基于Witness车辆路径问题的仿真建模与优化
基于witness的系统建模与仿真实验报告
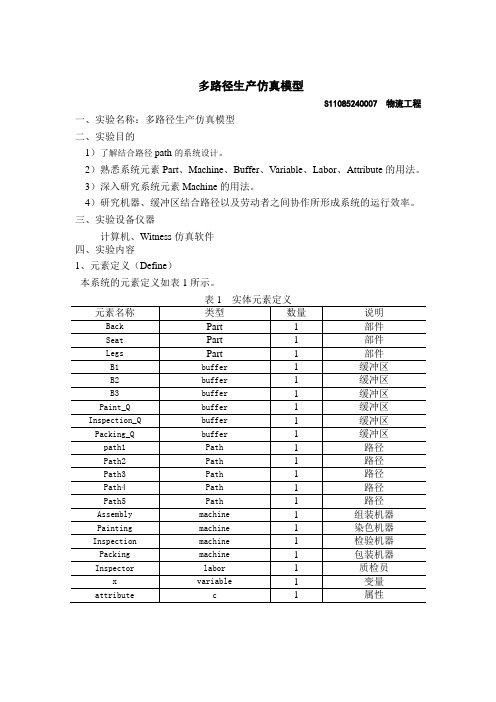
多路径生产仿真模型S11085240007 物流工程一、实验名称:多路径生产仿真模型二、实验目的1)了解结合路径path的系统设计。
2)熟悉系统元素Part、Machine、Buffer、Variable、Labor、Attribute的用法。
3)深入研究系统元素Machine的用法。
4)研究机器、缓冲区结合路径以及劳动者之间协作所形成系统的运行效率。
三、实验设备仪器计算机、Witness仿真软件四、实验内容1、元素定义(Define)本系统的元素定义如表1所示。
表1 实体元素定义元素名称类型数量说明Back Part 1 部件Seat Part 1 部件Legs Part 1 部件B1buffer 1 缓冲区B2buffer 1 缓冲区B3buffer 1 缓冲区Paint_Q buffer 1 缓冲区Inspection_Q buffer 1 缓冲区Packing_Q buffer 1 缓冲区path1Path 1 路径Path2Path 1 路径Path3Path 1 路径Path4Path 1 路径Path5Path 1 路径Assembly machine 1 组装机器Painting machine 1 染色机器Inspection machine 1 检验机器Packing machine 1 包装机器Inspector labor 1 质检员x variable 1 变量attribute c 1 属性2、元素可视化(Display)设置各个实体元素的显示特征定义设置如下图所示3、元素细节(Detail)设计1对Part各元素细节设计●可视化效果设定●属性定义:seat.Arrival Type=Activeseat.inter Arrival=2.0back.Arrival Type=Activeback.inter Arrival=2.0legs.Arrival Type=Activelegs.inter Arrival=2.0●规则定义:seat’s output Rules:PUSH to B1back’s output Rules:PUSH to B2legs’ output Rules:PUSH to B32对Buffer各元素细节设计display 选项中对话框对buffer icon 、name、part queue属性进行设置;3对Machine各元素的细节设计属性定义:Assembly.Type=AssemblyAssembly.Cycle Time=6.0Assembly. Input Quantity=3;!机器Assembly的输入零部件数量为3个;规则定义:Assembly.Input Rules(From):MATCH/ANY B1 #(1)B2 #(1)B3 #(1) !匹配缓冲区B1、B2、B3中的任意类型的part各一个;Assembly.Output Rules(To):PUSH to Paint_Q Using Path !通过路径将成品送至缓冲区Paint_Q;活动定义:Assembly.actions on finish:3.1)对machine元素Assembly的详细定义:属性定义:♦Assembly.Type=Assembly♦Assembly.Cycle Time=6.0♦Assembly. Input Quantity=3;!机器Assembly的输入零部件数量为3个;规则定义:Assembly.Input Rules(From):♦MATCH/ANY B1 #(1)B2 #(1)B3 #(1) !匹配缓冲区B1、B2、B3中的任意类型的part各一个;Assembly.Output Rules(To):♦PUSH to Paint_Q Using Path !通过路径将成品送至缓冲区Paint_Q;活动定义:Assembly.actions on finish:♦ICON = 115!通过变换图标,表示seat、back、legs组装成了一把白色椅子;3.2)对machine元素inspection的详细定义:属性定义:♦inspection.Type=Single♦inspection.Cycle Time=3.0♦bor=Inspector规则定义:inspection.Input Rules(From):♦PULL from Inspection_Q !从缓冲区Inspection_Q中提取零件加工;inspection.Output Rules(To):♦PERCENT /189 Packing_Q Using Path 90.00 ,Paint_Q With Inspector Using Path 10.00 !产生随机概率,以90%的概率通过检测,使用路径移向Packing_Q,进行打包;以10%的概率检测出油漆有质量问题,需要人工搬运,通过路径送回缓冲区Paint_Q,排队重新油漆。
基于Witness的C企业生产物流运输路径优化

