电炉冶炼不锈钢工艺最优化
不锈钢电炉冶炼工艺 -回复

不锈钢电炉冶炼工艺-回复不锈钢电炉冶炼工艺是一种常用于生产不锈钢的工艺方法。
通过电炉加热、熔炼和冷却等连续工艺步骤,将原材料(主要是铁合金和废钢)转化为高质量的不锈钢材料。
本文将详细介绍不锈钢电炉冶炼工艺的每一个步骤。
第一步:原材料准备在不锈钢电炉冶炼过程中,主要原材料是铁合金和废钢。
铁合金包括铁铬合金、铁镍合金和铁钒合金等,废钢包括废旧钢铁和废钢产品。
在准备原材料时,需要根据不同的合金配方和产品要求,控制好原材料的化学成分和比例。
第二步:电炉熔炼将准备好的原材料倒入电炉中进行熔炼。
电炉是一种利用电能将原材料加热到高温并融化的设备。
电炉通常分为直接电炉和感应电炉两种类型。
在熔炼过程中,电炉的温度和炉内气氛需要进行严格的控制,以确保合金成分和质量的稳定。
第三步:渣的处理在不锈钢电炉熔炼过程中,废钢中的杂质和氧化物将形成渣。
为了提高合金的纯度,需要对渣进行处理。
常用的渣处理方法有贫化处理、锻渣法和气体还原法等。
这些方法能够将渣中的有害元素和杂质去除,提高合金的品质。
第四步:合金成分调整根据不锈钢产品的要求,通过添加合适的合金元素和合金块,对合金的成分进行调整。
这一步骤需要根据不锈钢的合金配方和产品要求,控制好每一种元素的添加比例,以确保最终产品的质量。
第五步:脱氧和冶炼终点控制在不锈钢电炉冶炼过程中,为了降低合金中的氧含量,需要进行脱氧处理。
通常使用硅、铝、锰等作为脱氧剂。
同时,在冶炼过程的后期,需要进行冶炼终点控制,即控制合金的温度和成分,以满足产品的要求。
第六步:浇注和冷却经过以上几个步骤,不锈钢合金已经获得理想的成分和温度。
接下来,将合金倒入浇注工具中,进行模具浇注。
浇注工艺的控制直接影响着产品的质量和形状。
最后,待不锈钢合金冷却后,进行必要的热处理和实际应用。
热处理可通过控制温度和冷却速率来调整材料的组织结构和性能,使其达到理想的机械性能和耐腐蚀性能。
不锈钢电炉冶炼工艺虽然复杂,但凭借其高效、灵活和可控的优点,被广泛应用于不锈钢制造行业。
不锈钢冶炼工艺流程的分析比较

不锈钢冶炼工艺流程的分析比较不锈钢是一种具有高耐腐蚀性能的合金钢,常用于制造压力容器、化工设备、食品加工设备等。
不锈钢冶炼工艺流程主要包括原料配料、熔炼、铸造及热处理等环节。
在不锈钢冶炼过程中,选择合适的工艺流程能够提高不锈钢的品质和性能。
不锈钢的冶炼主要有两种工艺流程,即电弧炉冶炼和炉外法冶炼。
下面将对这两种工艺流程进行分析比较。
1.电弧炉冶炼工艺流程:(1)原料配料:将铁合金、废钢、镍合金等原料按照配方进行重量称量,然后均匀混合。
(2)熔炼:将混合好的原料装入电弧炉中,通过电弧的高温作用使原料快速熔化,形成不锈钢熔体。
(3)合金调整:根据熔体的成分及性质要求,添加合适的脱氧剂、脱硫剂和合金元素,对熔体进行调整。
(4)出钢:将熔体倒入包含板凭、保温层和冷却层的连铸机中,经过连铸机的坯料成型,冷却后形成连铸坯。
