汽车灯具双色模设计制造注意事项
双色模具设计及注塑时要注意的事项

双色模具设计及注塑时要注意的事项双色模具就是两种塑胶材料在同一台注塑机上注塑,分两次成型,通常由两套模具组成,后模要旋转180度,而前模不动,但是产品只出模一次的模具。
一般这种模塑工艺也叫双料注塑,且需要专门的双色注塑机。
双色模具设计及注塑时要注意的事项有:1、两型腔和型芯的运水布置尽量充分,并且均衡、一样。
2、模具的前模以中心旋转180º后,必须与后模吻合。
设计时必须注意这一点。
3、99%的情况是先注塑产品的硬胶部分,再注塑产品的软胶部分。
因为软胶易变形。
先成型成型温度高的塑胶原材料,再成型温度低的。
4、三板模的水口最好能设计成可以自动脱模动作。
特别要注意软胶水口的脱模动作是否可靠。
5、在设计时,请仔细查看双色模具注塑机的参数数据,如,最大容模厚度、最小容模厚度、顶棍孔距离等。
6、注塑时,第一次注塑成型的产品尺寸可以略大,以使它在第二次成型时能与另一个型腔压得更紧,以达到封胶的作用。
7、前模的两个形状是不同的,分别成型1种产品。
而后模的两个形状完全一样。
(注意:如有不一样,要做前模滑块来保证后模一致)8、注意在第二次注塑时,塑胶的流动是否会冲动第一次已经成型好的产品,使其胶位变形?如果有这个可能,一定要想办法改善。
9、为了使两种塑胶“粘”得更紧,要考虑材料之间的“粘性”以及模具表面的粗糙度。
双色模具注塑有专门的TPU;而模具表面越光滑,它们“粘‘得更紧。
10、在设计第二次注塑的型腔时,为了避免型腔插(或擦)伤第一次已经成型好的产品胶位,可以设计一部分避空。
但是必须慎重考虑每一处封胶位的强度,即:在双色模具注塑中,是否会有在大的注塑压力下,塑胶发生变形,导致第二次注塑可能会有批锋产生的可能。
双色模具设计及双色注塑成型的36条经验
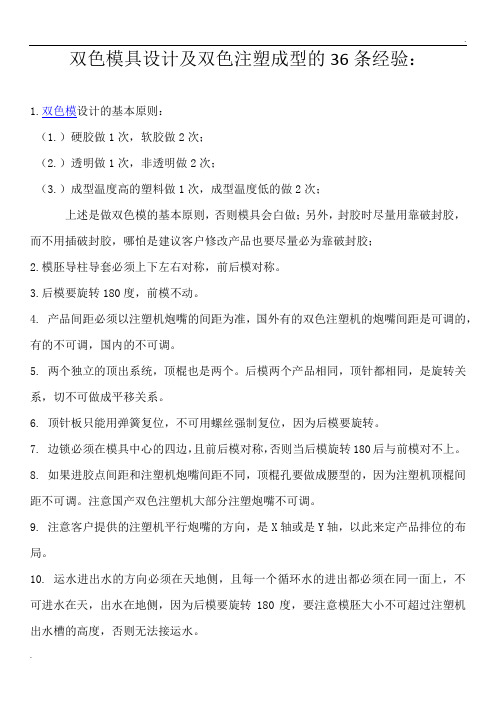
双色模具设计及双色注塑成型的36条经验:1.双色模设计的基本原则:(1.)硬胶做1次,软胶做2次;(2.)透明做1次,非透明做2次;(3.)成型温度高的塑料做1次,成型温度低的做2次;上述是做双色模的基本原则,否则模具会白做;另外,封胶时尽量用靠破封胶,而不用插破封胶,哪怕是建议客户修改产品也要尽量必为靠破封胶;2.模胚导柱导套必须上下左右对称,前后模对称。
3.后模要旋转180度,前模不动。
4. 产品间距必须以注塑机炮嘴的间距为准,国外有的双色注塑机的炮嘴间距是可调的,有的不可调,国内的不可调。
5. 两个独立的顶出系统,顶棍也是两个。
后模两个产品相同,顶针都相同,是旋转关系,切不可做成平移关系。
6. 顶针板只能用弹簧复位,不可用螺丝强制复位,因为后模要旋转。
7. 边锁必须在模具中心的四边,且前后模对称,否则当后模旋转180后与前模对不上。
8. 如果进胶点间距和注塑机炮嘴间距不同,顶棍孔要做成腰型的,因为注塑机顶棍间距不可调。
注意国产双色注塑机大部分注塑炮嘴不可调。
9. 注意客户提供的注塑机平行炮嘴的方向,是X轴或是Y轴,以此来定产品排位的布局。
