抽样风险及抽样方案
抽样方案有什么风险

抽样方案有什么风险引言在数据分析和研究中,抽样是一种常见的方法,用于从整个总体中选择一个相对较小的样本,以便进行研究和统计推断。
抽样方案的设计与执行对于研究结果的准确性和可靠性具有重要影响。
然而,抽样方案也存在一些潜在的风险,这些风险可能会对最终的研究结果产生不利影响。
本文将讨论抽样方案可能面临的一些风险,并提供相应的应对措施。
1. 抽样偏差风险抽样偏差风险是指从总体中选取样本时存在的系统性偏差。
这可能导致样本与总体不代表性、不均匀或偏向某一特定群体。
抽样偏差风险可能会对研究结果的推广性和泛化性产生负面影响。
应对措施: - 使用随机抽样方法,确保每个个体有相等的机会被选入样本。
-确保抽样过程的透明性和可重复性,避免主观因素的干扰。
2. 抽样误差风险抽样误差风险是指样本统计量与总体参数之间的差异。
样本统计量是对总体参数的估计,由于抽样的随机性,样本统计量与总体参数之间存在随机误差。
抽样误差风险可能导致统计结果的不准确性和误导性。
应对措施: - 增加样本容量,提高估计的准确性。
- 使用抽样分层,确保每个层内的样本足够代表该层的特征。
- 针对特定问题使用合适的抽样方法,如分层抽样、整群抽样等。
3. 数据收集风险数据收集风险是指在抽样过程中可能发生的数据错误或缺失。
这可能会导致样本数据不完整、不准确或具有偏见。
数据收集风险可能会影响研究结果的可信度和可靠性。
应对措施: - 提供明确的数据收集指导,并培训调查员以确保数据的准确性和一致性。
- 验证和核实收集的数据,识别和纠正潜在的错误和缺失。
- 使用多个数据收集源,以减少单一数据收集源的可靠性问题。
4. 样本代表性风险样本代表性风险是指样本与总体特征之间的差异。
如果样本不代表总体的重要特征,那么从样本中得出的结论可能无法泛化到整个总体。
样本代表性风险可能缩小研究的适用范围和推广性。
应对措施: - 在样本选择阶段考虑总体的特征,采用适当的抽样方法和样本大小。
审计抽样工作方案

审计抽样工作方案一、背景介绍在进行审计工作时,抽样是一种常用的方法。
通过抽取合适的样本,可以从大量的数据中获取足够的信息,以便评估整体的情况。
本文将介绍审计抽样的目的、原则、方法和步骤,以及抽样结果的应用。
二、目的审计抽样的目的在于通过对样本的审计程序,对于被审计单位的财务信息进行测试,以便评估其真实性、准确性和完整性。
通过抽样可以得出对整体的推断结果,从而判断被审计单位是否存在重大的错误或欺诈。
三、抽样原则1. 随机性原则:抽样必须具有随机性,确保每个单位或每个项目都有平等的机会被选中,以避免产生选择性偏差。
2. 代表性原则:抽样样本必须能够代表被审计单位整体的情况,样本的选择要与被抽样的总体具有相似的特征。
3. 效率性原则:抽样方法必须是高效的,既能减少审计工作的工作量,又能够得出具有充分可信度的结论。
4. 可靠性原则:抽样样本必须能够提供可靠的信息,能够准确反映被审计单位财务信息的真实情况,从而给出准确的审计意见。
四、抽样方法根据被抽样总体的特征和审计目的的不同,可以采用以下几种常用的抽样方法:1. 简单随机抽样:从总体中随机抽取样本,每个单位被选中的概率相等。
2. 系统抽样:按照一定的规则在总体中选择单位,例如每隔若干个单位选择一个样本。
3. 分层抽样:将总体分成若干个层次,从每个层次中分别抽取样本,以保证不同层次的单位都能得到充分代表。
4. 整群抽样:将总体按照一定的规则划分成若干个群组,然后随机抽取其中的若干个群组进行审计。
5. 配额抽样:根据被审计单位的特征,设置不同的配额,从符合配额要求的单位中抽取样本。
