铸铝车轮制造技术 A356合金的熔炼
《汽车轮毂用A356铝合金的精炼及净化》范文
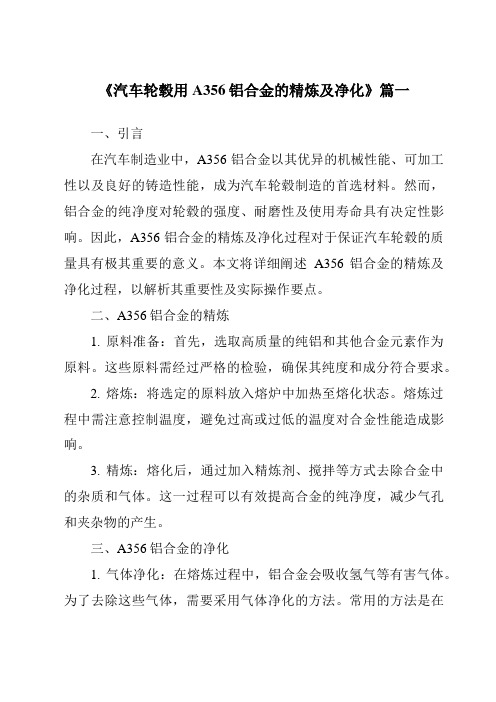
《汽车轮毂用A356铝合金的精炼及净化》篇一一、引言在汽车制造业中,A356铝合金以其优异的机械性能、可加工性以及良好的铸造性能,成为汽车轮毂制造的首选材料。
然而,铝合金的纯净度对轮毂的强度、耐磨性及使用寿命具有决定性影响。
因此,A356铝合金的精炼及净化过程对于保证汽车轮毂的质量具有极其重要的意义。
本文将详细阐述A356铝合金的精炼及净化过程,以解析其重要性及实际操作要点。
二、A356铝合金的精炼1. 原料准备:首先,选取高质量的纯铝和其他合金元素作为原料。
这些原料需经过严格的检验,确保其纯度和成分符合要求。
2. 熔炼:将选定的原料放入熔炉中加热至熔化状态。
熔炼过程中需注意控制温度,避免过高或过低的温度对合金性能造成影响。
3. 精炼:熔化后,通过加入精炼剂、搅拌等方式去除合金中的杂质和气体。
这一过程可以有效提高合金的纯净度,减少气孔和夹杂物的产生。
三、A356铝合金的净化1. 气体净化:在熔炼过程中,铝合金会吸收氢气等有害气体。
为了去除这些气体,需要采用气体净化的方法。
常用的方法是在熔炉中通入惰性气体(如氩气),通过置换熔融金属中的气体,将氢气等有害气体从金属中排出。
2. 机械净化:通过离心分离机等设备对熔融金属进行离心分离,进一步去除杂质和夹杂物。
离心分离可以有效分离密度较大的夹杂物和颗粒物,提高合金的纯净度。
四、精炼及净化过程中的注意事项1. 控制温度:在精炼及净化过程中,需严格控制温度。
过高的温度可能导致合金元素挥发,影响合金性能;过低的温度则可能导致精炼及净化效果不佳。
2. 添加适量精炼剂:精炼剂的添加量需根据实际情况进行调整。
过多或过少的精炼剂都会影响精炼及净化效果。
3. 定期检查设备:定期对熔炉、离心分离机等设备进行检查和维护,确保其正常运行和良好的工作状态。
五、结论A356铝合金的精炼及净化过程对于保证汽车轮毂的质量具有至关重要的作用。
通过精炼和净化过程,可以有效去除合金中的杂质和气体,提高合金的纯净度,从而保证汽车轮毂的强度、耐磨性及使用寿命。
《汽车轮毂用A356铝合金的精炼及净化》范文

《汽车轮毂用A356铝合金的精炼及净化》篇一一、引言随着汽车工业的飞速发展,汽车轮毂的制造材料及工艺成为行业关注的焦点。
A356铝合金因其优良的机械性能、铸造性能和抗腐蚀性能,被广泛应用于汽车轮毂的制造。
本文将详细解析A356铝合金的精炼及净化过程,以确保其达到汽车轮毂制造的高标准要求。
二、A356铝合金的基本特性A356铝合金是一种典型的压铸铝合金,具有良好的流动性和抗腐蚀性,能够满足汽车轮毂制造的严格要求。
然而,其成分中的杂质会对合金的性能产生影响,因此需要通过精炼和净化过程来提高其纯度和性能。
三、A356铝合金的精炼过程1. 原料准备:选择优质的A356铝合金原材料,进行预处理,去除表面杂质和氧化皮。
2. 熔炼:将预处理后的原材料放入熔炉中加热至熔化,这一过程需严格控制温度和时间,防止过烧和化学成分的变化。
3. 除气精炼:熔化后的铝液需通过除气机进行除气处理,以去除其中的氢气和其它气体杂质。
这一步骤对于提高合金的纯净度和机械性能至关重要。
4. 熔剂覆盖:在铝液表面覆盖一层熔剂,以防止空气和杂质的侵入,并进一步保护铝液的纯净度。