10. 运水进出水的方向必须在天地侧,且每一个循环水的进出都必须在同一面上,不可进水在天,出水在地侧,因为后模要旋转180度,要注意模胚大小不可超过注塑机出水槽的高度,否则无法接运水。
11. 第一次注塑的产品要放在非操作侧,因为第一次注塑后产品要旋转180度进行第二次注塑,正好转到操作侧,方便取产品。
12. 出口模的码模位要在操作侧和非操作侧,不可在天地侧,因为他们的产品要全自动。
13. 分型面的注意事项:后模分型面要将两个产品合并后取得的分型面为后模的;前模分型面要取单个产品的即可,不可取合并后的产品分型面。
14. 前后法兰的公差为负0.05mm,两法兰间距公差为正负0.02mm,顶棍与顶棍孔的间隙单边为 0.1mm,前后模导套导柱的中心距公差为正负0.01,模框四边和深度都要加公差,否则当后模旋转180度后,因高低不一致而产生批锋。
干货分享-双色模具设计经验总结
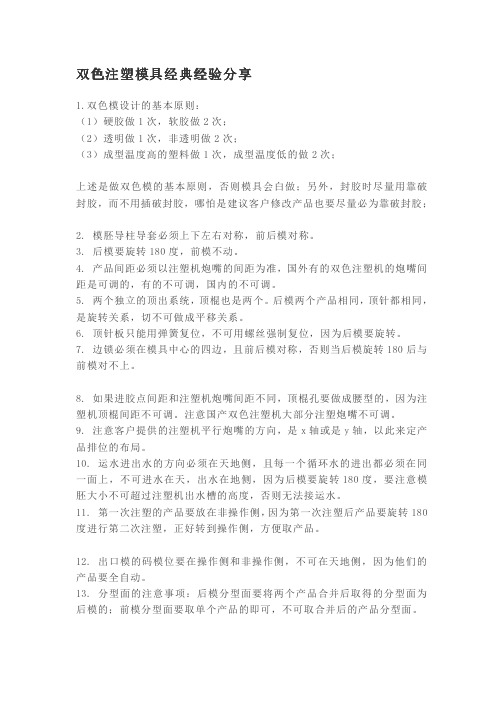
双色注塑模具经典经验分享1.双色模设计的基本原则:(1)硬胶做1次,软胶做2次;(2)透明做1次,非透明做2次;(3)成型温度高的塑料做1次,成型温度低的做2次;上述是做双色模的基本原则,否则模具会白做;另外,封胶时尽量用靠破封胶,而不用插破封胶,哪怕是建议客户修改产品也要尽量必为靠破封胶;2.模胚导柱导套必须上下左右对称,前后模对称。
3.后模要旋转180度,前模不动。
4.产品间距必须以注塑机炮嘴的间距为准,国外有的双色注塑机的炮嘴间距是可调的,有的不可调,国内的不可调。
5.两个独立的顶出系统,顶棍也是两个。
后模两个产品相同,顶针都相同,是旋转关系,切不可做成平移关系。
6.顶针板只能用弹簧复位,不可用螺丝强制复位,因为后模要旋转。
7.边锁必须在模具中心的四边,且前后模对称,否则当后模旋转180后与前模对不上。
8.如果进胶点间距和注塑机炮嘴间距不同,顶棍孔要做成腰型的,因为注塑机顶棍间距不可调。
注意国产双色注塑机大部分注塑炮嘴不可调。
9.注意客户提供的注塑机平行炮嘴的方向,是x轴或是y轴,以此来定产品排位的布局。
10.运水进出水的方向必须在天地侧,且每一个循环水的进出都必须在同一面上,不可进水在天,出水在地侧,因为后模要旋转180度,要注意模胚大小不可超过注塑机出水槽的高度,否则无法接运水。
11.第一次注塑的产品要放在非操作侧,因为第一次注塑后产品要旋转180度进行第二次注塑,正好转到操作侧,方便取产品。
12.出口模的码模位要在操作侧和非操作侧,不可在天地侧,因为他们的产品要全自动。
13.分型面的注意事项:后模分型面要将两个产品合并后取得的分型面为后模的;前模分型面要取单个产品的即可,不可取合并后的产品分型面。
14.前后法兰的公差为负0.05mm,两法兰间距公差为正负0.02mm,顶棍与顶棍孔的间隙单边为0.1mm,前后模导套导柱的中心距公差为正负0.01,模框四边和深度都要加公差,否则当后模旋转180度后,因高低不一致而产生批锋。
双色注塑模具设计及双色注塑成型注意事项与经验 共三十六条