五、抽样步骤1. 确定抽样目的和抽样方法:根据审计目的和被审计单位的情况,明确抽样目的和采用的抽样方法。
2. 制定抽样方案:确定抽样样本的大小和抽样比例,制定抽样方案,包括样本的选择方式和抽样程序的具体步骤。
3. 进行抽样测试:按照抽样方案进行抽样测试,执行审计程序,并记录样本的审计结果。
食品抽样环节中的常见问题及解决方案探讨

现阶段,我国仍将食品安全抽样工作列为食品安全监管中最有效的手段之一。
由此可见,抽样在安全监管环节中是重中之重。
由于抽样属于事后监管的范畴,因此可以有效防止或减少不合格、不安全的食品流入市场,造成食品安全隐患。
但在抽样过程中,也会存在一些常见问题影响抽样结果,导致抽样工作难以进行[1]。
1 食品抽样工作中常见问题1.1 部分抽样任务反复出现我国各级政府监管部门每年都会按计划制定食品安全抽检工作,同时会分配抽检工作。
如果食品安全抽样工作机制有所欠缺,会导致抽样工作计划和任务分配的整体协调性出现问题,抽样工作难免重复。
但由于采样量大而被抽样的单位数量有限,导致局部采样任务与国家、省级采样任务重叠,出现重复采样或无法抽到样品的现象[2]。
1.2 部分抽样任务难度系数较大不同地区有不同的风俗习惯和饮食习惯,人口众多,食品种类繁杂,导致采样难度系数较大。
在餐饮行业中,由于对当地的饮食习惯不了解,贸然的销售当地不畅销的食品,引发食品堆积,破坏原有的食品基础类型,引起抽样数量不能满足抽样任务,由此很难完成抽样任务。
1.3 抽样人员缺乏专业知识进行抽样的人员不仅要了解食品安全的法律、法规及相关工作程序监督抽样,而且要了解被抽检物的食品安全标准与属性(包括检验项目),从而确保样本的有效性,可用于检验。
比如,在生产和餐饮过程中采样,依据食品分类的要求,米线的采样主体应该是以大米为主要原料的食品,而甘薯粉和豆制品则不属于大米的分类范畴。
此外,不熟悉食品安全标准,使样品数量不能满足检验要求,如果重新取样,就会出现同一批样品已经售完的情况[3-4]。
1.4 外购原料再加工后样品难以溯源在食品抽样工作中,会出现原料难以溯源的问题。
例如被抽样单位出现外购原料的情况,将外购原料加工处理后进行出售。
抽样样品可以追溯到原材料。
但在食品饮料取样过程中,食品生产经营者若将购买的原料进行再次加工,样品出现不合格情况,就会无法确认样品是在生产过程中出现问题,还是在样品再加工处理过程中出现的问题。
抽检方案 风险控制

抽检方案风险控制引言抽检方案是企业质量管理体系中非常重要的一环,通过抽检方案可以对产品的质量进行实时监测和控制。
在抽检过程中,存在一定的风险,这些风险可能会影响到产品的质量以及企业的声誉。
因此,需要制定相应的风险控制策略,将风险降到最低,确保产品质量和企业利益的最大化。
抽检方案抽检方案是指根据一定的抽检规则和方法,从生产过程中随机选择样本进行检验,以评估产品的质量和合格率。
抽检方案的设计应综合考虑以下因素:1.检验标准:抽检方案应基于相应的检验标准,明确产品的质量要求。
2.检验方法:选择适宜的检验方法,确保能够准确评估产品的质量。
3.抽样规则:选择合适的抽样规则,例如随机抽样、系列抽样等,确保样本代表性。
4.抽样数量:确定抽样数量,保证统计意义和可靠性。
5.抽检频率:根据产品的生产情况和质量风险,确定抽检的频率和时机。
抽检方案的制定应参考相关的国家标准、行业标准以及企业内部的质量管理要求,确保抽检的合理性和有效性。
风险控制策略风险控制是抽检方案中的重要环节,有效的风险控制策略能够降低抽检过程中的风险,保护产品质量和企业利益。
1.风险评估:在制定抽检方案之前,需要进行风险评估,评估各种潜在的风险因素对产品质量的影响程度和可能性。
