史上分析最透彻的腐蚀破坏事故(5-6)
历史上五月发生的危险化学品事故
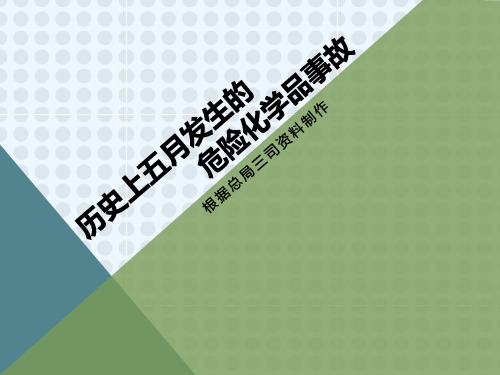
历史上5月发生的危险化学品事故
浙江衢州市合成氨厂“5•15”压缩机爆炸事故
1981年5月15日,浙江省衢州化学工业公司合成氨厂发生压 缩机爆炸事故,造成3人死亡、3人重伤、10人轻伤,经济 损失约400万元。 事故的直接原因是: 该厂油气化车间2号油气化炉停车检修完毕后,进行最后一次 充氮,准备抽油时,当班操作人员忘记关掉气化炉上的两 个充氮阀门,造成氧气倒入氮气总管。当合成车间工段打 开配氮阀后,氧气进入压缩机,导致系统爆炸。
历史上5月发生的危险化学品事故
重庆市长寿化工总厂污水池“5•4”爆炸事故
1987年5月4日,重庆市长寿化工总厂污水处理车间发生爆炸 事故,造成12人死亡,6人受伤,经济损失151.22万元。 事故的直接原因是: 在未办理动火作业手续的情况下,电话请示公司副经理得到 口头许可,即开始对污水处理分流槽管线法兰实施焊接作 业。焊接火花引燃了分流槽内的易燃物,引起大火,继而 引燃了污水处理池内的乙烯基乙炔、乙醛、乙炔等易燃气 体,发生爆炸。
历史上的 危险化学品事故
危化事故—— 污水处理 普通场所 容易忽视
历史上5月发生的危险化学品事故
案例▕史上分析最透彻的腐蚀破坏事故(7

案例▕史上分析最透彻的腐蚀破坏事故(7每期编制两篇真实腐蚀案例,希望大家喜欢。
点击页面底部“阅读原文”可查看腐蚀案例5-6事例7某厂生产氯化锌的方法是,将镀锌厂回收的锌和其它来源的锌用盐酸溶解,然后用化学药剂处理,再在浓缩槽中加热蒸发。
浓缩槽中使用的镍加热管发生孔蚀,寿命很短。
于是用锆制加热管在浓缩槽中进行了一个月试验,没有发现腐蚀问题,但锆制加热管仅使用了6个月就发生腐蚀破坏。
经过调查找出了原因:有的镀锌厂镀锌工艺配方中使用了氟化物,因此回收的锌中含氟化物。
评述锆是一种难熔金属,虽然锆的标准点位很负,化学性质活泼,但由于表面易生成致密的保护性氧化膜,所以具有优良的耐蚀性。
锆对碱和许多酸(包括氢碘酸和氢溴酸)耐蚀性很好,但锆不耐王水和氢氟酸的腐蚀,因为它们能使锆生成;络离子而溶解。
尽管锆对浓度低于35%、温度低于100℃的盐酸是耐蚀的,在本事例中耐蚀性应无问题,但由于回收锌中夹带氟化物,因而很快发生腐蚀破坏。
以上三个事例的共同点是:实际生产环境中含有某种杂质,对设备材料造成了严重的腐蚀问题。
而作为选材依据的腐蚀数据资料、使用经验、实验结果并没有包含这种环境细节。
相同的生产过程,相同的设备材质,往往腐蚀情况出现较大差异,一个重要原因就是杂质。
这方面的事例还有很多,如:1.有的硫酸生产厂为用户提供废酸处理设备,因为用户难以使用不影响环境的方法处理废酸。
