FMEA培训教材
2024年度FMEA培训教材ppt完整版

等级并制定应对措施,可提高系统或产品的可靠性和安全性。
2024/3/23
02 03
改进策略的制定
根据FMEA分析结果,针对高风险和中风险故障模式制定改进策略,包 括设计优化、工艺改进、材料替换等,以降低故障发生的可能性和影响 程度。
改进效果的跟踪
实施改进策略后,需对改进效果进行跟踪和评估,确保改进措施的有效 性。同时,将改进经验反馈到FMEA分析中,不断完善和优化分析过程 。
掌握了FMEA实施的基本技能
通过课程中的案例分析和实践操作,学员们表示已经掌握 了FMEA实施的基本技能,能够独立完成简单的FMEA分析 工作。
增强了团队协作和沟通能力
在课程中,学员们分组进行讨论和案例分析,不仅增强了 团队协作能力,还提高了沟通能力。
34
未来发展趋势预测
2024/3/23
01 02 03
23
05 FMEA在产品设 计阶段应用实践
2024/3/23
24
产品设计阶段FMEA实施流程
流程概述
01 明确FMEA在产品设计阶段的
目标和重要性,以及实施的基 本步骤。
团队组建与培训
02 组建专业的FMEA团队,并进
行必要的培训和技能提升。
功能分析与结构分解
03 对产品的功能进行详细分析,
并进行结构分解,以明确潜在 故障模式。
12
评估方法选择及实施流程
• 方法选择:根据失效模式的性质和影响程度选择合适的评 估方法,如风险矩阵、风险指数等。
2024/3/23
13
评估方法选择及实施流程
实施流程
1. 明确评估目标和范围
2. 收集相关数据和信息
2024/3/23
14
FMEA培训教材
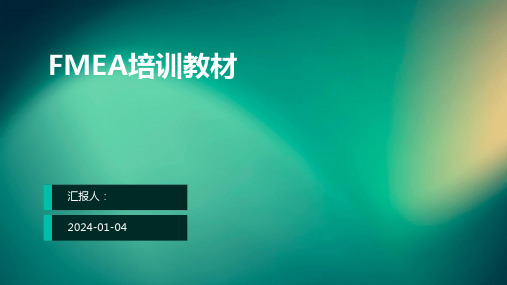
总结词
汽车刹车系统FMEA分析是一个典型的故障模式与影响 分析案例,通过对刹车系统的各个组成部分进行故障 模式分析,评估其对整个系统性能的影响。
详细描述
汽车刹车系统FMEA分析首先识别刹车系统中的各个组 成部分,然后对每个组成部分进行故障模式分析,包括 可能的故障类型、故障发生概率和故障影响程度。接着 ,根据分析结果,评估每个故障模式对刹车系统整体性 能的影响,并确定优先改进顺序。最后,制定相应的改 进措施和预防措施,降低故障发生概率和影响程度。
高级功能
介绍FMEA软件的高级功能,如 影响分析、优先级排序、报告 生成等。
常见问题与解决方案
列举使用FMEA软件过程中可能 遇到的问题,并提供相应的解 决方案。
FMEA软件应用实例
01
汽车刹车系统FMEA分析
通过实际案例,演示如何使用FMEA软件对汽车刹车系统进行故障模式
、影响和优先级分析,并提出相应的改进措施。
FMEA软件应用领域
FMEA软件广泛应用于汽车、航空、电子、医疗等制造业 领域,用于提高产品质量、降低产品风险和优化产品设计 。
FMEA软件操作教程
软件安装与启动
介绍如何下载和安装FMEA软件 ,以及如何启动软件并进入操 作界面。
基础操作
介绍FMEA软件的基本操作,如 创建项目、添加部件、设置故 障模式等。
感谢您的观看
FMEA的应用范围
总结词
FMEA可以应用于各种行业和领域,如汽车 、航空、医疗、电子等,用于评估产品设计 或流程的可靠性和安全性。
详细描述
FMEA是一种通用的质量工具,可以应用于 各种行业和领域。在汽车行业中,FMEA可 以用于评估汽车零部件的可靠性,提高车辆 的安全性能;在航空领域,FMEA可以用于 评估飞机设计和制造过程中的潜在故障模式 ,确保飞行的安全;在医疗领域,FMEA可 以用于评估医疗设备的可靠性和安全性,提 高患者的治疗效果;在电子行业,FMEA可 以用于评估产品的设计和制造流程,提高产 品的质量和可靠性。
