ADF-JDS-Paper
兄弟MFC-8460N_8860DN_DCP-8060维修手册
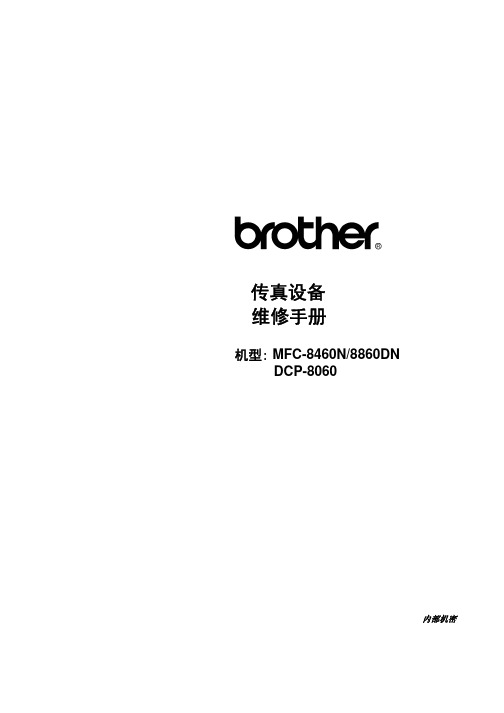
纤维测定方法NDF-ADF-ADL

步骤第一循环(a) 滤袋和样品的准备1) 样品准备:将待测样品烘干后过40目和60目筛(大于60目小于40目)2) 用耐溶剂的记号笔给滤袋编号。
3) 直接准确称取1.0 g 左右制备好的样品(m ) 于滤袋中。
4) 在距离滤袋上边缘大约5 mm用封口机封口。
然后将样品在滤袋中展平,均匀分布。
封口后滤袋和样品的总质量位M,计算出封口后空滤袋的质量(m1=M-m)5) 至少取一个空白滤袋(C1) C1 为空白袋子校正系数(烘干后质量m3/原来质量m0),同时做空白测定。
6) 一次最多可以在滤袋架上放24个滤袋。
无论放置滤袋数量多少,9层滤袋架上托盘要全部使用,每层放三个滤袋。
层与层之间错开120度。
然后将装有滤袋的支架放入纤维分析仪消煮器中,然后在顶部将金属压锤放上,以确保消煮过程中不浮起。
(b) 向2000 mL中性洗涤剂溶液中加入无水亚硫酸钠20 g (0.5 g/50 mL ND 溶液) 和4.0 mL 热稳定α-淀粉酶并保证无水亚硫酸钠在溶液中充分溶解。
然后将上述溶液加入消煮器中。
(c) 打开搅拌和加热开关,确保滤袋支架搅拌正常。
盖上盖子并完全密封好。
仪器将加热并维持溶液温度100°C。
处理时间75 min,包括加热升温时间。
(d) 消煮结束,关上加热和搅拌开关,打开排液阀(开始要慢一点),在打开盖子之前一定将热的溶液排完。
警示:消煮器中的溶液是有压力的。
在打开盖子之前一定将废液阀打开以释放压力。
确保废液排放管与废液容器安全连接。
(e) 溶液排完后,打开盖子,关闭排液阀,加2000 mL 预先加热好的(85°C~90°C) 去离子水,并且第1和第2次淋洗时同时加4.0 mL α-淀粉酶,放下盖子,但不旋紧。
打开搅拌开关(不打开加热开关)搅拌3~5 min。
排掉废液,重复2次,共淋洗3次。
(f) 最后一次淋洗后,加冷的去离子水以操作和使冷却容器,为下轮测定做好准备。
美国反倾销调查问卷D卷填写方法解析

美国反倾销调查问卷D卷填写方法解析作者:严光普来源:《对外经贸》2017年第01期[摘要]在美国贸易保护动作持续密集、中国出口企业面临常态贸易摩擦的背景下,本文详细介绍了美国常用贸易救济手段之一——反倾销其调查问卷D卷的内容,通过示例分析并系统讲解了D卷的填写方法,以期为遭遇美国反倾销调查的中国企业应诉提供详尽的方法参考。
[关键词]反倾销;替代国;非市场经济[中图分类号]F7411[文献标识码]A[文章编号]2095-3283(2017)01-0026-08[作者简介]严光普(1979-),男,陕西韩城人,对外经贸大学在职研究生,研究方向:国际贸易。
当前,中国对美出口企业正面临内外交困的局面。
外部:自美国奥巴马政府提出并实施重振美国制造业计划以来,美国对中国出口企业频频挥舞反倾销大棒。
内部:中国国内经济增速放缓,市场有效需求减少并改变。
内外因素叠加,中国对美出口企业尤其是传统产品制造企业面临着严重的生存挑战。
中国“一带一路”战略带来的政策效应尚需时日,如何走出制造业困境是诸多出口企业共同面临的长期问题。
而当下最亟待解决的问题是如何跨越反倾销壁垒。
为了帮助中国企业应对反倾销带来的挑战,本文基于应诉方视角,详细解析美国反倾销调查中成本问卷即D卷的填写方法。
以期能对遭遇反倾销调查的中国出口企业带来一些启发和帮助。
一、美国反倾销调查问卷D卷介绍从形式上看,D卷包括标准问卷和补充问卷。
标准问卷格式问题统一,并附有标准格式表格。
在美国商务部调查开始阶段,标准问卷作为首次问卷发放给应诉企业。
补充问卷没有统一格式,是基于标准问卷以及原告的评议由负责具体案件的调查官编撰的问卷。
在一次反倾销调查中,美国商务部会发放一到六甚至更多次的补充问卷。
从内容上看,D卷包括要求报告耗量的主问卷和要求展示成本勾稽的附属问卷。
D卷包含以下内容[1]:I问卷填写一般性指导。
说明生产要素报告方法、报告期间。
II描述涉案产品生产流程。
III客户提供投入情况报告。
美国FDA要求的DMF文件格式

DMF格式FDA要求此文件以8.5英寸*11英寸的纸张提交。
如遇平面布置图,工艺流程图,或批记录等较大纸张,需将这些页折成8.5英寸*11英寸装订(也可以用A4纸),此文件中所含的所有资料需以英文写,如原文非英文,须将原文稿及英文搞一并提交。
文件每一页须标明页码及日期。
(月/年)该申请须递交给FDA的CDER或CVM,一式两份。
公司的美国代理及制造商各保留副本。
SECTION A:地址文件ADDRESS FILE1. 企业地址提供地址,联系方式2. 生产地址提供地址,联系方式3. 相关代理3.1 本国联络人指出本国联络人,联系方式3.2 美国代理FDA要求国外生产商在美国指定一个文件代理,须明确该代理的职责。
联系方式。
联系方式应包括:名称,国家,省市,县,街道门牌号,电话,传真,电子邮件地址,甚至该原料药生产设施注册登记号。
对无菌原料药应包括进行无菌处理的区域。
SECTION B:承诺声明STA TEMENT of COMMITMENT我们承诺严格按照文件所描述的生产条件及规程生产***产品,我们承诺在生产操作中遵守cGMP.没有与文件描述不一致的地方,任何重大变更都将呈报FDA及该DMF的授权引用人征得其审核和批准。
文件每年修正一次,任何小的变化都应在修正中显示出来。
We hereby commit to producing strictly according to manufacturing conditions and procedures described in the DMF as well as cGMP.No deviation of description in this document is permitted.Any major amendment will be submitted to FDA and also submitted to the person(s) authorized to refer to the document for their review and approval.我们特此证明,我们不会在任何情况下接受违反联邦食品,药品和化妆品法案1992年修订本501(a)或(b)与本申请文件有关部分的人的服务。
一种混合的信用卡欺诈检测模型

本栏目责任编辑:梁书计算机工程应用技术一种混合的信用卡欺诈检测模型毛铭泽(同济大学电子与信息工程学院计算机科学与技术系,上海201804)摘要:信用卡欺诈检测是一个重要的问题,为了提升对于真实世界的信用卡欺诈数据的识别率,提出了一种混合的信用卡欺诈检测模型AWFD (Anomaly weight of credit card fraud detection ),首先通过异常检测的方法将数据划分为可信和异常数据,然后利用半监督的方法训练一个集成模型,最终再利用异常检测进一步剔除检测结果中的异常结果。
