76基于计算机实时控制液压同步提升技术的移动模架整体落架工法
移动模架、移动支架造桥机资料摘抄
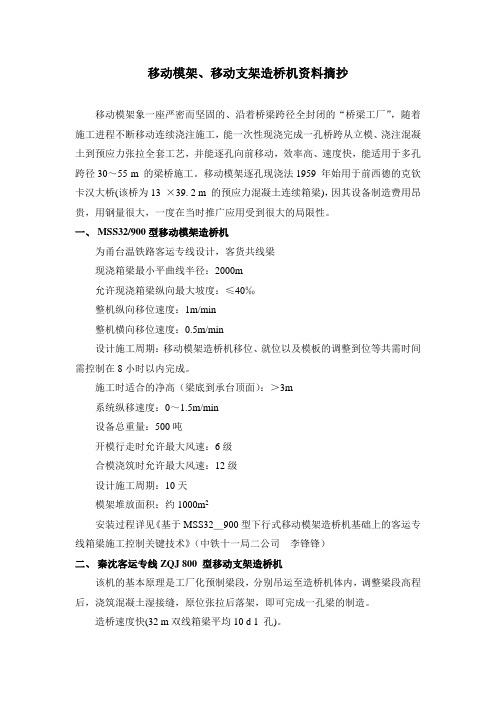
移动模架、移动支架造桥机资料摘抄移动模架象一座严密而坚固的、沿着桥梁跨径全封闭的“桥梁工厂”,随着施工进程不断移动连续浇注施工,能一次性现浇完成一孔桥跨从立模、浇注混凝土到预应力张拉全套工艺,并能逐孔向前移动,效率高、速度快,能适用于多孔跨径30~55 m 的梁桥施工。
移动模架逐孔现浇法1959 年始用于前西德的克钦卡汉大桥(该桥为13 ×39. 2 m 的预应力混凝土连续箱梁),因其设备制造费用昂贵,用钢量很大,一度在当时推广应用受到很大的局限性。
一、MSS32/900型移动模架造桥机为甬台温铁路客运专线设计,客货共线梁现浇箱梁最小平曲线半径:2000m允许现浇箱梁纵向最大坡度:≤40‰整机纵向移位速度:1m/min整机横向移位速度:0.5m/min设计施工周期:移动模架造桥机移位、就位以及模板的调整到位等共需时间需控制在8小时以内完成。
施工时适合的净高(梁底到承台顶面):>3m系统纵移速度:0~1.5m/min设备总重量:500吨开模行走时允许最大风速:6级合模浇筑时允许最大风速:12级设计施工周期:10天模架堆放面积:约1000m2安装过程详见《基于MSS32_900型下行式移动模架造桥机基础上的客运专线箱梁施工控制关键技术》(中铁十一局二公司李锋锋)二、秦沈客运专线ZQJ 800 型移动支架造桥机该机的基本原理是工厂化预制梁段,分别吊运至造桥机体内,调整梁段高程后,浇筑混凝土湿接缝,原位张拉后落架,即可完成一孔梁的制造。
造桥速度快(32 m双线箱梁平均10 d 1 孔)。
移动支架包括主桁架、下托梁、上平联和下平联,总质量253 t 。
箱梁高度2.687 m,翼缘宽度12.6 m。
技术性能和特点该造桥机造桥方法为节段拼装。
造桥跨度≤32m梁体宽度≤12.8 m梁体高度≤2.8 m梁体质量≤800 t梁段长度≤8 m梁段质量≤150 t线路纵坡≤12 ‰曲线半径≥3 000 m造桥速度为3~4 孔/ 月。
论计算机控制液压提升技术在屋盖网架提升中的应用
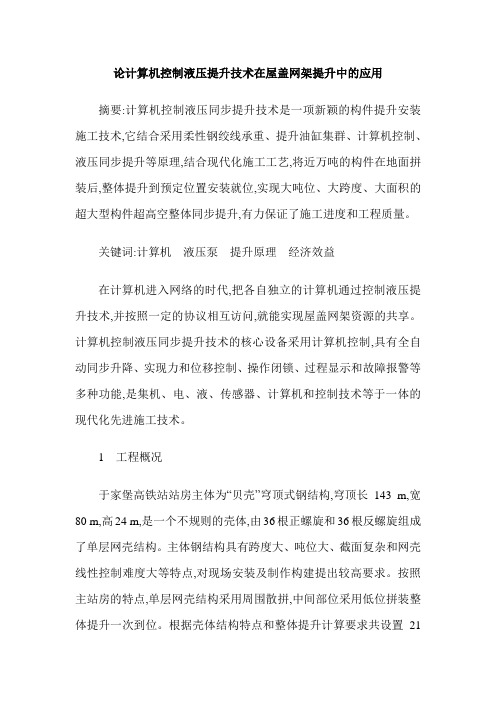
论计算机控制液压提升技术在屋盖网架提升中的应用摘要:计算机控制液压同步提升技术是一项新颖的构件提升安装施工技术,它结合采用柔性钢绞线承重、提升油缸集群、计算机控制、液压同步提升等原理,结合现代化施工工艺,将近万吨的构件在地面拼装后,整体提升到预定位置安装就位,实现大吨位、大跨度、大面积的超大型构件超高空整体同步提升,有力保证了施工进度和工程质量。
关键词:计算机液压泵提升原理经济效益在计算机进入网络的时代,把各自独立的计算机通过控制液压提升技术,并按照一定的协议相互访问,就能实现屋盖网架资源的共享。
计算机控制液压同步提升技术的核心设备采用计算机控制,具有全自动同步升降、实现力和位移控制、操作闭锁、过程显示和故障报警等多种功能,是集机、电、液、传感器、计算机和控制技术等于一体的现代化先进施工技术。
1 工程概况于家堡高铁站站房主体为“贝壳”穹顶式钢结构,穹顶长143 m,宽80 m,高24 m,是一个不规则的壳体,由36根正螺旋和36根反螺旋组成了单层网壳结构。
主体钢结构具有跨度大、吨位大、截面复杂和网壳线性控制难度大等特点,对现场安装及制作构建提出较高要求。
按照主站房的特点,单层网壳结构采用周围散拼,中间部位采用低位拼装整体提升一次到位。
根据壳体结构特点和整体提升计算要求共设置21个提升点,边缘17个提升点分别设置17个提升塔架,每个塔架上设置1台100 t油缸,网壳中间设置四个塔架,塔顶用圈梁连接,中间塔架上设置200 t油缸。
边缘一圈下吊点采用原有网壳节点板焊接耳板作为锚固结构;中间下吊点采用圈梁设置牛腿作为锚固结构。
于家堡站房屋盖提升总重约881.6 t。
总体布置如图1所示。
2 计算机控制液压同步提升系统2.1 系统组成计算机控制液压同步提升系统由钢绞线及提升油缸集群(承重部件)、液压泵站(驱动部件)、传感检测和主控计算机(控制部件)等组成。