FMEA培训教材
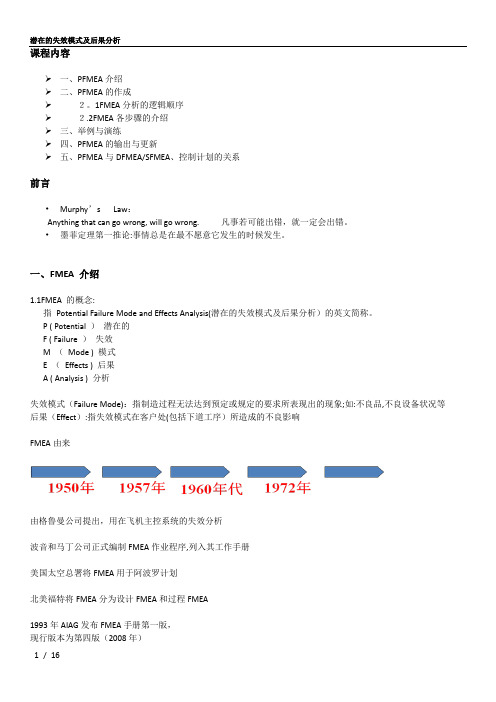
课程内容➢一、PFMEA介绍➢二、PFMEA的作成➢2。
1FMEA分析的逻辑顺序➢2.2FMEA各步骤的介绍➢三、举例与演练➢四、PFMEA的输出与更新➢五、PFMEA与DFMEA/SFMEA、控制计划的关系前言•Murphy’s Law:Anything that can go wrong, will go wrong. 凡事若可能出错,就一定会出错。
•墨菲定理第一推论:事情总是在最不愿意它发生的时候发生。
一、FMEA 介绍1.1FMEA 的概念:指Potential Failure Mode and Effects Analysis(潜在的失效模式及后果分析)的英文简称。
P ( Potential )潜在的F ( Failure )失效M (Mode ) 模式E (Effects ) 后果A ( Analysis ) 分析失效模式(Failure Mode):指制造过程无法达到预定或规定的要求所表现出的现象;如:不良品,不良设备状况等后果(Effect):指失效模式在客户处(包括下道工序)所造成的不良影响FMEA由来由格鲁曼公司提出,用在飞机主控系统的失效分析波音和马丁公司正式编制FMEA作业程序,列入其工作手册美国太空总署将FMEA用于阿波罗计划北美福特将FMEA分为设计FMEA和过程FMEA1993年AIAG发布FMEA手册第一版,现行版本为第四版(2008年)FMEA分类•DFMEA:system ,subsystem ,component•PFMEA:manufacturing,assembly•其他:MFMEA一、FMEA介绍:如何理解FMEA1。
FMEA是多方论证小组的工作2。
FMEA是预防的工具3。
FMEA是风险分析的工具4.FMEA是小组经验的累积5.FMEA是动态文件,在整个过程中更新FMEA —潜在的失效模式及后果分析,是“事前的预防措施”。
➢关键词:潜在的—失效还没有发生■可能发生■但不一定会发生➢“核心”集中于:预防-处理预计的失效,其原因及后果/影响➢主要工作:风险评估-潜在失效模式的后果影响➢FMEA 开始于产品设计和制造过程开发活动之前,并指导贯穿实施于整个产品周期1.2过程FMEA(也叫做P—FMEA):针对制造过程,重点分析由制造或装配过程缺陷引起的潜在产品失效.◆帮助分析的制造与装配过程;◆考虑到潜在制造和/或装配过程失效模式及其影响的可能性;◆鉴别过程缺陷,集中力量于控制,减少不合格产品或提高对不合格产品监测的方法;◆鉴别关键特性与重要特性,帮助制订全面的制造控制计划;◆建立过程改进措施的优先次序;◆将过程变更的编成文件以指导将来的制造/装配过程的发展。
FMEA培训教材-PPT精选全文

客户要求 方便调整
舒适 移动顺畅
ቤተ መጻሕፍቲ ባይዱ
产品规格 调节高度 坐垫厚度 旋转角度 椅轮松紧
9
1
3
9
3
1
9
9
重要性 60% 30% 10%
分值
640
330
180
90
FMEA 得原理
客户要求 方便调整
舒适 移动顺畅
分值
产品规格 调节高度 坐垫厚度 旋转角度 椅轮松紧
9
1
3
9
3
1
9
9
640
330
180
90
参数
