C=0抽样方案
GB2828抽样标准与C=0抽样方案-2022年学习资料

概论-。检验:为确定产品或服务的各特征是否合格,测定、-检查、试验或度量产品或服务的一种或多种特征,-并且 规定要求进行比较的活动。-o检验方式:1.全数检验-2.统计抽样检验-3.其他的抽样检验-4.免检
口全检-适用范围:1.批量太小,失去抽检意义-2检验手续简单,不至于浪费大量人力、经费-3.不允许不良品存 ,该不良品对使用有致命影响-4.工程能力不足,无法保证品质-5.为了解该批的实际质量状况-。免检:-适用范 :1.生产过程稳定,对后续生产无影响-2.国家批准的免检产品及产品质量认证产品!-的无试验买入-3.长期检 证明质量优良,双认可生产方的检验结果
o零缺陷管理C=0抽样方案-质ห้องสมุดไป่ตู้大师菲利普克劳士比-建议不要再使用AQL,而开始专注“零缺陷”。这就意味着 完-全符合要求,而不是浪费时间去计算我们到底偏离了多远。因-为问题出在我们自己身上,而不在几率身上。-中国 缺陷之父:杨钢-核心思想:第一次就把事情做对
抽样检验流程-d<Ac->-批产品合格-随机抽取-全检-样本-不合格品-N-n-2-批产品不合格-dzRe 0-判断准则Ac,Re
TABLE I-Sample Size Code Letters [ANSI/ASOC Z1.4]-Spe ial Inspection Levels-General Inspection Levels-Lot o Batch Size-s-1-S-2-S-3-S-4-Ⅱ-to-8-9-15-16-25-D-26-50 51-90-F-91-150-151-280-H-281-500-丁-501-1200-J-K-1201200-3201-10.000-M-10.001-35.000-35.001-150.000-P-150. 01-500.000-Q-500.001-and-over-R
【干货】零缺陷(C=0)抽样方案
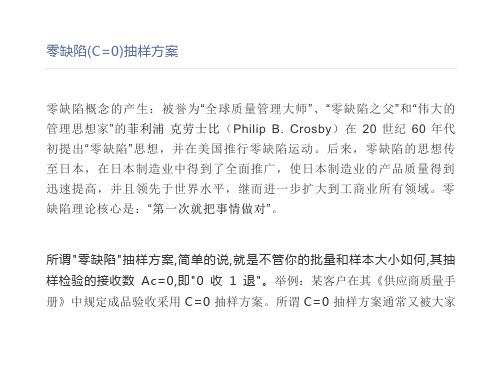
零缺陷(C=0)抽样方案零缺陷概念的产生:被誉为“全球质量管理大师”、“零缺陷之父”和“伟大的管理思想家”的菲利浦·克劳士比(Philip B. Crosby)在20世纪60年代初提出“零缺陷”思想,并在美国推行零缺陷运动。
后来,零缺陷的思想传至日本,在日本制造业中得到了全面推广,使日本制造业的产品质量得到迅速提高,并且领先于世界水平,继而进一步扩大到工商业所有领域。
零缺陷理论核心是:“第一次就把事情做对”。
所谓"零缺陷"抽样方案,简单的说,就是不管你的批量和样本大小如何,其抽样检验的接收数Ac=0,即"0收1退"。
举例:某客户在其《供应商质量手册》中规定成品验收采用C=0抽样方案。
所谓C=0抽样方案通常又被大家称为零缺陷抽样方案,即只有抽样产品全部经检验全部合格,整批产品才能够被接收;而只要在验收过程中发现有一个不良品,整批产品将被判为不合格。
客户的这一要求在公司内部引起了一些同事的担心,认为这样的要求是不是过于严格了?公司根本做不到,甚至有同事认为客户这样的要求是“霸王”条款。
事实上,C=0 抽样方案目前在国内已经被广泛使用。
它和我们中国应用较多的 GB/T2828.1-2012抽样方案一样,就方案本身来讲不存在严格不严格的概念。
在应用 GB/T2828.1-2012时,一个抽样计划严格与否取决于我们对于 AQL 的选择。
AQL 值小,抽样计划就严格;AQL 值大,抽样计划就宽松。
同样的,C=0 抽样方案也规定了一系列与GB/T2828.1-2012相同的AQL值,选择哪个AQL值完全在于我们自己的选择以及与客户的协商来决定。
所以有关“C=0抽样方案过于严格”的论断完全不成立,出现这种认识仅仅是因为大家不了解C=0 抽样方案。
需要说明的是,该客户的《供应商质量手册》是根据 IATF16949:2016建立的,而IATF16949:2016标准条款8.6.6中明确要求接收水平必须是零缺陷。
C=0抽样方案

和抽样有关的几个分布
• 二项分布:二项分布是n个独立的是/非试验中成功的次数 的概率分布,其中每次试验的成功概率一样。(二项分布 的计算方式如何推导?)
