聚醚醚酮及其复合材料的研究
PEEK研究报告
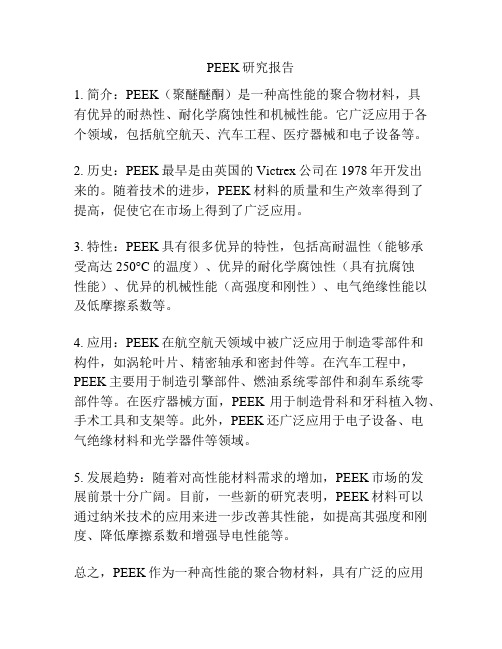
PEEK研究报告
1. 简介:PEEK(聚醚醚酮)是一种高性能的聚合物材料,具
有优异的耐热性、耐化学腐蚀性和机械性能。
它广泛应用于各个领域,包括航空航天、汽车工程、医疗器械和电子设备等。
2. 历史:PEEK最早是由英国的Victrex公司在1978年开发出
来的。
随着技术的进步,PEEK材料的质量和生产效率得到了
提高,促使它在市场上得到了广泛应用。
3. 特性:PEEK具有很多优异的特性,包括高耐温性(能够承
受高达250°C的温度)、优异的耐化学腐蚀性(具有抗腐蚀
性能)、优异的机械性能(高强度和刚性)、电气绝缘性能以及低摩擦系数等。
4. 应用:PEEK在航空航天领域中被广泛应用于制造零部件和
构件,如涡轮叶片、精密轴承和密封件等。
在汽车工程中,PEEK主要用于制造引擎部件、燃油系统零部件和刹车系统零
部件等。
在医疗器械方面,PEEK用于制造骨科和牙科植入物、手术工具和支架等。
此外,PEEK还广泛应用于电子设备、电
气绝缘材料和光学器件等领域。
5. 发展趋势:随着对高性能材料需求的增加,PEEK市场的发
展前景十分广阔。
目前,一些新的研究表明,PEEK材料可以
通过纳米技术的应用来进一步改善其性能,如提高其强度和刚度、降低摩擦系数和增强导电性能等。
总之,PEEK作为一种高性能的聚合物材料,具有广泛的应用
前景。
随着技术的不断发展和研究的深入,PEEK的性能将不断提高,相信它将在更多的领域得到应用。
聚醚醚酮与其它热塑性耐高温树脂共混纺丝研究

聚醚醚酮与其它热塑性耐高温树脂共混纺丝研究聚醚醚酮(PEEK)是一种热塑性耐高温树脂,具有优异的机械性能和化学稳定性,被广泛应用于航空航天、汽车、电子、化工等领域。
然而,由于PEEK的高成本和加工性能的限制,研究者们开始探索将PEEK与其他热塑性耐高温树脂进行共混纺丝的方法。
共混纺丝是一种将两种或多种树脂混合后进行纺丝加工的技术。
通过合理选择共混树脂的比例和加工条件,可以获得具有新的性能和应用领域的复合材料。
PEEK与其他热塑性耐高温树脂的共混纺丝研究,不仅可以降低材料成本,还可以改善PEEK的加工性能和优化其性能。
目前,研究者们已经在PEEK与聚酰胺、聚芳醚、聚酮等树脂的共混纺丝方面取得了一定的进展。
例如,PEEK与聚酰胺的共混纺丝材料具有较好的综合性能,可以应用于制备高性能的弹性体和耐磨材料。
PEEK与聚芳醚的共混纺丝材料具有较高的热稳定性和耐化学腐蚀性,适用于制备高性能的密封材料和化工管道。
PEEK与聚酮的共混纺丝材料具有较高的机械强度和耐高温性能,适用于制备高性能的结构材料和电子元件。
共混纺丝研究中,通过调整PEEK与其他树脂的比例、纺丝温度和纺丝速度等工艺参数,可以调控共混材料的结晶行为、分子链排列和相互作用,从而影响材料的力学性能、热性能和表面形态。
此外,研究者们还可以通过添加填料、改性剂和增容剂等功能性添加剂,进一步改善共混材料的性能。
总之,聚醚醚酮与其他热塑性耐高温树脂的共混纺丝研究具有重要的科学意义和应用前景。
通过合理选择共混树脂和添加剂,可以获得具有优异性能的复合材料,拓宽PEEK的应用领域。
未来,研究者们还可以进一步深入研究共混纺丝材料的微观结构和力学性能,以及其在航空航天、汽车、电子、化工等领域的应用。
浅析聚醚醚酮的发展概况

浅谈聚醚醚酮的研究进展摘要:本文介绍了特种工程塑料聚醚醚酮的性质、制备、应用以及对其应用前景的展望。