2.2 系统特点(1)先进的电液比例控制技术,通过电液比例控制技术,实现液压提升中的同步控制,控制精度高;例如:在国家数字图书馆钢结构整体提升工程中,共布置28个同步提升吊点,使用64台提升油缸,应用电液比例控制技术,各点之间的同步控制精度在±2 mm内。
移动模架施工工艺及技术标准

移动模架施工工艺及技术标准移动模架造桥施工工艺及施工控制技术标准一、施工工法DZ32/900造桥机是在预先安装于桥墩两侧的钢托架上~拼装带有模板的钢主梁,移动模架,~利用钢主梁承重~在预应力混凝土箱梁的设计位臵上整孔现浇箱梁混凝土~经养护待初张预应力钢束箱梁能安全承受自重后~移动模架整体下降~脱去底模和外模。
然后模架在墩旁托架上向前方移动一孔~再制造下一孔箱梁。
预应力钢束终张可按施工组织的合理安排适时进行。
而内模是在下一孔待制箱梁底腹板钢筋就位后~再从已制箱梁内用专用小车分段运出安装。
二、施工工艺,一,、移动模架制梁工艺流程造桥机拼装底、侧模板调整底、侧模板调整支座安装底、腹板钢筋、波纹管安装内模预拼内模安装调整顶板钢筋、端模安装砼浇注、养护初张拉终张拉、压浆、封端造桥机落架、脱模内模小车拆移内模造桥机移位造桥机顶升就位工艺流程图移动模架系统在现场拼装成型~进行模板调整、预拱度设臵及预压。
钢筋在加工场集中加工、专用运输车运输到施工桥位、吊车吊装到桥上作业面后进行绑扎,预应力孔道采用预埋波纹管成孔,底、腹板钢筋绑扎完成后~安装内模~最后进行顶板、翼缘板钢筋绑扎,混凝土在拌和站集中拌和、混凝土输送车运输~混凝土泵车入模~插入式振动器进行梁体混凝土振捣~桥面采用悬空式整平机整平,梁体养护采用自然养生,预应力筋张拉采用两端整拉工艺~真空压浆、封端,移动模架落架、脱模~纵向前移至下一浇筑孔位。
根据自行式移动模架工作原理及其结构形式~系统自行时要求桥墩高度不宜小于7m~结合设计资料对于桥墩高度大于7m的桥梁采用支撑托架自行的方案进行现浇梁施工,对于桥墩高度小于7m的桥梁~可在其墩旁用贝雷片搭设临时支架来支承移动模架主梁~在移动模架过孔时~同样利用移动模架前、中、后悬挂完成主梁的支撑。
? 移动模架组拼移动模架拼装顺序:牛腿支架、主梁组装的有关施工设备、机具就位?支墩搭设?牛腿支架组装?牛腿支架安装?主梁组装?主梁吊装就位?横梁安装?铺设底模?安装外侧模。
简支箱梁移动模架法施工技术

②
98.8
98.8
103.8
112.7
③
8.8
8.8
9.3
10.1
Ⅱ区域
2)整个拼装过程中应有足够的安全防护设施,参加拼装人员须进行岗前安全培训,经考试合格后,方可作业;3)需对所有参加拼装作业人员须进行专项安全交底,交底记录和签字必须齐全;4)特殊工种人员须持证上岗;5)施工过程中,安全、技术人员必须随时跟踪检查其各部件及连接是否稳妥、牢固,并做好检查记录,确保安全和质量。
2)墩旁托架:支承牛腿。是由矩形截面梁组拼成的三角形空间结构,与桥墩通过φ32的高强度精轧螺纹钢筋对拉而成。起承上启下的作用。
4)主箱梁:为对称的两组钢箱梁。 (MZ32/900)断面尺寸为1.6mx2.8m。主箱梁全长为38米,分为五节,中间节长为8米,其余节为7.5米;节间通过节点板、高强螺栓连接。主箱梁腹板开有孔口,孔口处,内外设计有两个支承托,以便安装梳形梁。
2.1.1上承(行)式移动模架的组装1)施工准备:(1)设备准备:50t流动吊机一台及必须的吊索具;电焊机2台;脚手架若干;缆绳;专用工具;爬梯等。(2)场地(桥台侧路基上):在长70米、桥两侧各20米宽范围内平整,无障碍物。(3)人员:起重工、钳工、电工、技术人员其他辅助工作人员。
2)技术准备(1)拼装人员应熟读图纸,清楚该设备的主要功能及各种动作。(2)整个装、试、拆的过程中应有足够的安全防护设施。(3)配齐各种检测器具,包括:水平仪、卷尺,靠尺等。
2.2制造:使用(设计)单位必须委托具有相应加工制造资质的单位进行加工制造,制造使用的原材料及材质必须符合设计要求;加工质量应满足相关验标规定,所有受力件应进行探伤检测;加工制造完毕,须经检验符合相关要求后才能出厂;出厂应有使用及维护说明书、出厂合格证、材质试验报告及探伤检测记录等。设计、使用单位宜派员监造。
计算机液压同步提升技术在某桥梁施工中的运用