处理工艺是:将被有机物污染的废酸焚烧,热气体通过废热锅炉回收热量。
有一个这样的厂一次发现废热锅炉钢管寿命突然很短。
检查结果表明,腐蚀是由于含磷酸盐和铅量很高的熔渣造成的,原来一个用户的废酸中含有这些组分。
2.某厂一台蒙乃尔合金制的石油化工装置萃取设备用于处理50%~65%硫酸和乙醇(温度29~38℃),热交换器管子预期寿命5年,但在5周就出乎预料发生破坏,更换的管子不到3周又发生破坏;腐蚀部位主要是焊缝。
溶液中所含的铜离子很高,难以用合金的简单溶解来解释。
案例▕史上分析最透彻的腐蚀破坏事故

小化04-04原文事例1-20某石油化工厂常减压车间减粘事故线在109号阀后管道穿孔,引起火灾,使常压工段停工。
破口在管线底部距法兰盘50mm处,破口呈三角形,高85mm,宽72mm。
事故线介质为减压蒸馏塔底渣油,温度400℃,含硫量1.2%,流速0.3m/s。
事故线材质为20号钢,原厚度7mm,使用2年被蚀穿,最大腐蚀率达3.5mm/a。
评述与上一事例一样,渣油系统的腐蚀主要为高温硫腐蚀。
该厂渣油硫含量高(1.2%),温度达400℃,H2S和H2S分解生成的活性S反应生成无保护性的FeS,所以对碳钢腐蚀十分严重。
另外,流速和流动状态对高温硫腐蚀也有很大影响。
事故线渣油流速为0.3m/s,平常操作中109阀开度不足二分之一,在阀后一定距离流体界面最小,流速最大(约为0.8m/s),渣油直接冲击管线底部,故对该处管线产生严重磨损腐蚀,造成穿孔。
所以,应选择更耐腐蚀和磨损的材料。
比如管道可选低合金钢Cr5Mo,弯头和阀后管道可选1Cr18Ni8不锈钢。
介质流速也是一个很重要的环境因素。
但流速对材料腐蚀的影响又是很复杂的。
不过在很多情况下流速增大将使材料腐蚀率增加。
因为当流速增大时腐蚀剂的供应会更充足,使浓度极化降低;腐蚀产物会更容易流走,难以对被腐蚀金属表面提供保护。
特别当介质流速很高时,会造成一种破坏性很大的局部腐蚀形态:磨损腐蚀。
这是由于高速流动介质产生的机械冲刷和腐蚀的联合作用所造成的破坏。
流体的冲刷使材料表面保护膜被破坏,露出新鲜金属表面,遭受介质的腐蚀;腐蚀造成表面不平,流动紊乱,形成涡流和涡旋,进一步增大了流体的冲刷。
这种相互促进的联合作用导致设备壁厚严重减薄,最终穿孔。
流动系统中的设备,如管道、管件、阀门、搅拌器、泵、叶轮、汽轮机叶片等,磨损腐蚀是一种常见的腐蚀破坏原因。
前面两个事例都属于高速高温硫化物环境中的磨损腐蚀破坏。
对这种环境中工作的设备,在选材时不仅要考虑到介质的腐蚀性,还要考虑介质流速和流动状态与腐蚀的联合作用。
酸碱灼伤事故案例分析

精选2021版课件
9
一般酸碱灼伤图
精选2021版课件
10
精选2021版课件
11
精选2021版课件
12
尊章守纪,珍爱生命
精选2021版课件
13
谢谢您的观看!