现代物流与采购现代商贸工业2018年第33期30㊀㊀作者简介:陈超(1993-),男,汉族,江苏南京人,硕士,济南大学商学院研究生,研究方向:物流系统化.基于W i t n e s s 的C 企业生产物流运输路径优化陈㊀超(济南大学商学院,山东济南250002)摘㊀要:针对C 企业生产物流运输路径的现状及生产物流中出现的主要问题,提出具体生产物流运输路径优化的方案,再运用W i t n e s s 仿真技术对C 企业生产物流优化运输路径进行仿真,帮助企业提高生产物流效率,增强企业的竞争能力.同时,研究的理论和方法对其它类似中小企业优化自身生产物流具有一定借鉴意义.关键词:生产物流;运输路径;W i t n e s s中图分类号:F 25㊀㊀㊀㊀㊀文献标识码:A㊀㊀㊀㊀㊀㊀d o i :10.19311/j.c n k i .1672G3198.2018.33.0151㊀概论经济全球化和信息技术的不断发展,物流作为 第三利润的源泉 越来越被各国企业关注.企业在激烈的市场竞争中为了生存与发展,已经把物流重心从社会物流转移到改善企业物流系统中来,其中生产物流更是企业物流的核心.在我国,企业生产物流是处于薄弱环节的.企业生产物流效率的低下,则会造成时间和空间的浪费,生产物料的等待,成品的堆积,工人的重复搬运,不仅影响了企业生产效率,更占用了大量流动资金,成为企业发展的瓶颈.本文以C 企业生产物流中运输路径为研究对象,运用W i t n e s s 仿真技术对企业生产运输路径进行优化,解决生产物流系统中问题,提高企业生产物流效率.2㊀企业生产物流运输路径现状目前C 企业主要有A 和B 两车间进行生产,生产中显现出如下突出问题,并且越演越烈,严重阻碍了生产效率的提高.(1)车间原材料的配送依靠人工从仓库搬运到两个生产车间,一方面人力消耗大,更重要的是运送原材料的不及时,两车间常常处于停工等待状态,造成了大量的时间和人力浪费.另一方面,运输工人面对两车间的同时催货到底先送谁的,常常出现某车间为了自己不断货,提前多报原材料的运送,势必造成另一车间送货的等待或者订货仓库定料的堆积.(2)两个车间的产成品堆积严重,不能及时运送入库,两车间常常堆积大量产成品和在制品,造成了车间产地的占用以及生产工序的不畅.(3)产量达不到预期目标,A 车间和B 车间目标产量为300单位和400单位,而现在A 和B 车间出来分别为240单位和310单位,严重阻碍了企业的发展.这些问题充分显现了C企业生产物流运输路径的低效率.为了解决C 企业目前面临生产物流运输路径的问题,建议引入准时制生产管理,减少车间等待,降低库存,降低产成品在车间的堆积,使生产工序有效畅通,提高企业生产物流效率.针对C 企业实际情况给出如下具体方案并通过仿真验证:(1)引入准时制生产制度,因为C 企业处于大工业园中,A 和B 车间原材料的供应商就在园区中,通过与供应商的协调,供应商将分别60m i n /次送A 车间原材料到达㊁45m i n /次送B 车间原材料到达,并采用标准统一托盘形式,送达到仓库指定地点,方便下部A G V 小车的运载,这样可以大大节约仓库原材料的库存.(2)采用两辆A G V 小车代替传统人工搬运原材料,既节省了人力资源也可以及时送货到车间工位,在运送完原材料的同时再把车间内产成品及时带走入库,既保证了原材料的及时送达也解决了车间产成品的堆积.(3)具体规划出5条路径供A G V 小车运输,保证运输路径的畅通有序.(4)由于A 和B 车间原材料到达时间有时间差,就不能固定A G V 小车只运输哪个车间原材料,因为这样造成A G V 小车的空等浪费大量时间.所以采用货物托盘的统一,也是为了A G V 小车可以交叉运输A B 车间原材料,这样就会出现1号小车先运A 货物,2号小车运B 货物,在一定时间变化中1号小车会运B 货物,2号小车会运A 货物,形成规律性变化,我将通过仿真来具体实现,这样大大提高了A G V 小车运输效率.下文将通过W i t n e s s 仿真技术实现具体优化方案.现代商贸工业2018年第33期31㊀3㊀C 企业生产物流运输路径仿真设计及结果分析3.1㊀系统描述现有两辆A G V 小车处于工作状态,把准时制制度下到达仓库指定地点的原材料运输到A 和B 两车间,并回来时候带回车间已经完成的产成品.原材料到达已托盘形式,A 车间所需原材料记为P a l l e t A 60m i n/次,B 车间所需原材料记为P a l l e t B 45m i n /次,且托盘货物重量在A G V 小车载重范围内.正如上文所说的不同车间所需原材料到达仓库有时间差,A G V 小车将会在一定时间变化内呈规律性交替运载货物,以至充分发挥运输效率,保证原材料P a l l e tA ㊁P a l l e t B 以及车间产成品有序运输至指定地点.现做如下规定:只要运输P a l l e tA 的小车只能通过T 2路径 T 5,而运输P a l l e tB 则通过T 3 T 5,进行仿真模拟实验.3.2㊀元素及其可视化定义元素定义如表1,分别对仿真系统中各个元素实体进行可视化设置,各个实体元素的显示特征如图1.