注塑模具毕业设计
注塑模具毕业设计例(衬套)
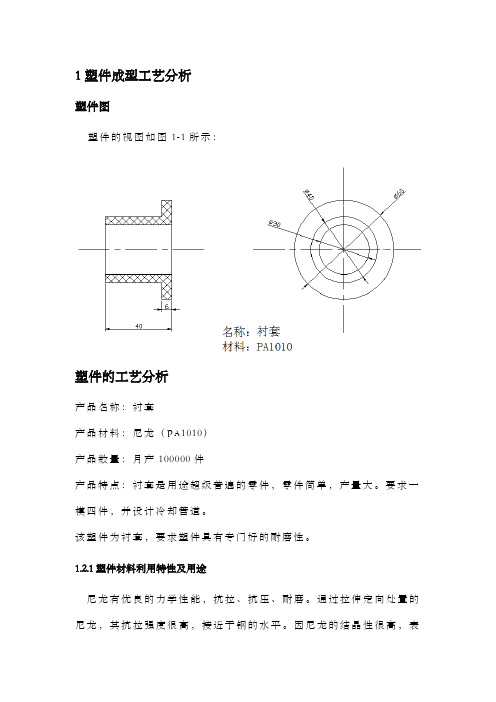
1塑件成型工艺分析塑件图塑件的视图如图1-1所示:塑件的工艺分析产品名称:衬套产品材料:尼龙(PA1010)产品数量:月产100000件产品特点:衬套是用途超级普遍的零件,零件简单,产量大。
要求一模四件,并设计冷却管道。
该塑件为衬套,要求塑件具有专门好的耐磨性。
1.2.1塑件材料利用特性及用途尼龙有优良的力学性能,抗拉、抗压、耐磨。
通过拉伸定向处置的尼龙,其抗拉强度很高,接近于钢的水平。
因尼龙的结晶性很高,表面硬度大,摩擦系数小,固具有十分突出的耐磨性和自润滑性。
它的耐磨性高于一样用做轴承材料的铜、铜合金、一般钢。
尼龙耐碱、弱酸,但强酸和氧化剂能侵蚀尼龙。
尼龙的缺点是吸水性强、收缩率大,常常因吸水而引发尺寸转变。
其稳固性较差,一样只能在80°C~100°C之间利用。
为了进一步改善尼龙的性能,常在尼龙中加入减摩剂、稳固剂、润滑剂、玻璃纤维填料等,以克服尼龙存在的一些缺点,提高机械强度。
1.2.2成形特点尼龙原料较易吸湿,因此在成形加工前必需进行干燥处置。
尼龙的热稳固性差,干燥时为幸免材料在高温时氧化,最好采纳真空干燥法;尼龙的熔融黏度低,流动性好,有利于制成强度专门高的薄壁塑件,但容易产生飞边,故模具必需采纳最小间隙;熔融状态的尼龙热稳固性较差,易发生降解是塑件性能下降,因此不许诺尼龙在高温料筒内停留太长时刻;尼龙成形收缩范围及收缩率大,方向性明显,易产生缩孔、凹痕、变形等缺点,因此应严格操纵成形工艺条件。
塑件成形工艺参数确信PA1010熔程较窄,一样为3~4℃。
熔融流动性较好。
适合注射成型、挤出成型和吹塑成型。
要紧成型工艺参数如下:密度g/ cm3;收缩率~(纵向) ~(横向)(1)干燥鼓风干燥温度90℃±5℃干燥时刻约4~5h、真空干燥温度85℃±5℃,一样最好选择真空干燥工艺,幸免热氧化变色(2)注塑工艺料筒温度: 后部190~210℃中部200~220℃前部210~230℃喷嘴200~210℃模具温度20~40℃注射压力60~80MPa注射周期30~50S2拟定模具结构形式型腔数量的确信为了制模具与注射机的生产能力相匹配,提高生产效率和经济性,并保证塑件精度,模具设计时应确信型腔数量。
模具设计与制造专业毕业论文--注塑模具设计
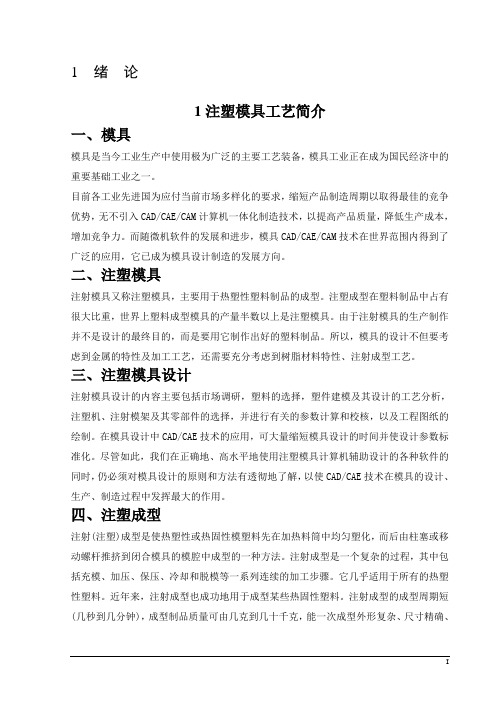
1 绪论1注塑模具工艺简介一、模具模具是当今工业生产中使用极为广泛的主要工艺装备,模具工业正在成为国民经济中的重要基础工业之一。
目前各工业先进国为应付当前市场多样化的要求,缩短产品制造周期以取得最佳的竞争优势,无不引入CAD/CAE/CAM计算机一体化制造技术,以提高产品质量,降低生产成本,增加竞争力。
而随微机软件的发展和进步,模具CAD/CAE/CAM技术在世界范围内得到了广泛的应用,它已成为模具设计制造的发展方向。
二、注塑模具注射模具又称注塑模具,主要用于热塑性塑料制品的成型。
注塑成型在塑料制品中占有很大比重,世界上塑料成型模具的产量半数以上是注塑模具。
