铋回收工艺的对比分析
从低品位铋渣中回收锌铜铋碲的试验研究

世界有色金属 2019年 6月下4冶金冶炼M etallurgical smelting1 前言采用火法冶炼从铅阳极泥中回收金银时,产出的铋渣是回收铋的重要原料[1]。
传统火法工艺是将铋渣用反射炉或转炉熔炼成粗铋,然后再用火法将粗铋精炼成精铋[2]。
典型的湿法工艺是用盐酸浸出铋渣中铜、铋,水解回收氯氧铋,置换回收海绵铜[3]。
也有采用硫酸和盐酸两段浸出,使铋渣中的铜和铋与其他有价金属分离,再经旋流电解提取浸出液中的铜和铋,从而回收铋渣中的铜和铋[4]。
这些工艺只能处理高品位铋渣,而且不利于其它有价金属的回收利用。
碲是重要的稀散金属,在高新技术产业中具有广泛的用途[5][6]。
工业提取碲的原料主要 有铜阳极泥和铅阳极泥[7]。
在锌、铟等金属冶炼过程中,含碲物料中的碲得不到很好的回收利用,随着不同的冶炼过程进一步贫化而无法回收,导致碲资源的浪费。
含铟次氧化锌粉在湿法冶炼回收锌的过程中,铟进入浸出液,浸出液中的铟一般采用萃取回收,在萃取前一般采用铁粉还原浸出液中的三价铁,得到的渣为低品位铋渣,还含有铜、锌、碲等有价金属,铋的常规冶炼方法无法处理该渣,而且其它有价金属也得不到很好的回收利用。
针对该类低品位铋渣,本文介绍了一种硫酸浸出锌、铜、碲,铁粉置换浸出液中的铜,得到的海绵铜与碲反应生成碲化铜沉淀,沉碲后液送硫酸锌溶液铜盐脱氯工艺的浸铜工序,浸出渣铋品位得到富集销售给铋生产企业采用常规冶炼技术回收铋。
2 试验2.1 试验原料试验所用原料为鑫联环保科技股份有限公司个旧分公司铟回收系统还原工序产生的低品位铋渣,成分见表1。
由表1可知,低品位铋渣中主要含有锌、铋、铜、碲、铅等有价金属,具有综合回收利用价值。
铋渣中的有价金属主要以金属单质形式存在,少量以氧化物的形式存在。
表1 低品位铋渣成分分析表(单位:wt%)2.2 工艺流程及试验方法针对低品位铋渣含锌、铜高,并含有少量碲,含铋低的特点,决定采用硫酸浸出低品位铋渣中的锌、铜、碲,浸出液进行碲沉淀富集,沉碲后液送本公司铜浸出工序,锌、铜随着浸铜液回硫酸锌溶液铜盐脱氯工序,锌、铜得到综合回收利用,浸出渣中的铋得到富集。
从阳极泥中回收铋新工艺生产实践

中 图分 类号 : TD 9 8 2
文 献标 识码 : A
文章 编号 : 1 1 — 5 0 0 4 ( 2 0 1 7) 0 3 — 0 0 4 2 - 2
铋 是 一 种 比较 稀 少 的 元 素 ,在 地 壳 中 含 量和 银 相 当 , 为 1 0 6 % ~1 0- v %。 我 国铋 矿 资源 丰富 ,主 要 分 布 在 湖 南 、广 东 、江 西 等 省 , 大都与钨 、钼 、铅矿床共生 。解放前 ,我 国并 无铋生产 工艺 ; 解 放 后 ,不 少 大 型 有 色 冶炼 企业 陆续 进行 了铋 的 回收 和 生产 , 铋工业 不断发展 。1 9 5 2年 。我国开始 从铅阳极泥 中回收铋 。 接着 。又扩 大处 理铋精 矿 ,采用 “ 还原熔 炼一 电解精 炼一 火 法精 炼”工艺流 程 ,产 出了二号精铋 ;1 9 5 8年起 ,也用铋 精 矿生 产精 铋 。