机械运动和动力学外文文献原文+译文
机械设计外文文献翻译、中英文翻译

外文原文Mechanical DesignAbstract:A machine is a combination of mechanisms and other components which transforms, transmits. Examples are engines, turbines, vehicles, hoists, printing presses, washing machines, and movie cameras. Many of the principles and methods of design that apply to machines also apply to manufactured articles that are not true machines. The term "mechanical design" is used in a broader sense than "machine design" to include their design. the motion and structural aspects and the provisions for retention and enclosure are considerations in mechanical design. Applications occur in the field of mechanical engineering, and in other engineering fields as well, all of which require mechanical devices, such as switches, cams, valves, vessels, and mixers.Keywords: Mechanical Design mechanisms Design ProcessThe Design ProcessDesigning starts with a need real.Existing apparatus may need improvements in durability, efficiency, weight, speed, or cost. New apparatus may be needed to perform a function previouslydone by men, such as computation, assembly, or servicing. With the objective wholly or partlyIn the design preliminary stage, should allow to design the personnel fully to display the creativity, not each kind of restraint. Even if has had many impractical ideas, also can in the design early time, namely in front of the plan blueprint is corrected. Only then, only then does not send to stops up the innovation the mentality. Usually, must propose several sets of design proposals, then perform the comparison. Has the possibility very much in the plan which finally designated, has used certain not in plan some ideas which accepts.When the general shape and a few dimensions of the several components becomeapparent, analysis can begin in earnest. The analysis will have as its objective satisfactory or superior performance, plus safety and durability with minimum weight, and a competitive cost. Optimum proportions and dimensions will be sought for each critically loaded section, together with a balance between the strengths of the several components. Materials and their treatment will be chosen. These important objectives can be attained only by analysis based upon the principles of mechanics, such as those of static for reaction forces and for the optimum utilization of friction; of dynamics for inertia, acceleration, and energy; of elasticity and strength of materials for stress and deflection; of physical behavior of materials; and of fluid mechanics for lubrication and hydrodynamic drives. The analyses may be made by the same engineer who conceived the arrangement of mechanisms, or, in a large company, they may be made by a separate analysis division or research group. Design is a reiterative and cooperative process, whether done formally or informally, and the analyst can contribute to phases other than his own. Product design requires much research and development. Many Concepts of an idea must be studied, tried, and then either used or discarded. Although the content of each engineering problem is unique, the designers follow the similar process to solve the problems. Product liability suits designers and forced in material selection, using the best program. In the process of material, the most common problems for five (a) don't understand or not use about the latest application materials to the best information, (b) failed to foresee and consider the reasonable use material may (such as possible, designers should further forecast and consider due to improper use products. In recent years, many products liability in litigation, the use of products and hurt the plaintiff accused manufacturer, and won the decision), (c) of the materials used all or some of the data, data, especially when the uncertainty long-term performance data is so, (d) quality control method is not suitable and unproven, (e) by some completely incompetent persons choose materials.Through to the above five questions analysis, may obtain these questions is does not have the sufficient reason existence the conclusion. May for avoid these questions to these questions research analyses the appearance indicating the direction. Although uses the best choice of material method not to be able to avoid having the product responsibility lawsuit, designs the personnel and the industry carries on the choice of material according to the suitable procedure, may greatly reduce the lawsuit the quantity.May see from the above discussion, the choice material people should to the material nature, the characteristic and the processing method have comprehensive and the basic understanding.Finally, a design based upon function, and a prototype may be built. If its tests are satisfactory, the initial design will undergo certain modifications that enable it to be manufactured in quantity at a lower cost. During subsequent years of manufacture and service, the design is likely to undergo changes as new ideas are conceived or as further analyses based upon tests and experience indicate alterations. Sales appeal.Some Rules for DesignIn this section it is suggested that, applied with a creative attitude, analyses can lead to important improvements and to the conception and perfection of alternate, perhaps more functional, economical,and durable products.To stimulate creative thought, the following rules are suggested for the designer and analyst. The first six rules are particularly applicable for the analyst.1. A creative use of need of physical properties and control process.2. Recognize functional loads and their significance.3. Anticipate unintentional loads.4. Devise more favorable loading conditions.5. Provide for favorable stress distribution and stiffness with minimum weight.6. Use basic equations to proportion and optimize dimensions.7. Choose materials for a combination of properties.8. Select carefully, stock and integral components.9. Modify a functional design to fit the manufacturing process and reduce cost.10. Provide for accurate location and noninterference of parts in assembly.Machinery design covers the following contents.1. Provides an introduction to the design process , problem formulation ,safety factors.2. Reviews the material properties and static and dynamic loading analysis ,Including beam , vibration and impact loading.3. Reviews the fundamentals of stress and defection analysis.4. Introduces fatigue-failure theory with the emphasis on stress-life approaches to high-cycle fatigue design, which is commonly used in the design of rotation machinery.5. Discusses thoroughly the phenomena of wear mechanisms, surface contact stresses ,and surface fatigue.6. Investigates shaft design using the fatigue-analysis techniques.7. Discusses fluid-film and rolling-element bearing theory and application8. Gives a thorough introduction to the kinematics, design and stress analysis of spurgears , and a simple introduction to helical ,bevel ,and worm gearing.9. Discusses spring design including compression ,extension and torsion springs.10. Deals with screws and fasteners including power screw and preload fasteners.11. Introduces the design and specification of disk and drum clutches and brakes. Machine DesignThe complete design of a machine is a complex process. The machine design is a creative work. Project engineer not only must have the creativity in the work, but also must in aspect and so on mechanical drawing, kinematics, engineerig material, materials mechanics and machine manufacture technology has the deep elementary knowledge. One of the first steps in the design of any product is to select the material from which each part is to be made. Numerous materials are available to today's designers. The function of the product, its appearance, the cost of the material, and the cost of fabrication are important in making a selection. A careful evaluation of the properties of a. material must be made prior to any calculations.Careful calculations are necessary to ensure the validity of a design. In case of any part failures, it is desirable to know what was done in originally designing the defective components. The checking of calculations (and drawing dimensions) is of utmost importance. The misplacement of one decimal point can ruin an otherwise acceptable project. All aspects of design work should be checked and rechecked.The computer is a tool helpful to mechanical designers to lighten tedious calculations, and provide extended analysis of available data. Interactive systems, based on computer capabilities, have made possible the concepts of computer aided design (CAD) and computer-aided manufacturing (CAM).How does the psychologist frequently discuss causes the machine which the people adapts them to operate. Designs personnel''s basic responsibility is diligently causes the machine to adapt the people. This certainly is not an easy work, because certainly does not have to all people to say in fact all is the most superior operating area and the operating process.Another important question, project engineer must be able to carry on the exchange and the consultation with other concerned personnel. In the initial stage, designs the personnel to have to carry on the exchange and the consultation on the preliminary design with the administrative personnel, and is approved. This generally is through the oral discussion, the schematic diagram and the writing material carries on.If front sues, the machine design goal is the production can meet the human need the product. The invention, the discovery and technical knowledge itself certainly notnecessarily can bring the advantage to the humanity, only has when they are applied can produce on the product the benefit. Thus, should realize to carries on before the design in a specific product, must first determine whether the people do need this kind of product Must regard as the machine design is the machine design personnel carries on using creative ability the product design, the system analysis and a formulation product manufacture technology good opportunity. Grasps the project elementary knowledge to have to memorize some data and the formula is more important than. The merely service data and the formula is insufficient to the completely decision which makes in a good design needs. On the other hand, should be earnest precisely carries on all operations. For example, even if places wrong a decimal point position, also can cause the correct design to turn wrongly.A good design personnel should dare to propose the new idea, moreover is willing to undertake the certain risk, when the new method is not suitable, use original method. Therefore, designs the personnel to have to have to have the patience, because spends the time and the endeavor certainly cannot guarantee brings successfully. A brand-new design, the request screen abandons obsoletely many, knows very well the method for the people. Because many person of conservativeness, does this certainly is not an easy matter. A mechanical designer should unceasingly explore the improvement existing product the method, should earnestly choose originally, the process confirmation principle of design in this process, with has not unified it after the confirmation new idea.外文资料翻译译文机械设计摘要:机器是由机械装置和其它组件组成的。