四、A356铝合金的净化过程1. 机械过滤:利用滤网等设备对铝液进行机械过滤,去除其中的固体杂质和悬浮颗粒。
2. 静置沉降:经过机械过滤后的铝液需静置一段时间,使微小杂质在重力的作用下沉降到底部。
3. 真空净化:采用真空技术对铝液进行进一步净化,通过降低压力使气体和杂质在铝液中上浮至表面,便于去除。
五、精炼及净化后的效果与质量控制经过精炼及净化后的A356铝合金,其纯度和性能得到显著提高,能够满足汽车轮毂制造的高标准要求。
为确保产品质量,需对精炼及净化后的铝合金进行严格的质量检测和控制,包括化学成分分析、机械性能测试等。
此外,还需对生产过程中的关键环节进行监控和记录,确保产品质量可追溯。
六、结论本文详细解析了汽车轮毂用A356铝合金的精炼及净化过程。
通过严格的精炼和净化措施,可以有效提高A356铝合金的纯度和性能,满足汽车轮毂制造的高标准要求。
A356合金熔炼原理

A356合金熔炼原理一、铝轮毂采用的合金及化学成分现代汽车铸造铝合金车轮应用最广的材料是美国材料与试验协会(ASTM)牌号A356合金,相当于中国ZL101A、日本AC4CH、德国AlSi7Mg、法国A-S7G03、俄罗斯Aл9-1。
除A356合金外,德国还采用AlSi9Mg、AlSi10Mg、AlSi11Mg,法国还采用A-S11G、A-S12.5。
这些高Si合金都不热处理,它们液态流动性好、补缩能力强、铸造性能好、铸造缺陷少。
但机械性能和机加工艺性能不如A356合金。
A356合金又分为A356.2、A356.1、A356.0,其化学成分,分别为下表:二、熔炼温度和时间控制A356合金大约在580℃时开始有液态出现,到640℃就可全部熔化,一般最高熔炼温度控制在760℃,铝液温度超过770℃,明显开始氧化,夹杂物和含气量大幅增加,凝固后组织晶粒也会粗大,铝液质量开始下降。
所以,对A356合金的熔炼时,低温熔炼有利提高铝液质量,提高材料的机械性能。
请看下图:氧化物增量μg /c ㎡h640 700 770 800 ℃温度→温度对铝合金液氧化的影响另外A356合金熔化时,时间不能太长,特别是在高温下保温时间太长,不利于铝液质量。
浇注温度也不能太高,低压铸造浇注温度一般在685~710℃,重力铸造一般控制在730℃左右。
国内铝合金车轮生产厂家,凡采用低压铸造工艺,都用中间包转运铝液,并进行除渣除气,如中间包烤的不好,铝液在中间包降温很快,一般铝液出炉温度控制在760℃,也有控制在770℃,如果选好的烤包器,中间包温度可烤到600℃,这样铝液降温就慢,铝液可在740℃出炉。
铝液质量就会大大提高,而烧损也少。
三、熔炼过程对环境水分控制A356合金在熔炼过程中,空气含水蒸气的量,原材料含水量,炉膛和工具吸水量,精练剂和打渣剂含水量,旋转除气中氩气或氮气含水量,低压铸造机用的压缩空气含水量等等,这些都与铝合金液接触,都能与铝液起以下反应:2Al (l )+3H 2O (g )=r-Al 2O 3+6[H]这个反映比铝液和空气中的氧反应还激烈,当水含量为10-21时,上述反应仍然进行,即使铝液表面有氧化膜保护时,这个反应也能进行。
《2024年汽车轮毂用A356铝合金的精炼及净化》范文

《汽车轮毂用A356铝合金的精炼及净化》篇一一、引言随着汽车工业的快速发展,汽车轮毂作为汽车的重要组成部分,其材料的选择与制造工艺的优化显得尤为重要。