这样可以有针对性地制定风险控制策略,重点关注高风险的环节和问题。
2.供应链管理:供应链管理是风险控制的重要一环。
企业应与供应商建立长期稳定的合作关系,并对供应商进行评估和监管。
只有在保证供应商的质量可靠性的前提下,才能确保自身产品的质量。
3.内部质量管理:企业内部应建立健全的质量管理体系,包括质量控制标准、检验流程和质量记录等。
通过内部的质量管理,可以将产品的不良率降到最低,减少产品在抽检过程中出现的问题。
4.抽检过程的监控:对抽检过程进行实时监控是风险控制的重要手段。
通过使用现代化的检验设备和技术手段,可以提高抽检的准确性和效率。
同时,对抽检过程中出现的问题进行记录和分析,及时采取纠正措施。
抽样方案范文4篇
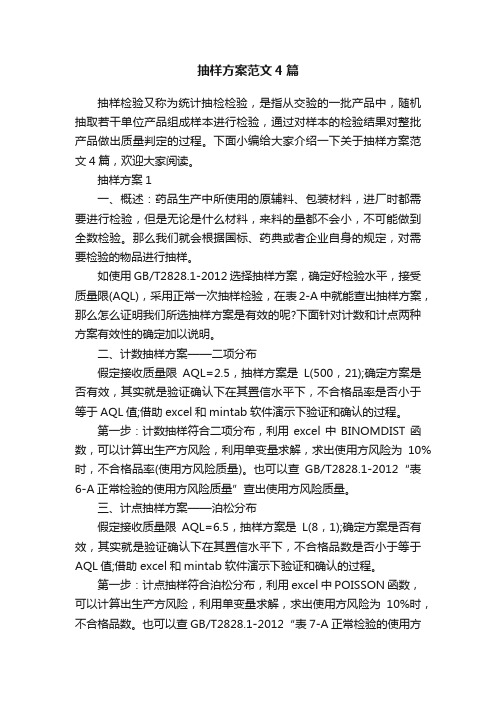
抽样方案范文4篇抽样检验又称为统计抽检检验,是指从交验的一批产品中,随机抽取若干单位产品组成样本进行检验,通过对样本的检验结果对整批产品做出质量判定的过程。
下面小编给大家介绍一下关于抽样方案范文4篇,欢迎大家阅读。
抽样方案1一、概述:药品生产中所使用的原辅料、包装材料,进厂时都需要进行检验,但是无论是什么材料,来料的量都不会小,不可能做到全数检验。
那么我们就会根据国标、药典或者企业自身的规定,对需要检验的物品进行抽样。
如使用GB/T2828.1-2012选择抽样方案,确定好检验水平,接受质量限(AQL),采用正常一次抽样检验,在表2-A中就能查出抽样方案,那么怎么证明我们所选抽样方案是有效的呢?下面针对计数和计点两种方案有效性的确定加以说明。
二、计数抽样方案——二项分布假定接收质量限AQL=2.5,抽样方案是L(500,21);确定方案是否有效,其实就是验证确认下在其置信水平下,不合格品率是否小于等于AQL值;借助excel和mintab软件演示下验证和确认的过程。
第一步:计数抽样符合二项分布,利用excel中BINOMDIST函数,可以计算出生产方风险,利用单变量求解,求出使用方风险为10%时,不合格品率(使用方风险质量)。
也可以查GB/T2828.1-2012“表6-A正常检验的使用方风险质量”查出使用方风险质量。
三、计点抽样方案——泊松分布假定接收质量限AQL=6.5,抽样方案是L(8,1);确定方案是否有效,其实就是验证确认下在其置信水平下,不合格品数是否小于等于AQL值;借助excel和mintab软件演示下验证和确认的过程。
第一步:计点抽样符合泊松分布,利用excel中POISSON函数,可以计算出生产方风险,利用单变量求解,求出使用方风险为10%时,不合格品数。
也可以查GB/T2828.1-2012“表7-A正常检验的使用方风险质量”查出使用方风险质量。
将出现数改为2,得出90.36%置信水平下不合格数下限是0.065029>0.065,不合格数大于方案设定值,因此按照方案应该拒收。
药品抽样实施方案

药品抽样实施方案为了保障药品质量和安全,确保市场上流通的药品符合相关标准,我国对药品进行抽样检验是非常重要的环节。
药品抽样实施方案是指根据国家相关法律法规和标准,对药品进行抽样检验的具体操作步骤和要求。
下面将介绍药品抽样实施方案的具体内容。
一、抽样对象药品抽样的对象主要包括生产企业、流通环节和医疗机构等单位的药品,主要针对国家药品监督管理部门确定的监测目标品种进行抽样检验。
二、抽样方式1. 随机抽样:根据一定的随机原则,从药品生产企业、流通环节和医疗机构等单位的药品中,随机抽取样品进行检验。
2. 有针对性抽样:根据药品监督管理部门的监测重点和风险提示,有针对性地选择特定品种或特定企业的药品进行抽样检验。
