汽车整车三维测量解决方案
汽车零件的三维检测与快速数字化建模

汽车零件的三维检测与快速数字化建模摘要:本文通过三维光栅扫描获取汽车挡雨板表面点云数据,并对点云数据做简化和曲面拟合处理,生成通用NURBS曲面。
结果显示,曲面-点云标准偏差为0.201071mm,符合高质量曲面重建要求。
关键词:光栅扫描点云简化曲面重构\1、前言逆向工程也称反求工程[1-3],是把实物转变为CAD模型相关的数字化技术、几何模型重建技术和产品制造技术的总称。
它一般包括三维数字扫描、点云数据处理、曲面重构等过程。
而通常所说的设计都是正向工程,初始没有实物,先形成设计思想和理念,然后利用正向软件,如CAD、UG NX、PROE、CATIA等进行设计,最后加工成型,属于“从无到有”的过程,遵从“概念设计-产品CAD 模型-产品”的过程。
逆向工程工作流程,首先采用三维测量仪对被测物体进行测量,获取测量数据,然后对点云除噪、点云简化、点云修补、点云拼接和曲面重构,形成连续的平滑曲面,之后和正向软件进行接口,形成数控加工代码,或者通过快速成型工艺和三维打印技术形成产品。
2、常用逆向软件在专用逆向软件出现之前,CAD模型重建主要利用通用正向软件实现,如UG NX、PRO/E和CATIA等,随着加工精度提高和加工时间的缩短,正向软件不能满足快速正确建模需要,目前应用的逆向软件很多,常见的有Imageware、CopyCAD、Geomagic Studio和Rapidform等。
Imageware是美国EDS公司专门为逆向工程开发的逆向软件,广泛应用于汽车、航空航天、家电、模具和计算机零部件设计与制造领域,具有强大的测量数据预处理、曲面拟合和精度检测功能,可以处理上百万的离散数据,根据点云数据重建的A级曲面具有良好的光顺性和连续性,其曲面检测功能可直观显示所构造的曲面模型与实际测量数据之间的偏差以及平面度、圆度等几何公差。
CopyCAD是英国DELCAM公司的产品,可以快速编辑数字化数据,在短时间内构造出高质量复杂曲面。
汽车车身变形测量矫正与修复

车身测量的控制点用于检测车身损伤与变形的程度。车身 设计与制造中设有多个控制点,检测时可以技术要求测量车身 上各个控制点之间的尺寸,如果误差超过规定的极限尺寸时, 应设法修复使之达到技术标准规定的范围。
对车身进行整体矫正时,可根据上述控制点的分布将车身 分为前、中、后三部分(图4-2),这种划分方法主要基于车 身壳体的刚度等级和区别损伤程度,分析不同控制点及其在车 身测量基准中的作用和意义。
第三节 车身损坏诊断
本节主要介绍的内容有:
● 车身受力与操作分析 ● 车身式车辆损坏 ● 车架损坏类型
一.车身力与操作分析
前侧中间处受外力所造成的损伤。通常容易使左右罩板向内侧拉伸, 因此应重点检查下述部位:
◆左右罩板配合处附近; ◆前横梁与左右侧梁的装配连接处附近。
二.车身式车辆损坏
1.前部损坏 前部损坏是由于车头撞上另一辆车或其他物体引起的损坏,碰撞力 大小取决于车重、车速、撞击物以及撞击面积。如果碰撞不大,将造成 保险杠后移,使前侧梁、保险杠座、前翼子板、散热器支座和发动机罩 锁支柱等发生弯曲变形。 如果碰撞进一步增加,前翼子板将被撞到前门上,发动机罩饺链将 上弯,触到发动机罩,前侧梁折皱,与悬架所在横梁接触。如果碰撞再 增大,前翼子板围裙和前车身支柱(特别是前门饺链上部区域)将发生 弯曲变形,前门可能被撞掉。此外,前侧梁折皱加大,使悬架横梁弯曲, 发动机与驾驶室之间的隔板和地板也会变弯以吸收碰撞。
(2)下陷变形 下陷变形是指前围部位发生低于正常位置的一种变形。前横梁处也 可能会出现下陷变形,表现为前梁两端的距离比正常值短,中部降低。
(3)侧倾变形 当车身前段、中段或后段发生侧向变形时就存在侧倾变形。 检测侧倾变形需要使用三个自定心规。
• 四、汽车碰撞诊断的基本步骤
汽车车身三坐标测量与数据处理