(5)热处理:通过热处理工艺,通过调整材料的组织和结构,提高材料的性能和性质。
(6)钢材加工:将连铸坯进行轧制、拉拔、冷轧等加工工艺,形成不锈钢板、棒、线等产品。
2.炉外法冶炼工艺流程:(1)原料预处理:将铁合金、废钢等原料进行破碎、球团化等预处理工艺,便于熔炼过程中原料的熔融。
(2)熔炼:将经过预处理的原料装入高炉或转炉中,通过高温燃烧使原料迅速熔融,形成不锈钢熔体。
(3)合金调整:根据不锈钢的成分要求,对熔体进行合金化调整,添加合适的合金元素,提高不锈钢的性能。
(4)出钢:将熔体倒入连铸机中,经过连铸机的坯料成型,冷却后形成连铸坯。
(5)热处理:同电弧炉冶炼工艺流程相同,通过热处理工艺提高材料性能。
(6)钢材加工:同电弧炉冶炼工艺流程相同,通过钢材加工工艺形成不锈钢产品。
电弧炉冶炼与炉外法冶炼相比(1)电弧炉冶炼的原料利用率高,废钢的回收利用效果好,有利于资源的节约和环境的保护。
(2)电弧炉冶炼的熔炼过程稳定,熔化温度高,能够更好地控制不锈钢的成分和组织,提高产品的品质和性能。
(3)电弧炉冶炼对原料的要求宽松,适用于较为复杂的原料混合物,避免了炉外法冶炼中对原料预处理的复杂性。
电炉炼钢高效洁净低成本生产技术进展
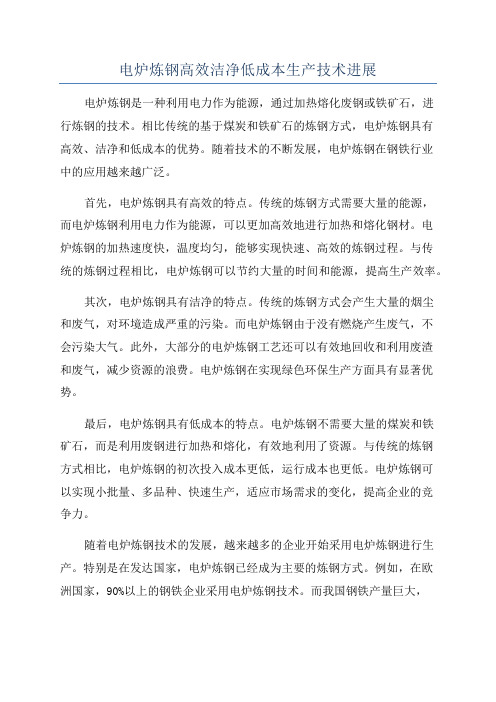
电炉炼钢高效洁净低成本生产技术进展电炉炼钢是一种利用电力作为能源,通过加热熔化废钢或铁矿石,进行炼钢的技术。
相比传统的基于煤炭和铁矿石的炼钢方式,电炉炼钢具有高效、洁净和低成本的优势。
随着技术的不断发展,电炉炼钢在钢铁行业中的应用越来越广泛。
首先,电炉炼钢具有高效的特点。
传统的炼钢方式需要大量的能源,而电炉炼钢利用电力作为能源,可以更加高效地进行加热和熔化钢材。
电炉炼钢的加热速度快,温度均匀,能够实现快速、高效的炼钢过程。
与传统的炼钢过程相比,电炉炼钢可以节约大量的时间和能源,提高生产效率。
其次,电炉炼钢具有洁净的特点。
传统的炼钢方式会产生大量的烟尘和废气,对环境造成严重的污染。
而电炉炼钢由于没有燃烧产生废气,不会污染大气。
此外,大部分的电炉炼钢工艺还可以有效地回收和利用废渣和废气,减少资源的浪费。
电炉炼钢在实现绿色环保生产方面具有显著优势。
最后,电炉炼钢具有低成本的特点。
电炉炼钢不需要大量的煤炭和铁矿石,而是利用废钢进行加热和熔化,有效地利用了资源。
与传统的炼钢方式相比,电炉炼钢的初次投入成本更低,运行成本也更低。
电炉炼钢可以实现小批量、多品种、快速生产,适应市场需求的变化,提高企业的竞争力。
随着电炉炼钢技术的发展,越来越多的企业开始采用电炉炼钢进行生产。
特别是在发达国家,电炉炼钢已经成为主要的炼钢方式。
例如,在欧洲国家,90%以上的钢铁企业采用电炉炼钢技术。
而我国钢铁产量巨大,但电炉炼钢的应用还相对较少。
但是,随着环保意识的增强和政策的推动,电炉炼钢在我国的应用前景广阔。
未来,电炉炼钢技术还有很大的提升空间。
一方面,可以进一步提高电炉炼钢的自动化水平,减少人工干预,提高生产效率。