AWFD 在保障对于可信数据的学习效果上,通过半监督集成学习的方法,利用异常数据进一步扩充集成模型的多样性,并将异常检测和集成模型融合。
实验结果表明,比起一些传统的机器学习方法,AWFD 可以提高整体的信用卡欺诈检测的识别率。
关键词:信用卡欺诈检测;异常检测;半监督;集成学习;多样性中图分类号:TP311文献标识码:A文章编号:1009-3044(2021)02-0194-03开放科学(资源服务)标识码(OSID ):A Hybrid Credit Card Fraud Detection Model MAO Ming-ze(Department of Computer Science and Technology,College of Electronics and Information Engineering,Tongji University,Shang⁃hai 201804,China)Abstract :Credit card fraud detection is a serious problem.In order to improve the recognition rate of real-world credit card fraud data,a hybrid credit card fraud detection model AWFD (Anomaly weight of credit card fraud detection)is proposed.Firstly,the da⁃ta is divided into trusted and abnormal data by anomaly detection method,and then an ensemble model is trained by semi-super⁃vised method.Finally,anomaly detection is used to further eliminate the abnormal results in the detection results.On the basis of guaranteeing the learning effect of trusted data,AWFD uses the abnormal data to further expand the diversity of the ensemble mod⁃el by semi-supervised ensemble learning method,and integrates the anomaly detection and the ensemble model.The experimental results show that AWFD can improve the overall recognition rate of credit card fraud detection compared with some traditional ma⁃chine learning methods.Key words :credit card fraud detection;anomaly detection;semi-supervised;ensemble learning;diversity 由于社会的不断发展,人的消费需求也在不断上升,随之而来的支付手段的改变,导致信用卡欺诈问题日趋严重,每年会导致数十亿美元的损失[1],因此对于信用卡欺诈检测问题的研究也受到了广泛的关注[5-6],有许多学者从不同的角度研究这一问题,例如:有从数据不均衡角度研究采样问题的[2],有从模型融合角度研究的[1],也有从特征工程角度研究该问题的[3-10]。
铁姆肯公司供应商要求手册第九版说明书

供应商要求手册第九版铁姆肯公司标准 29.1目录前言/简介 (1)标准要求–质量 (2)1.0 供应商最低要求 (4)1.1 简介 (4)1.2 供应商质量系统要求 (4)1.3 产品检验 (4)1.4 不合格(偏离)产品 (5)1.5 设计和过程变更的管理 (6)1.6 采购产品的提交和批准过程 (7)1.7 测量系统分析 (7)1.8 样品提交要求 (7)1.9 文件、证书和数据要求 (8)1.10 有害材料 - 化学品安全说明书 (8)1.11 发运和包装要求 (8)1.12 供应链要求 (8)1.13 供应商材料的追溯性 (9)1.14 材料质保书数据库 (9)1.15 控制项目 ( ) 部件和特殊项目或过程..... .. (9)1.16 记录 (10)1.17 供应商评估和过程 (10)1.18 供应商升级过程 (11)1.19 供应商控制发运 (11)1.20 供应商安全投产 (11)2.0 供应商发展和推荐的最佳实践 (11)2.1 前期产品质量策划和预防 (12)2.2 目标设定和问题解决 (12)2.3 成本削减方针 (13)2.4 费用索赔过程 (13)2.5 防错 (13)2.6 统计技术 (13)2.7 持续改善过程 (14)2.8 环境、健康和安全 (14)3.0 供应商质量保证航空规定 (15)3.1 抽样计划要求 (15)3.2 接受权威媒体 (15)3.3 检验和测试报告 (15)3.4 出货产品合格证 (15)3.5 首件检验 (15)3.6 可追溯性 (15)3.7 文件保留 (16)3.8 变更批准 (16)3.9 材料批准委员会授权 (16)3.10 政府财产 (16)3.11 访问权限 (16)3.12 符合 DFARS 美国国防联邦采购条例增补条例(252.225-7014 优先采购美国国产特种金属)要求的一致性Alternate I (16)3.13 DFARS 252.225-7016对钢球和滚子的限制 (18)3.14 NADCAP 对特殊过程的要求 (19)3.15 外物损坏 (19)术语[黑体字] (19)前言/简介供应商应对其产品及服务的质量负责。
东芝复印机英文缩写说明

东芝英文缩写说明ADF ........................................ 自动输稿器ADU ........................................ 自动双面器APS ........................................ 自动纸型选择AMS ........................................ 自动倍率选择APC ........................................ 自动电源控制API ........................................ 应用程序接口BYPASS ........................................ 旁路(手送供纸)CCD ........................................ 电荷耦合器/光电转换器CM ........................................ 纸盒组件CODEC ........................................ 