淬火、渗氮、镀铬
淬火液的配比

淬火液的配比淬火油是一种工艺用油,用做淬火介质。
淬火油必须具备以下特性:特性介绍良好的冷却性能冷却性能是淬火介质重要的性能,它的好坏直接影响到淬火零件的质量,良好的冷却性能可保证淬火后的零件具有一定的硬度和合格的金相组织,可以防止零件变形和开裂。
高闪点和燃点淬火时,油的温度会瞬时升高,如果油的闪点和燃点较低,可能发生着火现象。
因此淬火油应具有较高的闪点和燃点。
通常闪点应比使用油温要高出60-80 C。
良好的热氧化安定性淬火油长期在高温和连续作业的苛刻条件下使用,要求油品具有良好的抗氧化、抗热分解和抗老化等性能,以保证油品的冷却性能和使用寿命。
低粘度油品的粘度与它的附着量、携带损失和冷却性能有一定的关系。
在保证油品冷却性能和闪点的前提下,油品的粘度应尽可能小,这样既可以减少携带损失,又便于工件清洗。
水份含量低油品中的过量水份会影响零件的热处理质量,造成零件软点、淬裂或变形,也可能造成油品飞溅,发生事故。
因此一般规定淬火油中的含水量不超过0.05%。
其他特性除了上述特性外,淬火油还应无毒、无味、易处理、对环境无污染,并使淬火后的工件表面光亮。
其他淬火介质连介绍你见过不会变质变臭的淬火介质吗,你见过月用越好用的淬火介质吗你见过集水与油优点于一身的淬火介质吗如果你现在还在使用落伍的油,pag的传统淬火介质,保守油烟和气味的困扰,如果你想用最小的成本做最好的产品,这是您的一个选择淬火液的成分以及其性能指标热处理常用盐浴(碱浴)成分盐(碱)的配比(按重量%)熔化温度(C )使用温度(C )备注100%BaCI2 960 1100-1350常用于高温盐浴100%NaCI 808 850-1100高合金淬火加热80%BaCI2+20%NaCI 635 750-1000 50%BaCI2+50%NaCI 640 750-900常用于中温盐浴45%NaCI +55%KCI 660 720-1000 30%KCI+20%NaCI+50% BaCI2 560 580-880常用于高速钢分记级冷却21%NaCI+31%BaCI2+48%CaCI2 435 480-750用于低温盐浴回火、等温(冷却)用盐100%NaN03(另加2-4%NaOH) 317 325-600用于高速钢回火100%KNO3 337 350-600钢的分级淬火100%NaOH 322 350-500等温淬火100%KOH 360 400-550 50%KNO3+50%NaNO2 140 150-550用于合金钢冷却50%KNO3+50%NaNO3 218 260-550 80%KOH+20%NaOH(另力口10-15% 水)130 150-300用于碳钢或合金钢淬火80%KOH+14%NaNO2+6%H2O 140 150-250对于碳钢来说,盐水的硬度均匀,而且变形小一些。
淬火、渗氮、镀铬
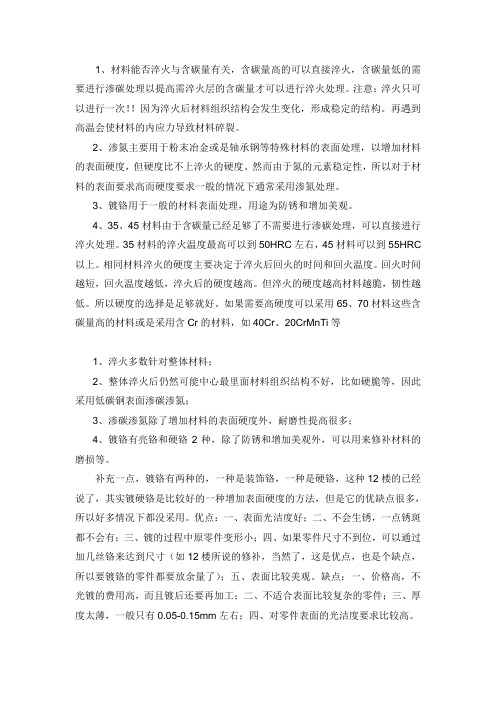
1、材料能否淬火与含碳量有关,含碳量高的可以直接淬火,含碳量低的需要进行渗碳处理以提高需淬火层的含碳量才可以进行淬火处理。
注意:淬火只可以进行一次!!因为淬火后材料组织结构会发生变化,形成稳定的结构。
