吸收塔的设计和选型
吸收塔设计技术标准
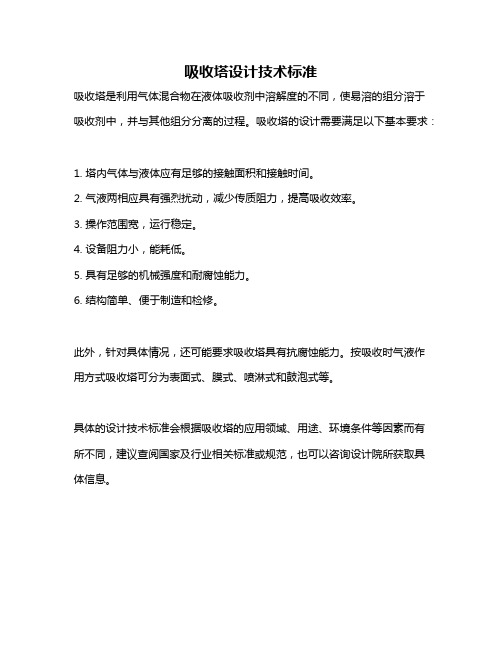
吸收塔设计技术标准
吸收塔是利用气体混合物在液体吸收剂中溶解度的不同,使易溶的组分溶于吸收剂中,并与其他组分分离的过程。
吸收塔的设计需要满足以下基本要求:
1. 塔内气体与液体应有足够的接触面积和接触时间。
2. 气液两相应具有强烈扰动,减少传质阻力,提高吸收效率。
3. 操作范围宽,运行稳定。
4. 设备阻力小,能耗低。
5. 具有足够的机械强度和耐腐蚀能力。
6. 结构简单、便于制造和检修。
此外,针对具体情况,还可能要求吸收塔具有抗腐蚀能力。
按吸收时气液作用方式吸收塔可分为表面式、膜式、喷淋式和鼓泡式等。
具体的设计技术标准会根据吸收塔的应用领域、用途、环境条件等因素而有所不同,建议查阅国家及行业相关标准或规范,也可以咨询设计院所获取具体信息。
水吸收SO2过程填料吸收塔的设计
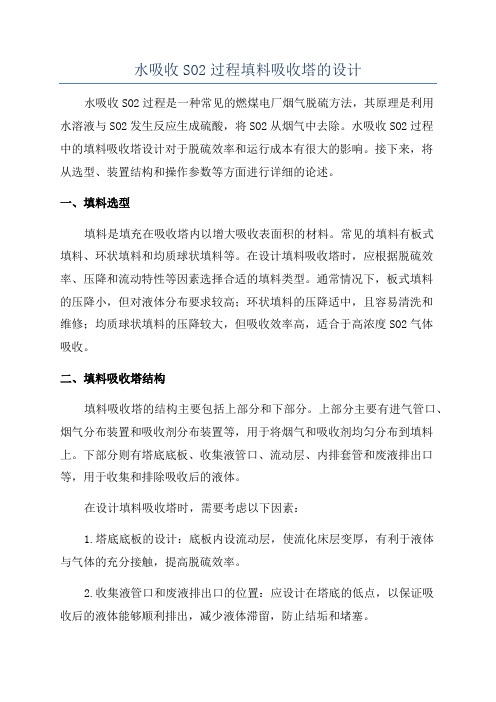
水吸收SO2过程填料吸收塔的设计水吸收SO2过程是一种常见的燃煤电厂烟气脱硫方法,其原理是利用水溶液与SO2发生反应生成硫酸,将SO2从烟气中去除。
水吸收SO2过程中的填料吸收塔设计对于脱硫效率和运行成本有很大的影响。
接下来,将从选型、装置结构和操作参数等方面进行详细的论述。
一、填料选型填料是填充在吸收塔内以增大吸收表面积的材料。
常见的填料有板式填料、环状填料和均质球状填料等。
在设计填料吸收塔时,应根据脱硫效率、压降和流动特性等因素选择合适的填料类型。
通常情况下,板式填料的压降小,但对液体分布要求较高;环状填料的压降适中,且容易清洗和维修;均质球状填料的压降较大,但吸收效率高,适合于高浓度SO2气体吸收。
二、填料吸收塔结构填料吸收塔的结构主要包括上部分和下部分。
上部分主要有进气管口、烟气分布装置和吸收剂分布装置等,用于将烟气和吸收剂均匀分布到填料上。
下部分则有塔底底板、收集液管口、流动层、内排套管和废液排出口等,用于收集和排除吸收后的液体。
在设计填料吸收塔时,需要考虑以下因素:1.塔底底板的设计:底板内设流动层,使流化床层变厚,有利于液体与气体的充分接触,提高脱硫效率。
2.收集液管口和废液排出口的位置:应设计在塔底的低点,以保证吸收后的液体能够顺利排出,减少液体滞留,防止结垢和堵塞。
3.塔体结构的牢固性:由于塔内液体的冲击和流动压力较大,塔体结构需要有足够的强度和刚度以承受这种压力,同时要考虑良好的密封性。
4.渗漏和冲击的处理:填料吸收塔内常常存在渗漏和冲击现象,应设计避免二次喷洒和渗漏的结构,同时防止冲击和振动对填料吸收塔的影响。
三、操作参数填料吸收塔的操作参数对于脱硫效率和运行成本也有重要影响,其中包括液气比、塔温和pH值等。
1.液气比:液气比是指吸收液和烟气之间的质量比。
液气比较小时,吸收剂的成本较低,但吸收效率较低,反之亦然。