机械外文文献翻译

Overall position of Agricultural Mechanization inTurkeyAgricultural equipment and machinery are the indispensable part of agricultural activities. If these instruments, which are used in various stages of production, are not used properly, there may be some problems. So, how can we use them properly ? As the proverb goes, “It is the want of care that makes the field bare”. They return the money and efforts invested in them if they are maintained well.Ploughs, which were being used in our country up until recently, resemble those ploughs of the various tribes that lived in Anatolia long time ago. It is because one society gets use of societies that lived before. Some of the black ploughs that were being used up until recently resemble the ploughs that had been used in the ancient Rome.The first agricultural school was established in the Ottoman Empire in 1846. The first domestic heavy ploughs was manufactured i n Izmir 90 years ago, and tractor was introduced 80 years ago. However, it was only the foundation of the Republic that the tractor began to be used in agricultural activities. Agricultural mobilization began with modern agricultural practices in the Atatürk Forest Farm, which was founded by the Great Atatürk. Use of modern agricultural equipment was encouraged, workshops and factories were established, and agricultural machinery was manufactured. Introduction of tractor and particularly its use in agricultural production began in 1938. In those years, tractor use in State Production Farms increased, and farmers recognized the benefits of tractor in agricultural productivity and labor. State production farms became places which clearly showed the importance of agricultural mechanization.Agricultural mechanization is a production technology which enables the appropriate use of energy and equipment required for high production in agricultural area.Warehousing, transporting and marketing the products have become faster and more economic with the help of agricultural mechanization.Tractor is the basic equipment that enables the use of other agricultural equipment. These equipment items are also produced in Turkey. As tractor and other mechanization equipment are expensive, they should be used in a way to achieve the highest productivity and managed by informed and efficient people.Agricultural production in Turkey is Cereal-BasedAgricultural production in Turkey is cereal-based. There are serious nutrition problems in more than the half of the developing countries. Every year, millions of people die of hunger. For this reason, agricultural production is highly important. Turkey is out of it’s available planting areas. They do not have any new places left for plantation. The only thing they can do is to increase productivity. In order to increase productivity, they need to use some imputs. The only way to increase these inputs such as fertilizers, chemicals, irrigation and high quality seedling is agricultural mechanization. It is achieved through ploughing the soil in the right time, planting with a particular plantation row and particular distance in order to utilize equally from all parts of soil, applying chemicals and fertilizers at the requested time and amount, harvesting in a short period and without loss of any grains, and storing the product.Necessary support is given to Turkey’s companiesAgricultural mechanization tools are expensive. However, if they are maintained well and used economically, they return their cost. State provides some opportunities such as low-interest rates for the procurement of Agricultural Mechanization Machineries. The equipment and machinery, which can be purchased with credits, are examined by the units established by the Ministry of Agriculture and Rural Affairs to be approved for the agricultural technique. In these institutions, all kinds of tools and machinery, including tractors, go under various tests. It is determined if these machines are appropriate for Turkey’s environment. Necessary support is given to Turkey’s companies and farmers in order to remove the deficiencies determined.As for the maintenance of these equipment and machinery, it is a great chance that via the improvement of technology, Turkey’s producers are provided withopportunities that will help them in agricultural activities. According to researches,if the maintenance of a machine is done right and on time, purchasing cost decreased by 1/5.农业机械化在土耳其的整体地位农业设备和机械在农业活动中是不可或缺的组成部分。
机械设计过程外文文献翻译、中英文翻译

附录英文Machine design processThe machine is the organization with other components combinations, transforms,the transmission or using the energ,the strength or the movementexample for the beneficial use has the engine.the turbine wheel,the vehicles.the hoist,the printer,the washer and the movie camera Many is suitable tbr themachine design principle and the strength law also is suitable to is not thegenuine machine finished product.the driven wheel hub and the file cabinet tothe measuring appl iance and the nuclear pressure vessel.”Machine designt thisterminology compared to”machine design”more generalized,it including machine design.But regarding certain instruments.1ike uses to determine hot,the mobile line and the volume thermal energy as well as the fluid aspect question needs alone to consider.But when machine design must consider themovement and the structure aspect question as well as preserved and the sealstipulation.In the mechanical engineering domain and all that project domainapplication machine design,all need such as mechanism and so on the svdtch,cam,valve,vessel and mixer.The design beginning tO being true or the imagination need.The existing instrument possibly needs in the durability,the efficiency,the weight,the speedor the cost performs to improve.]he possible need new instrument tO completebefore made the function by the person.1ike t was abundant Assembly or maintenance.After the goal completely or partially determines,the design nextstep is the idea carl complete needs the ffmction the organization and its thearrangement for this,the free hand drawing schematic diagram value is enormous,it not only takes a person idea the recording and the auxiliary.methodwhich if the other people discusses,moreover especially is suitable for with ownidea exchange,also needs to concern as the creative mentality stimulant to thepart widespread knowledge,because a new machine frequently by knew very well each kind of components rearrange or the replace become,perhaps changedthe size and the material.Regardless of after idea process or,a designer callcarry on fast either the sketchy computation or the analysis determines thegeneral size and the feasibility.After about need or may use the spatial meteidea determination,may start according to the proportion picture schematicdiagram.When several components approximate shapes and several sizes come out,the analysis was allowed truly to start.The analysis goal lies in enable it to havesatisfying or the superior performance,as well as will seek the best proportionand the size under the smallest weight security and the durability and thecompetitive cost designer for each essential load bearing section,as well asseveral components intensities balance then choice material and processingmethod.These important goals only have through only then may obtain based on the mechanism analysis,like about reacting force and friction most superioruse principie of statics;About inertia,acceleration and energy principle ofdynamics:About stress and deflection material elasticity and intensity principle;About material physical behavior principle;About lubrication and water poweractuation hydromechanics principle.The analysis may identical engineer whicharranges by the idea machinery do,or makes the analysis in the big company bythe independent analysis department or the research group the result,possibleneed new arrangement and new size.No matter is officially does orunofficialdoes,supposes Japan is relapse and the cooperation process.the analysis staffmay play the role to all stages but not merely is he stage.Some design criteriaIn this part,some people suggested carries on the analysis using the creative manner,this kind of analysis may cause the significant improvement aswell as to the spare product idea and the consummation,the product functionmore.more economical,is perhaps more durable. The creation stage does notneed is at first and the independent stage.Alttlough the analysis staff possiblycertainlv is not responsible for the entire design,but he not meyely is can fromthe numeral proposc wants question correct answer which he soIVes,not merelyis Droduces the stress value,the size or the work limit. He may propose a morewidespread opinion,in order to improvement standard or plan. Because beforethe analysis or in the analysis process,he can familiar install and its the workingcondition.he is in an idea to prepare chooses the plan the rantage Poinl.Best hecan propose the suggestion transfigure eliminates the moment of force or thestress concentration,but was not the permission constructs has the blgsectlonand the excessively many dynamic loads organization should better be he discards his careful desi{;n but is not afterwards saw the machinery discarded.In order to stimulate the creative thought,below suggested designs thepersonnel and the analysis staff uses the criterion.The first 6 criteria especially are suitable for the analysis staff,although he possibly involves to possesses this l o items.1.Creatively the use needs the physical performance and the control doesnot need.2.Knows the practical load and its the importance.3.D00s not consider the function load in advance.4.Invents the more advantageous loading environment.5.Provides the minimurn weight the most advantageous stress distributionand the rigidity.6.uses the fundamental equation computation proportion and causes thesize optimization.7.The selection material obtains the perlbrmance combination.8.In between spare parts and integrated components carefid choice. 