J g e h n fre a p e ti p p rit d c ste k ytc n q ei os n ese l o e . piain o o i d z e o x m l , s a e nr u e h e h iu n h i i gt te tw r Ap l t fc m・ n h o e t h c o
总宽 度 为 2 如 图 1 示 . 9m. 所
白鹭 大桥 主桥结 构形 式为 三跨 连续单 索 面独塔无 背索 竖琴式 斜 拉桥 , 跨跨 径 为 10 m, 边边 跨 跨 径 主 2 两 为 4 .9m, 5 2 总长 20 5 主梁 为钢梁 , 1 .8m. 采用 连续结构 , 塔梁 处与塔 、 固结 . 梁采 用 封 闭 型扁 平钢 箱 梁 在 墩 钢
Vo . 7 1 2 No. 3
J n.( 8 u 2J 0
计 算 机 液 压 同步 提 升技 术 在 某 桥 梁 施工 中的运 用
范 大 意 陈征 宇 ,
( . 铁 大桥 局 集 团 第 - t 程 有 限 公 司 , 西 九 江 320 ,. 江 市公 路 局 路 桥 _ 程 处 , 1中 i f 江 3 002 九 3 2 江西 九 江 3 20 ) 300 摘 要: 以景 德镇 白鹭 大 桥 主 桥 钢 塔 竖向 转 体 施 工 为 倒 , 阐述 了钢 塔 竖转 技 术 要 点 . 对 大 桥 无 背 索斜 拉 桥 钢 塔 的 针
维普资讯
第 2 卷 第 3期 7 20 0 8年 6月
文章 编 号 :64—07 (0 80 0 2 17 06 20 )3— 04—0 4
南 昌 工 程 学 院学 报
J und o a c a g I s tt o e h oo y' i
工法名单

GGG(京)B1019-2008
高政、王旭东、孙建波、周兴业、戴克斌
GGG(京)B3020-2008
橡胶沥青加工工法
北京市政路桥建材集团有限公司 交通部公路科学研究院 北京市公路桥梁建设集团有限公司
柳浩、王旭东、杨丽英、李美江、刘长剑
GGG(冀)B4021-2008
GTM设计加聚酯纤维沥青混合料 河北建设集团有限公司 路面施工工法
GGG(黑)A2007-2008
高寒地区沼泽地带路基下处理施 龙建路桥股份有限公司 工工法
李冰、林树丰、朱仲士、张佳鹏、张九华
GGG(鲁)A2008-2008
粉喷桩施工工法
山东省公路建设(集团)有限公司 第 1 页
贾海庆、周海防
工法编号
工法名称
完成单位
主要完成人
GGG(晋)A2009-2008
抛石强夯冲击碾压处理高寒湿地 山西省机械施工公司 公路软基施工工法 公路路堑段边坡防护客土吹附施 浙江省大成建设集团有限公司 工工法 大直径(钉型)双向深层水泥土 浙江省交通工程建设集团有限公司 搅拌桩施工工法 中国建筑第七工程局有限公司 中建七局(上海)有限公司
刘久明、郑春刚、晏志辉、姚怀新、周立
GGG(京)B3024-2008
王旭东、李美江、蔡玮、高政、吕志前
GGG(京)B3025-2008
橡胶沥青混凝土施工工法
王旭东、柳浩、李美江、高维兵、杨丽英
第 3 页
工法编号
工法名称
完成单位
主要完成人
GGG(黑)B4026-2008
聚酯纤维加强改性沥青混凝土桥 龙建路桥股份有限公司 面铺装施工工法
傅柏先、赵根生、徐景岩、周茂祥、周焕涛
GGG(鲁)C1057-2008
计算机控制液压同步提升技术在大空间网架工程中的应用
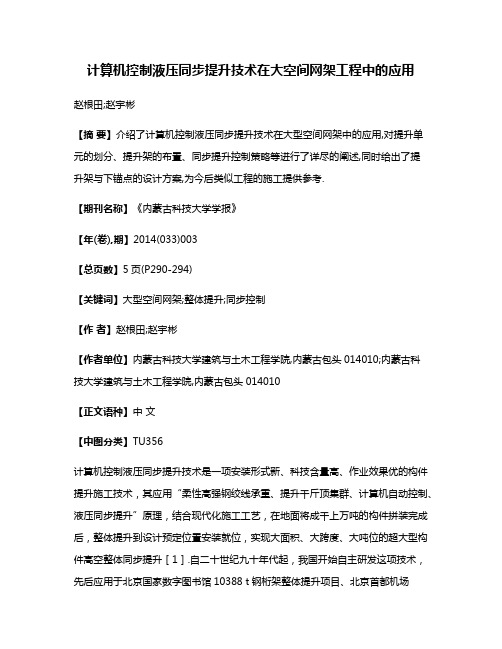
计算机控制液压同步提升技术在大空间网架工程中的应用赵根田;赵宇彬【摘要】介绍了计算机控制液压同步提升技术在大型空间网架中的应用,对提升单元的划分、提升架的布置、同步提升控制策略等进行了详尽的阐述,同时给出了提升架与下锚点的设计方案,为今后类似工程的施工提供参考.【期刊名称】《内蒙古科技大学学报》【年(卷),期】2014(033)003【总页数】5页(P290-294)【关键词】大型空间网架;整体提升;同步控制【作者】赵根田;赵宇彬【作者单位】内蒙古科技大学建筑与土木工程学院,内蒙古包头014010;内蒙古科技大学建筑与土木工程学院,内蒙古包头014010【正文语种】中文【中图分类】TU356计算机控制液压同步提升技术是一项安装形式新、科技含量高、作业效果优的构件提升施工技术,其应用“柔性高强钢绞线承重、提升千斤顶集群、计算机自动控制、液压同步提升”原理,结合现代化施工工艺,在地面将成千上万吨的构件拼装完成后,整体提升到设计预定位置安装就位,实现大面积、大跨度、大吨位的超大型构件高空整体同步提升[1].