钨钛合金切削液
车刀刃磨技术2
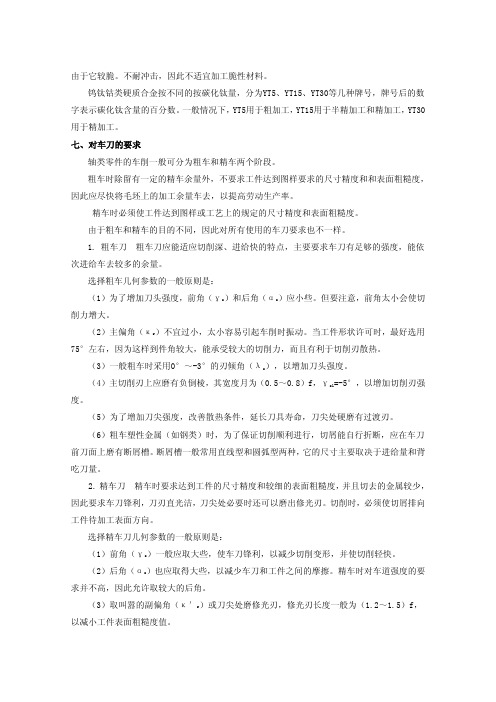
由于它较脆。
不耐冲击,因此不适宜加工脆性材料。
钨钛钴类硬质合金按不同的按碳化钛量,分为YT5、YT15、YT30等几种牌号,牌号后的数字表示碳化钛含量的百分数。
一般情况下,YT5用于粗加工,YT15用于半精加工和精加工,YT30用于精加工。
七、对车刀的要求轴类零件的车削一般可分为粗车和精车两个阶段。
粗车时除留有一定的精车余量外,不要求工件达到图样要求的尺寸精度和和表面粗糙度,因此应尽快将毛坯上的加工余量车去,以提高劳动生产率。
精车时必须使工件达到图样或工艺上的规定的尺寸精度和表面粗糙度。
由于粗车和精车的目的不同,因此对所有使用的车刀要求也不一样。
1. 粗车刀 粗车刀应能适应切削深、进给快的特点,主要要求车刀有足够的强度,能依次进给车去较多的余量。
选择粗车几何参数的一般原则是:(1)为了增加刀头强度,前角(γo)和后角(αo)应小些。
但要注意,前角太小会使切削力增大。
(2)主偏角(κr)不宜过小,太小容易引起车削时振动。
当工件形状许可时,最好选用75°左右,因为这样到件角较大,能承受较大的切削力,而且有利于切削刃散热。
(3)一般粗车时采用0°~-3°的刃倾角(λs),以增加刀头强度。
(4)主切削刃上应磨有负倒棱,其宽度月为(0.5~0.8)f,γo1=-5°,以增加切削刃强度。
(5)为了增加刀尖强度,改善散热条件,延长刀具寿命,刀尖处硬磨有过渡刃。
(6)粗车塑性金属(如钢类)时,为了保证切削顺利进行,切屑能自行折断,应在车刀前刀面上磨有断屑槽。
断屑槽一般常用直线型和圆弧型两种,它的尺寸主要取决于进给量和背吃刀量。
2. 精车刀 精车时要求达到工件的尺寸精度和较细的表面粗糙度,并且切去的金属较少,因此要求车刀锋利,刀刃直光洁,刀尖处必要时还可以磨出修光刃。
切削时,必须使切屑排向工件待加工表面方向。
选择精车刀几何参数的一般原则是:(1)前角(γo)一般应取大些,使车刀锋利,以减少切削变形,并使切削轻快。
金属切削液的基本知识

