精益生产丰田问题解决办法
利用丰田问题解决方法的事例

利用丰田问题解决方法的事例一、丰田问题解决方法简介丰田问题解决方法,又称丰田生产方式(Toyota Production System,简称TPS),起源于20世纪50年代的日本丰田汽车公司。
它是一种以降低成本、提高质量和提高效率为核心的生产管理模式,通过对生产流程、库存管理、质量控制等方面的优化,实现企业的持续改进和可持续发展。
丰田问题解决方法包括以下几个核心理念:1.追求零浪费:通过降低生产过程中的浪费,提高资源利用率,降低成本。
2.Just-In-Time(JIT)生产:根据客户需求进行实时生产,减少库存积压。
3.自动化生产:利用先进技术提高生产效率,降低人为错误。
4.持续改进:不断优化生产流程,实现企业持续发展。
二、丰田问题解决方法的应用事例1.生产线问题在丰田生产方式的应用中,生产线问题是一个典型的案例。
通过引入JIT 生产和自动化技术,丰田公司成功降低了生产过程中的浪费。
例如,当生产线出现故障时,传统企业通常会选择停机维修,从而导致生产延误。
而丰田公司则采用快速换线方式,在维修的同时保持生产进行,从而减少了生产中断时间。
2.供应链管理问题丰田公司通过与供应商建立紧密的合作关系,实现供应链的协同优化。
例如,丰田公司与供应商共享生产计划和库存信息,使供应商能够根据实际需求调整生产,降低库存积压。
同时,丰田公司还会对供应商进行培训,帮助他们提高生产质量和效率。
3.质量管理问题丰田公司注重产品质量的持续提升,采用“三现主义”原则进行质量管理,即“现场、现物、现实”。
当出现质量问题时,丰田公司会立即组织团队到现场调查,针对实际情况制定改进措施。
此外,公司还推行“零缺陷”理念,鼓励员工积极参与质量管理,发现并解决问题。
4.员工培训与激励问题丰田公司注重员工的培训和发展,通过定期举办培训课程,提高员工的技能和素质。
同时,公司采用绩效考核制度,激励员工积极参与改进活动。
此外,丰田公司还鼓励员工提出建议,对优秀建议给予奖励,激发员工的创新潜能。
精益生产之丰田生产方式
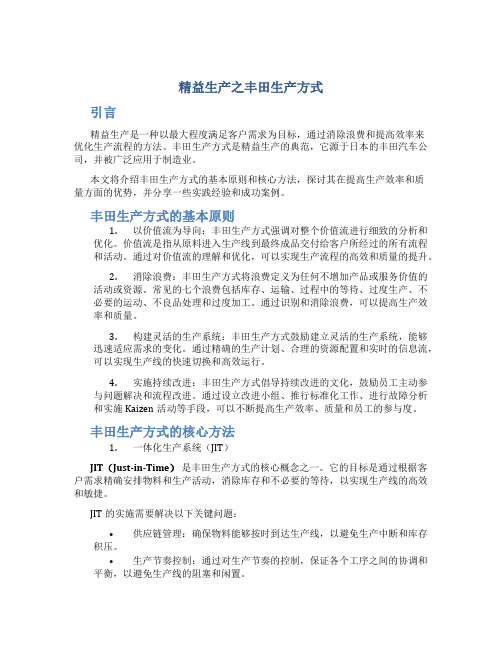
精益生产之丰田生产方式引言精益生产是一种以最大程度满足客户需求为目标,通过消除浪费和提高效率来优化生产流程的方法。
丰田生产方式是精益生产的典范,它源于日本的丰田汽车公司,并被广泛应用于制造业。
本文将介绍丰田生产方式的基本原则和核心方法,探讨其在提高生产效率和质量方面的优势,并分享一些实践经验和成功案例。
丰田生产方式的基本原则1.以价值流为导向:丰田生产方式强调对整个价值流进行细致的分析和优化。
价值流是指从原料进入生产线到最终成品交付给客户所经过的所有流程和活动。
通过对价值流的理解和优化,可以实现生产流程的高效和质量的提升。
2.消除浪费:丰田生产方式将浪费定义为任何不增加产品或服务价值的活动或资源。
常见的七个浪费包括库存、运输、过程中的等待、过度生产、不必要的运动、不良品处理和过度加工。
通过识别和消除浪费,可以提高生产效率和质量。
3.构建灵活的生产系统:丰田生产方式鼓励建立灵活的生产系统,能够迅速适应需求的变化。
通过精确的生产计划、合理的资源配置和实时的信息流,可以实现生产线的快速切换和高效运行。
4.实施持续改进:丰田生产方式倡导持续改进的文化,鼓励员工主动参与问题解决和流程改进。
通过设立改进小组、推行标准化工作、进行故障分析和实施Kaizen活动等手段,可以不断提高生产效率、质量和员工的参与度。