编码解码器DDNS ........................................ 动态域名服务DF ........................................ 输稿器DRAM ........................................ 动态随机存储器DPI ........................................ 点/英寸Firmware ........................................ 固化程序FQDN ........................................ 完全合格域名HPF ........................................ 高通滤波器HVPS ........................................ 高压板HSYNC ........................................(激光单元)水平同步检测IGBT ........................................ 绝缘栅双极性晶体管I/F ........................................ 接口IPC ........................................(复印机与整理器之间)接口板IVSYNC ........................................ 图象垂直同步LDAP ........................................ 轻量目录存取协议LCD ........................................ 液晶显示屏LED ........................................ 发光二极管LSI ........................................ 大规模集成电路LSU ........................................ 激光单元LVDS ........................................ 低电压差分信号LVPS ........................................ 低压电源板NCP ........................................ Netware 核心协议NDS ........................................ Netware 目录服务NVRAM ........................................ 非易失性随机访问存储器MIB ........................................ 管理信息基础系统MIME ........................................ 多用途网际邮件扩充协议PLL ........................................ 相位锁定环路PM ........................................ 定期保养PFP ........................................ 供纸工作台PWM ........................................ 脉冲宽度调制RADF ........................................ 翻转(双面)自动输稿器RFC ........................................ 请求注解RTC ........................................ 实时时钟SFB ........................................ 旁路(手送)供纸SLP ........................................ 服务定位协议SNMP ........................................ 简单网络管理协议SRAM ........................................ 静态随机存储器STP ........................................ 装订器WINS ........................................ Windows 网名服务英文缩写说明。
纸和纸板 耐脂度的测定 第3部分:松节油法-最新国标
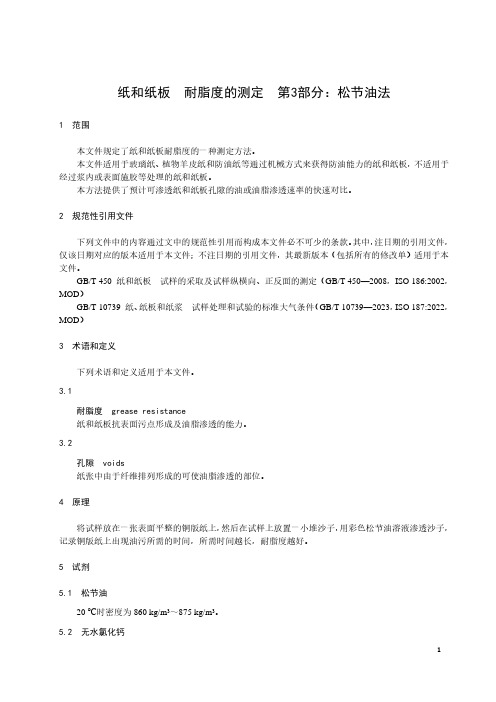
纸和纸板耐脂度的测定第3部分:松节油法1 范围本文件规定了纸和纸板耐脂度的一种测定方法。
本文件适用于玻璃纸、植物羊皮纸和防油纸等通过机械方式来获得防油能力的纸和纸板,不适用于经过浆内或表面施胶等处理的纸和纸板。
本方法提供了预计可渗透纸和纸板孔隙的油或油脂渗透速率的快速对比。
2 规范性引用文件下列文件中的内容通过文中的规范性引用而构成本文件必不可少的条款。
其中,注日期的引用文件,仅该日期对应的版本适用于本文件;不注日期的引用文件,其最新版本(包括所有的修改单)适用于本文件。
GB/T 450 纸和纸板试样的采取及试样纵横向、正反面的测定(GB/T 450—2008,ISO 186:2002,MOD)GB/T 10739 纸、纸板和纸浆试样处理和试验的标准大气条件(GB/T 10739—2023,ISO 187:2022,MOD)3 术语和定义下列术语和定义适用于本文件。
3.1耐脂度grease resistance纸和纸板抗表面污点形成及油脂渗透的能力。
3.2孔隙 voids纸张中由于纤维排列形成的可使油脂渗透的部位。
4 原理将试样放在一张表面平整的铜版纸上,然后在试样上放置一小堆沙子,用彩色松节油溶液渗透沙子,记录铜版纸上出现油污所需的时间,所需时间越长,耐脂度越好。
5 试剂5.1 松节油20 ℃时密度为860 kg/m3~875 kg/m3。
5.2 无水氯化钙分析纯。
5.3 油溶性染料例如苏丹红。
5.4 沙子测试专用沙。
沙子可通过800μm网孔筛,但截留在630μm网孔筛上。
注:沙子从某些实验室供应商处购得,例如石英砂。
5.5 测试溶液向100 mL松节油(5.1)中加入5 g无水氯化钙(5.2)和1.0 g油溶性染料(5.3),并储存于带塞玻璃瓶中。
充分摇匀,溶液至少静置10 h,偶尔摇晃。
然后在23℃±1℃下用干燥滤纸过滤,储存于玻璃瓶中。
6 仪器和设备6.1 空心管以刚性材料制成,内径25 mm,长度至少为25 mm,且两端打磨光滑。
- 1、下载文档前请自行甄别文档内容的完整性,平台不提供额外的编辑、内容补充、找答案等附加服务。
- 2、"仅部分预览"的文档,不可在线预览部分如存在完整性等问题,可反馈申请退款(可完整预览的文档不适用该条件!)。