三、抽样数量抽样数量应当符合国家相关法律法规和标准的要求,一般情况下,抽样数量应当满足统计学要求,能够代表被抽样对象的整体质量情况。
四、抽样地点抽样地点应当选择在药品生产企业、流通环节和医疗机构等单位的有关场所进行,确保抽样过程的公开、公平和公正。
五、抽样过程1. 抽样前,应当对抽样器具进行检验和校准,确保抽样器具的准确性和可靠性。
2. 抽样过程中,应当按照国家相关标准和规定进行操作,确保抽样的准确性和可靠性。
3. 抽样过程中,应当做好样品标识和保存,确保抽样样品的完整性和真实性。
六、抽样检验抽样检验应当由具有相应资质和能力的药品检验机构进行,确保检验结果的准确性和可靠性。
七、抽样结果处理1. 对于合格的抽样样品,应当及时向相关单位和公众公布抽样结果。
2. 对于不合格的抽样样品,应当及时通知相关单位采取相应的措施,确保不合格药品及时下架和召回。
八、抽样记录和报告抽样过程中应当做好抽样记录和报告,确保抽样过程的可追溯性和真实性。
以上就是药品抽样实施方案的具体内容,希望能够对相关工作人员的抽样工作提供一定的参考和指导。
在今后的工作中,我们将严格按照相关要求,确保药品抽样工作的严谨性和科学性,为维护人民群众的用药安全和健康做出积极的贡献。
抽样方案两类风险
抽样方案两类风险抽样方案的两类风险在抽样检验中,通过OC曲线可以评价抽样方案的判别能力,但一个抽样方案如何影响生产方和使用方的利益,可以通过两类风险进行具体分析。
1.生产方风险采用抽样检验时,生产方和使用方都要冒一定的风险。
因为抽样检验是根据一定的抽样方案从批中抽取样本进行检验,根据检验结果及接收准则来判断该批是否接收。
由于样本的随机性,同时它仅是批的一部分,通常还是很少的一部分,所以有可能做出错误的判断。
本来质量好的批,有可能被判为不接收;本来质量差的批,又有可能被判为接收。
生产方风险是指生产方所承担的批质量合格而不被接收的风险,又称第一类错误的概率,一般用α表示。
〖例3.1-8〗有一批产品,批量N=1000,批中不合格品数D=1,即批不合格品率为千分之一,生产方和使用方对这批产品的质量是满意的。
假定采用一个很简单的抽样方案,即只抽一个单位产品进行检验,如果它是合格品就接收该批;如果它是不合格品就不接收该批。
在抽样检验时,就有可能出现两种情况:第一种情况:n=1,d=0,接收该批产品;第二种情况:n=1,d=1,不接收该批产品。
例中第一种情况抽到的是合格品,根据检验方案接收该批产品,这种结果符合生产方和使用方的要求;但若恰好抽到批中唯一的不合格品,检验结果就是不接受该批产品。
这对生产方是完全不利的。
采用抽样检验,生产方就会有这样的风险,在本例中生产方冒不接收本来合格的批的风险为千分之一。
2.使用方风险使用方风险是指使用方所承担的接收质量不合格批的风险,又称第二类错误的概率,一般用β表示。
〖例3.1-9〗有一批产品,批量N=1000,批中不合格品数D=500,即批不合格品率为50%,这批产品当然是不合格的。
假定采用一个保险的抽样方案:抽n=500个单位产品进行检验,如果样本中没有一个不合格品,就接收该批,否则就不接收。
但既使这样,按抽样方案,仍有可能因恰巧抽到批中全部500个合格品而判为接收。
这种极端情况一旦发生,当然损害了使用方的利益。
抽样计划抽样方案的制定
一个不合格品可能出现一个
合 格
或多个缺陷。公司内规定当
判 一个不合格品上出现一个以
定 上缺陷时,以最严重之缺陷计
缺
缺陷(Minor defects). 其
陷 它与客户有不同协商规定时,
分 类
依具体规定执行。
算允收水准,允收数与拒收数
的判定依不合格品数目来进
行.