A356铝合金因其良好的铸造性能、机械性能以及成本效益,在汽车轮毂制造中得到了广泛应用。
然而,A356铝合金的精炼及净化过程对最终产品的性能和质量具有决定性影响。
本文将详细探讨A356铝合金的精炼及净化工艺,以期为相关领域的研究和应用提供参考。
二、A356铝合金的成分及特性A356铝合金是一种常用的铸造铝合金,主要由铝、硅、镁等元素组成。
其具有良好的铸造性能、机械性能以及抗腐蚀性能,适用于制造汽车轮毂等零部件。
然而,由于原材料中可能存在杂质和气体,因此在熔炼过程中需要进行精炼及净化处理。
三、A356铝合金的精炼工艺1. 原料准备:首先,需要准备好高质量的A356铝合金原料,清除原料表面的杂质和油污。
2. 熔炼:将准备好的原料放入熔炉中,进行熔炼。
在熔炼过程中,需要控制好温度和时间,以确保原料充分熔化。
3. 精炼剂添加:在熔炼过程中,需要添加精炼剂以去除熔液中的杂质和气体。
精炼剂的作用是吸附熔液中的杂质,使其上浮至熔液表面,从而达到净化熔液的目的。
4. 搅拌:添加精炼剂后,需要进行搅拌,使精炼剂与熔液充分混合,加速杂质的上浮。
5. 静置与撇渣:搅拌完成后,需要让熔液静置一段时间,使杂质充分上浮至表面。
然后,用撇渣工具将表面的杂质和气体撇去。
四、A356铝合金的净化工艺1. 气体净化:在熔炼过程中,可能会产生一些气体,如氢气等。
为了去除这些气体,可以在熔炉中通入惰性气体(如氩气),通过气体的流动带走熔液中的气体。
2. 熔剂覆盖:在熔液表面覆盖一层熔剂,可以防止空气中的杂质进入熔液,同时还可以促进杂质的上浮和分离。
3. 真空处理:对于要求更高的净化工艺,可以采用真空处理。
在真空环境下,熔液中的气体和杂质更容易被去除。
五、结论通过对A356铝合金的精炼及净化工艺的探讨,我们可以得出以下结论:1. 精炼及净化工艺对A356铝合金的性能和质量具有重要影响。
A356合金熔炼原理

A356合金熔炼原理一、铝轮毂采用的合金及化学成分现代汽车铸造铝合金车轮应用最广的材料是美国材料与试验协会(ASTM)牌号A356合金,相当于中国ZL101A、日本AC4CH、德国AlSi7Mg、法国A-S7G03、俄罗斯Aл9-1。
除A356合金外,德国还采用AlSi9Mg、AlSi10Mg、AlSi11Mg,法国还采用A-S11G、A-S12.5。
这些高Si合金都不热处理,它们液态流动性好、补缩能力强、铸造性能好、铸造缺陷少。
但机械性能和机加工艺性能不如A356合金。
A356合金又分为A356.2、A356.1、A356.0,其化学成分,分别为下表:二、熔炼温度和时间控制A356合金大约在580℃时开始有液态出现,到640℃就可全部熔化,一般最高熔炼温度控制在760℃,铝液温度超过770℃,明显开始氧化,夹杂物和含气量大幅增加,凝固后组织晶粒也会粗大,铝液质量开始下降。
所以,对A356合金的熔炼时,低温熔炼有利提高铝液质量,提高材料的机械性能。
请看下图:氧化物增量μg /c ㎡h640 700 770 800 ℃温度→温度对铝合金液氧化的影响另外A356合金熔化时,时间不能太长,特别是在高温下保温时间太长,不利于铝液质量。
浇注温度也不能太高,低压铸造浇注温度一般在685~710℃,重力铸造一般控制在730℃左右。