另一方面,可以研发出更高效的电炉炼钢设备和工艺,提高熔化效率,降低能耗。
此外,还可以进一步提高电炉炼钢生产的自动化水平,实现智能化生产,提高产品质量和生产效率。
综上所述,电炉炼钢是一种高效、洁净和低成本的炼钢技术。
随着环保意识的增强和技术的不断发展,电炉炼钢在钢铁行业中的应用前景广阔。
电炉双联法加VOD法冶炼不锈钢

电炉和精炼炉VOD双联法冶炼不锈钢工艺实践摘要根据我厂品种特点,总结了多年来不锈钢生产的经验,结合现场设备实际特点,摸索出了一套新的生产不锈钢的工艺方法,并在核电泵壳用钢Z3CN20-09M的冶炼中一次性试验成功。
本文主要阐述了Z3CN20-09M 钢的试验过程,并详细总结讨论了这种新工艺同传统VOD生产不锈钢对比的各种优缺点。
关键词不锈钢双联法VOD 工艺实践1.前言我们以前冶炼超低碳不锈钢通常采用两种工艺方法:一种是电炉提供初炼钢水,电炉调整镍钼成分,在精炼炉调整铬、锰、硅,然后倒入另一个精炼包进行VOD操作;另一种是在电炉冶炼初炼钢水时除调整镍钼外,部分调整铬、锰、硅合金,在精炼炉继续调整铬成分,最后倒入另一个精炼包进行VOD操作。
以上两种方法存在工艺烦琐,冶炼时间长等缺点。
在冶炼Z3CN20-09M钢上我们进行了一次重大工艺改进,就是其中一炉初炼钢水全部熔化合金,合兑后简单微调成份即进行VOD操作。
2.炼钢设备我公司新改造的VOD设备,为从原130T VD钢包精炼炉的基础上自行设计改造的。
在原VD 炉的真空盖上配置有拉瓦尔管式水冷氧枪,配有炉气温度显示仪及微氧含量分析仪,为VOD终点碳控制提供保证。
在真空盖上还装有电子视频监视系统,实时观察炉内反应进行状况及喷溅情况。
安装有两个500Kg真空加料仓,可在VOD结束后加造渣材料及脱氧合金。
真空抽气设备为500Kg 蒸汽喷射泵,分为四级,真空度可达到133Pa以下。
提供初练钢水的电弧炉有40TEBT和30T的EAF电弧炉。
3.冶炼工艺要点试验钢种Z3CN20-09M,钢水冶炼量70吨。
成品成份及初炼钢水要求如表1所示:3.1 工艺流程用40T的偏心炉底电炉为VOD精炼炉提供不调整任何合金元素的纯低磷氧化钢水,同时用30T电炉专门熔化合金。
工艺流程如图1所示。
图1 Z3CN20-09M钢试验工艺流程图为了尽量回收渣中的铬,30T电炉的合金直接带渣翻入LF精炼钢包。
电炉炼钢工艺优化
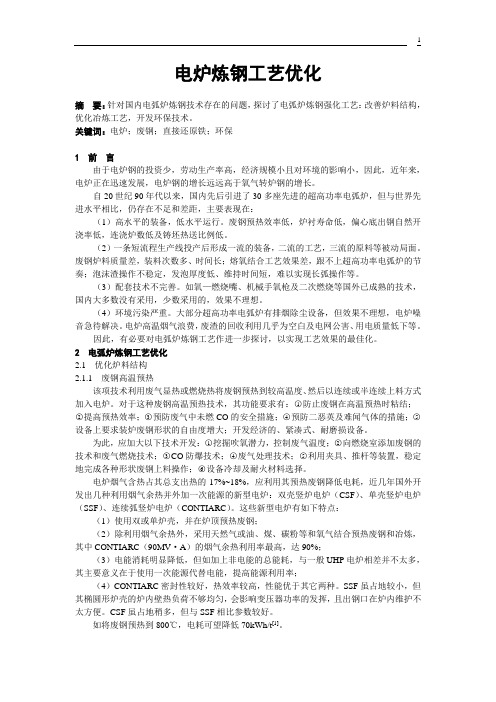
电炉炼钢工艺优化摘要:针对国内电弧炉炼钢技术存在的问题,探讨了电弧炉炼钢强化工艺:改善炉料结构,优化冶炼工艺,开发环保技术。
关键词:电炉;废钢;直接还原铁;环保1 前言由于电炉钢的投资少,劳动生产率高,经济规模小且对环境的影响小,因此,近年来,电炉正在迅速发展,电炉钢的增长远远高于氧气转炉钢的增长。
自20世纪90年代以来,国内先后引进了30多座先进的超高功率电弧炉,但与世界先进水平相比,仍存在不足和差距,主要表现在:(1)高水平的装备,低水平运行。
废钢预热效率低,炉衬寿命低,偏心底出钢自然开浇率低,连浇炉数低及铸坯热送比例低。