自二十世纪九十年代起,我国开始自主研发这项技术,先后应用于北京国家数字图书馆10388 t钢桁架整体提升项目、北京首都机场A380机库万吨屋盖整体提升项目[2]、潮汕机场航站楼钢屋盖整体提升项目等一系列重大建设工程[3],获得了令人瞩目的成功.该技术应用在本网架工程中,使得成本下降,工期缩短,为类似工程的施工提供了宝贵的借鉴经验.某大型空间网架工程,基本单元为正放四角锥型,以圆形钢管为主要受力构件,节点构造形式以螺栓球节点为主,局部采用焊接空心球节点和相贯线节点.整个网架为周边点支撑结构,项目建筑面积45955 m2,纵向长度为361.55 m,横向最大跨度为123.00 m,屋面最高标高为116.40 m,屋面采用双层压型钢板复合保温屋面,无组织排水.总体模型如图1所示.由于该项目结构复杂,施工面积广,高度大,如果采用传统的施工安装方法[4],将增加建设成本,增大高空作业量.经过多种方案对比研究,本工程屋盖网架采用地面拼装,高空分块吊装的方法进行施工;墙面网架安装则采用地面组装,液压同步整体提升屋盖网架的逆序施工法安装.本文主要针对墙面网架安装过程中,屋面网架整体提升过程进行研究.整个结构呈空间网架体系,上部半拱形网架屋盖已完成拼装,垂直高度为61.5 m;下部网架墙柱均竖直设置,垂直高度为54.9 m.墙面网架由九节高6.1 m的基本单元为正放四角锥型的网格构成.考虑墙架拼装过程中焊接操作的难易程度,同时为减少高空作业量,保证施工技术人员的安全,故将竖向网架墙面以正放四角锥网格单元为基准划分为12.2,12.2,6.1,12.2,12.2 m 五个作业单元,并且与逆作法施工相配合,进行五阶段液压提升器集群同步提升作业.按照上述单元的划分,整个主体结构第五次提升最大提升总重量约12000 t.根据本建筑结构的自身特点,将施工作业区域划分为东区、西区及山墙区三大区域.东、西区由20个小区域构成,山墙区划分为6个小区.每个小区设置一个钢提升架完成作业,各提升架安置在网架墙柱的柱间.除东20区和西20区的提升架各安置一台液压提升器外,其余每个提升支撑架上装备两台液压提升器对其左右两侧网格结构进行提升施工,即整个结构共布置提升点90个,如图2所示.整个结构沿南北方向(即长度方向)对称,故提升点布置也严格以南北轴对称.为保证结构受力均衡、传力稳定,将下吊点通常设置在网架墙柱的支座处或各网格球节点处,使得总体结构在施工过程中更加安全可靠.钢绞线及提升油缸是作业系统的承重部件,用来承受提升构件的重量.施工企业可以根据提升重量的大小来配置提升油缸的规格,每个提升吊点中油缸可以并联使用. 根据各作业点提升力的要求,本项目钢绞线采用高强度低松弛预应力钢绞线,公称直径为15.24 mm,抗拉强度为1860 N/mm2,破断拉力为260.7 kN.将若干液压油缸与液压阀组、泵站等组成液压千斤顶集群.在计算机自动控制下,集群的液压千斤顶同步作业,使提升结构的姿态平稳、承载均衡,从而顺利安装就位.本工程中的提升油缸为穿芯式结构,整个提升过程共布置90台,其中26台560 t油缸,64台350 t油缸.其各项指标性能见表1.建筑结构单向对称,故取东区45个提升点加以分析.提升点提升反力统计见表2.在确定提升器械的使用承载性能时,应对其额定值加以折减,穿心式液压千斤顶的折减系数取值一般在0.5至0.6之间[5].根据实际施工情况,本工程提升器额定值折减系数取0.6.以东20区门头处提升点1为例,提升反力为2906 kN,液压千斤顶安全储备系数为:3360/2906=1.16.提升器的承载能力在折减之后仍然有较高的安全储备,为整个提升作业的顺利完成提供了坚实的保障.综合考量液压千斤顶的提升能力、钢绞线最大配置量、提升反力及实际现场情况,确定各提升千斤顶的实际配置钢绞线数目.本工程采用的高强钢绞线破断拉力为260.7 kN.以东20区门头处提升点1为例,钢绞线安全储备系数为:260.7×25/2906=2.24.