汽车车身三坐标测量与数据处理摘要:三坐标测量机主要是针对汽车整车进行检测,该检测机器具有高精度,高速度的特点,并且对于测量的数据也能很快的进行处理,能够满足大量的汽车整车检测任务的需求,三坐标测量机的核心工作就是针对汽车的各项数据进行测量和分析,汽车车身的零部件在传统的测量方式下不易测量,同时加上其他因素的影响,使得测量数据误差较大,因此在长期的发展中三坐标测量在汽车车身数据测量中发挥了重要作用,三坐标测量机使用SPC技术,这门技术的使用大大的提高了对于车身的数据处理速度,本文提出了一种利用程序方法对数据进行汇总的数学模型和编程思路结合工作中的经验,对SPC技术的实际应用进行了一些粗浅的探讨。
通过使用这些技术和方法,可以实现数据采集数据处理和数据分析的全程自动化。
关键词:汽车车身;三坐标测量;数据处理引言汽车的质量好坏在进行出厂之前都需要通过检测合格后才能出厂,车身的检测是汽车零部件的重要部分,三坐标测量机主要是针对汽车整车进行检测,该检测机器具有高精度,高速度的特点,并且对于测量的数据也能很快的进行处理,能够满足大量的汽车整车检测任务的需求,而三坐标测量机能够有效的解决这个问题,它自身的灵活性使得在汽车车身整车的测量过程中,在使用三坐标测量机对于汽车车身进行测量的过程中,测量数据都是建立在零件的定位坐标系中,车身检测是汽车工业中关于零部件检测的重要部分,该项检测直接关系着整车的外观和质量。
三坐标测量机普遍具有高精度、高速度、很好的柔性、很强的数据处理和适应现场环境的能力,尤其是丰富的、不断扩展的软件功能,目前愈来愈多的应用于汽车车身检测中。
一,三坐标测量技术发展和应用我国汽车工业经过多年的快速发展,其生产已初具规模,各汽车生产厂家在提高产量,增加品种的同时,也在力图使用更为科学的方法对产品质量进行控制,其中三坐标测量机是必不可少的设备之一,三坐标测量机在产品研发和生产过程中发挥了巨大作用。
该机器配备了功能强大的PowerInspect测量软件,不但可以完成各种复杂零件的测量任务,而且还可应用于焊装生产线的统计过程控制。
汽车研发:DMU(数字化电子样车)校核的内容、方法及流程!

汽车研发:DMU(数字化电子样车)校核的内容、方法及流程!很多兄弟走在路上,看到身材很棒的妹纸,都喜欢走到妹子的前面,回过身来假装往后看,校核一下妹纸的脸蛋,其实汽车也要校核,经过校核,能查出很多问题,提升设计,降低量产后的问题。
今天漫谈君就和大家讲一讲:DMU(数字化电子样车)校核随着汽车工业的发展,计算机三维设计技术的使用,DMU校核已经发展为研发工作中重要的一项工作。
随着产品更新换代速度的加快,现有样机的制造周期和制造成本已难以适应产品开发的需求,使用计算机三维设计技术建立数字样机,可实现实物样机的作用,有效缩短周期、降低成本。
一、DMU是什么DMU是Digital Mock—Up的缩写,又叫数字化电子样车,指一个正确的、完整的整车三维数模,是由3D软件设计出的零部件按照其内在逻辑而组成的结构性的虚拟样车模型,而且这个虚拟样车可以进行不同的模拟和评价。
二、DMU的作用1、对整车设计进行检查和监控,并指出相关的问题,以便保证设计质量和项目进度。
2、提供各类、各种档次的可视化功能,用不同方式对电子样车进行全方位的审视、评估和模拟真实的视觉效果。
尽可能在数字化环境中看到产品在真实世界中相同的效果,实现低成本、高效率的产品可视化模拟。
3、对车型或部件间进行功能性分析,包括:机构运动、干涉、拆装、空间和管理分析等。
尽可能在数字化环境中进行与真实世界中相同的分析,使设计师在设计早期就发现问题,在设计的各个阶段,及时、大量地进行各种分析,提高产品设计质量。
4、应用关联设计,按照自上向下的设计方式,实现装配之间、零部件之间、一个模型文件中的多个几何实体之间、曲面模型和实体模型之间、特征之间等多种层次的端到端的各类关联。
基于骨架的DMU 设计分析方式,实现数字样机的快速更改,降低成本,快速地进行多方案的评估与研讨,通过建立关联性的设计模板进行管理和重用,提高设计效率。