• 超几何分布:由有限个物件中抽出n个物件,成功抽出指 定种类的物件的次数(不归还)。前述案例中已给出超几 何分布计算的案例。
• 泊松分布:当二项分布的n很大而p很小时,泊松分布可作
为二项分布的近似。事实上,泊松分布是由二项分布导出
的。
– 概率密度 – 累积概率
f
(
x
)
(
np
)
x
e
np
x!
r
F (x) f (x)
x0
OC曲线
• 案例:有N=10000个产品, 不良率为P,我们抽取n=100 个,1收2退。分别计算 P=1%,2%,3%时的接收概率 Pa
– 根据泊松分布,Pa分别为:
13
3201-10000 1250 800 500 315 200 192 189 116 86 68 50 38 29 22 15
10001-35000 1250 800 500 315 300 294 189 135 108 77 60 46 35 29 15
35001-150000 1250 800 500 490 476 294 218 170 123 96 74 56 40 29 15
*
*
* 315 200 125 80 50 48 47 29 21 16 11
9
501-1200
* 800 500 315 200 125 80 75 73 47 34 27 19 15 11
1201-3200
1250 800 500 315 200 125 120 116 73
C=0抽样方案

1﹑目的
明确品管部各单位的抽样标准,并提供文件支持。
2﹑范围
适用于本公司所生产的汽车工业链上的相关产品。
适用于进料、制程、成品检验时,计数型数值允收水准的确定。
3﹑权责
3.1品管经理:确定各阶段的AQL值。
3.2品检人员:C=0 抽样标准的实施。
4﹑定义
4.1 C=0抽样计划:零缺陷抽样计划,即0收1退,Acc=0,Rej=1。
5﹑作业内容
5.1使用方法
5.1.1确定检验项目、判定标准。
5.1.1.1抽检数量:样品全检(性能除外)。
量产抽检。
5.1.1.2检验项目:尺寸、外观、性能、装配等。
根据客户要求及产品特性确定。
5.1.2确定允收水准AQL值。
外观:AQL:0.65 Ac=0 Re=1
尺寸:AQL:6.5 Ac=0 Re=1
性能:AQL:6.5 Ac=0 Re=1
5.1.3根据实际批量及规定的AQL值从“附件一”中查出应抽取的样本数量。
5.1.4从批量中随机抽取规定的样本数。
5.1.5检验
根据Acc=0 Rej=1判定。
5.2如遇特殊情况,品管部可根据客户要求更改允收品质水准AQL,只需书面通知相关部门,而
无需更改本规定及相关检验标准。
6﹑参考文件
无
7﹑使用表单
无
8﹑附件
8.1 C=0抽样计划表
附件一:
C=0抽样计划表
注:* 表示整批须百分之百检验。
C=0抽样方案

内容摘要:本文经由过程介绍统计抽样磨练的成长简史和“零缺点”(C=0)抽样筹划,进一步剖析了履行“零缺点”(C =0)抽样筹划的对公司的诸多益处.0.媒介:客户在其《供给商质量手册》中划定成品验收采取C=0抽样筹划.所谓C=0抽样筹划平日又被大家称为零缺点抽样筹划,即只有抽样产品全体经磨练全体及格,整批产品才干够被吸收;而只要在验收进程中发明有一个不良品,整批产品将被判为不及格.客户的这一请求在公司内部引起了一些同事的放心,以为如许的请求是不是过于严厉了?我们公司基本做不到,甚至有同事以为客户如许的请求是“霸王”条目.事实上,C=0抽样筹划今朝在国内已经被普遍运用.它和国内运用较多的GB2828抽样筹划一样,就筹划本身来讲不消失严厉不严厉的概念.