精选2021版课件
14
精选2021版课件
15
精选2021版课件
16
• 2)各级领导和职能部门应在各自的工作范围内,对实现安全生产 负责;
• 3)加强全厂干部、工人的安全思想和安全技术教育,使广大职工 自觉遵章守纪的现象。
精选2021版课件
5
一起强碱溶液灼伤事故的分析
• 一起强碱溶液灼伤事故的分析 2000年12月26日,黑龙江 • 省某化工企业发生一起热碱液喷出伤人事故,造成1名检修 • 人员面部灼伤
• 2. 对引发此次事故的碱液管线取消伴热,增加了氮气吹扫管线,可以在配 液完成后半部将管线内的残存的碱液吹至临时贮罐,既防止了工艺上的冻堵现 象,又有效地避免了类似作业过程事故的再次发生。
• 3. 开展“我为工厂献一策”活动,以生产岗位工人为基础,工程技术人员 做指导,对工艺上存在的设计不合理,易形成隐患的部位彻底进行技术改造, 对有功人员给予适当的奖励,收效很好。
压力增大,当解开阀门填料压盖时,蒸汽夹带碱液喷出造成检修工李某面部灼伤,是事故发生 的直接原因 • 检修工李某在作业过程中未按规定佩带防护用具,违章作业也是造成此次事故的直接原因。 • 检修工李某和监护人王某安全意识淡簿,工厂安全管理存在不足是造成此次事故的间接原因。 • 工艺设计不合理是造成本次事故的主要原因。 • 另外,监护人王某未尽到监护职责,是造成此次事故的次要原因。
伤。
精选2021版课件
特种设备事故案例(举例)

重庆天原化工总厂压力容器爆炸氯气泄漏事故2004年4月15日21:00,重庆天原化工总厂氯氢分厂1号氯冷凝器列管腐蚀穿孔,造成含铵的盐水泄漏到液氯系统,生成大量三氯化氮。
4月16日凌晨发生排污罐爆炸,1:33全厂停车;2:15左右,排完盐水4h后的1号盐水泵在停止状态下发生粉碎性爆炸。
16日17:57,在抢险过程中,突然听到连续2声爆响,经查是5号、6号液氯储罐内的三氯化氮发生了爆炸。
爆炸使5号、6号液氯储罐罐体破裂解体,并将地面炸出1个长9m、宽4m、深2m的坑。
以坑为中心半径200m范围内的地面与建筑物上散落着大量爆炸碎片。
此次事故造成9人死亡,3人受伤,15万名群众疏散,直接经济损失277万元。
事故分析经调查分析确认,事故爆炸直接因素的关系链是:氯冷凝器列管腐蚀穿孔→盐水泄漏进入液氯系统→氯气与盐水中的铵反应生成三氯化氮→三氯化氮富集达到爆炸浓度→启动事故氯处理装置因震动引爆三氯化氮。
事故直接原因:1、设备腐蚀穿孔导致盐水泄漏,是造成三氯化氮形成和富集的原因。
根据重庆大学的技术鉴定和专家分析,造成氯气泄漏和含铵盐水流失是1号氯冷凝器列管腐蚀穿孔。
列管腐蚀穿孔的主要原因是:1)氯气、液氯、氯化钙冷却盐水对氯气冷凝器存在的腐蚀作用;2)列管内氯气中的水分对碳钢的腐蚀;3)列管外盐水中由于离子电位差对管材产生电化学腐蚀和点腐蚀;4)列管和管板焊接处的应力腐蚀;5)使用时间较长,并未进行耐压试验,对腐蚀现象未能在明显腐蚀和穿孔前及时发现。
1992年和2004年1月该液氯冷冻岗位的氨蒸发系统曾发生过泄漏,造成氨进入盐水,生成了含高浓度铵的氯化钙盐水。
1号氯冷凝器列管腐蚀穿孔,导致含高浓度铵的氯化钙盐水进入液氯系统,生成并大量富集具有极具危险的三氯化氮,演变成16日的三氯化氮大爆炸。