5、检查配置及零件完整性。
三、DMU校核内容1、DMU静态干涉检查静态干涉检查是DMU中也是整车设计中最重要的部分,干涉检查根据项目周期可以分为:1)设计过程中干涉检查;2)后期进行验证干涉检查;3)后期发生设计变更后的干涉检查。
VBOX汽车整车性能测试系统方案

1.VBOX III汽车整车性能测试方案1.1 系统方案介绍基于GPS的VBOX III数据采集系统是一种功能强大的仪器。
它是基于新一代的高性能卫星接收器,主机一套用于测量移动汽车的速度和距离并且提供横纵向加速度值,减速度,MFDD,时间和制动、滑行、加速等距离的准确测量;外接各种模块和传感器可以采集油耗,温度,加速度,角速度及角度,转向角速度及角度,转向力矩,制动踏板力,制动踏板位移,制动风管压力,车辆CAN接口信息等其它许多数据。
由于它的体积较小及安装简便,其非常适合汽车综合测试时使用。
由于VBOX本身带有标准的模拟,数字,CAN 总线接口,整个系统的功能可以根据用户的需要进行扩充。
系统组成图如下:以上第二——十九项为可选项1.2 可测量的参数的量程及精度:1.3特点:•全套测量系统体积极小,安装简便迅速•能完成国家标准要求的汽车动力性,经济性,操纵稳定性,制动性能等实验•在线显示4个测量参数•各种测量或采集到的参数可以实时显示•可根据要求设定各种不同的试验条件进行试验•制动触发形式多样,使试验更加方便•WINDOWS操作界面的设定和分析软件,使用方便•高精度、高可靠性,高耐振、抗冲击性能确保测试质量•用GPS非接触式速度和距离测量•现场即时打印功能,打印各个测量或采集到的参数,实现现场数据阅读•大容量紧凑式闪存卡(CF卡)即时存储数据,以便后处理•可扩展连接其他各种传感器•绘制轨迹图,圈数定时1.4 可进行的试验:•滑行试验•油耗试验•爬陡坡试验•最高车速试验•加速性能试验•制动性能试验•操纵稳定性试验•最小稳定车速试验•最小转弯直径测量实验•制动踏板力测量实验•制动踏板行程测量实验•制动管路压力测量实验•汽车防抱制动系统性能实验•温度测量实验•里程,速度表校验等其它试验1.5 可满足的国家标准:GB/T 12545 - 1990 汽车燃料消耗量GB/T 12547 - 1990 最低稳定车速GB/T 12536 - 1990 汽车滑行试验GB/T 12543 - 1990 汽车加速性能GB/T 12539 - 1990 汽车爬坡性能GB/T 12544 - 1990 汽车最高车速GB/T 12676 - 1999 汽车制动系统性能GB/T 6323 - 94 汽车操纵稳定性试验方法GB/T 12540 - 90 汽车最小转弯直径测定方法GB/T 13594 - 92 汽车防抱制动系统性能要求和试验方法1.6 应用实例图片:VBOX II在测试世界(芬兰)的应用:2. 关于Racelogic 公司VBOX产品概述GPS 技术在1995年就已经面世但是知道最近才足够精确用于车辆测试(见GPS的概述)。
车身三维尺寸视觉检测及其最新进展

基准坐标 系下( 即系统全局校准)传感器由系统 中 , 的计算机控制。 测量时 , 每个传感器测量相应点的三
维坐标, 并转换到基准坐标系中, 全部传感器给出车
身上所有被测点的测量结果 , 完成系统测量任务 。
2 车身三维尺 寸视觉检测原理
典型的车身三维尺寸视觉检测系统原理如图 1
邾继贵 , 杨学友 , 叶声华
( 天津大学工程精 密剥试技 术及仪嚣国家重点 弗验室 , 天津 307 ) 0 0 2
摘要 : 车身三维尺寸视觉检测技术是 近十几年发展起 来的一项 白车身尺寸测 试技术 , 具有非接 触 、 度 速
快 可在线等突出优点 , 为全面提高车身 的制造精度提供 了有效的检 测手段 。结台实 际科研经历 , 讨论了
传感器包括光平面投射器 和摄像机两部分 , 基 于三角法测量原理。 测量时, 光平面投射器投射出光 平面 , 光平面和被测物体表面相交形成光条 , 光条图