表1㊀元素定义元素名称类型数量说明P a l l e tA P a r t 1托盘货物A 车间P a l l e tB P a r t1托盘货物B 车间Q A G V B u f f e r 1托盘货物的缓冲区T 1T r a c k 1路径1T 2T r a c k 1路径2T 3T r a c k 1路径3T 4T r a c k 1路径4T 5T r a c k 1路径5QP a l l e tA B u f f e r 1托盘货物A 停放点QP a l l e tB B u f f e r 1托盘货物B 停放点A G V V e h i c l e 22辆A G V小车图1㊀仿真实体模型布局图3.3㊀元素细节设计(1)对P a r t 元素设计.N a m e :P a l l e tA㊀㊀㊀㊀㊀N a m e :P a l l e tBT y p e :A c t i v e ㊀㊀㊀㊀㊀㊀T y pe :A c t i v e I n t e rA r r i v a l :60I n t e rA r r i v a l :45O u t p u tR u l e s :P U S Ht oQ A G V O u t pu tR u l e s :P U S Ht oQ A G V (2)对B u f f e r 元素设计.元素Q A G V ㊁Q P a l l e t A ㊁Q P a l l e t B 的P a r tQ u e u e 都是C o u n t ,D i s p l a y Si z e 分别为1,3,3.(3)对V e h i c l e 元素设计.N a m e :A G V㊀㊀S t a r tD e l a y s :0.5L o a d e d :1.0㊀㊀S t o p D e l a y:0.5(4)对T r a c k 元素设计.首先设置T e x t 和P a t h,然后输入具体规则如表2.表2㊀T r a c k 元素代码元素名称按钮名称代码T 1O u t pu tT O...I FT Y P E =P a l l e tAP U S Ht oT 2E L S EP U S Ht oT 3E N D I F T 2O u t pu tT O...P U S Ht oT 4(1)O u t p u tU n l o a d i n g Ru l e ...P U S Ht oQ P a l l e t A A c t i o n s o nU n l o a d ...V E H I C L E (T 2,1)A T0:I C O N =77T r a n s f e rM o d eA l w a ys T 3O u t pu tT O...P U S Ht oT 5(1)O u t p u tU n l o a d i n g Ru l e ...P U S Ht oQ P a l l e t B A c t i o n s o nU n l o a d ...V E H I C L E (T 3,1)A T0:I C O N =77T r a n s f e rM o d eA l w a ys T 4O u t p u tT O...P U S Ht oT 5(1)T 5O u t pu tT O...P U S Ht oT 1(1)I n p u tL o a d i n g R u l e ...P U L Lf r o m Q A G V A c t i o n sO n l o a d ...I FT Y P E =P a l l e tA V E H I C L E (T 5,1)A T0:I C O N =4E L S EV E H I C L E (T 5,1)A T0:I C O N =5E N D I FT r a n s f e rM o d eA l w a ys 3.4㊀模型运行及数据报告结合生产的实际,按一个月26天,每天工时12小时,也就是187200个时间单位进行仿真模拟,运行结果如图2,具体仿真数据如表3.图2㊀仿真模型运行结果图㊀㊀备注:(1)A G V 小车从仓库Q A G V 指定堆放原材料地点托载A 和B 车间的原材料到路径T 4的终点放下原材料,然后再从A 和B 车间托载产成品经过T 5路径到达仓库Q A G V 产成品堆放点,再次托载原材料到T 4路径的A 和B 车间以此为循环.(2)两小车会在第二次,第六次,第九次,第十三次 两个小车会变换运载托盘货物的种类.