Teigha使用说明
托利多吊钩秤说明书
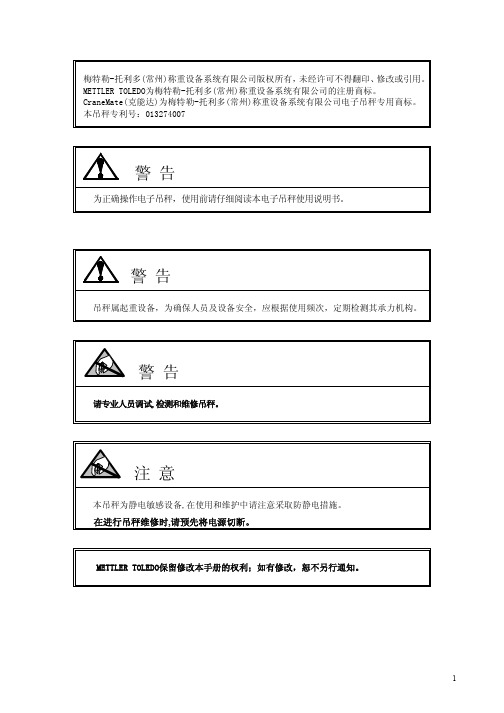
5.1. 开箱检查 .............................................................................................................................................................. 12
5. 使用准备 ................................................................................................................................................................. 12
3.1. 产品命名及型号 .................................................................................................................................................... 6
6.7. 累计调显 .............................................................................................................................................................. 15
6.4. 清皮 ...................................................................................................................................................................... 13
迪伯斯特拉超级耐用棒槌说明书

MAXIMUM BPM OF 2,200 MAX AIR PRESSURE: 90 PSIG,This Instruction Manual Contains Important Safety Information.Read THIS INSTRUCTION MANUAL Carefully and understand ALL INFORMATION Before Operating THIS Tool.• A lways operate, inspect and maintain thistool in accordance with American National Standards Institute Safety Code of Portable Air Tools (ANSI B186.1) and any other applicable safety codes and regulations.• F or safety, top performance andmaximum durability of parts, operate this tool at 90 psig/6.2 bar max air pressure with 3/8” diameter air supply hose.• A lways wear impact-resistant eye and face protection when operating or performing maintenance on this tool. Always wear hearing protection when using this tool.• H igh sound levels can cause permanent hearing loss. Use hearing protection as recommended by your employer orOSHA regulation.• K eep the tool in efficient operating condition.• O perators and maintenance personnel must be physically able to handle the bulk, weight and power of this tool.• A ir under pressure can cause severe injury. Never direct air at yourself or others. Always turn off the air supply, drain hose of air pressure and detach tool from air supply before installing, removing or adjusting any accessory on this tool, or before performing any maintenance on this tool. Failure to doso could result in injury. Whip hoses can cause serious injury. Always check for damaged, frayed or loose hoses and fittings, and replace immediately. Do not use quick detach couplings at tool. See instructions forcorrect set-up.• A ir powered tools can vibrate in use. Vibration, repetitive motions or uncomfortable positions over extended periods of time may be harmful to your hands and arms. Discontinue use of tool if discomfort, tingling feeling or pain occurs. Seek medical advice beforeresuming use.• P lace the tool on the work before starting the tool. Do not point or indulge in any horseplay with this tool.• S lipping, tripping and/or falling while operating air tools can be a major cause of serious injury or death. Be aware of excess hose left on the walking or work surface.• K eep body working stance balanced and firm. Do not overreach when operating the tool.• A nticipate and be alert for sudden changes in motion during start up and operation of any power tool.• D o not carry tool by the hose. Protect the hose from sharp objects and heat.• T ool shaft may continue to rotate briefly after throttle is released. Avoid direct contact with accessories during and after use. Gloves will reduce the risk of cuts or burns.• K eep away from rotating end of tool. Do not wear jewelry or loose clothing. Secure long hair. Scalping can occur if hair is not kept away from tool and accessories. Choking can occur if neckwear is not kept away from tooland accessories.• N ever use a chisel as a handstruck tool. They are designed and heat treated to be used only in air hammers. Select the correct shank and retainer for the tool.• N ever use dull accessories. Never cool a hot accessory in water as brittleness and early failure can result. Accessory breakage or tool damage may result from prying. Take smaller bites to avoid getting stuck.• D o not lubricate tools with flammable or volatile liquids such as kerosene, diesel orjet fuel.• D o not force tool beyond its rated capacity.• D o not remove any labels. Replace any damaged labels.