钴镍废料的回收利用
镍废料的电化学回收与电解法处理

镍废料的电化学回收与电解法处理镍是一种重要的金属资源,广泛应用于不同行业中。
然而,在镍加工和使用过程中,产生了大量的镍废料。
由于镍废料的高污染性和含有宝贵的金属资源,对其进行有效的回收和处理是非常重要和必要的。
电化学回收和电解法处理被广泛应用于镍废料的处理过程中。
电化学回收是指利用电化学技术将废料中的镍离子还原为纯金属镍的过程。
这种方法可以有效地回收镍资源,并且对环境影响较小。
电化学回收的关键是选择适当的电解质和电极材料。
一般来说,镍废料可以通过阳极氧化和阳极溶解两个步骤进行电化学回收。
在阳极氧化步骤中,镍废料中的镍被氧化为镍离子。
此时,选择合适的电解质对于确保高效的氧化过程至关重要。
常用的电解质包括硫酸镍、氯化镍等。
此外,控制电流密度和氧化时间也对阳极氧化的效果有重要影响。
适当的电流密度和氧化时间可以提高氧化效率,减少能量消耗。
在阳极溶解步骤中,氧化后的镍离子被还原为纯金属镍。
此过程需要适当的电解质和电极材料。
一般来说,采用钢网或钢板作为阴极,以及铜板或钼板作为阳极。
镍离子在阴极上还原为纯金属镍,并沉积在阴极上。
控制电流密度和电解时间是确保还原效率的关键因素。
适当的电流密度和电解时间可以提高还原效率,减少金属镍的损失。
电解法处理是通过将镍废料溶解在合适的溶剂中,然后经过电解反应将镍离子还原为金属镍。
与电化学回收不同的是,电解法处理更加注重对镍废料中其他杂质的处理。
常用的溶剂有硫酸镍溶液、氯化镍溶液等。
在电解过程中,使用合适的电解装置,如电解槽和电解池,以确保有效的反应和金属镍的纯度。
在电解法处理过程中,还需要注意控制电流密度、溶液温度和pH值等因素。
适当的电流密度可以提高反应速率和还原效率,而适当的溶液温度和pH值可以影响溶液中其他杂质的去除效果。
此外,还可以采用吸附、离子交换和过滤等方法来进一步提高杂质的去除效果。
总结而言,镍废料的电化学回收和电解法处理是两种有效的方法,可以回收宝贵的镍资源并降低环境污染。
镍钴矿的选矿废渣资源化利用

添加 标题
回收利用:将处理后的废渣进行回 收利用,如制作建筑材料、肥料等
Part Four
镍钴矿选矿废渣资 源化利用的应用实
例
实际应用案例
某镍钴矿选矿废渣资源化利用项 目,通过回收废渣中的镍、钴等 金属元素,实现资源再利用。
某公司采用先进的选矿技术,将 镍钴矿选矿废渣中的金属元素提 取出来,用于生产电池材料。
粒度细小:颗粒直径一般在0.110mm之间
02
含水量高:废渣含水量一般在10%30%之间
04
资源化利用价值:废渣中含有可回 收的金属和非金属元素,具有较高
的资源化利用价值。
06
废渣的危害
环境污染:废渣中含有重 金属等有害物质,容易造 成土壤、水源和空气污染
安全隐患:废渣中含有易 燃易爆物质,如果不妥善 处理,可能引发安全事故
经济效益的提升
镍钴矿选矿废渣资源化利用可以降低生产成本,提高经济效益。 废渣资源化利用可以减少废渣处理费用,降低环境污染。 废渣资源化利用可以创造新的经济增长点,带动相关产业发展。 废渣资源化利用可以提高资源利用率,实现可持续发展。
Part Three
镍钴矿选矿废渣资 源化利用的方法与
技术
废渣的预处理
经济效益与社会效益
经济效益:镍钴 矿选矿废渣资源 化利用可以降低 生产成本,提高