由于注射模具的生产制作并不是设计的最终目的,而是要用它制作出好的塑料制品。
所以,模具的设计不但要考虑到金属的特性及加工工艺,还需要充分考虑到树脂材料特性、注射成型工艺。
三、注塑模具设计注射模具设计的内容主要包括市场调研,塑料的选择,塑件建模及其设计的工艺分析,注塑机、注射模架及其零部件的选择,并进行有关的参数计算和校核,以及工程图纸的绘制。
在模具设计中CAD/CAE技术的应用,可大量缩短模具设计的时间并使设计参数标准化。
尽管如此,我们在正确地、高水平地使用注塑模具计算机辅助设计的各种软件的同时,仍必须对模具设计的原则和方法有透彻地了解,以使CAD/CAE技术在模具的设计、生产、制造过程中发挥最大的作用。
四、注塑成型注射(注塑)成型是使热塑性或热固性模塑料先在加热料筒中均匀塑化,而后由柱塞或移动螺杆推挤到闭合模具的模腔中成型的一种方法。
注射成型是一个复杂的过程,其中包括充模、加压、保压、冷却和脱模等一系列连续的加工步骤。
它几乎适用于所有的热塑性塑料。
近年来,注射成型也成功地用于成型某些热固性塑料。
注射成型的成型周期短(几秒到几分钟),成型制品质量可由几克到几十千克,能一次成型外形复杂、尺寸精确、带有金属或非金属嵌件的模塑品。
因此,该方法适应性强,生产效率高。
一模三用注塑模具设计
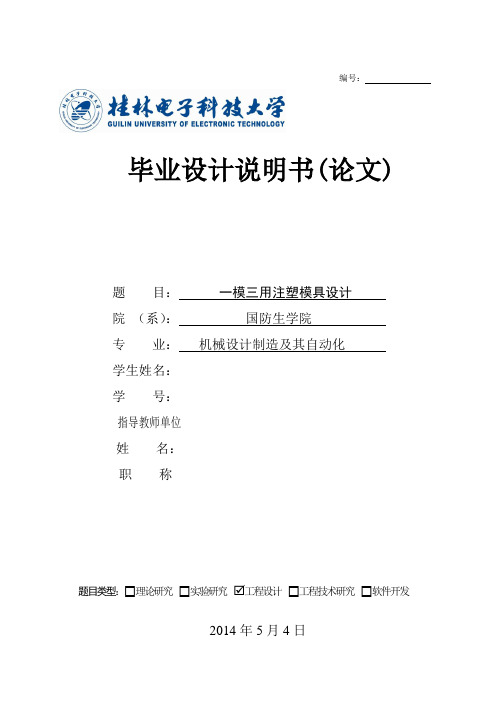
引言
自从我国加入世贸组织(WTO)后,将获得一个更加稳定的国际经贸环境,从而有利于我国与各国、各地区的经济贸易合作,有利于世界经济的稳定发展,我国的利用外资领域将进一步扩大,国内和国外模具企业都可以从中得到更多的机会和收益。
关键词:制件成本;一模多用;分线盒;分型面;冷却系统
Abstract
Analysis of plastic parts to reduce the cost method,proposed in order to reduce costs,willmeet certain conditions,the specifications of several forms of plastic parts used by forming a mold,is amulti-use die;the same time a study on the use of injection-mold the three forms of classification and conditionsof production examples of die design elements,such as mold ingenious structural characteristics.The practice has proved that under certain conditions,the use of a multi-use injection mold can reduce thenumber of mold,reduce costs,and greatly enhance their market competitiveness.