双色注塑模具设计及双色注塑成型注意事项与经验共三十六条1.双色注塑模具设计的基本原则:(1.)硬胶做1次,软胶做2次;(2.)透明做1次,非透明做2次;(3.)注塑成型温度高的塑料做1次,成型温度低的做2次;上述是做双色注塑模具的基本原则,否则注塑模具会白做;另外,封胶时尽量用靠破封胶,而不用插破封胶,哪怕是建议客户修改产品也要尽量必为靠破封胶;2.模胚导柱导套必须上下左右对称,前后模对称。
3.后模要旋转180度,前模不动。
4. 产品间距必须以注塑机炮嘴的间距为准,国外有的双色注塑机的炮嘴间距是可调的,有的不可调,国内的不可调。
5. 两个独立的顶出系统,顶棍也是两个。
后模两个产品相同,顶针都相同,是旋转关系,切不可做成平移关系。
6. 顶针板只能用弹簧复位,不可用螺丝强制复位,因为后模要旋转。
7. 边锁必须在模具中心的四边,且前后模对称,否则当后模旋转180后与前模对不上。
8. 如果进胶点间距和注塑机炮嘴间距不同,顶棍孔要做成腰型的,因为注塑机顶棍间距不可调。
注意国产双色注塑机大部分注塑炮嘴不可调。
9. 注意客户提供的注塑机平行炮嘴的方向,是X轴或是Y轴,以此来定产品排位的布局。
10. 运水进出水的方向必须在天地侧,且每一个循环水的进出都必须在同一面上,不可进水在天,出水在地侧,因为后模要旋转180度,要注意模胚大小不可超过注塑机出水槽的高度,否则无法接运水。
11. 第一次注塑的产品要放在非操作侧,因为第一次注塑后产品要旋转180度进行第二次注塑,正好转到操作侧,方便取产品。
12. 出口模的码模位要在操作侧和非操作侧,不可在天地侧,因为他们的产品要全自动。
13. 分型面的注意事项:后模分型面要将两个产品合并后取得的分型面为后模的;前模分型面要取单个产品的即可,不可取合并后的产品分型面。
14. 前后法兰的公差为负0.05mm,两法兰间距公差为正负0.02mm,顶棍与顶棍孔的间隙单边为0.1mm,前后模导套导柱的中心距公差为正负0.01,模框四边和深度都要加公差,否则当后模旋转180度后,因高低不一致而产生批锋。
车用组合灯具的质量控制与标准制定
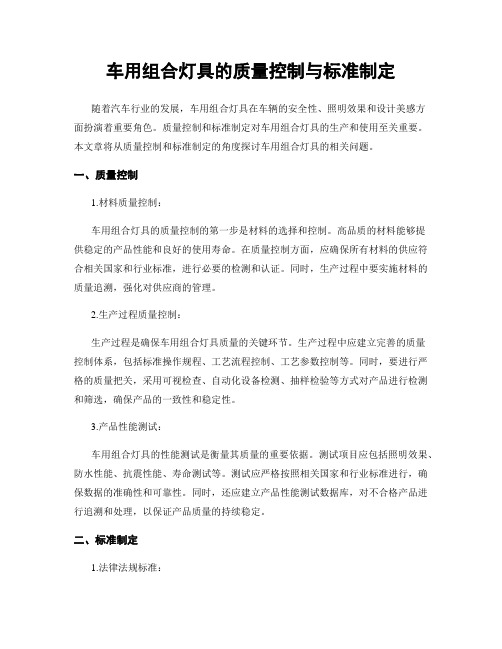
车用组合灯具的质量控制与标准制定随着汽车行业的发展,车用组合灯具在车辆的安全性、照明效果和设计美感方面扮演着重要角色。
质量控制和标准制定对车用组合灯具的生产和使用至关重要。
本文章将从质量控制和标准制定的角度探讨车用组合灯具的相关问题。
一、质量控制1.材料质量控制:车用组合灯具的质量控制的第一步是材料的选择和控制。
高品质的材料能够提供稳定的产品性能和良好的使用寿命。
在质量控制方面,应确保所有材料的供应符合相关国家和行业标准,进行必要的检测和认证。
同时,生产过程中要实施材料的质量追溯,强化对供应商的管理。
2.生产过程质量控制:生产过程是确保车用组合灯具质量的关键环节。
生产过程中应建立完善的质量控制体系,包括标准操作规程、工艺流程控制、工艺参数控制等。