• U se accessories recommended by Matco Tools.FAILURE TO OBSERVE THESE WARNINGS COULD RESULT IN INJURYOPERATIONAlways place a chisel in the hammer and hold the tool down to the work before operating. Damage to the tool or the retainer may result if this precaution is not followed.The chisel retainers are not designed for complete safety against accidental release of cutters or hammers. To avoid injury, the throttle must never be depressed unless the chisel is held firmly against the work place. When tool is not in actual use, the chisel must be removed. During operation, safety goggles should always be used to guard against flying rust and chips. When using tool, regulate the speed so that the chisel is not being driven out of the cylinder. If piston is allowed to strike the cylinder wall, internal damage will result.To change chisel, pull back on spring hook and insert chisel. Release spring hook.To regulate air, turn air regulator knob out for maximum air pressure and in for minimum.R EF. NO. PART NO. DESCRIPTION QTY.1 RS171801 Housing (incl. #2-14,22,26) 12 RS848002 Roll Pin (3 x 22mm) 23 RS848003 Inlet Bushing 14 RS848004 Cap 15 RS848005 O-Ring (4.9 x 2.2mm) 26 RS848006 Regulator 17 RS848007 O-Ring (11 x 2.4mm) 18 RS848008V Valve Stem 19 RS848009 O-Ring (3.8 x 1.9mm) 110 RS848010 O-Ring (3.5 x 1.5mm) 111 RS848011 Valve Bushing 112 RS848012 O-Ring (12 x 2mm) 113 RS848013 Spring 114 RS171814 Trigger Button 115 RS171815 Valve Block Assembly 1 15-1 RS848015S-1 Metal Washer 1 16 RS171816 Valve Disc 120 RS848019 Piston 121 RS171821 Cylinder 122 RS171822 Comfort Grip 123 MTCR1 Quick Change Chuck 124 RS171824 Exhaust Deflector 126 RS171826 Screw (M6 x 1.0) 127 RS171827 Nyloc Plug 2O I LD A I LY。
艾特霍纳UltraShift PLUS自动化变速箱说明书

UltraShift ® PLUSAutomated T ransmissionsCustom tailored to your jobThe Eaton UltraShift™ PLUS automated manualtransmission can be custom tailored to your job. Your spec. And your competitive edge. Our powerfulServiceRanger 4 diagnostic and programming tool provides access to many configurable features to give you exactly what you want. And it’s all backed by the solutions, support and expertise of theRoadranger® network. Find your Eaton edge at or contact your local Roadranger.S U P P O R TB AC K ED B YConfigurable with ServiceRanger 4 – Standard packageFEATURE DESCRIPTIONDefault Start Gear Sets the default start gear when Drive and Manual are selected.Maximum Start Gear The maximum possible start gear for Drive. Allowable start gear will varydepending on several vehicle inputs like load, grade and axle ratio.Coast Down Gear The last gear that is physically engaged before the vehicle startscoasting. Coast allows the transmission to roll to a stop.Default Reverse Gear The default start gear for Reverse.Maximum Reverse Gear The maximum reverse gear for Reverse.Transmission Shift Console Permits selection of clutch engagement options by shifter position to Mode Configuration provide optimum mobility for the vehicle application – includingStandard, Creep Mode, Blended Pedal, and Urge to Move.Vocational Shift Response The shift response setting controls the torque ramp-down before a shift and torque ramp-up after a shift to tune the transmission for specificloads and terrain.Grease Interval Enable Enables a Clutch Greasing Interval notice on the Gear Display (GI) after a specific number of clutch actuations. The number of actuations variesby transmission model.Auto-Neutral Tone Allows a tone when Auto Neutral is entered and the Park Brake Switchis released, but the system is not back in gear or Neutral.UltraShift ® PLUS Automated TransmissionsS U P P O R TB AC K ED B YNote: Features and specifications listed in this document are subject to change without notice and represent the maximum capa-bilities of the software and products with all options installed. Although every attempt has been made to ensure the accuracy of information contained within, Eaton makes no representation about the completeness, correctness or accuracy and assumes no responsibility for any errors or omissions. Features and functionality may vary depending on selected options.Eaton, Fuller, Roadranger, Solo, UltraShift and Fuller Advantage are registered trademarks of Eaton. All trademarks, logos and copyrights