中厚板轧制规程设计课程设计
30×2100×6000(Q215) 中厚板生产规程设计
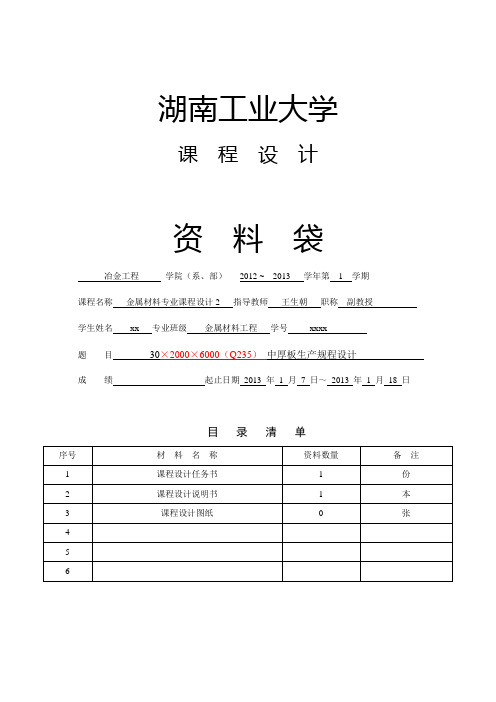
湖南工业大学课程设计资料袋冶金工程学院(系、部)2012 ~ 2013 学年第 1 学期课程名称金属材料专业课程设计2 指导教师王生朝职称副教授学生姓名xx 专业班级金属材料工程学号xxxx题目30×2000×6000(Q235)中厚板生产规程设计成绩起止日期2013 年1 月7 日~2013 年1 月18 日目录清单金属材料专业课程设计2设计说明书30×2000×6000(Q235)中厚板生产规程设计起止日期:2013 年 1 月7 日至2013 年 1 月18 日学生姓名xxx班级金属材料093班学号xxxx成绩指导教师(签字)冶金工程学院2013年1月17 日湖南工业大学课程设计任务书2012 —2013 学年第 1 学期冶金工程学院学院金属材料工程专业金属材料093 班级课程名称:金属材料专业课程设计2设计题目:30×2000×6000(Q235)中厚板生产规程设计完成期限:自2013 年 1 月7 日至2013 年 1 月17 日共两周指导教师(签字):王生朝2013年 1 月7 日系主任(签字):王生朝2013年1 月7 日冶金工程学院课程设计指导教师评阅表冶金工程学院课程设计答辩及最终成绩评定表说明:采用百分制计分,最终评定成绩=答辩评分(20%)+指导教师评分(80%),根据综合分值给出相应等级。
目录1 制定生产工艺 (1)1.1制定生产工艺 (1)1.2制定工艺制度 (1)2 制定压下规程 (1)2.1原料设计 (1)2.1.1原料的质量 (1)2.1.2原料的尺寸 (2)2.2轧制规程的设计 (2)2.2.1坯料的选择 (2)2.2.2道次压下量分配的影响因素 (2)2.2.3道次压下量的分配规律 (3)2.3轧制速度制度 (5)2.3.1轧辊的咬入和抛出转速及轧辊加速度的确定 (5)2.3.2最大轧制转速及最大轧制速度的确定 (5)2.3.3纯轧时间及间隙时间的确定 (6)2.4温度制度的确定 (8)2.5变形制度的确定 (9)2.5.1变形程度的计算 (9)2.5.2平均变形速度 (10)2.5.3变形抗力的计算 (10)2.6轧制力能参数计算 (13)2.6.1轧制压力的计算 (13)2.6.2计算各道传动力矩 (14)典型产品生产规程设计1 制定生产工艺1.1制定生产工艺选择坯料→原料清理→加热→除磷→横轧两道次(使宽度接近成品宽度)→转90°纵轧到底→矫直→冷却→表面检查→切边→定尺→表面尺寸形状检查→力学性能检测→标记→入库→发货。
中厚板轧制规程设计方法
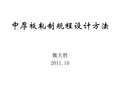
• 2.在采用控轧控冷时,要根据工艺要求, 结合温度制度、速度制度合理的安排压下 量。 • 3.双机架轧制时,要均衡分配道次和轧制 负荷,提高作业率。
三.设计步骤
• 1.根据原料尺寸和生产的钢板品种规格,在满足 轧件顺利咬入的条件下,确定轧制道次,分配各 道次的压下量和压下率。 • 2.制定速度制度,计算轧制时间和各道次的温度。 • 3.按上述确定的参数计算轧制力、轧制力矩和主 电机功率。 • 4.校核轧辊强度、传动系统强度、主电机功率。 • 5.对不合适的部分进行修正,得到合理的压下规 程。 • 中厚板轧制规程的制定流程图如下:
• 4.计算用主要数学模型 • (1)温度模型 • 轧钢生产中温度起着重要的作用,它会影响到材 料的变形抗力、工作辊热凸度等,最终影响到钢 材的性能和产品尺寸精度。因此必须计算不同阶 段的轧件温度。 • 轧钢生产时轧件的温度随着时间会发生变化: 有热量损失:如热辐射;热对流;水冷却;工作 辊间的热传导等,导致钢材温度降低。 有热量增加:如机械塑性加工热;钢板和工作辊 间的摩擦热等,导致钢材温度上升。 • 为了方便计算可以做如下假设: 宽度方向和轧制方向的热流量可以忽略,只考虑 厚度方向的热流量; 轧件的长度方向温度是光滑的变量;
• 1.轧制过程分为三个阶段 • ⑴成形阶段。 压下量主要考虑坯料纵横轧 制比 对坯料成形的矩形化影响;为横轧提供尺寸精度 的保证;轧制长度要考虑能转钢。 • ⑵展宽阶段。 压下量主要考虑宽度控制;考虑性 能控制,在可能情况下,尽量采用大压下量。 • ⑶伸长阶段 • ①前半道次。在设备能力允许的条件下,采 用大压下量。 • ②后半道次。考虑板形和厚度精度,一般采 用恒比例凸度优先的原则控制压下量;采用液压 弯辊时,可根据弯辊的能力设定压下量。
二.轧制规程设计原则
中厚板压下规程设计..