9.Revisions functional design adapts the production process and reduces thecost.10.In the consideration assembly causes the part pintpointing and mutuallydoes not disturb.Designs the personnel to have in such domain,like the statics,the inematics,dynamics and the materials mechanics have the good accomplishment,in addition.but also must familiar make the material and themanufacture craft.Designs the personnel to have to be able to combine allcollrelations the fact,carries on teaches Wei.the manufacture schematic diagramand the charting comes the manufacture request totransmit the workshop. Any product design one of first step of work is the choice uses in to makeeach part the material.Today design personnel may obtain innumerably.When choice,the product function,the outward appearance,the material cost and theproduction cost very are all important.Before any computation must carefullyappraise the material the performance.It is the necessary careful computation toguarantee the design the validity The computation ever does not appear on thechart,but is saved by ten each kind of reason.Once any part expires,had makeclear when is designing at first this had the flaw the components has made any;Moreover,。
文献翻译-机械运动和动力学

附录附录一英文资料Kinematics and dynamics of machineryOne princple aim of kinemarics is to creat the designed motions of the subject mechanical parts and then mathematically compute the positions, velocities ,and accelerations ,which those motions will creat on the parts. Since ,for most earthbound mechanical systems ,the mass remains essentially constant with time,defining the accelerations as a function of time then also defines the dynamic forces as a function of time. Stress,in turn, will be a function of both applied and inerials forces . since engineering design is charged with creating systems which will not fail during their expected service life,the goal is to keep stresses within acceptable limits for the materials chosen and the environmental conditions encountered. This obvisely requies that all system forces be defined and kept within desired limits. In mechinery , the largest forces encountered are often those due to the dynamics of the machine itself. These dynamic forces are proportional to acceletation, which brings us back to kinematics ,the foundation of mechanical design. Very basic and early decisions in the design process invovling kinematics wii prove troublesome and perform badly.Any mechanical system can be classified according to the number of degree of freedom which it possesses.the systems DOF is equal to the number of independent parameters which are needed to uniquely define its posion in space at any instant of time.A rigid body free to move within a reference frame will ,in the general case, have complex motoin, which is simultaneous combination of rotation and translation. In three-dimensional space , there may be rotation about any axis and also simultaneous translation which can be resoled into componention along three axes, in a plane ,or two-dimentional space ,complex motion becomes a combination of simultaneous along two axes in the plane. For simplicity ,we will limit our present discusstions to the case of planar motion:Pure rotation the body pessesses one point (center of rotation)which has no motion with respect to the stationary frame of reference. All other points on the body describe arcs about that center. A reference line drawn on the body through the center changes only its angulai orientation.Pure translation all points on the body describe parallel paths. A reference line drawn on the body changes its linear posion but does not change its angular oriention.Complex motion a simulaneous combination of rotion and translationm . anyreference line drawn on the body will change both its linear pisition and its angular orientation. Points on the body will travel non-parallel paths ,and there will be , at every instant , a center of rotation , which will continuously change location.Linkages are the bacis building blocks of all mechanisms. All common forms of mechanisms (cams , gears ,belts , chains ) are in fact variations of linkages. Linkages are made up of links and kinematic pairs.A link is an (assumed)rigid body which possesses at least two or more links (at their nodes), which connection allows some motion, or potential motion,between the connected links.The term lower pair is used to describe jionts with surface contact , as with a pin surrounded by a hole. The term higher pair is used to describe jionts with point or line contact ,but if there is any clerance between pin and hole (as there must be for motion ),so-called surface contact in the pin jiont actually becomes line contact , as the pin contacts actually has contact only at discrete points , which are the tops of the surfaces’asperities. The main practical advantage of lower pairs over higher pairs is their better ability to trap lubricant between their envloping surface. This ie especially true for the rotating pin joint. The lubricant is more easily squeezed out of a higher pair .as s result , the pin joint is preferred for low wear and long life .When designing machinery, we must first do a complete kinematic analysis of our design , in order to obtain information about the acceleration of the moving parts .we next want te use newton’s second law to caculate the dynamic forces, but to do so we need to know the masses of all the moving parts which have these known acceletations. These parts do not exit yet ! as with any design in order to make a first pass at the caculation . we will then have to itnerate to better an better solutions as we generate more information.A first estimate of your parts’masses can be obtained by assuming some reasonable shapes and size for all the parts and choosing approriate materials. Then caculate the volume of each part and multipy its volume by material’s mass density (not weight density ) to obtain a first approximation of its mass . these mass values can then be used in Newton’s equation.How will we know whether our chosen sizes and shapes of links are even acceptable, let alone optimal ? unfortunately , we will not know untill we have carried the computations all the way through a complete stress and deflection analysis of the parts. It it often the case ,especially with long , thin elements such as shafts or slender links , that the deflections of the parts, redesign them ,and repeat the force ,stress ,and deflection analysis . design is , unavoidably ,an iterative process .It is also worth nothing that ,unlike a static force situation in which a failed design might be fixed by adding more mass to the part to strenthen it ,to do so in a dynamic force situation can have a deleterious effect . more mass with the same acceleration will generate even higher forcesand thus higher stresses ! the machine desiger often need to remove mass (in the right places) form parts in order to reduce the stesses and deflections due to F=ma, thus the designer needs to have a good understanding of both material properties and stess and deflection analysis to properlyshape and size parts for minimum mass while maximzing the strength and stiffness needed to withstand the dynamic forces.One of the primary considerations in designing any machine or strucre is that the strength must be sufficiently greater than the stress to assure both safety and reliability. To assure that mechanical parts do not fail in service ,it is necessary to learn why they sometimes do fail. Then we shall be able to relate the stresses with the strenths to achieve safety .Ideally, in designing any machine element,the engineer should have at his disposal should have been made on speciments having the same heat treatment ,surface roughness ,and size as the element he prosses to design ;and the tests should be made under exactly the same loading conditions as the part will experience in service . this means that ,if the part is to experience a bending and torsion,it should be tested under combined bending and torsion. Such tests will provide very useful and precise information . they tell the engineer what factor of safety to use and what the reliability is for a given service life .whenever such data are available for design purposes,the engineer can be assure that he is doing the best justified if failure of the part may endanger human life ,or if the part is manufactured in sufficiently large quantities. Automobiles and refrigrerators, for example, have very good reliabilities because the parts are made in such large quantities that they can be thoroughly tested in advance of manufacture , the cost of making these is very low when it is divided by the total number of parts manufactrued.You can now appreciate the following four design categories :(1)failure of the part would endanger human life ,or the part ismade in extremely large quantities ;consequently, an elaborate testingprogram is justified during design .(2)the part is made in large enough quantities so that a moderate serues of tests is feasible.(3)The part is made in such small quantities that testing is not justified at all ; or the design must be completed so rapidlly that there is not enough time for testing.