(2)一条短流程生产线投产后形成一流的装备,二流的工艺,三流的原料等被动局面。
废钢炉料质量差,装料次数多、时间长;熔氧结合工艺效果差,跟不上超高功率电弧炉的节奏;泡沫渣操作不稳定,发泡厚度低、维持时间短,难以实现长弧操作等。
(3)配套技术不完善。
如氧—燃烧嘴、机械手氧枪及二次燃烧等国外已成熟的技术,国内大多数没有采用,少数采用的,效果不理想。
(4)环境污染严重。
大部分超高功率电弧炉有排烟除尘设备,但效果不理想,电炉噪音急待解决。
电炉高温烟气浪费,废渣的回收利用几乎为空白及电网公害、用电质量低下等。
因此,有必要对电弧炉炼钢工艺作进一步探讨,以实现工艺效果的最佳化。
2 电弧炉炼钢工艺优化2.1 优化炉料结构2.1.1 废钢高温预热该项技术利用废气显热或燃烧热将废钢预热到较高温度、然后以连续或半连续上料方式加入电炉。
对于这种废钢高温预热技术,其功能要求有:○1防止废钢在高温预热时粘结;○2提高预热效率;○3预防废气中未燃CO的安全措施;○4预防二恶英及难闻气体的措施;○5设备上要求装炉废钢形状的自由度增大;开发经济的、紧凑式、耐磨损设备。
为此,应加大以下技术开发:○1挖掘吹氧潜力,控制废气温度;○2向燃烧室添加废钢的技术和废气燃烧技术;○3CO防爆技术;○4废气处理技术;○5利用夹具、推杆等装置,稳定地完成各种形状废钢上料操作;○6设备冷却及耐火材料选择。
电弧炉冶炼不锈钢的作用
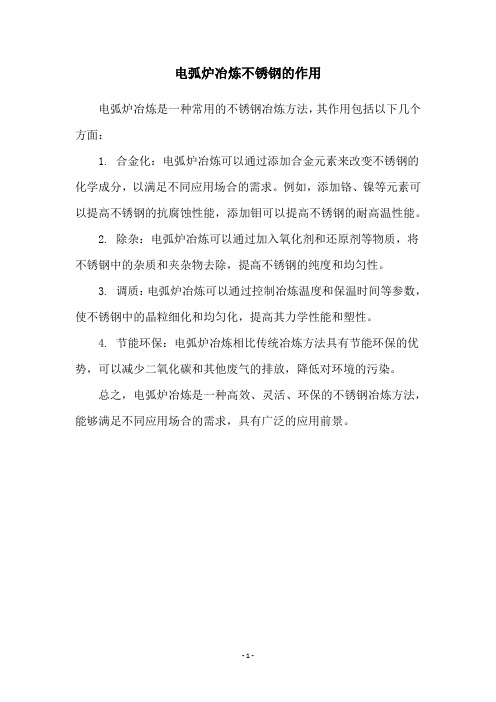
电弧炉冶炼不锈钢的作用
电弧炉冶炼是一种常用的不锈钢冶炼方法,其作用包括以下几个方面:
1. 合金化:电弧炉冶炼可以通过添加合金元素来改变不锈钢的化学成分,以满足不同应用场合的需求。
例如,添加铬、镍等元素可以提高不锈钢的抗腐蚀性能,添加钼可以提高不锈钢的耐高温性能。
2. 除杂:电弧炉冶炼可以通过加入氧化剂和还原剂等物质,将不锈钢中的杂质和夹杂物去除,提高不锈钢的纯度和均匀性。
3. 调质:电弧炉冶炼可以通过控制冶炼温度和保温时间等参数,使不锈钢中的晶粒细化和均匀化,提高其力学性能和塑性。
4. 节能环保:电弧炉冶炼相比传统冶炼方法具有节能环保的优势,可以减少二氧化碳和其他废气的排放,降低对环境的污染。
总之,电弧炉冶炼是一种高效、灵活、环保的不锈钢冶炼方法,能够满足不同应用场合的需求,具有广泛的应用前景。
- 1 -。
不锈钢的冶炼方法
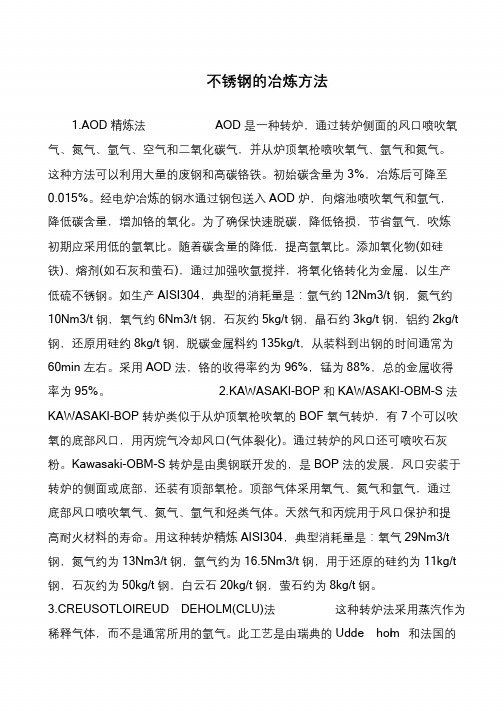
书山有路勤为径,学海无涯苦作舟不锈钢的冶炼方法1.AOD 精炼法AOD 是一种转炉,通过转炉侧面的风口喷吹氧气、氮气、氩气、空气和二氧化碳气,并从炉顶氧枪喷吹氧气、氩气和氮气。
这种方法可以利用大量的废钢和高碳铬铁。
初始碳含量为3%,冶炼后可降至0.015%。
经电炉冶炼的钢水通过钢包送入AOD 炉,向熔池喷吹氧气和氩气,降低碳含量,增加铬的氧化。
为了确保快速脱碳,降低铬损,节省氩气,吹炼初期应采用低的氩氧比。
随着碳含量的降低,提高氩氧比。