关键词:特种工程塑料;聚醚醚酮;聚醚醚酮性质;聚醚醚酮制备;聚醚醚酮应用;1.认识聚醚醚酮1.1聚醚醚酮介绍特种工程塑料聚醚醚酮(PEEK)是20世纪70年代末研究开发成功的一种新型半晶态芳香族热塑性工程塑料,与其他特种工程塑料相比,具有耐高温、机械性能优异、自润滑性好、易加工、耐化学品腐蚀、阻燃、耐剥离性、耐辐照性、绝缘性稳定、耐水解和易加工等优异性能,在航空航天、汽车、电子电气、医疗和食品加工等领域被广泛应用,开发利用前景广阔。
1.2聚醚醚酮性能1.2.1耐高温PEEK 树脂具有较高的玻璃化转变温度(143℃)和熔点(334℃),这是它可在有耐热性要求的用途中可靠应用的理由之一。
其负载热变型温度高达316℃(30%GF或CF增强牌号),连续使用温度为260℃。
1.2.2机械特性PEEK树脂是韧性和刚性兼备并取得平衡的塑料。
特别是它对交变应力的优良耐疲劳性是所有塑料中最出众的,可与合金材料媲美。
1.2.3自润滑性(耐腐蚀性)PEEK树脂在所有塑料中具有出众的滑动特性,适合于严格要求低摩擦系数和耐摩耗用途使用。
特别是碳纤、石墨、聚四氟乙烯各占10%比例混合改性的滑动牌号或30%CF增强牌号等均为具有优异滑动特性的牌号。
1.2.4 耐化学药品性PEEK树脂具有优异的耐化学药品性,在通常的化学药品中,能溶解或者破坏它的只有浓硫酸,它的耐腐蚀性与镍钢相近。
1.2.5阻燃性PEEK树脂是非常稳定的聚合物,1.45mm厚的样品,不加任何阻燃剂就可达到最高阻燃标准。
1.2.6耐剥离性PEEK 树脂的耐剥离性很好,因此可制成包覆很薄的电线或电磁线,并可在苛刻条件下使用。
1.2.7耐辐照性耐γ辐照的能力很强,超过了通用树脂中耐辐照性最好的聚苯乙烯。
可以作成γ辐照剂量达1100Mrad时仍能保持良好的绝缘能力的高性能电线。
peek复合材料
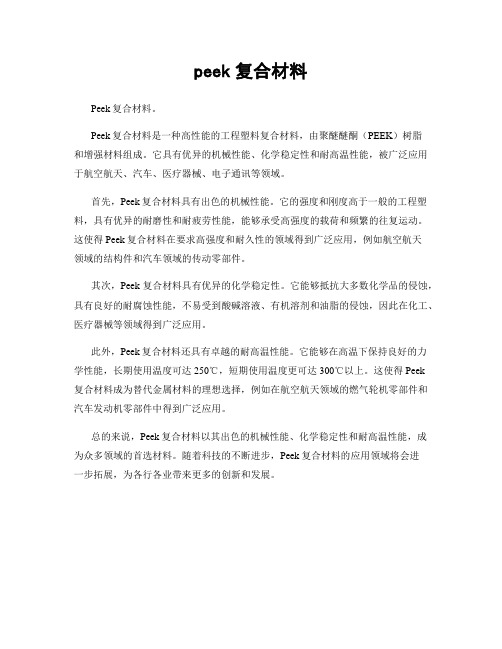
peek复合材料
Peek复合材料。
Peek复合材料是一种高性能的工程塑料复合材料,由聚醚醚酮(PEEK)树脂
和增强材料组成。
它具有优异的机械性能、化学稳定性和耐高温性能,被广泛应用于航空航天、汽车、医疗器械、电子通讯等领域。
首先,Peek复合材料具有出色的机械性能。
它的强度和刚度高于一般的工程塑料,具有优异的耐磨性和耐疲劳性能,能够承受高强度的载荷和频繁的往复运动。
这使得Peek复合材料在要求高强度和耐久性的领域得到广泛应用,例如航空航天
领域的结构件和汽车领域的传动零部件。
其次,Peek复合材料具有优异的化学稳定性。
它能够抵抗大多数化学品的侵蚀,具有良好的耐腐蚀性能,不易受到酸碱溶液、有机溶剂和油脂的侵蚀,因此在化工、医疗器械等领域得到广泛应用。
此外,Peek复合材料还具有卓越的耐高温性能。
它能够在高温下保持良好的力学性能,长期使用温度可达250℃,短期使用温度更可达300℃以上。
这使得Peek
复合材料成为替代金属材料的理想选择,例如在航空航天领域的燃气轮机零部件和汽车发动机零部件中得到广泛应用。
总的来说,Peek复合材料以其出色的机械性能、化学稳定性和耐高温性能,成为众多领域的首选材料。
随着科技的不断进步,Peek复合材料的应用领域将会进
一步拓展,为各行各业带来更多的创新和发展。
PEEK复合材料的性能研究

0 61 10- 6
40 43
1 79 10- 6
26 47
弯曲强度 / MPa
183 17
218 05
注: 1) 以上结果为 4 次测试的平均值