上升50CM
FMEA 得原理
一、FMEA基本知识
练习:
公司产品:车门 客户要求:
•方便开关 •噪音小 •安全
FMEA 得原理
FMEA 得原理
FMEA 得原理
客户质量要求 Input
客户质量目标
FMEA Output
CTQ 清单 CP 控制计划
FMEA
FMEA 得原理
Output
CTQ 清单
CTQ产出原则:
压 合 状 态
方法
特
样本Sample
殊 特 性 分
产品特 性/过程 参数规 格/公差
评价/ 测量技
术
容 量
频率
类
《
首检
MODULE 检验标
准》
5-20倍 显微镜
6P CS
:6PCS/ 抽检 : 每10PCS
抽1PCS
反应计
控制方法/ 统计技术
责任人
划
《CD-HFM0419701 LCM 镜检 不良明细
措施?
fmea培训资料最新版(141页)

FMEA培训资料最新版(141页)FMEA(失效模式和影响分析)是一种系统的、结构化的方法,用于识别和评估产品或过程中的潜在失效模式,以及这些失效模式对最终用户的影响。
FMEA培训资料旨在帮助参与者了解FMEA的基本概念、方法和工具,以便在实际工作中应用FMEA来提高产品或过程的质量和可靠性。
一、FMEA概述FMEA是一种预防性的质量工具,它通过系统性地识别和分析潜在的失效模式,以及这些失效模式对产品或过程的影响,来降低失效风险。
FMEA通常分为两个阶段:设计FMEA(DFMEA)和过程FMEA (PFMEA)。
DFMEA关注于产品设计和开发阶段,而PFMEA关注于制造和装配过程。
二、FMEA的基本步骤1. 定义项目范围:确定要分析的系统和子系统的范围。
2. 建立团队:组建一个跨职能的团队,包括设计、工程、制造和质量等部门的代表。
3. 识别失效模式:团队成员共同识别潜在的失效模式,并记录下来。
4. 分析失效影响:评估每个失效模式对最终用户的影响,包括安全性、成本、性能和可维护性等方面。
5. 评估失效严重性:根据失效影响的严重程度,对每个失效模式进行评分。
6. 评估失效发生概率:根据失效模式的已知历史数据或专家经验,评估每个失效模式的发生概率。
7. 评估检测难度:评估检测每个失效模式的难度,包括检测方法的有效性和成本。
8. 计算风险优先级数(RPN):将严重性、发生概率和检测难度相乘,得到每个失效模式的风险优先级数。
9. 采取预防措施:根据RPN,制定和实施预防措施,以降低失效风险。
10. 跟踪和更新:定期跟踪和更新FMEA,以确保其持续有效。
三、FMEA工具和模板FMEA工具和模板可以帮助团队更有效地进行FMEA分析。
常用的FMEA工具包括:1. FMEA表格:用于记录失效模式、影响、严重性、发生概率、检测难度和RPN等信息。
2. FMEA软件:提供自动化的FMEA分析功能,包括数据输入、计算和分析报告。
FMEA培训教材(共30张)

7、确定當前的工序控制方法并評估其檢測失效的可能性,附表1、4。
8、确定 RPN 值并根据 RPN 值采取相應的改善措施,附表1。
第16页,共30页。
附表1:在附表 1 中包含以下 6 個方面的內容,因附表 1 容量
太大,另存在 Excel 中
第9页,共30页。
5、FMEA 的應用范圍(2)-品質改善程序
DFMEA
改善行動
消除變异
合并
惡性
良性
研究變异 的性質
PFMEA
控制(kòngzhì)方案
投入
工序
出貨
產品
改善系統
尋找預期 的變异
研究變异 的原因
第10页,共30页。
否
是否變 异?
