综述cae技术的发展和应用.doc
cad,cae,cam的发展综述总结

CAD/CAE/CAM在化工产品中应用
目前,产品制造正向着高质量、高效率和低成本方向发展 ,产品轻小化,功能多样化,零件复杂化使得人们不断的寻 求更方便,更完善的设计途径、加工方法与工艺,尽可能的 优化零件的各技术参数与结构特征。 CAD/CAM/CAE系统的开发与应用为现代制造与加工领域带 来了新的技术革新。化工设备在生产过程中承受多种外力 的作用,因此其零部件要能够确保生产的安全,满足各种工 况的要求,具有好的设计结构以及长的使用寿命。 CAD/CAM/CAE技术能够对化工设备中各零部件进行合理的 结构设计与分析,进行动态仿真以及性能评定等,确保化工 设备具有良好
CAE技术的产生与发展
20世纪60~70年代,CAE技术处在探索发展阶段。这 一时期的有限元技术主要针对结构分析问题进行发 展,以解决航空航天技术发展过程中所遇到的结构 强度、刚度以及模拟实验和分析问题。1963年 Dr.Richard MacNeal和Mr.Robert Schwndler投资 成立MSC公司,开发了称之为SADSAM的结构分析软 件 20世纪70~80年代是CAE技术蓬勃发展时期。开发了 机械系统仿真软件ADAMS、结构非线性分析软件 ABAQUS等 20世纪90年代是CAE技术成熟壮大阶段。CAE软件发 展商积极发展与各CAD软件的专用接口并增强软件 的前后置处理能力
CAM技术的产生与发展
1952年MIT试制成功世界上第一台数控铣床,开发 了APT自动编程系统 20世纪70年代末以后,开发了CATIA、EUCLID、 UGNX、INTERGRAPH、Pro/ENGINEER、MasterCAM及 NPU/GNCP等系统,解决了几何造型、零件几何形状 的显示,交互设计、修改及刀具轨迹生成,走刀过 程的仿真显示、验证等问题 20世纪80年代是CAM技术迅速发展的时期,得CAM技 术得到了广发应用。同时发展了CAPP、CAQ等技术, 推动了CIMS的发展 从20世纪90年代起,CAM技术向标准化、集成化、 智能化的方向发展
03-CAE技术及其发展
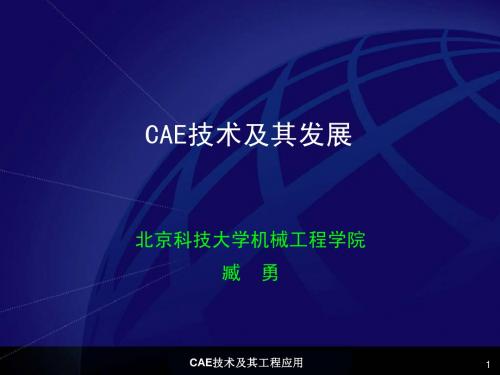
5
1 概述
1.0 概念 CAE
CAE,是用计算机辅助求解复杂工程和产品结构强度、 刚度、屈曲稳定性、动力响应、热传导、三维多体接触 、弹塑性等力学性能的分析计算以及结构性能的优化设 计等问题的一种近似数值分析方法。 CAE系统的核心思想是结构的离散化,就是将实际结构 离散为有限数目的规则单元组合体,实际结构的物理性 能可以通过对离散体进行分析,得出满足工程精度的近 似结果来替代对实际结构的分析。
CAE技术及其工程应用 技术及其工程应用
16
2 现状
2.2 结构
通用CAE的算法与软件模块 通用CAE的算法与软件模块 CAE
CAE技术及其工程应用 技术及其工程应用
17
2.2 结构
2.2.1 前处理
三维实体建模与参数化建模; 三维实体建模与参数化建模; 构件的布尔运算; 构件的布尔运算; 有限元自动剖分与节点自动编号; 有限元自动剖分与节点自动编号; 节点参数自动生成; 节点参数自动生成; 荷载与材料数据输入与公式化导入,节点荷载自动生成; 荷载与材料数据输入与公式化导入,节点荷载自动生成; 有限元模型信息自动生成, ...。 有限元模型信息自动生成, ...。
CAE技术及其工程应用 技术及其工程应用