至 此 ,我 国金属铋 的生 产具备 了一 定的规 模。 1 9 6 5年 ,改 进 了铋 的传统生 产工艺 ,用 “ 混合熔 炼一直接 火 法精 炼 ”代 替 了原有 的工艺 流程 ,产 出了达 到国 际先进水 平 的一 号精铋 ;1 9 7 2年起 ,用从钨矿 分离 出铋精 矿炼铋 ;也用 从 钨 钼 矿 分 离 出 的 铋 精 矿 炼 铋 。 目前 ,我 国铋 金 属 的 年 产 量 1 万 吨 左 右 ,约 占 世 界 总 产 量 的 1 5 %- 2 0 % ,从 阳 极 泥 中 回 收 铋 的产 量 占 到 4 0 %~ 5 0 %。
监
零
I
畦噩
幽
—
遮量 蕉 遗
回 收 银
、
r 工艺
铋 的 冶 炼 必 须 经 历 粗 炼 和 精 炼 两 个 阶 段 。粗 炼 是 将 含 铋 物 料通 过火 法或湿 法的初 步预处 理 ,产 出中 间产物粗 铋 ;粗 铋 进一 步精 炼 ,产 出精铋 。常见 的工艺 有两种 ,一种 是先湿 法 后 火 法 冶 炼 工 艺 ,另 一 种 是 火 法 冶 炼 工 艺 。 1 . 1 先 湿 法后 火 法 冶 炼 工 艺
粗铋综合回收的技术条件与操作

粗铋综合回收的技术条件与操作一、粗铋精炼1、熔析除杂初析400℃高析650~750℃总时间4~8小时将粗铋装入熔析锅中,在400℃捞出铋液表面的不熔物,然后升温到650~750℃,用铁制物将新鲜的湿木块压入铋液中氧化除部份As、Sb,当铋液表面无白烟并显火星时,开始出现一层血红色的油状物时此操作结束,注意操作时铋液喷浅烧伤。
2、加硫除铜加硫磺温度:280~330℃析渣温度450~350℃加硫量:Cu:S=1~0.8:1 搅拌时间2~4小时捞渣温度:280~330℃其操作方法参照粗铅加硫除铜。
3、氧化精炼鼓风温度:680~720℃鼓风时间:4~10小时脱铜后铋液升温到680~720℃,鼓入压缩空气,当铋液表面冒出白烟稀少时即为终点,捞出浮渣此阶段结束。
4、碱性精炼除Te、Sn、Se加碱温度:500~520℃加碱量铋液量的1~3% 搅拌时间6~10小时捞碲渣温度:400~450℃脱Sn加碱量Sn:NaOH=1:2脱S搅拌时间:0.5~1小时捞Sn渣温度500~520℃覆盖剂:Sn:NaOH:NaCl:NaNO3=1:2:0.6:0.5将氧化精炼后的铋液降温到500~520℃,加入约料量的1~2%的NaOH(分数次加入),熔化后,鼓入压缩空气搅拌,如此操作数次,当再加入NaOH并搅拌时浮渣不再变干,碲含量已降到0.05%±,除碲作业结束,降温捞出碲渣。
脱Sn、S作业,将除碲后的铋液调温到450℃,将NaOH、NaCl和NaNO3分次加入熔化,覆盖在铋液表面,升温500~520℃,鼓风氧化15~20分钟,再加入NaOH,继续鼓风30分钟,捞出浮渣即告结束。
说明:当粗铋中S、Sn含量不高时氧化精炼和除碲精炼合并到一道作业完成。
5、加氯除Pb通氯温度:含Pb 20%时450~500℃, 捞铅渣温度450℃,含Pb<10%时350~400℃,通氯时间12~24小时,捞铅渣温度400℃。
