4章 老化与防护4-疲劳老化与防护
第4章 -老化和防护2

防老剂4020(6PPD) 防老剂
N-(1,3-二甲基丁基)-N’-苯基对苯二胺 ( , 二甲基丁基 二甲基丁基) 苯基对苯二胺
防护功能介于防老剂4010和防老剂 和防老剂4010NA之间。 之间。 防护功能介于防老剂 和防老剂 之间 优秀的稳定剂; 是SBR 优秀的稳定剂; 挥发性小。 挥发性小。
§4.5 橡胶常用防老剂及选用原则
一.橡胶用防老剂分类
分类 化学结构 胺类 酚类 杂环类 其它 防护效果 抗氧 抗臭氧 抗疲劳 抗有害金属 抗紫外线
2011-1-7 1
二. 常用的橡胶防老剂
• • • 胺类防老剂 酚类防老剂 杂环及其它类防老剂
2011-1-7
2
1. 胺类防老剂
• 全面防护效果突出,品种最多。 全面防护效果突出,品种最多。 • 主要防护作用:对热氧老化、臭氧老化、重金 主要防护作用:对热氧老化、臭氧老化、 属及紫外线的催化氧化以及疲劳老化都有显著 的防护效果。 的防护效果。 • 缺点:有颜色污染性,不宜于白色或浅色橡胶 缺点:有颜色污染性, 制品。 制品。
2011-1-7 29
4. 非迁移性防老剂
永久性防老剂的特点: 难挥发、难迁移、难抽出。 永久性防老剂的特点 难挥发、难迁移、难抽出。 提高防老剂耐久性的措施: 提高防老剂耐久性的措施: 反应性防老剂-防老剂以化学键的形式与橡胶结合 ① 反应性防老剂 防老剂以化学键的形式与橡胶结合 a.在加工过程中防老剂与橡胶化学键合; 在加工过程中防老剂与橡胶化学键合; 在加工过程中防老剂与橡胶化学键合 b.在加工前将防老剂接枝到橡胶上 ; 在加工前将防老剂接枝到橡胶上 c.具有防护功能的单体与橡胶单体共聚。 具有防护功能的单体与橡胶单体共聚。 具有防护功能的单体与橡胶单体共聚 ② 高分子量防老剂
专题高分子材料老化与防老化详解演示文稿

第二十一页,共47页。
五、高分子材料老化的类型及防护措施
(2)链增长 大分子自由基R·在氧气(O2)的作用下,自动氧化生成 大分子过氧化自由基ROO·和大分子氢过氧化物ROOH,ROOH又会分解
成更多的活性自由基。
第二十二页,共47页。
五、高分子材料老化的类型及防护措施
供电子基
活泼,易被取代
氧气、臭氧、强氧化剂、腐蚀性介质
第十三页,共47页。
四一、、高分橡子胶材的料老老化化的原因
分子链结构:大分子链的弱键、薄弱环节越多越易老化;不饱和碳链高分
子比饱和碳链高分子更容易发生老化;支化的大分子比线型的大分子更容 易氧化。
硫化胶交联结构:交联键有-S-、-S2-、-SX-、-C-C-,交联键结构不同
这类抗氧剂的作用主要是与链增长自由基R·或RO2·反应,以终止链增
长过程来减缓氧化反应,该抗氧剂称为主抗氧剂。这类抗氧自由基与链增长
自由基反应的方式有加成或偶合,有电子转移或最常见的氢转移。根据它 们与自由基的作用方式不同又分为三类:氢给予体、自由基捕捉体和 电子给予体。
第二十九页,共47页。
六、抗氧剂的类型及其作用机理
➢ 老化的对象:所有的高分子原材料及其制品(包括树脂、生胶)
➢ 材料所处状态:贮存、加工或使用过程中 ➢ 老化条件:热、光、氧、臭氧和机械力等
➢ 老化表现:性能下降(拉伸强度、断裂伸长率、电绝缘性)