丰田生产方式的核心方法1.一体化生产系统(JIT)JIT(Just-in-Time)是丰田生产方式的核心概念之一。
它的目标是通过根据客户需求精确安排物料和生产活动,消除库存和不必要的等待,以实现生产线的高效和敏捷。
JIT的实施需要解决以下关键问题:•供应链管理:确保物料能够按时到达生产线,以避免生产中断和库存积压。
•生产节奏控制:通过对生产节奏的控制,保证各个工序之间的协调和平衡,以避免生产线的阻塞和闲置。
•节约资源:减少库存、运输和不必要的加工,以优化资源的利用率和降低生产成本。
2.精益流程改善(Kaizen)Kaizen是丰田生产方式中的另一个核心概念,意为持续改进。
精益运营系统

精益运营模式精益生产即丰田生产方式,它是丰田几代人智慧的结晶。
问题及解决方案:1、 上级安排任务,下属没有按照领导的意思去做2、 KPO 方面传递的信息,个别车间得不到相应信息3、 KPO 给车间传递的信息,经过车间自己做,却偏离了原来的轨道4、 车间在进行精益推行的时候,只是一味的单独去做某一个模块的改善,而不是有机的将各个模块(价值流图、5S 、TPM 、标准化、质量、快换)联系起来。
由于精益在车间的推行,主要靠价值流图、5S 、TPM 、标准化、质量、快换的推行效果来进行评价,所以先将六个工具(模块)的关系以“金字塔”模式展示出来,进行说明,如图:在图中显而易见:在精益的推行过程中,5S 作为重中之重,是精益推行的基础;价值流图是指引我们改善的方向标;质量是我们改善活动的一个重要目的,保障产品质量,削减浪费;标准化是规范生产操作的有效工具,同时质量、快换、TPM 、5S 还需要标准化来保障实施。
所以在车间推行精益有必要将各个模块联系起来,方便大家对精益的理解和掌握。
价值流图标准化5S针对车间推行精益出现的问题,在此提出车间的《精益运营系统》,主要内容围绕价值流图、5S 、TPM 、标准化、质量、快换:一、 精益运行系统1、在车间建立精益的运营机制,将各个模块系统控制。
要求车间在精益推行过程中,能够系统将六个模块联系在一起,找到它们之间的交叉点和不同点,最终能够保证各模块全面的运行,避免现有的工作“堵抢眼”模式。
2、保障所有工作能够按照PDCA 循环去开展,持续改进。
要求车间从看板管理入手,将所有问题的记录、分析都以PDCA 模式呈现,并能够在其中显示出员工对精益推行的参与情况。
标准化质量5STPM价值流二、价值流运营系统1、建立价值流运营小组,负责对价值流图的日常更新工作。
要求能够熟知价值流图中各项元素所代表的含义及内部数据的计算方法,小组成员以车间主任、精益推行员、工段长为主。
2、小组成员定期通过价值流图汇报车间工作情况。
利用丰田问题解决方法的事例

利用丰田问题解决方法的事例摘要:一、丰田问题解决方法简介二、丰田问题解决方法的应用事例1.供应链管理问题2.生产过程中的质量控制3.客户满意度提升三、丰田问题解决方法在我国企业的应用现状四、如何在我国企业中推广丰田问题解决方法五、总结正文:一、丰田问题解决方法简介丰田问题解决方法,又称丰田生产方式(TPS),起源于日本丰田汽车公司,是一种以降低成本、提高质量和提高效率为目标的生产管理方法。
其核心理念是追求精益求精,通过持续改进,实现生产过程的完美无缺。
丰田问题解决方法包括五个步骤:确定问题、分析问题、制定解决方案、实施解决方案和检查效果。
