揭秘世界最大新型捣固焦炉
6.78m捣固焦炉
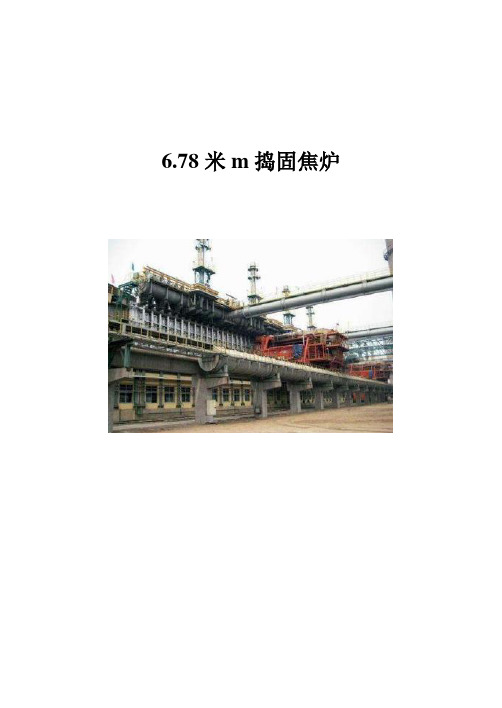
6.78米m捣固焦炉
化工设计院开发的6.78米m捣固焦炉
由化工设计院工程技术有限公司依据储备和XX煤焦公司公司的要求,决定为XX煤焦公司二期工程项目开发建设4座70孔,炭化室高6.78米m 的大型捣固焦炉及建设与其配套的生产设施、公用设施及辅助设施等。
年产焦碳在220万吨。
1.化工设计院对大型捣固焦炉进行了科学的总结,其特性如下:
1)煤饼从机侧装入炭化室;
2)煤饼上的荒煤气流通通道小;
3)炭化室锥度小;
4)装煤期间煤饼和炭化室墙面有空隙,装煤后很快消失;
5)煤饼和炭化室墙砖间有空隙;
6)机、焦侧煤饼头部有斜度;
7)焦侧煤饼头部倒塌,将被推到焦侧炉门处;
8)机侧炉头炭化室墙面温度波动大;
9)煤饼密度均匀,水分稳定;
10) 结焦时间达到2/3时,煤饼开始收缩;
11) 从结焦初期到相当长的结焦时间里,炭化室墙面承受很高的侧压。
2.炼焦车间布置
炼焦车间新建4×70孔炭化室高6.78米m超大型捣固焦炉,四座焦炉(3号、4号、5号、6号)布置在一条中心线上。
3号、4号焦炉组成一个炉组,5号、6号焦炉组成一个炉组,两个炉组之间设有独立的中控楼,除电力控制室和液压交换机室外,其余功能房间如中控室、休息室、办公室、洗手间、变送器室、自动放散点火装置控制室和集控室等各房间都布置在中控楼内。
在两炉组之间机侧设一个双曲线斗槽的煤塔及两条带有卸料小车的输送皮带。
焦炉端部设炉端台,在3号和6号焦炉端台的端部分别设置10吨电动葫芦一台,炉端台顶层设炉顶工人休息室,二间层设推焦杆托煤板实验站、事故煤槽和炉门修理站,底层设工具间、灰浆搅拌站和事故煤槽内煤料的输。
大型捣固焦炉资料

5.5米、6米、6.25米捣固焦炉使用情况6m捣固焦炉中鸿煤化有限公司年产260万吨焦炭项目一期工程建设的2*60孔炭化室高6m大型捣固焦炉,年产干全焦132万吨。
在国内属首座建成投产的6m捣固焦炉于2010年4月15日15时10分2#炭化室开始装煤;16日22时零9分推出第一炉焦炭。
该捣固焦炉炭化室长15980mm;高6000mm;平均宽500mm;锥度30mm;中心距1400mm;焦炉炉墙的极限侧负荷达10kpa ,加热水平高度805mm,采用12孔薄壁格子砖。
煤饼几何尺寸15140/14940*5800*450/430,煤饼体积38.882m3,煤饼高宽比13.18,单孔装干煤量42.22t,单孔产焦量31.67t,焦炉周转时间22.5h,每孔年产干焦炭12330t。
2*60孔捣固焦炉炉组配置60锤捣固机(其中4锤备用),捣固侧装煤车、推焦车2台(左右型各1台),炉顶导烟车2台(其中备用一台),拦焦车、熄焦车、电机车各2台(其中各备用1台),摇动给料机18台。