因此,在设计填料吸收塔时,需要根据脱硫要求和成本考虑确定液气比。
hcl含量5%吸收塔设计

hcl含量5%吸收塔设计
根据提供的信息,“HCl含量5%吸收塔”的设计通常需要考虑
以下几个方面:
1. 塔内设计:吸收塔是用于将HCl气体从气相吸收至液相的
装置,其内部通常包括塔床、填料层、旋流器、分布器、集液器和液体循环系统等部件。
设计时需要确定合适的塔床高度、填料类型和填料高度,以及旋流器和分布器的尺寸和位置等。
2. 塔外设计:吸收塔的外部设计包括塔壳、进出料口、管道连接、附件和支撑结构等。
塔壳通常需要满足压力容器设计标准,进出料口和管道连接要求符合工艺流程和安全要求,同时还需要设计合适的附件(如防爆装置、温度传感器等)和支撑结构。
3. 液相循环系统设计:HCl吸收塔中的液相循环系统负责将吸
收液循环回塔顶,并对吸收液进行再生或处理。
设计时需考虑合适的泵型、泵量和循环管道布置,以确保循环系统的稳定和高效运行。
4. 选型与模拟计算:根据具体的工艺要求和设备参数,需要根据HCl含量5%的气相流量和温度等信息,选择合适的设备或
填料,并进行模拟计算以评估吸收效果和设备性能。
以上只是关于“HCl含量5%吸收塔”的设计一些基本要点。
具
体的设计过程还需要详细的工艺和设备参数,以及操作条件等。
设计过程中还需要确保符合相关的设计规范和安全要求。
因此,建议在实际设计中,寻求专业工程师或相关专家的帮助和指导。
湿法脱硫工艺吸收塔及塔内件的设计选型

湿法脱硫工艺吸收塔及塔内件的设计选型1 吸收塔塔型的选择在湿法脱硫工艺中,吸收塔是一个核心部件,一个湿法脱硫工程能否成功,关键看吸收塔、塔内件及与之相匹配的附属设备的设计选型是否合理可靠。
在脱硫工程中运行阻力小、操作方便可靠的吸收塔和塔内件的布置形式,将具有较大的发展前景。
目前,在国内的脱硫工程中,应用较多的吸收塔塔型有喷淋吸收空塔、托盘塔、液柱塔、喷射式鼓泡塔等。
国内学者曾在实验室里对各种塔型做了实验测试(见图1),从测试情况看,在塔内烟气流速相同的情况下,喷淋吸收空塔的系统阻力最小,液柱塔的阻力次之,托盘塔的阻力相对较大。
由于喷淋吸收空塔塔内件较少,结垢的机率较小,运行维修成本较低,因此喷淋吸收空塔已逐渐成为目前应用最广泛的塔型之一。
图2为喷淋吸收空塔(以下简称吸收塔)的结构简图。
2 喷淋吸收空塔主要工艺设计参数(1)烟气流速在保证除雾器对烟气中所携带水滴的去除效率及吸收系统压降允许的条件下,适当提高烟气流速,可加剧烟气和浆液液滴之间的湍流强度,从而增加两者之间的接触面积。
同时,较高的烟气流速还可持托下落的液滴,延长其在吸收区的停留时间,从而提高脱硫效率。
另外,较高的烟气流速还可适当减少吸收塔和塔内件的几何尺寸,提高吸收塔的性价比。
在吸收塔中,烟气流速通常为3~4.5m/s。
许多工程实践表明,3.6m/s≤烟气流速(110%过负荷)≤4.2m/s是性价比较高的流速区域。
(2)液气比(L/G)L/G决定了SO2的吸收表面积。
