热风炉焊接工艺分析。
1热风炉焊接材质热风炉钢板材质一般采用Q345B(GB/T1591-2008),其力学、工艺性能和化学成分须符合GB/T1591-2008的规定。
Q345B的化学成分如下表1所示,Q345B的力学性能如下表2所示。
3热风炉质量要求炉壳焊接检验应符合GB50236-2011《现场设备、工艺管道焊接工程施工规范》中焊接检验的规定,焊缝外观质量达到规范中焊接质量分级标准的II级标准。
炉壳焊缝应按JB4730进行超声无损检测,检测比例均为100%。
焊接接头质量不低于I级为合格。
(工艺技术)热风炉焊接工艺(曲线立缝电渣焊)

热风炉焊接工艺按260m3高炉及其四座热风炉炉壳焊接工程中,板厚大于28mm 的炉壳垂直立焊缝,全部采用了管焊条熔嘴电渣焊工艺。
但由于设计外形上的要求,热风炉炉体上部为曲线变径,顶部为悬链线半球形,因而存在大量曲线和“S”形曲线拼接立焊缝。
在四座热风炉中,板厚大于28mm的立焊缝总长共443m,其中曲线和“S”形曲线立焊缝就有275m,占总长的65%。
在直线立缝采用电焊的工艺基础上,针对曲线立焊缝的特点,采取了相应的工艺措施,做了模拟试验,制订了相应的焊接工艺,在热风炉炉壳的曲线和“S”曲线立焊缝上,实现了管焊条熔嘴电渣焊。
一、热风炉炉壳焊接概况按260m3高炉共四座热风炉,设计为内燃式。
炉身直径8m,上部曲线变径处的直径9.5m,全高38m。
炉壳钢板的材质为SM41B,板厚分别为16、20、22、28、32、36、42mm。
总重1132t。
热风炉炉壳分成22带制造。
曲线变径处及半球形炉顶曲面部位共五带,全部分块热压成型,拼成曲面环节。
各分块间的拼接立缝,均为曲线立缝(如图1)。
其中第十五带,即曲线变径部位,原设计分为两带,在两圆弧切点处分开,由一条环形焊接联接。
由于在热加工时改进了加工工艺,将原设计的两带合并成一带,该带在炉体纵剖面上呈“S”形弯曲。
内弧的曲率半径为1400mm,外弧的曲率半径为3500mm,板厚42mm,垂直高度2340mm,弧长2470mm。
整个环带由14个分块组成,共56条曲线立缝,总长158m。
第十九带由14个分块组成,在炉体纵剖面上曲率半径为2400mm,板厚32mm,垂直高度为800mm,弧长832mm,共56条曲线立缝,总长46.6m。
第二十带由12个分块组成,在炉体总剖面上的曲线形状为设计给定的悬链线,板厚28mm,垂直高度1500mm,弧长1598mm,共48条曲线立缝,总长76.7m。
以上三带的曲线立缝均采用管焊条熔嘴电渣焊工艺方法焊接,其余两带曲线立缝,因板厚只有22mm,只能采用手工焊。
高炉炉壳制作方案
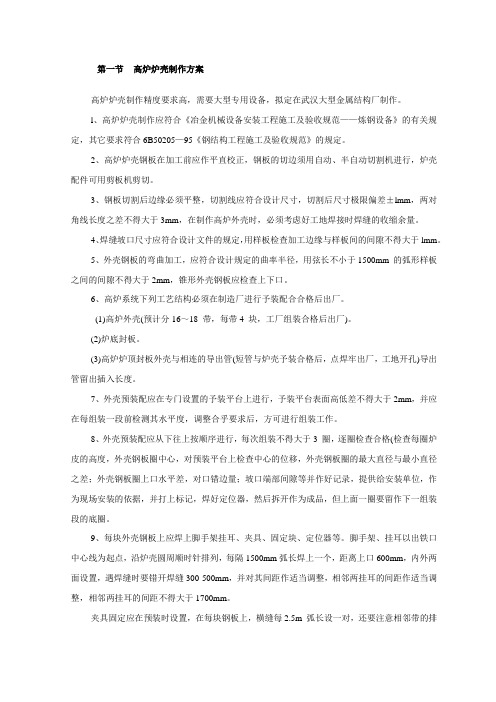
第一节高炉炉壳制作方案高炉炉壳制作精度要求高,需要大型专用设备,拟定在武汉大型金属结构厂制作。
l、高炉炉壳制作应符合《冶金机械设备安装工程施工及验收规范——炼钢设备》的有关规定,其它要求符合6B50205—95《钢结构工程施工及验收规范》的规定。
2、高炉炉壳钢板在加工前应作平直校正,钢板的切边须用自动、半自动切割机进行,炉壳配件可用剪板机剪切。
3、钢板切割后边缘必须平整,切割线应符合设计尺寸,切割后尺寸极限偏差±lmm,两对角线长度之差不得大于3mm,在制作高炉外壳时,必须考虑好工地焊接时焊缝的收缩余量。