经济效益。
添加标题
社会效益:镍钴 矿选矿废渣资源 化利用可以减少 环境污染,保护 生态环境,提高
社会效益。
添加标题
应用实例:某公 司通过镍钴矿选 矿废渣资源化利 用,每年节省生 产成本数百万元, 同时减少了废渣 对环境的污染。
利用的合法性和可持续性
THANKS
汇报人:
镍渣的处理及资源回收再利用工艺

镍渣是一种具有较高含量的金属废料,其中含有大量的有价金属镍、铜等,具有很高的回收再利用价值。
处理镍渣及资源回收再利用,不仅有助于减少环境污染,降低资源浪费,还可以为企业带来经济效益。
以下是一种可能的处理及资源回收再利用工艺的介绍。
首先,我们来了解一下镍渣的处理方法。
镍渣的处理主要分为两个步骤,首先是分离去除杂质,其次是回收有价金属镍、铜等。
常用的方法包括物理法、化学法及生物法等。
物理法主要是利用镍渣与杂质在物理性质上的差异进行分离。
例如,可以利用镍渣比重较重的特点,通过重力沉降、过滤等方法进行分离。
化学法则是通过添加化学试剂,使杂质与镍渣中的有价金属发生化学反应,生成易于分离的化合物,从而实现分离。
生物法则是利用微生物的分解作用,将镍渣中的有机物分解为无机物,从而去除杂质。
在镍渣处理完成后,接下来就是有价金属的回收再利用。
回收过程主要包括浸出、沉淀、净化及电解等步骤。
浸出是将回收剂加入到处理后的镍渣中,使有价金属进入溶液;沉淀是将回收剂与镍、铜等金属生成可分离的化合物;净化主要是去除溶液中的杂质;电解则是将分离后的金属收集到阴极上提取出金属镍、铜等。
在整个过程中,需要综合考虑回收率、成本、环保等因素。
为了提高回收率,可以采用多种方法结合的方式进行处理,如物理法与化学法的结合、生物法与化学法的结合等。
同时,为了降低成本并提高经济效益,可以采用先进的工艺技术和设备,如自动化设备、高效分离设备等。
此外,还需要考虑环保问题,如废水、废气、废渣的处理和排放等,确保在实现资源回收再利用的同时,符合环保法规的要求。
总的来说,镍渣的处理及资源回收再利用工艺是一项综合性的工作,需要从多个方面进行考虑和实施。
只有全面考虑各种因素,才能实现资源的有效利用和环境的可持续发展。
这不仅有助于减少资源浪费和环境污染,还有利于企业的可持续发展和经济效益的提升。
镍废料的环保科技创新与发展
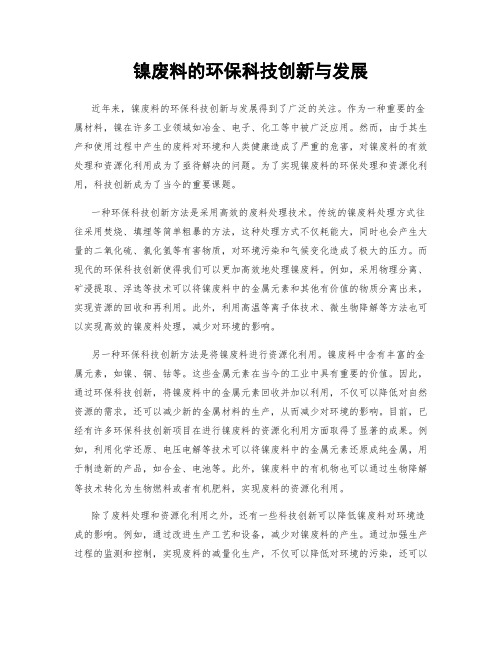
镍废料的环保科技创新与发展近年来,镍废料的环保科技创新与发展得到了广泛的关注。
作为一种重要的金属材料,镍在许多工业领域如冶金、电子、化工等中被广泛应用。
然而,由于其生产和使用过程中产生的废料对环境和人类健康造成了严重的危害,对镍废料的有效处理和资源化利用成为了亟待解决的问题。
为了实现镍废料的环保处理和资源化利用,科技创新成为了当今的重要课题。
一种环保科技创新方法是采用高效的废料处理技术。
传统的镍废料处理方式往往采用焚烧、填埋等简单粗暴的方法,这种处理方式不仅耗能大,同时也会产生大量的二氧化硫、氯化氢等有害物质,对环境污染和气候变化造成了极大的压力。
而现代的环保科技创新使得我们可以更加高效地处理镍废料。
例如,采用物理分离、矿浸提取、浮选等技术可以将镍废料中的金属元素和其他有价值的物质分离出来,实现资源的回收和再利用。