are those of their respective owners.For spec’ing or service assistance, call 1-800-826-HELP (4357) or visit /roadranger . In Mexico, call 001-800-826-4357.Roadranger: Eaton and trusted partnersproviding the best products and services in the industry, ensuring more time on the road.EatonVehicle Group13100 E. Michigan Ave.Kalamazoo, MI 49053 USA 800-826-HELP (4357)/roadranger © 2015 EatonAll Rights Reserved. Printed in USA.TRSL2548 0915Configurable with ServiceRanger 4 – Professional packageFEATURE DESCRIPTIONShift Point Calibration Determines the point at which the transmission upshifts and downshifts, depending on the vehicle’s application.Kick Downshift When throttle pedal transitions from low to high, often creates a downshift which can provide better acceleration.Hill Start Aid Threshold Enables changes to required % grade to activate Hill Start Aid function in the vehicle. The system uses foundation brakes to hold the vehicle stationary for up to 3 sec, holding the vehicle from rollback duringtransitions from brake to throttle pedal on grades.Hold Mode Gear Allows the ability to make Manual a Hold Gear function only (i.e.up/down buttons have no effect).In addition, provide an operator deterrent/nuisance tone when operating in Manual when a Hold Mode Gear isselected to discourage continuous use.Aux Transmission Model Indicates to the system that Eaton's AT-1202 Auxiliary Transmission is installed.Drive Train Type Allows for modification to the system's driveline torque limit when Aux Transmissions are installed.Remote Throttle Allows the transmission to be configured for Remote Throttle functionality. Turns on relay that allows throttle tobe controlled remotely. Primarily used in Mixer applications.Engine PTO Notifies transmission system that the vehicle has an engine-driven PTO on the vehicle. Primarily used for Mixer applications.PTO AutoNeutral Enable Allows the ability to allow or prevent a non-neutral mode selection when a PTO is active.Split Shaft PTOAllows the transmission to recognize that a split shaft PTO device is installed on the vehicle.Split Shaft PTO Default Gear Sets the default gear that will be selected when split shaft PTO is activated. This is only valid when the split shaftPTO is enabled.Split Shaft PTO Minimum Sets the minimum selectable gear for split shaft operation. This is only valid when the split shaft PTO is Gear Selectionenabled.。
旺迪汽车2018年7月13日发布的“旺迪低架滑动室车辆用户指南”说明书

In-Frame Low ProfileSlide-OutOWNER'S MANUALTABLE OF CONTENTSIntroduction2 Safety Requirements2 Operation Instructions3 Extending Slide-Out Room 3 Retracting Slide-Out Room 3 Basic Troubleshooting4 Basic Purge Procedure For Hydraulic Pump Units5 Hydraulic Cylinder Test5 Hydraulic Slide-Out Cylinder - Retract Test 5 Hydraulic Slide-Out Cylinder - Extend Test 6 Adjusting the Slide Room's Retracted Position 7 Adjusting the Slide Room's Extended Position 7 Maintenance8 Mechanical Maintenance 8 Low Pro Hydraulic Slide Assembly9 Low Pro Hydraulic Bed Slide Components10 Low Pro Hydraulic Bed Slide Components11IntroductionThe component's purpose is to hydraulically actuate slide-out rooms. Its function should not be used for any purpose or reason other than to actuate the slide-out room. To use the system for any reason other than what it is designed for may result in death, serious injury or damage to the coach.Safety RequirementsFailure to act in accordance with the following may result in death, serious injury,coach or property damage.Always wear gloves while handling.Moving parts can pinch, crush or cut. Keep clear and use caution.NOTe: Slide room is to be supported by a secondary means when servicing slide arms. Failure to do so could result in unexpected motion of the slide room.NOTe: All slide arms are over 100 pounds in weight. Ergonomic considerations should be made for safe install.Before actuating the system, please keep these things in mind:1. Parking locations should be clear of obstructions that may cause damage when the slide-out room isactuated.2. Be sure all persons are clear of the coach prior to the slide-out room actuation.3. Keep hands and other body parts away from slide-out mechanisms during actuation.4. To optimize slide-out actuation, park coach on solid and level ground.Operation InstructionsExtending Slide-Out