4、焊缝坡口尺寸应符合设计文件的规定,用样板检查加工边缘与样板间的间隙不得大于lmm。
5、外壳钢板的弯曲加工,应符合设计规定的曲率半径,用弦长不小于1500mm 的弧形样板之间的间隙不得大于2mm,锥形外壳钢板应检查上下口。
6、高炉系统下列工艺结构必须在制造厂进行予装配合合格后出厂。
(1)高炉外壳(预计分16~18 带,每带4 块,工厂组装合格后出厂)。
(2)炉底封板。
(3)高炉炉顶封板外壳与相连的导出管(短管与炉壳予装合格后,点焊牢出厂,工地开孔)导出管留出插入长度。
7、外壳预装配应在专门设置的予装平台上进行,予装平台表面高低差不得大于2mm,并应在每组装一段前检测其水平度,调整合乎要求后,方可进行组装工作。
8、外壳预装配应从下往上按顺序进行,每次组装不得大于3 圈,逐圈检查合格(检查每圈炉皮的高度,外壳钢板圈中心,对预装平台上检查中心的位移,外壳钢板圈的最大直径与最小直径之差;外壳钢板圈上口水平差,对口错边量;坡口端部间隙等并作好记录,提供给安装单位,作为现场安装的依据,并打上标记,焊好定位器,然后拆开作为成品,但上面一圈要留作下一组装段的底圈。
9、每块外壳钢板上应焊上脚手架挂耳、夹具、固定块、定位器等。
脚手架、挂耳以出铁口中心线为起点,沿炉壳圆周顺时针排列,每隔1500mm弧长焊上一个,距离上口600mm,内外两面设置,遇焊缝时要错开焊缝300-500mm,并对其间距作适当调整,相邻两挂耳的间距作适当调整,相邻两挂耳的间距不得大于1700mm。
热风炉的制作方法

热风炉的制作方法
热风炉是一种广泛应用于工业生产和家庭生活中的设备,它可以提供高温空气,用于烘干、加热、熔炼等工艺过程中。
下面将介绍一种简单有效的热风炉制作方法。
材料:
- 铁皮或不锈钢板,用于制作热风炉的壳体;
- 耐火材料,如陶瓷纤维或高温隔热材料,用于制作热风炉的内胆;
- 加热元件,如电热管或燃气加热器,用于提供热风炉的热量; - 温度控制系统,用于控制热风炉的温度。
步骤:
1. 根据需要制作热风炉的壳体,壳体应该是密封的,以避免热量散失。
2. 在壳体内部放置耐火材料,以形成热风炉的内胆。
内胆应该足够厚实,以承受高温环境的考验。
3. 在内胆中安装加热元件,以提供热风炉的热量。
加热元件应该能够适应高温环境,并且应该安装在内胆的底部,以确保热量能够均匀地传递到内胆中的空气。
4. 在热风炉的顶部安装温度控制系统,用于控制热风炉的温度。
温度控制系统应该能够准确地测量内胆中的温度,并且可以根据需要自动调节加热元件的功率,以保持内胆中的温度恒定。
5. 测试热风炉的性能,以确保它能够正常工作。
测试时应该检
查热风炉的密封性、加热元件的工作状态以及温度控制系统的准确性。
在使用热风炉时需要注意以下事项:
1. 确保热风炉的壳体密封,以避免热量散失。
2. 确保加热元件能够适应高温环境,并且应该经常检查其工作
状态,以避免损坏。
高炉热风炉工艺流程

高炉热风炉工艺流程
高炉热风炉工艺流程一般包括以下步骤:
1.原料预处理:将铁矿石、焦炭、石灰石等原料经过运输、堆存、加料等处理步骤后,送入高炉。
2.热风炉燃料预处理:热风炉一般使用重油、燃气等作为燃料,需要预先进行处理,如过滤、加热、调解等。
3.热风炉点火:在热风炉中点火,使其燃烧起来,产生高温高压的热风。
4.高炉炉料加料:在高炉顶部加入铁矿石、焦炭等原料,随着高炉的运行,炉料逐渐向下移动。
5.热风炉热风送入高炉:使用风机将经过预处理的热风送入高炉内,与炉料进行反应,产生高温高压。