再遇到高温会使材料的内应力导致材料碎裂。
2、渗氮主要用于粉末冶金或是轴承钢等特殊材料的表面处理,以增加材料的表面硬度,但硬度比不上淬火的硬度。
然而由于氮的元素稳定性,所以对于材料的表面要求高而硬度要求一般的情况下通常采用渗氮处理。
3、镀铬用于一般的材料表面处理,用途为防锈和增加美观。
4、35、45材料由于含碳量已经足够了不需要进行渗碳处理,可以直接进行淬火处理。
35材料的淬火温度最高可以到50HRC左右,45材料可以到55HRC 以上。
相同材料淬火的硬度主要决定于淬火后回火的时间和回火温度。
回火时间越短,回火温度越低,淬火后的硬度越高。
但淬火的硬度越高材料越脆,韧性越低。
所以硬度的选择是足够就好。
如果需要高硬度可以采用65、70材料这些含碳量高的材料或是采用含Cr的材料,如40Cr、20CrMnTi等1、淬火多数针对整体材料;2、整体淬火后仍然可能中心最里面材料组织结构不好,比如硬脆等,因此采用低碳钢表面渗碳渗氮;3、渗碳渗氮除了增加材料的表面硬度外,耐磨性提高很多;4、镀铬有亮铬和硬铬2种,除了防锈和增加美观外,可以用来修补材料的磨损等。
补充一点,镀铬有两种的,一种是装饰铬,一种是硬铬,这种12楼的已经说了,其实镀硬铬是比较好的一种增加表面硬度的方法,但是它的优缺点很多,所以好多情况下都没采用。
优点:一、表面光洁度好;二、不会生锈,一点锈斑都不会有;三、镀的过程中原零件变形小;四、如果零件尺寸不到位,可以通过加几丝铬来达到尺寸(如12楼所说的修补,当然了,这是优点,也是个缺点,所以要镀铬的零件都要放余量了);五、表面比较美观。
缺点:一、价格高,不光镀的费用高,而且镀后还要再加工;二、不适合表面比较复杂的零件;三、厚度太薄,一般只有0.05-0.15mm左右;四、对零件表面的光洁度要求比较高。
金属热处理,渗碳,渗氮,发黑发蓝等处理

金属热处理,渗碳,渗氮,发黑发蓝等处理金属热处理,渗碳,渗氮,发黑发蓝等处理金属热处理:1.金属热处理是将金属工件放在一定的介质中加热到适宜的温度,并在此温度中保持一定时间后,又以不同速度冷却,通过改变金属材料表面或内部的组织结构来控制其性能的一种工艺。
2.金属热处理是机械制造中的重要工艺之一,与其他加工工艺相比,热处理一般不改变工件的形状和整体的化学成分,而是通过改变工件内部的显微组织,或改变工件表面的化学成分,赋予或改善工件的使用性能。
其特点是改善工件的内在质量,而这一般不是肉眼所能看到的。
3.钢铁的热处理是金属热处理的主要内容。
另外,铝、铜、镁、钛等及其合金也都可以通过热处理改变其力学、物理和化学性能,以获得不同的使用性能。
4.热处理工艺一般包括加热、保温、冷却三个过程,有时只有加热和冷却两个过程。
这些过程互相衔接,不可间断。
5.加热是热处理的重要工序之一。
金属热处理的加热方法很多,最早是采用木炭和煤作为热源,进而应用液体和气体燃料。
电的应用使加热易于控制,且无环境污染。
利用这些热源可以直接加热,也可以通过熔融的盐或金属,以至浮动粒子进行间接加热。
6.金属加热时,工件暴露在空气中,常常发生氧化、脱碳(即钢铁零件表面碳含量降低),这对于热处理后零件的表面性能有很不利的影响。