4.4 AQL允收水准
4.5 检验要求
否作出判断的抽样检验方案。
**4.2.2公司内部规定只使用一次抽样方案执行抽样检验。
4.3合格与缺陷的确定
4.3.2缺陷依严重性一般分为:
4.3.1被检查的产品通常有多
A. 致命缺陷(Critical
项检查项目,每一个检查项目
defects) B. 严重缺陷
偏离了标准都构成一个缺陷。
(Major defects) C. 轻微
用不放回抽取方法,从总体中随机抽取一定数量观察单位组成样本。具体方法 ① 随机数字法 ② 抽签法 二、系统抽样(systematic sampling) 又称等距/机械抽样 ---抽样方法 先将总体的观察单位按某顺序号等分成n个部分 再从第一部分随机抽第k号观察单 位,依次用相等间 隔,机械地从每一部分各抽取一个观察单位组成样本。
的样本中最大允许不合格数,通常用Ac表示。 5.拒收数(不合格判定数): 在抽样方案中,预先规定的判定批产品不合格
的样本中最 小不合格数,通常用Re表示。 6.允收水准:供应商和客户就某种程度的不良品率达成的双方都可接受的
品质标 。
02
抽样方法
常用抽样方法 一、单纯随机抽样(simple random sampling) ---抽样方法 根据研究目的选定总体,首先对总体中所有的观察单位编号,遵循随机原则,采
抽样计划抽样方案的制定(一)
抽样计划抽样方案的制定(一)抽样计划抽样方案的制定是市场调研中的一个重要环节,其作用是进行样本图选、样本抽取、样本调查及数据收集等。
本文将从以下几个方面进行讨论:一、制定抽样计划的重要性制定抽样计划可以保证市场调研的准确性和客观性,避免在调研过程中出现样本数量过少或者样本不代表性等问题,从而能够提高调研结果的可信度和参考价值。
二、抽样方案的制定步骤1、确定研究目的和范围,明确人群特征和样本数量要求。
2、确定样本来源,比如样本来源可以是公司的客户、潜在客户、竞争对手、行业内的专家等。
3、确定抽样方式,如随机抽样、滚动抽样、分层抽样、系统抽样等,不同的抽样方式有不同的优势和劣势,需要根据研究目的和实际情况选择。
4、制定样本规模和分配方案,要考虑时间、人力、财力等资源的限制条件,尽可能确保分配得合理。
5、制定问卷或访谈计划,认真设计调查问卷或访谈问题,以确保所有问题都得到了准确的回答。
6、执行实地调研,并对数据进行收集、分析和解释,同时进行比较和统计推断,产出科学准确的数据分析报告。
三、抽样方案存在的风险和挑战在制定抽样方案时也存在一些风险和挑战。
比如,可能会遇到样本容易出现一些人为因素通过有意或无意的选择性参与调查,导致数据结果的不准确性等问题。
因此,在制定抽样计划的过程中,还需要仔细考虑、评估风险和挑战,并对这些问题进行定期监测。
综上所述,抽样计划抽样方案的制定是市场调研过程中的一项关键性任务,通过正确制定方案,能够保证市场调研的准确性和客观性,提高调研结果的可信度和参考价值。
因此,各大企业必须全面了解市场调研的相关规范和操作程序,学会制定科学可行的抽样计划抽样方案,才能在市场竞争中胜出,取得成功。
抽样风险及抽样方案课件
抽样风险可能导致估计的 参数值与真实值存在偏差, 影响对总体特征的准确判断。
假设检验误判
在假设检验中,抽样风险 可能导致对总体参数的错 误判断,造成第一类或第 二类错误的产生。
预测精度降低
在预测分析中,抽样风险 可能导致预测结果的不准 确,降低预测精度。
01
常见抽样方法
简单随机抽样
01