- 3、如文档侵犯您的权益,请联系客服反馈,我们会尽快为您处理(人工客服工作时间:9:00-18:30)。
J. Dairy Sci. 95 :2567–2570/ 10.3168/jds.2011-4946© American Dairy Science Association®, 2012 .A BSTRACTT he importance of a consistent and comprehensive milking routine as a critical component of any masti-tis control program is well documented. However, as pressure on time increases, farmers are faced with 3 options: (1) adjust the milking routine to suit the time available, (2) undertake the task less thoroughly, or (3) examine which elements of the milking routine can be automated and substitute capital expenditure for labor. A study was undertaken on 5 farms in the United Kingdom in October and November 2007 to assess the effect on milking time of installing a commercial au-tomatic postmilking teat disinfection and cluster back flushing system (ADF). Two of the farms recruited for the study were intending to purchase the ADF system in the near future and 3 farms had already invested in the technology. The farms ranged in size from 120 to 550 cows and included three 90° rapid exit parlors, a herringbone parlor, and an abreast parlor. All 5 farms were visited for 2 successive milkings before the ADF was installed or disabled, and a detailed time and mo-tion analysis was undertaken. After ADF was installed or the system reactivated, a further 2 milkings were monitored. All monitored farms showed a measurable reduction in milking time after the ADF system was installed. However, the magnitude of the reduction was greater than would be expected by simply removing the elements of postmilking teat disinfection and clus-ter sanitization. The benefits of ADF are greater than simply disinfecting teats and back flushing clusters and the time saving obtained may allow a more structured milking routine that may have additional benefits in terms of mastitis prevention and control.K ey words:p ostmilking teat disinfection ,d ipping , m ilking ,t imeShort CommunicationD airy herds in Europe and North America have in-creased considerably in size over the past decade. This increase in herd size has not seen a comparative increase in staff numbers, which has resulted in a labor squeeze (Wall Street Journal, 2009). One consequence of this labor squeeze is an increase in pressure on staff through the working day and in particular at and around milk-ing time. This has resulted in many farms compromis-ing their mastitis control programs (Bradley, 2007).T he time associated with milking an individual cow (the work routine) is likely to be the largest determi-nant of the performance of the milking system, whether it is measured in terms of cows milked per hour or liters produced per hour (Baines, 2001). Farms are con-stantly examining their milking routines to streamline the operation and improve performance. However, it is important that the streamlining not occur at the expense of milk quality or udder health. Postmilking teat disinfection (PMTD) is a good example of this in practice (Pankey et al., 1984). Spraying of teats after milking using a hand-held lance has emerged as the