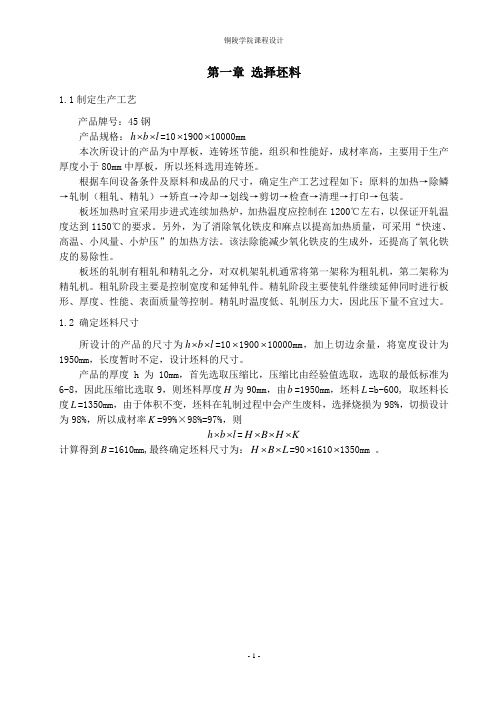
第一章选择坯料1.1制定生产工艺产品牌号:45钢产品规格:l⨯=10⨯1900⨯10000mmbh⨯本次所设计的产品为中厚板,连铸坯节能,组织和性能好,成材率高,主要用于生产厚度小于80mm中厚板,所以坯料选用连铸坯。
根据车间设备条件及原料和成品的尺寸,确定生产工艺过程如下:原料的加热→除鳞→轧制(粗轧、精轧)→矫直→冷却→划线→剪切→检查→清理→打印→包装。
板坯加热时宜采用步进式连续加热炉,加热温度应控制在1200℃左右,以保证开轧温度达到1150℃的要求。
另外,为了消除氧化铁皮和麻点以提高加热质量,可采用“快速、高温、小风量、小炉压”的加热方法。
该法除能减少氧化铁皮的生成外,还提高了氧化铁皮的易除性。
板坯的轧制有粗轧和精轧之分,对双机架轧机通常将第一架称为粗轧机,第二架称为精轧机。
粗轧阶段主要是控制宽度和延伸轧件。
精轧阶段主要使轧件继续延伸同时进行板形、厚度、性能、表面质量等控制。
精轧时温度低、轧制压力大,因此压下量不宜过大。
1.2 确定坯料尺寸所设计的产品的尺寸为l⨯=10⨯1900⨯10000mm,加上切边余量,将宽度设计为bh⨯1950mm,长度暂时不定,设计坯料的尺寸。
产品的厚度h为10mm,首先选取压缩比,压缩比由经验值选取,选取的最低标准为6-8,因此压缩比选取9,则坯料厚度H为90mm,由b=1950mm,坯料L=b-600, 取坯料长度L=1350mm,由于体积不变,坯料在轧制过程中会产生废料,选择烧损为98%,切损设计为98%,所以成材率K=99%×98%=97%,则h⨯⨯=KblH⨯⨯⨯HB计算得到B=1610mm,最终确定坯料尺寸为:L⨯=90⨯1610⨯1350mm 。
H⨯B第二章变形量分配2.1 确定轧制方法先经过二辊轧机纵轧一道,在不考虑切边的情况下,使板坯长度等于成品宽度,然后转90°横轧到所需规格。
2.2 确定道次压下量坯料尺寸:LBH⨯⨯ =90⨯1680⨯1350mm,则总的压下量为90-10=80mm。
毕业设计(论文)-16MnR_中厚板轧制规程制定

攀枝花学院学生课程设计(论文)题目:16MnR中厚板轧制规程制定学生姓名:学号:200911101052所在院(系):材料工程学院专业:材料成型及控制工程班级: 2011级压力加工班指导教师:肖玄职称:讲师2014年10 月13 日攀枝花学院教务处制攀枝花学院本科学生课程设计任务书目录1 绪论 (5)2中厚板生产工艺 (6)2.2中厚板生产工艺流程的制订 (7)2.3 中厚板生产工艺流程 (7)2.3.1坯料 (7)2.3.1.1坯料的选择 (7)2.3.1.2 铸坯的材质 (8)2.3.1.3 铸坯检查与清理 (8)2.3.2坯料加热 (8)2.3.2.1 加热炉选择 (8)2.3.2.2加热温度 (9)2.3.2.3 加热速度 (9)2.3.2.4 加热时间 (9)2.3.2.5保温时间 (9)2.3.2.6 燃料选择 (10)2.3.3 轧制 (10)2.3.3.1 除鳞 (10)2.3.3.2 粗轧 (10)2.3.3.3 精轧 (11)2.3.4 中厚板轧后冷却 (11)2.3.4.1 冷却方式 (11)2.3.4.2 冷床 (12)2.3.5 精整及热处理 (13)2.3.5.1 热处理 (13)2.3.5.2 矫直 (13)2.3.5.3 翻板、表面检查及修磨 (13)2.3.5.4 划线与剪切 (13)2.3.5.5 钢板的标志与包装 (14)2.3.5.6 钢板的质量检验 (14)3 总结 (15)参考文献 (16)1 绪论中厚板是指厚度4.5-25.0mm的钢板,主要用于制造石油、化工气体分离和气体储运的压力容器和其它类似设备,一般工作压力在常压到320kg/cm2甚至到630kg/cm2,温度在 -20-450°C范围内工作,要求容器钢板除具有一定强度和良好塑性和韧性外,还必须有较好冷弯和焊接性能,如:Q245R 、Q345R、14Cr1MoR、15CrMoR等。
中厚板轧制规程设计课程设计

前言板钢轧制制度的确定要求充分发挥设备潜力、提高产量、保证制度,并且操作方便、设备安全。
合理的轧制规程设计必须满足下列原则和要求:在设备允许的条件下尽量提高产量,充分发挥设备潜力提高产量的途径不外是提高压下量、减少轧制道次、确定合理速度规程、缩短轧制周期、提高作业率、合理选择原料增加坯重等。
在保证操作稳定的条件下提高质量,为保证钢板操作的稳定,要求工作辊缝成凸型,而且凸型值愈大操作愈稳定。
压下规程是钢板轧制制度中最基本的核心内容,它直接关系着轧机的产量和产品的质量。
轧制制度中得其他内容如温度制度、速度制度都是以压下制度为核心展开的。