金属通常应在可控气氛或保护气氛中、熔融盐中和真空中加热,也可用涂料或包装方法进行保护加热。
7.加热温度是热处理工艺的重要工艺参数之一,选择和控制加热温度,是保证热处理质量的主要问题。
加热温度随被处理的金属材料和热处理的目的不同而异,但一般都是加热到相变温度以上,以获得高温组织。
另外转变需要一定的时间,因此当金属工件表面达到要求的加热温度时,还须在此温度保持一定时间,使内外温度一致,使显微组织转变完全,这段时间称为保温时间。
采用高能密度加热和表面热处理时,加热速度极快,一般就没有保温时间,而化学热处理的保温时间往往较长。
8.冷却也是热处理工艺过程中不可缺少的步骤,冷却方法因工艺不同而不同,主要是控制冷却速度。
热处理方法的代号标注方法和含义
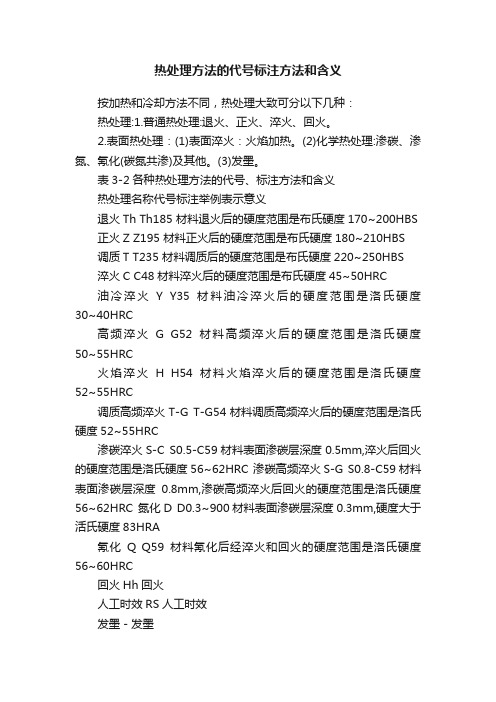
热处理方法的代号标注方法和含义
按加热和冷却方法不同,热处理大致可分以下几种:
热处理:1.普通热处理:退火、正火、淬火、回火。
2.表面热处理:(1)表面淬火:火焰加热。
(2)化学热处理:渗碳、渗氮、氰化(碳氮共渗)及其他。
(3)发墨。
表3-2各种热处理方法的代号、标注方法和含义
热处理名称代号标注举例表示意义
退火Th Th185 材料退火后的硬度范围是布氏硬度170~200HBS 正火Z Z195 材料正火后的硬度范围是布氏硬度180~210HBS
调质T T235 材料调质后的硬度范围是布氏硬度220~250HBS
淬火C C48材料淬火后的硬度范围是布氏硬度45~50HRC
油冷淬火Y Y35材料油冷淬火后的硬度范围是洛氏硬度30~40HRC
高频淬火G G52材料高频淬火后的硬度范围是洛氏硬度50~55HRC
火焰淬火H H54材料火焰淬火后的硬度范围是洛氏硬度52~55HRC
调质高频淬火T-G T-G54材料调质高频淬火后的硬度范围是洛氏硬度52~55HRC
渗碳淬火S-C S0.5-C59材料表面渗碳层深度0.5mm,淬火后回火的硬度范围是洛氏硬度56~62HRC 渗碳高频淬火S-G S0.8-C59材料表面渗碳层深度0.8mm,渗碳高频淬火后回火的硬度范围是洛氏硬度56~62HRC 氮化D D0.3~900材料表面渗碳层深度0.3mm,硬度大于活氏硬度83HRA
氰化Q Q59材料氰化后经淬火和回火的硬度范围是洛氏硬度56~60HRC
回火Hh回火
人工时效RS人工时效
发墨-发墨。
常见金属表面处理的种类及工艺、作用

金属表面处理的种类及工艺1、表面处理工艺简介:利用现代物理、化学、金属学和热处理等学科的技术来改变零件表面的状况和性质,使之与心部材料作优化组合,以达到预定性能要求的工艺方法,称为表面处理工艺。
表面处理的作用:提高表面耐蚀性和耐磨性,减缓、消除和修复材料表面的变化及损伤;使普通材料获得具有特殊功能的表面;节约能源、降低成本、改善环境。
2、金属表面处理工艺分类:总共可以分为4大类:表面改性技术、表面合金化技术、表面转化膜技术和表面覆膜技术。
一、表面改性技术1、表面淬火表面淬火是指在不改变钢的化学成分及心部组织情况下,利用快速加热将表层奥氏体化后进行淬火以强化零件表面的热处理方法。