在吸收塔中,喷淋雾滴的表面积与浆液的喷淋速率成一定的比例关系。
当烟气流速确定以后,L/G成为了影响系统性能的最关键变量,这是因为浆液循环率不仅会影响吸收表面积,还会影响吸收塔的其他设计,如雾滴的尺寸等。
L/G的主要影响因素有:吸收区体积、SO2的去除效率、吸收塔空塔速率、原烟气的SO2浓度、吸收塔浆液的氯含量等。
根据吸收塔吸收传质模型及气液平衡数据计算出液气比(L/G),从而确定浆液循环泵的流量。
吸收塔设计条件2

吸收塔设计条件
一、物料
气相:含有N 2H 4、NH 3的饱和水蒸气 液相:(N 2H 5)2SO 4、(NH 4)2SO 4的酸性水溶液 二、原理
塔内主要发生的是肼的中和反应,其电离平衡如下:
N 2H 4 + H + = N 2H 5+ H 2O (气)=3×10-6
吸收操作的目的是将气态易挥发的N 2H 4转化为离子态,而达到净化蒸气和回收N 2H 4的目的。
工艺需要选择压降小的塔形,以旋流塔为例,其满足工艺要求的外形如图:
进气
出气
液位视镜液位
取样出料加
酸
三、共需4台塔,初步参数如下:
四、其它
需选择耐酸腐蚀材质或内衬、喷涂耐腐层,保证在以上温度和压力条件下正常使用。
以上参数为我公司基于工艺条件的初步估算,请在具体设计时做相应调整。
宁夏日盛实业有限公司。
气田天然气吸收塔设计

气田天然气吸收塔设计
气田天然气吸收塔的设计需要考虑以下因素:
1. 气体性质:气体的物理特性和化学性质对吸收塔的设计具有重要影响。
需要了解气体的成分、密度、流量、温度、压力等信息。
2. 操作条件:需要考虑吸收塔的操作压力、温度、流量、载荷等参数,以便确保塔内操作的稳定性和效率。
3. 选择吸收剂:吸收塔的设计需要选取适合的吸收剂,以便达到吸附和去除气体的目的。
吸收剂的选取应考虑吸收剂的稳定性、效率、成本等因素。
4. 塔的材质:吸收塔的材质需要选取抗腐蚀、抗高压、抗高温、耐磨损等特性的材料。
5. 塔的结构:吸收塔的结构应该有一定的形式,以便实现操作过程中气体和吸收剂的有效接触和混合。
另外,需要考虑吸收塔的安装和维护。
总之,吸收塔的设计需要全方位考虑各种因素,以便有效地去除气体中的有害成分。
具体设计规范见相关行业标准。
吸收塔的设计

课程设计任务书1.设计题目:水吸收二氧化硫过程填料吸收塔的设计矿石焙烧炉送出的气体冷却到25℃后送入填料塔中,用20℃清水洗涤除去其中的SO2。
入塔的炉气流量为2250m3/h,其中进塔SO2的摩尔分数为0.05,要求SO2的吸收率为96%。
吸收塔为常压操作,因该过程液气比很大,吸收温度基本不变,可近似取为清水的温度。
吸收剂的用量为最小量的1.4倍。
2.工艺操作条件:(1) 操作平均压力常压101.325kpa(2) 操作温度t=20℃(4) 所用填料为D N38聚丙烯阶梯环形填料。
3.设计任务完成填料吸收塔的工艺设计与计算,有关附属设备的设计和选型,绘制吸收系统工艺流程图和吸收塔工艺条件图,编写设计说明书。