脱氯温度:680~720℃脱氯时间1~1.5小时氯气压力:0.31KPa~0.5 KPa将除碲铋液调温到450~500℃,用小钢管或玻璃管通入氯气,插入300~400㎜深,在含Pb>10%时氯化5~6小时停氯气捞渣,然后温度在450℃,继续通氯气,通氯气直到观察产浮量极少时,降温到400℃捞渣,尔后,升温到680~720℃,直到取试样表面不冒金属小粒,断面贯通致密,呈垂直条纹状结晶并具有金属光泽,无灰色斑点即到终点,降温到450~500℃时捞渣,此时铋液Pb<0.001%,根据Pb-Sb厂提供化验结果,即Pb很低,此道工序可以取消。
盐浸——置换法从硫酸铅渣回收铋

盐浸一置换法从硫酸铅渣回收铋
Extract Bismuth from Lead Sulfate Residue With Salt—dip Displacement Method
口文/王树楷李祖云薛兆丽
铋是一种“绿色”稀有金属,在 地壳中的丰度和银相当。铋一般作为 钨、铅、铝、铜、锡冶炼过程中的副产 品回收,如铅阳极泥、锡阳极泥、铅钙: 镁渣、锡钨镁渣、铜转炉烟尘等,其含 铋量波动在1%~5%之间,常采用先富 集再火法冶炼的工艺予以处理。
杂质成分, %≤
I=e
Zn
0.0023 O.001
0 0011 0.0005
O.001
0.005
Ag O 01 O.004 0 02
Sb
CI
0.O001 O.0014
0.0005 O.0015
As 4-S 0 0003
0.01
0.0001 0.005
0.05
发回收;中和后液返回转窑作窑 渣水淬的补充水,做到工艺体系 水闭路循环。
单耗
单价元
4.0
720
O.8 2.O
4000 3000
单位成本元/t 2880 3200 6000 800 1600 820 15300
备注 8人
项目
产品粗铋 一号铋 二号铋
Bi ≥
97.5 99.99 99 95
表4产品粗铋与国标精铋的成分比较
Cu O 08 O 001 0.003
Pb 2.4 O 001 0.01
表2湿法提铋工序典型产物化学成分表
Bi
Pb
Sn
Zn
In
97.4
2.4
O.03 0.001
Cu
铋渣冶炼回收铋的新工艺研究
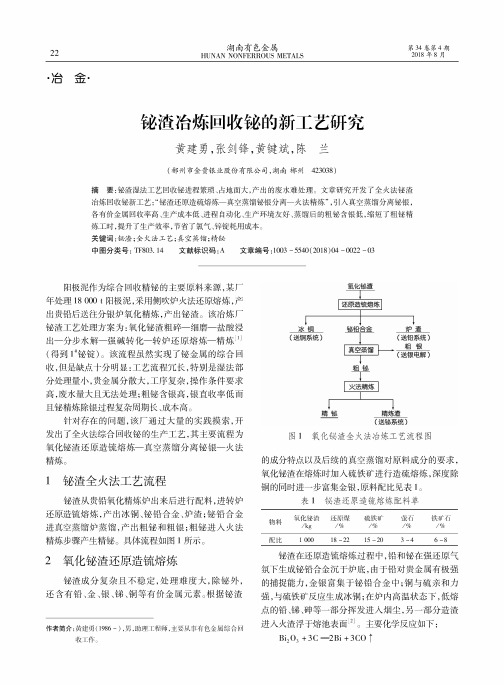
22湖南有色金属HUNAN NONFERROUS METALS第34卷第4期2018年8月冶金铋渣冶炼回收铋的新工艺研究黄建勇,张剑锋,黄键斌,陈兰(郴州市金贵银业股份有限公司,湖南郴州423038)摘要:铋渣湿法工艺回收铋进程繁琐、占地面大,产出的废水难处理。
文章研究开发了全火法铋渣冶炼回收铋新工艺:铋渣还原造硫熔炼一真空蒸馏铋银分离一火法精炼”,引入真空蒸馏分离铋银,各有价金属回收率高、生产成本低、进程自动化、生产环境友好、蒸馏后的粗铋含银低,缩短了粗铋精炼工时,提升了生产效率,节省了氯气、锌锭耗用成本。