2、三氯化氮富集达到爆炸浓度和启动事故氯处理装置造成振动引起三氯化氮爆炸。
调查证实,厂方现场处理人员未经指挥部同意,为加快氯气处理速度,在对三氯化氮富集爆炸危险性认识不足情况下,急于求成,判断失误,凭借以前操作处理经验,自行启动了事故氯处理装置,对4号、5号、6号液氯储罐(计量槽)及1号、2号、3号气化器进行抽吸处理。
腐蚀品事故案例分系

第八类腐蚀品1、硝酸惹祸的两起事故[案情介绍] 案例一1973年11月3日,欧罗巴帕美国航空公司的一架喷气式货运飞机自纽约机场起飞。
数分钟后,机场的地面指挥系统就接到飞机机长的报告:机上发生异常状况,机舱内着火。
尽管采取了自救措施仍未见效果。
35分钟后,飞机坠毁于波士顿机场,三名机组人员全部死亡。
经有关部门对事故进行深入调查发现:在所装的货物中有一批硝酸。
其包装不符合运输要求,是桶装容器外套木板箱,中间用木屑作衬垫。
货物在装上飞机时,作业人员没有注意箱顶上“该面朝上”的指示标志,而是随意堆放。
由于箱内货物倒置,硝酸自桶中渗漏出来,与木屑相混,自燃而引起火灾。
案例二1989年2月6日下午4时20分,从西安开往济南的207次列车行至三门峡铁门路段时,8号车厢尽头的行李架上突然冒出一股呛人的烟雾,旅客纷纷夺路而逃。
车上秩序顿时大乱。
这时列车员与乘警不顾个人安危,冲上去抓起那只冒烟的手提包,打开车窗扔到窗外,接着又拉下紧急刹车的制动阀。
经现场展开的调查,查实了手提包的主人是河南省灵宝县程村乡的一个叫朱红军的农民。
他携带了一瓶硝酸,逃过车站的检查后自以为没事了,没想到手提包在行李架上倾倒,硝酸自瓶口渗出,险些酿成大祸。
就是这样,奋不顾身扔包的女列车员的手背已被多次灼伤,身上的衣服也被腐蚀后发脆、变色。
这个肇事者当即受到治安拘留的处理。
[事故原因分析] 硝酸,联合国编号为2031,属第八类·腐蚀品,是具有严重危险性的物品。
硝酸透明、无色,通常因溶有二氧化氮而呈红棕色。
有独特的窒息性气体。
硝酸的化学性能相当活泼,具有极强氧化性,几乎可以与一切金属、非金属起反应。
硝酸中溶有的二氧化氮越多,其氧化能力越强,腐蚀性就越大。
硝酸在发生腐蚀反应时一般总会生成有毒气体一氧化氮或二氧化氮,从而对人体生成危害。
硝酸的氧化能力能引起木材和其他纤维素物品燃烧。
一般常见的有机物如松节油、醋酸、丙酮、乙醇等与浓硝酸相混即发生爆炸。
切尔诺贝利核污染等级

切尔诺贝利核污染等级
切尔诺贝利核事故发生后,国际原子能机构(IAEA)制定了
国际核事故事件分级,该分级系统称为国际核事件分级(INES)。
根据INES,核事故分为7个等级:从最轻微的一级到最严重
的七级。
下面是每个等级的描述:
1级 - 异常事件:对于核安全运行或核材料安全有一些异常情况,但一般不会导致放射性物质泄漏。
2级- 装置事故:超出了正常操作参数的设备故障或人为失误,导致一定程度的放射性物质泄漏。
3级 - 严重装置事故:设备或防护系统的严重失效,导致严重
的放射性物质泄漏风险,但辐射风险仍限制在事故现场。
4级 - 严重核事件:对工作人员和公众健康产生风险的放射性
物质泄漏。
危及事故现场的辐射范围扩大。