我们知道,在运用GB2828时,一个抽样筹划严厉与否取决于我们对于AQL的选择.AQL值小,抽样筹划就严厉;AQL值大,抽样筹划就宽松.同样的,C=0抽样筹划也划定了一系列与GB2828雷同的AQL值,选择哪个AQL值完整在于我们本身的选择以及与客户的协商来决议.所以有关“C=0抽样筹划过于严厉”的论断完整不成立,消失这种熟悉仅仅是因为大家不懂得C=0抽样筹划.须要解释的是,该客户的《供给商质量手册》是依据ISO/TS16949(即GB/T18305)建立的,而ISO/TS16949在条目中明白请求吸收程度必须是零缺点.(吸收准则:组织应划定吸收准则,请求时,由顾客同意.对于计数型数据抽样,吸收程度应是零缺点.)所以,客户的请求是依据的,不消失任何“霸王”请求.1.抽样磨练简介抽样磨练又称为统计抽检磨练,是指从交验的一批产品中,随机抽取若干单位产品构成样本进行磨练,经由过程对样本的磨练成果对整批产品做出质量剖断的进程.我们知道,磨练是不产生价值的工作,是以若何更经济.快捷的进行磨练就直接关系到临盆的成本和效力.统计抽样磨练理论是美国贝尔试验室的道奇和罗米格于1929年创立的,它和1924年休哈特提出的统计进程掌握(掌握图)一路被视为质量治理从质量磨练阶段进入统计质量掌握阶段的两个标记性成果.统计抽样磨练理论的消失转变了以往那种依附大批量磨练来包管产品德量的工作方法.从1950年美军宣布MIL-STD-105抽样尺度起,统计抽样磨练在全世界慢慢推广开来.MIL-STD-105的进级.延长版本被国际尺度化组织以及很多国度的国度尺度采取.美军MIL-STD-105尺度共阅历A~E五个版本,该尺度今朝已经被美军废除.2.两种“零缺点”抽样筹划1965年,美国的一位大学传授尼古拉斯•斯托格力亚揭橥C=0抽样筹划,几经改版,今朝最新的版本为第四版.C=0抽样筹划是依据MIL-STD105 修正而成,吸收准则限制为“0收1退”,因而又被人们称为“零缺点”抽样筹划.固然到今朝为止,C=0抽样筹划还不是国际以及任何国度的国度尺度,但因为“零缺点”的质量理念已经深刻人心,在加上ISO/TS16949:2002中有明白的条则请求,在企业界已经得到了普遍的运用.1994年,美国三大汽车厂商(通用.福特.克来斯勒)宣布了QS9000质量体系尺度,QS9000中的条目就明白请求:吸收准则必须是零缺点.QS9000的这一请求,促进了C=0抽样筹划的被敏捷推广运用.在QS9000被国际尺度化组织采取为国际尺度ISO/TS16949之后,使得C=0抽样筹划的运用又进一步扩展.2005年,为了表扬尼古拉斯•斯托格力亚传授创制C=0抽样筹划的凸起进献,美国质量学会把当年的谢宁奖章颁给已经退休的尼古拉斯•斯托格力亚传授.美国质量学会在表扬词中说:他最巨大的进献是开辟了一套实用.便于运用.经济的零缺点的数字抽样筹划.他的办法在军事和商用上,节俭了数以百万计的美元.因为他的办法被证实实用.简略单纯并且经济,因而被普遍接收.1996年,美军推出新版的抽样尺度MIL-STD-1916.和C=0抽样筹划一样,MIL-STD-1916也限制它的吸收准则为“0收1退”,所以MIL-STD-1916也可以称为零缺点抽样筹划.MIL-STD-1916不再像MIL-STD-105那样强调抽样的技巧,而是转为请求供给商建立预防性的质量体系和有效的进程质量掌握体系.MIL-STD-1916强调以事先的预防代替过后的磨练.因为ISO/TS16949只请求了“吸收程度应是零缺点”,并没有明白划定应采取C=0抽样筹划照样MIL-STD-1916.对于企业来说,运用哪一种“零缺点”抽样筹划可以联合企业自身以及客户的具体请求来决议.3.