注塑模设计-毕业设计说明书
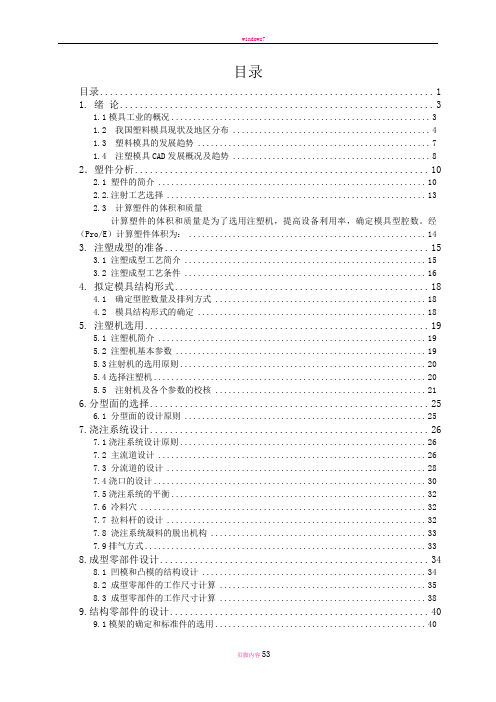
目录目录 (1)1. 绪论 (3)1.1模具工业的概况 (3)1.2 我国塑料模具现状及地区分布 (4)1.3 塑料模具的发展趋势 (7)1.4 注塑模具CAD发展概况及趋势 (8)2.塑件分析 (10)2.1 塑件的简介 (10)2.2.注射工艺选择 (13)2.3 计算塑件的体积和质量计算塑件的体积和质量是为了选用注塑机,提高设备利用率,确定模具型腔数。
经(Pro/E)计算塑件体积为: (14)3. 注塑成型的准备 (15)3.1 注塑成型工艺简介 (15)3.2 注塑成型工艺条件 (16)4. 拟定模具结构形式 (18)4.1 确定型腔数量及排列方式 (18)4.2 模具结构形式的确定 (18)5. 注塑机选用 (19)5.1 注塑机简介 (19)5.2 注塑机基本参数 (19)5.3注射机的选用原则 (20)5.4选择注塑机 (20)5.5 注射机及各个参数的校核 (21)6.分型面的选择 (25)6.1 分型面的设计原则 (25)7.浇注系统设计 (26)7.1浇注系统设计原则 (26)7.2 主流道设计 (26)7.3 分流道的设计 (28)7.4浇口的设计 (30)7.5浇注系统的平衡 (32)7.6 冷料穴 (32)7.7 拉料杆的设计 (32)7.8 浇注系统凝料的脱出机构 (33)7.9排气方式 (33)8.成型零部件设计 (34)8.1 凹模和凸模的结构设计 (34)8.2 成型零部件的工作尺寸计算 (35)8.3 成型零部件的工作尺寸计算 (38)9.结构零部件的设计 (40)9.1模架的确定和标准件的选用 (40)9.2 合模导向机构的设计 (41)10.推出机构的设计 (43)10.1 推出力的计算 (44)10.2 制品推出的基本方式 (44)11.温度调节系统的设计 (45)11.1 冷却回路的尺寸确定 (45)11.2 冷却水回路设置的基本原则 (48)11.3冷却系统的结构 (48)12.模具材料的选择 (49)12.1塑料模零件选材原则 (49)12.2 模具材料的选用 (49)13.结束语 (50)14.致谢 (51)15.参考文献 (52)1. 绪论1.1模具工业的概况模具是机械、汽车、电子、通讯、家电等工业产品的基础工艺装备之一。
注塑模具设计毕业设计
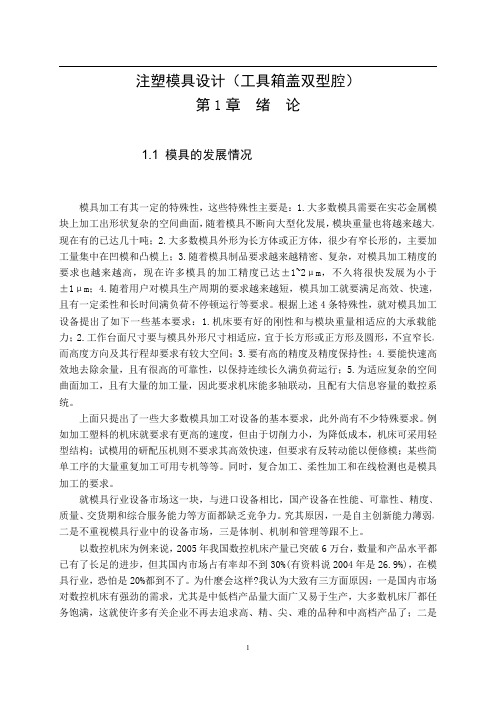
1.2 选题的依据和意义
这次的毕业设计题目是根据本次在哈尔滨齐塑汽车饰件有限公司的实习内容定的,
2
在原模件的基础上给与创新,设计奇瑞车的工具箱盖双型腔注塑模设计。 塑料制品已在工业,农业,国防和日常生活中的方面得到广泛应用。特别是在电
子业中则为突出。电子产品的外客大部分是塑料制品,产品性能的提高要求高素质的塑 料模具和塑料性能。成型工艺和制品的设计。
国内发展: 目前,国内生产的小模数塑料齿轮等精密塑料模具已达到国内外同类产品水平。使
用 CAD 三维设计、计算机模拟注塑成形、抽芯脱模机构设计新颖等对精密、复杂、大 型模具的制造水平起到了很大作用。34 英寸彩电塑壳和 48 英寸背投电视机壳模具,汽 车保险杠和仪表盘的注塑模等大型磨具,在国内已可以生产。 国外发展:
塑料制品的成型方法很多。其主要用于是注射,挤出,压制,压铸和气压成型等和 气压成型等。而注射模,挤出约占成型总数的 60%以上。注射成型分为加料,熔融塑料, 注射制件冷却和制件脱模等五个步骤。当然如利用电气控制。可实现半自动化或自动化 作业。
因注射模成型的广泛适用,正是我这个设计的根本出发点。
1.3 本课题在国内外的发展状况
虽然近几年模具出口增幅大于进口增幅,但所增加的绝对量仍是进口大于出口,致 使模具外贸逆差逐年增大。这一状况在 2008 年已得到改善,逆差略有减少。模具外贸 逆差增大主要有两方面原因:一是国民经济持续高速发展,特别是汽车产业的高速发展 带来了对模具旺盛需求,有些高档模具国内的确生产不了,只好进口;但也确实有一些 模具国内可以生产,也在进口。这与中国现行的关税政策及项目审批制度有关。二是对 模具出口鼓励不够。现在模具与其它机电产品一样,出口退税率只有 13%,而未达 17%。
(毕业设计论文)塑料注射模具设计