同时,要进行严格的质量把关,采用可视检查、自动化设备检测、抽样检验等方式对产品进行检测和筛选,确保产品的一致性和稳定性。
3.产品性能测试:车用组合灯具的性能测试是衡量其质量的重要依据。
测试项目应包括照明效果、防水性能、抗震性能、寿命测试等。
测试应严格按照相关国家和行业标准进行,确保数据的准确性和可靠性。
同时,还应建立产品性能测试数据库,对不合格产品进行追溯和处理,以保证产品质量的持续稳定。
二、标准制定1.法律法规标准:车用组合灯具的标准制定应符合国家相关法律法规的要求。
通过制定具体的标准,引导企业在生产和销售过程中遵守法律法规,保障车用组合灯具的质量和安全性。
同时,标准制定应与国际标准接轨,提高产品的竞争力和市场认可度。
2.行业标准:行业标准是车用组合灯具标准制定的重要依据。
通过行业组织、专家团队等方式,制定适用于不同车型和用途的车用组合灯具标准,为企业提供明确的生产和测试指南。
同时,行业标准还能促进技术创新和产品质量的提升,推动整个行业的健康发展。
3.用户需求标准:车用组合灯具的标准制定要充分考虑用户需求。
通过用户反馈和市场调研,了解用户对于照明效果、外观设计、节能环保等方面的需求,并将其纳入标准制定的范围。
双色模具设计及双色注塑成型的36条经验
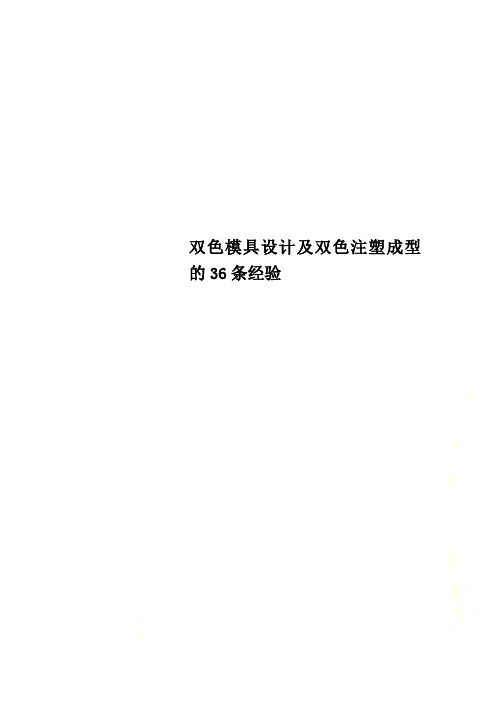
双色模具设计及双色注塑成型的36条经验双色模具设计及双色注塑成型的36条经验:1.双色模设计的基本原则:(1.)硬胶做1次,软胶做2次;(2.)透明做1次,非透明做2次;(3.)成型温度高的塑料做1次,成型温度低的做2次;上述是做双色模的基本原则,否则模具会白做;另外,封胶时尽量用靠破封胶,而不用插破封胶,哪怕是建议客户修改产品也要尽量必为靠破封胶;2.模胚导柱导套必须上下左右对称,前后模对称。
3.后模要旋转180度,前模不动。
4. 产品间距必须以注塑机炮嘴的间距为准,国外有的双色注塑机的炮嘴间距是可调的,有的不可调,国内的不可调。
5. 两个独立的顶出系统,顶棍也是两个。
后模两个产品相同,顶针都相同,是旋转关系,切不可做成平移关系。
6. 顶针板只能用弹簧复位,不可用螺丝强制复位,因为后模要旋转。
7. 边锁必须在模具中心的四边,且前后模对称,否则当后模旋转180后与前模对不上。
8. 如果进胶点间距和注塑机炮嘴间距不同,顶棍孔要做成腰型的,因为注塑机顶棍间距不可调。
注意国产双色注塑机大部分注塑炮嘴不可调。
9. 注意客户提供的注塑机平行炮嘴的方向,是X轴或是Y轴,以此来定产品排位的布局。
10. 运水进出水的方向必须在天地侧,且每一个循环水的进出都必须在同一面上,不可进水在天,出水在地侧,因为后模要旋转180度,要注意模胚大小不可超过注塑机出水槽的高度,否则无法接运水。
11. 第一次注塑的产品要放在非操作侧,因为第一次注塑后产品要旋转180度进行第二次注塑,正好转到操作侧,方便取产品。
12. 出口模的码模位要在操作侧和非操作侧,不可在天地侧,因为他们的产品要全自动。
13. 分型面的注意事项:后模分型面要将两个产品合并后取得的分型面为后模的;前模分型面要取单个产品的即可,不可取合并后的产品分型面。