(4) The part has already been designed, manufactured, and tested and found to be unsatisfactory. Analysis is required to understand why the part is unsatisfactory and what to do to improve it .It is with the last three categories that we shall be mostly concerned.this means that the designer will usually have only published values of yield strenth , ultimate strength,and percentage elongation . with this meager information the engieer is expected to design against static and dynamic loads, biaxial and triaxial stress states , high and low temperatures,and large and small parts! The data usually available for design have been obtained from the simpletension test , where the load was applied gradually and the strain given time to develop. Yet these same data must be used in designing parts with complicated dynamic loads applied thousands of times per minute . no wonder machine parts sometimes fail.To sum up, the fundamental problem of the designer is to use the simple tension test data and relate them to the strength of the part , regardless of the stress or the loading situation.It is possible for two metal to have exactly the same strength and hardness, yet one of these metals may have a supeior ability to aborb overloads, because of the property called ductility. Dutility is measured by the percentage elongation which occurs in the material at frature. The usual divding line between ductility and brittleness is 5 percent elongation. Amaterial having less than 5 percent elongation at fracture is said to bebrittle, while one having more is said to be ductile.The elongation of a material is usuallu measured over 50mm gauge length.siece this did not a measure of the actual strain, another method of determining ductility is sometimes used . after the speciman has been fractured, measurements are made of the area of the cross section at the fracture. Ductility can then be expressed as the percentage reduction in cross sectional area.The characteristic of a ductile material which permits it to aborb largeoverloads is an additional safety factot in design. Ductility is also important because it is a measure of that property of a material which permits it to be cold-worked .such operations as bending and drawing are metal-processing operations which require ductile materials.When a materals is to be selected to resist wear , erosion ,or plastic deformaton, hardness is generally the most important property. Several methods of hardness testing are available, depending upon which particular property is most desired. The four hardness numbers in greatest usse are the Brinell, Rockwell,Vickers, and Knoop.Most hardness-testing systems employ a standard load which is applied to a ball or pyramid in contact with the material to be tested. The hardness is an easy property to measure , because the test is nondestructive and test specimens are not required . usually the test can be conducted directly on actual machine element .Virtually all machines contain shafts. The most common shape for shafts is circular and the cross section can be either solid or hollow (hollow shafts can result in weight savings). Rectangular shafts are sometimes used ,as in screw driver bladers ,socket wrenches and control knob stem.A shaft must have adequate torsional strength to transmit torque and not be over stressed. If must also be torsionally stiff enough so that one mounted component does not deviate excessively from its original angular position relative to a second component mounted on the same shaft. Generally speaking,the angle of twist should not exceed one degree in a shaft lengthequal to 20 diameters.Shafts are mounted in bearing and transmit power through such device as gears, pulleys,cams and clutches. These devices introduce forces which attempt to bend the shaft;hence, tha shaft must be rigid enough to prevent overloading of the supporting bearings ,in general, the bending deflection of a shaft should not exceed 0.01 in per ft of length between bearing supports.In addition .the shaft must be able to sustain a combination of bending and torsional loads. Thus an equivalent load must be considered which takes into account both torsion and bending . also ,the allowable stress must contain a factor of safety which includes fatigue, since torsional and bending stress reversals occur.For fiameters less than 3 in ,the usual shaft material is cold-rolled steel containing about 0.4 percent carbon. Shafts ate either cold-rolled or forged in sizes from 3in. to 5 in. for sizes above 5 in. shafts are forged and machined to size . plastic shafts are widely used for light load applications . one advantage of using plastic is safty in electrical applications, since plastic is a poor confuctor of electricity.Components such as gears and pulleys are mounted on shafts by means of key. The design of the key and the corresponding keyway in the shaft must be properly evaluated. For example, stress concentrations occur in shafts due to keyways , and the material removed to form the keyway further weakens the shaft.If shafts are run at critical speeds , severe vibrations can occur which can seriously damage a machine .it is important to know the magnitude of these critical speeds so that they can be avoided. As a general rule of thumb , the difference betweem the operating speed and the critical speed should be at least 20 percent.Many shafts are supported by three or more bearings, which means that the problem is statically indeterminate .text on strenth of materials give methods of soving such problems. The design effort should be in keeping with the economics of a given situation , for example , if one line shaft supported by three or more bearings id needed , it probably would be cheaper to make conservative assumptions as to moments and design it as though it were determinate . the extra cost of an oversize shaft may be less than the extra cost of an elaborate design analysis.Another important aspect of shaft design is the method of directly connecting one shaft to another , this is accomplished by devices such as rigid and flexiable couplings.A coupling is a device for connecting the ends of adjacent shafts. In machine construction , couplings are used to effect a semipermanent connection between adjacent rotating shafts , the connection is permanent in the sense that it is not meant to be broken during the useful life of the machinem , but it can be broken and restored in an emergency or when worn parts are replaced.There are several types of shaft couplings, their characteristics depend on the purpose for which they are used , if an exceptionally long shaft is required in a manufacturing plant or a propeller shaft on a ship , it is made in sections that are coupled together with rigid couplings. A common type of rigid coupling consists of two mating radial flanges that are attached by key driven hubs to the ends of adjacent shaft sections and bolted together through the flanges to form a rigid connection. Alignment of the connected shafts in usually effected by means of a rabbet joint on the face of the flanges.In connecting shafts belonging to separate device ( such as an electric motor and a gearbox),precise aligning of the shafts is difficult and a fkexible coupling is used . this coupling connects the shafts in such a way as to minimize the harmful effects of shafts misalignment of loads and to move freely(float) in the axial diection without interfering with one another . flexiable couplings can also serve to reduce the intensity of shock loads and vibrations transmitted from one shaft to another .中文翻译机械运动和动力学运动学的基本目的是去设计一个机械零件的理想运动,然后再用数学的方法去描绘该零件的位置,速度和加速度,再运用这些参数来设计零件。
Kinematics of Machinery

英汉对照:Kinematics of Machinery机械运动学10.1 Introduction .Because motion is inherent in machinery; kinematic quantities such as velocity and acceleration are of engineering importance in the analysis and design of machine components. Kinematic values in machines have reached extraordinary magnitudes. Rotative speeds, once considered high at 10,000r/min, are approaching 100,000r/min; large rotors of jet engines operate at 10,00010.1介绍。
因为运动是机械所固有的,运动学参数例如速度和加速度等工程参数在分析与设计中的机械零件中起到了很重要的作用。
运动的数值在机械中已经起到了特别的重要性。
转动速度,一度被视为高于10000转/分钟,接近100000转/分钟,大转子喷气发动机运转速度在10000to 15,000r/min, and small turbine wheels rotate at 30,000到15000转/分钟,和小汽轮机的轮子转动速度为30000to 60,000r/min.到60000转/分钟。
Size and rotative speed in rotors are related such that such that the smaller the size the greater the allowable rotative speed. A more basic quantity in rotors is peripheral speeds, which depends on rotative speed and size .Peripheral speeds in turbo machinery are reaching 大小和转子旋转速度是相关的,这样,较小的规模能够允许有更大的转动速度。
机械类外文文献及翻译
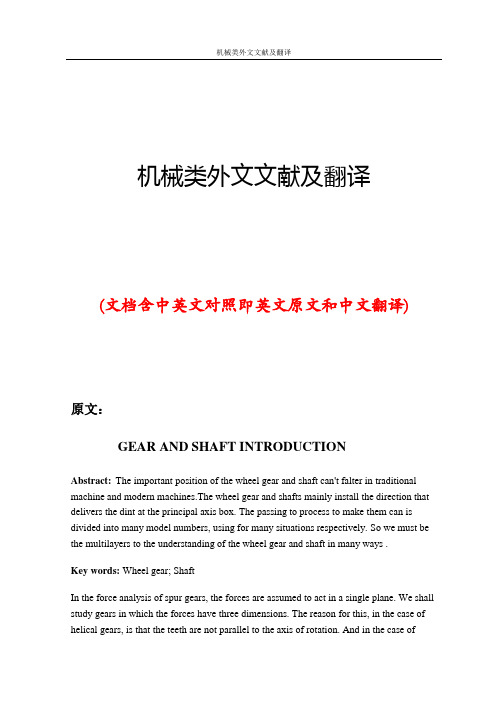
机械类外文文献及翻译(文档含中英文对照即英文原文和中文翻译)原文:GEAR AND SHAFT INTRODUCTIONAbstract:The important position of the wheel gear and shaft can't falter in traditional machine and modern machines.The wheel gear and shafts mainly install the direction that delivers the dint at the principal axis box. The passing to process to make them can is divided into many model numbers, using for many situations respectively. So we must be the multilayers to the understanding of the wheel gear and shaft in many ways .Key words: Wheel gear; ShaftIn the force analysis of spur gears, the forces are assumed to act in a single plane. We shall study gears in which the forces have three dimensions. The reason for this, in the case of helical gears, is that the teeth are not parallel to the axis of rotation. And in the case ofbevel gears, the rotational axes are not parallel to each other. There are also other reasons, as we shall learn.Helical gears are used to transmit motion between parallel shafts. The helix angle is the same on each gear, but one gear must have a right-hand helix and the other a left-hand helix. The shape of the tooth is an involute helicoid. If a piece of paper cut in the shape of a parallelogram is wrapped around a cylinder, the angular edge of the paper becomes a helix. If we unwind this paper, each point on the angular edge generates an involute curve. The surface obtained when every point on the edge generates an involute is called an involute helicoid.The initial contact of spur-gear teeth is a line extending all the way across the face of the tooth. The initial contact of helical gear teeth is a point, which changes into a line as the teeth come into more engagement. In spur gears the line of contact is parallel to the axis of the rotation; in helical gears, the line is diagonal across the face of the tooth. It is this gradual of the teeth and the smooth transfer of load from one tooth to another, which give helical gears the ability to transmit heavy loads at high speeds. Helical gears subject the shaft bearings to both radial and thrust loads. When the thrust loads become high or are objectionable for other reasons, it may be desirable to use double helical gears. A double helical