二、丰田问题解决方法的应用事例1.供应链管理问题在供应链管理方面,丰田问题解决方法帮助企业优化供应商关系,降低库存成本,提高物流效率。
例如,通过与供应商建立长期稳定的合作关系,降低采购成本;采用“拉动生产”方式,根据客户需求实时调整生产计划,减少库存积压。
2.生产过程中的质量控制在生产过程中,丰田问题解决方法强调“防错”原则,通过设计易于操作的工艺流程、制定严格的质量检查标准、实施全员质量管理等方式,确保产品质量。
例如,生产线上的工人参与质量检查,发现问题及时上报,避免不合格产品流入下一道工序。
3.客户满意度提升丰田问题解决方法注重从客户需求出发,优化产品设计和生产过程。
通过对客户需求的深入了解,企业可以更好地调整生产计划和产品结构,提高客户满意度。
例如,丰田汽车公司通过不断改进发动机性能、提高燃油效率、提升驾驶安全性等方面的技术,以满足消费者对环保、节能和高性价比的需求。
三、丰田问题解决方法在我国企业的应用现状近年来,我国企业越来越重视丰田问题解决方法的学习和应用。
许多企业已经开始在生产、质量管理等方面引入丰田问题解决方法,并取得了显著的效果。
然而,总体来说,我国企业在应用丰田问题解决方法方面仍处于初级阶段,需要进一步深化学习和实践。
四、如何在我国企业中推广丰田问题解决方法1.加强培训:组织企业员工参加丰田问题解决方法的培训课程,提高员工对丰田问题解决方法的认识和应用能力。
《丰田问题解决法》课件

质量控制与保证
质量控制流程
质量保证标准
介绍质量控制的最佳实践方法。
讨论质量保证的重要性及其标 准。
质量的持续改进
解释如何通过不断改进来实现 质量的提升。
员工培训与发展
1 持续培训计划
说明持续培训和发展在 质量标准中的重要性。
2 技能和知识建设
3 团队合作和协作
讨论如何通过技能和知 识建设来提高工作质量。
3 领导力不力
讨论质量管理中领导力的影响。
丰田的危机应对
1 召回和修复方案
2 沟通和透明度介绍公司采取的措Fra bibliotek来解决质量问题。
讨论公司改进沟通和透明度的努力。
3 恢复品牌声誉
解释如何重建消费者对丰田的信任。
丰田的生产系统
精益生产
解释丰田独特的生产方式如何导致了质量问题。
持续改进
讨论对生产系统的持续改进的重要性。
解释团队合作和协作在 质量管理中的关键作用。
客户参与
客户反馈与满意度
探讨如何通过积极的客户 参与来提高产品质量。
个性化定制
讨论个性化定制在质量管 理中的重要性。
客户关系管理
解释如何维护积极的客户 关系以实现质量管理的成 功。
数据和分析的重要性
1
数据收集
解释如何收集有效的数据以支持质量管理决策。
2
《丰田问题解决法》PPT 课件
丰田公司一直以来都是全球最大的汽车制造商之一。然而,近年来,公司出 现了一系列的质量问题,这些问题需要我们找到解决方案来重新确立品牌声 誉。
丰田质量问题的根本原因
1 工艺和设计不足
分析导致质量问题的制造和设计方面的因素。
2 供应链管理不当
丰田问题解决8步法!(干货收藏)「标杆精益」

丰田问题解决8步法!(干货收藏)「标杆精益」全文总计3333字,需阅读9分钟,以下为正文:—1—丰田工作方法10个基本意识1. 客户至上在为本部门或公司推展工作时,应始终将客户的利益放在第一位。
在丰田,后道工序也被看作是“客户”。
2. 经常自问自答“为了什么”不要将当前的手段混淆为目的。
常常自问,工作真正的目的是什么。
3. 当事者意识只有认识到自己是当事者,才能理解自己工作的使命和价值,产生自豪感。
