铸铁件氮气孔产生的原因分析及特征
分析铸造过程气孔生成的原因及对策

分析铸造过程气孔生成的原因及对策铸造过程中气孔生成的原因及对策分析铸造是一种重要的金属加工方法,可用于生产各种形状的金属制品。
然而,在铸造过程中,气孔的生成是一个常见的问题,它可能会影响到铸件的质量和性能。
本文将分析铸造过程中气孔生成的原因,并提出相关的对策。
一、原因分析1. 铸造材料的问题在铸造过程中,铸造材料的纯度、含气量和化学成分会直接影响气孔的生成。
杂质和气体在熔融金属中的存在可能会形成气泡,并在凝固过程中被包裹在铸件内部。
此外,如果铸造材料中的挥发性成分含量过高,也容易导致气孔的生成。
2. 模具设计和制造的问题模具的设计和制造不当也是气孔生成的原因之一。
设计不合理的浇口和冷却系统会导致金属在流动过程中吸入空气,形成气孔。
模具的材质和表面处理也会对气孔的生成产生影响,表面粗糙度过高或使用粘结性差的涂料可能会导致铸件表面气孔的形成。
3. 浇注工艺的问题浇注工艺是影响气孔生成的关键因素之一。
浇注温度、浇注速度和浇注角度等工艺参数的控制不当可能导致金属流动不畅,气泡无法完全排出,从而形成气孔。
此外,如果铸件内部存在复杂的几何形状,也会增加气泡在凝固过程中的积累和无法排出的可能性。
二、对策措施1. 提高铸造材料的质量为了减少气孔的生成,需要选用高纯度的铸造材料,并控制好化学成分和气体含量。
可以通过加入脱气剂来减少金属中的气体含量,同时加入合适的合金元素可以改善金属的流动性和凝固性能。
2. 优化模具设计和制造合理的模具设计可以改善金属流动状态,减少气体吸入的可能性。
浇口的设计应考虑到金属的流动路径和速度,确保金属在流动过程中尽量少吸入空气。
此外,模具的材质应选用适合的材料,并进行表面处理以提高其抗粘性和耐腐蚀性能。
3. 控制好浇注工艺参数合理控制浇注温度、浇注速度和浇注角度等参数可以使金属流动顺畅,减少气泡的生成。
同时,在铸造过程中可采用自动浇注系统和真空吸气设备来排除金属中的气体。
对于复杂几何形状的铸件,可以采用分次浇注或采用喷浇工艺来减少气孔的生成。
氮气孔
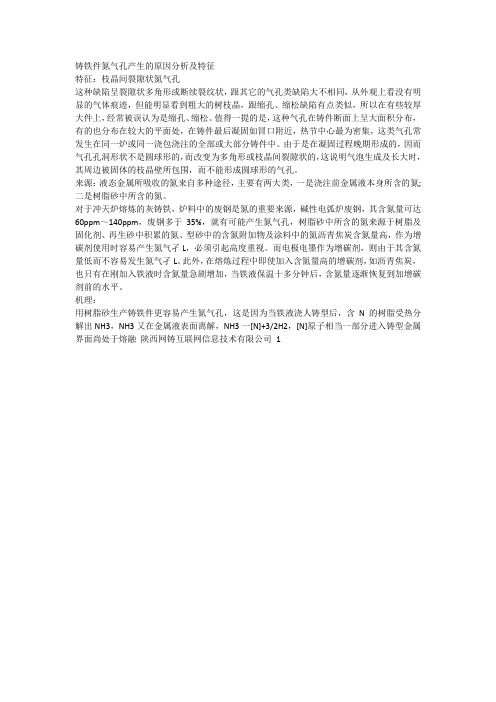
铸铁件氮气孔产生的原因分析及特征
特征:枝晶间裂隙状氮气孔
这种缺陷呈裂隙状多角形或断续裂纹状,跟其它的气孔类缺陷大不相同,从外观上看没有明显的气体痕迹,但能明显看到粗大的树枝晶,跟缩孔、缩松缺陷有点类似,所以在有些较厚大件上,经常被误认为是缩孔、缩松。
值得一提的是,这种气孔在铸件断面上呈大面积分布,有的也分布在较大的平面处,在铸件最后凝固如冒口附近,热节中心最为密集,这类气孔常发生在同一炉或同一浇包浇注的全部或大部分铸件中。