仅一套30锤固定式捣固机为德国制造进口,其余车辆等机械设备均为国内制造。
采用二轨式除尘拦焦车,设有装煤除尘地面站和推焦除尘地面站。
采用湿法熄焦,预留一套140t/h 干熄焦装置和牵车台位置。
捣固煤塔贮量为3000t.,在焦侧设置一座高125m烟囱,集气管布置在焦侧(焦炉与化产之间安全距离符合2008新版《焦化安全规程》之规定),采用双吸气管。
一组2痤60孔捣固焦炉用硅砖约23450吨6米捣固焦炉1、河南中鸿集团6米捣固焦炉(2号炉已完成炉体砌筑),计划明年1月份烘炉。
目前平煤集团已相对控股了该项目(占41%股权),建设过程已提速,1号炉建设也启动了,已完成炉体耐火砖订货。
武汉科技大学设计研究院设计的,拥有完全自主知识产权,并已得到专利授权。
炭化室中心距1400,炭化室平均宽500,锥度30,其余尺寸与6米顶装差不多,但加热水平做了调整。
5.5m捣固焦炉简介
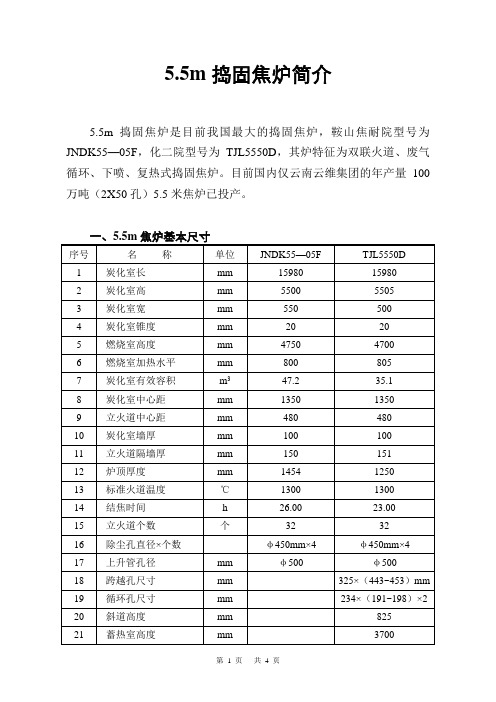
5.5m捣固焦炉简介5.5m捣固焦炉是目前我国最大的捣固焦炉,鞍山焦耐院型号为JNDK55—05F,化二院型号为TJL5550D,其炉特征为双联火道、废气循环、下喷、复热式捣固焦炉。
目前国内仅云南云维集团的年产量100万吨(2X50孔)5.5米焦炉已投产。
二、工艺参数(以公称能力100万吨/年干全焦规模计算)焦炉组数:2×50孔精煤堆比重(干):1.0t/m3煤饼尺寸(长×宽×高):15000×450×5200mm煤饼重量:35.1t焦炉周转时间:23hr产量计算:Q=365×24×2×50×35.1×0.75×0.97/23=97.26万吨/年三、焦炉的砖用量(1×50孔)四、焦炉机械(2×50孔)装煤推焦机2台720t/台除尘拦焦机2台216t/台熄焦车1台92t/台电机车1台45t/台导烟车2台85t/台24锤捣固机2台90t/台(固定)液压交换机2套 5.5/套五、焦炉新技术的应用1、蓄热室封墙内设计30mm厚硅酸钙隔热板,蓄热室外封墙设计50mm厚的复合硅酸盐整体面外加海泡石抹面,既减少了封墙漏气,又减少了热损失,改善了炉头加热,改善了操作环境。
2、在炉顶区和焦炉基础中采用强度大、隔热效率高的漂珠砖和高强度隔热砖,代替了传统焦炉采用的红砖和普通隔热砖,确保炉项表面层平整、严密,降低了炉顶面和焦炉顶板温度,改善了操作环境。
3、焦炉装煤过程产生的大量烟尘,采用炉顶导烟车收焦烟尘,送至地面站焚烧洗涤后达标排放。
4、出焦采用出焦地面站除尘工艺,除尘效率高,减少污染环境。
5、熄焦塔采用折流板除尘,预留干熄焦位置。
6、炉门采用新型弹簧炉门,加强炉门严密性,与敲打刀边炉门相比,显著减少炉门无组织排放。