Room1. Level the coach.2. Verify the battery is fully charged and hooked up to the electrical system.3. Remove transit bars (if so equipped).4. Press and hold the IN/OUT switch (Fig. 1) in the OUT position (Fig. 1B) until room is fully extended andstops moving.5. Release switch, which will lock the room into position.NOTe: Only hold OUT switch until room stops.Retracting Slide-Out Room1. Verify the battery is fully charged and hooked up to the electrical system.2. Press and hold the IN/OUT switch (Fig. 1) in the IN position (Fig. 1A) until the room is fully retracted andstops moving.3. Release the switch. This will lock the room into position.Fig. 1 NOTe: Only hold IN switch until room stops.4. Install the transit bars (if so equipped).ABBasic TroubleshootingThis troubleshooting chart outlines some common problems, their causes and possible corrective actions. If any part or serial number information is available, provide it to the service technician when asking for assistance.Every coach has its own personality and what may work to fix one may not work on another even if the symptoms appear to be the same.When something restricts room travel, system performance will be unpredictable. It is very important that slide tubes be free of contamination and allowed to travel full distance (stroke). Ice or mud buildup during travel is an example of some types of contamination that can occur.When you begin to troubleshoot the system, make sure the battery is fully charged, there are no visible signs of external damage to the system and that all connections are secure.During troubleshooting, remember that if you change something, that change may affect something else. Be sure any changes you make will not create a new problem.You can obtain additional information on the Lippert Slide-out System by visiting /customerservice or by calling 574-537-8900.What Is Happening?Why?What Should Be Done?Room doesn't move when switch is pressed.Restriction or obstruction insideor outside of unit.Check for and clear obstruction.Low battery voltage, blown fuse,defective wiring.Check battery voltage and charge ifneeded. Find and check fuse, replaceif blown. Check battery terminals andwiring. Look for loose, disconnected orcorroded connectors.Power unit runs but room does not move.Restrictions both inside andoutside of unit.Check for and clear restriction.Power unit runs, room moves slowly.Low battery, poor ground,extremely low outdoortemperature.Charge battery and check groundwire.Room drifts "in" or "out."Possible external leak in thehydraulic system.Tighten fittings.Inspect hoses, fittings and power unitfor external leaks.Air in system.After checking all connections,perform basic purge procedure, seeBasic Purge Procedure for HydraulicPump Units section.In the closed position, room drifts out.Leaking cylinder seal.See Hydraulic Cylinder Test section. Fluid bypassing cylinder piston.See Hydraulic Cylinder Test section. Hose from pump is leaking.Tighten fitting or replace hose. Fluid bypass in cartridge valve.Replace cartridge valve.Loose mounting bolts.Tighten mounting bolts.Basic Purge Procedure For Hydraulic Pump UnitsThe basic purge procedure to bleed the LCI Hydraulic Systems is performed without the use of any tools. The system's own function purges the air from the hydraulic lines and cylinders by simply running the pump. These simple steps will apply to Hydraulic Landing Gear (HLG), Hydraulic Stabilizer Jacks (HSJ), Class A Motorized Vehicles Leveling Jacks (LJ) and Hydraulic Slide-outs (S/O).1. Start with all hydraulic components in the fully retracted position, meaning all jacks, landing gearstabilizers and slide-outs brought back inside the coach as if it were ready to travel.2. Find the hydraulic pump location and note the amount of fluid currently in the reservoir. The fluid levelshould be about 1/4” from the top of the reservoir and no more than 1/2” from the top.NOTe: When checking the fluid level after ensuring all hydraulic components are retracted, note if there are any bubbles, froth or foam on top of the fluid. This is an indication that air has been pushed back tothe reservoir when the hydraulic components were retracted in the last cycle. Wait 15-20 minutesfor the foam to dissipate before beginning the purge process.3. If