金属表面划伤原因及修复方法
金属切削机床常见研伤的原因分析及排除

・
设 备s维修 ・
金属切削机床常见研伤的原因分析及排除
镇 江煤矿专 用设备 J
( 江苏
220 ) 冯 高 头 105
王 卫 彬
广 州 白云 电 器 设 备 有 限 公 司
( 14 0 506 )
机 床 上 一些 做 相对 滑 动 的零 、部件 ,如滑 板 与 面 )上 形 成划 痕 和 沟槽 ,也就 是 形成 粘 着磨 损 型 的
( )咬 死 当摩 擦 副 表面 瞬 时 闪发 的温 度相 当 4 高 、粘 着 区较 大 、粘 着 点 的强 度 也相 当高 ,粘结 不 能从 基 体 上 剪 切 掉 , 以致 造 成 相 对 运 动 中止 的 现
个摩 擦 表 面 接 触 时 ,实 际 上 是 两 个摩 擦 表 面 的 凸 峰 相 互 接 触 。
由于 接 触 应 力 很 大 , 以 致 产 生
象 咬死是 研 伤 中最 严 重 的一 种 。例 如轴 与 滑动 轴
承 当润 滑不 良而 出现 的 “ 轴 ” 抱 ,大 都 会 产 生 这 种 研 伤 ;大 型机 床 的导 轨 缺油 引 起 的大 面积 研 伤也 会
产生 咬死 。
弹 、塑 性 变 形 ,使 接 触 面 积 增 大 ,直 到 能 够 承 受 全 部 载 荷 时 两 个 金 属 表 面
磨 损 型 研 伤 。现 就这 两 种类 型 研 伤产 生 的原 因 、预 浅 的部 分 ,破坏 方 式 是 沿 运 动 方 向产 生 细小 划 痕 ,
பைடு நூலகம்
有 时硬 金属 表 面上 也有 可 能 划 伤 。最 常见 的是 在 机 床运 行 初期 、轴 和滑 动轴 承 处 于磨 合期 的磨损 。
不锈钢件表面处理问题及方法
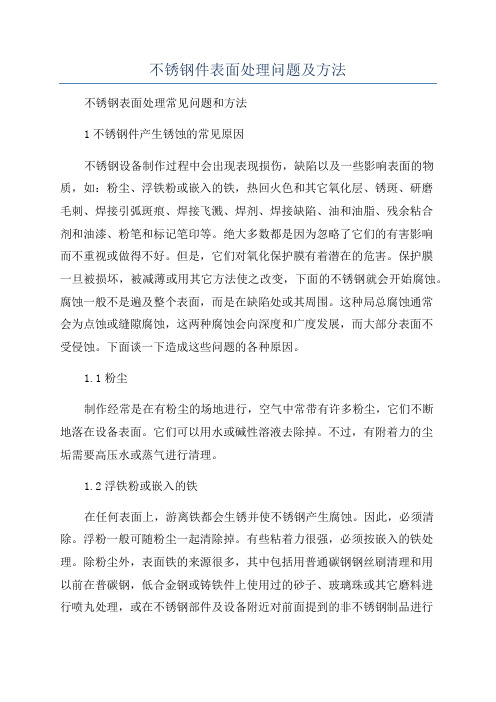
不锈钢件表面处理问题及方法不锈钢表面处理常见问题和方法1不锈钢件产生锈蚀的常见原因不锈钢设备制作过程中会出现表现损伤,缺陷以及一些影响表面的物质,如:粉尘、浮铁粉或嵌入的铁,热回火色和其它氧化层、锈斑、研磨毛刺、焊接引弧斑痕、焊接飞溅、焊剂、焊接缺陷、油和油脂、残余粘合剂和油漆、粉笔和标记笔印等。
绝大多数都是因为忽略了它们的有害影响而不重视或做得不好。
但是,它们对氧化保护膜有着潜在的危害。
保护膜一旦被损坏,被减薄或用其它方法使之改变,下面的不锈钢就会开始腐蚀。
腐蚀一般不是遍及整个表面,而是在缺陷处或其周围。
这种局总腐蚀通常会为点蚀或缝隙腐蚀,这两种腐蚀会向深度和广度发展,而大部分表面不受侵蚀。
下面谈一下造成这些问题的各种原因。
1.1粉尘制作经常是在有粉尘的场地进行,空气中常带有许多粉尘,它们不断地落在设备表面。
它们可以用水或碱性溶液去除掉。
不过,有附着力的尘垢需要高压水或蒸气进行清理。
1.2浮铁粉或嵌入的铁在任何表面上,游离铁都会生锈并使不锈钢产生腐蚀。
因此,必须清除。
浮粉一般可随粉尘一起清除掉。
有些粘着力很强,必须按嵌入的铁处理。
除粉尘外,表面铁的来源很多,其中包括用普通碳钢钢丝刷清理和用以前在普碳钢,低合金钢或铸铁件上使用过的砂子、玻璃珠或其它磨料进行喷丸处理,或在不锈钢部件及设备附近对前面提到的非不锈钢制品进行修磨。
在下料或吊过过程中如果不对不锈钢采取保护措施,钢丝绳、吊具和工作台面上的铁很容易嵌入或玷污表面。
1.3划痕为了防止工艺润滑剂或生成物和/或污物积留,必须对划痕和其它粗糙表面进行机械清理。
1.4热回火色和其它氧化层如果在焊接或修磨过程中不锈钢在空气中被加热到一定的高温,焊缝两侧、焊缝的下表面和底部都会出现铬氧化物热回火色。