近年来,焦炉不断向大型化、高效化、自动化、环保化发展,焦炉发展的主要标志是大容积,致密硅砖,提高火道温度,提高热效率及操作控制的自动化。
6.25米焦炉

6.25m捣固装煤推焦一体机(SCP机)是天津新港船舶重工有限责任公司和德国KOCH公司联合开发设计的大型捣固焦炉设备。
我们将应用世界上最新、最可靠的技术,采用先进科学的制造模式和管理手段,竭尽全力为用户打造世界一流、功能完善、设施先进、运行稳定的捣固焦炉设备。
2008年初开始为唐山佳华煤化工有限公司制作3台6.25mSCP一体机,现在已经有1台调试完毕,等待投产。
作为我国第一台大型捣固焦炉设备,它所表现出来的良好的性能得到了用户的一致好评。
一、6.25m SCP机功能简介SCP机工作于焦炉机侧,采用二点对位方式对焦炉炭化室进行操作。
SCP机主要设有煤料的储存和皮带输送机构、捣固系统、钢结构、走行装置、装煤装置、推焦装置、启闭炉门装置、炉门清扫装置、炉门框清扫装置、密封框装置以及在推焦头上设置的吹扫炭化室顶部及侧面石墨的超级汽刀装置等。
此外,还设有液压系统、集中润滑系统、气动系统、空调系统、电气系统、装煤和推焦自动显示和记录系统、自动定位系统等,各系统装置通过主控室控制协调,保证了整套SCP机高效、稳定、智能地完成生产任务。
现在将其工作过程描述如下。
在焦炉设备运行过程中,由皮带输送机将所需要的煤料连续不断地从SCP机皮带给料系统运送到SCP机车载的煤斗内,煤斗里的煤料再通过板式给料器输送到捣固箱中。
自动化操作的捣固系统安装在捣固箱上方,当检测系统检测到捣固箱底部有1m高的底煤时,捣固机驱动捣固锤上下移动,夯实装入捣固箱内的煤料,一直等到煤饼高度达到6m时停止捣固,等待装煤命令。
假设此时SCP机处于第n孔炭化室的推焦位置,通过取门装置打开(提起)机侧炉门,然后反压制动装置的楔块作用于轨道的基础结构,传输推焦过程中所产生的水平作用力。
随后,主控室发出控制信号,拦焦车作好拦焦准备,熄焦车作好接焦准备,推焦装置推出炽热的焦碳,同时打开推焦头处的超级汽刀,吹扫炭化室两侧及炉顶的石墨。
完成推焦操作的同时,清扫炉门框和炉门,退回反压制动装置的楔块,机车移动至装煤位置。
6.25m捣固焦炉简介
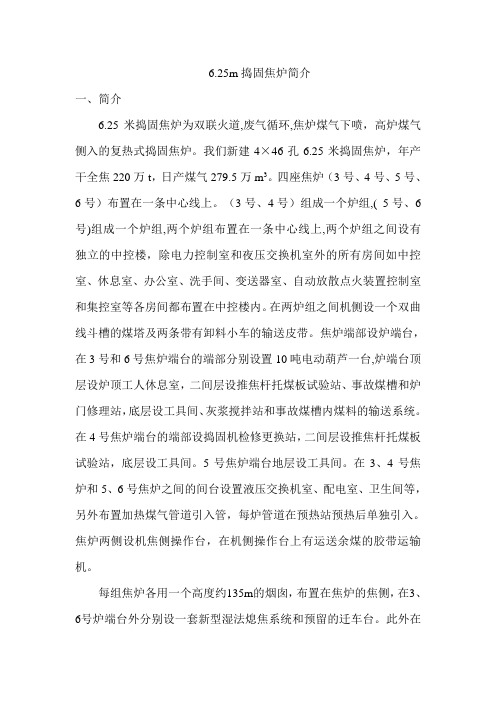
6.25m捣固焦炉简介一、简介6.25米捣固焦炉为双联火道,废气循环,焦炉煤气下喷,高炉煤气侧入的复热式捣固焦炉。
我们新建4×46孔6.25米捣固焦炉,年产干全焦220万t,日产煤气279.5万m3。
四座焦炉(3号、4号、5号、6号)布置在一条中心线上。
(3号、4号)组成一个炉组,( 5号、6号)组成一个炉组,两个炉组布置在一条中心线上,两个炉组之间设有独立的中控楼,除电力控制室和夜压交换机室外的所有房间如中控室、休息室、办公室、洗手间、变送器室、自动放散点火装置控制室和集控室等各房间都布置在中控楼内。