由于是在凝固过程晚期形成的,因而气孔孔洞形状不是圆球形的,而改变为多角形或枝晶间裂隙状的,这说明气泡生成及长大时,其周边被固体的枝晶壁所包围,而不能形成圆球形的气孔。
来源:液态金属所吸收的氮来自多种途径,主要有两大类,一是浇注前金属液本身所含的氮;二是树脂砂中所含的氮。
对于冲天炉熔炼的灰铸铁,炉料中的废钢是氮的重要来源,碱性电弧炉废钢,其含氮量可达60ppm~140ppm,废钢多于35%,就有可能产生氮气孔,树脂砂中所含的氮来源于树脂及固化剂、再生砂中积累的氮、型砂中的含氮附加物及涂料中的氮沥青焦炭含氮量高,作为增碳剂使用时容易产生氮气孑L,必须引起高度重视。
而电极电墨作为增碳剂,则由于其含氮量低而不容易发生氮气孑L。
此外,在熔炼过程中即使加入含氮量高的增碳剂,如沥青焦炭,也只有在刚加入铁液时含氮量急剧增加,当铁液保温十多分钟后,含氮量逐渐恢复到加增碳剂前的水平。
机理:
用树脂砂生产铸铁件更容易产生氮气孔,这是因为当铁液浇人铸型后,含N的树脂受热分解出NH3,NH3又在金属液表面离解,NH3一[N]+3/2H2,[N]原子相当一部分进入铸型金属界面尚处于熔融陕西网铸互联网信息技术有限公司1。
铸件气孔产生的原因
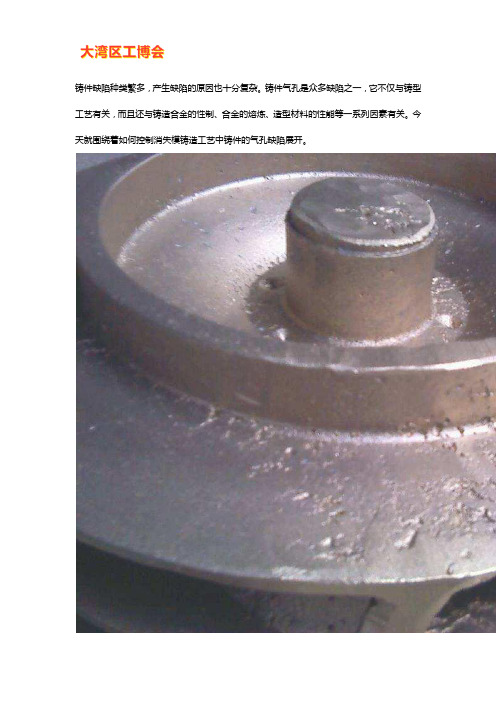
铸件缺陷种类繁多,产生缺陷的原因也十分复杂。
铸件气孔是众多缺陷之一,它不仅与铸型工艺有关,而且还与铸造合金的性制、合金的熔炼、造型材料的性能等一系列因素有关。
今天就围绕着如何控制消失模铸造工艺中铸件的气孔缺陷展开。
1、选择适宜的模型材料采用共聚泡沫模型材料,由于共聚物是拉链式分解,一次性气化程度高,液相比例小,小分子气体很容易从涂层溢出,白模密度在强度和光洁度保证的前提下尽可能小一些,减少发气总量,浇注系统采用空心直浇道并加设过滤器,对金属液进行机械挡渣、吸附梳流,使充型更平稳。
2、浇注系统及保温冒口的使用内浇道的开设要利于合金的顺利平稳快速充型,不形成死角区,在铸件的顶部设置大气压力保温冒口,集渣补缩于一体,相关部位设置随形隔砂冷铁,实现铸件的顺序凝固,把金属液内的气体、渣质及气化残留物快浮到冒口部位,减少气孔、渣孔、缩孔产生的几率。
3、提高涂料的透气性耐火骨料的粒度要适宜,采用复合粘结剂悬浮剂,配制的涂料具有高低温强度好、耐磨损、易涂刷、不开裂、排气能力强、透气性好、烧结均匀、开箱易脱落剥离,不与金属液润湿剂及化学反应,一般铸件涂刷2遍,涂层厚度2mm左右。
消失模涂料的质量管理十分关键。
在大量生产时,定期检查涂料的透气性,及时调整骨料的粒度。
由于涂料的粘结剂、悬浮剂中含有机物质,夏秋季节特别应该注意涂料的发酵酶变,合格的铸件离不开最佳的涂料,控制涂料的质量不可轻心。