此外,利用高温等离子体技术、微生物降解等方法也可以实现高效的镍废料处理,减少对环境的影响。
另一种环保科技创新方法是将镍废料进行资源化利用。
镍废料中含有丰富的金属元素,如镍、铜、钴等。
这些金属元素在当今的工业中具有重要的价值。
因此,通过环保科技创新,将镍废料中的金属元素回收并加以利用,不仅可以降低对自然资源的需求,还可以减少新的金属材料的生产,从而减少对环境的影响。
目前,已经有许多环保科技创新项目在进行镍废料的资源化利用方面取得了显著的成果。
例如,利用化学还原、电压电解等技术可以将镍废料中的金属元素还原成纯金属,用于制造新的产品,如合金、电池等。
此外,镍废料中的有机物也可以通过生物降解等技术转化为生物燃料或者有机肥料,实现废料的资源化利用。
除了废料处理和资源化利用之外,还有一些科技创新可以降低镍废料对环境造成的影响。
例如,通过改进生产工艺和设备,减少对镍废料的产生。
通过加强生产过程的监测和控制,实现废料的减量化生产,不仅可以降低对环境的污染,还可以提高资源利用率。
此外,开展环境友好型镍废料利用技术研究,如矿浸提取、浮选、生物法等,能够降低镍废料的处理成本,同时减少对环境的损害。
镍废料的经济评价与市场前景展望

镍废料的经济评价与市场前景展望随着全球经济的发展和工业化的推进,金属废料的回收利用变得越来越重要。
镍废料作为一种重要的金属废料,在电子、钢铁、化工等行业中具有广泛的应用。
本文将对镍废料的经济评价和市场前景进行展望,为相关行业的决策者提供参考。
首先,镍废料的经济评价是了解其市场前景的第一步。
镍废料主要来自于电子产品、废旧汽车等废弃物的处理,因此其产量相对较大。
与之相对应的是,镍废料的回收利用能够大幅度减少对镍矿石的需求,降低资源浪费和环境污染。
此外,镍废料中镍的含量较高,回收利用后的镍产品可以直接用于新材料的制备,减少生产成本,提高产能。
因此,从经济角度来看,镍废料的回收利用是具有较大价值和潜力的。
其次,镍废料的市场前景展望。
镍作为一种重要的合金元素,广泛应用于不锈钢、合金钢、电池等领域。
随着不锈钢行业的发展,对镍的需求量与日俱增。
而镍废料的回收利用可以满足这一需求,提供稳定的原材料来源。
此外,随着电动汽车等新兴产业的崛起,对镍的需求也将大幅增加。
镍废料的回收利用能够缓解镍资源供应的压力,为新兴产业的发展提供支持。
因此,从市场前景来看,镍废料的回收利用具有广阔的发展空间。
另外,镍废料的回收利用还可以带来环境效益。
镍矿石的开采和加工过程会产生大量的废水、废气和固体废物,对环境造成严重污染。
而镍废料的回收利用可以减少镍矿石的开采量,降低环境负担。
此外,镍废料中可能含有其他有价值的金属,如铜、钴等,其回收利用也能够提高资源利用效率,减少资源浪费。
因此,从环境角度来看,镍废料的回收利用是一种可持续发展的解决方案。
然而,镍废料的回收利用还存在一些挑战和问题。
首先,镍废料的收集和分类需要大量的人力和物力投入,如收集设备、分类设备等。
这对于发展中国家来说可能面临较大的困难。
其次,镍废料的回收利用涉及到相关技术和工艺的问题,如高温炉处理、化学还原等。
这些技术和工艺的改进与提升也需要进一步的研究和投入。
最后,镍废料的市场需求和价格波动也会对回收利用行业的盈利能力产生影响。
钴镍废料的回收利用