14. 前后法兰的公差为负0.05mm,两法兰间距公差为正负0.02mm,顶棍与顶棍孔的间隙单边为 0.1mm,前后模导套导柱的中心距公差为正负0.01,模框四边和深度都要加公差,否则当后模旋转180度后,因高低不一致而产生批锋。
双色模具设计的3大原则和6项注意事项
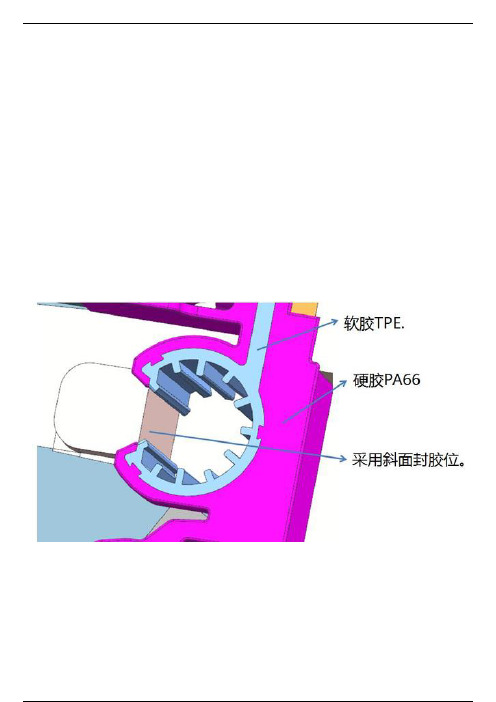
第一原则:确定硬胶与软胶相结合的粘性,另外要注意硬胶的融点要比软胶高,不要在成型软胶的时候,把硬胶融点,就不行。
1.第一射:硬胶:PA66+ 第二射:软胶:TPE 相结合是OK.2.第一射:硬胶:PC/ABS+ 第二射:软胶:PC 相结合是OK.3.第一射:硬胶:PP+ 第二射:软胶:TPU相结合就不行,因为PP材料和TPU材料是不相容的。
第二原则:确认第二射软胶与第一射硬胶成型后,不能有脱落现象。
1.第一射硬胶在于第二射软胶封胶时,尽量用平面来封胶。
2.如果侧面或者斜顶封胶时,硬胶封胶处尽量做偷胶0.1~0.15MM,采用模具钢位来封胶。
第三原则:结合公司现有的双色机,进行设计。
1.双色机正常类型是,双炮筒为并排样式。
2.非正常的双色机,两个炮筒产生90度样式,通常为定制或者是二次改造成的。
3.如果是嵌件放入注塑的情况下,正常使用立式注塑机。
第一个注意事项:硬胶与软胶的收缩率,统一按照硬胶的收缩率进行缩放。
第二个注意事项:模具导柱以及相关定位机构,需四个分钟,而且距离要统一,因为公模侧在模具设计时,是完全一样的,成型中需要旋转180度。
第三个注意事项:第一射成型硬胶进胶点,一定要使用三板模点进胶,或者使用热流道,因为公模侧是完全一样的,需要进行顶出产品。
第四个注意事项:1.公模侧的水路,尽量设计在模具内侧,因为公模侧需要旋转180度,如果水路在外侧的情况下,模具在旋转过程中,水路尽松动造成易漏水。
2.如果公模板为连体的情况下,水路设计在开侧,将水路固定好在注塑机的转圈上面。
第五个注意事项:当成型第一射完硬胶时,需成型第二射软胶时,需要软胶侧的模具钢位与硬胶一起来进行封软胶的情况下,模具钢位需要做过盈0.1~0.2MM,经过T0试模后,如果发现有压伤硬胶的情况下,再做微调整。
第六个注意事项:1.整全3D进行全检。
2.将后模进行旋转180度,再进行全检查,是否在存干涉。
3.将后模的水管同部创建好,再进行来回180度,旋转进行检查。
塑胶模具双色模具设计注意11项,以及软胶与硬胶材质的选用注意
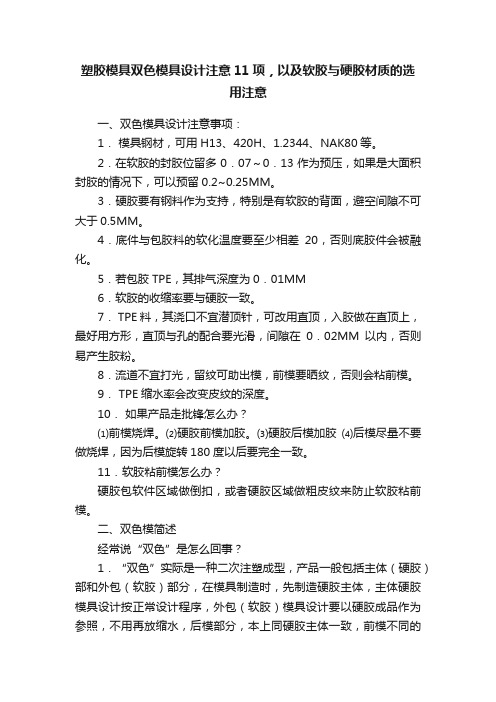
塑胶模具双色模具设计注意11项,以及软胶与硬胶材质的选用注意一、双色模具设计注意事项:1.模具钢材,可用H13、420H、1.2344、NAK80等。
2.在软胶的封胶位留多0.07~0.13作为预压,如果是大面积封胶的情况下,可以预留0.2~0.25MM。
3.硬胶要有钢料作为支持,特别是有软胶的背面,避空间隙不可大于0.5MM。
4.底件与包胶料的软化温度要至少相差20,否则底胶件会被融化。