才会思考“我想要做什么”,“我一定要达成这个”。
4. 可视化问题、信息、计划和对情况的认识和意见等需要共有的信息,以手册,日程表等形式,或放入共有文件夹、共有服务器或者在告示板上张贴,以达到信息的共有化。
5. 依据现场和事实进行判断摒弃先入为主的观念,以无拘无束之心、看待事物的真实方面。
不将臆测和事实混淆。
亲临现场、自己去看,去听,去感受。
6. 彻底的思考和执行深入思考、怀着“不到最后决不放弃”的强大意志和坚韧不拔的精神,将工作进行到最后。
7. 速度·时机迅速对应客户需求,贯彻实施对策。
如果对策的实施尚需一定时间,可先采取适当措施,避免错失做事的良机。
严守交货期。
8. 诚实·正直即使在没人监督的时候也按照既定顺序(工序)确实推进工作。
虚心听取别人的意见。
对自己的行为负起责任。
9. 实现彻底的沟通诚心诚意与客户或相关人员努力沟通,直至他们给与理解并能够主动积极提供协助。
10. 全员参与从项目的最初阶段起,动员一切可动员的力量,及时提供相关信息,引领团队以及相关人员,集思广益,以达到效果和效率的最大化。
—2—什么是丰田所谓的“问题”现状与理想状态之间的差距,就是问题。
2种问题:•发生型问题•设定型问题—3—问题解决八步法Step1.明确问题在丰田,没有哪一项工作是不存在问题的。
要从工作的真正目的出发,带着强烈的问题意识,主动地发现问题。
任何时候都不满足于现状,要志存高远,首先在脑海里描绘“理想状态”,将其与现状的差距“可视化”,从而将问题明确化。
丰田汽车案例-精益制造的14项管理原则

原则1:管理决策以长期理念为基础 即使因此牺牲短期财务目标也在所不惜
别让决策伤害到信任与相互尊重
丰田公司认识到,维持员工的饭碗是它对小区与社会的责任之一. 丰田并非以季度预算来衡量此投资,而是从使顾客及员工持续尊 敬丰田公司及其产品的角度来考虑的.丰田知道这个工厂熟练且 努力的员工必定能应用丰田生产方式持续地改进质量,去除浪费. 丰田相信这才是带动长期获利的主要因素.
第四类原则 持续解决根本问题是企业不断学习的驱动力
原则12: 亲临现场查看以彻底了解情况(现地现物) 原则13: 不急于作决策,以共识为基础,彻底考虑所有可能选择,并快速执 行决策 原则14: 通过不断省思与持续改进以变成一个学习型组织
第一类原则 长期理念
解决问题 (持续改进与学习) 员工与事业伙伴 (尊重他们、激励他们、 使他们成长) 流 程
原则1:管理决策以长期理念为基础 即使因此牺牲短财务目标也在所不惜
比赚钱更重要的使命
丰田公司经营企业的起点是为顾客,社会与经济创造
更高价值
原则1:管理决策以长期理念为基础 即使因此牺牲短期财务目标也在所不惜
做有益于顾客的事
丰田公司在1971年的“尼克松冲击”中坚持做有益于顾客的事. 虽然公司发生了很大的损失,但也使得顾客满意,并赢得长期顾 客关系.
真正的挑战在于必须建立一个懂得寻找方法减少使用广告牌 制度以降低存货,且最终解除缓冲存货的学习型企业
原则3:实施拉式生产制度以避免生产过剩
预定日程表的推式生产制度仍有可用之处
在丰田公司,仍然有很多地方使用依照预先排定生产日程表的推 式制度. 他们使用传统的排定日程表制度来下零部件订单,以适当的前 臵期来进行零部件的递送.日程表并非只是你必须尽量遵照的 原则,也是你务必竭尽全力实现的截止期限. 你不需要照单全收地仿效丰田公司所使用的特定工具,也能变得 像丰田公司一样精益.丰田模式是一种理念及一套工具,必须适当 地应用于你公司的情况.