所有提升点单根钢绞线安全储备系数均大于2,充分保证了提升过程中钢绞线的承载性能.提升架主要承受整体提升过程中液压千斤顶所传来的提升反力,并通过自身构件传递到地面.根据单次提升最大高度及实际现场施工情况,确定提升支撑架高度为17 m.由于提升架安置在主体结构网架墙柱之间,故设计提升架东西方向长度为6.15 m,南北方向宽4.05 m(如图3,4).提升钢架呈立方体型,所用构件均选用Q345钢材.其四角立柱为主要受力构件,选用截面为250×12的矩形钢管.支撑架底面采用截面形式为500×400×28×28的矩形钢管,同时在四脚端部与网架主体的基础支座相连,以保证支撑架的整体稳定.竖向斜撑主要以截面为140×6,159×8的圆形钢管为主,上部提升平台处受力较大,故斜向支撑选用245×10的圆管.水平支撑多采用89×6的圆形钢管.支撑架上部南北向设置提升平台,以截面尺寸为450×400×18×24的H型钢为主要承载构件,其间加设89×6的圆管予以加强连接.以东侧第9区提升架为例,其整体提升最不利工况出现在第五阶段,单次提升最大重量分别为147.8,146.7 t.故在提升平台两侧分别施加1478,1467 kN提升反力.经有限元分析软件SAP2000模拟,综合分析各构件强度性能、应力分布等特性,得出提升支撑架支座反力(如图5)及构件应力比(如图6).通过研究结构构件应力比量值,可知提升反力主要通过提升平台由竖向立柱传递至地面.支撑架上部斜向支撑充分发挥了承载作用,保证了整个结构均衡受荷的工作状态.上部提升平台应力比相对较大,最高值达0.872.所有构件应力比量值均小于1,整个结构承载性能良好,变形正常,可充分满足提升作业的承载需求.在各阶段整体提升过程中,下吊点以桁架式托梁作为主要受力构件支撑网架墙柱下部球节点,如图7所示.通过桁架结构主要传递轴力的特点,巧妙地将提升力传递到网架墙柱的柱脚与球节点,使整个结构传力直接、承载均衡,进一步保证了结构主体在提升过程中的可靠性.下锚点则通过锚固梁,以形似扁担的方式,将高强钢绞线上的力直接传递到桁架式托梁上,如图8所示.这样有效地连接了提升器与主体结构的同时,更加高效地畅通了传力途径,为施工的安全开展奠定了基础.根据实际工程结构特点,采用“吊点油压均衡,提升分级加载,行程同步控制,分级卸载就位”的控制策略,以保证各提升点的位置同步,相邻提升点误差限制在10 mm之内,从而满足结构提升要求[6].吊点油压均衡:在提升阶段,对每个提升点的液压提升设备施加均衡的油压,从而使各吊点以恒定的驱动力进行提升作业.提升分级加载:以仿真模拟的各吊点提升反力数据为参照,对各液压千斤顶进行统一加载,依次为20%,40%,60%,70%,80%分级加载,在检查结构各单元均无异常的情况下,继续由提升力的90%,95%加载至100%,直到整个网架体系全部脱离支座.行程同步控制:在整个施工过程中,各提升点之间的标高误差要求控制在10 mm 内.所有提升点的即时标高值通过网络反馈到控制中心.若出现超标现象,则计算机系统单独控制超标点提升,其余各提升点均保持原状态不动.当各提升点回到控制偏差内,传感器复位,并以调整后的标高作为新的起始位置.以此来保证结构在允许误差内以同步状态到达预定位置.分级卸载就位:整个结构下部墙柱网架安装完成后,计算机系统同步调整各提升点卸荷速度,并按照95%,90%,80%,70%,60%,40%,20%的态势逐级卸载. 基于某空间网架结构整体提升项目,提出了“屋盖网架五阶段整体提升,墙面网架逆序安装”的施工方法.同时在承重部件的设置方面,保证折减后的油缸储备系数大于1,钢绞线安全系数大于2.结合网架结构特点,采用“桁架式托梁”的下锚点设计,同时对提升架的承载性能的验算也保证了工程的可靠性,为大型钢结构工程的施工安装提供了宝贵的参考价值.【相关文献】[1]柳志华.液压整体提升技术在大型门式塔楼施工中的应用[J].建筑施工,2013,(4):279-281.[2]刘彪,刘航等.首都机场A380机库屋盖整体提升施工过程分析[J].施工技术,2008,37(4):50-52.[3]曾令权,郭正兴等.潮汕机场航站楼钢屋盖整体提升技术[J].施工技术,2011,40(1):70-72.[4]吴欣之.现代建筑钢结构安装技术[M].北京:中国电力出版社,2008.[5]空间网格结构技术规程,JGJ7-2010[S].北京:中国建筑工业出版社,2010.[6]李建全,陈至诚等.浦东机场波音机库钢屋盖结构液压整体提升施工技术[J].钢结构,2010,(8):65-67,82.。