most popular method of PMTD as dairy farms look to reduce the time spent on any element of the work routine; spraying takes about half the time of teat dip-ping (Burks et al., 2006). Although teat spraying may be quicker than teat dipping, most dairy practitioners recommend that teats be disinfected after milking by dipping. Dipping should ensure better teat coverage and better penetration of product into the teat canal. As a result, the incidence and prevalence of new IMI and bulk milk SCC are higher in herds that use spraying compared with dipping as a PMTD method (Barkema et al., 1998).M any dairy farms in the United Kingdom faced with a contagious mastitis challenge have resorted to manu-ally disinfecting the milking cluster after each animal (Bradley, 2007). Although farmers believe this practice helps to reduce cross infection, it adds considerably to the work routine, reducing milking system performance.Short communication: Effect of automatic postmilking teat disinfection and cluster flushing on the milking work routineI. O hnstad ,*1R. G. M. O lde Riekerink ,† P. H ogewerf ,‡ C. A. J. M. d e Koning ,‡ and H. W. B arkema §*T he Dairy Group, Taunton, TA1 2PX United Kingdom†G D Animal Health Service, NL-7425SB Deventer, the Netherlands‡W ageningen UR Animal Sciences Group, NL-8200AB Lelystad, the Netherlands§D epartment of Production Animal Health, Faculty of Veterinary Medicine, University of Calgary, Calgary, AB T2N 1N4, CanadaR eceived September 16, 2011.A ccepted December 3, 2011.1Corresponding author: i an.ohnstad@25672568OHNSTAD ET AL.Journal of Dairy Science Vol. 95 No. 5, 2012Dairy farmers are increasingly interested in the ap-plication of technology to replace labor to work more efficiently (Wilson, 2011). If a technological solution can be applied to automate any task within the milk-ing routine, the potential exists to improve milking system performance. Any improvement in the effi-ciency of the work routine could lead to a reduction in overall milking time, less stress on the operator and cows, or the release of time to concentrate on other essential elements of the routine. Clearly, the technol-ogy must be at least as consistent as the operator that it replaces.An automatic postmilking teat disinfection and clus-ter back flushing system (ADF ; ADF Milking Ltd., Slindon, UK) is designed to both disinfect the teat and sanitize the cluster between cows (Hogewerf et al., 2008). When the automatic cluster remover is activated, teat disinfectant is introduced into the hood of the liner while the liner is still located on the teat. As the liner is removed from the teat, disinfectant is applied to the teat surface. Once the liner is removed, the system goes through a series of flushes, alternating a peracetic acid solution with bursts of compressed air, to sanitize the liner surface. Similar systems have been described by Galton (2004) and Grindal and Priest (1989), in which the disinfectant is injected through the short milking tube or via a delivery tube within the long and short pulse