添加氧化物(如硅铁)、熔剂(如石灰和萤石),通过加强吹氩搅拌,将氧化铬转化为金属,以生产低硫不锈钢。
如生产AISI304,典型的消耗量是:氩气约12Nm3/t 钢,氮气约10Nm3/t 钢,氧气约6Nm3/t 钢,石灰约5kg/t 钢,晶石约3kg/t 钢,铝约2kg/t 钢,还原用硅约8kg/t 钢,脱碳金属料约135kg/t,从装料到出钢的时间通常为60min 左右。
采用AOD 法,铬的收得率约为96%,锰为88%,总的金属收得率为95%。
2.KAWASAKI-BOP 和KAWASAKI-OBM-S 法KAWASAKI-BOP 转炉类似于从炉顶氧枪吹氧的BOF 氧气转炉,有7 个可以吹氧的底部风口,用丙烷气冷却风口(气体裂化)。
通过转炉的风口还可喷吹石灰粉。
Kawasaki-OBM-S 转炉是由奥钢联开发的,是BOP 法的发展,风口安装于转炉的侧面或底部,还装有顶部氧枪。
顶部气体采用氧气、氮气和氩气,通过底部风口喷吹氧气、氮气、氩气和烃类气体。
天然气和丙烷用于风口保护和提高耐火材料的寿命。
用这种转炉精炼AISI304,典型消耗量是:氧气29Nm3/t 钢,氮气约为13Nm3/t 钢,氩气约为16.5Nm3/t 钢,用于还原的硅约为11kg/t 钢,石灰约为50kg/t 钢,白云石20kg/t 钢,萤石约为8kg/t 钢。
法这种转炉法采用蒸汽作为稀释气体,而不是通常所用的氩气。
电炉冶炼不锈钢工艺最优化

电炉冶炼不锈钢工艺最优化2007年,德国粗钢产量4860万t,其中31%为电炉生产。
近年来,能源和炼钢原材料价格的不断上涨,不仅引起全球的高度重视,也促进了欧洲钢铁工业界开发新的冶炼工艺以降低原材料燃料消耗和生产成本。
此外,最近几年欧洲钢铁界也致力于把直接和间接CO2排放量降至最低。
通过精确的工艺控制最大限度减少了原材料消耗,欧洲钢铁工业的生产成本有了显著降低。
同样,通过严格而准确控制脱C,也降低了原料加工过程中CO2的间接排放。
一种新的电炉炼钢工艺的出现使钢铁工业面临着新的机遇和挑战。
Deutsche Edelstahlwerke GmbH公司每年利用电炉生产不锈钢的产量较大。
为了最大限度提高喷氧时碳、硅的氧化效率,并最大限度地减少铁和铬氧化造成的经济损失和环境污染。
DEW公司(即Deutsche Edelstahlwerke GmbH)对硅、碳氧化与喷氧量的关系进行了研究。
虽然Ellingham图(氧势图)中的内容关于电炉冶炼不锈钢时元素氧化及化学反应,但由于电炉内有很多反应同时进行,而使问题变得复杂化。
而且,元素的氧化与温度、氧气分压以及钢液与炉渣的化学成分有关。
基于上述原因,以下将对各元素的复杂氧化过程进行更详细讨论。
元素氧化模拟:以冶炼工艺为基础模拟电炉喷氧期间氧化反应,且仅考虑热力学平衡条件而不考虑其它任何因素,例如不考虑传热、传质或动力学因素对模拟的影响。
此外,假设模拟时温度和元素分布均匀。
热力学模拟证实,氧喷射出现三个阶段,即早期、中期和末期。