目录摘要 (1)1绪论 (2)1.1吸收技术概况 (2)1.2吸收过程对设备的要求及设备的发展概况 (2)1.3吸收在工业生产中的应用 (2)1.3.1吸收的应用概况 (3)1.3.2典型吸收过程 (3)2设计方案 (4)2.1吸收方法及吸收剂的选择 (4)2.1.1吸收方法 (4)2.1.2吸收剂的选择: (4)2.2吸收工艺的流程 (5)2.2.1吸收工艺流程的确定 (5)2.2.2吸收工艺流程图及工艺过程说明 (6)2.3操作参数的选择 (6)2.3.1操作温度的选择 (6)2.3.2操作压力的选择 (6)2.3.3吸收因子的选择 (7)2.4吸收塔设备及填料的选择 (8)2.4.1吸收塔的设备选择 (8)2.4.2填料的选择 (8)3吸收塔的工艺计算 (9)3.1基础物性数据 (9)3.1.1液相物性数据 (9)3.1.2气相物性数据 (9)3.1.3气液平衡数据 (9)3.2物料衡算 (10)3.3塔径的计算 (10)3.3.1塔径的计算 (10)3.3.2泛点率校核 (11)3.3.3填料规格校核: (11)3.3.4液体喷淋密度校核 (11)3.4填料层高度计算 (11)H计算 (11)3.4.1传质单元高度OG3.4.2填料层高度Z的计算: (12)3.5填料层压降ΔP的计算: (12)3.6填料塔附属高度计算 (13)3.7离心泵的选择3.8进出液气接管管口的计管结论 (13)参考文献 (14)主要符号说明 (14)在化工生产中,气体吸收过程是利用气体混合物中,各组分在液体中溶解度或化学反应活性的差异,在气液两相接触是发生传质,实现气液混合物的分离。
吸收塔的设计选型和计算
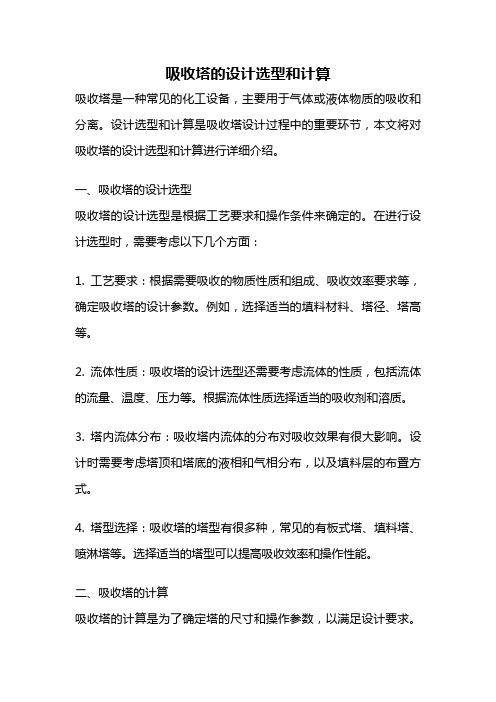
吸收塔的设计选型和计算吸收塔是一种常见的化工设备,主要用于气体或液体物质的吸收和分离。
设计选型和计算是吸收塔设计过程中的重要环节,本文将对吸收塔的设计选型和计算进行详细介绍。
一、吸收塔的设计选型吸收塔的设计选型是根据工艺要求和操作条件来确定的。
在进行设计选型时,需要考虑以下几个方面:1. 工艺要求:根据需要吸收的物质性质和组成、吸收效率要求等,确定吸收塔的设计参数。
例如,选择适当的填料材料、塔径、塔高等。
2. 流体性质:吸收塔的设计选型还需要考虑流体的性质,包括流体的流量、温度、压力等。
根据流体性质选择适当的吸收剂和溶质。
3. 塔内流体分布:吸收塔内流体的分布对吸收效果有很大影响。
设计时需要考虑塔顶和塔底的液相和气相分布,以及填料层的布置方式。
4. 塔型选择:吸收塔的塔型有很多种,常见的有板式塔、填料塔、喷淋塔等。
选择适当的塔型可以提高吸收效率和操作性能。
二、吸收塔的计算吸收塔的计算是为了确定塔的尺寸和操作参数,以满足设计要求。
吸收塔的计算主要包括以下几个方面:1. 塔径计算:根据流体的流量和操作要求,计算出吸收塔的塔径。
塔径的大小直接影响到液相和气相的接触效果和传质速率。