4、浇注温度要适宜由于消失模的充型过程中药放热汽化泡沫,钢铁的浇注温度较砂型铸造高30-50℃。
金属液与泡沫的热作用受热浇注温度的制约,浇注温度适宜热解充分,模样的热解产物主要呈小分子气态,在负压场的作用下容易排除型腔,当浇注温度低时,模样的热解不充分,液相残留物会堵塞涂料层,热解气体排出受阻,型腔内形成反压力,充型流动性由此下降,再加上凝固速度快,液体附近的气渣来不及浮集到冒口内,生成气孔的几率增大,当然浇注温度要与冶炼的材料匹配,以避免因温度高或底而产生的其他铸造缺陷。
氮气孔_Nitrogen_Fissures
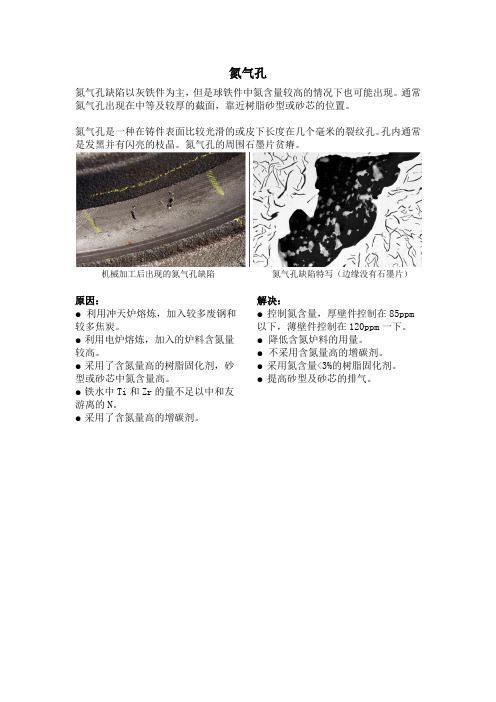
氮气孔
氮气孔缺陷以灰铁件为主,但是球铁件中氮含量较高的情况下也可能出现。
通常氮气孔出现在中等及较厚的截面,靠近树脂砂型或砂芯的位置。
氮气孔是一种在铸件表面比较光滑的或皮下长度在几个毫米的裂纹孔。
孔内通常是发黑并有闪亮的枝晶。
氮气孔的周围石墨片贫瘠。
机械加工后出现的氮气孔缺陷氮气孔缺陷特写(边缘没有石墨片)
原因:
●利用冲天炉熔炼,加入较多废钢和较多焦炭。
●利用电炉熔炼,加入的炉料含氮量较高。
●采用了含氮量高的树脂固化剂,砂型或砂芯中氮含量高。
●铁水中Ti和Zr的量不足以中和友游离的N。
●采用了含氮量高的增碳剂。
解决:
●控制氮含量,厚壁件控制在85ppm 以下,薄壁件控制在120ppm一下。
●降低含氮炉料的用量。
●不采用含氮量高的增碳剂。
●采用氮含量<3%的树脂固化剂。
●提高砂型及砂芯的排气。
铸造气孔解决方法
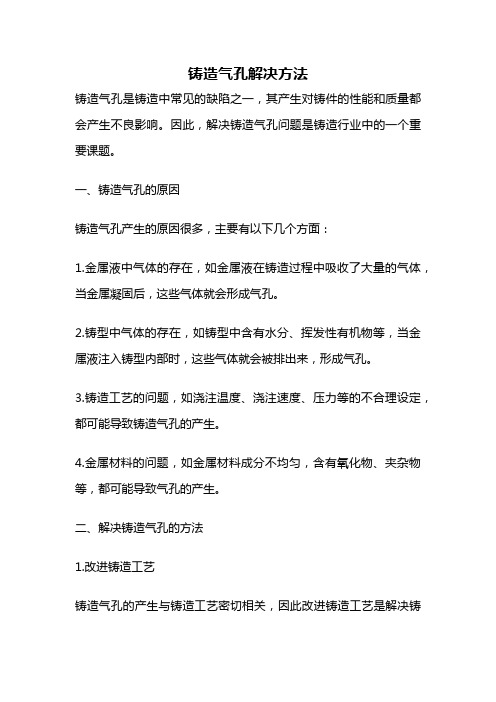
铸造气孔解决方法铸造气孔是铸造中常见的缺陷之一,其产生对铸件的性能和质量都会产生不良影响。
因此,解决铸造气孔问题是铸造行业中的一个重要课题。
一、铸造气孔的原因铸造气孔产生的原因很多,主要有以下几个方面:1.金属液中气体的存在,如金属液在铸造过程中吸收了大量的气体,当金属凝固后,这些气体就会形成气孔。
2.铸型中气体的存在,如铸型中含有水分、挥发性有机物等,当金属液注入铸型内部时,这些气体就会被排出来,形成气孔。
3.铸造工艺的问题,如浇注温度、浇注速度、压力等的不合理设定,都可能导致铸造气孔的产生。
4.金属材料的问题,如金属材料成分不均匀,含有氧化物、夹杂物等,都可能导致气孔的产生。
二、解决铸造气孔的方法1.改进铸造工艺铸造气孔的产生与铸造工艺密切相关,因此改进铸造工艺是解决铸造气孔问题的首要措施。
具体来说,可以采取以下措施:(1)提高浇注温度,减少金属液中气体的溶解度,从而减少气孔的产生。
(2)控制浇注速度和压力,使金属液充分填充铸型,减少气孔的产生。