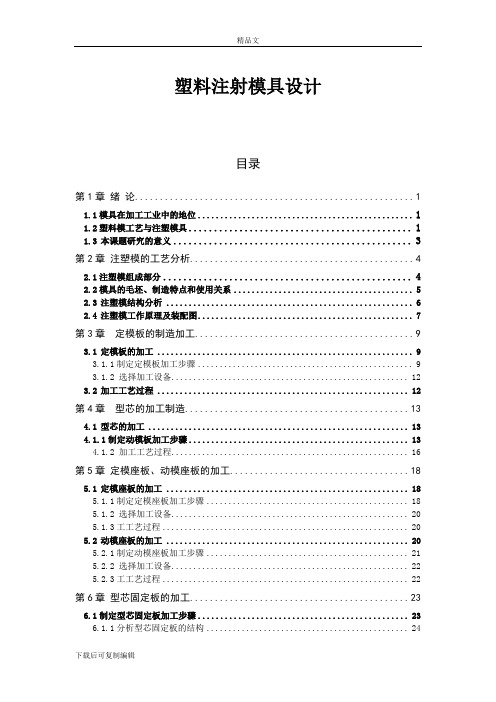
塑料注射模具设计目录第1章绪论 (1)1.1模具在加工工业中的地位 (1)1.2塑料模工艺与注塑模具 (1)1.3本课题研究的意义 (3)第2章注塑模的工艺分析 (4)2.1注塑模组成部分 (4)2.2模具的毛坯、制造特点和使用关系 (5)2.3注塑模结构分析 (6)2.4注塑模工作原理及装配图 (7)第3章定模板的制造加工 (9)3.1定模板的加工 (9)3.1.1制定定模板加工步骤 (9)3.1.2 选择加工设备 (12)3.2加工工艺过程 (12)第4章型芯的加工制造 (13)4.1型芯的加工 (13)4.1.1制定动模板加工步骤 (13)4.1.2 加工工艺过程 (16)第5章定模座板、动模座板的加工 (18)5.1定模座板的加工 (18)5.1.1制定定模座板加工步骤 (18)5.1.2 选择加工设备 (20)5.1.3工工艺过程 (20)5.2动模座板的加工 (20)5.2.1制定动模座板加工步骤 (21)5.2.2 选择加工设备 (22)5.2.3工工艺过程 (22)第6章型芯固定板的加工 (23)6.1制定型芯固定板加工步骤 (23)6.1.1分析型芯固定板的结构 (24)6.1.2 确定加工方法 (24)6.1.3 选择加工设备 (24)6.2加工工艺过程 (24)第7 章支承零部件的加工 (26)7.1支承板的加工 (26)7.1.1制定支承板加工步骤 (26)7.1.2 加工工艺过程 (27)7.2垫块的加工 (28)7.2.1制定垫块加工步骤 (28)7.1.2 加工工艺过程 (29)第8章推出机构的制造 (30)8.1推件板的加工步骤 (30)8.1.1制定推件板加工步骤 (30)8.1.2 加工工艺过程 (34)8.2推板的制造 (34)8.2.1制定推板加工步骤 (35)8.2.2 加工工艺过程 (35)8.3推杆固定板的加工 (36)8.3.1制定动模板加工步骤 (36)8.3.2 加工工艺过程 (37)第9章标准件的选用 (38)9.1导柱的选用 (38)9.2浇口套的选用 (39)第10章模具装配、试模与调试 (41)10.1模具装配工艺过程 (41)10.2连接件的调试与修整 (43)10.3注塑模中出现的问题 (44)10.4成型设备的参数 (44)结论 (46)参考文献 (47)致谢 (48)附录 (49)第1章绪论1.1模具在加工工业中的地位模具是工业生产的重要装备,是国民经济的基础设备,是衡量一个国家和地区工业水平的重要标志。
塑料盖注塑_模具设计
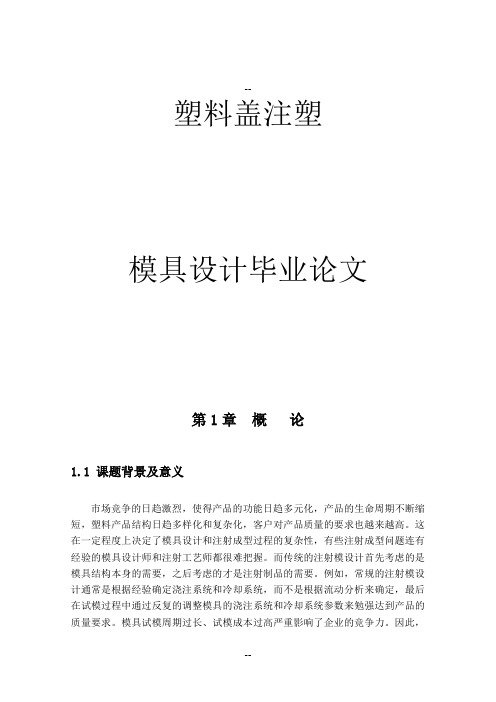
--塑料盖注塑模具设计毕业论文第1章概论1.1 课题背景及意义市场竞争的日趋激烈,使得产品的功能日趋多元化,产品的生命周期不断缩短,塑料产品结构日趋多样化和复杂化,客户对产品质量的要求也越来越高。
这在一定程度上决定了模具设计和注射成型过程的复杂性,有些注射成型问题连有经验的模具设计师和注射工艺师都很难把握。
而传统的注射模设计首先考虑的是模具结构本身的需要,之后考虑的才是注射制品的需要。
例如,常规的注射模设计通常是根据经验确定浇注系统和冷却系统,而不是根据流动分析来确定,最后在试模过程中通过反复的调整模具的浇注系统和冷却系统参数来勉强达到产品的质量要求。
模具试模周期过长、试模成本过高严重影响了企业的竞争力。
因此,--对塑料熔体的注射成型过程的计算机模拟对优化产品结构设计、模具设计以及注射成型工艺具有非常重要的指导意义[1][2][3]。
1.2 本课题及相关领域的国内外现状及发展1.2.1 塑料模功能分子材料加工领域中,用于塑料制品成形的模具,称为塑料成形模具,简称塑料模。
塑料模优化设计,是当前高分子材料加工领域中的重大课题。
在塑料材料、制品设计及加工工艺确定以后,塑料模设计对制品质量与产量,就具有决定性的影响。
首先,模腔形状、流道尺寸、表面粗糙度、分型面、浇注与排气位置选择、脱模方式以及定型方法的确定等,均对制品尺寸精度和形状精度以及塑件的物理力学性能、内应力大小、表观质量与内在质量等,起着十分重要的影响。
其次,在塑件加工过程中,塑料模结构的合理性,对操作的难易程度,具有重要的影响。