2. 塔高计算:根据吸收效率、塔径和填料性能等因素,计算出吸收塔的塔高。
塔高的大小决定了流体在塔内停留的时间,对传质效果有重要影响。
3. 填料计算:选择合适的填料材料,并根据填料的性能参数,计算填料层的高度和填料比表面积。
填料的选择和布置对吸收效果有重要影响。
4. 液相和气相流速计算:根据液相和气相的流量和流速要求,计算出液相和气相的流速。
流速的大小会影响到液相和气相的接触程度和传质速率。
5. 塔内压降计算:根据流体的性质和操作要求,计算出吸收塔的压降。
压降的大小对塔的能耗和操作费用有影响。
吸收塔的设计选型和计算是一项复杂而关键的工作,需要综合考虑多个因素。
合理的设计选型和计算可以提高吸收塔的吸收效率和操作性能,降低能耗和成本。
- 1、下载文档前请自行甄别文档内容的完整性,平台不提供额外的编辑、内容补充、找答案等附加服务。
- 2、"仅部分预览"的文档,不可在线预览部分如存在完整性等问题,可反馈申请退款(可完整预览的文档不适用该条件!)。
- 3、如文档侵犯您的权益,请联系客服反馈,我们会尽快为您处理(人工客服工作时间:9:00-18:30)。
Gm y1 − y 2 Gm y1 − y 2 = * * * * ∆y m kya k y a ( y1 − y1 ) − ( y2 − y2 ) * y − y1 ln( 1 ) * y2 − y2
k y a = k Y a =9.81×10 −4 G 0.7W 0.25 [ 4 ]
k L a = ∂W 0.82
其中:H0 为传质单元高度:H0=Gm/(kya)(ka 为污染物气相摩尔差推动力的总 传质系数,a 为塔内单位体积中有效的传质面积。 ) NTU 为传质单元数,近似数值为 NTU=(y1-y2)/ △ym,即气相总的浓 度变化除于平均推动力△ym=(△y1-△y2)/ln(△y1/△y2)(NTU 是表征吸收困难程 度的量,NTU 越大,则达到吸收目标所需要的塔高随之增大。 根据(1)可知:h=H0×NTU=
ζ =3600×
在喷淋塔操作温度
64 273 * u * y1η / h 22.4 273 + t
(7)
100 + 50 = 75 ° C 下、烟气流速为 u=3.5m/s、脱硫效率η =0.95 2
前 面 已经 求得原来 烟气二氧 化 硫 SO 2 质量浓度 为 a (mg/ m 3 ) 且 a=1.18 × 10 4 mg/m 3 而原来烟气的流量(145 ° C 时)为 20×10 4 (m 3 /h)换算成标准状态时(设为 V a ) 已经求得 V a =1.31×10 5 m 3 /h=36.30 m 3 /s
[ 4]
(2)
其中: y1,y2 为脱硫塔内烟气进塔出塔气体中 SO2 组分的摩尔比, kmol(A)/kmol(B)
* * , y2 为与喷淋塔进塔和出塔液体平衡的气相浓度,kmol(A)/kmol(B) y1