5.若包胶TPE,其排气深度为0.01MM6.软胶的收缩率要与硬胶一致。
7. TPE料,其浇口不宜潜顶针,可改用直顶,入胶做在直顶上,最好用方形,直顶与孔的配合要光滑,间隙在0.02MM以内,否则易产生胶粉。
8.流道不宜打光,留纹可助出模,前模要晒纹,否则会粘前模。
9. TPE缩水率会改变皮纹的深度。
10.如果产品走批锋怎么办?⑴前模烧焊。
⑵硬胶前模加胶。
⑶硬胶后模加胶⑷后模尽量不要做烧焊,因为后模旋转180度以后要完全一致。
11.软胶粘前模怎么办?硬胶包软件区域做倒扣,或者硬胶区域做粗皮纹来防止软胶粘前模。
二、双色模简述经常说“双色”是怎么回事?1.“双色”实际是一种二次注塑成型,产品一般包括主体(硬胶)部和外包(软胶)部分,在模具制造时,先制造硬胶主体,主体硬胶模具设计按正常设计程序,外包(软胶)模具设计要以硬胶成品作为参照,不用再放缩水,后模部分,本上同硬胶主体一致,前模不同的是有包胶形状,在生产时先生产出硬胶主体,然后把硬胶主体放入外包模具内,进外包软胶注塑生产.2.“双色”也可以称作“包胶”,如果产品产量不高的情况下,可以使用包胶模,先做一套硬胶模具,再通过人工将硬胶放入包胶模具中,成型软胶。
3.软包模具后模部分同主体硬胶一至,有少量避空位,而胶部位要用主体硬胶讨胶不可有虚位要注意的是TPU材料,本身的特性是比较容易粘模的,产品如果可以做沙面尽量做沙面,这样容易脱模!TPU的流动性比较慢,冷却周期也会比较长,只要在生产工艺上注意一些,也不会有什么大问题!三、双色模具双色模标准做法是软胶在模具设计中放收缩水,要与硬胶一致,两套模具公模部分完全一样,母模两个模仁不一样,两套模具装在一台注塑机上注塑(两套模的高度必须一致),第一射硬胶打好后(小水口点进胶),模具旋转180度,做第二射软胶,然后顶出产品,这才叫双色模。
- 1、下载文档前请自行甄别文档内容的完整性,平台不提供额外的编辑、内容补充、找答案等附加服务。
- 2、"仅部分预览"的文档,不可在线预览部分如存在完整性等问题,可反馈申请退款(可完整预览的文档不适用该条件!)。
- 3、如文档侵犯您的权益,请联系客服反馈,我们会尽快为您处理(人工客服工作时间:9:00-18:30)。
汽车灯具双色模设计制造注意事项
设计注意事项:
1、焊接筋上扁顶杆需要排密一些,最好是每隔50MM一根,另外因
为模温要求达到90度,扁顶杆易拉毛,因此扁顶杆需要采取镀钛处
理。
2、焊接筋的深度较深,有时会出现夹气和打光不良的现象,做成镶件,采用埋入式结构,这样不但有利于排气而且有利于扁顶杆孔的加工,
更重要的是有利于孔口飞边的焊接修整。
3、灯具双色模具都采用动模旋转,台湾的注射机转盘精度不是太高。
动模在开模时会带着产品下落,产品易给定模拉脱。
因此模具的精定位很重要,设计时需采用大面积的精定位(精定位面积小了易拉
毛)。
4、灯具一般都采用PMMA和PC材料,由于这些材料的的流动性都
比较差,如果我们设计时采用侧浇口时需将侧浇口设计大一些深一
些。
否则难打足且浇口处缺陷较多,例如流痕,缩印.