第十页,共47页。
三一、、高橡分胶子的材料老老化化的表现
3.2 老化的表现
(1)变软发粘 (天然橡胶老化,橡皮筋、乳胶管、乳胶手套)
可逆的结构和性能变化的现象。如行驶中轮胎、橡胶弹簧、运转中传送带和运输带等都 会发生疲劳老化。
橡胶的老化与防护概述
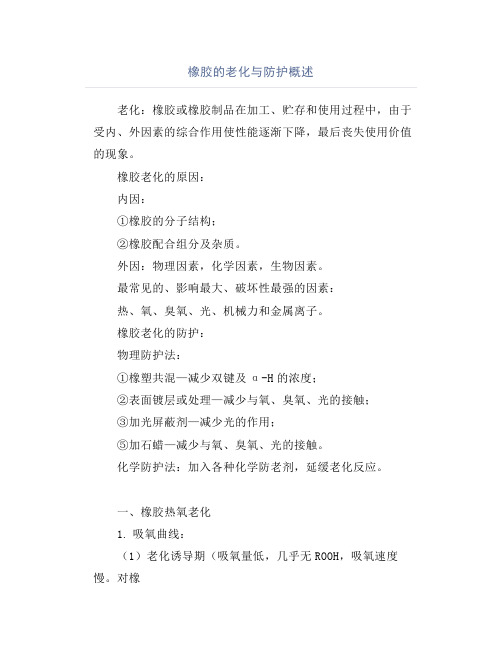
橡胶的老化与防护概述老化:橡胶或橡胶制品在加工、贮存和使用过程中,由于受内、外因素的综合作用使性能逐渐下降,最后丧失使用价值的现象。
橡胶老化的原因:内因:①橡胶的分子结构;②橡胶配合组分及杂质。
外因:物理因素,化学因素,生物因素。
最常见的、影响最大、破坏性最强的因素:热、氧、臭氧、光、机械力和金属离子。
橡胶老化的防护:物理防护法:①橡塑共混—减少双键及α-H的浓度;②表面镀层或处理—减少与氧、臭氧、光的接触;③加光屏蔽剂—减少光的作用;⑤加石蜡—减少与氧、臭氧、光的接触。
化学防护法:加入各种化学防老剂,延缓老化反应。
一、橡胶热氧老化1.吸氧曲线:(1)老化诱导期(吸氧量低,几乎无ROOH,吸氧速度慢。
对橡胶性能影响不大。
)(2)恒速吸氧阶段,吸氧量低,ROOH增加,在该阶段末期,ROOH几乎达到最高值。
(ROOH累积期)。
(3)吸氧速度激增,比诱导期大几个数量级;吸氧量急剧增加;ROOH急剧降低--自催化氧化阶段。
该阶段末期,橡胶老化,橡胶性能恶化。
(4)老化后期:恒速反应期,橡胶没有反应活性点—橡胶深度老化。
2.不饱和橡胶的热氧老化方式有两种类型(1)以分子链裂解为主—含异戊二烯单元的橡胶如NR、IR、IIR。
橡胶平均分子量下降,变软、发粘。
(2)以分子链间交联为主—含丁二烯单元的橡胶如BR、SBR、NBR。
分子量增大,变硬发脆。
3.影响橡胶热氧老化的因素1.橡胶本身的影响:(1)双键的含量及位置;(2)取代基的电子效应;(3)取代基的位阻效应;(4)橡胶的结晶性。
2.温度3.氧的浓度4.重金属离子(变价金属离子)(催化作用)5.硫化:硫化减少了α-H的量,减少了老化反应点;硫化胶的网络结构阻止O2的扩散、渗透;硫交联键有分解ROOH 的作用。
热氧老化的特点:自由基链式反应,自催化反应2.化学防护法(1)链终止型防老剂:自由基捕捉体型,电子给予体型,氢给予体型;(2)破坏ROOH型防老剂:辅助防老剂;(3)金属离子钝化剂:铜抑制剂和铁抑制剂.二、橡胶的臭氧老化及防护臭氧老化:生胶或橡胶制品在氧、臭氧、应力应变等因素共同作用下产生的一种老化现象。
第四章 橡胶的老化与防护ppt课件

发霉、失光、变色、粉化等。
4.1.2 橡胶老化的原因
ﻶ ﻶ
2020/3/30
生胶分子结构影响 工作环境影响(外部因素,包括物理、化学、生物因素)
第四章 橡胶老化与防护体系
4.1.3 橡胶老化的防护
橡胶老化是橡胶的实用价值逐渐丧失的过程,是一种复杂、不可逆的 化学反应过程。与塑料相比,因橡胶分子链易进行活泼的热运动使氧更易扩 散,橡胶更易被氧化。各种防护方法能延缓老化,延长寿命。
芳胺类和酚类化合物
含-NH或-OH基团,H很活泼,易脱出与自 由基R·或ROO结合,降低橡胶的被氧化速度。
自由基捕捉体
4.3.2 分解氢过氧化物型防老剂的作用机理