8
1 概述
1.2 作用 工程师进行创新设计的重要手段和工具 工程和制造企业的生命力在于工程/ 工程和制造企业的生命力在于工程/产品的 创新,而对于工程师来说, 创新,而对于工程师来说,实现创新的关 除了设计思想和概念之外, 键,除了设计思想和概念之外,最主要的 技术手段,就是采用先进可靠的CAE软件。 CAE软件 技术手段,就是采用先进可靠的CAE软件。
CAE技术及其工程应用 技术及其工程应用
关于cae技术及其应用的参考文献
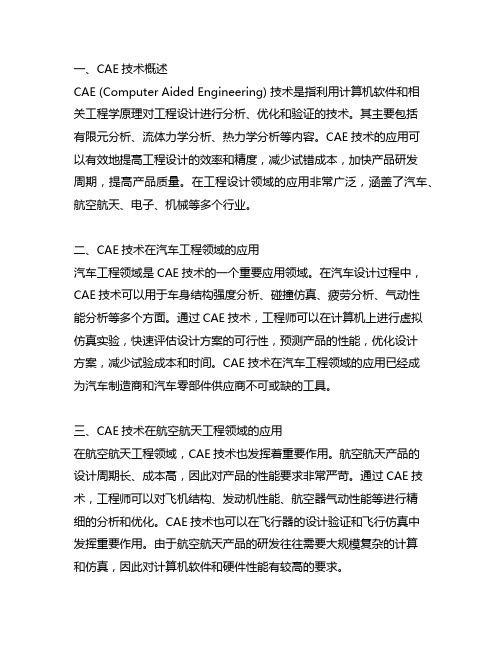
一、CAE技术概述CAE (Computer Aided Engineering) 技术是指利用计算机软件和相关工程学原理对工程设计进行分析、优化和验证的技术。
其主要包括有限元分析、流体力学分析、热力学分析等内容。
CAE技术的应用可以有效地提高工程设计的效率和精度,减少试错成本,加快产品研发周期,提高产品质量。
在工程设计领域的应用非常广泛,涵盖了汽车、航空航天、电子、机械等多个行业。
二、CAE技术在汽车工程领域的应用汽车工程领域是CAE技术的一个重要应用领域。
在汽车设计过程中,CAE技术可以用于车身结构强度分析、碰撞仿真、疲劳分析、气动性能分析等多个方面。
通过CAE技术,工程师可以在计算机上进行虚拟仿真实验,快速评估设计方案的可行性,预测产品的性能,优化设计方案,减少试验成本和时间。
CAE技术在汽车工程领域的应用已经成为汽车制造商和汽车零部件供应商不可或缺的工具。
三、CAE技术在航空航天工程领域的应用在航空航天工程领域,CAE技术也发挥着重要作用。
航空航天产品的设计周期长、成本高,因此对产品的性能要求非常严苛。
通过CAE技术,工程师可以对飞机结构、发动机性能、航空器气动性能等进行精细的分析和优化。
CAE技术也可以在飞行器的设计验证和飞行仿真中发挥重要作用。
由于航空航天产品的研发往往需要大规模复杂的计算和仿真,因此对计算机软件和硬件性能有较高的要求。
四、CAE技术在电子产品设计领域的应用随着电子产品的不断更新换代,产品设计的竞争日益激烈。
CAE技术在电子产品设计领域应用广泛,例如电路仿真、热学分析、电磁兼容性分析等。
通过CAE技术,工程师可以在产品设计的早期阶段发现问题,避免在后期产生成本和时间上的浪费。
尤其对于高频高速电子产品,如通信设备、计算机芯片等,CAE技术的应用更加重要。
五、CAE技术发展趋势随着计算机硬件性能的不断提升和计算机仿真软件的不断完善,CAE 技术在工程领域的应用前景十分广阔。
浅谈CAE技术现状及发展趋势
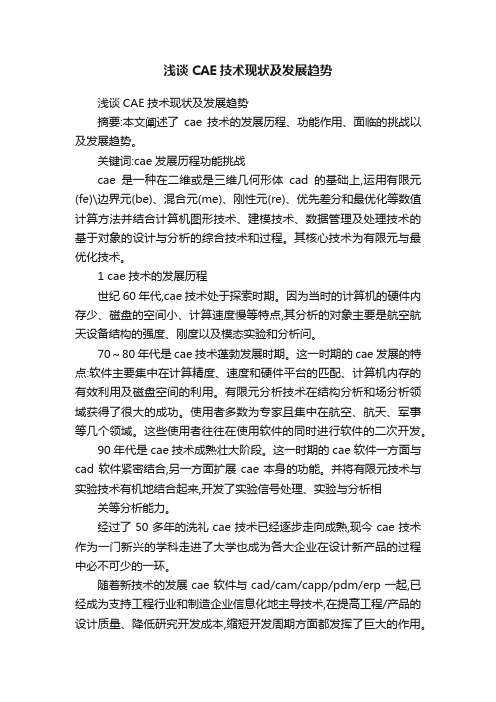
浅谈CAE技术现状及发展趋势浅谈CAE技术现状及发展趋势摘要:本文阐述了cae技术的发展历程、功能作用、面临的挑战以及发展趋势。
关键词:cae发展历程功能挑战cae是一种在二维或是三维几何形体cad的基础上,运用有限元(fe)\边界元(be)、混合元(me)、刚性元(re)、优先差分和最优化等数值计算方法并结合计算机图形技术、建模技术、数据管理及处理技术的基于对象的设计与分析的综合技术和过程。
其核心技术为有限元与最优化技术。
1 cae技术的发展历程世纪60年代,cae技术处于探索时期。
因为当时的计算机的硬件内存少、磁盘的空间小、计算速度慢等特点,其分析的对象主要是航空航天设备结构的强度、刚度以及模态实验和分析问。
70~80年代是cae技术蓬勃发展时期。