国内铝合金车轮生产厂家,凡采用低压铸造工艺,都用中间包转运铝液,并进行除渣除气,如中间包烤的不好,铝液在中间包降温很快,一般铝液出炉温度控制在760℃,也有控制在770℃,如果选好的烤包器,中间包温度可烤到600℃,这样铝液降温就慢,铝液可在740℃出炉。
铝液质量就会大大提高,而烧损也少。
三、熔炼过程对环境水分控制A356合金在熔炼过程中,空气含水蒸气的量,原材料含水量,炉膛和工具吸水量,精练剂和打渣剂含水量,旋转除气中氩气或氮气含水量,低压铸造机用的压缩空气含水量等等,这些都与铝合金液接触,都能与铝液起以下反应:2Al (l )+3H 2O (g )=r-Al 2O 3+6[H]这个反映比铝液和空气中的氧反应还激烈,当水含量为10-21时,上述反应仍然进行,即使铝液表面有氧化膜保护时,这个反应也能进行。
《汽车轮毂用A356铝合金的精炼及净化》范文
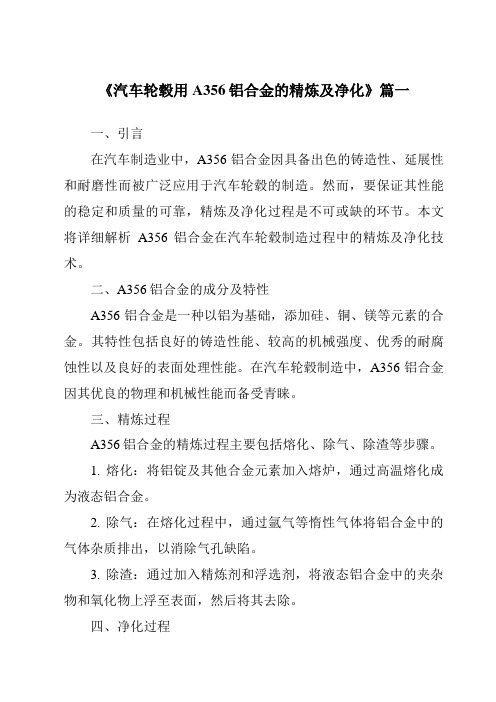
《汽车轮毂用A356铝合金的精炼及净化》篇一一、引言在汽车制造业中,A356铝合金因具备出色的铸造性、延展性和耐磨性而被广泛应用于汽车轮毂的制造。
然而,要保证其性能的稳定和质量的可靠,精炼及净化过程是不可或缺的环节。
本文将详细解析A356铝合金在汽车轮毂制造过程中的精炼及净化技术。
二、A356铝合金的成分及特性A356铝合金是一种以铝为基础,添加硅、铜、镁等元素的合金。
其特性包括良好的铸造性能、较高的机械强度、优秀的耐腐蚀性以及良好的表面处理性能。
在汽车轮毂制造中,A356铝合金因其优良的物理和机械性能而备受青睐。
三、精炼过程A356铝合金的精炼过程主要包括熔化、除气、除渣等步骤。
1. 熔化:将铝锭及其他合金元素加入熔炉,通过高温熔化成为液态铝合金。
2. 除气:在熔化过程中,通过氩气等惰性气体将铝合金中的气体杂质排出,以消除气孔缺陷。
3. 除渣:通过加入精炼剂和浮选剂,将液态铝合金中的夹杂物和氧化物上浮至表面,然后将其去除。
四、净化过程净化过程主要是通过化学和物理方法进一步去除A356铝合金中的杂质,提高其纯度和性能。
1. 化学净化:通过添加特定的化学试剂,与合金中的杂质发生化学反应,生成无害或低害的化合物,并通过精炼和浮选将其去除。
2. 物理净化:利用离心分离、真空蒸馏等技术,通过物理方法去除合金中的杂质和气体。
五、工艺控制及优化为了确保A356铝合金的精炼及净化效果,需要对整个过程进行严格的工艺控制及优化。
这包括控制熔炼温度、精炼剂和浮选剂的添加量、除气和除渣的时间和频率等。
此外,还需要定期对设备进行维护和检修,确保其正常运行和良好的工作状态。
六、结论A356铝合金的精炼及净化过程是汽车轮毂制造中不可或缺的环节。
通过精炼和净化,可以有效地去除合金中的杂质和气体,提高其纯度和性能,从而保证汽车轮毂的质量和性能。
在未来的汽车制造业中,随着对材料性能和质量的不断要求提高,A356铝合金的精炼及净化技术将不断得到优化和发展。
《2024年汽车轮毂用A356铝合金的精炼及净化》范文
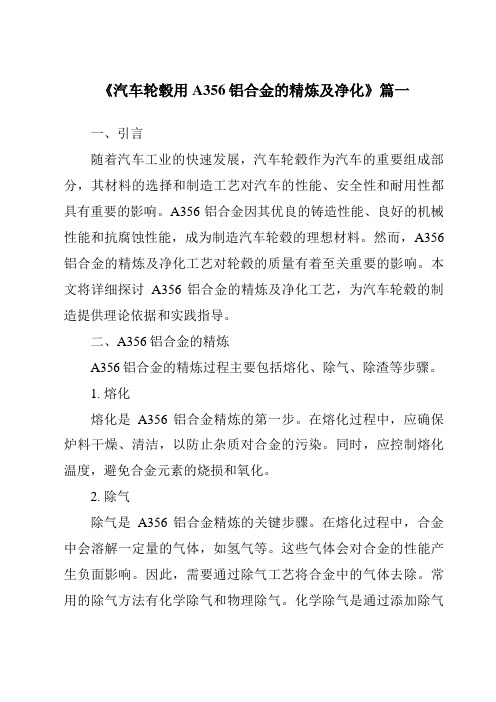
《汽车轮毂用A356铝合金的精炼及净化》篇一一、引言随着汽车工业的快速发展,汽车轮毂作为汽车的重要组成部分,其材料的选择和制造工艺对汽车的性能、安全性和耐用性都具有重要的影响。
A356铝合金因其优良的铸造性能、良好的机械性能和抗腐蚀性能,成为制造汽车轮毂的理想材料。
然而,A356铝合金的精炼及净化工艺对轮毂的质量有着至关重要的影响。