主要通过将大量氢过氧物还原为醇,阻止老化。
4.3.3 防老剂的结构与防护效能的关系 一、自由基终止型
1、胺类防老剂
2、酚类防老剂
取代基不同,抑制氧化的能力不同。
热氧老化 (<200℃,热+氧)
热降解 (> 200℃,热)
物理防护法:尽量避免橡胶与老化因 素相互作用,如橡塑共混、表面镀层、 加光屏蔽剂和石蜡等。 化学防护法:通过加入化学防老剂阻 止或延缓橡胶老化反应。
防老剂是橡胶配方中必要的组分。
4.2 橡胶的热氧老化
• 4.2.1 橡胶的氧化反应机理 自动催化自由基链反应
二、温度的影响
• 热氧老化过程中,热起着加速橡胶氧化,缩短其 寿命的作用,橡胶制品使用温度越高,越容易老 化。因此,建立在含氧气氛下的橡胶寿命与温度 的关系,对实际应用中的橡胶制品设计非常重要。
• 老化温度系数:
•
温度每升高10℃,氧化反应速度大约加快1倍。
–三、硫化的影响
交联键类型影响老化, 多硫键解离能低,容 易发生老化。
橡胶老化与防护、防老剂选择、胺类防老剂介绍

5)防老剂的环保性 6)防老剂的协同效应
在一般情况下,酚类、胺类防老剂作为第一防老剂,不单独使用,常和磷类、硫黄类防 老剂(第二防老剂)并用,利用 BHT(丁基化羟基甲苯)和磷类及硫黄类的协同效果,来防止老 化是常规做法。另外为提高耐热性,可利用第一防老剂和第二防老剂 MBI(巯基苯并咪唑)的 酸碱相互作用,来达到防老化的目的。
胶结合的牢固度更高!
2
从上图中可以看出胺类防老剂是综合效果最好的防老剂种类,现就针对胺类防老 剂做出简单的描述!
胺类防老剂分为对苯二胺类、酮/胺缩合物类,二苯胺衍生物类和萘胺类四种。 1)对苯二胺类这类防老剂可分为二烷基、烷基/芳基、二芳基对苯二胺类。 从防老化的速效性,抗臭氧性(静态)的功能上考虑,二烷基>烷基/芳基>二芳基;还 有,从耐久性、耐屈挠性和耐热性上考虑,二芳基>烷基/芳基>二烷基。作为一般抗 臭氧老化剂使用时,对老化的三大因素也都有效,即所说的全能性防老剂。二烷基 类中 44PD、77PD、88PD;烷基/芳基类中 IPPD、6PPD、8PPD;二芳基类中 DP-PD、 DNPD 等市场上均有销售。从耐抽出性、耐挥发性、与橡胶的互溶性上考虑,烷 基/芳基类的 IPPD 或 6PPD 使用较多(使用烷基的倾向增大)。 一定要注意,这类防老剂对橡胶的污染性排列顺序为(二烷基>烷基/芳基>二 芳基),在硫化胶中有喷霜(特别是二芳基的 DPPD)现象。这类防老剂还具有金属钝 化剂的作用,特别是 DNPD 效果明显。另外,DTPD 从环保方面考虑,在日本已不再 生产。 2)酮/胺缩合物类 作为二氢化喹啉类防老剂,有聚合体(n2~5)的 TMDQ,单体的乙氧基取代的 EMDQ;丙酮/二苯胺类的 ADPAL(液体)ADPAR(树脂状)。 CR(氯丁橡胶)也具有耐臭氧性(静态)。不过,它会阻碍焦烧的稳定性,尤其在夏 季未硫化胶料不能存库。ETMDQ(防老剂 AW)具有较好的耐屈挠性和耐臭氧性。 对苯二胺类防老剂可以延缓臭氧龟裂的发生,而 ETMDQ 可抑制龟裂产生后的增 长(当然,再加上石蜡,三者同时并用效果最好)。但是,因为它对橡胶的污染性大,在 橡胶中的使用量正在逐步减少。ADPAL(丙酮-二苯胺液体缩合物)(防老剂))具有 良好的耐热、耐屈挠性。 3)二苯胺类衍生物