这一时期的cae发展的特点:软件主要集中在计算精度、速度和硬件平台的匹配、计算机内存的有效利用及磁盘空间的利用。
有限元分析技术在结构分析和场分析领域获得了很大的成功。
使用者多数为专家且集中在航空、航天、军事等几个领域。
这些使用者往往在使用软件的同时进行软件的二次开发。
90年代是cae技术成熟壮大阶段。
这一时期的cae软件一方面与cad软件紧密结合,另一方面扩展cae本身的功能。
并将有限元技术与实验技术有机地结合起来,开发了实验信号处理、实验与分析相关等分析能力。
经过了50多年的洗礼cae技术已经逐步走向成熟,现今cae技术作为一门新兴的学科走进了大学也成为各大企业在设计新产品的过程中必不可少的一环。
随着新技术的发展cae软件与cad/cam/capp/pdm/erp一起,已经成为支持工程行业和制造企业信息化地主导技术,在提高工程/产品的设计质量、降低研究开发成本,缩短开发周期方面都发挥了巨大的作用。
但对于cae技术的用户企业和提供商而言,cae技术仍然面临着使用复杂,工程师理论知识缺乏,缺少经验以及计算机硬件与软件结合等诸多问题2 cae技术的功能和作用(1)采用各种优化技术,找出产品的最佳设计方案。
(发展战略)综述CAE技术的发展和应用最全版
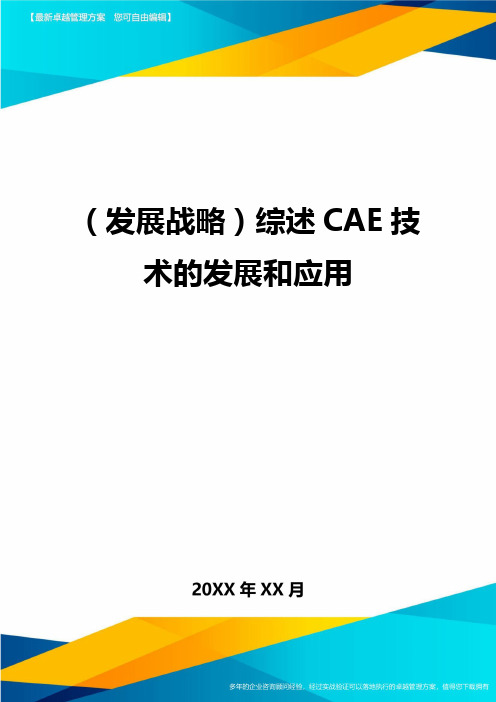
(发展战略)综述CAE技术的发展和应用综述CAE技术的发展和应用引言CAE(计算机辅助工程)的特点是以工程和科学问题为背景,建立计算模型且进行计算机仿真分析。
壹方面,CAE技术的应用,使许多过去受条件限制无法分析的复杂问题,通过计算机数值模拟得到满意的解答;另壹方面,计算机辅助分析使大量繁杂的T程分析问题简单化,使复杂的过程层次化,节省了大量的时间,避免了低水平重复的工作,使工程分析更快、更准确。
在产品的设计、分析、新产品的开发等方面发挥了重要作用,同时cAE这壹新兴的数值模拟分析技术在国外得到了迅猛发展,技术的发展又推动了许多相关的基础学科和应用科学的进步。
1概论CAE技术1.1CAE技术简述CAE即计算机辅助工程是用计算机辅助求解复杂丁程和产品结构强度、刚度、屈曲稳定性、动力响应、热传导、三维多体接触、弹塑性等力学性能的分析计算以及结构性能的优化设计等问题的壹种近似数值分析方法。
随着计算机技术的普及和不断提高,CAE系统的功能和计算精度都有很大提高,各种基于产品数字建模的CAE系统应运而生,且已成为结构分析和结构优化的重要工具,同时也是计算机辅助4c系统(CAD,CAE,CAPP/CAM)的重要环节。
CAD(计算机辅助设计)、CAM(计算机辅助制造)和CAPP(计算机辅助工艺)等都属于计算机辅助工程(CAE),而计算流体动力学CFD 和有限元分析(FEA)等则是支撑CAE的分析工具和手段。
采用CAD技术来建立CAE 的几何模型和物理模型。
完成分析数据的输入,通常称此过程为CAE的前处理。
同样,CAE的结果也需要用CAD技术生成形象的图形输出,如生成位移图、应力、温度、压力分布的等值线图,表示应力、温度、压力分布的彩色明暗图,以及随机械载荷和温度载荷变化生成位移、应力、温度、压力等分布的动态显示图。
我们称这壹过程为CAE的后处理。
1.2CAE技术发展历程CAE的理论基础有限元法:20世纪40年代起源于土木工程和航空工程中的弹性和结构分析问题的研究。
CAE技术的发展、应用及我国推广现状

CAE技术的发展、应用及我国推广现状[引言]:模具是生产各种工业产品的重要工艺装备,随着塑料工业的迅速发展以及塑料制品在航空、航天、电子、机械、船舶和汽车等工业部门的推广应用,产品对模具的要求越来越高,传统的模具设计方法已无法适应产品更新换代和提高质量的要求。
计算机辅助工程(CAE)技术已成为塑料产品开发、模具设计及产品加工中这些薄弱环节的最有效的途经。
同传统的模具设计相比,CAE技术无论在提高生产率、保证产品质量,还是在降低成本、减轻劳动强度等方面,都具有很大优越性。
近几年,CAE技术在汽车、家电、电子通讯、化工和日用品等领域逐步地得到了广泛应用。
一、CAE技术--模具设计的发展趋势目前,世界塑料成型CAE软件市场由美国上市公司Moldflow公司主导,该公司是专业从事注塑成型CAE软件和咨询公司,自1976年发行了世界上第一套流动分析软件以来,一直在此领域居领先地位。
利用CAE技术可以在模具加工前,在计算机上对整个注塑成型过程进行模拟分析,准确预测熔体的填充、保压、冷却情况,以及制品中的应力分布、分子和纤维取向分布、制品的收缩和翘曲变形等情况,以便设计者能尽早发现问题,及时修改制件和模具设计,而不是等到试模以后再返修模具。
这不仅是对传统模具设计方法的一次突破,而且对减少甚至避免模具返修报废、提高制品质量和降低成本等,都有着重大的技术经济意义。
在今天,塑料模具的设计不但要采用CAD技术,而且还要采用CAE技术。
这是发展的必然趋势。
注塑成型分两个阶段,即开发/设计阶段(包括产品设计、模具设计和模具制造)和生产阶段(包括购买材料、试模和成型)。
传统的注塑方法是在正式生产前,由于设计人员凭经验与直觉设计模具,模具装配完毕后,通常需要几次试模,发现问题后,不仅需要重新设置工艺参数,甚至还需要修改塑料制品和模具设计,这势必增加生产成本,延长产品开发周期。
采用CAE技术,可以完全代替试模,CAE技术提供了从制品设计到生产的完整解决方案,在模具制造之前,预测塑料熔体在型腔中的整个成型过程,帮助研判潜在的问题,有效地防止问题发生,大大缩短了开发周期,降低生产成本。
论CAE技术的发展应用及我国推广现状

论CAE技术的发展、应用及我国推广现状作者:汪豪蒂机械工程及自动化1108班201103130297[引言]:模具是生产各种工业产品的重要工艺装备,随着塑料工业的迅速发展以及塑料制品在航空、航天、电子、机械、船舶和汽车等工业部门的推广应用,产品对模具的要求越来越高,传统的模具设计方法已无法适应产品更新换代和提高质量的要求。
计算机辅助工程(CAE)技术已成为塑料产品开发、模具设计及产品加工中这些薄弱环节的最有效的途经。
同传统的模具设计相比,CAE技术无论在提高生产率、保证产品质量,还是在降低成本、减轻劳动强度等方面,都具有很大优越性。
近几年,CAE技术在汽车、家电、电子通讯、化工和日用品等领域逐步地得到了广泛应用。
一、CAE技术--模具设计的发展趋势目前,世界塑料成型CAE软件市场由美国上市公司Moldflow公司主导,该公司是专业从事注塑成型CAE软件和咨询公司,自1976年发行了世界上第一套流动分析软件以来,一直在此领域居领先地位。
利用CAE技术可以在模具加工前,在计算机上对整个注塑成型过程进行模拟分析,准确预测熔体的填充、保压、冷却情况,以及制品中的应力分布、分子和纤维取向分布、制品的收缩和翘曲变形等情况,以便设计者能尽早发现问题,及时修改制件和模具设计,而不是等到试模以后再返修模具。