6.高炉渣铁分离:在高温高压下,炉料中的铁分离出来,流入熔融状态下的铸造口,而渣则从高炉底部排出。
7.高炉废气处理:高炉产生大量的废气,需要通过除尘、脱硫、脱硝等步骤进行处理,使其达到环保标准后排放。
以上就是高炉热风炉的主要工艺流程,具体的工艺流程可能因工厂的不同而有所差异。
4000m3高炉炉壳制作技术

1 工 程 概ห้องสมุดไป่ตู้况
首钢迁安钢铁有限公 司配套 完善工程3 号高炉容 积为4 0 0 0 m , 高4 6 . 6 5 m, 最大直径为1 6 . 4 2 m( 内径) , 炉 壳厚 为5 O , 6 5 , 7 0 , 9 0 m m 等规格 , 炉壳材质为B B 5 0 3 , 炉
厂
4 o
2 . B e i j i n g WO W J o i n t Ma c h i n e r y C o . ,L t d . ,1 0 1 1 1 8 ,B e i j i n g ,C h i n a )
Abs t r a c t : Du in r g c o n s t r u c t i o n o f 4 0 0 0 m3 b l a s t f u r n a c e ,i n n o v a t i v e c o n s t uc r t i o n t e c h n i q u e s a r e c r e a t e d t o r e a l i z e e f f e c t i v e c o n t r o l o n s a mp l i n g b e f o r e o p e n i n g h o l e ,d i a me t e r o f p l a n e h o l e ,c e n t r a l p o i n t o f h o l e ,h o l e o p e n i n g a n g l e a n d h o l e o p e n i n g mo d e ,e t c .P l a n e h o l e o p e n i n g t e c h n i q u e a n d c e n t r l r a o l l e r f a b ic r a t i o n me t h o d
- 1、下载文档前请自行甄别文档内容的完整性,平台不提供额外的编辑、内容补充、找答案等附加服务。
- 2、"仅部分预览"的文档,不可在线预览部分如存在完整性等问题,可反馈申请退款(可完整预览的文档不适用该条件!)。
- 3、如文档侵犯您的权益,请联系客服反馈,我们会尽快为您处理(人工客服工作时间:9:00-18:30)。
攀钢2#高炉热风炉炉壳制作工艺
徐小勇 (攀冶修建分公司机械工程项目部邮编617023)
摘要:介绍了2#高炉热风炉炉壳的特点,制作热风炉炉壳的工艺流程和制作工艺。
认为借鉴转炉炉壳的制作工艺,再辅之以切合实际的技术措施,能够保证热风炉炉壳的制作质量。
关键词:热风炉炉壳制作流程成型校正
1.引言
在高炉生产过程中,热风炉设备是高炉生产系统的重要设备。
修建公司自从1996年年初开始承担了炼铁厂2#高炉3座热风炉炉壳结构制作安装任务以来,依次进行了炼铁厂三座高炉的热风炉炉壳的制作安装。
在首次承担的炉壳制作量就达537t,其中2#高炉的1#热风炉仅制作炉帽部分,共计四带;2#和3#热风炉为整座炉皮制作(两座炉结构完全一样),每座共计二十四带。