是
研究 / 測量
与控制界限
進行比較
6、PFMEA 的程序步驟(2)
2、确定所要分析的失效模式 (potential failure mode), 附表1。
3、分析失效模式對客戶的所造成的影響 (potential failure effect), 附表1。
4、評估影響的嚴重程度 (severity), 附表1、2。 5、分析失效的可能原因 (failure cause),人、机、料、法、環等原
繪出流程(liúchéng)圖
确定各個工序的功能
确定失效模式
標識其效應
標識其原因
標識當前控制
方法
估計嚴重性 估計發生概率
估計測試性
RPN =O x S x D
是
RPN= 風險指數
制作 Pareto
圖
選擇失效模式
FMEA培训教材

12
2019/11/12
page
FMEA 培 训 教 材
潜在失效模式及后果分析与失效分析比较
失效分析
潜在的失效模式及后果分析
--产品设计FMEA不能依靠过程检测作为控制措施; · PFMEA应将DFMEA作为重要的输入,对DFMEA中标明的特
殊特性也必须在PFMEA中作为重点分析的内容。
21
2019/11/12
page
FMEA 培 训 教 材
十、FMEA同GB/T 18305 idt ISO/TS 16949的关系
ISO/TS 16949 2002 有关条款 --7.3.1.1 多方论证方法 --7.3.2.2 制造过程设计输入 --7.3.2.4 特殊特性 --7.3.3.1 产品设计输出—补充 --7.3.3.2 制造过程设计输出 --7.5.1.2 控制计划
---提高质量、可靠性和安全性。 ---针对失效可能产生的各个方面评价一个过程、设计或服务 ---持续地减少失效的频度持续地减少失效的后果。 ---防止现有的/潜原失效到达顾客处。 ---失效的风险顺序量化以引导采取措施。 ---优先使用行政的和工程的努力、时间、人力资源和其他资源。 ---运用团队原则和持续改进方法以获得好的产品。
3
2019/11/12
page
FMEA 培 训 教 材
(a) 发现并评价产品/过程中的潜在失效以及该失效的后果; (b) 确定能够消除或减少潜在失效发生机会的措施; (c) 将全部过程形成文件.
关于确定设计或过程必须做哪些事情才能使顾 客满意,FMEA是对这一过程的补充.
FMEA培训教材(PPT 99页)

DFMEA
第一版
原始稿日期
第二版
第三版
最新修订日期
DFMEA
8)核心小组 列出有权确定和/或执行任务的责任部门的 名称和个人的姓名(建议所有参加人员的姓 名、部门、电话、地址等都应记录在一张分发 表上。)
项目/功能要求 ➢ 填入被分析项目的名称和其他相关信息(如编号、零
件级别等)。利用工程图纸上标明的名称并指明设计水
察觉的现象相同。
➢ 潜在失效的后果,就是失效模式对系统功能的影响,可以使用顾客感受的语 言来描述.
➢ 要根据顾客可能发现或经历的情况来描述失效的后果,要记住顾客既可 能是内部的顾客也可能是最终用户。
➢ 如果失效模式影响可能影响安全性或对法规的符合性,要清楚地予以说 明。
➢ 失效的后果应按照所分析的具体的系统、子系统或部件来说明,还应记住 不同级别的部件、子系统和系统之间存在着一种系统层次上的关系。例 如,一个零件可能会断裂,这样会引起总成的振动、从而导致一个系统 间歇性运行。系统的间歇性运行可能会造成性能的下降并最终导致顾客 的不满。分析的意图就是在小组所拥有的知识层次上,尽可能的预测到 失效的后果。
知识的人员组成,(如设计、分析/试验、制造、装配、服务、 回收、质量及可靠性等方面有丰富经验的工程师)。 ➢ FMEA由责任单位的工程师开始启动,责任单位可能是原 设备制造厂(OEM,即生产最终产品)、供方或分承包方 ➢ FMEA工基本概念是预防为主,一定要在任何未知的设计 或制造的故障产生之前实施。 ➢ FMEA是一个重复的,周期性永不间断的改进程序
概要
FMEA的历史 20世纪50年代,美国格鲁曼公司开发了FMEA,用于飞
机制造业的发动机故障防范,取得了较好的成果.美 国航空及太空总署(NASA)实施阿波罗登月计划时, 在合同中明确要求实施FMEA.