热回火色比氧化保护膜薄,而且明显可见。
颜色决定于厚度,可呈见彩虹色、蓝色、紫色到淡黄色和棕色。
较厚的氧化物一般为黑色。
它是由于在高温或长时间在较高度下停留所致。
宽厚板钢板表面划伤的原因分析及对策

设备管理与维修2019翼10(上)宽厚板钢板表面划伤的原因分析及对策潘喜贵,赵解来(华菱湘钢宽厚板厂,湖南湘潭411101)摘要:钢板表面划伤的机理及形式,分析宽厚板生产线设备运行中对钢板划伤的影响,制定并实施避免钢板划伤对策,并取得了良好效果。
关键词:钢板;表面;划伤;对策中图分类号:TG335文献标识码:BDOI :10.16621/ki.issn1001-0599.2019.10.430引言随着钢材产品供大于求状况的进一步加剧,市场的竞争日趋激烈,客户对钢材质量的要求也越来越高。
对于板材,客户以前主要关注的是钢材的内部质量,现在对钢板表面要求也非常苛刻。
由外观质量引起的非计划及质量异议逐年递增,尤其是钢板的表面划伤缺陷引起的非计划及质量异议占比较大,因此提高钢板表面质量、尤其是防止划伤,已成为非常紧迫的问题。
1钢板划伤的主要型式钢板表面划伤指钢材在轧制、矫直和输送过程中,被设备、工具刮出的单条或多条沟痕状表面缺陷,见图1。
沿纵向或横向存在于钢板表面,一般呈直线型,也有的呈曲线型,其长度、宽度、深度各异,肉眼可见底部。
划伤分热态划伤和冷态划伤,热态划伤的颜色与钢板表面颜色基本相同,冷态划伤呈金属色或浅蓝色。
根据钢板划伤的方向可分为纵向划伤和横向划伤。
2钢板划伤成因分析2.1热态划伤钢板表面热态划伤指钢板在高温状态下出现的划伤,根据宽厚板生产线流程,一般是指钢板在轧制区域即钢板上冷床之前出现的划伤,这个温度一般跃400益。
这种高温下产生的划伤,划伤沟痕表面很容易在高温下迅速氧化,致使划痕表面的颜色与钢板表面的颜色基本一致。
钢板热态划伤主要是在上冷床之前产生,热态划伤也主要跟冷床之前的设备有关。
冷床之前的设备主要有加热炉、高压水除鳞、轧机、ACC (加速冷却系统)、热矫直机、热喷码机、热分切剪、输送辊道等设备。
可根据轧制线设备的运行情况分析划伤来源。
(1)加热炉和高压水除鳞。
加热炉和高压水除鳞设备位于轧机之前,也是钢坯温度最高的时候,温度跃1000益,若设备划伤钢板表面,经过轧机反复压延之后划痕会消失,因此轧机之前的加热炉、高压水除鳞及轧机前的输送辊道对最终成品钢板不会造成划痕影响。
圆钢常见缺陷及原因

调整成品前料型正确
6
折叠
沿轧制方向呈直线状分布,外形似裂纹,边缘有时呈锯齿状,连续或断续分布,深浅不一,内有氧化铁皮,在横断面上看,一般呈折角
1、前某一道次出耳子
2、前某道次产生划伤、轴错、轧槽损坏或磨损严重、飞边等
3、原料表面有尖锐棱角或裂纹
检查前部道次料型和原料情况
消除前道次缺陷
检查轧槽磨损情况,酌情换槽
2
结疤
一般呈舌形或指甲形,宽而厚的一端和基体相连;有时其外形呈一封闭的曲线,嵌在钢材表面上。
1、前一孔型轧槽损坏破损或磨损严重。
2、外界金属落在轧件上被带入孔型,压入钢材表面。
3、前一道次轧件表面有深度较大的凹坑。
检查前一道次孔型的磨损程度及轧件表面有无大的凹坑
3
耳子
出现于成品的两旁辊缝处,呈平行于轴线的突起条状。有两侧耳子、单侧耳子、全长出耳、局部出耳和周期出耳等
1、孔型设计不良,宽展估计过小
2、成品前料型高度较大
3、成品孔辊缝小
4、终轧温度低,宽展增加
5、成品导板安装不正、尺寸大或磨损严重
6、横梁或导板盒松动
7、轧槽更换错误或轧机轴承损坏