kya 为气相总体积吸收系数,kmol/(m3 . h﹒kpa)
x2,x1 为喷淋塔石灰石浆液进出塔时的 SO2 组分摩尔比,kmol(A)/kmol(B) G 气相空塔质量流速,kg/(m2﹒h) W 液相空塔质量流速,kg/(m2﹒h) y1×=mx1, y2×=mx2 (m 为相平衡常数,或称分配系数,无量纲) kYa 为气体膜体积吸收系数,kg/(m2﹒h﹒kPa) kLa 为液体膜体积吸收系数,kg/(m2﹒h﹒kmol/m3) 式(2)中 ∂ 为常数,其数值根据表 2[4]
烟气脱硫工艺主要设备吸收塔设计和选型
4.1 吸收塔的设计 吸收塔是脱硫装置的核心,是利用石灰石和亚硫酸钙来脱去烟气中二氧化硫 气体的主要设备,要保证较高的脱硫效率,必须对吸收塔系统进行详细的计算, 包括吸收塔的尺寸设计,塔内喷嘴的配置,吸收塔底部搅拌装置的形式的选择、 吸收塔材料的选择以及配套结构的选择(包括法兰、人孔等) 。 4.1.1 吸收塔的直径和喷淋塔高度设计 本脱硫工艺选用的吸收塔为喷淋塔,喷淋塔的尺寸设计包括喷淋塔的高度设 计、喷淋塔的直径设计 4.1.1.1 喷淋塔的高度设计 喷淋塔的高度由三大部分组成,即喷淋塔吸收区 高度、喷淋塔浆液池高度和喷淋塔除雾区高度。但是吸收区高度是最主要的,计 算过程也最复杂,次部分高度设计需将许多的影响因素考虑在内。而计算喷淋塔 吸收区高度主要有两种方法: (1) 喷淋塔吸收区高度设计(一) 达到一定的吸收目标需要一定的塔高。通常烟气中的二氧化硫浓度比较低。 吸收区高度的理论计算式为 h=H0×NTU (1)
故在标准状态下、单位时间内每立方米烟气中含有二氧化硫质量为
m SO2 =36.30×1.18×10 4 mg/m 3 =42.83×10 4 mg =428.3g
V SO2 = 428.3 g × 22.4 L/mol =149.91L/s=0.14991 m 3 /s≈0.15 m 3 /s 64 g / mol
ζ =G(y1-y2)/h
(5)
吸收效率 ζ =1-y 1 /y 2 ,按照排放标准,要求脱硫效率至少 95%。二氧化硫质量浓 度应该低于 580mg/m3(标状态)
所以
y 1 η ≥y 1 -0.0203%
(6)
又因为 G=22.4×(273+t)/273=u(流速) 将式子(5) ζ 的单位换算成 kg/( m 2 .s),可以写成
e.烟气流速。通过除雾器断面的烟气流速过高或过低都不利于除雾器的正常 运行 ,烟气流速过高易造成烟气二次带水,从而降低除雾效率,同时流速高系统阻 力大,能耗高。通过除雾器断面的流速过低,不利于气液分离,同样不利于提高除雾 效率。设计烟气流速应接近于临界流速。根据不同除雾器叶片结构及布置形式, 设计流速一般选定在 3.5~5.5m/ s 之间。本方案的烟气设计流速为 6.9m/s。 f.除雾器叶片间距。 除雾器叶片间距的选取对保证除雾效率 ,维持除雾系统稳 定运行至关重要。