(3)改进浇注系统,减少金属液的冲击和喷溅,从而减少气孔的产生。
2.改进金属材料金属材料的成分和质量对铸造气孔的产生也有很大的影响。
因此,改进金属材料也是解决铸造气孔问题的重要措施。
具体来说,可以采取以下措施:(1)改进金属材料的制备工艺,减少夹杂物、氧化物等的产生。
(2)优化金属材料的成分和配比,使其成分均匀,减少气孔的产生。
3.改进铸型和模具铸型和模具的质量对铸造气孔的产生也有很大的影响。
因此,改进铸型和模具也是解决铸造气孔问题的重要措施。
具体来说,可以采取以下措施:(1)优化铸型设计,使其能够充分填充金属液,减少气孔的产生。
(2)加强铸型的密封性,减少铸型中气体的存在,从而减少气孔的产生。
(3)采用高质量的模具材料,减少模具中气体的存在,从而减少气孔的产生。
4.采用热处理技术热处理技术可以改变铸件中的组织结构,从而减少气孔的产生。
具体来说,可以采用以下热处理技术:(1)固溶处理:将铸件加热到一定温度,使其中的溶质均匀分布,从而减少气孔的产生。
压铸件气孔产生的原因

压铸件气孔产生的原因产生气孔的原因有以下几点:一、氢气残留。
原材料里面还有氢气,坩埚及环境还有湿气,导致气体加热产生氢气夹裹在原材料里面,容易产生针状气孔。
二、压射室充满度不高。
压射室充满度不高会导致压射室内含空间过大,铝汤在压射前,出现回流撞击,产生涡流。
气泡是模具温度及铝温太高,容易产生气泡。
氢气,压射缸卷起,流道卷起,型腔内压力卷起,水蒸气产生气孔这些都是模具气孔的主因。
产生原因:1、金属液在压射室充满度过低(控制在45%~70%),易产生卷气,初压射速度过高。
2、模具浇注系统不合理,排气不良。
3、熔炼温度过高,含气量高,熔液未除气。
4、模具温度过高,留模时间不够,金属凝固时间不足,强度不够过早开模,受压气体膨胀起来。
5、脱模剂、注射头油用量过多。
6、喷涂后吹气时间过短,模具表面水未吹干。
解决压铸件气孔的办法:先分析出师什么原因导致的气孔,再来取相应的措施。
(1)干燥、干净的合金料。
(2)控制熔炼温度,避免过热,进行除气处理。
(3)合理选择压铸工艺参数,特别是压射速度。
调整高速切换起点。
(4)顺利填充有利于型腔气体排出,直浇道和横浇道有足够的长度(>50mm),有利于合金液平稳流动和气体有机会排出。
可改变浇口厚度、浇口方向、在形成气孔的位置设置溢流槽、排气槽。
溢流品截面积总和不能小于内浇口截面积总和的60%,否则排渣效果差。
(5)选择性能好的涂料及控制喷涂量。
预防措施:1、调整压铸工艺参数、压射速度和高压射速度的切换点。
2、修改模具浇道,增设溢流槽、排气槽。
3、降低缺陷区域模温,从而降低气体的压力作用。