用沉淀法从废加氢脱硫催化剂的EDTA浸出液中别离并回收镍盐1 前言钴镍金属具有储能、防腐、耐磨、耐高温和高强度等优异性能,是不锈钢、充电电池、电镀、汽车配件、军工器件的关键原材料,因此被列为国民经济开展的重要战略物资[1]。
以目前的消耗速度,原生钴、镍资源可供开采年限不到67年[2],如何对现有钴、镍资源进展有效的二次利用就显得非常必要。
目前,按照行业可将钴镍废料分为六大类:废硬质合金、废高温合金、电池废料、废催化剂、废磁性材料和冶金中间渣,这其中尤以废催化剂和废旧电池的钴镍含量最高,其含量水平甚至远高于原生矿的品位。
因此,最大限度地开展钴镍资源的二次回收综合利用,将成为缓解各国钴镍资源短缺的一个重要途径。
目前工业上应用的含钴镍催化剂[3]包括加氢脱硫〔HDS〕催化剂、加氢脱氮〔HDN〕催化剂、加氢脱金属(HDM〕催化剂、FDS-4A 型加氢精制催化剂、苯乙酸催化剂、加氢裂化催化剂等。
从废催化剂中回收钴镍普遍使用“浸取法〞,主要是利用废催化剂中钴镍金属在不同浸取剂中的溶解性或与浸取剂反响的能力不同而进展选择性的别离回收[4]。
酸、碱浸取法,即首先将废催化剂进展焙烧处理以去除其中的油分,随后利用无机酸〔HCl,H2SO4,HNO3等〕或水溶性有机酸、氨水与废催化剂中的目的金属钴镍在一定反响温度、压力条件下发生化学反响,生成可溶的钴镍金属化合物〔CoCl2,NiCl2,CoSO4,NiSO4等〕。
经除杂后,浸出液通过采用结晶、离子交换[5]、溶剂萃取[6]、磁别离、膜别离等技术加以别离提纯,最后再通过沉淀-焙烧方法制备钴镍的氧化物产品。
以HDS为例,它指的是一类在炼油等过程中,通过加氢转化脱硫,使原料中的有机硫化物发生氢解,转化为易于脱除的H2S。
HDS催化剂的活性组分一般是过渡金属如Mo、Cu、Ni、Pt和Pd等化合物,最常用的搭配为Co-Mo、Ni-Mo、Ni-W,并通常以Al2O3为载体。
通常在浸出此种催化剂采用浓硫酸,同样地,也可采用采用诸如EDTA的有机酸来做浸出剂,此种条件下,一些Al和少量的Mo会溶解,而EDTA通常在强酸性条件下会沉淀,从而回收剩下的金属。
镍渣的处理及资源回收再利用工艺

镍渣的处理及资源回收再利用工艺镍渣是一种常见的废弃物,产生于镍冶炼过程中。
为了减少环境污染和资源浪费,需要对镍渣进行处理和资源回收再利用。
本文将介绍一种常用的镍渣处理工艺,以及相应的资源回收再利用方法。
镍渣处理的第一步是固液分离。
镍渣中含有大量的水分和杂质,需要通过固液分离将其分离出来。
常用的方法有离心分离和过滤分离。
离心分离是利用离心力将镍渣和水分分离,过滤分离则是通过过滤器将水分过滤出去。
这两种方法都能有效地将水分和杂质从镍渣中分离出来,为后续的处理提供了基础。
接下来,对于固液分离后的镍渣,可以选择进行热处理。
热处理可以将镍渣中的有机物和一些易挥发物去除,同时还能够改善镍渣的物理性质。
热处理通常使用高温炉进行,将镍渣加热至一定温度,使其中的有机物和挥发物挥发出去。
这样处理后的镍渣更加干燥,杂质含量也更低。
经过热处理后的镍渣可以进行资源回收再利用。
一种常见的方法是将镍渣进行磁选。
由于镍渣中含有一定的镍金属,可以利用磁性将其分离出来。
通过磁选,可以将镍渣中的镍金属回收,用于生产其他产品或者合金。
还可以将镍渣进行化学处理。
通过化学方法可以将镍渣中的有价金属分离出来,例如镍、铜等。