表面淬火的主要方法有火焰淬火和感应加热,常用的热源有氧乙炔或氧丙烷等火焰等。
2、激光表面强化激光表面强化是用聚焦的激光束射向工件表面,在极短时间内将工件表层极薄的材料加热到相变温度或熔点以上的温度,又在极短时间内冷却,使工件表面淬硬强化。
激光表面强化可以分为激光相变强化处理、激光表面合金化处理和激光熔覆处理等。
激光表面强化的热影响区小,变形小,操作方便,主要用于局部强化的零件,如冲裁模、曲轴、凸轮、凸轮轴、花键轴、精密仪器导轨、高速钢刀具、齿轮及内燃机缸套等。
3、喷丸喷丸强化是将大量高速运动的弹丸喷射到零件表面上,犹如无数个小锤锤击金属表面,使零件表层和次表层发生一定的塑性变形而实现强化的一种技术。
作用:提高零件机械强度以及耐磨性、抗疲劳和耐蚀性等;用于表面消光、去氧化皮;消除铸、锻、焊件的残余应力等。
4、滚压滚压是在常温下用硬质滚柱或滚轮施压于旋转的工件表面,并沿母线方向移动,使工件表面塑性变形、硬化,以获得准确、光洁和强化的表面或者特定花纹的表面处理工艺。
应用:圆柱面、锥面、平面等形状比较简单的零件。
5、拉丝拉丝是指在外力作用下使金属强行通过模具,金属横截面积被压缩,并获得所要求的横截面积形状和尺寸的表面处理方法称为金属拉丝工艺。
QPQ技术简介
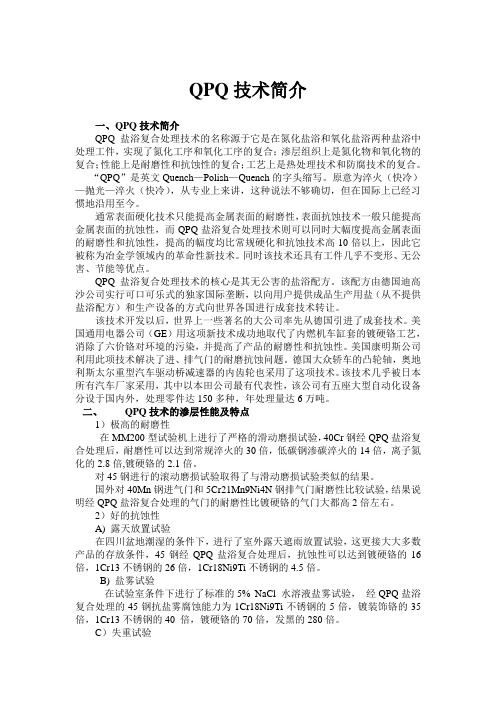
QPQ技术简介一、QPQ技术简介QPQ盐浴复合处理技术的名称源于它是在氮化盐浴和氧化盐浴两种盐浴中处理工件,实现了氮化工序和氧化工序的复合;渗层组织上是氮化物和氧化物的复合;性能上是耐磨性和抗蚀性的复合;工艺上是热处理技术和防腐技术的复合。
“QPQ”是英文Quench—Polish—Quench的字头缩写。
原意为淬火(快冷)—抛光—淬火(快冷),从专业上来讲,这种说法不够确切,但在国际上已经习惯地沿用至今。
通常表面硬化技术只能提高金属表面的耐磨性,表面抗蚀技术一般只能提高金属表面的抗蚀性,而QPQ盐浴复合处理技术则可以同时大幅度提高金属表面的耐磨性和抗蚀性,提高的幅度均比常规硬化和抗蚀技术高10倍以上,因此它被称为冶金学领域内的革命性新技术。
同时该技术还具有工件几乎不变形、无公害、节能等优点。
QPQ盐浴复合处理技术的核心是其无公害的盐浴配方。
该配方由德国迪高沙公司实行可口可乐式的独家国际垄断,以向用户提供成品生产用盐(从不提供盐浴配方)和生产设备的方式向世界各国进行成套技术转让。
该技术开发以后,世界上一些著名的大公司率先从德国引进了成套技术。
美国通用电器公司(GE)用这项新技术成功地取代了内燃机车缸套的镀硬铬工艺,消除了六价铬对环境的污染,并提高了产品的耐磨性和抗蚀性。
美国康明斯公司利用此项技术解决了进、排气门的耐磨抗蚀问题。
德国大众轿车的凸轮轴,奥地利斯太尔重型汽车驱动桥减速器的内齿轮也采用了这项技术。
该技术几乎被日本所有汽车厂家采用,其中以本田公司最有代表性,该公司有五座大型自动化设备分设于国内外,处理零件达150多种,年处理量达6万吨。
二、QPQ技术的渗层性能及特点1)极高的耐磨性在MM200型试验机上进行了严格的滑动磨损试验,40Cr钢经QPQ盐浴复合处理后,耐磨性可以达到常规淬火的30倍,低碳钢渗碳淬火的14倍,离子氮化的2.8倍,镀硬铬的2.1倍。