国内抽样尺度的运用情形1981年我国开端参照ISO2859(即MIL-STD-105D)制定中国的统计抽样尺度GB2828.GB2828经由1987年和2003年两次修订,今朝在国内运用最为普遍.固然MIL-STD-105在美国已经被废除,但是该尺度今朝在我国仍有很多企业在运用,甚至还有少数企业在运用早期的版本MIL-STD-105D.今朝,C=0抽样筹划已经在我国浩瀚的汽车行业企业和其它自愿采取ISO/TS16949尺度的企业中被普遍的运用.4.“零缺点”的概念“零缺点”(C=0)抽样筹划是依据MIL-STD-105修正而来,有关统计抽样的概念与GB2828出自同源,GB2828相干的术语界说在“零缺点”(C=0)抽样筹划都可以运用.为了凸起“零缺点”这一重要概念,“零缺点”(C=0)抽样筹划把GB2828中“不及格”.“不及格品”两个术语修正为“缺点”.“缺点品”.因为“零缺点”(C=0)抽样筹划的剖断准则限制为“0收1退”,只要消失一个缺点品,不管批量大小.样本若干,都可以判整批不及格.凸起“零缺点”不雅念,可以促进大家质量意识晋升.“零缺点”(C=0)抽样筹划的别的斟酌是:假如你的质量相当差,大于0的允收数并没有多大的帮忙;当你的抽样筹划允收数大于零,你在授权你的磨练人员接收一些可能没有效的产品;零缺点强迫对任何不及格采纳措施;假如你正在尽力迈向零缺点,那你怎能许可你的抽样筹划许可出缺点数呢?我们看到很多公司经常运用“零缺点”的概念来进行质量宣扬,但“零缺点”的精力要怎么去贯彻落实呢?假如我们一方面宣扬着“零缺点”,另一方面仍然在运用GB2828的抽样筹划来吸收不良品,那本身就是一个自相抵触的笑话.5.“零缺点”(C=0)抽样筹划的轻便性与GB2828比拟“零缺点”(C=0)抽样筹划不消失加严.放宽与正常磨练之间的转移划定,也没有二次及多次抽样筹划.“零缺点”(C=0)抽样筹划仅运用一张主抽样表,相对GB2828的几十张抽样表大大简化,即便利进修,也便于运用治理.同时,“零缺点”(C=0)抽样筹划不但实用于逐批磨练,也实用于孤立批次磨练.6.履行“零缺点”(C=0)抽样筹划的益处有助于形成严谨务实的工作风格固然三星电气品德治理部分在现行的成品磨练尺度中,把产品功效参数类磨练项目标抽样筹划划定为不及格品GB2828ⅡAQL=0.65%;而外不雅类磨练项目则划定为不及格品GB2828ⅡAQL=1.0% .但是否严厉按抽样筹划进行了抽检照样一个问题.磨练员们在被问题按何种尺度磨练产品时,经常会答复:按GB2828磨练.但是我们是按GB2828的哪一级磨练水准?各类质量特征分离拔取何种AQL值呢?大家答不上来.事实上,一批产品在抽检时应当抽取若干样本?以及若何剖断及格与否?往往都是主管人员凭感到.凭小我经验的指导.如许做的问题是:抽检工作缺乏合理性,抽检剖断缺乏公正性,对出厂产品的质量风险把控也不具有科学性.不管我们选用GB2828或是“零缺点”(C=0)抽样筹划,尺度一旦确立,就必定要包管按尺度进行磨练.必须转变那种靠人的主不雅经验剖断的不良习惯,促使工作严谨性.而因为“零缺点”(C=0)抽样筹划的易学易用性,更有助于帮忙我们形成严谨.务实的工作风格.选用“零缺点”(C=0)抽样筹划更经济在拔取雷同AQL值的情形下,“零缺点”(C=0)抽样筹划的抽检风险概率与GB2828相似,同时抽检量大大削减.与GB2828一样,运用“零缺点”(C=0)抽样筹划时同样须要为不合类此外质量特征划定不合的AQL(吸收质量限).“零缺点”(C=0)抽样筹划实用于:期望是临盆的产品完整达到规范请求.对一些非症结的特征愿望用比较少的磨练.