本文将详细探讨A356铝合金的精炼及净化工艺,为汽车轮毂的制造提供理论依据和实践指导。
二、A356铝合金的精炼A356铝合金的精炼过程主要包括熔化、除气、除渣等步骤。
1. 熔化熔化是A356铝合金精炼的第一步。
在熔化过程中,应确保炉料干燥、清洁,以防止杂质对合金的污染。
同时,应控制熔化温度,避免合金元素的烧损和氧化。
2. 除气除气是A356铝合金精炼的关键步骤。
在熔化过程中,合金中会溶解一定量的气体,如氢气等。
这些气体会对合金的性能产生负面影响。
因此,需要通过除气工艺将合金中的气体去除。
常用的除气方法有化学除气和物理除气。
化学除气是通过添加除气剂与合金中的气体反应,从而将气体从合金中排出。
物理除气则是利用真空泵将合金中的气体抽出。
3. 除渣除渣是A356铝合金精炼的另一重要步骤。
在熔化和除气过程中,会生成一些浮渣和夹杂物。
这些浮渣和夹杂物会降低合金的机械性能和抗腐蚀性能。
因此,需要通过除渣工艺将这些杂质去除。
常用的除渣方法有静置沉淀法、离心除渣法等。
三、A356铝合金的净化A356铝合金的净化主要包括固溶处理、晶粒细化及人工时效等步骤。
1. 固溶处理固溶处理是将合金加热到一定温度,使合金元素充分溶解在基体中,然后迅速冷却,使合金元素以过饱和固溶体的形式存在于基体中。
这一过程可以消除合金中的偏析、成分不均等问题,提高合金的性能。
2. 晶粒细化晶粒细化是通过添加晶粒细化剂来改善合金的晶粒结构。
晶粒细化可以显著提高合金的机械性能和抗腐蚀性能。
常用的晶粒细化剂有钛、硼等元素。
《2024年汽车轮毂用A356铝合金的精炼及净化》范文

《汽车轮毂用A356铝合金的精炼及净化》篇一一、引言随着汽车工业的飞速发展,对汽车零部件的性能和轻量化要求越来越高。
其中,汽车轮毂作为承载整车重量和传输动力的重要部件,其材料的选择至关重要。
A356铝合金以其优异的铸造性能、力学性能以及良好的可加工性成为汽车轮毂的首选材料。
然而,其在使用前需要进行严格的精炼及净化处理,以保证其性能的稳定性和可靠性。
本文将详细探讨汽车轮毂用A356铝合金的精炼及净化工艺。
二、A356铝合金的成分及特性A356铝合金是一种常用的铸造铝合金,具有优良的铸造性能、良好的加工性能和较高的强度。
其主要成分包括铝、硅、铜等元素。
其中,硅元素可以提高合金的流动性,有利于铸造;铜元素可以提高合金的强度和硬度。
此外,A356铝合金还具有良好的耐腐蚀性和可回收性,符合环保要求。
三、精炼工艺A356铝合金的精炼工艺主要包括熔化、除气、除渣等步骤。
首先,将原材料按照一定比例加入炉中熔化。
在熔化过程中,需要严格控制温度和时间,以防止合金元素的氧化和烧损。
其次,通过除气工艺去除熔体中的气体杂质。
常用的除气方法包括气体喷吹法、真空除气法等,这些方法可以有效地去除熔体中的氢气和氧化物。
最后,通过除渣工艺去除熔体中的夹杂物和浮渣。
除渣方法包括机械除渣和化学除渣等,这些方法可以有效地去除熔体中的夹杂物和浮渣,提高合金的纯净度。
四、净化工艺A356铝合金的净化工艺主要包括精炼剂添加和炉内精炼两步。
首先,在精炼过程中加入适量的精炼剂,如氯化物等,这些精炼剂可以与熔体中的杂质元素发生化学反应,生成易于浮出熔体的化合物,从而达到净化合金的目的。
其次,在炉内进行精炼处理,使合金在高温下充分熔解和均匀混合,进一步去除合金中的杂质元素。