再次,塑料模对塑件成本也有相当大的影响,除简易模具外,一般说来制模费用是十分昂贵的,大型塑料模更是如此。
现代塑料制品生产中,合理的加工工艺、高效率的设备和先进的模具,被誉为塑料制品成形技术的“三大支柱”。
尤其是塑料模对实现塑件加工工艺要求、塑件使用要求和塑件外观造型要求起着无可代替的作用。
高效全自动化设备,也只有装上能自动化生产的模具,才能发挥其应有的效能。
塑料模具毕业,课程设计说明任务书,圆盖注塑模设计与制造(好东西)
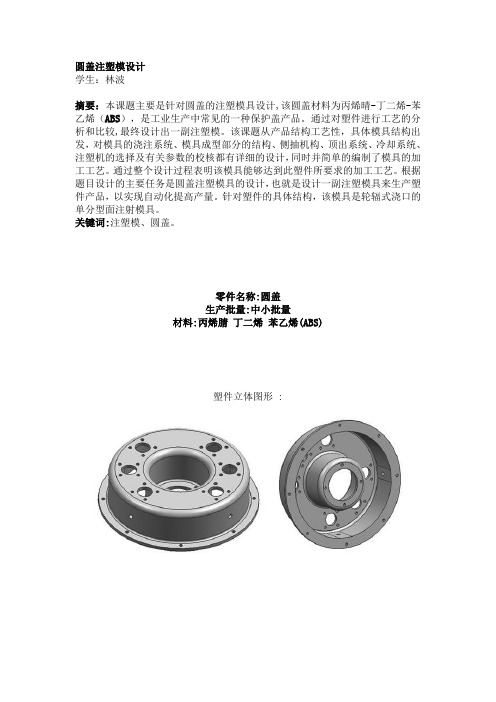
圆盖注塑模设计学生:林波摘要:本课题主要是针对圆盖的注塑模具设计,该圆盖材料为丙烯晴-丁二烯-苯乙烯(ABS),是工业生产中常见的一种保护盖产品。
通过对塑件进行工艺的分析和比较,最终设计出一副注塑模。
该课题从产品结构工艺性,具体模具结构出发,对模具的浇注系统、模具成型部分的结构、侧抽机构、顶出系统、冷却系统、注塑机的选择及有关参数的校核都有详细的设计,同时并简单的编制了模具的加工工艺。
通过整个设计过程表明该模具能够达到此塑件所要求的加工工艺。
根据题目设计的主要任务是圆盖注塑模具的设计,也就是设计一副注塑模具来生产塑件产品,以实现自动化提高产量。
针对塑件的具体结构,该模具是轮辐式浇口的单分型面注射模具。
关键词:注塑模、圆盖。
零件名称:圆盖生产批量:中小批量材料:丙烯腈丁二烯苯乙烯(ABS)塑件立体图形 :一、塑件的工艺性分析塑件的工艺性分析包括:塑件的原材料分析、塑件的尺寸精度分析、塑件表面质量和塑件的工艺性分析,其具体分析如下:1、塑件的原材料分析:塑料品种结构特点使用温度化学稳定性性能特点成型特点丙烯腈、丁二烯、苯乙烯(ABS),属于热塑性塑料非结晶态树脂,不透明小于85-110℃,脆化温度未-18℃有较良好的耐化学试剂性,不耐浓的氧化性酸及醛、酮、酯、氧化烃等不透明,具有良好的综合物理力学性能,耐热、耐腐、耐磨及良好的抗蠕变性,介电性能好,吸水性较强熔融温度高(超过250℃时才出现分解),熔体粘度不太高,流动性中等(溢边值为0.04mm),与流动性和压力有关,对压力更敏感,冷却速度较快,成型收缩小结论: ①熔融温度较高,熔体黏度中等,一般采用螺杆注射机成型,模具温度可控制在60-80℃②吸湿性强,含水量应小于0.3%,必须充分干燥③易发生熔接熔接痕,应注意选择进料口位置形式,顶出力过大或机械加工时塑件表面呈现“白色痕迹”(但在热水中加热可消失),脱模斜度应取2°以上2、塑件的结构工艺性分析:⑴ 从图纸上分析,该塑件的外形为回转体,壁厚均匀,都为3.5mm,且符合最小壁厚要求.⑵ 塑件型腔较大,有尺寸不等的孔,如:36-Ф3.5 、6-Ф16,它们均符合最小孔径要求.⑶ 在塑件侧壁有四个Ф5mm的孔,因此成型后塑件不易取出,需要考虑侧抽装置.3 、塑件的尺寸精度分析:该塑件的未注公差按MT5级公差要求,其余公差要求按制件的制件图所示公差要求塑件的外形尺寸: ФФ内形尺寸: Ф孔尺寸: ФФФФ空心距尺寸: ФФФФ4、塑件表面质量分析:该塑件为工业用圆盖塑料,对其表面质量没有什么高的要求,粗糙度可取Ra3.2um ,塑件内部也不需要较高的表面粗糙度要求,所以内外表面的粗糙度都3取Ra3.2um.结论:该塑件可采用注射成型加工,且加工性能较好,但成型以后需要设置侧抽芯机构才能将塑件顺利脱出.二、成型设备选择与模塑工艺规程编制1、计算塑件的体积:+2、注塑机的初步选择塑件成型所需的注射总量应小于所选注塑机的注射容量.注射容量以容积()表示时,塑件体积(包括浇注系统)应小于注塑机的注塑容量,其关系是:式中- 塑件与浇注系统的体积()- 注射机注射容量()0.8- 最大注射容量利用系数根据塑件的原材料分析,查相关手册①得知该塑件的原材料所需的注射压力为60-100 ,由于塑件的尺寸较大,型芯较多,所以选择较大的注射压力.模具所需的注射压力应小于或等于注射机的额定注射压力,其关系按下式:式中- 塑件成型是所需的压力()- 所选注射机的额定注射压力()模具所需的最大锁模力应小于或等于注射机的额定锁模力,其关系式如下:式中- 模具型腔压力,取45MPa- 塑件与浇注系统在分型面上的投影面积()- 注射机额定锁模力(N)再根据塑件形状及尺寸采用一模一件的模具结构,由以上数据,相关资料②初选螺杆式注塑机:XS-ZY-250.