在两炉组之间机侧设一个双曲线斗槽的煤塔及两条带有卸料小车的输送皮带。
焦炉端部设炉端台,在3号和6号焦炉端台的端部分别设置10吨电动葫芦一台,炉端台顶层设炉顶工人休息室,二间层设推焦杆托煤板试验站、事故煤槽和炉门修理站,底层设工具间、灰浆搅拌站和事故煤槽内煤料的输送系统。
在4号焦炉端台的端部设捣固机检修更换站,二间层设推焦杆托煤板试验站,底层设工具间。
5号焦炉端台地层设工具间。
在3、4号焦炉和5、6号焦炉之间的间台设置液压交换机室、配电室、卫生间等,另外布置加热煤气管道引入管,每炉管道在预热站预热后单独引入。
焦炉两侧设机焦侧操作台,在机侧操作台上有运送余煤的胶带运输机。
每组焦炉各用一个高度约135m的烟囱,布置在焦炉的焦侧,在3、6号炉端台外分别设一套新型湿法熄焦系统和预留的迁车台。
此外在两炉组之间的焦侧预留两套与焦炉配套的干熄焦装置。
焦炉炉体的主要尺寸及技术指标二、焦炉炉体的主要尺寸及技术指标注:附表1中数据均为焦炉冷态尺寸。
四、焦炉机械1.焦炉机械配置如下表4×46孔焦炉机械配置表2.焦炉机械的主要性能及特点焦炉机械的设计在引进国际最先进技术的基础上,同时吸收我国6m 焦炉机械的技术优势,并在总结其设计经验的基础上进行了完善和提高。
从提高机械效率、降低劳动强度和改善操作环境为出发点又吸收7.63m焦炉机械的一些优点,以先进、安全、实用、可靠为原则进行设计、制造的。
捣固式焦炉设备的结构和构造特点分析

捣固式焦炉设备的结构和构造特点分析焦炉是一种常见的冶炼设备,被广泛应用于钢铁行业。
捣固式焦炉是其中的一种常见类型,本文将对捣固式焦炉设备的结构和构造特点进行详细分析。
捣固式焦炉是一种用于冶炼焦炭的设备,主要用于生产高质量的焦炭。
其主要结构包括炉壳、焦嘴、炉底、炉身、炉门等部分。
首先,炉壳是焦炉的外部包围结构,通常由一层厚实的钢板构成。
炉壳的主要功能是保护焦炉内部设备不受外界环境的影响,同时能够承受炉内高温和压力。
炉壳的厚度和材料的选择对焦炉的使用寿命和安全性有重要影响。
焦嘴是焦炉中最关键的组件之一,它位于炉顶,用于将煤气和空气喷入炉腔进行燃烧反应。
焦嘴的结构通常是圆锥形,有多个喷嘴。
焦嘴的尺寸和布置对燃烧效果和炉内温度分布起着重要影响。
炉底是焦炉的底部结构,它承受焦炭的重量和进料物料的冲击。
炉底通常采用耐火砖砌筑,以保证其耐高温和耐磨性。
为了增强炉底的稳定性,通常还会在炉底上方设置一层薄铁板,以分散炉料的力量和热量。
炉身是焦炉的主体结构,由数段炉筒组成。
炉身内部设有炉墙,其主要作用是将炉体分割为上、中、下三个区域,以便实现不同物料的分层和燃烧反应的控制。
炉身上方还设有一个温度控制装置,用于调节焦炉内的温度分布,提高燃烧效率和焦炭品质。