关键词:铋淹;全火法工艺;真空蒸馏;精铋中图分类号:TF803. 14 文献标识码:A文章编号:1003 -5540(2018)04 -0022 -03阳极泥作为综合回收精铋的主要原料来源,某厂年处理4 000 t阳极泥,采用侧吹炉火法还原熔炼,产出贵铅后送往分银炉氧化精炼,产出铋渣。
该冶炼厂铋渣工艺处理方案为:氧化铋渣粗碎一细磨一盐酸浸出一分步水解一强碱转化一转炉还原熔炼一精炼[1](得到4铋锭)。
该流程虽然实现了铋金属的综合回收,但是缺点十分明显:工艺流程冗长,特别是湿法部分处理量小,贵金属分散大,工序复杂,操作条件要求高,废水量大且无法处理;粗铋含银高,银直收率低而且铋精炼除银过程复杂周期长、成本高。
针对存在的问题,该厂通过大量的实践摸索,开发出了全火法综合回收铋的生产工艺,其主要流程为 氧化铋渣还原造锍熔炼一真空蒸馏分离铋银一火法 精炼。
1铋渣全火法工艺流程铋渣从贵铅氧化精炼炉出来后进行配料,进转炉 还原造锍熔炼,产出冰铜、铋铅合金、炉渣;铋铅合金 进真空蒸馏炉蒸馏,产出粗铋和粗银;粗铋进入火法 精炼步骤产生精铋。
具体流程如图1所示。
2氧化铋渣还原造锍熔炼铋渣成分复杂且不稳定,处理难度大,除铋外,还含有铅、金、银、锑、铜等有价金属元素。
根据铋渣作者简介:黄建勇(186 -)男,助理工程师,主要从事有色金属综合回收工作。
金属铋的回收率

金属铋的回收率取决于回收过程中的多个因素,包括回收方法、处理过程和设备、原料质量等。
以下是一些常见的金属铋回收方法及其预期回收率范围:
熔铸回收:将废铋制品或含铋废料进行高温熔融,使铋分离出来。
预期回收率通常在70%至90%之间,具体取决于废料的纯度和熔铸条件的控制。
水冶回收:利用水冶法将含铋废料溶解,并通过杂质的沉淀和过滤来分离出纯铋。
回收率预期在80%至95%之间,取决于废料的纯度和处理过程的优化。
电解回收:通过电解池将含铋废料溶解在适当的电解液中,利用电流将铋沉积在阴极上。
电解回收的预期回收率通常在80%至95%之间,具体取决于电解液和电流密度的选择。
化学回收:利用化学方法将含铋废料进行溶解,然后通过还原、沉淀、结晶等步骤将铋分离出来。
回收率预期在70%至90%之间,具体取决于化学反应条件和纯化步骤的控制。
需要注意的是,以上回收率范围仅为一般参考值,实际的回收率可能受到多种因素的影响。
另外,回收过程中的环保问题也需要重视,确保回收过程符合环保标准和相关法规要求。
因此,在进行金属铋回收时,应根据具体情况选择适当的回收方法,并通过优化和改进来提高回收率。
国外从铜熔炼烟尘中回收铋

书山有路勤为径,学海无涯苦作舟
国外从铜熔炼烟尘中回收铋
处理含铋的铜精矿时,在炼铜过程中铋主要进入熔炼烟尘,成为提铋原
料。
(一)日本宫古冶炼厂从铜转炉烟尘中回收铋,烟尘成分为(%):Bi 2~6,Pb 30~40,Cu 1~4,Zn 7~14,Cd 0.7~1.3。
其工艺流程如图1。
图1 宫古厂回收铋工艺流程图
此流程的特点是对还原熔炼产出的Pb-Bi 合金施行两次电解,第一次铅电
解产出电铅,第二次铋电解产出电铋,从而分离并提纯铅、铋。
(二)日本国富冶炼厂处理澳大利亚佩科矿含铋0.4%~1%之铜精矿,产出