它的注射容量为250,注塑压力为130MPa,锁模力为1800KN,均满足以上条件.3、塑件模塑成型工艺参数的确定ABS注射成型工艺参数见下表,试模时,可根据实际情况作适当调整工艺参数规格工艺参数规格预热和干燥温度t/℃: 80-95成型时间/s 注射时间0-5时间/h: 4-5保压时间15-30料筒温度t/℃ 后段150-170 冷却时间15-30 中段165-180 总周期40-70 前段180-200螺杆转速n/()30-60喷嘴温度t/℃ 170-180后处理方法红外线灯烘箱模具温度t/℃ 50-80 温度t/℃ 70 注射压力p/Mpa 60-100时间/h2-4三、注射模的结构设计注射模结构设计主要包括: 分型面的选择、模具型腔数目的确定及型腔的排列、浇注系统设计、型芯、型腔结构的确定、推件方式、侧抽芯机构的设计、模具结构零件设计等内容.1、分型面的选择该塑件为工业用圆盖塑料,对其表面质量没有什么高的要求,只要求外径没有明显的斑点及熔接痕.在选择分型面时,根据分型面的选择原则,考虑不影响塑件的外观以及成型后能够顺利取出制件如图所示,塑件留动模,塑件的脱模容易实现,且模具的加工相对以上方案简单,方便. 所以,通过对以上几种分型面的考虑以及塑件的外观的要求,选择大端底平面作为分型面的方案较合适.2、型腔数目的确定及型腔的排列由于该塑件采用一模一件成型,所以,型腔布置在模具的中间.这样也有利于浇注系统的排列和模具的平衡.3、浇注系统的设计(1)主流道设计主流道是指浇注系统中从注射机喷嘴与模具接触处开始到分流道为止的塑料熔体的流动通道,是熔体最先流经模具的部分,它的形状与尺寸对塑料熔体的流动速度和充模时间有较大的影响,因此,必须使熔体的温度降和压力损失最小。
- 1、下载文档前请自行甄别文档内容的完整性,平台不提供额外的编辑、内容补充、找答案等附加服务。
- 2、"仅部分预览"的文档,不可在线预览部分如存在完整性等问题,可反馈申请退款(可完整预览的文档不适用该条件!)。
- 3、如文档侵犯您的权益,请联系客服反馈,我们会尽快为您处理(人工客服工作时间:9:00-18:30)。
需要图纸资料可联系我电话:131********QQ411978492目录摘要 (2)第一章:塑件成型工艺性分析 (3)第二章:模流分析 (7)第三章:拟定模具结构 (17)第四章:注塑机型号的确定 (20)第五章:浇注系统形式和浇口的设计 (21)第六章:成型零件尺寸表 (25)第七章:模架的确定和标准件的选用 (28)第八章:脱模推出机构 (28)第九章:排气系统的设计 (32)第十章:冷却系统的设计 (32)第十一章:型腔数量及注射机有关工艺参数的校核 (34)第十二章:非标零件的加工工艺 (37)小结 (41)致谢 (45)参考文献 (46)手机保护罩的计算机辅助设计摘要:本课题主要是针对手机保护罩的注射模设计。
从模具的开模和分型开始,再结合一定的理论知识和成型工艺的要求进行整套模具的设计和必要的尺寸计算等,设计出结构合理的模具。
在设计过程中运用了MOLD FLOW、PRO/E、UG、AUTOCAD2007。
运用MOLD FLOW做模具的模流分析、PRO/E做模具的结构设计、UG做模具的加工程序、AUTOCAD2007绘制零件的装配图和零件图。
关键词:聚碳酸酯工艺分析、结构方案、浇注系统、脱模结构、斜顶针Computer Aided Design of mobile protection cover Abstract:This topic is mainly aimed at mobile protective shield of the injection mold,Mold from the mold and start typing,Combined with theoretical knowledge and process requirement for complete mold design and the necessary size calculation,Reasonable structure of the mold design,In the design process used the MOLD FLOW、PRO/E、UG、AUTOCAD2007、MOLD FLOW make molds using mold flow analysis、PRO / E to do the structural design of mold、UG do mold processing、AUTOCAD2007 draw assembly drawings of parts and parts diagram。