现代物流与采购现代商贸工业2018年第33期32㊀㊀表3㊀仿真数据汇总数据一N a m eT o t a l i n T o t a l o u tN o wI n M a xM i n A v g S i z e A v g T i m e QP a l l e tA31203123120156.249374.59QP a l l e tB 41604164160208.049361.94数据二N a m e%I d l e %T r a n s f e r %L o a d e d %B l o c k e d D i s t a n c e L o a d A G V (1)54.8215.8829.3118.6111821.0364A G V (2)54.7215.9729.3118.5211804.0364数据三N a m e %E m p t y %B u s %B l o c k e d N o .0T 171.8128.190.00728T 287.9212.080.00312T 350.8918.3330.78416T 489.484.176.35312T 50.001000.007293.5㊀数据分析及优化保障建议(1)由数据一可以看出,2种托盘货物的运载量,由于到货的时间差,Q P a l l e t A 运输312单位,而Q P a l l e t B 运输416单位,认为原料到达车间量为最后产成品产量,所以完全符合企业生产目标要求.并且2个小车平均运行时间几乎接近,说明了A G V 小车发挥了最大运输效率,此生产物流运输路径优化可以使用,比较合理.建议:①统一托盘货物P a l l e tA 和P a l l e tB 货物的尺寸和规格,因为2种小车由于到货的时间差会分别按一定时间变换交互运载2种货物,所以托盘货物规格尺寸要适合A G V 小车的运载且在载重范围内.②全面实施准时制生产,把准时制生产理论普及到每一个员工,相应的组织管理制度要配合准时生产.(2)由数据二可以看到2个A G V 小车的运行距离,传递,负荷以及堵塞率几乎接近.并且2个小车分别运载了364次,共728次,与A 和B 车间原材料总量一致.说明2个A G V 小车的运输是合理的,没有出现某小车运载过多超负荷运行.建议:①调整相关生产车间的布局,继续优化小车运输路径,提高小车运输效率,并且注意小车日常的维修与保养.②小车托运原材料到达车间以及从车间托运产成品到仓库,要做好物料搬运的衔接,保证A G V小车能够快速运输避免发生停留与空车运输.③培养相关员工操作A G V 小车专业知识.(3)由数据三可以看出T 1 T 5路径,每条路径的空闲率㊁繁忙率㊁堵塞率,通过次数.可以看出T 5是最繁忙的,其次是T 1,然后T 3,T 2最后T 4.堵塞率最高的为T 3和T 4.运输路径通过次数由高到低依次为,T 5=T 1,T 3,T 2=T 4.建议:①由于T 5㊁T 1㊁T 3路径较为繁忙,尤其T 5,所以必须保证各条路径的畅通,不能有任何障碍阻碍A G V 小车运输.②由于路径T 3堵塞率较高,后期将拓宽路径T 3,避免堵塞造成A G V 小车运输停滞,对生产带来影响.③对T 5和T 1路径进行重点监控,因为其繁忙率和通过率都很高.后期将设置备用路径,保证T 5和T 1路径的畅通.通过仿真模拟验证了生产物流运输路径优化是可行的,A 和B 车间产成品分别提高了23%和25.5%,并且达到了生产目标要求,提高企业生产物流效率的同时,也提升了企业生产效率,此生产物流运输路径优化对C 企业具有良好的实践意义.4㊀结论本文以C 企业现有生产物流运输路径为研究对象,提出具体优化方案并通过W i t n e s s 仿真运行.既提高了企业生产物流运输效率,也增强了企业市场竞争能力.同时把仿真技术与生产物流的结合为类似中小企业优化自身生产物流提供了借鉴.参考文献[1]赵小荣,周盛世.基于W i t n e s s 的产品生产物流系统仿真研究[J ].物流科技,2013,36,(09):61G64.[2]龚波.基于W I T N E S S 的生产物流系统仿真研究[D ].武汉:武汉理工大学,2008.[3]李钒尘.建模仿真技术在生产物流系统中的应用[D ].大连:大连海事大学,2010.[4]汪佳.某转向器制造企业生产物流系统仿真研究[D ].南京:南京理工大学,2008.[5]孟亮,彭瑜.W i t n e s s 生产物流系统仿真研究范例[J ].经济研究导刊,2011,(02):261G262.[6]刘晓莉.企业生产物流系统的研究[J ].物流科技,2004,(11):6G8.[7]朱华炳,吕冬梅.基于W i t n e s s 的生产物流系统仿真与优化[J ].机械工程师,2006,(03):135G137.。
基于Witness发动机测试线布局优化和仿真分析

的应 用价值 。
关键 词 : Wi t n e s s ; 发 动机 ; 空间布局 优化 ; 节拍 中 图分类 号 : T H1 2 2; T G 5 0 6 文献 标 识码 : A
第 9期 2 0 1 6年 9月
组 合 机 床 与 自 动 化 加 工 技 术
Mo du l a r Ma c h i n e To o l& A u t o ma t i c Ma nu f a c t u r i ng Te c h n i q u e
NO. 9 S e p.2 01 6
( 1 . S c h o o l o f M e c h a n i c a l E n g i n e e r i n g , D a l i a n U n i v e r s i t y o f T e c h n o l o g y , D a l i a n L i a o n i n g 1 1 6 0 2 4 , C h i n a ; 2 .