橡胶的老化与防护体系(原理)
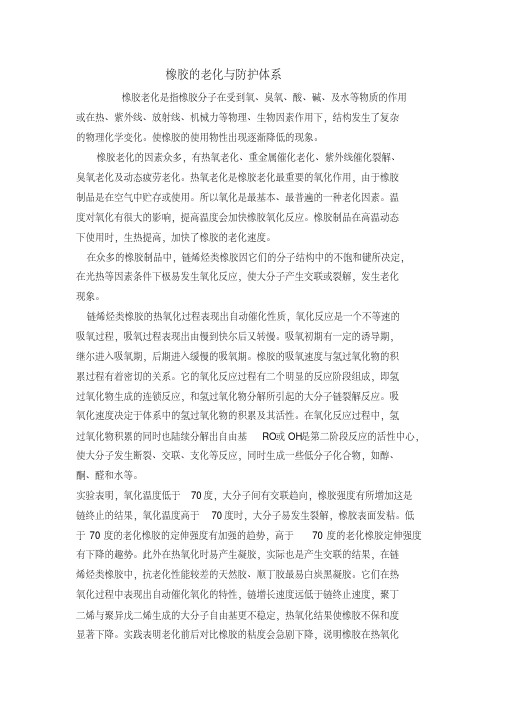
橡胶的老化与防护体系橡胶老化是指橡胶分子在受到氧、臭氧、酸、碱、及水等物质的作用或在热、紫外线、放射线、机械力等物理、生物因素作用下,结构发生了复杂的物理化学变化。
使橡胶的使用物性出现逐渐降低的现象。
橡胶老化的因素众多,有热氧老化、重金属催化老化、紫外线催化裂解、臭氧老化及动态疲劳老化。
热氧老化是橡胶老化最重要的氧化作用,由于橡胶制品是在空气中贮存或使用。
所以氧化是最基本、最普遍的一种老化因素。
温度对氧化有很大的影响,提高温度会加快橡胶氧化反应。
橡胶制品在高温动态下使用时,生热提高,加快了橡胶的老化速度。
在众多的橡胶制品中,链烯烃类橡胶因它们的分子结构中的不饱和键所决定,在光热等因素条件下极易发生氧化反应,使大分子产生交联或裂解,发生老化现象。
链烯烃类橡胶的热氧化过程表现出自动催化性质,氧化反应是一个不等速的吸氧过程,吸氧过程表现出由慢到快尔后又转慢。
吸氧初期有一定的诱导期,继尔进入吸氧期,后期进入缓慢的吸氧期。
橡胶的吸氧速度与氢过氧化物的积累过程有着密切的关系。
它的氧化反应过程有二个明显的反应阶段组成,即氢过氧化物生成的连锁反应,和氢过氧化物分解所引起的大分子链裂解反应。
吸氧化速度决定于体系中的氢过氧化物的积累及其活性。
在氧化反应过程中,氢过氧化物积累的同时也陆续分解出自由基RO或OH是第二阶段反应的活性中心,使大分子发生断裂、交联、支化等反应,同时生成一些低分子化合物,如醇、酮、醛和水等。
实验表明,氧化温度低于70度,大分子间有交联趋向,橡胶强度有所增加这是链终止的结果,氧化温度高于70度时,大分子易发生裂解,橡胶表面发粘。
低于70度的老化橡胶的定伸强度有加强的趋势,高于70度的老化橡胶定伸强度有下降的趣势。
此外在热氧化时易产生凝胶,实际也是产生交联的结果,在链烯烃类橡胶中,抗老化性能较差的天然胶、顺丁胶最易白炭黑凝胶。
它们在热氧化过程中表现出自动催化氧化的特性,链增长速度远低于链终止速度,聚丁二烯与聚异戊二烯生成的大分子自由基更不稳定,热氧化结果使橡胶不保和度显著下降。
橡胶的老化反应与防护

橡胶的老化反应与防护老化现象是指橡胶材料在加工、贮存和使用过程中,由于化学因素和物理因素的作用使其结构发生化学变化,致使性能逐渐下降,使用价值逐渐丧失的现象。
橡胶在老化过程中主要发生两种化学反应,即降解反应和交联反应(也称结构化反应)。
而且降解反应和交联反应并非彼此孤立、毫无联系的,往往这两种反应同时发生,由于橡胶分子结构的特征和老化条件的不同,使其中的一种反应占主导地位。
橡胶材料寿命受环境条件(化学因素和物理因素等)的影响极大,诸如氧、臭氧、化学介质、热、光、应力(应变)等均能加速橡胶的老化过程。
所以橡胶的老化反应是多种因素参与的复杂的化学反应。
收到普遍关注的是氧化老化、臭氧老化和疲劳老化等反应。
橡胶老化现象的宏观表现是变软发黏或变脆龟裂或发霉粉化等,造成性能下降,丧失使用价值。
橡胶的老化现象不能防止,只能采取化学的或物理的方法延缓或阻滞老化反应的进行。