这不仅是对传统模具设计方法的一次突破,而且对减少甚至避免模具返修报废、提高制品质量和降低成本等,都有着重大的技术经济意义。
在今天,塑料模具的设计不但要采用CAD技术,而且还要采用CAE技术。
这是发展的必然趋势。
注塑成型分两个阶段,即开发/设计阶段(包括产品设计、模具设计和模具制造)和生产阶段(包括购买材料、试模和成型)。
传统的注塑方法是在正式生产前,由于设计人员凭经验与直觉设计模具,模具装配完毕后,通常需要几次试模,发现问题后,不仅需要重新设置工艺参数,甚至还需要修改塑料制品和模具设计,这势必增加生产成本,延长产品开发周期。
计算机辅助工程(CAE)的发展及应用

浅谈计算机辅助工程(CAE)的发展及应用摘要计算机辅助工程,即cae(computer aided engineering),是一个涉及面广、集多学科与工程技术于一体的综合性、知识密集型技术。
在产品开发阶段,企业应用cae能有效地对零件和产品进行仿真检测,确定产品和零件的相关技术参数,发现产品缺陷、优化产品设计,并极大降低产品开发成本。
在产品维护检修阶段能分析产品故障原因,分析质量因素等。
目前,cae主要应用于汽车、航空、电子、土木工程、通用机械、兵器、核能、石油和化工等行业。
本文主要阐述了计算机辅助工程的发展过程,介绍了计算机辅助工程软件的分类和应用现状,并着重对有限元软件abaqus的应用架构进行了详细介绍。
关键词计算机辅助工程;有限元;abaqus中图分类号tb237 文献标识码a 文章编号1674-6708(2010)25-0232-021 cae技术发展概述cae是以有限元法、有限差分法及有限体积法为数学基础发展起来的。
其中有限元分析在cae中运用最广,基于有限元技术的cae软件,在数量及应用范围上都处于主要地位。
有限单元法的基本思想是将物体离散成有限个简单单元的组合,用这些单元的集合来模拟或逼近原来的物体,从而将一个连续的无限自由度问题简化为离散的有限自由度问题。
物体被离散后,通过对其中各个单元进行单元分析,最终得到对整个物体的分析结构。
随着单元数目的增加,解的近似程度将不断增大和逼近真实情况。
cae技术发展大致可分为4个阶段(与计算机硬件发展密切相关):第一阶段是上世纪五六十年代,主要开发基本的结构分析程序,基于力法和简单的二维和三维位移有限元法;第二阶段是上世纪七十年代,主要开发通用有限元程序,如nastran、ansys、marc、sap等,也产生了混合元和杂交元理论,形成高效数值求解器,线性静力问题求解基本成熟;第三阶段是上世纪八十年代,主要完善及扩充通用有限元软件,产生了结构优化设计技术、前后置处理软件及计算机辅助设计系统,出现了断裂力学的奇异元技术、边界元技术、有限元与其他数值方法联合求解技术;第四阶段从上世纪九十年代中期至今,是微机、网络和仿真时代,一方面,计算结构技术软件适应新的计算机环境;另一方面,计算结构技术与其他学科的综合技术发展迅速,迎来了结构仿真和虚拟验证时代的到来。
- 1、下载文档前请自行甄别文档内容的完整性,平台不提供额外的编辑、内容补充、找答案等附加服务。
- 2、"仅部分预览"的文档,不可在线预览部分如存在完整性等问题,可反馈申请退款(可完整预览的文档不适用该条件!)。
- 3、如文档侵犯您的权益,请联系客服反馈,我们会尽快为您处理(人工客服工作时间:9:00-18:30)。
综述CAE技术的发展和应用引言CAE(计算机辅助工程)的特点是以工程和科学问题为背景,建立计算模型并进行计算机仿真分析。
一方面,CAE技术的应用,使许多过去受条件限制无法分析的复杂问题,通过计算机数值模拟得到满意的解答;另一方面,计算机辅助分析使大量繁杂的T程分析问题简单化,使复杂的过程层次化,节省了大量的时间,避免了低水平重复的工作,使工程分析更快、更准确。
在产品的设计、分析、新产品的开发等方面发挥了重要作用,同时cAE这一新兴的数值模拟分析技术在国外得到了迅猛发展,技术的发展又推动了许多相关的基础学科和应用科学的进步。
1 概论CAE技术1.1 CAE技术简述CAE即计算机辅助工程是用计算机辅助求解复杂丁程和产品结构强度、刚度、屈曲稳定性、动力响应、热传导、三维多体接触、弹塑性等力学性能的分析计算以及结构性能的优化设计等问题的一种近似数值分析方法。
随着计算机技术的普及和不断提高,CAE系统的功能和计算精度都有很大提高,各种基于产品数字建模的CAE系统应运而生,并已成为结构分析和结构优化的重要工具,同时也是计算机辅助4c系统(CAD,CAE,CAPP /CAM)的重要环节。
CAD(计算机辅助设计)、CAM(计算机辅助制造)和CAPP(计算机辅助工艺)等都属于计算机辅助工程(CAE),而计算流体动力学CFD和有限元分析(FEA)等则是支撑CAE的分析工具和手段。
采用CAD技术来建立CAE的几何模型和物理模型。
完成分析数据的输入,通常称此过程为CAE的前处理。
同样,CAE的结果也需要用CAD技术生成形象的图形输出,如生成位移图、应力、温度、压力分布的等值线图,表示应力、温度、压力分布的彩色明暗图,以及随机械载荷和温度载荷变化生成位移、应力、温度、压力等分布的动态显示图。
我们称这一过程为CAE的后处理。
1.2 CAE技术发展历程CAE的理论基础有限元法:20世纪40年代起源于土木工程和航空工程中的弹性和结构分析问题的研究。
它的发展可以追溯到Alexander Hrennikoff(1941)和Richard courant(1942)的工作,他们的方法具有共同的本质特征:利用网格离散化将一个连续区域转化为一族离散的子区域,通常叫做元。
HrenfIikofr的丁作离散用类似于格子的网格离散区域;Courant的方法将区域分解为有限个三角形的子区域,用于求解来源于圆柱体转矩问题的二阶椭圆偏。
Courant的贡献推动了有限元的发展。
1963一1964年Besseling等确认了有限元法是处理连续介质问题的一种普遍方法。
而后,随着计算机技术的广泛应用和发展,有限元技术依靠数值计算方法,才迅速发展起来。
近10年来。
有限元法的应用范围有了大幅度的提高,已由简单的弹性力学的平面问题扩展到空间问题、板壳问题,由静力问题扩展到稳定性问题、动力学问题和波动问题;分析对象从弹性材料扩展到塑性、粘塑性和复合材料,从固体力学扩展到流体力学、传热学、电磁学等连续介质力学领域。
将有限元分析技术逐渐由传统的分析和校核扩展到优化设计,并与计算机辅助设计(CAD)和计算机辅助制造(CAM)密切结合,形成了现在CAE技术框架。
CAE软件的发展:早期的CAE软件只是计算处理特殊单一问题的简单程序。
上个世纪60年代开始出现大型通用CAE软件。
在此期间世界三大CAE软件公司:MSC、SDEC和ANSYS先后成立。
1963年Msc公司开发了sADsAM结构分析软件。
在1965年Msc 参与美国国家航空及宇航局(NASA)发起的计算结构分析方法研究,SADsAM也正式更名为Msc/NASTRAN。
1967年sDRC公司成立,在1971年推出商用有限元分析软件supertab(I—DEAs)。
1970年sAsI公司成立,后来重组后改为称ANSYS公司,开发了ANSYS通用有限元分析软件。
20世纪70—80年代是CAE技术的蓬勃发展时期,这期间许多CAE软件公司相继成立。
如致力于发展用于高级1二程分析通用有限元程序的MARc公司;致力于机械系统仿真软件开发的MDI公司;针对大结构、流固耦合、热及噪声分析的csAR公司;致力于结构、流体、流固耦合分析的ADIND公司等等。
90年代,各CAD软件开发商一方面大力发展自身CAD软件的功能.如CA,11A、SOUDw0RKs、UG都增加了基本的CAE前后处理及简单的线性、模态方面通过并购另外的cAE软件来增加其软件的cAE功能,如PK(PR0/E)对RAsAN的收购。
在cAD软件商大力增强其软件cAE功能的同时,cAE分析软件也在向cAD靠拢。
如MAc/NATTRAN 在1994年收购了PATRAN作为自己的前后处理软件,并先后开发了与cAllA、UG等cAD软件的数据接口。
ANsYs也在大力发展其软件的ANsYs前后处理功能。
sDRc公司利用I—DEAs自身的cAD功能强大的优势,积极开发与别的cAD模型传输接口。
先后投放了与PR0/E、UG、cArl’IA等的接口,以保证cAD,cAE的相关性。
同时cAE软件也在积极扩展本身的功能。
ANsYS把其产品扩展为ANsY洲EcHNIcAL。
ANsYs,lS-DYNA。
ANsYs,PREP0sT等多个应用软件。
sDRc则在自己的单一分析模型的基础上先后形成了多专项应用技术,并将有限元技术与实验技术有机地结合起来。
2 CAE技术在内燃机设计中的应用内燃机作为动力机械,其各项指标涉及到燃烧、排放、油耗、密封、强度、噪声等多方面内容,所以对应的分析也涉及到热力学、流动力学、动力学、疲劳分析等多个方面。
而且内燃机的许多零部件,如曲柄连杆机构和配气机构的形状结构、受力,以及发动机的流动、传热传质、燃烧等工作过程十分复杂。
因此建立这些零部件及整机的数学模型是十分困难的,而求解数学模型则更为闲难。
另外在现代内燃机中由于对内燃机的性能和可靠性指标愈来愈高,其中的一些参数的变化趋势相互制约,参数优化空间相对变小,研发的风险加大;产品开发需要考虑的变量不断增加。
系统的复杂性增大;要求缩短产品开发的周期;降低产品开发的成本和风险。
为满足现代内燃机丁业的发展需要,必须对传统的“绘图+经验+发动机台架试验”的设计方法进行改进。
按照现代研发的基本流程,一款内燃机的研发主要包括设计、试验、试制、投产等阶段。
cAE分析主要涉及设计和试验阶段,设计和验证阶段的数字化开发可细分为概念设计阶段、布置设计阶段和详细设计阶段。
每个阶段都包含了数字化设计和验证工作的并行和协同:设计工程师按照时间进度提交零部件、装配的子系统及整机的CAD设计数据;验证t 程师应用CAE手段对设计部门提交的CAD数据进行包括最基本的尺寸和运动学校核、复杂的动力学分析和功能实现以及最复杂的可靠性分析等进行全方位验证。
2.1概念设计阶段概念设计阶段是发动机产品开发流程中进入工程化开发过程的第一阶段,也是最重要的阶段。
理论上来说,有关所开发产品的所有重大决策性问题都要在这一阶段内解决。
概念设计阶段的主要工作有:对前期项目策划阶段完成的市场、法规、竞争对手和竞争机型调查研究的结果进行分析和评估,并转换为概念设计阶段的设计输入;产品设计、工艺设计、生专家们在概念设计阶段需协同进行可行性研究工作;根据产品的市场定位和仓业品牌的内涵,结合当前行业的技术发展水平等因素。