4、调整熔炼工艺、5、延长留模时间,调整喷涂后吹气时间。
6、调整脱模剂、压射油用量。
气孔是压铸件中常见多发的缺陷之一。
气孔呈圆形或扁平椭圆形气泡状,直径为1mm至20mm不等,内表面光滑,覆有一层氧化层,通常分散在加工表面下。
一、气孔缺陷的成因01 金属杂质过多原材料或回收料中含有较多的氧化物和其他杂质,一些杂质(如氧化物、氢化物、油脂)在熔炼过程中会释放气体。
检测铸件气孔的方法

检测铸件气孔的方法一、引言在我国的铸造行业中,铸件气孔是一个常见的问题。
气孔的存在不仅影响铸件的外观质量,还会对其使用性能产生严重影响。
为了确保铸件的质量,对铸件气孔的检测至关重要。
本文将对铸件气孔的成因、危害以及常用的检测方法进行介绍,以帮助大家更好地了解和解决这一问题。
二、铸件气孔的成因及危害铸件气孔主要是由于铸造过程中,金属液与型砂、芯砂等固体粒子发生反应产生的气体在凝固过程中无法及时排出而在铸件内部形成的。
铸件气孔的存在会使铸件的强度、硬度、耐磨性等性能降低,同时还容易导致铸件在使用过程中出现裂纹、变形等现象。
三、检测铸件气孔的常用方法1.肉眼观察:通过肉眼直接观察铸件表面和断面,观察是否存在气孔。
这种方法适用于较大型的铸件,但对于微小气孔和内部气孔难以发现。
2.低倍显微镜检测:使用低倍显微镜观察铸件的表面和断面,可以较准确地检测到微小气孔。
但低倍显微镜检测仍然难以发现内部气孔。
3.超声波检测:利用超声波在铸件中的传播特性,检测铸件内部是否存在气孔。
这种方法无损检测,适用于各种类型的铸件,但对于形状复杂、厚度变化的铸件检测效果有所降低。
4.射线检测:通过射线对铸件进行透射,观察射线底片上是否存在气孔。
这种方法适用于厚壁、大型铸件的检测,但射线对人体有一定危害,需采取防护措施。
5.渗透检测:将渗透剂涂抹在铸件表面,通过检测气孔处渗透剂的扩散情况来判断气孔的存在。
这种方法适用于表面光滑、无油污的铸件,但对于内部气孔和微小气孔检测效果较差。
四、各种检测方法的优缺点对比1.肉眼观察和低倍显微镜检测:优点是操作简便、成本低,适用于大型铸件的表面气孔检测。
缺点是难以发现微小气孔和内部气孔。
2.超声波检测:优点是无需破坏铸件,可以检测到内部气孔。
缺点是对形状复杂、厚度变化的铸件检测效果有所降低,且对微小气孔检测效果较差。
3.射线检测:优点是适用于厚壁、大型铸件的检测,检测精度较高。
缺点是射线对人体有一定危害,需采取防护措施。
铸铁件N2孔的原因分析及防止
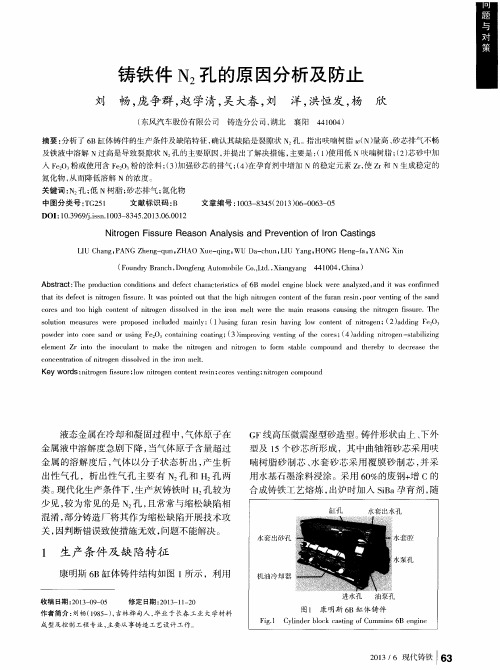
