出货检验作业流程
[出货流程程序]出货检验程序
![[出货流程程序]出货检验程序](https://img.taocdn.com/s3/m/f7becafedd36a32d737581e5.png)
[出货流程程序]出货检验程序产品出货管理流程一、目的为了确保客户和企业自身利益,对成品出货流程进行规范,确保出货成品数量的准确性、时间的及时性及产品运输防护同安全的有效监控性。
二、范围所有公司产品的出货管理。
三、职责1、仓库负责产品物质进出的管理;负责账目管理并向相关部门提供相关的数据、报表等信息。
2、质检部负责出货产品出库前的检验工作。
3、生产部负责出货产品的审核、管理工作。
4、供应部负责出货产品的流程跟踪及与客户间的协调工作。
四、程序要求1、成品仓管员接到供应部提供由财务开具的《发货单》后,认真核实单中产品品号、品名、规格等是否一致,并确认相关人员的签名是否齐全。
2、成品出货所用承运商为与供应部人员签订协议的承运商。
装货车辆到厂后,成品仓管员须核实司机及车辆信息。
如有异常须立即向上级反馈并最终确认。
货柜须核对车牌号、出货资料是否一致,接下来检查运输车辆及货柜的七点:前板,左侧,右侧,底面,顶板,箱顶,内/外门,底部外架等有无破损、脏污及其它不明物体等影响货物贮存的现象,如有异常须及时向上级反馈,并要求承运方解决。
3、装货车辆资料核实及卫生条件符合标准后,仓库应立即着手装货前准备工作。
装车时必须由相关仓管员监督及核对所装货物内容同出货通知文件上内容的一致性。
装货过程中,若出货通知文件遇临时变更,须第一时间知会成品仓主管及供应人员,如装货作业己正在操作须立即停止,待信息统一后方可继续。
装货操作人员必须为成品仓主管级以上指定人员。
装货及装柜过程中相关仓管员不得离开现场,确保装货质量、数量等信息准确。
4、搬运过程中须遵守“安全第一”的原则,所有搬运操作人员必须通过产品防护、搬运安全等相关知识的培训,严禁在货物上踩踏,野蛮装卸、倒置及其它有损货物的行为。
5、装货后,监装人员必须将货物单独及车辆(包含车牌号码)、货物一起拍照存档。
6、由监装、仓库等相关人员签字确认并拍照保存发货信息后的运输车辆,如果客户反馈数量不符、构件破损等信息,原则上由运输单位承担相应责任。
成品出货检验工作标准流程
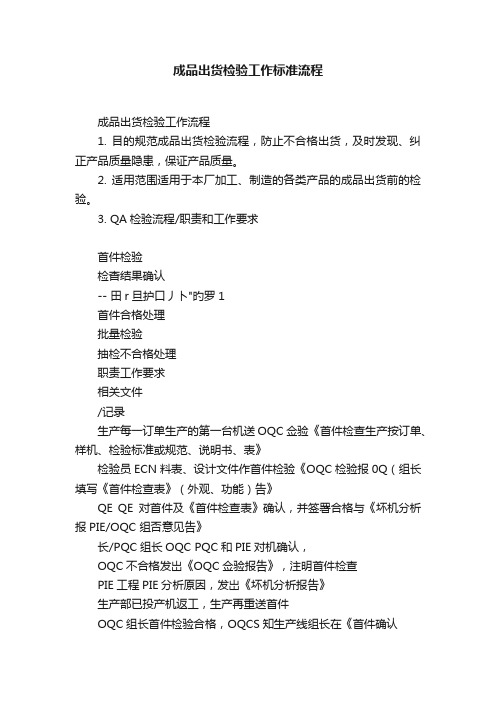
成品出货检验工作标准流程成品出货检验工作流程1. 目的规范成品出货检验流程,防止不合格出货,及时发现、纠正产品质量隐患,保证产品质量。
2. 适用范围适用于本厂加工、制造的各类产品的成品出货前的检验。
3. QA检验流程/职责和工作要求首件检验检杳结果确认-- 田r旦护口丿卜"旳罗1首件合格处理批量检验抽检不合格处理职责工作要求相关文件/记录生产每一订单生产的第一台机送OQC佥验《首件检查生产按订单、样机、检验标准或规范、说明书、表》检验员ECN料表、设计文件作首件检验《OQC检验报0Q(组长填写《首件检查表》(外观、功能)告》QE QE对首件及《首件检查表》确认,并签署合格与《坏机分析报PIE/OQC 组否意见告》长/PQC组长OQC PQC和PIE对机确认,OQC不合格发岀《OQC佥验报告》,注明首件检查PIE工程PIE分析原因,发岀《坏机分析报告》生产部已投产机返工,生产再重送首件OQC组长首件检验合格,OQCS知生产线组长在《首件确认检验员表》上签字确认后,生产部批量生产OQC组长首件检验合格,OQC批量抽检/PQC 组长/PIE根据产品检验标准、规范,《产品检验抽样规定》,OQC主管设计文件,批量抽检检验员记录抽检的每台机流水号PIE首批检验合格机抽一箱做整箱落地试验首批检验合格机(配有电源的产品)抽一箱做24小时煲机试验根据抽检结果填写OQC佥验报告批量抽检不合格PQC OQC PIE对机确认OQC主管在OQC佥验报告上签字确认OQC在生产部产成品送检单上填写REJ,注明不良项目,发岀《OQC佥验报告》,工程PIE发岀《坏机分析报告》,在线指导生产线返工,返工后重新送检。