金属切削的基本知识切削液的配比(1)苏打水苏打(无水碳酸钠):1% 亚硝酸钠:0.25%---0.6% 水:余量将上述物质,加以3---4倍质量的热水(水温40---50度),搅拌3---5分钟,再加入剩余质量的水,再搅拌5分钟。
优点:冷却性能好,防腐蚀作用,良好的洗涤性,成本低(2)乳化液取1.5%---2.5%左右的乳化油,先用少量的温水融化,然后倒入储有足量水的水箱中即可。
但要求有较高的防锈,防腐蚀性能时,加入苏打和亚硝酸钠各0.2%左右。
优点:具有良好的冷却性能和润滑性能,有防腐蚀作用。
常用刀具材料有碳素工具钢、合金工具钢、高速钢、硬质合金等。
(1) 碳素工具钢(如T10、T12A)及合金工具钢(如9SiCr)特点是淬火硬度较高,价廉。
但耐热性能较差,淬火时易产生变形,通常只用于手工工具及形状较简单、切削速度较低的刀具。
(2) 高速钢高速钢是含有较多W、Mo、Cr、V 等元素的高合金工具钢。
高速钢具有较高的硬度(热处理硬度可达HRC62-67)和耐热性(切削温度可达500-600°C)。
它可以加工铁碳合金、非铁金属、高温合金等广泛的材料。
高速钢具有高的强度和韧性,抗冲击振动的能力较强,适宜制造各类刀具。
但因耐热温度较硬质合金低,故不能用于高速切削。
常用牌号分别是W18Cr4V和W6Mo5Cr4V2等。
(3) 硬质合金硬质合金是在高温下烧结而成的粉末冶金制品。
具有较的硬度(70~175HRC),能耐850℃~1000℃的高温,具有良好的耐磨性和耐热性以及高硬度。
因而其切削速度比高速钢刀锯提高2到3倍,主要用于高速切削,但其强度、韧性和工艺性不如高速钢,因此通常将硬质合金焊接或机械夹固在刀体(刀柄)上使用(如硬质合金车刀)。
常用的硬质合金有钨钴类(YG类)、钨钛钴类(YT类)和钨钛钽(铌)类硬质合金(YW类)三类。
① 钨钴类硬质合金(YG类) YG类硬质合金主要由WC和Co组成, YG类硬质合金的抗弯强度和冲击韧性较好,不易崩刃,很适宜切削切屑呈崩碎状的铸铁等脆性材料。
钨钢切削液

钨钢切削液
13年切削液生产研发经验,专业解决金属切削难题
钨钢切削液,具有高润滑及清洗性能,废宵沉淀快,内含特性防氧成份,可有效杜绝铜铝合金工件在加工后出现白斑或发黑等氧化变色现象。
适用于各种铝合金、铜合金、不锈钢等金属材料的切削,冲压,钻孔加工等。
【美科切削液全国招商火热进行中,诚邀您的加盟!】一、钨钢切削液参数:
二、钨钢切削液相关推荐:
三、钨钢切削液知识分享:
东莞美科钨钢切削液广泛用于电子和汽车工业。
尤其适合于解决在加工这些产品时经常遇见的一些问题,如不容易控制PH值、乳化液不稳定、产生氢气以及变色等问题。
适用于镁合金的加工,也适合于黑色金属、铝合金和以铜为基体的合金的加工。
特别是在难度较高
的加工条件下,如硬镁合金的绞孔、攻螺纹等更能发挥其优越的加工性能。
四、美科切削液格言分享:
我们不能总是为我们的青年造就美好未来,但我们能够为未来造就我们的青年一代。
美国总统罗斯福
只要一个人还有所追求,他就没有老。
直到后悔取代了梦想,一个人才算老。
美国演员巴里穆尔,J。
切削液分类及废切削液净化、处理

切削液分类及废切削液净化、处理一、切削液分类切削液(cuttingfluid,coolant)是一种用在金属切削、磨加工过程中,用来冷却和润滑刀具和加工件的工业用液体,切削液由多种超强功能助剂经科学复合配合而成,同时具备良好的冷却性能、润滑性能、防锈性能、除油清洗功能、防腐功能、易稀释特点。
克服了传统皂基乳化液夏天易臭、冬天难稀释、防锈效果差的的毛病,对车床漆也无不良影响,适用于黑色金属的切削及磨加工,属当前最领先的磨削产品。
切削液各项指标均优于皂化油,它具有良好的冷却、清洗、防锈等特点,并且具备无毒、无味、对人体无侵蚀、对设备不腐蚀、对环境不污染等特点。
1.分类水基的切削液可分为乳化液、半合成切削液和全合成切削液。
乳化液、半合成以及全合成的分类通常取决于产品中基础油的类别:乳化液是仅以矿物油作为基础油的水溶性切削液;半合成切削液是既含有矿物油又含有化学合成基础油的水溶性切削液;全合成切削液则是仅使用化学合成基础油(即不含矿物油)的水溶性切削液。
每一种类型的切削液都会含有除基础油以外的各种添加剂:防锈剂、有色金属腐蚀钝化剂、消泡剂等。
有些厂家会有微乳液的分类;通常认为是介于乳化液和半合成切削液之间的类别。
乳化液的稀释液在外观上呈乳白色;半合成液的稀释液通常呈半透明状,也有一些产品偏乳白色;全合成液的稀释液通常完全透明如水或略带某种颜色。
2、配方体系切削液配方主要成分包含主要成分有:乙二醇、四硼酸钠、偏硅酸钠、磷酸钠。
乙二醇:乙二醇乙二醇又名〃甘醇〃、〃L2-亚乙基二醇〃,简称EG o化学式为(HoCH2)2,是最简单的二元醇。
乙二醇是无色无臭、有甜味液体,对动物有毒性,人类致死剂量约为L6g∕kg0乙二醇能与水、丙酮互溶,但在醛类中溶解度较小。
用作溶剂、防冻剂以及合成涤纶的原料。
乙二醇的高聚物聚乙二醇(PEG)是一种相转移催化剂,也用于细胞融合;其硝酸酯是一种炸药。
四硼酸钠:四硼酸钠,或称硼砂,分子式Na2B4O7∙10H2O,是非常重要的含硼矿物及硼化合物。
2.3 切削条件的合理选择