5、上板需知:
A.注塑机两头中心距尺寸及定位圈尺寸。
定位圈高出上板15MM,口部5MM处必须要有单边15度导向倒角,定位圈尺寸比名义尺寸小0.1-0.2MM.
B.上板压模螺丝及中心距尺寸C.定位圈要在旋转中心轴线上,半副凹模组装后校直基准平面后,依据凹模固定板中心销孔,在31号五轴数控铣加工上板定位圈.
6、凸凹模固定板,设计时应做到:
A.模板中心需有中心销孔。
B.模板导柱孔需要与中心销对称,因为模板需旋转。
7、底板需知:
A.注塑机底板上有三个定位圈,确认注塑机上尺寸,中心定
位圈高出底板勿超过10MM,因为中心有时有水管易干涉。
两侧定位圈高出底板15MM,口部5MM处必须要有单边15度导向倒角,定位圈尺寸比名义尺寸小0.1-0.2MM.
B.底板压模螺丝规格及中心距规格。
C.底板需确认顶出孔规格及尺寸。
D.定位圈要在旋转中心轴线上,半副凸模组装后校直基准平面后,依据凸模固定板中心销孔,在31号五轴数控铣加工底板定位圈。
注:5、6、7点特别重要,否则无法正常试模.一定要确认好,否则试模时调试模具很麻烦 (双色机建议开两副模具,刚开始试模时将不受特殊限制。
8、顶出距离尽可能缩小,只要确保顶出产品即可,这样扁顶杆有效长度可以减短,就增加了扁顶杆的强度,不至于发生扁顶杆扁曲或断裂。
9、白片成型:
A.白片型腔比理论尺寸加深0.1MM,这样有利于二次注塑白片无需打得很饱,既有利于保护薄壁凹模强度不至于凹模产生开裂可能,而且产品在最终成型时白片有了预压量,白片不易在注塑过程中移动而被冲裂。
B.白片型腔侧面斜度尽可能做单边10度,避免产品留凹模,但同时需要顾及加强分型面薄壁强度。
C.白片外围面比凸模面让开0.5MM,以加强薄壁分型面强度。
此时干万要认真检查反光电铸件位置,高度勿与其干涉,因为电铸件高出凸模表面,极易被忽视,否则后果很严重.一般电铸件价格8-10万.
D.白片面与凸模面对插面放0.1M, M间隙,不易过大,图形上做好。
否则薄壁受压力注射而使其断裂.太小模具热涨后白片外侧分型面易擦毛红片成型面而增加产品包紧力,造成产品开裂
E.白片侧面与外围让档面角落处不能清角,尽可能增加R角1 0.5 ,以提高薄壁强度。
10、凸模部分:
A.所有筋口部不能清角R<0.3MM,(产品壁厚一般为2.5MM,同时考虑缩印否则易产生应力而在顶出时产品开裂.如果在产品允许情况下与客户沟通确认,白片处筋可以比红片处低0.5至1MM ,以增加产品在凸模侧包紧力,不至于产品留凹模。
B.当白片处没有扁顶杆时凸模需放1度的斜度,依据试模情况逐渐增加拔模.有扁顶杆时不放斜度,但不般情况下客户在此处不允许有顶杆,否则会影响产品外观。
C.在客户允许情况下,增设扁顶杆,利于顶出及排气,白片凸模改成镶件,采用埋入式结构。
D.周边融接筋尽可能加大拔模,单边大于或等于3度(但是筋大头不允许超过1.80MM否则将引起缩印。
E.扁顶杆尺寸尽可能做1.2MM (不得小于1.0MM,凸模上配合段长度一般20MM,以增加扁顶杆强度,不易弯曲或断裂.