率和维护成本。 最新研制的视觉传感器采用 了基于立体视觉检 测原 理的 统一结 构 ,克服 了两种 传感器 结构及 校 准 方法不统一的缺点 , 传感器原理如图4所示。
维普资讯
邾继责等: 车身三雏足寸视觉检测厦 其最新进展
a 传感器校准困难 、 . 精度低。 传感器在使用前 ,
必须标定光平面和摄像机之间的空间关系 ,目前的 方法是使用细丝散射结合经纬仪的方法,这种方法 受散射光点无法精确瞄准的影响 ,校准精度难 以提
视觉传感器而言是两种不同类型的被测点 ,需要光
条结构光传感器和光栅结构光传感器 。光条结构光 传感器原理如图 2 所示 , 用于测量棱线点 ; 光栅结构 光传感器原理如图 3 所示 , 当于具有多个光平面 相 的光条传感器 ,一次测量可以同时得到多个不同空 间位置上点的三维坐标 ( 如测量圆孔时 , 可得到圆周 上多个点的坐标 )由此计算 出被测特征点 ( , 如圆孔
提高汽车车身零件的三坐标测量
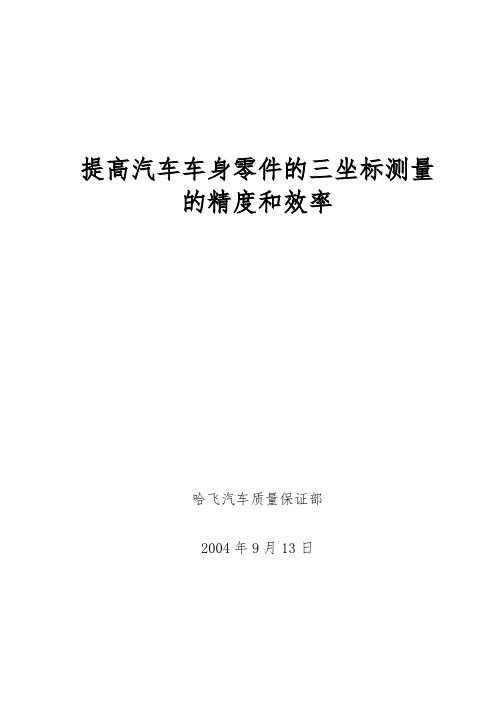
提高汽车车身零件的三坐标测量的精度和效率哈飞汽车质量保证部2004年9月13日目录一、建立正确的零件坐标系,是实现汽车车身零件精确测量的基础1、建立正确的零件坐标系的重要性2、建立坐标系的原则和基准的选择3、建立坐标系的方法和应用4、三阶平面在建立坐标系中的应用5、临时坐标系的运用6、建立零件坐标系过程的自动测量二、正确的零件夹紧方案是汽车车身零件测量精度的保证1、夹紧方案选择2、FIVE U-unique柔性夹具系统在车身零件夹紧定位上的应用三、测量方案的选取1、编制自动测量程序,实现车身零件的自动测量2、单件零件的测量3、矢量点的测量四、测量的准备阶段——探针的校准,是精确测量的保证和前提五、测量数据的处理和应用[摘要]:本文从零件坐标系的建立,测量基准的选择,测量方案的制定、测量夹紧方案的选择、以及自动测量程序的编写等方面内容,结合实际工作中积累的经验和研究对如何保证汽车车身零件的三座标测量的精度和提高测量的效率进行了论述。
[关键词]:三坐标测量机测量坐标系基准精度效率测量方案[前言]:随着汽车工业的高速发展,行业间的竞争也更加激烈,而质量是赢得竞争的基础,不论是对冲压件还是焊接总成零件的质量要求都越来越高,对测量工作也提出了更高的要求。
三坐标测量机以其快捷、精确、方便的特点在汽车制造业发挥着越来越大的作用,成为质量控制不可缺少的手段。
利用三坐标测量机强大的空间检测能力和分析计算功能可以实现对汽车车身零部件快速准确的测量,提供形状、尺寸、和位置的完善测量,并可执行包括首件检测、轮廓测量、逆向工程、焊接生产线的夹具调整、过程控制以及文件归档等在内的多种测量与检测任务,从而为降低开发研制周期,进行产品全过程控制,提高产品的质量,增加经济效益,提高产品的竞争力作出贡献。
简化测量机的使用方法、减少人机对话实现自动测量减少人为因素造成的误差、缩短测量工时提高利用率是三坐标使用中的主要课题和研究探索的方向。
整车碰撞模型测量点及局部坐标系定义

Q/JLY J711 -2009整车碰撞模型测量点及三维坐标系定义流程与规范编制:校对:审核:审定:标准化:批准:浙江吉利汽车研究院有限公司二〇〇九年三月前言为了给整车碰撞模型进行测量点、三维坐标系定义和加速度传感器布置提供依据,指导CAE分析后处理操作,评价碰撞后车身位移量和侵入速度,结合本企业实际情况,制定出本规范。
本标准由浙江吉利汽车研究院有限公司提出。
本标准由浙江吉利汽车研究院有限公司工程分析部负责起草。
本标准起草人:闫高峰本标准于2009年2月31日发布并实施。
1 范围本标准规定了乘用车进行CAE分析时整车测量点、三维坐标系的定义和加速度传感器的布置。
本标准适用于完全正面碰撞分析、40%正面偏置碰撞分析和侧面碰撞试验分析。