there is no froth or foam in the reservoir and the fluid is not within 1/2” of the top, fill the reservoir towithin the level described in Step 2.4. With the fluid level full and no foam in the reservoir, begin cycling the hydraulic system:CLASS A - Extend LJ fully, taking the coach off the tires. If the unit has hydraulic S/O, extend all S/O.Once all LJ and S/O are extended, immediately retract all S/O and then all LJ.5TH WHEELS - Extend HLG until footpads contact the ground, extend HSJ to touch the ground, extendall S/O. Retract all S/O immediately, retract HSJ and then retract HLG.NOTe: Purging of the hydraulic system on fifth wheels should be performed with the unit coupled to the tow vehicle, a king pin stand under the pin box or jack stands under the front portion of the frame.FIFTH WHEELS WITH LEVEL-UP 6-POINT LEVELING - Fifth Wheels with the Level-Up 6-point Levelingsystem have the unique ability to have the HLG and LJ extend fully, resulting in the tires beinglifted off the ground. These particular fifth wheels can be purged in the same fashion as the Class Aunits.Do not attempt to purge this system without the front end of the fifth wheel safely supported. Doing socould result in death or serious bodily injury.5. Check the reservoir for foam. If foam is present, see NOTE above and repeat Steps 3 & 4. Repeat thesesteps until no foam is present in the reservoir. If no foam is present, the system is purged of air. Hydraulic Cylinder TestHydraulic Slide-Out Cylinder - Retract Test1. Retract (close) all slide-outs (rooms) completely.2. Disconnect all rooms from system (if coach is equipped with IRC, close all but one room).3. Loosen hose from “E” (extend) port on the manifold of the Power Unit.4. Plug opening on manifold to prevent drawing air into the system.Do not attempt to run room out with the “e” port hose loose. The system will experience rapid fluid loss.5. Energize the Pump Unit to retract (close) room.The coach MUST be supported per manufacturer's specifications before working underneath. Failureto do so may result in death or serious injury.Always wear eye protection when performing service or maintenance to the coach. Other safety equipment to consider would be hearing protection, gloves and possibly a full face shield, dependingon the nature of the service.Moving parts can pinch, crush or cut. Keep clear and use caution.NOTe: Lippert Components, Inc. recommends that the following inspections, troubleshooting, componentreplacement, and verifications be completed only by certified RV technicians.6.When room is fully retracted, continue to run the room in and watch for fluid flow from hose/port “E.” Fluid flow greater than a few drops will indicate internal cylinder leaking (bypassing of piston seal). If greater than a few drops leak from hose fitting, piston seal is bad and will need to be replaced. If there is no fluid flow, reconnect hose to “E” port and tighten.7.Repeat steps 2 through 6 for each slide-out until all slide-outs have been tested. Energize the Pump Unit to retract (close) room.Be sure to reconnect and tighten hose at the “e” port before attempting to extend (open) the room or thesystem will experience rapid fluid loss.Hydraulic Slide-Out Cylinder - Extend Test1. Extend (open) all slide-outs (rooms) completely.2. Disconnect all rooms from system (if coach is equipped with IRC, open all but one room).3.Loosen hose from “R” (retract) port on the manifold of the Power Unit. Individual slide-outs can be tested if the unit is equipped with an IRC block. Close all valves in IRC except the one to be tested.Do not attempt to run room in with the “R” port hose loose. The system will experience rapid fluid loss. 4. Plug opening on manifold to prevent drawing air into the system.5. Energize the Pump Unit to extend (open) room.6.Continue to run the room out and watch for fluid flow from hose/port “R" (or IRC block if coach is equipped with IRC). Fluid flow greater than a few drops will indicate internal cylinder leaking(bypassing of piston seal). If greater than a few drops leak from hose fitting, piston seal is bad and will need to be replaced. If there is no fluid flow, reconnect hose to “R” port and tighten.7.Repeat steps 2 through 6 for each slide-out until all slide-outs have been tested.Be