这些有价金属可以用于生产合金或者直接销售,从而实现资源的再利用。
对于处理后的镍渣残渣,可以选择进行填埋或者焚烧处理。
填埋是将残渣埋在合适的地方,焚烧则是将其进行燃烧处理。
这两种方法都能够有效地降低镍渣对环境的影响,但需要考虑相应的环境要求和法规。
镍渣的处理和资源回收再利用是一项重要的工作。
通过固液分离、热处理、磁选和化学处理等方法,可以将镍渣中的有价金属回收,同时减少对环境的影响。
这些工艺的应用需要遵循相应的法规和环保要求,以确保处理过程的安全和可持续性。
通过对镍渣的有效处理和资源回收,可以实现资源的循环利用,减少对自然资源的消耗,保护环境,促进可持续发展。
镍钴矿的选矿废渣综合利用

用率低
废渣处理成本 高,企业不愿 意投入大量资 金进行废渣处
理
废渣处理过程 中产生的二次 污染问题严重, 需要加强环保
监管
废渣处理技术 研发投入不足, 需要加强技术
研发和创新
05
镍钴矿选矿废渣的综合利用技术和方法
物理法
磁选法:利用磁性差异,分离废 渣中的镍钴金属
案例分析及其效果评价
案例背景:某镍钴矿选矿厂产生的废渣处理问题 处理方法:采用湿法冶金技术对废渣进行综合利用 效果评价:废渣中的镍、钴等有价金属得到有效回收,减少了环境污染,提高了经济效益 案例启示:镍钴矿选矿废渣综合利用具有重要的环保和经济价值,应得到广泛推广和应用。
07
镍钴矿选矿废渣综合利用的未来展望
国外研究现状:注重选 矿废渣的环境影响和生 态修复,如废渣的堆放、 处理和处置等。
研究热点:废渣的资 源化利用,如制备陶 瓷、玻璃、水泥等建 筑材料。
发展趋势:加强废渣 的综合利用,减少环 境污染,实现可持续 发展。
现有综合利用技术
选矿废渣的堆放和填埋
选矿废渣的回收和再利 用
选矿废渣的焚烧和热解
选矿废渣的生物处理和 生态修复
合物
溶剂萃取法: 利用溶剂将废 渣中的镍钴金
属萃取出来
生物法
原理:利用微生物的生物化学反应,将废渣中的有害物质转化为无害物质
优点:环保、节能、高效
应用:已在多个国家和地区得到广泛应用
前景:随着科技的发展,生物法在废渣综合利用领域的应用前景广阔
联合法
原理:利用不 同选矿方法的 优点,实现废 渣的综合利用
对资源的浪费
镍钴矿选矿废渣的产生量大,导致资源浪费严重 废渣中含有有价值的金属元素,未得到有效回收利用 废渣的堆放和处理需要占用大量土地,造成土地资源的浪费 废渣的渗滤液可能污染地下水和土壤,影响生态环境
- 1、下载文档前请自行甄别文档内容的完整性,平台不提供额外的编辑、内容补充、找答案等附加服务。
- 2、"仅部分预览"的文档,不可在线预览部分如存在完整性等问题,可反馈申请退款(可完整预览的文档不适用该条件!)。
- 3、如文档侵犯您的权益,请联系客服反馈,我们会尽快为您处理(人工客服工作时间:9:00-18:30)。
用沉淀法从废加氢脱硫催化剂的EDTA浸出液中分离并回收镍盐1 前言钴镍金属具有储能、防腐、耐磨、耐高温和高强度等优异性能,是不锈钢、充电电池、电镀、汽车配件、军工器件的关键原材料,因此被列为国民经济发展的重要战略物资[1]。
以目前的消耗速度,原生钴、镍资源可供开采年限不到67年[2],如何对现有钴、镍资源进行有效的二次利用就显得非常必要。