丰田管理方法与丰田问题解决法

丰田管理方法与丰田问题解决法丰田是一家以丰田管理方法闻名的全球汽车制造公司。
其管理方法以卓越的质量控制和持续改进为核心,为公司的成功奠定了坚实的基础。
以下是丰田管理方法的一些重要原则以及丰田问题解决法的一些示例。
一、丰田管理方法的原则:1. 全员质量控制:丰田认为所有员工都应该参与到质量控制中来,而不仅仅是质量控制部门的责任。
通过团队合作和全员参与,在每个环节上实施严格的质量控制,从而确保产品的质量和可靠性。
2. 问题解决的基本原则:丰田鼓励员工在工作中积极面对问题,并追求长期解决方案,而不是简单地解决眼前的困难。
通过对问题进行深入分析和持续改进,可以避免类似问题再次发生。
3. 持续改进:丰田相信,持续改进是实现卓越的关键。
公司要求员工不断反思和改进自己的工作方法和流程,以提高效率和质量。
通过设立绩效指标和目标,鼓励员工主动探索和实施改进措施。
二、丰田问题解决法的示例:1. 5W1H法:在丰田,问题解决从弄清问题的本质和原因开始。
使用5W1H法(即什么、为什么、在哪里、何时、如何和谁),团队对问题进行全面的分析和调查,从而找出根本原因而不仅仅是表象的问题。
2. 根因分析:丰田强调通过分析问题的根本原因,而不仅仅是应对其中的表面问题。
使用相关工具如鱼骨图等,团队可以深入地研究问题,找到真正的原因,并采取合适的解决方案。
3. PDCA循环:丰田采用PDCA(即计划、实施、检查和行动)循环的方法来解决问题。
通过制定计划,实施方案,检查成果和采取行动,团队可以持续改进,并确保问题解决方案的有效性。
丰田的管理方法与问题解决法为公司在全球市场取得了巨大的成功。
通过全员质量控制和持续改进,丰田能够不断提升产品和服务的质量,满足客户的需求。
同时,丰田问题解决法的应用也让公司能够快速而有效地解决问题,确保生产线的稳定性和可靠性。
这些管理方法和解决问题的思路也为其他公司提供了宝贵的借鉴。
丰田作为一家世界知名的汽车制造公司,其管理方法与问题解决法的成功经验为其他企业提供了重要的借鉴。
- 1、下载文档前请自行甄别文档内容的完整性,平台不提供额外的编辑、内容补充、找答案等附加服务。
- 2、"仅部分预览"的文档,不可在线预览部分如存在完整性等问题,可反馈申请退款(可完整预览的文档不适用该条件!)。
- 3、如文档侵犯您的权益,请联系客服反馈,我们会尽快为您处理(人工客服工作时间:9:00-18:30)。
目标:移印区零不良 Target: Zero defect in printing area
11
内容介绍 Content Introduction
(1)头脑风暴,分析所有可能导致原因 Brainstorm to analyze all possible causes (2)征求现场作业者的意见,查看问题发生点 Get input from job performers and check the process (3)选取最具可能性的问题导致原因 Select the most likely causes (4)创建“原因”和“结果”分析链 Create “why chain” apply “therefore” test
移印不良(10) Printing failure 首要问题 PP 调油墨 Blend the printing inc
组件错误 (3) HW failure
标签错误(5) Label failure
包装盒错误(2) Box failure
安装印版 Install the plate
安装移印头 Install the head
1. 澄清问题 Clarify the problem 2. 分解问题 Break down the problem
P
3. 设定目标 Target setting
4. 根源分析 Root cause analysis
5. 制定对策 Develop countermeasures 6. 分析对策 See countermeasures through
将大问题分解成小的更具体的问题 Break the big problem into small and specific problems 将问题进行分类并进行轻重标识 Classify and quantify the problems 将问题进行描述并指出问题发生点 Describe the PP and find the PoO 如果不能正确描述问题,也就无法正确解决问题 If you can’t describe the PP correctively, you can’t resolve the PP correctively.