简单随机抽样是一种基本的抽样 方法,每个样本单位被选中的概 率相等。
分层抽样
适用于总体异质性较高、需要分 层研究的情况。
系统抽样
适用于总体有序排列、需要按照 一定顺序抽取样本的情况。
加强质量控制
培训抽样员
对抽样员进行专业培训,确保其掌握正确的抽样 方法和技巧。
监督与检查
对抽样过程进行全程监督和检查,确保抽样工作 的规范性和准确性。
数据复核与校验
对采集的数据进行复核和校验,确保数据的真实 性和准确性。
产生原因
01
02
03
样本设计不科学
样本设计不合理可能导致 样本代表性不足,从而影 响统计推断的准确性。
样本选取偏误
样本选取过程中可能出现 的选择性偏误、无响应偏 误等,导致样本数据失真。
抽样方法不恰当
不恰当的抽样方法可能导 致样本结构与总体结构不 一致,增加抽样风险。
对统计推断的影响
参数估计误差
分层抽样能够保证各层内部的同质性,从而提高样本的代表性。
整群抽 样
整群抽样是将总体划分为若干个群,然后从这些群中随机 抽取一定数量的群作为样本。
整群抽样适用于群内个体特征较为一致的情况,可以提高 样本的代表性。
多阶段抽样
多阶段抽样是将总体分为若干个阶段,逐阶段进行抽样,最终得到所需的样本。
- 1、下载文档前请自行甄别文档内容的完整性,平台不提供额外的编辑、内容补充、找答案等附加服务。
- 2、"仅部分预览"的文档,不可在线预览部分如存在完整性等问题,可反馈申请退款(可完整预览的文档不适用该条件!)。
- 3、如文档侵犯您的权益,请联系客服反馈,我们会尽快为您处理(人工客服工作时间:9:00-18:30)。
First.会有不良品出货给客户 Second .产生接收不良品的心理习惯
不良品交付到客户端:
1、售后维修、换货的费用增加 结果 2、增加客户处理不良物料的成 本 3、刚好被客户抽检到不良,客 户投诉
C=0 抽样计划
√1995年:美国军方废除MIL-STD-105E(美国国防部军用标准),使用美国国家 标准 ANSI/ASQC Z1.4-1993 √ 2003年发布了2003版美国国家标准ANSI/ASQ Z1.4-2003 √ 2008年:发布美国国家标准ANSI/ASQ Z1-2008 √ 1996年,美军推出新版的抽样标准MIL-STD-1916。MIL-STD-1916也限定它的 接收准则为“0收1退”,所以MIL-STD-1916也可以称为零缺陷抽样方案。 √C=0 抽样计划之优点与缺点:较少的检验数量,达到较高的消费者保障 对消费者的保证比较大; 对生产者的风险比较高。 √ ISO/TS16949只要求了“接收水平应是零缺陷”,并没有明确规定应采用C=0 抽样方案还是MIL-STD-1916 √ C=0抽样检验计划-国际认可的标准是:MIL-STD-1916。美国国防部采购抽 样标准
应对已在控制计划中标识为不稳定和能力不足的特性启动适当的反应计 划。反应计划应包括适当的控制过程输出和100%检验。 7. 1. 2 接收准则 接收准则应有组织定义,要求时,应由顾客批准。 对于计数型数据抽样,接收等级应是零缺陷
全检、抽检、免检
√汽车行业的关键质量特性,过程能力指数CPK值≥1.67,须全 检,SPC控制等,须做测量系统分析,重要质量特性:过程能力 指数CPK值≥ 1.33; √制程较不稳定,生产过程不能保证,如CPK达不到要求 √出口至国外的产品。退货费用高,退货周期长,质量问题不 便处理; √涉及人身安全、法律法规; √高风险产业,如航天工业/卫星发射; √ 现有技术条件,无法检测的项目 √ 生产辅助性材料,包装材料 √ A级供应商,制程稳定且一定时期内有优秀的供货业绩 √风险不大,但是制程能力较差,异常及不良多 √风险极大,航天产品:卫星、导弹、宇宙飞船 100%检验