- 1、下载文档前请自行甄别文档内容的完整性,平台不提供额外的编辑、内容补充、找答案等附加服务。
- 2、"仅部分预览"的文档,不可在线预览部分如存在完整性等问题,可反馈申请退款(可完整预览的文档不适用该条件!)。
- 3、如文档侵犯您的权益,请联系客服反馈,我们会尽快为您处理(人工客服工作时间:9:00-18:30)。
2、生產過程的FMEA (PFMEA---Process FMEA): 、生產過程的 :
針對工序間的首要坏品,可運用 PFMEA 作量化分析,在影響坏品產生的諸因素中,哪 一個系統原因影響最大?是否主要原因。。。。。其它,如 CPk 低、生產過程异常等等都可 以通過采用 PFMEA 直觀地找出主要原因,進行改善達到應有的效應。
人
環境
7.1 FMEA計分標准 FMEA計分標准
FMEA 定義 概念性 說明 原因, 原因, 失效模式, 失效模式, 效應 和 控制方案 風險評估 分數
1 2 3 4 5 6 7 8 9 10
嚴重性( 嚴重性(S): 對應于某潛 在 失效效應的嚴重程度。 對工序或客戶無影響 客戶可能忽略的失效 對性能有微小影響 對性能有較小影響 對性能有影響 工序/產品性能會降 低但安全 工序/產品性能會降低 很嚴重以致不可修 复或無法使用 非常嚴重 (帶有 警報提示的影響) 安全性或可靠性故障 (不帶有警報提示的影響) 發生概率( 發生概率(O): 對應于原 因 与失效模式比例的評估。 极為少 < 1 in 1,500,000 小概率 1 in 150,000 失效較少 1 in 15,000 微量失效 偶然性失效 一般 較多 大量 非常多 几乎全部 1 in 2,000 1 in 500 1 in 100 1 in 50 1 in 10 1 in 5 >1 in 2 測試性( 測試性(D): 在客戶方發生 失效的可能性的等級。 可靠的測試控制 比較可靠的測試控制 良好的測試控制 測試控制
3、設備維護的FMEA (EFMEA---Equipment FMEA): 、設備維護的 :
如新設備的投入運行,我們亦可以預先進行 EFMEA,分析、考慮由于設備可能造成的 產品品質問題及可靠度問題等原因,預防采取措施消除不良因素;現有設備、特定的一种設 備在運行中出現的設備故障等均可采用FMEA進行改善,以确保設備的正常運轉。
* 确定當前的工序控制方法并評估其檢測失效的可能性。
* 确定 RPN 值并根据 RPN 值采取相應的改善措施。
附表2: 附表 : 評估影響的嚴重程度
影響 危害的程度 等級 10 不帶有報警性 當一個潛在的失效模式影響安全生產或不适應所規定的控制要求----提示的影響 很高 的危害性,失效的出現可能不帶有任何報警性的提示 9 帶有報警性提 當一個潛在的失效模式影響安全生產或不适應所規定的控制要求----示的影響 很高 很高 的危害性,失效的出現可能帶有報敬性的提示 對產品生產線是主要的破坏因素,產品可能全部報廢,由于產品失去 了基本的功能需不能使用,客戶很不滿意 高 對產品生產線有較高的破坏性影響,產品需要Sorting,部分有可能報 廢,產品可以使用,但是由于性能降低而客戶不滿意 中等 對產品生產線有較高的破坏性影響,部分有可能報廢但不需要Sorting, 但是有諸多本該方便舒适的操作不能使用,使客戶覺得不方便 低 對產品生產線有破坏性影響,產品有可能全部需要返工,在降低性能 的情況下產品可以使用,但客戶還是感到不滿意 很低 對產品生產線有較低的破坏性影響,產品可能需要Sorting, 部分產品需 要返工,產品的不足被許多客戶所注意 微小 對產品生產線有較微小的破坏性影響,部分產品有可能需要在生產線 返工,產品的不足被一般客戶所注意 很細微 對產品生產線有較微小的破坏性影響,部分產品有可能需要在生產線 返工,產品的不足被很敏銳的客戶所注意 無 1 2 3 4 5 6 7 8
RPN 評价 1 < RPN< 50
51 < RPN <100
101 < RPN <1,000
理解或行動