移动模架施工技术

•(2)、梁型。目前国内造桥机基本都能够实现 32m、24m变跨施工的要求,但每次变跨都要 投入较大的人力物力,因而一座桥梁中如果 变跨频繁则采用移动模架法施工工效较低。
•(3)、墩高及地形。墩高是确定选用何种形式 移动模架的关键因素。墩身较低时,若地形
条件较好则采用满堂支架法施工效果较好。
但若地基较差,地基处理投入过高则可考虑
主梁 横梁 吊架 外模 内模 移动模架施工技术
PPT文档演模板
2020/11/24
支架 推进工作车
主梁 横梁 吊架 外模 内模 移动模架施工技术
PPT文档演模板
2020/11/24
支架 推进工作车
主梁 横梁 吊架 外模 内模 移动模架施工技术
PPT文档演模板
2020/11/24
支架 推进工作车
• (3) 纵移过孔
PPT文档演模板
移动模架施工技术
六、移动模架造桥机安装
• 安装常用的方法有两种:
• 1、直接吊装法
•
适用于墩身较矮,地形条件较好,需
要大型的吊装设备。
PPT文档演模板
移动模架施工技术
• 2、提升法
•
适用于墩身较高,地形条件较好,不
需要大型的吊装设备。但需加工提升设备。
PPT文档演模板
移动模架施工技术
PPT文档演模板
移动模架施工技术
PPT文档演模板
移动模架施工技术
“0,2 x L”
模板安装就位
调整吊杆,将造桥机调整到浇注 混凝土位置
但此时主梁后方不再使用墩顶支 撑支撑。
安装并使用吊架的2台主千斤顶 将主梁提升就位。
“0,2 x L”
PPT文档演模板
移动模架施工技术
- 1、下载文档前请自行甄别文档内容的完整性,平台不提供额外的编辑、内容补充、找答案等附加服务。
- 2、"仅部分预览"的文档,不可在线预览部分如存在完整性等问题,可反馈申请退款(可完整预览的文档不适用该条件!)。
- 3、如文档侵犯您的权益,请联系客服反馈,我们会尽快为您处理(人工客服工作时间:9:00-18:30)。
基于计算机实时控制液压同步提升技术的移动模架整体落架工法GGG(浙)C3076-2008吴墀忠单光炎范厚彬卞永明宋文杰(浙江省交通工程建设集团有限公司上海同新机电控制技术有限公司)1.前言移动模架是先进的造桥设备,适用于跨越山谷、软弱地基、河道、海上滩涂以及高墩区现浇连续梁桥施工。
近年来移动模架广泛用于跨海桥梁滩涂区连续梁桥施工,完成连续梁桥施工后,往往处于海中高墩区。
由于设备自重较大,单套50m自行式移动模架自重近800t,,这种条件下拆卸移动模架的关键,是如何安全、快速地将设备整体落架到拆卸平台上,这是技术难度高、风险大的操作。
为解决该技术难题,浙江省交通工程建设集团有限公司与上海同新机电技术控制有限公司开展了技术攻关,采用基于计算机实时控制的液压同步提升技术进行50m自行式移动模架的整体落架施工,成功实现了移动模架安全拆卸。
该技术在舟山大陆连岛工程金塘大桥Ⅴ合同工程得到成功应用。
经过两个项目的成功实施,总结编写成本工法。
2.工法特点本工法自动化程度高,避免了传统施工方法的诸多不足之处,安全、经济、高效。
2.0.1 技术先进。
本工法采用基于计算机实时液压同步提升技术,通过计算机实时控制系统实现液压油缸的多点同步控制,技术含量较高。
2.0.2 安全可靠。
首先,本工法考虑了操作过程中各种可能的情况并采取了有效的预防技术措施,在材料和设备的选用方面有较大的保险系数。
其次,该工法在正式落架时只需要少数观测和计算机操作人员,劳动强度低,现场文明情况好,有利于安全管理。
2.0.3 环保高效。
本工法不需要数台大型吊机和大型临时平台,免去大量的周转材料和施工费用。
主要准备工作是安装液压设备和计算机控制系统,准备周期短,正常落架可达到4m/h,效率高。
2.0.4 费用低廉。
该工法可节约大量的人、机、料费用,只需要成套的设备和少量的周转材料即可进行设备整体落架。
3.适用范围本工法适用于移动模架的整体提升、整体落架,也适用于同类工程大型构件的整体提升或整体下放工程施工。