Key words:Polycarbonate process analysis、Structure of the program、Gating system、Stripping structure、Oblique thimble.第一章塑件成型工艺性分析一、塑件图1.1 塑件1.塑件尺寸如图1.1所示2.塑料名称:聚碳酸酯(PC)3.色调:无色透明4.生产纲领:小批量5.塑件结构及成型工艺性分析(1)结构分析如下该零件为手机保护罩,对于外观要求较高,不允许出现熔接痕、顶杆痕迹、印纹等。
在塑件的两边有内凹结构,成型时推出要平稳,而且需要斜顶针,零件壁厚很薄需要用推板推出。
(2)成型工艺分析如下1精度等级选为5级,MT52脱模斜度3°6.塑件壁厚聚碳酸酯树脂(PC)作为一种综合性能比较优秀的热塑性工程塑料,在国民经济不少领域都已得到应用,其制品可用注塑、挤塑吹塑、吸塑等成型工艺制备。
在使用注射成型制成的产品中,不乏有作为结构零件使用的实例。
然而由于注射成型的一般规律和PC本身的一些工艺特性,故在产品设计时,其壁厚一般均要求在0.5-5.0mm围内,而且要求壁厚能均匀过渡。
8.塑件的原材料分析PC是分子链中含有碳酸酯一类化合物的总称。
在其分子主链结构中除了含有酯基外,还有苯环和异丙基。
碳酸酯链赋予PC有一定的柔顺性和韧性;而苯环则赋予PC具有刚性,因此这些基团使PC具有既韧又刚的力学性能。
主链苯环空间位阻大,因此在一定程度上刚性占有主导地位,这正是PC制品容易造成内应力甚至制品易开裂的主要原因之一。
为此,要求制品合理设计并正确掌握成型工艺。
酯基对水敏感,易吸潮水解,特别是在高温下树脂更易水解。
将透明的PC 产品在121℃、0.015 MPa水中反复蒸煮10次,则会完全失去透明度而成为乳白色不透明产品。
这就要求PC树脂在成型加工之前必须进行充分的干燥处理,在加工过程中对于加料斗中的或待加工已经干燥的树脂,必需采取严格的保温措施,以防树脂重新吸潮。
目前常用的PC树脂,大部分是以双酚A作为主要原料聚合而成的。
对此类的PC,链节重复单元较长(约100左右)每一个链节中又有两个苯环,它限制了分子的柔顺性,导致 PC的玻璃化温度和熔融温度都比较高,熔体黏度较大。
PC分子链虽对称简单,但结构庞大,空间位阻大,使PC成为无定形结构,无明显熔点。
PC的这些特征要求模具的浇道、浇口设计短而粗,尽量减少熔体流动阻力,同时需采用较高的注射压力,而较高的注射压力,可能会因PC分子刚性大,取向和解取向都困难,使制品内应力较大。
PC树脂的熔体黏度较高,可多达1.0x104Pa·s (比一般的塑料要大出2个数量级),而且熔体黏度对剪切速率的依赖性较小,对注射压力的依赖性较小,而对温度的敏感性较大。
这就是说要提高熔体的流动性,应采用提高注射温度的办法而不是采用增大注射压力的办法来实现。
二:热塑性塑料的注射成型过程及工艺参数1.注射成型过程(1)成型前准备。
成型之前必须预干燥,水分含量应低于0.02%,微量水份在高温下加工会使制品产生白浊色泽,银丝和气泡。
(2)注射过程。
在料筒内经过加热,塑化达到流动状态后,由模具的浇注系统进入模具型腔成型。
过程可分为充填、压实、保压、倒流、和冷却。
(3)塑件后处理2.注射工艺参数表1.1塑件注射成型工艺参数如表1所示,试模时,可根据实际情况作适当调整。