(5) 涂层硬质合金
采用化学气相沉积(CVD)法或物理气相沉积 (PVD)法,在高韧性的硬质合金基体表面上涂覆 5~8um的一层耐磨性很高的金属化合物,涂层可采 用单涂层,也可采用双涂层或多涂层。
(5) 涂层硬质合金
涂层硬质合金比基体具有更高的硬度和耐磨性, 有低的摩擦系数和高的耐热性,切削力和切削温度均 比未涂层刀片低,因而刀具寿命可以提高好几倍,涂 层刀片可用于加工不同材料,通用性广。
2. 切削液的种类
1) 水溶液 2) 乳化液 3) 切削油
冷却作用 润滑作用
强
弱
弱
强
(1) 按加工性质选用
1) 粗加工时,应选用以冷却为主的水溶液或乳化 液。
2) 精加工时,应选用润滑为主的极压切削油或高 浓度的极压乳化液。
3) 钻削、铰削、拉削和深孔加工时,应选用粘度 较小的极压水溶液、极压乳化液和极压切削油,并应 加大流量和压力。
它是指在保证加工质量的前提下,充分利用刀具 和机床的性能,能获得高的生产率和低的加工成本的 切削用量。
1. 切削用量选择的原则
在切削过程中,切削用量三要素asp、f、vc对 切削生产率、刀具寿命和加工质量有着重大影响。
1. 切削用量选择的原则
材料切除率 Q = 1000 vc asp f (mm3/min)
min刀具寿命t可转位车刀1015硬质合金车刀2060高速钢车刀3090硬质合金端铣刀120180高速钢钻头80120齿轮刀具200300自动线上的刀具240480在制定工艺规程时一般情况下宜采用刀具的经济寿命t及其所允许的切削速度只有在紧急的单件生产市场紧缺或批量生产中出现薄弱环节时才采用最高生产率寿命t粗加工时首先应将精加工的和半精加工的余量留下来剩下的余量尽可能在一次走刀下切除
钛合金加工切削液选择

钛合金加工切削液选择
切削钛合金时,为了降低切削温度,应当向切削区域浇注大量的以冷却作用为主的切削液。
因为钛合金热导系数低,只有钢的1/7,铝的1/6,在切削液过程中热量不会迅速的随切屑传递出去,所以在加工是产生的温度达1000℃以上,容易使刀口过早磨损,制造成本增加。
对切削液的要求有导热系数大、比热大、热容量大、汽化热大、汽化速度快、流量大、流速快。
一般说来,水比油的导热系数大3~5倍,比热大1倍,汽化热几乎大10倍左右,故用水溶性切削液较为合适。
车、铣削钛合金时,常采用乳化液,或采用有极压添加剂的水溶性切削液,更不容易达到燃点温度。
加工速度只要只够低,任何尺寸大小的切屑。
钛合金加工最好不使用含氯的冷却液,避免产生有毒物质和引起氢脆,也能防止钛合金高温应力腐蚀开裂。
钛合金切削加工特点及刀具材料选用