对45钢进行的滚动磨损试验取得了与滑动磨损试验类似的结果。
淬火和渗氮的区别
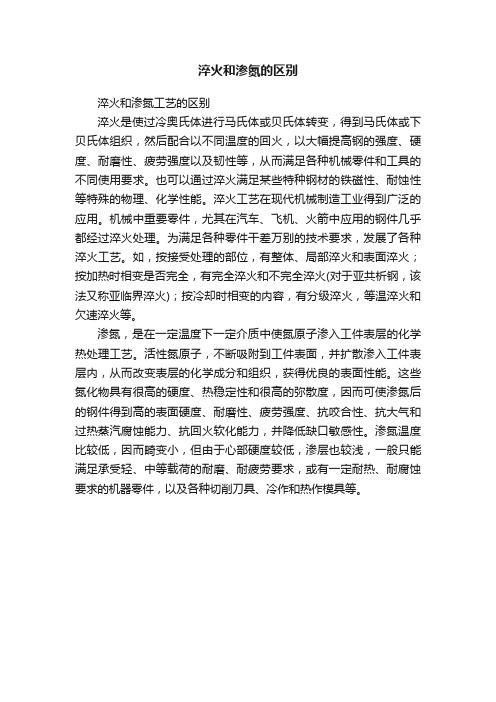
淬火和渗氮的区别
淬火和渗氮工艺的区别
淬火是使过冷奥氏体进行马氏体或贝氏体转变,得到马氏体或下贝氏体组织,然后配合以不同温度的回火,以大幅提高钢的强度、硬度、耐磨性、疲劳强度以及韧性等,从而满足各种机械零件和工具的不同使用要求。
也可以通过淬火满足某些特种钢材的铁磁性、耐蚀性等特殊的物理、化学性能。
淬火工艺在现代机械制造工业得到广泛的应用。
机械中重要零件,尤其在汽车、飞机、火箭中应用的钢件几乎都经过淬火处理。
为满足各种零件干差万别的技术要求,发展了各种淬火工艺。
如,按接受处理的部位,有整体、局部淬火和表面淬火;按加热时相变是否完全,有完全淬火和不完全淬火(对于亚共析钢,该法又称亚临界淬火);按冷却时相变的内容,有分级淬火,等温淬火和欠速淬火等。
渗氮,是在一定温度下一定介质中使氮原子渗入工件表层的化学热处理工艺。
活性氮原子,不断吸附到工件表面,并扩散渗入工件表层内,从而改变表层的化学成分和组织,获得优良的表面性能。
这些氮化物具有很高的硬度、热稳定性和很高的弥散度,因而可使渗氮后的钢件得到高的表面硬度、耐磨性、疲劳强度、抗咬合性、抗大气和过热蒸汽腐蚀能力、抗回火软化能力,并降低缺口敏感性。
渗氮温度比较低,因而畸变小,但由于心部硬度较低,渗层也较浅,一般只能满足承受轻、中等载荷的耐磨、耐疲劳要求,或有一定耐热、耐腐蚀要求的机器零件,以及各种切削刀具、冷作和热作模具等。
镀铬知识简介及镀铬分类、镀铬层厚度、硬度控制方法

镀铬知识简介及镀铬分类、镀铬层厚度、硬度控制方法镀铬知识简介及镀铬分类、镀铬层厚度、硬度控制方法-CAL-FENGHAI-(2020YEAR-YICAI)_JINGBIAN镀铬知识简介及镀铬分类、镀铬层厚度、硬度控制方法一镀铬简介镀铬属于发展较晚的工艺,早在1854年就有人从三价格槽液中镀得金属铬,1856年又发明从三价格槽液中镀铬的工艺,但是直到本世纪20年代,镀铬工艺才在国外得到广泛应用。
镀铬工艺传到我国比较晚,有关镀铬知识的介绍和应用的记载大都是在30年代初期。
我国对金属铬元素的介绍和命名直到19世纪60年代才开始进行。
二镀铬的一般特性(一)镀铬特点1.镀铬用含氧酸做主盐,铬和氧亲和力强,电析困难,电流效率低;2.铬为变价金属,又有含氧酸根,故阴极还原过程很复杂;3.镀铬虽然极化值很大,但极化度很小,故镀液的分散能力和覆盖能力很差,往往要采用辅助阳极和保护阴极;4.镀铬需用大电流密度,而电流效率很低,大量析出氢气,导致镀液欧姆电压降大,故镀铬的电压要比较高;5.镀铬不能用铬阳极,通常采用纯铅、铅锡合金、铅锑合金等不溶性阳极。
(二)镀铬过程的特异现象镀铬与其它金属电沉积相比,有如下特异现象:(1)随主盐铬酐浓度升高而电流效率下降;(2)随电流密度升高而电流效率提高;(3)随镀液温度提高而电流效率降低;(4)随镀液搅拌加强而电流效率降低,甚至不能镀铬。
上述特异现象均与镀铬阴极还原的特殊性有关。
三镀铬层的种类和标记(一)防护—装饰性镀铬防护—装饰性镀铬,俗称装饰铬。