s o l u t i o n n l e a s u r e s w e r e p r o p o s e d i n c l u d e d ma i n l y :( 1 ) u s i n g f u r a n r e s i n h a v i n g l o w c o n t e n t o f n i t r o g e n: ( 2) a d d i n g F e 2 0 3
e l e me n t Z r i n t o t h e i n o e u l a n t t o ma k e t h e n i t r o g e n a n d n i t r o g e n t o f o r m s t a b l e c o mp o u n d a n d t h e r e b y t o d e c r e a s e t h e
铸铁件 N 2 孑 L 的原 因分析及 防止
刘 畅 , 庞争群 , 赵 学清 , 吴大春 , 刘 洋, 洪恒发 , 杨 欣
( 东风汽车股份有限公司 铸造分公司 , 湖北 襄阳 4 4 1 0 0 4 )
摘要 : 分析 了 6 B缸体铸件的生产 条件及缺 陷特征 , 确认其 缺陷是裂 隙状 N 孔。 指 出呋 喃树脂 ( N) 量高 、 砂芯排气不畅 及铁液 中溶解 N过高是导致裂隙状 N 孔的主要原 因 , 并提出了解决措施 , 主要是 : ( 1 ) 使用低 N呋喃树脂 ; ( 2 ) 芯砂 中加
L 1 U Ch a n g , P ANG Z h e n g — q u n, Z HAO Xu e - q i n g , WU Da - e h u n, L I U Ya n g , HONG He n g — f a , YA NG Xi n
- 1、下载文档前请自行甄别文档内容的完整性,平台不提供额外的编辑、内容补充、找答案等附加服务。
- 2、"仅部分预览"的文档,不可在线预览部分如存在完整性等问题,可反馈申请退款(可完整预览的文档不适用该条件!)。
- 3、如文档侵犯您的权益,请联系客服反馈,我们会尽快为您处理(人工客服工作时间:9:00-18:30)。
铸铁件氮气孔产生的原因分析及特征
特征:枝晶间裂隙状氮气孔
这种缺陷呈裂隙状多角形或断续裂纹状,跟其它的气孔类缺陷大不相同,从外观上看没有明显的气体痕迹,但能明显看到粗大的树枝晶,跟缩孔、缩松缺陷有点类似,所以在有些较厚大件上,经常被误认为是缩孔、缩松。
值得一提的是,这种气孔在铸件断面上呈大面积分布,有的也分布在较大的平面处,在铸件最后凝固如冒口附近,热节中心最为密集,这类气孔常发生在同一炉或同一浇包浇注的全部或大部分铸件中。
由于是在凝固过程晚期形成的,因而气孔孔洞形状不是圆球形的,而改变为多角形或枝晶间裂隙状的,这说明气泡生成及长大时,其周边被固体的枝晶壁所包围,而不能形成圆球形的气孔。