炉门是焦炉的出料口,通常由一系列复杂的机构组成,以保证炉门的密封性和耐高温性能。
炉门通常由两部分组成,上翻门和下翻门,以方便焦炭的顺利出料和炉内渣水的排出。
除了上述结构部分,捣固式焦炉还包括一系列辅助设备,如焦炉煤气管网、除尘设备等。
焦炉煤气管网是将煤气从炉腔引出、输送到其他设备或供应给其他用途的管道系统。
除尘设备主要用于净化焦炉煤气中的灰尘和有害物质,以保证环境的清洁和燃气利用的安全。
总的来说,捣固式焦炉设备的结构和构造特点主要包括炉壳、焦嘴、炉底、炉身、炉门等部分。
这些组成部分的设计和选择对焦炉的性能和运行效率有重要影响。
通过合理的结构设计和构造选择,可以提高焦炉的使用寿命、节约能源、减少环境污染。
捣固式焦炉设备的工作原理和机制分析

捣固式焦炉设备的工作原理和机制分析焦炉作为冶金工业中重要的设备,用于生产焦炭,它的工作原理和机制对于保证冶金工业生产效率和质量具有重要意义。
捣固式焦炉设备是一种常用的焦炉类型,本文将对其工作原理和机制进行分析。
捣固式焦炉设备是由焦炉本体、焦炉顶部装置、干熄焦装置等组成的,它的工作原理是通过在炉体中连续加热和冷却焦炭,实现焦炭的较高质量和产量。
其工作机制主要包括焦炭燃烧、焦炭升温和焦炭冷却三个阶段。
首先,焦炭燃烧是焦炉工作的第一个阶段。
在这个阶段,焦炭被加热至高温,燃烧生产气体。
捣固式焦炉设备通过控制供气量和供气速率,使得焦炭能够在适当的温度和气氛下燃烧,从而提高焦炭质量。
燃烧过程中,焦炭中的挥发分和焦炭表面的氧化物被燃烧生成CO、CO2等气体,这些气体在炉体中上升并经过气体清洗装置进行净化,最终排出。
接下来是焦炭升温阶段。
在这个阶段,炉料层内的焦炭被加热至高温状态,以便焦炭中的固定碳进一步结晶和石墨化。
捣固式焦炉设备通过提供适当的加热方式(如燃烧室、辐射等),将热能传递给炉料层内的焦炭,使焦炭温度逐渐升高。
在这个过程中,焦炭中的挥发分逐渐释放、挥发,并通过气体清洗装置排出。
最后是焦炭冷却阶段。
在这个阶段,高温的焦炭通过冷却方式进行降温,使焦炭达到适当的冷却温度。
捣固式焦炉设备通过控制冷却方式和冷却速率,有效地控制焦炭的冷却过程,从而使焦炭具备一定的强度和抗冷碱性能。
冷却过程中,焦炭会通过通风和冷却水冷却,冷却过程中产生的烟气将通过烟气处理装置进行净化处理。
捣固式焦炉设备的工作原理和机制分析表明,其通过控制焦炭燃烧、升温和冷却过程,有效地提高了焦炭的质量和产量。
在实际应用中,还需注意控制焦炭的热传递和物料输送,以进一步提高焦炭的质量和生产效率。
总结起来,捣固式焦炉设备的工作原理和机制主要包括焦炭燃烧、升温和冷却三个阶段。
通过控制这三个阶段的过程参数,可以有效提高焦炭的质量和产量。