廖 忠情 , 郑华栋 , 丛
连 1 1 6 0 3 6 )
明 , 刘 冬 , 刘云ቤተ መጻሕፍቲ ባይዱ
( 1 . 大连 理 工大 学 机 械 工程 学 院 , 辽 宁 大连 1 1 6 0 2 4 ; 2 . 大连 豪 森 瑞德 设 备 制 造 有 限公 司, 辽 宁 大
摘要 : 根 据 某发 动机 测 试 线的 实际运 行情 况 , 运 用 Wi t n e s s 仿 真 软件 对 生产 线进 行 建模 和 优化 分 析 。 利 用软 件 的分析模 块 对仿 真结 果进行 图像 化 处理 , 发现 了原检 测线 中存 在 的 限制 整体 生 产 节拍 的设 计 缺 陷 。通过 对测试 线 的空 间布局 进行 局部 调 整 , 减 少 了测 试 线 的 生产 节拍 和 占地 面 积 、 提 高 了年
Witness物流系统建模与仿真
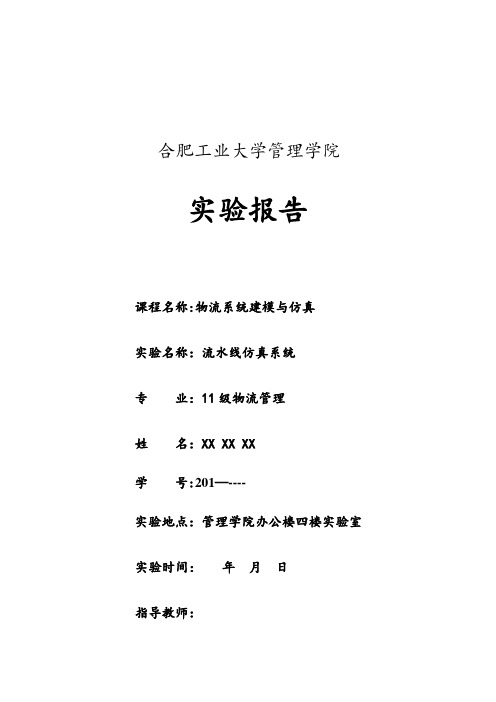
合肥工业大学管理学院实验报告课程名称:物流系统建模与仿真实验名称:流水线仿真系统专业:11级物流管理姓名:XX XX XX学号:201—----实验地点:管理学院办公楼四楼实验室实验时间:年月日指导教师:一、实验目的(1)part、machine、conveyor、labor 实体元素、variable 逻辑元素的使用;(2)掌握可视化输入、输出关系的建立;(3)掌握 report 工具栏的使用和分析,并根据分析,进行系统优化设计二、实验设备Witness 2008Educational Version 、PC机一台三、实验内容1、学习元素的定义2、学习各元素可视化的设置3、学习各元素细节的设计4、运行模型四、实验步骤1.构建第一阶段(Stage1。
mod)模型1)定义元素定义如下图所示的几个元素:2)建模元素详细设计这一阶段主要是输入机器加工时间、改变元素的名字3)建立元素之间的逻辑规则各个元素之间链接的逻辑规则,规则输入可以通过以下两种方法:一是通过工具栏和鼠标,一是通过元素细节对话框.下面以机器为例:●点击选中Weigh图标, 然后单击element工具栏中的visualinput rule图标,出现input rule for weigh 对话框:●规则文本框的缺省值为pull――;●在规则文本框中输入“PULL Widget out of WORLD”,定义了机器Weigh 加工完成一个Widget 之后,从本系统模型的外部WORLD 处拉进一个Widget 进行加工。
规则定义结果显示如图4)运行模型模型运行100 分钟会有19widgets 被加工完成。
2.构建第二阶段(Stage1.mod)模型1)本阶段需要添加的机器为清洗(wash)、加工(produce)、检测(inspect),添加的输送带为C1、C2、C3,同时添加了一个逻辑元素――变量output,用于动态显示模型中加工完成的小零件的数量。
witness建模及仿真实验指导书
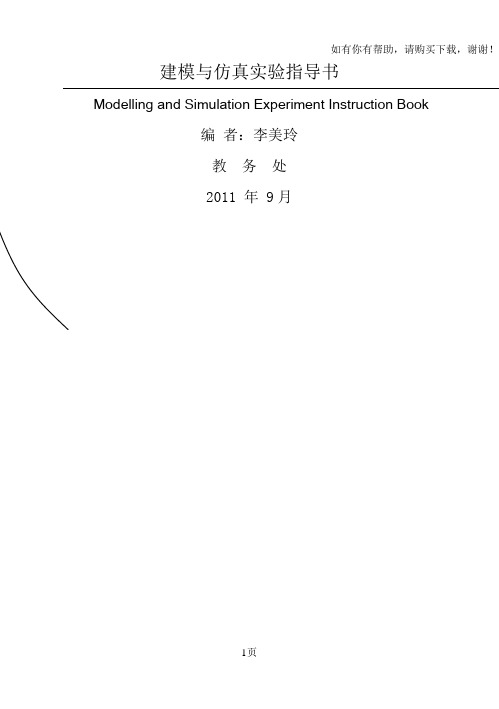
如有你有帮助,请购买下载,谢谢!建模与仿真实验指导书Modelling and Simulation Experiment Instruction Book编者:李美玲教务处2011 年 9月目录建模与仿真实验要求.................................................................... 错误!未定义书签。
实验一流水线仿真系统............................................................ 错误!未定义书签。
实验二单服务台排队系统仿真................................................ 错误!未定义书签。
实验三库存系统仿真................................................................ 错误!未定义书签。
实验四生产线物流路径系统及物流成本分析 ........................ 错误!未定义书签。
实验五配送中心系统仿真设计................................................ 错误!未定义书签。
实验六连续系统仿真—液体灌装线仿真设计 ........................ 错误!未定义书签。
实验七供应链系统的仿真设计与改善.................................... 错误!未定义书签。
实验八装卸服务中心人员调度仿真系统设计 ........................ 错误!未定义书签。
实验九混合流水线系统仿真设计............................................ 错误!未定义书签。
建模与仿真实验要求一、实验目的本实验是与《建模与仿真》课程相配合的实践教学环节。
基于witness的厂区物流系统仿真与分析

很 大 的相似性 。基于 Wi es 真 建模 主 要 步骤 为 : t s仿 n 首