目前,按照行业可将钴镍废料分为六大类:废硬质合金、废高温合金、电池废料、废催化剂、废磁性材料和冶金中间渣,这其中尤以废催化剂和废旧电池的钴镍含量最高,其含量水平甚至远高于原生矿的品位。
因此,最大限度地开展钴镍资源的二次回收综合利用,将成为缓解各国钴镍资源短缺的一个重要途径。
目前工业上应用的含钴镍催化剂[3]包括加氢脱硫(HDS)催化剂、加氢脱氮(HDN)催化剂、加氢脱金属(HDM)催化剂、FDS-4A 型加氢精制催化剂、苯乙酸催化剂、加氢裂化催化剂等。
从废催化剂中回收钴镍普遍使用“浸取法”,主要是利用废催化剂中钴镍金属在不同浸取剂中的溶解性或与浸取剂反应的能力不同而进行选择性的分离回收[4]。
酸、碱浸取法,即首先将废催化剂进行焙烧处理以去除其中的油分,随后利用无机酸(HCl,H2SO4,HNO3等)或水溶性有机酸、氨水与废催化剂中的目的金属钴镍在一定反应温度、压力条件下发生化学反应,生成可溶的钴镍金属化合物(CoCl2,NiCl2,CoSO4,NiSO4等)。
经除杂后,浸出液通过采用结晶、离子交换[5]、溶剂萃取[6]、磁分离、膜分离等技术加以分离提纯,最后再通过沉淀-焙烧方法制备钴镍的氧化物产品。
以HDS为例,它指的是一类在炼油等过程中,通过加氢转化脱硫,使原料中的有机硫化物发生氢解,转化为易于脱除的H2S。
HDS催化剂的活性组分一般是过渡金属如Mo、Cu、Ni、Pt和Pd等化合物,最常用的搭配为Co-Mo、Ni-Mo、Ni-W,并通常以Al2O3为载体。
通常在浸出此种催化剂采用浓硫酸,同样地,也可采用采用诸如EDTA的有机酸来做浸出剂,此种条件下,一些Al和少量的Mo会溶解,而EDTA通常在强酸性条件下会沉淀,从而回收剩下的金属。
如果此种条件下EDTA不能完全沉淀的话,那么就需要电化学等手段从EDTA溶液里通过置换反应回收金属。
2 实验过程[7]2.1 废HDS催化剂的浸出第一阶段的浸出最优条件为:废催化剂先在500℃下焙烧90min,然后采用微波辅助加热的办法浸出(NaOH 10g/L,S/L=50g/L,4次加热,每次30s),过滤得到废催化剂,并且在105℃下烘干12h至恒重。
第二阶段的浸出条件为:采用0.1M的EDTA水溶液,微波加热(pH=10.8,S/L=50g/L,4次加热循环,每次60s)。
4次循环后,过滤分离固体和浸出液,浸出液被用来进一步沉淀回收。
2.2 EDTA的沉淀加入浓HNO3来降低浸出液的pH使得EDTA沉淀出来,在室温下搅拌该溶液使得反应达到平衡。
pH的条件根据EDTA是在Al和Mo之前还是之后沉淀而进行了验证,第一种EDTA的沉淀条件为:pH由0.1-2.5,持续3-24h,第二种EDTA的沉淀条件为:pH变化范围为0-0.5,持续3-4d。
2.3 Al和Mo的沉淀在EDTA先沉淀出来后,向反应液中加入NaOH,使pH增加到3-10。
2.4 Ni的回收加入NaOH使pH>9,使Ni以Ni(OH)2的形式沉淀出来。
为了得到Ni3(PO4)2的沉淀,需要用Fe3+置换出Ni离子,预先制备好0.4M的FeCl3·6H2O和1M的Na2HPO4·12H2O。
一定量的Fe溶液加入到Ni-EDTA溶液中,持续搅拌1天使反应达到平衡,此时Fe取代了Ni。
然后在磷酸盐加入后,立刻加入NaOH提高体系的pH(7-11.5),过滤分离固体和液体。
3 结果与讨论反应流程图见图1。