5级 - 严重核事故:大规模放射性物质泄漏,需要采取进一步
保护措施以减小辐射的影响。
危及事故现场外的人员和环境。
6级 - 严重核事故:大规模放射性物质泄漏,对大范围区域造
成严重辐射影响。
可能需要疏散周围地区居民。
7级 - 严重核事故:大规模放射性物质泄漏,对全球范围造成
严重影响。
切尔诺贝利核事故被评定为INES的最高级别七级。
切尔诺贝利核事故是迄今为止唯一一个被评定为七级的核事故,被认为是人类历史上最严重的核灾难之一。
具体腐蚀事例
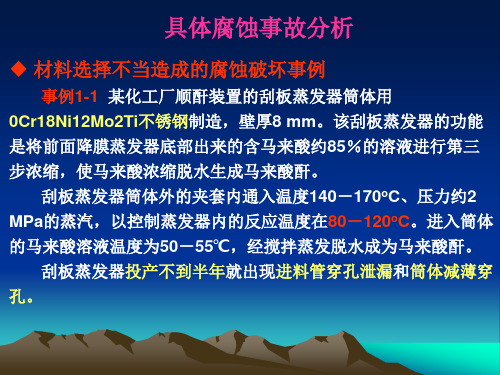
材料选择不当造成的腐蚀破坏事例
事例1-1 某化工厂顺酐装置的刮板蒸发器筒体用 0Cr18Ni12Mo2Ti不锈钢制造,壁厚8 mm。该刮板蒸发器的功能 是将前面降膜蒸发器底部出来的含马来酸约85%的溶液进行第三 步浓缩,使马来酸浓缩脱水生成马来酸酐。 刮板蒸发器筒体外的夹套内通入温度140-170oC、压力约2 MPa的蒸汽,以控制蒸发器内的反应温度在80-120oC。进入筒体 的马来酸溶液温度为50-55℃,经搅拌蒸发脱水成为马来酸酐。 刮板蒸发器投产不到半年就出现进料管穿孔泄漏和筒体减薄穿 孔。
事例1—7 某厂输送35%硫酸的泵,原来的材质为20号 合金。在20号合金泵损坏后,改用哈氏合金B。这是因为人 们都知道哈氏合金B对中等浓度硫酸的耐蚀性很好。但哈氏合 金B泵只用两周就发生腐蚀破坏。 腐蚀原因是管路中有一个喷嘴。 评述 腐蚀图中的硫酸是指“纯硫酸”,即硫酸中不含 其他杂质。如果硫酸中含有氧化性物质,如溶解氧、硝酸等, 哈氏合金B的腐蚀率将大大增加。 这是因为哈氏合金B的主要成分是镍(68%)、钼(28%), 另有少量铁(5%)、钒(1%),不含对氧化性介质耐蚀性好的合 金元素铬,所以哈氏合金B只是在非氧化性酸中表现出优良的 耐蚀性,比如在不含溶解氧的纯盐酸中,在整个浓度和温度 范围内哈氏合金B都是耐蚀的。
事例1—2 某厂卤水蒸发器一效加热室列管使用钛合金制
造,一效加热室管间通入温度为127-147oC的蒸汽,使管内
卤水加热到115-135oC。管内卤水含氯化钠280 g/L左右, 评述 钛在大气、海水和天然水中都具有优异的耐蚀性,
pH 5.5—6.5。投入运行仅10个月,就有几十根钛管破裂穿孔。 这是因为钛的钝化能力很强。钛可以用于常温下的稀盐酸(5
但是,钛在无水的氧化性介质中则是危险的,因为
- 1、下载文档前请自行甄别文档内容的完整性,平台不提供额外的编辑、内容补充、找答案等附加服务。
- 2、"仅部分预览"的文档,不可在线预览部分如存在完整性等问题,可反馈申请退款(可完整预览的文档不适用该条件!)。
- 3、如文档侵犯您的权益,请联系客服反馈,我们会尽快为您处理(人工客服工作时间:9:00-18:30)。
史上分析最透彻的腐蚀破坏事故(5-6)
事例5
一个碳钢容器装浓的乙二醇脚料,温度150℃。
脚料中含
0.2%NaOH。
使用不久,碳钢容器发生严重的全面腐蚀,器壁减薄。
评述
碳钢在NaOH溶液中的腐蚀与碱浓度和温度有很大关系。
在常温稀碱溶液中,碳钢腐蚀速度很小,属于耐蚀材料,这是因为表面生成了致密的保护膜。