两种 PEEK 复合材料的常规力学性能和摩擦磨损 性能如表 1 所示。从表 1 中可以看出, 黑色 PEEK 复 合材料具有更好的韧性。两种 PEEK 复合材料的摩擦 系数 都 很小, 黑 色 PEEK 复 合 材 料 的 摩擦 系 数 为 0 21, 而灰色 PEEK 复合材料 的摩擦系数只有 0 18; 这是由于其中的固体润滑剂 PTFE 比石墨本身具有更 好的润滑性能所致。另外, 从表 1 还可以看出, 两种 PEEK 复合材料的磨损率都很小; 因为 PEEK 中除添 加有固体润滑剂外, 还添加有其它增强材料如无机纳 米粉末等。
第 30 卷第 4 期
颜红侠 宁 荣昌 黄 英: PEEK 复合材料的性能研究
45
PEEK 复合材料的摩擦系数为 0 21, 黑色 PEEK 复合 材料具有更好的韧性, 两种复合材料主要受粘着磨损 机制控制, 并伴有热塑性流动磨损。
图 1 灰色 PEEK 的 SEM 照片
Fig 1 SEM photo of gray PEEK composite
试验载荷为 196 N, 转速为 200 r/ min, 摩擦时间为 2
h。采用感量为 0. 01 mg 的分析天平称量试样磨损质
量变化, 将其转换为磨损体积损失, 以单位载荷单位
磨损行程内试样的磨损体积损失作为磨损率; 通过测 定摩擦力矩并计算得出摩擦系数, 摩擦系数取值为达
到稳定磨损状态后 1 h 内的平均值。
2 结果与讨论
表 1 两种 PEEK 复合材料和 力学性能和摩擦磨损性能1)
聚醚醚酮复合材料摩擦学性能研究现状

为 : 面 S 、i ~方 i S N 等纳 米粒子 在滑 动摩擦过程 中通过 与 C
璃纤维 ( F 、 G )无机纳米粒子等复合增 强 , 为米粒子被氧化为 S 可 i , O
4% , 8 其在无定形状 态下密度为 12 6s c 在最大 结晶度 。 5 /m ,
等粒子也可明显提 高 P E E K复合 材料 的摩擦 学性能 。JV .. V o 等 研 究 发 现 , C S粒 子 的体 积分 数 为 3% 时 , or t 当 u 5
下密度为 130g11 E K 的结 晶结 构使其具 有 突出 的 .2 2 /1 。P E 1 ' 耐热性能和力学 性 能 , 在 20 可 5" C下长 期使 用 , 间使用 温 瞬
聚醚醚酮 ( E K) 英 国 I I 司于 17 PE 是 C公 9 7年 开发成 功
并于 18 年正式生产 销售的 一种 高性 能工程 塑料 , 的摩 90 它 擦系数低 , 耐磨性 能好 , 是一种优 良的低摩 耐磨 材料 , 广泛应
1% 时 ,E K复合材料 的摩擦 系数 分别小 于 02 、.0和 5 PE .20 3 02 , .4 而磨损率则随纳米粒子 含量 的增加 而呈 现先 下降后 上 升趋势 。同时 P E E K复合 材料 的摩 擦 系数 随载荷 的增加 而
良的润滑性能 。Wag . . n H 等 研究发现 , FT Q 当 IE的体 积
分数小于 5 时 , 着 P F % 随 T E含 量 的增 加 , E K P F P E / T E复 合
弯曲强度/ P Ma 弯曲弹性模量/ P Ga
压缩 强度/ P M a
聚醚醚酮及其复合材料激光粉末床熔融成形的研究现状与展望

精 密 成 形 工 程第15卷 第11期46 JOURNAL OF NETSHAPE FORMING ENGINEERING2023年11月收稿日期:2023-08-02 Received :2023-08-02基金项目:国家重点研发计划(2022YFB4600101,2022YFB4600103)Fund :National Key R&D Program of China (2022YFB4600101, 2022YFB4600103)引文格式:李亚洲, 杨强, 彭瑞龙, 等. 聚醚醚酮及其复合材料激光粉末床熔融成形的研究现状与展望[J]. 