抽样误差 样本量 50 100 150 250 350 1000 抽样误差 ±13.9% ±9.8% ±8.0% ±6.2% ±5.2% ±3.2%
最小抽样量的计算公式: 抽样量需要 > 30个才算 足够多,可以用以下近似的误差/样本量估算公 式;
n: 为样本量; :方差,抽样个体值和整体均值之间的偏离程度, 抽样数值分布越分散方差越大,需要的采样量越 多; E: 为抽样误差(可以根据均值的百分比设定), 由于是倒数平方关系,抽样误差减小为1/2,抽样 量需要增加为4倍; : 为可靠性系数,即置信度,置信度为95%时, Z=1.96,置信度为90%时,=1.645,置信度越高需 要的样本量越多;95%置信度比90%置信度需要的 采样量多40%;
抽样风险及抽样方案
质量部 Prepare by : Chaste li 李凤设
抽样风险案例 出货10000PCS至客户X公司,客户依照检验规则抽样尺寸10PCS,发现 1PCS尺寸不良,于是整批判退,我司派人前往X公司全检返工,10000PCS 终于返工完毕,总共发现2PCS不良,不良率0.02%,良率99.8% 良率99%以上的批次为什么被判退?
讨论:
小批量试产验证制程能力 验证物料、制程能力,应该使用多少数量的物料、成品试验,可以反映批质量状况? 20个数据可以计算CPK吗? TS16949一般是连续8小时生产的数量,或者300PCS样品来验证过程
传统抽样方案的弊端 出货批量5000PCS,按照外观AQL=0.65, 抽样数n=200,3收4退,代表意义:抽样 发现3PCS或3PCS以下不良,则这批会放行 出货,但是根据我们抽样结果,这批次里 面很可能存在1.5%的不良,这些不良品会 出货到客户端
哪些情形 免检?
免检
抽样风险及控制
避免风险 识别抽样风险 分析风险 评价风险 降低风险 控制抽样风险
风险系数RPN概念: Risk Priority Number风险优先系数 严重度/严重程度S:一旦发生所造成后果的严重程度 频度/可能性O:发生的概率,一定时期内,一定条件下发生的次数 可检测性/探测度D :被发现的难易程度 RPN=严重度S*频度O*探测度D
供应商的一批来料有“红” 有“蓝”,有大有小,我们 怎么才能抽到“大奖”?
抽到的样品,全部是“大”的, 没有抽到“小”的
尺寸不良率为10%的总体的批次, 尺寸我们抽检5PCS,抽到不良品的 概率是9.52%,风险极大
尺寸抽检5PCS,发现1PCS尺 寸不良 尺寸抽检5PCS,发现1PCS尺寸不 良
情形1:要么发生 了小概率事件 情形2:要么不良率极高
抽到0PCS不良的概率P(0)=0.19% 抽到1PCS不良的概率P(1)=1.2% 抽到2PCS不良的概率P(2)=3.76% 抽到3PCS或3PCS以上不良的概率P=94.85%,表明采用AQL=0.65抽样,这批产品 被拒收的概率很高,GB2828给出的抽样方案是可行的
抽样误判的风险
抽到的样品,有“大”有“小”
外观/尺寸
外观/尺寸 外观/功能
√
√ √ √
抽样方案设计
我们希望供应商来料良率达到99%,达到此 质量水平,以95%的概率接收,良率为90% 时,以10%的概率接收。供应商来料一批 3000PCS,应该检验多少,拒收数是多少?