tubes, respectively.Several motivations may lead a dairy farmer to invest in technology such as ADF. These include expected improvements in individual cow and bulk milk SCC (our unpublished data), reduction in the incidence rate of new IMI, and improved efficiency in the milk-ing routine. Improvements in udder health have also been described in earlier experimental studies with comparable but slightly different systems (Grindal and Priest, 1989; Galton, 2004). To quantify the poten-tial efficiency gains that could be achieved by fitting ADF, a detailed time and motion study was carried out during 20 milkings. Five dairy farms were studied during 2 consecutive milkings with and 2 consecutive milkings without an ADF installed. The means of the consecutive milking times with an ADF installed were compared with the means of the consecutive milking times without an ADF installed.A milking technology specialist from The Dairy Group (Taunton, United Kingdom) visited 5 dairy farms during October and November 2007. The 5 farms selected included 2 new ADF installations and 3 existing users of the technology. A range of milking systems was selected (Table 1). Farms A andB were new users of ADF. These farms were visited for 2 con-secutive milkings before the ADF system was installed. Once the system had been installed and commissioned, another visit was undertaken and 2 consecutive milk-ings observed. Farms C, D, and E were already users of the ADF system. These farms were visited for 2 consecutive milkings where they used the ADF system as designed. These farms were then asked to disable the ADF system and revert to their previous practice before installation of the ADF.A full analysis of every operation carried out by the milkers was undertaken, and total time associated with each task was calculated (Armstrong and Quick, 1986). A rolling record of milking time was used to assess the time associated with cow loading, teat preparation, feeding, cluster attachment, PMTD, parlor unloading, cleaning equipment surfaces, and cleaning cow stand-ings, with any time not attributed to a main task con-sidered as miscellaneous.Overall milking times for each farm without ADF installed varied between 122 and 271 min (Table 1). All values were rounded to the nearest minute. Milk-ing time after the installation of the ADF system was reduced on all 5 farms visited and varied between 99 and 219 min. However, when the data from each farm were examined, it became clear that some of the time savings were related to other elements of the milkingSHORT COMMUNICATION:AUTOMATIC DIPPING AND MILKING ROUTINE2569routine, such as loading the milking parlor, teat prepa-ration, and miscellaneous time.The saving in milking time that was directly attrib-utable to automatic dipping of teats and cluster sanita-tion ranged between 15 and 62 min (Table 1). With the exception of farm C, the reduction in time directly attributable to the installation of ADF ranged from 48 to 85% (Table 1). Although farm C demonstrated a 15-min reduction in milking