反过来,温度制度、速度制度也影响到压下速度。
目录1·制定生产工艺和工艺制度…………………………………………………………1·1制定生产工艺流程……………………………………………………………1·2制定生产工艺制度……………………………………………………………2·压下规程制定……………………………………………………………………2·1坯料的选择………………………………………………………………………2·2确定轧制方法……………………………………………………………………2·3轧制道次的确定,分配各道次压下量…………………………………………2·4咬入能力的校核…………………………………………………………………3·速度制度确定…………………………………………………………………………4·温度制度确定…………………………………………………………………………5·压下规程表的制定……………………………………………………………………6·各道次变形程度和变形速率的制定…………………………………………………6.1 变形程度的确定…………………………………………………………………6.2 变形速率的确定…………………………………………………………………7·轧制压力的制定…………………………………………………………………………7.1 变形抗力的确定…………………………………………………………………7.2 平面变形抗力的确定……………………………………………………………7.3 计算平均压力p…………………………………………………………………7.4 轧制压力的确定…………………………………………………………………8·电机输出力矩的制定…………………………………………………………8.1 传动力矩的计算………………………………………………………8.2 附加摩擦力矩的确定…………………………………………………8.3 空转力矩的计算………………………………………………………8.4 动力矩的计算…………………………………………………………8.5 电机输出力矩的计算…………………………………………………8.6 电机额定力矩的计算…………………………………………………9·电机的校核…………………………………………………………………9.1 主电机能力的限制…………………………………………………9.2 各机架电机输出力矩等效力矩的计算……………………………9.3 校核各机架的电机输出力矩………………………………………9.4 校核各机架的电机输出力矩………………………………………10·电机输出负荷图……………………………………………………………10.1 速度制度图………………………………………………………10.2 电机负荷图………………………………………………………参考文献…………………………………………………………………………………1·制定生产工艺和工艺制度1·1制定生产工艺选择坯料→原料清理→加热→除磷→纵轧到底→矫直→冷却→表面检查→切边→定尺→表面尺寸形状检查→力学性能检测→标记→入库→发货。
中厚板生产压下规程课程设计概论
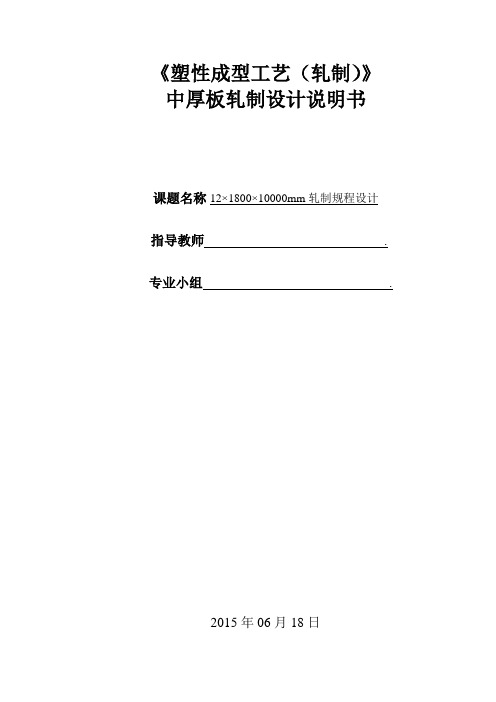
《塑性成型工艺(轧制)》中厚板轧制设计说明书课题名称12×1800×10000mm轧制规程设计指导教师. 专业小组.2015年06月18日目录第一章制定生产工艺及工艺制度 ........................................................... - 3 -一、制定生产工艺及工艺制度 ............................................................................... - 3 -二、坯料选择 ........................................................................................................... - 3 -三、中厚板压下量 ................................................................................................... - 3 -第二章设计变形工具................................................................................ - 5 -一、设计二辊 ........................................................................................................... - 5 -二、设计四辊 ........................................................................................................... - 5 -第三章计算力能参数................................................................................ - 7 -一、选择速度图 ....................................................................................................... - 7 -二、设计轧制速度(n1、n2、n3、a、b)....................................................... - 7 -三、速度图 ............................................................................................................... - 7 -四、计算各道次时间 ............................................................................................... - 7 -五、计算各道次轧制温度 ....................................................................................... - 8 -六、计算各道次变形抗力 ....................................................................................... - 9 -七、选用Sims公式计算各道次轧制力 ................................................................. - 9 -第四章轧辊强度校核............................................................................... - 11 -一、二辊轧机强度校核 ......................................................................................... - 11 -二、四辊轧机强度校核 ......................................................................................... - 12 -第五章主电机容量校核.......................................................................... - 14 -一、绘制力矩图 ..................................................................................................... - 14 -二、计算各机架电机最大输出力矩及等效力矩 ................................................. - 15 -三、校核各机架主电机容量 ................................................................................. - 16 -参考文献.................................................................................................... - 23 -第一章制定生产工艺及工艺制度一、制定生产工艺及工艺制度1.制定生产工艺选择坯料→原料清理→加热→除鳞→纵轧一道(使长度接近成品宽度)→转90°横轧到底→矫直→冷却→表面检查→切边→定尺→表面尺寸形状检查→力学性能试验→标记→入库。
中厚板生产课程设计指导书