AQL范围 0.01-1000
不合全性/电气性能 结构尺寸及装配性 外观
抽样风险
1、样本容量/抽样数:影响抽样误差 2、检测工具:设备未校准,设备偏差等等,设备 误测误判,影响检测能力、准确程度 3、抽样方法:取样未能代表批质量状况;一般重 复抽样误差比不重复抽样误差要大一些。 4、总体各单位标志值的差异程度:如制程能力, 标准偏差,制程波动较大
这么好的产品 为什么判退
如何管控这 些风险
选择优质供应商 须提供质量担保 供应商辅导/推动 IQC合理抽检 减少不良品流入
☆ 不同模具的差异 ☆ 不同穴号的差异 ☆ 不同原材料导致差异 ☆ 不同生产工艺技术的 差异 ☆ 不同制程参数的差异: 压力、温度、时间等 ☆ 不同作业人员的差异 ☆ 不同测量工具的差异 ☆ 人员疲劳、机器磨损、 夹具松动、夹具移位
抽样风险的计算
例1、电镀外观良率95%,来料 3000PCS,抽检100PCS,抽检到不良 品的概率是多少?抽到2PCS不良品 的概率是多少? 抽到不良品的概率: P=1-0.67%=99.33% 抽到2PCS或2PCS以上不良的概率: P=95.97% 没有抽到不良品的概率: P=90.48% 抽到1PCS或1PCS以上不良的概率: P=9.52%,表明10%不良率的批次,我们 抽检5PCS,抽检到不良的概率很低
√
√ √ √
耐磨套
线圈绕线 衔铁压推杆 三楼制 程 测试 测试 测试 测试 线包注塑 四楼制 程
外观/尺寸
低(CPK≤0.8) 耐压 漏电流 电阻 吸力 外观/尺寸
尚可(CPK:1.001.33) 良好(CPK:≥1.33 )
√
√ √ √ √ 良好 √ √ √ 尚可
滑轮注塑
工字铁注塑 M4外壳注塑 多臂电磁棒
例2、孔径良率90%,来料2000PCS, 孔径抽检5PCS,抽检到0PCS不良品, 抽到1PCS以上不良品的概率分别是 多少??
批量N=3000PCS,p=5%,按AQL=0.65,则抽样n=125PCS,AC=2,抽到3PCS或3PCS以 上不良的概率是多少?
P=
( np )
d!
d
e - np
, N ≧ 10n 且 p < 0.1
注意:以下数据是假定的数据;下面我们依据制程能力,风险来评估检验的程度
工序 内容 线材 铜线 铁件 来料 质量特性 机械环境性能 耐压等 尺寸/盐雾 低(CPK≤0.8) √ 制程能力 严重度S 可能性O 探测度D 全检 抽检 免检 √ √
塑胶件
端子 热缩管 顶杆
外观/尺寸
外观/尺寸 外观/尺寸 外观/尺寸
CPK等级 A+ A B C D CPK Greater than1.67 1.33-1.67 1.00-1.33 0.67-1.00 Less than0.67 原则 无缺陷 维持 改进为A级 不良较多 设计、制造需整改
分担风险 承受风险
讨论:
• •
检验并不增加价值,检验属于鉴定成本,通过改善,减少检验,以降低 总质量成本;检验是在制程能力不足的情形下,为减少风险必须实施; 以目前我们供应商的来料状况,生产线的制程能力,哪些必须实施加强 检验,必须100%全检;哪些项目可以免检?理由是什么?
ISO/TS16949 7.1.2接收准则:组织应规定接收准则,要求
时,由顾客批准。对于计数型数据抽样,接收水平应是零 缺陷。
什么是计数型? 好与坏,通/止,Pass/fail,Go/NoGo等,一般是统计其不良率或不良数
TS16949零缺陷抽样的要求
• 中国GB/T 2828参考ANSI/ASQC Z1.4制定 • 抽样标准MIL-STD-1916是美国国防工业采用的标准,美军采购时主要 选用的抽样标准,是零缺陷抽样;强调不允许不良品之存在。 • ANSI/ASQC Z1.4是美国国家标准,不是零缺陷抽样 TS16949条款对反应计划及抽样的规定 8. 2. 3. 1 制造过程的监视和测量
产品类型 航天产品:卫星、导弹、宇宙飞 船 重要军工产品:舰艇、飞机 工业产品:汽车、机电 民用产品:家电、纺织、日化用 品、生活用品
严 重要质量特性 宽 次要质量特性
生产者风险α=0.05(0.01-0.1);消费者风险β=0.10 不良率P0=1%时,接收概率L(P0)=95% 不良率P1=10%时,接收概率 L(P0)=10% 可以算出抽样数n,Ac