sure to reconnect and tighten hose at the “R” port before attempting to retract (close) the room or thesystem will experience rapid fluid loss.Adjusting the Slide Room's Retracted Position1. Locate cylinder coming through the frame.2. Retract the room completely in.3. Check the outside T- mold and seal positioning.4. Partially extend room.5. Hold jam nut (Fig. 2A) in place with wrench.6.Adjust nylock nut (Fig. 2C) towards the bracket if the room does not seal. Adjust the nylock nut (Fig. 2C) away from the bracket if the room is too tight and damages the fascia.NOTe: Make small adjustments, running the room in after each adjustment until proper seal is achieved.Adjusting the Slide Room's Extended Position1. Locate cylinder coming through the frame.2. Extend room completely out.3. Check the inside fascia and seal positioning.4. Partially retract room.5. Loosen and back off jam nut (Fig. 2A) from nut (Fig. 2B) to give nut (Fig. 2B) room for adjustment.6.Adjust nut (Fig. 2B) away from the bracket if the room extends too far and damages the inside fascia. Adjust nut (Fig. 2B) towards the bracket if the room does not seal. NOTe: Make small adjustments, running the room out after each adjustment until proper seal is achieved.7.Tighten jam nut (Fig. 2A) to nut (Fig. 2B).Up to 3"Free TravelFig. 2BracketHydraulic CylinderCBAMaintenanceThe Lippert In-Frame Lo-Pro Slide-out System has been static tested to over 4,000 continuous cycles withoutany noticeable wear to rotating or sliding parts. It is recommended that when operating in harsh environments (road salt, ice build up, etc.) the moving parts be kept clean. They can be washed with mild soap and water. No grease or lubrication is necessary and in some situations may be detrimental to the environment and long term dependability of the system.Electrical System MaintenanceFor optimum performance, the slide-out system requires full battery current and voltage. The battery MUST be maintained at full capacity. Other than good battery maintenance, check the terminals and other connections at the battery, the control switch, and the system for corrosion, and loose or damaged terminals. Check motor leads under the trailer chassis. Since these connections are subject to damage from road debris, be sure they are in good condition.NOTe: The Lippert In-Frame Lo-Pro Slide-out System is designed to operate as a negative ground system.A negative ground system utilizes the chassis frame as a ground and an independent groundwire back to battery is necessary. It is important that the electrical components have good wire tochassis contact. To ensure the best possible ground, a star washer should be used. Over 90% ofunit electrical problems are due to bad ground connections.Mechanical MaintenanceAlthough the system is designed to be almost maintenance free, actuate the room once or twice a month to keep the seals and internal moving parts lubricated. Check for any visible signs of external damage after and before movement of the travel trailer.NOTe: For long-term storage: It is recommended that the room be closed (retracted).SLIDe-OUTSLOW PRO HYDRAULIC SLIDE ASSEMBLYUpper Frame AssemblySliding Base AssemblyCylinderStationary Base AssemblySLIDe-OUTSLOW PRO HYDRAULIC BED SLIDE COMPONENTSA BCDeFG HI JKLMNCallout Part #DescriptionA178058Stabilizer Roller Bearing AssemblyB1186063/4 - 10; Hex GR5 Zinc Nut for Cylinder MountC1298643/8 - 16 x 1; Hex Tap BoltD1191253/8 - 16 Hex NutE1186131/2 - 13 x 5 Hex BoltF1186101/2 - 13; Hex NutG113131Straight FittingH141109O-Ring Face Seal Straight FittingI173738O-Ring Face Seal Elbow FittingJ138416Hose CouplingK249363O-Ring Hose End FittingL113128JIC to O-Ring 90 Degree Elbow FittingM113130T-Fitting with O-Ring on RunN139417Long Straight FittingRev: 07.12.18Page 11CCD-0001599SLIDe-OUTS LOW PRO HYDRAULIC BED SLIDE COMPONENTS O P Q CalloutPart #Description O12565324" Hydraulic Cylinder P248654Orange Hydraulic Hose Q 248653Black Hydraulic HoseThe contents of this manual are proprietary and copyright protected by Lippert Components, Inc. (“LCI”). LCI prohibits the copying or dissemination of portions of this manual unless prior written consent from an authorized LCI representative has been provided. Any unauthorized use shall void any applicable warranty. The information contained in this manual is subject to change without notice and at the sole discretion of LCI.Revised editions are available for free download from .Please recycle all obsolete materials.For all concerns or questions, please contactLippert Components, Inc.Ph: (574) 537-8900 | Web: | Email:************************In-Frame Low Profile Slide-out Owner's Manual。