先定 义构 成 系统 的基 本 单 元 模 块 , 仿 真 系 统 中的 一 即 些静 态实 体 , 如物 流 系 统 中 的 运 输设 备 、 存 设 备 、 缓 装 卸工 位 、 运设 备 、 存 区域 等 ; 后 对 通 过 模 块 的 动 搬 库 然 态实 体 ( 如车 辆 ) 行 进 的 路 线 进 行 定 义 , 物 流 系 统 所 在 中是 指物 流车 辆 的 流 向 、 卸 人 员 的移 动或 者 各 个 模 装
K e r s:h di g a d ta po tton; i y wo d n n n r ns ra i a l smulto o e ; pt ia in;w o k t to s c nf rto a in m d l o i z to m r s ai n o i u g a in
好 局面 。 因此 , 企业 管理 层 开始 考虑 扩 大 生产规模 , 初 步提 出新增 多条 生产 线 的方 案 。生产 线 的增 加 势必 带 来仓库 产成品数量 的增加 以及原 材料 需求 的增加 ; 另一 方面, 由于厂 区面积 以及库 存 容量 的限制 , 求 物流 系 要 统要把 当天的产品运 出厂 区 , 并且要 把所 有原 材料 准时 运到仓库 指定位置 。因此 , 给定数 量 的物流 车辆 能否 在
何配置相应 的资源才能使得 花费的时 间最 短。
2 厂 区物 流 系统 仿 真 建 模
为 了实 现 厂 区 内物 流 状 况 的预 先 模 拟 、 时再 现 实 和对 仿真过 程进 行实 时干 预 , 用 Wi es 真系 统对 应 t s仿 n
为此 , 文 以某 包 装 企业 厂 区 内的 物流 系统 为研 本 究对 象 , 利用 wtes 真工 具 建 立 了从 厂 门 口到 仓 库 i s仿 n
基于Witness的汽车销售物流配送中心规划与仿真的开题报告

基于Witness的汽车销售物流配送中心规划与仿真
的开题报告
一、选题目的
基于Witness的汽车销售物流配送中心规划与仿真,旨在探究汽车
销售物流配送中心规划与优化的方法,并运用Witness仿真软件实现销售物流配送中心的模拟,进而分析和优化物流配送中心的业务流程和资源
配置策略,提高物流配送效率和质量。
二、主要研究内容
1. 研究销售物流配送中心的业务流程、资源配置和运作模式,分析
销售物流配送中心的物流配送作业流程和资源利用效率。
2. 采用Witness仿真软件对销售物流配送中心进行建模和仿真,进
一步分析销售物流配送中心的运作效率及优化方案,为物流配送流程提
出改进建议。
3. 分析车辆出入库运作过程,考虑物流设备布局、作业流程、工作
时间等多个因素,提高汽车销售物流配送中心的装卸、存储、分拣等物
流作业效率。
4. 研究销售物流配送中心的门店配送和客户配送方案,通过评估门
店和客户配送路线、配送时间等重要因素,使配送效率和质量得以提升。
三、研究意义
汽车销售物流配送中心的优化与改进,是提高汽车物流配送效率和
服务质量的重要途径。
本文结合Witness仿真软件,对销售物流配送中心的业务流程和资源配置策略进行评估,探索出一套基于模拟和优化的销
售物流配送中心规划方案,为汽车销售企业提供科学的管理决策和改进
思路。
四、预期研究结果
本研究旨在设计和实现一个基于Witness的销售物流配送中心实验
模型,以验证和测试物流配送中心的运作效率,探索出适合汽车销售企
业的物流配送优化策略,并建立一套科学的销售物流配送中心管理体系,进一步提高汽车销售物流配送的效率和质量。
JIT看板生产系统WITNESS仿真建模和优化实现

JIT看板生产系统WITNESS仿真建模和优化实现摘要随着全球制造业的发展,越来越多的企业采用Just-In-Time(JIT)生产系统来实现高效的生产管理。
JIT看板生产系统作为JIT生产系统的重要组成部分,是一种基于看板的生产控制方法。
本文将重点介绍JIT看板生产系统的WITNESS仿真建模和优化实现。
通过使用WITNESS仿真软件,企业可以模拟真实的生产环境,并通过优化模型参数和工艺流程,实现生产系统的高效运行。
1. 引言JIT看板生产系统是一种基于看板的生产控制方法。
它通过设置看板来控制生产流程,以达到减少库存和降低生产成本的目的。
JIT看板生产系统可以帮助企业实现生产效率的提升和生产成本的降低,从而增强企业的竞争力。
然而,在实际应用中,JIT看板生产系统的建立和优化存在一定的挑战。
因此,使用仿真建模和优化方法来分析和改进JIT看板生产系统成为一种重要的研究方向。
2. JIT看板生产系统的WITNESS仿真建模WITNESS是一种基于离散事件仿真的软件平台,可以用于模拟和优化各种生产系统。
在JIT看板生产系统的仿真建模中,可以使用WITNESS来模拟真实的生产环境,并对系统进行分析和优化。
首先,需要对JIT看板生产系统进行实地调研,收集相关的数据和信息。
然后,根据收集到的数据和信息,可以建立JIT看板生产系统的仿真模型。
仿真模型可以包括生产线布局、工艺流程、物料运输等方面的信息。
在建立仿真模型之后,可以通过设置仿真参数和仿真实验来模拟不同的生产场景。
通过对模拟结果的分析,可以评估当前JIT看板生产系统的性能,并发现潜在的瓶颈和问题。