對產品有較小的危害
對產品有中等的危害,需進一步改善
對產品有嚴重危害,需深入調查分析
5、FMEA 的應用范圍 、 的應用范圍(1)
1、設計階段的FMEA (DFMEA---Design FMEA): 、設計階段的 :
不完全的測試控制
較低水平的控制 低水平的控制 難于控制 很難控制 几乎無法控制
附表1: 個方面的內容, 附表 :在附表 1 中包含以下 6 個方面的內容,因附表 1 容量
太大, 太大,另存在 Excel 中
* 确定所要分析的失效模式。
* 分析失效模式對客戶的所造成的影響 。
* 評估影響的嚴重程度。 * 評估其發生的可能性。
備注:1 in 2 可以理解為 2 個產品中就有 1 個可能出現失效
2、什么是 FMEA (1) 、
FMEA 的中文意思是失效模式和效應分析 ; 失效模式 (Failure Mode): 指制造過程無法達到預定或規定的要 求所表現出的現象; 求所表現出的現象;如:坏品、不良設備狀況等; 坏品、不良設備狀況等 效應 (Effect): 指失效模式在客戶處(包括下工序 所造成的結果; 指失效模式在客戶處 包括下工序)所造成的結果 包括下工序 所造成的結果
否
否
* 收集數据 * 排定原因 * 收集數据 * 致力改善 * 确認效果 * 推廣行動
FMEA Development Process Work Sheet
Page:
of
潛在的原因 法
Design or Process Function
潛在影響 机
料
失敗模式
3、FMEA 的特點 、
分析失效模式;确定失效原因;評估失效效應; 分析失效模式;确定失效原因;評估失效效應; 將“失效的嚴重性、失效發生的可能性、失效檢測的 失效的嚴重性、失效發生的可能性、 可能性”這三方面進行量化; 可能性”這三方面進行量化; 确認改善效果。 确認改善效果。
風險优先指數(RPN) 風險优先指數
2、什么是 FMEA (2) 、
FMEA 是一种用來确認風險的分析方法,它包含: 是一种用來确認風險的分析方法,它包含: 确認潛在的失效模式并評价其產生的效應; 确認潛在的失效模式并評价其產生的效應; 确認失效模式對客戶所產生的影響; 确認失效模式對客戶所產生的影響; 确認潛在的產品/過程失效原因; 确認潛在的產品 過程失效原因; 過程失效原因 确認現有控制產品/過程失效的方法; 确認現有控制產品 過程失效的方法; 過程失效的方法 确定排除或降低失效改善方案; 确定排除或降低失效改善方案; 設計之前預先進行風險分析,确保設計水平。 設計之前預先進行風險分析,确保設計水平。
附表3 附表 :評估其發生的可能性
失效的可能性 很高;失效是不可避免 可能的失效率 >> = 1 in 2 1 in 3 高:通常与工序聯系在一起,類似于 經常出現失效的前工序 中等:通常与工序聯系在一起,類似 于偶爾出現換效的前工序。但不 是主要的部分。 低:与類似的工序聯系在一起的唯一 的缺點 (失效) 很低:与完全相同的工序聯系在一起 的唯一的缺點 (失效) 微小:不可能出現失效 << 1 in 1, 500, 000 > = 1.67 1 1 in 150, 000 > = 1.50 2 1 in 8 1 in 20 1 in 80 1 in 400 1 in 2, 000 1 in 15, 000 CPk < 0.33 > = 0.33 > = 0.51 > = 0.67 > = 0.83 > = 1.00 > =1.17 > =1.33 等級 10 9 8 7 6 5 4 3
6、PFMEA 的程序步驟 、 的程序步驟(2)
繪出流程圖 确定各個工序的功能 RPN =O x S x D 制作 Pareto 圖 選擇失效模式 進行改善 標識其效應 標識其原因 標識當前控制 方法 估計嚴重性 估計發生概率 估計測試性
是
确定失效模式
RPN= 風險指數
完成? 完成? 是
明确如何改善: 明确如何改善: 嚴重性? 嚴重性? 發生概率? 發生概率? 測試性? 測試性?