它具有防腐蚀和外观装饰的双重作用。
为达此目的在锌基或钢铁基体上必须先镀足够厚度的中间层,然后在光亮的中间镀层上镀以~μm的薄层铬。
例如钢基上镀铜、镍层再镀铬、低锡青铜上镀铬、多层镍上镀铬、镍铁合金镀层上镀铬等等。
在现代电镀中,在多层镍上镀取微孔或微裂纹铬是降低镀层总厚度,又可获得高耐蚀性的防护—装饰体系,是电镀工艺发展的方向。
在黄铜上喷砂处理或在缎面镍上镀铬,可获得无光的缎面铬,是用作消光的防护—装饰镀铬。
- 1、下载文档前请自行甄别文档内容的完整性,平台不提供额外的编辑、内容补充、找答案等附加服务。
- 2、"仅部分预览"的文档,不可在线预览部分如存在完整性等问题,可反馈申请退款(可完整预览的文档不适用该条件!)。
- 3、如文档侵犯您的权益,请联系客服反馈,我们会尽快为您处理(人工客服工作时间:9:00-18:30)。
1、材料能否淬火与含碳量有关,含碳量高的可以直接淬火,含碳量低的需要进行渗碳处理以提高需淬火层的含碳量才可以进行淬火处理。
注意:淬火只可以进行一次!!因为淬火后材料组织结构会发生变化,形成稳定的结构。
再遇到高温会使材料的内应力导致材料碎裂。
2、渗氮主要用于粉末冶金或是轴承钢等特殊材料的表面处理,以增加材料的表面硬度,但硬度比不上淬火的硬度。
然而由于氮的元素稳定性,所以对于材料的表面要求高而硬度要求一般的情况下通常采用渗氮处理。
3、镀铬用于一般的材料表面处理,用途为防锈和增加美观。
4、3
5、45材料由于含碳量已经足够了不需要进行渗碳处理,可以直接进行淬火处理。
35材料的淬火温度最高可以到50HRC左右,45材料可以到55HRC 以上。
相同材料淬火的硬度主要决定于淬火后回火的时间和回火温度。
回火时间越短,回火温度越低,淬火后的硬度越高。
但淬火的硬度越高材料越脆,韧性越低。
所以硬度的选择是足够就好。
如果需要高硬度可以采用65、70材料这些含碳量高的材料或是采用含Cr的材料,如40Cr、20CrMnTi等
1、淬火多数针对整体材料;
2、整体淬火后仍然可能中心最里面材料组织结构不好,比如硬脆等,因此采用低碳钢表面渗碳渗氮;
3、渗碳渗氮除了增加材料的表面硬度外,耐磨性提高很多;
4、镀铬有亮铬和硬铬2种,除了防锈和增加美观外,可以用来修补材料的磨损等。
补充一点,镀铬有两种的,一种是装饰铬,一种是硬铬,这种12楼的已经说了,其实镀硬铬是比较好的一种增加表面硬度的方法,但是它的优缺点很多,所以好多情况下都没采用。
优点:一、表面光洁度好;二、不会生锈,一点锈斑都不会有;三、镀的过程中原零件变形小;四、如果零件尺寸不到位,可以通过加几丝铬来达到尺寸(如12楼所说的修补,当然了,这是优点,也是个缺点,所以要镀铬的零件都要放余量了);五、表面比较美观。
缺点:一、价格高,不光镀的费用高,而且镀后还要再加工;二、不适合表面比较复杂的零件;三、厚度太薄,一般只有0.05-0.15mm左右;四、对零件表面的光洁度要求比较高。
渗氮,表面感应淬火,这是两条路线,都可以的。
渗氮硬度更高,变形小,但深度只有0.4~0.6,若要修磨就被磨掉了。
表面淬火变形大要上磨床磨,但深度可大。
不同的制造厂各有各的偏好。