3.1 EDTA的沉淀用0.1M的EDTA溶液浸出废HDS Ni-Mo催化剂得到的浸出液含Ni 1.16g/L,Al 0.532g/L,Mo 0.115g/L。
总所周知,EDTA在较低pH下得到H4EDTA,故而常采用这种办法回收EDTA。
然而络合的EDTA比较难沉淀,这取决于络合物的溶解性和稳定性。
由表2可知,在pH>1.5时,Ni、Al、Mo都以络合的形式存在,而60%的EDTA没有络合。
在pH低于1.5时,Mo开始破络,然后是Al。
在pH=0.75时,这两种金属完全解离出来,80%的EDTA没有被络合,剩下的20%以Ni-EDTA的形式存在。
在pH小于0.5时,更稳定的Ni也开始离解。
如预期的一样,EDTA的回收率随着pH的下降而增加,这是由于金属开始解离,使得EDTA更容易被沉淀。
当pH在0-0.4时,EDTA的最大回收率为95%,此固体含Ni0.05 wt%,含Al0.1 wt%,含Mo0.2 wt%。
图2 EDTA的沉淀率随pH变化图(溶液起始Ni、Al、Mo和EDTA含量分别为2.0×10-2,1.9×10-2,1.2×10-3和0.1M)3.2 Al和Mo的分离Al在pH4-11之间因形成Al(OH)3而难溶于水,而Ni在pH大于7的时候开始沉淀,然后实际上,这两种金属的分离通常采用溶剂萃取。
因为在提高pH在4-5范围来沉淀Al(OH)3时,也会导致Ni的共沉淀,Mo也一样,会和Al一起沉淀。
通过图3得出结论:首先第一段pH在0.9-1.0时,79%EDTA沉淀出来,然后提高pH到4-6,94%的Al和67%的Mo沉淀出来,而Ni损失3%左右。
固体主要是Al(OH)3,其中约含有4 wt%的Mo和1.5 wt%的Ni;相应浸出液里含有Ni 1.13g/L,Al 29.6mg/L,Mo38.2 mg/L,以及0.02M EDTA。
Ni/Al质量比由之前的2.2上升到38,而Ni/Mo质量比由10变为30。
图3 在EDTA沉淀完后溶液中Ni、Al、Mo沉淀率随pH变化关系3.3 Ni的回收在经历了3.2的步骤后,浸出液里主要有1:1的Ni和EDTA构成,在这里比例下,Ni与几乎在整个pH范围内都与EDTA络合,由于Ni-EDTA络合物非常稳定,这样就很难通过提高pH使Ni沉淀得到Ni(OH)2。
为了回收Ni,以下介绍了3种办法。
(1)Ni-EDTA络合物在pH低于0.5时开始离解,使得EDTA可以完全沉淀下来。
为了促进Al从Ni中分离,EDTA的沉淀需要稍高的pH,在经历此分离步骤后,剩余的EDTA可以通过低于0.5的pH条件沉淀出来,从来实现Ni的沉淀。
由于在分离了Al和Mo后,EDTA的浓度已非常低了,该反应非常慢。
在加入了HNO3后,溶液里没有明显变化,经过1天后,才出现了沉淀。
3天后沉淀基本不增加。
最佳结果是pH在0.2-0.4时,70%的EDTA沉淀出来,其中含有0.02 wt%的Ni。
在加入这个结果到第一次在pH=0.9将EDTA沉淀下来后,EDTA 总的回收率为86%,这个结果比第一阶段在pH0.2-0.4之间沉淀EDTA的产率(94%)稍低。
这是由于第二次沉淀时EDTA的浓度已降低,反应平衡发生了变动所致。
在大部分EDTA沉淀后,EDTA/Ni的摩尔比约为0.3,Ni主要为自由离子并且可以被沉淀。