然而,在实际应用中,还需根据具体工艺要求和设备特点进行合理的工艺操作和设备优化,以达到最佳的工作效果。
捣固焦炉型号
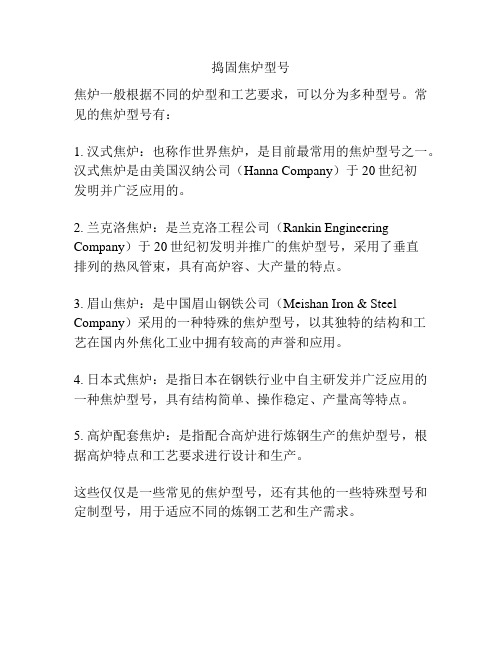
捣固焦炉型号
焦炉一般根据不同的炉型和工艺要求,可以分为多种型号。
常见的焦炉型号有:
1. 汉式焦炉:也称作世界焦炉,是目前最常用的焦炉型号之一。
汉式焦炉是由美国汉纳公司(Hanna Company)于20世纪初
发明并广泛应用的。
2. 兰克洛焦炉:是兰克洛工程公司(Rankin Engineering Company)于20世纪初发明并推广的焦炉型号,采用了垂直
排列的热风管束,具有高炉容、大产量的特点。
3. 眉山焦炉:是中国眉山钢铁公司(Meishan Iron & Steel Company)采用的一种特殊的焦炉型号,以其独特的结构和工艺在国内外焦化工业中拥有较高的声誉和应用。
4. 日本式焦炉:是指日本在钢铁行业中自主研发并广泛应用的一种焦炉型号,具有结构简单、操作稳定、产量高等特点。
5. 高炉配套焦炉:是指配合高炉进行炼钢生产的焦炉型号,根据高炉特点和工艺要求进行设计和生产。
这些仅仅是一些常见的焦炉型号,还有其他的一些特殊型号和定制型号,用于适应不同的炼钢工艺和生产需求。
- 1、下载文档前请自行甄别文档内容的完整性,平台不提供额外的编辑、内容补充、找答案等附加服务。
- 2、"仅部分预览"的文档,不可在线预览部分如存在完整性等问题,可反馈申请退款(可完整预览的文档不适用该条件!)。
- 3、如文档侵犯您的权益,请联系客服反馈,我们会尽快为您处理(人工客服工作时间:9:00-18:30)。
揭秘世界最大新型捣固焦炉
文章来源:法钢
节能减排是全球钢铁行业发展的一个重要课题和必然趋势,这也促使煤焦化工业更新技术和装备,以满足日益苛刻的环保要求。
在这种情况下,德国ZKS焦化厂建造的3号焦炉点火投产。
该焦炉采用了单孔炭化室压力控制系统,使炭化室内的压力在整个炼焦过程中保持稳定,而且能够避免装煤过程中产生烟尘。
ZKS的第二座新型焦炉(1号)也正在加紧建设,即将竣工投产。
两座焦炉的总产量约为每年130万吨焦炭。
位于德国迪林根(Dillingen)市的ZKS焦化厂的3号新型焦炉是基于捣固炼焦技术的焦炉组。
在捣固式焦炉中,煤饼是在装入焦炉之前被压实的,通过机侧炉门装入。
得益于这一技术,即使采用半焦煤也能生产出优质焦炭。
该工程由两个阶段组成(3号和1号焦炉),总体规划计划如下:兴建3号焦炉(50孔)3号焦炉投产拆除原有1号焦炉在原址新建1号焦炉(40孔)新建的1号和3号焦炉投产后,关停2号焦炉。
该大型投资项目采用最先进的环保型炼焦技术,同时维持ZKS焦化厂原有的约130万吨焦炭年生产能力。
未来2号焦炉是否重建需要ZKS最终作出决定。
最大的捣固式焦炉