3. JIT看板生产系统的优化实现基于WITNESS仿真模型,可以通过优化实验来改进JIT看板生产系统的性能和效率。
优化实验可以包括调整模型参数、改进工艺流程、优化看板管理等方面的措施。
首先,可以通过调整模型参数来模拟不同的生产策略。
例如,可以调整看板的容量和补充策略,以达到减少库存和提高生产效率的目标。
- 1、下载文档前请自行甄别文档内容的完整性,平台不提供额外的编辑、内容补充、找答案等附加服务。
- 2、"仅部分预览"的文档,不可在线预览部分如存在完整性等问题,可反馈申请退款(可完整预览的文档不适用该条件!)。
- 3、如文档侵犯您的权益,请联系客服反馈,我们会尽快为您处理(人工客服工作时间:9:00-18:30)。
点,7 个提货点 P 和 7 个收货点 D,其中 P 和 D 的编号是 相对应的,给 Pi 点处的货物需要运送到 Di 处,经过某科 研小组的优化研究,目前在用车辆及其所经路径如图 1 所示,目标成本为 3933.1 元。
6 4 2 0 -2 -4 -6 -6
选择 S1、S2 分别设置它们的 text,icon.rectangle 属性 项,选择 V1、V3、V2、V7,设置它们的 Style、text 属性项, 选择 t 元素,设置它们的 Style 属性项,选择 p、d 元素设置 它们的 icon、text 属性等。 3.2.3 变量的设置
模型的设计中使用了大量的变量,总数有 106 个变 量,这些变量是实数型的全局变量,应用这些全局变量的 好处是我们既能在模型中显示全局变量和它们的值,又 能生成全局变量的报告,便于对模型的分析,另外一个重 要的原因是,我们可以方便对变量的修改,产生新的优化 方案。这些变量如 v1speed、V1lucheng、V1time、V1sumtime、
表2
服务时间 下限 上限 装卸量 服务时间 下限 上限 装卸量
P1 5
12 16 5.76 D1 4
20 25 -5.76
P2 3
5 10 9.50 D2 8
32 40 -9.50
P3 10
6 9 14.21 D3 6
21 25 -14.21
P4 7
35 40 5.95 D4 11 50 55 -5.95
对 tr4 元素的细节设计
General On.action on: V1time(9)=TIME. V1speed(1)=NORMAL(50,2,10) Front.action on front: V1time(10)=TIME V1lucheng(5)=200 V1sumtime (4)=V1time (10)-V1time(9). V1shijian=V1time(10)-V1time(1) IF V1shijian>50 V1chechaoshijian=V1shijian-50 ENDIF v1chengben=V1lucheng(1)+V1lucheng(2)+ V1lucheng(3)+V1lucheng(4)+V1lucheng(5) +0.5*V1shijian+1.5*V1chechaoshijian
Unloading.output unloading rule: PUSH Part007 to Con1 at Rear, Part006 to Con1 at Rear
对 tr3 元素的细节设计
General On.action on: V1time(7)=TIME. V1speed(2)=NORMAL(50,2,9) Front.action on front: V1time(8)=TIME. V1lucheng(4)=500 V1sumtime (4)=V1time (8)-V1time(7). V1kongzh(i 4)=V1time(8)-V1time(1) Out put to : PUSH to tr4 Unloading.output unloading rule:PUSH Part007 to d2
1 车辆路径问题的描述 车辆路径问题(Vehicle Routing Problem,简称 VRP)
是物流配送优化中的一个重要问题,是由 G.Dantzing 和 J.Ramser 于 1959 年提出的一个典型的组合优化问题,是 交通和物流配送领域的一个核心问题,其典型定义如下: 一般指对一系列的客户点,组织适当的行车路线,使车辆 有序地通过它们,在满足一定的约束条件下(如货物需求 量,车辆容量限制,以及到达时间限制等),达到一定的目 标(如运距最短,费用最小,车辆数尽量少和客户满意度 最佳等)。 2 仿真概述
型,然后运行仿真模型,得到仿真输出结果,通过对模型结果的输出分析,寻找车辆路径问题的瓶颈因素,通过对瓶颈因
素的解决,进行问题的优化,最后得到更优的可行解。
关键词:车辆路径问题;仿真;模型;系统;优化
中图分类号:TP301.6
文献标识码:A
文章编号:1002-2333(2009)11-0056-04
Simulation Modeling and Optimization of Vehicle Routing Problem Based on Witness MIN Xu-dong, HAN Xiao-long