之转炉烟尘成分为(%);Bi 10,Pb 27,Zn 12,Cu 0.2,S 12,用文丘里洗涤器洗涤过滤,滤饼用硫酸加食盐浸出,与洗水一道用铁屑置换,产出含铋40%~65%的海绵铋,与铜鼓风炉静电沉积尘一道制粒,在反射炉内与焦粉、
纯碱、石英粉一道还原熔炼,产出之粗铋含铋90%以上,含Pb 低于5%,装入精炼锅进行火法精炼,其工艺流程如图2。
图2 国富厂回收铋工艺流程图
此流程包括浸出、置换、还原熔炼、火法精炼等工序,合理地利用了铜转炉
与鼓风炉烟尘、湿法与火法相结合,流程紧凑,程序安排合理,值得推广借
鉴。
(三)加拿大默多维尔冶炼厂处理含铋0.03%的钢精矿,熔炼电收尘之烟尘
含铋15%左右,还原熔炼产出之粗铋含铋80%以上,采用火法精炼,其工艺流程如图3。
粗铋回收锡

书山有路勤为径,学海无涯苦作舟
粗铋回收锡
对于含锡1.5%左右的粗铋,可采用碱性精炼生产锡酸钠。
粗铋熔化后,首先氧化脱砷,脱砷后粗铋降温至420℃左右,加入NaOH,待NaOH 熔化后,搅拌中缓慢加入NaNO3,待碱渣变干后捞出,再加NaOH 与NaNO3,反复数次,待铋样表面出现叶状花纹为终点。
固体碱与硝酸钠加入量为:Sn∶NaOH∶NaNO3=1∶3∶0.5。
生产锡酸钠的粗铋及渣料成分列于下表。
包括浸出、净化、浓缩结晶,干燥等工序。
图1 生产锡酸钠工艺流程图
二、主要技术条件
(一)水淬。
水淬的目的是分离碱液中的铋珠,并使碱渣细碎。
在90℃搅拌浸出水淬渣,直至溶液清亮。
加热水淬可带走一半的砷,但也造成部分锡的损失;也可采用常温水淬。
终点控制在水淬滤液密度1.35~1.4 克/厘米3 之间。
(二)浸出。
浸出的目的是使锡酸钠溶于水溶液中以利于净化。
浸出液固比(3~4)∶1;浸出时间4~6 小时,由于锡酸钠在水中的溶解度随温度上升而下降,而锑酸钠在水中的溶解度随温度上升而增高,所以宜采用常温浸出,浸出率可在85%~90%之间。
(三)净化。
浸出液含Sn40~50 克/升,Pb1~1.5 克/升,Sb0.1 克/升左右,应除去其中的铅与锑:
除铅:加Na2S 除铅,温度90~95℃,配成10%的Na2S 溶液,搅拌中加入,至无黑色沉淀产生即终点,Na2S 加入需过量。
- 1、下载文档前请自行甄别文档内容的完整性,平台不提供额外的编辑、内容补充、找答案等附加服务。
- 2、"仅部分预览"的文档,不可在线预览部分如存在完整性等问题,可反馈申请退款(可完整预览的文档不适用该条件!)。
- 3、如文档侵犯您的权益,请联系客服反馈,我们会尽快为您处理(人工客服工作时间:9:00-18:30)。
附件7 铋回收工艺的对比分析
一.铋回收冶炼方法简介
从铜铅阳极泥回收金银过程的附产品氧化铋渣中,回收生产金属铋,是多数冶炼企业综合生产的内容之一。
以氧化铋渣为原料,回收生产精铋的工艺,有纯火法流程,也有湿法、火法混合流程。
纯火法工艺主要分为两段:一段是用铋原料还原熔炼粗铋,二段是粗铋的精炼,得到产品精铋。
这主要分为①反射炉还原熔炼+火法精炼工艺;②转炉还原熔炼+火法精炼工艺;湿法与火法混合流程又可分为几种:③氧化铋渣湿法浸出+火法还原+火法精炼工艺;④火法还原熔炼+湿法电解精炼工艺等。