凡是能够延缓或阻滞老化反应、延长橡胶使用寿命的物质通称为防老剂。
可分为化学防老剂(也称稳定剂)和物理防老剂两大类。
化学防老剂按防护功能又可以分为抗氧剂、抗臭氧剂、金属离子钝化剂、紫外光吸收剂和抗疲劳剂或屈挠龟裂抑制剂等。
随着科技的进步和人们生活水平的提高,近年来,所有先进国家不断提出新的产品安全性法规和环保法规,橡胶制品业也在其功能性要求得到满足的同时,安全性要求必将越来越受到用户重视。
思齐积累22年经验,建立了研发和测试平台,通过选材、配方实验、甚至新助剂开发合成等研究,产品达到美国和欧盟标准,并长期被多家世界知名企业采用。
未来,思齐专注食品医疗级橡胶制品解决方案,坚持客户至上,品质高扬的质量方针,达到以人为本,服务至上,创新致远,务实高效的经营理念,跟紧时代的步伐,不断满足市场的需求。
第四章橡胶的老化与防护

第四章橡胶的老化与防护橡胶及橡胶制品在成型加工、长期贮存和使用过程中,由于受到氧、臭氧、 变价金属离子以及其它化学物质的作用,加之受机械应力、光、热、高能辐射等 物理因素的影响,会逐渐变软发粘、或变硬发脆、龟裂、物性降低。
这种现象称 为老化。
橡胶(包括生胶和硫化胶)老化的原因,其内部因素是橡胶大分子中存在着弱鍵,以至于很容易受到氧的侵袭,从而破坏原橡胶的结构;而外界因素即上述化 学、物理因素加速了橡胶的老化作用。
但是,基本的原因则是氧化作用。
由于引起橡胶老化的因素很多,因而有各种各样的老化。
橡胶老化常见类型 见表4-1。
表4-1橡胶老化常见类型一、热氧老化橡胶及其制品在贮存、加工和使用时,都会受到热和氧的作用,故或快或慢 都会发生热氧老化。
热氧老化是最普遍、最基本的橡胶老化方式。
尤其是二烯类 橡胶,由于它们的大分子中,都含有不饱和双鍵,易与氧进行氧化反应。
其氧化 过程具有自动催化性质和游离基连锁反应机理。
氧与橡胶大分子的反应机理可表示如下:链引发: RH (橡胶)+02—- R∙ +HQ •链传递: R •+ Q → RQQR •+ R∙→ R-RRQQ •+ R∙→ RQQR全部氧化反应过程由两个阶段组成,即第一阶段过氧化物(RQQH 生成的连锁反应和第二阶段不断积累的氢过氧化物分解成新的游离基,导致氧化速度加快。
RQQR → RQ∙ +HQ∙RQ∙ +RH→ RQH+R H0∙ +RH→ HQH+R R ∙ +Q → RQQ橡胶氧化的结果,会导致大分子断裂,支化或交联反应,橡胶大分子结构 发生改变,导致性能下降。
当然,由于不同品种的橡胶,其化学组成及结构、双 鍵含量及其活泼程度各有差异,所以它们的氧化特性不完全一样。
高不饱和度的 天然橡胶、异戊橡胶、顺丁橡胶、丁苯橡胶和丁腈橡胶,最易氧化。
丁苯橡胶中, 如苯乙烯含量越RQQ链终止 2RQ • + RH → RQQH+R 2 ∙→ RQQR+Q多,主链上的双鍵含量也就越少,氧化速度因之减慢。
- 1、下载文档前请自行甄别文档内容的完整性,平台不提供额外的编辑、内容补充、找答案等附加服务。
- 2、"仅部分预览"的文档,不可在线预览部分如存在完整性等问题,可反馈申请退款(可完整预览的文档不适用该条件!)。
- 3、如文档侵犯您的权益,请联系客服反馈,我们会尽快为您处理(人工客服工作时间:9:00-18:30)。
孙举涛