叶片间距大 ,除雾效率低 ,烟气带水严重 ,易造成风机故障 , 导致整个系统非正常停运。 叶片间距选取过小,除加大能耗外 ,冲洗的效果也有所 下降 ,叶片上易结垢、堵塞 ,最终也会造成系统停运。叶片间距一般设计在 20~ 95mm。目前脱硫系统中最常用的除雾器叶片间距大多在 30~50mm。 g.除雾器冲洗水压。除雾器水压一般根据冲洗喷嘴的特征及喷嘴与除雾器之 间的距离等因素确定,喷嘴与除雾器之间距离一般小于 1m ,冲洗水压低时,冲洗 效果差,冲洗水压过高则易增加烟气带水,同时降低叶片使用寿命。 h.除雾器冲洗水量。选择除雾器冲水量除了需满足除雾器自身的要求外,还 需考虑系统水平衡的要求,有些条件下需采用大水量短时间冲洗,有时则采用小水 量长时间冲洗,具体冲水量需由工况条件确定,一般情况下除雾器断面上瞬时冲洗 耗水量约为 1-4m3/m2.h ③ 除雾器的最终设计参数 本设计中设定最下层冲洗喷嘴距最上层喷淋层 3m。 距离最上层冲洗喷嘴 3.5m。 1)数量:1 套× 1units=套 2)类型:V 型 级数:2 级
因而选择合适的烟气速度是很重要的, 典型的 FGD 脱硫装置的液气比在脱硫 率固定的前提下,逆流式吸收塔的烟气速度一般在 2.5-5m/s 范围内[5][6],本设计 方案选择烟气速度为 3.5m/s。 湿法脱硫反应是在气体、液体、固体三相中进行的,反应条件比较理想,在脱 硫效率为 90%以上时(本设计反案尾 5%) ,钙硫比(Ca/S)一般略微大于 1,最佳 状态为 1.01-1.02,而比较理想的钙硫比(Ca/S)为 1.02-1.05,因此本设计方案选择 的钙硫比(Ca/S)为 1.02。 (3)喷淋塔吸收区高度的计算 含有二氧化硫的烟气通过喷淋塔将此过程中塔内总的二氧化硫吸收量平均到 吸收区高度内的塔内容积中,即为吸收塔的平均容积负荷――平均容积吸收率, 以 ζ 表示。 首先给出定义,喷淋塔内总的二氧化硫吸收量除于吸收容积,得到单位时间 单位体积内的二氧化硫吸收量
表3 温度与 ∂ 值的关系
温度/
∂
10 0.0093
15 0.0102
20 0.0116
25 0.0128
30 0.0143
采用吸收有关知识来进行吸收区高度计算是比较传统的高度计算方法, 虽然计 算步骤简单明了,但是由于石灰石浆液在有 喷淋塔自上而下的流动过程中由于 石灰石浓度的减少和亚硫酸钙浓度的不断增加, 石灰石浆液的吸收传质系数也在 不断变化,如果要算出具体的瞬间数值是不可能的,因此采用这种方法计算难以 得到比较精确的数值。 以上是传统的计算喷淋塔吸收区高度的方法,此外还有另外一种方法可以计 算。 (2) 喷淋塔吸收区高度设计(二) 采用第二种方法计算,为了更加准确,减 少计算的误差,需要将实际的喷淋塔运行状态下的烟气流量考虑在内。而这部分 的计算需要用到液气比(L/G) 、烟气速度 u(m/s)和钙硫摩尔比(Ca/S)的值。 本设计中的液气比 L/G 是指吸收剂石灰石液浆循环量与烟气流量之比值 (L/M3) 。