2 规范性引用文件下列文件中的条款通过本标准的引用而成为本标准的条款。
凡是注日期的引用文件,其随后所有的修改单(不包括勘误的内容)或修订版均不适用于本标准,然而,鼓励根据本标准达成协议的各方研究是否可使用这些文件的最新版本。
凡是不注日期的引用文件,其最新版本适用于本标准。
C-NCAP 管理规程GB 11551-2003 乘用车正面碰撞的乘员保护3 软硬件设施a)软件设施:主要运用的软件有HYPERMESH和HYPERVIEW、LS-PREPOST;b) 硬件设施:高性能计算机4 输入条件4.1 整车测量点位置和三维坐标系模型、加速度传感器模型碰撞仿真分析后处理所需模型a) 整车测量点位置;b) 加速度传感器模型;c) 三维坐标系模型;4.2 整车碰撞分析模型测量点、三维坐标系定义和加速度传感器布置需要在整车环境下进行,数据要求如下:a)碰撞分析模型;b)实车实验中相对应的测量点和加速度传感器位置。
c)及其他必要参数。
5 输出物输出整车加速度传感器模型和三维坐标系模型的K文件。
6 整车碰撞建模中测量点、加速度传感器及三维坐标系布置流程7 整车测量点位置7.1 正面碰撞正面碰撞变形量测量点位置包括:a)前地板(驾驶员搁脚处);b)前地板(前排乘员搁脚处);c)中央通道;d)左右前排乘员舱框架;e)油门、制动及离合踏板中心的三个点或该三点对应在防火墙上面的三点;f)转向管柱上端面中心;g)方向盘中心对应在IP横梁上的一点,以及横向距离该点150mm处左右两点;图1 前地板、中央通道变形量测量参考点图2 左右前排乘员舱框架测量点图3 踏板、防火墙和转向管柱测量点7.2 侧面碰撞侧面碰撞变形量测量点位置包括:a)左前/后车门外板;b)左B柱;c)左上边梁;d)左下边梁(门槛);图4 左车门、上下边梁和B柱参考点图5 B柱测量点7 三维坐标系定义7.1 三维坐标系形状a)三维坐标系几何特征下图为三维坐标系的几何形状。
- 1、下载文档前请自行甄别文档内容的完整性,平台不提供额外的编辑、内容补充、找答案等附加服务。
- 2、"仅部分预览"的文档,不可在线预览部分如存在完整性等问题,可反馈申请退款(可完整预览的文档不适用该条件!)。
- 3、如文档侵犯您的权益,请联系客服反馈,我们会尽快为您处理(人工客服工作时间:9:00-18:30)。
佛山市顺德区路前产品设计有限公司,简称:路前科技。
位于广东省佛山市顺德区大良镇,成立于2013年。
公司成立依托顺德职业技术学院《逆向工程与快速成型实验室》,顺德大学位于佛山市顺德区大良德胜东路,实验室具备行业内最为先进的设备(主要设备:德国ATOS扫描系统、Dimension SST 1200es工业级3D打印机、project 660全彩3D打印机)
以下为佛山市顺德区路前产品设计有限公司运用实验室配备的天远三维摄影测量系统DigiMetric在汽车行业的应用方案:
在进行整车三维测量时,由于被测物体较大,仅仅采用三维扫描仪进行整车测量的话,会造成累计误差过大。
为有效消除累计误差造成的影响,我们提出以下解决方案:
先用天远三维摄影测量系统DigiMetric进行三维摄影测量,获得高精度的全局框架点数据,再将框架点数据导入天远三维扫描仪OKIO进行三维扫描,以框架点数据为骨架进行三维数据的拼接,从而有效地消除累计误差,提高数据测量的精度,在采用该解决方案后能够将系统累积误差控制在0.1mm/4m的范围之内。
1、在汽车车身上布置编码点和标志点
2、用天远三维摄影测量系统DigiMetric对整车进行多角度拍照
3、将照片导入天远三维摄影测量软件DigMetric中
4、通过天远三维摄影测量系统软件DigMetric计算得到车身上标志点的三维框架数据
全局框架点数据
5、将框架点数据导入到天远三位摄影测量系统OKIC中,以三维摄影获得的框架点数据为骨架,进行整车扫描测量。
6、扫描得到整车三维点云数据
欢迎莅临顺德大学《逆向工程与快速成型实验室》参观指导!。