比方三星电气公司的电能表产品,对于表计功效.机能等重要质量特征是客户重点存眷的,并且也必须知足“零缺点”;而对于外不雅等次要质量特征,客户平日其实不会像看待工艺品一样深究,就不须要保持大量的抽检,那样显著是不经济的.将帮忙我们建立“零缺点”的质量意识并晋升产品德量程度因为“零缺点”(C=0)抽样筹划的剖断准则限制为“0收1退”,只要消失一个不良品,就可以判整批不及格,就必须采纳全检返措施.在履行的初期无疑将会加大效力和成本的压力,从而促使全部公司真正建立“零缺点”的不雅念,不容忍一个不良品.当我们每小我都形成了不克不及够容忍不良品和不克不及够容忍工作错误之后,信任我们的产品德量程度也必定会响应的晋升.有助于晋升客户信念,并帮忙拓展海外市场.今朝,“零缺点”的质量不雅念已经风靡全球,假如期望打入欧美日等成熟的高端市场,我们必须运用顾客可以或许听懂的“零缺点”质量说话来跟顾客接轨.“零缺点”(C=0)抽样筹划契合公司的经营理念公司建议准确.高效.务实.简略的工作文化,而“零缺点”(C=0)抽样筹划正好相符这四个词的请求.总之,“零缺点”是今朝企业质量治理的潮流所向,我们应当把本次客户的请求转化为公司内部改良的一次机遇,积极的迎难而上:履行C=0抽样筹划,建立零缺点意识!。
零缺陷(C=0)抽样方案

零缺陷概念的产生:被誉为“全球质量管理大师”、“零缺陷之父”和“伟大的管理思想家”的菲利浦·克劳士比(Philip B. Crosby)在20世纪60年代初提出“零缺陷”思想,并在美国推行零缺陷运动。
后来,零缺陷的思想传至日本,在日本制造业中得到了全面推广,使日本制造业的产品质量得到迅速提高,并且领先于世界水平,继而进一步扩大到工商业所有领域。
零缺陷理论核心是:“第一次就把事情做对”。
所谓"零缺陷"抽样方案,简单的说,就是不管你的批量和样本大小如何,其抽样检验的接收数Ac=0,即"0收1退"。
举例:某客户在其《供应商质量手册》中规定成品验收采用 C=0 抽样方案。
所谓 C=0 抽样方案通常又被大家称为零缺陷抽样方案,即只有抽样产品全部经检验全部合格,整批产品才能够被接收;而只要在验收过程中发现有一个不良品,整批产品将被判为不合格。
客户的这一要求在公司内部引起了一些同事的担心,认为这样的要求是不是过于严格了?公司根本做不到,甚至有同事认为客户这样的要求是“霸王”条款。
事实上,C=0 抽样方案目前在国内已经被广泛使用。
它和我们中国应用较多的GB/T2828.1-2012抽样方案一样,就方案本身来讲不存在严格不严格的概念。
在应用GB/T2828.1-2012时,一个抽样计划严格与否取决于我们对于 AQL 的选择。
AQL 值小,抽样计划就严格;AQL 值大,抽样计划就宽松。
同样的,C=0 抽样方案也规定了一系列与GB/T2828.1-2012 相同的 AQL值,选择哪个AQL 值完全在于我们自己的选择以及与客户的协商来决定。
所以有关“C=0 抽样方案过于严格”的论断完全不成立,出现这种认识仅仅是因为大家不了解C=0 抽样方案。
需要说明的是,该客户的《供应商质量手册》是根据IATF16949:2016 建立的,而IATF16949 :2016标准条款8.6.6中明确要求接收水平必须是零缺陷。
C=0-抽样方案介绍
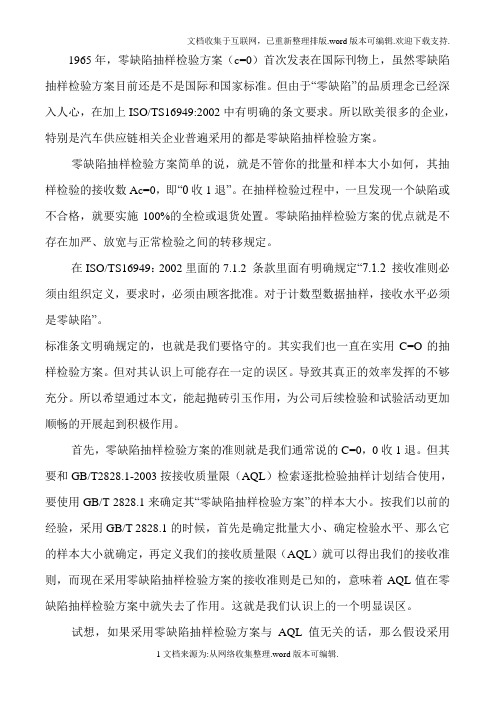
1965年,零缺陷抽样检验方案(c=0)首次发表在国际刊物上,虽然零缺陷抽样检验方案目前还是不是国际和国家标准。
但由于“零缺陷”的品质理念已经深入人心,在加上ISO/TS16949:2002中有明确的条文要求。
所以欧美很多的企业,特别是汽车供应链相关企业普遍采用的都是零缺陷抽样检验方案。