目录1 产品标准和技术要求1.1.1钢材的尺寸、外形及允许偏差钢板和钢带的尺寸、外形及允许偏差见国标GBT/709-2006《热轧钢板和钢带的尺寸、外形、重量及允许偏差》(国标可从网上下载,下同)。
1.1.2技术要求合金牌号和化学成分可查国标,如碳素结构钢可查GB/T700-2006,低合金结构钢可查GB/T1591,优质碳素结构钢 GB/T 699-1999等另外,技术要求可查找GB 3524-2005《碳素结构钢和低合金结构钢热轧钢带》,GB/T4237-2007《不锈钢热轧钢板和钢带》,GB/T8749-2008《优质碳素结构热轧钢带》等。
(1)钢的牌号、化学成分和力学性能见表1-6。
2 生产工艺流程及主要设备参数2.1生产工艺流程根据车间设备条件及原料和成品的尺寸,生产工艺过程一般如下:原料的加热→除鳞→轧制(粗轧、精轧)→矫直→冷却→划线→剪切→检查→清理→打印→包装。
板坯的轧制有粗轧和精轧之分,但粗轧与精轧之间无明显的划分界限。
在单机架轧机上一般前期道次为粗轧,后期道次为精轧;对双机架轧机通常将第一架称为粗轧机,第二架称为精轧机。
粗轧阶段主要是控制宽度和延伸轧件。
精轧阶段主要使轧件继续延伸同时进行板形、厚度、性能、表面质量等控制。
精轧时温度低、轧制压力大,因此压下量不宜过大。
中厚板轧后精整主要包括矫直、冷却、划线、剪切、检查及清理缺陷,必要时还要进行热处理及酸洗等,这些工序多布置在精整作业线上,由辊道及移送机纵横运送钢板进行作业,且机械化自动化水平较高。
2.2 主要生产工艺(1)加热板坯加热目的:中厚板加热目的是提高钢的塑性,降低变形抗力,利于轧制;生成表面氧化铁皮,去除表面缺陷;加热到足够高的温度,使轧制过程在奥氏体化温度区域内完成;在可能的下并可以溶解在后阶段析出的氮化物和碳化物。
一般厚板加热炉的型式有两种:连续式和半连续式。
比较而言,连续式加热炉的产量高、热效率高,装入,抽出方便间歇式加热炉产量一般在10~20t/h,热效率也低。
板带钢轧制工艺课程设计(新)
板带钢轧制工艺课程设计(新)2板带钢轧制工艺课程设计2.1《中厚板带轧制技术》课程设计大纲2.1.1课程设计目的及基本要求本课程设计是学生在学习了板带材轧制工艺理论课程后的一个重要的独立实践教学环节。
其目的是培养学生在一定条件下,结合工程实践,尝试制定中厚板、热带带钢或冷轧带钢的轧制工艺体系。
通过培训,学生可以更好地将理论与实践相结合,培养综合运用所学理论知识分析和解决实际工程问题的能力,帮助学生巩固、深化和拓展知识,获得更全面的设计培训。
为毕业设计和实际工程设计打下基础。
本课程设计基本要求是学生在指导老师下达的设计任务书的基础上,理论联系实际,确定板带钢轧制方式,初步拟定轧制道次及道次变形量,通过运用所学相关理论知识对拟定的压下制度进行计算与校验,其间涉及板带钢轧制温度制度、速度制度、张力制度与辊型制度等的制订,并最终完善板带钢压下制度的修正与制订。
2.1.2课程设计内容和任务板带钢轧制工艺制度制订的内容主要包括压下制度、速度制度、温度制度、张力制度及辊型制度等。
压下制度即压下规程或轧制规程,是板带钢轧制工艺制度的制订的核心内容。
其中压下制度必然影响到速度制度、温度制度和张力制度,而压下制度与辊型制度决定着板带轧制时的辊缝大小和形状。
压下系统的内容包括轧制方式(中厚板生产)、轧制孔型次数、孔型压下率(率)等。
速度制度的内容包括主电机传动方式、各道次轧制时的咬入(穿带)速度、抛出(甩尾)速度、稳定轧制速度(或最大转速)等。
该温度系统针对热轧板带的生产,包括起始轧制温度、孔型轧制温度、终轧温度、卷取温度等,以及轧制持续时间、间隙时间和冷却速度的确定。
张力制度针对冷轧带钢生产,其内容包括连轧机机架间张力、开卷(卷取)机与轧机间的张力的确定。
辊型制度的内容包括板带轧机机整个辊系总的辊型值大小的确定、辊型值的分配,轧辊辊型曲线的选择、换辊制度及新型板形轧机(如cvc轧机)辊型曲线的确定等。
中厚板带轧制工艺课程设计作业由讲师发布。
2[1].4 中厚钢板轧机压下规程设计
结 合 以 知 识 讲 解
1. 制定压下规程的方法:理论方法和经验方法(常用经验方法) 。 前 所 学
教
学
过
程
及
教
学
内
容
方法手段