原有的1号和2号焦炉共由90孔炭化室组成,高度(热态)为6.25米,新建的50孔3号焦炉与原有的两座焦炉并排而立,高度为6.25米。
新焦炉的尺寸设计旨在增加炉体耐材的坚固性(与原焦炉相比增加30%),其SUGA值(焦炉炉墙的极限负荷)达到12千帕,并且适用原有的焦炉机械设备。
该新建焦炉为世界上炭化室最高的捣固式焦炉,整个焦炉的设计、供货、安装和烘炉涵盖以下方面:炉体耐材模块、支撑系统、操作走台、燃烧系统和荒煤气系统(包括单孔炭化室压力控制系统)。
3号焦炉的加热系统设计为枪式双烟道构造,以交错助燃空气和废气再循环设计对称加热。
该项目的主要特点是集先进的炼焦技术与环保措施于一身,其主要技术参数见附表。
技术创新层出不穷
复热式加热技术。
意大利PW公司成功开发出复热式焦炉加热技术,运用于此焦炉,既可以用混合煤气加热,也可以用焦炉煤气加热。
该技术设置的自动加热控制系统可以实现多种加热方式:1/3焦炉使用混合煤气,2/3焦炉使用焦炉煤气;1/3焦炉使用焦炉煤气,2/3焦炉使用混合煤气;焦炉全部使用混合煤气;焦炉全部使用焦炉煤气。
同时,加热方式的切换可以不依靠人工操作,而由PLC(可编程逻辑控制器)控制的卷扬机完成。
废气箱通过两个气缸实现加热方式的转换,一个气缸用于风门瓣的选择(一个较大的风门瓣用于混合煤气加热,2个较小的风门瓣用于焦炉煤气加热),另一个气缸用于废
气瓣的位置调节(焦炉煤气送气位置和混合煤气送气位置)。
热控制技术。
该焦炉蓄热室划分为以下部分:机侧炉头(加热1火道~4火道)、机侧中间部分(加热5火道~18火道)、焦侧炉头(加热31火道~34火道)和焦侧中间部分(加热19火道~30火道)。
废气箱内设置了2个调节板(上下各1个),操作者可以轻松地控制炉头与中间部分空气和混合煤气的流量。
炉头火道通过标准化的调节板实现微调,使炉头加热得以控制,减少损耗,节省能源。
炉体耐火材料设计。
整个焦炉的设计包括焦炉的所有特色的基本设计和详细设计。
120名耐火砖筑砌工人在工棚里每天工作,在不到7个月的时间里筑砌800种不同形状的17000吨耐火砖。
砖型设计借助于VAP(仿真组装程序)完成,实现了精准设计、对耐火材料用量的精确估计和砌筑方案的优化。
耐火砖由德国和捷克共和国的厂家制造。
该焦炉设计过程中,采用了多套特殊软件工具以优化焦炉设计,使整个设计过程得以完全控制,从而达到所需的尖端水平。
仿真组装程序是一款可以对复杂的焦炉炉衬进行3D设计的软件包,从小烟道到焦炉顶的每一块砖都可以在程序中进行尺寸设计及合适的位置摆放。
仿真组装程序是设计和施工的得力助手,尤其是在滑动缝和膨胀缝方面,能减少设计错误,避免安装问题。
仿真组装程序可以提供详细的耐材表、工程量清单、施工草图和剖面图。