gear (herringbone) is equivalent to two helical gears of opposite hand, mounted side by side on the same shaft. They develop opposite thrust reactions and thus cancel out the thrust load. When two or more single helical gears are mounted on the same shaft, the hand of the gears should be selected so as to produce the minimum thrust load.Crossed-helical, or spiral, gears are those in which the shaft centerlines are neither parallel nor intersecting. The teeth of crossed-helical fears have point contact with each other, which changes to line contact as the gears wear in. For this reason they will carry out very small loads and are mainly for instrumental applications, and are definitely not recommended for use in the transmission of power. There is on difference between a crossed heli : cal gear and a helical gear until they are mounted in mesh with each other. They are manufactured in the same way. A pair of meshed crossed helical gears usually have the same hand; that is ,a right-hand driver goes with a right-hand driven. In the design of crossed-helical gears, the minimum sliding velocity is obtained when the helix angle areequal. However, when the helix angle are not equal, the gear with the larger helix angle should be used as the driver if both gears have the same hand.Worm gears are similar to crossed helical gears. The pinion or worm has a small number of teeth, usually one to four, and since they completely wrap around the pitch cylinder they are called threads. Its mating gear is called a worm gear, which is not a true helical gear. A worm and worm gear are used to provide a high angular-velocity reduction between nonintersecting shafts which are usually at right angle. The worm gear is not a helical gear because its face is made concave to fit the curvature of the worm in order to provide line contact instead of point contact. However, a disadvantage of worm gearing is the high sliding velocities across the teeth, the same as with crossed helical gears.Worm gearing are either single or double enveloping. A single-enveloping gearing is onein which the gear wraps around or partially encloses the worm.. A gearing in which each element partially encloses the other is, of course, a double-enveloping worm gearing. The important difference between the two is that area contact exists between the teeth of double-enveloping gears while only line contact between those of single-enveloping gears. The worm and worm gear of a set have the same hand of helix as for crossed helical gears, but the helix angles are usually quite different. The helix angle on the worm is generally quite large, and that on the gear very small. Because of this, it is usual to specify the lead angle on the worm, which is the complement of the worm helix angle, and the helix angle on the gear; the two angles are equal for a 0-deg. Shaft angle.When gears are to be used to transmit motion between intersecting shaft, some of bevel gear is required. Although bevel gear are usually made for a shaft angle of 0 deg. They may be produced for almost any shaft angle. The teeth may be cast, milled, or generated. Only the generated teeth may be classed as accurate. In a typical bevel gear mounting, one of the gear is often mounted outboard of the bearing. This means that shaft deflection can be more pronounced and have a greater effect on the contact of teeth. Another difficulty, which occurs in predicting the stress in bevel-gear teeth, is the fact the teeth are tapered.Straight bevel gears are easy to design and simple to manufacture and give very good results in service if they are mounted accurately and positively. As in the case of squr gears, however, they become noisy at higher values of the pitch-line velocity. In these cases it is often go : od design practice to go to the spiral bevel gear, which is the bevel counterpart of thehelical gear. As in the case of helical gears, spiral bevel gears give a much smoother tooth action than straight bevel gears, and hence are useful where high speed are encountered.It is frequently desirable, as in the case of automotive differential applications, to have gearing similar to bevel gears but with the shaft offset. Such gears are called hypoid gears because their pitch surfaces are hyperboloids of revolution. The tooth action between such gears is a combination of rolling and sliding along a straight line and has much in common with that of worm gears.A shaft is a rotating or stationary member, usually of circular cross section, having mounted upon it such elementsas gears, pulleys, flywheels, cranks, sprockets, and other power-transmission elements. Shaft may be subjected to bending, tension, compression, or torsional loads, acting singly or in combination with one another. When they are combined, one may expect to find both static and fatigue strength to be important design considerations, since a single shaft may be subjected to static stresses, completely reversed, and repeated stresses, all acting at the same time.The word “shaft” covers numerous v ariations, such as axles and spindles. Anaxle is a shaft, wither stationary or rotating, nor subjected to torsion load. A shirt rotating shaft is often called a spindle.When either the lateral or the torsional deflection of a shaft must be held to close limits, the shaft must be sized on the basis of deflection before analyzing the stresses. The reason for this is that, if the shaft is made stiff enough so that the deflection is not too large, it is probable that the resulting stresses will be safe. But by no means should the designer assume that they are safe; it is almost always necessary to calculate them so that he knows they are within acceptable limits. Whenever possible, the power-transmission elements, such as gears or pullets, should be located close to the supporting bearings, This reduces the bending moment, and hence the deflection and bending stress.Although the von Mises-Hencky-Goodman method is difficult to use in design of shaft, it probably comes closest to predicting actual failure. Thus it is a good way of checking a shaft that has already been designed or of discovering why a particular shaft has failed in service. Furthermore, there are a considerable number of shaft-design problems in which the dimension are pretty well limited by other considerations, such as rigidity, and it is only necessary for the designer to discover something about the fillet sizes, heat-treatment,and surface finish and whether or not shot peening is necessary in order to achieve the required life and reliability.Because of the similarity of their functions, clutches and brakes are treated together. In a simplified dynamic representation of a friction clutch, or brake, two in : ertias I and I traveling at the respective angular velocities W and W, one of which may be zero in the case of brake, are to be brought to the same speed by engaging the clutch or brake. Slippage occurs because the two elements are running at different speeds and energy is dissipated during actuation, resulting in a temperature rise. In analyzing the performance of these devices we shall be interested in the actuating force, the torque transmitted, the energy loss and the temperature rise. The torque transmitted is related to the actuating force, the coefficient of friction, and the geometry of the clutch or brake. This is problem in static, which will have to be studied separately for eath geometric configuration. However, temperature rise is related to energy loss and can be studied without regard to the type of brake or clutch because the geometry of interest is the heat-dissipating surfaces. The various types of clutches and brakes may be classified as fllows:. Rim type with internally expanding shoes. Rim type with externally contracting shoes. Band type. Disk or axial type. Cone type. Miscellaneous typeThe analysis of all type of friction clutches and brakes use the same general procedure. The following step are necessary:. Assume or determine the distribution of pressure on the frictional surfaces.. Find a relation between the maximum pressure and the pressure at any point. Apply the condition of statical equilibrium to find (a) the actuating force, (b) the torque, and (c) the support reactions.Miscellaneous clutches include several types, such as the positive-contact clutches, overload-release clutches, overrunning clutches, magnetic fluid clutches, and others.A positive-contact clutch consists of a shift lever and two jaws. The greatest differences between the various types of positive clutches are concerned with the design of the jaws. To provide a longer period of time for shift action during engagement, the jaws may be ratchet-shaped, or gear-tooth-shaped. Sometimes a great many teeth or jaws are used, and they may be cut either circumferentially, so that they engage by cylindrical mating, or on the faces of the mating elements.Although positive clutches are not used to the extent of the frictional-contact type, they do have important applications where synchronous operation is required.Devices such as linear drives or motor-operated screw drivers must run to definite limit and then come to a stop. An overload-release type of clutch is required for these applications. These clutches are usually spring-loaded so as to release at a predetermined toque. The clicking sound which is heard when the overload point is reached is considered to be a desirable signal.An overrunning clutch or coupling permits the driven member of a machine to “freewheel” or “overrun” bec ause the driver is stopped or because another source of power increase the speed of the driven. This : type of clutch usually uses rollers or balls mounted between an outer sleeve and an inner member having flats machined around the periphery. Driving action is obtained by wedging the rollers between the sleeve and the flats. The clutch is therefore equivalent to a pawl and ratchet with an infinite number of teeth.Magnetic fluid clutch or brake is a relatively new development which has two parallel magnetic plates. Between these plates is a lubricated magnetic powder mixture. An electromagnetic coil is inserted somewhere in the magnetic circuit. By varying the excitation to this coil, the shearing strength of the magnetic fluid mixture may be accurately controlled. Thus any condition from a full slip to a frozen lockup may be obtained.齿轮和轴的介绍摘要:在传统机械和现代机械中齿轮和轴的重要地位是不可动摇的。