泰克高空安全作业指南说明书

* 所有防坠器均带有连接环。
防坠落装置是专为防止作业者发生坠落的设备.随防坠器同时发出的使用手册中清晰定义了防坠距离及用途缓降器爬轨器作业吊篮提升机轨道门栏速差器轨道门栏独立式扶手锚固点绳索和抓绳器™- EN 352-2安全带锚固点PA标准 - EN 795-A1带连接环的固定织带AS19S标准 - EN 795-B+安全线tempo 3标准- EN 795-B锚固点标准 - EN 795-E织带式安全绳带减震器标准- EN 355HT electra标准 - EN 358/EN 361HT55 A标准- EN 361HT22标准 - EN 361blocfor™ 1.8A ESD- EN 360™ 10 ESDblocfor™ 6 ESD- EN 360自动回缩式防坠器安全绳固定点工作安全绳LC标准 - EN 354双头限位安全绳- LDF标准 - EN 354如需限位移动或工作点定位,防坠系统与安全绳配套使用,即可将作业者限位至安全区域内这些产品不可单独作防坠使用定位安全绳- LCM06标准 - EN 358为了在发生坠落时保护作业者,安装一整套安全防护系统是至关重要的,这套系统必须包含:一个锚固点一个防坠落装置一条安全带防坠落系统HT11标准 - EN 361上海达克泰机械设备技术有限责任公司地址:上海市浦东新区秀浦路3500号1幢厂房2楼, 邮编201315邮箱:****************.cn个人防护设备:法律责任欧洲高空防坠法规指出高空作业人员均应配备整套防坠落保护系统。
此系统在集成防护装置失效后可作个人防护使用。
高空作业时,必须遵循当地法律法规用于高空防坠的个人防护装置需带有CE标识,并由多个指定机构对质量管理进行监督。
达克泰为每个产品提供手册,该手册详细说明其地址、存储指南、用途、维护及各类标识含义达克泰是首家研发容量超过100公斤的防坠落系统制造商之一,并符合EC要求。
此系列包括锚固点,连接环,防坠器,自动防坠器,滑动防 坠器,安全带,腰带,根据欧洲规范检测的安全绳:CNB/P/11.062 (超过100公斤使用),CNB/P/11.060 - 074 - 075 (水平作业/屋顶作业).台的高空安全作业。
PH45 牵绳钩安装说明书和用户指南

1. This will help stabilize the drawbar in the pintle hook. 2. It will help directional control on cornering. 3. It will minimize the sawing effect of the drawbar during
Never exceed the rated capacities of towing devices. For off road usage, use with a swivel type drawbar and reduce capacity by 25%.
Page 4
VERTICAL LOAD:
Vertical Load.... .. .. ....... ...... .................. .. .......... .. .........4, 5
Mounting Height. ......Байду номын сангаас.... ...................................... ....... 6
Page I
SPECIFICATIONS: (LOAD CAPACITIES)
Max Gross Trailer Weight: ....................................... 90,000 Ibs.
Max Vertical Load: ... .. .......... .. ........... .. ..... ............ .. .. 18,000 Ibs.
味达维皇家系列说明书

目录
第一章. 高速快锅如何工作
1
第二章. 使用注意事项
1
第三章. 味达维高速快锅描述及其优点
3
第四章. 首次使用须知
5
第五章. 基本使用方法
容量
请注意以下关于容量的信息,锅内的容量指示线能更方便地为您测量容量
最小容量
这由高速快锅的直径大小决定,至少需要 200-300ml 的水来产生蒸汽,无论 你有没有放任何东西在锅内。在 200-300ml 液体之下,绝不要使用高速快锅。
18 cm: 200 ml 22 cm: 250 ml 26 cm: 300 ml 最大容量
2 使用注意事项
在您使用该产品之前请仔细阅读产品使用说明书和其他资料,不正确的使用可能导致锅具损坏或者人身伤害 及其它物品损失的风险。 在没有阅读说明书之前,请不要让任何人使用高速快锅。 如果您把高速快锅转让给他人,请务必连同使用说明书一并交给他。
注意! 请不要让儿童接近高速快锅烹饪区域。
高速快锅的使用
联系方式见第13重要事项联系联系联系方式见方式见方式见第13第13第13容量指示锁定指示器烹饪指示器安全装置安全突起安全装置芳香阀锅盖把手辅助把手释放锁钮蒸汽排出口蒸汽排出口1011121918172321252224222014131516锅底加热保护装置定位卡钉定位辅助标锅盖把手螺丝防滑锅身把手圆锥形锅身硅胶圈控制阀螺母芳香阀密闭圈安全阀门橡胶塞阀门圈硅胶帽10111213141516171819202122232425ce标志标准容量锅盖把手可以拆卸方便清洗释放锁钮用于泄压和打开高速快锅锁定指示器指示锅子是否完全扣合蒸汽排出口用释放锁钮进行泄压时蒸汽将被放出控制阀有烹饪指示在超过压力限制时会自动排气可以拆卸清洗起来简单烹饪指示器可以根据颜色指示来调节热源蒸汽排出口控制阀内如果压力比所设定值高则在进行烹饪时会放出蒸汽定位辅助标当您在盖上锅盖时可以借助它来定位定位卡钉在定位时所用的卡钉防滑锅身把手加热保护装置高速快锅在煤气灶上使用时保护手柄远离火源容量指示min
捷安特 双避震车使用手册 说明书

2019.09目录介绍3 3 3 34 4 4 45 5 5 56 67 8介绍基本术语 和避震器设置概念保固条款设定下压值设定避震器回弹设定踏板平台一般保养前避震行程 及 下压值设定油压弹簧前叉设定气压弹簧前叉设定避震器 下压值设定建议表后避震器设定指南油压弹簧避震器设定气压避震器设定气/油压 后避震器 及 回弹调整 避震器设定值后避震器 下压值建议设定值99 10 11MY20 bike models MY19 bike models MY18 bike models MY17 bike models11本手册旨在作为快速入门参考指南,帮助您熟悉新的GIANT全避震山地车架。
并不能替代自行车随附的一般自行车用户手册或避震器制造商的技术手册。
如果您没有收到这些手册,请联系您的GIANT授权经销商。
我们鼓励您在第一次骑行之前阅读所有与自行车及其避震组件有关的手册。
所有手册均包含有关自行车安全和操作的重要信息。
在骑行GIANT自行车之前,请参阅自行车附带的制造商技术信息,以获取有关避震功能和设置的特定详细信息。
如果您没有收到这些技术手册,请与GIANT 授权经销商联系。
如果您不理解快速入门说明或设置困难,请在骑GIANT自行车之前先咨询GIANT授权经销商。
仅GIANT Glory 型号自行车被设计用于双肩避震前叉。
在这些型号以外的任何GIANT自行车上使用双肩避震前叉会导致保修失效,并可能导致车架故障,从而导致人身伤亡。
GIANT Bicycle Inc.对使用双肩前叉对自行车和骑行者造成的损坏不承担任何责任。
基本术语 和 避震器设置概念条款•触底/Bottom Out:当后避震器或避震前叉(以下简称“避震器”)被完全压缩到底且所有避震器行程已被全数使用时。
压缩触底:震动对冲击的声响。
•阻尼/Damping:控制压缩或回弹速度的内部机制。
•PSI:每压力的 磅/平方英寸。
•回弹/Rebound:控制避震器回弹的速度,也是避震器回复的速度。
- 1、下载文档前请自行甄别文档内容的完整性,平台不提供额外的编辑、内容补充、找答案等附加服务。
- 2、"仅部分预览"的文档,不可在线预览部分如存在完整性等问题,可反馈申请退款(可完整预览的文档不适用该条件!)。
- 3、如文档侵犯您的权益,请联系客服反馈,我们会尽快为您处理(人工客服工作时间:9:00-18:30)。
3.02及以下版本命名空间应将 Teigha 换为DWGdirect 。
1、Teigha 中DWG 数据库结构:经 常用到 的有 TextStyleTable 、LayerTable 、LinetypeTable 、BlockTable 及其对应的TextStyleTableRecord 、LayerTableRecord 、LinetypeTableRecord 、BlockTableRecord 及 Entity 。
2、具体使用2.1添加引用使用前应该添加 TD_Mgd_3.03_9.dll 或是其他版本类库, 类库分为64位与32位,32位类库在64位系统上运行效果可能不太好。
3.02版本及一下版本可能没有 64位的类库。