如果增大液气比 L/G,则推动力增大,传质单元数减少,气液传质面 积就增大,从而使得体积吸收系数增大,可以降低塔高。在一定的吸收高度内液 气比 L/G 增大,则脱硫效率增大。但是,液气比 L/G 增大,石灰石浆液停留时 间减少,而且循环泵液循环量增大,塔内的气体流动阻力增大使得风机的功率增 大,运行成本增大。在实际的设计中应该尽量使液气比 L/G 减少到合适的数值 同时有保证了脱硫效率满足运行工况的要求。 湿法脱硫工艺的液气比的选择是关键的因素,对于喷淋塔,液气比范围在 8L/m 3 -25 L/m 3 之间 [5] , 根据相关文献资料可知液气比选择 12.2 L/m 3 是最佳的数 值[5][6]。 烟气速度是另外一个因素,烟气速度增大,气体液体两相截面湍流加强,气 体膜厚度减少,传质速率系数增大,烟气速度增大回减缓液滴下降的速度,使得 体积有效传质面积增大,从而降低塔高。但是,烟气速度增大,烟气停留时间缩 短,要求增大塔高,使得其对塔高的降低作用削弱。
其中: G 为载气流量(二氧化硫浓度比较低, 可以近似看作烟气流量), kmol/( m2.s) Y1,y2 分别为、 进塔出塔气体中二氧化硫的摩尔分数 (标准状态下的体积分数) ky 单位体积内二氧化硫以气相摩尔差为推动力的总传质系数,kg/(m3﹒s) a 为单位体积内的有效传质面积,m2/m3. ∆y m 为平均推动力,即塔底推动力,△ym=(△y1-△y2)/ln(△y1/△y2) 所以
故吸收区高度 h=18.33≈18.3m (4)喷淋塔除雾区高度(h3)设计(含除雾器的计算和选型) 吸收塔均应装备除雾器,在正常运行状态下除雾器出口烟气中的雾滴浓度应 该不大于 75mg/m3 [9] 。 除雾器一般设置在吸收塔顶部(低流速烟气垂直布置)或出口烟道(高流速
烟气水平布置),通常为二级除雾器。除雾器设置冲洗水,间歇冲洗冲洗除雾器。 湿法烟气脱硫采用的主要是折流板除雾器,其次是旋流板除雾器。 ① 除雾器的选型 折流板除雾器 折流板除雾器是利用液滴与某种固体表面相撞击而将液滴凝 聚并捕集的,气体通过曲折的挡板,流线多次偏转,液滴则由于惯性而撞击在挡 板被捕集下来。通常,折流板除雾器中两板之间的距离为 20-30mm,对于垂直 安置,气体平均流速为 2-3m/s;对于水平放置,气体流速一般为 6-10m/s。气 体流速过高会引起二次夹带。 旋流板除雾器 气流在穿过除雾器板片间隙时变成旋转气流,其中的液滴在 惯性作用下以一定的仰角射出作螺旋运动而被甩向外侧,汇集流到溢流槽内,达 到除雾的目的,除雾率可达 90%-99%。 喷淋塔除雾区分成两段,每层喷淋塔除雾器上下各设有冲洗喷嘴。最下层冲 洗喷嘴距最上层喷淋层(3-3.5)m,距离最上层冲洗喷嘴(3.4-32)m。 ② 除雾器的主要设计指标 a.冲洗覆盖率:冲洗覆盖率是指冲洗水对除雾器断面的覆盖程度。冲洗覆盖 率一般可以选在 100 %~300 %之间。