机械运动和动力学中英文对照外文翻译文献

(文档含英文原文和中文翻译)中英文对照翻译英文资料Kinematics and dynamics of machineryOne princple aim of kinemarics is to creat the designed motions of the subject mechanical parts and then mathematically compute the positions, velocities ,and accelerations ,which those motions will creat on the parts. Since ,for most earthbound mechanical systems ,the mass remains essentially constant with time,defining the accelerations as a function of time then also defines the dynamic forces as a function of time. Stress,in turn, will be a function of both appliedand inerials forces . since engineering design is charged with creating systems which will not fail during their expected service life,the goal is to keep stresses within acceptable limits for the materials chosen and the environmental conditions encountered. This obvisely requies that all system forces be defined and kept within desired limits. In mechinery , the largest forces encountered are often those due to the dynamics of the machine itself. These dynamic forces are proportional to acceletation, which brings us back to kinematics ,the foundation of mechanical design. Very basic and early decisions in the design process invovling kinematics wii prove troublesome and perform badly.Any mechanical system can be classified according to the number of degree of freedom which it possesses.the systems DOF is equal to the number of independent parameters which are needed to uniquely define its posion in space at any instant of time.A rigid body free to move within a reference frame will ,in the general case, have complex motoin, which is simultaneous combination of rotation and translation. In three-dimensional space , there may be rotation about any axis and also simultaneous translation which can be resoled into componention along three axes, in a plane ,or two-dimentional space ,complex motion becomes a combination of simultaneous along two axes in the plane. For simplicity ,we will limit our present discusstions to the case of planar motion:Pure rotation the body pessesses one point (center of rotation)which has no motion with respect to the stationary frame of reference. All other points on the body describe arcs about that center. A reference line drawn on the body through the center changes only its angulai orientation.Pure translation all points on the body describe parallel paths. A reference line drawn on the body changes its linear posion but does not change its angular oriention.Complex motion a simulaneous combination of rotion and translationm . any reference line drawn on the body will change both its linear pisition and its angular orientation. Points on the body will travel non-parallel paths ,and there will be , at every instant , a center of rotation , which will continuously change location.Linkages are the bacis building blocks of all mechanisms. All common forms of mechanisms (cams , gears ,belts , chains ) are in fact variations of linkages. Linkages are made up of links and kinematic pairs.A link is an (assumed)rigid body which possesses at least two or more links (at their nodes), which connection allows some motion, or potential motion,between the connected links.The term lower pair is used to describe jionts with surface contact , as with a pin surrounded by a hole. The term higher pair is used to describe jionts with point or line contact ,but if there is any clerance between pin and hole (as there must be for motion ),so-called surface contact in thepin jiont actually becomes line contact , as the pin contacts actually has contact only at discrete points , which are the tops of the surfaces’asperities. The main practical advantage of lower pairs over higher pairs is their better ability to trap lubricant between their envloping surface. This ie especially true for the rotating pin joint. The lubricant is more easily squeezed out of a higher pair .as s result , the pin joint is preferred for low wear and long life .When designing machinery, we must first do a complete kinematic analysis of our design , in order to obtain information about the acceleration of the moving parts .we next want te use newton’s second law to caculate the dynamic forces, but to do so we need to know the masses of all the moving parts which have these known acceletations. These parts do not exit yet ! as with any design in order to make a first pass at the caculation . we will then have to itnerate to better an better solutions as we generate more information.A first estimate of your parts’masses can be obtained by assuming some reasonable shapes and size for all the parts and choosing approriate materials. Then caculate the volume of each part and multipy its volume by material’s mass density (not weight density ) to obtain a first approximation of its mass . these mass values can then be used in Newton’s equation.How will we know whether our chosen sizes and shapes of links are even acceptable, let alone optimal ? unfortunately , we will not know untill we have carried the computations all the way through a complete stress and deflection analysis of the parts. It it often the case ,especially with long , thin elements such as shafts or slender links , that the deflections of the parts, redesign them ,and repeat the force ,stress ,and deflection analysis . design is , unavoidably ,an iterative process .It is also worth nothing that ,unlike a static force situation in which a failed design might be fixed by adding more mass to the part to strenthen it ,to do so in a dynamic force situation can have a deleterious effect . more mass with the same acceleration will generate even higher forces and thus higher stresses ! the machine desiger often need to remove mass (in the right places) form parts in order to reduce the stesses and deflections due to F=ma, thus the designer needs to have a good understanding of both material properties and stess and deflection analysis to properlyshape and size parts for minimum mass while maximzing the strength and stiffness needed to withstand the dynamic forces.One of the primary considerations in designing any machine or strucre is that the strength must be sufficiently greater than the stress to assure both safety and reliability. To assure that mechanical parts do not fail in service ,it is necessary to learn why they sometimes do fail. Then we shall be able to relate the stresses with the strenths to achieve safety .Ideally, in designing any machine element,the engineer should have at his disposal should have been made on speciments having the same heat treatment ,surface roughness ,and size asthe element he prosses to design ;and the tests should be made under exactly the same loading conditions as the part will experience in service . this means that ,if the part is to experience a bending and torsion,it should be tested under combined bending and torsion. Such tests will provide very useful and precise information . they tell the engineer what factor of safety to use and what the reliability is for a given service life .whenever such data are available for design purposes,the engineer can be assure that he is doing the best justified if failure of the part may endanger human life ,or if the part is manufactured in sufficiently large quantities. Automobiles and refrigrerators, for example, have very good reliabilities because the parts are made in such large quantities that they can be thoroughly tested in advance of manufacture , the cost of making these is very low when it is divided by the total number of parts manufactrued.You can now appreciate the following four design categories :(1)failure of the part would endanger human life ,or the part ismade in extremely large quantities ;consequently, an elaborate testingprogram is justified during design .(2)the part is made in large enough quantities so that a moderate serues of tests is feasible.(3)The part is made in such small quantities that testing is not justified at all ; or the design must be completed so rapidlly that there is not enough time for testing.(4) The part has already been designed, manufactured, and tested and found to be unsatisfactory. Analysis is required to understand why the part is unsatisfactory and what to do to improve it .It is with the last three categories that we shall be mostly concerned.this means that the designer will usually have only published values of yield strenth , ultimate strength,and percentage elongation . with this meager information the engieer is expected to design against static and dynamic loads, biaxial and triaxial stress states , high and low temperatures,and large and small parts! The data usually available for design have been obtained from the simple tension test , where the load was applied gradually and the strain given time to develop. Yet these same data must be used in designing parts with complicated dynamic loads applied thousands of times per minute . no wonder machine parts sometimes fail.To sum up, the fundamental problem of the designer is to use the simple tension test data and relate them to the strength of the part , regardless of the stress or the loading situation.It is possible for two metal to have exactly the same strength and hardness, yet one of these metals may have a supeior ability to aborb overloads, because of the property called ductility. Dutility is measured by the percentage elongation which occurs in the material at frature. The usual divding line between ductility and brittleness is 5 percent elongation. Amaterial having less than 5 percent elongation at fracture is said to bebrittle, while one having more is said to be ductile.The elongation of a material is usuallu measured over 50mm gauge length.siece this did not a measure of the actual strain, another method of determining ductility is sometimes used . after the speciman has been fractured, measurements are made of the area of the cross section at the fracture. Ductility can then be expressed as the percentage reduction in cross sectional area.The characteristic of a ductile material which permits it to aborb largeoverloads is an additional safety factot in design. Ductility is also important because it is a measure of that property of a material which permits it to be cold-worked .such operations as bending and drawing are metal-processing operations which