样品测试 Sample test
移印开始 Start printing
问题点 PoO
油墨调的不合适导致包装区抽查百个成品中有10个移印不良品 The printing inc was not blended properly so there were 10 printing defects from 100 finished parts during the check
6
举例 Example
1.澄清问题 Clarify the problem
最终目标:提供客户需求的高性能的无任何质量问题的合格刹车片产品 Ultimate goal: Provide high quality pads for customers with no any quality risk defects 标准:包装区检查不合格品率为零 Standard: Zero audit defect from packing area 目前状态:每百个成品中不合格品为20 Current situation: 20 defects from every 100 finished parts
4. 根源分析 Root cause analysis
人 Man
机 Machine
问题 Problem
料 Material
法 Method
环 Environment
12
举例 Example
油墨调的不正确 Inc was not properly blended 油墨颜色太浅 Color of inc was very light 稀料添加的太多 Too much thinner added 操作方法不正确 Operation method was not correct 现场没有比例说明 No ratios instructing work at job site 没有比例测试装备 No ratio test gage 之前未考虑到,未购买 Didn’t consider this so didn’t buy it
Content instruction
问题 & 讨论 Question & Discussion
2
冰山理论 Ice –berg Theory
可视觉化的只是问题的表象 What can be seen is only the visem 问题的根源却在表象之下 The root of a problem hides behind its presentation 发掘根源才能彻底解决问题 Only finding the root can help to completely resolve the problem
我所付的职责 & 工作 My responsibilities & work
完成生产计划 To meet production plans
我的工作的目的 My job’ purpose
满足客户需求 To meet customer demand
最终目标 Ultimate goal
在规定的时间内将合理价格的高性能和高质量的刹车片提供给客户 To provide customers with high functional and high quality pads at reasonable prices in a timely manner
13
内容介绍 Content Introduction
5. 制定对策 Develop countermeasures
(1)尽可能多的考虑解决措施 Develop as many countermeasures as possible (2)选取增值最高的解决措施 Select the highest value added countermeasures (3)与其他人取得一致意见 Build consensus with others (4)创建一个清晰的详细的行动计划 Develop a clear and detailed action plan
表象 Visual presentation
根源 The root
标准 Standard 差距 Gap = 问题 Problem
目前状态 Current situation
目前状态与标准之间的差异就是问题 The current situation gap to the standard is problem 解决问题的根源就是使目前状态彻底达到标准要 求 Resolve the root of a problem is to make the current situation completely meet the standard
1. 澄清问题 Clarify the problem
目前状态 Current situation 标准 Standard
差距 = 问题 Gap = problem
5
内容介绍 Content Introduction
澄清你所负职责&工作的“最终目标” Clarify the “ultimate goal ” of your responsibilities & work
3
概念介绍 Concept Introduction
8 step problem solving is a systematic and logical problem solving procedure, which aims to find the root cause and follow the actions to establish a new standard. 新旨 的在 八 标发 步 准现 问 。问 题 题解 的决 根法 源是 并一 对套 问系 题统 解的 决有 办逻 法辑 进的 行问 跟题 踪解 以决 形步 成骤 ,
主要问题 PP
问题点 PoO
大问题 Big problem
目前状态 Current situation
问题 Problem
问题 Problem
目标 Target
问题 Problem
10
举例 Example
抽查包装区100个成品中有20个不合格品 20 defects from every 100 finished parts
D C A
7. 监督结果与过程 Monitor both results and processes 8. 将成功的过程标准化 Standardize successful processes
4
内容介绍 Content Introduction
(1)澄清你所负职责&工作的“最终目标” Clarify the “ultimate goal ” of your responsibilities & work (2)澄清你所负工作的“标准” Clarify the “standard” of your work (3)澄清你所负工作的“目前状态” Clarify the “current situation” of your work (4)目视观察“目前状态”与“标准”之间的差距 Visualize the gap between the “current situation” and the “standard”
通常在对所有可能的解决对策进行评价时需要综合考虑一下因素,以确定最佳解决对策: Usually, when we do evaluation for all possible countermeasures , we need to comprehensively consider the following elements in order to find the best one: