产品不良率高分析课件
产品不良分析报告表格

产品不良分析报告表格1. 引言该报告旨在对公司的产品不良情况进行分析并提供解决方案。
通过对不良产品的统计和分析,我们将揭示不良产生的原因,并提出相应的改进措施,以提高产品质量。
2. 数据搜集和分析为了获取产品不良的数据,我们对以下方面进行了调查和分析:2.1 不良产品的类型及数量我们对过去一个月的生产批次进行了不良产品的统计。
统计结果如下:产品类型不良数量A 50B 30C 20D 10总计110从上表可以看出,不良产品最多的是产品A,共有50个。
2.2 不良产品的产生原因通过对不良产品的分析和追溯,我们归纳了以下主要原因:•材料质量不合格:20%的不良产品是因为使用了不合格的材料。
•设计问题:30%的不良产品是由于产品设计存在缺陷导致。
•加工过程问题:40%的不良产品是由于生产过程中的操作失误或技术问题引起的。
•人员技术水平问题:10%的不良产品是由于操作人员技术水平不达标导致的。
2.3 不良产品的影响不良产品不仅会给公司带来经济损失,还会影响公司声誉和客户满意度。
具体影响如下:•经济损失:出现不良产品会造成材料和劳动力的浪费,增加公司成本。
•客户满意度下降:不良产品会影响客户使用体验,降低客户满意度。
•公司声誉受损:频繁出现不良产品会对公司品牌形象造成负面影响。
3. 改进方案针对以上不良产品产生的原因,我们提出了以下改进方案:3.1 材料质量管控•加强对供应商的材料质量审核和监督。
•加强对材料检验过程的把控,确保只使用符合质量标准的材料。
3.2 产品设计优化•设计部门应跟踪客户反馈和市场需求,及时修改产品设计,并通过有效的测试验证产品质量。
3.3 加强生产过程管控•加强对生产过程的监控,确保操作规范和操作人员技术水平达标。
•实施严格的生产工艺流程,避免操作失误和技术问题。
3.4 培训和技术提升•加强对操作人员的培训和技术提升,提高其技术水平和质量意识。
4. 结论通过对产品不良情况的分析,我们发现不良产品主要是由于材料质量、设计问题、加工过程和人员技术水平等多方面原因导致的。
如何降低不良率回修率ppt课件
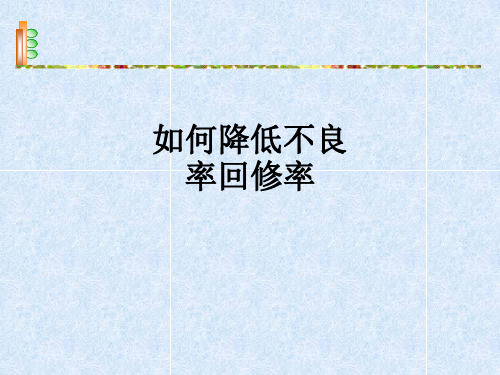
原理三:保险原理
例如冲床的操作开关必须左右手同时按住才可启动, 避免手指受伤。
原理四:对比原理
利用两个明显的差异,区别不同的地方,例如用不同 颜色区分不同的溶剂,以防止错误产生。
原理五:顺序原理
连续的工作必须按顺序才可正确完成,可明确标示顺 序号码,按顺序操作。
6
原理六:层别原理
以分门别类的方法,例如公文置放区分收文、发文及 待办等层,清楚的层别避免放错位置。
9
3
(3)不要让产品互相碰触。例如刮伤、碰伤、擦伤、撞伤等。 生产流程中要注意每一细节,绝对不让产品互相碰触,
既便加了保护层也要确定无碍,装入包装箱更要注意堆
叠有没有关系,处处都要实验求证过,确认都没有问题才 行; 综合以上三项,最好的制程还是以一个流、一贯化、 同步化的生产方式,就可合乎要求,让不良无从发生了。
4
3. 管理面:
(1)防止人为疏失产生:防错法十大原理的应用
原理一:简化原理
为防止错误发Leabharlann ,利用简化的原理,简化组装产品的螺丝为一种就好,不要太多种螺丝容易拿错。
原理二:异形原理
利用物体材料、零件的不规则形状,例如个人电脑的
各种不同的连接线,被设计成不同的插头形状及颜色,容 易找到正确的位置,也较不易犯错。
原理七:隔离原理
把不应该发生的动作或物品,分隔出来,例如冲床机 器加装隔离罩,避免作业者手伸入加工点发生危检。
原理八:自动原理
例如感应器的应用,计数器的自动计算投入数与产 出数。
7
原理九:缓和原理
为避免对产品的伤害,例如成品包装时使用泡棉保护
缓冲搬运中的碰伤。
原理十:配套原理
印刷电路板的组装,避免漏装、误装,可事先把一片 印刷电路板所要装的零件,一整套依组装顺序排列,依序 置入,可清楚查觉漏装与误装等状况。
最新smt制程不良原因及改善措施分析ppt课件
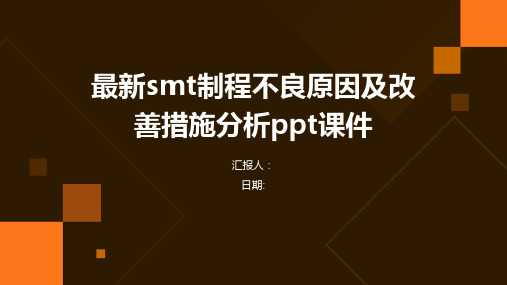
汇报人: 日期:
目录
• SMT制程概述 • SMT制程不良原因分析 • SMT制程改善措施分析 • 案例分析与实施效果评估
01
SMT制程概述
SMT制程简介
表面组装技术
SMT是表面组装技术(Surface Mounted Technology)的缩写,是一种将电 子元件直接安装在印刷电路板(PCB)表面的技术。
降低成本
SMT技术提高了生产效率 ,降低了生产成本,使得 电子产品更加普及和个性 化。
SMT制程常见问题
锡膏印刷问题:锡膏印刷是SMT制程中的关键步 骤之一,常见问题包括锡膏量不足、偏移、桥接 等,影响焊接质量。
焊接问题:焊接过程中可能出现虚焊、冷焊、焊 接不良等问题,主要原因包括温度设置不当、焊 接时间不足、PCB污染等。
元件贴装问题:元件贴装过程中可能出现元件偏 移、翻转、损坏等问题,主要原因包括设备参数 设置不当、元件供料器故障等。
针对以上问题,我们将详细介绍不良原因分析及 改善措施,以提高SMT制程的良率和生产效率。
01
SMT制程不良原因分析
设备故障导致的不良
设备老化
长时间运行的设备可能出 现磨损和老化,导致定位 不准、传输错误等不良现 象。
维护不足
设备缺乏定期维护和保养 ,可能导致精度下降、故 障率增加。
操作不当
操作人员对设备不熟悉或 操作不规范,可能引发误 操作,造成产品不良。
材料问题导致的不良
原材料缺陷
原材料本身存在缺陷,如PCB 板翘曲、元器件引脚氧化等,
影响制程质量。
储存条件不当
材料储存环境湿度过高、温度过高 或过低可能导致材料性能发生变化 。
品管不良分析方法ppt课件
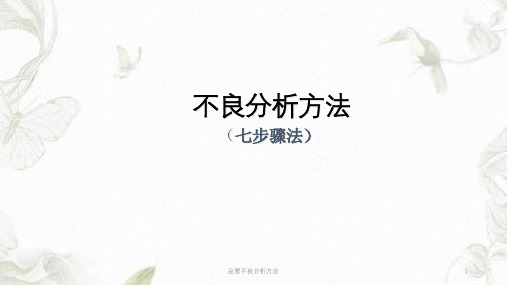
2、将现有的库存按18%进行全部检查;
完成时间:4月3日(责任人:XXX))
品管不良分析方法
9
步骤三:ቤተ መጻሕፍቲ ባይዱ定改善对策
恒久对策
恒久对策是为了彻底消除不良产生原因,防预不良再发生 而采取的一些系统有效的措施。
案例6:
封口不良恒久对策
1、将每台封口机的加热时间固定在2-2.5秒之间,制作封口机设备点检表,
1、制做喷码长度点检表,每批首件检测喷码长度并记录;2、发现喷码长度 不符的线材立即报废处理。但点检表实施过一段时间就不使用了,第二点对策 也没有实施。这样的例子太多。
制定改善对策的目的在于解决问题,而非为了搪塞客户。要那样就只是一种 形式了。
品管不良分析方法
14
步骤五:效果确认
对策实施后,必须跟进和评价对策实施的效果: 1)责任部门有没有依对策规定要求进行作业? (包括作
业方法变更、参数设置变更、材料的变更、培训的实 施等等) 2)依对策规定要求作业后 ,产品品质有没有得到改善?
的原因所采取的措施。
预防措施:为消除潜在的不合格或其它潜在的不良情
况的原因所采取的措施。
品管不良分析方法
8
步骤三:制定改善对策
暂定对策 暂定对策是指为了保证生产的一种临时应对措施, 其中包括对己生产产品的处理。
案例5: 封口不良暂定对策:
1、将不稳定的机台取替(增加新机台)
完成时间:即日(责任人:XXX)
10
步骤三:制定改善对策
比如说,在制程发生了不合格品时,想想如何做到防止再次发生。 1)仔细观察不合格现象和发生不合格原因处。 2)确定发生不合格的工位和有关的检查工位。 3)确认特定工位的作业指导书(标准)和作业内容。 4)根据结果进行以下对策。
品质不良原因分析及其改善方法PPT课件(18张)

是否在系统面存在缺陷造成不良的发生, 在程序 /流程/规范/规格/图面/SOP/SIP/BOM/设计准则 等等中未定义
四.不良分析方法
1.问题描述的要求:
1.1 不良现象的说明要明确,是什么不良(WHAT) 1.2 不良发生的地点要清楚(WHERE) 1.3 不良的生产日期或D/C要明确 (WHICH) 1.4 不良是谁通知的(WHO) 1.5 不良的比例是多少与出货的数量(HOW MANY) 1.6 不良品与良品对比图=DATA要明确
谢谢观看
3. 鉴定成本:评定产品是否满足规定的质量要求所需的费用。
4. 内部损失成本:产品交货前因不满足规定的质量要求而支 付的有关费用。
5. 外部损失成本:产品交货后因不满足规定的质量要求,导 致索赔、修理、更换或信誉损失等而支付的费用。
6. 外部质量保证成本:为提供用户要求的客观证据所支付的 费用。它包括特殊的和附加的质量保证措施、程序、数据、 证实试验和评定的费用。
1.原因与对策的一致性原则
2.明确由谁何时做什么原则(WHO TO DO WHAT BY WHEN)
3.系统水平展开原则(WHO TO DO WHAT BY WHEN)
六. 问题的持续监控
1. 系统的规范定义及控制方法的执行(打三盲) 2. CLCA的结案执行原则系统的改善与持
续执行
七.不良分析执行的定义
品质不良原因分析与改善方法 培训教材
2010/11/02
品质不良产生成本放大效应
品质损失的五个层面
第一层次:终端客户发现不良, 整机退货,客户维修==》死路一条
每二层次:加工客户发现不良, 重工/维修与停线==》损失惨重
第三层次:产出后才发现不良, 重工与报废==》痛心与无奈
产品不良率的分析方法 (1)

产品内有杂物
焊锡
焊锡操作不规范,锡量过多, 产生较多小锡块
内检 外检
没有完全敲打出杂物 敲出的杂物落入已检产品
外检再次敲打出异物 打螺丝时产生的碎屑
page
不良品案例分析
指示灯不良
来料不良 操作不良 检测时责任心不强
焊伤指示灯线 高压测试烧坏指示灯Fra bibliotekpage
不良品案例分析
螺丝组装不良
螺丝槽口不良;有混料现象 面板不良,螺丝孔过大 责任心不强,漏打、未打到位、打花
page
不良品案例分析
线套不良
操作责任心不强,出现多穿、 漏穿和穿反现象
打螺丝过程,未将线套压入产 品卡槽内
page
不良品案例分析
标贴纸不良
贴标操作手法不正确 未贴到位,被刮擦出现损伤 贴纸保存不够仔细,出现损坏
page
谢谢观赏!
产品不良率的分析方法
不良品案例分析
不良案例
内有 杂物
指示灯 不良
焊锡 不良
标贴纸 不良
螺丝组 装不良
线套 不良
page
不良品案例分析
人
焊锡不良
机器
原料
操作不熟练,手法不正确 责任心不强,未遵守“三不” 生产节拍不均匀 烙铁头损伤 焊锡机温控不稳定
松油浸泡锡丝,焊锡产生松 油渍
page
不良品案例分析
品质不良分析报告
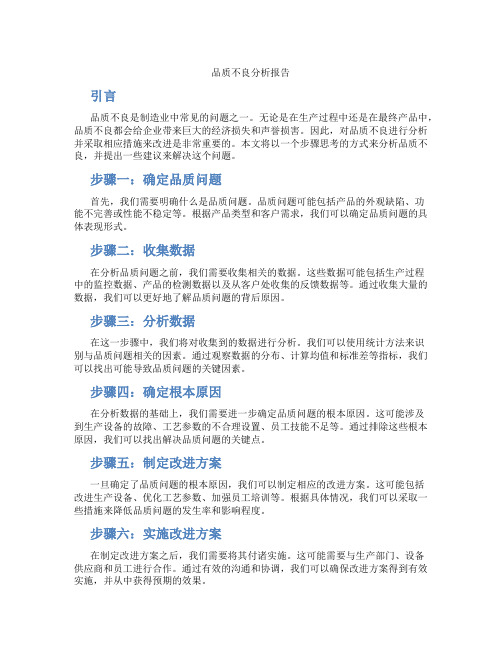
品质不良分析报告引言品质不良是制造业中常见的问题之一。
无论是在生产过程中还是在最终产品中,品质不良都会给企业带来巨大的经济损失和声誉损害。
因此,对品质不良进行分析并采取相应措施来改进是非常重要的。
本文将以一个步骤思考的方式来分析品质不良,并提出一些建议来解决这个问题。
步骤一:确定品质问题首先,我们需要明确什么是品质问题。
品质问题可能包括产品的外观缺陷、功能不完善或性能不稳定等。
根据产品类型和客户需求,我们可以确定品质问题的具体表现形式。
步骤二:收集数据在分析品质问题之前,我们需要收集相关的数据。
这些数据可能包括生产过程中的监控数据、产品的检测数据以及从客户处收集的反馈数据等。
通过收集大量的数据,我们可以更好地了解品质问题的背后原因。
步骤三:分析数据在这一步骤中,我们将对收集到的数据进行分析。
我们可以使用统计方法来识别与品质问题相关的因素。
通过观察数据的分布、计算均值和标准差等指标,我们可以找出可能导致品质问题的关键因素。
步骤四:确定根本原因在分析数据的基础上,我们需要进一步确定品质问题的根本原因。
这可能涉及到生产设备的故障、工艺参数的不合理设置、员工技能不足等。
通过排除这些根本原因,我们可以找出解决品质问题的关键点。
步骤五:制定改进方案一旦确定了品质问题的根本原因,我们可以制定相应的改进方案。
这可能包括改进生产设备、优化工艺参数、加强员工培训等。
根据具体情况,我们可以采取一些措施来降低品质问题的发生率和影响程度。
步骤六:实施改进方案在制定改进方案之后,我们需要将其付诸实施。
这可能需要与生产部门、设备供应商和员工进行合作。
通过有效的沟通和协调,我们可以确保改进方案得到有效实施,并从中获得预期的效果。
步骤七:持续改进改进品质是一个持续的过程。
一旦改进方案得到实施,我们需要不断监控和评估其效果。
如果发现新的品质问题或改进方案不起作用,我们应该及时进行调整和改进,以确保产品的品质得到持续提升。
结论品质不良是制造业中一个常见但严重的问题。
三星不良率改善案例经典.ppt
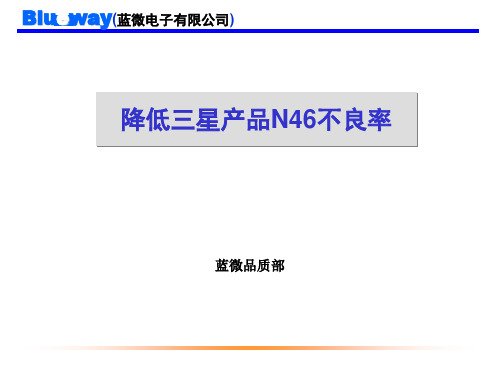
计量型
计数型 计量型
Gage R&R
DMA I C
二次元测试系统分析
Gage R&R (ANOVA) for Y
Gage name: Date of study:
Reported by: Tolerance: Misc:
MOS 镍片
DM A I C
IC 电阻
PTC
导线
Y定义
区分 不良类别(Y值)
DM A I C
不良图示
露铜不良
来 料 不 良
过孔不通
B+铜箔边缘露铜。
Y定义
区分 不良类别(Y值)
不良图示
DM A I C
导线长短不一
标准为6.50-7.10mm
制
Y1: 焊导线拉拔力 >1.0kgf
程
不
Y2: 外观品质: (1)少锡
40 400
200
20
0
0
C1
露铜不良 过孔不通 假性露铜 镍片划伤
Count
548
454
112
84
Percent
45.7
37.9
9.3
7.0
Cum %
45.7
83.6
93.0
100.0
来料占主要不良为露铜不良及过孔不通
制程不良
Pareto Chart of 制程不良
1200
100
1000
主要不良
800
DM A I C
改善KPI
38700PPM
下 降 80%
7500PPM
品质现况
改善目标
品质现况分析
制程不良率 来料不良数
48% 52%
- 1、下载文档前请自行甄别文档内容的完整性,平台不提供额外的编辑、内容补充、找答案等附加服务。
- 2、"仅部分预览"的文档,不可在线预览部分如存在完整性等问题,可反馈申请退款(可完整预览的文档不适用该条件!)。
- 3、如文档侵犯您的权益,请联系客服反馈,我们会尽快为您处理(人工客服工作时间:9:00-18:30)。
冲孔跳废料
冲头太短 模具有磁性
加长冲头 去磁
备注:粉红色字体为改善方案
间隙不当
Hale Waihona Puke 重新线割入块二:第二工程冲孔,跳料孔如图所示:
此孔易跳料
跳料的主要可能原因是:
1、冲头太短 2、模具有磁性 3、间隙太大
第二工程:冲孔、压毛边、打压线
冲孔跳废料
冲头太短 模具有磁性
加长冲头 去磁
备注:粉红色字体为改善方案
0.147% 0.004%
0.496% 0.017%
0.569% 0.394% 0.194%
0.512% 00..325850%%
0.441% 0.451%
0.278% 0.254%
00..009322%%
0.119% 0.009%
10.7-10.12 10.13-10.18 10.19-10.24 10.25-10.29 10.30-11.5 11.6-11.10
清洗环境 改善清洗环境 产品在清洗蓝中的活动空间过大 改善清洗蓝
对人员进行教育训练 教育不足
清洗
变形
冲压
操作人员 机械手
模具
调整机械手
修模
备注:红色字体为改善方案
产品压伤主要是以下两处冲孔跳料造成:
一:第一工程下料长方孔易跳料如下图所示:
跳料的主要可能原因是: 1、冲头太短 2、模具有磁性 3、间隙太大
间隙不当
重新线割入块
牙孔不良主要是牙孔缺损、烂牙、牙孔开裂。
牙孔开裂主要是此孔漏冲造成 牙孔缺损、烂牙也是此孔但具体原因尚不确定可能原因是:
1、抽孔,下模孔位偏移 2、攻牙歪斜 3、机械手放不到位 我认为是抽孔,下模孔位偏移造成的可能性较大,原因是: 在抽孔处加油后无此现象。
改善方案:1)临时对策:加油生产 2)重新割入块
谢谢大家!
▪
安全在于心细,事故出在麻痹。20.11.720.11.721:38:5221:38:52November 7, 2020
▪
加强自身建设,增强个人的休养。2020年11月7日下 午9时38分20.11.720.11.7
▪
追求至善凭技术开拓市场,凭管理增 创效益 ,凭服 务树立 形象。2020年11月7日 星期六 下午9时38分52秒21:38:5220.11.7
92.02%
300 80.00%
250
69.51%
200
60.00%
144
150
41.03%
100
100
79
50
0 变形
19 6
压伤 牙孔不良 漏冲孔 刮伤
40.00%
20.00%
3 异色
0.00%
不良数
不良累 计百分 比
10月24日至10月29日冲压制程不良项目分析
98.30%
100% 100.00%
0.115%
0.138%
0.000%
10.5-10.11 10.12-10.16 10.17-10.21 10.24-10.29 10.30-11.5 11.6-11.10
压伤不良率 变形不良率 牙孔不良不良率
由上图可以看出冲压制程各项不良率均有不同程度下降。
总不良率
不良品图
变形
变形
变形
牙孔不良
变形
220
90.00%
200
81.78%
180
80.00%
160
70.00%
140
60.00%
120
103
100
43.64% 90
80
60
39
40
20
50.00%
40.00%
30.00%
20.00%
4
10.00%
0 变形
0.00%
压伤
牙孔不良
漏冲孔
不良数
不良累 计百分 比
通过以上分析得出结论:不良率高的主要原因是变形、压伤以及牙孔不良。
▪
严格把控质量关,让生产更加有保障 。2020年11月 下午9时 38分20.11.721:38November 7, 2020
▪
重标准,严要求,安全第一。2020年11月7日 星期六 9时38分52秒21:38:527 November 2020
▪
好的事情马上就会到来,一切都是最 好的安 排。下 午9时38分52秒 下午9时38分21:38:5220.11.7
压伤不良率 变形不良率 牙孔不良不良率 由上图可以看出清洗各项不良率均有不同程度下降。
总不良率
10月5日-11月10日冲压制程不良统计
10月5日-11月10日冲压制程各主要不良率-折线图
1.200%
1.130%
1.000%
0.800%
0.600%
0.534%
0.478%
0.582%
0.400%
0.200%
变形产品
变形
变形
牙孔不良 压伤
压伤 压伤
结语
▪ 不良改善已有初步成效:
1)冲压不良率由最高时的1.13%下降到现在的0.138%. 2)清洗不良率由最高时的1.337%下降到现在的0.451%.
取得以上成绩是与各部门的积极配合是分不开的:
1)制造.品保每天利用晨会进行宣导,进行教育训练,大大提高了人员品质意识,加强了 操作人员责任感,大大降低了因人为因素而造成的大量不良.
改善进程(成果初现)—折线图 10月7日-11月10日清洗各主要不良统计
10月7日-11月10日清洗各主要不良率—折线图
1.600% 1.400% 1.200% 1.000% 0.800% 0.600% 0.400% 0.200% 0.000%
1.337% 1.218% 1.247%
0.956% 0.798% 0.804%
问 题 点 分 析 – 鱼骨图分析
教育不足
新进操作人员
机械手放料不到位
人员流动性大
清洗机故障
工作时间较长 人员较疲劳
作业人员品 质意识不足
作业人员情绪 不稳定
攻牙机故障 模具异常
四个折弯边,有一边有 一个缺囗,强度较弱
产品本身较易变形 Material(料)
作业人员取拿产品 方法不当
冲压检查方法不正确
教育不足
新进操作人员
工作时间较长 人员较疲劳
人员流动性大
作业人员情绪 不稳定
机械手放不到位
教育不足
新进操作人 员
工作时间较 长人员较疲
劳
人员流动性 大
作业人员情 绪不稳定
问题点提取及改善计划方案
组装
喷码 测牙 贴Mylar 全检 测平整度 装脆盘
插蓝 清洗过程 清洗蓝
手法不当
从清洗蓝中取出时易造成变形 新进操作人员 操作人员品质意识不足 操作人员马虎 人员流动性大
2)开发部人员对模具进行了多次检修,使压伤,牙孔不良的不良率大为降彽. 3)冲压课,生技课人员多次对机械手进行调整,大大降低了变形不良率;另外,特别值得 一提的是:组装课每班抽调一人对不良品进行修复,大大降低了变形不良率.
最后,谢谢大家的大力支持和积极配合.
▪
加强做责任心,责任到人,责任到位 才是长 久的发 展。20.11.720.11.7Saturday, November 07, 2020
41-D011880产品不良率高分析
冲压、组装、品管、生技、模具部分人员 制作:王红军
2006年11月11日
概要
目录
▪ 1. 成员结构 ▪ 2. 不良统计 ▪ 3. 不良项目分析(柏拉图) ▪ 4. 问题点分析(鱼骨图) ▪ 5. 问题点提取及改善方案 ▪ 6. 改善进程(成果初现) ▪ 7. 不良品图 ▪ 8. 结语
▪
弄虚作假要不得,踏实肯干第一名。21:38:5221:38:5221:3811/7/2020 9:38:52 PM
▪
安全象只弓,不拉它就松,要想保安 全,常 把弓弦 绷。20.11.721:38:5221:38Nov-207-N ov-20
▪
重于泰山,轻于鸿毛。21:38:5221:38:5221:38Saturday, November 07, 2020
Team 成 员 结 构
产品不良率改善小组
徐卫明、郇丛明、王红军 确立改善方针,确认改善活动
王红军
统计分析确立,表单设计,文件制作
葛玉娣、李小燕、FQC 人员、何礼文、王红军
数据收集及整理
徐卫明、郇丛明 王红军、吕炳煌、王湘
确认改善计划的实施
徐卫明、郇丛明、吕炳煌 王红军、李玲、谢秋菊等
针对不良问题进行分析,改善,具体实施
通过此表填写此表可以增强操作人员责任感,大大减少因人为因素造成的不良。
宁波嘉彰电子五金有限公司
包装制程人员安排记录表
机种:
料号:
时间:
日期: 生产总数:
工号/姓名 工位/主要负责工作 发现不良品数量统计 工号/姓名 工位/主要负责工作 发现不良品数量统计
备注:A:漏攻牙 B牙孔开裂(破损)C压伤 D变形 E刮伤 F漏工程 G其它________
5
异色
100%
4
毛刺
100.00% 90.00% 80.00% 70.00% 60.00% 50.00% 40.00% 30.00% 20.00% 10.00% 0.00%
不良 数
不良 累计 百分 比
10月24日至10月28日清洗不良项目分析
350
98.29% 99.14% 100.0100%0.00%
▪
每天都是美好的一天,新的一天开启 。20.11.720.11.721:3821:38:5221:38:52Nov- 20
▪