命名空间有:Teigha.DatabaseServices; Teigha.Geometry; Teigha.Colors; Teigha.Export_Import; Teigha.GraphicsI nterface; Teigha.GraphicsSystem; Teigha.Ru ntime;O.nD no.nQ . n| u_nV ewporl ISbK RotoidUC3 R&c ortiRocotdEHork r 劉© RftCOrtlCEiGCt2.2 打开、新建、保存数据库使用之前应加上这个:using ( Services ser = new Services ())// 一个应用程序加上一个就行了,否则出错1、打开数据库( dwg 文件)using ( Database pDb = new Database( false , false ))// 不加参数会出错{ pDb.ReadDwgFile( Application .StartupPath + "\\TABMENU.dwg",FileOpenMode.OpenForReadAndWriteNoShare, false , "" );}2、新建数据库using ( Database pDb = new Database())// 加参数出错3、保存(1)保存格式SaveType pSavetype = SaveTypeSave12; 〃Save12 为.dwg Save13 为dxf 默认保存为dwg ,可以不用指定。
(2)保存版本类型DwgVersion dwgver = DwgVersion.vAC18; //ACAD2010为vAC24;ACAD200为vAC21;ACAD200为vAC18;很重要,保存时要用,版本过高时低版本AutoCAD 不能打开。
(3)保存pDb.SaveAs(filename, dwgver);pDb 为数据库( Database),filename 为dwg 文件名,dwgver 为版本。
2.3 写数据2.3.1 添加文本样式ObjectId styleId = ObjectId .Null;using ( TextStyleTable pStyles =( TextStyleTable )pDb.TextStyleTableId.GetObject( OpenMod.eForWrite)){// 文本样式记录using ( TextStyleTableRecord pStyle = new TextStyleTableRecord ()){// 表对象(记录)添加到表之前必须命名// isShapeFile flag must also be set (if true) before adding the object// to the database. = styleName; // 必须设定pStyle.IsShapeFile = isShapeFile; // 添加(记录)到数据库之前必须设定(如果为true )// Add the object to the table. 添加对象(记录)到表styleId = pStyles.Add(pStyle);// 设置剩下的属性。
(可以添加后设置也可以添加之前设置) pStyle.TextSize = textSize;pStyle.XScale = xScale; pStyle.PriorSize = priorSize; pStyle.ObliquingAngle = obliquing;pStyle.FileName = fileName;if (isShapeFile) pStyle.PriorSize = 22.45;if (! string .IsNullOrEmpty(ttFaceName)) pStyle.Font = newFontDescriptor (ttFaceName, bold, italic, charset, pitchAndFamily);return styleId;}}注:pDb 为Database2.3.2 添加线型using ( LinetypeTable pLinetypes =( LinetypeTable )pDb.LinetypeTableId.GetObject( OpenMod.eForWrite)){// 线表记录using ( LinetypeTableRecord pLinetype = new LinetypeTableRecord ()) { = name; // 必须命名ObjectId linetypeId = pLinetypes.Add(pLinetype); // 添加记录return linetypeId;}注:线型要有相应的线型文件,且不一定能够加成功,线型可以在使用之前手动加在dwg 模板中,从其他文件向dwg 文件复制线型,可能不成功。
2.3.3 添加块例:using ( BlockTable blockTable = ( BlockTable )pDb.BlockTableId.GetObject( OpenMod.eForWrite)) {ObjectId annoBlockId;using ( BlockTableRecord btr = new BlockTableRecord ()){ = "AnnoBlock" ;annoBlockId = blockTable.Add(btr);using ( Circle pCircle = new Circle ()){pCircle.SetDatabaseDefaults(pDb);btr.AppendEntity(pCircle);Point3d center = new Point3d (0, 0, 0);pCircle.Center = center;pCircle.Radius = 0.5;}}}向块表中加入块之前,块一定要有名字。
同时可以从其他文件中提取块,加入到目标数据库中例:using ( Database db = new Database( false , false )){if (! File .Exists( Application .StartupPath + "\\BLOCKS\\" + blockname +".dwg" )){MessageBoxShow("没找到CAS块文件");return ObjectId .Null;}db.ReadDwgFile( Application .StartupPath + "\\BLOCKS\\" + blockname + ".dwg" , FileOpenMode.OpenForReadAndAllShare, false , "" );using ( BlockTable pTable =( BlockTable )db.BlockTableId.Open( OpenMode.ForRead)){using ( BlockTable bt =( BlockTable )pDb.BlockTableId.Open( OpenMod.eForWrite)){using ( BlockTableRecord btr = new BlockTableRecord ())foreach ( ObjectId id in pTable){using ( BlockTableRecord pBlock =( BlockTableRecord )id.Open( OpenMod.eForRead)){foreach ( ObjectId entid in pBlock){ using ( Entity pEnt =( Entity )entid.Open( OpenMod.eForRead, false , true )){btr.AppendEntity(( Entity )pEnt.Clone());}}}} = blockname;ObjectId blockid = bt.Add(btr);return blockid;}}}}234向模型(model)空间画实体(线、面等)加入线,例:using ( BlockTable blockTable = ( BlockTable )pDb.BlockTableId.GetObject( OpenMod.eForWrite)) { ObjectId modelSpaceID = blockTable[ BlockTableRecord .ModelSpace]; using ( BlockTableRecord btr =( BlockTableRecord )modelSpaceID.GetObject( OpenMod.eForWrite)){using ( Polyline2d pline = new Polyline2d ()){ btr.AppendEntity(pline);// 向块记录中添加线Vertex2d pVertex = new Vertex2d ();// 顶点Point3d pos = start;// 起点pVertex = new Vertex2d (); pline.AppendVertex(pVertex);pos = start;//pVertex.Position = pos;pVertex.Dispose();起点pVertex = new Vertex2d (); pline.AppendVertex(pVertex); pos = end;// 顶点,终点pVertex.Position = pos;if (linewidth >= 0.0){pVertex.StartWidth = linewidth; // 线宽pVertex.EndWidth = linewidth;}pVertex.Dispose();//pline.Closed = false;// if(linestyle != null ) {pline.Linetype = linestyle;//}yer = LayerName;//}}}}加入面的操作与上面加入线类似,但最后线的此属性在画线时不加,但在成面时将属性变为true 线型图层名Closed 属性应设置成true。