精密成形工程, 2023, 15(11): 46-60.LI Ya-zhou, YANG Qiang, PENG Rui-long, et al. Research Status and Prospect of Laser Powder Bed Fusion of Polyethere-therketone and Its Composites[J]. Journal of Netshape Forming Engineering, 2023, 15(11): 46-60. 聚醚醚酮及其复合材料激光粉末床熔融成形的研究现状与展望李亚洲,杨强*,彭瑞龙,王富,李涤尘(西安交通大学 a.机械制造系统工程国家重点实验室 b.机械工程学院,西安 710049) 摘要:聚醚醚酮(PEEK )及其复合材料因具有优异的力学性能、耐化学腐蚀性及生物相容性而受到广泛关注,然而随着对复杂结构以及个性化PEEK 零件的需求日益增加,传统的注塑成形工艺显然已经难以满足高度复杂化与个性化制造的需求。
激光粉末床熔融(LPBF )技术为PEEK 及其复合材料的成形制造提供了一种新的方法。
介绍了激光粉末床熔融工艺的基本原理与PEEK 及其复合材料的激光粉末床熔融制备工艺的特点和应用,总结归纳了PEEK 及其复合材料的激光粉末床熔融成形装备的发展状况与性能特点,目前的成形装备在预热温度和激光功率等参数方面已经有了很大的提升,可以保证一定的成形精度,但要形成一套成熟的高精密和大尺寸复杂成形系统仍需进一步的研究。
基于冷压烧结成型的PTFEPEEK复合材料摩擦学及力学性能研究

第12期2020年4月No.12April ,2020基于冷压烧结成型的PTFE/PEEK 复合材料摩擦学及力学性能研究摘要:文章研究了聚醚醚酮(PEEK )填充的聚四氟乙烯(PTFE )复合材料的摩擦学及力学性能,随后研究了碳纤维改性的PTFE/PEEK 复合材料摩擦学性能。
PEEK 的加入降低了PTFE/PEEK 复合材料的滑动摩擦系数及磨损量,提高了PTFE/PEEK 复合材料的压缩性能,但是降低了材料的拉伸性能。
当PEEK 质量分数超过30%时,PTFE/PEEK 复合材料拉伸呈脆性断裂。
碳纤维加入PTFE/PEEK 复合材料,由于摩擦转移膜连续性变差,降低了复合材料的摩擦学性能。
关键词:聚醚醚酮;聚四氟乙烯;摩擦学;力学性能;冷压中图分类号:TB472文献标志码:A江苏科技信息Jiangsu Science &Technology Information夏炎,王孝刚,徐辉(南京肯特复合材料股份有限公司,江苏南京211162)作者简介:夏炎(1990—),男,安徽无为人,工程师,硕士;研究方向:特种工程塑料制备与成型。
0引言聚四氟乙烯(PTFE )具有摩擦系数低、使用温度区间宽、耐化性优异、表面能极低等特点,在摩擦磨损及密封领域占有十分重要的地位。
但纯PTFE 耐磨性差、硬度低、高温机械强度损失较大,限制了其在运动组件、机械承载密封等领域的应用。
目前,人们通常采用填充及复合的方法改善其缺点。
常用的填料可分为无机物、有机物、金属及金属氧化物三类。
部分无机填料、金属及金属氧化物改性的PTFE 复合材料在作为动密封材料时容易损伤对偶,且存在比重大、机加工性能差、耐化性下降等缺点。
因此,研究者开发了一系列耐高温的芳杂环聚合物如聚苯酯(POB )、聚苯硫醚(PPS )、聚酰亚胺(PI )、聚醚醚酮(PEEK )和芳纶(AF )等填充改性的PTFE 复合材料[1-2]。
PEEK 具有优良的综合性能,研究多集中使用PTFE 作为固体润滑剂改善PEEK/PTFE 复合材料的摩擦性能[3-4]。