修改孔型
压下成品前料,减小辊缝
放大成品辊缝
压K2高度
更换导轮减小夹铁宽度
固定横梁及导板盒
换槽或换辊
4
弯曲
有头部弯曲、局部弯曲、全长弯曲等
1、出口导卫安装过高或过低
2、温度不均
3、上下辊径差过大
4、连接轴丢转
5、冷床拨爪不齐
调整导卫合适
调整钢温均匀
换辊
更换连接轴
调整拨爪一致
5
扭转
绕纵轴呈螺旋状旋转
金属零件表面划伤修复方法

金属零件表面划伤修复方法
金属零件表面划伤的修复方法有多种,以下是一些常见的方法:
1. 抛光:对于较浅的划痕,可以使用抛光剂或抛光布进行抛光,这可以去除表面的划痕和瑕疵,使金属表面更加光滑。
2. 填补:对于较深的划痕,可以使用金属填补剂进行填补。
首先清洁表面,然后使用填补剂涂在划痕上,等待填补剂干燥后进行打磨或抛光,使表面恢复平滑。
3. 电镀:如果金属零件的表面是镀层的,可以通过电镀的方式对划痕进行修复。
首先清洁表面,然后使用电镀液将金属颗粒电镀到划痕处,等待干燥后进行抛光或打磨,使表面恢复光滑。
4. 喷涂:对于较大的划痕或损坏,可以使用喷涂的方式进行修复。
首先清洁表面,然后使用合适的涂层材料(如金属粉末)进行喷涂,等待干燥后进行抛光或打磨,使表面恢复光滑。
需要注意的是,不同金属材料的修复方法和效果可能有所不同,因此在实际操作时应根据具体情况选择合适的修复方法。
此外,在进行修复前应先进行试验,以确保所选方法不会对金属表面造成更大的损害。
金属表面主要缺陷定义

金属表面主要缺陷定义:模具痕:折弯等模具成型过程中在结构件表面产生的压痕、轻微凹坑等。
磨擦痕:加工过程中板材在机床台面运动过程中产生的轻微划痕,无凹入感。
运动部件摩擦痕:螺丝,旋转轴等运动部件在运动过程中和基体产生的痕迹。
焊渣:指电镀、氧化前,金属焊接时飞溅到焊缝位置以外区域的、牢固粘附在基材表面的金属点状颗粒。
烧伤:拉丝处理时因操作不当、造成零件表面过热而留下的烧蚀痕迹。
凹坑:由于基体材料缺陷、或在加工过程中操作不当等原因而在材料表面留下的小坑状痕迹。
抛光区:对基材上的腐蚀、划伤、焊接区、铆接区等部位进行机械打磨抛光后表现出的局高光泽、光亮区域及焊接的背面所呈现出的打磨痕迹。
镀前划伤:指电镀或氧化之前的基体材料上的划伤痕迹,手摸有明显的凹入感。
镀后划伤:指电镀之后因操作不当等人为造成的表面划伤痕迹。
基材花斑:电镀或氧化前因基体材料腐蚀、材料中的杂质或者材料微孔等原因所造成的、与周围材质表面不同光泽或粗糙度的斑块状花纹外观。
镀层起泡:电镀不良、或因基材原因而出现的镀层鼓起甚至脱落现象。
露白:镀锌彩色钝化膜因磨擦而被去除、露出锌层,或因缝隙截留溶液导致的无钝化膜现象,呈现为区别于周围彩色的白色。
黑点:镀锌彩色钝化膜上因初期腐蚀变化而出现的零星分散的小黑点。
雾状:镀铬、镀镍表面上的模糊、不清晰、不光亮的现象。
水印:电镀或氧化后因清洗水未及时干燥或干燥不彻底所形成的斑纹、印迹。
挂具印:电镀或者氧化时挂具和结构件接触部位局部无镀层或者膜层的现象。
指印:镀层表面的指纹等缺陷。
水纹:压铸件成形时,熔体流动产生的可见条纹。
缩水:因材料、工艺等原因使压铸件表面出现凹陷的收缩现象。
砂眼:压铸件表面的疏松针孔。
披锋:压铸件上浇口残留物取掉后的毛刺。
局部无铬层:指镀铬表面因电镀工艺的局限而在凹槽内、深孔内、折弯内角等低电位区出现铬层未电镀上的现象腐蚀:因各种原因所导致的表面金属生锈、氧化现象。
修补:因膜层损伤、轻微腐蚀等原因而用涂料所作的局部遮盖处理。
产品表面划伤分析报告