高分子科学与工程学院 College of Polymer Science and Engineering
一.疲劳老化的概念
橡胶疲劳老化是指在交变应力或应变作用下, 橡胶的物理机械性能逐渐降低,以致最后丧 失使用价值的现象。 如轮胎的胎侧、橡胶传动带、减振橡胶制品 等有疲劳老化现象。
高分子科学与工程学院 College of Polymer Science and Engineering
三.影响疲劳老化的因素
橡胶的疲劳寿命常用试样出现损坏时所经受的周
期性应力(或应变)次数——裂纹引发实验。
试样在预定次数的应力周期中出现损坏时对应的
破坏程度——裂口增长实验。 频率和振幅 温度 空间介质 填料的活性 交联结构
高分子科学与工程学院 College of Polymer Science and Engineering
四.疲劳老化的防护
配方设计:提高硫化胶的强度。 加入化学防老剂:AW, BLE,R高分子科学与工程学院 College of Polymer Science and Engineering
高分子科学与工程学院 College of Polymer Science and Engineering
二.疲劳老化的机理
1.机械破坏理论
疲劳老化纯粹是由施加到橡胶上的机械应力
的作用结果;
化学反应只视为疲劳过程的一个因素。 该理论很难解释橡胶在真空或惰性介质中比
在空气中的疲劳寿命长这一现象。
② 在NR中加入抗氧剂或自由基捕捉剂,可使空气中的疲劳 寿命延长。
高分子科学与工程学院 College of Polymer Science and Engineering
应力活化
应力使主链上双键氧化反应的活化能降低。 未受应力时,双键与氧的反应活化能为21
kcal/mol;
受应力作用时,活化能降为18.1 kcal/mol。
高分子科学与工程学院 College of Polymer Science and Engineering
2.力化学理论
应力引发:应力引发加速橡胶的热氧老化。
R-R 力 2R· R· O2 + ROO· ROO· RH + ROOH + R· 实验依据:
① NR硫化胶在真空中的疲劳寿命大于空气中的疲劳寿命;
高分子科学与工程学院 College of Polymer Science and Engineering
影响疲劳老化的因素
1. 频率和振幅 频率高,应力松弛下降,易产生应力集中; 振幅大,变形大,生热高,热氧化断链增多, 疲劳老化加剧。 2. 温度 温度升高,分子链的运动性增大,应力集中下 降,应力引发断链几率下降,疲劳老化减轻; 温度升高,热机械氧化加剧,使疲劳老化加剧。 综合结果,温度升高,疲劳老化加剧。
高分子科学与工程学院 College of Polymer Science and Engineering
影响疲劳老化的因素
3.环境介质 O2加剧疲劳老化,惰性介质减轻疲劳老化。 4.填料及补强剂的活性: 活性高的容易形成应力集中点,引发疲劳破坏。 但强度高又使耐疲劳性提高。 5.橡胶的结晶性: 结晶易产生应力集中,加剧疲劳老化。 6.交联键的结构 硫交联键中多硫键耐疲劳老化性好,单硫键和双硫键 耐疲劳性差;碳碳交联键耐疲劳差。