喷氧的第一个临界点在早期阶段结束。
中间阶段保持在第一个临界点和第二个临界点之间。
硅的剧烈氧化在喷氧早期出现。
当喷氧强度达4.3kgO2/t钢时,硅氧化结束。
随后,钢液中硅维持在较低水平。
Ellingham图表明,由于硅氧化的吉布斯能(Gibbs Energy)较低,所以硅的氧化较其它元素更容易。
此外,硅的活度系数是一定值,所以随着钢液中硅活度的降低,钢液中的硅活性随之降低。
- 1、下载文档前请自行甄别文档内容的完整性,平台不提供额外的编辑、内容补充、找答案等附加服务。
- 2、"仅部分预览"的文档,不可在线预览部分如存在完整性等问题,可反馈申请退款(可完整预览的文档不适用该条件!)。
- 3、如文档侵犯您的权益,请联系客服反馈,我们会尽快为您处理(人工客服工作时间:9:00-18:30)。
电炉冶炼不锈钢工艺最优化
2007年,德国粗钢产量 4860万t,其中31%为电炉生产。
近年来,能源和炼钢原材料价格的不断上涨,不仅引起全球的高度重视,也促进了欧洲钢铁工业界开发新的冶炼工艺以降低原材料燃料消耗和生产成本。
此外,最近几年欧洲钢铁界也致力于把直接和间接CO2 排放量降至最低。
通过精确的工艺控制最大限度减少了原材料消耗,欧洲钢铁工业的生产成
本有了显著降低。
同样,通过严格而准确控制脱C,也降低了原料加工过程中CO2的间接
排放。
一种新的电炉炼钢工艺的出现使钢铁工业面临着新的机遇和挑战。
Deutsche Edelstahlwerke GmbH公司每年利用电炉生产不锈钢的产量较大。
为了最大限
度提高喷氧时碳、硅的氧化效率,并最大限度地减少铁和铬氧化造成的经济损失和环境污染。
DEW公司(即Deutsche Edelstahlwerke GmbH )对硅、碳氧化与喷氧量的关系进行了研究。
虽然Ellingham图(氧势图)中的内容关于电炉冶炼不锈钢时元素氧化及化学反应,
但由于电炉内有很多反应同时进行,而使问题变得复杂化。
而且,元素的氧化与温度、氧气
分压以及钢液与炉渣的化学成分有关。
基于上述原因,以下将对各元素的复杂氧化过程进行
更详细讨论。
元素氧化模拟:
以冶炼工艺为基础模拟电炉喷氧期间氧化反应,且仅考虑热力学平衡条件而不考虑其
它任何因素,例如不考虑传热、传质或动力学因素对模拟的影响。
此外,假设模拟时温度和
元素分布均匀。
热力学模拟证实,氧喷射出现三个阶段,即早期、中期和末期。
喷氧的第一个临界点
在早期阶段结束。
中间阶段保持在第一个临界点和第二个临界点之间。
硅的剧烈氧化在喷氧
早期出现。
当喷氧强度达 4.3kgO2/t钢时,硅氧化结束。
随后,钢液中硅维持在较低水平。
Ellingham图表明,由于硅氧化的吉布斯能( Gibbs Energy )较低,所以硅的氧化较其它元素更容易。
此外,硅的活度系数是一定值,所以随着钢液中硅活度的降低,钢液中的硅活性随
之降低。
实践证明,硅的低活度遵循亨利定律( Henry Law )。
在此情况下,喷氧中期C和Cr开始强烈氧化。
C活性随着钢液中硅浓度的降低而增