在车辆路径优化中,我们根据实际需要,建立车辆路 径的仿真模型,通过运行一定的时间,得到数据输出报告, 进行仿真模型的分析,可以预先得出模型的瓶颈问题,如 车辆太少,速度太慢等,然后提前进行优化,以提高效益, 降低成本,以高水平实现物流的供应,满足客户的需求。 3 车辆路径问题的仿真建模与优化 3.1 问题描述
d1 Con1
Part005 p7
Tr2 Part006 p1
Tr3
t2
d7 t1
t3
Tr1 p2 Part007
Tr5 d2
V2 Demand List s2 V7
V1 Demand List
Tr4
t8
Demand List
V3
s1
d6 t7 p6
t4
Demand List
p5 Part003
tr10 d4
对 tr2 元素的细节设计
General On.action on: V1time(5)=TIME. V1speed(2)=NORMAL(50,2,8) Front.action on front: V1time(6)=TIME. V1lucheng(3)=100 V1sumtime (3)=V1time (6)-V1time(5). V1kongzh(i 3)=V1time(6)-V1time(1) Out put to:PUSH to tr3 Loading.input loading rule: PULL from Part007 out of Con1 at Front
为 0.8。以 P1 到 P7 为例,其距离为 200,则慢速车行走的
成本为 220,中速车行走的成本为 200,快速车行走的成
本为 160。
车辆超出最大工作时间的单位时间惩罚成本为 1.5,
车辆总行走时间的换算当量成本系数为 0.5,即:obj=车
56 机械工程师 2009 年第 11 期
制造业信息化
Entry.to:PUSH to Tr5 In motion.unloaded:v1speed(1),loaded:v1speed(2)
对 tr5 元素的细节设计
General On.action on: V1time(1)=TIME. V1speed(1)=NORMAL(50,2,6) Front.action on front: V1time(2)=TIME. V1lucheng(1)=200 V1sumtime (1)=V1time (2)-V1time(1). V1kongzh(i 1)=V1time(2)-V1time(1) Out put to: PUSH to Tr1
P5 14
9 15 7.39 D5 5
35 40 -7.39
P6 13 45 51 12 D6 8
63 70 -12
P7 6
3 5 4 D7 6
11 13 -4
3.2 构建结构模型 定义车辆路径系统元素,并布置可视化模型结构图,
根据现行状态构建的仿真模型,如图 2 所示,可以清晰地 看出各实体的相互关系,s 代表车场,v 代表车辆,t 代表 路径,p 代表提货点,d 代表收货点。
制造业信息化
MANUFACTURING INFORMATIZATION 仿真 / 建模 / CAD/ CAM/ CAE/ CAPP
基于 Witness 车辆路径问题的仿真建模与优化
闵旭东, 韩晓龙 (上海海事大学 科学研究院,上海 200135)
摘 要:简要介绍了车辆路径问题及仿真的知识,针对实际问题,利用 Witness 仿真软件,建立车辆路径问题的仿真模
仿真 / 建模 / CAD/ CAM/ CAE/ CAPP MANUFACTURING INFORMATIZATION
辆行走成本+0.5×车辆总行走时间+1.5×车辆超出最大工 作时间的时间。
各点之间的路程如下(公里): S1_(200)_p2_(141)__p1_(100)_d1_(500)_d2 S1_(283)_p3_(141)_d3_(316)_p4_(224)_d4 S2_(200)__p7_(141)__d7 S2_(224)_p5_(424)__d5_(224)__p6_(224)_d6 各任务点的参数如表 2。
tr6 Part001
p3
Part004
t6
t5
d5
tr9
tr7
Part002 p4
d3 tr8
图2
3.2.1 结构模型的设置 结构模型的设置包括元素的可视化设置与细节设
置,可视化设计的主要元素有:车辆 (Vehicle),路径 (Tracks),提货点、收货点(Buffers),货物(Part)等。 3.2.2 元素的可视化设置
Loading .Input loading rule: PULL from Part007 out of p2
对 tr1 元素的细节设计
General On.action on: V1time(3)=TIME,V1speed(2)=NORMAL(50,1,7) Front.action on front: V1time(4)=TIME. V1lucheng(2)=141 V1sumtime (2)=V1time (4)-V1time(3). V1kongzh(i 2)=V1time(4)-V1time(1) Out put to:PUSH to Tr2 Loading.Input loading rule:PULL from Part006 out of p1