产品表面划伤分析报告1. 简介本文旨在对产品表面划伤进行分析,以帮助了解划伤的原因、特征和可能的解决方案。
通过对划伤的分析,可以更好地保护产品的外观质量,提升用户体验。
2. 划伤的定义划伤是指产品表面出现的细小划痕或磨损,常见于各种材质的产品中,如金属、塑料、玻璃等。
划伤会影响产品的外观质量,给用户带来不良的视觉体验。
3. 划伤的原因划伤的产生往往与以下几个方面有关:3.1. 不当的使用划伤可能是由于用户在使用过程中不当操作所导致。
例如,在使用金属制品时使用力度过大,或者在玻璃制品上使用尖锐物体刮擦等。
3.2. 环境因素划伤也可能是由于环境因素引起的,如灰尘、砂粒等微小颗粒的摩擦作用。
这些颗粒在产品表面移动时可能会引起划痕。
3.3. 产品质量问题有时,划伤是由于产品制造过程中的质量问题引起的。
例如,在产品生产过程中,使用了不合适的工具或材料,导致产品表面易受划伤。
4. 划伤的特征了解划伤的特征有助于判断其产生的原因,并采取相应的措施进行修复或预防。
4.1. 划痕的深度和长度划痕的深度和长度是判定划伤程度的重要指标。
浅表的划痕可能只影响表面层,而深度较大的划痕可能会损坏产品的结构。
4.2. 划伤的形状和方向划痕的形状和方向可以提供有关划伤原因的线索。
例如,直线状的划痕可能是由于尖锐物体的刮擦,而圆形的划痕可能是由于金属产品之间的碰撞。
4.3. 划伤的分布范围划伤的分布范围可以反映产品在使用过程中受到的划伤程度。
如果划痕遍布整个产品表面,则说明产品的使用寿命可能受到较大影响。
5. 解决方案针对不同原因导致的划伤,可以采取以下解决方案:5.1. 提供使用指南为了减少不当使用造成的划痕,可以向用户提供详细的使用指南,建议正确的使用方法和操作注意事项。
5.2. 提供外部保护为了防止环境因素引起的划痕,可以考虑为产品提供外部保护措施,例如使用保护套、膜等。
5.3. 改善产品质量为了避免产品质量问题导致的划伤,应该优化生产工艺和材料选择,确保产品表面的耐划性和耐磨性。
金属表面划伤原因及修复方法

淄博索雷工业设备维护技术有限公司金属表面划伤原因及修复方法关键词:金属划伤修复,金属修复,修复方法,纳米技术一、以液压缸为例介绍金属表面划伤修复液压缸划伤问题,俗称“拉缸”现象,传统方法无法实现现场修复,只能拆卸后运往生产厂家进行补焊加工或报废更换。
采用SD7101金属聚合物材料现场修复液压缸划伤,其具有超强的粘着力,极好抗压性、均衡的综合物理化学性能、良好的耐磨性。
通过现场涂抹修复,固化后回复标准尺寸,即可免机加工现场修复缸筒划伤,避免报废更换。
液压缸金属划伤原因液压缸是工程机械最主要部件,也是最易出现问题的部件,尤其是油缸内表面划伤更为普遍。
主要原因如下:1.装配过程中零件毛刺处理不干净混入异物造成的缸壁划伤。
2.划伤沟槽挤出的材料屑沫会嵌入密封件,运行时在损坏密封件工作部位,造成新划伤区域痕路。
3.活塞滑动表面面压过大造成的烧结现象因活塞杆自重作用使活塞倾斜,出现别劲现象,或者由于横向载荷等的作用,使活塞滑动表面的压力上升,将引起烧结现象。
时间延长就造成严重划伤。
4.活塞环的损坏活塞环在运行中发生破损,其碎片夹在活塞的滑动部分,造成划伤。
5.电镀硬铬层的磨损,多数是由于活塞的摩擦铁粉的研磨作用造成的,中间夹有水分时,磨损更快。
因金属的接触电位差造成的腐蚀,只发生在活塞接触到的部位,而且腐蚀是成点状发生的。
6.其它原因。
金属表面划伤修复步骤1.表面除油,将常年渗金属表面的油清洗干净。
2.用角磨机对将划伤部位表面处理,并沿缸筒壁打磨出沟槽,最好是燕尾槽。