require ductile materials.When a materals is to be selected to resist wear , erosion ,or plastic deformaton, hardness is generally the most important property. Several methods of hardness testing are available, depending upon which particular property is most desired. The four hardness numbers in greatest usse are the Brinell, Rockwell,Vickers, and Knoop.Most hardness-testing systems employ a standard load which is applied to a ball or pyramid in contact with the material to be tested. The hardness is an easy property to measure , because the test is nondestructive and test specimens are not required . usually the test can be conducted directly on actual machine element .Virtually all machines contain shafts. The most common shape for shafts is circular and the cross section can be either solid or hollow (hollow shafts can result in weight savings). Rectangular shafts are sometimes used ,as in screw driver bladers ,socket wrenches and control knob stem.A shaft must have adequate torsional strength to transmit torque and not be over stressed. If must also be torsionally stiff enough so that one mounted component does not deviate excessively from its original angular position relative to a second component mounted on the same shaft. Generally speaking,the angle of twist should not exceed one degree in a shaft length equal to 20 diameters.Shafts are mounted in bearing and transmit power through such device as gears, pulleys,cams and clutches. These devices introduce forces which attempt to bend the shaft;hence, tha shaft must be rigid enough to prevent overloading of the supporting bearings ,in general, the bending deflection of a shaft should not exceed 0.01 in per ft of length between bearing supports.In addition .the shaft must be able to sustain a combination of bending and torsional loads. Thus an equivalent load must be considered which takes into account both torsion and bending . also ,the allowable stress must contain a factor of safety which includes fatigue, since torsional and bending stress reversals occur.For fiameters less than 3 in ,the usual shaft material is cold-rolled steel containing about 0.4 percent carbon. Shafts ate either cold-rolled or forged in sizes from 3in. to 5 in. for sizes above 5in. shafts are forged and machined to size . plastic shafts are widely used for light load applications . one advantage of using plastic is safty in electrical applications, since plastic is a poor confuctor of electricity.Components such as gears and pulleys are mounted on shafts by means of key. The design of the key and the corresponding keyway in the shaft must be properly evaluated. For example, stress concentrations occur in shafts due to keyways , and the material removed to form the keyway further weakens the shaft.If shafts are run at critical speeds , severe vibrations can occur which can seriously damage a machine .it is important to know the magnitude of these critical speeds so that they can be avoided. As a general rule of thumb , the difference betweem the operating speed and the critical speed should be at least 20 percent.Many shafts are supported by three or more bearings, which means that the problem is statically indeterminate .text on strenth of materials give methods of soving such problems. The design effort should be in keeping with the economics of a given situation , for example , if one line shaft supported by three or more bearings id needed , it probably would be cheaper to make conservative assumptions as to moments and design it as though it were determinate . the extra cost of an oversize shaft may be less than the extra cost of an elaborate design analysis.Another important aspect of shaft design is the method of directly connecting one shaft to another , this is accomplished by devices such as rigid and flexiable couplings.A coupling is a device for connecting the ends of adjacent shafts. In machine construction , couplings are used to effect a semipermanent connection between adjacent rotating shafts , the connection is permanent in the sense that it is not meant to be broken during the useful life of the machinem , but it can be broken and restored in an emergency or when worn parts are replaced.There are several types of shaft couplings, their characteristics depend on the purpose for which they are used , if an exceptionally long shaft is required in a manufacturing plant or a propeller shaft on a ship , it is made in sections that are coupled together with rigid couplings. A common type of rigid coupling consists of two mating radial flanges that are attached by key driven hubs to the ends of adjacent shaft sections and bolted together through the flanges to form a rigid connection. Alignment of the connected shafts in usually effected by means of a rabbet joint on the face of the flanges.In connecting shafts belonging to separate device ( such as an electric motor and a gearbox),precise aligning of the shafts is difficult and a fkexible coupling is used . this coupling connects the shafts in such a way as to minimize the harmful effects of shafts misalignment of loads and to move freely(float) in the axial diection without interfering with one another .flexiable couplings can also serve to reduce the intensity of shock loads and vibrations transmitted from one shaft to another .中文翻译机械运动和动力学运动学的基本目的是去设计一个机械零件的理想运动,然后再用数学的方法去描绘该零件的位置,速度和加速度,再运用这些参数来设计零件。
机械专业外文文献翻译

利用CAD / CAM/ CAE系统开发操纵机器人H.S.李*,S.E.张华为技术学院,电力机械工程,云林,台湾,中国摘要在这项研究中,需要开发用于机器人操作臂的CAD/CAE/CAM集成系统。
通过变换矩阵,利用D-H坐标系变换方法对机器人的位姿进行分析,我们使用MATAB软件对其进行计算。
一般来说,利用PRO/E对机械臂的参数进行实体化建模,用Pro / Mechanical软体模拟动态仿真和工作空间,MasterCAM用来实现切削模拟仿真,而最终的模型用CNC数控铣床制造出来。
这样,一个用于机器人操作臂的CAD/CAE/CAM集成系统便开发出来了。
我们用一个范例来验证这种设计,分析以及制造的结果的正确性。
该集成系统不仅促进机器人的生产自动化功能,而且还简化了机械臂的CAD / CAE / CAM的分析过程。
这种集成系统是用于开发一个实用的计算机辅助机构设计课程的教学辅助工具。
©2003由Elsevier B.V.出版关键词:CAD / CAE/ CAM;机械臂;Denavit,Hartenberg坐标系变换引言许多研究已涉及到的CAD / CAE/ CAM集成系统的原理。
吕[1]讨论了平面五杆受电弓的运动学分析并设计制造了基于此弓的机械手。
通过研究五杆受电弓的运动性能,设计出一款简单的控制器来对机械手进行控制。
李某和陈某[2]描述了一个自动升降轮椅固定装置内的全尺寸货车的开发。
开发的过程中,包括机制的概念设计,运动仿真,工程分析,原型开发和测试。
周[3]使用参数化CAD系统的实体模型表达设计理念。
首先开发的是模具,其次是基于CAM系统的模型。
通过与产业界的合作,对试模调整,粉末形成,烧结,烧结后处理在专业的粉末冶金工厂进行了实验。
徐[4]在UG2通用CAD / CAM系统的基础上通过将注塑模具的CAD/CAM软件与注塑模具CAE软件集成建立了一个注塑用CAD / CAE/ CAM系统。
- 1、下载文档前请自行甄别文档内容的完整性,平台不提供额外的编辑、内容补充、找答案等附加服务。
- 2、"仅部分预览"的文档,不可在线预览部分如存在完整性等问题,可反馈申请退款(可完整预览的文档不适用该条件!)。
- 3、如文档侵犯您的权益,请联系客服反馈,我们会尽快为您处理(人工客服工作时间:9:00-18:30)。
此文档word版本下载后可任意编辑修改原文Kinematics and dynamics of machineryOne princple aim of kinemarics is to creat the designed motions of the subject mechanical parts and then mathematically compute the positions, velocities ,and accelerations ,which those motions will creat on the parts. Since ,for most earthbound mechanical systems ,the mass remains essentially constant with time,defining the accelerations as a function of time then also defines the dynamic forces as a function of time. Stress,in turn, will be a function of both applied and inerials forces . since engineering design is charged with creating systems which will not fail during their expected service life,the goal is to keep stresses within acceptable limits for the materials chosen and the environmental conditions encountered. This obvisely requies that all system forces be defined and kept within desired limits. In mechinery , the largest forces encountered are often those due to the dynamics of the machine itself. These dynamic forces are proportional to acceletation, which brings us back to kinematics ,the foundation of mechanical design. Very basic and early decisions in the design process invovling kinematics wii prove troublesome and perform badly.Any mechanical system can be classified according to the number of degree of freedom which it possesses.the systems DOF is equal to the number of independent parameters which are needed to uniquely define its posion in space at any instant of time.A rigid body free to move within a reference frame will ,in the general case, have complex motoin, which is simultaneous combination of rotation and translation. In three-dimensional space , there may be rotation about any axis and also simultaneous translation which can be resoled into componention along three axes, in a plane ,or two-dimentional space ,complex motion becomes a combination of simultaneous along two axes in the plane. For simplicity ,we will limit our present discusstions to the case of planar motion:Pure rotation the body pessesses one point (center of rotation)which has no motion with respect to the stationary frame of reference. All other points on the body describe arcs about that center. A reference line drawn on the body through the center changes only its angulai orientation.Pure translation all points on the body describe parallel paths. A reference line drawn on the body changes its linear posion but does not change its angular oriention.Complex motion a simulaneous combination of rotion and translationm . any reference line drawn on the body will change both its linear pisition and its angular orientation. Points on the body will travel non-parallel paths ,and there will be , at every instant , a center of rotation , which will continuously change location.Linkages are the bacis building blocks of all mechanisms. All common forms of mechanisms (cams , gears ,belts , chains ) are in fact variations of linkages. Linkages are made up of links and kinematic pairs.A link is an (assumed)rigid body which possesses at least two or more links (at their nodes), which connection allows some motion, or potential motion,between the connected links.The term lower pair is used tohe moving parts .we next want te use newton’s second law to caculate the dynamic forces, but to do so we need to know the masses of all the moving parts which have these known acceletations. These parts do not exit yet ! as with any design in order to make a first pass at the caculation . we will then have to itnerate to better an better solutions as we generate more information.A first estimate of your parts’masses can be obtained by assuming some reasonable shapes and size for all the parts and choosing approriate materials. Then caculate the volume of each part and multipy its volume by material’s mass density (not weight density ) to obtain a first approximation of its mass . these mass values can then be used in Newton’s equation.How will we know whether our chosen sizes and shapes of links