在净化过程中,还需要对合金进行充分的搅拌和静置处理,以使杂质元素充分上浮并去除。
五、结论通过对A356铝合金进行严格的精炼及净化处理,可以有效地去除合金中的杂质元素和气体杂质,提高合金的纯净度和性能稳定性。
- 1、下载文档前请自行甄别文档内容的完整性,平台不提供额外的编辑、内容补充、找答案等附加服务。
- 2、"仅部分预览"的文档,不可在线预览部分如存在完整性等问题,可反馈申请退款(可完整预览的文档不适用该条件!)。
- 3、如文档侵犯您的权益,请联系客服反馈,我们会尽快为您处理(人工客服工作时间:9:00-18:30)。
铸铝合金车轮制造技术第一章 A356 合金的熔炼(内 部 资 料)XX 铝 轮 毂 有 限 公 司目 录第 1 章 A356 合金的熔炼……………………………………………………………… 11 1.1 熔炼用的原材料………………………………………………………………… 111.1.1 A356 合金锭和各合金元素的作用………………………………………… 111.1.2 回炉料的分级和回用……………………………………………………… 111.1.3 精炼剂……………………………………………………………………… 121.1.4 清渣剂……………………………………………………………………… 131.1.5 合金细化用的中间合金…………………………………………………… 13 1.2 A356 合金熔炼设备……………………………………………………………… 131.2.1 铝合金快速集中熔化炉及投料机………………………………………… 131.2.2 2.1t/h铝锭、铝屑兼用熔化保持炉………………………………………… 141.熔化炉设备主要构成………………………………………………………… 142.2.1t/h铝锭、铝屑兼用熔化炉正面配置图…………………………………… 153.铝锭、铝屑熔化炉设备流程图……………………………………………… 154.铝屑熔化炉熔化示意图……………………………………………………… 165.主要技术指标和操作要点…………………………………………………… 171.2.3 中间包及中间包预热装置………………………………………………… 181.2.4 熔炼用的工具……………………………………………………………… 191.浇包………………………………………………………………………… 192.撇渣勺………………………………………………………………………… 193.钟形罩………………………………………………………………………… 194.压罩………………………………………………………………………… 1101.2.5 石墨转子除气机…………………………………………………………… 1101.石墨转子使用寿命…………………………………………………………… 1112.石墨转子尺寸………………………………………………………………… 111 1.3 A356 合金熔炼工艺……………………………………………………………… 1111.3.1 熔炼温度和时间…………………………………………………………… 1111.3.2 熔炼过程中的吸气………………………………………………………… 1121.3.3 熔炼过程中的氧化………………………………………………………… 1121.3.4 熔炼过程中的精炼(炉内精炼)………………………………………… 