三座热风炉均由圆锥体、圆筒体和双曲面体组成。
就修建公司而言,当时制作2#高炉热风炉炉壳尚属首次,无制作经验,尤其是热风炉双曲面体的冷压成型工艺难度更大,加之工期短,任务紧,更为此次的检修工作增加了难度。
为此,针对工程实际,开发了热风炉炉壳制作工艺。
这些工艺技术经过这么多年的应用,其效果是明显的,工艺技术是成功的,至今还在继续使用和不断发展,并增加了一些新的工艺。
现结合首次制作情况,将热风炉炉壳的工艺流程和制作工艺归纳如下:
2.工艺流程
为了更简明地看到炉壳结构特点,可以将炉壳的圆锥体和圆筒体合称为直段,而将双曲面体改称为球段,由此可认为炉壳由直段和球段两大结构组成。
另外,修建公司曾经制作过的转炉炉壳结构与热风炉炉壳结构非常相似,借鉴转炉炉壳的制作工艺,并结合热风炉炉壳制作实际,得出制作热风炉炉壳直段和球段的工艺流程见图1、图2。
比较直段和球段的工艺流程,可以看到,球段比直段工序更多,更复杂,制作难度更大。
因此,要确保炉壳制作质量,尤其是球段落的制作质量,就一定要确保每道工序质量,而工序质量的保证是寻求合理的切合实际的制作工艺。
为了保证热风炉炉壳的制作质量,把住工序质量关,本次炉壳制作实施工艺卡,对分部分项质量进行严格检查,发现质量问题及时处理。
3.制作工艺
对球段的第一带用3块试块进行了压制试验,得到球段炉皮压制成型操作步骤:首先,
将炉皮初压一道;其次,加校正板条加以校正成型(板条加法见后述内容)。
图1 直段工艺流程图
3.1 炉壳板下料
必须按规定划好中心线、煨弯线、切开线、切去线、轨道线、坡口线、检查线。
各种线均用划针划线,并以洋冲打出。
洋冲间距规定如图3所示。
应注意各种划线必须准确,复查对角线应在±1mm以内。
为使尺寸一致,应使用样杆检查(可用30mm×50mm的干松木或旧盘尺)。
各带下料尺寸见表1。
3.2 炉壳板切割
所有直段均留线切割,球段压线切割。
切割必须垂直和光滑,以防止缺口和孔洞。
切口垂直度偏差应小于1mm ,有缺口处必须补平磨光。
切割时,仔细检查尺寸,保证切割线到检查距离在50±2mm 以内。
打坡口时,要求坡口均按规定尺寸精确加工成形。
按规定,凡直段带的横缝和竖缝坡口尺寸用刨边机加工成形,但必须注意此次坡口均为不对称型坡口,其角度与板面的正反必须分清,做好标记,写明正反面,确保加工坡口的准确性并为下步工序做好准备。
在刨边的同时,必须检查坡口尺寸、切割尺寸、对角线尺寸,从而保证下料后最终
图2 球段工艺流程图
表1 2#热风炉炉壳板下料尺寸
尺寸的准确性。
各尺寸的误差均应在±1mm以内。
3.3 压架系统及胎膜
从工艺流程图中看出,压架系统及胎膜是制作热风炉炉壳的关键,因此,首先应解决压架系统及胎膜的设计制作问题,然后,在压架系统及胎膜的设计制作上,严格按图纸进行施
工。
为了防止胎膜制作过程中的焊接变形,将常规组装顺序进行了改进,原来的常规组装顺序为:底板→立筋板→加强筋板→面板。
改进后的组装顺序为:底板→立筋板→面板→加强筋板。
需强调的是:面板与加强筋板在相关位置要同步,即该位置的面板装完后,也应将该位置内的加强筋板装完,也就是说,一段面板对应该段位置的加强筋板,需边装面板边装加强筋板。
通过改进,利用面板来控制因先装加强筋板引起的变形。
这样,有效地控制了变形,将上下胎膜变形量由原来的30~50mm降至10mm以内,确保了胎膜制作质量。