are even acceptable, let alone optimal ? unfortunately , we will not know untill we have carried the computations all the way through a complete stress and deflection analysis of the parts. It it often the case ,especially with long , thin elements such as shafts or slender links , that the deflections of the parts, redesign them ,and repeat the force ,stress ,and deflection analysis . design is , unavoidably ,an iterative process .It is also worth nothing that ,unlike a static force situation in which a failed design might be fixed by adding more mass to the part to strenthen it ,to do so in a dynamic force situation can have a deleterious effect . more mass with the same acceleration will generate even higher forces and thus higher stresses ! the machine desiger often need to remove mass (in the right places) form parts in order to reduce the stesses and deflections due to F=ma, thus the designer needs to have a good understanding of both material properties and stess and deflection analysis to properlyshape and size parts for minimum mass while maximzing the strength and stiffness needed to withstand the dynamic forces.One of the primary considerations in designing any machine or strucre is that the strength must be sufficiently greater than the stress to assure both safety and reliability. To assure that mechanical parts do not fail in service ,it is necessary to learn why they sometimes do fail. Then we shall be able to relate the stresses with the strenths to achieve safety .Ideally, in designing any machine element,the engineer should have at his disposal should have been made on speciments having the same heat treatment ,surface roughness ,and size as the element he prosses to design ;and the tests should be made under exactly the same loadingconditions as the part will experience in service . this means that ,if the part is to experience a bending and torsion,it should be tested under combined bending and torsion. Such tests will provide very useful and precise information . they tell the engineer what factor of safety to use and what the reliability is for a given service life .whenever such data are available for design purposes,the engineer can be assure that he is doing the best justified if failure of the part may endanger human life ,or if the part is manufactured in sufficiently large quantities. Automobiles and refrigrerators, for example, have very good reliabilities because the parts are made in such large quantities that they can be thoroughly tested in advance of manufacture , the cost of making these is very low when it is divided by the total number of parts manufactrued.You can now appreciate the following four design categories :(1)failure of the part would endanger human life ,or the part ismade in extremely large quantities ;consequently, an elaborate testingprogram is justified during design .(2)the part is made in large enough quantities so that a moderate serues of tests is feasible.(3)The part is made in such small quantities that testing is not justified at all ; or the design must be completed so rapidlly that there is not enough time for testing.(4) The part has already been designed, manufactured, and tested and found to be unsatisfactory. Analysis is required to understand why the part is unsatisfactory and what to do to improve it .It is with the last three categories that we shall be mostly concerned.this means that the designer will usually have only published values of yield strenth , ultimate strength,and percentage elongation . with this meager information the engieer is expected to design against static and dynamic loads, biaxial and triaxial stress states , high and low temperatures,and large and small parts! The data usually available for design have been obtained from the simple tension test , where the load was applied gradually and the strain given time to develop. Yet these same data must be used in designing parts with complicated dynamic loads applied thousands of times per minute . no wonder machine parts sometimes fail.To sum up, the fundamental problem of the designer is to use the simple tension test data and relate them to the strength of the part , regardless of the stress or the loading situation.It is possible for two metal to have exactly the same strength and hardness, yet one of these metals may have a supeior ability to aborb overloads, because of the property called ductility. Dutility is measured by the percentage elongation which occurs in the material at frature. The usual divding line between ductility and brittleness is 5 percent elongation. Amaterial having less than 5 percent elongation at fracture is said to bebrittle, while one having more is said to be ductile.The elongation of a material is usuallu measured over 50mm gauge length.siece this did nota measure of the actual strain, another method of determining ductility is sometimes used . after the speciman has been fractured, measurements are made of the area of the cross section at the fracture. Ductility can then be expressed as the percentage reduction in cross sectional area.The characteristic of a ductile material which permits it to aborb largeoverloads is an additional safety factot in design. Ductility is also important because it is a measure of that property of a material which permits it to be cold-worked .such operations as bending and drawing are metal-processing operations which require ductile materials.When a materals is to be selected to resist wear , erosion ,or plastic deformaton, hardness is generally the most important property. Several methods of hardness testing are available, depending upon which particular property is most desired. The four hardness numbers in greatest usse are the Brinell, Rockwell,Vickers, and Knoop.Most hardness-testing systems employ a standard load which is applied to a ball or pyramid in contact with the material to be tested. The hardness is an easy property to measure , because the test is nondestructive and test specimens are not required . usually the test can be conducted directly on actual machine element .Virtually all machines contain shafts. The most common shape for shafts is circular and the cross section can be either solid or hollow (hollow shafts can result in weight savings). Rectangular shafts are sometimes used ,as in screw driver bladers ,socket wrenches and control knob stem.A shaft must have adequate torsional strength to transmit torque and not be over stressed. If must also be torsionally stiff enough so that one mounted component does not deviate excessively from its original angular position relative to a second component mounted on the same shaft. Generally speaking,the of length between bearing supports.In addition .the shaft must be able to sustain a combination of bending and torsional loads. Thus an equivalent load must be considered which takes into account both torsion and bending . also ,the allowable stress must contain a factor of safety which includes fatigue, since torsional and bending stress reversals occur.For fiameters less than 3 in ,the usual shaft material is cold-rolled steel containing about 0.4 percent carbon. Shafts ate either cold-rolled or forged in sizes from 3in. to 5 in. for sizes above 5 in. shafts are forged and machined to size . plastic shafts are widely used for light load applications . one advantage of using plastic is safty in electrical applications, since plastic is a poor confuctor of electricity.Components such as gears and pulleys are mounted on shafts by means of key. The design of the key and the corresponding keyway in the shaft must be properly evaluated. For example, stress concentrations occur in shafts due to keyways , and the material removed to form thekeyway further weakens the shaft.If shafts are run at critical speeds , severe vibrations can occur which can seriously damage a machine .it is important to know the magnitude of these critical speeds so that they can be avoided. As a general rule of thumb , the difference betweem the operating speed and the critical speed should be at least 20 percent.Many shafts are supported by three or more bearings, which means that the problem is statically indeterminate .text on strenth of materials give methods of soving such problems. The design effort should be in keeping with the economics of a given situation , for example , if one line shaft supported by three or more bearings id needed , it probably would be cheaper to make conservative assumptions as to moments and design it as though it were determinate . the extra cost of an oversize shaft may be less than the extra cost of an elaborate design analysis.Another important aspect of shaft design is the method of directly connecting one shaft to another , this is accomplished by devices such as rigid and flexiable couplings.A coupling is a device for connecting the ends of adjacent shafts. In machine construction , couplings are used to effect a semipermanent connection between adjacent rotating shafts , the connection is permanent in the sense that it is not meant to be broken during the useful life of the machinem , but it can be broken and restored in an emergency or when worn parts are replaced.There are several types of shaft couplings, their characteristics depend on the purpose for which they are used , if an exceptionally long shaft is required in a manufacturing plant or a propeller shaft on a ship , it is made in sections that are coupled together with rigid couplings. A common type of rigid coupling consists of two mating radial flanges that are attached by key driven hubs to the ends of adjacent shaft sections and bolted together through the flanges to form a rigid connection. Alignment of the connected shafts in usually effected by means of a rabbet joint on the face of the flanges.In connecting shafts belonging to separate device ( such as an electric motor and a gearbox),precise aligning of the shafts is difficult and a fkexible coupling is used . this coupling connects the shafts in such a way as to minimize the harmful effects of shafts misalignment of loads and to move freely(float) in the axial diection without interfering with one another . flexiable couplings can also serve to reduce the intensity of shock loads and vibrations transmitted from one shaft to another .译文机械运动和动力学运动学的基本目的是去设计一个机械零件的理想运动,然后再用数学的方法去描绘该零件的位置,速度和加速度,再运用这些参数来设计零件。