在设计和建设时,相关施工人员将焦炉炉衬耐材砖层的高度提高到了140毫米,以减少燃烧室的水平砖缝,避免炉役后期炭化室之间窜漏和减少CO有害气体的排放。
火焰分析。
进行火焰分析的目的是评估NOx(氮氧化物)值和温度分布情况。
为了满足原燃料消耗、环保和产品质量等方面的要求,根据火焰分析对燃烧室进行了精心设计。
焦炉设计时,建立了1个3D的CFD(计算流体动力学)模型来优化燃烧室内的气流热循环系统,并对空气进气孔和废气循环进行测试,以保证加热均匀和减少氮氧化物的生成,而模拟分析采用的CFD计算工具能够处理复杂的运算。
支撑系统的优化。
支撑系统旨在给予炉衬耐材适当的压力,以抵消燃烧室内的拉应力。
在支撑系统设计时,其遵从了下列连贯的步骤设计:首先,确定支撑系统的基本尺寸(炉壁防护板、支柱、门框、燃烧室炉头)和初期应力分布;其次,用Ansys软件对热应力和机械应力下的炉头(炉壁防护板、门框、燃烧室炉头)进行FEM(有限单元法)分析;最后,对燃烧室进行FEM分析。
支撑力的计算基于以下操作条件:膨胀压力(煤干馏)导致的拉应力和推焦造成的拉应力。
为了将计算的压力与燃烧室的不同部分相关联,防护板被设计成许多相互独立的板块。
这一特殊设计可以确保在正常焦炉操作条件下支撑系统始终通过防护板与炉衬耐材接触,尤其能防止裂纹的形成,而裂纹形成正是高度超过5米和安装整体防护板的焦炉常出现的问题。
巧妙控制“绝”烟尘
在捣固焦炉装煤中,煤饼是通过机侧炉门装入的,装煤饼过程会产生大量烟尘。
为减少烟尘排放,过去运用了多种治理方法,例如使用密封框,但是密封框只能部分减少而不能杜绝这种烟尘排放。
在ZKS的新焦炉中,采用的烟尘控制方法能在焦炉装煤时的集气管内产生400帕的强大负压。
在不装煤时的干馏过程中,集气管内的负压力设置在零值附近,在开始推焦之前又被转换到较高的负压设置。
为此,意大利PW公司设计开发了Sopreco阀门。
这种特殊的控制阀位于水封阀与桥管之间。
该阀门与作用于气动阀致动器上的压力控制环路相配合,使炭化室内的压力稳定在正值,在ZKS的3号新焦炉中预设为130帕。
由于采用了这种设计,再借助于水封阀,可将焦炉炭化室与集气管完全切断。
随着ZKS焦化厂3号焦炉的投产,50个Sopreco阀门投入使用,基本杜绝了烟尘排放。
焦炉点火性能稳定
焦炉在预热控制系统的操作下开始加热,加热曲线严格遵循理论曲线,最大偏差不超过0.4%。
在耐材完全膨胀以后,焦炉被维持在一个稳定而狭窄的温度范围内,以测试用于新焦炉的原有设备。
焦炉经微调以后,又成功地进行了5天的混合煤气加热性能测试,平均干馏时间为22小时。
试验结果显示,该焦炉不仅操作性能更加稳定,而且还达到了国际上现行最严格的环保标准。
随着ZKS焦化厂新3号焦炉成功地通过性能测试,其新1号焦炉的建设也在紧锣密鼓的进行之中。
德国迪林根,迪林根,Dillingen。