113 1.3.5 熔炼过程中的清渣………………………………………………………… 114 1.3.6 熔炼过程中的合金细化…………………………………………………… 114 1.3.7 熔炼中的合金变质………………………………………………………… 114 1.3.8 A356 合金的炉外精炼……………………………………………………… 115 1.3.9 A356 合金典型熔炼工艺…………………………………………………… 1161.熔炼前的准备………………………………………………………………… 1162.配料准备……………………………………………………………………… 1163.装料次序……………………………………………………………………… 1164.熔化和精炼…………………………………………………………………… 116 1.4 A356 合金熔炼铝液质量………………………………………………………… 117 1.4.1 什么铝液为合格的铝液…………………………………………………… 117 1.4.2 铝液中氢含量与铸件的针孔……………………………………………… 117 1.4.3 铝液中夹杂物含量与铸件的渣孔………………………………………… 118 1.4.4 A356 合金铝液的流动性…………………………………………………… 119 1.4.5 A356 合金铝液凝固时的收缩性…………………………………………… 119 1.5 熔炼工序设备…………………………………………………………………… 119 1.5.1 快速集中熔化炉………………………………………………………………1191.设备值点检…………………………………………………………………… 1192.泄漏试验……………………………………………………………………… 1203.安全动作确认………………………………………………………………… 120 1.5.2 保温炉………………………………………………………………………121 1.5.3 除气机……………………………………………………………………… 1211.传动机构……………………………………………………………………… 1212.升降机构……………………………………………………………………… 121第 1 章 A356合金的熔炼1.1 熔炼用的原材料1.1.1 A356合金锭和各合金元素的作用生产铝合金车轮各工厂采购进来的A356合金锭称作 A356.2,熔炼过程中的合金称 A356.1,产品的合金称 A356.0。
三者成分差别在表1—1中列出。
表1—1 A356系合金化学成份化学成分% 杂质元素%不同阶段的牌 号名称 A356Si Mg Ti ※Sr Fe Cu Zn Mn 每种 总和采购铝锭 A356.2 6.57.50.300.450.080.20≤0.12≤0.05≤0.05≤0.05≤0.05≤0.15熔炼规定 A356.1 6.57.50.300.450.080.200.020.025 ≤0.15≤0.10≤0.10≤0.10≤0.05≤0.15成品标准 A356.0 6.57.50.250.450.080.200.0080.018≤0.18≤0.10≤0.10≤0.10≤0.05≤0.15※ 添加微量元素 Sr 可以改变针状 Si 的形态并细化晶粒的长期效果,从而改善合金机械性能,但由 于它具有吸湿性,所以特殊情况下也有不用 Sr,而加入锑(Sb)的,其 A356.1 的加入量为 0.100.20; A356.0 的加入量为0.080.18。