以上几种工艺的简要描述如下:
①反射炉还原熔炼+火法精炼工艺:就是以反射炉作为还原熔炼的主要冶金设备,配以还原剂、熔剂、造锍剂等辅料,通过供热、反应,生成粗铋、冰铜、炉渣、烟尘等产出物。
粗铋采用精炼锅分步骤除去砷锑、铅、银、铜等杂质,最后得产品精铋。
反射炉熔炼比较原始,进料、出炉等过程全靠人员手工操作、扒渣,但因处理量大,煤燃料易得,仍有很多厂家使用。
②转炉还原熔炼+火法精炼工艺:就是以转炉作为还原熔炼的主体设备,其它的原理、辅材配料比等,以及精炼的所有过程,与①工艺完全相同。
转炉熔炼的优势是:使用油或气作供热源,进料放渣出炉可实现半机械化,减轻了手工操作劳动量,可减少用人成本。
我公司自上世纪八十年代初就采用了此工艺。
③氧化铋渣湿法浸出+火法还原+火法精炼工艺:氧化铋渣经破碎、湿式球磨成细沙状,在65℃左右用盐酸浸出,使铜、锑、铋进入溶液,固液分离后,浸出渣(主要为含铅、银)返回阳极泥熔炼。
浸出液第一步先水解(Ph2.0--2.5)分离氯氧化铋,第二步再调Ph值(4.5左右)沉淀氯氧锑,第三步再调Ph在7左右沉淀铜。
在反射炉用木炭对氯氧化铋进行还原,即得到含铋95%以上的粗铋。
粗铋再用与上述相同的火法精炼,得到产品。
氯氧锑粉直接送锑冶炼,铜渣用于回收铜。
④火法还原熔炼+湿法电解精炼工艺:前部分的火法熔炼与上述①或②的相同,不同的是精炼。
它是把粗铋铸成阳极板,以硅氟酸作电解液,以精铋片作阴极,在直流电作用下,得到电解析出铋,再精炼熔铸成精铋产品。
此工艺现使用的厂家很少,目前所知,只有郴州金旺铋业公司采用了。
其特点是精炼部分占用
大量的粗铋量,投入产出慢,资金占用巨大。
我们也认为该工艺没有突出优势,
不列入工艺对比范围来考察。
二.工艺对比分析
1.各自工艺的优缺点
铋回收工艺的优劣性比对表1
参数 \ 工艺①反射炉熔炼工
艺
②转炉熔炼工艺③湿法浸出工艺主要设备型号炉床面积13m2φ2650mm
L4450mm
浸出罐30M3*5等
处理能力8--12t/炉.24小时6--8t/炉.16小时3--5t/槽.16小时精铋产量(t/a) 380--450 300--420 450--500
工序过程繁简性相对简单简单繁复
操作便利性进\出炉\扒渣靠人工进\出炉自流,操作便
利
液固分离,操作便利设备维护维修停炉中小修停炉中小修日常不停产修理主要设备问题砖墙炉底易渗漏钢筒体渗漏较少设备易腐蚀跑液设备寿命120炉±100炉±1--1.5年
环保性炉体密闭,环保性好通过科学的设计收
尘系统可实现清洁
无污染的生产无粉尘污染,但含砷废水难以处理
2.效益分析对比
鉴于株冶转型方案中铅系统的设计产能只有10--12万吨,所以铅阳极泥年
产量也就在4500t左右,氧化铋渣物料处理量为1300吨左右,所以,铋回收系统以选择建设一套铋氧化渣处理能力为1300t/a(年产精铋300吨)的铋生产设施为条件,来作投资与效益成本分析如下:
铋回收工艺的投资、效益比对表2
参数 \ 工艺①反射炉熔炼工
艺
②转炉熔炼工艺③湿法浸出工艺主要设备型号炉床面积13m2φ2650mm