零缺陷抽样检验方案简单的说,就是不管你的批量和样本大小如何,其抽样检验的接收数Ac=0,即“0收1退”。
在抽样检验过程中,一旦发现一个缺陷或不合格,就要实施100%的全检或退货处置。
零缺陷抽样检验方案的优点就是不存在加严、放宽与正常检验之间的转移规定。
在ISO/TS16949:2002里面的7.1.2 条款里面有明确规定“7.1.2 接收准则必须由组织定义,要求时,必须由顾客批准。
对于计数型数据抽样,接收水平必须是零缺陷”。
标准条文明确规定的,也就是我们要恪守的。
其实我们也一直在实用C=O的抽样检验方案。
但对其认识上可能存在一定的误区。
导致其真正的效率发挥的不够充分。
所以希望通过本文,能起抛砖引玉作用,为公司后续检验和试验活动更加顺畅的开展起到积极作用。
首先,零缺陷抽样检验方案的准则就是我们通常说的C=0,0收1退。
但其要和GB/T2828.1-2003按接收质量限(AQL)检索逐批检验抽样计划结合使用,要使用GB/T 2828.1来确定其“零缺陷抽样检验方案”的样本大小。
按我们以前的经验,采用GB/T 2828.1的时候,首先是确定批量大小、确定检验水平、那么它的样本大小就确定,再定义我们的接收质量限(AQL)就可以得出我们的接收准则,而现在采用零缺陷抽样检验方案的接收准则是已知的,意味着AQL值在零缺陷抽样检验方案中就失去了作用。
这就是我们认识上的一个明显误区。
试想,如果采用零缺陷抽样检验方案与AQL值无关的话,那么假设采用GB/T2828.1里面的正常检验一次抽样方案II级检验水平的话,意味着样本量是统一的。
C=0-抽样方案介绍

C=0-抽样方案介绍1965年,零缺陷抽样检验方案(c=0)首次发表在国际刊物上,虽然零缺陷抽样检验方案目前还是不是国际和国家标准。
但由于“零缺陷”的品质理念已经深入人心,在加上ISO/TS16949:2002中有明确的条文要求。
所以欧美很多的企业,特别是汽车供应链相关企业普遍采用的都是零缺陷抽样检验方案。
零缺陷抽样检验方案简单的说,就是不管你的批量和样本大小如何,其抽样检验的接收数Ac=0,即“0收1退”。
在抽样检验过程中,一旦发现一个缺陷或不合格,就要实施100%的全检或退货处置。
零缺陷抽样检验方案的优点就是不存在加严、放宽与正常检验之间的转移规定。
在ISO/TS16949:2002里面的7.1.2条款里面有明确规定“7.1.2接收准则必须由组织定义,要求时,必须由顾客批准。
对于计数型数据抽样,接收水平必须是零缺陷”。
标准条文明确规定的,也就是我们要恪守的。
其实我们也一直在实用C=O的抽样检验方案。
但对其认识上可能存在一定的误区。
导致其真正的效率发挥的不够充分。
所以希望通过本文,能起抛砖引玉作用,为公司后续检验和试验活动更加顺畅的开展起到积极作用。
首先,零缺陷抽样检验方案的准则就是我们通常说的C=0,0收1退。
但其要和GB/T2828.1-2003按接收质量限(AQL)检索逐批检验抽样计划结合使用,要使用GB/T2828.1来确定其“零缺陷抽样检验方案”的样本大小。
按我们以前的经验,采用GB/T2828.1的时候,首先是确定批量大小、确定检验水平、那么它的样本大小就确定,再定义我们的接收质量限(AQL)就可以得出我们的接收准则,而现在采用零缺陷抽样检验方案的接收准则是已知的,意味着AQL值在零缺陷抽样检验方案中就失去了作用。
这就是我们认识上的一个明显误区。
试想,如果采用零缺陷抽样检验方案与AQL值无关的话,那么假设采用GB/T2828.1里面的正常检验一次抽样方案II级检验水平的话,意味着样本量是统一的。