表1.1 注射工艺参数料筒温度喂料区70~90℃(80℃)区1230~270℃(250℃)区2260~310℃(270℃)区3280~310℃(290℃)区4290~320℃(290℃)区5290~320℃(290℃)喷嘴300~320℃(290℃)括号内的温度建议作为基本设定值,行程利用率为35%和65%,模件流长与壁厚之比为50:1到100:1熔料温度280~310℃料筒恒温220℃模具温度80~110℃注射压力因为材料流动性差,需要很高的注射压力:90-110MPa保压压力注射压力的40%~60%;保压越低,制品应力越低背压10~15MPa(100~150bar)注射速度取决于流长和截面厚度:薄壁制品需要快速注射;需要好的表面质量,则用多级慢速注射螺杆转速最大线速度为0.6m/s;使塑化时间和冷却时间对应;螺杆需要大扭矩计量行程(0.5~3.5)D残料量2~6mm,取决于计量行程和螺杆直径预烘干在120℃温度下烘干3h;保持水份低于0.02%,会使得力学性能更优回收率最多可加入20%回料;较高的回料比例会保持抗热性,但力学性能会降低收缩率0.6%~0.8%,若为玻璃增强类型,0.2%~0.4%浇口系统浇口直径应该至少等于制品最大壁厚的60%~70%,但是浇口直径至少为1.2mm(浇口斜度为3~5,或表面质量好的制品需要2);对壁厚均匀的较小制品可采用点式浇口机器停工时段如生产中断,操作机器像挤出机那样直到没有塑料挤出并且温度降到200℃左右:清洗料筒,用高粘性PE,将螺杆从热料筒中抽出并用钢丝刷刷去残料料筒设备标准螺杆,止逆环,直通喷嘴三:PC的主要性能指标聚碳酸酯(Polycarbonate,简称PC)是一种无色透明的无定性热塑性材料。
其名称来源于其内部的CO3基团。
聚碳酸酯无色透明,耐热,抗冲击,阻燃BI级,在普通使用温度内都有良好的机械性能。
同性能接近聚甲基丙烯酸甲酯相比,聚碳酸酯的耐冲击性能好,折射率高,加工性能好,需要添加阻剂才能符合UL94 V-0级。
但是聚甲基丙烯酸甲酯相对聚碳酸酯价格较低,并可通过本体聚合的方法生产大型的器件。
随着聚碳酸酯生产规模的日益扩大,聚碳酸酯同聚甲基丙烯酸甲酯之间的价格差异在日益缩小。
不能长期接触60℃以上的热水,聚碳酸酯燃烧时会发出热解气体,塑料烧焦起泡,但不着火,离火源即熄灭,发出稀有薄的苯酚气味,火焰呈黄色,发光淡乌黑色,温度达140℃开始软化,220℃熔解,可吸红外线光谱。
聚碳酸酯的耐磨性差。
一些用于易磨损用途的聚碳酸酯器件需要对表面进行特殊处理。
密度:1.20-1.22 g/cm 线膨胀率:3.8×10 cm/cm°C 热变形温度:130°C。
不耐强酸,不耐强碱。
聚碳酸酯耐酸,耐油。
聚碳酸酯不耐紫外光,不耐强碱。
聚碳酸酯的耐磨性差。
一些用于易磨损用途的聚碳酸酯器件需要对表面进行特殊处理。
第二章模流分析目前,CAD/CAM技术已经比较成熟的运用在注塑模具设计与制造中,且能制造出高质量和高精度的模具,但如果仅凭经验的进行设计、制造,必将会进行多次的修模,浪费大量的时间与成本。
因此,需要运用CAE技术对产品进行模流分析。
注塑成型CAE技术采用有限元计算方法来模拟整个注塑过程及这一过程对注塑成型产品质量的影响,它可以模拟塑料制品在注塑成型过程中的流动,保压和冷却过程以及预测制品中的应力分布、分子取向、收缩和翘曲变形等,帮助设计人员及早发现问题,及时修改模具设计,提高一次试模成功率,帮助企业缩短产品上市周期,增强市场竞争能力。
单个塑件模流分析:模型详细资料:图1:划分网格图网格类型= 双层面网格匹配百分比= 89.8 %相互网格匹配百分比= 86.5 %节点总数= 3427注射位置节点总数= 1注射位置节点标签是:2754 单元总数= 6862制品单元数= 6862主流道/流道/浇口单元数= 0管道单元数= 0连接器单元数= 0分型面法线(dx) = 0.0000(dy) = 0.0000(dz) = 1.0000 三角形单元的平均纵横比= 3.2478三角形单元的最大纵横比= 96.1119具有最大纵横比的单元数= 112三角形单元的最小纵横比= 1.1570具有最小纵横比的单元数= 2277总体积= 2.7710 cm^3最初充填的体积= 0.0000 cm^3要充填的体积= 2.7710 cm^3要充填的制品体积= 2.7710 cm^3要充填的主流道/流道/浇口体积= 0.0000 cm^3 总投影面积= 7.7080 cm^2注塑机参数:注塑机参数:最大注塑机锁模力= 7.0002E+03 tonne最大注射压力= 1.8000E+02 MPa最大注塑机注射率= 5.0000E+03 cm^3/s注塑机液压响应时间= 1.0000E-02 s工艺参数:充填时间= 0.4000 s自动计算已确定注射时间。