mm,精轧机φ 1020/2000×3500mm,精轧机最大允许轧制力为 6000t, 轧制力矩为 2×280t-m,主电机功率为 2×5750kw,转速为 0-50- 120prm,额定转速下的过载系数为 2.5,开轧温度为 1150℃,进入 精轧机前待温到 900℃,此时轧件尺寸为 90×3150×3784mm。制定 精轧机的压下规程。 解: 1. 确定轧制方法。先横轧达到宽度后转 90°进行纵轧,进入精轧 机后全部采用纵轧。 2. 按经验分配压下量,例表。再进行校核修订。 3. 校核咬入能力 。 热轧时最大咬入角为 15°~20°, 表中各道咬 入角均小于 15°~20°,咬入不成问题。 4. 确定各道的轧制速度。 采用梯形速度制度。将各道轧制速度和选取的间隙时间列于表中。 5. 确定轧件在各道中的轧制时间。 轧件在每道中的轧制时间由道次间隙时间、升速轧制时间、匀速轧 制时间、减速轧制时间组成,分别计算。 6. 轧制温度的确定。 7. 计算各道次的变形程度,列于表中。 8. 计算各道的平均变形速度,列于表中。 9. 计算各道的平均单位压力。 10.计算各道的轧制压力。 11.校核轧辊设备强度。 12.计算各道的传动力矩。 13.作出各道的电机力矩图。 (校核电机的过载能力和发热能力) 14.进行修订。
16839523.doc 第 2 页 共 8 页
结 合 原 理 知 识 讲解
教
学
过
程
及
教
学
材料成型课程设计——热轧中厚板工艺设计
材料成型课程设计——中厚板工艺设计指导老师:钱健清姓名:许天成学号: 109024076班级:型103专业:材料成型及控制工程2014 年 1月 13 日安徽工业大学目录一. 题目及要求二. 设计目的三. 已知条件四. 基本要求五. 设计说明书(一)产品技术要求及步骤(二)工艺流程图(三)轧制规程设计3.1 轧制方法3.2 安排轧制规程3.3 校核咬入能力3.4 确定速度制度3.5 确定轧制延续时间3.6 轧制温度的确定3.7 计算各道的变形程度3.8 计算各道的平均变形速度3.9 求各道的变形抗力3.10 计算各道的平均单位压力P及轧制力P3.11 计算各道总压力3.12 计算传动力矩(四)强度校核(五)电机功率校核(六)参考文献(七)车间平面布置图六.总结一、题目及要求题目:热轧中厚板工艺设计,使成品尺寸规格为25*2500mm课程名称:材料成型课程设计课程类型:必修课教学对象:材料成型专业本科生二、设计目的《材料成型课程设计》是材料成型专业必修课之一,是课程教学的一个重要环节。
其轧钢方向的课程设计要求达到以下目的:1)把《塑性工程学》、《塑性加工原理》、《塑性加工车间设计》、《孔型设计》等专业课程中所学的知识在实际设计工作中综合加以运用,巩固所学的专业知识,提高对专业知识和相关技能的综合运用能力。
2)本次设计是毕业设计前的最后一个教学环节,为进一步培养学生工程设计的独立工作能力,团队协作意识,树立正确的设计思想,掌握工艺设计的基本方法和步骤,为毕业设计工作打下良好的基础。
三、已知条件主要设备参数项目粗轧机精轧机轧机型式四辊可逆轧机PC轧机工作辊辊身尺寸 /mm Ø850~950×3800 Ø850~950×3800 支撑辊辊身尺寸 /mm Ø1700~1800×3700 Ø1700~1800×3700 工作辊辊颈尺寸 /㎜Ø500×480 Ø450×420支撑辊辊颈尺寸 /㎜Ø1200×1150 Ø1200×1150 工作辊材质合金铸铁合金铸铁支撑辊材质铸钢铸钢最大轧制压力 /MN 70 70最大轧制力矩 /MN*m 2×2.6 2×1.975最大轧制速度 /ms-1 4.239 6.123最大工作开口度 /mm 500 400 主电机功率 /Kw 2×5000 2×5500主电机转速 /rpm 0~45~90 0~65~130压下速度 /mm s-125 15本设计主电机的功率分别选用:P=2×5000Kw粗轧机组H1P=2×5500Kw精轧机组H2计算钢种:Q235坯料及产品规格坯料:2000*1500*200 mm厚的连铸坯规格:20*2000(mm)四、基本要求独立完成工艺流程、规程设计(孔型设计),掌握工艺设计的基本内容,基本步骤和方法,熟练使用AutoCAD进行工程图的绘制。
- 1、下载文档前请自行甄别文档内容的完整性,平台不提供额外的编辑、内容补充、找答案等附加服务。
- 2、"仅部分预览"的文档,不可在线预览部分如存在完整性等问题,可反馈申请退款(可完整预览的文档不适用该条件!)。
- 3、如文档侵犯您的权益,请联系客服反馈,我们会尽快为您处理(人工客服工作时间:9:00-18:30)。
前言板钢轧制制度的确定要求充分发挥设备潜力、提高产量、保证制度,并且操作方便、设备安全。
合理的轧制规程设计必须满足下列原则和要求:在设备允许的条件下尽量提高产量,充分发挥设备潜力提高产量的途径不外是提高压下量、减少轧制道次、确定合理速度规程、缩短轧制周期、提高作业率、合理选择原料增加坯重等。
在保证操作稳定的条件下提高质量,为保证钢板操作的稳定,要求工作辊缝成凸型,而且凸型值愈大操作愈稳定。
压下规程是钢板轧制制度中最基本的核心内容,它直接关系着轧机的产量和产品的质量。