加,该结果与其它研究结果一致。
第一个临界点后,当C的氧化开始减弱时,铬将强烈氧
化。
到达第二临界点喷氧浓度达到18.1kgO2/t钢时,Cr将按指数规律氧化。
与此同时,当
C的氧化进行到第二临界点后,渣中的氧化铁含量开始增加。
该研究对硅和碳在精炼期间的强烈氧化进行了研究,表明脱碳的开始与硅强烈氧化的
结束有关。
如果硅的强烈氧化能够较早完成,那么强烈的脱碳将会开始。
因此,第一临界点
将会左移,将导致第二临界点的左移以减少氧气消耗。
这时脱碳反应将提早发生,喷氧从
6.6kgO2/t钢降至5.4kgO2/t钢,碳硅输入比例将增加到 75%。
电炉冶炼的废气分析:
为了获得炉内元素的氧化情况,DEW公司采用废气分析法(分析废气除尘系统中废
气的化学成分)以监控电炉冶炼不锈钢期间炉内元素的氧化,便于及时准确调整喷氧等工艺
操作。
选取了两个测量点即A点和B点进行测量和分析。
A点直接固定在电炉弯头,B点
固定在距弯头30m测量废气后燃烧完成的废气化学成分。
废气分析设备由水冷探针、过滤器、检测仪和信号转换器等部分组成,用于测量废气
成分、温度和流动速度。
废气成分如CO和CO2由红外线吸收光谱仪测定,氧气由顺磁机
理测定,废气温度薄膜热电偶测定。
同时将这些来自检测仪测试的废气的不同压力、温度和成分等参数进行不断地传输和记录以进行连续分析。
为此,将探针安装在除尘系统中完成二
次燃烧的B点。
依靠测得废气的不同压力,废气流动管道的横断面积,利用修正系数对废气的体积流量和质量流量进行计算。
喷氧期间元素氧化监测:
该研究利用废气和炉渣分析结果研究精炼期间元素的氧化过程。
A点废气分析证实,温度、浓度和体积流量在炉子径向分布极不均匀。
因此,只有利用 B点的废气分析结果才能准确监测元素的氧化。
此外,利用 B点的废气分析得到的 CO2含量为基础监测参数有利准确监测,因为 B点的CO含量接近于零值。
因为模拟仅仅以热力学平衡条件为基础,可见模拟结果和实测分析结果之间存在着明显的差别。
以热力学为基础的模拟结果表明,直到第一个临界点到达时仍无碳氧化。
其实,
废气分析表明,在达到第一临界点时碳的氧化虽不强烈,但早已开始。
差别是因为元素氧化
不仅取决于热力学条件,还与其它许多过程有关。
例如,与质量和热量传输、流动机理和动
力学条件等。
此外,温度和元素分布不均也造成差别,特别是精炼期氧分布不均所致。
实践证明,喷氧区的温度越高、喷氧浓度越高,碳的氧化越强烈。
喷吹区的大小取决于氧枪位置、氧气的质量流量、钢液密度及其化学成分。
然而,模拟结果与分析结果仍然存在着相似性。
例如,废气分析结果与模拟结果均指
出,碳的强烈氧化发生在喷氧中期。
废气分析证实同样存在着两个临界点。
碳开始强烈氧化是在喷氧到达第一临界点在喷氧量为 3.4kgO2/t钢之后,即相当于模拟结果的喷氧量为
4.6kgO2/t钢,硅强烈氧化末期。
第二临界点在喷氧量为10.5kgO2/t钢,与模拟结果的脱碳
速度开始降低、喷氧量为 18.1kgO2/t钢相当。
分析表明,硅的强烈氧化是在喷氧的早期阶段。