3.4 顶压成型
直段先用顶床将头子压好后,再用卷板机卷制成形,而球段直接用胎膜顶压成形。
在直段中,先将老顶床改制合格,保证顶辊横平竖直,顶床内胎也必须要横平竖直,同时保证支承平台水平。
在顶床的顶辊上有中心线,返出基准线,保证对线准确,防止对线偏差,边顶压边检查,检查样板取2m长,确保弧度误差在±2mm以内,欠顶或过顶均需重新顶压,直至满足标准要求。
在球段中,由于本次炉壳球段制作采用的是胎膜冷压成型工艺,不同于以往转炉炉壳球段的制作(转炉球段采用的是胎膜热压成型工艺)。
就热压与冷压两种成型工艺来说,热压后的炉壳成型效果很好,回弹量非常小,而经冷压后的炉壳成型效果很不理想,回弹量比较大,除特殊情况(如弯曲半径很小)外,一般都不能一次冷压成型,而必须通过校正方法进行校正,才能最终成型。
值得一提的是,有时回弹情况不一致,不均匀,无疑也会使校正次数增多,并且最终成型质量不如热压成型质量。
但应该指出,虽然热压成型较冷压成型质量要好,但热压成型改变了母材特有的技术指标,而冷压成型却没有。
至于优先选用何种压制成型工艺,这得由设计工艺要求等因素决定。
在本次炉壳球段制作中,要求采用冷压成型工艺。
为了控制好冷压成型质量,决定采取下述方法:①、每块炉壳第一次用胎膜压完后,用立体样板检查成型误差量。
②、根据成型误差量加校正板条给予校正,见图4。
顺序为:先校高度方向;再校上下口方向(校正板条宽一般取40mm,厚度由压制误差值决定,板条数可视实际情况增多),再记录各校正位置的回弹量。
③、若加板条后,炉壳成规律性地变化,考察每次回弹量,加板条就可直接校正,若炉壳局部存在不规则变化,局部就需另加板条加以校正。
同时还应在炉壳上用立体样板划出成型轮廓线,确定尺寸检查点,用尺寸直接进行局部成型检查。
本次炉壳冷压采用2台320t油压顶进行压制。
当板料放在下胎膜上找正后,放下上胎膜,再打压,打压时要求两台油压顶同时加压,步调要一致。
通过实施该工艺,较好地解决了炉壳冷压技术难关。
3.5 误差校正
将压制成型的每块炉皮按弧度、高度、对角线逐项检查,并将偏差控制在±2mm以内,
超差处钢材许可校正方法将各尺寸校正合格。
特别要注意其扭角、弧度不自然等情况,校正方法要得当。
3.6 合装及预装
球段炉壳要先合装一次,将每块炉壳处理合格后,才能进入预装,而直段炉壳处理好后可直接进入预装。
每块炉壳处理合格后,按要求点焊好各预装所需固定器、脚手架环以及各件逐一对号入座。
预装时的注意事项为:①、基准尺寸必须找准;②、在预装中出现水平度、错边、扭角等方面的较大问题时,必须找准原因,制定切实可行的措施进行处理,以达到技术规范的要求,严禁任意修口或强拉硬压。
预装技术规范为:①、每带的水平度相邻点在±1mm,对应点在±2mm以内;②、各缝错边在±1.5mm以内;③、间隙在3~6mm以内;④、垂直度在±2mm以内;⑤、各带的椭圆度在±5mm以内。
本次预装每次分三带进行,每三带装完后,将最上一带作为下三带预装的底带,依次循环。
每三带预装完后,记录各要求数据,并在炉壳上返出热风口中心线,并做好标记符号,写明“热风口中心线”字样。
经检验合格后,再焊各固定卡具。
4.结束语
制作2#高炉热风炉炉壳过程中,借鉴了以往转炉炉壳制作经验,并针对热风炉炉壳实际,制定了热风炉炉壳的制作工艺,并采取一系列切实可行技术措施,把住了每道工序质量关,经检验,热风炉炉壳的质量达制作要求,能够满足公司生产需要。