来源:液态金属所吸收的氮来自多种途径,主要有两大类,一是浇注前金属液本身所含的氮;二是树脂砂中所含的氮。
对于冲天炉熔炼的灰铸铁,炉料中的废钢是氮的重要来源,碱性电弧炉废钢,其含氮量可达
60ppm~140ppm,废钢多于35%,就有可能产生氮气孔,树脂砂中所含的氮来源于树脂及固化剂、再生砂中积累的氮、型砂中的含氮附加物及涂料中的氮沥青焦炭含氮量高,作为增碳剂使用时容易产生氮气孑L,必须引起高度重视。
而电极电墨作为增碳剂,则由于其含氮量低而不容易发生氮气孑L。
此外,在熔炼过程中即使加入含氮量高的增碳剂,如沥青焦炭,也只有在刚加入铁液时含氮量急剧增加,当铁液保温十多分钟后,含氮量逐渐恢复到加增碳剂前的水平。
机理:
用树脂砂生产铸铁件更容易产生氮气孔,这是因为当铁液浇人铸型后,含N的树脂受热分解出NH3,NH3又在金属液表面离解,NH3一[N]+3/2H2,[N]原子相当一部分进入铸型金属界面尚处于熔融
状态的金属表层,并由表向里扩散,致使表层金属液为氮饱和。
而到金属凝固期间,氮的溶解度急剧下降,就会析出氮气,形成氮气孔
铁水中含氮量大于100ppm时,往往会产生氮气孔,凝固前金属液所含全氮量=浇注前金属液本身的全氮量+树脂砂分解侵入金属液的氮量
金属液内的含氮量主要靠控制原材料废钢进行
砂铁比过高,型砂烧不透,这是导致再生砂残留含N量过高的重要因素,检测烧灼减量是监控树脂砂里面残留N量的一个主要手段
熔炼方式对灰铸铁中含氮量有较大的影响。
即使是C、Si含量相同的铁液,用工频电炉熔炼比冲天炉熔炼时的白口倾向大,含氮量也高。
对于酚醛尿烷树脂中的聚异氰酸酯,在潮湿的环境下使用时,NCO与水强烈反应,产生NH2,则要确保聚异氰酸酯容器的密封,减少它与空气的接触。
铁液含氮量高引起的氮气孔的防止方法是:铁液中加入钛铁,降低铸铁白口倾向和正确选用增碳剂。
防止树脂砂含氮量高引起的氮气孔的方法是:选用低氮树脂,型砂或涂料中加入氧化铁粉和避免树脂受潮。
1)将废钢加入量由3O降至2O%;
2)在铁液中加入氮稳定剂——锆、钛以及硼、铝,和氮生成稳定的化合物,从而降低了溶解[N]的浓度,即减少了含N量,也起脱氮作用。
特别是低碳当量灰铸铁件,当含氮量过高时,会产生枝晶间裂隙状氮气孔,铁液中加人Ti可以消除这种氮气孔。
灰铸铁含碳、硅低,即碳当量低时,氮在铁液中的溶解度增大。
因此,高牌号灰铸铁件易产生裂隙状氮气孔。
当熔融状态的铸铁中含有Zr、Al、Ti、Mg等元素时,可能形成氮化物,使铁液中的含氮量减少。
3)选用含N量5的中氮树脂,减少粘结剂中含N量;
4)下大力气着重解决再生砂的含N量问题,通过加大除尘力度,增强再生效果,提高脱膜率等措施,降低再生砂中的灼烧减量来。