然而当pH提高到12时,Ni的沉淀率也只有72%,这说明Ni-EDTA 络合物在溶液中并没有发生改变。
所得沉淀的纯度约为97%,Al和Mo是主要杂质。
(2)通过采用另一种金属置换掉Ni,使得Ni尽可能完全沉淀出来。
铁离子由于其无毒,并且与EDTA有很强的络合能力而被选中。
通过计算模拟(图4)得出在pH低于3时,EDTA更倾向于与Fe络合,从而释放出Ni。
Ni(EDTA)(aq)+Fe3+(aq)=Ni2++Fe(EDTA)(aq)高于这个pH,平衡会向与Ni络合的方向进行,使Fe沉淀得到氢氧化铁。
当Fe 置换后,溶液中自由的Ni2+却不能以氢氧化物的形式沉淀出来。
这是因为升高pH会导致螯合反应的逆向反应,而且氢氧化铁比氢氧化镍更容易沉淀出来。
有数据指出Ni的磷酸盐比氢氧化物更容易沉淀出来。
所以当上面描述的EDTA在第二次被沉淀出来后,Fe被加入到浸出液中并反应一天以达到平衡。
蓝色的Ni-EDTA溶液变成黄色的Fe-EDTA。
然后讲Na2HPO4溶液也加入到溶液中。
置换反应条件:见图5Fe用量:Fe需要用来置换出Ni,但过量的Fe会和Ni共沉淀出来。
通过考察在Fe/EDTA=1-1.3,pH=7的条件下反应2min,可以得出Fe/EDTA的量的变化对Ni的回收率影响很小,并且固体里Fe的含量随着Fe/EDTA的量增加而增加,可见Fe对Ni的置换比较彻底,并且也不需要太多的Fe。
所以Fe/EDTA的比例为1是比较好的条件。
反应pH:研究显示在Ni-EDTA溶液中,如果开始吧pH维持在0.4左右,当加入磷酸盐后并没有磷酸镍沉淀出来,即使增加pH。
磷酸镍的溶解性随着pH 的增加而减小,在pH9-10时溶解度最小。
实验结果显示在pH=9,[PO43-]/[Ni2+]=1,[Fe]/[EDTA]=1的条件下反应2min,Ni最高的回收率可以达到93%。
同样地,Fe在沉淀中的含量随着pH的增加而增加,这说明即使在EDTA的存在下,高pH 有利于Fe(OH)3沉淀出来。
图4 计算模拟Ni、Fe在不同pH水溶液中物种分布(Ni、Fe和EDTA含量分别为2.0×10-2,6×10-3,6×10-3M)磷酸盐用量:按照磷酸盐与Ni的摩尔比在0-2.5中算好用量,在加入相应量的磷酸盐后,用NaOH将pH升至9并反应2min。
结果显示在不加磷酸盐时,Ni回收率较低,而沉淀中Fe含量较高。
[PO43-]/[Ni2+]的摩尔比至少要为0.7,才能保证Ni的回收率以及沉淀中Fe的含量。
反应时间:由于在pH=9时,Ni-EDTA的络合能力强于Fe-EDTA,所以Fe会生成Fe(PO4)达到平衡。
故而选取较短的反应时间进行研究,从30 s到20 min。
结果显示,Ni的回收率只有在30 s到20 min才有较大的变化,超过这个时间并没有明显的变化。
同样地,沉淀中的Fe含量也有类似规律。
故而选择此时间段进行反应。
图5不同条件下Ni的回收率以及沉淀中Fe杂质含量变化图。
A不同Fe用量,B不同pH,C不同磷酸盐用量。
(3)根据之前的研究,选择将Fe的置换反应作为第三步,并且把第二次EDTA的沉淀步骤去掉。
在第二步分离出Al和Mo得到的浸出液中,Ni和EDTA 的摩尔浓度约为0.02M,pH为5-6。
那么Fe的用量要与EDTA的量相同,并且pH要低于2.5以防止Fe沉淀。