time that could be directly attributable to ADF, the farmer spent an extra 5 min washing the milking equipment, resulting in only a 10-min reduction in overall milking time.Farms A and B, with reductions in milking time ap-proximately twice that expected by simply automating PMTD and cluster back flushing, both demonstrated a reduction in parlor loading time and miscellaneous time (Table 1). Although both farms A and B showed a reduction in overall milking time, time associated with teat preparation increased slightly, suggesting a more thorough cleaning.The majority of the reduction in milking time noted on farms D and E (74 and 85%, respectively) was as-sociated with the practice of PMTD and cluster back flushing. Farm E was able to spend slightly longer on teat preparation, and cow loading and miscellaneous time decreased with both farms. Farm E manually disinfected every cluster after milking when the ADF system was not installed.Of the farms visited, each farm showed a reduction in milking time following the installation of the ADF system. The potential time savings obtained on farm C was markedly less than that on other visited farms because the operator chose to spend additional time washing the external cluster surfaces. Previous studies showed a cow milking routine time reduction of 10% if PMTD was replaced by an automatic spraying system (Armstrong and Quick, 1986).It was apparent that the milking routine was more structured and less erratic when milkings were moni-tored with the ADF operating. The automation of certain elements of the milking routine potentially re-leases time for the operator to assist with cow loading and adopt a more structured, more efficient milking routine. This may explain, in part, why reductions in overall milking time were observed beyond that directly associated with dipping teats and sanitizing clusters. To quantify the labor saving from fitting ADF, an hourly labor charge of €10/h was used (I. Powell, The Dairy Group, Taunton, UK; personal communication). For the purpose of this calculation, we assumed that farms A and D used 1.3 labor units per milking (a labor unit was defined as a member of staff exclusively em-ployed for the milk harvesting process; he/she was not involved in marshalling cows, feeding calves, or other associated tasks); farms B and C used 1.0 labor unit per milking; and farm E used 2.0 labor units per milk-ing. The potential annual labor savings from reducing overall milking times ranged from €1,217 to € 17,763 per year (Table 2). When this figure was considered on a per-cow basis, the potential benefits ranged from €5 to €65 per cow.The labor saving that can be directly attributed to ADF ranged from €1,825 to €15,087 per year, with the labor saving on a per-cow basis ranging from €7 to €31 per cow (Table 2).In conclusion, the 5 farms monitored all showed a reduction in overall milking time following the installa-tion of the ADF system. When the reduction in milking time is considered, the potential to reduce labor costs exists. Reductions