出货检验规范

出货检验规范建立出货检查控制程序 ,为确保产品出厂前进行最终检验和测试,判定产品品质符合顾客要求,防止不合格品流出。
一、职责1)品质部负责产品出货前检验的执行与结果记录,负责所有技术要求的相关检验记录。
2)研发工程部负责检验项目及参数值的确定。
3)营销部负责产品出货前的检验通知。
4)仓库负责产品出货检验工作的配合。
5)生产部负责对不合格产品进行返工返修及按需要执行纠正措施。
二、检验控制流程1)产品入库前/出货检验实施:①生产部装配车间完成装配后首先进行内部自检、互检、复检,确认合格后填写《内部报检单》向品质部报检。
(报检单内容应清楚反映:机型、名称、报检数量、装配员工自检签名、复检人员签名、具体报检时间)②品质部接到生产部装配车间《内部报检单》后,首先确认报检的机型、数量与销售部出货通知单相符。
③品质部确定了生产部报检信息与出货信息一致后对出货产品进行检验。
④品质部应重点对机器的结构、功能、系统等按照标准文件设定参数进行测试。
⑤在检验过程中发现不良问题较多而且超过 3个低级问题时,检验员无须再检验可以直接向生产部车间主管提出拒检,同时做好不良标识待处理。
⑥品质部拒绝检验已作好不良标识后要及时向生产主管反馈不良信息,由生产部装配主管或生产工艺人员找到异常问题机器的装配者要求立即返工并对机器重新检验,直到自检合检后再次向品质报检。
⑦品质部接到生产部装配车间二次报检后,应重点对返工的部位进行检验,同时按照系统出厂参数设定值进行调试确保合格,最后将检验结果记录于《产品检验报告》中。
⑧二次检验合格下架后,品质部还要根据客户远近评估包装方式并对包装要求进行监控,一定要满足在运输过程中对机器造成损坏因素的预防效果。
⑨最后检查包装所使用的包装是否符合规格要求,是否有破损,出货标贴或警示标识是否醒目等,所有工作完成后方可出货。
⑩最后品质部还得跟装车过程,监督在装车过程中防止造成损坏。
2)库存品出货检验实施:①仓库接到销售部出货通知后通知生产部,要求安排员工将要出货的产品重新提交待检验区,挂上“待检”牌待检,同时并向品质部报检。
品管检验出货流程(印刷)

包装导单步骤
一、包装说明 包装员从待包装区拿取绿色周转箱(QA已抽检OK产品)到打包台进行产 品包装。一次只能取一个箱子进行包装。禁止多款同时包装.
二、包装动作 1. 把产品从周转箱拿出来,放在包装台上,根据产品的大小(客户要求)裁 剪包装用的PE薄膜或牛皮纸,把产品放到PE薄膜或牛皮纸中间,用胶带 把四周封好。 2. 成品包好贴标签时,要先核对标签与产品底纸上QC写的客户名称、制造 单号、订单 数、工号是否与标签一致,OK后贴于产品外包装上,在标签 空白处盖上“QA合格”章.
FQC 检验步骤(四)
四、检验后产品的放置
FQC检验OK的产品装入专用的绿色胶筐 (检验周转箱)放到指定的货架上,写标 签人员取下胶筐根据里面制造单/客人的出 货要求进行标签的填写,确认OK后交QA 人员进行抽检.
写标签步骤
一、产品确认 根据FQC在产品底纸上注明的客户名称、制造单 号、数量、工号是否与制造单一致.