因此碳钢是处理常温稀碱溶液的常用结构材料。
当NaOH浓度大于30%,表面膜的保护性能降低,腐蚀速度增大。
当NaOH 浓度大于50%,碳钢发生强烈腐蚀。
随温度升高,这一过程变得更显著。
碱浓缩罐中的腐蚀和锅炉碱腐蚀就是这类实例。
一般说来,碳钢材料可用于处理87℃以下、浓度小于50%的NaOH溶液。
当材料中存在应力,碳钢还会发生应力腐蚀破裂(关于应力腐蚀破裂,在以后的事例中还要介绍)。
本事例中虽然温度较高,但脚料中NaOH含量很低。
所以在使用中比较注意碳钢是否会发生应力腐蚀破裂,这当然是无可非议的。
但忽略了碳钢的全面腐蚀问题,结果造成了严重破坏,原因是没有考虑到设备的具体情况。
这里虽然相对于整个脚料NaOH浓度很低,但相对于混合物中的水,NaOH的浓度就大得多,即这种有机化合物脚料中的水时NaOH浓溶液;加之温度较高,故发生了很高的全面腐蚀速度。
我们反复强调,在为设备选择制造材料时,首先要把设备将服役的环境条件搞清楚,所谓环境条件,当然是最主要的是介质的种类、浓度和温度。
腐蚀数据手册和图标一般也是按照这三个条件来组织和表达数据的。
但是,对于介质的浓度,除了应注意主体浓度,还应注意介质浓度的不均匀,比如局部区域介质因浓缩而比主体浓度高很多。
本事例就是这种情况,因此这里的选材时错误的,考虑到NaOH 局部浓度,温度亦较高,应选用更耐蚀的材料,如304型不锈钢。
事例6
某厂输送35%硫酸的泵,原来的材质为20号合金。
在20号合金泵损坏后,改用哈氏合金B。
这是因为人们都知道哈氏合金B对中等浓度硫酸的耐蚀性很好。
但哈氏合金B泵只用两周就发生腐蚀破坏。
腐蚀原因是管路中有一个喷嘴。
评述
前面已指出,可以用“腐蚀图”来考察金属材料在某种介质中的腐蚀行为。
20号合金在硫酸中有很好的耐蚀性能,铸材Durimet20适合制造泵和阀门;在本事例中没有说明20号合金泵为什么发生损坏,但比较20号合金和哈氏合金B在硫酸中的腐蚀图,可知在中等浓度硫酸溶液中,哈氏合金B在腐蚀速度低于20号合金。
图1-4是哈氏合金B在硫酸中的腐蚀图。
从图1-4中看出,在中等浓度硫酸范
围内,直到沸点,哈氏合金B的腐蚀率都是很低的,即哈氏合金B是能在中等浓度硫酸中使用的耐蚀金属材料。
但是,图1-4中的硫酸是指“纯硫酸”,即硫酸中不含其他杂质。
如果硫酸中含有氧化性物质,如溶解氧、硝酸等,哈氏合金B的腐蚀率将大大增加。
这是因为哈氏合金B的主要成分是镍(68%)、钼(28%),另有少量铁(5%)、钒(1%),不含对氧化性介质耐蚀性好的合金元素铬,所以哈氏合金B知识在非氧化性酸中表现出优良的耐蚀性,比如在不含溶解氧的纯盐酸中,在整个浓度和温度范围内哈氏合金B都是耐蚀的。
实际考查一下本事例中所用的泵,原来硫酸是经过了一个洗涤喷嘴后才进入泵,在经过喷嘴时吸入了空气。
因此泵送的硫酸中含有饱
和的空气,这就使哈氏合金B泵的腐蚀性为和不含空气的“纯硫酸”中该合金的腐蚀性为有很大差别,而这一点在选材时被忽视了。
对于这种含有空气的硫酸,应选用哈氏合金C。
哈氏合金C含有18%的铬,提高了对氧化性介质的耐蚀性,使它对含氧化剂的酸中耐蚀性由于哈氏合金B。
这是微量成分影响腐蚀的典型例子。