3.用无水乙醇对修复面进行清洗。
4.将金属聚合物材料涂至整个修复部位后反复按压,确保材料填实并达到所需厚度,使之比缸筒壁表面略高。
5.卤钨灯加温固化,以缩短固化时间。
6.材料固化后,用油石沾水修复出标准面,确保密封性。
二、金属划伤修复案例欣赏三、金属划伤修复技术高分子聚合物修复技术是目前较为成熟和性价比较高的一种维修方案。
时间短、费用低、效果好是该技术的几个主要特点。
- 1、下载文档前请自行甄别文档内容的完整性,平台不提供额外的编辑、内容补充、找答案等附加服务。
- 2、"仅部分预览"的文档,不可在线预览部分如存在完整性等问题,可反馈申请退款(可完整预览的文档不适用该条件!)。
- 3、如文档侵犯您的权益,请联系客服反馈,我们会尽快为您处理(人工客服工作时间:9:00-18:30)。
淄博索雷工业设备维护技术有限公司
金属表面划伤原因及修复方法
关键词:金属划伤修复,金属修复,修复方法,纳米技术
一、以液压缸为例介绍金属表面划伤修复
液压缸划伤问题,俗称“拉缸”现象,传统方法无法实现现场修复,只能拆卸后运往生产厂家进行补焊加工或报废更换。
采用SD7101金属聚合物材料现场修复液压缸划伤,其具有超强的粘着力,极好抗压性、均衡的综合物理化学性能、良好的耐磨性。
通过现场涂抹修复,固化后回复标准尺寸,即可免机加工现场修复缸筒划伤,避免报废更换。
液压缸金属划伤原因
液压缸是工程机械最主要部件,也是最易出现问题的部件,尤其是油缸内表面划伤更为普遍。
主要原因如下:
1.装配过程中零件毛刺处理不干净混入异物造成的缸壁划伤。
2.划伤沟槽挤出的材料屑沫会嵌入密封件,运行时在损坏密封件工作部位,造成新划伤区域痕路。
3.活塞滑动表面面压过大造成的烧结现象因活塞杆自重作用使活塞倾斜,出现别劲现象,或者由于横向载荷等的作用,使活塞滑动表面的压力上升,将引起烧结现象。
时间延长就造成严重划伤。
4.活塞环的损坏活塞环在运行中发生破损,其碎片夹在活塞的滑动部分,造成划伤。
5.电镀硬铬层的磨损,多数是由于活塞的摩擦铁粉的研磨作用造成的,中间夹有水分时,磨损更快。
因金属的接触电位差造成的腐蚀,只发生在活塞接触到的部位,而且腐蚀是成点状发生的。
6.其它原因。
金属表面划伤修复步骤
1.表面除油,将常年渗金属表面的油清洗干净。
2.用角磨机对将划伤部位表面处理,并沿缸筒壁打磨出沟槽,最好是燕尾槽。
3.用无水乙醇对修复面进行清洗。
4.将金属聚合物材料涂至整个修复部位后反复按压,确保材料填实并达到所需厚度,使之比缸筒壁表面略高。
5.卤钨灯加温固化,以缩短固化时间。
6.材料固化后,用油石沾水修复出标准面,确保密封性。
二、金属划伤修复案例欣赏
三、金属划伤修复技术
高分子聚合物修复技术是目前较为成熟和性价比较高的一种维修方案。
时间短、费用低、效果好是该技术的几个主要特点。
美国索雷高分子纳米聚合物技术是由纳米无机材料、碳纳米管增强的高性能环氧双组份复合材料。
该材料最大优点是利用特殊的纳米无机材料与环氧环状分子的氧进行键合,提高分子间的键力,从而大幅提高材料的综合性能,可很好的粘着于各种金属、混凝土、玻璃、塑料、橡胶等材料。
有良好的抗高温、抗化学腐蚀性能。
同时良好的机加工和耐磨性能可以服务于金属部件的磨损再造。
各种材
料在性能上互相取长补短,产生协同效应,使复合材料的综合性能优于原组成材料。
具备极强的粘接力、机械性能、和耐化学腐蚀等性能,因而广泛应用于金属设备的机械磨损、划伤、凹坑、裂缝、渗漏、铸造砂眼等的修复以及各种化学储罐、反应罐、管道的化学防腐保护及修复。