钛合金切削加工特点及刀具材料选用钛合金切削加工特点及刀具材料选用2011-7-27钛合金以优异的综合力学性能、低密度以及良好的耐腐蚀性,被誉为是一种使人类走向太空时代的战略性金属材料,不仅在航空航天及军工领域得到广泛的使用,而且开始逐渐渗透到经济生活的各个方面。
随着中国航空航天事业的发展,钛合金的加工技术受到更多的关注和研究。
钛合金的分类钛合金按照不同的方法有不同的分类,最常用的分类方法是按退火后组织特点分类,可分成α、α+β、β型钛合金[1-4]。
α型钛合金密度小,有很好的热强性和热稳定性,焊接性能好,室温、超低温和高温性能良好,但不能进行热处理强化。
例如TiAl在600℃时,仍然有很高的强度,而且蠕变性能、热稳定性、疲劳性能和断裂韧性等方面都有好的表现,常用于喷气发动机涡轮盘和叶片的制造。
图1 钛合金航空发动机叶轮α+β型钛合金双相合金,组织稳定,韧性、塑性和高温变形性能随着β相稳定元素的增加而提高;有较好的热压力加工性,能进行淬火时效使合金强化,热处理后的强度约比退火状态提高50% ~100%;高温强度高,可在400~500℃的温度下长期工作,其热稳定性次于α钛合金。
α+β型钛合金中Ti-6Al-4V( 中国牌号TC4) 是钛合金中使用量最大的钛合金,在美国,其产量占钛合金产量一半以上,以其优良的综合力学性能和切削加工性大量用于航空零件制造[5-9]。
图1为钛合金航空发动机叶轮。
β钛合金是β相固溶体组成的单相合金,室温的强度较高,冷加工和冷成型加工能力强,未热处理即具有较高的强度,淬火时效后合金强度得到进一步强化,室温强度可达1372~1666MPa;但热稳定性较差,不宜在高温下使用[10-13]。
钛合金切削加工的特点钛合金本身所具有的物理和化学性能给切削加工带来了困难,具体表现有以下6点。
(1)钛合金的导热性差,是不良导热体金属材料。
由于导热、导温系数小,是45号钢的1/6,所以在加工时所产生的高热量不能有效扩散,同时刀具的切削刃和切屑的接触长度短,使热量大量聚集在切削刃上,温度急剧上升,导致刀刃的红硬性下降,刀刃软化,加快刀具磨损[14]。
金属切削刀具的切削试验方法考核试卷

9.金属切削过程中,所有的磨损都是由于磨粒磨损造成的。()
10.在金属切削中,加工精度主要受到刀具磨损的影响。()
五、主观题(本题共4小题,每题5分,共20分)
1.请简述金属切削刀具的几何角度对切削力、切削温度和加工表面质量的影响。
2.描述金属切削过程中,如何通过选择合适的切削液来优化切削性能,并减少刀具磨损。
A.刀具材料
B.刀具几何角度
C.切削速度
D.刀具颜色
2.下列哪种材料的刀具适合于高速切削?()
A.高速钢
B.硬质合金
C.钨钢
D.铸铁
3.在金属切削过程中,下列哪种磨损形式最为常见?()
A.磨粒磨损
B.化学磨损
C.腐蚀磨损
D.热磨损
4.切削试验中,以下哪种切削液主要用途是冷却?()
A.油性切削液
B.水性切削液
A.手工刃磨
B.机械刃磨
C.电化学刃磨
D.激光修整
三、填空题(本题共10小题,每小题2分,共20分,请将正确答案填到题目空白处)
1.在金属切削过程中,切削力的三个主要分量分别是______、______和______。
2.金属切削刀具的______角度对切削力的大小有直接影响。
3.高速钢刀具适用于______切削速度的加工。
4.硬质合金刀具的主要成分是______和______。
5.切削液在金属切削过程中的作用包括______、______和______。
6.为了提高金属切削的效率,可以采取的措施有______、______和______。
7.金属切削刀具的磨损主要分为______磨损、______磨损和______磨损。
- 1、下载文档前请自行甄别文档内容的完整性,平台不提供额外的编辑、内容补充、找答案等附加服务。
- 2、"仅部分预览"的文档,不可在线预览部分如存在完整性等问题,可反馈申请退款(可完整预览的文档不适用该条件!)。
- 3、如文档侵犯您的权益,请联系客服反馈,我们会尽快为您处理(人工客服工作时间:9:00-18:30)。
钨钛合金切削液
钨钛合金切削液,外观清澈透明,使用寿命长,具有极佳的润滑性能和防锈性能,可有效提高钛合金工件表面的光洁度,适用于钛合金、不锈钢、钨钢等金属的切削、磨削、钻孔作业。
一、钨钛合金切削液参数:
二、钨钛合金切削液相关推荐:
三、钨钛合金切削液知识分享:
切削液是一种用在金属切、削、磨加工过程中,用来冷却和润滑刀具和加工件的工业用液体切削液是金属切削加工的重要配套材料。
18世纪中后期以来,切削液在各种金属加工领域
中得到了广泛的应用。
20世纪初,人们从原油中提炼出大量润滑油,发明了各种润滑油添加剂,真正拉开了现代切削液技术的历史序幕。