液相质量传输决定着早期喷氧阶段的
脱硅速度。
在此阶段,脱硅速度取决于每个反应位置的表面积(A),钢液密度(P),钢
液重量(W),每一个反应位置的硅传输系数( K),钢液中的硅含量( WT%)和钢液中接近于零的硅平衡含量(WT% )。
因此,强化反应条件,例如钢液良好混合,增大硅和氧之间的接触面积是判断这个
时期钢液脱硅速度的重要条件。
中期脱碳速度与喷氧量成线性关系,因为这时的脱碳速度受化学反应控制。
喷氧量
达到第二个临界点后,脱碳速度随着喷氧量的增加而降低。
这说明过剩氧量的脱碳作用很小,
这是由于碳在钢液中的浓度降到临界点以下,使碳的活性已经变得很低的缘故。
末期脱碳速度降低是由于钢液中碳含量的降低,这是脱碳动力学驱动力不足的原因。
末期,碳的质量传输控制脱碳。
脱碳速度取决于钢液中的含碳量,特殊反应位置的
质量传输系数(K)以及接近于零的平衡碳含量。
在缺碳条件下,氧气氧化铬和铁。
这时可减少
10%的喷氧量,即相当于降低氧消耗
1.5kgO2/t。
脱碳末期,可喷入氩气促使钢液内部良好混合以强化脱碳。
此外,喷入氩气还可降低钢液中的平衡碳浓度水平,提高脱碳速度。
至泌第二临界点后停止喷氧,可节约氧气的消耗,还可使铁和铬的氧化降至最低。
因为脱碳末期FeO和Cr2O3的生成变得更强烈。
通过回归分析后发现,直线截距为0.7kg/t 可知,虽然早期和中期铁的氧化不严重,但已经开始氧化。
末期开始前,由于Cr2O3回归
直线的截距较高(12.3kg/t,可见这时铬的氧化比铁氧化更强烈,计算结果也与模拟结果一致。
实践与分析指出,铬的氧化与铁略有不同。
即铁氧化表明渣中一氧化铁含量与末期
喷氧过剩量之间存在着关系。
有研究报导,钢液中铬的活性与钢液中铬的含量成非线性关系。
超过最佳铬含量,铬的活性与铬在钢液中的含量成负相关。
在第二临界点中止,喷氧不仅可防止铬和铁的进一步氧化,还可使铬被钢渣界面间
的一氧化铁氧化造成的损失减至最小,同时改善氧化铬的还原效率。
永久性的废气分析装置:
通过在电炉除尘系统中安装永久性废气分析装置,成功开发了一套动态实时工艺控制装置。
它可将在 B点的废气中的CO2含量,直观地显示在计算机屏幕上,以便到达第二临界点后。
B点的CO2含量显示降低时电炉操作者能够及时中止喷氧。
此系统除了可用于电炉,还可用于其它与此相关的脱碳工艺,例如,还可用于氧气顶吹转炉(BOF ),氩氧脱
碳炉(AOD )和真空吹氧脱碳炉(VOD )。
应用废气分析系统可直接减少铁和铬的氧化,提高金属收得率,增加钢产量,有利
于降低吨钢电耗,节约氧气,减少石灰和硅铁用量。
DEW钢厂在热力学模拟实验和炉渣、钢液与废气分析的基础上,成功开发出一套用
于电炉炼钢监测炉内各元素氧化的废气分析装置。
实验证明,它不仅可监测和掌控炉内元素
氧化,且能使炉子冶炼不锈钢时实现最大的硅、碳氧化和最小的铁、铬氧化。
从而有效缩短冶炼时间,喷氧时最大限度减少贵重金属损失,有利于增加金属收得率和炉子生产率,全面
提高电炉冶炼不锈钢的经济效益。