轧制制度中得其他内容如温度制度、速度制度都是以压下制度为核心展开的。
反过来,温度制度、速度制度也影响到压下速度。
目录1·制定生产工艺和工艺制度…………………………………………………………1·1制定生产工艺流程……………………………………………………………1·2制定生产工艺制度……………………………………………………………2·压下规程制定……………………………………………………………………2·1坯料的选择………………………………………………………………………2·2确定轧制方法……………………………………………………………………2·3轧制道次的确定,分配各道次压下量…………………………………………2·4咬入能力的校核…………………………………………………………………3·速度制度确定…………………………………………………………………………4·温度制度确定…………………………………………………………………………5·压下规程表的制定……………………………………………………………………6·各道次变形程度和变形速率的制定…………………………………………………6.1 变形程度的确定…………………………………………………………………6.2 变形速率的确定…………………………………………………………………7·轧制压力的制定…………………………………………………………………………7.1 变形抗力的确定…………………………………………………………………7.2 平面变形抗力的确定……………………………………………………………7.3 计算平均压力p…………………………………………………………………7.4 轧制压力的确定…………………………………………………………………8·电机输出力矩的制定…………………………………………………………8.1 传动力矩的计算………………………………………………………8.2 附加摩擦力矩的确定…………………………………………………8.3 空转力矩的计算………………………………………………………8.4 动力矩的计算…………………………………………………………8.5 电机输出力矩的计算…………………………………………………8.6 电机额定力矩的计算…………………………………………………9·电机的校核…………………………………………………………………9.1 主电机能力的限制…………………………………………………9.2 各机架电机输出力矩等效力矩的计算……………………………9.3 校核各机架的电机输出力矩………………………………………9.4 校核各机架的电机输出力矩………………………………………10·电机输出负荷图……………………………………………………………10.1 速度制度图………………………………………………………10.2 电机负荷图………………………………………………………参考文献…………………………………………………………………………………1·制定生产工艺和工艺制度1·1制定生产工艺选择坯料→原料清理→加热→除磷→纵轧到底→矫直→冷却→表面检查→切边→定尺→表面尺寸形状检查→力学性能检测→标记→入库→发货。
1·2制定工艺制度在保证压缩比的情况下,坯料尺寸尽量小,加热时出炉温度应在1120-1300℃,温度不要过高,以免发生过热或过烧现象;用高压水去除表面的氧化铁皮;矫直时采用辊式矫直机矫直,开使冷却温度一般要接近纵轧温度,轧后快冷到相变温度以下,冷却速度大都选用5-10°或稍高一些,切边时用圆盘式剪切机进行纵剪,然后用飞剪定尺。
2·压下规程制定已知成品规格为12mm×2000mm×lmm2·1坯料的选择初轧坯、连铸坯:H(250)×B(2000)×L(2200)mm材质:Q2352·2确定轧制方法纵轧到底。
2·3轧制道次的确定,分配各道次压下量2.3.1轧制道次的确定坯料尺寸:H×B×L=250×2000×2200mm,总的压下量为250-12=238mm。
根据经验值选取轧制道次n=20,制定压下规程。
2.3.2各道次压下量的分配粗轧阶段压下量分配原则为:(1)粗轧机组变形量一般要占总变形量的70~85%;(2)为保证精轧机组的终轧温度,应尽可能提高精轧机组轧出的带坯温度;(3)一般粗轧机轧出的带坯厚度为20~40mm;(4)第一道考虑咬入及坯料厚度偏差不能给以最大压下量,中间各道次应以设备能力所允许的最大压下量轧制,最后道次为了控制出口厚度和带坯的板形,应适当减小压下量精轧机组的主要任务是在6~8架连轧机上将粗轧带坯轧制成板坯,尺寸符合要求大成品带钢,并保证带钢的表面质量和终轧温度。
精轧连轧机组分配各架压下量的原则是充分考虑利用温度的有利条件,把压下量尽量集中在前几架,在后几架保证板形,厚度和精度及表面质量,压下量逐渐减小。