设备重量较大、提升或落架高度较高,如超过100T重的大型设备需要提升或落架12m以上,采用传统的起重作业不经济、不安全时,适宜采用该工法。
4.工艺原理移动模架整体落架时,设备的梁体、底模连成整体,保持工作状态,通过4个吊点悬吊于整体提升系统上,如图4.0.1-1。
每个吊点设2只提升油缸,置于已完成的箱梁上,预应力钢绞线穿过提升油缸和箱梁预留孔,与固定在移动模架主梁上的4个转换器锚接,形成4个对称的吊点。
液压同步提升设备由提升油缸、液压泵站和计算机实时控制系统三部分组成。
计算机实时控制系统包括主控计算机、分散在现场各处的智能节点以及将它们连成一体的传输线路,以控制提升油缸的操作。
主控计算机通过智能节点采集现场信息、控制液压泵站,自动实现对提升油缸的组合动作同步的控制,采用间歇式的作业方式,以4m/h的速度将设备整体下放到拆卸平台上。
同步控制的目标是:位置载荷均衡控制和同步控制。
图4.0.1-1 移动模架整体落架吊点布置图4.0.1 载荷均衡控制由于1、2和3、4提升吊点相距较远,为保证结构安全,整体下放时,要求各点实际载荷与理论计算载荷基本符合。
在每个提升吊点布置1个压力传感器,主控计算机通过它实时采集各个提升吊点的载荷,掌握各个提升吊点的载荷分配,从而根据理想的载荷分配比例进行实时调整,保证下降载荷分配的正确性。
4.0.2 位置同步控制控制系统必须调整好移动模架的空中姿态。
空中姿态可以通过“绝对”加“相对”的测量方法来确定。
在距离测量系统中,使用激光测距仪进行长距离的测量,以获取“大”的绝对位移,而使用实时性能较好的行程传感器来获取“小”的相对位移。
4.0.3 下放系统提升油缸的动作同步控制整体下放时,控制系统必须有效地、有序地控制提升油缸的动作。
主控计算机通过实时控制系统收集各个吊点提升油缸的状态信息(锚具和主油缸),根据控制逻辑顺序控制电磁换向阀,从而控制提升油缸的锚具和主油缸动作。
5.施工工艺流程及操作要点5.1 工艺流程本工法工艺流程见图5.1-1图5.1-1 工艺流程图5.2 操作要点5.2.1 技术准备技术准备阶段最主要的工作是编制方案、进行相关安全性计算、确定相关临时设施、辅助设备材料和组织技术交底培训等。
相关材料设备进场后,要及时进行材料试验检测和设备安全性检查。
5.2.2 搭设拆卸平台移动模架拆卸平台包括两部分,一是移动模架整体落架到位后的支撑塔架,塔架安装在承台顶面,在墩身的左右两侧对称布置,并用对拉螺杆对拉;二是设备拆卸平台,利用桩基、下部结构施工平台,进行加固和维护保养,拆卸平台实景见图5.2.10-1。
5.2.3 安装液压系统液压系统包括提升油缸、液压泵站以及相关的辅助支撑材料和临时设施。
如图4.0.1-1,每个吊点设两台200t提升油缸,共有8只提升油缸,每个液压泵站连接4个提升油缸,共有2台液压泵站。
提升油缸安装在加工好的型钢支架上。
安装完成的液压系统如图5.2.3-1。
为便于安装和移动模架整体下放操作,在液压系统安装前,先拆除移动模架的腹板和翼板模板,以方便系统安装,降低结构自重。
图5.2.3-1 安装完成的液压系统5.2.4 安装实时控制系统将压力传感器、智能传感器、油缸锚具传感器等安装在各液压泵站和提升油缸相应位置上,并通过导线与主控计算机连接,形成计算机实时控制系统,用以收集各智能节点的数据信息并传输泵站和提升油缸操作的控制指令。
各类传感器见图5.2.4-1~5.2.4-4。
图5.2.4-1 主控计算机图5.2.4-2 行程传感器(测量行程)图5.2.4-3 长距离传感器(精度:0.25mm)图5.2.4-4 油压传感器(精度:0.5%)5.2.5 安装吊点移动模架整体落架,两根主梁各对称设2个吊点,共设4个吊点,吊绳采用钢铰线。
每只提升油缸各夹19根钢绞线,其长度通过计算确定,要有富余量。
上吊点通过提升油缸内的锚具夹住钢铰线形成,下吊点通过安装在移动模架主梁上的转换器形成。
转换器下端通过精轧螺纹钢吊杆吊住移动模架主梁,并锚固在主梁上,上端通过P锚夹紧从提升油缸中穿下来的钢铰线,将移动模架和提升油缸连接起来,实现荷载传递。
转换器是移动模架整体落架重要的受力部件,其设计和加工必需经过严格的计算和检查。
转换器实景如图5.2.5-1。