品管检验流程图
1.数量确认 2.版卡与样品 3.产品与制单内容是否相符
1.检验前SIIP阅读 2.良品不良品判定 3.异常报告和处理
品管收货输入系统
FQC检验
QA抽检
1.写标签 2.写出货报告/检验报告 3.核对内容、数量、规格
包装
1.核对客户名称、制造单 号、数量、工号
2.根据客户要求包装 3.盖QA合格章
FQC检验步骤(三)
三、点数和日报记录
QC将产品检验完,根据客户所需订单量清点 数量,每100大张用橡皮圈扎起来,尾数扎底 纸上注明数量,在尾数扎底纸上注明:客户名 称、制造单号、订单数、工号并贴样(备注相 应的检验序号是否环保、扫描OK)多扎产品 时要用大号橡皮圈捆在一起,避免遗漏,QC要 在制单上的FQC处签工号,制单的左上角制单 号旁边签工号及不良数,QC检验的每款产品都 需记录在《FQC工作日报表》上并贴样.
出货检验通用流程

出货检验通用流程When it comes to the general process of inspecting shipments, there are several key steps that must be followed to ensure that the products being shipped meet the necessary quality standards. The first step in the process is to thoroughly inspect the products as they are being loaded onto the shipment vehicle. This includes checking the packaging for any signs of damage, ensuring that the products are securely packed, and verifying that the correct quantity of each item is included in the order.在检查装运物品时,首要步骤是仔细检查产品,确保它们符合必要的质量标准。
这包括检查包装是否有任何损坏迹象,确保产品包装牢固,并验证每个物品订购的正确数量。
Once the products have been loaded onto the shipment vehicle, the next step is to verify that all necessary documentation is in order. This includes checking that the packing list matches the actual products being shipped, confirming that the products are labeled correctly, and ensuring that any necessary customs documentation isincluded. It is important to double-check all of the documentation to avoid any delays or issues during the shipping process.当产品装上运输工具后,下一步是核实所有必要的文件是否齐全。
OQC检验操作流程

OQC 组 件 出 货 检 验 流 程物料按出货单备货
OQC 按《出货作业指导书》对
出货单号、规格型号、数量、
OQC 把相关出货单号、托盘号按序输入《组件条码查询系
统》读取数据并逐条核对条
码及数据
物料提供给OQC ,出货单对应的集装箱号(麦头)物料装车出货
OQC 按序记录相关检验信息
OQC 在出货单上签字确认
OQC 根据集装箱号在对应的实
物上按序贴麦头。
OQC 在麦头的序号处敲章
*OQC 在贴麦头时,
按检验记录的序号、
托盘号、麦头序号一
一对应后,贴在组件
实物有托盘号、条形NG
NG
敲OQC 章
麦头内容:集装箱号、
组件序号、出货日期
实物立刻进行现OQC 填写异常联
实物立刻进行现无锡尚德太阳能电力有限公司。
出货检验控制程序

5.3.1不合格之出货产品,由品管部确认NG判退,以“重工处理单”知会资材,并按“不
合格品管理程序”及“纠正预防措施管理程序”处理(涉及到产品无法重工,需报废处
理,以“报废作业办法”处理)。
5.3.2确需重工的产品,如为急料时,OQC附NG样品及“重工处理单”,由资材安排
告”上,以便日后追溯,检验OK时,需核对实物与“交货资料”内容是否一致。
5.2检验合格时,,在“货品外箱”盖上“PASS”章,并填写相关的“出货检验报告”,
如客户有要求时,则须填写相应之“出货检验报告”随同产品附一份给客户,原件
本厂保存。
5.3检验不合格时,在包装上贴上ห้องสมุดไป่ตู้色“不合格标签”,将成品移至不合格品区,并须
4.2品管部:成品出货之品质检验。
4.3各部门:成品出货异常处理。
5、作业内容:
5.1作业说明:
5.1.1仓库人员备货完毕后,并及时通知OQC人员检查人员抽检检验。
5.1.2 OQC人员依“成品检验规范”、“图纸/SIP”、“承认书”及“抽样计划作业办
法”实施抽样检验,允收标准为CR:0 ,MA:1.5,MI:2.5,并做出允收或拒收之判定,将检验结果记录于“出货检验报
6.3文件及记录控制程序
6.4产品标识与追溯控制程序
6.5返工、报废管理办法
6.6抽样计划作业办法
6.7成品检验规范
7、引用表单:
7.1QA验货报告
7.2返工处理单
7.3特采申请单
7.4报废申请单
7.5可靠性测试报告
7.6品质异常处理报告
责任部门重工。
5.3.3重工OK的产品,由责任部门重新报检于OQC,依此程序流程要求作业。
04出货检验管控流程

厦门新为达包装有限公司 管理制度 文件编号:XWD-PG04成品出货检验流程1.0 目的:出货前对成品进行开箱抽检,对装箱过程、装柜过程进行监督,对柜子装好后封签进行确认,特拟订本流程。
2.0 范围:成品出货适用本流程。
3.0 成品出货检验流程:序号生管品管部生产车间仓库 流程说明相关表单11.1 生管:应提前知会品管部,以便品管部安排人员跟进1.2 品管:根据出货安排,对急需出货的成品优先进行检验 生产计划出货安排22.1 品管部:开箱检验判定;2.2 抽样标准:至少抽取5%进行全检判定要对照客户样、生产首件样、生产指令单、作业指导书.....不合格项分为严重不合格项、一般不合格项,只要发现严重不合格项的即可判定该批次不合格,需全部返工,具体依“品管作业指导书”进行成品出货检验记录品管作业指导书33.1 生产车间:对品管判定不合格的批次,结合检验中发现的问题,组织生产人员进行返工作业 3.2 品管部:全程跟踪返工情况,对返工好的成品再次开箱检验,直至判定合格才放行装柜出货 3.3 品管部:经检验合格的成品,盖“QA ”章成品出货检验记录 工程异常单44.1仓库:首先确认是否有盖品质合格章,依出货计划安排出货,对出货的数量进行确认4.2品管部:对柜子是否干净、是否有严重破损进行检查,装柜方式是否合理,柜子封印是否正确等进行核对4.3品管部:每批次成品出货检验进行记录成品出货检验记录签发: 审核: 拟稿: 抄报:生产部、品管部、仓库、行政部厦门新为达包装有限公司2016年11月7日出货安排开箱抽检返工 检验装柜出货YESNOYES。
- 1、下载文档前请自行甄别文档内容的完整性,平台不提供额外的编辑、内容补充、找答案等附加服务。
- 2、"仅部分预览"的文档,不可在线预览部分如存在完整性等问题,可反馈申请退款(可完整预览的文档不适用该条件!)。
- 3、如文档侵犯您的权益,请联系客服反馈,我们会尽快为您处理(人工客服工作时间:9:00-18:30)。
出货检验作业流程
出货检验是企业质量管理的重要环节,它通过对产品的外观、功能和
性能等方面进行检查,以确保产品质量符合标准和客户要求。
下面是一个
典型的出货检验作业流程,分为以下几个步骤:
1.准备工作:
在进行出货检验前,需要进行一些准备工作。
首先,检验人员需要明
确出货的产品类型和数量,并熟悉相应的标准要求和检验方法。
其次,需
要准备好所需的检验设备和工具,包括测量仪器、测试工装以及样品等。
2.确定检验样品:
根据出货批次和客户要求,从货物中抽取一定比例的样品进行检验。
样品的选择应尽可能代表整个批次的产品,并且要随机抽取,以确保结果
的公正和可靠。
3.外观检验:
首先进行外观检验,以评估产品外观的质量和外观缺陷。
根据产品的
不同特点,可以采用目测或者使用特定的测量仪器进行检查。
外观检验的
内容包括产品的颜色、大小、形状、表面光滑度、划痕、凹陷、变形等。
4.功能检验:
除了外观检验,还需要对产品的功能进行测试。
根据产品的特性和要求,可以使用不同的测试方法,例如使用电流表、电压表、频谱分析仪等。
通过测试,评估产品是否能正常运行、是否符合规定的参数和性能要求。
5.抽样检验:
出货量较大的情况下,不可能对每件产品都进行全面检验,可以采取抽样检验的方式。
根据统计学原理,通过对样品的测试,可以预测整个批次的产品质量情况。
抽样检验需要确定样本量、抽样方法和接收质量水平等,以确保检验结果具有统计学意义。
6.检验记录:
在进行检验的过程中,需要详细记录检验结果和数据。
记录可以包括样品编号、检验日期、检验人员、检验设备和方法、检验结果等。
这些记录可以作为以后追溯产品质量问题、改进产品设计和制造过程的依据。
7.判定和处理:
根据检验结果和标准要求,对产品进行判定。
如果产品符合要求,可以继续进行出货;如果产品不符合要求,需要进行处理,例如修复、返工或者淘汰。
对于不合格的产品,需要分析原因,并采取相应的纠正和预防措施,以避免类似问题再次发生。
8.出货操作:
最后,根据检验结论和客户要求,对合格的产品进行包装和出货。
出货前需要确保产品的数量和质量与订单一致,并进行相应的标识和记录,以便追溯和管理。
以上是一个典型的出货检验作业流程,其中每个步骤都非常重要,任何一环节的疏漏都可能导致产品质量问题和客户投诉。
因此,企业需要建立科学的出货检验管理制度,并合理配备检验设备和人员,以确保产品质量和客户满意度。