为保证带钢机械性能,最后一架压下率不低于10%。
精轧机组压下量分配一般利用现场经验资料表2-1:道次压下量和轧后尺寸分配2·4咬入能力的校核热轧钢板时最大咬入角为15°~20°,低速咬入取20°。
在自然咬入条件下应满足:Δh ≤max h ∆max h ∆可按最大咬入角或摩擦系数来计算:max h ∆=D g (1-cos αmax )=56mm式中:Δh —— 道次的绝对压下量,㎜; β —— 摩擦角,°; D g —— 轧辊直径,㎜。
,故咬入符合要求。
3·速度制度确定3·1选择速度图中厚板生产中,由于轧件较长,为方便操作,采用梯形速度图,见图3-4.3·2轧制速度的确定粗轧机:N=2×2400kWn=0~30~60 rpma=15 rpm/s; b=30 rpm/s精轧机:N=4800kWn=0~30~60 rpm a=30rpm/s ; b=60 rpm/s 二辊辊径:d=690 mm;D=1150mm四辊辊径:工作辊 d=510 mm;D=800mm支承辊 d=750 mm; D=1400mm 二辊速度:ny=15 rpm ;np=20 rpm ;nd=30 rpm四辊速度:ny=20 rpm ;np=30 rpm ;nd=60 rpm 二辊、四辊轧机最大允许的轧制压力:4000t3·3计算各道次轧制时间第一道次:加速轧制时间t1,减速轧制时间t3,等速轧制时间t2对于四辊轧机:加速轧制时间t1:t1=(nd– ny)/a=(30-15)/15=1s减速轧制时间t3:t3=(nd– np)/b=(30-20)/30=0.3s等速轧制时间t2:t2={L-0.5(vy+ vd)*t1-0.5(vp+ vd)*t3}/nd=0.2s所以纯轧时间tz = t1+ t2+ t3=4s如果轧件长度l≤3.5m,取间隙时间tj=2.5s轧件长度3. 5≤l<8m,取间隙时间tj=6s轧件长度l>8m,取间隙时间tj=4s因此间隙时间tj=2.5同理,依次求的第二道次到二十道次轧制时间如表3-1所示。
表3-1:各道次轧制速度和时间分配4·温度制度确定为了确定各道次轧制温度,必须求出各道的温度降。
高温时轧件温度降可以按辐射热算,而认为对流和传导所损失的热量大致可与变形功所转化的热量相抵消。
由于辐射热所引起的温度降在热轧板带材时,可用以下公式近似计算:/1000)4△t=12.9×Z/h×(T1Z-该道次轧制时间和前道次间隙时间之和h-轧出厚度-前一道次的绝对温度T1根据经验,双机架中厚板轧机轧制材料为普碳钢,其粗轧开轧温度为1160℃。
所以第一道次温降为△t=12.9×4.02/240×(1433/1000)4=0.9℃,所以=1159℃。
t2同理,依次求的第二道次到二十道次轧制温度如表4-1所示。
表4-1:所有道次轧制温度5·压下规程表的制定表5-1:压下规程6·各道次变形程度和变形速率的制定6.1变形程度的确定由公式变形程度:ε=△h/H ,其中△h 为各道次压下量,H 为各道次轧制前的厚度,则ε1=10/240=4.2%,其他各道次变形程度见表6-1。
6.2变形速率的确定 由公式其中v 表示各道次轧辊最大速率,H 为各道次轧制前的厚度,h 为各道次轧制后的厚度,△h 表示各道次压下量,R 表示工作辊的辊身的半径。
因为咬入速度,稳轧速度,抛出速度取值不同,则v 在各道次不全相同。
一道次 s m /972.057510240250180621=+⨯=ε, 其他各道次变形速率见表6-1。
表6-1ε•=7·轧制压力的制定7.1变形抗力的确定由各道相应的变形速度及轧制温度即可查找出30%压下来是钢的变形抗力,再经换算成实际压下率时的变形抗力。
各道次的变形抗力见变7-1。
7.2平面变形抗力的确定由公式平面变形抗力: K =1.15σs各道次平面变形抗力见表7-1。
7.3计算平均压力p根据中厚板轧制的情况,可取应力状态影响系数η=0.785+0.25l/h,其中h是变形区轧件的平均厚度,l为变形区长度,l=p=1.15σs*η。
各道次平均压力p见表7-1。
7.4轧制压力的确定由公式:P=BLp,第一道次的轧制力为P=2000*75.83*42.84=6497.44Kn其余道次轧制压力见表7-1。
表7-18· 电机输出力矩的制定8.1计算传动力矩M z 由公式2z M lpϕ=,l —表示接触弧长度,根据大量实验数据统计,热轧板带材ϕ=0.42~0.5,取ϕ=0.5。
第一道次:J p l M z k 69.4921044.649783.755.0223111=⨯⨯⨯⨯==-ϕ; 其它道次计算方法如上,计算结果见表8-1。