F.红白产品,浇口位置必须要做流动分析,确认融接线及气痕位置,再与客户沟通并且确认扁顶杆及排气镶件位置。
G.凹模侧分型面必须要密布排气槽`,因为凹模分型面原则上不能动,一腔配两个凸模)。
11、冷却:
A.凹模4进4出,分开冷却单个型腔.耐高温O型圈.浇口尽可能单独有冷却水路,增设水路.
B.凸模4进4出, 分开冷却单个凸模.耐高温 O型圈
C.凹模侧进出水朝向地侧水管孔不能为沉孔,用油管接头,所有水管连接孔,孔径尽可能大一般为15mm,水管离开型面2倍孔径,以免存在开裂可能.冷却水必须模内连接,以防漏水烫伤可能。
D.气阀控制口内O型圈必须用耐高温O型圈,连接管用高温油管连出,否则易烫坏气阀控制器.气阀控制器需要增设保护装置在允许情况下放大模板(尽可能放大操作者对侧、不允许放上方,操作不方便,同时外接气源进入气阀控制器必须要增设滤清器,否则将堵塞气阀控制器气路及阀芯
12、导套必须增设,导套盖板(因为上下模在注塑机上有不同心现象,易把导套拉出固定板
13、凸模侧进出水,靠近操作者侧进出朝向地侧,非操作者侧朝天,因为水温较高以防烫伤,水管不能做沉孔,用油管接头,所有水管连接头孔,孔径尽可能大一般为15mm,水管离开型面2倍孔径,以免存在开裂可能,冷却水必须模内连接,以防漏水烫伤可能。
14、凸模因都为淬火件,所以在分型面不能有清角存在易裂,产品清角用小R连接,此点请设计一定要考虑。
15、凸凹模侧面所有耐磨板及精定位必须采用埋入式,干万不能平贴,(因模具温度高,易涨紧螺丝易断。
16、上下底板依据情况增设隔热板。
(因为模温较高,不过少数双色注塑机前后墙板上附带有隔热板
17、型腔型芯正面尽量避开增设水管闷头,(以防漏水,腐蚀型腔、型芯。
18、所有白片红片针阀式浇口,出口一般都2MM,否则将影响产品处观,仔细检查热流道公司最终确认版本,若超差一定要与客户沟通,否则将引起凹模报废。
制造注意事项:
1、现在公司设计的精定位在制造过程中都不尽人意,都是放在模
具上看看的,没有起到精定位的作用(有些精定位的间隙都在
0.2MM左右),双色旋转模因机床精度问题,今后必须要做准精
度。
2、焊接筋上的扁顶杆最好做平整,绝对不能低于凸模槽,若低于
凸模槽会产生扁顶杆处高出焊接筋,使焊接时开裂。
低于焊接筋
0.2MM以内也可以,焊接时熔化塑件一般在0.8MM左右,低的太
多会焊接时强度不够及漏水。
3、电铸件边缘口部成形处需打光到2000粒砂纸,固定框口部成形
处也需打光,否则产品易开裂。
4、所有筋及侧面都需认真打光,打光时需注意脱模斜度,面需打
平整。
5、因模具都采用高温,在配合面配合的过程中都要考虑到热涨的
因素,可配松一些。
6、模具装配时镶件及扁顶杆不能有油,装配时一定要用酒精擦干
净.因为模具温度高受热后,油熔化打入产品,需打几十模也不会全部清理,严重浪费了原材料。
7、顶出板与凸模固定板之间用两只螺丝连接,因为顶板与凸模固定板之间有复位弹簧且扁顶杆配合段较短,且今后在拆顶杆固定板时有时不一定能较为顺利吊出,在上下过程中扁顶杆易脱开凸模配合段,扁顶杆角碰撞让档台阶从而造成顶杆塌角.
8、凸模侧热融筋粗冲时可以单冲,但是精冲时一定要与扁顶杆组合冲,否则扁顶杆孔口勿塌角而且底面易产生断差.
9、凸模侧热融筋出光时干万要小心扁顶杆口部塌角,底面最好组合扁顶杆后一起出光.
10、当白片不被红片包围而是对融时,红片白片扁顶杆位置一定要靠近对融边,因为该种类型产品融接边连接强度较差,如果离对融边较远时,产品易开裂.
11、凸模为两腔一样,所以所有分型面,特别白片分型面深度及侧面一定要一致,在同一台夏米尔机床加工,误差控制在0.02mm之内,如果有差异将直接影响钳工配模,根本无法修整.
项目部工艺组
2008/1/7。