表5.2.5-1移动模架下放吊点载荷分布表吊点 1 2 3 4 吊点载荷计算值230 230 190 190油缸额定载荷(t)200+200 200+200 200+200 200+200钢绞线数量(根)19+19 19+19 19+19 19+19钢绞线安全系数 4.30 4.30 5.20 5.20油缸储备系数 1.74 1.74 2.11 2.11[注]:钢绞线安全系数=26吨/钢绞线每根最大受力图5.2.5-1 转换器实景系统安装完成后,移动模架整体落架前的实景如图5.2.5-2。
图5.2.5-2 移动模架吊点安装完成,整体落架前实景图5.2.6 单点手动调试在提升油缸、液压泵站等设备安装完毕后,即可进行泵站和提升油缸的单点手动调试。
单点手动调试是对吊点逐个进行人工调试,包含以下操作:1)给液压泵站供电,检查正反转;2)启动液压泵站,检查锚具压力和系统压力;3)手动控制提升油缸的空缸伸缩缸动作;4)检查截止阀动作是否正常;5)检查液压泵站和提升油缸的泄漏等是否正常;6)调试比例阀控制伸缩缸速度;7)调定安全阀等的压力设定;8)检查压力表读数是否正常;9)完成其它相关调试工作。
5.2.7 单点加载试验单点手动调试合格后,对吊点逐个进行单点加载试验,需要测量人员配合,包含以下操作:1)从理论计算负载的20%、40%、60%、80%、100%、115%进行加载试验;2)加载的时间和间隔期按照方案要求进行;3)加载试验完成后,对该点进行卸载。
5.2.8 系统联合调试在各点手动调试和计算机控制系统安装完成后,进行系统联合调试,包含以下操作:1)通过计算机手动控制各点锚具油缸动作,检查锚具传感器是否正常;2)通过计算机手动控制各点伸缸、缩缸动作,检查油缸行程传感器是否正常;3)检查截止阀工作是否正常;4)检查压力传感器是否正常;5)检查比例阀输出设定是否正常;6)检查控制系统工作是否正常。
5.2.9 试提升在系统联调和其它结构检查结束并且正常的情况下,进行试提升,包含以下操作:1)检查各种备件、通讯工具是否完备;2)检查设备和传感器等是否正常;3)按照理论负载的20%、40%、60%、80%、100%对各点进行逐级加载;4)检查结构的脱架情况;5)在确定结构完全脱架的情况下,将结构提升20厘米左右;6)在试提升过程中和试提升完成后,需对结构等进行观察。
5.2.9 正式下放经过试提升观察,结构和吊点无任何异常后,进入正式整体落架阶段,如图5.2.9-1。
图5.2.9-1 移动模架整体落架现场实景图1)检查各种备件、通讯工具是否完备;2)检查设备和传感器等是否正常;3)提升移动模架,使设备置于悬吊状态,将移动模架的托架从墩身预留孔中拔出,解除托架对拉螺杆,解除移动模架整体落架的一切约束;4)进入计算机自动控制程序,进行正式下放;5)在正式下放过程中,记录各点压力和高度;6)各点进行设备监控,如有异常,应及时反映情况或紧急停机;7)对压力、高差等数据进行比较,若有数据偏差,应认真分析;8)根据分析的结果,决策下一步操作。
5.2.10 设备到达平台在计算机自动控制程序的控制下,液压系统采用间歇式的作业方式,以4m/h的速度匀速下降。
在降到吊机和人工可操作的高度时,先拆除移动模架托架的下半部分,保留上节导轨,然后匀速降到支撑塔架上,即可进行设备的拆卸。
拆卸时先拆除底模及横梁系统,两根独立的主梁分别在各自的支撑塔架上边纵向移动边分段拆除。
移动模架整体落架至平台如图5.2.10-1。
图5.2.10-1 移动模架整体落架至平台6.材料与设备6.1 移动模架整体落架主要耗材及周转材料主要材料有以下几项,其数量根据方案及设计确定:钢铰线,用于承担移动模架整体落架的吊绳,数量为144根,长度根据现场计算定。
门式支架,用于搭设钢铰线梳理支架。
H型钢,用于搭设提升油缸支承支架和底座。
钢管、型钢、钢板,用于搭设移动模架拆卸平台,其型号根据平台设计确定。
6.2 移动模架整体落架主要设备及配件见表6.2-1。
表6.2-1 移动模架整体落架主要设备配件表7.质量控制1)钢铰线进场后要进行抽检,钢铰线的下料长度符合设计要求,安装完成后要求所有钢铰线松紧程度基本一致。
所有的夹具要经过检查合格。
2)临时钢结构的设计要经过验算,焊接和安装要满足质量要求,转换器焊缝要经过探伤检测。