L4450mm
浸出罐30M3*5等
投资:主要设备/投资
额反射炉+精炼锅+收
尘器3000万
转炉+精炼锅+收尘
器2800万
湿法系统+还原炉+
精炼锅+收尘器
/3500万
加工成本:辅材动力 1.1元/kg 1.1元/kg 1.2元/kg
能耗燃煤5-6t/tBi或燃气
1000m3/tBi;1.5元/kg 燃油4--4.5t/tBi+精
炼时燃气700m3/tBi;
1.2元/kg
蒸汽4--6t/tBi+燃气
1000m3/tBi;1.6元/kg
用工人数/用工成本20-24人/人工成本
高;4元/kg 16-20人/人工成本
低;3.7元/kg
22-26人/成本高;5
元/kg
维修费用按照投资额的3%计
算,90万元/年,折
算成成本为3元/kg 按照投资额的3%计
算,84万元/年,折
算成成本为 2.8元
/kg
按照投资额的3%计
算,105万元/年,折
算成成本为 3.5元
/kg
设备折旧费用(13
年)
7.7元/kg 7.2元/kg 9元/kg
总加工费17.3元/kg 16元/kg 20.3元/kg
铋的直/回收率%60-65/80-85 64--68/85--88 78-85/90--95 粗炼银回收率/碲直收
率%
94--96/60--65 94--96/60-65 95--98/10--20
精炼银回收率/碲直收
率%
85--90/30--35 85--90/30--35 88-92/20--30
综合评价作为传统工艺之一,
工艺成熟稳定;但是
加工费较高,自动化
程度较低。
作为传统工艺之一,
工艺成熟稳定;加工
费较低,自动化程度
比反射炉更高。
直收率和回收率比
火法冶炼要高;但是
所需的化学药剂成
本以及人工成本比
火法高;工艺波动性
比较大,水口山冶炼
厂以前使用湿法工
艺,后因工艺不稳定
的原因而改用火法
工艺;最大的缺陷是
含砷废水难以处理,
成为目前尚无法破
解的难题。
三.工艺选型建议
1.建议采用转炉熔炼→火法精炼的工艺,理由如下:
(1)与反射炉相比,加工费更低,自动化程度更高,指标更好,回收率、直收率均更高。
反射炉加工费为17.3元/kg,转炉只有16元/kg,每年可节约成本39万元;反射炉需要开口放渣、出炉,转炉只需要转动炉体即可实现;反射炉渣含铋为0.2%,铋冰铜含铋5%,转炉渣含铋为0.15%,铋冰铜含铋4%,均优于反射炉;反射炉直收率为60%-65%,转炉直收率为64%-68%;反射炉回收率为80-85%,转炉回收率为85-88%。
所以转炉明显优于反射炉。
(2)与湿法工艺相比,加工费更低,工艺更加稳定可靠。
湿法工艺加工费为20.3元/kg,比转炉多4.3元/kg,成本每年增加129万元。
湿法工艺波动大,工艺不稳定,并且存在含砷废水难以处理的难题。
2.对该工艺的描述如下所示。
从氧化铋渣中回收生产精铋,工艺分为两段。
一段是用铋原料还原熔炼粗铋,二段是粗铋的精炼,得到产品精铋。
其工艺流程如下图1所示:
氧化渣、成品渣、熔剂
配料。
图1 铋生产工艺流程
稀贵冶炼厂 2015-4-22。