确定所开发产品在性能、质量、成本等方面适当的目标水平、具体指标和规格要求;进行整机系统总体布置研究;确定产品的总体技术方案和各子系统的总体技术路线等。
此阶段的cAE分析多以一维分析为主,以基本结构和基本参数为输入,在整机级和各大系统级建立虚拟样,通过cAE分析方法确定发动机的基本性能、冷却系统布置、曲轴系布置和与整车的匹配等。
此阶段的cAE 分析任务有:内燃机气体交换过程模拟,此类分析软件主要有GT—Power和AVL-B00st等。
内燃机热动力学分析和整机性能预测.在气体交换的基础上增加发动机缸内燃烧过程的仿真分析,预测发动机的总体性能,如功率、扭矩和燃油消耗率等。
然后反过来确定进气系统、排气系统、由缸盖、缸体和活塞组成的燃烧系统等子系统的主要参数和技术方案。
内燃机冷却系统一维cFD分析.此类分析软件有cT-C砌等。
内燃机润滑系统一维cFD分析,此类分析软件有f'10wM艄ter 等。
装备该内燃机的整车的基本性能仿真分析,该类分析软件主要有AVL—Cmise 和GT—Drive等。
2.2布置设计阶段:布置设计阶段主要是确定各主要零部件的尺寸和和相互之间的关系及接口,进一步对概念设计阶段确定的技术方案进行细化。
此阶段的cAD设计工作主要是根据概念设计阶段的cAE仿真结果建立内燃机各大子系统的表面模型,确定和建立各大子系统之间的装配关系和模型等。
CAE仿真分析则需要对所有的概念设计阶段的分析模型进行更新,使之更加具体和复杂,仿真的输出结果也更加详细和准确。
同时。
增加新的一些cAE仿真分析内容和领域,涉及动力学、有限元、cFD 分析等,如应用MsC.ADAMs等行业常用的专业软件建立分析模型,首先埘前端轮系和配气机构子系统的布置设计结果进行各运动零部件之间的装配和运动学关系进行检查和校核.然后开始动力学分析。
缸盖、缸体、曲轴、凸轮轴和连杆五大主要零部件的有限元分析,常用的分析软件有Hyperworks、NAsTRAN、ABAQus、AVL—ExCl7I等。
2.3详细设计阶段:详细设计阶段,数字化开发范围将覆盖所有新设计零部件的全部特性,包括如详细的尺寸、尺寸和几何公差、设计基准、表面粗糙度、热处理和材料技术条件等,在详细设计阶段结束时将保证每一个零部件的cAD设计数据(包括i维实体设计数据和二维平面设计数据)将能具体指导工厂的生产制造,因此,cAD设计的工作量急剧增长,成为详细设计阶段的主要1二作。
同时,在详细设计阶段将应用CAE分析手段对所有新设计零部件的CAD设计进行分析和验证,以确保在数字化开发阶段解决每个新设计的零部件以及从零部件到各子系统、最后到整机的每个层次都不存在问题。
此阶段,CAE分析的首要任务是对前两个阶段所有的分析模型根据详细设计阶段能够获得的最全面的设计信息进行最后的更新和拓展,进一步更准确地验证各零部件、系统和整机的功能和特性。
比如在概念设计和布置设计阶段进行的发动机气体交换一维cFD分析的基础上将进一步拓展和更新到进行一维或三维的进排气噪声分析,进排气系统和发动机缸内流动的=三维cFD分析。
目的是从三维角度考察发动机的气体交换过程和流体在发动机缸内的流动过程,保证发动机各缸进排气的均匀度和发动机缸内流动的最佳化,以及在保证发动机性能设计指标的前提下尽量降低发动机的进排气噪声。
在详细设计阶段所有零部件和子系统新的CAD设计都必须经CAE仿真分析验证,确保任何设计问题解决后,开发流程才能进入样机制造和验证阶段。