A356合金中含硅量为6.5~7.5%,硅可以使合金流动性增加,铸造性能好,减少铸造缺陷。
另外硅还可以与 Mg 形成 Mg2Si, Mg2Si 是 A356 合金的强化相。
成品中含 Mg 为0.25~0.45%,其中 0.20%左右的 Mg 溶解在α-Al 中,其余的 Mg 生成 Mg2Si,在热处理过程中起固溶强化和时效硬化作用。
合金中含Ti为0.08~0.20%,Ti在合金中生成TiAl3,TiAl3为异质晶核,可细化α(Al),使合金得到细化,这种细化称合金基础细化作用。
Fe含量一般规定≤0.20%,通常工厂控制≤0.18%,Fe在这个范围内主要生成Fe2Si2Al9,在金相组织中为针状,具有脆性,热处理改变不了,使力学性能和抗蚀性变坏。
1.1.2 回炉料的分级和回用在生产铝合金车轮过程中,有铸造废轮、电镀废轮、涂装废轮、飞边、浇口、回舀 铝液铸锭、铝屑复化锭、浇口复化锭、渣灰分离出来的合金锭、跑铝块等产生,它们可 作为回炉料使用。
一级回炉料:铸造废轮、回舀铝液铸锭;二级回炉料:退镀废轮、飞边、跑铝块、复化锭;三级回炉料:涂装废轮、渣灰分离出来的合金锭、浇口;四级回炉料:粘有油污和水的各种回炉料。
一、二、三级回炉料,可根据不同炉型,按一定的比例回炉使用,四级回炉料不能 直接回用。
粘有油污的回炉料,制成复化锭再使用,含有水的回炉料,要烘烤干净才能 回用。
不同类型的炉,用回炉料的比例也不同。
快速熔化炉和中频感应炉所用的回炉料 要小于50%,其它一些反射炉和电阻炉可小于 70%。
生产实践证明,A356合金有一定的遗传性。
在熔炼过程中有一定比例的回炉料,对 材料的综合机械性能有利。
100%使用从未采用过的新 A356 铝锭,其机械性能不如含有 一定比例的回炉料好。
但是,回炉料回用比例不能太高。
如果太高,会使铝锭含渣量和 含气量增高,材料机械性下降,影响车轮整体使用性能。
1.1.3 精炼剂A356 合金在熔炼过程中,是不断产生夹杂物和含气量的过程,也是不断除渣和除 气的过程。
对铝液进行精炼过程,就是除渣和除气过程。
在精炼时,要用精炼剂,精炼 剂应满足以下条件:1. 精炼剂中所含成分的化合物不应与A356合金中的元素起反应,且不溶解在铝液 中;2. 精炼剂的比重要轻于铝液的比重;3. 精炼剂的熔点要低于A356合金的熔炼温度;4. 精炼剂中的化合物对各种氧化物夹杂有强烈吸附作用,或起化学反应,吃掉氧化 物中的氧;5. 精炼剂在铝液中溶化后,粘度要小,有一定造渣作用;6. 对环境无公害。
铸铝合金的精炼剂其主要成分有:NaCl、KCl 、Na2SiF6、K2SiF6、Na3AlF6(K3AlF6)、 Na2CO3、C2Cl6 等。
NaCl 和 KCl 按一定比例可配出熔点低的精炼剂;Na2SiF6 可吃掉一 部分γ—Al2O3,并起渣液分离作用;Na3AlF6 有强烈吸附氧化物的作用,Na2CO3 起精炼沸腾作用;C2Cl6 含气量比较少,是非常理想的除渣、除气的化合物,通过一定比例 配合,可制作比较理想的精炼剂。
缺点是精炼产生的气体有毒,对环保不利。
1.1.4 清渣剂清渣剂又称打渣剂或除渣剂。
清渣剂主要是除掉熔炼过程中铝液表面上的渣,使渣 液分离,将铝液表面的渣扒出炉外。