in overall milking time occurred be-yond that expected directly by automating PMTD and cluster flushing. We suggest that some of the additional labor saving is obtained by a more structured and or-ganized milking routine that is achieved following the automation of key components. In reality, capturing the labor saving is difficult when milking staff are paid a salary, although the reduction in milking time can be viewed as an opportunity to improve working condi-tions for staff, free up time for other tasks, or milk more animals. The scale of the benefit obtained from installing ADF was closely related to the milking rou-tine previously used and the size of the herd.Journal of Dairy Science Vol. 95 No. 5, 20122570OHNSTAD ET AL.Journal of Dairy Science Vol. 95 No. 5, 2012ACKNOWLEDGMENTSThe authors acknowledge the assistance and coopera-tion of the dairy farmers who took part in this study.REFERENCESArmstrong, D. V., and A. J. Quick. 1986. Time and motion to measuremilking parlor performance. J. Dairy Sci. 69:1169–1177.Baines, J. R. 2001. Choosing a milking parlour to minimise mastitis.Pages 39–44 in Proc. British Mastitis Conference, Stoneleigh, UK. Institute for Animal Health Compton, Compton, UK.Barkema, H. W., Y. H. Schukken, T. J. G. M. Lam, M. L. Beiboer, H.Wilmink, G. Benedictus, and A. Brand. 1998. Management prac-tices associated with low, medium, and high somatic cell counts in bulk milk. J. Dairy Sci. 81:1917–1927.Bradley, A. J. 2007. The way forward for UK mastitis control. Pages25–32 in Proc. British Mastitis Conference, Stoneleigh, UK. Crown Publishing, Lincoln, UK.Burks, T. F., L. W. Turner, and W. L. Crist. 2006. Distribution fittingand parameterization of individual operator work routine times for small dairy parlors. J. Dairy Sci. 89:2343–2352.Galton, D. M. 2004. Effects of an automatic postmilking teat dippingsystem on new intramammary infections and iodine in milk. J. Dairy Sci. 87:225–231.Grindal, R. J., and D. J. Priest. 1989. Automatic application of teatdisinfectant through the milking machine cluster. J. Dairy Res. 56:579–585.Hogewerf, P. H., A. H. Ipema, C. J. A. M. de Koning, H. J. Schuiling,B. A. Slaghuis, V. Tancin, I. Ohnstad, and H. W. Barkema. 2008. Impact of automatic teat dipping and cluster flushing system on iodine residuals, milking characteristics and teat coverage. Pages 349–356 in Mastitis Control: From Science to Practice, T. J. G. M. Lam, ed. Wageningen Academic Publishers, Wageningen, the Netherlands.Pankey, J. W., R. J. Eberhart, A. L. Cuming, R. D. Daggett, R. J.Farnsworth, and C. K. McDuff. 1984. Uptake on postmilking teat antisepsis. J. Dairy Sci. 67:1336–1353.Wall Street Journal. 2009. Got workers? Dairy farms run low on labor.Even in recession, U.S. job candidates are scarce; milk producers relying on immigrants worry about a crackdown. Accessed Sept. 16, 2011. /article/SB124890678343891639.html.Wilson, P. 2011. Decomposing variation in dairy profitability: The im-pact of output, inputs, prices, labour and management. J. Agric. Sci. 149:507–517.。